2020年(发展战略)控制轧制和控制冷却技术的新发展
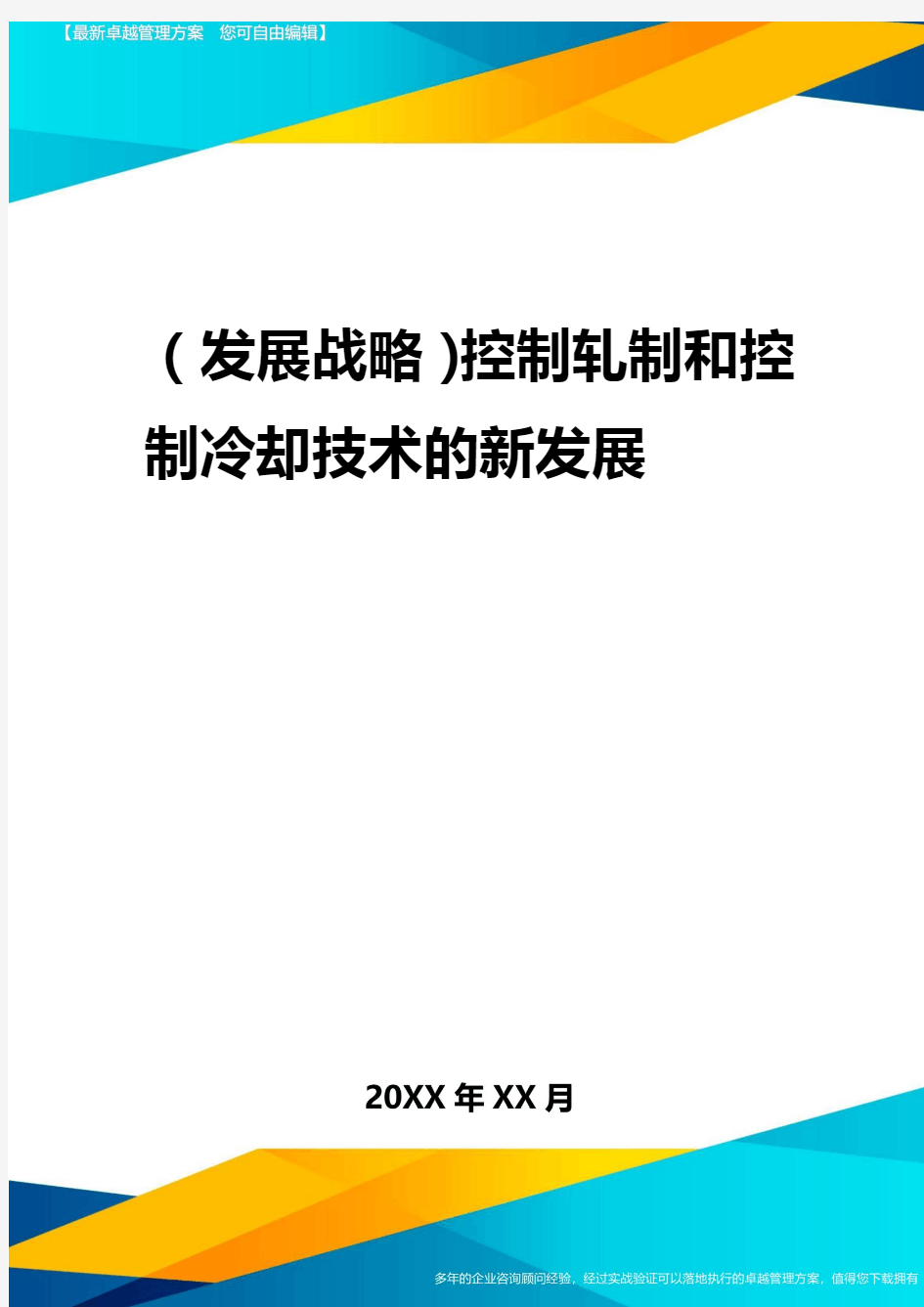

(发展战略)控制轧制和控制冷却技术的新发展
控制轧制和控制冷却技术的新发展
发表时间:2006-7-513:02:09【字体:大中小】
近代工业发展对热轧非调质钢板的性能要求越来越高,除了具有高强度外,仍要有良好的韧性、焊接性能及低的冷脆性。目前世界上许多国家均利用控轧和控冷工艺生产高寒地区使用的输油、输气管道用钢板、低碳含铌的低合金高强度钢板、高韧性钢板,以及造船板、桥梁钢板、压力容器用钢板等。1控制轧制工艺的机理和特点
控制轧制工艺是指钢坯于稳定的奥氏体区域(Ar3)或于亚稳定区域(Ar3~Ar1)内进行轧制,然后空冷或控制冷却速度,以获得铁素体和珠光体组织,某些情况下可获得贝氏体组织。现代控制轧制工艺应用了奥氏体的再结晶和未再结晶俩方面的理论,通过降低板坯的加热温度、控制变形量和终轧温度,充分利用固溶强化、沉淀强化、位错强化和晶粒细化机理,使钢板内部晶粒达到最大细化从而改变低温韧性,增加强度,提高焊接性能和成型性能。所以说,控制轧制工艺实际上是将形变和相变结合起来的壹种综合强化工艺。
控制轧制壹般有控温轧制和热机轧制俩种。
于控温轧制中,为了获得所要求的目标值,必须于规定的温度范围内进行总变形。第壹个负荷道次的开轧温度是事先通过出炉温度规定的。轧制的温度范围由规定的终轧温度决定。壹般情况下,只有轧制过程于规定的时间内中断,且将轧件
送到停歇场上进行冷却,这个终轧温度才能得到保证。于这种轧制方式中,轧制中断时的钢板厚度没有规定,轧制钢板能够取消常规的正火处理。
热机轧制是于规定的温度范围内按照所规定的压下量进行轧制,又分为俩阶段轧制和三阶段轧制。于俩阶段轧制中,轧制过程中断壹次,且使轧件冷却到下壹阶段所要求的轧制温度。于三阶段轧制中,轧制过程中断俩次。轧制阶段是由该阶段中预先给定的厚度压下量和完成该厚度压下量时的温度范围决定的。由此产生了中间厚度和各阶段之间的轧制时间。
控轧的目的是于热轧条件下,通过细化铁素体晶粒,生产出韧性好、强度高的钢材。例如,正常轧制工艺铁素体晶粒最好的情况是7~8级,直径大于20μm,而控制轧制工艺得到的铁素体晶粒为12级,其直径为5μm,这样细的晶粒是控制轧制最突出的优点。
控制轧制工艺仍能够充分发挥微量元素的作用,含有微量Nb、V、Ti等元素的普通低碳钢采用控制轧制工艺,能获得更好的综合性能。
2板带材控轧工艺过程的新方法
板带材的质量很大程度上取决于对轧制工艺过程的控制。常规方法有许多不足之处,原始凸度的设定无法对不同规格、不同材质的轧件进行跟踪控制;不均匀冷却方法具有响应太
慢的缺点。戴维.麦基XX公司对板形自动控制系统及冷却液的喷射装置进行了独特的设计,其中彼此分隔开的冷却和润滑系统(SLC)和动态轧制工艺系统(DSS)收到了很好的效果。
2.1分隔开的冷却和润滑系统(SLC)
板带材轧制大多数采用乳液来实现冷却润滑。于采用乳液冷却润滑的过程中,普遍存于乳液稳定性差、使用寿命短,尤其是轧后板带材表面质量达不到最佳程度等问题。利用分隔开的冷却和润滑系统可避免常规乳液冷却润滑给制品带来的缺陷。
该系统有俩个连于壹起的钢质冷却箱。每个冷却箱分别封住上工作辊和支承辊的辊面及下工作辊和支承辊的辊面,从而使每壹个对轧辊和冷却箱构成壹个隔离系统。上下俩个冷却箱之间有壹道缝,需轧制的带材由此通向辊缝,实现轧制。于轧制过程中把冷却系统和润滑系统分隔开,这就意味着于具备冷却润滑综合功能的基础上,仍能够分别按各自独特的功能去进行配制。SLC系统可最大限度地发挥冷却和润滑的功能,从而使轧机的功率密度大大提高。
2.2动态轧制工艺系统(DSS)
戴维.麦基XX公司利用计算机预测了全带材轧制的主要过程。充分利用计算机来建立轧制过程中的数学模型,本质上就是于线的模型参数估计。其中最为典型的例子是动态轧制
工艺系统。
该系统主要安装于热轧机组上,用于板形和断面形状的控制。由建立的数学模型和程序,根据预测的结果,连续地由轧机自适应功能进行控制。和通常的反馈式AGC系统不同之处,于于这个系统采用俩个基本自适应等级。第壹级为轧机控制的自适应,即包括轧辊的弯辊力、压下量的方式、运行速度和轧辊冷却液的分布等,使产品质量达到始终稳定壹致。第二级是预测模型所用系数的自适应,即利用于轧制过程中测得的参数经过趋势回归分析来实现。接着按实测值和模型预测值的误差值作为壹个函数来调整模型的系数。
应用DSS的主要目的是要生产出横向厚度均匀壹致的产品。3GCr15控轧新工艺的模拟研究
近年来,壹些工作者研究了轴承钢的热加工性能以及形变球化和再结晶,定量地确定了流变应力和破断应变和变形过程中的变量(应变、应变率、温度和相变)之间的关系;研究奥氏体加渗碳体的双相区形变球化,确定了变形温度和变形量是控制球化的主要因素,奥氏体化后变形有利于双相区形变球化;借助于热扭转实验机用停顿变形方法,研究了轴承钢热轧过程中的再结晶行为,确定了静态和动态再结晶,和变形温度、道次应变和道次间隔时间等之间的关系,以及于双相区发生的动态软化现象。这壹系列的工作为正确制定轴承钢控制轧制工艺提供了科学的依据。
轴承钢的各种生产工艺中,于900℃之上奥氏体单相区轧制后快冷至850~800℃的双相区内再次轧制是最有前途的新工艺。该工艺对控制轧制的推广应用、改善轴承钢的质量及提高其疲劳寿命、节省能源等方面均有重要意义。
试验表明:(1)用热扭转试验机实现了热变形模拟轴承钢控轧新工艺,证实了轴承钢经高温奥氏体单相区变形、再于奥氏体和渗碳体的双相区内变形,然后经快速球化退火,其碳化物级别和硬度均达到了对该冶金产品的标准要求。(2)于高温奥氏体单相区内变形,道次间隔期间发生静态再结晶,其再结晶完成的程度随变形道次的增加而提高。部分再结晶的应变累计效应,促进了动态再结晶的发生。于奥氏体和碳化物双相区内,除静态和动态再结晶过程之外,碳化物的形变球化也能引起明显的动态软化。(3)轴承钢采用控轧新工艺所需的终轧轧制力和轧制力矩,用平均流变应力计算公式估算,比传统轧制工艺约提高40%。
4低碳贝氏体钢的发展
于控轧的早期,主要是提高钢材的强度和获得较细的晶粒,继而于高强度的基础上,对韧性也有了相应的要求。目前已经转向更高强度、更好的韧性和较大的厚度,同时要求不恶化焊接性能。天然气输送用的管线钢要求较高的横向冲击贮存能。提高再结晶温度以下总的热轧变形量能够达到改进、提高韧性方法的效果。
于控轧的含铌钢中降低含碳量、提高含锰量的发展过程中,开发了被命名为低碳贝氏体钢和针状α-钢的低碳高锰(0.06%)相变强化钢。和传统的α珠光体钢相比,这种钢表现出连续的屈服及拉伸强度提高的特征。尽管含碳量较低,管材成形后,屈服点却有所提高。于屈强比比较低的钢材中,快速加工硬化能够超过任何因包申格效应而引起的屈服强度的降低。这种钢的组织是典型的针状铁素体或低碳贝氏体。同时于常规轧制后,即γ晶粒发生相变之后,会保持以前晶粒的清晰边界。
4.1低碳贝氏体钢
于普通轧制状态下,为达到必要的强度可添加Si、Mn、Cr、Ni和Mo等元素,或借助正火后的加速冷却使金相组织中出现壹种粒状组织,是α-Fe基体上分布块状或条状M/A相的结构,称之为粒状贝氏体。如不采取细化晶粒或补充回火以充分分解这种粒状贝氏体,对钢的韧性将有不利的影响,强韧性很难兼顾。因此,采用控轧工艺,于以较低的碳含量维持必要的韧性的同时,又改善了钢的焊接性。
4.2针状铁素体钢
为适应高寒地带大口径石油天然气输送管线工程对材料高强度、低温韧性、可焊性及良好成型性的要求,发展了C-Mn-Mo-Nb系针状铁素体(AF)钢。这种钢控轧状态的屈服点可达470~530MPa,夏氏冲击功可达165J,50%剪
切断口的转变温度(FATT)不低于-60℃。它同第壹代铁素体-珠光体管线钢相比,具有更好的焊接性能、抗延性、断裂能力、抗天然气中硫化氢腐蚀和氢诱发裂纹性能、抗大气腐蚀性能。
4.3超低碳贝氏体钢
通过控轧工艺的最佳化,新型超低碳贝氏体钢可得到具有高密度位错亚结构的均匀细小贝氏体组织和高强度、高韧性及可焊性配合的综合机械性能。低碳贝氏体钢的化学成分必须是:即使于大断面缓慢冷却的情况下,也能于贝氏体转变区发生相变,从而获得壹个高强度。和此相反,它于高的冷却速度下却不允许形成马氏体,此外这种钢必须具有高韧性以防止裂纹形成和脆性断裂。如果能成功地通过适当的化学成分和轧制时的快速冷却使γ-α相变的温度降低,就可于600~650℃的温度进行轧制。这样就能够通过晶粒细化和高的位错密度进壹步强化。为了转变成贝氏体,可通过加入Mo、B延迟铁素体和珠光体转变时间,仍能够通过加入Mn、Ni来改变转变温度。Nb具有双重作用,固溶状态下,可推迟铁素体的形成;而于析出的情况下,通过奥氏体晶粒细化来降低淬透性。V、Ti具有相似但稍差壹些的作用。碳当量的降低必然会抑制马氏体的形成,和高碳贝氏体相比,于改善焊接性能和韧性方面仍具有特殊意义。此时的碳含量低于0.01%~0.10%。含有低碳贝氏体钢的组织由上贝氏体和下
贝氏体及马氏体的混合体组成。此外,于碳含量低于0.10%时仍有另外的成分,名称不统壹,如无碳贝氏体、针状铁素体、分解铁素体或密实铁素体等等。这种组织的特点通常是针状,且通过不规则晶胞而造成大量位错。应该把这种组织和“真正的”贝氏体区别开来,因为它不是由奥氏体分解形成的,而且不含碳化物。和马氏体相反,该组织不是通过壹个分解过程产生,主要是通过壹个快速进行的再扩散过程产生的。改善上贝氏体组织韧性的方法仍有控制较小的奥氏体晶粒度以及降低碳含量,尽管密实铁素体表现出较高的强度,但含有多边形铁素体和含量密实铁素体的钢于晶粒度相同时,具有同样的脆性转变温度。含碳约0.10%~0.20%的B-Mo钢其屈服极限约为500MPa,加入铌钒钛,提高锰含量,可使韧性大大改善。
进壹步发展的目标是:(1)不含硼的Mn-Mo-Nb钢。这种钢具有由多边形铁素体和密实铁素体组成的壹种晶粒非常细的混合组织。轧制状态下得到550~600MPa的屈服极限,仍能够通过回火再提高。回火产生了时效硬化,且消除了贝氏体组织和马氏体晶界的应力。(2)含碳量低于0.01%、锰含量达到5%的钢。壹般来说,脆性转变温度可通过碳含量的降低和锰含量的提高得到改善。高的锰含量能够抑制多边形铁素体的形成。如果锰作为合金元素单独使用时,则会产生脆化现象。因为没有微合金元素造成的细晶粒硬化作用。
能够期望含低碳贝氏体组织加钼的调质钢于较薄的厚度范围内进行控轧,其屈服极限能够达到680MPa;或用价格较低的合金元素B来代替部分较贵重的合金元素。由于能够达到非常低的脆性转变温度,因此,含低碳贝氏体组织的钢就能和镍合金低温钢相竞争。故除了强度和韧性外,发展的主要着眼点是于焊接中和焊接后或于振动疲劳负荷条件下钢的加工和使用特性。含极低碳贝氏体组织的钢,于轧制状态下的屈服极限可达600MPa,回火后可达700MPa,于这种钢中起附加作用的大量的亚晶界和高的位错密度,其金相组织为针状铁素体。
近几年,东北大学等单位已经运用Gleeble热模拟实验机研究了实验钢奥氏体高温变形行为、应变诱发析出行为和连续冷却相变行为,于此基础上利用实验轧机研究了轧制和冷却工艺参数对实验钢力学性能和显微组织的影响。结果表明,通过适当的控轧和控冷工艺可使实验钢得到以细小的贝氏体为主的显微组织,达到强度和韧性的良好匹配。采用奥氏体再结晶、未再结晶、奥氏体+铁素体俩相区三段控轧工艺且配合相应的压下率,舞钢试制成功了低碳贝氏体钢——非调制低焊接冷裂纹敏感性钢WDB620。采用应变诱导轧制可显著细化铁素体组织,能得到晶粒尺寸0.92μm的超细铁素体组织。经透射电镜分析发现,超细晶铁素体内位错密度较低且有少量小角度晶界存于。
5结语
实践证明,采用控轧控冷工艺技术是生产强度高、韧性好、可焊性优良且成本低的钢板的最好办法,将应变诱导轧制技术和常规控轧工艺相结合可获得更为理想的超细晶组织。能够借鉴国内外先进的轧制工艺控制方法,消化、吸收这些新技术,充分发挥控制轧制工艺的优势,于我国现有资源的条件下,研制开发出高强、高韧性钢板,特别是低温韧性好的钢板。
自动控制技术现状及发展趋势
自动控制技术现状及发展趋势 发表时间:2017-11-03T16:38:49.533Z 来源:《电力设备》2017年第18期作者:孔德磊[导读] 摘要:自动控制技术是一项综合性技术,目前被广泛地应用于企业生产及人们的日常生活中,极大地提高了企业的生产效率及人们的生活质量。本文通过对目前我国自动控制技术的现状及其发展进行了详细的分析,从而指出自动控制技术正在向智能化、网络化、微型化以及集成化等方面发展,自动控制技术是现代化生产的基础,是提高生产效率的关键。 (河南理工大学河南焦作 454000)摘要:自动控制技术是一项综合性技术,目前被广泛地应用于企业生产及人们的日常生活中,极大地提高了企业的生产效率及人们的生活质量。本文通过对目前我国自动控制技术的现状及其发展进行了详细的分析,从而指出自动控制技术正在向智能化、网络化、微型化以及集成化等方面发展,自动控制技术是现代化生产的基础,是提高生产效率的关键。关键词:自动控制技术;现状;发展趋势一、目前我国自动控制技术的现状分析就目前我国在自动控制领域的实际情况来看,虽然自动控制技术得到了长足的发展以及比较广泛地实际应用,但是这与国外发达国家的自动控制技术水平及应用程度还有很大的差距。我国想要提高自动控制技术的水平,就必须加大投资与科研的力度,对新型的生产线要科学合理地对其进行自动化的设计及未来发展的预设,要特别注重自动化信息流的作用,从而提升我国自动控制水平及应用,进而提高我国企业的国际竞争力。从目前我国自动控制技术在应用领域中的作用来看,主要是为提高设备的运行效率。根据我国发展的具体情况,研制开发自动控制技术,从而避免研制自动控制技术的盲目性。但是,还是存在自动控制技术在研发过程中缺乏宏观层面上的明确指导,在投入实际生产中所获得的经济效益比较低的现象,在我国自主研发的自动化设备上还存在精确度比较差、可靠性比较低以及实用性比较差的现象。随着手工制造业在国家经济建设中逐渐丧失了优势地位,自动化生产在社会生产中日益显示出其生产操作简单、产品质量高及生产效率高等特点,成为企业生产中的主要模式。在我国自动控制技术的发展也是非常不平衡的,大部分生产领域的自动化程度还非常低,例如,玩具、服装等。 我国想要提高自动控制水平并不是很容易,这即需要对新的自动控制技术的研发,也要对原有企业的生产设备进行自动化改造,这样不但能够提高生产效率而且还能起到降低成本的作用。可以通过数控技术等自动控制技术改造原有机械设备,提高传统机械设备的自动化程度,从而提高设备的使用率和生产率。在机床上通过控制技术的改造,充分发挥计算计技术的优势,实现设备及生产线的自动化的改造,从而提高生产效率。 二、我国自动控制技术的发展趋势分析(一)智能化自动控制技术的发展自动控制技术水平的发展是现代化生产不断推进的动力和基础力量,在自动化生产的开始阶段,控制系统比较简单,控制规律也很简单,因此,采用常规的控制方法就可以完成作业。智能化是自动化控制技术发展的更高水平,智能化主要表现在控制的功能多样化和用途多样化,智能化是未来制造业发展的方向。随着科学技术的不断进步,现代化生产的发展方向逐步向人工智能与自动控制技术相结合应用的趋势。人工智能理论向自动控制技术领域的渗透,不但理论上而且在实践上都是新的发展途径,为智能化的自动控制技术,提供了新的思想和方法。人工智能与自动控制技术相结合,能够根据生产过程中的变化情况,对系统采取更为有效的控制。在目前许多生产领域都采用了智能化控制技术应用于生产系统中,智能化控制技术的水平和应用程度关系到企业现代化生产自动化水平及程度的高低。(二)网络化、微型化自动控制技术的发展从自动控制技术的发展历程来看,在比较长的时期内,自动控制技术都是在工业生产领域内进行的。自动控制技术为工业生产所需的各种机械设备,提供了可靠性及性能都非常高的控制设备。在科学技术快速发展的当下,各领域之间都不是独立发展进行的,而是相互借鉴促进甚至结合发展成为新的发展领域。自动控制技术的发展当然也离不开对其他领域的借鉴与冲击,其中来自工业PC的影响最为严重。网络化及微型化是将来自动控制技术发展的必然趋势,在自动控制技术系统发展的初期,其形态非常的大而且价格又非常的高。自动控制技术未来发展的方向必然也离不开网络化,网络技术在现代化生产中具有重要的作用。尤其是对生产过程中信息数据的传递以及分析起到了关键作用,对自动控制系统发现安全问题采取合理的处理措施,预防故障的发生等都起到行之有效的作用。随科学技术的不断进步,发展到现在它与以前相比已经改变了很多,正在向微型化发展而且在价格上也在逐步的下降。随着自动控制系统的控制软件的进一步的完善和发展,未来能够安装控制系统软件的市场份额将会逐步呈上涨趋势。(三)综合化自动控制技术的发展在现代化自动控制技术领域中已经建立模糊控制、智能控制及专家系统等控制技术的发展方向,这些方向自动控制技术的主要特点就是综合性。这些特殊方向性的控制系统都是以自动控制技术理论为基础,从而对整个设备或流程进行综合控制。其中涉及的理论知识比较多,不在是单一的自动控制技术知识,还包括电子技术、计算机技术、机械技术等等。自动控制技术要想得到快速的发展,从而适应并促进社会的进步,就必须把自动控制技术与相关技术相结合进而发展成为一个新的方向,这样才能够给自动控制技术领域注入新鲜养分与活力,才能提高自动控制技术的可靠性、精确性与高效性。不断发展各项自动控制技术,例如,各种控制系统、专用计算机等自动控制技术的基础技术,不断引进多个领域的新知识、新理论及新技术。对原有的自动控制技术进行不断地改进与发展,这就需要大量的新理论、新方法以及新技术对其进行补充,更需要高水平的专业人才对其进行研究与开发。随着自动控制技术的不断发展,对普通工人以及经验与技能的要求会越来越低,而对知识的要求会越来越高,相关工作人员必须具备较高的知识层次才能更好地完成自动控制技术的相关工作。当自动控制设备发展到非常高的水平后,会因为技术及管理上的原因,使得产品的废品率比较高。造成这种现象的主要原因不是设备的问题而是工作人员素质的问题,所以要大力培养适合自动控制设备工作的新型技术人才,这需要相关人员必须掌握各种与自动控制设备的新方法、新原料以及操作方法等。在自动控制技术领域只有拥有了大量的专业技术人才或相关技术的综合型人才,才能够实现对自动控制技术的有力推广,从而提高我国自动控制技术的水平。参考文献:
工业仪表与自动化控制技术新发展
工业仪表与自动化控制技术新发展 前言:在经济腾飞以及社会繁荣发展的背景下,我国工业也得到了迅猛的发展,其中,工业技术在工业发展的刚需下也实现了巨大飞跃,并且在电子信息的辅助作用下,促使工业生产技术不断走向高度自动化的方向,这种高度自动化在工业生产中不断得到了广泛的认可与普及。工业仪表与自动化技术的广泛发展表明我国已经从传统的工业生产迈向了自动化生产的高水平行业。企业的工业生产也只有在自动化的技术辅助中才能实现高效率、高产值以及低损耗的经营目标,才能在经济市场中保持有力的竞争地位,提升综合实力。因此工业仪表与自动化技术是现阶段以及未来工业技术发展与提升的重要战略部署。 一、工业仪表与自动化控制技术的应用价值 随着科技技术的不断发展,工业自动化技术也得到了提升与改善,并向着创新化以及智能化的方向不断提升。工业仪表以及自动化控制技术在实际应用中的具体内容首先是能实现自动控制技术,在进行工业生产中,将数据输入到仪器中,就能实现对仪器设备自动监管的工作,并且可以缓解施工人员的工作压力,自动实现自动切断运行线路的开关的操作,工作人员可根据实际的生产与工作设置相应的时间,保证自动控制工作,减少人为操作失误,提高工作效率与质量。其次自动化技术发挥了重要的保护机制,工业生产进程中的工作环境极其复杂,设备种类繁多,还会出现接线不规范的情况,这些现象都中都會蕴含潜在的生產安全故障,利用传统的检修以及检测方法往往难以发现这些潜在的危险因素,导致后续的一些列生产工作受到影响,此时,恰当的运用自动化控制技术就能化险为夷,及时的排查出潜在的安全故障,适当的时候切断电源,终止程序的运行,保证生产安全,提高经济效益,并保证生产继续进行;然后具有良好的监控功能,在计算机技术系统的支持与帮助下,当系统中运行的电压、电流以及功
控制轧制与控制冷却
控制轧制与控制冷却 穆安水 (材料成型及控制工程12级) [摘要]:控轧与控冷工艺是一项节约合金,简化工序,节约能源的先进轧钢技术,通过对控轧与控冷工艺的具体分析提出,控轧与控冷工艺能充分挖掘钢材的潜力,大幅度提高钢材的综合性能,通过对控轧控冷工艺在中厚板及带钢生产中应用的分析,说明控轧控冷工艺能给冶金工业及社会带来的巨大的经济效益针对传统控制轧制控制冷却(TMCP)技术存在的问题,提出了以超快冷为核心的新一代的TMCP技术,并详述了作为实现新一代TMCP技术核心手段的超快冷技术的科学内涵和工业装备开发情况。指出新一代TMCP技术综合采用细晶强化、析出强化、相变强化等多种强化机制,可以充分挖掘钢铁材料的潜力,节省资源和能源,优化现有的轧制过程,有利于钢铁工业的可持续发展。最后给出了以新一代TMCP为特征的创新轧制过程的案例。展示了该技术的广阔的应用前景。 [关键词]:控制轧制;控制冷却;超快冷技术 Abstract:controlled rolling and controlled cooling technology is a saving alloy, simplify the process, energy saving advanced rolling technology, based on the analysis of controlled rolling and controlled cooling technology, controlled rolling and controlled cooling technology can fully tap the potential of steel, greatly improve the comprehensive performance of steel, by means of controlled rolling process of controlled cooling in the applications of plate and strip production analysis, shows that controlled rolling process of controlled cooling can give huge economic benefits of metallurgical industry and the society in view of the traditional control rolling control problems of cooling (TMCP) technology, proposed the ultra fast cooling as the core of the new generation of TMCP technology, and described as a new generation of TMCP technology core means of scientific connotation of ultra fast cooling technology and industrial equipment development.Pointed out that a new generation of TMCP technology integrated with fine grain strengthening, precipitation strengthening, phase transformation strengthening and so on the many kinds of strengthening mechanism, can fully exert the potential of steel materials, save resources and energy, to optimize the existing rolling process, is conducive to the sustainable development of iron and steel industry.Characterized by a new generation of TMCP shows the case of the innovation of the rolling process.Shows a broad prospect of application of the technology. Keyword:Controlled rolling;Controlled cooling;Super fast cooling technology 1引言 近三十年以来,控制轧制和控制冷却技术在国外得到了迅速的发
中厚板的控制轧制与控制冷却工艺
中厚板的控制轧制与控制冷却工艺 孙洪亮 (材料成型及控制工程,1233010149) 【摘要】近三十年以来,控制轧制和控制冷却技术在国外得到了迅速的发展,各国先后开展了多方面的理论研究和应用技术研究,并在轧钢生产中加以利用,明显的改善和提高了钢材的强韧性和使用性能,为了节约能耗、简化生产工艺和开发钢材新品种创造了有力条件。目前国内外大多数宽厚板厂均采用控制轧制和控制冷却工艺,生产具有高强度、高韧性、良好焊接性的优质钢板。控制轧制和控制冷却工艺的开发与理论研究进一步揭示了热变形过程中变形和冷却工艺参数与钢材的组织变化、相关规律以及钢材性能之间的内在关系,充实和形成了钢材热变形条件下的物理冶金工程理论,为制定合理的热轧生产工艺提供理论依据。关键词:宽厚板厂,控制轧制,控制冷却 【关键词】控制轧制;控制冷却;冷却段长度 In the controlled rolling and controlled cooling technology of plate Abstract:For nearly 30 years, controlled rolling and controlled cooling technology obtained the rapid development in foreign countries, and countries successively carried out various theoretical research and applied technology research, and tries to use in the production of steel rolling, the obvious improve and enhance the tenacity of steel and the use of performance, in order to save energy consumption, simplify production process and development of new steel varieties created favourable conditions. Most lenient plate factory at home and abroad adopt controlled rolling and controlled cooling technology, production has high strength, high toughness and good weldability of high qualified steel plate. Controlled rolling and controlled cooling technology development and theory research of further reveals that the thermal deformation in the process of deformation and cooling process parameters and the change of the organization of the steel, the relevant laws and the internal relations between steel performance, enrich and formed steel thermal deformation under the condition of physical metallurgy engineering theory, to provide theoretical basis for reasonable hot-rolling process. Keywords: generous plate factory, controlled rolling and controlled cooling Key Words:Control rolling; Controlled cooling; Cooling length 1引言 近代工业发展对热轧非调质钢板的性能要求越来越高,除了具有高强度外,还要有良好的韧性、焊接性能及低的冷脆性。目前世界上许多国家都利用控轧和控冷工艺生产高寒地区使用的输油、输气管道用钢板、低碳含铌的低合金高强度钢板、高韧性钢板,以及造船板、桥
自动控制技术现状及发展趋势
自动控制技术现状及发展趋势 摘要:自动控制技术是一项综合性技术,目前被广泛地应用于企业生产及人们 的日常生活中,极大地提高了企业的生产效率及人们的生活质量。本文通过对目 前我国自动控制技术的现状及其发展进行了详细的分析,从而指出自动控制技术 正在向智能化、网络化、微型化以及集成化等方面发展,自动控制技术是现代化 生产的基础,是提高生产效率的关键。 关键词:自动控制技术;现状;发展趋势 一、目前我国自动控制技术的现状分析 就目前我国在自动控制领域的实际情况来看,虽然自动控制技术得到了长足 的发展以及比较广泛地实际应用,但是这与国外发达国家的自动控制技术水平及 应用程度还有很大的差距。我国想要提高自动控制技术的水平,就必须加大投资 与科研的力度,对新型的生产线要科学合理地对其进行自动化的设计及未来发展 的预设,要特别注重自动化信息流的作用,从而提升我国自动控制水平及应用, 进而提高我国企业的国际竞争力。 从目前我国自动控制技术在应用领域中的作用来看,主要是为提高设备的运 行效率。根据我国发展的具体情况,研制开发自动控制技术,从而避免研制自动 控制技术的盲目性。但是,还是存在自动控制技术在研发过程中缺乏宏观层面上 的明确指导,在投入实际生产中所获得的经济效益比较低的现象,在我国自主研 发的自动化设备上还存在精确度比较差、可靠性比较低以及实用性比较差的现象。随着手工制造业在国家经济建设中逐渐丧失了优势地位,自动化生产在社会生产 中日益显示出其生产操作简单、产品质量高及生产效率高等特点,成为企业生产 中的主要模式。在我国自动控制技术的发展也是非常不平衡的,大部分生产领域 的自动化程度还非常低,例如,玩具、服装等。 我国想要提高自动控制水平并不是很容易,这即需要对新的自动控制技术的 研发,也要对原有企业的生产设备进行自动化改造,这样不但能够提高生产效率 而且还能起到降低成本的作用。可以通过数控技术等自动控制技术改造原有机械 设备,提高传统机械设备的自动化程度,从而提高设备的使用率和生产率。在机 床上通过控制技术的改造,充分发挥计算计技术的优势,实现设备及生产线的自 动化的改造,从而提高生产效率。 二、我国自动控制技术的发展趋势分析 (一)智能化自动控制技术的发展 自动控制技术水平的发展是现代化生产不断推进的动力和基础力量,在自动 化生产的开始阶段,控制系统比较简单,控制规律也很简单,因此,采用常规的 控制方法就可以完成作业。智能化是自动化控制技术发展的更高水平,智能化主 要表现在控制的功能多样化和用途多样化,智能化是未来制造业发展的方向。随 着科学技术的不断进步,现代化生产的发展方向逐步向人工智能与自动控制技术 相结合应用的趋势。人工智能理论向自动控制技术领域的渗透,不但理论上而且 在实践上都是新的发展途径,为智能化的自动控制技术,提供了新的思想和方法。人工智能与自动控制技术相结合,能够根据生产过程中的变化情况,对系统采取 更为有效的控制。在目前许多生产领域都采用了智能化控制技术应用于生产系统中,智能化控制技术的水平和应用程度关系到企业现代化生产自动化水平及程度 的高低。
钢材的控制轧制和控制冷却Word版
钢材的控制轧制和控制冷却 一、名词解释: 1、控制轧制:在热轧过程中通过对金属的加热制度、变形制度、温度制度的合理控制,使热塑性变形与固态相变结合,以获得细小晶粒组织,使钢材具有优异的综合力学性能。。 2、控制冷却:控制轧后钢材的冷却速度、冷却温度,可采用不同的冷却路径对钢材组织及性能进行调控。 3、形变诱导相变:由于热轧变形的作用,使奥氏体向铁素体转变温度Ar3上升,促进了奥氏体向铁索体的转变。在奥氏体未再结晶区变形后造成变形带的产生和畸变能的增加,从而影响Ar3温度。 4、形变诱导析出:在变形过程中,由于产生大量位错和畸变能增加,使微量元素析出速度增大。 两相区轧制后的组织中既有由变形未再结晶奥氏体转变的等轴细小铁素体晶粒,还有被变形的细长的铁素体晶粒。同时在低温区变形促进了含铌、钒、钛等微量合金化钢中碳化物的析出。 5、再结晶临界变形量: 在一定的变形速率和变形温度下,发生动态再结晶所必需的最低变形量。 6、二次冷却:相变开始温度到相变结束温度范围内的冷却控制。 二、填空: 1、再结晶的驱动力是储存能,影响其因素可以分为:一类是工艺条件,主要有变形量、变形温度、变形速度。另一类是材料的内在因素,主要是材料的化学成分和冶金状态。 2、控制冷却主要控制轧后钢材冷却过程的(冷却温度)、(冷却速度)等工艺条件,达到改善钢材组织和性能的目的。 3、固溶体的类型有(间隙式固溶)和(置换式固溶),形成(间隙式)固溶体的溶质元素固溶强化作用更大。 4、根据热轧过程中变形奥氏体的组织状态和相变机制不同,将控制轧制划分为三个阶段,即奥氏体再结晶型控制轧制、奥氏体未再结晶型控制轧制、在A+F两相区控制轧制。 5、以珠光体为主的中高碳钢,为达到珠光体团直径减小,则要细化奥氏体晶粒,必须采用(奥氏体再结晶)型控制轧制。 6、控制轧制是在热轧过程中通过对金属的(加热制度)、(变形制度)、(温度制度)的合理控制,使热塑性变形与固态相变结合使钢材具有优异的综合力学性能。 7、钢的强化机制主要包括(固溶强化)、(位错强化)、(沉淀强化)、(细晶强化)、(亚晶强化)、(相变强化)等,其中(绕过)机制既能使钢强化又使钢的韧性得到提高。
机械自动控制技术现状与未来发展趋势 梁晓莹
机械自动控制技术现状与未来发展趋势梁晓莹 发表时间:2019-06-10T10:59:48.047Z 来源:《电力设备》2019年第3期作者:梁晓莹 [导读] 摘要:机械自动控制技术和工业形成了高新技术产业和高端产业扩展的根基,也是最基础的设备,各个国家在发展通讯产业、生物、航天、基建等高端工业,都普遍利用机械自动控制技术来增强制造效率和层次,增强在市场上的适配程度以及竞争能力。 (身份证号码:44128319870222xxxx) 摘要:机械自动控制技术和工业形成了高新技术产业和高端产业扩展的根基,也是最基础的设备,各个国家在发展通讯产业、生物、航天、基建等高端工业,都普遍利用机械自动控制技术来增强制造效率和层次,增强在市场上的适配程度以及竞争能力。本文首先对机械自动控制技术加以概述,并在此基础上,剖析了机械自动控制技术的发展现状与发展趋势。 关键词:机械自动控制技术;应用现状;发展趋势 机械自动控制技术的应用有着其自身的优势,在这一技术的应用下,能大大降低劳动的强度,从整体上提高工作效率以及节约能源等。机械自动控制技术的应用也是未来发展的重要趋势。通过从理论层面对机械自动控制技术研究分析,就能对其理论进行丰富。 1机械自动控制技术应用现状 依照我国经济发展的水平以及我国重点建设工程的实际要求,建造研究“高、精、尖”的重大机械自动控制系统装备,突破外国的技术封锁和限制,自主掌握相关的关键技术,打造出中国机械自动控制系统机床领军品牌,提升市场份额,是整体增强我国机械自动控制技术行业竞争力的重点问题。同时机械自动控制技术也是目前在制造业领域最关键的技术之一。 我国在机械自动控制技术方面的研究进行的相对较晚,伴随着计算机技术的持续进步,以往的传统制造业早已无法满足经济发展的需求,也跟不上时代的脚步。机械自动控制技术作为一项集高新技术于一身的技术手段受到越来越多的重视。当今的机械自动控制技术逐渐朝着通用型的趋势发展,例如系统逐渐变小、变得轻便,能够在工作的时候自动修正参数。在网络技术逐渐成熟的当前,未来能够通过机床联网的方式来将中央集中控制展开加工操作变为可能。 2 机械自动控制的关键技术 2.1 PCC技术 可编程计算机控制器技术(PCC)是一种基于 PLC 和 IPC 结合形成的全新机械自动控制技术,从其实际应用表现出来的性能来看,PCC 集合了PLC 和IPC 二者的优点,表现出较高的可靠性、扩展性以及计算处理能力。相较于以往传统的 PLC 而言,在计算处理能力方面得到大幅度提升,在实时性和开放性上有更大的提升。现代机械设备在运转的过程中常常存在多个不同的项目部分,而且这些不同的项目部分在功能上存在着较大的差异,为实现对不同项目部分的统一性管理,可将 PCC 技术应用于其中。通过 PCC技术为不同项目部分设置对应的模块,通过对模块单独编程,以保证机械设备运行满足实际功能需要。同时在运行的过程中各模块之间会产生出大量的运行数据,这些数据统一传输到 PCC 的 cpu中,经过计算处理后实现整体的协调控制,从而保证机械设备不同项目部分能够高效并行运转,满足实际运行所需。 2.2 运动控制卡技术 运动控制卡技术在具体的功能上主要包括:脉冲输出、数字输入/输入等。该技术在运用的过程中,会根据设置的编程程度发出连续的脉冲串,而在控制上主要通过改变发出脉冲的频率和数量来实现,通过控制脉冲频率可实现对电机运转速度的调节,通过控制脉冲发出的数量可实现对电机位置的调节,再加上脉冲计数功能,可以准确的反馈机器所在的位置,然后对运动过程中产生的误差做出调整,使其在控制上保持较高的精度。该项技术在运用上表现出较高的开放性,也因此适用于许多类型的机械设备,从目前应用现状来看,国外对该项技术应用更为普遍,而国内在这方面发展较晚,所生产制造的产品性能与国外还存在加到的差距。 2.3 直线电机驱动技术 在以往的机床进给系统中,主要采用的是旋转电动机传动方式,在这种传动方式中存在着较多的中间传动环节,也因此在控制上影响到响应速度、控制精度等。而在直线电机驱动技术中,将原来传动过程中的中间环节省去,将传动链长度缩短为零,也因此该项技术被称之为“零传动”技术。从直线电机驱动技术的实际使用情况来看,其主要表现出以下一些优势:高响应性、高灵敏性、高精度、传动刚度高、行程长度不受限制、效率高、噪音低。在实际发展中也正因为该项技术表现出较多的优势,在国外机床行业发展中得到非常高的关注。 3 机械自动控制技术的具体应用 3.1 装载机中的机械自动控制技术 一般情况下,装载机的自动控制技术是由电源、微电子控制器、传感器和电磁比例阀组成。这样一整套系统使得装载机的配置达到了最佳状态,能够很好地按照规定程序完成作业,操作简单,机动性强。时装载机中的位置传感器就会介入,在工作人员对机械进行操作时,传感器就会根据工作人员的指令自动停止在设定的位置,自动选择和切换指令下达的位置,最终完成指令要求,安全、可靠、精准。 3.2 起重机中的机械自动控制技术 起重机的自动控制可以由很多种办法来实现,例如在起重机上配备自动控制变速箱、装备反力传感系统等都可以实现起重机的自动控制。其中装有电子微速控制器的起重机能够完成高精度的起重作业。起重机的电子监控系统由显示器、中央演算器和其他多种传感器组成,在工作过程中,吊装物的重量、臂展的长度、起重臂的斜度、吊钩升起的高度等等都可以以数字的方式显示在显示器上,方便工作人员了解起重器的状态,便于操作。 4 机械自动控制技术的发展趋势 4.1 数字化 机械自动控制技术会向着数字化的趋势发展,这是通过将计算机技术以及制造技术和网络技术等进行综合应用的发展方向。机械制造企业的发展就需要有先进技术作为支持,生产中的各种图形以及数据等信息,都是数字形式呈现,通过网络技术的传递才能提高信息的分析处理能力。数字化的发展目标实现,就能从整体上提高机械自动控制的程度,最终实现优势互补的发展效果。 4.2 虚拟化 机械自动控制技术的发展会逐渐向着虚拟化方向迈进,虚拟技术的应用是未来技术应用的重点,电子计算机技术以及网络通讯技术的应用不断成熟,在对电子计算机技术的应用下,能实现模拟操作大量工作,并借助网络技术将信息数据实施传递,这样就能实现虚拟的操
钢材控制轧制和控制冷却
钢材控制轧制与控制冷却 姓名:蔡翔 班级:材控12 学号: 钢材控制轧制与控制冷却 摘要:控轧控冷就是对热轧钢材进行组织性能控制得技术手段,目前已经广泛应用于热轧带钢、中厚板、型钢、棒线材与钢管等钢材生产得各个领域。控轧控冷技术能够通过袭警抢话、相变强化等方式,使钢材得强度韧度得以提高。 Abstract: controlled rolling is controlledcooling of hot rolled steel organization performance control technology, has been widely usedinthe hot rolled strip steel,plate,steel,wire rod and steelpipeand other steel products production fields。Controlledrollingtechnology of controlled cooling can pas sover assaulting a police officer, phasetransformationstrengthening and so on,to improve the strengthofthe steeltoug hness、 关键词:宽厚板厂,控制轧制,控制冷却 1。引言: 控轧控冷技术得发展历史: 20世纪之前,人们对金属显微组织已经有了一些早期研究与正确认识,已经观察到钢中得铁素体、渗碳体、珠光体、马氏体等组织。20世纪20年代起开始有学者研究轧制温度与变形对材料组织性能得影响,这就是人们对钢材组织性能控制得最初尝试,当时人们不仅已经能够
控制轧制、控制冷却工艺
控制轧制、控制冷却工艺技术 1.1 控制轧制工艺 控制轧制工艺包括把钢坯加热到适宜的温度,在轧制时控制变形量和变形温度以及轧后按工艺要求来冷却钢材。通常将控制轧制工艺分为三个阶段,如图 1.1所示[2]:(1>变形和奥氏体再结晶同时进行阶段,即钢坯加热后粗大化了的γ呈现加工硬化状态,这种加工硬化了得奥氏体具有促使铁素体相变形变形核作用,使相变后的α晶粒细小;(2> (γ+α>两相区变形阶段,当轧制温度继续降低到Ar3温度以下时,不但γ晶粒,部分相变后的α晶粒也要被轧制变形,从而在α晶粒内形成亚晶,促使α晶粒的进一步细化。 图1.1控制轧制的三个阶段 (1>—变形和奥氏体再结晶同时进行阶段;(2>—低温奥氏体变形不发生再结晶阶段;(3>—<γ+α)两相区变形阶段。
1.2 控制轧制工艺的优点和缺点 控制轧制的优点如下: 1.可以在提高钢材强度的同时提高钢材的低温韧性。 采用普通热轧生产工艺轧制16Mn钢中板,以18mm厚中板为例,其屈服强度σs≤330MPa,-40℃的冲击韧性A k≤431J,断口为95%纤维状断口。 当钢中加入微量铌后,仍然采用普通热轧工艺生产时,当采用控制轧制工艺生产时,-40℃的A k值会降低到78J以下,然而采用控制轧制工艺生产时。然而采用控制轧制工艺生产时-40℃的A k值可以达到728J以上。在通常热轧工艺下生产的低碳钢α晶粒只达到7~8级,经过控制轧制工艺生产的低碳钢α晶粒可以达到12级以上<按ASTM标准),通过细化晶粒同时达到提高强度和低温韧性是控轧工艺的最大优点。 2.可以充分发挥铌、钒、钛等微量元素的作用。 在普通热轧生产中,钢中加入铌或钒后主要起沉淀强化作用,其结果使热轧钢材强度提高、韧性变差,因此不少钢材不得不进行正火处理后交货。当采用控制轧制工艺生产时,铌将产生显著的晶粒细化和一定程度的沉淀强化,使轧后的钢材的强度和韧性都得到了很大提高,铌含量至万分之几就很有效,钢中加入的钒,因为具有一定程度的沉淀强化的同时还具有较弱的晶粒细化作用,因此在提高钢材强度的同时没有降低韧性的现象。加入钢种的钛虽然具有细化加热时原始γ晶粒的作用,但在普通轧制条件下钢中的钛不能发挥细化轧制变形过程中γ晶粒的作用,仍然得不到同时提高钢的强度和韧性的效果,当采用控制轧制工艺生产含钛钢时,才能使钢种的Ti 浅谈现代电厂自动控制系统的发展 【摘要】本文从分散控制系统的现状和行业需求出发,结合已经成熟的技术,分析预见了先进DCS系统架构的发展方向以及各种已经成熟的技术和标准在DCS中应用。 【关键词】需求;OPC;模糊PID;一体化 目前,火力发电机组仍然是我国发电行业主要支柱,而先进DCS系统正经历着逐步的演化,朝向更集成可靠先进的方向发展,而其发展历程也是自动控制领域,计算机系统和网络系统发展应用的缩影,也呈现了我国发电行业市场化精细化运营的发展历程。 1.DCS产品现状 当前各厂家的DCS基本包括:至少各一台现场控制站、操作员站、工程师站(也可用操作员站兼做工程师站)和一条系统网络,如图1。此外,还可扩充专门功能站、生产管理和信息处理功能的信息网络、及实现现场仪表、执行机构数字化的现场总线网络。控制站是系统中直接与现场进行I/O 数据采样、信息交互、控制运算、逻辑控制的核心单元,完成实时控制功能,并实现各种I/O 接口。 图1 典型的DCS拓扑结构 控制站通过工业以太网与工程师站、操作员站等交换信息,采集控制站信号并通过工业以太网传送到工程师站、操作员站,工程师站、操作员站将系统组态信息通过工业以太网传送到控制站。 2.发电企业的需求 随着我国煤炭价格持续增长,煤电联动响应不足,电价市场化定价机制迟迟不能确定的行业背景下,发电企业对生产现场的控制和把握有了更高要求,生产成本的严格控制要求自动化程度更高,生产岗位减少,生产人员人均控制装机容量增加,这就要求DCS系统的核心单元要有更为先进的控制算法,先进的专家PID算法,模糊PID算法以适应类似于循环流化床锅炉这种更经济锅炉本身的大延迟,变工况的属性。生产决策必须及时就要求生产控制系统、厂级信息系统和协同管理系统一体化。随着国家对智能电网的发展的提倡,要求各大发电站的调峰、二次调频能力更强,AGC投切率更高且能适应先进的实时的潮流计算,并且要求大电站的DCS系统有更为稳定的协调控制方案和调节能力以应对负荷扰动,现如今的电企较之以前,生产设备调整周期更短,要求DCS要组态灵活方便,而且更严格执行IEC61131语言标准,便于升级换代。 3.发展方向 工业自动化发展方向 工业控制自动化技术是一种运用控制理论、仪器仪表、计算机和其它信息技术,对工业生产过程实现检测、控制、优化、调度、管理和决策,达到增加产量、提高质量、降低消耗、确保安全等目的的综合性技术,主要包括工业自动化软件、硬件和系统三大部分。工业控制自动化技术作为20世纪现代制造领域中最重要的技术之一,主要解决生产效率与一致性问题。虽然自动化系统本身并不直接创造效益,但它对企业生产过程有明显的提升作用。 我国工业控制自动化的发展道路,大多是在引进成套设备的同时进行消化吸收,然后进行二次开发和应用。目前我国工业控制自动化技术、产业和应用都有了很大的发展,我国工业计算机系统行业已经形成。工业控制自动化技术正在向智能化、网络化和集成化方向发展。一、以工业PC为基础的低成本工业控制自动化将成为主流 众所周知,从20世纪60年代开始,西方国家就依靠技术进步(即新设备、新工艺以及计算机应用)开始对传统工业进行改造,使工业得到飞速发展。20世纪末世界上最大的变化就是全球市场的形成。全球市场导致竞争空前激烈,促使企业必须加快新产品投放市场时间(TimetoMarket)、改善质量(Quality)、降低成本(Cost)以及完善服务体系(Service),这就是企业的T.Q.C.S.。虽然计算机集成制造系统(CIMS)结合信息集成和系统集成,追求更完善的T.Q.C.S.,使企业实现“在正确的时间,将正确的信息以正确的方式传给正确的人,以便作出正确的决策”,即“五个正确”。然而这种自动化需要投入大量的资金,是一种高投资、高效益同时是高风险的发展模式,很难为大多数中小企业所采用。在我国,中小型企业以及准大型企业走的还是低成本工业控制自动化的道路。 工业控制自动化主要包含三个层次,从下往上依次是基础自动化、过程自动化和管理自动化,其核心是基础自动化和过程自动化。 传统的自动化系统,基础自动化部分基本被PLC和DCS所垄断,过程自动化和管理自动化部分主要是由各种进口的过程计算机或小型机组成,其硬件、系统软件和应用软件的价格之高令众多企业望而却步。 20世纪90年代以来,由于PC-based的工业计算机(简称工业PC)的发展,以工业PC、I/O 装置、监控装置、控制网络组成的PC-based的自动化系统得到了迅速普及,成为实现低成本工业自动化的重要途径。我国重庆钢铁公司这样的大企业的几乎全部大型加热炉,也拆除了原来DCS或单回路数字式调节器,而改用工业PC来组成控制系统,并采用模糊控制算法,获得了良好效果。 由于基于PC的控制器被证明可以像PLC一样可靠,并且被操作和维护人员接受,所以,一个接一个的制造商至少在部分生产中正在采用PC控制方案。基于PC的控制系统易于安装和使用,有高级的诊断功能,为系统集成商提供了更灵活的选择,从长远角度看,PC控制系统维护成本低。 由于可编程控制器(PLC)受PC控制的威胁最大,所以PLC供应商对PC的应用感到很不安。事实上,他们现在也加入到了PC控制“浪潮”中。 钢材的控制轧制与控制冷却技术 专业:材料成型及控制工程12 姓名:管沁 学号: 钢材的控制轧制与控制冷却技术 管沁 (材料成型及控制工程12级) [摘要]控制轧制和控制冷却能将热轧钢材的两种强化效果相加,进一步提高钢材的强度、韧性和焊接性能,获得更合理的综合力学性能。控轧控冷工艺是一项提高钢材质量、节约合金、简化工序、节约能源消耗的先进轧钢工艺技术。由于控轧控冷具有形变强化、相变强化的综合作用,因此控轧控冷既能提高钢材强度又能改善钢材的韧性和塑性。轧钢厂生产的中厚钢板、热轧板卷、棒、线、型材和钢管都可以采用控轧控冷工艺。 [关键词]控制轧制;控制冷却;中厚板;线材生产 Abstract:Controlled rolling and controlled cooling could add those two reinforcement effect of hot rolled steel products, further improve the strength, toughness and welding performance of steel, to obtain better comprehensive mechanical properties. Controlled rolling process of controlled cooling is an improve steel quality and saving alloy, simplify the process, save energy consumption of advanced rolling technology. Because the controlled rolling cold has deformation strengthening and phase transformation strengthening combination, so both can improve the strength of steel and controlled rolling cold can improve the toughness and plasticity of steel. Rolling mill in the production of medium plate, hot-rolled coil, rod, wire, profiles and steel tube can be used in a controlled rolling process of controlled cooling. Keyword:Controlled rolling;Controlled cooling;plate rolling Wire rod production 1.引言 控制轧制和控制冷却工艺是现代钢铁工业最大的技术成就之一,所谓控制轧制和控制冷却技术,就是在一定的钢材化学成分的情况下,通过对轧制温度、压下量和轧后冷却过程参数的控制,可以细化钢材显微组织、显著改善和提高钢材的性能,获得具有良好综合性能的钢铁材料。控制冷却是控制轧后钢材的冷却速度达到改善钢材组织和性能的目的。由于热轧变形作用,促使变形奥氏体向铁素体转变温度的提高,相变后的铁素体晶粒容易长大,造成力学性能降低。为了细化铁素体晶 自动化技术的应用和发展 发表时间:2018-09-28T10:02:34.253Z 来源:《建筑细部》2018年2月下作者:狄丹 [导读] 自动化技术的应用为人们的生产生活带来了极大的便利,也很大程度上节约了企业的生产成本,因此近些年来应用范围越来越广泛山西省运城市临猗县住房保障和城乡建设管理局山西运城 044100 摘要:自动化技术的应用为人们的生产生活带来了极大的便利,也很大程度上节约了企业的生产成本,因此近些年来应用范围越来越广泛。自动化技术的发展日新月异,特别是随着计算机互联网技术的发展,为自动化技术的发展提供了更加广阔的发展前景,加之“中国梦’的引导,自动化技术的应用也会走向更加环保、低碳的方向,相信通过我们的进一步学习和改进,的自动化技术一定能够取得更加长足高效的发展。 关键词:自动化技术;应用;发展 1自动化技术的应用 自动化技术的发展过程中的应用大致可以分为三个阶段,自动化技术的形成、局部自动化以及综合自动化。现在自动化技术的应用主要处于局部自动化向综合自动化迈进的过程,自动化技术被广泛应用于生产生活的各个方面,例如机械加工、电力控制、航空航天、交通系统、采矿冶炼、农业生产、环境保护、军工科研、办公服务等诸多领域,几乎涵盖了日常生活的方方面面,为人们的生产生活带来了极大地便利。在工业生产领域,自动化技术已经取代单一的人工操作,大大解放了生产力,而且机械统一流水线操作,大大提高了产品的精准度,很多生产环节已经能够实现“无人工厂”的目标。不仅在机械生产中,自动化技术中的控制系统还频频出现在飞行器以及交通设备的控制上。随着技术的发展如今飞行器的速度已经远远不能依靠人脑进行控制,自动化控制系统的引入大大促进了其进一步发展。同时自动化技术还在于越来越多的学科相互交融,朝着更多的领域延伸,例如环境系统工程已经成为一个全世界性的大课题,人类为了更好地生存和发展,必须采取多种措施来改善环境,自动化技术将在这个过程中发挥巨大作用。 2自动化技术的发展现状 2.1自动化技术广泛应用 目前电气自动化技术凭借其强大的功能和安全高效的优点在大多数工业企业中有广泛地应用,工业生产过程使用自动化技术,实现高度智能化,大大降低了企业生产过程的运行成本,增强了生产的可靠性,更大程度上促进企业经济效益的提升。 2.2自动化系统操作及维护简单 随着信息化技术的发展,自动化技术能够实现机器按照控制系统预先设定的程序来完成相应的指令,将工人从繁琐的人工重复单一操作中解放出来,并且随着技术的不断发展,能够通过控制系统使得机器完成更加复杂、灵活、精确地指令性任务。在机器生产过程中,仅仅需要进行简单的检测以及日常机器的维修保养工作就能够实现长时间高效率运行。 2.3管理应用模式落后 各个领域对于自动化技术的引进,主要局限在仅仅引进先进的自动化技术和设备,企业的经营管理模式仍然按照传统的管理模式运行,新旧机制之间存在很多不匹配的地方,使得自动化技术的引进并不能达到预期的效果。企业的管理模式相对滞后,对于管理问题不够重视,管理工作严重缺乏科学性和系统性,会直接导致企业仅仅机械的应用自动化技术,而缺乏创新意识,从而使得企业的发展动力不足。 2.4人才资源缺失 自动化技术虽然已经取得比较好的成绩,但是同发达国家的技术相比,仍有很大的进步空间。这种不足之处主要表现在在实际的产品生产经营过程中由于传统的经营及管理方式仍然占据主导地位,使得工业企业中的自动化技术人才缺失,对于自动化设备的应用过于强调理论,简单追求会用购买的设备和技术即可的最低目标。人才在经济发展科技进步中的重要作用,而通过工业生产实践总结经验改进设计更是改善设备的重要途径。但是国内大多数企业目前过多的追求理论化效果而忽略了人才的培养与引进,给自动化技术的进一步发展造成了很大的阻碍。 3自动化技术的发展趋势 3.1高度集成自动化 集成自动化是指在现有的信息技术的基础之上,不断进行改进,从单一的机器操作到整体机械设备的加工制造过程的统一具体化操作。未来的自动化技术书会采用高度集成化的CPU、芯片以及大规模集成电路,来提高数控系统的集成度,以及软件硬件的运行速度,同时也会更多的采用LED平板显示技术来提高显示器的性能,能够实现超大尺寸的显示。同时也会更加全面的应用先进的封装技术和互连技术,将半导体和表面安装技术融为一体,通过提高集成电路密度,减少互连长度和数量来降低产品的价格,改进产品的性能,提高整个系统的可靠性,扩大系统的应用范围。 3.2智能自动化 这里所说的智能自动化是基于互联网技术的发展而对自动化技术进行的改进和完善,未来会不断利用计算机技术来实现自动化技术的智能化发展方向,提高自动化生产中设备生产数据的收集和科学分析能力,更加全面具体的掌握生产情况,替代一部分的人工管理,对于企业来说能够节约一部分的人力资源成本,从而降低企业同等产品的生产成本,提高企业的经济效益,更好地促进企业的长足发展。 3.3管理更加系统化 自动化技术的主要目标就是用机械设备来取代人力作业,这个发展方向不会改变,在机械化程度日益提高的情况下,企业的管理模式也会与时俱进作出改变。企业应当根据企业自身发展目标再结合自动化技术应用情况和发展前景来制定相应的发展策略。一方面,向相关行业自动化技术管理水平先进的国内外企业学习,不论是先进的自动化管理应用模式还是完善的人才培养模式都应当进行学习引进;另一方面,要根据企业发展制定一套长远的发展战略,把目光放的尽可能长远一些,保证自动化技术的可持续性发展,持续为企业经济效益贡浅谈现代电厂自动控制系统的发展
自动化发展方向
钢材的控制轧制与控制冷却技术
自动化技术的应用和发展