车身轻量化与钢铝一体化结构新技术的研究进展
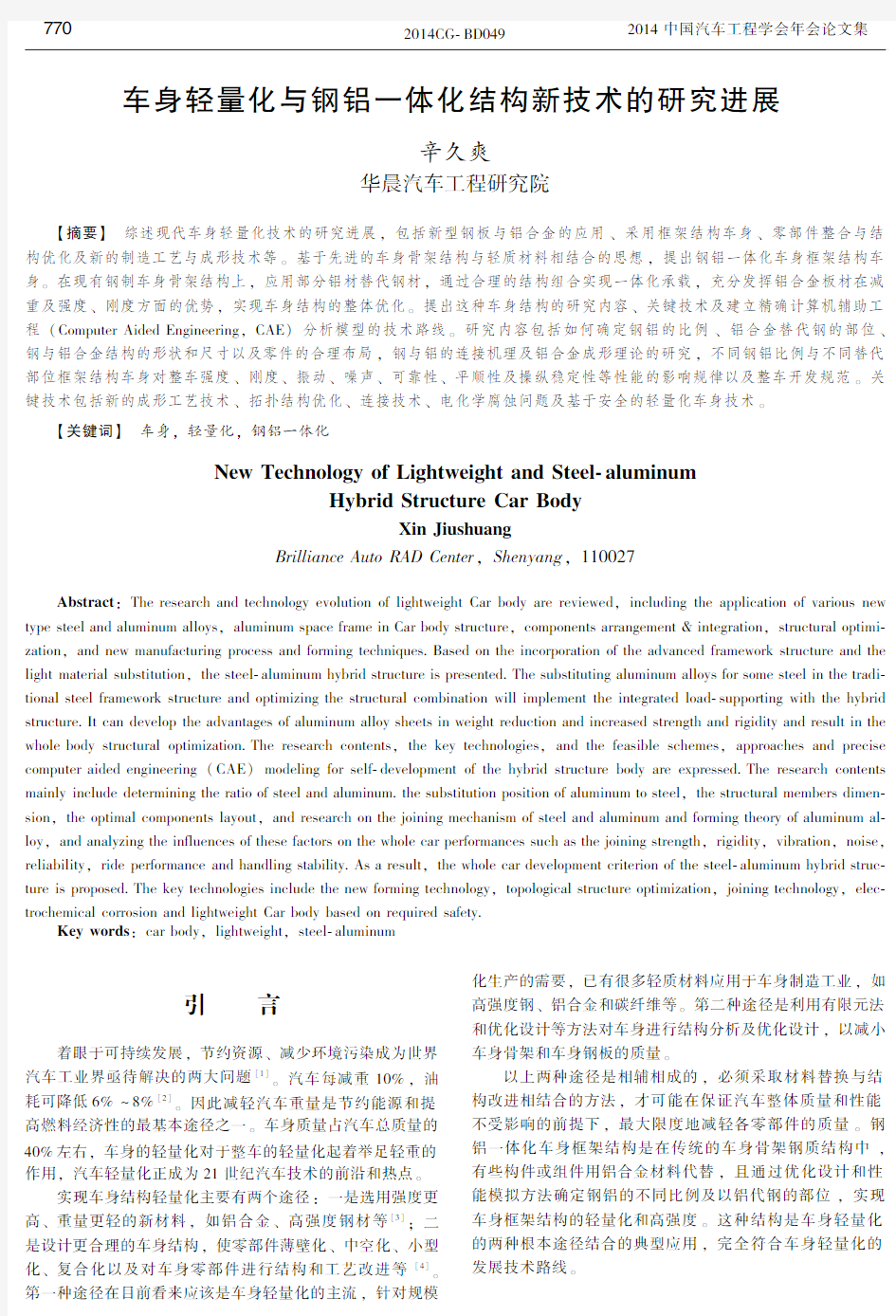

车身轻量化与钢铝一体化结构新技术的研究进展
辛久爽
华晨汽车工程研究院
?摘要?一综述现代车身轻量化技术的研究进展?包括新型钢板与铝合金的应用二采用框架结构车身二零部件整合与结构优化及新的制造工艺与成形技术等?基于先进的车身骨架结构与轻质材料相结合的思想?提出钢铝一体化车身框架结构车身?在现有钢制车身骨架结构上?应用部分铝材替代钢材?通过合理的结构组合实现一体化承载?充分发挥铝合金板材在减重及强度二刚度方面的优势?实现车身结构的整体优化?提出这种车身结构的研究内容二关键技术及建立精确计算机辅助工程(ComputerAidedEngineering?CAE)分析模型的技术路线?研究内容包括如何确定钢铝的比例二铝合金替代钢的部位二钢与铝合金结构的形状和尺寸以及零件的合理布局?钢与铝的连接机理及铝合金成形理论的研究?不同钢铝比例与不同替代部位框架结构车身对整车强度二刚度二振动二噪声二可靠性二平顺性及操纵稳定性等性能的影响规律以及整车开发规范?关键技术包括新的成形工艺技术二拓扑结构优化二连接技术二电化学腐蚀问题及基于安全的轻量化车身技术??关键词?一车身?轻量化?钢铝一体化
NewTechnologyofLightweightandSteel ̄aluminum
HybridStructureCarBody
XinJiushuang
BrillianceAutoRADCenter?Shenyang?110027
一一Abstract:TheresearchandtechnologyevolutionoflightweightCarbodyarereviewed?includingtheapplicationofvariousnewtypesteelandaluminumalloys?aluminumspaceframeinCarbodystructure?componentsarrangement&integration?structuraloptimi ̄zation?andnewmanufacturingprocessandformingtechniques Basedontheincorporationoftheadvancedframeworkstructureandthelightmaterialsubstitution?thesteel ̄aluminumhybridstructureispresented Thesubstitutingaluminumalloysforsomesteelinthetradi ̄tionalsteelframeworkstructureandoptimizingthestructuralcombinationwillimplementtheintegratedload ̄supportingwiththehybridstructure Itcandeveloptheadvantagesofaluminumalloysheetsinweightreductionandincreasedstrengthandrigidityandresultinthewholebodystructuraloptimization Theresearchcontents?thekeytechnologies?andthefeasibleschemes?approachesandprecisecomputeraidedengineering(CAE)modelingforself ̄developmentofthehybridstructurebodyareexpressed Theresearchcontentsmainlyincludedeterminingtheratioofsteelandaluminum thesubstitutionpositionofaluminumtosteel?thestructuralmembersdimen ̄sion?theoptimalcomponentslayout?andresearchonthejoiningmechanismofsteelandaluminumandformingtheoryofaluminumal ̄loy?andanalyzingtheinfluencesofthesefactorsonthewholecarperformancessuchasthejoiningstrength?rigidity?vibration?noise?reliability?rideperformanceandhandlingstability Asaresult?thewholecardevelopmentcriterionofthesteel ̄aluminumhybridstruc ̄tureisproposed Thekeytechnologiesincludethenewformingtechnology?topologicalstructureoptimization?joiningtechnology?elec ̄trochemicalcorrosionandlightweightCarbodybasedonrequiredsafety
Keywords:carbody?lightweight?steel ̄aluminum
引一一言
着眼于可持续发展?节约资源二减少环境污染成为世界汽车工业界亟待解决的两大问题[1]?汽车每减重10%?油耗可降低6%~8%[2]?因此减轻汽车重量是节约能源和提高燃料经济性的最基本途径之一?车身质量占汽车总质量的40%左右?车身的轻量化对于整车的轻量化起着举足轻重的作用?汽车轻量化正成为21世纪汽车技术的前沿和热点?实现车身结构轻量化主要有两个途径:一是选用强度更高二重量更轻的新材料?如铝合金二高强度钢材等[3]?二是设计更合理的车身结构?使零部件薄壁化二中空化二小型化二复合化以及对车身零部件进行结构和工艺改进等[4]?第一种途径在目前看来应该是车身轻量化的主流?针对规模化生产的需要?已有很多轻质材料应用于车身制造工业?如高强度钢二铝合金和碳纤维等?第二种途径是利用有限元法和优化设计等方法对车身进行结构分析及优化设计?以减小车身骨架和车身钢板的质量?
以上两种途径是相辅相成的?必须采取材料替换与结构改进相结合的方法?才可能在保证汽车整体质量和性能不受影响的前提下?最大限度地减轻各零部件的质量?钢铝一体化车身框架结构是在传统的车身骨架钢质结构中?有些构件或组件用铝合金材料代替?且通过优化设计和性能模拟方法确定钢铝的不同比例及以铝代钢的部位?实现车身框架结构的轻量化和高强度?这种结构是车身轻量化的两种根本途径结合的典型应用?完全符合车身轻量化的发展技术路线?
1一国内外车身轻量化技术发展现状
1 1一新材料实现车身轻量化
自1973年石油危机以来?世界各汽车厂在轿车上进行轻量化研究的进展较为明显?现代汽车中?占自重90%的6类材料大体为:钢55%~60%?铸铁12%~15%?塑料
8%~12%?铝6%~10%?复合材料4%?陶瓷及玻璃3%?用新型板材及轻型材料(如镁二铝二塑料和复合材料等)替换车身骨架及内二外壁板原有的钢材来实现轻量化是车身轻量化技术的重要途径之一?主要体现在以下几个方面?1 1 1一新型钢板
目前诸多的汽车企业致力于减轻汽车用钢铁材料的重量?以期达到汽车轻量化目的?汽车用钢逐步向高强度化方向发展?当钢板厚度分别减少0 05二O 10二0 15mm时?车身减重分别为6%二12%二18%?采用先进的高强度钢?增加了安全性?降低了噪声和振动?提高了燃油效率?降低了汽车总质量?成本没有增加?而加速性二驾驶性能却有所改善?
随着钢材品质和性能大大提高?到2010年?新型钢材的使用已超过70%?日本三菱公司为该公司最新的SUV帕杰罗SPORT设计了全新的车身结构?车身70%的构件由高强度钢板制成?整车的扭转刚度甚至比大切诺基还要高45%?车身的承载能力可达2t以上?韩国现代公司的索纳塔车身结构也用高强度钢板进行了加强?横梁和立柱全部使用800MPa的高强度钢?奔驰公司在SLK车身骨架中大量使用高强度钢?使扭转刚度增加了70%?安全性大大提高的同时也减少了车身的质量?1999年问世的宝马3系列车身骨架?其中使用了50%的高强度钢?福特的Windstar车身骨架中60%是高强度钢?丰田最新车型Vitz的车身结构中?高强度钢占了48%?比该公司生产的Starlet车减轻质量17kg?捷豹XType2 5在车身结构上采用了整片式车舱结构?实现了显著的轻量化效果?
1 1 2一铝与铝合金
铝作为汽车材料有许多优点?如在满足相同力学性能的条件下?比钢减少质量60%?且易于回收二在碰撞过程中比钢多吸收50%的能量二无需防锈处理等[4?5]?比强度和比刚度十分优良的铝金属基复合材料的研究开发成功?为汽车轻量化的进一步发展提供了途径?2008年?每辆轿车的平均铝使用质量将进一步上升到130kg?与1998年相比增长53%?世界铝协会发表的一项研究报告中宣布?铝在汽车中的用量已超过(铸)铁?成为仅次于钢的第二大汽车材料[5]?北美二欧洲和日本汽车的单车平均用铝质量[5]如图1所示?其中北美汽车铝的应用水平最高?乘用车每车平均用铝质量目前已达145kg?欧洲平均每车用铝118kg?日本情况与欧洲比较接近?
1 2一结构优化实现车身轻量化
1 2 1一铝合金车身框架结构
从各国汽车制造商推出的概念车看?在车体结构上大多数采用无骨架式结构和空间框架式结构?而且大多数以铝挤压型材为主[6]?如图2所示[6]?
尽管铝材的强度和刚度比
图1一北美二欧洲和日本汽车的单车平均用铝量
钢材小很多?但是通过框架结构设计及采用更厚的板材?补偿了这个不足?使用铝材后的车身空间框架式结构质量下降
47%?同时采用改进的断面形式?使车身抗扭抗弯能力增加了13%
?
图2一框架结构图例
奥迪公司的A2型轿车?采用了全铝骨架车身和铝合金蒙皮结构?使总质量减少到895kg?车身由车身框架二刚性型材二铸铁接头和罩壳板组成?比传统钢体车身轻43%?力学性能提高40%?另外?奥迪A8系列良好的碰撞安全性也是基于它的ASF(铝合金空间框架结构)车身结构[5]?这种车身采用高强度铝合金骨架?包围整个乘员室?就像一个防护的笼子?宝马Z8型车也采用了骨架结构和铝合金蒙皮车身?不仅提高了整车的刚度?而且减少了汽车的振动?使Z8成为宝马家族中最受欢迎的一种车型?可见?采用铝合金骨架以及蒙皮车身在增加整个车身的刚度?提高汽车被动安全性的同时?大大降低了车身的总重量?
但是?由于铝材料的回弹大且易出现裂纹?使铝板在冲压时比钢板难度大?还没有大批量完全采用铝板生产汽车?目前采用全铝制车身一般是年产量在几千辆的小批量生产的汽车?大批量生产的中型轿车车身中?铝结构的比重只占3%~7%?
1 2 2一零部件整合和结构优化
整合零部件?减少其数量也是实现零件结构轻量化的有效途径?某些车型的车身骨架零件数已由400个减到了75个?质量减轻达到30%左右?由于减少了零部件之间的连接?车身刚度得以加强?在提高车身舒适性的同时?达到减重的目的?奥迪A6采用了整体式发动机舱盖结构(发动机舱盖与散热器罩做成了一个整体)?由厚度为1 1mm的铝板
制成?在保留了奥迪车造型特征的同时?具有质量轻二耐腐蚀等优点?
结合有限元法与结构优化方法?对零部件进行结构优化?也是实现零部件轻量化的一个重要研究方向?目前结构断面优化的理论和方法已比较成熟?形状优化有了很大发展?人们已经把研究重点转向拓扑优化等更高层次的结构优化问题?
结构拓扑优化研究方法目前有解析方法和数值方法[11 ̄13]?解析方法不大适合工程应用?工程应用中常采用数值方法?连续体结构目前已成为结构拓扑优化的主要研究对象?连续体结构的拓扑优化设计具有两个不同的求解体系?国内学者主要研究局部应力约束下的强度拓扑优化设计?而国外学者主要研究全局体积约束下的刚度拓扑优化设计[13]?
在汽车轻量化结构优化设计中已普遍采用拓扑优化的方法?YANG等[14]研究了基于有限元软件MSC/NASTRAN和CSA/NASTRAN的汽车车身二底盘二焊点位置等的拓扑优化设计问题?WANG等[15]利用有限元法与拓扑优化方法对汽车车身的加强筋部分进行了优化?通过优化设计?在既定成本下?汽车车身的整体刚度能够得到充分的提高?FREDRICSON等[16]对拓扑优化设计在汽车设计中的应用作了综述?重点介绍了车身设计中的拓扑优化进展?EOM等[17]对车身焊点配置进行了拓扑优化?在确保车身整体刚度要求的情况下?得到焊点最佳位置?使得焊点数量最少?VOLZ等[18]介绍了在产品开发的初期应用线性拓扑优化及非线性形状优化相结合研究车身碰撞性能的方法?LYU等[19]应用多目标遗传算法的拓扑优化方法研究了铝合金空间框架结构的优化问题?石琴等[20]在结构设计的开始阶段引入拓扑优化理论?先对结构进行布局优化?以获得较合理的初始结构方案?再通过结构参数优化设计?得到满足其强度和刚度及设计工艺要求的最优结构?杨树凯等[21]用变密度法建立了汽车支架结构拓扑优化数学模型?利用有限元法进行了结构拓扑优化设计?王宏雁等[22]采用拓扑方法优化二改进结构?并通过有限元结构模拟计算?对汽车发动机舱盖进行了优化设计?高云凯等[23]把拓扑优化设计理论引入某电动改装车的承载式车身设计?实现了多工况二多状态变量条件下的拓扑优化设计?确定了下车身的最佳结构方案?陈茹雯等[24]利用基于有限元法的拓扑优化技术设计车身大骨架的拓扑结构?经拓扑优化后的车身大骨架各项特性参数指标均有不同程度的提高?
可见?拓扑优化正成为车身轻量化设计中结构优化的重要手段?更广泛的应用还有待进一步研究?
1 3一新的制造工艺与成形技术
在继续推进汽车轻量化的进程中努力开发新的制造方法?并对传统的制造工艺与成形技术进行变革?也是汽车车身结构轻量化的研究方向之一?针对目前所开发的新型材料?如高强度钢板二超高强度钢板?轻金属材料?如镁铝合金二塑料以及复合材料等?新的成形方法主要有拼焊板成形二液压成形以及针对轻金属材料开发的半固态成形等?国际钢铁协会成立了由18个国家35家钢铁公司组织的ULSAB ̄AVC项目?它通过车辆的整体设计来实现车身的轻量化?在成形工艺方面?其中有30%以上的零部件采用拼
焊板成形?20%以上的部件采用了液压成形技术?大力发展
和推广内高压成形技术二管件液压成形技术和塑料中空成形
技术等新工艺应用于车身制造[3]?使车身的一些结构件和附件?通过有效的断面设计和合理的壁厚设计形成复杂的整
体式结构?不仅减小了结构质量?同时强度二刚度及局部硬
度都得到了相应的提高?并且具有较强的成形自由性和设计
工作的灵活性?例如?本田公司的Insight采用了挤压成形
铝合金的前纵梁结构?其断面为正六边形?整个前纵梁结构
只需一次挤压成形?与原钢结构相比?省去了焊接工艺过
程?在保证原有刚度及吸能特性的同时?减重效果达37%?
制造工艺的改进和成形技术的发展?促进了车身构件的
大型化以及车身表面平整化?减少了车身结构件的数量?降
低了噪声与振动?改善了舒适性?提高了车身的刚性?最终
实现了车身结构的轻量化?
2一钢铝一体化车身框架结构技术发展钢铝一体化车身框架结构是高性能轻质材料与优化车身结构相结合路线的典型应用?国外虽然已经有少数公司研究并开始试用这种技术?也仅见2004年宝马公司推出世界第一个采用创新的钢铝混合结构技术的车身及2006年奥迪公司在其新款TT跑车上应用钢铝混合车身结构?但是应用还处于起步阶段?没有开发方法二设计规范和制造工艺方面的文献介绍?仍有很多工作迫切需要开展?国内尚无人开展这方面的工作?在钢铝一体化框架车身的轻量化方向研究方面没能有自主的创新技术?积极开展该项工作对于提升国内汽车自主研发水平有着极其重要的意义?
2 1一钢铝一体化车身框架结构的概况
现代车身轻量化过程中?普遍采用新型材料应用与优化
车身结构相结合的技术方案?应用更先进的车身骨架结构以
及轻质材料?使得强度合理分配到车身上?可以实现在既定
成本内提高整个车身强度二刚度的同时?减轻车身的重量?
这种思想正逐步为国内各开发人员所接受?如2006年北京
车展上?一汽自主研发的奔腾汽车?在车身结构设计上采取
了4H车身结构?如图3所示?这种结构虽然为全钢材料?
但在不同部位采用不同强度级别的材料?主要的骨架部分也
就是构成4H结构形状的部分采用高强度钢板?在发动机底
架二车身的门窗等部分采用更高强度的钢板?而在正面二后
面二侧面等碰撞接触部位?如前后保险杠等部位则采用最高
级别强度钢板?其余部位采用的主要是普通钢板?
基于类似的思想?钢铝一体化车身框架结构是在传统的
车身骨架钢质结构中?有些构件或组件用铝合金材料代替?
且可以通过优化设计和性能模拟方法确定钢铝的不同比例和
以铝代钢的部位?实现车身框架结构的轻量化和高强度?钢
铝一体化结构的设计及其参数优化对于整车的轻量化起着举
足轻重的作用?同时也对车身和整车的其他性能有重要的影
响?如何确定框架结构中哪些部分用钢二哪些结构用铝以及
它们本身的断面和板厚等参数是开发中的关键?目标是在降
低重量的前提下?提高车身的承载能力?在钢铝一体化车身
框架结构的开发过程中?存在许多问题急待研究解决?比如
铝的成形工艺技术二钢与铝的连接方法二电化学腐蚀问题二
基于安全的车身技术及钢铝一体化车身框架结构的开发方法等
?
图3一奔腾汽车框架图
2 2一新的成形工艺技术
现代车身?特别是轿车车身的骨架及覆盖件大都采用冷冲压成形工艺加工制造?冷冲压工艺具有生产效率高二产品互换性好及批量生产成本低等诸多优点?但成形过程会导致冲压件的厚度及力学性能发生变化?同时还会引起不同程度的残留应力?这些都会直接影响到车身结构的强度二刚度二耐久性等可靠性指标?由于这些改变设计者无法预测也无法控制?因此?在以往的计算机辅助工程(ComputerAidedEngineering?CAE)分析中也无法予以考虑?使仿真分析的精度与可靠性都受到一定程度的影响?特别是对车身结构的疲劳强度的影响可能更大?这些方面已经有一些研究?1998年?菲亚特公司的VALENT等[25]提出了一个改善车身结构分析精度的方法?他们用一个T形铝合金冲压件研究了成形过程对其静强度特性的影响?研究表明?对T形冲压件而言?不考虑成形引起的厚度减薄将使其弯曲刚度比实测值高
10%左右?HUB等
[126?27]
的课题组针对成形过程对车身结构
件碰撞特性的影响问题进行了一系列研究?并用前纵梁二S形梁等典型件进行了试验对比?发现如果在碰撞模拟中不考虑成形过程的影响可能会引起高达20%的计算误差?兰风崇等
[28?29]
对汽车覆盖件的毛坯形状设计及冲压成形的回弹
控制问题进行了仿真研究?得到了更精确估计拉伸件毛坯尺寸的算法及一套包括前处理和后处理的设计系统?建立了有限元网格节点列经过处理构造NURBS标准曲面的方法?板料成形FE中网格大量节点数据重构参数曲面提供了回弹控制二光滑复杂模具型面重构方法?
铝材料已广泛应用在发动机二车门二内外发动机舱盖二挡泥板二轮圈二仪表板装饰及其他零部件上
[30]
?但在车身
制造上还比较少见?主要是受到加工技术和成本的约束?如何从根本上解决铝合金板成形性能差的问题?从而获得稳定可靠的成形工艺?逐渐成为各汽车制造商和众多学者的研究热点
[1]
?
铝合金板本身力学和力学性能是决定其可成形性能的根本问题?从前人的大量研究结果[31?33]中可以看出?提高铝合金板的成形温度?以增强铝合金板的塑性?改善成形性能?已成为各大汽车制造商和学者们的共识?另外一些研究也表明?除了成形温度外?成形速度(应变速率)也会对
铝合金板的可拉深性能产生影响?但是?铝合金板的成形性能除了受到外在因素(如成形温度和变形速率等)的影响外?根本上还是取决于铝合金板本身的性能?因此?众多学者对不同铝合金板的化学成分二晶粒大小二热处理方式等对成形性能的影响进行了大量的研究?并得出了许多有益的成果[35 ̄38]?但是?铝合金板作为一种用于汽车覆盖件成形的新型材料?其成形工艺所涉及的许多关键技术还有待于进一步研究解决?
2 3一钢与铝的连接技术
车辆的主要承载构件多是由空间薄壁梁结构组成的?其拓扑结构已很少改变?因此?钢铝一体化车身框架结构也不例外地由薄壁梁结构组成?相对而言?轻金属铝二镁和复合
材料对连接技术的要求较高?而多种材料组合的要求就更高?在复合材料车体中?多种材料的连接很难由传统的点焊来完成?为了车身的多方面要求?需采用多种现代连接方法?因此?开发新的连接技术是扩大铝合金应用的前提[5?6?39 ̄44]?研究钢与铝等不同材质零件之间的连接技术是钢铝一体化车身框架结构设计中的关键技术?
车身的连接技术一般为焊接二粘接二机械连接(包括铆接)?在钢铝一体化车身框架结构中?钢与铝的连接机理研究将围绕这三种连接形式展开?
焊接的种类比较多?目前常用的主要有电阻点焊二电弧焊二激光焊二搅拌摩擦焊和等离子电弧焊等?对于铝及铝合金的连接?这些焊接方法都各有其优缺点[6?39 ̄44]?没有哪种焊接方法是完美无缺的?尤其是钢与铝之间的连接?正成为研究的热点?传统的汽车车身冲压件的材料大都是具有良好焊接性能的低碳钢?焊接是应用最广泛的连接方式?其中电阻点焊又占据了焊接工作量的70%以上?有的车身几乎全部采用电阻点焊?因此?在研究钢与铝的连接技术时?首先从电阻点焊的连接性能开始研究?点焊接头的种类有很多种?但是在设计汽车车身电阻点焊工艺时?根据需要常采用三种接头形式?即搭接二折边二搭折?如图4所示?在建立精确的CAE仿真分析模型时?将分别对这几种接头形式进行建模分析与试验研究?
粘接连接的优点已经为多数汽车生产企业生产的许多产品所证明?如捷豹XJ220二福特AIV二罗孚ECV3二LotusElise及本田NSX等?由于粘接采用面接触而非点接触?与点焊及铆接相比?有改善连接刚度与强度?减少应力集中?提高密封性?减少受潮及脏物等进入?通过接合处的合理设计能很好地吸收能量?减少振动与降低噪声等优点[6?43]?但是?异种金属粘接的强度二刚度二疲劳度和可靠性等都是通过试验验证的?数值规律研究及粘接连接CAE分析模型?未见报道?研究探索钢与铝的连接时?粘接也是重点研究的形式?粘接连接的5种基本承载情况[43]如图5所示?在考虑粘接连接时?将围绕这5种加载情况进行CAE分析及试验研究?机械连接也是车身连接技术中常用的方法?对于铝合金
车身连接装配?常采用技术被称为自冲铆[43?44]?它是一种冷压成形铆接方法?图6为自冲铆基本过程示意图[44]?与电阻点焊相比?自冲铆具有成本低二强度高二质量可靠等优点?因而能够用于轻质车身特别是铝合金车身的制造?如奥迪A8二捷豹XJ8等?是铝合金车身连接装配的主要方法?
但是这种自冲铆连接的效率二质量控制二强度刚度及可靠性分析等都还没有理论支持
?
图4一
点焊接头形式示意图
图5一粘接连接的5
种基本承载情况
图6一自冲铆基本过程示意图
一一此外?还有一些扩散连接技术也常被用于异种金属之间的连接
[43]
?由于钢与铝的连接技术尚属起步阶段?还没有
形成成熟理论与技术工艺?因此钢铝连接机理与技术的研究对开发钢铝一体化框架结构车身具有重大意义?
2 4一电化学腐蚀问题
由于钢和铝具有不同的电化学效能?钢二铝间的电极电位相差较大?且铝的电极电位更负?因此两者混合连接时可能发生严重的电化学腐蚀:电偶腐蚀二缝隙腐蚀二丝状腐蚀二膏状腐蚀二晶间腐蚀及应力腐蚀?钢铝一体化车身结构如果采用铆接工艺?车身的电化学腐蚀比全钢焊接车身更为严重?相比而言?影响最大的腐蚀形式为电偶腐蚀二缝隙腐蚀以及冲击腐蚀?
针对钢铝一体化车身结构的腐蚀特点?在进行结构设计
时?应在既定成本内?从以下几个方面综合考虑:选择耐蚀性好的钢板二选择合适的连接方式二对紧固件及标准件进行防腐处理二选择合适的涂装工艺?通过合理的防腐设计?保证钢铝一体化框架结构车身开发的顺利进行?
2 5一基于安全的轻量化车身技术
轻量化必须以保证车辆的安全性为最基本的前提?应该通过车身结构二材质二制造工艺的优化来取得?采用更先进的车身骨架结构以及轻质材料[6]?使得强度合理分配到车身上?可以在提高整个车身强度二刚度的同时?减轻车身的重量?
车身结构设计必须具备如下功能:车辆发生碰撞时?其碰撞能量必须能被车身结构的指定部位吸收?从而保证碰撞后车身座舱的生存空间?减少碰撞造成的乘员伤害?防止由
于碰撞作用导致的乘员与室内部件的撞击?必须利用车身结构的变形来吸收碰撞能量?从而尽可能缓和地吸收车辆及乘员的运动能量?车身轻量化不能盲目地减重?应在保证汽车整体质量和性能不受影响的前提下?最大限度地减轻各零部件的质量?通过对车辆碰撞时的减速度二车身伸缩变形长度和状态二碰撞力吸收能状况等重要指标的分析对比?评价轻量化方案的可行性?评价车身轻量化的技术标准还包括空气动力学性能二减振降噪舒适性二可制造性及零件的合理布局等方面的指标?
2 6一钢铝一体化车身框架结构开发方法的形成
钢铝一体化车身是在传统的车身骨架钢质结构中?有些构件或组件用铝合金材料代替?且可以通过优化设计和性能模拟方法确定钢铝的不同比例和以铝代钢的部位?实现车身框架结构的轻量化和高强度?但是具体在哪部分零件?哪些部位换成铝?换成铝后的车身强度二刚度及动态特性结果如何?将是钢铝一体化车身框架结构开发方法形成的关键?不同的钢铝比例?不同的钢铝部位?不同的连接方法?不同的断面结构等都将影响车身的整体性能?因此应采取先通过计算机精确的CAE分析?排列组合出各种不同情况进行分析?得出大量数据?从中选取在既定成本内减重最明显二性能最可靠的方案进行制作实物模型?然后建立对其进行试验分析的技术路线?建立精确的CAE分析模型的技术路线如图7所示?
完成初步实物试验后?得出改进方案?对结构进行改进?再进行CAE分析及试验?直到得到满意的结果?在这种设计开发及研究的过程中?形成相对完善的钢铝一体化车身框架结构的开发方法与规范?
3一结论
综合国内外已经开展的研究?足见汽车车身结构轻量化的理论研究和实际应用都取得了重要的进展?
1)车身骨架在保证强度二刚度和吸能安全性的基础上?通过使用高强度钢板或部分采用高强度钢构成组合式车身骨架已经成为当代汽车车身设计时的必备技术?2)车身覆盖件零件中已经开始采用普通钢板以外的新型材料?如高强度钢板二不等厚拼焊钢板二夹层钢板等?收到了减重和提高强度的双重效果?大量的研究成果已经逐步地得到应用?
3)铝制零件在车身结构中的应用是未来汽车轻量化的重要方向?其中?钢铝一体化框架结构?更有利于实现车架的不同强度和刚度梯度要求?设计出吸能要求合理的安全车身框架?是具有重要理论研究和应用前景的新结构理念?4)各种不同材料的力学性能二连接技术及成形规律的研究还很欠缺?致使车身新型结构开发二材料选用以及CAE工作尚待完善?当前最迫切的研究工作应该围绕以下几方面
?
图7一建立钢铝一体化车身框架结构
CAE精确模型流程
一一①开展关于钢铝一体化框架结构车身关键技术的研究?
包括钢与铝的连接技术二铝的成形技术二钢与铝组合的电化
学腐蚀问题等?
②开展关于钢铝一体化框架结构车身设计和分析方法
的研究?逐步建立钢铝联合框架结构的开发规范?
③在此基础上逐步推进钢铝一体化框架结构车身在企
业新产品开发中的应用?首先尝试在小批量生产中加以采
用?以考验这种结构的设计与分析方法以及实际应用效果?
不断积累铝合金材料在车身结构中的应用经验?同时也为其
他轻质材料?如镁合金二碳纤维及塑料的应用奠定基础?参考文献
[1]一CORNETTED?GALTIERA.InfluenceoftheformingprocessingOilcrashingandfatigueperformanceofhighstrengthsteelsforautomotivecomponents[R].SAEPa ̄per2002.01.0642.
[2]一BENEDYKJC.Lightmetalsinautomotiveapplications[J].LightMetalAge?2000?10(1):34 ̄35. [3]一范军锋?陈铭.中国汽车轻量化之路初探[J].铸造?2006?55(10):995 ̄l003.
[4]一张宇?朱平?陈关龙?等.基于有限元法的轿车发动机罩板轻量化设计[J].上海交通大学学报?2006?
40(1):163 ̄166.
[5]一中国汽车工程学会.世界汽车技术发展跟踪研究[M].北京:北京理工大学出版社?2006. [6]一BARNESTA?PASHBYIR.Joiningtechniquesforalu ̄minumspaceframesusedinautomobiles(PartI solid
andliquidphasewelding)[J].JournalofMaterialsPro ̄
cessingTechnology?2000?99(1 ̄3):62 ̄71. [7]一孙凌玉?BIANS?姚迎宪.车身薄壁梁结构轻量化设计的理论研究[J].北京航空航天大学学报?2004?
30(12):1163 ̄1167.
[8]一谭继锦?张代胜?熊良平?等.某型大客车车身骨架轻量化设计[J] 汽车工程?2006?28(4):
394 ̄397.
[9]一陈吉清?兰风崇?LINJ.客车概念设计阶段的车身结构优化设计分析[J].机械设计与研究?2004?20
(3):15 ̄17.
[10]一YANGRJ.Topologyoptimizationofvehiclestructure[C].ASME?1997:233 ̄242.
[11]一HANSAE?NIELSO.Topologyoptimizationofcontinu ̄umstructures:areview[J].AppliedMechanicsRe ̄
view?2001?54(4):331 ̄390.
[12]一周克民?李俊峰?李霞.结构拓扑优化研究方法综述[J].力学进展?2005?35(1):69 ̄76. [13]一罗震?陈立平?黄玉盖.连续体结构的拓扑优化设计[J].力学进展?2004?34(4):463 ̄476. [14]一YANGRJ?ChuangChinhung?CHEXiangdong?eta1.
Newapplicationsoftopologyoptimizationinautomotive
industry[J].InternationalJournalofVehicleDesign?
2000?23(21):1 ̄15.
[15]一WANGLiangsheng?BASUPK?LEIVAJP.Automo ̄bilebodyreinforcementbyfiniteelementoptimization
[J].FiniteElementsinAnalysisandDesign?2004?
40(8):879 ̄893.
[16]一FREDRICSONH.Structuraltopologyoptimization:Anapplicationreview[J].InternationalJournalofVehicle
Design?2005?37(1):67 ̄80.
[17]一EOMJS?JUBH?CHOIN?etal.Optimizationonthespotweldedconfigurationofvehiclecomponentscon ̄
sideringthestructuralperformance[J].KeyEngineer ̄
ingMaterials?2006?326 ̄328(II):957 ̄962. [18]一VOLZKDIRSCHMIDFDUDDECl.ECrashoptimizationofthebody ̄in ̄whiteintheearlyphaseoftheproduct
developmentprocess[J].VDIBerichte?2006(1):
199 ̄216.
[19]一LYUNursing?LEEByungwoo?SAITOUKazuhiro.Op ̄timalsubassemblypartitioningofspaceframestructures
forin ̄processdimensionaladjustabilityandstiffness
[J].JournalofMechanicalDesign?Transactionsofthe
ASME?2006?128(3):527 ̄535.
[20]一石琴?洪洋?张雷?等.拓扑及参数优化方法在专用汽车车架结构设计中的应用[J].机械设计?
2005?22(12):30 ̄32.
[21]一杨树凯?朱启昕?吴仕赋.基于有限元技术的汽车支架拓扑优化设计研究[J].汽车技术?2006?3:
16 ̄18.
[22]一王宏雁?高卫民?潘玲玲?等.轻质结构发动机罩设计研究[J].同济大学学报(自然科学版)?
2006?34(8):1098 ̄1103.
[23]一高云凯?孟德建?姜欣.电动改装轿车车身结构拓扑优化分析[J].中国机械工程?2006?17(23):
2522 ̄2525.
[24]一陈茹雯?李守成?吴小平.基于有限元法的拓扑优化技术在某军车车身骨架设计中的应用研究[J].
汽车工程?2006?28(4):390 ̄393.
[25]一VALENTEF?LIX?MESSINAA?etal.ANewmeth ̄odologyforimprovingaccuracyofstructuralanalysisof
carbodyparts[C].SAEPaper982336.
[26]一KANGWJ?HUHH.Crashanalysisofthin ̄walledstructureswithallelasto ̄plasticexplicitfiniteelement
method[J].KeyEngineeringMaterial?2000?177 ̄
180:201 ̄212.
[27]一YOONJH?HUHH.Efficiencyenhancementinsheetmetalforminganalysiswithameshregularizationmethod
[J].JournalofMaterialsProcessingTechnology?
2003?140(1 ̄3):616 ̄621.
[28]一LANF'LINJ?CHENJ.Anintegratednumericaltech ̄niqueindeterminingblankshapeforNetscapesheetmet ̄
alforming[J].JournalofMaterialsProcessingTech ̄
nology?2006?177(1 ̄3):72 ̄75.
[29]一LANF'CHENJ?LINJ.AmethodofconstructingsmoothtoolsurfacesforFEpredictionofspringbackin
sheetmetalforming[J].JamalofMaterialsProcessing
Technology?2006?177(1 ̄3):382 ̄385.
[30]一CHENFKHUANGTB.DeepdrawingofsquarecupswithmagnesiumalloyAZ31sheets[J].International
JournalofMaterialsTools&Manufacture?2003?43:
1553 ̄1559.
[31]一FUCHSEAWILLIAMSDIL.Strainmeasurementatel ̄evatedtemperatureandhighstrainrates[C].The5th
AnnualHostileEnvironmentsandHighTemperature
MeasurementsConferenceProceedings?SocietyforEx ̄
perimentalMechanics?CostaMesa?CA.Bethel?CT
(US):SEM?1988:42 ̄48.
[32]一COLEGS?SHERMANAM.Lightweightmaterialsforautomotiveapplications[J].MaterialsCharacteriza ̄
tion?1995?35(1):3 ̄9.
[33]一NAKAT?NAKAYAMAYUEMORIT?etal.Effectsoftemperatureonyieldlocusfor5083aluminumalloysheet
[J].JournalofMaterialsProcessingTechnology?
2003?140(I ̄3):494 ̄499.
[34]一PAINTERMJ?PEARCEHotformingofaluminum ̄mag ̄nesiumalloysheet[C].ASTM?1982:105 ̄118. [35]一MANSESHHD?TAHERIAK.Bondstrengthandformabilityofanaluminum ̄cladsteelsheet[J].Jour ̄
nalofAlloyandCompounds?2003?361(1 ̄2):
138 ̄143.
[36]一SLAMOVAM?KARLIKM?ROBAUT?etal.Differ ̄encesinmicrostructureandtextureofAl ̄Mgsheetspro ̄
ducedbytwin ̄rollcontinuouscastingandbydirect ̄chill
casting[J].MaterialCharacterization?2002?49
(3):231 ̄240.
[37]一MICHAELKHERBERTB?DAVIDH?etal.Enhan ̄cingtheformabilityofaluminumcomponentsviatemper ̄
aturecontrolledhydroforming[J].JournalofMaterials
ProcessingTechnology?2005?167(2 ̄3):363 ̄370. [38]一HUSSAING?DARNU?GAOL?etal.AcomparativestudyOfftheforminglimitsofanaluminumsheet ̄metal
innegativeincrementalforming[J].JournalofMateri ̄
alsProcessingTechnology?2007?187 ̄188:94 ̄98. [39]一雷振?秦国梁?林尚扬.铝与钢异种金属焊接的研
究与发展概况[J].焊接?2006(4):16 ̄20. [40]一LAUKANTH?WALLMANNE?MLLERM?etal.
Flux ̄lesslaserbeamjoiningofaluminumwithzinccoa ̄
tedsteel[J].ScienceandTechnologyofWeldingand
Joining?2005?10(2):219 ̄226.
[41]一RATHODMJ?KUTSUNAM.UseofpulsedC02laserinlaserrollbondingofA5052aluminumalloyandlow
carbonsteel[J].WeldingintheWorld?2006?50
(7 ̄8):28 ̄36.
[42]一AIZAWATomokatsu?KASHANIMehrdad?OKAGAWAKeego.Applicationofmagneticpulseweldingforalumi ̄
numalloysandSPCCsteelsheetsjoints[J].Welding
intheWorld?2005?49(9):212 ̄222.
[43]一BARNESTA?PASHBYIR.Joiningtechniquesfora ̄luminumspaceflamesusedinautomobiles(PartⅡad ̄
hesivebondingandmechanicalfasteners)[J].Journal
ofMaterialsProcessingTechnology?2000?99(1 ̄3):
72 ̄79.
[44]一SUNXin?STEPHENSAEVKHALEELMA.Fatiguebehaviorsofself ̄piercingrivetsjoiningsimilaranddis ̄
similarsheetmetal[J].InternationalJournalofFa ̄
tigue?2007?29(2):370 ̄386.
幕墙铝合金立柱+型钢内芯组合构件的设计计算方法
2012.06 12 幕墙专栏 摘要:在玻璃幕墙设计中,遇到层高较大,铝合金型材强度、刚度难以满足需要时,设计者往往采用“铝合金立柱+型钢内芯”组合构件来解决。本文就该种情况下强度及挠度的计算方法进行探讨。 关键词:铝合金立柱;型钢内芯;组合构件;设计计算1 引言 玻璃幕墙是由铝型材与玻璃等材料组成的建筑外围护结构。在抗风、抗震设计中,立柱是主要的受力构件。一般都按简支梁或连续梁模式承受水平风力、地震力和竖向自重等外部作用,并按拉弯构件计算其强度和变形。因此合理选材,对保证玻璃幕墙具有良好的承载力、刚度及稳定性,确保其使用的安全性,无疑有着极其重要的作用。在幕墙工程设计中,遇到层高较大,铝合金型材强度、刚度难以满足需要时,经常采用型钢内芯增强铝合金立柱在抗风压、地震、自重等荷载效应下的强度和刚度值,以满足安全和挠度的要求。 2 计算方法探讨 设定组合构件的不同部件间“紧密相接”,但接触面没有抗剪能力。由于这种方式组成的构件不是“有机”的组合在一起的,各构件所分担的部分荷载必须通过解超静定结构的方法求解,即应该满足静力平衡,力与变形的物理关系—虎克定律,不同部件间的变形协调三个条件下求解。 首先,这种组成的构件内力与变形符合虎克定律—变形与内力成正比的弹性变形范围内,其次,这种组成的构件的各部件因“紧密相接”而变形一致,满足变形协调条件,所以各部件承担的荷载是与各自的刚度成正比。即抗弯构件按抗弯刚度EI正比分配,抗轴力构件按抗轴力刚度EF正比分配;抗剪力构件按抗剪切刚度GF正比分配;(E为弹性模量,G为剪切模量,I为截面惯性矩,F为截面面积)。幕墙立柱均以风压和地震力作用下的抗弯为主,所以,组合构件的各部件所承担的荷载主要与抗弯刚度成正比。 外荷载(F)根据铝型材与钢型材的刚度进行分配:铝型材荷载分配系数: μ1=E1I1/EI=E1I1/(E1I1+E2I2)钢型材荷载分配系数: μ2=E2I2/EI=E2I2/(E1I1+E2I2) 式中:EI=E1I1+E2I2—组合构件截面刚度E1I1—铝型材刚度 E2I2—钢型材刚度 知道每个构件所承担的荷载值后,就可以根据各个荷载类型的内力和挠度计算公式,叠加每个构件在各种类型荷载作用下的内力和挠度,验证其强度和挠度是否分别满足幕墙的安全和正常使用两个方面的要求。 3 工程应用实例3.1 工程概况 一幕墙工程位于北京市海淀区,楼层高度(幕墙的层间高度)为H=3.6m,幕墙的分格宽度为B=1.5m,基本风压按照50年一遇考虑,ω0=0.45kN/m2,地面粗超度为C类,8度抗震设防烈度。最危险点标高为He=100m。立柱采用“铝合金立柱+型钢内芯”组合构件,结构如图1所示。铝型材的材料特性及截面特征见表1,型钢的材料特性及截面特征见表2。 表1 铝型材的材料特性及截面特征牌号及状态 6063-T6 弹性模量E1/N/mm2 70000 抗拉屈服强度f1/N/mm2 150 惯性矩Ix1/mm4 3673500 抵抗矩Wx1/mm3 46710 截面面积A1/mm2 122100 表2 型钢的材料特性及截面特征 牌号 Q235 弹性模量E2/N/mm2 210000 抗拉屈服强度f2/N/mm2 235 惯性矩Ix2/mm4 734700 抵抗矩Wx2/mm3 2240 截面面积A2/mm2 61050 经计算:风荷载标准值Wk=1.468kN/m2; y轴方向(垂直于幕墙表面)的地震作用qEy=0.27kN/m2。3.2 刚度计算 “铝合金立柱+型钢内芯”组合构件所受线荷载和作用组合值为: q=Wk×B=1.468×1.5=2.202kN/m铝型材荷载分配系数: μ1=E1I1/(E1I1+E2I2)=70000×3673500/(70000×3673500+210000×734700)=0.63 钢型材荷载分配系数: μ2=E2I2/(E1I1+E2I2)=2 10000×73470/(70000×3673500+210000×734700)=0.37 铝合金立柱所承担的荷载为: q1=μ1q=0.63×2.202=1.387kN/m型钢内芯所承担的荷载为: q2=μ2q=0.37×2.202=0.815kN/m 按单跨简支梁计算,产生的挠度按下式计算: 铝合金立柱f1=5q1×L4/384E1I1=5×1.387×36004/384×70000×3673500=11.60mm 型钢内芯f2=5q2×L4/384E2I2=5×0.815×36004/384×210000×734700=11.60mm 幕墙“铝合金立柱+型钢内芯” 组合构件的设计计算方法 宋金虎 山东交通职业学院 a) b) c)图1“铝合金立柱+型钢内芯”组合构件结构示意图a)“铝合金立柱+型钢内芯”组合构件;b)铝合金立柱; c)型钢内芯
铝合金结构与钢结构对比分析
铝合金结构与钢结构对比分析 比较内容比较项目钢结构铝合金结构组合形式以钢网架、桁架或其它形式作为主体结构,主要采用工厂预制,现场焊接的方式连接。平方耗材量大,自重较重。以单层铝合金网架为主体结构,主要采用工厂精密加工,现场螺栓连接的方式组装。平方耗材量大概是钢结构的1/2-1/3,自重轻。结构对比1、结构用钢量较大2、大部分节点须采用现场焊接连接3、钢的密度为7850KG/m31、结构用量约为18KG/㎡2、全部采用不锈钢螺栓连接3、铝合金密度为2780KG/m3跨度依目前技术水平单层结构最大跨度在100M左右。(屋面凸出部分跨度大,矢高9米,钢结构很难一次性跨过,须在下部金属屋面上做大量密集的支撑,对下部钢结构荷载及屋面的防水影响极大,支撑用量大。依目前技术水平单层结构最大跨度在300M左右。(铝合金结构只需在四周适当位置设立支撑,可一次性跨过,这样减少了屋面大量的钢结构支撑,既减少了对金属屋面的破坏,减轻了下部钢结构的荷载,同时大大增加了建筑美观度。安装形式需要大型机械配合吊装,道路场地要求高,施工半径大。现场焊接量大,耗时长,现场焊接工艺难以控制。(会展场馆单体宽度为70米,在70米宽的屋面上安装钢结构需要大型的机械设备。采用现场焊接,现场工作量大,工期长,品质难以控制。)属高
空散装、不需大型机械,对道路场地要求低,施工半径小。现场全部采用螺栓连接。(铝合金杆件单支重量轻,采用高空散装,螺栓连接,轻便,快速。)施工工艺总体建筑约65000个节点,现场大量焊接、修改,施工管理及质量控制很复杂。(曲面形状的钢结构节点焊接复杂,外观美观差。)现场全部采用螺栓连接,由一家单位一次性施工完成。施工环节单一,大大降低了施工管理及质量控制难度。钢结构铝合金结构工期该网架是设立在铝镁锰屋面上,只有当下部结构完成后方可施工,而钢结构需要大型机械参与施工,约束条件多,现场焊接量大,所以整体工期较长。无大型机械,无现场焊接。现场安装工期大概可节约60%。维护维修该场馆位于嘉陵江边,重庆雾多,空气潮湿,再加上还有酸雨天气,所以钢结构采用树脂油漆防腐,湿气、酸碱腐蚀严重。一般使用5年后需翻新。铝合金结构母材的防腐性能就很好,湿气、酸碱抵蚀力均很强。要是进行阳极氧化,防腐性能更佳。使用生命期内不需翻新。下部结构钢结构自重较重,对下部结构反力较大,下部结构应满足上部结构的自重要求。铝合金结构自重轻,同等跨度下,大概是钢结构的1/2-1/3,大大减轻了下部结构的荷载。下部结构可节省5%-8%的直接造价。节能环保属传统结构形式,没有节能环保的新概念。在结构上耗用的原材料大大降低。同时铝合金型材在再生利用率上比钢材高出30%。
浅析钢铝组合结构在幕墙设计中的应用
浅析钢铝组合结构在幕墙设计中的应用 发表时间:2019-08-23T16:55:27.580Z 来源:《建筑细部》2018年第28期作者:罗玲霞 [导读] 随着幕墙在建筑中的广泛应用,其建筑材料也在不断更新,钢铝结构的型材一出现就受到市场追捧,本文就重点探讨一下钢铝组合结构在幕墙设计中的应用。 上海华艺幕墙系统工程有限公司上海 200000 摘要:钢铝结构的型材投放市场以来,深受建筑工程用户喜爱,因为它承重力好、耐腐蚀、寿命长、易操作、重量轻等特点一举击败传统型材占领了建筑市场。但是钢铝组合也不是无懈可击的,所以在应用中要了解它的特点扬长避短,才能发挥出它的潜能,下文就是笔者对钢铝结构在幕墙设计中的应用的研究。 关键词:钢铝组合结构;幕墙设计;计算机辅助计算 随着建筑市场的持续升温,幕墙这种新兴建筑形式也在不断地发展更新,这种保温、美观、安全防火的建筑形式现在被普遍应用在建筑项目中。现代建筑已经不满足其简单的固有属性,而是向美观性、实用性、欣赏性发展。幕墙技术恰恰迎合了这种要求,得以迅猛发展壮大起来。随着幕墙在建筑中的广泛应用,其建筑材料也在不断更新,钢铝结构的型材一出现就受到市场追捧,本文就重点探讨一下钢铝组合结构在幕墙设计中的应用。 一、钢铝组合结构应用于幕墙设计中的技术优势 1、钢铝组合的综合优势强 同样面积的幕墙型材类型进行比较,幕墙工程选用钢铝组合结构的建材的话,和单纯铝型材结构,单纯钢件结构等建筑材料相比的话,钢铝结构在价格方面,承重方面,加工方面综合下来的话是最有优势的,市场上铝锭的价格大概1万4千多一吨,而碳素钢则为5800多一吨,钢铝组合既避免了大量使用铝型材造成的成本过量,又避免全部使用钢型材造成的运输及施工难度,钢铝结构相对减轻了很多重量,所以就可以更加紧密的固定在建筑外表,给建筑减轻了负担本身也更加安全耐用了,最重要的是满足结构要求的条件下节省了工程费用。 2、钢铝组合的强度大 如果用单纯的铝型材做建筑幕墙的话,那么铝合金的弹性是0.7X103MPa,强度是85.5MPa在高层建筑中和大风天气下,很难达到设计要求;而钢材的弹性模是2.1x103MPa,强度设计是215MPa其强度是铝合金的三倍,所以幕墙采用钢铝结构以后强度上来了、质量降低了所以受到欢迎。 3、钢铝组合设计灵活 钢铝组合型材在幕墙中应用的时候,选择了两种金属的优点进行组合,使其特点是既有坚韧性又质量轻。钢材用于幕墙的称重部分,铝型材比较美观就用在幕墙外面做装饰。这样的设计既可以用到刚才坚固耐用,又兼顾了铝材质量轻、耐腐蚀、不生锈还美观的特点,真是相得益彰完美的组合,这样的应用在幕墙上比较经济实惠还坚固耐用。 4、钢铝组合结构设计的防火性能强 铝合金在建筑中承重方面的性能偏弱一点,因为这种型材不耐高温随着温度升高,它的承重能力就会下降直到全部丧失承重能力。而钢材却恰恰相反,钢材在高温条件下,其承重能力不降反升。所以建中工程中一定要采用钢材作为承重之用,建筑幕墙就是看中了钢材的这种特点,采用钢材做承重部分既安全又可靠。 二、钢铝组合结构应用于幕墙设计中存在的问题 目前钢铝结构的组合在幕墙工程的应用中由于缺少规范所以比较混乱,钢铝组合幕墙因其明显的优势被广泛的应用在建筑幕墙施工中,国家也作了相应的规定,但是由于钢铝组合占领市场时间不长,相对应的数据指标还在检测阶段,所以职能机构目前没有比较规范的指标来对钢铝组合幕墙进行规范,这种情况下就不能对钢铝结构幕墙进行有效的管理工作,会直接影响到工程质量。 三、钢铝组合结构在幕墙设计中应用计算机进行计算 为了分析钢铝结构能否符合设计要求,可不可以应用在建筑幕墙施工中,就要对幕墙的承重、质量等指标进行检测。在目前我国对这种型材的检测还处在实验阶段,方法还不成熟接下来跟大家分享一个检测方法。 1、计算机辅助计算方法的假设条件的设定 (1)由于钢铝结构在幕墙应用中是紧密结合在一起的,所以它们垂直的受力是相等的。 (2)经过过分析认为,轴向力的影响很小所以就忽略不计了。 2、等效形心轴的求解 通过公式进行验算,我们看到钢材和铝材的受力是按钢度分担的,所以先算出钢度然后再根据弹性模量和惯性的计算然后求出等效形心轴。 3钢铝组合结构的计算机辅助计算方法 在得出了等效形心轴以后,就可以对钢铝结构的面积进行计算了,在计算中要用到布尔运算定律和质量特性,来进行求解最后得出基于等效形心轴的数据。 挠数是一个比较重要的参数,在大型幕墙施工中钢铝组合的总重要的指标就是挠数。借助计算机辅助计算钢铝结构的参数地方法,也会有一定的误差但是它已经不会对始终造成什么影响了,因为已经比较细微可以忽略不计了。 四、加强幕墙结构技术的对策研究 1、增强幕墙结构设计的质量意识,提高质量管理水平 工程设计人员在设计幕墙结构以后还要反复核查,幕墙在设计中要兼顾很多因素,必须做出合理的解释。在施工中相关承建单位要设立行之有效的质量管理体系,严把施工质量关对关键控制性环节指派专人进行质量把关,因为幕墙施工是一个建筑物的“门面”所以必须做
钢铝组合截面杆件的设计
钢铝组合截面杆件的设计 摘要 钢铝组合截面是工程中经常应用的一种截面形式。本文对钢铝组合截面的截面特性计算以及截面验算进行简略的介绍。 关键词 钢铝组合截面,钢铝叠合截面 一.引言 在幕墙支承结构和铝合金门窗骨架设计中,为了节省铝合金用量、降低成本,往往采用钢、铝组合截面的杆件,外露部分采用铝合金型材,隐蔽部分亦即主要受力部分采用钢型材,这样,即达到了外表美观靓丽、截面小巧而承载能力高、造价又低廉的目的。另外,在幕墙加固工程中,钢铝组合截面也时有应用。 钢、铝组合截面的形式,一般常用的不外乎如图 1所示的两种。其中 a 所示的是将钢型材川入铝合金型材的腔内;而 b 所示是钢、铝合金型材并列,二者截面一般有一个共同的对称轴。 对于这两种截面形式,视钢、铝型材的 组合方式,又可分为叠合式和组合式两种。 所谓叠合式,即钢、铝型材之间不加连接,仅仅从构造上能保证二者同时受力即可;而 组合式和叠合式不同,它是在钢、铝型材之 间用物理的或化学的方法将二者紧密相连的 组合形式。由于这两种截面的组合方式不同, 所以在受力后的表现也不同,设计计算方法 也完全不同,下面分别予以介绍。 图1 二.叠合式截面杆件的设计 如图 2所示叠合式截面杆,当其在横向力作用下受弯时,杆件将发生弯曲变形。由于钢、铝型材之间不加连接,因此,在二者接触面间无任何约束(忽略摩擦),当杆件发生弯曲变形时,在接触面间,二者会产生相互错动,受荷前在同一竖向截面内的abcd 亦不在同一截面了,可见,此时的受弯杆件,已不符合“平截面的假定”条件,因此,二者已不能按一体进行计算了。 考虑到钢、铝型材受荷后,截面未脱开,二者有着共同的边界约束条件,在正常受力情况下,变形在弹性范围内,因此二者各自沿自身截面中和轴产生挠曲,且,二者产生的挠度相等。所以: g l q q = gx g lx l I E I E 亦即,二者分配的荷载与其刚度成正比,于是有: q l =gx g lx l lx l I E I E I E q +;q g =gx g lx l gx g I E I E I E q + 若以内力的形式来表达,亦可写成如下的形式: M l =gx g lx l lx l I E I E I E M +;M g =gx g lx l gx g I E I E I E M + N l =g g l l l l A E A E A E N +;N g =g g l l g g A E A E A E N + 其中:M , N-----总弯矩,总轴力 图 2 M l ,N l -----铝合金型材分配的弯矩,轴力
钢铝型材
钢铝组合截面杆件的设计 闭思廉李硕龚沁华 深圳中航幕墙工程有限公司深圳市皇城广场1804室 518045 摘要钢铝组合截面是工程中经常应用的一种截面形式。本文对钢铝组合截面的截面特性计算以及截面验算进行简略的介绍。 关键词钢铝组合截面,钢铝叠合截面 一.引言 在幕墙支承结构和铝合金门窗骨架设计中,为了节省铝合金用量、降低成本,往往采用 钢、铝组合截面的杆件,外露部分采用铝合金型材,隐蔽部分亦即主要受力部分采用钢型材, 这样,即达到了外表美观靓丽、截面小巧而承载能力高、造价又低廉的目的。另外,在幕墙 加固工程中,钢铝组合截面也时有应用。 钢、铝组合截面的形式,一般常用的不外乎如图 1所示的两种。其中 a所示的是将钢 型材穿入铝合金型材的腔内;而 b所示是钢、铝合金型材并列,二者截面一般有一个共 同的对称轴。 钢、铝型材的组合方式,又可分 为叠合式和组合式两种。所谓叠 合式,即钢、铝型材之间不加连 接,仅仅从构造上能保证二者同 时受力即可;而组合式和叠合式 不同,它是在钢、铝型材之间用 物理的或化学的方法将二者紧 密相连的组合形式。由于这两种 截面的组合方式不同,所以在受 力后的表现也不同,设计计算方 法也完全不同,下面分别予以介 绍。图 1 二.叠合式截面杆件的设计 如图 2所示叠合式截面杆,当其在横向力作用下受弯时,杆件将发生弯曲变形。由于 钢、铝型材之间不加连接,因此,在二者接触面间无任何约束(忽略摩擦),当杆件发生弯 曲变形时,在接触面间,二者会产生相互错动,受荷前在同一竖向截面内的abcd亦不在同 一截面了,可见,此时的受弯杆件,已不符合“平截面的假定”条件,因此,二者已不能按 一体进行计算了。 考虑到钢、铝型材受荷后,截面未脱开,二者有着共同的边界约束条件,在正常受力情 况下,变形在弹性范围内,因此二者各自沿自身截面中和轴产生挠曲,且二者产生的挠度相 等。所以:
钢结构和铝结构的执行标准
钢结构和铝结构的实施标准 Part 2:钢结构的技术要求 前言 这个英国标准是UK BS1090-2:2008的补充。它取代了DD ENV1090-1:1998,DD ENV1090-4:2001 和DD ENV1090-6:2001已经被取缔,BS5400-6:1999 和 BS5950-2:2001将在2010年3月取缔。 UK委托B/512钢结构标准技术协会和B/525/10桥梁技术协会共同参与标准的准备工作。该组织的成员名单可以从委员会秘书处获得。 其他信息 BSI作为CEN的成员有权出版EN1090-2:2008作为英国标准,但是,值得注意的是,随着欧洲标准的发展,UK委员会对本标准作为欧洲标准提出反对意见。 UK委员会反对的原因是,担心就执行等级和焊接质量水平而言,可能会出现错误的规定。如果出现,关于选择范围和基础有可能导致低于规范、安全和高于规范的问题,可能产生贸易壁垒。建议这些版本要低一些,避免这类风险。 本标准(EN1090-2)给出了钢结构实施(生产和安装)的技术要求,是BS EN1090-1 Part1的支持标准。她与BS EN1090-1 Part1的一致性评估需要生产者在工厂生产控制过程中进行实际操作。对于产品的的质量管理要求包括,例如:可追溯性和焊接质量管理,可参考BS EN1090-2给出的定义。 本标准取代了几种现存的标准,所以范围非常广泛,因此在每一部分使用之前需要制作系列项目或明确的应用结论来进行分类。附录A列出了其他的可供选择的信息。 实施等级 本标准引进了实施等级的概念,用来对整套结构、单个部件和详细元件进行等级区分,附录3列出了标准对等级划分的要求。 由设计决定整套结构、单个部件和详细元件的等级选择, BS EN1090-2 附录B给出了关于等级划分决策的一些信息指导,划分的主要原因是提供可靠性标准,避免后续过程中结构、部件或元件出现破坏或故障(见BS EN1990,欧洲规范-结构设计基础,更多信息)。因此实施等级在本标准中被广泛使用,作为质量决策、试验要求和合格标准的可靠性区分依据。但是新的区分标准和BS EN1990推荐的区分标准之间的关系没有完全的界定。 BS EN1090-2 附录B推荐等级的选择可以根据服务种类(SC)来确定部件设计的使用环境和产品种类(PC)确定部件的使用方法,其他两种型号(结构和元件)也适应这种分类,对于结构、部件和元件的等级划分,要根据使用或生产过程的困难程度,形成线性增长。
2004钢铝组合结构的计算机辅助结构计算
钢铝组合结构的计算机辅助结构计算 深圳市方大装饰工程有限公司 林勇生 董格林 谢士涛 [摘 要] 介绍了钢铝组合结构的计算机辅助结构计算方法,可供设计人员参考。 [关键词] 钢铝组合结构 等效形心轴 计算机辅助结构计算 1.钢铝组合结构的产生和发展 随着建筑幕墙技术的发展,幕墙被应用到越来越多的建筑中,而对于大分格、大跨度、大风压地区(如大连、厦门、深圳等)的玻璃幕墙,采用铝合金结构已不能满足幕墙对骨架结构强度和刚度的要求。 于是有设计师开始选用工字钢、方钢通等钢型材来作为受力构件。但实际使用中,由于生产加工过程中其精度难以控制在理想范围,导致装饰效果差,而且由于受表面处理的局限性和材料本身性能的影响,极易出现褪色、漆膜脱落等现象,严重者甚至锈迹斑斑。有的设计师想到在钢结构外包饰一层铝塑复合板,但新的问题又出现了,由于铝塑复合板需在工地现场折弯,折弯角度难以控 22.1强度要求 《玻璃幕墙工程技术规范》(以下简称96102-JGJ )和《金属与石材幕墙工程技术规范》(以下简称2001133-JGJ )规定构件截面最大应力设计值不应超过材料强度设计值: f ≤σ )1( 式中 σ 荷载和作用产生的截面最大应力设计值)(MPa ; f 材料强度设计值)(MPa 。 2.2 刚度要求 )96102(-JGJ 和)2001133(-JGJ 规定横梁或立柱的最大挠度应符合下式要求: ][u u ≤ )2( 式中 u 荷载和作用标准值产生的挠度最大值)(mm ; ][u 挠度允许值)(mm 。 具体指标为: 当跨度不大于m 5.7时: 铝型材:180/l u ≤ 且mm u 20≤ 钢型材:300/l u ≤ 且mm u 15≤ 当跨度大于m 5.7时: