各材料常用刀具转速进给参数对照表
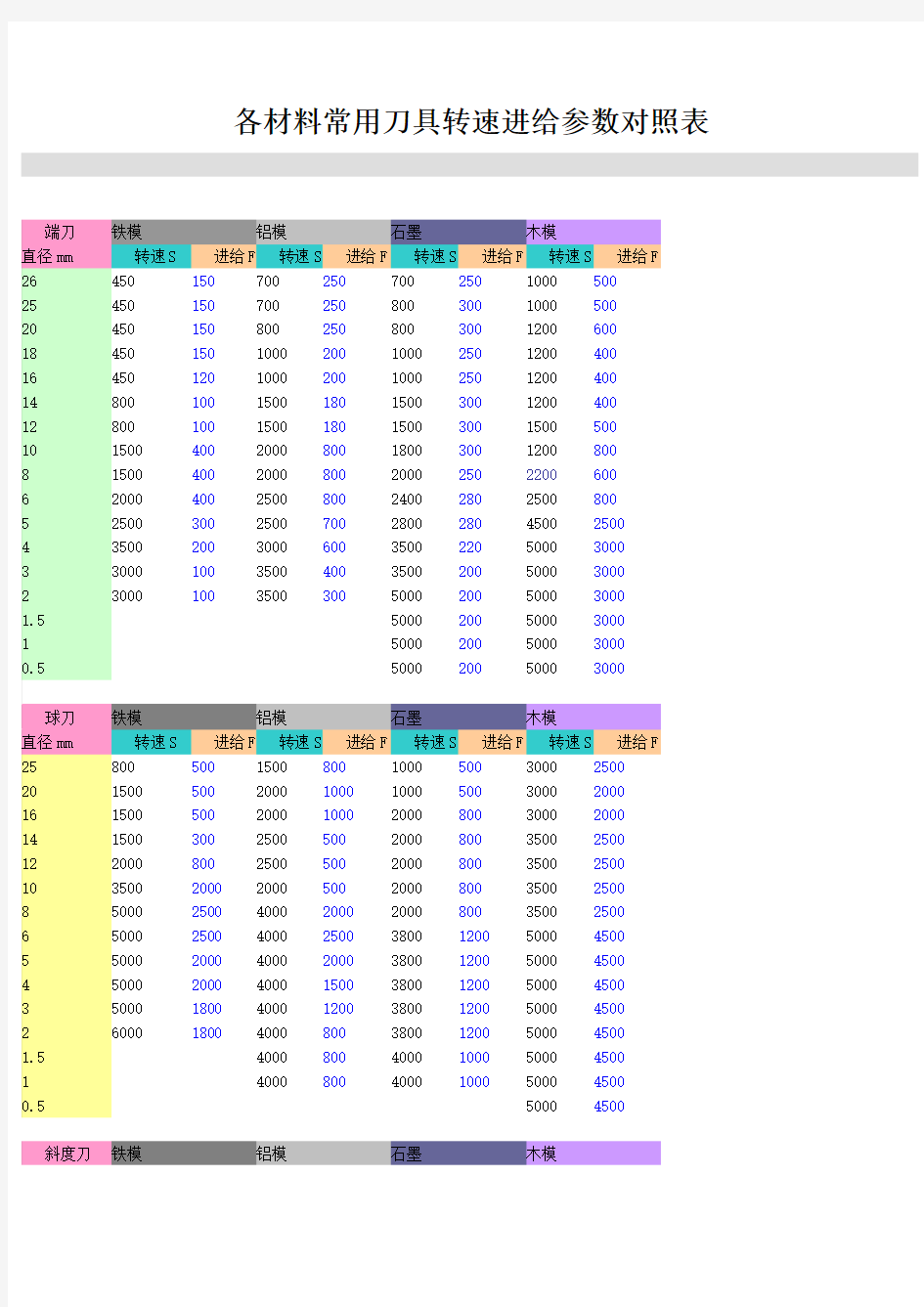

各材料常用刀具转速进给参数对照表
端刀铁模铝模石墨木模
直径mm转速S 进给F转速S进给F转速S进给F转速S进给F 264501507002507002501000500 254501507002508003001000500 204501508002508003001200600 18450150100020010002501200400 16450120100020010002501200400 14800100150018015003001200400 12800100150018015003001500500 101500400200080018003001200800 81500400200080020002502200600 62000400250080024002802500800 525003002500700280028045002500 435002003000600350022050003000 330001003500400350020050003000 230001003500300500020050003000
1.5500020050003000 1500020050003000
0.5500020050003000
球刀铁模铝模石墨木模
直径mm转速S进给F转速S进给F转速S进给F转速S进给F 258005001500800100050030002500 20150050020001000100050030002000 16150050020001000200080030002000 1415003002500500200080035002500 1220008002500500200080035002500 10350020002000500200080035002500 85000250040002000200080035002500 650002500400025003800120050004500 550002000400020003800120050004500 450002000400015003800120050004500 350001800400012003800120050004500 26000180040008003800120050004500
1.540008004000100050004500 140008004000100050004500
0.550004500
斜度刀铁模铝模石墨木模
类型转速S进给F转速S进给F转速S进给F转速S进给F TAP-10-30700300100050012001000 TAP-10-20700300100050012001000 TAP-10-10700300100050012001000 TAP-10-5700300100050012001000 TAP-6-10700300100050012001000 TAP-6-5700300100050012001000 TAP-6-2700300100050012001000 MAKING35007004500120050004500
圆鼻刀铁模铝模
类型转速S进给F转速S进给F
D25R62500150030002000
D25R52500150030002000
D20R42500150030002000
D16R42500150030002000
主轴转速切削速度进给量背吃刀量进给次数
切削速度 vc——是刀具切削刃上的某一点相对于待加工表面在主动动方向上的瞬时速度.(cutting speed) 进给量 f——刀具在进给运动方向上相对于工件的位移量(feed) 背吃刀量 ap——一般指工件上已加工表面和待加工表面间的重直距离。(切削深度)(back engagement) 背吃刀量一般指工件上已加工表面和待加工表面间的垂直距离。 进给量是刀具在进给运动方向上相对于工件的位移量。 切削速度是刀具切削刃上的某一点相对于待加工表面在主运动方向上的瞬时速度。 数控编程时,编程人员必须确定每道工序的切削用量,并以指令的形式写入程序中。切削用量包括切削速度、背吃刀量及进给速度等。对于不同的加工方法,需要选用不同的切削用量。 1、切削用量的选择原则 粗加工时,一般以提高生产率为主,但也应考虑经济性和加工成本;半精加工和精加工时,应在保证加工质量的前提下,兼顾切削效率、经济性和加工成本。具体数值应根据机床说明书、切削用量手册,并结合经验而定。 从刀具的耐用度出发,切削用量的选择顺序是:先确定背吃刀量,其次确定进给量,最后确定切削速度。 2、背吃刀量的确定 背吃刀量由机床、工件和刀具的刚度来决定,在刚度允许的条件下,应尽可能使背吃刀量等于工件的加工余量,这样可以减少走刀次数,提高生产效率。 确定背吃刀量的原则: (1)在工件表面粗糙度值要求为Ra12.5μm~25μm时,如果数控加工的加工余量小于5mm~6mm,粗加工一次进给就可以达到要求。但在余量较大,工艺系统刚性较差或机床动力不足时,可分多次进给完成。 (2)在工件表面粗糙度值要求为Ra3.2μm~12.5μm时,可分粗加工和半精加工两步进行。粗加工时的背吃刀量选取同前。粗加工后留0.5mm~1.0mm余量,在半精加工时切除。 (3)在工件表面粗糙度值要求为Ra0.8μm~3.2μm时,可分粗加工、半精加工、精加工三步进行。半精加工时的背吃刀量取1.5mm~2mm。精加工时背吃刀量取0.3mm~0.5mm。 3、进给量的确定 进给量主要根据零件的加工精度和表面粗糙度要求以及刀具、工件的材料选取。最大进给速度受机床刚度和进给系统的性能限制。 确定进给速度的原则: 1)当工件的质量要求能够得到保证时,为提高生产效率,可选择较高的进给速度。一般在100~200m/min范围内选取。 2)在切断、加工深孔或用高速钢刀具加工时,宜选择较低的进给速度,一般在20~50m/min范围内选取。 3)当加工精度,表面粗糙度要求高时,进给速度应选小些,一般在20~50m/min 范围内选取。 4)刀具空行程时,特别是远距离“回零”时,可以选择该机床数控系统设定的最高进给速度。 4、主轴转速的确定
主轴转速切削速度进给量背吃刀量进给次数
主轴转速切削速度进给 量背吃刀量进给次数 Pleasure Group Office【T985AB-B866SYT-B182C-BS682T-STT18】
切削速度 vc——是刀具切削刃上的某一点相对于待加工表面在主动动方向上的瞬时速度.(cutting speed) 进给量 f——刀具在进给运动方向上相对于工件的位移量(feed) 背吃刀量 ap——一般指工件上已加工表面和待加工表面间的重直距离。(切削深度)(back engagement) 背吃刀量一般指工件上已加工表面和待加工表面间的垂直距离。 进给量是刀具在进给运动方向上相对于工件的位移量。 切削速度是刀具切削刃上的某一点相对于待加工表面在主运动方向上的瞬时速度。 数控编程时,编程人员必须确定每道工序的切削用量,并以指令的形式写入程序中。切削用量包括切削速度、背吃刀量及进给速度等。对于不同的加工方法,需要选用不同的切削用量。 1、切削用量的选择原则 粗加工时,一般以提高生产率为主,但也应考虑经济性和加工成本;半精加工和精加工时,应在保证加工质量的前提下,兼顾切削效率、经济性和加工成本。具体数值应根据机床说明书、切削用量手册,并结合经验而定。 从刀具的耐用度出发,切削用量的选择顺序是:先确定背吃刀量,其次确定进给量,最后确定切削速度。 2、背吃刀量的确定 背吃刀量由机床、工件和刀具的刚度来决定,在刚度允许的条件下,应尽可能使背吃刀量等于工件的加工余量,这样可以减少走刀次数,提高生产效率。 确定背吃刀量的原则:
(1)在工件表面粗糙度值要求为μm~25μm时,如果数控加工的加工余量小于5mm~6mm,粗加工一次进给就可以达到要求。但在余量较大,工艺系统刚性较差或机床动力不足时,可分多次进给完成。 (2)在工件表面粗糙度值要求为μm~μm时,可分粗加工和半精加工两步进行。粗加工时的背吃刀量选取同前。粗加工后留~余量,在半精加工时切除。(3)在工件表面粗糙度值要求为μm~μm时,可分粗加工、半精加工、精加工三步进行。半精加工时的背吃刀量取~2mm。精加工时背吃刀量取~。 3、进给量的确定 进给量主要根据零件的加工精度和表面粗糙度要求以及刀具、工件的材料选取。最大进给速度受机床刚度和进给系统的性能限制。 确定进给速度的原则: 1)当工件的质量要求能够得到保证时,为提高生产效率,可选择较高的进给速度。一般在100~200m/min范围内选取。 2)在切断、加工深孔或用高速钢刀具加工时,宜选择较低的进给速度,一般在20~50m/min范围内选取。 3)当加工精度,表面粗糙度要求高时,进给速度应选小些,一般在20~ 50m/min范围内选取。 4)刀具空行程时,特别是远距离“回零”时,可以选择该机床数控系统设定的最高进给速度。 4、主轴转速的确定 主轴转速应根据允许的切削速度和工件(或刀具)直径来选择。其计算公式为:
数控加工中心刀具转速进给参考表
面铣刀下刀量S F備註?110.320002000P20*0.8?130.320002000P20*0.8?170.520002000~2400P20*0.8?210.520002000~2400P20*0.8?260.520002000~2400P20*0.8麻花鑽Q值S F備註?3以下11500~1800100一律使用G83?3~?5.51~21200~1500100一律使用G83?6~?8.521000~1200100一律使用G83?9~?10.52800~1000100一律使用G83?11~?132600~800100一律使用G83?14~?162500~600100一律使用G83?17~?192400~50080~100一律使用G83?20~?231~2300~40080以下一律使用G83?24~?271~2300以下80以下一律使用G83沉頭刀Q值S F備註?211~250050~100一律使用G73?261~250050~100一律使用G73?311~250050~100一律使用G73?361~250050~100一律使用G73?411~250050~100一律使用G73
?461~250050~100一律使用G73?481~250050~100一律使用G73?551~250050~100一律使用G73粗膛刀Q值S F備註?200800100使用G81?250800100使用G81?300800100使用G81?320800100使用G81?350800100使用G81?400600~80080~100使用G81?420600~80080~100使用G81?48060080~100使用G81?55060080~100使用G81精膛刀Q值S F備註?8~?120800100使用G81?12~?140800100使用G81?15~?180800100使用G81?18~?200800100使用G81?20~?250800100使用G81?25~?320800100使用G81?32~?420800100使用G81?42~?520600100使用G81
数控加工中心刀具转速进给参考表
CNC 轉速進給S50C參考飛刀下刀量S F 備註?11 0.320002000P20*0.8?130.320002000P20*0.8?170.520002000~2400P20*0.8?210.520002000~2400P20*0.8?260.520002000~2400P20*0.8圓刀下刀量S F 備註?350.5 1500 3000~3500 P20*0.8?500.5 1000 3000~3500 P20*0.8?630.5 1000 3000~3500 P20*0.8噴水鑽Q值S F 備註?28 2 600~800 70~100 一律使用G73 ?33 2 600~800 50~70 一律使用G73 ?381~2 600~800 50~70 一律使用G73 ?471~2 500~600 50以下一律使用G73 ?541~2 500~600 50以下一律使用G73
麻花鑽Q值S F 備註?3以下 1 1500~1800 100 一律使用G83 ?3~?5.5 1~2 1200~1500 100 一律使用G83 ?6~?8.5 2 1000~1200 100 一律使用G83 ?9~?10.5 2 800~1000 100 一律使用G83 ?11~?13 2 600~800 100 一律使用G83 ?14~?16 2 500~600 100 一律使用G83 ?17~?19 2 400~500 80~100 一律使用G83 ?20~?231~2300~400 80以下一律使用G83 ?24~?27 1~2300以下80以下一律使用G83 沉頭刀Q值S F 備註?21 1~2 500 50~100 一律使用G73 ?26 1~2 500 50~100 一律使用G73 ?31 1~2 500 50~100 一律使用G73 ?36 1~2 500 50~100 一律使用G73 ?41 1~2 500 50~100 一律使用G73 ?46 1~2 500 50~100 一律使用G73 ?48 1~2 500 50~100 一律使用G73 ?55 1~2 500 50~100 一律使用G73
cnc刀具试用报告表格
cnc刀具试用报告表格 篇一:CNC加工中心程序单 CNC加工中心程序单 篇二:1CNC刀具管理办法 福州有限公司 福州有限公司 篇三:雕刻刀具参数表 刀具工艺参数表 ——黄铜的加工参数 下图为计算刀具路径时的“设定切削用量”对话框,根据当前所用刀具正确查取刀具工艺表格,对应图中的“吃刀深度”即最大单边切深度、“开槽深度”即一次开槽深度、“路径间距”即侧向进给,分别输入加工参数值。 表一:20○系列刀具开粗加工黄铜材料的工艺参数表 表二:20○系列刀具修边加工黄铜材料的工艺参数表表三:20○系列刀具清角加工黄铜材料的工艺参数表表四:10○系列刀具开粗加工黄铜材料的工艺参数表 表五:10○系列刀具修边加工黄铜材料的工艺参数表 表六:10○系列刀具清角加工黄铜材料的工艺参数表 表七:30○系列刀具修边加工黄铜材料的工艺参数表 表八:30○系列刀具清角加工黄铜材料的工艺参数表 表九:使用螺纹铣刀开粗加工黄铜时的工艺参数表
使用螺纹铣刀开粗是充分利用螺纹铣刀的侧向切削能力强的优势,从实际加工的现象来看是:吃刀深度大,侧向进给量小,进给速度大,整体的材料去除量大,加工效率大幅度提高,这种加工方式称为:“大吃深,少吃料,快进给”。螺纹铣刀不但加工效率高,而且刀具比较耐用,加工的底面效果好,尺寸精度容易保证。 紫铜的加工参数 表一:20○系列刀具开粗加工紫铜材料的工艺参数表 表二:20○系列刀具修边加工紫铜材料的工艺参数表 表三:20○系列刀具清角加工紫铜材料的工艺参数表表四:30○系列刀具修边加工紫铜材料的工艺参数表表五:30○系列刀具清角加工紫铜材料的工艺参数表表六:使用螺纹铣刀进行紫铜开粗加工时的工艺参数铬钢的加工参数 表一:20○系列刀具开粗加工铬钢材料的工艺参数表 表二:20系列刀具修边加工铬钢材料的工艺参数表 表三:20○系列刀具清角加工铬钢材料的工艺参数表表四:30○系列刀具修边加工铬钢材料的工艺参数表 表五:30○系列刀具清角加工铬钢材料的工艺参数表表六:使用螺纹铣刀进行铬钢开粗加工时的工艺参数切削线速度 切削线速度计算公式: V=πDN
CNC各种材料选用刀具与转速参数表.doc
CNC各种材料选用刀具和转速参数表CNC钻头切削参数表CNC铰刀切削参数表 材料名 称刀具材 质 铣刀直径 主轴转速 (转/ 分) 进给率 最大切削 深度 加工材料钻头直径主轴转速进给率材料主轴转速进给率 2 5000-6000 80-120 0.3-0.5 1-2 5000-6000 120-150 200-300 61-92 低碳钢(软钢) 有机玻 璃白钢立 铣刀 3-4 4000-5000 100-150 0.5-1 2-3 4000-5000 120-150 中碳钢125-200 38-61 5-6 3000-4000 200-300 1-2 有机玻璃3-5 4000-5000 120-150 高碳钢50-125 15-38 8-10 3000-4000 250-350 2-4 5-8 2500-3500 100-120 工具钢50-125 15-38 12以上3000-4000 250-350 3-6 8以上2000-3000 80-100 自由马赫150-250 46-76 2 5500-6500 100-130 0.3-0.5 1-2 5000-6000 150-180 奥氏体150-250 46-76 POM 白钢立 铣刀 3-4 4500-5000 120-180 0.5-1 2-3 4000-5000 120-150 铁素体80-120 24-37 不锈钢 5-6 3000-4000 200-300 1-2 3-5 4000-5000 120-150 马氏体80-120 24-37 POM PH & HT 400 8-10 3000-4000 250-350 2-4 5-8 2500-3500 100-120 60-100 18-31 Series 12以上3000-4000 250-350 3-6 8以上2000-3000 80-100 软的150-250 46-76 2 4500-5000 50-80 0.3-0.5 1-2 4000-5000 100-120 中等75-150 23-46 铝白钢立 铣刀 3-4 4500-5000 80-100 0.5-1 2-3 4000-5000 100-120 50-75 15-23 硬的 铸铁 5-6 3000-4000 100-150 1 3-5 3000-4000 80-100 125-200 38-61 铝可锻的 8-10 3000-4000 150-200 1-2 5-8 2000-3000 50-80 125-200 38-61 柔软的 12以上3000-4000 200-300 2-3 8以上1500-2000 30-50 纯钛50-100 15-31 钛 2 3000-4000 20-50 0.1-0. 3 1-2 2500-3000 80-100 35- 50 11-15 钛合金 A3或45#钢钨钢立 铣刀 3-4 2000-2500 50-80 0.3-0.5 2-3 2000-2500 80-100 含镍40- 70 12-21 A3或45# 高温合金 5-6 1200-2000 80-100 0.5-0.8 3-5 1500-2000 50-80 含钴30-45 9-14 钢 8-10 600-800 100-120 0.5-1 5-8 1000-1500 30-50 45#钢100-150 31-46 2 3000-4000 20-50 0.3-0.5 1-2 3000-4000 100-120 >10% Si 12以上500-600 120-150 1-2 8以上600-1000 20-30 <10% Si 铝500-1000 153-305