疲劳可靠性

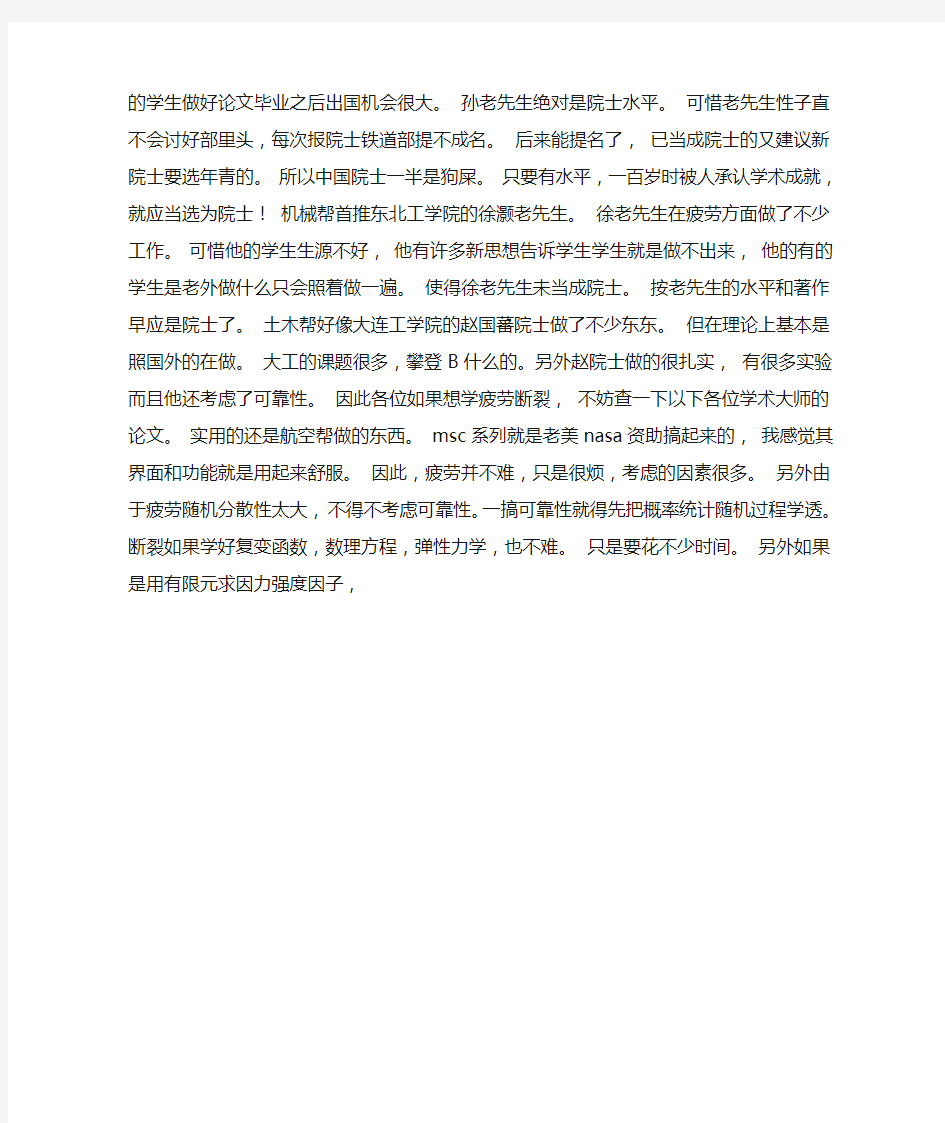
机械
机械构件的疲劳强度或疲劳寿命受众多因素的影响,如材料本质(如化学成分、金相组织、纤维方向、内部缺陷分布)、工作条件(如载荷特性、加载频率、服役温度、环境介质)、零件状态(如应力集中、尺寸效应、表面加工)等[1]。其中,最为复杂的是应力集中、表面加工和尺寸效应这三方面因素的影响。
关于应力集中、表面质量和尺寸因素各自对试样疲劳寿命或疲劳强度的影响,已有大量的研究[1飊5]。对于在疲劳设计中如何考虑这些因素的影响见文献[4],文献[5]则在此基础上考虑了各因素的分散性。目前考虑各因素对机械零件疲劳强度或疲劳寿命的影响,疲劳断裂的前提是结构应力分析,因此有限元求应力是第一步!目前疲劳断裂国内分成力学帮,航空帮,机械帮,和土木帮。力学帮主要在求三维断裂,以西交大的匡振邦,清华的杨卫为主。但他们的研究的大多是静态加载,没考虑循环加载,无法进行结构的寿命估算。航空帮又分疲劳帮和断裂帮。航空疲劳帮以北航的高镇同为主,主要是疲劳可靠性和雨流法。如果不考虑可靠性,很简单了,考虑了可靠性,由于以前的老家伙没几个懂概率统计,所以全被老高头蒙得一愣一愣的(笑)。其实西工大的吴富民教授水平很高,他的疲劳书比老高头的好。航空断裂帮以前是西工大的黄玉珊(黄神童),后来是北航的张行。主要是求飞机结构的应力强度因子。后来又搞了损伤容限与耐久性设计。这个很蒙人,没一两年时间你学不会。因为首先要学懂断裂力学,然后实际搞的是裂纹扩展。黄神童当年自
做聪明,70年在国内第一个搞断裂力学,(当时清华的黄克智还在算什么波纹板应力分析呢,可现在成了断裂帮总舵主)。黄玉珊认为疲劳比断裂简单多了,所以向航空部建议北航成立疲劳小组,西工大成立断裂小组。可惜黄是江浙人,喜欢单干,后又得了病早逝。加上我国的飞机一直以修修补补为主,使得航空疲劳帮一直有科研课题,有课题就自然会得奖,奖多了就会当院士。与黄玉珊同时搞断裂的是西南交大的孙训方先生。孙老先生水平很高,学生出国的很多。他经常出国开会发现什么是热门就让学生做,因此他的学生做好论文毕业之后出国机会很大。孙老先生绝对是院士水平。可惜老先生性子直不会讨好部里头,每次报院士铁道部提不成名。后来能提名了,已当成院士的又建议新院士要选年青的。所以中国院士一半是狗屎。只要有水平,一百岁时被人承认学术成就,就应当选为院士!机械帮首推东北工学院的徐灏老先生。徐老先生在疲劳方面做了不少工作。可惜他的学生生源不好,他有许多新思想告诉学生学生就是做不出来,他的有的学生是老外做什么只会照着做一遍。使得徐老先生未当成院士。按老先生的水平和著作早应是院士了。土木帮好像大连工学院的赵国蕃院士做了不少东东。但在理论上基本是照国外的在做。大工的课题很多,攀登B什么的。另外赵院士做的很扎实,有很多实验而且他还考虑了可靠性。因此各位如果想学疲劳断裂,不妨查一下以下各位学术大师的论文。实用的还是航空帮做的东西。 msc系列就是老美nasa资助搞起来的,我感觉其界面和功能就是用起来舒服。因此,疲劳并不难,只是很烦,考虑
的因素很多。另外由于疲劳随机分散性太大,不得不考虑可靠性。一搞可靠性就得先把概率统计随机过程学透。断裂如果学好复变函数,数理方程,弹性力学,也不难。只是要花不少时间。另外如果是用有限元求因力强度因子,
疲劳试验简介
疲劳试验(fatigue test)利用金属试样或模拟机件在各种环境下,经受交变载荷循环作用而测定其疲劳性能判据,并研究其断裂过程的试验,即为金属疲劳试验。 1829年德国人阿尔贝特(J.Albert)为解决矿山卷扬机服役过程中钢索经常发生突然断裂,首先以10次/分的频率进行疲劳试验。1852~1869年德国人沃勒(A.W hler)为研究机车车辆,开始以15次/分的频率对车辆部件进行拉伸疲劳试验,以后又用试样以72次/分的频率在旋转弯曲疲劳试验机进行旋转弯曲疲劳试验,他的功绩是指出一些金属存在疲劳极限,并将疲劳试验结果绘成应力与循环周次关系的S-N曲线(图1),又称为W hler曲线。1849年英国人古德曼(J.Goodman)首先考虑了平均应力不为零时非对称载荷下的疲劳问题,并提出耐久图,为金属制件的寿命估算和安全可靠服役奠定理论基础。1946年德国人魏布尔(W.Weibull)对大量疲劳试验数据进行统计分析研究,提出对数疲劳寿命一般符合正态分布(高斯分布),阐明疲劳测试技术中应采用数理统计。 60年代初,从断裂力学观点分析金属疲劳问题,进一步扩大了疲劳研究内容。近年来,由于电液伺服闭环控制疲劳试验机的出现以及近代无损检验技术、现代化仪器仪表等新技术的采用,促进了金属疲劳测试技术的发展。今后应着重各种不同条件(特别是接近服役条件)下金属及其制件的疲劳测试技术的研究。 试验种类和判据 金属疲劳试验种类很多,通常可分为高周疲劳、低周疲劳、热疲劳、冲击疲劳、腐蚀疲劳、接触疲劳、声致疲劳、真空疲劳、高温疲劳、常温疲劳、低温疲劳、旋转弯曲疲劳、平面弯曲疲劳、轴向加载疲劳、扭转疲劳、复合应力疲劳等。应根据金属制件的服役(工作)条件来选择适宜的疲劳试验方法,测试条件要尽量接近服役条件。进行金属疲劳试验的目的在于测定金属的疲劳强度(抗力),由于试验条件不同,表征金属疲劳强度的判据(指标)也不一样。 高周疲劳:高周疲劳时,金属疲劳强度判据是疲劳极限(或条件疲劳极限)即金属经受“无限”多次(或规定周次)应力循环而不断裂的最大应力,以σr表示,其中γ为应力比,即循环中
机械结构抗疲劳与可靠性分析
机械结构抗疲劳与可靠性分析 发表时间:2019-04-18T15:51:40.703Z 来源:《基层建设》2019年第6期作者:秦俊沛 [导读] 摘要:在机械结构运行过程中,疲劳破坏现象是影响机械运行的主要因素之一。 广州广电计量检测股份有限公司广东省广州市 510000 摘要:在机械结构运行过程中,疲劳破坏现象是影响机械运行的主要因素之一。疲劳破坏过程复杂多样,常发生在机械设备某些隐蔽处且易断裂、易磨损的部位,通过局部的损伤来影响整个机械结构的正常运行。因此怎样增强疲劳寿命与结构的可靠性一直是机械产品设计研究中的热点内容,也是企业提高生产质量与经济效益的关键。本文主要论述对机械结构抗疲劳的方法与分析影响结构可靠性的原因。 关键词:机械疲劳;结构可靠性;交变应力 引言 大多数机械结构中,疲劳破坏现象发生主要因为物体受到力或方向周期性变化的交变载荷作用。长期以来,机械疲劳时刻影响着企业的生产技术与质量。随着机械设备智能、精准的发展方向,通过对机械结构可靠性的分析来增加疲劳寿命,从根本上解决因疲劳破坏给结构造成的损伤,并对机械结构疲劳方面做出安全评估。 1.分析机械结构疲劳与抗疲劳 1.1机械结构疲劳的概述 疲劳是机械设备受到循环交变载荷作用下,材料局部逐渐产生永久性累积断裂、磨损、腐蚀等损伤的过程。在材料设备受到循环应变与应力不断变化的载荷作用时,应力值虽然在材料的极限强度范围内,甚至低于材料的弹性极限时,就有可能发生破坏,在这种交变载荷循环作用下材料发生的破坏,叫做机械结构的疲劳破坏。 机械结构疲劳主要因素为循环应力次数、平均应力强弱、应力值大小。在交变载荷作用下机械零件经过一定时间,因结构内部的不均匀,承受应力的多变性,导致在高应力集中区域形成细小裂纹,再由小裂纹逐步扩展至断裂。使其具有瞬时性以及对缺陷的突发性常常不易发现且易造成事故,影响生产。调查发现机械零件疲劳破坏占企业事故发生率的80%左右,应力的高低直接影响疲劳寿命的长短。通常条件下,根据静力实验来测试材料的机械性能,但是静力破坏与疲劳破坏存在本质上的区别。首先,静力破坏是在超负荷作用下一次完成,而疲劳破坏是受反复作用力很长时间才发生的破坏。其次,在交变应力小于屈服强度,甚至远小于静强度时,可能发生疲劳破坏,但却不会发生静应力破坏。最后,疲劳破坏没有明显的破坏现象,例如金属的脆性破坏不易察觉。静力破坏有明显塑性变形。所以在确定材料的弹性极限、强度极限、屈服极限等机械性能时,不能单单依靠静力实验数据,来反映材料在受到交变应力时的特性。 1.2提高抗疲劳性能的方法 1.2.1添加“维生素” 在金属零件中添加不同种类的“维生素”可以增强零件抗疲劳的性质,延长疲劳寿命。例如:在有色金属和钢材里,加入一定比例的稀土元素,可以提高金属抗疲劳的强度极限值。 1.2.2结构表面处理 因材料承受扭转、弯曲等应力大部分都集中与表层,故对金属零件表面进行电镀或涂层处理,可有效改善应力腐蚀、锈蚀现象以及零件间滑动过程中的摩擦。还可以利用辅助工具将表面打磨光滑或对零件使用前进行塑性变形,有助于提升材料强度及屈服极限值。此外表面热处理通过淬火、氰化、渗碳等措施,改善机械结构表层材料的抗疲劳强度。 1.2.3改变机构外形 在设计构件时,常采用改变外形来减小应力的集中。例如在轴与轮毂安装时,可以通过在轮毂或者轴上开减荷槽。过盈配合时,可以增大配合轴的直径。当需要改变构件横截面时,应增大过度圆弧,以上都可以有效减小应力集中。 1.2.4降低温度、负荷 设备运行时,零部件之间的摩擦生热是正常现象,通过对局部降温的方法,可有效增加疲劳寿命。如电子元器件,采用降温技术可以提升70%的使用寿命。在交变应力作用较低的环境下机械部件不易发生疲劳破损,一旦发生疲劳损伤,其速度也较为缓慢。结合实际,当机构在低应力作用下稳定工作一定时间,再逐步提升到所需求的应力范围,可有效改善抗疲劳强度。 1.2.5利用豪克能技术 常温下的金属具有冷塑性,利用豪克能中冲击能和激活能复合技术对材料表面进行二次深加工,可以使金属零件表面Ra值在0.2以下,降低表层的损伤,通过改善表面的压应力,提高表面的耐磨性、显微硬度以及疲劳寿命。 2.分析机械结构可靠性 2.1对机械结构可靠性的分析 进行机械结构设计时,在保证产品性能、质量及成本的情况下,需要重视产品可靠性技术、理论以及使用过程中维护方面的研究。机械结构可靠性是指在规定时间和环境下,产品性能的完成情况。其影响因素有很多种,如生产过程中机械设备及系统的日常维护保养、人工操作水平以及产品制造技术等。而在正常使用中,机械结构通常受到材料本身机械性能、环境、受力时间长短以及负荷大小,都会减短产品疲劳寿命,以上过程同时考验静态与动态下的产品可靠性。我国对于机械结构可靠性的研究相比较发达国家仍然存在着较大的差距,技术不够成熟发展缓慢,需要大力培养可靠性研发的技术人员以及对各个领域机械机构进行可行性的研究创新,所以不管进行产品设计制造还是使用过程中维护维修方面,可靠性都属于重要的研究对象。 2.2机械结构可靠性的设计方法 2.2.1储备技术 储备技术又称为冗余技术,是保障机械设备的稳定运转而采取系统并联模型来提高可靠性的一种方法。为保证设备工作有冗余,通常是同种规格两个或两个以上的结构单元并联工作,使各处受力均匀,来增强可靠性。 2.2.2产品疲劳寿命估算 产品的可靠性会随着受到交变应力的时间长短而发生变化,从静态试验角度出发,以产品在常温、常态应力作用下的力学性能,为参考条件,评估产品使用过程中的疲劳寿命。当达到评估值时,及时对机械结构易损件进行更换,从而稳定运行。
发动机台架试验 -可靠性试验讲解
学生实验报告实验课程名称:发动机试验技术
目录 一、试验目的 二、试验内容 1.试验依据 2.试验条件 3.试验仪器设备 4.试验样机 5.试验内容与方案 (1)交变负荷试验 (2)混合负荷试验 (3)全速负荷试验 (4)冷热冲击试验 (5)活塞机械疲劳试验 (6)活塞热疲劳试验 三、试验进度安排 四、试验结果的提供
摘要 国外在可靠性试验方面己做了许多有益的研究工作,但到目前为止尚未形成统一的试验方法,而且考虑到该试验的非普遍性及技术保密性,将来也不可能形成统一的试验规范。相对于热疲劳研究状况来讲,国内对机械疲劳的研究还比较少。为适应发动机比功率和排放法规日益提高的苛刻要求,发动机面临着更高机械负荷和热负荷的严峻考验。国内高强化发动机最大爆发压力已超过22 Mpa。活塞的机械疲劳损伤主要体现在销孔、环岸等部位。活塞环岸、销座及燃烧室等部位由于在较高的工作温度下承受着高频冲击作用的爆发压力,润滑状况较差,摩擦磨损,其他破坏可靠性的腐蚀磨损(缸套一环换向区、排气门/排气门座锥面等)、疲劳磨损(挺杆、轴瓦、齿轮表面等)、微动磨蚀(轴瓦钢背、飞轮压紧处、飞轮壳压紧处、湿缸套止口处等)、电蚀(火花塞电极等)和穴蚀(水泵叶轮等)这些都是可靠性试验的主要目标,也是实施可靠性设计、试验研究的重点部位。 众所周知,在内燃机整机上进行零部件可靠性试验成本昂贵。本文将参照原有的可靠性试验方法,通过看一些关于可靠性的零部件加速寿命实验技术制定一种评价内燃机可靠性的考核规范,包括活塞机械疲劳试验和活塞热疲劳试验,可迅速做出其可靠性恰当的评价,可以降低研发成本、缩短研发时间。 一、试验目的 1通过理解内燃机可靠性评估,评定发动机的可靠性。 1.1了解评估的多种理论方法,如数学模型法、上下限法、相似设备法、蒙特卡洛法、故障分析( 包括故障模式影响分析和故障树分析) 等。并掌握故障分析法。 1.2学会可靠性试验评估,为进行可靠性设计奠定基础理论,为发动机及相关零部件提供测试、验证以及改进的技术支持。 2掌握可靠性试验方法 2.1掌握内燃机可靠性综合性试验及专项试验。综合性试验的考核对象是零件的可靠性、零件表面性状的变化和发动机性能的保持性;专项试验是超水温( 耐热性) 、超负荷、混合负荷、交变负荷循环、超爆发压力、超速等试验。 二、试验内容 1试验依据 参考的试验标准: GB /T 19055-2003 汽车发动机可靠性试验方法 GB /T 18297-2001 汽车发动机性能试验方法 JB/T 5112-1999 中小功率柴油机产品可靠性考核 2试验条件 一般试验条件: 2.1燃料及机油:采用制造厂所规定的牌号,柴油中不得有消烟添加剂。
结构疲劳试验
结构试验报告结构疲劳试验 道桥08 丁宇 0804110304
结构疲劳试验 中文名称: 疲劳试验 英文名称: fatigue test 定义:为评定材料、零部件或整机的疲劳强度及疲劳寿命所进行的试验。 疲劳简介 疲劳破坏现象的出现,始于19世纪初叶。产业革命以后,随着蒸汽机车和机动运载工具的发展,以及机械设备的广泛应用,运动部件的破坏经常发生。破坏往往发生在零构件的截面突变处,破坏处的名义应力不高,低于材料的抗拉强度和屈服点。破坏事故的原因一时使工程师们摸不着头脑,直至1829年德国人艾伯持用矿山卷扬机焊接链条进行疲劳试验,破坏事故才被阐明。1839年,法国工程师彭赛列首先使用“疲劳”这一术语来描述材料在循环载荷作用下承载能力逐渐耗尽以致最后突然断裂的现象。1843年苏格兰人兰金发表了第一篇疲劳论文,论文中指出,机车车辆的破坏是由于运行过程中金属性能逐渐变坏所致。他分析了车轴轴肩处尖角的有害影响,指出了加大轴肩处的圆角半径可以提高其疲劳强度。1842年Hood(胡持)提出了结晶理论,认为金属在循环应力下的疲劳强度降低是振动引起的结晶化所致。1849年美国机械工程学会还举行了专门会议对此理论进行讨论。 对疲劳现象最先进行系统试验研究的学者是德国人Wholer(沃勒),他从1847年至1889年在斯特拉斯堡皇家铁路工作期间,对金属的疲劳进行了深入系统的试验研究。1850年他设计出了第一台疲劳试验机(亦称WohLer疲劳试验机),用来进行机车车轴疲劳试验,并首次使用金届试样进行了疲劳试验。他在1871年发表的论文中,系统论述了疲劳寿命与循环应力的关系,提出了S—N曲线和疲劳极限的概念,确定了应力幅是疲劳破坏的主要因素,奠定了金属疲劳的基础。因此Wholer被公认是疲劳的奠基人。 从19世纪70年代到90年代,戈贝尔研究了平均应力对疲劳强度的影响,提出了戈贝尔抛物线方程。英国人古德曼提出了著名的简化曲线----古德曼图。1884年包辛格在验证沃勒的疲劳试验时,发现了循环载荷下弹性极限降低的“循环软化”现象,引入了应力—应变滞后回线的概念。但是他的工作当时并未引起人们重视,直到1952年邱杨在做铜棒实验时才把它重新提出来,并命名为“包辛格”效应。因此,包辛格是首先研究应力循环的人。 20世纪初叶,开始使用金相显微镜来研究疲劳机制。欧文和汉弗莱1903年在单晶铝和多晶铁上发现了循环应力产生的滑移痕迹。他们通过微观研究推翻了老的结晶理论,指出了疲劳变形是由于与单调变形相类似的滑移所产生。1901年拜尔斯透研究了循环载荷下应力—应变曲线的变化,测定了滞后回线,建立了循环硬化和循环软化的概念,并且进行了多级疲劳试验(程序试验)。在此期间,英国人高夫对疲劳机制的了解贡献很大。他研究了多轴疲劳,说明了弯、扭的复合作用。并在1924年发表了一本巨著《金属疲劳》。 1920年格里菲斯发表了他用玻璃研究脆断的理论计算和实验结果。他发现,玻璃的强度取决于微裂纹尺寸,得出了S√a=常数的关系式(S为断裂时的名义
滚动轴承的疲劳可靠性
滚动轴承的疲劳可靠性 化工过程机械邓坤军612080706048 摘要: 以可靠性理论为出发点,研究了滚动轴承在不同可靠度要求时的设计计算方法,找出了轴承寿命与可靠度间的关系及基本额定动载荷与可靠度间的关系。对从事可靠性设计的工程技术人员有一定的参考价值。 1 引言: 滚动轴承是一种应用相当广泛的标准零件,在它的选用设计中,通常要进行抗疲劳点蚀的寿命计算。目前使用的计算方法规定,在等于基本额定动载荷C 的当量动载荷作用下,滚动轴承可以工作10 车,而其中90 %不发生疲劳点蚀失效,这就意味着其可靠度为0.9。随着科学技术的迅速发展,对轴承组件的可靠性要求越来越高,如美国探险者1号宇宙飞船上仪器的滚动轴承要求可靠度为0.999999999。为了用样本中的基本额定动载荷C 进行不同可靠度的轴承选用设计。在工业生产中轴承作为经常使用的零件应用十分广泛, 由于轴承工特点作的,经常更换维护。一般的轴承主要起支撑转动轴的作用,有的轴承也在支撑转轴的同时也承受很高的载荷。正确地评价一个滚动轴承的有效、安全的工作寿命对安全生产,提高设备生产效率,延长设备使用寿命, 使生产顺利高质量进行是十分重要的技术问题。我国现行的国家标准规定的滚动轴承寿命计算方法[1],是先 计算出可靠性为90% 的额定寿命, 再对不同可靠度下的寿命用可靠性系数 a进 1 行修正, 其中 a的导出是以寿命服从二参数Weibull 分布为基础的。这种方法在 1 通常情况下可以取得较好的效果, 多年来一直在工程实践中应用。但是, 早在1962年, T. Tallian 分析了2520 套轴承的寿命试验数据后指出对存活概率在0. 4~ 0. 93之间时[2], 寿命分布与二参数Weibull 分布吻合较好, 超出此范围, 则有较大偏离。此外, 近年来,国外的一些轴承研究机构( 如瑞典的SKF工程研究中心)在轴承疲劳寿命试验中,观察到了超长寿命现象,亦即轴承在理想条件下进行耐久试验,其寿命远远高于上述方法计算出的寿命。因此,无论在理论上还是在实际中,滚动轴承均存在一个无限寿命,同时也存在着一个不为零的最小寿命。二参数Weibull 分布不能很好地体现上述两个特点, 这些都说明用二参数Weibull来描述滚动轴承寿命的局限性。这里以文献[3]的观点为基础,对在不同可靠度范围下的寿命分别采用二参数和三参数Weibull 分布的规律进行计算, 使计算结果更加接近于实际。 2 滚动轴承的寿命与可靠度间的关系 滚动轴承的承载能力和寿命的关系通常用,P—L 曲线(见图1)表示,P 是载
疲劳试验方案
1 试验概况 (1) 2 试验标准及要求 (1) 2.1试验标准 (1) 2.2试验要求 (1) 3 试验仪器技术指标 (1) 4 试验方法 (2) 4.1 试验装置 (2) 4.2 加载制度 (3) 4.2.1 预加载 (3) 4.2.2 正常加载 (3) 4.3 试验测量 (4) 4.3.1 位移计及力传感器的布置 (4) 4.3.2 混凝土应变片的布置 (4) 4.3.3 钢筋应变片的布置 (5) 4.3.4 试验记录 (5)
疲劳试验方案 1 试验概况 梁的抗弯疲劳试验。以混凝土梁为例,对不同强度的混凝土梁进行抗弯疲劳试验,对比不同强度混凝土梁在低周疲劳荷载作用下的刚度退化情况。本次试验共3组试件,分别为记为L1,L2,L3 ,如表1。 表1混凝土梁试件参数 2 试验标准及要求 2.1试验标准 1 《混凝土结构试验方法标准》GB50152-92。 2 《混凝土结构设计规范》 GB50010-2010。 2.2试验要求 1 试验前,仪器必须经过精准校对,降低误差。 2 试件两端由固定支座固定,如用简支梁支座固定,则需考虑平面外稳定。 3 试验人员需做好安全防范措施,如带好安全帽等。 3 试验仪器技术指标 本次试验采用微机控制电液伺服疲劳试验机,主要技术指标如表2所示。 表2试验仪器的主要技术指标
4 试验方法 4.1 试验装置 混凝土梁抗弯疲劳试验在微机控制电液伺服疲劳试验机(PWS-1000)上进行,混凝土梁采用固定支座固定在底梁上,其试验装置示意图如图1所示。 正面图 侧面图 图1试验装置示意图
4.2 加载制度 4.2.1 预加载 预加载的目的:使试件的支承约束部位和加载部位接触良好,进入正常工作状态;检查全部试验装置的可靠性;检查全部测量仪器工作是否正常。预加载的具体步骤如下: (1)对混凝土梁施加压力至预加载值,然后卸载至零;预加载值为疲劳荷载下限值; (2)在完成预加载的过程中,记录各应变片、位移计的数据,检查每级荷载下的数 据是否与理论计算指相符: a)所有位移随着荷载的增加呈线性变化; b)当卸载为零时,所有读数回到初始读数; c)位移计不能有过大的变化。 (3)如果不满足第(2)步规定的要求,检查试验装置是否正确安装,测量仪器是否正 常工作,然后重复第(1)步的预加载过程,直至满足要求为止。 4.2.2 正常加载 根据理论计算,破坏梁,在中点荷载作用下,如图2,试验梁的极限承载能力为 65kN (也可以做一次破坏试验取实验值)。取疲劳荷载上限值为37k N(极限值的57%),下限值为8k N(极限值的12%),进行疲劳试验。 对梁进行低周疲劳试验,在疲劳循环次数到 0次、10000次、15000次、20000次、25000次、30000次、35000次、40000次、45000次、50000次,对试验梁进行静力加载,测量试验梁的挠度变化,以此来测量梁的刚度退化情况。最大静力荷载为疲劳荷载的上限值。如果经过50000次循环加载后试验梁未发生破坏,则对其进行静力加载至破坏。 试验过程中记录加载点位移、荷载与位移计的数据及试验宏观现象;当完成所有加载或试件破坏时,中止试验,并对整个试件及典型部位拍摄照片。 出现以下情况之一,即判定为试件破坏: 1、某一根纵向受拉钢筋疲劳断裂,或受压区混凝土疲劳破坏; 2、某一根与临界斜裂缝相交的腹筋(箍筋或弯筋)疲劳断裂, 3、混凝土剪压疲劳破坏, 4、与临界斜裂缝相交的纵向钢筋疲劳断裂; 5、在锚固区钢筋与混凝土的粘结锚固疲劳破坏; 6、在停机受力情况进行一个循环的静载试验时,出现受拉主筋处的最大裂缝宽度 达到1.5mm,或挠度达到跨度的1/50,将此作为钢筋屈服的标志。 图2 混凝土梁加载疲劳荷载
疲劳可靠性
机械 机械构件的疲劳强度或疲劳寿命受众多因素的影响,如材料本质(如化学成分、金相组织、纤维方向、内部缺陷分布)、工作条件(如载荷特性、加载频率、服役温度、环境介质)、零件状态(如应力集中、尺寸效应、表面加工)等[1]。其中,最为复杂的是应力集中、表面加工和尺寸效应这三方面因素的影响。 关于应力集中、表面质量和尺寸因素各自对试样疲劳寿命或疲劳强度的影响,已有大量的研究[1飊5]。对于在疲劳设计中如何考虑这些因素的影响见文献[4],文献[5]则在此基础上考虑了各因素的分散性。目前考虑各因素对机械零件疲劳强度或疲劳寿命的影响,疲劳断裂的前提是结构应力分析,因此有限元求应力是第一步!目前疲劳断裂国内分成力学帮,航空帮,机械帮,和土木帮。力学帮主要在求三维断裂,以西交大的匡振邦,清华的杨卫为主。但他们的研究的大多是静态加载,没考虑循环加载,无法进行结构的寿命估算。航空帮又分疲劳帮和断裂帮。航空疲劳帮以北航的高镇同为主,主要是疲劳可靠性和雨流法。如果不考虑可靠性,很简单了,考虑了可靠性,由于以前的老家伙没几个懂概率统计,所以全被老高头蒙得一愣一愣的(笑)。其实西工大的吴富民教授水平很高,他的疲劳书比老高头的好。航空断裂帮以前是西工大的黄玉珊(黄神童),后来是北航的张行。主要是求飞机结构的应力强度因子。后来又搞了损伤容限与耐久性设计。这个很蒙人,没一两年时间你学不会。因为首先要学懂断裂力学,然后实际搞的是裂纹扩展。黄神童当年自
做聪明,70年在国内第一个搞断裂力学,(当时清华的黄克智还在算什么波纹板应力分析呢,可现在成了断裂帮总舵主)。黄玉珊认为疲劳比断裂简单多了,所以向航空部建议北航成立疲劳小组,西工大成立断裂小组。可惜黄是江浙人,喜欢单干,后又得了病早逝。加上我国的飞机一直以修修补补为主,使得航空疲劳帮一直有科研课题,有课题就自然会得奖,奖多了就会当院士。与黄玉珊同时搞断裂的是西南交大的孙训方先生。孙老先生水平很高,学生出国的很多。他经常出国开会发现什么是热门就让学生做,因此他的学生做好论文毕业之后出国机会很大。孙老先生绝对是院士水平。可惜老先生性子直不会讨好部里头,每次报院士铁道部提不成名。后来能提名了,已当成院士的又建议新院士要选年青的。所以中国院士一半是狗屎。只要有水平,一百岁时被人承认学术成就,就应当选为院士!机械帮首推东北工学院的徐灏老先生。徐老先生在疲劳方面做了不少工作。可惜他的学生生源不好,他有许多新思想告诉学生学生就是做不出来,他的有的学生是老外做什么只会照着做一遍。使得徐老先生未当成院士。按老先生的水平和著作早应是院士了。土木帮好像大连工学院的赵国蕃院士做了不少东东。但在理论上基本是照国外的在做。大工的课题很多,攀登B什么的。另外赵院士做的很扎实,有很多实验而且他还考虑了可靠性。因此各位如果想学疲劳断裂,不妨查一下以下各位学术大师的论文。实用的还是航空帮做的东西。 msc系列就是老美nasa资助搞起来的,我感觉其界面和功能就是用起来舒服。因此,疲劳并不难,只是很烦,考虑
疲劳测试
疲劳测试 疲劳测试是可靠性测试一种,其利用橡胶、塑料试样或模拟机件在各种环境下,经受交变载荷而测定其疲劳性能判据,并研究其断裂过程的试验。科标检测作为专业的可靠性能检测机构可依照ISO、ASTM、DIN、GB、HB等标准完成各类产品的疲劳试验、老化性能等测试,国家认可的检测报告和分析报告。 【检测范围】 1.试验应力(应变)和寿命(循环周次):高周疲劳低周疲劳室温疲劳低温疲劳高温疲劳热疲劳试验环境腐蚀疲劳接触疲劳微动磨损疲劳等等; 2.加载方式:拉压疲劳弯曲疲劳(旋转弯曲疲劳、三点弯曲疲劳、四点弯曲疲劳、悬臂弯曲疲劳)扭曲疲劳复合应力疲劳等等; 3.试验方法:扩展速率试验 S-N曲线的测定旋转弯曲方法等; 科标服务特点: ◇更短的检测周期-帮助客户快速获取精准检测结果 ◇更低的检测费用-合理的收费体系降低客户测试服务成本 ◇更完善的检测方案-为客户提供检测分析一站式服务 ◇更优质的售后服务-帮助客户解决服务后期技术疑问 【检测方法】 1. 领取试验所需试样,用游标卡尺测量试件的原始尺寸。表面有加工瑕疵的试样不能使用。 2. 开启机器,设置各项试验参数。 3. 安装试件。使试样与试验机主轴保持良好的同轴性。
4. 静力试验。取其中一根合格试样,先进行拉伸测其σb。静力试验目的一方面检验材质强度是否符合热处理要求,另一方面可根据此确定各级应力水平。 5. 设定疲劳试验具体参数,进行试验。第一根试样最大应力约为(0.6~0.7)σb,经N1次循环后失效。继取另一试样使其最大应力σ2=(0.40~0.45) σb,若其疲劳寿命N<107,则应降低应力再做。直至在σ2作用下,N2>107。这样,材料的持久极限σ-1在σ1与σ2之间。在σ1与σ2之间插入4~5个等差应力水平,它们分别为σ3﹑σ4﹑σ5﹑σ6,逐级递减进行实验,相应的寿命分别为N3﹑N4﹑N5﹑N6。 6. 观察与记录。由高应力到低应力水平,逐级进行试验。记录每个试样断裂的循环周次,同时观察断口位置和特征。 7. 实验结束,取下试件。清理实验场地,试验机一切机构复原。 8. 根据实验记录进行有关计算。将所得实验数据列表;然后以lgN为横坐标,σmax为纵坐标,绘制光滑的S-N曲线,并确定σ-1的大致数值。
疲劳分析.
疲劳分析方法 疲劳问题的研究可追溯到19世纪初,经过近二百年探索,目前已经取得了很大的发展。工程上,对疲劳设计主要采用四种方法,即名义应力法、局部应力应变法、损伤容限设计、疲劳可靠性设计。 (1)名义应力法(Miner线性累计损伤理论) 名义应力法又称常规疲劳设计法或影响系数法,用名义应力法来估算构件或结构的寿命的前提是:材料和构件、结构是理想连续体,且承受的载荷不大,断面的应力值小于材料的屈服极限,应力应变成线性关系,应力循环作用下的寿命较小。因此,用该方法进行寿命估算的依据是应力谱、材料的抗力指标P—S—N 曲线和累积损伤理论。 (2)局部应力应变法 零件的疲劳破坏都是从应变集中部位的最大局部应变处开始,并且在裂纹萌生以前,都要产生一定的塑性变形。局部应力应变法以缺口根部的局部应力—应变历程为依据,再结合材料相应的疲劳特性曲线进行寿命估算。该方法的合理性主要表现为考虑了金属的塑性应变和由此而引起的残余应力对疲劳性能的影响。它所指的寿命就是缺口边上出现可见裂纹的寿命。 (3)损伤容限设计 损伤容限设计是一项复杂的系统工程,它以断裂力学特别是线弹性断裂力学理论为基础,以保证结构安全为目标,以无损检测技术、断裂韧度和疲劳裂纹扩展速率的测定技术为手段,以有初始缺陷或裂纹的零件的剩余寿命估算为中心,以断裂控制为保证,目的是确保结构在给定使用寿命期内,不致因未发现的初始缺陷的扩展造成严重事故。 (4)疲劳可靠性设计 疲劳可靠性设计即概率疲劳设计,它是根据构件工作应力和疲劳强度分布曲线,应用概率设计理论,在给定可靠性指标下,进行构件的可靠性设计。疲劳可靠性设计不但需要知道构件的应力和疲劳强度的平均值,而且还要知道构件的应力和疲劳强度分布。 综上所述,名义应力法和局部应力应变法都是以材料内部没有缺陷和裂纹为
基于可靠性技术的材料疲劳极限快速试验方法
武汉汽车工业大学学报000616 武汉汽车工业大学学报 JOURNAL OF WUHAN AUTOMOTIVE POLYTECHNIC UNIVERSITY 2000 Vol.22 No.6 P.64-67 基于可靠性技术的材料疲劳极限快速试验方法 吴波 黎明发 摘 要:利用疲劳破坏的基本特性而建立起来的疲劳强度频率分布与疲劳寿命频率分布之 间的数学关系式,探讨一种快速确定机械工程材料疲劳强度极限分布的寿命试验方法。 关键词: 可靠性 ; 疲劳极限 ; 试验方法 ; 加速试验 中图法分类号: TH 140.7 文献标识码: A 文章编号: 1007 - 144X(2000)06 - 0064 - 04 Research of the Engineer Material Fatigue Limit Rapid Experiment Method Which is on Account of Reliance Technique Wu Bo, Li Mingfa (School of Mechanical and Electrical E ngineering, WAPU, Wuhan 430070, China.) Abstract:This paper uses essential specific property of the fatigue destroy to establish a math relation equality. This relation equality is between frequency distribution of the fatigue strength and frequency distribution of the fatigue l ife. At the same time inquire into a kind of life experiment method which can ra pidly definite fatigue strength limit distribution of the mechanical engineering material. Key words: reliance ; fatigue limit ; experiment method ; accelerate experiment 作者简介:吴 波(1962-),男,湖北武汉人,武汉汽车工业大学副教 授. 吴波(武汉汽车工业大学 机电工程学院, 湖北 武汉 430070; ) 黎明发(武汉汽车工业大学 基础 课部, 湖北 武汉 430070) 参考文献: [1] 王锡山. 机械强度数据库[J]. 机械强度,1991,13(3):54-59 [2] 高镇同,付惠民. 疲劳强度的频率分布和疲劳强度特征函数[J]. 机械强度,1985,7(2 ):12-15 [3] 黎明发,吴 波. 用Monte Carlo法分析机械零件在分布应力下的疲劳寿命[J]. 武汉工 学院学报,1988,10(2):52-59 [4] 王时任,陈继平. 可靠性工程概论[M]. 武汉:华中理工大学出版社,198 3. [5] 徐 灏. 机械强度的可靠性设计[M]. 北京:机械工业出版社,1984. 收稿日期: 2000-04-25. file:///E|/qk/whqcgydxxb/whqc2000/0006/000616.htm2010-3-23 9:52:19