莫来石的低温合成与结构研究_刘从华
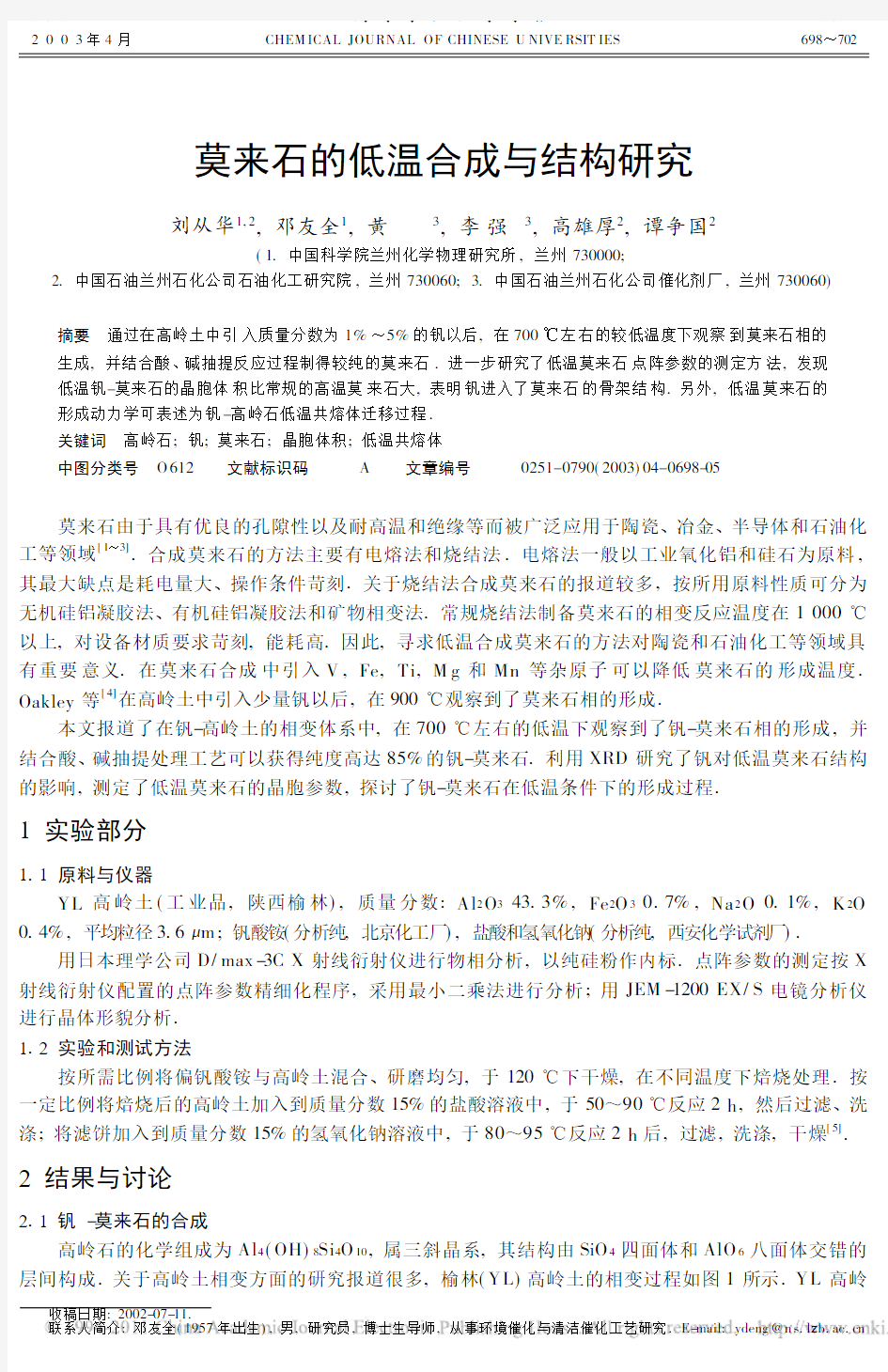

Vol.24高等学校化学学报 No.4 2003年4月 CHEM ICAL JOURNAL OF CHINESE U NIVE RSIT IES 698~702
莫来石的低温合成与结构研究
刘从华1,2,邓友全1,黄 3,李 强3,高雄厚2,谭争国2
(1.中国科学院兰州化学物理研究所,兰州730000;
2.中国石油兰州石化公司石油化工研究院,兰州730060;
3.中国石油兰州石化公司催化剂厂,兰州730060)
摘要 通过在高岭土中引入质量分数为1%~5%的钒以后,在700℃左右的较低温度下观察到莫来石相的生成,并结合酸、碱抽提反应过程制得较纯的莫来石.进一步研究了低温莫来石点阵参数的测定方法,发现低温钒-莫来石的晶胞体积比常规的高温莫来石大,表明钒进入了莫来石的骨架结构.另外,低温莫来石的形成动力学可表述为钒-高岭石低温共熔体迁移过程.
关键词 高岭石;钒;莫来石;晶胞体积;低温共熔体
中图分类号 O612 文献标识码 A 文章编号 0251-0790(2003)04-0698-05
莫来石由于具有优良的孔隙性以及耐高温和绝缘等而被广泛应用于陶瓷、冶金、半导体和石油化工等领域[1~3].合成莫来石的方法主要有电熔法和烧结法.电熔法一般以工业氧化铝和硅石为原料,其最大缺点是耗电量大、操作条件苛刻.关于烧结法合成莫来石的报道较多,按所用原料性质可分为无机硅铝凝胶法、有机硅铝凝胶法和矿物相变法.常规烧结法制备莫来石的相变反应温度在1000℃以上,对设备材质要求苛刻,能耗高.因此,寻求低温合成莫来石的方法对陶瓷和石油化工等领域具有重要意义.在莫来石合成中引入V,Fe,Ti,M g和Mn等杂原子可以降低莫来石的形成温度. Oakley等[4]在高岭土中引入少量钒以后,在900℃观察到了莫来石相的形成.
本文报道了在钒-高岭土的相变体系中,在700℃左右的低温下观察到了钒-莫来石相的形成,并结合酸、碱抽提处理工艺可以获得纯度高达85%的钒-莫来石.利用XRD研究了钒对低温莫来石结构的影响,测定了低温莫来石的晶胞参数,探讨了钒-莫来石在低温条件下的形成过程.
1 实验部分
1.1 原料与仪器
YL高岭土(工业品,陕西榆林),质量分数:Al2O343.3%,Fe2O30.7%,Na2O0.1%,K2O 0.4%,平均粒径3.6 m;钒酸铵(分析纯,北京化工厂),盐酸和氢氧化钠(分析纯,西安化学试剂厂).
用日本理学公司D/max-3C X射线衍射仪进行物相分析,以纯硅粉作内标.点阵参数的测定按X 射线衍射仪配置的点阵参数精细化程序,采用最小二乘法进行分析;用JEM-1200EX/S电镜分析仪进行晶体形貌分析.
1.2 实验和测试方法
按所需比例将偏钒酸铵与高岭土混合、研磨均匀,于120℃下干燥,在不同温度下焙烧处理.按一定比例将焙烧后的高岭土加入到质量分数15%的盐酸溶液中,于50~90℃反应2h,然后过滤、洗涤;将滤饼加入到质量分数15%的氢氧化钠溶液中,于80~95℃反应2h后,过滤,洗涤,干燥[5].
2 结果与讨论
2.1 钒-莫来石的合成
高岭石的化学组成为Al4(OH)8Si4O10,属三斜晶系,其结构由SiO4四面体和AlO6八面体交错的层间构成.关于高岭土相变方面的研究报道很多,榆林(YL)高岭土的相变过程如图1所示.YL高岭收稿日期:2002-07-11.
联系人简介:邓友全(1957年出生),男,研究员,博士生导师,从事环境催化与清洁催化工艺研究.E-mail:ydeng@n https://www.360docs.net/doc/f53873788.html,
土的原晶相部分主要是高岭石相,基本不含石英和伊梨石等杂质.经过焙烧,在600℃左右转变成偏高岭土,晶相衍射峰基本消失,表明偏高岭土以无定形状态存在.随着焙烧温度的升高,直到850~900℃,未发现有新的晶相生成.温度升至950℃时,可以看出有少量尖晶石相生成.含有外加氧化钠(质量分数约3.0%)的样品在950℃形成了少量的莫来石相.
高岭土载有不同含量的钒,于750℃焙烧2h ,XRD 物相分析表明,当钒质量分数少于0.5%时,无明显新晶相生成;当w (V)= 1.5%时,有少量新晶相生成;当钒质量分数升至3.0%~5.0%时,这种新晶相大量生成.通过与PDF 卡片15-776对比(图2谱线a ),证实这种未知新晶相为莫来石相.进一步研究表明,即使在660~700℃时,也可在钒-高岭土混合体系中观察到莫来石的生成
.
Fig .1 XRD patterns of YL kaolin calcined at diff erent
temperatures
a .Hydr o -k aolin ;
b .600℃,1h ;
c .850℃,1h ;
d .900℃,1h ;
e .950℃,1h ;
f .950℃,1h (con-
tain ing mas s fr action 3.0%Na 2O)
.Fig .2 XRD patterns of calcined kaolin through process of acid and caustic leaching a .Calcin ed kaolin [w (V )=5.0%,750℃,2h ];b .after acid leaching;c .after acid and caustic leaching.
一般通过粘土矿(如高岭土)高温转化法难以制得较纯的莫来石.这是因为,一方面,粘土的天然化学组成难以达到莫来石的组成要求,因而只能在粘土中部分形成莫来石;另一方面,粘土经过高温(>1000℃)焙烧,其中的氧化铝被彻底钝化,丧失了与酸或碱的反应活性,因此难以将莫来石从高温焙烧粘土中提纯分离.从上面的讨论可知,在钒-高岭土体系中,在660~700℃的低温下也能生成莫来石.由于在此温度下高岭土中的氧化铝被活化了,故对酸具有反应活性.同时,由于在该温度下形成了莫来石,高岭土中的氧化硅显然也得到了充分活化.在这种钒-高岭土体系中,于上述温度焙烧形成莫来石后,剩余的铝和硅同时得到充分活化,它们可分别与酸和碱发生反应而被分离出来,从而可制得较纯的莫来石,这种推测在实验中得到了证实(图2).载有钒质量分数5%的高岭土经过750℃,2h 处理形成较大量的钒-莫来石相(图2谱线a ),另外还生成了方英石(2 =21.9°).将上述样品用酸处理,莫来石相的含量有所提高(图2谱线b ),这是因为酸处理将样品中的活性氧化铝分离出去,从而提高了样品中莫来石的相对含量.继续用碱处理该样品,可明显看到样品中方英石相消失,样品中大量的活性氧化硅与碱性物质发生反应而被分离开,剩余部分则基本上都变成莫来石相,莫来石质量分数可以达到85%以上(图2谱线c ).
按本实验制备的低温莫来石(样品A )和常规硅铝凝胶法制备的高温莫来石(样品B )的SEM 形貌特征如图3所示.低温合成的莫来石晶粒呈明显的积聚状态,而高温合成的莫来石呈分散状态.
2.2 莫来石形成过程的研究
高岭土相变形成莫来石的动力学已有文献报道[6],在900~1000℃出现的尖晶石是形成莫来石的速控步骤.随着焙烧温度的升高,Si —O 和Al —O 键断裂,铝的配位数由4变成8,在1200℃左右形成莫来石.在1250~1300℃莫来石由立方构型转化为正交构型.也有文献报道[6],引入Cr 3+等离子,可以有效地降低硅铝母体的莫来石反应的活化能,但反应温度都在1000℃以上.对于V 5+离子导致的低温莫来石反应的动力学过程尚未见报道.
钒对高岭土相变过程中莫来石生成量的影响见图4.图4表明,钒含量较低时,莫来石的形成量很少;随着钒含量的增加,莫来石的生成量迅速增加;当钒质量分数达到5%时,莫来石质量分数增加至
699N o.4刘从华等:莫来石的低温合成与结构研究
Fig .3 The SEM images of mullites prepared by dif ferent methods
(A )Phase transformation of m ullite pr epared at a low temperatu re v ia acid and caustic leachin g ;
(B)phase tan sformation of s ilica-alumin a gel pr epared at a high
temperature.
Fig .4 Ef fect of mass f raction of vanadium on mullite
f ormation f rom kaolin calcined at 750℃f or 2h 20%以上.如图5所示,在750℃下焙烧10~
15min,也有大量莫来石生成.随着焙烧时间的延
长,莫来石增加并不明显,但伴随有大量方英石
(晶面衍射2 =21.9°)生成.这表明,在一定的钒
含量和焙烧温度下,高岭石的莫来石化时间大大缩
短.从前面的讨论可知,这种伴生的方英石也不同
于常规合成的方英石,它能由碱(如氢氧化钠)抽提
出来.当焙烧温度降至660℃时,也可形成莫来石
相(图6).若再降低焙烧温度,就难以在XRD 图上检测到莫来石相的生成.V 2O 5的熔点为670℃,与
含钒高岭土的低温莫来石化温度极为相近,这种现象并非偶然.另外,当高岭土中的钒质量分数降至
2.5%时,也可以观察到类似的现象,不过此时生成的莫来石量较少
.
Fig .5 XRD patterns of kaolin containing vanadium
calcined at 750℃for diff erent time
Calcinating time /h :a .1/4;b .0.5;c .1.0;d . 2.
0.Fig .6 XRD patterns of kaolin containing 5.0%vanadium at diff erent temperatures for 2h Calcinating tem prature /℃:a .540;b .660;c .700;
d .750;
e .800.
总之,有钒存在下,高岭土的莫来石化反应是一个低温熔变过程,当焙烧温度达到V 2O 5的熔点时,V 2O 5与偏高岭土形成低温共熔体,这是一个快速反应步骤.在低温共熔体中Si —O 和Al —O 键发生断裂、迁移和重组,并在局部达到莫来石的组成要求,这是相变反应的控速步骤,随后便快速形成莫来石相.在形成莫来石之前并不经过尖晶石相的形成过程,对于纯高岭土的相变,则往往伴随着尖晶石相和莫来石相的同时生成.
2.3 钒-莫来石的点阵参数
莫来石的典型晶体结构为正交晶系.在高岭石的高温相变中可以观察到立方莫来石相过渡态,随着焙烧温度的升高,立方构型转化为稳定的正交晶系构型,也有人用有机硅铝试剂合成了假四方莫来700 高等学校化学学报V ol.24
石[7].外加元素可引起莫来石a 0,b 0和c 03个晶轴的变化,但并不改变其正交晶体对称性.在实验中采用最小二乘法按下述原理测定了钒-莫来石的点阵参数.
正交晶系的点阵参数与晶面衍射指数之间的关系为
1d =h 2a 0+k 2b 0+l 2
c 0
, 2d sin = 式中h ,k 和l 为某一晶面的衍射指数,a 0,b 0和c 0为晶体的点阵参数(nm ),d 为对应于hk l 的晶面间距(nm ), 为对应于hkl 的晶面衍射角(°), 为Cu K 辐射的特征波长(0.15178nm ).选择莫来石晶相的某几组晶面衍射峰,代入相应的晶面衍射指数和晶面间距,组成联立方程组,就可获得正交晶系的点阵参数.晶胞体积(V )可由式V =a 0 b 0 c 0计算.
按照D/m ax-3C X 射线衍射仪配置的点阵参数精细化程序,选择最小二乘法分析钒-莫来石的点阵参数.直接利用PDF 卡片15-776中有关纯莫来石的衍射峰数据,考察选择不同衍射峰对莫来石晶胞参数计算结果的影响(表1).分析过程中每组选择5个衍射峰,一是受分析程序所需最小衍射峰数量的限制,最低不少于5组;二是在不影响计算结果的前提下,尽量少选以缩短分析时间.另外,还必须优选有代表性的强峰.从表1可见,衍射峰的选取对莫来石的点阵参数计算结果的影响很大.通过与PDF 卡片值对比,选择110,210,220,111,121这5组晶面衍射计算的晶胞参数与PDF 卡15-776值相当接近,因此在测定过程中以这5组强峰作为分析依据.虽然包含次强峰(120)组的分析相对误差也很小,但由于当莫来石含量较低时(质量分数小于10%),最强峰与次强峰不易分开,从而严重影响分析结果的准确性,因此舍弃.
Table 1 Ef fect of dif f raction peak selections on uint cell parameters of mullite
Selection of peak
a 0/nm
b 0/nm
c 0/nm 103V (Unit cell)/nm 3Relative deviation *(%)110,210,220,111,121
0.75510.76880.2883167.36+0.01001,210,220,111,121
0.74970.71670.2870165.10-1.34230,210,220,111,121
0.75940.77010.2892169.13+1.06120,210,220,111,121
0.75460.76870.2881167.09-0.16PDF card 15-7760.75460.76900.2884167.350.00
*C on sidering th e data in PDF 15-776is correct.
按照上述正交晶系点阵参数的测定方法,测定了含有低温钒-莫来石和高温纯莫来石的点阵参数,实验结果见表2.将钒引入莫来石后,其晶胞体积发生明显变化.随着钒质量分数从1.5%增加至5.0%,莫来石的晶胞体积不断变大.a 0轴的增幅最为明显,b 0轴略有变化,c 0轴则基本不变.由此可见,钒插入莫来石引起的膨胀过程对a 0,b 0和c 0晶轴是非线性的.钒对莫来石晶胞结构的影响主要在于a 0轴的激烈膨胀[8].这种现象在硅铝凝较法合成莫来石的加热过程中也会发生[6].Schneider [6,7,9]认为a 0以及晶胞体积的增加主要来自于铝氧八面体发生的畸变、旋转和倾斜过程,另外,铝氧四面体的畸变也不能忽略.
Table 2 Determination of several mullite ′s unit cell parameters
S am ple
w (Vanadium )(%)a 0/nm b 0/nm c 0/nm 103V (U nit cell)/nm 31#
5.00.76050.76930.2896169.432#
3.00.75920.76850.2887168.443#
1.50.75870.76720.2888168.104#
00.75460.76880.2884167.31PDF car d 15-77600.75460.76900.2884167.35
在高岭土相变过程中引入钒,大大降低了莫来石的形成温度,低温合成的莫来石的晶胞体积的膨胀方式与高温合成的有所不同.当高岭石的钒质量分数达到5%时,样品经过540℃,2h 处理,在XRD 图上看到明显存在V 2O 5晶相.当焙烧温度达到750℃时,V 2O 5已熔化成液体,并与高岭土的硅-铝化合物形成低温共熔体.同时,钒部分取代硅和铝进入所形成的莫来石骨架中,使其被钝化而失去反应活性,这极有可能是半合成裂化催化剂中,高岭土具有抗钒作用的重要原因.由于钒的常见离子(V 5+)半径比Si 4+或Al 3+的大,从而引起莫来石的晶胞体积膨胀.另外,钒在莫来石的骨架中部分占
701N o.4
刘从华等:莫来石的低温合成与结构研究
据了八面体铝位置,引起铝氧八面体的畸变.同样,硅氧、铝氧四面体也会发生类似的变化.V 2O 5在高岭土相变过程中发生了类似于“矿化剂”的作用.由于Na 2O 熔点较高,含质量分数3%Na 2O 的高岭石的莫来石化温度一般高于950℃(图1),而含有Cr 2O 3的硅铝凝胶母体,也只有在1250℃以上才能生成莫来石相,这时引入离子的矿化作用是较小的[9~11].
参 考 文 献
[1] Silverman L.D.,S peronello B.K..EP 15188[P],1985
[2] Vincent S.R..E P 134770[P],1985
[3] Yamagata M.,Ok amoto Y.,T ok ush ima K.et al ..JP 02298324[P],1990
[4] Oakley M .J .,Sharp J .H ..T ran s .J .Br .Ceram .S oc .[J ],1983,82(5):177—187
[5] LIU Cong-Hua(刘从华),PAN Zhong -Liang (潘仲良),ZHANG Yong-M ing (张永明).CN 1232803[P],1999
[6] Sch neider H..J.Am.Ceram.S oc.[J],1993,76(11):2896—2994
[7] Sch neider H..J.Am.Ceram.S oc.[J],1988,71(3):C162—C175
[8] Occelli M.L..Catal.Rev.[J],1991,33(3—4):241—280
[9] Sch neider H ..J .Eu r .Ceram .S oc .[J ],1996,16:211—220
[10] ZHEN G Jin-Yu(郑金玉),QIU Kun -Yu an (丘坤元),W EI Yen(危 岩).Chem.J.Chin es e Universities(高等学校化学学报)
[J],2000,21(4):647—649
[11] WANG Xing -Yi(王幸宜),WAN Ying(万 颖),LU Guan-Zhong(卢冠忠).Ch em.J.Chin es e U nivers ities (高等学校化学学报)
[J],2000,21(9):1470—1472
Mullite Synthesis at Low Temperature and Its Crystal
Structure Characterization
LIU Cong -Hua 1,2,DENG You-Quan 1*,HU ANG Quan 3,LI Qiang 3
,
GAO Xiong -Ho u 2,T AN Zheng-Guo 2(1.L anz hou I nstitute of Chemical Phy sics ,Chinese A cad emy of S ciences ,L anz hou 730000,China ;
2.Petr ochemical Resear ch I nstitute ,L anz hou Petr ochemical Comp any of P etr oChina ,L anz hou 730060,China ;
3.Cataly st P lant ,L anz hou Petr ochemical Comp any of P etr oChina ,L anz hou 730060,China )
Abstract Vanadium -mullite had been surprisingly observed in the phase transitio n o f kaolin in the pr esence 1%—5%v anadium at about 700℃,and quite a pure vanadium -mullite could be obtained thr oug h the pro cess of acid &base leaching reaction and separation.In addition,unit cell parameter s of various mullites were especially determ ined by XRD and the unit cell volum e of vanadium -mullite fo rmed at a low tem perature w as found to be greater than that of the co mmo n m ullite ,w hich could be deduced that v anadium incor por ated into the m ullite fr am ew or k.Furtherm ore,the r eaction process of vanadium -mullite for matio n could be expressed as low -melting v anadium-kaolin eutectic tr ansition.Keywords Kaolin ;Vanadium ;M ullite ;Unit cell volume ;Eutectic
(Ed .:V ,X )702 高等学校化学学报V ol.24
氨合成塔 (2)
氨合成塔 在高压、高温下用来使氮气和氢气发生催化反应以进行氨合成的设备。氨合成塔是合成氨厂的心脏,是一种结构复杂的反应器。 目录 ?1基本资料 ?2技术原理 ?内部换热 ?间断换热式 氨合成塔- 基本资料 在高压、高温下用来使氮气和氢气发生催化反应以进行氨合成的设备。氨合成塔是合成氨厂的心脏,是一种结构复杂的反应器。 现在工业上氨合成是在压力15.2~30.4MPa、温度400~520℃下进行的,为防止高压、高温下氢气对钢材的腐蚀,氨合成塔由耐高压的封头、外筒和装在筒体内耐高温的内件组成。内件外有保温层,操作时进塔的冷气体流过内、外筒间的环隙,从而避免外筒温度过高。这样,外筒只承受高压,可用低合金高强度钢制作。内件虽然是在高温下操作,但是只承受氨合成塔进出口的压力差,可用耐热镍铬合金钢制作。内件包括催化剂筐和换热器两个主要部分,筐内装铁催化剂,氨合成反应在此进行。从催化剂筐出来的热气体温度通常在460℃
以上,进氨合成塔的冷气体温度根据流程的不同,有的为20~30℃,有的可达140℃以上。为了使进氨合成塔的气体能加热到反应温度,同时又能冷却反应后气体,在塔内还设有换热器。换热器有列管式、螺旋板式和波纹板式,其中以列管式采用最多。氨合成催化剂在开车之前必须还原(见氨合成),还原需要提供一定的热量,为此中小型氨合成塔内部装有电加热器,大型氨合成塔则采用塔外设置开工加热炉的办法来解决。在给定的铁催化剂和压力下,氨合成温度不同,反应速度也不同。对于一定的氨含量,氨合成反应速度最大时的温度称为最佳温度,此最佳温度随着氨含量增大而降低。由于氨合成为放热反应,催化剂床层的温度将随着反应进行而不断升高。为使氨合成反应能在接近最佳温度下进行,需要采取措施移走多余的热量。工业上按传热方式区分催化剂筐的类型。[1] 氨合成塔- 技术原理 内部换热 式又称连续换热式。特点是在催化剂床层中设置 冷却管,通过冷却管进行床层内冷热气流的间接 换热,以达到调节床层温度的目的。冷却管形式 有单管、双套管和三套管之分,根据催化剂床层 和冷却管内气体流动方向的异同,又有逆流式和 并流式冷却管之分。以并流双套管式氨合成塔为 例(图1),气体从塔顶部进入,在环隙中沿塔壁
氨合成塔内件安装注意事项
氨合成塔内件安装注意事项 一、安装前的检查 1、仔细阅读合成塔外筒、内件、测温点布置等图纸。对合成塔顶部、尾部各相关尺寸,如合成塔大盖,内件小盖上部的热电偶,付线,中心管的孔距,孔径,平面布置角度,尾部填料盒高度,直径等尺寸掌握清楚。 2、按照图纸对合成塔外筒,内件的各部位尺寸进行逐一校核,发现问题做出相应的处理。 3、按照合成塔内件图纸及实物,校核热电偶外套管,内套管的尺寸。 4、按照合成塔内件图纸及实物,电炉图纸,校核电炉丝长度。 二、合成塔内件安装前的准备 1、若是自卸催化剂内件,紧固好催化剂自卸孔压板。 2、把内筒上热电偶位置标记引到吊装法兰上平面。根据合成塔小盖付线的位置,以热电偶位置为基准,在吊装法兰上标出。 3、准备好4 块斜铁,以备调正合成塔内外筒环隙以及内件中心管与大盖中心孔的同心度。 4、在合成塔外筒上封头的上平面标出热电偶及付线的位置。 5、带上合成塔内件尾部填料盒压盖,带上3-4 扣即可。(若不带上,在吊装过程中有碰坏螺纹的可能,若带满扣卸下时麻烦。) 三、合成塔内件的安装 1、合成塔内件吊入外筒后,根据外筒热电偶,付线位置和内筒 吊装法兰上热电偶,付线位置找正 2、卸下合成塔内件尾部填料盒压盖。 3、调正内外筒环隙,内外筒同心度。
4、进一步校核内件热电偶外套管,付线与合成塔外筒的位置均无误后转入下一步工作, 四、装催化剂前的准备工作 1、装0 米定位板,装热电偶外套管,以热电偶外套管为基准对0米压板进行紧固。 2、按照内件图纸把热电偶外套管上提到相应位置,并进行紧固。 3、再一次校核热电偶外套管与内件内筒的位置。 4、用白布或其它办法堵严热电偶外套管口中心管口内外筒环隙,及相应付线管口。 5、装好四段催化剂填加漏斗。 五、装填料催化剂 1、装四段填料催化剂。 2、四段催化剂装完后装上四段催化剂封堵。 3、装三段催化剂。 4、卸下0 米定位板。 5、装上部换热器。 6、装上部换热器筒体外壁与内筒内壁气体封环。 7、装0 米定位板,并按第一次装0 米定位板的方法对0 米定位板,热电偶外套管,相关付线管进行找正,紧固,并用白布或其它有效的方法对中心管,热电偶外套管,付线管,上部换热器上升管堵严。 8、装二段催化剂。 9、卸下0 米压板。
氨合成塔维护检修规程
氨合成塔维护检修规程 1氨合成塔的维护 1。1日常维护 1。1。1日常维护内容 a.严格按照操作规程进行升降压、升降温、升降电流,严禁超温、超压运行; b.调节塔的负荷、热点温度及压力时,操作不宜过猛,开关阀门应缓慢; c.严格控制各项工艺指标,循环气体成分、氢氮比、惰性气体含量、进口氨含量应控制在工艺指标规定范围内,有毒气体含量不得超过规定指标,严防触媒中毒; d.启用电加热器前,应检查电加热器和调功器的绝缘,防止电炉丝短路或绝缘太低而烧坏电炉丝; e.操作、停车或充氮期间均应检查合成塔壁温并做记录,如有疑问时应箸查,严禁塔壁超温; f.防止液氨带入合成塔而造成塔温急剧下降,导致内筒脱焊甚至严重损坏; g.定期对主螺栓和其它螺栓涂防腐油脂,并检查合成合成塔及管道保温有无损坏; h.及时消除跑、冒、滴、漏和不正常因素,暂时不能消除的又不影响安全生产的问题应挂牌示意,待停车处理; i.检查各仪表的灵敏和准确性; j.保持设备及周围环境整洁,做好文明生产; k.发现紧固件松动或爬梯、平台、护栏等设施破损及时加固、完善。 1。1.2日常巡回检查内容 a.按操作规程定时检查设备压力、温度等运行参数,并做好记录; b.每班检查一次合成塔及阀门、管道、管架等,消除跑、冒、滴、漏和振动等不正常现象,运行状态中不能处理且不影响生产和安全的问题应挂牌提示,待停车检修时处理; c.检查筒塔多层包扎是否完好各部螺栓紧固情况,发现松动及时处理;; d.检查设备各进出口管道有无震动、摩擦;平台、扶梯、栏杆是否牢固;及时清除不安全因素; e.检查保温、基础等完好情况。 1.2定期检验内容 1.2.1 外部检验,每年一次,按检测周期由压力容器检测部门完成。 1.2.2内外部检查,按检验报告的检验期及时安排计划由压力容器检测部门完成。 1。2.3 耐压试验,每两次内外部检验期内进行一次,由压力容器检测部门完成。1。2.4按仪器、仪表检验周期要求,检查、校验自动液位装置、压力、温度测量仪表。 1。2。5 非定期检验。属下列情况之一时应进行检验: a.氨合成塔在运行中发现有严重缺陷的; b.改变或修理氨合成塔的主要受压元件或主要结构的; c.停止使用一年重新使用时; d.新安装或移装的; e.对氨合成塔的安全性能有怀疑时.
新型氨合成塔内件的应用与研究总结报告
新型氨合成塔内件的应用与研究总结报告 1项目立项背景 永骏化工在原西平第一化肥厂基础上,于2003年投资扩建,2006年竣工投产,拥有年产10万吨合成氨、13.2万吨尿素,3万吨粗甲醇的能力,合成车间包括甲醇、精炼、合成、氨库、压缩等四个工段。从2006年6月投产运行至2014年5月,合成高压圈系统存在以下问题: 1、合成塔塔压差大、系统压力高,合成塔内件易出现问题且不易查明解决; 2、合成触媒使用周期短,使用效果差; 3、合成氨产量低。 2原因分析 2.1原合成塔采用湖南安淳高新技术有限公司IIIJ99-?1200内件,2006年竣工后投产使用至今,用8年多时间,已到更换周期。此内件塔压差较大,系统压力偏高,动力消耗大,影响公司经济效益,另外,调节手段单一,塔内部易出现问题,且不能有效分析查找原因,给生产带来一定难题。 2.2原塔催化剂颗粒设计不合理,反应活性差,加不上循环量,系统压力高,动力消耗高,氨合成率低,产量较低,严重影响公司经济效益。 2.3外管线根据原IIIJ99-?1200内件设计,不符合新改造内件要求。与南京国昌结合后,根据塔内件气体走向改造外管线。 3项目技术方案及实施效果 3.1合成塔内件改造 本次合成塔内件改造为南京国昌化工科技有限公司提供的GC-R112型?1200氨合成塔内件,主要工艺原理及特点如下:
3.1.1.氨合成工艺 合成氨回路是将经过造气、净化等工段制得的合格原料气中的氢气、氮气在氨合成塔内高温、高压环境和催化剂的作用下转化成氨,其化学反应可用下式表示: N 2 + 3H2 2NH 3 + 46.22 KJ/mol 反应所生成的氨经过冷却分离,可以得到 产品液氨,由于合成氨反应是可逆反应, 受转化率的限制,原料气中的氢气、氮气 不可能一次完全转化为氨,因此分离产品 液氨后所剩余的氢氮气必须用循环机进 行循环回到氨合成塔内再反应,并不断地 补充原料气(也称新鲜气),不断地分离 出产品液氨,周而复始地循环,这就是我 们通常所说的合成回路。 3.1.2轴径向氨合成塔 本回路的核心设备氨合成塔也是采用先 进的轴径向技术,由南京国昌化工科技有 限公司开发的GC-R112YZ型φ1200氨合 成塔,这种塔型具有阻力低、净值高、操 控维修方便的特点,并具有催化剂自卸功 能。合成塔由外筒和内件构成,外筒净高 16m,内件中有三层绝热型催化剂床,共
合成氨车间二氧化碳吸收塔设计毕业设计
摘要 在工业合成氨的生产过程中,粗原料气经过一氧化碳变换以后,变换气中除氢气外,还有二氧化碳和甲烷等成分,其中二氧化碳含量多达15%-35%。二氧化碳不仅降低氨合成催化剂的活性,又是制造尿素、碳酸氢铵等氮肥的原料,因此要想法除去。 本设计的目的是根据所给技术特性参数,合理设计Ι段二氧化碳吸收塔,用来脱除变换气中的二氧化碳气体。根据《GB150-1998钢制压力容器》、《JBT4710-2005钢制塔式容器》等标准,通过常规设计方法步骤进行设计,包括塔体的筒体和封头壁厚计算和水压试验,接管、接管法兰、人孔法兰和塔内件的选取,裙座的计算和设计,开孔补强计算,风载荷和地震载荷的计算和校核,以及筒体和裙座的应力分析等。强度校核时,大部分情况下将受压元件的应力限制在材料的需用应力以内,用来确保设计的安全性和经济性。 关键词:二氧化碳合成塔;填料塔;合成氨
引言 塔设备又称塔器,塔设备有许多种类型,塔设备是化工、石油化工和炼油生产中最重要的设备之一。用以使气体与液体、气体与固体、液体与液体或液体与固体密切接触,并促进其相互作用,以完成化学工业中热量传递和质量传递过程。 二氧化碳吸收塔,是利用碳酸钾溶液来脱去变换气中的二氧化碳气体,要保证较高的脱碳效率和设备的安全性能,必须对吸收塔系统进行合理的设计,包括吸收塔的尺寸设计,吸收塔材料的选择以及塔部件的选取。吸收塔的主要部件有外壳、填料、填料支承、液体分布器、中间支承和再分布器、气体、液体进出口接管等。 填料塔是以塔内的填料作为气液两相间接触构件的传质设备。填料塔的塔身是一直立式圆筒,底部装有填料支承板,填料以乱堆或整砌的方式放置在支承板上。填料的上方安装填料压板,以防被上升气流吹动。液体从塔顶经液体分布器喷淋到填料上,并沿填料表面流下。气体从塔底送入,经气体分布装置后,与液体呈逆流连续通过填料层的空隙,在填料表面上,气液两相密切接触进行传质。填料塔属于连续接触式气液传质设备,两相组成沿塔高连续变化,在正常操作状态下,气相为连续相,液相为分散相。 当液体沿填料层向下流动时,有逐渐向塔壁集中的趋势,使得塔壁附近的液流量逐渐增大,这种现象称为壁流。壁流效应造成气液两相在填料层中分布不均,从而使传质效率下降。因此,当填料层较高时,需要进行分段,中间设置再分布装置。液体再分布装置包括液体收集器和液体再分布器两部分,上层填料流下的液体经液体收集器收集后,送到液体再分布器,经重新分布后喷淋到下层填料上。 填料塔具有生产能力大,分离效率高,压降小,持液量小,操作弹性大等优点。填料塔也有一些不足之处,如填料造价高;当液体负荷较小时不能有效地润湿填料表面,使传质效率降低;不能直接用于有悬浮物或容易聚合的物料;对侧线进料和出料等复杂精馏不太适合等。塔内件是填料塔的组成部分,它与填料及塔体共同构成一个完整的填料塔。塔内件的作用是使气液在塔内更好地接触,以便发挥填料塔的最大效率和最大生产能力,因此塔内件设计的好坏直接影响填料性能的发挥和整个填料塔的性能。另外,填料塔的“放大效应”除填料本身因素外,塔内件对它的影响也很大。填料塔的内件主要有:填料支撑装置、填料压紧
磷石膏晶须制备及改性实验方案
工业磷石膏水热合成硫酸钙晶须及其改性研究实验方案 1.实验试剂: 试剂名称说明纯度 磷石膏广西鹿寨化肥厂CaSO4≥85.5% 丙三醇成都市科龙化工试剂厂分析纯 硬脂酸成都市科龙化工试剂厂分析纯 硬脂酸钠成都市科龙化工试剂厂分析纯 无水乙醇成都市科龙化工试剂厂分析纯 蒸馏水 2.实验设备及仪器: 仪器名称规格型号 反应罐、反应釜50mL;5L 电子天平ESJ205-4 台式高速冷冻离心机TGL-20M 星型球磨机QM-3SP4J 数控超声波清洗器KQ-100DE SEM XRD FT-IR XRF TG/DTA 3.实验步骤: 3.1硫酸钙晶须的制备: (一)磷石膏预处理: (1)将一定量的磷石膏原样过60目筛网; (2)将经(1)处理后的样品在50±2℃下烘干至恒重; (3)将经(2)处理的样品加入到350r/min的星型球磨机中球磨1.5h。 (4)将经(3)处理的样品,用适量的蒸馏水洗涤,磁力搅拌,静置,过滤,烘干备用。 (二)小规模(50mL)制备: (1)将2.00g预处理磷石膏、20--30mL蒸馏水、8--15mL丙三醇加入50ml的聚四氟乙烯反应罐中,用玻璃棒搅拌均匀后盖上盖子,放入140(增加一组130)℃的烘箱中,反应2 h。关闭烘箱的电源,使反应罐于烘箱中自然冷却(5至6小时)至反应罐解盖。 (2)取出反应罐,将罐中产物搅拌均匀,用玻棒取悬浊液均匀涂饰于载玻片上,自然风干制成片,于偏光显微镜下观察形貌尺寸并拍照。 (3)反应罐中的物质于5000r/min高速冷冻离心机中洗涤3次,5min/次。产物于100---140℃下干燥至恒重(约1h)。 (4)将烘干后的产物A进行形貌测试,计算晶须合成率。 (三)大规模(5L)制备: (1)将200g预处理磷石膏,2000--3000mL蒸馏水,800--1500mL丙三醇加入到5L的
GC型φ1800三轴一径氨合成塔的设计及运行总结
GC型φ1800三轴一径氨合成塔的设计及运行总结 1概述 江苏灵谷化工有限公司总部原有合成氨系统两套,一套为老合成系统(φ1000合成系列),规模为年产8万吨合成氨(于1998年10月份投产),简称老系统;另一套为新合成系统(φ1200合成系列),规模为年产12万吨合成氨(2002年4月投产),简称新系统。两套系统生产能力为20万吨合成氨。老系统(φ1000合成)设备陈旧、管路复杂、系统阻力大,尤其是触媒已严重老化(设计寿命为3年,实际已使用了5年半),严重影响了生产力,也不利于安全与节能。为进一步增加市场竞争能力,为取得经济效益的最大化和发展空间,实现我公司的战略要求,公司于2003年10月份决定在合成工段再扩建一套18万吨合成氨系统(即φ1800合成)。同时将拆除下来的φ1000合成塔、高压管道及附属设备等移至姜堰重组公司,配套了姜堰重组公司扩能技改工程。公司领导和有关技术人员经过各方调研和细致分析、论证后,确定南京国昌公司作为设计、制造“GC型φ1800三轴一径合成塔内件及系统配套设备”单位。合成塔外筒制造,选定由上海化机厂制作;所有高压管件均选定浙江工业大学设计、生产、制造,并交送现场安装;安装单位选定江苏省工业设备安装公司。 φ1800合成系统终于在2004年3月29日一次开车投运成功。投运至今已有5个多月,从运行情况及各项技经数据显示,基本达到了设计的预期效果,为本公司的健康发展奠定了基础。 2合成系统设计: 2.1设计参数及技术特性: 合成系统压力25-28Mpa 入塔气量295600Nm3/h 新鲜气量72000Nm3/h 冷却水温度34℃ 气氨总管压力0.2Mpa 氨产量25TNH3/h 合成塔阻力≤0.8Mpa 系统压差≤2.0Mpa 2.2工艺流程选择: 由透平循环机出口油分来的气体分为两股,一股约占入塔总气量30%的气体通过塔主阀送至塔上部沿合成塔环隙自上而下,约升至86℃出塔后再分为两股,一股作为冷激气直接送至塔顶作为控制径向段触媒层温度。另外还有一股与约占总气量70%的气体合并,进入加热器通过加热至180℃后的气体又分为两股,一股直接从合成塔底部入塔,通过下部换热器管层与两次出塔气换热,温度升至380℃-400℃由合成塔中心管引入触媒层。另一股作为冷激气通过f0、f1、f2调节阀分别控制塔内上面一、二、三层触媒层温度,经反应后的气体通过合成塔下部换热器壳层与两次进塔气(管程)换热后出塔,出合成塔后气体约340℃进入废热锅炉,从废热锅炉出来的气体温度约223℃进入循环换热器热气入口,换热后温度约87℃-95℃的气体进入水冷器,经冷却后的气体温度约37℃进入冷交换器管外。由水冷器、冷交中冷凝的液氨在此分离(约分离掉70%的液氨),分离后的气体再进入氨冷器,气体中氨进一步得到冷凝,然后出来的气液温度约-3℃--5℃进入氨分离器,冷凝后的液氨进一步得到分离,然后出来后的气体进入冷交换热器冷气入口,出冷交
氨合成塔内件安装方案及过程控制Word版
合成塔内件安装方案 一、内件验收: 1、确定项目负责人,项目负责人召集采购单位人员、使用单位代表、压力容器主管一起按附表一(压力容器验收控制表)进行验收。 2、验收的内容严格按附表一的内容,验收标准:图纸、GB150、GB151、《压力容器安全技术监察规程》。 3、附表一在验收完毕后,应和压力容器档案一起存档,备查。 二、内件的存放、转运严格按图纸的要求进行支撑和拴挂以防筒体变形。 三、内件安装: 1、内件的安装应编制合成塔内件安装过程控制表,附表二是一米合成塔两轴一径内件的表格,同类型的内件直接按附表二执行,其他类型的参照附表二编制,编制的过程控制表应经设备部长审核、生产副总审批。 2、内件的安装过程严格按合成塔内件安装过程控制表进行,由项目负责人负责,记录由项目负责人或项目负责人指定专人负责,每一工序必须经过验收合格后方可进行下一工序,记录完毕后存档,备查。 3、为防止内件变形接触塔壁,新内件在中部环向焊接4-6个钢珠,钢珠直径为外筒与内筒外壁的平均环隙减去5㎜,旧内件也在中部选择直线度偏差最大处焊接钢珠,钢珠数量和分布视具体情况而定,钢珠直径与新内件一样,焊接钢珠后,其所对应部位的保温皮应挖长圆孔,长圆孔应在钢珠对应下部留有30—40㎜,以方便内件温度上升后内件和保温皮的相对热位移。 4、环隙检查;用4㎜厚的扁钢条同使用塞尺一样检查环隙,扁钢条的长度应超过外筒体内部深度的2/3,扁钢条的插入深度应超过外筒体内部深度的一半。 四、触媒升温还原: 1、触媒升温还原应编制方案,由项目负责人负责编制,生产部长审核,生产副总审批,审批合格的方案方可用于执行。附表三为触媒升温还原方案样本。 2、触媒升温还原过程应严格按方案执行,出现异常情况,须修订方案的,必须经生产副总批准。触媒升温还原过程记录应存档,备查。 3、升、降温速率和升降压速率严格按操作规程的要求执行。 附:合成内件验收、内件安装以及触媒升温还原表格
莫来石晶须改善耐火材料
无机材料测试技术 班级:09材料无非(5)班 姓名:潘俊阳 学号:200910210510 实验名称:原位合成莫来石晶须改善耐火材料指导教师:顾幸勇 景德镇陶瓷学院
1 前言 耐火材料一般是由多种不同的化学成分和矿物组成的非均质体。它的各种性质不仅取决于它的化学成分,而且更依赖于其中的化学组成,分布及各相的特性,即取决于制品的化学,矿物组成与结构。目前,我国耐热材料的生产与管理都不是很完善,尤其在原料的加工,合成及材质的选择等方面存在很大的缺陷,导致生产出来的产品不能满足节能降耗的标准。随着现代陶瓷行业的快速发展,特别是建筑陶瓷行业的蓬勃发展给耐火材料的要求有了更高的要求,从而促使了耐火材料的发展,因此,如何在耐热材料的加工、合成和选择上满足现代技术性能的要求,怎样提高耐火材料的使用性能以适应陶瓷行业的发展,是一个急需解决的问题。 2 文献综述 2.1 耐火材料的概述 耐火材料通常是指能耐1580℃以上温度的无机物材料。它们是修建窑炉、燃烧室和其他需耐高温的建筑材料。可抑制高温物体和低温物体的热辐射和传导热,对于高温物体可以保持70%的热量不损失。 2.2 耐火材料的作用 耐火材料的用途十分广泛,涉及到的行业也十分的多。我们熟知的陶瓷行业,机械、冶金、化工、电子、航空航天、国防等众多工业领域,例如刚玉质耐火材料,由于有耐高温,耐腐蚀,高强度等特性,故用作冶炼希贵金属,特种合金,玻璃拉丝,制作激光玻璃的坩埚及器皿;各种高温炉窑,如窑炉的内衬。又如莫来石质的耐火材料,由于其制品有优良的抗高温蠕变性能和耐酸碱,抗熔渣等性能广泛用于冶金工业的热风炉,建材玻璃窑焰顶,蓄热室,加热炉等窑具。2.3 耐火材料的种类 根据耐火材料的矿物组成与化学组成,将耐火材料分为以下几种 2.3.1 Al2O3—SiO2系耐火原料 (1)硅质和半硅质耐火原料 硅质,半硅质耐火原料是指以SiO2为主成分的天然矿物或人工合成原料,通常硅质原料的含量大于96%,如硅石,石英砂,脉石英,水晶和熔融石英等;半硅质耐火原料中的SiO2含量大于65%,如叶腊石,硅藻土,硅微粉等。(2)黏土质耐火原料 黏土是自然界中硅酸盐类岩石,如长石,微晶花岗岩,斑岩,片麻岩等经
ⅢJD2000型-φ2200氨合成塔
概述 湖南安淳高新技术有限公司(以下简称安淳公司)从上世纪80年代起,在分析了国际国内氨合成塔内件优缺点的基础上,独创了ⅢJ型氨合成塔内件,取得了国家专利,是国内数种氨合成塔内件中唯一经原化工部鉴定的内件,鉴定结论是,该内件为国内首创,主要技术指标取得突破性进展,达到国际先进水平。安淳公司不断创新、不断进取,随后又推出了ⅢJ99型氨合成内件,包含3个新的国家专利技术。ⅢJ型、ⅢJ99型氨合成内件经由φ800、φ1000到φ1200;后又开发了ⅢJD2000型φ1400、φ1600、φ1800、φ2000氨合成内件。单塔年产氨能力由20 kt(φ600塔)发展到180 kt、200 kt。近几年开发的ⅢJD2000型-φ2200氨合成塔,在技术上又有较大的提升;单塔生产能力日均达850~910 t,受到了用户的青睐。 2 ⅢJD2000型-φ2200氨合成塔的设计思想 为实现单系统生产能力规模化和进一步降低能耗,安淳公司在ⅢJD2000型-φ1800、φ2000氨合成内件的基础上,引入新的理念,设计了ⅢJD2000型-φ2200氨合成内件,具体如下。 (1)充分发挥第一绝热层的作用。进入零米未反应气氨含量低,距离反应平衡很远,反应速度很快,尽量在开始反应的第一层多产氨,使第一层之氨净值达到8%~9%,即第一绝热层温升110~133 ℃。具体措施如下。 ①增加第一绝热层的高度,第一绝热层设计高度2.5~3.1 m。 ②降低零米温度,提高热点温度。进第一绝热层零米点的循环气,氨含量最低(约2.16%),温度低(370~380 ℃),离反应平衡点最远;如零米温度为380 ℃,将第一绝热层反应终点温度设计为490~513 ℃,则第一绝热层的氨含量增加8%~9%(氨净值),即第一绝热层完成氨合成反应的50%。 (2)第一层绝热反应后的热气体,不再采取冷激,而是用塔内换热器间接冷却后再进入第二层,这样更有利于氨合成反应温度接近最适宜温度曲线。 (3)冷管束(段间冷却器)的气体出口设在催化剂床层表面,使进塔气体100%地通过第一层催化剂,有利于降低零米温度,提高氨净值。 (4)分流气占到近50%,使通过中心管和换热器的气体由原来的65%~70%减少至50%,降低塔阻力。 (5)提高出塔温度。设计最高出塔温度为380 ℃,产生3.0~4.0 MPa过热蒸汽,使回收蒸汽的利用价值更高。 (6)大幅度提高出塔氨含量。 3 ⅢJD2000型-φ2200氨合成塔的结构特点
绿色莫来石晶须骨架多孔陶瓷的制备与性能
绿色莫来石晶须骨架多孔陶瓷的制备与性能建筑废弃物排放量大,资源化利用率低,其大量堆积、填埋不仅挤占良田,污染水土资源、空气环境,甚至会造成严重的二次灾害。建筑废弃物主要化学成分是SiO2、Al2O3、CaO等,属于有用矿产资源。 莫来石是大气压下Al2O3-SiO2系中稳定的化合物,以此为基体的多孔陶瓷具有密度低、导热系数小、抗热震性好、热膨胀系数低、高温力学性能好、耐腐蚀等优点,广泛用于隔热、过滤、吸音、催化剂载体等领域。但是,其作为多孔材料,不可避免孔隙率高而机械强度低的缺点,且其传统制备原料主要源于高岭土等不可再生资源。 因此,本文以建筑废弃物的精细化利用、莫来石多孔陶瓷的制备、原位晶须增强多孔陶瓷为契机,利用建筑废弃物低温制备莫来石晶须骨架多孔陶瓷,详细研究工艺、配方、结构、性能之间的关系,并探讨相关的机理。本文首先研究了建筑废弃物的物理化学性质和莫来石晶须的烧成过程与机理。 采用红外光谱分析、热重分析、硅酸盐快速测定、晶相分析等手段,研究了建筑废弃物主要化学成分为SiO2、Al2O3和CaO。然后,以其为主要原料,氧化铝做补充铝源(按莫来石经典组成 3Al2O3.2SiO2配比),综合采用莫来石晶须生成工艺中的气相法和氧化物掺杂法,制备原位莫来石晶须增强的晶须骨架多孔陶瓷。 详细研究烧成温度、保温时间、升温速率、成型压力、球磨时间等工艺参数对烧结样品晶相组成、断面微观结构、吸水率、开口孔隙率、孔径分布、体积密
粉煤灰制备托贝莫来石晶须工艺及其机理
粉煤灰制备托贝莫来石晶须工艺及其机理 托贝莫来石型硅酸钙材料具有市场容量大、强度高、导热系数低、容重低等突出优势,在建筑外墙、工业炉窑等重要节能领域应用前景广阔。粉煤灰是我国主要固体废弃物之一,粉煤灰的大量堆积,给我国造成了严重的社会问题和环境 问题。 本研究以开发粉煤灰量大面广综合利用途径为出发点,并结合我国节能减排的重大需求,提出以粉煤灰为硅质原料采用动态水热法合成托贝莫来石晶体的新方法,重点研究粉煤灰合成托贝莫来石晶须的新工艺及反应机理。论文取得的主要创新性进展如下:(1)探索并优化了以粉煤灰作为硅质原料制备托贝莫来石晶须的新工艺,获得了最佳的工艺条件:Ca/(Al+Si)摩尔比1.0,反应时间5h,反应温度220℃,液固比30mL/g,搅拌强度为200~400rpm。 在最佳条件下合成的托贝莫来石为晶须相互缠绕而成的球形二次粒子。(2)深入研究了机械活化对提高粉煤灰反应活性的影响机制。 研究结果显示,机械活化作用后,粉煤灰比表面积大幅提高,反应活性点大幅增加,极大地提高了粉煤灰的反应活性,使合成的托贝莫来石晶型更加完整,晶须长径比变大,晶须相互缠绕形成的球形二次粒子表面更加光滑,二次粒子累计孔 体积显著增大,这些变化非常有利于托贝莫来石制品绝热保温性能和强度的提高。 (3)明晰了粉煤灰合成托贝莫来石的反应机理。 在反应过程中,粉煤灰表面活性Si02优先和Ca(OH)2反应,生成C-S-H凝胶,同时在溶液中OH-的作用下,粉煤灰表面非活性Si02不断被活化,参与与Ca(OH)2反应;生长在粉煤灰表面的这些凝胶,在特定反应体系下,不断晶化、纤维化,并进而相互缠绕成球形二次粒子;粉煤灰中的A1由于与Si性质相似,可部分取代
硅酸钠溶液合成托贝莫来石晶须
梁振华等:低温热压制备半透明α/β Si3N4复相陶瓷? 1721 ?第40卷第12期 硅酸钠溶液合成托贝莫来石晶须 李光辉,张吉清,罗骏,陈浩远,曾精华,姜涛 (中南大学资源加工与生物工程学院,长沙 410000) 摘要:以硅酸钠为硅质原料,研究了动态水热法合成托贝莫来石的条件及其对产物纯度和形貌的影响。结果表明:硅酸钠和石灰乳直接反应合成的产物主要为针钠钙石;而在苛性碱溶液中反应时,针钠钙石向生成托贝莫来石的方向转化,随苛性碱浓度提高,托贝莫来石生成量增加;加入铝离子且其含量达到钙铝摩尔比为5时,可获得纯的1.1nm托贝莫来石;溶液中的氯离子可促进晶须生长,当钙氯摩尔比为5时,托贝莫来石晶须的长度为2~13μm,直径为0.2~0.5μm。在优化的合成条件下,以实际含硅碱液为原料,合成出长度为2~10μm、直径为0.2~1.0μm的托贝莫来石晶须。在合成托贝莫来石过程中,苛性碱改变了水化硅酸钙的生成环境,铝离子使硅氧四面体双链无法形成而得到四面体单链,最终合成出纯的1.1nm托贝莫来石;而氯离子所产生的盐效应促进了托贝莫来石结晶长大,有助于制备组分单一、结晶晶面完整的托贝莫来石晶须。 关键词:硅酸钠;托贝莫来石;晶须;水热合成法 中图分类号:TB3221;X751 文献标志码:文章编号:0454–5648(2012)12–1721–07 网络出版时间:2012–11–29 10:09:55 网络出版地址:https://www.360docs.net/doc/f53873788.html,/kcms/detail/11.2310.TQ.20121129.1009.201212.1721_012.html Preparation of Tobermorite Whisker from Sodium Silicate Solution LI Guanghui,ZHANG Jiqing,LUO Jun,CHEN Haoyuan,ZENG Jinghua,JIANG Tao (School of Minerals Processing & Bioengineering, Central South University, Changsha 410000, China) Abstract: Tobermorite was synthesized with sodium silicate solution as silicous material by dynamic hydrothermal synthesis method. The effect of synthesis conditions on the purity and morphology of tobermorite was investigated. The main phase of the product syn-thesized from sodium silicate and lime milk was pectolite. In the presence of caustic soda, pectolite was converted partly into clinoto-bermorite. And the amount of clinotobermorite increased with the increasing of caustic soda concentration. Pure 1.1nm tobermorite was obtained when aluminum ion was added at a calcium/aluminum mole ratio of 5. The growth of tobermorite whisker was en-hanced by the presence of chlorine ion in the solution. At a calcium/chlorine molar ratio of 5, the tobermorite whiskers obtained were 2–13μm in length and 0.2–0.5μm in diameter. With a practical sodium silicate solution containing alkali and aluminum as the mate-rial, tobermorite whiskers with 2–10μm in length and 0.2–1.0μm in diameter was synthesized under the optimal synthesis condition. In the synthesis of tobermorite, the reaction environment for the formation of hydrated calcium silicate was changed by the caustic soda solution. The bonding of the bridging tetrahedral sheets in the structure of tobermorite was restrained by aluminum ions, result-ing in the formation of pure 1.1nm tobermorite with single tetrahedralsheet structure. The salt-effect of the solution resulted from the addition of chlorine ion enhance the whisker growth of tobermorite. Key words: sodium silicate; tobermorite; whisker; hydrothermal synthesis 托贝莫来石(5CaO·6SiO2·5H2O)是硅酸钙水化物中的一种。由于脱水温度高,热稳定性好,以托贝莫来石为主要成分的水化硅酸钙保温材料已在建筑、石化等领域中获得广泛应用[1]。在生物材料领域,托贝莫来石纳米线因具有快速诱导沉积类骨羟基磷灰石的能力,并具有良好吸附蛋白和细胞的功能,可提高骨形成能力,促进骨修复进程,有望用作骨修复材料[2]。 托贝莫来石为层状结构,各层均由硅氧四面体所形成的三元链重复排列而得到。根据层与层之间的排列方式和层间距的不同,托贝莫来石可分为单斜托贝莫来石、0.9nm托贝莫来石、1.1nm托贝莫来石和1.4nm托贝莫来石4种类型[3]。单斜托贝莫来石和1.1nm托贝莫来石在结构上具有相似性,而 收稿日期:2012–06–22。修订日期:2012–09–11。 基金项目:国家自然科学基金(51174230,51234008)资助项目。第一作者:李光辉(1972—),男,博士,教授。Received date:2012–06–22. Revised date: 2012–09–11. First author: LI Guanghui (1972–), male, Ph.D., Professor. E-mail: liguangh@https://www.360docs.net/doc/f53873788.html, 第40卷第12期2012年12月 硅酸盐学报 JOURNAL OF THE CHINESE CERAMIC SOCIETY Vol. 40,No. 12 December,2012
DN1600多层直接冷激式氨合成塔结构设计
1绪论 现今氨合成工艺在我国氮肥厂得到广泛的应用。展望国内氨合成塔内件可以说种类繁多,绝大多数的氨厂合成操作压力为31.36MP&合成塔内件为传统的冷管型内件。其中三套管、单根并流、双套管式内件占大多数。此外,另有一批冷管改进型内件:比如川J型、YD型、NC型、轴径向、副产蒸汽式等。塔内换热器大部分为列管式,还有少数为螺旋式、波纹板式。小型氨厂大部分采用? 600、? 800直径塔。日产合成氨达80t、100t、150t不等。中型氨厂大多采用? 1000、? 1200直径塔。高压筒体高度为13.5?16m日产氨200t、250t、290t不等。传统型内件氨净值大部分为9%?12%之间,改进型内件在12%?16%之间。合成塔阻力降0.6?1.2MP&配置的余热回收装作吨氨副产蒸汽为600?800kg/t NH 3, 压力为1.3?2.5MP& 下面简单介绍两种内件: 全冷激式内件全冷激式内件是一种在中小型氨厂推广使用的新型内件,它与传统内件(内冷式内件)有本质区别,将圆催化剂中的冷管取消,将一个大的催化剂反应床分割为若干个小的催化剂反应床,床层之间采取冷激换热的方式将反应热一直,以便将反应能继续进行下去。冷激式内件是多层绝热、层间换热式内件中最简单的一种。它与层间水冷式内件几乎同时应用与多种合成氨厂。它具有结构简单,运行可靠的特点。此种内件根据合成系统工作压力、催化剂活性温度、催化剂温区范围、反应热回收方式等因素以及要达到的氨净值来确定催化剂床的数量。 多层换热式内件具有三大特点: (1)多层绝热,层间换热。用未反应的气体作为冷源,一方面将反应后的热气体热量移走;另一方面自身温度提高达到第一绝热床时的零米温度。 (2)催化剂筐采用径向型 (3)宽温区催化剂 对于整台合成塔,需设计和制造外壳,所设计的外壳具有一下特点: (1)球形封头结构成熟,使用材料较省,若采用锻件,则将增加一倍以上的重 量。 (2)多层包扎筒体国内制造经验丰富。成熟可靠,材料也易于解决,设备安全
氨合成塔吊装方案样本
天脊中化高平40-60工程 氨合成塔内件吊装方案 编制: 审核: 批准: 中化二建集团40-60项目部 .11.4 目录
一、编制说明 二、编制依据 三、工程概述 四、准备工作 五、吊装方法 六、受力计算及索具配置 七、合成塔吊装梁强度校核 八、施工技术要求 九、安全技术措施 十、劳动力计划 十一、施工机具、手段用料计划十二、附图 1、编制说明
天脊中化高平40-60工程是一个年产40万吨氨醇60万吨尿素的大项目, 其中氨合成塔的内件以及多余能量收集器是由瑞士CASALE公司制造提供( 三床换热式轴径向氨合成塔内件) , 氨合成装置为双系列设计, 氨合成塔是氨合成装置的主要核心设备, 设备重量大且放至于氨合成框架内, 吊装难度大, 为安全的吊装好两台氨合成塔特编制此方案。 2、编制依据 2.1、《化工工程建设起重施工规范》HGJ201-83 2.2、天脊中化高平40-60氨合成装置区平面图 2.3、天脊中化高平40-60氨合成框架图 2.4、天脊中化高平40-60氨合成设备图 2.5、《石油化工吊装工作手册》 2.6、《起重机械与吊装》 3、工程概况 氨合成塔是氨合成工段氨合成框架内的主要设备, 其详细技术参数如下: 设备吊装拟采用绑扎双吊点滑移法。氨合成塔是氨合成工段的核心设备, 也是最重的一台设备。根据土建设计的框架结构, 将在39m的主梁处增加两根钢梁做为吊装梁。 4、吊装前应具备条件 4.1施工场地平整, 道路畅通。 4.2临时电源已接通, 并能保证连续供应。 4.3设备基础梁已按设计要求预制完毕, 并经相关单位验收合格。 4.4设备经验收合格, 并办理完相关交接出库手续。 4.5 施工方案已经有关部门批准, 技术交底已进行。 4.6 起吊用机索具已按要求配备好, 并有合格证明。如无合格证明者, 须经有关部门检验合格后方可使用。对检验中发现的问题必须得妥当解决, 并有见证资料。 4.7吊装钢梁已制作安装完毕, 并经检查确认安全可靠。
合成氨毕业设计doc
合成氨毕业设计 篇一:合成氨本科毕业设计 摘要 合成氨生产任务设计决定了生产合成氨的规模,设备的要求以及工艺流程的状况。本设计所采用的方法是半水煤气合成法,其主要原料是煤和氮气,利用煤来生成氢气,第一步是造气,即制备含有氢、氮的原料气;第二步是净化,不论选择什么原料,用什么方法造气,都必须对原料气进行净化处理,以除去氢、氮以外的杂质;第三步是压缩和合成,将纯净的氢、氮混合压缩到高压,在铁催化剂与高温条件下合成为氨。 目前氨合成的方法,由于采用的压力、温度和催化剂种类的不同,一般可分为低压法、中压法和高压法三种。本设计主要是对合成塔工段的设计,故所用原料直接采用氮气和氢气,其以合成塔为主要设备,在氨冷器、水冷器、气—气交换器、循环机、分离器、冷凝塔等辅助设备的作用下,以四氧化三铁为触媒,在485—500℃的高温高压条件下来制得氨气。 本设计要求要掌握合成塔的工作原理,生产的工艺路线,并能根据工艺指标进行操作计算。在工艺计算过程中,包含物料衡算,热量衡算及设备选型计算等,在合成效率方面也有进一步研究。
关键词:氮气;氢气;四氧化三铁催化剂;氨合成塔 Abstract Ammonia production design determines the size of the production of synthetic ammonia, equipment requirements, as well as the status process. The design of the method used was semi-water gas synthesis, the main raw material is coal and nitrogen, the use of coal to generate hydrogen, while the design is a synthesis of the main section of the tower design, it is the direct use of raw materials used in nitrogen and hydrogen, its synthesis tower as the main equipment, in the ammonia cooler, water coolers, gas - gas exchange, recycling machines, separators, auxiliary equipment, such as condensation of the tower under the four iron oxide catalyst, in the high-temperature conditions of 485-500 ℃ obtained from ammonia. The first step is to build gas, Preparation that contains hydrogen, nitrogen gas; second step is purification, regardless of what materials, what methods of gas must be carried out on the feed gas purification to remove hydrogen and
氨合成塔
氨合成塔 氨合成塔,是在高压、高温下用来使氮气和氢气发生催化反应以进行氨合成的设备。氨合成塔是合成氨厂的心脏,是一种结构复杂的反应器。现在工业上氨合成是内件外有保温层,操作时进塔的冷气体流过内、外筒间的环隙,从而避免外筒温度过高。这样,外筒只承受高压,可用低合金高强度钢制作。内件虽然是在高温下操作,但是只承受氨合成塔进出口的压力差,可用耐热镍铬合金钢制作。 ?1简介 ?2详细 ?3分类 ?4其他介绍 ?5工艺流程 ?6反应催化剂 1简介 氨合成塔(ammonia synthesis converter )是在高压、高温下用来使氮气和氢气发生催化反应进行氨合成的设备。氨合成塔是合成氨厂的心脏,是种结构 复杂的反应器。现在工业上氨合成是在压力 15.2~30.4MPa、温 度 400~520℃下进行的,为防止高压、高温下氢气对钢的腐蚀,氨合成塔由耐高压的封头、外筒和装在筒体耐高温的内件组成。 2详细
现在工业上氨合成是内件外有保温层,操作时进塔的冷气体流过内、外筒间的环隙,从而避免外筒温度过高。这样,外筒只承受高压,可用低合金高强度钢 制作。内件虽然是在高温下操作,但是只承受氨合成塔进出口的压力差,可用耐热镍铬合金钢制作。内件包括催化剂筐和换热器两个主要部分,筐内装铁催化剂,氨合成反应在此进行。从催化剂筐出来的热气体温度通常在460℃以上,进氨合成塔的冷气体温度根据流程的不同,有的为20~30℃,有的可达140℃以上。为了使进氨合成塔的气体能加热到反应温度,同时又能冷却反应后气体,在塔内还设有换热器。换热器有列管式、螺旋板式和波纹板式,其中以列管式采用最多。氨合成催化剂在开车之前必须还原(见氨合成),还原需要提供一定的热量,为此中小型氨合成塔内部装有电加热器,大型氨合成塔则采用塔外设置开工加热炉的办法来解决。在给定的铁催化剂和压力下,氨合成温度不同,反应速度也不同。对于一定的氨含量,氨合成反应速度最大时的温度称为最佳温度,此最佳温度随着氨含量增大而降低。由于氨合成为放热反应,催化剂床层的温度将随着反应进行而不断升高。为使氨合成反应能在接近最佳温度下进行,需要采取措施移走多余的热量。工业上按传热方式区分催化剂筐的类型。 3分类 内部换热式:又称连续换热式。特点是在催化剂床层中设置冷却管,通过冷却管进行床层内冷热气流的间接换热,以达到调节床层温度的目的。 冷却管形式有单管、双套管和三套管之分,根据催化剂床层 和冷却管内气体流动方向的异同,又有逆流式和并流式冷却管之分。以并流双套管式氨合成塔为例,气体从塔顶部进入,在环隙中沿塔壁而下,经换热器壳程后到分气盒,分散到各双套管的内冷却管,到管顶折至外冷却管,气体被预热到铁催化剂的活性温度(通常为400℃左右),再流经设有电加热器的中心管。从上而下通过催化剂床层,氮气和氢气在此反应后,出催化剂筐,通过换热器管程降低