余热发电系统并网运行的技术特点3
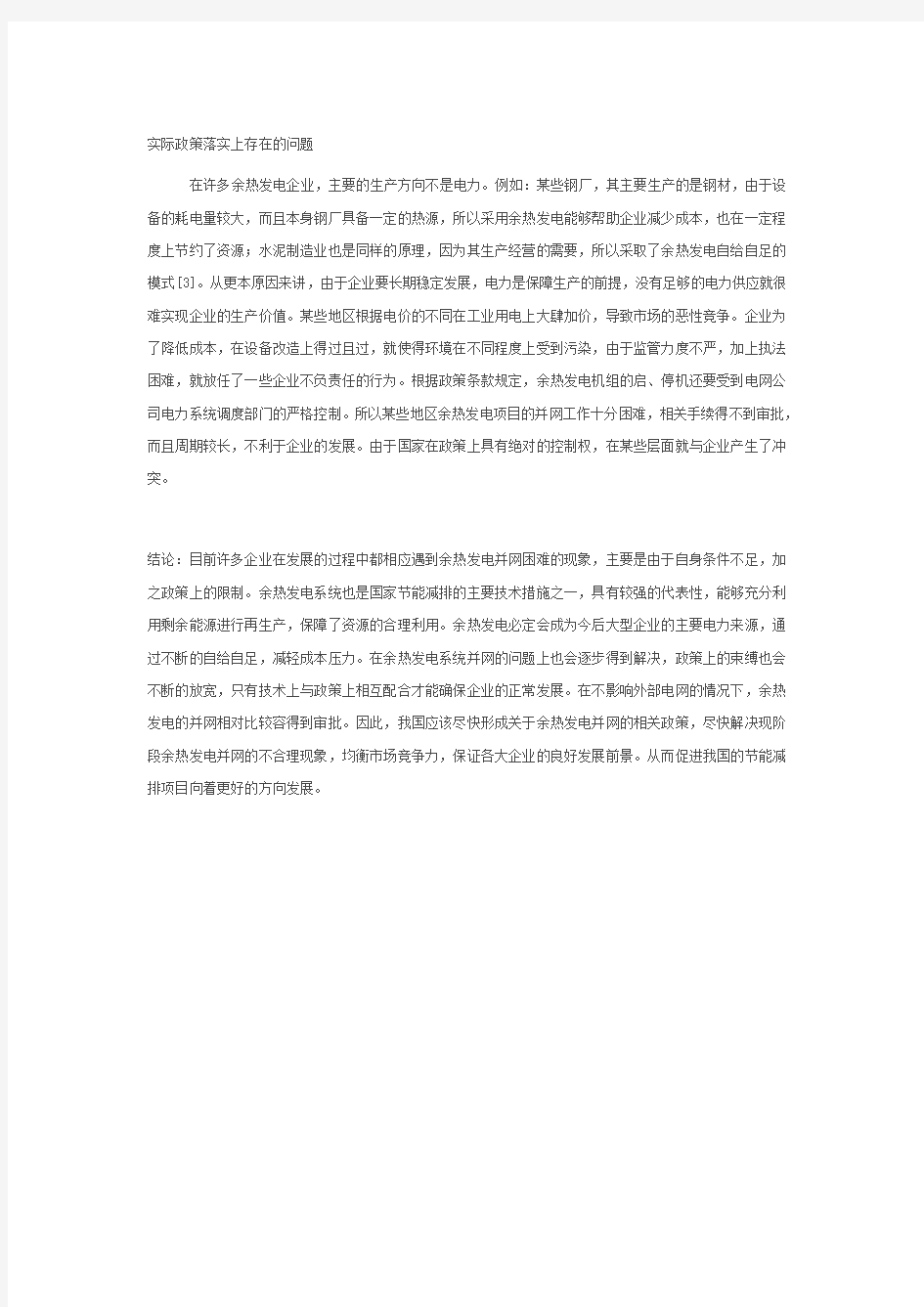
实际政策落实上存在的问题
在许多余热发电企业,主要的生产方向不是电力。例如:某些钢厂,其主要生产的是钢材,由于设备的耗电量较大,而且本身钢厂具备一定的热源,所以采用余热发电能够帮助企业减少成本,也在一定程度上节约了资源;水泥制造业也是同样的原理,因为其生产经营的需要,所以采取了余热发电自给自足的模式[3]。从更本原因来讲,由于企业要长期稳定发展,电力是保障生产的前提,没有足够的电力供应就很难实现企业的生产价值。某些地区根据电价的不同在工业用电上大肆加价,导致市场的恶性竞争。企业为了降低成本,在设备改造上得过且过,就使得环境在不同程度上受到污染,由于监管力度不严,加上执法困难,就放任了一些企业不负责任的行为。根据政策条款规定,余热发电机组的启、停机还要受到电网公司电力系统调度部门的严格控制。所以某些地区余热发电项目的并网工作十分困难,相关手续得不到审批,而且周期较长,不利于企业的发展。由于国家在政策上具有绝对的控制权,在某些层面就与企业产生了冲突。
结论:目前许多企业在发展的过程中都相应遇到余热发电并网困难的现象,主要是由于自身条件不足,加之政策上的限制。余热发电系统也是国家节能减排的主要技术措施之一,具有较强的代表性,能够充分利用剩余能源进行再生产,保障了资源的合理利用。余热发电必定会成为今后大型企业的主要电力来源,通过不断的自给自足,减轻成本压力。在余热发电系统并网的问题上也会逐步得到解决,政策上的束缚也会不断的放宽,只有技术上与政策上相互配合才能确保企业的正常发展。在不影响外部电网的情况下,余热发电的并网相对比较容得到审批。因此,我国应该尽快形成关于余热发电并网的相关政策,尽快解决现阶段余热发电并网的不合理现象,均衡市场竞争力,保证各大企业的良好发展前景。从而促进我国的节能减排项目向着更好的方向发展。
余热发电系统工艺流程
生产工艺流程: (19)余热发电系统 本方案拟采用单压纯低温余热发电技术,与双压系统和闪蒸系统相比,单压系统流程相对较简单,当设计选择的锅炉能完全吸收烟气放出的热量时,采用单压设计更为合理,系统内不同参数的工质较少,控制操作都更简单,窑头锅炉和汽轮机设备造价降低,系统管路减少,投资相对更省。 结合本工程的生产规模及投资环境,拟采用单压纯低温余热发电技术。该技术不使用燃料来补燃,因此不对环境产生附加污染,是典型的资源综合利用工程。主蒸汽的压力和温度较低,运行的可靠性和安全性高,运行成本低,日常管理简单。 综合考虑本工程2500t/d熟料新型干法水泥生产线窑头、窑尾的余热资源分布情况和水泥窑的运行状况,确定热力系统及装机方案如下:系统主机包括一台PH余热锅炉、一台AQC余热锅炉和一套凝汽式汽轮发电机组。 据2500t/d水泥熟料生产线窑头冷却机废气排放温度的分布,在满足熟料冷却及工艺用热的前提下,采驭中部取气,从而提高进入窑头余热锅炉-AQC炉的废气温度,减少废气流量,在缩小 AQC炉体积的同时增大了换热量。并且提高了整个系统的循环热效率。 在窑头冷却机中部废气出口设置窑头余热锅炉 AQC炉,该锅炉分 2段设置,其中I段为蒸汽段,II段为热水段。AQC炉 II段生产的 150° C 热水提供给AQC炉 I段及PH锅炉°AQC炉I段生产的 1.6MPa- 3 2 0。C 的过热蒸汽作为主蒸汽与窑尾余热锅炉 P H炉生产的同参数过热蒸汽合并后,一并进入汽轮机作功。汽轮机的凝结水进入余热锅炉AQC炉I工段,加热后分别作为锅炉给水进入余热锅炉 SP炉、余热锅炉A QC炉的I
段。 ②PH余热锅炉:在窑尾预热器的废气出口管道上设置PH余热锅炉,该锅炉包括过热器和蒸发器,生产 1.6MPa-32 0C的过热蒸汽,进入蒸汽母管后通入汽轮发电机组,出 P H余热锅炉废气温度降到18 0 —200C,供生料粉磨烘干使用。P H锅炉热效率可达35%以上。 ③汽轮发电机组:上述二台余热锅炉生产的蒸汽共可发电 4100kW 因此配置4500kW凝汽式汽轮机组一套。 整个工艺流程是:40 C左右的给水经过除氧,由锅炉给水泵加压进入 AQC 锅炉省煤器后加热成135 C左右的热水,热水分成两部分,一部分送往AQC锅炉,另一部分送往SP锅炉;然后依次经过各自锅炉的蒸发器、过热器产生1.6MPa-320C和1.6MPa-320C的过热蒸汽,在蒸汽母管汇合后进入汽轮发电机组做功,做功后的乏汽进入凝汽器成为冷凝水,冷凝水和补充纯水经除氧器除氧再进行下一个热力循环。 PH锅炉出口废气温度180-200 C左右,用于烘干生料。 表2-6主要余热发电设备一览表
发动机余热发电系统设计方案
发动机余热发电系统设计方案 1.1 课题研究的背景 我国建设节约型社会的现状不容乐观,进入21世纪以来,我国经济社会继续保持了快速发展的势头,取得了有目共睹的伟大成就,也遭遇前所未曾有过的资源约束和环境制约。针对这些情况,中央适时地提出了建设资源节约型、环境友好性社会等一系列新的观念和决策。节约型社会目的是通过“加快建设资源节约型社会,推动循环经济发展。解决全面建设小康社会面临的资源约束和环境压力问题。保障国民经济持续快速协调健康发展(国办发(2004330号文件),强调在经济活动中节约资源和保护环境的同等重要性,要求经济效率和环境保护并驾齐驱。要求人类发展生态经济,追求以节约资源、能源和减少污染为前提的生念经济效率,要求人类在经济活动中实现经济与环境的协凋统一。目前,建没节约型社会多从节能技术、绿色技术、循环经济等方面展开,这有利于节约型社会建设的深入发展。在现在这个飞速发展的社会通无疑是很重要的一块,而汽车、飞机、船舶等交通运输工具又是不可或缺的,而发动机是汽车、飞机、船舶等交通运输工具的核心部件,其应用围非常广泛。随着人类社会的发展,发动机的数量急速增加。以汽车为例,2005年汽车保有量达3300万台,预计2010年将超过7000万台。与之相对应的是发动机数量的剧增和废热的大量排放。调查研究表明,发动机燃料燃烧所发出的能量只有34%~38%(柴油机)或25%~28%(汽油机)被有效利用。其它的能量被排放到发动机体外,仅由排气带走的热量就占进入发动机中的燃料所产生热量的30%~45%。这一方面造成了较大的能源浪费,另一方面使周边环境温度升高,带来了城市的热岛效应等不良影响。热污染首当其冲的受害者是水生物,由于水温升高使水中溶解氧减少,水体处于缺氧状态,同时又使水生生物代率增高而需要更多的氧,造成一些水生生物在热效力作用下发育受阻或死亡,从而影响环境和生态平衡。此外,河水水温上升给一些致病微生物造成一个人工温床,使它们得以滋生、泛滥,引起疾病流行,危害
余热发电的工艺流程、主要设备和工作原理简单介绍
纯低温余热发电工艺流程、主机设备和工作原理简介 直接利用水泥窑窑头窑尾排放的中低温废气进行余热回收发电,无需消耗燃料,发电过程不产生任何污染,是一种经济效益可观、清洁环保、符合国家清洁节能产业政策的绿色发电技术,具有十分广阔的发展空间与前景。 工艺流程: 凝汽器热水井内的凝结水经凝结水泵泵入.2闪蒸器出水集箱,与出水汇合,然后通过锅炉给水泵升压泵入锅炉省煤器进行加热,经省煤器加热后的水(223℃)分三路分别送到炉汽包炉汽包和.1闪蒸器内。进入两炉汽包内的水在锅炉内循环受热,最终产生一定压力下的过热蒸汽作为主蒸汽送入汽轮机做功.进入.1闪蒸器内的高温水通过闪蒸技术产生一定压力下的饱和蒸汽送入汽轮机第三级后做功,而№.1闪蒸器的出水作为№.2闪蒸器闪蒸饱和蒸汽的热源,№.2闪蒸器闪蒸出的饱和蒸汽送入汽轮机第五级后做功,做过功后的乏汽经过凝汽器冷凝后形成凝结水重新参与热力循环。生产过程中消耗掉的水由纯水装置制取出的纯水经补给水泵打入热水井。 主机设备性能特点: 一、余热锅炉: 炉和炉 锅炉的设计特点如下: 锅炉型式为立式,锅炉由省煤器、蒸发器、过热器、汽包及热力管道等构成。锅炉前设置一预除尘器(沉
降室),降低入炉粉尘。废气流动方向为自上而下,换热管采用螺旋翅片管,以增大换热面积、减少粉尘磨损的作用。锅炉内不易积灰,由烟气带走,故未设置除灰装置,工质循环方式为自然循环方式。 过热器作用:将饱和蒸汽变成过热蒸汽的加热设备,通过对蒸汽的再加热,提高其过热度(温度之差),提高其单位工质的做功能力。 蒸发器作用:通过与烟气的热交换,产生饱和蒸汽。 省煤器作用:设置这样一组受热面,对锅炉给水进行预热,提高给水温度,避免给水进入汽包,冷热温差过大,产生过大热应力对汽包安全形成威胁,同时也避免汽包水位波动过大,造成自动控制困难。一方面最大限度地利用余热,降低排烟温度,另一方面,给水预热后形成高温高压水,作为闪蒸器产生饱和蒸汽的热源。 沉降室作用:利用重力除尘的原理将烟气中的大颗粒熟料粉尘收集,避免粉尘对锅炉受热面的冲刷、磨损。 锅炉的设计特点如下: 锅炉型式为卧式,锅炉由蒸发器、过热器、汽包及热力管道构成,废气流动方向为水平流动,换热管采用蛇形光管,以防止积灰。因生料具有粘附性,故锅炉设置振打装置进行除灰,工质循环为采用循环泵进行强制循环方式。 二、汽轮机 汽轮机是用具有一定温度和压力的蒸汽来做功的回转式原动机。依其做功原理的不同,可分为冲动式汽轮机和反动式汽轮
余热发电工艺参数
余热发电运行数据参数 油系统规
汽水系统 暖管 1汽机一切检查准备工作就绪后,值班长通知热机操作员,稍开AQC(SP炉汽门的旁路门,保持压力维持在0.2?0.3Mpa,以温升速度为5?10C/min暖管;当管壁温度达130?140C后,以0.25 Mpa/min的速度提升管压力至额定后(1.2 5Mpa),全开AQC (SP)炉并汽门,关闭旁路门。 2开始暖管时,疏水门应全开,随着管壁温度和管压力的升高,应逐渐关小疏水门,以防大量蒸汽漏出;
3在升压过程中若发生管道振动,应立即降压直至振动消除,经充分疏水后, 方可继续升压。 4在暖管中完成保安系统的静态试验; 5为防止在调节保安系统进行试验时有蒸汽漏入汽缸引起转子变形,在试验 过程中要持续盘车;转子未转动之前,严禁蒸汽漏入汽缸及用任何方式预热汽轮机; 6暖管同时,首先启动循环水泵,再向凝汽器灌水;启动凝结水泵并开启再循环门,使凝结水在凝汽器之间循环,维持好热井水位。 7在升压过程中随时注意检查管道膨胀和支吊状况,在暖管过程中随着温度 压力升高,注意调整控制旁路门及疏水门的开启。 凝结器抽真空 1启动射水泵,使真空迅速提高; 2当真空升高到-0.085Mpa后,可以扣上危急遮断油门; 3当润滑油温达到35~38 C时,逐渐进行低速暖机. 汽轮机下列条件禁止启动 1主要表计或任一保安装置失灵; 2电动主汽门、自动主汽门有卡涩现象; 3调速系统不能维持汽轮机空负荷运行或甩去全负荷后不能控制转速; 4交流高压油泵、交流润滑油泵、直流油泵均不正常; 5油质不合格,或润滑油压低于正常值; 6汽轮发电机组振动超过0.05mm ; 7汽轮发电机组转动部分有明显摩擦声;
余热发电工艺流程大纲纲要及主机设备具体工作原理.doc
纯低温余热发电工艺流程及主机设备工作原理 工艺流程 :凝汽器热水井内的凝结水经凝结水泵泵入闪蒸器出 水集箱,与出水汇合 , 然后通过锅炉给水泵升压泵入AQC锅炉省煤器进行加热 , 经省煤器加热后的水(167 ℃ ) 分三路分别送到AQC炉汽包,PH 炉汽包和闪蒸器内。进入两炉汽包内的水在锅炉内循环受热, 最终产生一定压力下的过热蒸汽作为主蒸汽送入汽轮机做功 . 进入闪蒸器内的高温水通过闪蒸技术产生一定压力下的饱和蒸汽送入汽轮 机后三级做功,做过功后的乏汽经过凝汽器冷凝后形成凝结水重新参 与热力循环。生产过程中消耗掉的水由纯水装置制取出的纯水经补给 水泵打入热水井。 主机设备性能及原理: 一、余热锅炉 : AQC 炉和 PH炉 AQC锅炉的设计特点如下 :锅炉型式为立式,锅炉由省煤器、蒸发器、过热器、汽包及热力管道等构成。锅炉前设置一预除尘器(沉降室),降低入炉粉尘。废气流动方向为自上而下,换热管采用螺旋翅片管,以增大换热面积、减少粉尘磨损的作用。锅炉内不易积灰,由 烟气带走,故未设置除灰装置,工质循环方式为自然循环方式。 过热器作用:将饱和蒸汽变成过热蒸汽的加热设备,通过对蒸汽的 再加热,提高其过热度(温度之差),提高其单位工质的做功能力。 蒸发器作用:通过与烟气的热交换,产生饱和蒸汽。 省煤器作用:设置这样一组受热面,对锅炉给水进行预热,提高
给水温度,避免给水进入汽包,冷热温差过大,产生过大热应力对汽 包安全形成威胁,同时也避免汽包水位波动过大,造成自动控制困难。一方面最大限度地利用余热,降低排烟温度,另一方面,给水预热后 形成高温高压水,作为闪蒸器产生饱和蒸汽的热源。 沉降室作用:利用重力除尘的原理将烟气中的大颗粒熟料粉尘收 集,避免粉尘对锅炉受热面的冲刷、磨损。 PH 锅炉的设计特点如下: 锅炉型式为卧式, 锅炉由蒸发器、过热器、汽包及热力管道构成,废气流动方向为水平流动, 换热管采用蛇形光管 , 以防止积灰。因生料具有粘附性,故锅炉设置振打装置进行除灰 , 工质循环为采用循环泵进行强制循环方式。 锅炉工作原理:利用废气加热蒸发设备,使设备内的水变成蒸汽 , 为气轮机提供气源。 二、汽机系统 汽轮机是用具有一定温度和压力的蒸汽来做功的回转式原动机。 依其做功原理的不同,可分为冲动式汽轮机和反动式汽轮机两种类 型。两种型式汽轮机各具特点,各有其发展的空间。 冲动式汽轮机:蒸汽的热能转变为动能的过程,仅在喷嘴中发生,而工作叶片只是把蒸汽的动能转变成机械能的汽轮机。即蒸汽仅在喷嘴中产生压力降,而在叶片中不产生压力降。 反动式汽轮机:蒸汽的热能转变为动能的过程,不仅在喷嘴中发生,而且在叶片中也同样发生的汽轮机。即蒸汽不仅在喷嘴中进行膨胀,产生压力降,而且在叶片中也进行膨胀,产生压力降。 冲动式与反动式在构造上的主要区别在于:
余热发电DCS系统应用介绍
余热发电DCS系统 应用介绍
目录 第一章工业生产中余热发电背景介绍 (1) 第一节工业生产中能源综合利用现状 (1) 第二节我国冶金行业余能综合利用发展前景 (1) 第三节余热发电发展趋势 (2) 第四节工业生产过程中的余热综合利用概况 (2) 第二章水泥厂余热发电介绍 (3) 第一节水泥厂余热发电项目的兴起 (3) 第二节水泥厂余热发电的工作过程 (3) 第三节应用和推广前景 (3) 第三章集散控制系统(DCS)简介 (5) 第一节DCS网络 (5) 第二节DCS节点和系统组态 (5) 第三节DCS系统的发展 (5) 第四节DCS系统的应用 (6) 第四章项目现场设备介绍 (8) 第一节现场锅炉、汽机、主要辅机设备及现场仪表 (8) 一、监控中心二楼 (9) 二、一楼凝汽器、冷油器、泵房、循环水管等。 .................................... 错误!未定义书签。 三、监控中心楼下的配电屏柜.................................................................... 错误!未定义书签。 第二节中控室控制设备 ............................................................................... 错误!未定义书签。 一、常规监控系统屏柜与后台系统............................................................ 错误!未定义书签。 二、余热发电控制器及IO屏...................................................................... 错误!未定义书签。
余热发电工艺流程讲解
余热发电工艺流程讲解
余热发电工艺流程讲解 授课人:孙飞 原水箱 纯水装置 凝汽器 凝结水泵 锅炉给水泵 AQC 炉省煤器 AQC 炉汽包 AQC 蒸发器 AQC 炉过热器 汽轮机 发电机 PH 炉汽包 PH 炉过热器 PH 炉蒸发器 闪蒸器 纯水箱 纯低温水泥窑余热发电技术是直接利用窑头窑尾排放的中低温废气进行余热回收发电,无需消耗燃料,发电过程不产生任何
污染,是一种经济效益可观、清洁环保、符合国家清洁节能产业政策的绿色发电技术,具有十分广阔的发展空间与前景。 工艺流程(见附图): 余热电站的热力循环是基本的蒸汽动力循环,即汽、水之间的往复循环过程。蒸汽进入汽轮机做功后,经凝汽器冷却成凝结水,凝结水经凝结水泵(150A/B)泵入闪蒸器出水集箱,与闪蒸器出水汇合,然后通过锅炉给水泵(230A/B)升压泵入AQC锅炉省煤器进行加热,经省煤器加热后的高温水(167℃)分三路分别送到AQC炉汽包,PH炉汽包和闪蒸器内。进入两炉汽包内的水在锅炉内循环受热,最终产生一定压力下的过热蒸汽作为主蒸汽送入汽轮机做功.进入闪蒸器内的高温水通过闪蒸原理产生一定压力下的饱和蒸汽送入汽轮机第七级起辅助做功作用,做过功后的乏汽经过凝汽器冷凝后形成凝结水重新参与热力循环。生产过程中消耗掉的水由纯水装置制取出的纯水经补给水泵(511)打入热水井(凝汽器140)。 水泥厂余热资源的特点是:流量大,品位较低。以宁国水泥厂4000t/d生产线为例,PH(预热器)和AQC(冷却机)出口废气流量和温度分别为258550Nm3/h、350℃和306600Nm3/h、238℃,余热发电便是充分利用这两部分余热资源进行热能回收。 1)热力系统 整个热力系统设计力求经济、高效、安全,系统工艺流程是
余热发电油系统介绍
余热发电汽轮机组油系统工艺知识介绍 一、油系统的作用及工艺流程 1. 油系统的作用 (1)减少轴承的摩擦损失,并带走因磨擦产生的热量和由转子传来的热量; (2)向调节系统和保护系统装置供油,以保证其正常工作;(3)供给传动机构的润滑用油 (4)供油过程中对管道及轴承起到清洗和防腐蚀的作用。 2.供油的工艺流程 由主油泵或高压交流油泵打出的油被送到润滑油过滤器和油冷却器处,控制油压力调节阀将使油压保持在0. 8MPa以上,另外调整油冷却器入口冷却水量,控制油温度调节阀使汽机、发电机各处轴承入口处供油温度保持在35-45℃之间。 油路在润滑油过滤器入口处分为两条支路: (1)一路到控制系统部分,控制油送到调节器主伺服电机,紧急停车阀及超速调节器导引阀等停车设施,为使控制油压波动最小,在管线上装有过压阀:注入润滑油压力为0.6MPa压力;(2)另一路为润滑路线,0.8MPa高压油由双重孔板及润滑油压调节阀来降至0.1~0.13MPa左右,润滑油被送至汽机的每个轴承、减速机与发电机、减速啮合齿轮及盘车设施。 二、供油系统的设备组成及作用
1.余热发电油系统的组成:主油泵、高压交流油泵、润滑交流油泵、直流油泵、注油器、油过滤器、冷油器、油净化器、低压油过压阀、启动排油阀、油雾风扇、油箱、单向阀及相关的管道和阀门。 2.作用 1、主油泵:离心式油泵,位于减速机齿轮轴的前向端,由主减速齿轮通过一套泵驱动齿轮来驱动,离心泵由主轴直接带动,设备简单,系统紧凑,但自吸能力差,需使用注油器向油泵供油。 2. 高压交流油泵:又称启动油泵或调速油泵,其作用是在主油泵不能正常工作时向调节、保护、润滑系统供油。自动启动连锁条件:润滑油压≤1MPa时高压油泵自动启动; 3. 润滑交流油泵、直流油泵:润滑交流油泵和直流油泵又称低压辅助油泵或事故油泵,作用是在主油泵不能供给系统润滑油时向各轴承及盘车装置提供润滑油。自动启动连锁条件:润滑油压≤0.05MPa时润滑交流油泵自动启动;润滑油压≤0.04MPa时直流油泵自动启动; 4.冷油器:对润滑油进行降温冷却的设备,控制润滑油温度在35°C~45°C之间,属于表面式换热器。油从上而下沿若干隔板构成的弯曲流道流动,冷却水则是自上而下在铜管中流动。要求油侧压力要高于水侧压力,防止铜管破裂时由内进水而使油质恶化。 5.润滑油过滤器、调速油过滤器在切换时:
发电汽轮机组油系统工艺知识介绍
讲义余热发电 余热发电汽轮机组油系统工艺知识介绍(一) 一、系统组成 三线汽轮机供油系统一部分由主油泵向汽轮机发电机组各轴承提供润滑油及调节保安系统提供压力油;另一部分是主油泵通过滤油器向DEH中电液驱动器供油。机组推荐采用GB11120-89中规定的L-TSA46汽轮机油,在冷却水温度经常低于15oC情况下,允许用GB11120-89中规定的L-TSA32汽轮机油来代替。 1、低压控制系统 主要包括主油泵,注油器I,注油器II,主油泵启动排油阀,高压交流油泵,交流、直流润滑油泵,油箱,冷油器,滤油器,润滑油压力控制器及过压阀等。 离心式主油泵由汽轮机主轴直接带动,正常运转时主油泵出口油压为1.3MPa,出油量为3.0m3/min,该压力油除供给调节系统及保安系统外,大部分是供给两只注油器的。两只注油器并联组成,注油器I出口油压为0.10~0.15MPa,向主油泵进口供油,而注油器II的出口油压为0.22MPa,经冷油器,滤油器后供给润滑油系统。 机组启动时应先开低压润滑交流油泵,以便在低压的情况下驱除油管道及各部件中的空气。然后再开启高压交流油泵,进行调节保安系统的试验调整和机组的启动。在汽轮机启动过程中,由高压交流电动油泵供给调节保安系统和通过注油器供给各轴承润滑用油。为了防止压力油经主油泵泄走,在主油泵出口装有逆止阀。同时还装有主油泵启动排油阀,以使主油泵在起动过程油流畅通。当汽轮机升速至额定转速时(主油泵出口油压高于电动油泵出口油压),可通过出口管道上的阀门减少供油量,然后停用该泵,由主油泵向整个机组的调节保安和润滑系统供油。在停机时,可先启动高压电动油泵,在停机后的盘车过程中再切换成交流润滑油泵。 为了防止调节系统因压力油降低而引起停机事故,所以当主油泵出口油压降低至1.3MPa时,由压力开关使高压交流油泵自动启动投入运行。 当运行中发生故障,润滑油压下降时,由润滑油压力控制器使交流润滑油泵自动启动,系统另备有一台直流润滑油泵,当润滑油压下降而交流润滑油泵不能正常投入工作时,由润滑油压力控制器使直流润滑油泵自动启动,向润滑系统供油。 正常的润滑油压力为:0.08~0.15MPa 油压降低时要求:小于0.08 MPa 发信号 小于0.05 MPa 交流润滑油泵自动投入
余热发电系统
2.6 余热发电系统 概述 本工程拟利用垃圾焚烧余热锅炉产生的过热蒸汽,供凝汽式汽轮发电机组发电。 垃圾焚烧余热锅炉产生的过热蒸汽参数为4.1MPa 400C。考虑 到由余热锅炉过热器出口至汽轮机蒸汽入口间管路上的温度、压力损失,本工程汽机进汽参数确定为3.8MPa 390C。在设计条件下3台焚 烧余热锅炉产汽108.51t/h ,供汽轮机用汽。按照全厂处理能力 8 1200t/d,全年运行8000h计算,汽轮机组年发电约:1.787 X 10 KWh 全厂热效率约为:18.68%,厂用电率:21%。 选用2台12MW最大15MW凝汽式汽轮发电机组。一段非调整抽汽 供焚烧炉空气预热器,二段非调整抽汽共除氧及采暖用。 热力系统及辅助设备选择 根据垃圾焚烧发电厂以处理垃圾为主的特点,汽轮发电机组采用“机随炉”的运行方式。为保证在汽轮机故障或检修期间垃圾焚烧炉的稳定运行,设置了汽机旁路系统,用于汽机停机时将主蒸汽通过两级减温减压后送入凝汽器,凝结水送至除氧器,在除氧器除氧加热后用给水泵送至余热锅炉,维持垃圾焚烧锅炉的正常运行。凝汽式机组的抽汽为非调整抽汽,抽汽压力和流量随着机组负荷的变化而变化。 在汽轮机负荷较低时,一、二级抽汽量不能满足空气预热器和 除氧器的加热蒸汽的要求,设置主蒸汽减温减压器,补充抽气量的不足。在汽机检修而焚烧炉仍然运行时,通过减温减压器全部或部分提供空气预热器和除氧器加热蒸汽。 热力发电系统主要有下列四种运行工况: 1) 正常发电工况
在正常焚烧发电工况下,3炉2机运行。3台余热余热锅炉产生的过热 蒸汽送往汽轮发电机组,汽轮机一级抽汽送至焚烧炉空气预热器用于加热一次风,其疏水回收送至除氧器;二级抽汽进入除氧器加热给水。三级抽汽进入低压加热器,加热从凝汽器经凝结水泵加压后经汽封加热器预热的凝结水。此工况下,汽轮机的进汽按照余热锅炉产汽量调节。汽机检修与锅炉检修同时进行。 2) 停机不停炉工况 1台汽轮机检修或故障停机,3台垃圾焚烧锅炉正常运行,产汽量为 108.51t/h 。扣除汽水损失,剩余汽量为105.3t/h, 在此工况下,另一台汽轮机在最大工况下运行,发电15MWV进汽量约为71.04t/h,剩余 34.26t/h ,一部分通过减温减压器用于空气预热器和除氧器,其余进入检修汽机的旁路蒸汽冷凝系统,旁路蒸汽冷凝系统的一、二级减温减压器和待修汽机的冷凝器投入运行。 3) 机炉检修工况 当1台垃圾焚烧锅炉检修时,另1台运行的锅炉以最大产气量运行,供 1 台汽轮机在最大工况下运行,故可同时安排另1 台汽轮机检修。因此,在每年大修时应同时安排锅炉与汽机检修,以提高经济效益。 主蒸汽系统(含旁路蒸汽冷凝系统) 余热锅炉过热蒸汽集汽联箱出口到汽轮机进口的蒸汽母管,以
余热发电工艺流程讲解
余热发电工艺流程讲解 授课人:孙飞 纯低温水泥窑余热发电技术是直接利用窑头窑尾排放的中低温废气进行余热回收发电,无需消耗燃料,发电过程不产生任何
污染,是一种经济效益可观、清洁环保、符合国家清洁节能产业政策的绿色发电技术,具有十分广阔的发展空间与前景。 工艺流程(见附图): 余热电站的热力循环是基本的蒸汽动力循环,即汽、水之间的往复循环过程。蒸汽进入汽轮机做功后,经凝汽器冷却成凝结水,凝结水经凝结水泵(150A/B)泵入闪蒸器出水集箱,与闪蒸器出水汇合,然后通过锅炉给水泵(230A/B)升压泵入AQC锅炉省煤器进行加热,经省煤器加热后的高温水(167℃)分三路分别送到AQC炉汽包,PH炉汽包和闪蒸器内。进入两炉汽包内的水在锅炉内循环受热,最终产生一定压力下的过热蒸汽作为主蒸汽送入汽轮机做功.进入闪蒸器内的高温水通过闪蒸原理产生一定压力下的饱和蒸汽送入汽轮机第七级起辅助做功作用,做过功后的乏汽经过凝汽器冷凝后形成凝结水重新参与热力循环。生产过程中消耗掉的水由纯水装置制取出的纯水经补给水泵(511)打入热水井(凝汽器140)。 水泥厂余热资源的特点是:流量大,品位较低。以宁国水泥厂4000t/d生产线为例,PH(预热器)和AQC(冷却机)出口废气流量和温度分别为258550Nm3/h、350℃和306600Nm3/h、238℃,余热发电便是充分利用这两部分余热资源进行热能回收。 1)热力系统 整个热力系统设计力求经济、高效、安全,系统工艺流程是由两台高效余热锅炉AQC、PH?锅炉闪蒸器和一套汽轮发电机
组组成,辅之以冷却水系统、纯水制取系统、锅炉给水系统及锅炉粉尘输送系统。余热锅炉内进行热交换产生压力为25kg/cm2、温度为335℃~350℃、额定蒸发量为101t/h的过热蒸汽通入汽轮机,进行能量转换,拖动发电机向电网输送电力。 (1)采用凝汽式混汽式汽轮机。凝汽式是指做过功的蒸汽充分冷凝成凝结水,重新进入系统循环,减少系统补充水量。混汽式是指汽轮机除主蒸汽外,另有一路低压饱和蒸汽导入汽轮机做功,从而提高汽轮机相对内效率,提高发电机输出功率。 (2)设置具有专利技术、高热效率的余热PH锅炉,采用特殊设计的机械振打装置进行受热面除灰,保证锅炉很高的传热效率。 (3)应用热水闪蒸技术(高压热水进入低压空间瞬间汽化现象),设置一台低压闪蒸器,一方面将闪蒸出的饱和蒸汽导入汽轮机做功,进一步提高汽轮机做功功率,另一方面形成锅炉给水系统循环,可以有效地控制AQC炉省煤器段出口水温,保证锅炉给水工况稳定。 (4)由于PH出口废气还要用于原料烘干,所以PH锅炉无省煤器,只设蒸发器和过热器,控制出炉烟温在250℃,仍可满足水泥生产线工艺需求。 (5)采用热水闪蒸自除氧结合化学除氧的办法进行除氧,不另设除氧器,减少了工艺设备,简化了工艺流程。
纯低温余热发电系统
第十一章纯低温余热发电系统 11.1 发电规模 发电规模按5000t/d熟料生产线配套设计。 水泥生产线的窑头、窑尾会排放大量的废气,通常仅利用废气的余热来烘干原料,利用率很低,其余大量废气的余热不仅没有得到利用,而且还要对废气进行喷水降温,浪费水和电能。因此,利用余热发电技术回收这部分废气的热能,可以使水泥生产企业提高能源利用效率,降低成本,提高产品市场竞争力,降低污染物排放量。 综合考虑水泥熟料生产线的工艺流程、场地布置、供配电结构、供水设施等因素,利用生产线窑头、窑尾余热资源,可建设一条装机容量为9000KW的纯低温余热电站。 11.2 设计原则 1)余热电站在正常运行时应不影响原水泥生产线的正常生产; 2)充分利用窑头、窑尾排放的废气余热; 3)采用工艺成熟、技术先进的余热发电技术和装备; 4)余热电站尽可能与水泥生产线共用水、电、机修等公用设施; 5)贯彻执行有关国家和拟建厂当地的环境保护、劳动安全、消防设计的规范。 11.3 设计条件 1)余热条件 从更合理的利用窑头余热考虑,窑头篦冷机需要进行改造,在篦冷机的中部增加一个废气出口,改造后的窑头废气参数为:240000Nm3/h,360℃。此部分废气余热全部用于发电。 窑尾经五级预热器出口的废气参数为:312500Nm3/h,320℃。此部分废气经利用后的温度应保持在220℃左右,用于生料粉磨烘干。 2)建设场地 本工程包括:窑头AQC锅炉、窑尾SP锅炉、汽机房、化学水处理车间、冷却塔及循环水泵房等车间。 各车间布置遵循以下原则:窑头AQC锅炉和沉降室布置在窑头
厂房旁边的空地上,窑尾SP锅炉布置在窑尾高温风机的上方,汽机房的布置靠近锅炉,化学水处理车间、冷却塔及循环水泵房尽量靠近汽机房。在布置有困难时可以适当调整,不能影响水泥生产线的布置。 AQC锅炉占地面积:14.2m×6.35m SP锅炉占地面积:22m×12m 汽机房占地面积:31m×20.4m 3)水源、给水排水 电站的用水有:软化水处理、锅炉给水、循环冷却水及其它生产系统消耗,消防用水,部分用水可循环使用。 11.4 电站工艺系统 1)余热电站流程 本方案拟采用纯低温余热发电技术,该技术不使用燃料来补燃,因此不对环境产生附加污染;是典型的资源综合利用工程。主蒸汽的压力和温度较低,运行的可靠性和安全性高,运行成本低,日常管理简单。 综合考虑目前水泥生产线窑头、窑尾的余热资源分布情况和水泥窑的运行状况,确定热力系统及装机方案如下: 系统主机包括两台余热锅炉、一套补汽式汽轮发电机组。 a.AQC余热锅炉:利用冷却机中部抽取的废气(中温端,~360℃),在生产线窑头设置AQC余热锅炉,余热锅炉分为高压蒸汽段、低压蒸汽段和热水段运行;高压蒸汽段生产 1.6MPa-350℃的过热蒸汽,进入蒸汽母管后通入汽轮发电机组,低压蒸汽段生产0.15MPa-140℃的过热蒸汽,热水段生产的140℃热水后,作为AQC 余热锅炉蒸汽段及SP余热锅炉的给水,出AQC锅炉废气温度降至110℃。 b.SP余热锅炉:在窑尾设置SP余热锅炉,仅设置蒸汽段,生产 1.6MPa-305℃的过热蒸汽,进入蒸汽母管后通入汽轮发电机组,出SP余热锅炉废气温度降到220℃,供生料粉磨烘干使用。 c.汽轮发电机组:上述余热锅炉生产的蒸汽共可发电7.9MW,因此配置9MW补汽式汽轮机组一套。
余热发电的工艺流程、主要设备和工作原理简单介绍讲课教案
余热发电的工艺流程、主要设备和工作原理简单介绍
纯低温余热发电工艺流程、主机设备和工作原理简介 直接利用水泥窑窑头窑尾排放的中低温废气进行余热回收发电,无需消耗燃料,发电过程不产生任何污染,是一种经济效益可观、清洁环保、符合国家清洁节能产业政策的绿色发电技术,具有十分广阔的发展空间与前景。 工艺流程: 凝汽器热水井内的凝结水经凝结水泵泵入No.2闪蒸器出水集箱,与出水汇合,然后通过锅炉给水泵升压泵入AQC锅炉省煤器进行加热,经省煤器加热后的水(223℃)分三路分别送到AQC炉汽包,PH炉汽包和No.1闪蒸器内。进入两炉汽包内的水在锅炉内循环受热,最终产生一定压力下的过热蒸汽作为主蒸汽送入汽轮机做功.进入No.1闪蒸器内的高温水通过闪蒸技术产生一定压力下的饱和蒸汽送入汽轮机第三级后做功,而№.1闪蒸器的出水作为№.2闪蒸器闪蒸饱和蒸汽的热源,№.2闪蒸器闪蒸出的饱和蒸汽送入汽轮机第五级后做功,做过功后的乏汽经过凝汽器冷凝后形成凝结水重新参与热力循环。生产过程中消耗掉的水由纯水装置制取出的纯水经补给水泵打入热水井。 主机设备性能特点: 一、余热锅炉: AQC炉和PH炉
AQC锅炉的设计特点如下: 锅炉型式为立式,锅炉由省煤器、蒸发器、过热器、汽包及热力管道等构成。锅炉前设置一预除尘器(沉降室),降低入炉粉尘。废气流动方向为自上而下,换热管采用螺旋翅片管,以增大换热面积、减少粉尘磨损的作用。锅炉内不易积灰,由烟气带走,故未设置除灰装置,工质循环方式为自然循环方式。 过热器作用:将饱和蒸汽变成过热蒸汽的加热设备,通过对蒸汽的再加热,提高其过热度(温度之差),提高其单位工质的做功能力。 蒸发器作用:通过与烟气的热交换,产生饱和蒸汽。 省煤器作用:设置这样一组受热面,对锅炉给水进行预热,提高给水温度,避免给水进入汽包,冷热温差过大,产生过大热应力对汽包安全形成威胁,同时也避免汽包水位波动过大,造成自动控制困难。一方面最大限度地利用余热,降低排烟温度,另一方面,给水预热后形成高温高压水,作为闪蒸器产生饱和蒸汽的热源。 沉降室作用:利用重力除尘的原理将烟气中的大颗粒熟料粉尘收集,避免粉尘对锅炉受热面的冲刷、磨损。 PH 锅炉的设计特点如下: 锅炉型式为卧式,锅炉由蒸发器、过热器、汽包及热力管道构成,废气流动方向为水平流动,换热管采用蛇形光管,以防止积灰。因生料具有粘附性,故锅炉设置振打装置进行除灰,工质循环为采用循环泵进行强制循环方式。 二、汽轮机
余热发电项目技术方案
饱和蒸汽发电项目 技术方案 编制单位: 目录
第一章项目概况 (1) 第二章项目现有发电条件 (1) 2.1现有余热 2.2蒸汽利用情况 第三章余热发电方案拟定 (2) 3.1汽轮机部分 3.2发电机及配电保护部分 3.3工艺流程图 3.4方案特点 第四章循环水系统 (5) 第五章电气系统 (5) 5.1电气主接线 5.2系统组成 5.3控制保护系统 5.4站用电配电 5.5直流配电系统 5.6过电压保护和电力装置的接地 5.7主要电气设备选型 第六章总平面设计布置方案 (6) 6.1场址选择 6.2总平面设计主要技术指标 6.3建筑设计方案 第七章项目内容及投资预算 (7) 7.1建设内容 7.2项目投资预算 第八章项目主要技术经济指标及建设周期 (10) 8.1项目营运主要经济指标 8.2项目建设周期 结语 (10) 第一章项目概况
现有两台饱和蒸汽锅炉,蒸汽产汽量分别为6.0T/H和5.3T/H,锅炉工作制度为330天/年、24H/天。目前所产蒸汽全部排空,为实现节能减排,有效利用能源,要求利用现有余热条件,制定发电方案。 第二章项目现有发电条件 2.1现有余热 根据现场考察及甲方提供的条件,现有余热锅炉产汽情况如下表: 2.2蒸汽利用情况 经向甲方了解,目前业主生产工艺没有利用蒸汽的负荷,生产所产生的饱和蒸汽经过管网后直接排空,没有任何利用。详见下表:
第三章余热发电方案拟定 根据上述热能条件,初步拟定发电方案为:饱和蒸汽凝汽式汽轮机发电机组方案,本方案主要设备及参数如下: 3.1汽轮机部分 3.1.1汽轮机参数 排汽参数:0.014Mpa(a),52.6℃ 回热抽汽参数:0.612 Mpa(a),160℃,0.9 t/h 额定工况:6500rpm, 进汽量:10.3 t/h, 补汽量:1.0 t/h, 电功率:1.29MW, 汽耗:7.98kg/(kw.h), 热耗:16957KJ/(kw.h)。 3.1.2汽轮机随机清单 ⑴、随机工具一套、随机备件一套 ⑵、循环水泵2台 ⑶、交流油泵1台 ⑷、给水及蒸汽管道、电动阀门1台 ⑸、凝结水泵2台 ⑹、DEH(汽机电调系统)、ETS(汽机停电保护)、TSI(汽机安全监视装置)1套 ⑺、凉水塔:800立方/时1座
余热发电系统工艺流程
生产工艺流程: (19)余热发电系统 本方案拟采用单压纯低温余热发电技术,与双压系统和闪蒸系统相比,单压系统流程相对较简单,当设计选择的锅炉能完全吸收烟气放出的热量时,采用单压设计更为合理,系统内不同参数的工质较少,控制操作都更简单,窑头锅炉和汽轮机设备造价降低,系统管路减少,投资相对更省。 结合本工程的生产规模及投资环境,拟采用单压纯低温余热发电技术。该技术不使用燃料来补燃,因此不对环境产生附加污染,是典型的资源综合利用工程。主蒸汽的压力和温度较低,运行的可靠性和安全性高,运行成本低,日常管理简单。 综合考虑本工程2500t/d熟料新型干法水泥生产线窑头、窑尾的余热资源分布情况和水泥窑的运行状况,确定热力系统及装机方案如下: 系统主机包括一台PH余热锅炉、一台AQC余热锅炉和一套凝汽式汽轮发电机组。 ① 据2500t/d水泥熟料生产线窑头冷却机废气排放温度的分 布,在满足熟料冷却及工艺用热的前提下,采驭中部取气, 从而提高进入窑头余热锅炉-AQC炉的废气温度,减少废气流 量,在缩小AQC炉体积的同时增大了换热量。并且提高了整 个系统的循环热效率。 在窑头冷却机中部废气出口设置窑头余热锅炉AQC炉,该锅炉分2段设置,其中I段为蒸汽段,II段为热水段。AQC炉II段生产的150°C热水提供给AQC炉I段及PH锅炉。AQC炉I段生产的1.6MPa- 320。C的过热蒸汽作为主蒸汽与窑尾余热锅炉PH炉生产
的同参数过热蒸汽合并后,一并进入汽轮机作功。汽轮机的凝结水进入余热锅炉AQC炉I工段,加热后分别作为锅炉给水进入余热锅炉SP炉、余热锅炉AQC炉的I段。 ②PH余热锅炉:在窑尾预热器的废气出口管道上设置PH余热锅炉,该锅炉包括过热器和蒸发器,生产1.6MPa-320℃的过热蒸汽,进入蒸汽母管后通入汽轮发电机组,出PH余热锅炉废气温度降到180-200℃,供生料粉磨烘干使用。PH锅炉热效率可达35%以上。 ③汽轮发电机组:上述二台余热锅炉生产的蒸汽共可发电4100kW,因此配置4500kW凝汽式汽轮机组一套。 整个工艺流程是:40℃左右的给水经过除氧,由锅炉给水泵加压进入AQC锅炉省煤器后加热成135℃左右的热水,热水分成两部分,一部分送往AQC锅炉,另一部分送往SP锅炉;然后依次经过各自锅炉的蒸发器、过热器产生1.6MPa-320℃和1.6MPa-320℃的过热蒸汽,在蒸汽母管汇合后进入汽轮发电机组做功,做功后的乏汽进入凝汽器成为冷凝水,冷凝水和补充纯水经除氧器除氧再进行下一个热力循环。PH锅炉出口废气温度180-200℃左右,用于烘干生料。 表2-6主要余热发电设备一览表 序号没备名称及型号数量主要技术参数、性能、指标 1 凝汽式汽轮机 1 型号: BN4.1-0.689/0.13 额定功率: 4.1MW 最大功率4.4MW 额定转速: 5600r/min 输出轴转速: 3000r/min 主汽门前压力:0.689MPa 主汽门前温度:313.9℃ 排气压力:7k Pa 2 4.5MW发电机 1 型号: 额定功率:4.5MW 额定转速:3000r/min
低温余热发电系统设计方案
低温余热发电系统设计方案 1. 需考虑的问题 低温余热发电系统的窑尾余热锅炉(SP炉)和篦冷机余热锅炉(AQC炉)串联于熟料生产线上,两锅炉阻力均小于1000Pa。设计时,必须考虑下列问题: (1)窑尾主排风机和窑头、窑尾电除尘器及其风机的能力是否适应增设窑尾余热锅炉和篦冷机余热锅炉的条件; (2) 原料磨的热风系统能否满足工艺要求; (3) 该两台锅炉系统的安装是否不破坏原生产厂房。 经对窑系统设计资料认真复核,确认增设两台锅炉系统后所涉及的上述设备能力可以满足要求,不须作任何改造;两台锅炉系统的布置可以不破坏原生产厂房;出窑尾锅炉废气被送至生料原系统作为烘干热源,经核算,只要控制出窑尾锅炉废气温度≥240℃~℃260就可满足入磨原料综合水份≤5%的烘干要求。 双压纯低温余热发电技术介绍 双压余热发电技术就是按照能量梯级利用的原理,在同一台余热锅炉中设置2个不同压力等级的汽水系统,分别进行汽水循环,产生高压和低压两种过热蒸汽;高压过热蒸汽作为主蒸汽、低压过热蒸汽作为补汽分别进入补汽凝汽式汽轮机,推动汽轮机做功发电,双压余热发电系统使能量得到合理利用,热回收效率高。 余热资源参数不同,余热锅炉的低压受热面与高压受热面有不同的布置方式。根据辽源金刚水泥厂窑头(AQC)和窑尾(SP)的余热特点和工艺要求,经过余热利用后,要使AQC余热锅炉排烟温度降到100℃左右。使窑尾SP余热锅炉排烟温度降低到220℃左右后进入原料磨烘干原料,其设置的双压余热发电系统简图如 图1。
双压余热发电系统与常规余热发电系统不同之处在于其窑头(AQC)余热锅炉增设了低压汽水系统,其汽轮机组在第四压力级之后增加了补汽口,并适当增大补汽口以后汽轮机通流部分面积。 采用双压系统的主要目的是为了提高系统循环效率。使低品位的热源充分利用,获得最大限度的发电功率,降低窑头(AQC)双压余热锅炉的排气温度;其次是双压系统的低压蒸汽是过热的,进入汽轮机后能保证汽轮机内的蒸汽最大湿度控制在14%以下,使汽轮机叶片工作在安全范围内,并提高机组的效率;同时低压蒸汽还可用于供热等其它需要热源的地方,提高运行灵活性。 双压余热发电系统简单灵活、成本低、热利用率高。由于在余热锅炉上增设了低压省煤器、低压蒸发器,并且增设了低压过热器,能够把更多的低温余热吸收利用,比单压系统多发电10%左右,并且必要时能够解列,维持单压系统正常运行。而对于能够增加发电量的闪蒸系统来说,需要增加闪蒸器、汽水分离器等设备;闪蒸器产生的是饱和蒸汽,在进入汽轮机做功后,易使汽轮机排汽干度不能满足汽轮机的要求。 1995年8月17日国家计委、原国家建材局与日本新能源产业技术综合开发机构(NEDO)签订了基本协议书,由中国安徽海螺集团宁国水泥厂与日本川崎重工株式会社实施。该项目1996年10月18日动工,199 5年2月8日并网发电一次成功。 水泥厂余热资源的特点是流量大、品位低。在宁国水泥厂4000t/d生产线上,预热器(PH)和冷却机(AQC)出口废气流量和温度分别为258550Nm3/h、340℃和306600Nm3/h、238℃,其中部分预热器废气用来烘干燃煤和原料。针对上述特点,热力系统采用减速式两点混气式汽轮机,利用参数较低的主蒸汽和闪蒸汽的饱和蒸汽发电;根据余热资源的工艺状况设置两台余热锅炉,保证能够充分利用余热资源;应用热水闪蒸技术,设置一台高压闪蒸器和一台低压闪蒸器,闪蒸出的饱和蒸汽混入汽轮机做功;对现有AQC 进行废气二次循环改造。由于PH出口废气还要用于烘干原料,因此未设省煤器,只设蒸发器和过热器。加强系统密封。系统采用先进的DCS集散控制系统进行操作控制,具有功能齐全、自动控制、操作简便等特点。 工艺流程图(见图) 此主题相关图片如下:
余热发电工艺参数
余热发电工艺参数-标准化文件发布号:(9456-EUATWK-MWUB-WUNN-INNUL-DDQTY-KII
余热发电运行数据参数主机技术规范 汽机主要参数 油系统规范
汽水系统 暖管 1汽机一切检查准备工作就绪后,值班长通知热机操作员, 稍开AQC(SP)炉汽门的旁路门, 保持压力维持在0.2~0.3Mpa,以温升速度为5~10℃/min暖管;当管壁温度达130~140℃后,以0.25 Mpa/min的速度提升管内压力至额定后(1.2 5Mpa),全开AQC(SP)炉并汽门,关闭旁路门。 2开始暖管时,疏水门应全开,随着管壁温度和管内压力的升高,应逐渐关小疏水门,以防大量蒸汽漏出; 3在升压过程中若发生管道振动,应立即降压直至振动消除,经充分疏水后,方可继续升压。 4在暖管中完成保安系统的静态试验; 5为防止在调节保安系统进行试验时有蒸汽漏入汽缸引起转子变形,在试验过程中要持续盘车;转子未转动之前,严禁蒸汽漏入汽缸及用任何方式预热汽轮机; 6暖管同时,首先启动循环水泵,再向凝汽器灌水;启动凝结水泵并开启再循环门,使凝结水在凝汽器之间循环,维持好热井水位。 7在升压过程中随时注意检查管道膨胀和支吊状况,在暖管过程中随着温度压力升高,注意调整控制旁路门及疏水门的开启。 凝结器抽真空 1启动射水泵,使真空迅速提高; 2当真空升高到-0.085Mpa后,可以扣上危急遮断油门; 3当润滑油温达到35~38℃时,逐渐进行低速暖机. 汽轮机下列条件禁止启动 1主要表计或任一保安装置失灵; 2电动主汽门、自动主汽门有卡涩现象;
3调速系统不能维持汽轮机空负荷运行或甩去全负荷后不能控制转速; 4交流高压油泵、交流润滑油泵、直流油泵均不正常; 5油质不合格,或润滑油压低于正常值; 6汽轮发电机组振动超过0.05mm; 7汽轮发电机组转动部分有明显摩擦声; 8因发生异常情况停机,汽机本体设备有明显损坏或尚未查明原因。 9主蒸汽温度低于250℃。 10蒸汽室温度低于200℃。 11启动时真空值不应低于-0.006Mpa。 为了保持汽轮机能在经济状态下运行,主汽门前参数应保持在下列范围内: