镀膜设备原理及工艺
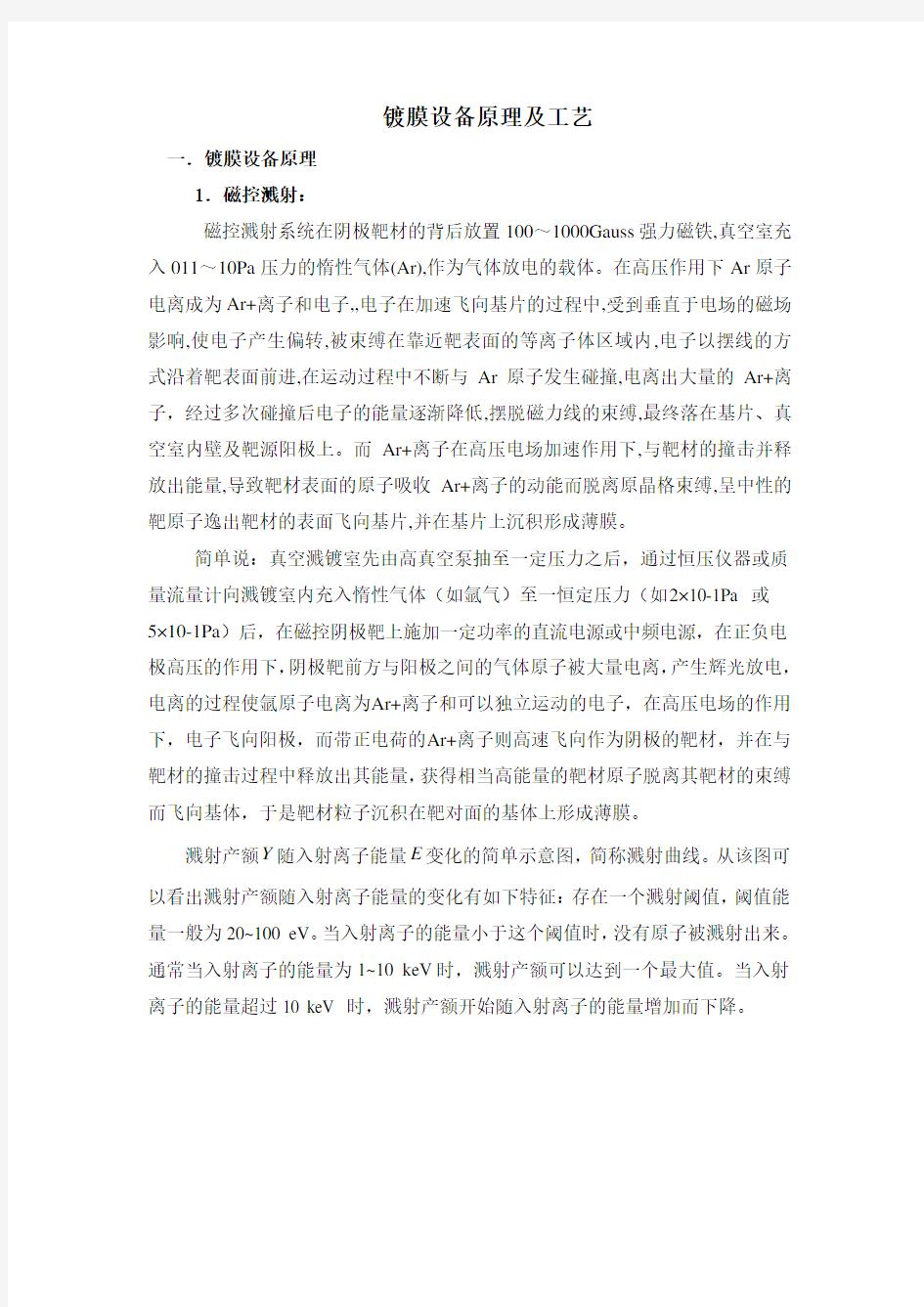

镀膜设备原理及工艺
一.镀膜设备原理
1.磁控溅射:
磁控溅射系统在阴极靶材的背后放置100~1000Gauss强力磁铁,真空室充入011~10Pa压力的惰性气体(Ar),作为气体放电的载体。在高压作用下Ar原子电离成为Ar+离子和电子,,电子在加速飞向基片的过程中,受到垂直于电场的磁场影响,使电子产生偏转,被束缚在靠近靶表面的等离子体区域内,电子以摆线的方式沿着靶表面前进,在运动过程中不断与Ar原子发生碰撞,电离出大量的Ar+离子,经过多次碰撞后电子的能量逐渐降低,摆脱磁力线的束缚,最终落在基片、真空室内壁及靶源阳极上。而Ar+离子在高压电场加速作用下,与靶材的撞击并释放出能量,导致靶材表面的原子吸收Ar+离子的动能而脱离原晶格束缚,呈中性的靶原子逸出靶材的表面飞向基片,并在基片上沉积形成薄膜。
简单说:真空溅镀室先由高真空泵抽至一定压力之后,通过恒压仪器或质量流量计向溅镀室内充入惰性气体(如氩气)至一恒定压力(如2×10-1Pa 或
5×10-1Pa)后,在磁控阴极靶上施加一定功率的直流电源或中频电源,在正负电极高压的作用下,阴极靶前方与阳极之间的气体原子被大量电离,产生辉光放电,电离的过程使氩原子电离为Ar+离子和可以独立运动的电子,在高压电场的作用下,电子飞向阳极,而带正电荷的Ar+离子则高速飞向作为阴极的靶材,并在与靶材的撞击过程中释放出其能量,获得相当高能量的靶材原子脱离其靶材的束缚而飞向基体,于是靶材粒子沉积在靶对面的基体上形成薄膜。
溅射产额Y随入射离子能量E变化的简单示意图,简称溅射曲线。从该图可以看出溅射产额随入射离子能量的变化有如下特征:存在一个溅射阈值,阈值能量一般为20~100 eV。当入射离子的能量小于这个阈值时,没有原子被溅射出来。通常当入射离子的能量为1~10 keV时,溅射产额可以达到一个最大值。当入射离子的能量超过10 keV 时,溅射产额开始随入射离子的能量增加而下降。
Y
3
2
1
10 102103 104105106
入射离子的能量E(eV)
图 6.1 溅射产额随入射离子能量变化的示意图。
2.主要溅射方式:
反应溅射是在溅射的惰性气体气氛中,通入一定比例的反应气体,通常用作反应气体的主要是氧气和氮气。
直流溅射(DC Magnetron Sputtering)、射频溅射(RF Magnetron Sputtering)、脉冲溅射(PulsedMagnetro n Sp uttering)和中频溅射(Medium Fre2quency Magnetro n Sp uttering)
直流溅射方法用于被溅射材料为导电材料的溅射和反应溅射镀膜中,其工艺设备简单,有较高的溅射速率。
中频交流磁控溅射在单个阴极靶系统中,与脉冲磁控溅射有同样的释放电荷、防止打弧作用。中频交流溅射技术还应用于孪生靶(Twin2Mag)溅射系统中,中频交流孪生靶溅射是将中频交流电源的两个输出端,分别接到闭合磁场非平衡溅射双靶的各自阴极上,因而在双靶上分别获得相位相反的交流电压,一对磁控溅射靶则交替成为阴极和阳极。孪生靶溅射技术大大提高磁控溅射运行的稳定性,可避免被毒化的靶面产生电荷积累,引起靶面电弧打火以及阳极消失的问题,溅射速率高,为化合物薄膜的工业化大规模生产奠定基础。
连续式的磁控溅射生产线总体上可以分为三个部分: 前处理, 溅射镀膜, 后处理。
2. 1 前处理(清洗工序)
要获得结合牢固、致密、无针孔缺陷的膜层, 必须使膜层沉积在清洁、具有一定温度甚至是激活的基片上。为此前处理的过程包括机械清洗(打磨、毛刷水洗、去离子水冲洗、冷热风刀吹净)、烘烤、辉光等离子体轰击等。机械清洗的目的是去除基片表面的灰尘和可能残留的油渍等异物, 并且不含活性离子, 必要时还可采用超声清洗。烘烤的目的是彻底清除基片表面残余的水份, 并使基片加热到一定的温度, 很多材质在较高的基片温度下可以增强结合力和膜层的致密性。基片的烘烤可以在真空室外进行, 也可以在真空室内继续进行, 以获得更好的效果。但在真空室内作为提供热源的电源应有较低的电压, 否则易于引起放电。辉光等离子体轰击清洗可以进一步除去基片表面残留的不利于膜层沉积的成份, 同时可以提高基片表面原子的活性, 更有利于基片与沉积的材质原子产生牢固的结合。使用中频电源会取得比直流放电更明显的效果。
2. 2 溅射镀膜
这部分应是生产线的主体, 而且是处在真空状态下的一个系统, 是由不锈钢或碳钢做成的一个个独立的室体连接组成。它的两端为了反复地使清洗过的玻璃基片进入和让镀制好的基片输出, 而处在一个特殊的状态, 称为真空锁室。每个锁室的两端都有阀门并配置抽气能力强大的真空机组, 可以容易地完成真空和大气的转换。与真空锁室相连的真空室体称之为过渡室。它的作用是停留由锁室输入的待镀基片, 或让沉积好的基片停留于此, 等待输出锁室, 起到调配基片运行的作用。过渡室亦应配置真空机组, 并要保持较高的真空度。输入端的过渡室内可以设置辉光放电等离子清洗装置。但应考虑与基片运行方向相邻的室体的隔离, 这种隔离主要是相邻的室体维持不同的压力。辉光放电的压力一般较高, 而溅射镀膜的工作压力往往在更低的量级。在前后过渡室之间的部分称为镀膜室或溅射室。每个镀膜室是一个独立的沉积区域。所谓独立是指该镀膜室内的工作压力以及工作氛围不受其它室体的影响。每个溅射室设有一付或两付靶位。每付靶位上可以安装一付磁控溅射靶, 或称为阴极。溅射室的数量亦或溅射靶的数量, 包括选用的靶材, 取决于生产线开发膜系的能力和产量。磁控溅射靶的功率密度一般13W/ cm2, 比直流溅射要高得多。但实际的电源往往很难保证靶的功率。没
有大的功率就没有高沉积速率,而高沉积速率是现代镀膜所推崇的。电源的并联是增强功率的一个途径。平面磁控靶的结构分为直冷式和间冷式两类。直冷式适合于气密性好的靶材。由于冷却效果好, 功率更大一些。间冷式的适合于气密性较差的靶材, 功率要小一些。靶内磁体目前更多采用的是钕铁硼永磁体, 只要保证磁场的均匀, 再在工作气体的布气装置上采用合理的方式, 在整个靶面的区
域内, 实践证明均能获得均匀的溅射刻蚀。这是膜层横向均匀性的重要保证。考虑到靶的两端所产生的边缘效应, 为使基片的两端也获得与中间部分相同的膜厚, 靶的两端要伸出基片边缘足够的长度。高真空的背景是溅射沉积的必要条件, 所以溅射室对称设置有高真空机组。目前采用的大多是扩散泵机组。进口设备中, 配置涡轮分子泵的, 但维修麻烦, 更换轴承需由厂家进行;配置扩散泵的还加有液氮冷阱, 这样有更好的挡油效果, 但维持费用高。这种泵用于进片室可以免油蒸汽对基片的污染, 并可防止活性气体周期性的混入镀膜室内。在溅射镀膜中尽量抑制油蒸汽的污染的必要性应是无可争议的。为了保证每个溅射室能在独立的气氛下工作, 相邻的溅射室之间应采取气氛隔离措施。这可通过狭缝装置来达到隔离的目的。所谓狭缝是用两块横贯室体的钢板水平围成的长200~ 300mm , 高10~ 12mm 的空间, 这是一种流导模型, 在分子态下具有很小的传输几率。狭缝所处位置的室体横截面, 除了缝外完全隔断。这样两道狭缝相距40~ 50 cm 设置便可形成一种物理上的隔离。两狭缝围成空间的两端配置有高真空机组, 可使隔离效果更佳, 控制在1% 以内。这种结构的优越之处在于隔离气氛和传输玻璃可同时兼顾。如若不能实现有效的隔离, 当相邻的沉积区域气氛不同时,则相互的影响将严重的破坏膜层的均匀性, 甚至结构,这是不能允许的。
2. 3 后处理
镀制好的基片从真空室内输送到大气中后, 一般还要经过清洗及检测。清洗的要求没有前处理那么严格。目的是使膜层的缺陷更容易暴露出来, 以便在后续的检测中被发现。最简单的检测就是目测, 为便于观察, 基片的底部分布有光源, 可以发现针孔的存在和数量, 有无放电的痕迹。出线端的透过率检测仪可以指出膜层最终的透过率。也可以在基片范围内布置多道探头, 采集数据由计算机处理来评估膜层的纵向和横向的均匀性及有无异常。对于特殊用途的光学薄膜出线后即进入净化室, 覆上一层保护用的带胶薄膜后存放。
二 .工艺流程:
2.1 SITO结构涂OC保护层:(黄光区)
2.2 SITO结构涂SiO2保护层:
磁控溅射镀膜原理和工艺设计
磁控溅射镀膜原理及工艺 摘要:真空镀膜技术作为一种产生特定膜层的技术,在现实生产生活中有着广泛的应用。真空镀膜技术有三种形式,即蒸发镀膜、溅射镀膜和离子镀。这里主要讲一下由溅射镀 膜技术发展来的磁控溅射镀膜的原理及相应工艺的研究。 关键词:溅射;溅射变量;工作气压;沉积率。 绪论 溅射现象于1870年开始用于镀膜技术,1930年以后由于提高了沉积速率而逐渐用于工业生产。常用二极溅射设备如右图。 通常将欲沉积的材料制成板材-靶,固定在阴 极上。基片置于正对靶面的阳极上,距靶一定距 离。系统抽至高真空后充入(10~1)帕的气体(通 常为氩气),在阴极和阳极间加几千伏电压,两极 间即产生辉光放电。放电产生的正离子在电场作 用下飞向阴极,与靶表面原子碰撞,受碰撞从靶 面逸出的靶原子称为溅射原子,其能量在1至几十 电子伏范围内。溅射原子在基片表面沉积成膜。 其中磁控溅射可以被认为是镀膜技术中最突出的 成就之一。它以溅射率高、基片温升低、膜-基结 合力好、装置性能稳定、操作控制方便等优点, 成为镀膜工业应用领域(特别是建筑镀膜玻璃、透 明导电膜玻璃、柔性基材卷绕镀等对大面积的均 匀性有特别苛刻要求的连续镀膜场合)的首选方 案。 1磁控溅射原理 溅射属于PDV(物理气相沉积)三种基本方法:真空蒸发、溅射、离子镀(空心阴极离子镀、热阴极离子镀、电弧离子镀、活性反应离子镀、射频离子镀、直流放电离子镀)中的一种。 磁控溅射的工作原理是指电子在电场E的作用下,在飞向基片过程中与氩原子发生碰撞,使其电离产生出Ar正离子和新的电子;新电子飞向基片,Ar正离子在电场作用下加速飞向阴极靶,并以高能量轰击靶表面,使靶材发生溅射。在溅射粒子中,中性的靶原子或分子沉积在基片上形成薄膜,而产生的二次电子会受到电场和磁场作用,产生E(电场)×B(磁场)所指的方向漂移,简称E×B漂移,其运动轨迹近似于一条摆线。若为环形磁场,则电子就以近似摆线形式在靶表面做圆周运动,它们的运动路径不仅很长,而且被束缚在靠近靶表面的等离子体区
真空蒸发和离子溅射镀膜
实验一真空蒸发和离子溅射镀膜 随着材料科学的发展,近年来薄膜材料作为其中的一个重要分支从过去体材料一统天下的局面中脱赢而出。如过去需要众多材料组合才能实现的功能,现在仅需数几个器件或一块 集成电路板就能完成,薄膜技术正是实现器件和系统微型化的最有效的技术手段。薄膜技术 还可以将各种不同的材料灵活的复合在一起,构成具有优异特性的复杂材料体系,发挥每种 材料各自的优势,避免单一材料的局限性。薄膜的应用范围越来越宽,按其用途可分为光学薄膜、微电子学薄膜、光电子学薄膜、集成光学薄膜、信息存储薄膜、防护功能薄膜等。目前,薄膜材料在科学技术和社会经济各个领域发挥着越来越重要的作用。因此薄膜材料的制 备和研究就显得非常重要。 薄膜的制备方法可分为物理法、化学法和物理化学综合法三大类。物理法主要指物理气 相沉积技术(Physical Vapor Deposition, 简称PVD),即在真空条件下,采用各种物理方法 将固态的镀膜材料转化为原子、分子或离子态的气相物质后再沉积于基体表面,从而形成固 体薄膜的一类薄膜制备方法。物理气相沉积过程可概括为三个阶段: 1.从源材料中发射出粒 子;2.粒子输运到基片;3.粒子在基片上凝结、成核、长大、成膜。由于粒子发射可以采用不同的方式,因而物理气相沉积技术呈现出各种不同形式,主要有真空蒸发镀膜、溅射镀膜 和离子镀膜三种主要形式。在这三种PVD基本镀膜方法中,气相原子、分子和离子所产生的方式和具有的能量各不相同,由此衍生出种类繁多的薄膜制备技术。本实验主要介绍了真空 蒸发和离子溅射两种镀膜技术。在薄膜生长过程中,膜的质量与真空度、基片温度、基片清 洁度、蒸发器的清洁度、蒸发材料的纯度、蒸发速度等有关。在溅射薄膜的生长过程中,气体流量(压力)也会对形成的薄膜的性质产生影响。通过改变镀膜条件,即可得到性质炯异的薄膜材料。 对制备的薄膜材料,可通过 X射线衍射、电子显微镜(扫描电镜、透射电镜等)、扫描探针(扫描隧道显微镜、原子力显微镜等)以及光电子能谱、红外光谱等技术来进行分析和 表征,还可通过其它现代分析技术测试薄膜的各种相应特性等。 【实验目的】 1?掌握溅射的基本概念,学习直流辉光放电的产生过程和原理; 2?掌握几种主要溅射镀膜法基本原理及其特点,掌握真空镀膜原理; 3.掌握真空镀膜和溅射镀膜的基本方法; 4?熟悉金属和玻璃片的一般清洗技术,学习薄膜厚度的测量方法; 5.了解真空度、基片温度、基片清洁度、蒸发器的清洁度、蒸发材料的纯度、蒸发速度等 因素,在薄膜生长过程中对形成薄膜性质的影响。 【实验原理】 一真空蒸发镀膜原理 任何物质在一定温度下,总有一些分子从凝聚态(固态,液态)变成为气态离开物质表 面,但固体在常温常压下,这种蒸发量是极微小的。如果将固体材料置于真空中加热至此材料蒸发温度时,在气化热作用下材料的分子或原子具有足够的热震动能量去克服固体表面原子间的吸引力,并以一定速度逸出变成气态分子或原子向四周迅速蒸发散射。当真空度高,分子平均自由程—远大于蒸发器到被镀物的距离d时(一般要求2~ 3 d ),材料的蒸气分子在散射途中才能无阻当地直线达到被镀物和真空室表面。在化学吸附(化学键力引起 的吸附)和物理吸附(靠分子间范德瓦尔斯力产生的吸附)作用下,蒸气分子就吸附在基片
溅射技术及其发展的历程
溅射技术及其发展的历程 1842年格洛夫(Grove)在实验室中发现了阴极溅射现象。他在研究电子管阴极腐蚀问题时,发现阴极材料迁移到真空管壁上来了。但是,真正应用于研究的溅射设备到1877年才初露端倪。迄后70年中,由于实验条件的限制,对溅射机理的认同长期处于模糊不请状态,所以,在1950年之前有关溅射薄膜特性的技术资料,多数是不可*的。19世纪中期,只是在化学活性极强的材料、贵金属材料、介质材料和难熔金属材料的薄膜制备工艺中,采用溅射技术。1970年后出现了磁控溅射技术,1975年前后商品化的磁控溅射设备供应于世,大大地扩展了溅射技术应用的领域。到了80年代,溅射技术才从实验室应用技术真正地进入工业化大量生产的应用领域。最近15年来,进一步发展了一系列新的溅射技术,几乎到了目不暇接的程度。在21世纪来临的时刻,回顾一下溅射技术发展的历程,寻找其中某些规律性的思路,看来是有一定意义的。 1.最初溅射技术改革的原动力主要是围绕着提高辉光等离子体的离化率,增强离化的措施包括: [1]热电子发射增强—由原始的二极溅射演变出三极溅射。三极溅射应用的实际效果对离化率增强的幅度并不大,但是对溅射过程中,特别是在反应溅射过程中,工艺的可控性有明显地改善。 [2]电子束或电子弧柱增强—演变出四极溅射。Balzers一直抓住这条线,形成有其特色的产品系列,最近几年推出在中心设置一个强流热电子弧柱,配合上下两个调制线圈,再加上8对孪生靶,组合成新型纳米涂层工具镀膜机。是一个典型实例。 [3]磁控管模式的增强溅射—磁控溅射。利用磁控管的原理,将等离子体中原来分散的电子约束在特定的轨道内运转,局部强化电离,导致靶材表面局部强化的溅射效果。号称为“高速、低温”溅射技术。磁控溅射得到广泛应用的原因,除了效果明显之外,结构不复杂是一个重要的因数,大面积的溅射镀膜工艺得到推广。应该看到,靶面溅射不均匀导致靶材利用率低是其固有的缺点。 [4]最近有人推出离子束增强溅射模式。采用宽束强流离子源,配合磁场调制,与普通的二极溅射结合组成一种新的溅射模式。他不同于使用窄束高能离子束进行的离子束溅射(这种离子束溅射的溅射速率低),采用宽束强流离子源,配合磁场调制后,既有离子束溅射的效果,更重要的是具有直接向等离子体区域供应离子的增强溅射效果。同时还可以具有离子束辅助镀膜的效果。 2.1985年之后,溅射模式的变革增加了新的目标,除了继续追求高速率之外,追求反应溅射稳定运行的目标、追求离子辅助镀膜—获得高质量膜层的目标、等等综合优越性的追求目标日益增强。例如: [1]捷克人J.Musil在研究低压强溅射的工作中,在磁控溅射的基础上,重复使用各种原来在二极溅射增强溅射中使用过的手段。从“低压强溅射”一直发展到“自溅射”效应。其中大部分工作仍然处于实验室阶段。 [2]针对立体工件获得均匀涂层和色泽,Leybold推出对靶溅射运行模式。在随后不断改进的努力下,对靶溅射工艺仍然具有涂层质量优异的美名。 [3]针对膜层组分可随意调节的目标,推出非对称溅射的运行模式。我国清华大学范毓殿教授采用调节溅射靶磁场强度的方法,进行了类似的工作。 [4]推出非平衡溅射的运行模式最基本的目的是为了改善膜层质量,呈现离子辅助溅射的效果。后来,一些研究工作扩展磁场增强的布局,磁场在真空室内无处不在,看来效果并不理想,“非平衡”的热潮才逐渐降温。 [5]1996年Leybold 推出多年研发的成果:中频交流磁控溅射(孪生靶溅射)技术,消除了阳极”消失”效应和阴极“中毒”问题,大大提高了磁控溅射运行的稳定性,为化合物薄膜的工业化大规模生产奠定了基础。最近在中频电源上又提出短脉冲组合的中频双向供电模式,运行稳定性进一步提高。 [6]最近英国Plasma Quest Limited(PQL)公司推出S400型专利产品,名为“高密度等离子体发送系统”(High Plasma Launch System),属于上面提到的离子束增强二极溅射模式。其特点是:高成膜速率、
溅射镀膜
溅射镀膜介绍 一: 溅射镀膜应用: 溅射镀膜主要用于半导体生产的金属薄膜的生长.如下图的金属层1到金属层6都是运用溅射镀膜所生产. 溅射镀膜到形成所需的金属线的过程为: 溅射镀膜--→光照显影--→蚀刻(形成金属连接线) 二: 溅射镀膜原理 溅射淀积(溅射)是另一种老工艺,能够适应现代半导体制造需要。它几乎可以在任何衬底上淀积任何材料,而且广泛应用在人造珠宝涂层,镜头和眼镜的光学涂层的制造。
在真空反应室中,由镀膜所需的金属构成的固态厚板被称为靶材(target)(图1),靶材接阴极,衬底接阳极并接地。首先将氩气充入室内,并且电离成正电荷。带正电荷的氩离子被不带电的靶吸引,加速冲向靶。在加速过程中这些离子受到引力作用,获得动量,轰击靶材。这样在靶上就会出现动量转移现象(momentum transfer)。正如在桌球,球杆把能量传递到其他球,使它们分散一样,氩离子轰击靶,引起其上的原子分散。被氩离子从靶上轰击出的原子和分子进入反应室。这就是溅射过程。从靶上轰击出原材料之后,氩离子、轰击出的原材料、气体原子和溅射工艺所产生的电子在靶前方形成一个等离子区域。等离子区是可见的,呈现紫色。而黑色区域将等离子区和靶分开,我们称之为暗区(dark space)。 图1 溅射工艺的原理 被轰击出的原子或分子散布在反应室中,其中一部分渐渐地停落在晶圆上,形成薄膜,溅射工艺的主要特征是淀积在晶圆上的靶材不发生化学或合成变化。形成薄膜的过程有如下几个过程(图2所示): 1长晶 2 晶粒成长 3 晶粒聚集 4 缝隙填补 5 沉积膜的成长
图2 溅射工艺的原理 三:溅射镀膜相对于真空蒸发优点: 1 靶材的成分不会改变。这种特征的直接益处就是有利于合金膜和绝缘膜的淀积。合金真空蒸发的问题在前一部分已作描述。对于溅射工艺来说,含有2%铜的铝靶材就可以在晶圆上生长出含有2%铜的铝薄膜。 2 阶梯覆盖度也可以通过溅射改良。蒸发来自于点源,而溅射来自平面源。因为金属微粒被从靶材各个点溅射出来的,所以在到达晶圆承载台时,它们可以从各个角度覆盖晶圆表面。阶梯覆盖度还可以通过旋转晶圆和加热晶圆,得到进一步的优化。 3溅射形成的薄膜对晶圆表面的粘附性也比蒸发工艺提高很多。首先,轰击出的原子在到达晶圆表面时的能量越高,因而所形成薄膜的粘附性就越强。其次,反应室中的等离子环境有“清洁”5晶圆表面的作用,从而增强了粘附性。因此在淀积薄膜之前,将晶圆承载台停止运动,对晶圆表面溅射一小段时间,可以提高粘附性和表面洁净度。在这种模式下,溅射系统所起的作用与在第十章介绍的离子刻蚀(溅射刻蚀,反溅射)设备一样。 4溅射最大的贡献恐怕就是对薄膜特性的控制了。这种控制是通过调节溅射参数达到的,包括压力、薄膜淀积速率和靶材。通过多种靶材的排列,一种工艺就可以溅射出像三明治一样的多层结构。 5清洁干燥的氩气(或氖气)可以保持薄膜的成分特征不变,而且低湿度可以阻止薄膜发生不必要的氧化。反应室装载晶圆之后,泵开始抽气(向外),将其压力减小到1×10-9托左右。然后充入氩气,并使其电离。要严格控制进入室内的氩气的量,因为氩气增多会造成室内压力升高。由于氩气和轰击出的原材料存在,室内压力将上升到大约10-3托。 四:溅射分类: 1直流溅射 在反应室中,靶接负电压呈阴极;而衬底呈阳极。带负电的靶驱逐电子,使其加速飞向阳极。在运动过程中,电子与氩原子碰撞,使氩原子电离成氩离子。具有正电性的氩离子加速飞向靶,开始溅射工艺。氩离子(+)和靶(-)形成了两极。
真空蒸发和离子溅射镀膜
实验一 真空蒸发和离子溅射镀膜 随着材料科学的发展,近年来薄膜材料作为其中的一个重要分支从过去体材料一统天下的局面中脱赢而出。如过去需要众多材料组合才能实现的功能,现在仅需数几个器件或一块集成电路板就能完成,薄膜技术正是实现器件和系统微型化的最有效的技术手段。薄膜技术还可以将各种不同的材料灵活的复合在一起,构成具有优异特性的复杂材料体系,发挥每种材料各自的优势,避免单一材料的局限性。薄膜的应用围越来越宽,按其用途可分为光学薄膜、微电子学薄膜、光电子学薄膜、集成光学薄膜、信息存储薄膜、防护功能薄膜等。目前,薄膜材料在科学技术和社会经济各个领域发挥着越来越重要的作用。因此薄膜材料的制备和研究就显得非常重要。 薄膜的制备方法可分为物理法、化学法和物理化学综合法三大类。物理法主要指物理气相沉积技术(Physical Vapor Deposition,简称PVD),即在真空条件下,采用各种物理方法将固态的镀膜材料转化为原子、分子或离子态的气相物质后再沉积于基体表面,从而形成固体薄膜的一类薄膜制备方法。物理气相沉积过程可概括为三个阶段:1.从源材料中发射出粒子;2.粒子输运到基片;3.粒子在基片上凝结、成核、长大、成膜。由于粒子发射可以采用不同的方式,因而物理气相沉积技术呈现出各种不同形式,主要有真空蒸发镀膜、溅射镀膜和离子镀膜三种主要形式。在这三种PVD 基本镀膜方法中,气相原子、分子和离子所产生的方式和具有的能量各不相同,由此衍生出种类繁多的薄膜制备技术。本实验主要介绍了真空蒸发和离子溅射两种镀膜技术。在薄膜生长过程中,膜的质量与真空度、基片温度、基片清洁度、蒸发器的清洁度、蒸发材料的纯度、蒸发速度等有关。在溅射薄膜的生长过程中,气体流量(压力)也会对形成的薄膜的性质产生影响。通过改变镀膜条件,即可得到性质炯异的薄膜材料。 对制备的薄膜材料,可通过X 射线衍射、电子显微镜(扫描电镜、透射电镜等)、扫描探针(扫描隧道显微镜、原子力显微镜等)以及光电子能谱、红外光谱等技术来进行分析和表征,还可通过其它现代分析技术测试薄膜的各种相应特性等。 【实验目的】 1.掌握溅射的基本概念,学习直流辉光放电的产生过程和原理; 2.掌握几种主要溅射镀膜法基本原理及其特点,掌握真空镀膜原理; 3.掌握真空镀膜和溅射镀膜的基本方法; 4.熟悉金属和玻璃片的一般清洗技术,学习薄膜厚度的测量方法; 5.了解真空度、基片温度、基片清洁度、蒸发器的清洁度、蒸发材料的纯度、蒸发速度等因素,在薄膜生长过程中对形成薄膜性质的影响。 【实验原理】 一 真空蒸发镀膜原理 任何物质在一定温度下,总有一些分子从凝聚态(固态,液态)变成为气态离开物质表面,但固体在常温常压下,这种蒸发量是极微小的。如果将固体材料置于真空中加热至此材料蒸发温度时,在气化热作用下材料的分子或原子具有足够的热震动能量去克服固体表面原子间的吸引力,并以一定速度逸出变成气态分子或原子向四周迅速蒸发散射。当真空度高,分子平均自由程λ远大于蒸发器到被镀物的距离d 时(一般要求()d 3~2λ=),材料的蒸气分子在散射途中才能无阻当地直线达到被镀物和真空室表面。在化学吸附(化学键力引起
溅射镀膜技术
溅射镀膜技术 薄膜是一种特殊的物质形态,由于其在厚度这一特定方向上尺寸很小,只是微观可测的量,而且在厚度方向上由于表面、界面的存在,使物质连续性发生中断,由此使得薄膜材料产生了与块状材料不同的独特性能。薄膜的制备方法很多,如气相生长法、液相生长法(或气、液相外延法)、氧化法、扩散与涂布法、电镀法等等,而每一种制膜方法中又可分为若干种方法。薄膜技术涉及的范围很广,它包括以物理气相沉积和化学气相沉积为代表的成膜技术,以离子束刻蚀为代表的微细加工技术,成膜、刻蚀过程的监控技术,薄膜分析、评价与检测技术等等。现在薄膜技术在电子元器件、集成光学、电子技术、红外技术、激光技术以及航天技术和光学仪器等各个领域都得到了广泛的应用,它们不仅成为一间独立的应用技术,而且成为材料表面改性和提高某些工艺水平的重要手段。 溅射是薄膜淀积到基板上的主要方法。溅射镀膜是指在真空室中,利用荷能粒子轰击镀料表面,使被轰击出的粒子在基片上沉积的技术。 一.溅射工艺原理 溅射镀膜有两类:离子束溅射和气体放电溅射 1. 离子束溅射:在真空室中,利用离子束轰击靶表面,使溅射出的粒子在基片
表面成膜。 特点:①离子束由特制的离子源产生 ②离子源结构复杂,价格昂贵 ③用于分析技术和制取特殊薄膜 2. 气体放电溅射:利用低压气体放电现象,产生等离子体,产生的正离子,被电场加速为高能粒子,撞击固体(靶)表面进行能量和动量交换后,将被轰击固体表面的原子或分子溅射出来,沉积在衬底材料上成膜的过程。 二. 工艺特点 1.整个过程仅进行动量转换,无相变 2.沉积粒子能量大,沉积过程带有清洗作用,薄膜附着性好 3.薄膜密度高,杂质少 4.膜厚可控性、重现性好 5.可制备大面积薄膜 6.设备复杂,沉积速率低。 三.溅射的物理基础——辉光放电 溅射镀膜基于高能粒子轰击靶材时的溅射效应。整个溅射过程是建立在辉光放电的基础上,使气体放电产生正离子,并被加速后轰击靶材的离子离开靶,沉积成膜的过程。 不同的溅射技术采用不同的辉光放电方式,包括:直流辉光放电—直流溅射、射频辉光放电—射频溅射和磁场中的气体放电—磁控溅射 1. 直流辉光放电指在两电极间加一定直流电压时,两电极间的稀薄气体(真空度约为13.3-133Pa)产生的放电现象。 2. 射频辉光放电指通过电容耦合在两电极之间加上射频电压,而在电极之间产生的放电现象。电子在变化的电场中振荡从而获得能量,并且与原子碰撞产生离子和更多的电子。 3. 电磁场中的气体放电在放电电场空间加上磁场,放电空间中的电子就要围绕磁力线作回旋运动,其回旋半径为eB/mv,磁场对放电的影响效果,因电场
EMI溅射镀膜的原理 - 硬件和射频工程师
什么是EMI 电磁兼容性(Electro magnetic Compatibility)缩写EMC,就是指某电子设备既不干扰其它设备,同时也不受其它设备的影响。电磁兼容性和我们所熟悉的安全性一样,是产品质量最重要的指标之一。安全性涉及人身和财产,而电磁兼容性则涉及人身和环境保护。 电磁波会与电子元件作用,产生干扰现象,称为EMI(Electromagnetic Interference)。例如,TV 荧光屏上常见的“雪花”便表示接受到的讯号被干扰。 为什么要做EMI镀膜 一. 技术驱动力 设备的小型化使源与敏感器靠得很近。这使传播路径缩短,增加了干扰的机会。器件的小型化增加了它们对干扰的敏感度。由于设备越来越小并且便于携带,象汽车电话、膝上计算机等设备随处可用,而不一定局限于办公室那样的受控环境。这也带来了兼容性问题。例如,许多汽车装有包括防抱死控制系统在内的大量的电子电路,如果汽车电话与这个控制系统不兼容,则会引起误动作。 互联技术的发展降低了电磁干扰的阈值。例如,大规模集成电路芯片较低的供电电压降低了内部噪声门限,而它们精细的几何尺寸的较低的电平下就受到电弧损坏。它们更快的同步操作产生更尖的电流脉冲,这会带来从I/O端口产生宽带发射的问题。一般来说,高速数字电路比传统的模拟电路产生更多的干扰。 传统上,电子线路装在金属盒内,这种金属盒能够通过切断电磁能量的传插路径来提供屏蔽作用。现在,为了减轻重量、降低成本,越来越多地采用塑料机箱。塑料机箱对与电磁干扰是透明的,因此敏感器件处于无保护的状态。 法律的变化也是驱动力之一。控制电磁发射和敏感度的强制标准的实施,迫使制造商们实施EMC计划。产品可靠性的法规将使可靠性成为头等重要的事项,因为一旦设备由于干扰而产生误动作造成伤害,制造商要承担法律责任。这对于医疗设备特别重要。 在竞争日益激烈的工业中,可靠性已经成为电子设备的一个重要市场特征。自动化设备,特别是医疗设备,必须连续工作,这时设备内的EMI屏蔽技术提高了设备的可靠性。 对于数据保密的要求是屏蔽市场发展的一个重要动力。已有报道揭露美国驻莫斯科使馆追究中的信息已被前苏联窃取到,这是通过接收使馆内设备产生的电磁能量来实现的。同样的技术也被用来截获密码,然后攻击银行计算机系统。通过屏蔽,设备的电磁发射能够减小,提高系统的安全性。 现在,人们越来越开始注意各种辐射对健康的影响。过量的X射线和紫外线照射的危险已经被充分证明了。现在讨论的焦点是微波和射频显示单元产生的辐射对妇女健康的伤害,因为已经有充分的证据说明在高压线附近生活会患疾病。 二. 法规和标准 现在有许多关于产品辐射和传导发射限制的国家标准和国际标准。有些还规定了对各种干扰的最低敏感度要求。通常,对于不同类型的电子设备有不同的标准。虽然一个产品要获得市场的成功,满足这些标准是必要的,但符合这些标准是自愿的。 但是,有些国家给出的是规范,而不是标准,因此要在这些国家销售产品,符合标准是强制性的。有些规范不仅规定了标准,还赋予当局罚没不符合产品的权力。 三. 市场因素 笔记本电脑,ADSL和移动电话等3C产品都会因高频电磁波干扰产生杂讯,影响通讯品质。另若人体长期暴露于强力电磁场下,则可能易患癌症病变。因此防电磁波干扰已是必备而且势在必行的制程。 怎么做EMI防护
磁控溅射镀膜的简介及其实际操作
磁控溅射镀膜的简介及其实际操作 作者:徐超群 作者单位:乐山师范学院物理与电子工程系 【摘要】溅射技术的最新成就之一是磁控溅射。对于二级溅射、偏压溅射、三级或四级溅射和射频溅射而言。它们的缺点是沉积速率较低,特别是阴极溅射。因为它们在放电过程中只有大约0.3~0.5%的气体分子被电离。为了在低气压下进行高速溅射,必须有效的提高气体的离化率。由于在磁控溅 射中引入了正交电磁场使离化率提高到5~6%。于是溅射速率比三级溅射提高10倍左右,对许多材料,溅射速率达到了电子束蒸发的水平。 【关键字】溅射电子电场磁场高速 1.磁控溅射的工作原理: 电子e在电厂E的作用下在飞向基板的过程中与Ar原子发生碰撞使其电离Ar+和一个新的电子e,电子飞向基片,Ar+在电场的作用下加速飞向阴极靶,并以高能能量轰击靶表面使靶材发生溅射,在溅射粒子中,中性的靶原子或分子则由于不显电性而直接沉积在基片上形成薄膜。二次电子e一旦离开了靶面,就会同时受到电场和磁场的作用,产生E(电场)×B(磁场)所指的方向漂移,简称E×B漂移,其运动轨迹近似于一条摆线。若为环形磁场,则电子就以近似摆线形式在靶表面做圆周运动,它们的运动路径不仅很长,而且被束缚在靠近靶表面的等离子体区域内,并且在该区域中电离出大量的Ar 来轰击靶材,从而实现了高的沉积速率。随着碰撞次数的增加,二次电子的能量消耗殆尽,逐渐远离靶表面,并在电场E的作用下最终沉积在基片上。由于该电子的能量很低,传递给基片的能量很小,致使基片温升较低。 综上所述:磁控溅射是入射粒子和靶的碰撞过程。入射粒子在靶中经历复杂的散射过程,和靶原子碰撞,把部分动量传给靶原子,此靶原子又和其他靶原子碰撞,形成级联过程。
镀膜设备原理及工艺
镀膜设备原理及工艺 一.镀膜设备原理 1.磁控溅射: 磁控溅射系统在阴极靶材的背后放置100~1000Gauss强力磁铁,真空室充入011~10Pa压力的惰性气体(Ar),作为气体放电的载体。在高压作用下Ar原子电离成为Ar+离子和电子,,电子在加速飞向基片的过程中,受到垂直于电场的磁场影响,使电子产生偏转,被束缚在靠近靶表面的等离子体区域内,电子以摆线的方式沿着靶表面前进,在运动过程中不断与Ar原子发生碰撞,电离出大量的Ar+离子,经过多次碰撞后电子的能量逐渐降低,摆脱磁力线的束缚,最终落在基片、真空室内壁及靶源阳极上。而Ar+离子在高压电场加速作用下,与靶材的撞击并释放出能量,导致靶材表面的原子吸收Ar+离子的动能而脱离原晶格束缚,呈中性的靶原子逸出靶材的表面飞向基片,并在基片上沉积形成薄膜。 简单说:真空溅镀室先由高真空泵抽至一定压力之后,通过恒压仪器或质量流量计向溅镀室内充入惰性气体(如氩气)至一恒定压力(如2×10-1Pa 或 5×10-1Pa)后,在磁控阴极靶上施加一定功率的直流电源或中频电源,在正负电极高压的作用下,阴极靶前方与阳极之间的气体原子被大量电离,产生辉光放电,电离的过程使氩原子电离为Ar+离子和可以独立运动的电子,在高压电场的作用下,电子飞向阳极,而带正电荷的Ar+离子则高速飞向作为阴极的靶材,并在与靶材的撞击过程中释放出其能量,获得相当高能量的靶材原子脱离其靶材的束缚而飞向基体,于是靶材粒子沉积在靶对面的基体上形成薄膜。 溅射产额Y随入射离子能量E变化的简单示意图,简称溅射曲线。从该图可以看出溅射产额随入射离子能量的变化有如下特征:存在一个溅射阈值,阈值能量一般为20~100 eV。当入射离子的能量小于这个阈值时,没有原子被溅射出来。通常当入射离子的能量为1~10 keV时,溅射产额可以达到一个最大值。当入射离子的能量超过10 keV 时,溅射产额开始随入射离子的能量增加而下降。