(完整word版)低碳钢、铸铁的拉伸试验

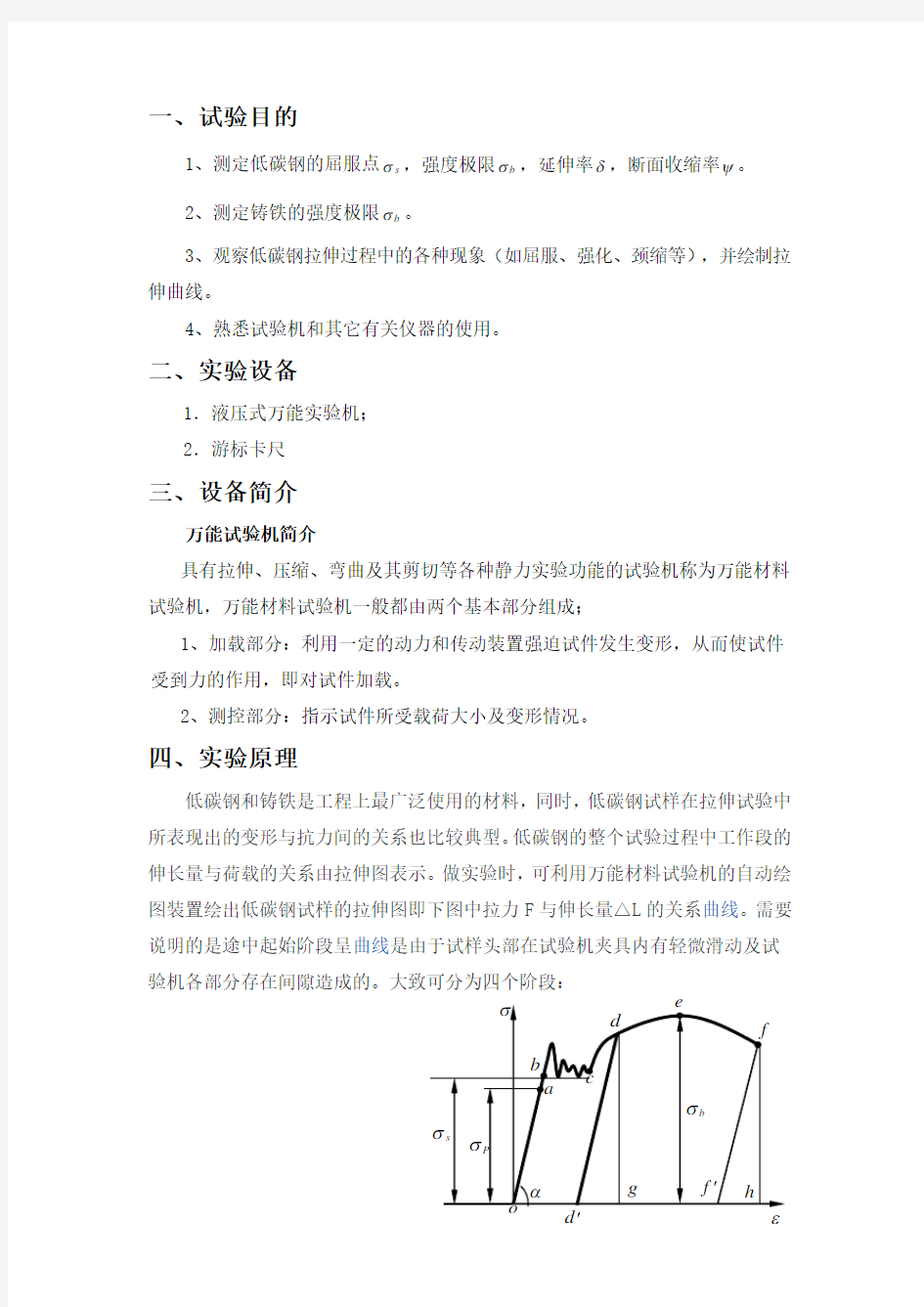
低碳钢、铸铁的拉伸试验
工程力学实验报告 实验名称: 试验班级: 实验组号: 试验成员: 实验日期:
一、试验目的 1、测定低碳钢的屈服点 σ,强度极限bσ,延伸率δ,断面收缩率ψ。 s 2、测定铸铁的强度极限 σ。 b 3、观察低碳钢拉伸过程中的各种现象(如屈服、强化、颈缩等),并绘制拉伸曲线。 4、熟悉试验机和其它有关仪器的使用。 二、实验设备 1.液压式万能实验机; 2.游标卡尺 三、设备简介 万能试验机简介 具有拉伸、压缩、弯曲及其剪切等各种静力实验功能的试验机称为万能材料试验机,万能材料试验机一般都由两个基本部分组成; 1、加载部分:利用一定的动力和传动装置强迫试件发生变形,从而使试件受到力的作用,即对试件加载。 2、测控部分:指示试件所受载荷大小及变形情况。 四、实验原理 低碳钢和铸铁是工程上最广泛使用的材料,同时,低碳钢试样在拉伸试验中所表现出的变形与抗力间的关系也比较典型。低碳钢的整个试验过程中工作段的伸长量与荷载的关系由拉伸图表示。做实验时,可利用万能材料试验机的自动绘图装置绘出低碳钢试样的拉伸图即下图中拉力F与伸长量△L的关系曲线。需要说明的是途中起始阶段呈曲线是由于试样头部在试验机夹具内有轻微滑动及试验机各部分存在间隙造成的。大致可分为四个阶段: σe
(1)弹性阶段(Ob段) 在拉伸的初始阶段,ζ-ε曲线(oa段)为一直线,说明应力与应变成正比,即满足胡克定理,此阶段称为线形阶段。线性段的最高点则称为材料的比例极限(ζ p ),线性段的直线斜率即为材料的弹性摸量E。 线性阶段后,ζ-ε曲线不为直线(ab段),应力应变不再成正比,但若在整个弹性阶段卸载,应力应变曲线会沿原曲线返回,载荷卸到零时,变形也完全 消失。卸载后变形能完全消失的应力最大点称为材料的弹性极限(ζ e ),一般对于钢等许多材料,其弹性极限与比例极限非常接近。 (2)屈服阶段(bc段) 超过弹性阶段后,应力几乎不变,只是在某一微小范围内上下波动,而应变却急剧增长,这种现象成为屈服。使材料发生屈服的应力称为屈服应力或屈服极 限(ζ s )。 当材料屈服时,如果用砂纸将试件表面打磨,会发现试件表面呈现出与轴线成45°斜纹。这是由于试件的45°斜截面上作用有最大切应力,这些斜纹是由于材料沿最大切应力作用面产生滑移所造成的,故称为滑移线。 (3)强化阶段(ce段) 经过屈服阶段后,应力应变曲线呈现曲线上升趋势,这说明材料的抗变形能力又增强了,这种现象称为应变硬化。 若在此阶段卸载,则卸载过程的应力应变曲线为一条斜线(如d-d'斜线),其斜率与比例阶段的直线段斜率大致相等。当载荷卸载到零时,变形并未完全消失,应力减小至零时残留的应变称为塑性应变或残余应变,相应地应力减小至零时消失的应变称为弹性应变。卸载完之后,立即再加载,则加载时的应力应变关系基本上沿卸载时的直线变化。因此,如果将卸载后已有塑性变形的试样重新进行拉伸实验,其比例极限或弹性极限将得到提高,这一现象称为冷作硬化。 在硬化阶段应力应变曲线存在一个最高点,该最高点对应的应力称为材料的 强度极限(ζ b ),强度极限所对应的载荷为试件所能承受的最大载荷F b 。 (4)局部变形阶段(ef段) 试样拉伸达到强度极限ζ b 之前,在标距范围内的变形是均匀的。当应力增 大至强度极限ζ b 之后,试样出现局部显著收缩,这一现象称为颈缩。颈缩出现
实验一 低碳钢及铸铁的拉伸试验
实验一 低碳钢及铸铁的拉伸试验 一、实验目的 1、通过拉伸破坏试验观察、分析低碳钢和铸铁的拉伸过程,比较其机械性能。 2、测定材料的强度指标和塑性指标。 二、实验设备 1、WEW-600屏显万能材料试验机或WE-B600液压万能材料试验机 2、千分尺、游标卡尺、直钢尺 三、试样的制备 一般拉伸试样由三部分组成,即工作部分、过渡部分和夹持部分。工作部分必须保持光滑均匀以确保材料表面的单向应力状态。均匀部分的有效工作长度L 0称做标距,d 0、A 0分别代表工作部分的直径和面积,它们的 关系规定为L 0= k 0A 。为了使各种材料试件的尺寸和形状按国家统一规定,取试件直径d 0=10mm 标距L 0=10d 0或L 0=5d 0。 四、实验原理及方法 常温下的拉伸实验可以测定材料的弹性模量E 、屈服极限σs 、强度极限σb 、延伸率δ和断面收缩率Ψ等力学性能指标,这些参数都是工程设计的重要依据。 1、低碳钢弹性模量E 的测定 由材料力学可知,弹性模量是材料在弹性变形范围内应力与应变的比值,即 E=εσ 因为σ=P /A, ε=ΔL/L 0,所以弹性模量E 又可表示为 E=L A PL 0 ? 式中: E —材料的弹性模量,σ —应力,ε —应变,P —实验时所施加的载荷 A —以试件直径的平均值计算的横截面面积,L 0—引伸仪标距 ΔL —试件在载荷P 作用下,标距L 0段的伸长量。 可见在弹性变形范围内,对试件作用拉力P ,并量出拉力P 引起的标距内伸长ΔL ,即可求得弹性模量E 。
实验时,如使用WEW-600屏显万能材料试验机,它采用电子测量技术,由计算机对数据进行处理,屏幕显示试验力和变形。 如使用WE-B600液压万能材料试验机,拉力P 值由试验机读数盘示出,标距L 0=50mm (不同引伸仪标距不同),试件横截面面积A 可算出,只要测出标距段的伸长量ΔL ,就可得到弹性模量E 。 在弹性变形阶段内试件的变形很小,标距段的变形(伸长量ΔL )需用放大倍数为200倍的球铰式引伸仪来测量。为检验载荷与变形之间的关系是否符合胡克定律,并减少测量误差,实验时一般用等增量法加载,即把载荷分成若干个等级,每次增加相同的载荷ΔP ,逐级加载。为保证应力不超出弹性范围,以屈服载荷的70%-80%作为测定弹性模量的最高载荷n P 。此外,为使试验机夹紧试件,消除试验机构的间隙等因素的影响,对试件应施加一个初始载荷P 0(本实验中P 0=2.0KN )。 实验过程中,从P 0到 n P 逐级加载,载荷的每级增量均为ΔP 。对应着每级载荷P i ,记录相应的伸长i L ?,1+?i L 与i L ?之差即为变形增量()i L ??,它是p ?引起的变形(伸长) 增量。在逐级加载中,如果得到的 ()i L ??基本相等,则表明ΔL 与P 为线性关系,符合虎克定理。完成一次加载过程,将得到P i 和i L ?的一组数据,按平均法计算弹性模量,即 ()L A L P E ??????=0200其中[]()i n i L n L ∑=??=??11为变形增量的 平均值;200为测量变形的放大倍数。 2、 屈服极限σs 、强度极限σb 的测定 测定弹模后继续加载使材料到屈服阶段,进入屈服阶段时,载荷常有上下波动,其中较大的载荷称为上屈服点,较小的称为下屈服点。一般用第一个波峰的下屈服点表示材料的屈服载荷P S ,它所对应的应力为屈服极限σs 。 屈服阶段过后,材料进入强化阶段,试件又恢复了承载能力。载荷达到最大值P b 时,试件某一局部的截面明显缩小,出现“颈缩”现象。这时载荷迅速下降,试件即将被拉断,这时所示的载荷即为破坏载荷P b ,它所对应的应力叫强度极限σb 。 即 0A P s s = σ, 0A P s s =σ 其中20041d A π=,0d 为最小直径。 3、 延伸率δ和断面收缩率Ψ的测定
材料的拉伸试验实验报告
材料的拉伸试验 实验内容及目的 (1)测定低碳钢材料在常温、静载条件下的屈服强度s σ、抗拉强度b σ、伸长率δ和断面收缩率ψ。 (2)掌握万能材料试验机的工作原理和使用方法。 实验材料及设备 低碳钢、游标卡尺、万能试验机。 试样的制备 按照国家标准GB6397—86《金属拉伸试验试样》,金属拉伸试样的形状随着产品的品种、规格以及试验目的的不同而分为圆形截面试样、矩形截面试样、异形截面试样和不经机加工的全截面形状试样四种。其中最常用的是圆形截面试样和矩形截面试样。 如图1所示,圆形截面试样和矩形截面试样均由平行、过渡和夹持三部分组成。平行部分的试验段长度l 称为试样的标距,按试样的标距l 与横截面面积A 之间的关系,分为比例试样和定标距试样。圆形截面比例试样通常取d l 10=或 d l 5=,矩形截面比例试样通常取A l 3.11=或A l 65.5=,其中,前者称为长比例 试样(简称长试样),后者称为短比例试样(简称短试样)。定标距试样的l 与A 之间无上述比例关系。过渡部分以圆弧与平行部分光滑地连接,以保证试样断裂时的断口在平行部分。夹持部分稍大,其形状和尺寸根据试样大小、材料特性、试验目的以及万能试验机的夹具结构进行设计。 对试样的形状、尺寸和加工的技术要求参见国家标准GB6397—86。
(a ) (b ) 图1 拉伸试样 (a )圆形截面试样;(b )矩形截面试样 实验原理 进行拉伸试验时,外力必须通过试样轴线,以确保材料处于单向应力状态。低碳钢具有良好的塑性,低碳钢断裂前明显地分成四个阶段: 弹性阶段:试件的变形是弹性的。在这个范围内卸载,试样仍恢复原来的尺寸,没有任何残余变形。 屈服(流动)阶段:应力应变曲线上出现明显的屈服点。这表明材料暂时丧失抵抗继续变形的能力。这时,应力基本上不变化,而变形快速增长。通常把下屈服点作为材料屈服极限(又称屈服强度),即A F s s = σ,是材料开始进入塑性的标志。结构、零件的应力一旦超过屈服极限,材料就会屈服,零件就会因为过量变形而失效。因此强度设计时常以屈服极限作为确定许可应力的基础。 强化阶段:屈服阶段结束后,应力应变曲线又开始上升,材料恢复了对继续变形的抵抗能力,载荷就必须不断增长。D 点是应力应变曲线的最高点,定义为材料的强度极限又称作材料的抗拉强度,即A F b b = σ。对低碳钢来说抗拉强度是材料均匀塑性变形的最大抗力,是材料进入颈缩阶段的标志。 颈缩阶段:应力达到强度极限后,塑性变形开始在局部进行。局部截面急剧收缩,承载面积迅速减少,试样承受的载荷很快下降,直到断裂。断裂时,试样的弹性变形消失,塑性变形则遗留在破断的试样上。 材料的塑性通常用试样断裂后的残余变形来衡量,单拉时的塑性指标用断后伸长率δ和断面收缩率ψ来表示。即 %1001?-= l l l δ
低碳钢和铸铁的拉伸实验
实验一 低碳钢和铸铁的拉伸实验 一、实验目的要求 1.测定低碳钢的流动极限S σ、强度极限b σ、延伸率δ、截面收缩率ψ和铸铁的强度极 限b σ。 2.低碳钢和铸铁在拉伸过程中表现的现象,绘出外力和变形间的关系曲线(L F ?-曲 线)。 3.比较低碳钢和铸铁两种材料的拉伸性能和断口情况。 二、实验设备和仪器 CMT5504/5105电子万能试验机、游标卡尺等 图1-1 CMT5504/5105电子万能试验机
三、拉伸试件 金属材料拉伸实验常用的试件形状如图所示。图中工作段长度l 称为标距,试件的拉伸变形量一般由这一段的变形来测定,两端较粗部分是为了便于装入试验机的夹头内。 为了使实验测得的结果可以互相比较,试件必须按国家标准做成标准试件,即d l 5=或d l 10=。 对于一般板的材料拉伸实验,也应按国家标准做成矩形截面试件。其截面面积和试件标距关系为A l 3.11=或A l 65.5=,A 为标距段内的截面积。 低碳钢拉伸 铸铁拉伸 图1-2 拉伸试件
四、实验原理和方法 1.低碳钢拉伸实验 低碳钢试件在静拉伸试验中,通常可直接得到拉伸曲线,如图1—3所示。用准确的拉 σ-曲线。首先将试件安装于试验机的夹头内,之后匀速缓伸曲线可直接换算出应力应变ε 慢加载(加载速度对力学性能是有影响的,速度越快,所测的强度值就越高),试样依次经过弹性、屈服、强化和颈缩四个阶段,其中前三个阶段是均匀变形的。 图1-3 低碳钢拉伸曲线 OA段,没有任何残留变形。在弹性阶段,载荷与变形 (1) 弹性阶段是指拉伸图上的' 是同时存在的,当载荷卸去后变形也就恢复。在弹性阶段,存在一比例极限点A,对应的应σ,此部分载荷与变形是成比例的。 力为比例极限 p (2) 屈服阶段对应拉伸图上的BC段。金属材料的屈服是宏观塑性变形开始的一种标志,是由切应力引起的。在低碳钢的拉伸曲线上,当载荷增加到一定数值时出现了锯齿现象。这种载荷在一定范围内波动而试件还继续变形伸长的现象称为屈服现象。屈服阶段中一个重要的力学性能就是屈服点。低碳钢材料存在上屈服点和下屈服点,不加说明,一般都是指下 F,即试件发生屈服而力首次下降前的最屈服点。上屈服点对应拉伸图中的B点,记为 SU F,是指不计初始瞬时效应的屈服阶段中的最小力值,注意这里的大力值。下屈服点记为 SL 初始瞬时效应对于液压摆式万能试验机由于摆的回摆惯性尤其明显,而对于电子万能试验机或液压伺服试验机不明显。
哈工大—低碳钢拉伸试验
试验一 金属材料的拉伸与压缩试验 1.1概 述 拉伸实验是材料力学实验中最重要的实验之一。任何一种材料受力后都要产生变形,变形到一定程度就可能发生断裂破坏。材料在受力——变形——断裂的这一破坏过程中,不仅有一定的变形能力,而且对变形和断裂有一定的抵抗能力,这些能力称为材料的力学机械性能。通过拉伸实验,可以确定材料的许多重要而又最基本的力学机械性能。例如:弹性模量E 、比例极限R p 、上和下屈服强度R eH 和R eL 、强度极限R m 、延伸率A 、收缩率Z 。除此而外,通过拉伸实验的结果,往往还可以大致判定某种其它机械性能,如硬度等。 我们以两种材料——低碳钢,铸铁做拉伸试验,以便对于塑性材料和脆性材料的力学机械性能进行比较。 这个实验是研究材料在静载和常温条件下的拉断过程。利用电子万能材料试验机自动绘出的载荷——变形图,及试验前后试件的尺寸来确定其机械性能。 试件的形式和尺寸对实验的结果有很大影响,就是同一材料由于试件的计算长度不同,其延伸率变动的范围就很大。例如: 对45#钢:当L 0=10d 0时(L 0为试件计算长度,d 0为直径),延伸率A 10=24~29%,当L 0=5d 0时,A 5=23~25%。 为了能够准确的比较材料的性质,对拉伸试件的尺寸有一定的标准规定。按国标GB/T228-2002、GB/P7314-1987的要求,拉伸试件一般采用下面两种形式: 图1.1 1. 10倍试件; 圆形截面时,L 0=10d 0 矩形截面时,L 0=11.3 0S 2. 5倍试件 圆形截面时,L 0=5d 矩形截面时, L 0=5.65 0S =π0 45S d 0——试验前试件计算部分的直径; S 0——试验前试件计算部分断面面积。 此外,试件的表面要求一定的光洁度。光洁度对屈服点有影响。因此,试件表面不应有刻痕、切口、翘曲及淬火裂纹痕迹等。 1.2拉伸实验 一、实验目的: 1.研究低碳钢、铸铁的应力——应变曲线拉伸图。 2.确定低碳钢在拉伸时的机械性能(比例极限R p 、下屈服强度R eL 、强度极限R m 、延伸率A 、断面收缩率Z 等等)。 3. 确定铸铁在拉伸时的力学机械性能。 二、实验原理: 拉伸实验是测定材料力学性能最基本的实验之一。在单向拉伸时F —ΔL (力——变形)曲线的形式代表了不同材料的力学性能,利用: 0F S σ= 0L L ε?= 可得到σ—ε曲线关系。
低碳钢和铸铁拉伸试验.docx
实验编号2 低碳钢和铸铁的拉伸实验 低碳钢和铸铁拉伸试验 概述 常温,静载下的轴向拉伸试验是材料力学实验中最基本,应用最广泛的实验。通过拉伸试验,可以全面地测定材料地力学性能,如弹性、塑性、强度、断裂等力学性能指标。弹性模量E是表征材料力学性能中弹性的重要指标之一,它反映了材料抵抗弹性变形的能力。这些性能指标对材料力学地分析计算、工程设计、选择材料和新材料开发都有极其重要的作用。 二、实验目的 1、测定低碳钢的下屈服点δSL 、抗拉强度δb、断后伸长率δ、断面收缩率ψ 2、验证虎克定律,测定低碳钢的弹性模量E 3、测定铸铁的抗拉强度δb 4、观察分析两种材料在拉伸过程中的各种现象 5、学习自动绘制σ—ε曲线及微机控制电子万能实验机、电子引伸计的 操作 三、实验设备和仪器 1、微机控制电子万能实验机(IOT) 2、游标卡尺 3、低碳钢和铸铁圆形拉伸试样 四、实验原理 1、低碳钢拉伸 低碳钢拉伸实验过程分四个阶段: (1)、弹性阶段OE在此阶段中的OP段拉力和伸长成正比关系,表明钢材的应力和应 变为线性关系。完全遵循虎克定律δ= Eε,故点P的应力δP称为材料的比例极限。 如图1-1所示,当应力继续增加达到材料的弹性极限δ E 对应的E点时,应力和应变间的关系不再是线性关系,但变形仍然是弹性的,即卸除拉力后变形完全消失,工程上对弹性极限和比例极限不严格的区分它们。 (2)、屈服阶段ES,当应力超过弹性极限到达S点时,应变有明显的增加,而应力 先是下降,然后作微小的波动,在σ—ε曲线上出现锯齿形线段。这种应力基本保持不变,而应变显著增加的现象,称为屈服。在屈服阶段内的最高应力和最低应力分别称为上屈服极限和下屈服极限。上屈服极限的数值与试样形状、加载速度等因素有关,一般不稳定。下屈服极限则有比较稳定的数值,能够反应材料的性能。通常把下屈服极限称为屈服极限或屈服点,用δSL来表示。屈服应力是衡量材料强度的一个重要指标。其计算公式为δSL=F S L/A O
低碳钢拉伸实验报告
低碳钢拉伸试验报告 材科1002班任惠41030096 一、试验目的 1、测定低碳钢在退火、正火和淬火三种不同热处理状态下的强度与塑性性能 2、测定低碳钢的应变硬化指数和应变硬化系数 二、试验原理和要求 原理:低碳钢材料的机械性能指标是由拉伸破坏试验来确定的,拉伸过程有弹性变形、塑性变形和断裂三个阶段。通过拉伸试验,可以确定材料的屈服强度、抗拉强度、断后伸长率、断面收缩率等性能指标。而且可以通过Hollomon公式计算出材料的应变硬化系数与应变硬化指数。 要求:按照相关国标标准(GB/T228-2002:金属材料室温拉伸试验方法)要求完成试验测量工作。三、试验材料与试样 试验材料:退火低碳钢、正火低碳钢、淬火低碳钢的R4标准试样各一个。试样规格尺寸及公差要求如表1、表2所示;试样示意图如图1所示: 图 1 低碳钢拉伸试样示意图 表 1 R4试样的规格尺寸 原始标距L o平行长度L c截面原始直径d 过渡弧半径r 头部直径d’ 50 mm 60 mm 10 mm 8 mm 20 mm 表 2 R4试样的横向尺寸公差 尺寸公差形状公差 ±0.07 mm 0.04 mm 四、试验测试内容与相关的测量工具、仪器、设备 1.试验测试内容 (1) 直接测量的物理量:试样的原始标距L0、断后标距L u、原始直径d0、断后直径d u。 (2) 连续测量加载过程中的载荷P和试样的伸长量ΔL=L-L0数据。(由万能材料试验机给出应力-应变曲线)
2.测量工具、仪器、设备 (1) 万能材料试验机。其主要技术规格及参数如下: a.最大试验力:200 kN b.试验力准确度:优于示值的0.5% c.力值测量范围:最大试验力的0.4%-100% d.变形测量准确度:在引伸计满量程的2%-100%范围内优于示值的1% e.横梁位移测量:分辨率的0.001mm f.横梁速度范围:0.005mm/min -500mm/min,无级,任意设定 g.夹具形式:标准楔形拉伸附具、压缩附具、弯曲附具 (2) 游标卡尺:精确度0.02 mm (3) 载荷传感器:0.5级,是指载荷传感器示值的最大相对误差为±0.5% (4) 引伸计:标距为50 mm,0.5级,0.5级引伸计的标距相对误差为±0.5% (5) 划线器:标记应准确到±1% 注:低碳钢淬火后抗拉强度可达600MPa,而试样直径为10 mm,故最大试验力为:600 MPa×π(10 mm/2)2=47.1 kN<200 kN,因此试验机加载能力满足要求。 五、试验步骤 1.拿到试样,给试样标号:1号、2号和3号; 2.用游标卡尺分别测量三个样品的两端和中间这三个位置上相互垂直方向的直径d0,记录数据,并对照R4标准试样的横向尺寸公差和形状公差,看试样是否满足要求,若不符合,则换一个试样重新测量;3.用划线器在试样上标记试样的原始标距L0,标记4条线,线和线之间的距离是10mm+40mm+10mm;4.将引伸计固定在试样的标距之间,同时将试样安装卡紧至拉伸试验机的夹头之间,试验中用引伸计检测试样的变形量,载荷传感器固定安置于试验机的下横梁和下夹头之间; 5.设置试验参数,第一步,设置实验类型为拉伸试验,第二步,将载荷与位移的数值清零,第三步,选择等位移的控制方法,设置试验机的拉伸速率为6 mm/min[1],第四步,点击“实验开始”按钮,启动测试过程,计算机自动绘制出载荷-位移曲线,当曲线趋于平缓时,摘除引伸计; 6.继续拉伸试验,观察试样出现颈缩直至断裂,试验机自动停止,从试验机的夹头之间取下试样,观察断口形貌; 7.再用游标卡尺测量断后标距L u[2]和颈缩处最小直径d u[3]; 8.重复以上步骤,测量不同热处理状态的试样; 9.根据测试结果,处理数据。
低碳钢和铸铁拉伸和压缩试验
低碳钢和铸铁拉伸压缩实验报告 摘要:材料的力学性能也称为机械性质,是指材料在外力作用下表现的变形、破坏等方面的特性。它是由试验来测定的。工程上常用的材料品种很多,下面我们以低碳钢和铸铁为主要代表,分析材料拉伸和压缩时的力学性能。 关键字:低碳钢 铸铁 拉伸压缩实验 破坏机理 一.拉伸实验 1. 低碳钢拉伸实验 拉伸实验试件 低碳钢拉伸图 在拉伸实验中,随着载荷的逐渐增大,材料呈现出不同的力学性能:
低碳钢拉伸应力-应变曲线 (1)弹性阶段(Ob段) 在拉伸的初始阶段,ζ-ε曲线(Oa段)为一直线,说明应力与应变成正比,即满足胡克定理,此阶段称为线形阶段。线性段的最高点则称为材料的比例极限(ζ p ),线性段的直线斜率即为材料的弹性摸量E。 线性阶段后,ζ-ε曲线不为直线(ab段),应力应变不再成正比,但若在整个弹性阶段卸载,应力应变曲线会沿原曲线返回,载荷卸到零时,变形也完全 消失。卸载后变形能完全消失的应力最大点称为材料的弹性极限(ζ e ),一般对于钢等许多材料,其弹性极限与比例极限非常接近。 (2)屈服阶段(bc段) 超过弹性阶段后,应力几乎不变,只是在某一微小范围内上下波动,而应变却急剧增长,这种现象成为屈服。使材料发生屈服的应力称为屈服应力或屈服极 限(ζ s )。 当材料屈服时,如果用砂纸将试件表面打磨,会发现试件表面呈现出与轴线成45°斜纹。这是由于试件的45°斜截面上作用有最大切应力,这些斜纹是由于材料沿最大切应力作用面产生滑移所造成的,故称为滑移线。 (3)强化阶段(ce段) 经过屈服阶段后,应力应变曲线呈现曲线上升趋势,这说明材料的抗变形能力又增强了,这种现象称为应变硬化。 若在此阶段卸载,则卸载过程的应力应变曲线为一条斜线(如d-d'斜线),其斜率与比例阶段的直线段斜率大致相等。当载荷卸载到零时,变形并未完全消失,应力减小至零时残留的应变称为塑性应变或残余应变,相应地应力减小至零时消失的应变称为弹性应变。卸载完之后,立即再加载,则加载时的应力应变关系基本上沿卸载时的直线变化。因此,如果将卸载后已有塑性变形的试样重新进行拉伸实验,其比例极限或弹性极限将得到提高,这一现象称为冷作硬化。 在硬化阶段应力应变曲线存在一个最高点,该最高点对应的应力称为材料的 强度极限(ζ b ),强度极限所对应的载荷为试件所能承受的最大载荷F b 。 (4)局部变形阶段(ef段) 试样拉伸达到强度极限ζ b 之前,在标距范围内的变形是均匀的。当应力增 大至强度极限ζ b 之后,试样出现局部显著收缩,这一现象称为颈缩。颈缩出现后,使试件继续变形所需载荷减小,故应力应变曲线呈现下降趋势,直至最后在f点断裂。试样的断裂位置处于颈缩处,断口形状呈杯状,这说明引起试样破坏的原因不仅有拉应力还有切应力。 (5)伸长率和断面收缩率 试样拉断后,由于保留了塑性变形,标距由原来的L变为L1。用百分比表示的比值 δ=(L1-L)/L*100% 称为伸长率。试样的塑性变形越大,δ也越大。因此,伸长率是衡量材料塑性的指标。 原始横截面面积为A的试样,拉断后缩颈处的最小横截面面积变为A1,用百分比表示的比值
低碳钢拉伸试验
低碳钢和灰口铸铁的拉伸、压缩实验 1 实验目的 ⑴.观察低碳钢在拉伸时的各种现象,并测定低碳钢在拉伸时的屈服极限s σ,强度极限 b σ,延伸率10δ和断面收缩率ψ。 ⑵.观察铸铁在轴向拉伸时的各种现象。 ⑶.观察低碳钢和铸铁在轴向压缩过程中的各种现象。 ⑷.观察试样受力和变形两者间的相互关系,并注意观察材料的弹性、屈服、强化、颈缩、断裂等物理现象。测定该试样所代表材料的F S 、F b 和l ?等值。 ⑸.对典型的塑性材料和脆性材料进行受力变形现象比较,对其强度指标和塑性指标进行比较。 ⑹.学习、掌握电子万能试验机的使用方法及其工作原理。 2 仪器设备和量具 50KN 电子万能试验机,单向引伸计,钢板尺,游标卡尺。 3 试件 实验证明,试件尺寸和形状对实验结果有影响。为了便于比较各种材料的机械性能, 国家标准中对试件的尺寸和形状有统一规定。根据国家标准,(GB6397-86),将金属拉伸比例试件的尺寸列表如下: 本实验的拉伸试件采用国家标准中规定的长比例试件(图2-1),实验段直径mm d 100=,标距mm l 1000=。本实验的压缩试件采用国家标准(GB7314-87)中规定的圆柱形试件 2/0=d h ,mm d 150=(图2-2)。
4 实验原理和方法 (一)低碳钢的拉伸实验 在拉伸实验前,测定低碳钢试件的直径0d 和标距0l 。实验时,首先将试件安装在实验机的上、下夹头内,并在实验段的标记处安装引伸仪,以测量实验段的变形。然后开动实验机,缓慢加载,与实验机相联的微机会自动绘制出载荷-变形曲线(l F ?-曲线,见图2-3)或应力-应变曲线(εσ-曲线,见图2-4),随着载荷的逐渐增大,材料呈现出不同的力学性能: (1)弹性阶段(Ob 段) 在拉伸的初始阶段,εσ-曲线(Oa 段)为一直线,说明应力与应变成正比,即满足胡克定理,此阶段称为线形阶段。线性段的最高点称为材料的比例极限(P σ),线性段的直线斜率即为材料的弹性摸量E 。 线性阶段后,εσ-曲线不为直线(ab 段),应力应变不再成正比,但若在整个弹性阶段卸载,应力应变曲线会沿原曲线返回,载荷卸到零时,变形也完全消失。卸载后变形能完全消失的应力最大点称为材料的弹性极限(e σ),一般对于钢等许多材料,其弹性极限与比例极限非常接近。 (2)屈服阶段(bc 段) 超过弹性阶段后,应力几乎不变,只是在某一微小范围内上下波动,而应变却急剧增长,这种现象成为屈服。使材料发生屈服的应力称为屈服应力或屈服极限(s σ)。 当材料屈服时,如果用砂纸将试件表面打磨,会发现试件表面呈现出与轴线成0 45斜纹。这是由于试件的0 45斜截面上作用有最大切应力,这些斜纹是由于材料沿最大切应力作用面产生滑移所造成的,故称为滑移线。 Δl 图2-2 压缩试件 图2-3 图2-4
拉伸实验报告
实验一拉伸实验报告 一、实验目的 1、掌握如何正确进行拉伸实验的测量; 2、通过对拉伸实验的实际操作,测定低碳钢的弹性模量E、屈服极限бs、强度极限бb 、延伸率δ、截面收缩率ψ; 3、观察在拉伸过程中的各种现象,绘制拉伸图(P―Δ曲线) ; 4、通过适当转变,绘制真应力-真应变曲线S-e,测定应变硬化指数n ,并了解其实际意义。 二、实验器材与设备 1、电子万能材料试验机(载荷、变形、位移) 其设备如下: 主机 微机处理系统 测试控制 CSS-44200
2、变形传感器(引申仪) 型 号 ∶YJ Y ―11 标 距 L ∶50 mm 量 程 ΔL ∶ 25mm 3、拉伸试件 为了使试验结果具有可比性,按GB228-2002规定加工成标准试件。 其标准规格为:L 0=5d 0,d 0=10mm 。 试件的标准图样如下: 标准试件图样 三、实验原理与方法 1、低碳钢拉伸 随着拉伸实验的进行,试件在连续变载荷作用下经历了弹性变形阶段、屈服阶段、强化阶段以及局部变形阶段这四个阶段。 其拉伸力——伸长曲线如下: 夹持部分 工作部分 过渡部分
弹性阶段屈服阶段强化阶段局部变形阶段 低碳钢的拉伸力——伸长曲线 2、低碳钢弹性模量E的测定 在已经获得的拉伸力—伸长曲线上取伸长长度约为标距的1%~8%的相互距离适当的两点(本实验选取了伸长为4%和8%的两点),读出其力和伸长带入相关的计算公式计算出弹性模量E。
3、应变硬化指数n的测定 在金属整个变形过程中,当外力超过屈服强度之后,塑性变形并不是像屈服平台那样连续流变下去,而需要不断增加外力才能继续进行。这表明金属材料有一种阻止继续塑性变形的能力,这就是应变硬化性能。塑性应变是硬化的原因,而硬化则是塑性应变的结果。应变硬化是位错增值,运动受阻所致。 准确全面描述材料的应变硬化行为,要使用真实应力——应变曲线。因为工程应力——应变曲线上的应力和应变是用试样标距部分原始截面积和原始标距长度来度量的,并不代表实际瞬时的应力和应变。当载荷超过曲线上最大值后,继续变形,应力下降,此与材料的实际硬化行为不符。 在拉伸真实应力——应变曲线上,在均匀塑性变形阶段,应力与应变之间符合Hollomon关系式 S=Ke n 式中,S为真实应力;K为硬化系数,亦称强度系数,是真实应变等于1.0时的真实应力;e为真实应变;n为应变硬化指数。 应变硬化指数n反映了金属材料抵抗均匀塑性变形的能力,是表征金属材料应变硬化行为的性能指标。 根据GB5028-85,应变硬化指数n的计算过程如下: 首先,要绘制出真实的应力——应变曲线,然后根据在塑性变形阶段下:真应力S=F/A 真应变e=△L/L SA F= = + =SdA AdS dF ) 1 ln( 0 ε+ = =?l l l dl e
低碳钢的拉伸实验
材料力学实验教案 实验一 低碳钢的拉伸实验 一、实验名称 低碳钢的拉伸实验。 二、实验目的 1.测定低碳钢的屈服极限σs 、强度极限σb 、伸长率δ和断面收缩率Ψ; 2.观察低碳钢拉伸过程中的弹性变形、屈服、强化和缩颈等物理现象; 3. 熟悉材料试验机和游标卡尺的使用。 三、实验设备 1.手动数显材料试验机 2.MaxTC220试验机测试仪 3.游标卡尺 四、试样制备 低碳钢试样如图所示,直径d=10mm ,测量并记录试样的原始标距L 0。 五、实验原理 1. 材料达到屈服时,应力基本不变而应变增加,材料暂时失去了抵抗变形的能力,此时的应力即为屈服极限σs 。 2. 材料在拉断前所能承受的最大应力,即为强度极限σb 。 3. 试样的原始标距为L 0,拉断后将两段试样紧密对接在一起。量出拉断后的长 度L 1,伸长率为拉断后标距的伸长量与原始标距的百分比,即 %100L L L 0 01?-=δ 4. 拉断后,断面处横截面积的缩减量与原始横截面积的百分比为断面收缩率,
即%100A A A 0 10?-=ψ 式中A 0—试样原始横截面积;A 1—试样拉断后断口处最小横截面积。 六、实验步骤 1.调零。打开力仪开关,待示力仪自检停后,按清零按钮,使显示屏上的按钮显示为零。 2.加载。用手握住手柄,顺时针转动施力使动轴通过传动装置带动千斤顶的丝杠上升,使试样受力,直至断裂。 3.示力。在试样受力的同时,装在螺旋千斤顶和顶梁之间的压力传感器受压产生压力信号,通过回蕊电缆传给电子示力仪,电子示力仪的显示屏上即用数字显示出力值。 4.关机。实验完毕,卸下试样,操作定载升降装置使移动挂梁降到最低时关闭力仪开关,断开电源。 七、数据处理 1. 记录相关数据 参数 原始直径 断口直径 原始标距 拉断后标距 长度(mm ) d o =10mm d 1= L o = L 1= 2. 计算伸长率δ和断面收缩率Ψ %100L L L 0 01?-=δ %100A A A 0 10?-=ψ 3. 在应力应变图中标出屈服极限σs 和强度极限σ b 八、应力应变图分析 低碳钢的拉伸过程分为四个阶段,分别为弹性变形阶段、屈服阶段、强化阶段和缩颈阶段。 1. 弹性变形阶段:在拉伸的初始阶段,应力和应变的关系为直线,此阶段符合胡克定律,即应力和应变成正比; 2. 屈服阶段:超过弹性极限后,应力增加到某一数值时,应力应变曲线上出现
低碳钢、铸铁拉伸试验
低碳钢、铸铁拉伸试验 一、实验目的 本试验以低碳钢和铸铁为代表,了解塑性材料在简单拉伸时的机械性质。它是力学性能试验中最基本最常用的一个。一般工厂及工程建设单位都广泛利用该实验结果来检验材料的机械性能。试验提供的 E ,R eL ,R m ,A 和Z 等指标,是评定材质和进行强度、刚度计算的重要依据。本试验具体要求为: 1.了解材料拉伸时力与变形的关系,观察试件破坏现象。 2.测定强度数据,如屈服点R eL ,抗拉强度R m 。 3.测定塑性材料的塑性指标:拉伸时的伸长率A ,截面收缩率Z 。 4.比较塑性材料与脆性材料在拉伸时的机械性质。 二、实验原理 进行拉伸试验时,外力必须通过试样轴线,以确保材料处于单向应力状态。一般试验机都设有自动绘图装置,用以记录试样的拉伸图即F-ΔL 曲线,形象地体现了材料变形特点以及各阶段受力和变形的关系。但是F-ΔL 曲线的定量关系不仅取决于材质而且受试样几何尺寸的影响。因此,拉伸图往往用名义应力、应变曲线(即R-ε曲线)来表示: 0F R S = ——试样的名义应力 L L ?=ε——试样的名义应变 S 0和L 0分别代表初始条件下的面积和标距。R-ε曲线与F-ΔL 曲线相似,但消除了几何尺寸的影响。因此,能代表材料的属性。单向拉伸条件下的一些材料的机械性能指标就是在R-ε曲线上定义的。如果试验能提供一条精确的拉伸图,那么单向拉伸条件下的主要力学性能指标就可精确地测定。 不同性质的材料拉伸过程也不同,其R-ε曲线会存在很大差异。低碳钢和铸铁是性质截然不同的两种典型材料,它们的拉伸曲线在工程材料中十分典型,掌握它们的拉伸过程和破坏特点有助于正确、合理地认识和选用材料。 低碳钢具有良好的塑性,由R-ε曲线(图1-1)可以看出,低碳钢断裂前明显地分成四个阶段: 弹性阶段(OA):试件的变形是弹性的。在这个范围内卸载,试样仍恢复原来的尺寸,没有任何残余变形。习惯上认为材料在弹性范围内服从虎克定律,其应力、应变为正比关系,即 R E ε= (1-1) 比例系数E 代表直线OA 的斜率,称作材料的弹性模量。 屈服(流动)阶段(BC):R-ε曲线上出现明显的屈服点。这表明材料暂时丧失抵抗继续变形的能力。这时,应力基本上不变化,而变形快速增长。通常把下屈服点(B ˊ)作为材料屈服极限R eL 。R eL 是材料开始进入塑性的标志。结构、零件的应力一旦超过R eL ,材料就会屈服,零件就会因为过量变形而失效。因此强度设计时常以屈服极限R eL 作为确定许可应力的基础。从屈服阶段开始,材料的变形包含弹性和塑性两部分。如果试样表面光滑,材料杂质含量少,可以清楚地看到表面有45°方向的滑移线。
材料力学性能拉伸试验报告
材料力学性能拉伸试验报告 材化08 李文迪 40860044
[试验目的] 1. 测定低碳钢在退火、正火和淬火三种不同热处理状态下的强度与塑性性能。 2. 测定低碳钢的应变硬化指数和应变硬化系数。 [试验材料] 通过室温拉伸试验完成上述性能测试工作,测试过程执行GB/T228-2002:金属材料室温拉伸试验方法: 1.1试验材料:退火低碳钢,正火低碳钢,淬火低碳钢的R4标准试样各一个。 1.2热处理状态及组织性能特点简述: 1.2.1退火低碳钢:将钢加热到Ac3或Ac1以上30-50℃,保温一段时间后,缓慢而均匀 的冷却称为退火。 特点:退火可以降低硬度,使材料便于切削加工,并使钢的晶粒细化,消除应力。1.2.2正火低碳钢:将钢加热到Ac3或Accm以上30-50℃,保温后在空气中冷却称为正 火。 特点:许多碳素钢和合金钢正火后,各项机械性能均较好,可以细化晶粒。 1.2.3淬火低碳钢:对于亚共析钢,即低碳钢和中碳钢加热到Ac3以上30-50℃,在此 温度下保持一段时间,使钢的组织全部变成奥氏体,然后快速冷却(水冷或油冷),使奥氏体来不及分解而形成马氏体组织,称为淬火。 特点:硬度大,适合对硬度有特殊要求的部件。 1.3试样规格尺寸:采用R4试样。 参数如下:
1.4公差要求 [试验原理] 1.原理简介:材料的机械性能指标是由拉伸破坏试验来确定的,由试验可知弹性阶段 卸荷后,试样变形立即消失,这种变形是弹性变形。当负荷增加到一定值时,测力度盘的指针停止转动或来回摆动,拉伸图上出现了锯齿平台,即荷载不增加的情况下,试样继续伸长,材料处在屈服阶段。此时可记录下屈服强度R 。当屈服到一定 eL 程度后,材料又重新具有了抵抗变形的能力,材料处在强化阶段。此阶段:强化后的材料就产生了残余应变,卸载后再重新加载,具有和原材料不同的性质,材料的强度提高了。但是断裂后的残余变形比原来降低了。这种常温下经塑性变形后,材料强度提高,塑性降低的现象称为冷作硬化。当荷载达到最大值Rm后,试样的某一部位截面开始急剧缩小致使载荷下降,至到断裂。 [试验设备与仪器] 1.1试验中需要测得: (1)连续测量加载过程中的载荷R和试样上某段的伸长量(Lu-Lo)数据。(有万能材料试验机给出应力-应变曲线) (2)两个个直接测量量:试样标距的长度 L o;直径 d。 1.2试样标距长度与直径精度:由于两者为直接测量量,工具为游标卡尺,最高精度为 0.02mm。 1.3检测工具:万能材料试验机 WDW-200D。载荷传感器,0.5级。引伸计,0.5级。 注1:应力值并非试验机直接给出,由载荷传感器直接测量施加的载荷值,进而转化成工程应力,0.5级,即精确至载荷传感器满量程的1/500。 注2:连续测试试样上某段的伸长量由引伸计完成,0.5级,即至引伸计满量程的1/50。
低碳钢拉伸试验
试验一 金属材料的拉伸与压缩试验 1.1 概 述 拉伸实验是材料力学实验中最重要的实验之一。任何一种材料受力后都要产生变形,变形到一定程度就可能发生断裂破坏。材料在受力——变形——断裂的这一破坏过程中,不仅有一定的变形能力,而且对变形和断裂有一定的抵抗能力,这些能力称为材料的力学机械性能。通过拉伸实验,可以确定材料的许多重要而又最基本的力学机械性能。例如:弹性模量E 、比例极限R p 、上和下屈服强度R eH 和R eL 、强度极限R m 、延伸率A 、收缩率Z 。除此而外,通过拉伸实验的结果,往往还可以大致判定某种其它机械性能,如硬度等。 我们以两种材料——低碳钢,铸铁做拉伸试验,以便对于塑性材料和脆性材料的力学机械性能进行比较。 这个实验是研究材料在静载和常温条件下的拉断过程。利用电子万能材料试验机自动绘出的载荷——变形图,及试验前后试件的尺寸来确定其机械性能。 试件的形式和尺寸对实验的结果有很大影响,就是同一材料由于试件的计算长度不同,其延伸率变动的范围就很大。例如: 对45#钢:当L 0=10d 0时(L 0为试件计算长度,d 0为直径),延伸率A 10=24~29%,当L 0=5d 0时,A 5=23~25%。 为了能够准确的比较材料的性质,对拉伸试件的尺寸有一定的标准规定。按国标GB/T228-2002、GB/P7314-1987的要求,拉伸试件一般采用下面两种形式: 图1.1 1. 10倍试件; 圆形截面时,L 0=10d 0 矩形截面时,L 0=11.30S 2. 5倍试件 圆形截面时,L 0=5d 矩形截面时, L 0=5.650S = 045 S d 0——试验前试件计算部分的直径; S 0——试验前试件计算部分断面面积。 此外,试件的表面要求一定的光洁度。光洁度对屈服点有影响。因此,试件表面不应有刻痕、切口、翘曲及淬火裂纹痕迹等。 1.2 拉伸实验 一、实验目的: 1.研究低碳钢、铸铁的应力——应变曲线拉伸图。 2.确定低碳钢在拉伸时的机械性能(比例极限R p 、下屈服强度R eL 、强度极限R m 、延伸率A 、断
低碳钢和铸铁在拉伸试验中的力学性能教学内容
低碳钢和铸铁在拉伸试验中的力学性能
低碳钢和铸铁在拉伸和压缩时的力学性能 根据材料在常温,静荷载下拉伸试验所得的伸长率大小,将材料区分为塑性材料和脆性材料。它是由试验来测定的。工程上常用的材料品种很多,下面我们以低碳钢和铸铁为主要代表,分析材料拉伸和压缩时的力学性能。 1、低碳钢拉伸实验 在拉伸实验中,随着载荷的逐渐增大,材料呈现出不同的力学性能: (1)弹性阶段 在拉伸的初始阶段,ζ-ε曲线为一直线,说明应力与应变成正比,即满足胡克定理,此阶段称为线形阶段。线性段的最高点则称为材料的比例极限(ζp ),线性段的直线斜率即为材料的弹性摸量E 。线性阶段后,ζ-ε曲线不为直线,应力应变不再成正比,但若在整个弹性阶段卸载,应力应变曲线会沿原曲线返回,载荷卸到零时,变形也完全消失。卸载后变形能完全消失的应力最大点称为材料的弹性极限(ζe ),一般对于钢等许多材料,其弹性极限与比例极限非常接近。 (2)屈服阶段 超过弹性阶段后,应力几乎不变,只是在某一微小范围内上下波动,而应变却急剧增长,这种现象成为屈服。使材料发生屈服的应力称为屈服应力或屈服极限(ζs )。当材料屈服时,如果用砂纸将试件表面 1 打磨,会发现试件表面呈现出与轴线成45°斜纹。这是由于试件的45°斜截面上作用有最大切应力,这些斜纹是由于材料沿最大切应力作用面产生滑移所造成的,故称为滑移线。 (3)强化阶段 经过屈服阶段后,应力应变曲线呈现曲线上升趋势,这说明材料的抗变形能力又增强了,这种现象称为应变硬化。若在此阶段卸载,则卸载过程的应力应变曲线为一条斜线,其斜率与比例阶段的直线段斜率大致相等。当载荷卸载到零时,变形并未完全消失,应力减小至零时残留的应变称为塑性应变或残余应变,相应地应力减小至零时消失的应变称为弹性应变。卸载完之后,立即再加载,则加载时的应力应变关系基本上沿卸载时的直线变化。因此,如果将卸载后已有塑性变形的试样重新进行拉伸实验,其比例极限或弹性极限将得到提高,这一现象称为冷作硬化。 在硬化阶段应力应变曲线存在一个最高点,该最高点对应的应力称为材料的强度极限(ζb ),强度极限所对应的载荷为试件所能承受的最大载荷 Fb 。 (4)局部变形阶段 试样拉伸达到强度极限ζb 之前,在标距范围内的变形是均匀的。当应力增大至强度极限ζb 之后,试样出现局部显著收缩,这一现象称为颈缩。颈缩出现后,使试件继续变形所需载荷减小,故应力应变曲 2
低碳钢的拉伸实验
实验一低碳钢的拉伸实验 实验项目性质:验证性 所涉及课程:材料力学 计划学时:2学时 【实验目的】 1.研究低碳钢的应力—应变曲线拉伸图。 2.确定低碳钢在拉伸时的机械性能(比例极限R e、下屈服强度R eL、强度极限R m、延伸率A、断面收缩率Z等等)。 【实验设备】 1.微机控制电子万能试验机一台,型号WDD-LCJ-150; 2.游标卡尺; 3.记号笔; 4.低碳钢试件(Q235); 【实验原理】 低碳钢试件拉伸过程中,通过力传感器和位移传感器进行数据采集,A/D转换和处理,并输入计算机,得到F-?L曲线,即低碳钢拉伸曲线,见图1。 k 图1 低碳钢拉伸曲线 低碳钢材料,由图1曲线中发现oe直线,说明F正比于?l,此阶段称为弹性阶段。屈服阶段(e-L)常呈锯齿形,表示载荷基本不变,变形增加很快,材
料失去抵抗变形能力,这时产生两个屈服点。其中,H 点为上屈服点,它受变形大小和试件等因素影响;L 点为下屈服点。下屈服点比较稳定,所以工程上均以下屈服点对应的载荷作为屈服载荷。测定屈服载荷F eL 时,必须缓慢而均匀地加载,并应用R eL =F eL / S 0(S 0为试件变形前的横截面积)计算屈服强度。 屈服阶段终了后,要使试件继续变形,就必须增加载荷,材料进入强化阶段。当载荷达到强度载荷F m 后,在试件的某一局部发生显著变形,出现颈缩现象,载荷逐渐减小,直至试件断裂。应用公式R m =F m /S 0计算强度极限(S 0为试件变形前的横截面积)。根据拉伸前后试件的标距长度和横截面面积,计算出低碳钢的延伸率A 和端面收缩率Z ,即 %10000?-= L L Lu A ,%1000 0?-=S Su S Z 式中,L 0、L u 为试件拉伸前后的标距长度,S u 为颈缩处的横截面积。 【实验步骤及内容】 (1)试件准备:在试件上划出长度为L 0的标距线(默认值为100mm ),在标距的两端及中部三个位置上,沿两个相互垂直方向各测量一次直径取平均值,再从三个平均值中取最小值作为试件的直径d 0。 (2)试验机准备:按试验机→计算机的顺序开机,开机后须预热十分钟才可使用。按照“软件使用手册”,运行配套软件。 (3)安装夹具:根据试件情况准备好夹具,并安装在夹具座上。若夹具已安装好,对夹具进行检查。 (4)夹持试件:先将试件夹持在下夹头上,点击软件初始试验消除试件自重后再夹持试件的另一端。 (5)开始实验:点击软件界面工具菜单,选择试验为拉伸试验,在弹出窗口设置低碳钢标距、直径、横截面积等参数;按启动命令按钮,开始加载,加载速度可自行设置。 (6)记录数据:试件拉断后,取下试件,将断裂试件的两端对齐、靠紧,用游标卡尺测出试件断裂后的标距长度L u 及断口处的最小直径d 1(一般从相互垂