注塑成型模拟分析

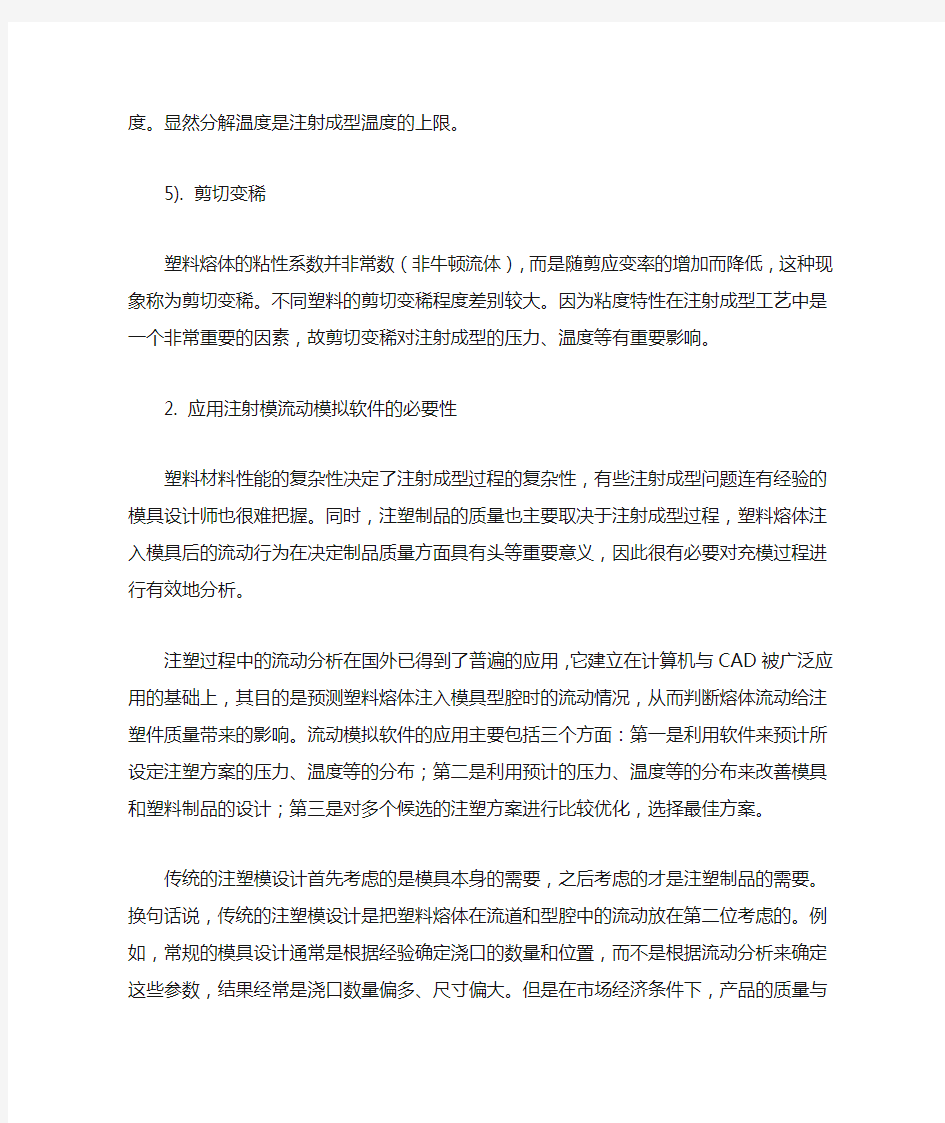
为什么要进行注塑成型模拟分析
1 塑料及其性质
由于塑料的内部结构比金属复杂,故掌握其性能特点也就比较困难。然而要想有效地进行塑料的注射成型,就应该对其与成型有关的性能有所了解。
1).比热容
不同塑料的比热容差别较大,并随着温度的变化而变化。
2). 热扩散系数
塑料的热扩散系数对成型中材料的温度与冷却有较大关系,并且也随着温度的变化而变化。
3). 密度/比容
塑料的密度与温度有强烈的依赖关系,温度升高时密度较小。注射成型过程中,温度不断变化,故材料的密度也在不断变化,这种变化对产品的质量有重要影响。
4). 热降解、分解温度
塑料因加工温度偏高,或在较高温度下停留时间过长,从而使平均分子量降低的现象称为热降解。如出现这种情况,则熔体的粘度降低,制品出现飞边、气泡和银丝,机械性能变差,如弹性消失、强度降低等。分解温度是指聚合物因受热而迅速分解为低分子的温度。显然分解温度是注射成型温度的上限。
5). 剪切变稀
塑料熔体的粘性系数并非常数(非牛顿流体),而是随剪应变率的增加而降低,这种现象称为剪切变稀。不同塑料的剪切变稀程度差别较大。因为粘度特性在注射成型工艺中是一个非常重要的因素,故剪切变稀对注射成型的压力、温度等有重要影响。
2. 应用注射模流动模拟软件的必要性
塑料材料性能的复杂性决定了注射成型过程的复杂性,有些注射成型问题连有经验的模具设计师也很难把握。同时,注塑制品的质量也主要取决于注射成型过程,塑料熔体注入模具后的流动行为在决定制品质量方面具有头等重要意义,因此很有必要对充模过程进行有效地分析。
注塑过程中的流动分析在国外已得到了普遍的应用,它建立在计算机与CAD被广泛应用的基础上,其目的是预测塑料熔体注入模具型腔时的流动情况,从而判
断熔体流动给注塑件质量带来的影响。流动模拟软件的应用主要包括三个方面:第一是利用软件来预计所设定注塑方案的压力、温度等的分布;第二是利用预计的压力、温度等的分布来改善模具和塑料制品的设计;第三是对多个候选的注塑方案进行比较优化,选择最佳方案。
传统的注塑模设计首先考虑的是模具本身的需要,之后考虑的才是注塑制品的需要。换句话说,传统的注塑模设计是把塑料熔体在流道和型腔中的流动放在第二位考虑的。例如,常规的模具设计通常是根据经验确定浇口的数量和位置,而不是根据流动分析来确定这些参数,结果经常是浇口数量偏多、尺寸偏大。但是在市场经济条件下,产品的质量与成本已成为企业生存发展的生命线,注射成型模拟软件可以辅助企业确立竞争优势。
二.如何应用注塑成型分析报告指导模具设计
1. 注塑条件对制品成型的影响
1). 塑料材料
如前所叙,塑料材料性能的复杂性决定了注射成型过程的复杂性。而塑料材料的性能又因品种不同、牌号不同、生产厂家不同、甚至批次不同而差异较大。不同的性能参数可能导致完全不同的成型结果。对注射成型过程影响比较大的材料参数见“基础篇”
2). 注射温度
熔体流入冷却的型腔,因热传导而散失热量。与此同时,由于剪切作用而产生热量,这部分热量可能较热传导散失的热量多,也可能少,主要取决于注塑条件。熔体的粘性随温度升高而变低。这样,注射温度越高,熔体的粘度越低,所需的充填压力越小。同时,注射温度也受到热降解温度、分解温度的限制。
3). 模具温度
模具温度越低,因热传导而散失热量的速度越快,熔体的温度越低,流动性越差。当采用较低的注射速率时,这种现象尤其明显。
4). 注射时间
注射时间对注塑过程的影响表现在三个方面:
(1)缩短注射时间,熔体中的剪应变率也会提高,为了充满型腔所需要的注射压力也要提高。
(2)缩短注射时间,熔体中的剪应变率提高,由于塑料熔体的剪切变稀特性,熔体的粘度降低,为了充满型腔所需要的注射压力也要降低。
(3)缩短注射时间,熔体中的剪应变率提高,剪切发热越大,同时因热传导而散失的热量少,因此熔体的温度高,粘度越低,为了充满型腔所需要的注射压力也要降低。
以上三种情况共同作用的结果,使图1中的充满型腔所需要的注射压力的曲线呈现“U”形。也就是说,存在一个注射时间,此时所需的注射压力最小。
图1 注射时间与注射压力、熔体温度的关系
2. CAE软件的指导作用
注射模流动模拟软件的指导意义十分广泛,她是一种设计工具,能够辅助模具设计者优化模具结构与工艺,指导产品设计者从工艺的角度改进产品形状,选择最佳成型性能的塑料,帮助模具制造者选择合适的注射机,当变更塑料品种时对现有模具的可行性做出判断,分析现有模具设计弊病。同时,流动软件又是一种教学软件工具,能够帮助模具工作者熟悉熔体在型腔内的流动行为,把握熔体流动的基本原则。下面逐项分析三维流动软件的主要输出结果是如何用来指导设计的。
1). 熔体流动前沿动态显示
三维流动模拟软件能显示熔体从进料口逐渐充满型腔的动态过程,由此可判断熔体的流动是否较理想的单项流形式(简单流动)(复杂流动成型不稳定,容易出现次品)。各个流动分支是否在同时充满型腔的各个角落(流动是否平衡)。若熔体的填充过程不理想,可以改变进料口的尺寸,数量和位置,反复运行流动模拟软件,一直到获得理想的流动形式为止。若仅仅是为了获得较好的流动形式而暂不考察详尽的温度场,应力场的变化,或是初调流道系统,最好是运行简易三维流动分析(等温流动分析),经过几次修改,得到较为满意的流道设计后,再运行非等温三维流动分析。
2). 型腔压力
在填充过程中最大的型腔压力值能帮助判断在指定的注射机上熔体能否顺利充满型腔(是否短射),何处最可能产生飞边,在各个流动方向上单位长度的压力差(又称压力梯度)是否接近相等(因为最有效的流动形式是沿着每个流动分支熔体的压力梯度相等),是否存在局部过压(容易引起翘曲)。流动模拟软件还能给出在熔体填充模具所需的最大锁模力,以便用户选择注射机。
3). 熔体温度
流动模拟软件提供型腔内熔体在填充过程中的温度场。可鉴别在填充过程中熔体
是否存在着因剪贴发热而形成的局部热点(易产生表面黑点、条纹等并引起机械性能下降),判断熔体的温度分布是否均匀(温差太大是引起翘曲的主要原因),判断熔体的平均温度是否太低(引起注射压力增大)。熔体接合点的温度还可帮助判断熔合纹的相对强度
4). 剪切速率
剪贴速率又称应变速率或者速度梯度。该值对熔体的流动过程影响甚大。实验表明,熔体在剪贴速率为103S-1左右成型,制品的质量最佳。流道处熔体剪贴速率的推荐值约为5*102~5*103S-1,浇口处熔体剪贴速率的推荐值约为
104~105S-1 。流动软件能给出不同填充时刻型腔各处的熔体剪切速率,这就有助于用户判断在该设计方案下预测的剪切速率是否与推荐值接近,而且还能判断熔体的最大剪切速率是否超过该材料所允许的极限值。剪切速率过大将使熔体过热,导致聚合物降解或产生熔体破裂等弊病。剪切速率分布不均匀会使熔体各处分子产生不同程度的取向,因而收缩不同,导致制品翘曲。通过调整注射时间可以改变剪切速率。
5). 剪切应力
剪切应力也是影响制品质量的一个重要因素,制品的残余应力值与熔体的剪切应力值有一定的对应关系,一般,剪切应力值大,残余应力值也大。因此总希望熔体的剪切应力值不要过大,以避免制品翘曲或开裂。根据经验,熔体在填充型腔时所承受的剪切应力不应超过该材料抗拉强度的1%。
6). 熔合纹/气穴
两个流动前沿相遇时形成熔合纹,因而,在多浇口方案中熔合纹不可避免,在单浇口时,由于制品的几何形状以及熔体的流动情况,也会形成熔合纹。熔合纹不仅影响外观,而且为应力集中区,材料结构性能也受到削弱。改变流动条件(如浇口的数目与位置等)可以控制熔合纹的位置,使其处于制品低感光区和应力不敏感区(非“关键”部位)。而气穴为熔体流动推动空气最后聚集的部位,如果该部位排气不畅,就会引起局部过热、气泡、甚至充填不足等缺陷,此时就应该加设排气装置。流动模拟软件可以为用户准确地预测熔合纹和气穴的位置。
7). 多浇口的平衡
当采用多浇口时,来自不同浇口的熔体相互汇合,可能造成流动的停滞和转向(潜流效应),这时各浇口的充填不平衡,影响制品的表面质量及结构的完整性,也得不到理想的简单流动。这种情况应调整浇口的位置。
流动模拟软件在优化设计方案更显优势。通过对不同方案的模拟结果的比较,可以辅助设计人员选择较优的方案,获得最佳的成型质量。
3. 流动软件的正确使用
注射模流动模拟软件只是一种辅助工具,它能否在产生中性层发挥作用并产生经济效益,在很大程度上取决于模具设计者的正确使用。
1). 流动软件的使用人员
流动软件的使用者必须熟悉注射成型工艺,具有一定的注射模设计经验。这样,用户才能针对性地利用流动软件解决模具结构设计或工艺问题,例如,如果浇口处剪切速率过高,是修正浇口尺寸,还是改变熔体温度,抑或更换注射材料呢,不具备注射成型工艺知识的人很难做出正确选择的。流动软件的输出的结果涉及到塑料粘度,剪切速率,温度,压力以及它们的相互作用,即使是经验丰富的模具设计师也应学一点塑料流变学的知识,总结注射流动的基本规律,这样才能站在理论与实践结合的高度用好流动模拟软件。
2). 输入数据的正确性
首先要输入合理的注射成型工艺参数,常用材料的成型温度见表1(仅供参考)。
表1 常用材料的成型参考温度
除此之外,还要有正确的材料参数(如热传导率,比热,密度,不流动温度以及粘度等)。如前所叙,塑料材料的性能参数(流变性、压缩性等)十分重要,不同的性能参数将导致完全不同的模拟结果。同时,塑料材料的性能又因品种不同、牌号不同、生产厂家不同、甚至批次不同而差异较大。因此,获得所用材料的准确的性能参数是使用CAE软件的前提条件。尤其是材料的粘性参数,对充模流动有重要影响,又不易通过实验直接获得,华中科技大学模具技术国家重点实验室塑料模研究室可以为客户测试并拟合材料的粘度参数。
三.注射模流动模拟软件的指导作用
注射模流动模拟软件的指导意义十分广泛,它是一种设计工具,能够辅助模具设计者优化模具结构与工艺,指导产品设计者从工艺的角度改进产品形状,选择最佳成型性能的塑料,帮助模具制造者选择合适的注射机,当变更塑料品种时对现有模具的可行性做出判断,分析现有模具设计弊病。同时,流动软件又是一种教学软件工具,能够帮助模具工作者熟悉熔体在型腔内的流动行为,把握熔体流动的基本原则。下面逐项分析三维流动软件的主要输出结果是如何用来指导设计的。
1 熔体流动前沿动态显示(图2)
图2 熔体流动前沿动态显示
三维流动模拟软件能显示熔体从进料口逐渐充满型腔的动态过程,由此可判断熔体的流动是否较理想的单项流形式(简单流动)(复杂流动成型不稳定,容易出现次品)。各个流动分支是否在同时充满型腔的各个角落(流动是否平衡)。若熔体的填充过程不理想,可以改变进料口的尺寸,数量和位置,反复运行流动模拟软件,一直到获得理想的流动形式为止。若仅仅是为了获得较好的流动形式而暂不考察详尽的温度场,应力场的变化,或是初调流道系统,最好是运行简易三维流动分析(等温流动分析),经过几次修改,得到较为满意的流道设计后,再运行非等温三维流动分析。
2 型腔压力(图3)
图3 型腔压力
在填充过程中最大的型腔压力值能帮助判断在指定的注射机上熔体能否顺利充满型腔(是否短射),何处最可能产生飞边,在各个流动方向上单位长度的压力差(又称压力梯度)是否接近相等(因为最有效的流动形式是沿着每个流动分支熔体的压力梯度相等),是否存在局部过压(容易引起翘曲)。流动模拟软件还能给出在熔体填充模具所需的最大锁模力,以便用户选择注射机。
3 熔体温度(图4)
图4 熔体温度
流动模拟软件提供型腔内熔体在填充过程中的温度场。可鉴别在填充过程中熔体是否存在着因剪贴发热而形成的局部点(易产生表面黑点、条纹等并引起机械性能下降),判断熔体的温度分布是否均匀(温差太大是引起翘曲的主要原因),判断熔体的平均温度是否太低(引起注射压力增大)。熔体接合点的温度还可帮助判断熔合纹的相对强度。
4 剪切速率(图5)
图5 剪切速率
剪贴速率又称应变速率或者速度梯度。该值对熔体的流动过程影响甚大。实验表明,熔体在剪贴速率为103S-1左右成型,制品的质量最佳。流道处熔体剪贴速率的推荐值约为5*102~5*103S-1,浇口处熔体剪贴速率的推荐值约为
104~105S-1 。流动软件能给出不同填充时刻型腔各处的熔体剪切速率,这就有助于用户判断在该设计方案下预测的剪切速率是否与推荐值接近,而且还能判断熔体的最大剪切速率是否超过该材料所允许的极限值。剪切速率过大将使熔体过
热,导致聚合物降解或产生熔体破裂等弊病。剪切速率分布不均匀会使熔体各处分子产生不同程度的取向,因而收缩不同,导致制品翘曲。通过调整注射时间可以改变剪切速率。
5 剪切应力(图6)
图6 剪切应力
剪切应力也是影响制品质量的一个重要因素,制品的残余应力值与熔体的剪切应力值有一定的对应关系,一般,剪切应力值大,残余应力值也大。因此总希望熔体的剪切应力值不要过大,以避免制品翘曲或开裂。根据经验,熔体在填充型腔时所承受的剪切应力不应超过该材料抗拉强度的1%。
6 熔合纹/气穴(图7)
图7 熔合纹/气穴
两个流动前沿相遇时形成熔合纹,因而,在多浇口方案中熔合纹不可避免,在单浇口时,由于制品的几何形状以及熔体的流动情况,也会形成熔合纹。熔合纹不仅影响外观,而且为应力集中区,材料结构性能也受到削弱。改变流动条件(如浇口的数目与位置等)可以控制熔合纹的位置,使其处于制品低感光区和应力不敏感区(非“关键”部位)。而气穴为熔体流动推动空气最后聚集的部位,如果该部位排气不畅,就会引起局部过热、气泡、甚至充填不足等缺陷,此时就应该加设排气装置。流动模拟软件可以为用户准确地预测熔合纹和气穴的位置。
7 多浇口的平衡
当采用多浇口时,来自不同浇口的熔体相互汇合,可能造成流动的停滞和转向(潜流效应),这时各浇口的充填不平衡,影响制品的表面质量及结构的完整性,也得不到理想的简单流动。这种情况应调整浇口的位置。
四.结束语
流动模拟软件在优化设计方案更显优势。通过对不同方案的模拟结果的比较,可以辅助设计人员选择较优的方案,获得最佳的成型质量。
注射模流动模拟软件只是一种辅助工具,它能否在产生中发挥作用并产生经济效益,在很大程度上取决于模具设计者的正确使用。
薄壁注塑成型技术的研究进展
薄壁注塑成型技术的研究进展 摘要:由于3C产品向轻、薄、短、小方向发展得越来越快,所以薄壁注塑成型技术也受到人们的高度重视,而薄壁注塑成型数值模拟技术是薄壁注塑成型技术得以应用的重要保证。本文介绍了薄壁注塑成型技术产生的背景和科学意义,综述了薄壁注塑成型中的制品设计、模具设计、注塑机和材料选用以及薄壁注塑成型数值模拟技术的研究与应用概况,探讨了薄壁注塑成型数值模拟技术发展中所面临的一些关键问题,指出了薄壁注塑成型数值模拟技术的研究发展方向。关键词:薄壁注塑成型;模具设计;数值模拟;流长厚度比;冷凝层。近年来,笔记本电脑和移动电话等3C(Computer, Communication and Consumer)产品更新换代的速度非常快,这类产品的设计理念正朝着“轻、薄、短、小”方向发展,同时人们对这些产品的需求也在快速增长,于是在常规注塑成型(Conventional Injection Molding, CIM)技术的基础上,薄壁注塑成型(Thin-Wall Injection Molding , TWIM)技术迅速发展起来。薄壁化因具有减小产品重量及外形尺寸、便于集成设计及装配、缩短生产周期、节约材料和降低成本等优点成为塑料消费行业追求的目标,已成为塑料成型行业中新的研究热点。薄壁注塑成型技术是一种仅有十几年发展历史的新兴技术,其理论体系尚未形成,缺少系统性的研究,而薄壁注塑成型数值模拟研究也只是近几年才提出的,还有许多理论上和实践中的问题尚待解决。薄壁注塑成型技术的概念目前关于薄壁注塑成型还没有统一的定义,Mahishi 和Maloney把其定义为流长厚度比L/T(L:Length,流动长度;T:Thickness,塑件厚度;L/T也简称为流长比)在100或者150以上的注塑为薄壁注塑;而Whetten和Fasset是这样定义薄壁注塑成型的:所成型塑件的厚度小于1mm,同时塑件的投影面积在50cm2以上的注塑成型。由此可见要给出一个统一的定义还是比较困难的;同时随着技术的发展,薄壁注塑成型定义的临界值也将发生变化,它应该是一个相对的概念。常规注塑成型工艺已为人们所熟悉,但薄壁注塑成型则不然,因为随着壁厚的减薄,聚合物熔体在型腔中的冷却速度加剧,在很短的时间内就会固化,这使得成型过程变得复杂,成型难度加大,常规的注塑成型工艺条件已不能满足需要。常规注塑成型的一个不足就是填充过程和冷却过程往往是交织在一起的,但由于常规塑件的尺寸比较大,所以对成型过程影响不大,但在薄壁注塑成型中这个不足就成为致命的问题。所以,不能把常规注塑成型中的理论和操作简单地照搬到薄壁注塑成型中去。薄壁注塑成型中的制品设计、模具设计、注塑机及材料选用薄壁制品的设计思想和方法更为复杂,并进一步受到成型局限及材料选择的影响。薄壁制品要求应该具有高的冲击强度、良好的外观质量和尺寸稳定性,并能承受大的静态载荷,成型材料的流动性要好。设计过程中要重点考虑制品的刚性、抗冲击性和可制造性。成型薄壁制品时一般需要专门设计的薄壁制品专用模具。与常规制品的标准化模具相比,薄壁制品的模具从模具结构、浇注系统、冷却系统、排气系统和脱模系统等都发生了重大变化。主要表现在以下几个方面:(1)模具结构:为承受成型时的高压,薄壁成型模具的刚度要大、强度要高。因此模具的动、定模板及其支承板重量较大,厚度通常比传统模具的模板要厚。支撑柱要多,模具内可能要多设置内锁,以保证精确定位和良好的侧支撑,防止弯曲和偏移。另外,高速射出速度增加了模具的磨损,因此模具要采用较高硬度的工具钢,高磨损、高冲蚀区(如浇口处)硬度应大于HRC55。(2)浇注系统:成型薄壁制品,特别是制品厚度非常小时,要使用大浇口,而且浇口应该大于壁厚。如是直浇口应设置冷料井,以减少浇口应力,协助填充,减少制品去除浇口时的损坏。为保证有足够的压力充填薄的模腔,流道系统中应尽可能减少压力降。为此,流道设计要比传统的大一些,同时要限制熔体的驻留时间,以防止树脂降解劣化。当是一模多腔时,浇注系统的平衡性要求远高于常规模具的要求。值得注意的是薄壁制品模具的浇注系统中还引入了两项先进技术,即热流道技术和顺序阀式浇口(SVG)技术。(3)冷却系统:薄壁制品不像传统壁厚件那样可以承受较大的因传
摄像头支架零件的注塑成型模拟分析【毕业作品】
摄像头支架零件的注塑成型模拟分析 摘要 本此论文设计采用UG进行摄像头支架零件的三维建模,并转换成jgs格式。利用Moldflow Plastic Insight(MPI)软件对部件注塑成型整个过程进行模拟分析、并改善塑件成型缺陷。此软件分析过程总体包括充填、流动、冷却、翘曲等方面分析,从分析中获得最佳浇口位置、气穴、熔接痕、流动时间、残余应力、冻结时间、压力和温度分布的准确信息。对摄像头支架零件的浇口位置进行模拟分析,通过显示结果的充填时间、压力、气穴、熔接痕等进行优化对比,选出最佳的进浇位置方案。并以此进浇点设计出浇注系统,进行流动翘曲分析。由于本此设计塑件材料采用塑料聚碳酸酯(PC)为原料,通过模流分析在充填时间、气压、气穴、熔接痕等工艺参数对比下得到优化参数,选出最佳方案进行注塑成型。 经过对比优化后的进浇位置,使注件充填时间得到改善,气穴问题明显减少,熔接痕也得到改善,优化后的冷却水路,使注塑件在加工过程中制品温度得到改善。这些优化后的方案提高能够塑件质量,减少生产周期,这就是CAE技术在制造业广泛应用的原因之一。 关键词:模拟分析;流动;翘曲;填充时间;气穴;压力;熔接痕
目录 摘要 ............................................................................................................................ I 1.绪论 (1) 1.1研究背景 (1) 1.1.1发展趋势 (1) 1.2模拟过程的理论基础 (1) 1.2.1塑料注塑成型原理 (1) 1.2.2 CAE技术应用理论 (2) 1.3本此毕业设计主要工作 (2) 2.摄像头支架实体 (3) 2.1摄像头产品造型 (3) 2.2 产品设计三视图 (3) 3.摄像头支架注塑成型分析 (4) 3.1制件成型条件分析 (4) 3.2制件网格划分 (4) 3.1.1网格划分统计 (5) 3.1.2网格修复 (6) 3.3型腔数量选择 (6) 3.4最佳浇口位置分析 (7) 4.进浇位置选择 (8) 4.1进浇位置设计方案 (8)
注塑件常见品质问题及原因分析、解决方法
注塑件常见品质问题及原因分析、解决方法 一、注塑件常见品质问题 塑胶件成型后,与预定的质量标准(检验标准)有一定的差异,而不能满足下工序要求,这就是塑胶件缺陷,即常说的品质问题,要研究这些缺陷产生原因,并将其降至最低程度,总体来说,这些缺陷不外乎是由如下几方面造成:模具、原材料、工艺参数、设备、环境、人员。现将缺陷问题总结如下: 1、色差:注塑件颜色与该单标准色样用肉眼观看有差异,判为色差,在标准的光源下(D65)。 2、填充不足(缺胶):注塑件不饱满,出现气泡、空隙、缩孔等,与标准样板不符称为缺胶。 3、翘曲变形:塑胶件形状在塑件脱模后或稍后一段时间内产生旋转和扭曲现象,如有直边朝里,或朝外变曲或平坦部分有起伏,如产品脚不平等与原模具设计有差异称为变形,有局部和整体变形之分。 4、熔接痕(纹):在塑胶件表面的线状痕迹,由塑胶在模具内汇合在一起所形成,而熔体在其交汇处未完全熔合在一起,彼此不能熔为一体即产生熔接纹,多表现为一直线,由深向浅发展,此现象对外观和力学性能有一定影响。 5、波纹:注塑件表面有螺旋状或云雾状的波形凹凸不平的表征现象,或透明产品的里面有波状纹,称为波纹。 6、溢边(飞边、披锋):在注塑件四周沿分型线的地方或模具密封面出现薄薄的(飞边)胶料,称为溢边。 7、银丝纹:注塑件表面的很长的、针状银白色如霜一般的细纹,开口方向沿着料流方向,在塑件未完全充满的地方,流体前端较粗糙,称为银丝纹(银纹)。 8、色泽不均(混色):注塑件表面的色泽不是均一的,有深浅和不同色相,称为混色。
9、光泽不良(暗色):注塑件表面为灰暗无光或光泽不均匀称为暗色或光泽不良。 10、脱模不良(脱模变形):与翘曲变形相似,注塑件成型后不能顺利的从模具中脱出,有变形、拉裂、拉伤等、称为脱模不良。 11、裂纹及破裂:塑胶件表面出现空隙的裂纹和由此形成的破损现象。 12、糊斑(烧焦):在塑件的表面或内部出现许多暗黑色的条纹或黑点,称为糊斑或烧焦。 13、尺寸不符:注塑件在成型过程中,不能保持原来预定的尺寸精度称为尺寸不符。 14、气泡及暗泡:注塑件内部有孔隙,气泡是制品成型后内部形成体积较小或成串孔隙的缺陷,暗泡是塑胶内部产生的真空孔洞。 15、表面混蚀:注塑件表面呈现无光、泛白、浊雾状外观称为混蚀。 16、凹陷:注塑件表面不平整、光滑、向内产生浅坑或陷窝。 17、冷料(冷胶):注塑件表面由冷胶形成的色泽、性能与本体均不同的塑料。 18、顶白/顶高:注塑件表面有明显发白或高出原平面。 19、白点:注塑件内有白色的粒点,粒点又叫“鱼眼”,多反映在透明制品上。 20、强度不够(脆裂):注塑件的强度比预期强度低,使塑胶件不能承受预定的负裁 二、常见品质(缺陷)问题产生原因 1、色差: ①原材料方面因素:包括色粉更换、塑胶材料牌号更改,定型剂更换。 ②原材料品种不同:如PP料与ABS料或PC料要求同一种色,但因材料品种不同而有轻微色差,但允许有一限度范围。 ③设备工艺原因:A、温度;B、压力;C熔胶时间等工艺因素影响。 ④环境因素:料筒未清干净,烘料斗有灰尘,模具有油污等。
2017《注塑缺陷的原因分析与解决对策》--邓益善
注塑缺陷的原因分析与解决对策 【主办单位】一六八培训网 【时间地点】2017年04月15-16日上海 04月22-23日深圳 2017年08月19-20日上海 08月26-27日深圳 2017年12月16-17日深圳 12月23-24日上海 【收费标准】¥3200元/人(包括资料费、午餐及上下午茶点等) 3. 大量典型实例讲解、分析; 4. 学员自带不良品、现场解决问题、互动探讨; 5. 世界最先进的、全国独有的系统,全真展现注塑生产过程,动态显示生产现场看得见以及 看不见的环节和变化,等于将注塑车间搬到培训大厅。 片面的经验,对一些综合性的问题缺乏科学系统的分析能力,对已经出现的生产问题缺乏解决问题的措施。 邓益善老师基于扎实的生产实践与技术指导经历,将实实在在从根源上帮助解决这些问 第二部分:最佳注塑工艺设定方法 1. 如何设定各项关键注塑工艺参数;
2. 时间、温度、压力、速度、位置等参数设定要点; 3. 螺杆相关设定要点; 4. 多段充填的设定与实际使用; 5. 多段保压的设定与实际使用; 6. 速度/压力切换点的设定方法; 7. 多视窗注塑成型技术运用; 8. 塑料分子排向对质量的影响以及如何控制 9. 注塑残余内应力对质量的影响以及如何控制 第三部分:注塑现场问题分析与解决对策 注塑问题描述、原因分析,如常见的缩孔、缩水、不饱模、毛边、熔接痕、银丝、喷痕、烧焦、翘曲变形、开裂/破裂、尺寸超差及其它等等,以及在产品结构设计、模具设计、成型工艺控制及塑料材料等方面之全面解决对策。 1. 注塑件周边缺胶、不饱模的原因分析及解决对策; 2. 批锋(毛边)的原因分析及解决对策; 3. 注塑件表面缩水、缩孔(真空泡)的原因分析及解决对策; 4. 银纹(料花、水花)、烧焦、气纹的原因分析解决对策; 5. 注塑件表面水波纹、流纹(流痕)的原因分析及解决对策; 6. 注塑件表面夹水纹(熔接痕)、喷射纹(蛇纹)的原因分析及解决对策; 7. 注塑件表面裂纹(龟裂)的原因分析及解决对策; 8. 注塑件表面色差、光泽不良、混色、黑条、黑点的原因分析及解决对策; 9. 注塑件翘曲变形、内应力开裂的原因分析及解决对策; 10. 注塑件尺寸偏差的原因分析及解决对策; 11. 注塑件透明度不足、强度不足(脆断)的原因分析及解决对策; 12. 学员自带产品问题解答。 第四部分:模具设计优化 实际上目前有相当部分产品品质问题是由模具设计不合理导致的,只是很多模具设计相关人员将责任推给了注塑相关人员。 1. 如何设计注塑车间生产OK的模具; 2. 如何设计注塑车间稳定、高效生产的模具; 3. 如何设计上档次的模具; 4. 浇口合理设计; 5. 流道合理设计; 6. 冷却水路合理设计; 7. 产品缩水率的设定与调整; 第五部分:模流分析技术应用(融汇于第三、四部分) 如何利用目前世界最强大的Moldflow模流分析技术快速地有效地预测问题、优化注塑工艺
薄壁注塑成型技术发展
薄壁注塑成型技术发展 由于3C产品向轻、薄、短、小方向发展得越来越快,所以薄壁注塑成型技术也受到人们的高度重视,而薄壁注塑成型数值模拟技术是薄壁注塑成型技术得以应用的重要保证.本文介绍了薄壁注塑成型技术产生的背景和科学意义,综述了薄壁注塑成型中的制品设计、模具设计、注塑机和材料选用以及薄壁注塑成型数值模拟技术的研究与应用概况,探讨了薄壁注塑成型数值模拟技术发展中所面临的一些关键问题,指出了薄壁注塑成型数值模拟技术的研究发展方向.关键词:薄壁注塑成型;模具设计;数值模拟;流长厚度比;冷凝层. 近年来,笔记本电脑和移动电话等3C(Computer, Communication and Consumer)产品更新换代的速度非常快,这类产品的设计理念正朝着"轻、薄、短、小"方向发展,同时人们对这些产品的需求也在快速增长,于是在常规注塑成型(Conventional Injection Molding, CIM)技术的基础上,薄壁注塑成型(Thin-Wall Injection Molding , TWIM)技术迅速发展起来.薄壁化因具有减小产品重量及外形尺寸、便于集成设计及装配、缩短生产周期、节约材料和降低成本等优点成为塑料消费行业追求的目标,已成为塑料成型行业中新的研究热点. 薄壁注塑成型技术是一种仅有十几年发展历史的新兴技术,其理论体系尚未形成,缺少系统性的研究,而薄壁注塑成型数值模拟研究也只是近几年才提出的,还有许多理论上和实践中的问题尚待解决.薄壁注塑成型技术的概念https://www.360docs.net/doc/fa8647260.html, 目前关于薄壁注塑成型还没有统一的定义,Mahishi和Maloney把其定义为流长厚度比L/T(L:Length,流动长度;T:Thickness,塑件厚度;L/T也简称为流长比)在100或者150以上的注塑为薄壁注塑;而Whetten和Fasset是这样定义薄壁注塑成型的:所成型塑件的厚度小于1mm,同时塑件的投影面积在50cm2以上的注塑成型.由此可见要给出一个统一的定义还是比较困难的;同时随着技术的发展,薄壁注塑成型定义的临界值也将发生变化,它应该是一个相对的概念. 常规注塑成型工艺已为人们所熟悉,但薄壁注塑成型则不然,因为随着壁厚的减薄,聚合物熔体在型腔中的冷却速度加剧,在很短的时间内就会固化,这使得成型过程变得复杂,成型难度加大,常规的注塑成型工艺条件已不能满足需要.常规注塑成型的一个不足就是填充过程和冷却过程往往是交织在一起的,但由于常规塑件的尺寸比较大,所以对成型过程影响不大,但在薄壁注塑成型中这个不足就成为致命的问题.所以,不能把常规注塑成型中的理论和操作简单地照搬到薄壁注塑成型中去.薄壁注塑成型中的制品设计、模具设计、注塑机及材料选用薄壁制品的设计思想和方法更为复杂,并进一步受到成型局限及材料选择的影响.薄壁制品要求应该具有高的冲击强度、良好的外观质量和尺寸稳定性,并能承受大的静态载荷,成型材料的流动性要好.设计过程中要重点考虑制品的刚性、抗冲击性和可制造性. 成型薄壁制品时一般需要专门设计的薄壁制品专用模具.与常规制品的标准化模具相比,薄壁制品的模具从模具结构、浇注系统、冷却系统、排气系统和脱模系统等都发生了重大变化.主要表现在以下几个方面: (1)模具结构:为承受成型时的高压,薄壁成型模具的刚度要大、强度要高.因此模具的动、定模板及其支承板重量较大,厚度通常比传统模具的模板要厚.支撑柱要多,模具内可能要多设置内锁,以保证精确定位和良好的侧支撑,防止弯曲和偏移.另外,高速射出速度增加了模具的磨损,因此模具要采用较高硬度的工具钢,高磨损、高冲蚀区(如浇口处)硬度应大于HRC55. (2)浇注系统:成型薄壁制品,特别是制品厚度非常小时,要使用大浇口,而且浇口应该大于壁厚.如是直浇口应设置冷料井,以减少浇口应力,协助填充,减少制品去除浇口时的损坏.为保证有足够的压力充填薄的模腔,流道系统中应尽可能减少压力降.为此,流道设计要比传统的大一些,同时要限制熔体的驻留时间,以防止树脂降解劣化.当是一模多腔时,浇注系统的平衡性要求远高于常规模具的要求.值得注意的是薄壁制品模具的浇注系统中还引入了两项先进技术,即热流道技术和顺序阀式浇口(SVG)技术. (3)冷却系统:薄壁制品不像传统壁厚件那样可以承受较大的因传热不均而产生的残余应力.为保证制品的尺寸稳定性,把收缩和翘曲控制在可以接受的范围内,就必须加强模具的冷却,确保冷却均衡.较好的冷却措施有在型芯
摄像头底座零件的注塑成型模拟分析【毕业作品】
摄像头底座零件的注塑成型模拟分析 摘要 目前,在我国制造行业出现了转型期,高效率,高质量的生产占据核心,新型的辅助制造工具也是蓬勃发展,然而moldflow(模流分析)却独树一帜,成为模拟仿真系统之中不可或缺的一份子。它成功的解决了传统设计制造的短板,低效率,高成本的计算,还有对技术人员的技术经验要求特别这高,这样很影响模具设计与生产的速度和质量,moldflow是利用计算机对产品的数据进行客观分析的软件,它具有客观性,高效性,低成本等特征,由于利用计算机辅助计算不再需要人工花费大量时间进行计算,试模,将很多大错误提前排除,避免模具成型后报废,降低成本。 关键词:仿真模拟;高效率;计算机数据计算;moldflow
目录 前言 (1) 1 模流分析的基本流程介绍 (2) 1.1 建立模型............................................................................ 错误!未定义书签。 1.2 参数设定 (3) 1.3 分析结果 (3) 2 moldflow实际案例分析....................................................... 错误!未定义书签。 2.1 基础分析............................................................................ 错误!未定义书签。 2.2 不同浇口对比分析 (7) 2.2.1 对比两制件的压力 (8) 2.2.2 制件充填时间的对比 (9) 2.2.3 气穴 (9) 2.2.4 熔接痕的对比 (10) 3 冷却系统对比分析 (12) 3.2制件冷却水路设计 (12) 3.2制件优化水路设计 (14) 总结 (17) 致谢 (18) 参考文献 (19)
注塑产品不良原因分析及解决方案
注塑成型品质改善原因分析 未射饱(缺料) 1.射出压力不足; 2.保压压力不足; 3.射出时间不足; 4.加料(储料)不足; 5.射料分段位置太小; 6.射出终点位置太小; 7.射出速度不够快; 8.射嘴﹑料管温度不够; 9.模具温度不够;10.原料烘干温度﹑时间不足;11.注塑周期太快,预热不足;12.原料搅拌不均匀;(背压不足,转速不够) 13.原料流动性不足(产品壁太薄);14.模具排气不足;15.模具进料不均匀;16.冷料井设计不合理;17.冷料口太小,方向不合理;18.模穴內塑胶流向不合理;19.模具冷卻不均匀;20.注塑机油路不精确﹑不够快速;21.电热系統不稳定,不精确;22.射嘴漏料,有异物卡住;23.料管內壁﹑螺杆磨损,配合不良; 毛边(飞边) 1.射出压力和压力太大; 2.锁模高压不够; 3.背压太大; 4.射出和保压时间太长; 5.储料延迟和冷却时间太长; 6.停机太长,未射出热料; 7.射出压.保压速度太快; 8.螺杆转速太快,塑胶剪切,磨擦过热; 9.料管温度太高.流延;10.模温太高﹑模腔冷却不均匀;11.注塑行程调试不合理;12.保压切换点,射出终点太大; 13.模具裝配组合不严密;14.合模有异物,调模位置不足;15.锁模机构不平行﹑精确;16.顶针润滑﹑保养不足;17.滑块﹑斜导柱配合压不到位;18.模腔镶件未压到位,撐出模面;19.进料口设计分布不均匀合理;20.产品设计导致某处內壁太薄和结尾处太远;21.小镶件组合方式不合理,易发生变形;22.镶件因生产中磨损﹑变形﹑圆角;23.镶件未设计稳固性﹑未抱合,加固;24.模腔內排气槽太深; 气泡(气疮) 1.射出﹑保压压力不足; 2.背压太小﹑原料不够扎实; 3.射出速度太快; 4.储料速度太快; 5.料管温度太高, 模具温度太低; 6.材料烘干温度﹑时间不足; 7.射退太多; 8.注塑周期太长(预热时间增加); 9.加料位置不足,射出终点太小; 10.前﹑后松退位置太长;11.机器油压不稳定;12.料管﹑螺杆压缩比不够;13.原料下料﹑搅拌不均匀; 14.料管逆流,有死角;15.模具进料口太小﹑模穴內流动不够快速;16.冷料井设计不当,冷料进入模穴;17.模具冷卻不当,模仁温度太高; 18.产品设计內壁太厚,內应力不均匀;19.原料添加剂不当,易分解析出;
立体光照成型的注塑模具工艺的综合模拟
立体光照成型的注塑模具工艺的综合模拟 摘要功能性零部件都需要设计验证测试,车间试验,客户评价,以及生产计划。在小批量生产零件的时候,通过消除多重步骤,建立了有快速成型形成的注塑模具,这种方法可以保证缩短时间和节约成本。这种潜在的一体化由快速成型形成注塑模具的方法已经被多次证明是可行的。无论是模具设计还是注塑成型的过程中,缺少的是对如何修改这个模具材料和快速成型制造过程的影响有最根本的认识。此外,数字模拟技术现在已经成为模具设计工程师和工艺工程师开注塑模具的有用的工具。但目前所有的做常规注塑模具的模拟包已经不再适合这种新型的注塑模具,这主要是因为模具材料的成本变化很大。在本文中,以完成特定的数字模拟注塑液塑造成快速成型模具的综合方法已经发明出来了,而且还建立了相应的模拟系统。通过实验结果表明,目前这个方法非常适合处理快速成型模具中的问题。 关键词注塑成型,数字模拟,快速成型 1引言 在注塑成型中,聚合物熔体在高温和高压下进入模具中。因此,模具的材料需要有足够的热性能和机械性能来经受高温和高压的塑造循环。许多研究的焦点都是直接有快速成型形成注塑模具的过程。在生产小批量零件的时候,通过消除多重步骤,直接由快速成型形成的注塑模具可以保证缩短时间和节约成本。这种潜在的有快速成型形成注塑模具的方法已经被证明成功了。快速成型模具在性能上是有别与传统的金属模具。主要差异是导热性能和弹性模量(刚性)。举例来说,在立体光照成型模具中的聚合物的导热率小于铝制的工具的千分之一。在用快速成型技术来制造铸模时,整个模具设计和注塑成型工艺参数都需要修改和优化,传统的方法是改变彻底的刀具材料.不过,目前还没有对如何修改这个模具材料的方法有根本的了解.在当前的模具中,仅仅改变一些材料的性能是不能得到一个合理的结果的。同样,使用传统方法的时候,实际生产的零件也会有出先次品。因此,研究出一个快速成型过程,材料和注塑模具之间的互动关系是非常火急的。这样就可以确定模具设计标准和快速模具的注塑的技术。 此外,计算机模拟是一种预测模塑件的质量的有效的方法。目前,商用仿真软件包已经成为模具设计师和工艺工程师在注塑过程中例行性的工具。不幸的是,目前常规注塑成型的模拟程序已经不再适用于这个快速成型模具,因为它极大的需要不同的刀具材料。例如,利用现在的仿真软件在铝和立体光照模具之间做个实验比较一下,虽然铝模具模拟植的部分失真是合理的,但是结果是不可以接受的,因为误差超过了百分之五十。在注塑成型中,失真主要是由于塑料零件的收缩和翘曲,模具也是一样的。对于通常模具,失真的主要因素是塑料件的收缩和翘曲,这个在目前的模拟中能测试准确。但是对于快速成型模具,潜在的失真会更多,在当前的测试中,其中就会有些失真会被忽视。例如,用一个简
基于MPI技术的注射成型流动数值模拟研究
2008年第27卷 1月 第l期 机械科学与技术 Mechallicalscience肌dTechnolo贸forAe瑚paceE蟛neering J髓uary2008 V01.27No.1俞鸿斌 基于MPI技术的注射成型流动数值模拟研究 俞鸿斌1,赵阳2,王志明1 (1金华职业技术学院机电工程学院,浙江金华321017;2浙江树人大学,杭州310015) 摘要:以塑料注射成型流动分析软件MPI为工具,对注塑过程中流动数值模拟技术进行了深入研究,建立了塑料熔体流动过程的数学模型。对注射成型模型进行了简化数值计算,以更清楚的认识各物理变量对成型过程的影响,并通过实例说明MPI技术在注射成型流动数值模拟技术的合理应用,用软件预测了温度、压力分布,注射充填型腔计算机模拟,以指导模具设计工作。 关键词:注射流动模拟分析;注射成型;流动模拟;数学模型 中图分类号:TG76;TQ320.6文献标识码:A文章编号:l003—8728(2008)01旬127旬3 N啪ericalFlowSimlnationofI哪ectionM0lIling YuHongbinl,zhaoYan驴,wangzhimin91 (1Depanment0fMech叭ical趴dElectIicalEngin∞ring,JiIIll岫CouegeofProfessionandTechIlology,JiIllIM321017; 2 zheji锄gShumnuIIive墙蚵,H觚铲hou310015) Abst腿ct:WemakeuseoftllesoftwareMPI(MoldnowPlastichIsigllt)tocarryoutn啪ericalflowsi瑚雌l撕帆ofinjectionmolding.Wefi璐testablish山emat}lematicalmodel0ftllenowpmce8sofmeltingpl黯tic,觚dt}Ien8impli-fj,tlleabovemDdelino柑ertohaveaclearerunderst蛐ding0ftIIeeffects0fdi妇ferentphysicalvariable8∞tllemold—ingproce瞄.Finauy,蚰ex跚pleis舀Ventoshowthe印plicationofmoldingpIDce88’snumericalnow8imul撕on.Keywords:moldnowplasticinsight;injectionmolding;now8imulation;matllematicalmodel 注射成型是现代塑料工业中极为重要的一种加工技术,适于大批量生产形状复杂、尺寸要求精确的塑料制品。注射流动模拟分析可以预测熔体流经流道、浇口充填型腔的过程,帮助优化产品和型腔设计,在注射成型过程中有很高的工程应用价值…。 通过对成型加工过程进行数值模拟,研究加工条件的变化规律,预测制品的结构和性能,选择制品、模具设计及工艺条件的最佳方案,使成型加工从一项实用技术变为一门应用科学呤J。流动模拟的目的是预测塑料熔体流经流道、浇口并充填型腔的过程,计算流道、浇口及型腔内的压力场、温度场、速度场、剪切应变速率及剪切应力分布,并将结果以图形等值线图和阴影图的形式显示在计算机屏幕上∞】。通过流动模拟可优化浇口布置及注射工艺参数(料温、模温、注射时间等),预测所需的注射压力及锁模力并可能出现的短射、不合理的熔接线位置、气穴等缺陷H,5J。 收稿日期:2007一04—19 作者简介:俞鸿斌(1971一),副教授,硕士,研究方向为数控技术,模具cAD/cAM/cAE等,确hylIb@163.com 本文就注塑成型中流动数值模拟技术问题进行研究,根据注射流动模拟理论,首先建立了流动过程的数学模型,并对注射成型模型进行了简化,得到了易于数值求解的数学模型,可以更清楚的认识各物理变量对成型过程的影响。最后通过实例说明了注射成型流动数值模拟技术的合理应用。 l注射流动过程的数学描述 1.1粘性非牛顿流体力学基本方程 塑料熔体充模过程可以认为是粘性不可压缩非等温流动与传热过程,它总是伴随着与内摩擦、传热有关的能量耗散过程,可以采用粘性不可压缩流体的基本方程来描述哺】。 (1)连续性方程 上挈+v?秽=o(1) Pu‘ 在不可压缩条件下,连续性方程退化为 V?矿=O(2)利用直角坐标系分量可表示为 塑+丝+塑:O (3) 万方数据
注塑常见问题及分析
1.塑料缩水就是塑料收缩的问题,很少有资料谈过.塑料收缩有四种情况:热收缩、相变收 缩、取向收缩、压缩收缩与弹性恢复。收缩过程有三部分组成:浇口凝固前的收缩、冷却收缩和脱模后收缩。 2. 缩水的主要原因:1,注射量不够2,熔体温度过高3,注射压力和保压压力过小4, 注射时间和保压时间过少5,注射速度过大6模具温度不当 3. 缩孔的主要原因:1,注射量不够2,注射压力太低3,注射速度不当4,模具温度 过低 4.注塑件缺胶、不饱模---Short Shot 原因分析 ?塑胶熔体未完全充满型腔。 ?塑胶材料流动性不好。 ?对策 ?制品与注塑机匹配不当,注塑机塑化能力或注射量不足。 ?料温、模温太低,塑胶在当前压力下流动困难,射胶速度太慢、保压或保压压力过低。 ?塑料熔化不充分,流动性不好,导致注射压力损失大。 ?增加浇口数,浇口位置布置要合理、多腔不平衡排布充填。 ?流道中冷料井预留不足或不当,冷料头进入型腔而阻碍塑胶之正常流动,增加冷料穴。 ?喷嘴、流道和浇口太小,流程太长,塑胶填充阻力过大。 ?模具排气不良时,空气无法排除。 5.披峰(毛边)---Burring & Flashing ?原因分析 ?塑胶熔体流入分模面或镶件配合面将发生-Burring。 ?锁模力足够,但在主浇道与分流道会合处产生薄膜状多余胶料为Flash ?对策 ?锁模力不足,射入型腔的高压塑胶使分模面或镶件配合面产生间隙,塑胶熔体溢进此间隙。 ?模具(固定侧)未充分接触机台喷嘴,公母模产生间隙。(没装紧) ?模温对曲轴式锁模系统的影响。 ?提高模板的强度和平行度。 ?模具导柱套摩损/模具安装板受损/拉杆(哥林柱)强度不足发生弯曲,导致分模面偏移。 ?异物附着分模面。排气槽太深。 ?型腔投影面过大/塑胶温度太高/过保压。 6.?表面缩水、缩孔(真空泡)--Sink Mark & Void & Bubble ?原因分析 ?制品表面产生凹陷的现象。 ?由塑胶体积收缩产生,常见于局部肉厚区域,如加强筋或柱位与面交接区域。 ?制品局部肉厚处在冷却过程中由于体积收缩所产生的真空泡,叫缩孔(Void)。 ?塑胶熔体含有空气、水分及挥发性气体时,在注塑成型过程空气、水分及挥发性气体进入制品内部而残留的空洞叫气泡(Bubble)。 ?对策
注塑成型充填过程的数值模拟技术
注塑成型充填过程的数值模拟技术 王利霞申长雨 郑州大学檬塑模具国家工程研究中心,郑州、450002 注塑成型充模流动过程是一个相当复杂的物理过程,非牛顿的高温塑料熔体在压力的驱动下通过流道、浇口向温度较低的模腔充填,塑料熔体压力、温度、剪切速率等物理量在充模过程中的变化.将直接影响者塑件的最终彤状、内部结构、取向和残余应力。模具设计人员应综合考虑这些因素,才能正确设计出合格的模具。注射模cAE技术的出现,使人们在模具制造之前就能预测熔体的充填状况,以便及早发现问题,修改图纸而不是返修模具。 l数学模型 注塑模充填模拟基于型腔内熔体充填机理和流变学基本方程,视聚合物熔体在型腔中的流动为粘性不可压流体的流动,忽略垂直于流动方向的速度分量,进行合理简化,建立了广义Hele-¥haw流动的数学模型。 连续性方程旦㈦+曼!坐尘=0n) 0xay。 运动方程罢一导(卵要b:o(2) ujOZ口= 罢一_c3(叩_dv)=o(3) vyo=口z 能量方程,o(乓拿+。导£+,要马:I要≥+口,。(4) ul“^u,_z 其中,tl、v分别为x、y方向的速度分量,P为密度,Cp、k分别是比热窖和热传导率,P、T分别代表熔体的压力和温度,x、Y为中面坐标,z为厚度方向坐标,Y为剪切速率,n为剪切粘度,可采用Cross模型。 2数值离散 由于注塑件大多是薄壁件,采用中面模型处理三维问题,即沿型腔中面划分为三角形单元,对型腔厚度方向和时间采用有限差分。计算区域离散后,引入控制体积概念,即对于每一个三角形单元,通过连结形心和边的中点而将单元划分成三个子体积,相应于每个节点的控制体积是由与此节点相连的所有子体积构成的,它是一多边形区域。 1)温度场计算: 在充填过程中,聚合物熔体粘度对温度具有高度敏感性,温度分布在注塑成型模拟中十分重要。采用有限差分法求解能量方程时,由于热传导、热对流项和粘性热项对每个控制体积结点的贡献在单元内边界处可能是不连续的,需加权平均。为了保持数值计算稳定性,采用“上风法”处理对流项和粘性热项,从而可得到每一个结点的能量差分方程。利用松弛法求解能量方程可得到流动区域的温度场分布。 2l压力场计算: 假设流动过程中熔体不可压,根据每个结点的控制体积的质量守恒关系可建立压力场求 曲8
注塑缺陷原因分析及改善对策
龙源期刊网 https://www.360docs.net/doc/fa8647260.html, 注塑缺陷原因分析及改善对策 作者:李涛程详奎 来源:《丝路视野》2017年第22期 [摘要]塑料件注塑缺陷严重影响塑料件的使用效果。对工艺的准确把握成为保障塑料件质量的关键方式。注塑除了对相关工具和设备有较高的要求外,还需要技术人员对常见的缺陷进行总结分析,避免反复出现同类缺陷。本文对注塑缺陷原因分析及改善对策进行分析和探讨。 [关键词]注塑;缺陷原因;改善对策 一、流涎缺陷以及熔融塑料粘度原因及改善对策 流涎问题是很多注塑机运作过程中会出现,主要原因是喷嘴温度过高。在模具没有合模之前,熔融塑料就已经流入了定模一侧。在温度较低的模具流道中就会出现凝固,导致熔融塑料不能顺利流入模具中。流涎问题一般可通过降低机筒前端和喷嘴的温度、减少机筒的储料量,增加松退和减低背压压力来解决。 在温度较低的条件下,熔融塑料会快速降温,增加熔融塑料的粘性,导致其流动性随之变低,注塑出现的塑料件会出现明显的接痕和填充缺陷。在温度不是极低的情况下,一般使用加大注射压力与注射速度的方法给予改善。 二、黑条、烧痕缺陷原因及改善对策 在实际的注塑过程中黑条、烧痕也是容易出现的一种现象。其表征特点是呈一条黑色条纹状,若是料筒有相关的杂质就会产生这种情况,树脂在实际的热分解当中,也会造成黑条以及烧痕产生。在树脂热分解烧结到螺杆当中之后,清除的不彻底就会产生黑条和烧痕。在塑料成型的材料中,会添加一些着色剂。这些着色剂很容易被分解,产生烧痕。对于树脂所产生烧痕的主要原因有:第一,螺杆料筒温度设定不合理。第二,注射速度和标准不相符,注射速度太快,在成型阶段超前分解的树脂就会出现烧痕。第三,螺杆旋转速度不科学造成树脂受热过多,所以形成烧痕。因此,就需要从这三方面人手:(1)在机械设备方面,不论是料筒温度不合适使树脂分解受到影响,还是料筒内的喷嘴和螺杆的螺纹、止回阀等部位使得树脂的滞流状况形成的烧痕。(2)模具,加排气槽反排气杆等。(3)成型条件方面的改善措施,背压不得超过300Mpa,可避免料筒部分温度过高,螺杆转速在40至90r/min范围内,可避免过热。 三、溢料(飞边)缺陷原因分析及改善对策 溢料又称飞边、毛边或披锋等。制品生产过程中,模具的锁模力低,难以保持成型整个过程模具紧闭,模具结构变形在分型线处有缝隙,在型腔压力较高处便会造成溢料。溶胶速度过高或射胶压力过大导致溶胶流动性过高,不当的排气孔、槽设计,也会导致溢料的产生。需要从以下两个方面人手。第一,有关工艺参数的改进对策。(1)依据制品壁厚程度,调整射胶
基于DOE法的注塑成型工艺仿真优化
摘要 注塑成型制品质量控制方面存在的困难主要来源于力学的复杂性和在温度、压力波动下材料行为的不可预测性,研究工艺参数对注塑制品质量的影响关系,建立工艺参数与制品质量之间的关系模型,并用DOE法对工艺进行仿真优化是注塑制品工艺优化的前提。 本文选用半结晶型和无定型ABS两种材料,针对一维流动平板两个方向上的收缩、强度,熔接线强度、制品重量及沉降斑等质量指标进行了实验研究。研究了工艺参数对质量指标的影响及因素之间的交互作用。本文主要工作包括以下几方面: 1 工艺参数对制品质量的交互影响分析;2 应用DOE法结合析因分析结果;3.CAE技术结合DOE法进行设计,并用MOLDFLOW进行仿真分析,为质量控制技术提供了工艺模型。 关键词: 注塑成型,正交实验,Moldflow,三维建模,工艺仿真优化,实验设计
Abstract Quality control of injection molding products, mainly difficulties from that exist in the complexity of process dynamics and in the temperature and pressure fluctuations unpredictable behavior of materials, of process parameters on product quality of injection molding between the relationship,DOE method with simulation and optimization technology of injection molding products, process optimization is a prerequisite. Semi-crystalline and amorphous ABS we usd in this paper,For a flat that two-dimensional flow direction shrinkage, strength, weld line strength, weight and sink marks and other products, the quality indicators studied. In this paper, include the following:1. Process parameters on product quality of interaction analysis;2. Application of DOE method with the results of factorial analysis;3. CAE design method combined with DOE,Simulation and analysis with MOLDFLOW,quality control technology provides for the process model. Key words:Injection Molding,Orthogonal,Moldflow,Three-dimensional modeling,Process simulation and optimization,design of experiment.
《注塑成型计算机模拟》--英语单词
Thermosetting热固性塑料 Thermoplastic热塑性塑料 plastic industry塑料(工业)行业 blow molding die for plastics塑料吹模机 standard die components for plastics塑料模具标准化零部件 thermoforming machine for plastics塑料热成型机 foaming mold for plastics泡沫塑料模型 plastic molding press塑料制品成型压力机 other plastics converting machine其它塑料加工机械 compression molding machine压塑机 extruder double-screw for plastics塑料加工用双螺杆挤压机 extruder single-screw for plastics塑料加工用单螺杆挤压机 laminating machine层压机 compression mold压缩模(也叫压制模) parting surface分型面 transfer mold压注模(也称传递模) flash-type mold溢出式压缩模 semi-positive mold半溢式压缩模 positive mold不溢式压缩模 portable transfer mold移动式压注模 thermosetting resin binder热固树脂粘结剂 dwell pressure保压压力 dwell time保压时间 filling velocity充填速度 mold for plastics塑料成型模具(简称塑料模)mold for thermoplastics热塑性塑料模 Draft脱模斜度
为什么要进行注塑成型模拟分析
为什么要进行注塑成型模拟分析 一.为什么要进行注塑成型模拟分析 1 塑料及其性质由于塑料的内部结构比金属复杂,故掌握其性能特点也就比较困难。然而要想有效地进行塑料的注射成型,就应该对其与成型有关的性能有所了解。 1).比热容不同塑料的比热容差别较大,并随着温度的变化而变化。 2). 热扩散系数塑料的热扩散系数对成型中材料的温度与冷却有较大关系,并且也随着温度的变化而变化。 3). 密度/比容塑料的密度与温度有强烈的依赖关系,温度升高时密度较小。注射成型过程中,温度不断变化,故材料的密度也在不断变化,这种变化对产品的质量有重要影响。 4). 热降解、分解温度塑料因加工温度偏高,或在较高温度下停留时间过长,从而使平均分子量降低的现象称为热降解。如出现这种情况,则熔体的粘度降低,制品出现飞边、气泡和银丝,机械性能变差,如弹性消失、强度降低等。分解温度是指聚合物因受热而迅速分解为低分子的温度。显然分解温度是注射成型温度的上限。 5). 剪切变稀塑料熔体的粘性系数并非常数(非牛顿流体),而是随剪应变率的增加而降低,这种现象称为剪切变稀。不同塑料的剪切变稀程度差别较大。因为粘度特性在注射成型工艺中是一个非常重要的因素,故剪切变稀对注射成型的压力、温度等有重要影响
2. 应用注射模流动模拟软件的必要性塑料材料性能的复杂性决定 了注射成型过程的复杂性,有些注射成型问题连有经验的模具设计师也很难把握。同时,注塑制品的质量也主要取决于注射成型过程,塑料熔体注入模具后的流动行为在决定制品质量方面具有头等重要意义,因此很有必要对充模过程进行有效地分析。注塑过程中的流动分析在国外已得到了普遍的应用,它建立在计算机与CAD被广泛应用的基础上,其目的是预测塑料熔体注入模具型腔时的流动情况,从而判断熔体流动给注塑件质量带来的影响。流动模拟软件的应用主要包括三个方面:第一是利用软件来预计所设定注塑方案的压力、温度等的分布;第二是利用预计的压力、温度等的分布来改善模具和塑料制品的设计;第三是对多个候选的注塑方案进行比较优化,选择最佳方案。传统的注塑模设计首先考虑的是模具本身的需要,之后考虑的才是注塑制品的需要。换句话说,传统的注塑模设计是把塑料熔体在流道和型腔中的流动放在第二位考虑的。例如,常规的模具设计通常是根据经验确定浇口的数量和位置,而不是根据流动分析来确定这些参数,结果经常是浇口数量偏多、尺寸偏大。但是在市场经济条件下,产品的质量与成本已成为企业生存发展的生命线,注射成型模拟软件可以辅助企业确立竞争优势。 二.如何应用注塑成型分析报告指导模具设计 1. 注塑条件对制品成型的影响 1). 塑料材料如前所叙,塑料材料性能的复杂性决定了注射成型过程的复杂性。而塑料材料的性能又因品种不同、牌号不同、生产厂