干法刻蚀

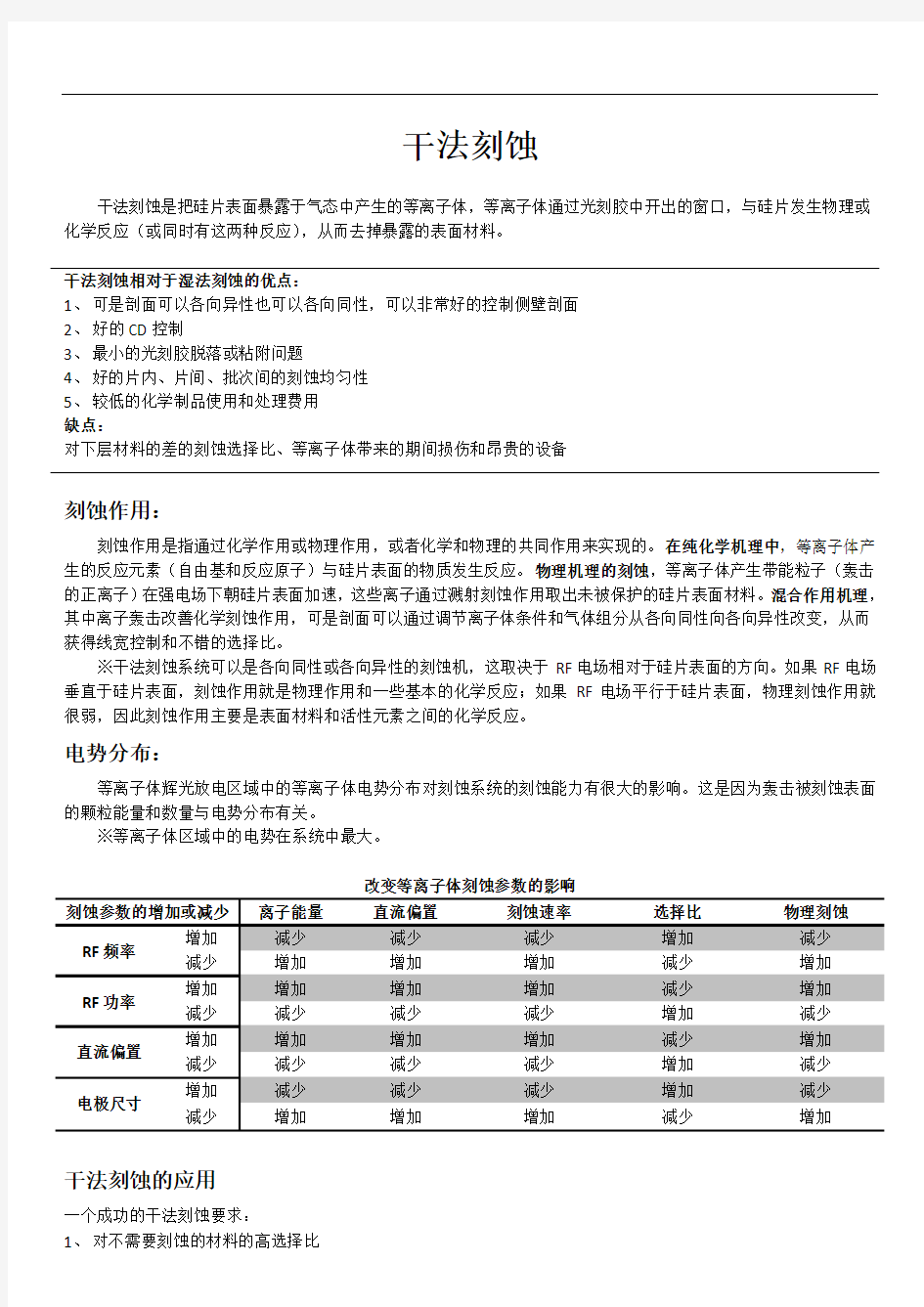
1、刻蚀速率
刻蚀速率是指在刻蚀过程中去除硅片表面材料的速度,通常用?/min表示。
※?:埃米,1埃米Angstrom =1/10000000000米(10的负10次方)。
刻蚀速率=△T/t(?/min)
△T=去掉的材料厚度(?或μm)
t=刻蚀所用的时间(分)
※负载效应:刻蚀速率和刻蚀面积成反比。
2、刻蚀剖面
刻蚀剖面是指被刻蚀图形的侧壁形状。
※各向同性和各向异性:各向同性,刻蚀在各个方向的速率一致;各向异性,刻蚀在各个方向的速率不一致。
3、刻蚀偏差
刻蚀偏差是指刻蚀以后线宽或关键尺寸间距的变化。
刻蚀偏差=W b-W a
W b=刻蚀前光刻胶的线宽
W a=光刻胶去掉后被刻蚀材料的线宽
4、选择比
选择比指的是在同一刻蚀条件下一种材料与另一种材料的刻蚀速率比。
选择比S R=E f/E r
E f=被刻蚀材料的刻蚀速率
E r=掩蔽层材料的刻蚀速率(如光刻胶)
5、均匀性
刻蚀均匀性是一种衡量刻蚀工艺在整个硅片上,或整个一批,或批与批之间刻蚀能力的参数。
※ARDE,微负载效应。
6、残留物
刻蚀残留物是刻蚀以后留在硅片表面不想要的材料。它常常覆盖在腔体内壁或被刻蚀图形的底部。
7、聚合物
聚合物是在刻蚀过程中由光刻胶中的碳转化而来并与刻蚀气体(如C2F4)和刻蚀生成物结合在一起形成的。
8、等离子体诱导损伤
A、一种主要的损伤是非均匀等离子体在晶体管栅电极产生陷阱电荷,引起薄栅氧化硅的击穿。
B、另一种器件损伤是能量粒子对暴露的栅氧化层的轰击。发生在刻蚀时栅电极的边缘。
9、颗粒沾污和缺陷
等离子体带来的硅片损伤有时也由硅片表面附近的等离子体产生的颗粒沾污而引起的。由于电势的差异,颗粒产生在等离子体和壳层的界面处。当没有等离子体时,这些颗粒就会掉到硅片表面。氟基化学气体等离子体比氯基或溴基等离子体产生较少的颗粒,因为氟产生的刻蚀生成物具有较高的蒸汽压。
干法刻蚀是把硅片表面暴露于气态中产生的等离子体,等离子体通过光刻胶中开出的窗口,与硅片发生物理或化学反应(或同时有这两种反应),从而去掉暴露的表面材料。
干法刻蚀相对于湿法刻蚀的优点:
1、可是剖面可以各向异性也可以各向同性,可以非常好的控制侧壁剖面
2、好的CD控制
3、最小的光刻胶脱落或粘附问题
4、好的片内、片间、批次间的刻蚀均匀性
5、较低的化学制品使用和处理费用
缺点:
对下层材料的差的刻蚀选择比、等离子体带来的期间损伤和昂贵的设备
刻蚀作用:
刻蚀作用是指通过化学作用或物理作用,或者化学和物理的共同作用来实现的。在纯化学机理中,等离子体产生的反应元素(自由基和反应原子)与硅片表面的物质发生反应。物理机理的刻蚀,等离子体产生带能粒子(轰击的正离子)在强电场下朝硅片表面加速,这些离子通过溅射刻蚀作用取出未被保护的硅片表面材料。混合作用机理,其中离子轰击改善化学刻蚀作用,可是剖面可以通过调节离子体条件和气体组分从各向同性向各向异性改变,从而获得线宽控制和不错的选择比。
※干法刻蚀系统可以是各向同性或各向异性的刻蚀机,这取决于RF电场相对于硅片表面的方向。如果RF电场垂直于硅片表面,刻蚀作用就是物理作用和一些基本的化学反应;如果RF电场平行于硅片表面,物理刻蚀作用就很弱,因此刻蚀作用主要是表面材料和活性元素之间的化学反应。
电势分布:
等离子体辉光放电区域中的等离子体电势分布对刻蚀系统的刻蚀能力有很大的影响。这是因为轰击被刻蚀表面的颗粒能量和数量与电势分布有关。
※等离子体区域中的电势在系统中最大。
干法刻蚀的应用
一个成功的干法刻蚀要求:
1、对不需要刻蚀的材料的高选择比
2、获得可以接受的产能的刻蚀速率
3、好的侧壁剖面控制
4、好的片内均匀性
5、低的器件损伤
6、宽的工艺制造窗口
※对于每一种特殊的干法刻蚀应用,关键的刻蚀工艺参数通过工艺优化来确定。
硅的干法刻蚀:
硅的等离子体干法刻蚀是硅片制造中的一项关键工艺技术,用等离子体刻蚀的两个主要硅层是制作MOS栅结构的多晶硅栅和制作器件隔离或DRAM电容结构中的单晶硅槽。
◆多晶硅栅刻蚀:在MOS器件中,掺杂的LPCVD多晶硅是用做栅极的导电材料。
掺杂多晶硅线宽决定了有源器件的栅长,并会影响晶体管的性能。刻蚀多晶硅(硅)通常是一个三步工艺工程。这使得在不同的刻蚀步骤中能对各向异性刻蚀和选择比进行优化。这三个步骤是:A、第一步是预刻蚀,用于去除自然氧化层、硬的掩蔽层(如SiON)和表面污染物来获得均匀的刻蚀。B、接下来的是刻蚀至终点的主刻蚀。这一步用来刻蚀掉大部分的多晶硅膜,并不损伤栅氧化层和获得理想的各向异性的侧壁剖面。C、最后一步是过刻蚀,用于去除刻蚀残留物和剩余的多晶硅,并保证对栅氧化层的高选择比,这一步应避免在多晶硅周围的栅氧化层形成微槽。
※多晶硅栅是难以刻蚀的结构,在刻蚀过程中需要仔细且精密。具有0.15μm特征尺寸器件的栅氧化层厚度是20~30?(等于6到10个氧化硅原子层的厚度)。氧化硅厚度的损伤不得超过5?(大约1.5个氧化硅原子层)。为了防止栅氧化层的穿透,刻蚀的选择比要大于150:1;为了去除刻蚀残留物和多余的多晶硅,过刻的选择比要大于250:1。
◆单晶硅的刻蚀:单晶硅刻蚀主要用于制作沟槽,如器件隔离沟槽或高密度DRAM IC中的垂直电容的制作。
※在集成电路中硅槽的刻蚀要求对每一个沟槽都进行精确地控制。在微米甚至亚微米结构中,每个沟槽都要求一致的光洁度、接近垂直的侧壁、正确的深度和圆滑的沟槽顶角和底角。
金属的干法刻蚀
金属刻蚀的一个主要应用是作为金属互联线的铝合金刻蚀。
金属刻蚀的要求主要有以下几点:
1、高刻蚀速率(大于1000nm/min)。
2、对下面层的高选择比,对掩蔽层(大于4:1)和层间介质层(大于20:1)。
3、高的均匀性,且CD控制很好,没有微负载效应(在硅片上的任何位置小于8%)。
4、没有等离子体诱导充电带来的期间损伤。
5、残留污染少(如铜硅残留物、显影液侵蚀和表面缺陷)。
6、快速去胶,通常是在一个专用的去胶腔体中进行,不会带来残留物污染。
7、不会腐蚀金属。
◆铝和金属复合层:通常用氯基气体来刻蚀铝。为了得到各向异性的刻蚀工艺,必须在刻蚀气体中加入聚合物(如CHF3或从光刻胶中获得的碳)来对侧壁进行钝化。
典型步骤:
1、取出自然氧化层的预刻蚀。
2、刻蚀ARC层(可能与上一步结合起来)。
3、刻铝的主刻蚀。
4、去除残留物的过刻蚀,它可能是主刻蚀的延续。
5、阻挡层的刻蚀。
6、为防止侵蚀残留物的选择性去除。
7、去除光刻胶。
※等离子体去胶:去胶机是通过氧原子与光刻胶在等离子体环境中发生反应来去除光刻胶的。原子氧通过微波或RF能量分解氧分子而生成。也常常加入N2或H2来提高去胶性能并加强对残留聚合物的去除。光刻胶的基本成分是碳氢化合物。氧原子很快与光刻胶反应生成挥发性的一氧化碳和二氧化碳和水等主要生成物。这些生成物可以被真空系统抽走。
◆钨:钨是在多层金属结构中常用的一种用于通孔填充的重要金属。可用氟基或氯基气体来刻蚀钨。
※常常在氟基的刻蚀气体中加入N2来获得对光刻胶的好的选择比;有时加入O2来减少碳的沉积。氯基气体(如CL2和CCL4)能用来刻蚀钨并改善各向异性特性和选择比。
常见的干法刻蚀检查及故障排除方法
问题可能的原因纠正措施
1.刻蚀速率不对A.RF功率发生变化检查和修复RF发生器和匹配单元
B.温度不对检查硅片背冷系统
C.压力有问题校准真空计(如电容压力计)和压力控制系统
D.终点监测不能正常工作检查终点监测系统
E.硅片间距不合适检查硅片与电极的间距
F.气体流量不合适校验气体运输系统
G.维护不当湿法清洗腔体
H.刻蚀程序不对校验工艺程序和参数
2.选择比不够A.刻蚀速率太快校验刻蚀速率
B.不适合的气体流量或压力校正MFC和真空计
C.终点监测有问题检验/校正终点检测
D.错误的硅片温度检验硅片冷却系统
E.工艺程序不对确认工艺程序和参数
3.侧壁角度不合适A.侧壁沾污检查腔体内的聚合物生成
B.硅片温度硅片的背面沾污引起加热不均匀
C.系统压力检查/校正MFC和检漏以检查是否有沾污
D.工艺程序不对工艺错误
4.片内刻蚀不均匀A.由于ARDE带来的刻蚀气体浓度损耗校验硅片上密的和不密区域的设计
B.不适合的气体流量检查/校正气体输运系统
C.硅片的温度检查热电偶和硅片冷却系统
D.硅片在腔体中的位置不合适检查硅片自动传送系统的真空卡盘
E.腔体结构检查反应器和电极板间距
F.膜厚不合适测量和校验膜厚
G.维护不当湿法清洗腔体
5.等离子体损伤A.等离子体不均匀等离子体设备设计和维护差
B.栅氧化层过量的离子轰击不是最佳的工艺条件
C.RF功率过大
D.维护不当
6.颗粒沾污A.气体管路的泄漏和沾污MFC漏气或有问题
B.操作问题不恰当的关机、操作或维护
C.不合适的化学气体错误的工艺顺序
进行湿法清洗
7.金属侵蚀A.潮湿刻蚀后清除残留物时间太长
B.气流检查MFC,使用正确的工艺气体
C.刻蚀工艺带来的沾污控制去胶的时间
D.错误地维护程序检查维护程序
干法刻蚀工艺
干法刻蚀工艺 干法刻蚀工艺可分为物理性刻蚀与化学性刻蚀两种方式。物理性刻蚀是利用辉光放电将气体(如氩)电离成带正电的离子,再利用偏压将离子加速,溅击在被刻蚀物的表面而将被刻蚀物的原子击出,该过程完全是物理上的能量转移,故称为物理性刻蚀。其特色在于,具有非常好的方向性,可获得接近垂直的刻蚀轮廓。但是由于离子是全面均匀地溅射在芯片上,所以光刻胶和被刻蚀材料同时被刻蚀,造成刻蚀选择性偏低。同时,被击出的物质并非挥发性物质,这些物质容易二次沉积在被刻蚀薄膜的表面及侧壁上。因此,在超大规模集成化制作工艺中,很少使用完全物理方式的干法刻蚀方法。 化学性刻蚀或称为等离子体刻蚀( PLASMA Etching,PE),是利用等离子体将刻蚀气体电离并形成带电离子、分子及反应性很强的原子团,它们扩散到被刻蚀薄膜表面后与被刻蚀薄膜的表面原子反应生成具有挥发性的反应产物,并被真空设备抽离反应腔。因这种反应完全利用化学反应,故称为化学性刻蚀。这种刻蚀方式与前面所讲的湿法刻蚀类似,只是反应物与产物的状态从液态改为气态,并以等离子体来加快反应速率。因此,化学性干法刻蚀具有与湿法刻蚀类似的优点与缺点,即具有较高的掩膜/底层的选择比及等向性。鉴于化学性刻蚀等向性的缺点,在半导体工艺中,只在刻蚀不需要图形转移的步骠(如光刻胶的去除)中应用纯化学刻蚀方法。 最为广泛使用的方法是结合物理性的离子轰击与化学反应的反应离子刻蚀( RIE)。这种方式兼具非等向性与高刻蚀选择比的双重优点。刻蚀的进行主要靠化学反应来实现,加入离子轰击的作用有两方面。 1)破坏被刻蚀材质表面的化学键以提高反应速率。 2)将二次沉积在被刻蚀薄膜表面的产物或聚合物打掉,以使被刻蚀表面能充分与刻蚀气体接触。由于在表面的二次沉积物可被离子打掉,而在侧壁上的二次沉积物未受到离子的轰击,可以保留下来阻隔刻蚀表面与反应气体的接触、使得侧壁不受刻蚀,所以采用这种方式可以获得非等向性的刻蚀效果。 当应用于法刻蚀时,主要应注意刻蚀速率、均匀度、选择比及刻蚀轮廓等因素。
干法刻蚀工艺总结
干法刻蚀工艺总结 离子束刻蚀机(IBE-150A) 背景: 利用辉光放电原理将氩气分解为氩离子,氩离子经过阳极电场的加速对样品表面进行物理轰击,以达到刻蚀的作用。把Ar、Kr或Xe之类惰性气体充入离子源放电室并使其电离形成等离子体,然后由栅极将离子呈束状引出并加速,具有一定能量的离子束进入工作室,射向固体表面撞击固体表面原子,使材料原子发生溅射,达到刻蚀目的,属纯物理过程。 技术指标: 装片:一片六英寸衬底、或1片四英寸,向下兼容。 抽气速度:30min由ATM到1.0×10-3Pa 极限真空度:2×10-4Pa 离子能量:300eV-400eV
ICP刻蚀机(OXFORD ICP 180) 背景: 通入反应气体使用电感耦合等离子体辉光放电将其分解,产生的具有强化学活性的等离子体在电场的加速作用下移动到样品表面,对样品表面既进行化学反应生成挥发性气体,又有一定的物理刻蚀作用。因为等离子体源与射频加速源分离,所以等离子体密度可以更高,加速能力也可以加强,以获得更高的刻蚀速率,以及更好的各向异性刻蚀。另外,由于该系统使用了Cl基和Br基的刻蚀气体,因此该ICP系统适合于对Ⅲ-Ⅴ族化合物材料进行刻蚀。 技术指标: ICP离子源:0~3000W RF射频源:0~600W 装片:1片四英寸,向下兼容 基底刻蚀温度:0℃-200℃可调。 刻蚀气体:BCl 3、Cl 2 、HBr、Ar、O 2 可刻蚀材料包括:GaN、GaAs、InP等Ⅲ-Ⅴ族化合物材料
ICP刻蚀机(STS HRM) 背景: 通入反应气体使用电感耦合等离子体辉光放电将其分解,产生的具有强化学活性的等离子体在电场的加速作用下移动到样品表面,对样品表面既进行化学反应生成挥发性气体,又有一定的物理刻蚀作用。因为等离子体源与射频加速源分离,所以等离子体密度可以更高,加速能力也可以加强,以获得更高的刻蚀速率,以及更好的各向异性刻蚀。该系统使用了F基的刻蚀气体,具有Bosch工艺,适合于对硅材料进行大深宽比刻蚀。 技术指标: ICP离子源:0-3000W RF射频源:0-600W 装片系统:六英寸,向下兼容 基底刻蚀温度:0℃-200℃可调。 刻蚀气体:SF6、C4F8、O2、Ar 可刻蚀材料包括:硅材料
半导体工艺 干法刻蚀 铝刻蚀
干法刻蚀之铝刻蚀 在集成电路的制造过程中,刻蚀就是利用化学或物理方法有选择性地从硅片表面去除不需要的材料的过程。从工艺上区分,刻蚀可以分为湿法刻蚀和干法刻蚀。前者的主要特点是各向同性刻蚀;后者是利用等离子体来进行各向异性刻蚀,可以严格控制纵向和横向刻蚀。 干法的各向异性刻蚀,可以用表面损伤和侧壁钝化两种机制来解释。表面损伤机制是指,与硅片平行的待刻蚀物质的图形底部,表面的原子键被破坏,扩散至此的自由基很容易与其发生反应,使得这个方向的刻蚀得以持续进行。与硅片垂直的图形侧壁则因为表面原子键完整,从而形态得到保护。侧壁钝化机制是指,刻蚀反应产生的非挥发性的副产物,光刻胶刻蚀产生的聚合物,以及侧壁表面的氧化物或氮化物会在待刻蚀物质表面形成钝化层。图形底部受到离子的轰击,钝化层会被击穿,露出里面的待刻蚀物质继续反应,而图形侧壁钝化层受到较少的离子轰击,阻止了这个方向刻蚀的进一步进行。 在半导体干法刻蚀工艺中,根据待刻蚀材料的不同,可分为金属刻蚀、介质刻蚀和硅刻蚀。金属刻蚀又可以分为金属铝刻蚀、金属钨刻蚀和氮化钛刻蚀等。目前,金属铝作为连线材料,仍然广泛用于DRAM和flash等存储器,以及以上的逻辑产品中。本文着重介绍金属铝的刻蚀工艺。
金属铝刻蚀通常用到以下气体:Cl2、BCl3、Ar、 N2、CHF3和C2H4等。Cl2作为主要的刻蚀气体,与铝发生化学反应,生成的可挥发的副产物AlCl3被气流带出反应腔。BCl3一方面提供BCl3+,垂直轰击硅片表面,达到各向异性的刻蚀。另一方面,由于铝表面极易氧化成氧化铝,这层自生氧化铝在刻蚀的初期阻隔了Cl2和铝的接触,阻碍了刻蚀的进一步进行。添加BCl3 则利于将这层氧化层还原(如方程式1),促进刻蚀过程的继续进行。 Al2O3 + 3BCl3→ 2AlCl3 + 3BOCl (1) Ar电离生成Ar+,主要是对硅片表面提供物理性的垂直轰击。 N2、CHF3和C2H4是主要的钝化气体,N2与金属侧壁氮化产生的AlxNy,CHF3和C2H4与光刻胶反应生成的聚合物会沉积在金属侧壁,形成阻止进一步反应的钝化层。 一般来说,反应腔的工艺压力控制在6-14毫托。压力越高,在反应腔中的Cl2浓度越高,刻蚀速率越快。压力越低,分子和离子的碰撞越少,平均自由程增加,离子轰击图形底部的能力增强,这样刻蚀反应速率不会降低甚至于停止于图形的底部。
干法刻蚀技术
蚀刻技术 最早的蚀刻技术是利用特定的溶液与薄膜间所进行的化学反应来去除薄膜 未被光阻覆盖的部分,而达到蚀刻的目的,这种蚀刻方式也就是所谓的湿式蚀刻。因为湿式蚀刻是利用化学反应来进行薄膜的去除,而化学反应本身不具方向性,因此湿式蚀刻过程为等向性,一般而言此方式不足以定义3微米以下的线宽,但对于3微米以上的线宽定义湿式蚀刻仍然为一可选择采用的技术。 湿式蚀刻之所以在微电子制作过程中被广泛的采用乃由于其具有低成本、高可靠性、高产能及优越的蚀刻选择比等优点。但相对于干式蚀刻,除了无法定义较细的线宽外,湿式蚀刻仍有以下的缺点:1) 需花费较高成本的反应溶液及去离子水;2) 化学药品处理时人员所遭遇的安全问题;3) 光阻附着性问题;4) 气泡形成及化学蚀刻液无法完全与晶圆表面接触所造成的不完全及不均匀的蚀刻; 5) 废气及潜在的爆炸性。 湿式蚀刻过程可分为三个步骤:1) 化学蚀刻液扩散至待蚀刻材料之表面; 2) 蚀刻液与待蚀刻材料发生化学反应; 3) 反应后之产物从蚀刻材料之表面扩散至溶液中,并随溶液排出(3)。三个步骤中进行最慢者为速率控制步骤,也就是说该步骤的反应速率即为整个反应之速率。 大部份的蚀刻过程包含了一个或多个化学反应步骤,各种形态的反应都有可能发生,但常遇到的反应是将待蚀刻层表面先予以氧化,再将此氧化层溶解,并随溶液排出,如此反复进行以达到蚀刻的效果。如蚀刻硅、铝时即是利用此种化学反应方式。 湿式蚀刻的速率通常可藉由改变溶液浓度及温度予以控制。溶液浓度可改变反应物质到达及离开待蚀刻物表面的速率,一般而言,当溶液浓度增加时,蚀刻速率将会提高。而提高溶液温度可加速化学反应速率,进而加速蚀刻速率。 除了溶液的选用外,选择适用的屏蔽物质亦是十分重要的,它必须与待蚀刻材料表面有很好的附着性、并能承受蚀刻溶液的侵蚀且稳定而不变质。而光阻通常是一个很好的屏蔽材料,且由于其图案转印步骤简单,因此常被使用。但使用光阻作为屏蔽材料时也会发生边缘剥离或龟裂的情形。边缘剥离乃由于蚀刻溶液的侵蚀,造成光阻与基材间的黏着性变差所致。解决的方法则可使用黏着促进剂来增加光阻与基材间的黏着性,如Hexamethyl-disilazane (HMDS)。龟裂则是因为光阻与基材间的应力差异太大,减缓龟裂的方法可利用较具弹性的屏蔽材质来吸收两者间的应力差。 蚀刻化学反应过程中所产生的气泡常会造成蚀刻的不均匀性,气泡留滞于基材上阻止了蚀刻溶液与待蚀刻物表面的接触,将使得蚀刻速率变慢或停滞,直到气泡离开基材表面。因此在这种情况下会在溶液中加入一些催化剂增进蚀刻溶液与待蚀刻物表面的接触,并在蚀刻过程中予于搅动以加速气泡的脱离。 以下将介绍半导体制程中常见几种物质的湿式蚀刻:硅、二氧化硅、氮化硅及铝。 5-2-1 硅的湿式蚀刻 在半导体制程中,单晶硅与复晶硅的蚀刻通常利用硝酸与氢氟酸的混合液来进行。此反应是利用硝酸将硅表面氧化成二氧化硅,再利用氢氟酸将形成的二氧化硅溶解去除,反应式如下: Si + HNO3 + 6HF à H2SiF6 + HNO2 + H2 + H2O 上述的反应中可添加醋酸作为缓冲剂(Buffer Agent),以抑制硝酸的解离。而蚀刻速率的调整可藉由改变硝酸与氢氟酸的比例,并配合醋酸添加与水的稀释
1干法刻蚀和湿法刻蚀
1 干法刻蚀和湿法刻蚀 干法刻蚀是把硅片表面暴露于空气中产生的等离子体,等离子体通过光刻胶中开出的窗口,与硅片发生物理或化学反应,从而去掉暴露的表面材料。 湿法腐蚀是以液体化学试剂以化学方式去除硅片表面的材料。 2刻蚀速率是指在刻蚀过程中去除硅片表面材料的速度,通常用。A/min表示 刻蚀速率=T/t(。A/min) 其中T=去掉的材料厚度 t=刻蚀所用的时间 为了高的产量,希望有高的刻蚀速率。 3刻蚀选择比指的是同一刻蚀条件下一种材料与另一种刻蚀材料相比刻蚀速率快多少。他定义为被刻蚀材料的刻蚀速率与另一种材料的刻蚀速率的比。 干法刻蚀的选择比低,通常不能提供对下一层材料足够高的刻蚀选择比。 高选择比意味着只刻除想要刻去的那层。 4干法刻蚀的主要目的完整的把掩膜图形复制到硅片表面上。 优点:刻蚀剖面是各向异性,具有非常好的侧壁剖面控制, 好的CD控制 最小的光刻胶脱落或粘附问题 好的片内,片间,批次间的刻蚀均匀性 较低的化学制品使用和处理费用 不足:对下层材料的差的刻蚀选择比,等离子体带来的器件损伤和昂贵的设备。 5化学机理:等离子体产生的反应元素与硅片表面的物质发生反应,为了获得高的选择比,进入腔体的气体都经过了慎重选择。等离子体化学刻蚀由于它是各向同性的,因而线宽控制差。 物理机理:等离子体产生的带能粒子在强电场下朝硅片表面加速,这些离子通过溅射刻蚀作用去除未被保护的硅片表面材料。 6基本部件:发生刻蚀反应的反应腔,一个产生等离子体的射频电源,气体流量控制系统,去除刻蚀生成物和气体的真空系统。 氟刻蚀二氧化硅,氯和氟刻蚀铝,氯,氟和溴刻蚀硅,氧去除光刻胶。 7 ECR反应器在1-10毫托的工作压力下产生很密的等离子体,他在磁场环境中采用微波激励源来产生高密度等离子体。ECR反应器的一个关键点是磁场平行于反映剂的流动方向,这使得自由电子由于磁力的作用做螺旋形运动。当电子的回旋频率等于所加的微波电场频率时,能有效把电能转移到等离子体中的电子上。这种振荡增加了电子碰撞的可能性,从而产生高密度的等离子体,获得大的离子流。 8氟基气体 三个步骤:1,预刻蚀,用于去除自然氧化层,硬的掩蔽层和表面污染物来获得均匀的刻蚀2,刻至终点的主刻蚀,用来刻蚀大部分的多晶硅膜,并不损伤栅氧化层和获得理想的各向异性的侧壁剖面。
综述报告——刻蚀简介
微加工技术——刻蚀简介 自从半导体诞生以来,很大程度上改变了人类的生产和生活。半导体除了在计算机领域应用之外,还广泛地应用于通信、网络、自动遥控及国防科技领域。本文主要介绍半导体制造工艺中的刻蚀工艺。随着半导体制造大规模集成电路技术的发展,图形加工线条越来越细,硅片尺寸越来越大,对刻蚀工艺的要求也越来高。因此,学习了解刻蚀工艺十分必要。本文将主要从刻蚀简介、刻蚀参数及现象、干法刻蚀和湿法刻蚀四个方面进行论述。 1、刻蚀简介 1.1 刻蚀定义及目的 刻蚀就是用化学的、物理的或同时使用化学和物理的方法,有选择地把没有被抗蚀剂掩蔽的那一部分薄膜层除去,从而在薄膜上得到和抗蚀剂膜上完全一致的图形。刻蚀的基本目的,是在涂光刻胶(或有掩膜)的硅片上正确的复制出掩膜图形[1]。 刻蚀,通常是在光刻工艺之后进行。通过刻蚀,在光刻工艺之后,将想要的图形留在硅片上。从这一角度而言,刻蚀可以被称之为最终的和最主要的图形转移工艺步骤。在通常的刻蚀过程中,有图形的光刻胶层〔或掩膜层)将不受到腐蚀源显著的侵蚀或刻蚀,可作为掩蔽膜,保护硅片上的部分特殊区域,而未被光刻胶保护的区域,则被选择性的刻蚀掉。其工艺流程示意图如下。
1.2 刻蚀的分类 从工艺上分类的话,在半导体制造中有两种基本的刻蚀工艺:干法刻蚀和湿法腐蚀。 干法刻蚀,是利用气态中产生的等离子体,通过经光刻而开出的掩蔽层窗口,与暴露于等离子体中的硅片行物理和化学反应,刻蚀掉硅片上暴露的表面材料的一种工艺技术法[1]。该工艺技术的突出优点在于,是各向异性刻蚀(侧向腐蚀速度远远小于纵向腐蚀速度,侧向几乎不被腐蚀),因此可以获得极其精确的特征图形。超大规模集成电路的发展,要求微细化加工工艺能够严格的控制加工尺寸,要求在硅片上完成极其精确的图形转移。任何偏离工艺要求的图形或尺寸,都可能直接影响产品性能或品质,给生产带来无法弥补的损害。由于干法刻蚀技术在图形转移上的突出表现,己成为亚微米尺寸下器件刻蚀的最主要工艺方法。在特征图形的制作上,已基本取代了湿法腐蚀技术。 对于湿法腐蚀,就是用液体化学试剂(如酸、碱和溶剂等)以化学的方式去除硅片表面的材料。当然,在通过湿法腐蚀获得特征图形时,也要通过经光刻开出的掩膜层窗口,腐蚀掉露出的表面材料。但从控制图形形状和尺寸的准确性角度而言,由于湿法刻蚀是各向同性刻蚀(侧向与纵向腐蚀速度相同),在形成特征图形方面,湿法腐蚀一般只被用于尺寸较大的情况(大于3微米)。由于这一特点,湿法腐蚀远远没有干法刻蚀的应用广泛。但由于它的高选择比和批量制作模式,湿法腐蚀仍被广泛应用在腐蚀层间膜、去除干法刻蚀残留物和颗粒等工艺步骤中。干法刻蚀和湿法刻蚀的区别可以见如下示意图。 (a)湿法刻蚀的各向同性刻蚀剖面(b)干法刻蚀的各向异性刻蚀剖面从刻蚀材料上来分类的话,刻蚀主要可分为金属刻蚀、介质刻蚀、硅(多晶硅)刻蚀。
硅的干法刻蚀简介
https://www.360docs.net/doc/ec8576813.html, → 着硅珊MOS器件的出现,多晶硅渐渐成为先进器件材料的主力军。除了用作MOS栅 极之外多晶硅还广泛应用于DRAM的深沟槽电容极扳填充,闪存工艺中的位线和字线。这些工艺的实现都离不开硅的干法刻蚀技术其中还包括浅槽隔离的单晶硅刻蚀和金属硅化物的刻蚀。为了满足越来越苛刻的要求,业界趋向于采用较低的射频能量并能产生低压和高密度的等离子体来实现硅的干法刻蚀。感应耦合等离子刻蚀技术(ICP)被广泛应用于硅及金属硅化物刻蚀,具有极大技术优势和前景。它比典型的电容耦合(CCP)等离子刻蚀技术高出10 ̄20倍。此外,其对离子浓度和能量的独立控制扩大了刻蚀工艺窗口及性能。 硅栅(Poly Gate)的干法刻 蚀: 随着晶体管尺寸的不断缩小对硅栅的刻蚀就越具有挑战性。这种挑战体现在对关键尺寸(CD)及其均匀性的控制,即对栅氧化层选择比的提高,对剖面轮廓的一致性控制以及减少等离子导致的损伤。 因为受到光刻线宽的限制,为达到最后的CD 线宽要求往往需要先对光阻进行缩小处理,然后进一步往下刻蚀。BARC打开后,再以光阻为阻挡层将TEOS 打开。 接着把剩余的光阻去除,再以TEOS作为阻挡层对硅栅进行刻蚀。为了保护栅极氧化层不被损伤,通常要把硅栅的刻蚀分成几个步骤:主刻蚀、着陆刻蚀和过刻蚀。主刻蚀通常有比较高的刻蚀率但对氧化硅的选择比较小。通过主刻蚀可基本决定硅栅的剖面 硅的干法刻蚀简介 应用材料中国,葛强 轮廓和关键尺寸。着陆刻蚀通常对栅极氧化层有比较高的选择比以确保栅极氧化层不被损伤。一旦触及到栅极氧化层后就必须转成对氧化硅选择比更高的过刻蚀步骤以确保把残余的硅清除干净而不损伤到栅极氧化层。 CL2,HBr,HCL是硅栅刻蚀的主要气体,CL2和硅反应生成挥发性的SiCl4而HBr和硅反应生成的SiBr4 同样具有挥发性。通常会在这些主刻蚀气体中加入小流量的氧气,一方面是为了在侧壁生成氧化硅从而增加对侧壁的保护;另一方面也提高了对栅极氧化层的选择比。在标准的ICP双耦合刻蚀腔体中,HBr-O2的组合通常能达到大于100:1的选择比。为了避免伤及栅极氧化层,任何带F基的气体如CF4,SF6,NF3都不能在过刻蚀的步骤中使用。 浅沟槽(STI)的干法刻蚀: 在0.25um和以下的技术节点中,浅沟槽隔离技术被广泛应用。 因为它在减小表面积的同时提供更加有效的隔离。作为沟槽硅刻蚀的阻挡层可以直接用光阻但更多是采用氮化硅作为硅刻蚀的阻挡层。先用光阻作为氮化硅刻蚀的阻挡层,然后用氧等离子体将剩余的光阻除去,最后以氮化硅为阻挡层完成浅沟槽的刻蚀。 浅沟槽刻蚀的难点在于沟槽深度的匀度小于100仯 饩拖嗟庇谛∮?.25% 的均匀性。随着硅片尺寸的增加要达到这样的要求就必须严格控制氮化过刻蚀、BT刻蚀和浅槽刻蚀的均匀性,每一步都会对最后的结果产生影响。其次为了满足沟槽隔离氧化物的填充要求,剖面轮廓的控制也是非常重要的环节。因 随 为太垂直的轮廓不利于HDPCVD的沉积,所以通常会要求适当的倾斜度。另外随着工艺尺寸的缩小,要求达到更高的深宽比使得剖面轮廓控制和深度均匀性控制受到更大的挑战.。当然CD 的均匀性和剩余氮化硅的均匀性也是重要的技术指标。 CL2和HBr依然是浅沟槽的刻蚀的主要气体,再配合小流量的氧气和氮气来产生氮氧化硅形成侧壁钝化层从而达到理想的刻蚀剖面轮廓。氦气和氩气通常用作辅助稀释的作用。 另外浅槽底部轮廓同样影响到氧化物的填充。采用CL2 做为主刻蚀的气体容易形成比较直的剖面轮廓和凸型的底部轮廓。采用HBr 作为主刻蚀气体能得到比较斜的剖面轮廓和凹形的底部轮廓。 在实际生产中经常会遇到硅刻蚀的反应物没有被及时的清洗从而导致产品被污染的现象。这是因为硅片完成刻蚀离开反应腔时,在硅片的表面还有大量的Cl 和Br 残留。 它们具有较强的挥发 性。当硅片暴露在空气中,空气中的水汽和CL、Br形成HCL和 HBr。这些酸性物质会腐蚀和它们接触的表面形成一定程度的污染。为了防止这样的现象发生可以采用O2等离子清除表面的残留,或者利用腔体净化功能减少污染源。另外还应尽量减少硅片暴露在空气中的时间,尽快洗去表面污染物。 随着关键尺寸的不断缩小和硅片尺寸的扩大。先进的300mm 硅刻蚀工艺腔体的气体和温度多采用内圈和外圈独立的控制以满足苛刻的工艺要求。可变的腔体尺寸也是业界的方向之一。腔体内环境的控制和不同硅片的一致性控制也是生产中最常遇到的问题。
第二章干法刻蚀的介绍
第二章干法刻蚀的介绍 2. 1刻蚀、干法刻蚀和湿法腐蚀 2. 1 .1关于刻蚀 刻蚀,是指用化学或物理方法有选择地从硅片表面去除不需要的材料的过程。刻蚀的基本目的,是在涂胶(或有掩膜)的硅片上正确的复制出掩膜图形[1]。 刻蚀,通常是在光刻工艺之后进行。我们通常通过刻蚀,在光刻工艺之后,将想要的图形留在硅片上。从这一角度而言,刻蚀可以被称之为最终的和最主要的图形转移工艺步骤。在通常的刻蚀过程中,有图形的光刻胶层〔或掩膜层)将不受到腐蚀源显著的侵蚀或刻蚀,可作为掩蔽膜,保护硅片上的部分特殊区域,而未被光刻胶保护的区域,则被选择性的刻蚀掉。 2.1.2干法刻蚀与湿法刻蚀 在半导体制造中有两种基本的刻蚀工艺:干法刻蚀和湿法腐蚀。 干法刻蚀,是利用气态中产生的等离子体,通过经光刻而开出的掩蔽层窗口,与暴露于等离子体中的硅片行物理和化学反应,刻蚀掉硅片上暴露的表面材料的一种工艺技术法[1]。该工艺技术的突出优点在于,可以获得极其精确的特征图形。超大规模集成电路的发展,要求微细化加工工艺能够严格的控制加工尺寸,要求在硅片上完成极其精确的图形转移。任何偏离工艺要求的图形或尺寸,都可能直接影响产品性能或品质,给生产带来无法弥补的损害。由于干法刻蚀技术在图形轶移上的突出表现,己成为亚微米尺寸下器件刻蚀的最主要工艺方法。在特征图形的制作上,已基本取代了湿法腐蚀技术。 对于湿法腐蚀,就是用液体化学试剂(如酸、碱和溶剂等)以化学的方式去除硅片表面的材料。当然,在通过湿法腐蚀获得特征图形时,也要通过经光刻开出的掩膜层窗口,腐蚀掉露出的表面材料。但从控制图形形状和尺寸的准确性角度而言,在形成特征图形方面,湿法腐蚀一般只被用于尺寸较大的情况(大于3微米)。由于这一特点,湿法腐蚀远远没有干法刻蚀的应用广泛。但由于它的高选择比和批量制作模式,湿法腐蚀仍被广泛应用在腐蚀层间膜、去除干法刻蚀残留物和颗粒等工艺步骤中。 2. 2干法刻蚀的原理 2. 2. 1干法刻蚀中的等离子体 干法刻蚀工艺是利用气体中阴阳粒子解离后的等离子体来进行刻蚀的。所谓的等离子体,宇宙中99%的物质,均处于等子状态。其中包含了中性的粒子、离子和电子,它们混合在一起,表现为电中性。在干法刻蚀中,气体中的分子和原子,通过外部能量的激发,形成震荡,使质量较轻的电子脱离原子的轨道与相邻的分子或原子碰撞,释放出其他电子,在这样的反复过程中,最终形成气体离子与自由活性激团。而干法刻蚀,则利用了气体等离子体中的自由活性激团与离子,与被刻蚀表面进行反应,以此形成最终的特征图形[2]。 2.2.2干法刻蚀的特征 干法刻蚀与湿法腐蚀工艺利用药液处理的原理不同,干法刻蚀在刻蚀表面材料时,既存在化学反应又存在物理反应。因此在刻蚀特性上既表现出化学的等方性,又表现出物理的异方性。 所谓等方性,是指纵横两个方向上均存在刻蚀。而异方性,则指单一纵向上的刻蚀。2.2. 3干法刻蚀过程 我们可以了解到干法刻蚀的主要过程。反应腔体内气体等离子体中的离子,在反应腔体的扁压作用下,对被刻蚀的表面进行轰击,形成损伤层,从而加速了等离子中的自由活性激团在其表面的反应,经反应后产生的反应生成物,一部分被分子泵从腔体排气口排出,一部分则在刻蚀的侧壁上形成淀积层。干法刻蚀就是在自由活性激团与表面反应和反应生成物不断淀积的过程中完成的。离子轰击体现了干法刻蚀的异方性,而由于侧壁的淀积,则很好的
干法刻蚀技术的应用与发展
干法刻蚀技术的应用与发展 摘要 在半导体生产中,干法刻蚀是最主要的用来去除表面材料的刻蚀方法。而干法刻蚀是一个惯称,它指的是在低气压下雨等离子体有关的腐蚀方法。经过二十多年的发展,经历了多样化的发展过程,使技术不断完善和创新。一定程度上,干法刻蚀的水平决定了集成电路器件性能和生产规模。 本课程设计主要讨论半导体制造工艺中非常重要的步骤---刻蚀,详细描述了干法刻蚀的物理方法和化学方法以及基本原理,重点讲述干法刻蚀技术在半导体制造工艺中的应用和未来的发展。 关键词:半导体制造,刻蚀,干法刻蚀,金属刻蚀
目录 摘要 (1) 目录 (2) 第1章绪论 (3) 第2章干法刻蚀的机制和原理 (5) 2.1刻蚀工艺 (5) 2.2刻蚀作用 (5) 2.2.1 物理刻蚀 (6) 2.1.2 化学刻蚀 (7) 第3章干法刻蚀的应用 (9) 3.1介质的干法刻蚀 (9) 3.1.1 氧化物 (10) 3.1.2 氮化物 (11) 3.2硅的干法刻蚀 (11) 3.2.1 多晶硅栅刻蚀 (11) 3.2.2 单晶硅的刻蚀 (12) 3.3金属的干法刻蚀 (12) 3.3.1 铝和金属复合层 (12) 3.3.2 钨 (13) 第4章干法刻蚀设备的构成和主要性能指标 (14) 4.1.干法刻蚀设备的概述 (14) 4.2.干法刻蚀工艺流程 (15) 4.3.设备的主要的组成部分 (15) 4.4.干法刻蚀设备的主要性能指标 (16) 总结与展望 (18) 参考文献 (19) 致谢 (20)
第1章绪论 在微电子学领域中,自1948年发明晶体管,随后出现集成电路,直到整个六十年代的二十年里,半导体器件光刻工艺中对各种材料均采用不同的实际进行腐蚀,惯称湿法腐蚀。然而,当器件集成度进入中规模。结构尺寸小于十微米时,惯用的湿法腐蚀由于毛细现象和各向同性的腐蚀性就难以保证精度和重复性,迫切需要寻找新的技术途径。虽然人们早已认识到原子核游离基具有远强于分子的化学活性,但一直没有应用到对固体材料的腐蚀技术上。直至六十年代末才发现氧等离子体可用于去除残留碳化物,并成功地用于等离子体去胶工艺中。随后很快地发展了半导体器件工艺中的干法刻蚀技术。自七十年代初,以辉光放电产生的气体等离子体进行腐蚀加工。至今三十多年,经历了多样化的发展过程,使技术不断得到完善和创新。它的发展是与集成电路的高速发展有着密切关系的。反过来说,干法刻蚀的水平很大程度上决定了集成电路器件和生产规模。 广义而言,所谓的刻蚀技术,是将显影后所产生的光阻图案忠实地转印到光阻下的材质上,形成由光刻技术定义的图形。它包含了将材质整面均匀移除及图案选择性部分去除,可分为湿式刻蚀(wet etching)和干式刻蚀(dry etching)两种技术。湿式刻蚀具有待刻蚀材料与光阻及下层材质良好的刻蚀选择比(selectivity)。然而,由于化学反应没有方向性,因而湿式刻蚀是各向同性刻蚀。当刻蚀溶液做纵向刻蚀时,侧向的刻蚀将同时发生,进而造成底切(Undercut)现象,导致图案线宽失真,如下图所示。 图1-1 底切现象 自1970年以来,元件制造首先开始采用电浆刻蚀技术(也叫等离子体刻蚀技术),人们对于电浆化学性的了解与认识也就越来越深。在现今的半导体集成电路或LCD制造过程中,要求精确地控制各种材料尺寸至次微米大小,而且还必须具有极高的再现性,
干法刻蚀
1、刻蚀速率 刻蚀速率是指在刻蚀过程中去除硅片表面材料的速度,通常用?/min表示。 ※?:埃米,1埃米Angstrom =1/10000000000米(10的负10次方)。 刻蚀速率=△T/t(?/min) △T=去掉的材料厚度(?或μm) t=刻蚀所用的时间(分) ※负载效应:刻蚀速率和刻蚀面积成反比。 2、刻蚀剖面 刻蚀剖面是指被刻蚀图形的侧壁形状。 ※各向同性和各向异性:各向同性,刻蚀在各个方向的速率一致;各向异性,刻蚀在各个方向的速率不一致。 3、刻蚀偏差 刻蚀偏差是指刻蚀以后线宽或关键尺寸间距的变化。 刻蚀偏差=W b-W a W b=刻蚀前光刻胶的线宽 W a=光刻胶去掉后被刻蚀材料的线宽 4、选择比 选择比指的是在同一刻蚀条件下一种材料与另一种材料的刻蚀速率比。 选择比S R=E f/E r E f=被刻蚀材料的刻蚀速率 E r=掩蔽层材料的刻蚀速率(如光刻胶) 5、均匀性 刻蚀均匀性是一种衡量刻蚀工艺在整个硅片上,或整个一批,或批与批之间刻蚀能力的参数。 ※ARDE,微负载效应。 6、残留物 刻蚀残留物是刻蚀以后留在硅片表面不想要的材料。它常常覆盖在腔体内壁或被刻蚀图形的底部。 7、聚合物 聚合物是在刻蚀过程中由光刻胶中的碳转化而来并与刻蚀气体(如C2F4)和刻蚀生成物结合在一起形成的。 8、等离子体诱导损伤 A、一种主要的损伤是非均匀等离子体在晶体管栅电极产生陷阱电荷,引起薄栅氧化硅的击穿。 B、另一种器件损伤是能量粒子对暴露的栅氧化层的轰击。发生在刻蚀时栅电极的边缘。 9、颗粒沾污和缺陷 等离子体带来的硅片损伤有时也由硅片表面附近的等离子体产生的颗粒沾污而引起的。由于电势的差异,颗粒产生在等离子体和壳层的界面处。当没有等离子体时,这些颗粒就会掉到硅片表面。氟基化学气体等离子体比氯基或溴基等离子体产生较少的颗粒,因为氟产生的刻蚀生成物具有较高的蒸汽压。