不锈钢板中锰_钛_铝_铌夹杂物的原位统计分布分析
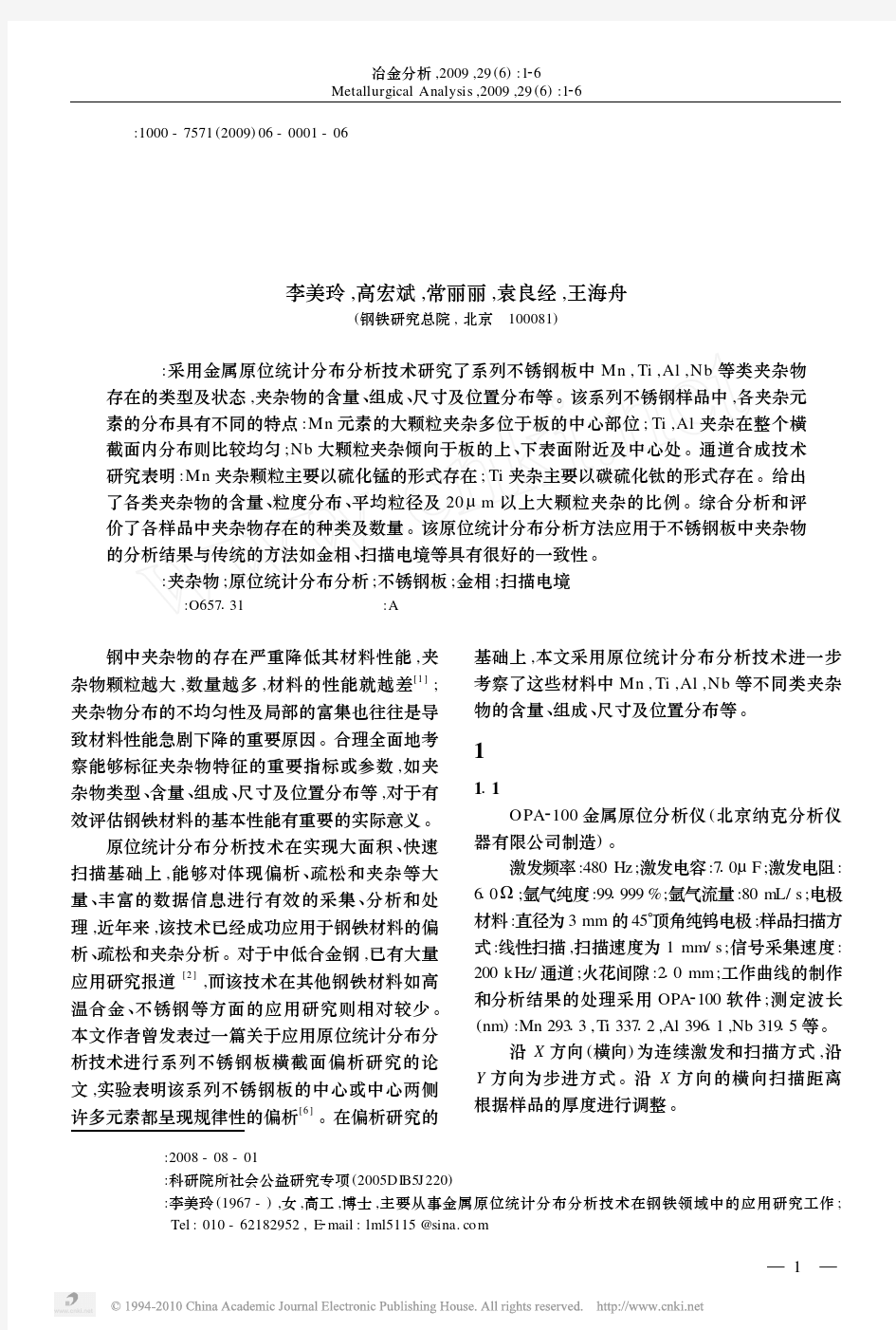
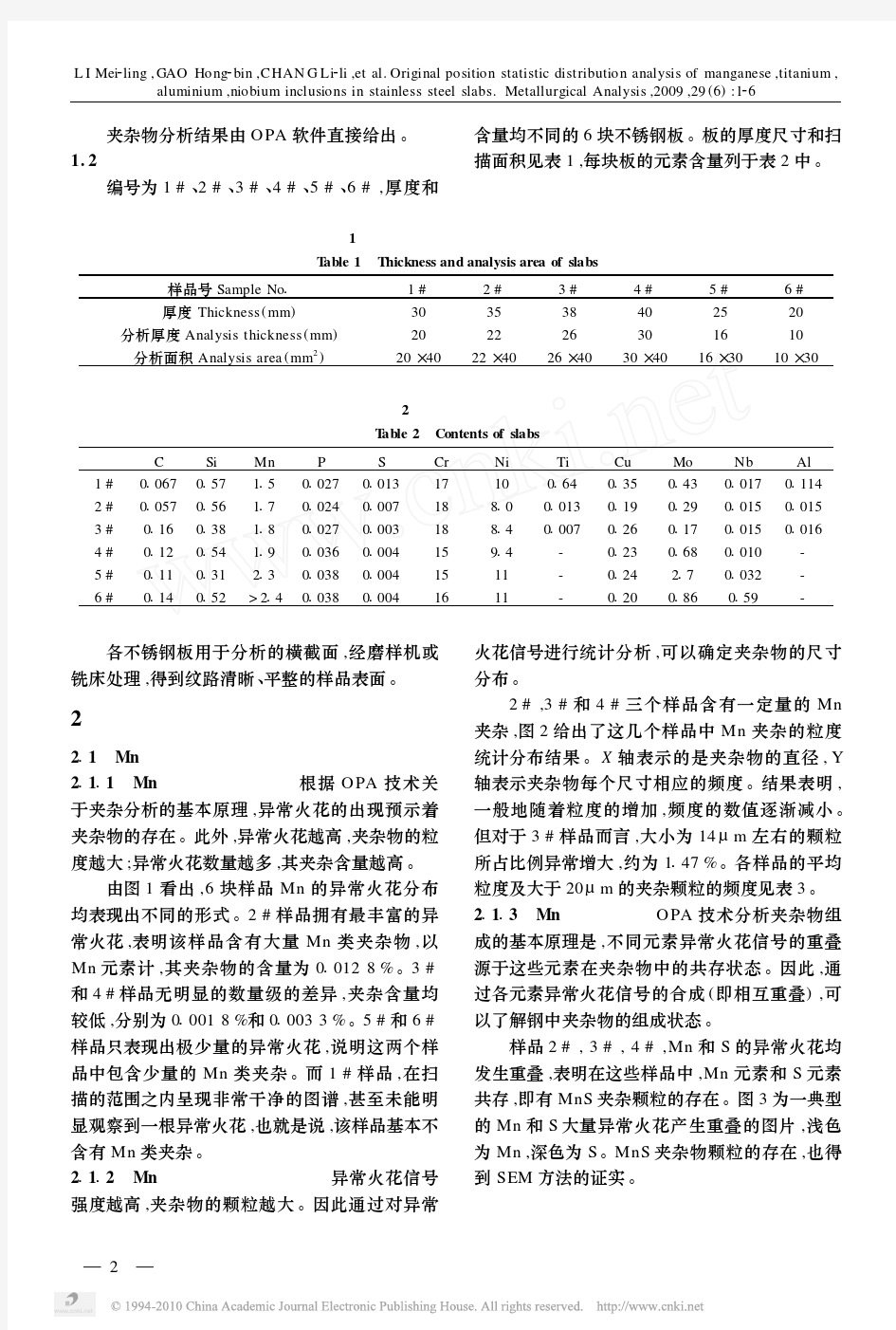
加氢脱硫催化剂载体的研究现状
加氢脱硫催化剂载体的研究现状 王万福 (湖南理工学院化学化工学院09应用化学班,学号14091801290)摘要:介绍了目前加氢脱硫催化剂载体的种类和研究现状,包括氧化物载体、介孔分子筛载体、活性炭载体、酸碱载体等。分析了不同载体所具有的的优缺点,并展望了未来载体的研究方向。 关键词:加氢脱硫;催化剂;载体 Latest researches in the supports of HDS catalyst Wang Wanfu (09 Applied Chemistry of The Department of Chemical Engineering , Hunan Institute of Techology, Student No.14091801290) Abstract:Introduced species and the present status of the hydrodesulfurization catalyst support, including the oxide carrier, the carrier of mesoporous molecular sieves, activated carbon carrier, and acid-base carrier. Different carriers have advantages and disadvantages, and future research directions of the future carrier. Keywords:Hydrodesulfurization;Catalyst;Carrier 随着人们对环护意识的不断增强,环保法对尾气排放及其相应成品油中有害杂质的含量要求更加苛刻。另外,随着石油重质化,S、N 等杂原子化合物的含量也逐渐升高,易引起产品加工过程毒化,并且脱除困难。催化剂制造技术作为加氢脱硫技术的核心部分,近年来,人们通过研究各种类型的脱硫催化剂载体来改善催化剂的性能。本文针对不同时期深度加氢脱硫催化剂载体的研究进行了综述。 1 载体 载体在催化剂中起担载活性组分、提高活性组分和助剂分散度的作用,在一定程度上也参与了某些反应。加氢脱硫催化剂的载体主要是γ-A12O3,随着研究的深入,人们发现TiO2、ZrO2、活性炭、复合氧化物、介孔分子筛等更适合做加氢脱硫催化剂的载体,并进行了大量的研究。在加氢脱硫催化剂载体研究方面,主要从以下三个方面进行: (1)对γ-A12O3进行进一步研究,提高其表面积、孔结构等。 (2)使用TiO2、ZrO2、活性炭、介孔分子筛等载体代替γ-A12O3。 (3)在γ-A12O3中添加TiO2、SiO2等构成复合载体,以提高催化剂活性组分的分散度或
钢中夹杂物控制原理修订稿
钢中夹杂物控制原理 WEIHUA system office room 【WEIHUA 16H-WEIHUA WEIHUA8Q8-
钢中夹杂物控制原理钢中氧的存在形式 T[O]=[O]溶+[O]夹 (1)转炉吹炼终点: [O]夹=>0,T[O]→[O]溶=200~1000ppm [O]溶决定于: l 钢中[C],转炉吹炼终点钢中[C]与a[O] 关系如图 l 渣中(FeO); l 钢水温度。 1 顶底复吹转炉炉龄 C–Fe的选择性氧化平衡点 根据式 [C] + [O] = {CO} (1) lg (Pco/ac* [%O])= 1149/T–2.002 以及反应 [Fe] + [O] = (FeO) (2) lg aFeo/[%O] = 6317/T – 2.739 得到反应(FeO)+ [C] = [Fe] + {CO} (3) lg (Pco/ac* aFeo)= –5170/T+4.736 结论钢液中C-Fe的选择性氧化平衡点为[C]=0.035%,也就是说终点[C] < 0.035%时,钢水的过氧化比较严重。图1-1的统计数据也说明了这点。同时由式(1)可以求出此时熔池中的平衡氧含量为740ppm。 理论分析
1)终点 时钢水的 当终点[C]在0.02~0.04Ⅰ)有些 2)温度对氧含量的影响 200400 600800100012001400 16001800160016201640166016801700172017401760 终点温度(℃)终点氧含量(p p m )
在终点[C] = 0.025~0.04%时,终点氧含量虽然较分散,但总的趋势是随着终点温度的升高,终点氧基本呈上升趋势。 渣中(FeO+MnO )增加,终点[O]有增加趋势;
实验五 非金属夹杂物的分析与评定
实验五 非金属夹杂物的分析与评定 (验证性) 一、实验目的及要求 1.掌握钢中非金属夹杂物的分类与形态特征。 2.掌握使用标准评定钢中非金属夹杂物的级别。 二、实验原理 钢铁中的非金属夹杂物的出现是不可避免。钢中非金属夹杂物的金相检验主要包括夹杂物类型的定性和定量评级。夹杂物的检验评定可按照GB/T10561-2005《钢中非金属夹杂物显微评定方法》执行。 1、检验钢中的非金属夹杂物的必要性 因为非金属夹杂物破坏了金属基体的连续性、均匀性,易引起应力集中,造成机械性能下降,导致材料的早期破坏,其影响程度主要取决于夹杂物的形状、大小、分布和聚集状态。 钢中夹杂物的检验一般在出厂前钢厂检验或者收货单位验收时检验。 2、钢中非金属夹杂物的来源 a)内在的:包括①铁矿石②钢厂在冶炼时,用Si、Al脱氧造成,反应式: 3FeO + 2Al → 3Fe + Al2O3 2FeO + Si → 2Fe + SiO2 b)外来的:浇铸过程卷入的耐火材料、炉渣等。 3、制样要求 a、取样时沿轧制方向,磨制纵向截面观察夹杂物大小、形状、数量,横向截面观察夹杂物从边缘到中心的分布。试样表面无划痕、无锈蚀点、无扰乱层。 b、淬火以提高试样的硬度,保留夹杂物的外形。 c、试样表面不浸蚀。 4、非金属夹杂物的分类 a、氧化物:FeO、MnO、Cr2O3、Al2O3; b、硫化物:FeS、Mn S及其共晶体; c、硅酸盐:2FeO·SiO2、2MnO·SiO2; d、氮化物:TiN、VN; e、稀土夹杂物 5、非金属夹杂物的金相鉴别方法
主要是指利用光学显微镜中的明场、暗场和偏振光灯照明条件下夹杂物的光学反映差异,以及在标准试剂中腐蚀后,夹杂物发生化学反应而出现色差及侵蚀程度的不同来区分鉴别。 a明场:检验夹杂物的数量、大小、形状、分布、抛光性和色彩。不透明夹杂物呈浅灰色或其他颜色,透明的夹杂物颜色较暗。 b暗场:检验夹杂物的透明度、色彩。透明夹杂物发亮,不透明夹杂物呈暗黑色、有时有亮边。 c偏光:检验夹杂物的各向同性和各向异性,色彩、黑十字现象。 金相法鉴定夹杂物的优点是简单直观,易与钢材的质量联系起来;缺点是不能确定夹杂物的成分和晶体结构。 6、非金属夹杂物的特征 具体形貌如图: a)硫化物主要有硫化铁(FeS)和硫化锰(MnS),以及它们的共晶体等。在钢材中,硫化物常沿钢材伸长方向被拉长呈长条状或者纺锤形,塑韧性较好。在明场下,硫化铁呈淡黄色,硫化锰呈灰蓝色,而两者的共晶体为灰黄色;在暗场下一般不透明但有明显的界限,硫化锰稍呈灰绿色;在正交偏光下都不透明,转动载物台一周,硫化铁有四次明亮、四次消光,呈各向异性,硫化锰及其共晶体都为各向同性。图3-2-20,3-2-21,3-2-23,3-2-27 b)氧化物常见氧化物有氧化亚铁(FeO)、氧化亚锰(MnO)、氧化铬(Cr2O3)、氧化铝(Al2O3)等。压力加工后,它们往往沿钢材延伸方向呈不规则的点状或细小碎块状聚集成带状分布。在明场下,它们大多呈灰色;在暗场下,FeO不透明,沿边界有薄薄的亮带;MnO透明呈绿宝石色;Cr2O3不透明,有很薄一层绿色;Al2O3透明,呈亮黄色。在偏光下,FeO、MnO呈各向同性,Cr2O3、Al2O3呈各异性。二氧化硅(SiO2)也是常见的氧化物。在明场下呈球形,深灰色;在暗场下无色透明,在偏光下呈各向异性、透明,并称黑十字现象。 图3-1-1,3-1-4,3-1-7,3-1-8,3-1-10,3-1-11,3-1-16,3-1-17,3-1-183-1-19,3-1-20,3-1-36,3-1-34 c)硅酸盐夹杂物来源于炼钢时加入Si-Ca脱氧剂或者与耐火砖发生作用。常见的硅酸盐夹杂物有铁橄榄石(2FeO·SiO2)、锰橄榄石 (2MnO·SiO2)、复合铁锰硅酸盐(nFe·mMnO·pSiO2)以及硅酸铝(3Al2O3·2SiO2)等。在明场下均呈暗灰色,带有环状反光和中心两点;在暗场下,一般均透明,并带有不同的色彩;在偏光下,除多数铁
铝合金挤压型材常见缺陷及其解决办法
建筑高强度6063铝合金型材以其良好的塑性和热处理后获得高强度、低重量建筑型材、良好的防锈蚀自防能力以及阳极氧化处理后可获得表面华丽多色泽等诸多优点而被广泛应用于建筑外装饰面材和结构承力构件。但在生产过程中经常会出现一些缺陷而导致使产品质量低下,成品率降低.生产成本增加,效益下降,最终导致企业的市场竞争能力下降, 造成工程不安全不可靠、社会不安全、不合谐的严重后果。 因此,从根源上着手解决6063(LD31)铝合金挤压型材质量的缺陷问题是企业提高自身竞争力的一个极其重要环节。作者根据多年耒在铝型材生产实践中对此6063(LD31)铝合金挤压型材生产过程中常见缺陷及其解决方法作一下小结和众多同行者交流,以期相互促进共同提高,确保产品质量以增强企业竞争力获得更大经济效益。 1、型材表面:划伤、擦伤、碰划 原因:1、铸锭表面附着杂物 2、铸锭成分偏析,表面存在大量偏析浮出物 3、一而铸锭又未进行均匀化处理或均匀化处理效果不好时铸锭内存在一定数量的坚硬的金属颗粒.在挤压过程中金属流经工作带时这些偏析浮出物或坚硬的金属颗粒附着在工作带表面或对工作带造成损伤,最终对型材表面造成划伤。 4、模具型腔或工作带上有杂物,模具工作带硬度较低,使工作带表面在挤压时受伤而划伤型材。 5、出料轨道或摆床上有裸露的金属或石墨条内有较硬的夹杂物.当其与型材接触时对型材表面造成划伤; 6、在叉料杆将型材从出料轨道上送到摆床上时,由于速度过快造成型材碰伤; 7、在摆床上人为拖动型材造成擦伤; 8、在运输过程中型材之间相互摩擦或挤压造成损伤。 解决方法:1、严格对铸锭化学成分质量的控制; 2、提高模具修理质量, 3、提高模具制造精度及模具定期氮化并严格执行氮化工艺参数; 4、用软质毛毡、塑胶条将型材与辅具隔离.尽量减少型材与辅具的接触损伤; 5、生产中要轻拿轻放,尽量避免随意拖动或翻动型材; 6、在料框中合理摆放型材,尽量避免相互摩擦。 2、力学性能不合格 原因:1、挤压时温度过低,挤压速度太慢,型材在挤压机的出口温度达不到固溶温度,起不到固溶强化作用; 2、型材出口处风机少.风量不够.导致冷却速度慢.不能使型材在最短的时间内降到200C°以下.使粗大的Mg2Si过早析出.从而使固溶相减少.影响了型材热处理后的机械性能; 3、铸锭成分不合格,铸锭中的Mg、si含量达不到标准要求; 4、铸锭未均匀化处理,使铸锭组织中析出的Mg2sj相无法在挤压的较短时间内重新固溶,造成固溶不充分而影响了产品性能; 5、时效工艺不当、热风循环不畅或热电偶安装位置不正确,导致时效不充分或过时效。 解决办法: 1、合理控制挤压温度和挤压速度,使型材在挤压机的出口温度保持在最低固溶温度以上; 2、强化风冷条件,有条件的工厂可安装雾化冷却装置,以期达到6063合金冷却梯度的最低要求: 3、加强铸锭的质量管理; 4、对铸锭进行均匀化处理; 5、合理确定时效工艺,正确安装热电偶。正确摆放型材以保证热风循环通畅。 3、形位及尺寸超差 原因:
铝合金常见缺陷
6063铝合金型材以其良好的塑性、适中的热处理强度、良好的焊接性能以及阳极氧化处理后表面华丽的色泽等诸多优点而被广泛应用。但在生产过程中经常会出现一些缺陷而致使产品质量低下,成品率降低,生产成本增加,效益下降,最终导致企业的市场竞争能力下降。因此,从根源上着手解决6063铝合金挤压型材的缺陷问题是企业提高自身竞争力的一个重要方面。笔者根据多年的铝型材生产实践,在此对6063铝合金挤压型材常见缺陷及其解决办法作一总结,和众多同行交流,以期相互促进。 1 划、擦、碰伤 划伤、擦伤、碰伤是当型材从模孔流出以及在随后工序中与工具、设备等相接触时导致的表面损伤。 1.1 主要原因 ①铸锭表面附着有杂物或铸锭成分偏析。铸锭表面存在大量偏析浮出物而铸锭又未进行均匀化处理或均匀化处理效果不好时,铸锭内存在一定数量的坚硬的金属颗粒,在挤压过程中金属流经工作带时,这些偏析浮出物或坚硬的金属颗粒附着在工作带表面或对工作带造成损伤,最终对型材表面造成划伤; ②模具型腔或工作带上有杂物,模具工作带硬度较低,使工作带表面在挤压时受伤而划伤型材; ③出料轨道或摆床上有裸露的金属或石墨条内有较硬的夹杂物,当其与型材接触时对型材表面造成划伤; ④在叉料杆将型材从出料轨道上送到摆床上时,由于速度过快造成型材碰伤; ⑤在摆床上人为拖动型材造成擦伤; ⑥在运输过程中型材之间相互摩擦或挤压造成损伤。 1.2 解决办法 ①加强对铸锭质量的控制; ②提高修模质量,模具定期氮化并严格执行氮化工艺; ③用软质毛毡将型材与辅具隔离,尽量减少型材与辅具的接触损伤; ④生产中要轻拿轻放,尽量避免随意拖动或翻动型材;
⑤在料框中合理摆放型材,尽量避免相互摩擦。 2机械性能不合格 2.1 主要原因 ①挤压时温度过低,挤压速度太慢,型材在挤压机的出口温度达不到固溶温度,起不到固溶强化作用; ②型材出口处风机少,风量不够,导致冷却速度慢,不能使型材在最短的时间内降到200℃以下,使粗大的Mg2Si过早析出,从而使固溶相减少,影响了型材热处理后的机械性能; ③铸锭成分不合格,铸锭中的Mg、Si含量达不到标准要求; ④铸锭未均匀化处理,使铸锭组织中析出的Mg2Si相无法在挤压的较短时间内重新固溶,造成固溶不充分而影响了产品性能; ⑤时效工艺不当、热风循环不畅或热电偶安装位置不正确,导致时效不充分或过时效。 2.2 解决办法 ①合理控制挤压温度和挤压速度,使型材在挤压机的出口温度保持在最低固溶温度以上; ②强化风冷条件,有条件的工厂可安装雾化冷却装置,以期达到6063合金冷却梯度的最低要求; ③加强铸锭的质量管理; ④对铸锭进行均匀化处理; ⑤合理确定时效工艺,正确安装热电偶,正确摆放型材以保证热风循环通畅。 3几何尺寸超差 3.1 主要原因 ①由于模具设计不合理或制造有误、挤压工艺不当、模具与挤压筒不对中、不合理润滑等,导致金属流动中各点流速相差过大,从而产生内应力致使型材变形; ②由于牵引力过大或拉伸矫直量过大导致型材尺寸超差。
钢中夹杂物浅析
钢中夹杂物浅析 1. 钢中夹杂物的分类 1.1 根据钢中非金属夹杂物的来源分类 (1)内生夹杂物钢在冶炼过程中,脱氧反应会产生氧化物和硅酸盐等产物,若在钢液凝固前未浮出,将留在钢中。溶解在钢液中的氧、硫、氮等杂质元素在降温和凝固时,由于溶解度的降低,与其他元素结合以化合物形式从液相或固溶体中析出,最后留在钢锭中,它是金属在熔炼过程中,各种物理化学变化而形成的夹杂物。内生夹杂物分布比较均匀,颗粒也较小,正确的操作和合理的工艺措施可以减少其数量和改变其成分、大小和分布情况,但一般来说是不可避免的。 (2)外来夹杂物钢在冶炼和浇注过程中悬浮在钢液表面的炉渣、或由炼钢炉、出钢槽和钢包等内壁剥落的耐火材料或其他夹杂物在钢液凝固前未及时清除而留于钢中。它是金属在熔炼过程中与外界物质接触发生作用产生的夹杂物。如炉料表面的砂土和炉衬等与金属液作用,形成熔渣而滞留在金属中,其中也包括加入的熔剂。这类夹杂物一般的特征是外形不规则,尺寸比较大,分布也没有规律,又称为粗夹杂。这类夹杂物通过正确的操作是可以避免的。 1.2 根据夹杂物的形态和分布,标准图谱分为A、B、C、D和DS五大类。 这五大类夹杂物代表最常观察到的夹杂物的类型和形态: (1)A类(硫化物类):具有高的延展性,有较宽范围形态比(长度/宽度)的单个灰色夹杂物,一般端部呈圆角; (2)B类(氧化铝类):大多数没有变形,带角的,形态比小(一般<3),黑色或带蓝色的颗粒,沿轧制方向排成一行(至少有3个颗粒); (3)C类(硅酸盐类):具有高的延展性,有较宽范围形态比(一般>3)的单个呈黑色或深灰色夹杂物,一般端部呈锐角; (4)D类(球状氧化物类):不变形,带角或圆形的,形态比小(一般<3),黑色或带蓝色的,无规则分布的颗粒; (5)DS 类(单颗粒球状类):圆形或近似圆形,直径>13μm的单颗粒夹杂物。 2. 钢中夹杂物主要类型及特征 2.1 硫化物
铝合金熔体中夹杂物与含氢量的关系_丛红日
实用研究特种铸造及有色合金 2000年第3期 铝合金熔体中夹杂物与含氢量的关系 山东工业大学 丛红日 边秀房 摘 要 采用英国HYSCANⅡ测氢仪研究铝合金熔体中夹杂物与含氢量的关系,结果表明:在夹杂沾污度超过2.5%时,熔体含氢量会增加3倍以上;同时也研究了夹杂物尺寸和熔炼温度对含氢量的影响。 关键词:铝合金 含氢量 夹杂沾污度 中图分类号:TG292 文献标识码:A 文章编号:1001-2449(2000)03-0021-02 铝及其合金因含气体和夹杂,严重阻碍它的进一步应用[1]。铝合金中的气体H2占全部气体的60%~90%[2]。氢在铝熔体中主要以下列几种形式存在:原子态,即[H]溶解于铝熔液中;分子态,H以H2存在于Al2O3的裂缝中,形成负曲率半径的氢气泡[3];化合态,氢原子与铝液中的某些元素形成氢化物。铝液中的夹杂可分为两类,第一类是宏观组织中分布不均匀的大块夹杂物,它使组织不连续,铸件渗漏,或成为腐蚀的根源,明显降低合金的强度和塑性;第二类是弥散状的夹杂,在低倍显微镜下看不到。它使铝液粘度增大,降低凝固时铝液的补缩能力。目前很难控制熔体中氢和夹杂的含量,而其含量的增加必然导致铸件力学性能下降,致使铸件报废。因此,有必要研究合金熔体中氢与夹杂之间的内在联系。 1 试验方法 试验所用原材料为含不同夹杂量的AlTiB中间合金。其制备方法是:将质量分数为99.7%的工业纯铝在950℃熔化,然后加入质量分数为99.0%的K2TiF6和质量分数为98.0%的KBF4,保温一段时间后进行除渣,根据要求得到不同的夹杂含量。熔化设备采用坩埚式电阻炉,坩埚材质为石墨粘土。引入夹杂沾污度表示夹杂的含量,用游标卡尺进行测量。 将含夹渣的AlTiB中间合金浇铸成一定尺寸的试样。加热后,经过足够的变形,然后沿变形方向打开断口,测定断口单位面积上夹杂的数目和面积,即可获得夹杂沾污度η[4]。 η=πD2/(4l·d) 式中 D———夹杂直径 l———断口长度 d———断口宽度 铝合金中氢含量的测定采用英国SE VERN SCI-ENCE公司制造的HYSCANⅡ测氢仪。该仪器采用RPT (Reduced Pressure Test)法测氢。其测氢精度为0.1 mL/g。 2 试验结果与分析 2.1 夹杂物对含氢量的影响 经过对不同夹杂量的AlTiB中间合金的测氢分析,如图1所示,发现随着夹杂沾污度的增加,铝合金中的含氢量呈上升趋势,且从图1能够看出, 当夹杂沾污度 图1 夹杂沾污度与含氢量的关系 从0达到2.5%时,其含氢量就会增加3倍以上。有资料表明,一定温度下,铝熔体中的氢含量一定,即使人为通入氢气,在达到动态平衡后,铝熔体中含氢量也基本保持不变。因此,有理由相信,铝合金熔体中的氢大部分是夹杂物带进去的。为了对这一现象进行深入剖析,有必要分析夹杂物的组成成分。试样的X射线衍射分析结果如图2所示,夹杂物主要由Al,Al2O3,KAlF4, TiAl3及微量TiB2组成。夹杂物的形貌可由扫描电镜拍出,如图3所示。从图3a能够看出,夹杂物的形貌并不唯一,它主要由板状物与针状物组成。对针状物进行放大处理,如图3b,可以看到组织中存在很多显微缩松,这些缩松就构成了夹杂物疏松多孔的特性。 从热力学观点来看,在熔体中形成气泡需满足以下两方面的条件。第一,要有足够的气体分子凝聚;第二, 21 丛红日,男,1977年出生,硕士生,山东工业大学液态金属及遗传工程研究所,济南经十路73号(250061) 收稿日期:2000-01-05山东省自然科学基金资助项目(Z99F01)
20002001年度课题一览表
2000-2001年度课题一览表 课题号项目名称申请者所在单位 00-G001甲烷低温活化BETA沸石负载 Ni-Pa纳米金属簇催化剂的合成和 表征 马静红太原理工大学 00-G002 Pd/CexZr1-xO2催化剂上NO, CO 吸附的原位红外表征陈诵英 马磊 浙江大学催化研究所 00-G003二氧化碳加氢制甲醇甲醚铜系催化 剂研究 费金华浙江大学催化研究所 00-G004CH4、CO2与O2制合成气:负载 钴、镍催化剂研究莫流业 郑小明 浙江大学催化研究所 00-G005固定化生物酶的手性催化作用研 究-氨基酸光学对映体的酶法析分 与转化 李绪渊兰州大学化学化工学院 00-G006 选择性氧化反应的化学选择性控制何静北京化工大学 00-G007 强酸性介孔材料的合成与表征吴通好吉林大学化学系 00-G008 纳米结构催化层抗CO阳极的表征张华民大连化物所三室 00-G009 新催化材料的合成与表征王祥生大连理工大学化工学院00-G010 DMC和苯酚酯交换反应多相催化 剂的研究 王公应成都有机化学研究所 00-G011 纳米Pd催化剂的物理法制备及纳 米Pd在载体上的分散研究 杜芳林青岛化工学院 00-G012 稀土改性的钼基分子筛载体催化 剂上的甲烷无氧芳构化 余林汕头大学化学系 00-G013 质子交换膜燃料电池用MEA材料 的微观结构与性能的表征 邢丹敏大连化物所三室 00-G014 新型分子筛催化材料表征肖丰收吉林大学化学系 00-G015 沸石分子筛的光谱表征肖丰收吉林大学化学系 00-G016 乙烯直接氧化合成醋酸 高活性Pd-SiW12/SiO2催化剂活性 机制研究王新平 蔡天锡 大连理工大学 00-G017 加氢催化剂活性相的研究聂红 龙湘云 中石化北京石化院 00-G018 分子筛催化甲苯歧化反应机理的原 位表征研究朱志荣 孔德金 陈庆龄 上海石油化工研究院 00-G019 合成β-紫罗兰酮的新型催化剂研究蒋淇忠上海交通大学 00-G020 负载型Ru, Rh等催化剂上POM反 应机理的TAP技术研究 万惠霖厦门大学化学系 00-G021 酸碱催化模型反应的TAP和微观动 力学研究 沈俭一南京大学化学系 00-G022 超强酸化TiO2基固体的表面酸性 与光催化性能的关联研究 付贤智福州大学光催化研究所
DIN 50602 钢中非金属夹杂物评级方法(1)
n -D o w n l o a d -B e u t h -L G A T r a i n i n g & C o n s u l t i n g G m b H P a t e n t e u n d N o r m e n -K d N r .6937382-L f N r .3263428001-2006-07-07 11:40
n -D o w n l o a d -B e u t h -L G A T r a i n i n g & C o n s u l t i n g G m b H P a t e n t e u n d N o r m e n -K d N r .6937382-L f N r .3263428001-2006-07-07 11:40
n -D o w n l o a d -B e u t h -L G A T r a i n i n g & C o n s u l t i n g G m b H P a t e n t e u n d N o r m e n -K d N r .6937382-L f N r .3263428001-2006-07-07 11:40
n -D o w n l o a d -B e u t h -L G A T r a i n i n g & C o n s u l t i n g G m b H P a t e n t e u n d N o r m e n -K d N r .6937382-L f N r .3263428001-2006-07-07 11:40
铝合金常见缺陷
6063铝合金常见缺陷 6063铝合金>铝合金型材以其良好的塑性、适中的热处理强度、良好的焊接性能以及阳 极氧化处理后表面华丽的色泽等诸多优点而被广泛应用。但在生产过程中经常会出现一些缺 陷而致使产品质量低下,成品率降低,生产成本增加,效益下降,最终导致企业的市场竞争 能力下降。因此,从根源上着手解决6063铝合金挤压型材的缺陷问题是企业提高自身竞争 力的一个重要方面。笔者根据多年的铝型材生产实践,在此对6063铝合金挤压型材常见缺 陷及其解决办法作一总结,和众多同行交流,以期相互促进。 1. 碰伤划伤、擦伤、碰伤是当型材从模孔流出以及在随后工序中与工具、设备等 相接触时导致的表面损伤。 1.1主要原因: 1.1.1 铸锭表面附着有杂物或铸锭成分偏析。铸锭表面存在大量偏析浮出物而铸锭又未进 行均匀化处理或均匀化处理效果不好时,铸锭内存在一定数量的坚硬的金属颗粒,在挤压 过程中金属流经工作带时,这些偏析浮出物或坚硬的金属颗粒附着在工作带表面或对工作 带造成损伤,最终对型材表面造成划伤; 1.1.2 模具型腔或工作带上有杂物,模具工作带硬度较低,使工作带表面在挤压时受伤而 划伤型材; 1.1.3 出料轨道或摆床上有裸露的金属或石墨条内有较硬的夹杂物,当其与型材接触时对 型材表面造成划伤; 1.1.4 在叉料杆将型材从出料轨道上送到摆床上时,由于速度过快造成型材碰伤; 1.1.5 在摆床上人为拖动型材造成擦伤; 1.1.6 在运输过程中型材之间相互摩擦或挤压造成损伤。 1.2解决办法 1.2.1 加强对铸锭质量的控制; 1.2.2 提高修模质量,模具定期氮化并严格执行氮化工艺; 1.2.3 用软质毛毡将型材与辅具隔离,尽量减少型材与辅具的接触损伤; 1.2.4 生产中要轻拿轻放,尽量避免随意拖动或翻动型材; 1.2.5 在料框中合理摆放型材,尽量避免相互摩擦。 2. 机械性能不合格 2.1主要原因 2.1.1 挤压时温度过低,挤压速度太慢,型材在挤压机的出口温度达不到固溶温度,起不 到固溶强化作用; 2.1.2 型材出口处风机少,风量不够,导致冷却速度慢,不能使型材在最短的时间内降到200 C 以下,使粗大的Mg2Si过早析出,从而使固溶相减少,影响了型材热处理后的机械性能; 2.1.3 铸锭成分不合格,铸锭中的Mg、Si含量达不到标准要求; 2.1.4 铸锭未均匀化处理,使铸锭组织中析出的Mg2Si相无法在挤压的较短时间内重新 固溶,造成固溶不充分而影响了产品性能; 2.1.5 时效工艺不当、热风循环不畅或热电偶安装位置不正确,导致时效不充分或过时效。2.1.6 挤压系数过低。 2.2解决办法 2.2.1 合理控制挤压温度和挤压速度,使型材在挤压机的出口温度保持在最低固溶温度以 上; 2.2.2 强化风冷条件,有条件的工厂可安装雾化冷却装置,以期达到6063合金冷却梯度
粗苯加氢技术进展
芳烃化合物苯、甲苯、二甲苯(BTX)是一类重要的基础化工原料,炼焦副产品焦化粗苯是芳烃化合物的一个重要来源。焦化粗苯含较多的杂质,特别是噻吩硫的含量比较高,必须对其进行纯化才能使用。传统的酸洗法工艺只能部分脱除粗苯中的含硫化合物和杂质,而且污染严重。催化加氢精制工艺,由于其三苯收率高,“三废”排放量大大降低,所得产品质量好,正逐步取代酸洗法。目前国外粗苯加氢工艺分为高温法(600~630 ℃,即Litol 法)与低温法(320~380 ℃,以K.K 法为代表)。高温法相对于低温法而言,反应温度和压力都很高,对设备、管道、仪表要求高,投资大,所以低温加氢精制法比较适合我国采用,关键设备可以实现国产化。粗苯加氢精制的关键步骤是预加氢和主加氢,通过预加氢可以饱和易于聚合的二烯烃和苯乙烯,主加氢主要是脱除含硫的噻吩类化合物。实现粗苯低温加氢精制的一个关键技术是低温加氢催化剂, 1 实验 以Ti-Al复合氧化物为载体,(NH4)6Mo7O24·4H2O和Ni(NO3)2·6H2O、Co(NO3)2·6H2O 为前体,采用分步浸渍法制备了一系列不同组成的预加氢催化剂NiMo/Ti-Al 和主加氢催化剂CoMo/Ti-Al。催化剂在使用前进行预硫化处理,在WFSM-3060 高压微型固定床反应器上评价其活性。 2 结果与讨论 2.1 预加氢催化剂NiMo/Ti-Al 的筛选预加氢的目的是除去粗苯中易聚合的二烯烃、苯乙烯等物质,以二烯烃的脱除率来表征预加氢催化剂的活性。反应条件:T=180 ℃,P= 3.0 MPa 催化剂装量 2 mL,粗苯流量为0.067 mL/min,氢气流量4 4.6 mL/min。从图 1 可知,Ni/(Ni+Mo)=0.325时,即选用2Ni8Mo/Ti-A(l负载量2%NiO,8%MoO3)催化剂能够使环戊二烯烃的脱除率达到最高。同时在预加氢阶段对噻吩硫也有23.5%脱除。 2.2 主加氢催化剂的筛选 主加氢的主要目的是除去原料里面的噻吩硫,因此可以通过比较噻吩硫的脱除效率来选择合适的催化剂。 2.2.1 Co/(Co+Mo)摩尔比值不同的催化剂的活性比较在反应条件:T =310 ℃、P= 3.0 MPa,催化剂装量2 mL,原料液流速为0.067 mL/min,氢气流量4 4.6 mL/min,对粗苯原料进行了脱硫试验。结果如图2 所示。由图2 可知催化剂的脱硫活性在Co/(Co+Mo)=0.324 时达到最大值。 2.2.2 Co/(Co+Mo)值相同而负载量不同的催化剂的活性比较维持Co/(Co+Mo)=0.324,改变负载量,选择1.5Co6Mo/Ti-Al、2Co8Mo/Ti-Al、2.5Co10Mo/Ti-Al、3Co12Mo/Ti-Al 四个催化剂进行了活性评价。反应温度为310 ℃,其它条件同上。结果如图3。
钢中夹杂物含量评定的标准试验方法
ASTM E45-2013 钢中夹杂物含量评定的标准试验方法 Standard Test Methods for Determining the Inclusion Content of Steel ①本标准的固定编号为E45;其后面的数字表示最初釆用或最后修订的年份。括号里的数字表示此标准 的最后重新批准时间。上标希腊字母(ε)表示最后一次修订或复审后的编辑修改。 本标准已经美国国防部认可采用。 1. 范围 1.1 本标准的试验方法为测定锻钢中非金属夹杂物含量的方法。宏观试验法包括低倍腐蚀、断口、台阶和磁粉法。显微试验法通常包括5 种检测。依据夹杂物形状而不以化学特点,显微法将夹杂物划分为不同类型。这里主要讨论了金相照相技术,它允许形状类似的夹杂物之间略有不同。这些方法在主要用来评定夹杂物的同时,某些方法也可以评估诸如碳化物、氮化物、碳氮化物、硼化物和金属间化合物的组成。除了钢以外,其它合金在有些情况下也可以应用这些方法的一种或多种。根据这些方法在钢中的应用情况,将分别给予介绍。 1.2 本标准介绍了依据显微试验方法A 和方法D,使用JK 评级图评定夹杂物的程序。 1.3 按照钢的类型和性能要求,可以采用宏观法或显微法,也可以将二者结合起来,以得到最佳结果。 1.4 这些试验方法仅仅为推荐方法,对任何级别的钢而言,这些方法都应不能作为合格与否的判据。
1.5 该标准以国际单位制规定的单位为标准单位,圆括号里的内容为转化的近似值。 1.6 本标准未注明与安全相关的事项,如果有的话,也只涉及本标准的使用。标准使用者应建立适当的安全和健康操作规程,并且在使用标准前应确定其适用性。 2. 引用文件 2.1 ASTM 标准: ② E3 制备金相试样指南 E7 金相显微检测相关术语 ①本试验方法由ASTM 的E04《金相》委员会管辖,并由E04.09《夹杂物》分委员会直接负责。 现版本于2013 年5 月1 日批准,2013 年5 月出版。原版本在1942 年批准。前一个最新版是2011 年批准 的E45-11a。DOI: 10.1520/E0045-13。 ②对于ASTM 的参考标准,可登陆ASTM 网站,https://www.360docs.net/doc/3811298354.html, 或联系service@https://www.360docs.net/doc/3811298354.html, 的ASTM 客户服务 部。ASTM 标准年报资料,参见ASTM 网站的本标准的文件概要页。 ASTM E45-2013 钢中夹杂物含量评定的标准试验方法 2 E381 钢棒,钢坯,钢锭和锻件的宏观试验法 E709 磁粉检测指南 E768 自动测定钢中夹杂物的试样的制备和评定操作规程 E1245 用自动图像分析法确定金属中夹杂物或第二相含量的操作规程 E1444 磁粉探伤法的操作规程 E1951 十字线和光学显微镜放大倍率的校准指南
钢中夹杂物的类型及控制技术发展
钢中夹杂物的类型及控制技术发展 XX (河北联合大学冶金与能源学院,唐山,063009) 摘要:综合论述了钢中非金属夹杂物的按化学成分、形态、粒度、来源的分类以及控制夹杂物含量时所采用的气体搅拌-钢包吹氩、中间包气幕挡墙、电磁净化-钢包电磁搅拌、中间包离心分离和结晶器电磁制动、过滤器技术、超声处理技术和渣洗技术,并针对钢中夹杂物的控制技术的优、缺点进行了简要的归纳。随着氧化物冶金工艺纯净钢产品的开发,夹杂物去除技术的不断进步,非金属夹杂物的控制技术仍面临着新任务。 关键词:非金属夹杂物;夹杂物类型;控制技术 Types and Progress on Technique for Removel of inclusions in steel XX (College of Metallurgy and Energy Hebei United University, Tangshan 063009) Abstract:The behavior of inclusions in molten steel includes physical processes such as nucleation, growth, polymerization and transmission. The removal of inclusions can be seen as the result of transmission, which involves inclusion growth, floating and separating. The key progress on technique for removal of inclusions in steel is gas stirring-ladle argon blowing, gas shielding weir and dam in tundish, electromagnetic cleaning-ladle electromagnetic stirring, tundish centrifugal separating and mold electromagnetic braking, slag washing, ultrasonic technique ,and filter technique. Key words:non-metallic inclusions Typesof inclusions, Technique for Removel of inclusions 1引言 钢中非金属夹杂物是指钢中不具有金属性质的氧化物、硫化物、硅酸盐或氮化物。它们是钢在冶炼过程中加入脱氧剂而形成的氧化物、硅酸盐和钢在凝固过程中由于某些元素溶解度下降而形成的硫化
铝合金铸件中夹杂和氢含量关系
铝合金铸件中夹杂和氢含量关系 随着汽车工业的发展铝合金铸件的使用越来越多,对铸件的要求也越来越高。除要求保证化学成分、力学性能和尺寸精度外,铝合金铸件还不允许有缩孔、缩松、气孔、渣孔等铸造缺陷。铝液净化处理是保证高质量铝合金产品的措施之一,也是提高铝合金综合质量的主要手段。铝液的精炼效果对气孔、缩孔、夹杂的形成有重要的影响,且直接影响铝合金铸件的物理性能、力学性能。没有高质量的铝液,即使后续处理再先进,缺陷一旦产生它就始终存在产品之中,高质量的铸件就难以获得。因此必须重视铝液中的气体和夹杂物,并采取措施来清除铝液中的气体和夹杂物。 1、铝液中的气体和夹杂物 铝液中的气体主要是氢气(约占80%~90%),其次是氮气、氧气、一氧化碳等。氢几乎不溶于固态铝,而在液态溶解度很大。氢在固相线上下的溶解度为每100g 铝液的氢含量是0.65mL和0.034mL(氢在0.1MPa的条件下),即氢在固液两相的溶解度相差19.1倍,而每100g熔融铝中正常的氢含量为0.1~0.4mL。由于溶解度的不同氢就倾向于从熔体中逸出,当氢气压力大于表面张力和液体静压力时就形成气泡,进而在铸件中产生针孔。因此,在铝合金熔体净化方面,主要存在的问题是铝合金的含氢量较高,而现有手段不能满足高质量铝合金铸件的生产要求。通常每100g铝的含氢量在0.1~0.2mL时基本能满足生产要求,对特殊要求的铸件(像航空铸件)每100g铝的含氢量要在0.06mL以下。 夹杂是指在液相线以上的任何固体及液体以外的物质。铝液中常见的非金属杂质有氧化物、氮化物、碳化物、硼化物等,大都以颗粒状存在,典型的颗粒尺寸在1~30μm范围内。除来自炉料外,主要是熔化过程中化学反应的产物。铝表面的氧化膜厚度在2~10μm,接近熔点时增至200μm,液面上的氧化膜不仅更厚,而且结构发生了变化;面向铝液一侧是致密的对铝液有保护作用,而铝液外侧是疏松的,内有直径5~10μm的小孔并被氢、空气、水汽充满,如果将液膜搅入铝液就会增杂、增气。另外在高合金熔体中还会出现一些不希望有的初生金属间化合物,如铝锆、铝钛等,含铁的铝合金还会形成富铁的铝铁相、铝硅铁相等,铝硅铁相是一种针状化合物严重破坏铝的基体,影响力学性能。 铝合金中的夹杂物与气体存在很强的交互作用,铝液中的含氢量受夹杂影响很大,当夹杂含量为0.002%和0.02%时,相应的氢含量为0.2mL/100gAl和 0.35mL/100gAl。在含氢量相同的情况下,夹杂物含量越高针孔率越高;相反,当铝液中含杂量很低时,含氢量也很低;即使人为通入氢气,也会自动析出,很快恢复到原来的含量。即使少量夹杂存在,也能显着降低形成气孔的临界浓度值。另一方面在无夹杂(或夹杂含量很低)的情况下,形成气孔的临界氢浓度可以达到0.3mL/100gAl。因此,除杂和除气应同时进行,同样重要。不管用哪种精炼 方式,除气和除杂的效果往往是兼而有之,但各有侧重。 2、铝合金熔体净化技术的现状
钛铝合金研究现状
TiAl基合金研究现状 γ-TiAl金属间化合物的密度仅为镍基高温合金的1/2左右,而高温力学性能却与之相近,因此是一种很有应用前景的高温结构材料[1-5]。作为结构材料使用的TiAl系金属间化合物主要有三种:α2-Ti3Al、γ-TiAl和δ-TiAl3,其中综合性能最好的是γ-TiAl合金,目前普遍认为它完全有潜力替代700~990℃上使用的镍基高温合金,可以使航空发动机构件重量减轻约1/2,因而引起广泛重视,成为TiAl合金研究中的焦点。 γ-TiAl基合金具有良好的物理和机械性能,与普通的钛合金和高温合金相比具有明显的优势(表1-1)。表1-1给出了Ti-Al系金属间化合物(α2-Ti3Al和γ-TiAl)的主要高温性能。可见除塑性外,Ti-Al系金属间化合物的各方面性能均高于Ti合金,特别是γ-TiAl的密度小(仅有3.9g·cm-3,不到Ni基超合金密度的一半(8.3g·cm-3)),其它性能又与之接近,这对于航空材料有十分重要意义。由于共价键的作用使与扩散有关的高温性能,如蠕变、持久强度和断裂韧性等性能都得到改善,同时作为铝化合物γ-TiAl还具有优异的抗高温氧化性能和耐腐蚀性能,所以γ-TiAl金属间化合物是很有潜力的高温结构材料。 表1-1 γ-TiAl基合金与 2-Ti3Al基合金、Ti基合金、超合金的性能比较 性能 Ti-基 2-Ti3Al基 γ-TiAl基 Ni-基 密度, g/cm3 4.54 4.15-4.7 3.76-3.9 8.3 模量, GPa 96-110 110-145
207 蠕变极限, ℃540 730 1038 1090 氧化极限, ℃590 705 1038 1090 室温延性, % 15 2.4 1-3 3-10 高温延性, %/℃15-50 10-20/660
《利用扫描电镜对钢中夹杂物进行评定和分类的方法》编制说明
《利用扫描电镜对钢中夹杂物进行评定和 分类的方法》编制说明 (送审稿) 一、任务来源 随着我国钢铁行业的发展,夹杂物的检测分析日益受到技术人员的重视,目前利用光学显微镜对夹杂物进行评定和分类已不能满足高性能钢铁产品质量控制的要求,对于尺寸较小(如2μm以下)的夹杂物,光学显微镜难以辨认,且光学显微镜不能给出夹杂物的化学组成信息,然而利用扫描电镜则可对钢中夹杂物进行形态、尺寸和成分的完整分析,为此有必要引进国外利用扫描电镜对钢中夹杂物进行评定和分类的先进标准,以满足国内钢铁产品夹杂物检测的发展要求。 目前国外标准有ASTM E45《钢中夹杂物含量的测定方法》和ASTM E1122《利用图像分析仪进行夹杂物评级的方法》,国内标准有GB/T 18876.2-2006《应用自动图像分析测定钢和其他金属中金相组织、夹杂物含量和级别的标准试验方法—第2部分:钢中夹杂物级别的图像分析与体视学测定》,这些标准提供了夹杂物的金相评定方法,而ASTM E2142-2008《利用扫描电镜对钢中夹杂物进行评定和分类的方法》提供了夹杂物的扫描电镜评定方法,涵盖了夹杂物的化学组成信息,可得到更准确的夹杂物分类评级结果。 根据全国钢标准化技术委员会钢标委“2011年第二批国家标准制定计划项目”321号的要求,由首钢技术研究院、冶金工业信息标准研究院共同承担《利用扫描电镜对钢中夹杂物进行评定和分类的方法》国家标准制定工作,项目编号为:GB 20111039-T-605,并要求于2012年完成。
以首钢技术研究院、冶金工业信息标准研究院为主要起草单位的《利用扫描电镜对钢中夹杂物进行评定和分类的方法》项目组,根据近年来国内钢铁产品夹杂物检测分析的实际情况、用户反馈意见以及会议讨论意见,形成了标准的送审讨论稿。 二、标准主要制定内容 1、修改采用国际ASTM标准E2142–2008 ―Standard Test Methods for Rating and Classifying Inclusions in Steel Using the Scanning Electron Microscope‖。 主要技术内容:介绍了利用扫描电镜(SEM)对钢中夹杂物进行尺寸分布、化学分类及评级的程序。描述了2种方法,方法1主要依据化学组成、形态及宽度对夹杂物进行自动分类和评级。方法2对夹杂物进行个性化的自定义分析,如体积分数、数量分数等。 2、根据我国工业的特殊需要,本标准在采用E2142–2008时进行了如下修改: a)在第1章―范围‖内修改1.2条,为突出扫描电镜的化学分类优势,删掉原方法1,只采用原方法2和方法3,并在新标准中重命名为方法1和方法2; 并增加了适用范围,方法1是扫描电镜分类法,依据化学组成、形态和宽 度分类评级,适用于压缩比大于或等于3的轧制或锻制钢材中的2μm以 上非金属夹杂物的显微评定。方法2用来确定某类夹杂物的具体细节,如 体积分数、数量分数等体视学参数,适用于各种铸坯或钢材中所有尺寸 (包括2μm以下)夹杂物的统计分类。删除了文中的相关章节,如原文 第12章。 b)引用文件用相应的国家标准代替:E1122用GB/T 18876.2-2006代替,E1245用GB/T 18876.1-2002代替,E45用GB/T10561-2005代替,E768用