齿轮知识1
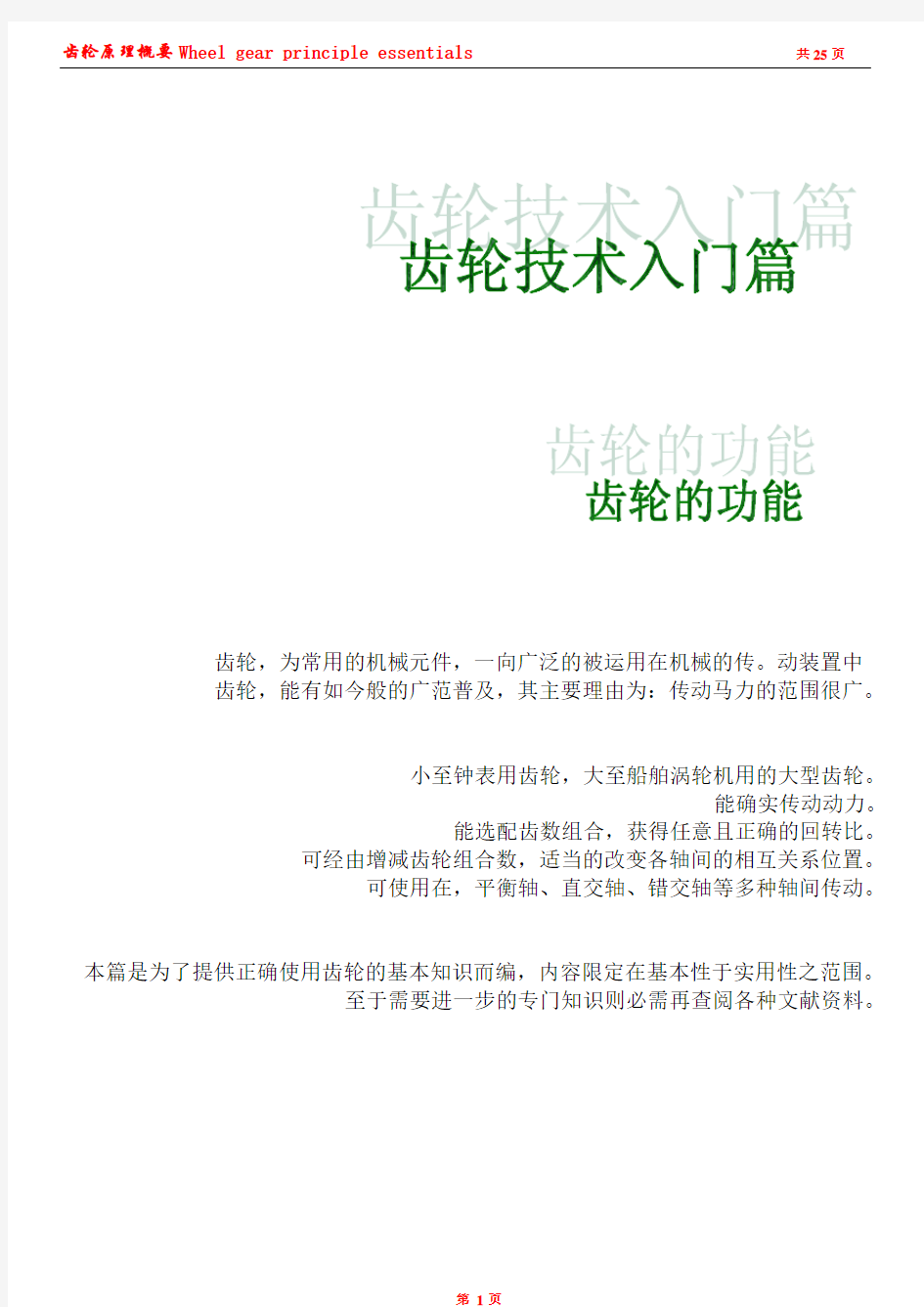

齿轮,为常用的机械元件,一向广泛的被运用在机械的传。动装置中
齿轮,能有如今般的广范普及,其主要理由为:传动马力的范围很广。
小至钟表用齿轮,大至船舶涡轮机用的大型齿轮。
能确实传动动力。
能选配齿数组合,获得任意且正确的回转比。
可经由增减齿轮组合数,适当的改变各轴间的相互关系位置。
可使用在,平衡轴、直交轴、错交轴等多种轴间传动。
本篇是为了提供正确使用齿轮的基本知识而编,内容限定在基本性于实用性之范围。
至于需要进一步的专门知识则必需再查阅各种文献资料。
第一章齿轮一般知识.
一、齿轮的种类:
1.平行轴之齿轮(圆柱齿轮)
(1)正齿轮(直齿轮)(Spur gear ):齿筋平行于轴心之直线圆筒齿轮。
(2)齿条( Rack ):与正齿轮咬合之直线条状齿轮,可以说是齿轮之节距在大小变成无限大时之特殊情形。
(3)内齿轮(Internal gear):与正齿轮咬合之直线圆筒内侧齿轮。
(4)螺旋齿轮(Helical gear):齿筋成螺旋线(helicoid)之圆筒齿轮。
(5)斜齿齿条(Helical rack):与螺旋齿轮咬合之直线状齿轮。
(6)双螺旋齿轮(Double helical gear):左右旋齿筋所形成之螺旋齿轮。
2.直交轴之齿轮(圆锥齿轮)
(1)直齿伞形齿轮(Straight bevel gear):齿筋与节圆锥之母线(直线)一致之伞形齿轮。
(2)弯齿伞形齿轮(Spiral bevel gear):齿筋为具有螺旋角之弯曲线的伞形齿轮。
(3)零螺旋弯齿伞形齿轮(Zerol bevel gear):螺旋角为零之弯齿伞形齿轮。
3.错交轴之齿轮(蜗轮和蜗杆)
(1)圆筒蜗轮齿轮(Worm gear):圆筒蜗轮齿轮为蜗杆(Worm)及齿轮(Wheel)之总称。
(2)错交螺旋齿轮(screw gear):此为圆筒形螺旋齿轮,利用要错交轴(又称歪斜轴)间传动时称之。
(3)其它之特殊齿轮:
面齿轮(Face gear):为能与正齿轮或与螺旋齿轮咬合之圆盘形的面齿轮。
鼓形蜗轮齿轮(Concave worm gear):凹鼓形蜗杆及与此咬合之齿轮的总称。
戟齿轮(Hypoid gear):传达错交轴之圆锥状齿轮。形状类似弯齿伞形齿轮。
二、齿轮切削方法:
1.成形切削法:利用具有齿沟轮廓之刀具一齿接一齿切削之方法(一齿完成后将材料
转动(移动)1个节距再切削下1个齿沟之方法)。
利:只要有万能铣床、分度盘及刀具、在任何工场皆可进行。
弊:即使是同系统之齿轮(齿形节距、压力角、齿长)随着齿数、齿沟轮廓形状不同就必须准备相当数量之刀具。
2.创成切削法(展成法):依据刀具和齿轮工件相互运动,切出齿轮之方法(1把刀
具可以切出同系统同节距、不同齿数之齿轮)。
(1)依滚齿刀(HOB)之创成法(本厂用之方法)
(2)齿条形刀具之创成法(Rack)
(3)圆筒形拉刀之创成法(Pinion Cuffer)
三、齿轮专用特殊用语:
1、齿形修整(Tip relief of gear)
(1)齿冠部分修整(普遍):就是以特殊之加工方法将齿冠部分切成比正确的渐开线略显凸形,因而当齿面受传动力变形时,会缓和对相互咬合之齿轮所可能产
生之干扰,并可降低咬合时之噪音及增长寿命,效果显著。但若修整过量则正如
加大齿形误差之齿轮,对齿轮咬合有不良影响。
(2)齿根部分修整
2、削鼓形齿筋及削端齿筋(Cowning、Relieving)
削鼓形加工及削端加工,都是齿筋方向修整法。尤其削鼓加工为使齿面之接触集中在齿幅中央部位,而使齿筋修整成微微带有鼓形之状态,但若鼓形过甚,等于减低齿形之接触面积,对齿形之强度有不良影响。至于削端加工则是将齿筋两端微微倒角,如此可具近似鼓形齿筋之效果。
3、外径滚削及外端倒角(Topping and Semitopping)
以滚齿刀(Gear Hob)创生加工齿形之同时,顺便将齿轮之外径滚削或将齿顶部倒角切削,以齿条形刀具(Back form cutter)创生齿形同时切削齿轮外径之情形。这种齿轮因外径与齿形同步被切削,故其外径之偏差最低同时亦可削除齿形所产生之毛边。
外端倒角用之刀具形状及被创生切削之齿形,这种齿形可以防止齿尖部常发生打痕以及毛边之产生。
若外端倒角量过大,则齿形之有效齿冠高度显著减少,同时咬合率也会降低,故通常不希望过量之外端倒角。
四、渐开线齿面的加工
滚齿
属于展成法加工。
1、加工原理:用齿轮滚刀滚切圆柱齿轮实质上是按一对螺旋齿轮啮合的原理来加
工工件的。
有三种运动:
①主运动:即滚刀的旋转运动n0。
②分齿运动:保证滚刀转速和被切齿轮转速之间啮合关系的运动。
③垂直进给运动:滚刀沿被切齿轮的轴轴线方向作垂直进给运动。
注:滚齿时,必须将滚刀搬动一个角度,使刀齿运动方向与被切齿轮的轮齿方向一致。
2、特点:
①与铣齿相比,齿形精度高,精滚加工可加工出6级精度的齿轮。
②可以用同一模数的滚刀,加工相同模数的各种不同齿数的圆柱齿轮。
③连续切削,加工过程平稳,生产率高。
④使用范围广。但不能加工内齿轮、人字齿轮和相距太近的多联齿轮。
六、滚齿机之种类:
1.立式:被装设之工件为垂直方向;
2.横式(卧式):被装设之工件为水平方向(本厂之机型)。
七、齿轮各部份名称:
1.渐开线:如图所示,在圆盘的圆周上围绕一根棉线,并在线头 a 上栓一支铅笔,
然后拉紧线头 a ,逐渐展开铅笔尖在纸上
画出的曲线就叫做渐开线。齿轮的齿形就
是这条渐开线上的一段,而那个圆盘叫做
基圆(基圆以内无渐开线)。棉线在展开过
程中,总是和基圆相切的,任意选择一个
位置bo这时棉线和基圆相切在c点,所以
bc垂直于基圆,半径oc,bc亦称作渐开线
的发生线。
从渐开线的形成过程可知:
1)发生线的长度等于基圆的展开弧长
ac;
2)发生线bc是渐开线上b点的法线;
3)渐开线的形状取决于基圆的大小,基圆越大,渐开线就越平直;基圆越小渐开线就越弯曲,并且同一基圆的渐开线完全一样。
渐开线的优点:中心距离略有变动也不影响咬
合运转之平滑性与正确性。
2.分度圆:在一个标准齿轮中槽宽和齿厚相等的那个圆。(dg=mz)
3.齿顶圆:通过齿轮顶部的圆。(da=m(z+2))
4.齿根圆:通过齿轮根部的圆。(df=m(z-2.5))
5.齿距:相邻两个齿的对应点在分度圆周上的弧长(p=πm)
6.齿宽:齿轮轮齿部份的轴向长度;(b)
7.齿厚:一个轮齿在分度圆上所占的弧长。(=1.5708m)
8.槽宽:一个齿槽在分度圆周上所占的弧长。(e=1.5708m)
9.齿顶高:从齿顶圆到分度圆的径向距离。(hk=m)
10.齿根高:从齿根圆到分度圆的径向距离。(hf=1.25m)
11.全齿高:齿的全深,为齿顶高与齿根高之和;(h=2.25m)
12.顶隙:当两个齿轮完全啮合的时候,一个齿轮的齿顶与另一个齿轮的齿根间的间
隙。(ck=0.25m)
13.中心距:互相啮合的两个齿轮轴线之间的距离。(a=m(z1+z2)/2)
14.压力角:渐开线齿形上任意一点的受力方向线(如图)与运动方向线之间的夹角。
根据几何关系,图中∠boc 就是 b 点的压力角,从图中可以看出,在同一条渐开线上各点的压力角都不相同,齿顶的压力角大,齿根处小。压力角已标准化。一般为20o,这个角度也称齿形角 a 。
15.导程:(LEAD)螺旋线回转一圈,所移动的距离。(l=mzπ/sinβ)
16.齿直角压力角:螺旋齿轮的齿直角平面内的压力角。(an)
17.轴平面压力角:螺旋齿轮的横向轴断面内所形成的压力角。(ax)
八、齿数比与数比:
1.在一对齿轮中,齿数少的齿轮叫小齿轮,齿数多的齿轮叫大齿轮,齿数同等的情
况下,驱动齿轮叫小齿轮,被驱动齿轮叫大齿轮;
2.在一对外齿轮中,其运转为你逆向运转,小齿轮向右转动,大齿轮向左转动;
3.在一对内齿轮中,两齿轮运转方向一致;
4.在一对齿轮中,运转数、齿数成反比例,小齿轮比大齿轮的转数多,其齿数比,
速度比如下:
大齿轮齿数被驱动齿轮齿数
齿数比ⅰ=或
小齿轮齿数驱动齿轮齿数
大齿轮齿数被驱动齿轮齿数
速比u=或
小齿轮齿数驱动齿轮齿数
蜗母齿轮:
蜗轮齿数
齿数比ⅰ=
蜗杆条数
蜗杆条数
速比u=
蜗轮齿数
5.速比设计范围:
直齿轮、螺旋齿轮:1/1-1/12
伞齿轮:1/1-1/10
蜗母:1/3.5-1/100
第二章关于滚齿刀(HOB)
一、滚齿刀切齿:
1.切削条件:
针对切削速度、进给量(走刀速度)及滚刀摩耗量之关系,一般有:(1)为了减少滚刀之摩耗量,切削速度变慢会比较好。但是切削进给量太小反而不好;
(2)为了增加滚刀耐久性,与其采用高切削速度,不如采用高切削进给量,不过齿面会不好;
(3)切削速度加快(回转数变大),进给量降低,齿面会变好;
(4)滚齿机自身之刚性,对滚刀寿命有非常大影响。
(5)滚刀材质分:(1)工具钢(镀钛);(高速钢、氦石)
(2)超硬(钨钢);
(6)依滚刀之螺旋方向(本厂为右旋)被切削齿轮之螺旋方向确认是否加装惰轮。
二、滚刀及其应用:
滚刀的精度等级可分为AAA、A、B、C级,相应加工6级以上、7、8、9、10级齿轮。
三、滚齿刀(HOB)之切齿:
1.滚刀是在螺牙上加上几个纵沟,螺牙导程上有许多切刃之切齿用刀具;
(1)一体型滚齿刀(本厂用之滚齿刀)
(2)组合型滚齿刀
2.滚刀和工件之关系:(滚齿过程、成形方法)。
滚刀装设时,刀刃导程会对准齿轮之齿筋方向,此时滚刀之刀刃导程相当于假想之齿条,在渐开线齿轮场合,齿条刀刃形状是直线,滚刀只要有回转,
接二连三的刀刃往工件里切入,切出齿。因为刀刃是沿着螺纹分布,随着回转
而切入之刀刃往左边移动,工件也配合此动作往左边移动。只要回转齿轮工件
就会从齿顶部逐渐往齿部切出齿形。1条(单口,本厂均是)滚刀之场合,滚刀
1回转,相当于假想齿条前进一个节距。齿轮工件也只需运转1个节距即可。即
要切削Z齿数齿轮时,相对于齿轮工件之1回转、滚刀必须有Z回转才可。
四、滚刀精度误差对其生产中之影响:
1.因滚刀再研磨引起之齿形误差
(1)滚刀分割误差:有分割误差发生时会反应在齿形误差上,影响非常大,压力角20o之滚刀在外周有0.1mm之分割误差时,会造成6um之齿形误差。
(2)倾斜角误差:滚刀倾斜角误差会变成齿轮之压力角误差,滚刀之倾斜角误差1o时,压力角误差约为3′,并非大影响。
(3)切刃面之误差:滚刀之切刃面并非直线,而是凹凸时,会造成齿形误差。
(4)刃沟之螺旋误差:通常滚刀轴心和切刃沟是平行的,如果有此误差,会产生左右齿面非对称之压力角误差,1o约为10′之误差。
2.因滚刀之偏摆而造成之齿形误差。
(5)滚刀如果有偏摆,齿轮会产生很大弯曲误差,偏摆量0.03mm、压力角20o时的齿形误差约10um (该误差非常大)。
(6)滚刀偏心有下列现象:
a)切刃及孔之偏心(滚刀制作时产生)
b)滚刀装设时之偏心。
滚刀内孔和滚刀轴有间隙;
滚刀之螺帽上紧时之偏心:螺帽、垫片、滚刀端面的平行度不良;切削时铁渣附着等造成滚刀轴弯曲,或不当上太紧造成滚刀轴弯曲;
(2)滚刀轴本身之偏心。
3.因滚刀之切刃沟引起多角形误差:
(7)多角形误差,可因切刃沟数多而变小;
(8)滚刀之条数愈多,误差愈大;
(9)齿数无法被滚刀条数整除时,误差变小;
(10)齿数可以被滚刀条数整除时,误差变大。
4.其它齿形误差原因:
(1)滚刀压力角误差,直接成为齿轮压力角误差;
(2)滚刀节距同样伸缩状态时会产生压力角误差;
(3)滚刀齿筋误差,会造成齿轮齿形误差。
以上均存在于滚刀制作精度。
(4)如果使用滚刀两端,就可能发生创成不完全而产生齿形误差;
(5)齿面出棱—修刀不等分;
(6)齿形不对称—滚刀安装不对中;
(7)齿形角误差—修刀不通过;
(8)齿形周期误差—安装刀具后径向、轴向跳动大;
(9)节距误差、累积节距误差—滚刀主轴轴向窜动大,滚刀径向跳动大(刀具精度不够);
(10)滚刀重新研磨后,请用黄铜刷子将切刃之棱线除去。
五、滚刀的选用:
可根据加工零件的精度要求来选用滚刀,通常加工5级精度(GB)的齿轮应采用“AAA”级的滚刀,加工6-7级精度的齿轮采用“AA”级的滚刀,加工8-9级精度的齿轮可采用“A”级或普通级的滚刀。
六、滚刀安装:
滚刀安装应根据压力角、模数、精度以及刀杆直径选择相应的滚刀,滚刀在刀杆安装夹紧后,应使用百分表,检查滚刀上两个凸台的径向跳动(有些滚刀只有一个凸台),两凸台的跳动方向和数值应尽可能一致,以避免滚滚刀安装的偏斜。根据加工零件的不同精度等级,滚刀安装允许的径向跳动值为:(依GB精度)
1.滚切5级精度齿轮,A、B处允许的径向跳动值为0.005-0.007mm;
2.滚切6级精度齿轮,A、B处允许的径向跳动值为0.007-0.009mm;
3.滚切7级精度齿轮,A、B处允许的径向跳动值为0.01mm。
当滚刀径向跳动超过允许值不大时,可以松开滚刀紧固螺冒,转动滚刀或垫圈,再重新夹紧进行检查。反复多次直至到达滚刀的安装精度要求。
六、刀具使用上研磨后误差(精度):
公法线齿厚容许差及齿顶圆直径容许差的关系
δda=δW / sin a δW=δda * sin a
δW:公法线齿厚容许差δda:齿顶圆直径容许差
mm)
。
第三章齿轮精度
一、提高轴齿轮滚齿加工技术精方法:
轴齿轮是变速箱中最主要的零件,其加工精度的高低直接影响变速箱的整体质量。目前我们采用的轮齿齿部加工方法是滚齿一剃齿法。要通过滚、剃齿工艺制造出高精度齿轮,就必须把滚、剃工艺水平发挥到最好。而剃齿精度在很大程度上依鞍滚齿精度,所以滚齿中的一些误差项目必须严格控制,才能制造出高质量齿轮。滚齿是一种常用的齿轮加工方法,在精度很高的滚齿机上,采用精密滚刀,可以加工出4—5级精度的轮齿。在普通级滚齿机上,用普通精度滚刀,只能加工出8级精度轮齿。变速箱轴齿轮齿部要求的精度为8—7—7级,而且滚齿加工时主要是以两中心孔和端面做定位基准,因此分析滚齿的误差来源,掌握保证和提高加工精度的方法非常重要。
1滚齿加工精度分析
轴齿精度主要和运动精度、平稳性精度、接触精度有关。滚齿加工中用控制公法线长度和齿圈径跳来
保证运动精度,用控制齿形误差和基节偏差来保证工作平稳性精度,用控制齿向误差来保证接触精度。下面对滚齿加工中易出现的几种误差原因进行分析:
1.1齿圈径向跳动误差(即几何偏心)
齿圈径向跳动是指在齿轮一转范围内,测头在齿槽内或轮齿上,与齿高中部双面接触,测头相对于轮齿轴线的最大变动量。也是轮齿齿圈相对于轴中心线的偏心,这种偏心是由于在安装零件时,零件的两中心孔与工作台的回转中心安装不重合或偏差太大而引起。或因顶尖和顶尖孔制造不良,使定位面接触不好造成偏心,所以齿圈径跳主要应从以上原因分析解决。
1.2公法线长度误差(即运动偏心)
滚齿是用展成法原理加工齿轮的,从刀具到齿坯间的分齿传动链要按一定的传动比关系保持运动的精确性。但是这些传动链是由一系列传动元件组成的。
它们的制造和装配误差在传递运动过程中必然要集中反映到传动链的末端零件上,产生相对运动的不均匀性,影响轮齿的加工精度。公法线长度变动是反映齿轮牙齿分布不均匀的最大误差,这个误差主要是滚齿机工作台蜗轮副回转精度不均匀造成的,还有滚齿机工作台圆形导轨磨损、分度蜗轮与工作台圆形导轨不同轴造成,再者分齿挂轮齿面有严重磕碰或挂轮时咬合太松或太紧也会影响公法线变动超差。
1.3齿形误差分析
齿形误差是指在齿形工作部分内,包容实际齿形廓线的两理想齿形(渐开线)廓线间的法向距离。在实际加工过程中不可能获得完全正确的渐开线齿形,总是存在各种误差,从而影响传动的平稳性。齿轮的基圆是决定渐开线齿形的惟一参数,如果在滚齿加工时基圆产生误差,齿形势必也会有误差。基圆半径R=
滚刀移动速度/工作台回转角速度xcosao(ao为滚刀原始齿形角),在滚齿加工过程中渐开线齿形主要靠滚刀与齿坯之间保持一定速比的分齿来保证,由此可见,齿形误差主要是滚刀齿形误差决定的,滚刀刃磨质量不好很容易出现齿形误差。同时滚刀在安装中产生的径向跳动、轴向窜动(即安装误差)也对齿形误差有影响。常见的齿形误差有不对称、齿形角误差(齿顶变肥或变厚)、产生周期误差等。
1.4齿向误差分析
齿向误差是在分度圆柱面上,全齿宽范围内,包容实际齿向线的两条设计齿向线的端面距离。引起齿向误差的主要原因是机床、刀架的垂直进给方向与零件轴线有偏移,或上尾座顶尖中心与工作台回转中心不一致,还有滚切斜齿轮时,差动挂轮计算误差大,差动传动链齿轮制造和调整误差太大。另外夹具和齿坯制造、安装、调整精度低也会引起齿向误差。
1.5齿面粗糙度分析
齿面粗糙度不好一般有几种现象:发纹、啃齿、鱼磷、撕裂。
引起齿面粗糙度差的主要原因有以下几方面:机床、刀具、工件系统整体刚性不足、间隙大;滚刀和工件相对位置发生变化;滚刀刃磨不当、零件材质不均匀;切削参数选择不合适等。
二、齿轮误差:
1.齿形误差:(f p)
通过实际之齿形和节距圆之交点之正确渐开线为基准,在其垂直方向所测得之齿形检查范围内之正侧误差及负侧误差之和(针对轴直角齿形而言)(包含压力角误差和凹凸误差)
2.齿筋方向误差:(f q)
实际齿轮之齿筋曲线与理论曲线间之差异。此方向误差影响齿面之接触情况,而此误差可能引发齿轮两端部集中接触现象,因而产生局部接触不良后果。为避免这种不良的接触,通常将齿面加以鼓形加工或削端加工(Crowning or relieving )。
3.单一节距误差( f t)
齿轮任意相鄰同侧齿面在节圆上之实测节距与节距理论值间之差异。
4.鄰接节距误差(f tu)
一个齿轮,在节圆上相互相鄰之两个实测节距间之差异。
5.累积节距误差(F t)
一个齿轮上任意两个隔离齿在节圆上实测节距之和与正确值间之误差。
6.法线节距误差(f te)
齿轮正面法线节距之实测值与理论值间之误差。
7.齿沟偏差(节圆跳动 PITCH LINE RUNOUT )(f r)
使用能与齿面节点附近接触之测球或测柱,逐一地放在各个齿沟中,如此一整周,所测得半径方向之最大偏心量。
注:此项对齿轮噪音会产生不良影响,又大大受制于齿轮加工,以及研磨时工作物轴心之精度,因此为了提高偏心精度,除了要使用精良之加工母机外,特别要使用高精度之工作轴心。(中心孔)
三、齿轮误差分析:
1.齿轮制造误差分析:
(1)理论误差
(2)机床误差
(3)刀具误差
(4)夹具误差
(5)量具误差
(6)变形误差
(7)操作误差
2.齿轮齿形加工误差分析:
(1)齿轮的运动误差(机床、工件、主轴或刀具回转偏心);
(2)齿轮的平稳性误差;
(3)齿轮的接触误差;
(4)侧隙引起的误差;
3.滚齿常出现的误差及原因:
(1)齿形误差:
①齿面出棱(修刀不等分)
②齿形不对称(滚刀安装不对中)
③齿形角误差(修刀不通过)
④齿形节距误差(安装刀具后径向、轴向跳动大)
(2)齿面光洁度不好
①撕裂(工件材质不均匀)
②啃齿(刀架松动,齿轮传动间隙大)
③振纹(传动间隙大,工件、刀具、装夹刚性不够,切削用量不当)
④鱼鳞(热处理方法不当、(不均匀))
(3)节距误差超差及累积节距超差
①滚刀主轴的轴向窜动大,滚刀径向跳动大(刀具精度不够,挂轮有碰伤、磕碰)
②工件安装不正(工作台旋转轴心偏心以及机床分度传动链精度不够)
(4)齿圈径向跳动过大(节圆跳动)及齿筋超差
工件安装偏心,齿坯定位基准超差,检验基准与制造基准不重合。
四、齿轮之噪音对策:
齿轮噪音形成的原因有许多,尤其高负荷转速之动转中,噪音与振动始终是急需去克服的问题。其将减低噪音之要点及对策整理如下:
(1)选用良好精度之齿轮;
①将节距误差、齿形误差、齿沟误差、齿筋误差改小,则噪音自然会变小;
②研磨齿面,除了改善齿轮之各个精度外,还可改良齿面粗度,故对减低噪音有
很好的效果。
(2)采用光滑之齿面;
研磨、擦磨、砥磨均可达到很理想齿面粗度,另在油中热身运转一段时间也可以改善齿面粗度,这对噪音均有隆低作用。
(3)正确的齿面接触;
①实施齿面彭形加工(crowning)或削端加工(Relieving)防止单片接触,噪音自
然会降低;
②适当的齿形修整对降低噪音也有效;
③消除齿面上的碰伤或打痕。
(4)适当之齿隙;
①若为脉动性之传动,则较小之齿隙对噪音之降低有帮助;
②一般较均衡性之负荷,齿隙略大对噪音之降低有利。
(5)较大的咬合率;
①咬合率越大噪音越小,因此减小压力角或加高齿深均可以增加咬合率;
②重叠率加大也可以降低噪音,因此螺旋齿轮比正齿轮噪音小。
(6)较小的齿轮:采用较小之模数及较小的外径;
(7)较高之刚性;
①加宽齿幅,高刚性之形状对噪音之降低有利;
②加强齿轮箱及轴类之刚性。
(8)采用振动减衰率高之材质;
①若为轻负荷回转之齿轮采用塑胶齿轮是很好的选择,但要注意温度上升问题;
②铸铁齿轮比钢齿轮对降低噪音有效。
(9)适当之润滑;
①实施充份之润滑;
②粘度高的润滑油噪音较低。
(10)低速运转及低负荷。
齿轮之转数尽量压低,负荷尽量减轻可减小噪音。
五、滚齿误差产生原因消除方法:
齿圈径向圆跳动超差
1)齿坯几何偏心和安装偏心
2)用顶尖装夹定位时,顶尖与机床中心偏心
1)提高齿坯基准面精度;提高夹具定位面精度;提高调整水平
2)更换或重新装调顶尖
公法线长度变动超差
1)机床分度蜗杆副制造及安装误差造成运功偏心
2)机床工作台定心锥形导轨副间隙过大造成工作台运动中心线不稳定
3)滚刀主轴系统轴向圆跳动过大或平面轴承咬坏
1)提高分度蜗杆副的制造精度和安装精度
2)提高工作台锥形导轨副的配合精度
3)提高滚刀主轴系统轴向精度,更换咬坏的平面轴
齿距偏差超差
1)滚刀的轴向和径向圆跳动过大
2)分度蜗杆和分度蜗轮齿距误差
3)齿坯安装偏心
1)提高滚刀的安装精度
2)修复或更换分度蜗杆副
3)消除齿坯安装误差
基节超差
1)滚刀的轴向齿距误差,齿行误差及前刃面非径向性和非轴向性误差2)分度蜗杆副的齿距误差
3)齿坯的安装几何偏心
4)刀架回转角度不正确
1)提高滚刀铲磨精度和刃磨精度
2)修复或更换分度蜗杆副
3)消除几问偏心
4)调整角度
齿顶部变肥,左右齿廓对称
滚刀铲磨时齿形角度小或刃磨产生较大的正前角,使齿形角变小
更换滚刀或重磨齿形角及前刃面
齿顶部变瘦,左右齿廓对称
滚刀铲磨时齿形角变大或刃磨时产生较大的负前角,使形角变大
更换滚刀或重磨齿形角及前刀面
齿形不对称
滚刀安装对中不好,刀架回转角误差大,滚刀前刀面有导程误差
保证滚刀安装精度,提高滚刀刃磨精度,控制前刀面导程误差,微调滚刀回转角
齿面出棱
滚刀制造或刃磨时容屑槽等分误差
重磨滚刀达到等分要求
齿性周期性误差
滚刀安装后,径向或端圆跳动大,机床工作台回转
不均匀,分齿交换齿轮安装偏心或齿面有磕碰,刀架滑板松动,齿坯装夹不合理,产生振动
控制滚刀的安装精度,检查,调整分度蜗杆副传动精度,重新调整分齿交换齿轮、滑板和齿坯
齿向误差超差
1)垂直进给导轨与工作台轴线平行度误差或歪斜上、下顶针不同轴,卜下顶针轴线与工作台回转轴线同轴度差
2)夹具和齿坯的制造、安装、调整精度低
3)分齿、差动交换齿轮误差大
4)齿坯或夹具刚性差,夹紧后变形
1)根据误差原因,加以消除
2)提高夹具、齿坯的制造和调整精度
3)重新计算分齿及差动交换齿轮,修正误差
4)改进齿还或夹具设计,正确夹紧
撕裂
1)齿坯材质不均匀
2)齿坯热处理方法不当
3)滚刀用钝,不锋利
4)切削用量选择不当,冷却不良
1)控制齿坯材料质量
2)建议采用正火处理:45钢、40cr钢、18CrMnTi
3)滚刀移位或更换新刀
4)正确选用切削用量,选用润滑性能良好的切削液,充分冷却
啃齿
1)刀架立柱导轨太松或太紧
2)油压不稳定
3)刀架斜齿轮啮合间隙大
1)调整立柱导轨塞铁松紧
2)保持油路畅通,油压稳定
3)刀架斜齿轮若磨损,应更换之
振纹
1)机床内部某传动环节的间隙过大
2)工件与刀具的装夹刚性不够
3)切削用量选用过大
4)后托架安装后,间隙大
1)修理或调整机床
2)提高波刀装夹刚性,缩小支承间距离,加大轴径;提高工件刚性,尽量加大支承面
3)正确选用切削用量
4)正确安装后托架
鱼鳞
1)工件材料硬度过高
2)滚刀磨钝
3)冷却润滑不良
找出原因,分别消除
第四章 各计算公式
一、 齿轮各部分名称:(标准正齿轮如图)
°m
m m m m πm t e cos α0mz d o cos α0
二、 切削实际所需时间:
)(F
NC )
(60秒??++?Z ?=
T n C B A
) )((直齿—w dc w A -?=
))cos (
2(螺旋齿—hk w
dk dc w A -Φ
-+=
C = 0 — (直齿)
(螺旋齿)— 0.1tan tan cos 0+Φ
+?=
α
βhk C
三、 滚齿时滚出长度的计算:
滚齿时滚刀的中心需要超出齿轮下端面多少才能滚出全部齿形?
找到以下近似公式。
齿轮基础知识
齿轮综合知识 直齿圆柱齿轮各部分的名称和尺寸代号 1、齿顶圆--齿轮齿顶所在的圆。其直径(或半径)用da(或ra )表示。 2、齿根圆--齿轮齿槽底所在的圆。其直径(或半径)用df(或rf)表示。 3、分度圆--用来分度(分齿)的圆,该圆位于齿厚和槽宽相等的地方。其直径(或半径)用d(或r表示)。 4、齿顶高--齿顶圆与分度圆之间的径向距离,用ha表示。 5、齿根高--齿根圆与分度圆之间的径向距离,用hf表示。 6、全齿高--齿顶圆与齿根圆之间的径向距离,用h表示。显然有: h = ha + hf 7、齿厚--一个齿的两侧齿廓之间的分度圆弧长,用s表示。 8、槽宽--一个齿槽的两侧齿廓之间的分度圆弧长,用e表示。 9、齿距--相邻两齿的同侧齿廓之间的分度圆弧长,用p表示。显然有: p = s + e 10、齿宽--齿轮轮齿的宽度(沿齿轮轴线方向度量),用b表示。 直齿圆柱齿轮的基本参数和尺寸关系 齿数z 一个齿轮的轮齿总数。 模数m 以z表示齿轮的齿数,那么齿轮的分度圆周长=πd = z p。因此分度圆直径为:d=(p/p)?z, 式中:p/p称为齿轮的模数,用m表示,即 要使两个齿轮能啮合,它们的齿距必须相等。因此互相啮合的两齿轮的模数m必须相等。从d = mz中可见,模数m越大,轮齿就越大;模数m越小,轮齿就越小。 模数m是设计、制造齿轮时的重要参数。不同模数的齿轮,要用不同模数的刀具来加工制造。为了便于设计和减少加工齿轮的刀具数量,GBI357一78对齿轮的模数m已系列化,如下表所示。 在选用模数时,应优先采用第一系列的模数,其次是第二系列,括号内的尽可能不用。 压力角a (啮合角、齿形角)在节点P处,两齿廓曲线的公法线与两节圆的公切线所夹的锐角称啮合角,也称压力角。我国采用的压力角a一般为20°,加工齿轮的原始基本齿条的法向压力角称齿形角。因此,压力角a=啮合角=齿形角。 当标准直齿圆柱齿轮的模数m确定后,按照与m的比例关系可算出轮齿的各基本尺寸。 1 齿轮传动机构的特点及分类 齿轮传动机构的特点: a. 齿轮机构是现代机械中应用最广泛的传动机构,用于传递空间任意两轴或多轴之间的运动和动力。 b. 齿轮传动主要优点:传动效率高,结构紧凑,工作可靠、寿命长,传动比准确。 c. 齿轮机构主要缺点:制造及安装精度要求高,价格较贵,不宜用于两轴间距离较大的场合。 齿轮传动机构的分类 按轴的相对位置平行轴齿轮传动机构①
齿轮基本知识问题及答案
齿轮基本知识问题及答案 基本概念题和答案 1.什么是齿廓啮合基本定律,什么是定传动比的齿廓啮合基本定律?齿廓啮合基本 定律的作用是什么? 答:一对齿轮啮合传动,齿廓在任意一点接触,传动比等于两轮连心线被接触点的公法线所分两线段的反比,这一规律称为齿廓啮合基本定律。若所有齿廓接触点的公法线交连心线于固定点,则为定传动比齿廓啮合基本定律。 作用;用传动比是否恒定对齿廓曲线提出要求。 2.什么是节点、节线、节圆?节点在齿轮上的轨迹是圆形的称为什么齿轮? 答:齿廓接触点的公法线与连心线的交点称为节点,一对齿廓啮合过程中节点在齿轮上的轨迹称为节线,节线是圆形的称为节圆。具有节圆的齿轮为圆形齿轮,否则为非圆形齿轮。 3.什么是共轭齿廊? 答:满足齿廓啮合基本定律的一对齿廓称为共轭齿廓。 4.渐开线是如何形成的?有什么性质? 答:发生线在基圆上纯滚动,发生线上任一点的轨迹称为渐开线。 性质:(1)发生线滚过的直线长度等于基圆上被滚过的弧长。 (2)渐开线上任一点的法线必切于基圆。 (3)渐开线上愈接近基圆的点曲率半径愈小,反之则大,渐开线愈平直。 (4)同一基圆上的两条渐开线的法线方向的距离相等。 (5)渐开线的形状取决于基圆的大小,在展角相同时基圆愈小,渐开线曲率愈大,基圆愈大,曲率愈小,基圆无穷大,渐开线变成直线。 (6)基圆内无渐开线。 5.请写出渐开线极坐标方程。 答:rk = rb / cos αkθk= inv αk = tgαk一αk 6.渐开线齿廓满足齿廓啮合基本定律的原因是什么? 答;(1)由渐开线性质中,渐开线任一点的法线必切于基圆 (2)两圆的同侧内公切线只有一条,并且两轮齿廓渐开线接触点公法线必切于两基圆,因此节点只有一个,即 i12 =ω1 / ω2 =O2P / O1P =r2′/ r1′= rb2 / rb1 = 常数 7.什么是啮合线? 答:两轮齿廓接触点的轨迹。 8.渐开线齿廓啮合有哪些特点,为什么? 答:(1)传动比恒定,因为i12 =ω1 /ω2=r2′/r1′ ,因为两基圆的同侧内公切线只有一条,并且是两齿廓接触点的公法线和啮合线,因此与连心线交点只有一个。故传动比恒定。 (2)中心距具有可分性,转动比不变,因为i12 =ω1/ω2=rb2 / rb1 ,所以一对齿轮加工完后传动比就已经确定,与中心距无关。 (3)齿廓间正压力方向不变,因为齿廓间正压力方向是沿接触点的公法线方向,这公法线又是两基圆同侧内公切线,并且只有一条所以齿廓间正压力方向不变。 (4)啮合角α随中心距而变化,因为a COSα = a′COSα′。 (5)四线合一,1.啮合线是两基圆同侧内公切线,2. 是齿廓接触点的公法线,3.接触点的轨迹是啮合线,4.是齿廓间正压力作用线又是接触点曲率半径之和。 9.什么是模数和分度圆? 答:m = p / π为模数,m 和α为标准值的那个圆称为分度圆。
齿轮基本知识精编版
齿轮基本知识 公司标准化编码 [QQX96QT-XQQB89Q8-NQQJ6Q8-MQM9N]
齿轮基本知识 1.什么是齿廓啮合基本定律,什么是定传动比的齿廓啮合基本定律齿廓啮合基本 定律的作用是什么 答:一对齿轮啮合传动,齿廓在任意一点接触,传动比等于两轮连心线被接触点的公法线所分两线段的反比,这一规律称为齿廓啮合基本定律。若所有齿廓接触点的公法线交连心线于固定点,则为定传动比齿廓啮合基本定律。 作用;用传动比是否恒定对齿廓曲线提出要求。 2.什么是节点、节线、节圆节点在齿轮上的轨迹是圆形的称为什么齿轮 答:齿廓接触点的公法线与连心线的交点称为节点,一对齿廓啮合过程中节点在齿轮上的轨迹称为节线,节线是圆形的称为节圆。具有节圆的齿轮为圆形齿轮,否则为非圆形齿轮。 3.什么是共轭齿廊 答:满足齿廓啮合基本定律的一对齿廓称为共轭齿廓。 4.渐开线是如何形成的有什么性质 答:发生线在基圆上纯滚动,发生线上任一点的轨迹称为渐开线。 性质:(1)发生线滚过的直线长度等于基圆上被滚过的弧长。 (2)渐开线上任一点的法线必切于基圆。 (3)渐开线上愈接近基圆的点曲率半径愈小,反之则大,渐开线愈平直。 (4)同一基圆上的两条渐开线的法线方向的距离相等。 (5)渐开线的形状取决于基圆的大小,在展角相同时基圆愈小,渐开线曲率愈大,基圆愈大,曲率愈小,基圆无穷大,渐开线变成直线。 (6)基圆内无渐开线。 5.请写出渐开线极坐标方程。 答:rk = rb / cos αk θk= inv αk = tgαk一αk 6.渐开线齿廓满足齿廓啮合基本定律的原因是什么 答;(1)由渐开线性质中,渐开线任一点的法线必切于基圆 (2)两圆的同侧内公切线只有一条,并且两轮齿廓渐开线接触点公法线必切于两基圆,因此节点只有一个,即 i12 =ω1 / ω2 = O2P / O1P =r2′/ r1′= rb2 / rb1 = 常数 7.什么是啮合线 答:两轮齿廓接触点的轨迹。 8.渐开线齿廓啮合有哪些特点,为什么 答:(1)传动比恒定,因为 i12 =ω1 /ω2=r2′/r1′ ,因为两基圆的同侧内公切线只有一条,并且是两齿廓接触点的公法线和啮合线,因此与连心线交点只有一个。故传动比恒定。(2)中心距具有可分性,转动比不变,因为 i12 =ω1 /ω2= rb2 / rb1 ,所以一对齿轮加工完后传动比就已经确定,与中心距无关。
齿轮学基础知识
齒輪學基礎知識 一.齒輪之功用 a.能夠傳達動力. b.能通過先選配齒數組合,獲得任意正確的速度比. c.能通過增減齒輪組合數,改變各軸之間的相互位置關係. 二.齿轮的种类 齿轮有许多种类,根据轴向和位置关系可大致分为3类:①平行轴②交叉轴类③偏移轴。 ①平行轴类 (正齿轮) 齿向与轴平行的齿轮,最为常用。 (斜齿轮) 齿向沿螺旋线回转。 正齿轮是1个齿或2个齿反复地啮合,而 斜齿轮的啮合率则上升,为2或3个齿。 因此斜齿轮噪音低而强度大。 齿向分左旋和右旋两种。同为左旋或同为 右旋都不能啮合。使用时应使左旋和右旋 啮合。 (齿条) 一般圆形齿轮的齿形是一种称为渐开线 的曲线,而这种齿条则是一条直线,且呈 锯齿状。啮合对象是斜齿轮时则称作斜齿 条。 (齿条) (斜齿条)
(内齿轮) 是一种轮齿向内且位于圆筒内部的齿 轮。多与结构复杂、被称为行星齿轮的齿轮配套使用。 (人字齿轮) 由齿向不同的上下两部分构成的一种齿轮。 斜齿轮啮合时所产生的力会使两个齿轮 发生轴向错位,但人字齿轮则没有错位现象。 ②交叉轴类 (伞齿轮) 正齿轮为圆柱状,而伞齿轮则是名副其实的伞状(圆锥状)。 常用于塑料玩具汽车来改变转轴方向。 (螺旋伞齿轮) 是伞齿轮的斜齿版。与斜齿轮相同,噪音低和强度大是其特点。
③偏移轴类 (蜗轮蜗杆) 想要极度降低转速时使用。正齿轮的轮齿会 发出撞击声,而蜗轮则不会发出这种声音。 三. 精度等级執行規範 JIS:日本国家工业齿轮规范 JGMA:日本齿轮工会规范 AGMA:美国齿轮工会规范 DIN:德国齿轮工会规范 四.正齒輪各部位之名稱及定義: 1.模數(M):表示公制齒輪上齒的大小. 2.齒數(Z):一個齒輪齒的數量. 3.壓力角(a):指一對嚙合齒輪間之壓力線與節圓在節點之公切線所夾之角度.常用 壓力角有14.5°; 20°; 22.5° 4.節圓:為節線在圓周上的軌跡,即互相嚙合的兩齒間假想互為滾動之圓.為 齒輪設計與制造上的主要數據. 5.基圓:與壓力角線相切之圓,即產生漸開線齒廓之圓. 6.齒冠圓:為通過齒輪頂部之圓. 7.齒根圓:為通過齒輪根部之圓. 8.齒冠:又稱齒頂高,為齒冠圓與節圓半徑之差. 9.齒根:又稱齒底高,為節圓與齒根圓半徑之差. 10.齒深:即全齒高,齒冠與齒齒根之和.
圆柱齿轮传动精度设计知识大全
外啮合圆柱齿轮所有计算公式大全、检验方法、各精度差数表格汇总 注:角标n为法面,t为端面;1为小齿轮,2为大齿轮。 齿轮标准模数(mm) 渐开线圆柱齿轮的基本齿廓mm (GB1356—88) 注:1. 本标准适用于模数m≥1mm,齿形角α=20°的渐开线圆柱齿轮。 2. 允许齿顶修缘。 中心距系列(推荐使用)mm 动力齿轮传动的最大圆周速度m/s
5级以上≥15 ≥30 ≥12 ≥20 6级<15 <30 <12 <20 7级<10 <15 <8 <10 8级<6 <10 <4 <7 9级<2 <4 <1.5 <3 齿轮常用材料及其力学性能图例 45 正火 ≤100 ≤50 588 294 169~217 40~50 101~300 51~150 569 284 162~217 调质 ≤100 ≤50 647 373 229~286 101~300 51~150 628 343 217~255 42SiMn 调质 ≤100 ≤50 784 510 229~286 45~55 101~200 51~100 735 461 217~269 201~300 101~150 686 441 217~255 40MnB 调质 ≤200 ≤100 750 500 241~286 45~55 201~300 101~150 686 441 241~286 35CrMo 调质 ≤100 ≤50 750 550 207~269 40~45 101~300 51~150 700 500 207~269 40Cr 调质 ≤100 ≤50 750 550 241~286 48~55 101~300 51~150 700 500 241~286 20Cr 渗碳淬火 +低温回火 ≤60 ≤30 637 392 56~62 20CrMnTi 渗碳淬火 +低温回火 30 15 1079 883 56~62 ≤80 ≤40 981 785 38CrMoAl 调质、渗氮30 1000 850 229 渗氮HV>850 ZG310-570 正火 ZG340-640 正火 ZG35CrMnSi 正火、回火700 350 ≤217 调质785 588 197~269 HT300 290 190~240 HT350 340 210~260 QT500-7 500 320 170~230 QT600-3 600 370 190~270 KTZ550-04 550 340 180~250 KTZ-650-02 650 430 210~260 齿轮传动荐用的润滑油运动粘度ν /40℃ 齿轮材料 圆周速度v(m/s) <0.5 0.5~1 1~2.5 2.5~5 5~12.5 12.5~25 >25 铸铁、青铜320 220 150 100 80 60 钢 σB=(450~1000)MPa 500 320 220 150 100 80 60 σB=(1000~1250)MPa 500 500 320 220 150 100 80 σB=(1250~1600)MPa 1000 500 500 320 220 150 100 渗碳、表面淬火1000 500 500 320 320 150 100 齿轮精度等级、公差的说明 本网络手册中的圆柱齿轮精度摘自(GB10095—88),现将有关规定和定义简要说明如下: (1) 精度等级 齿轮及齿轮副规定了12个精度等级,第1级的精度最高,第12级的精度最低。齿轮副中两个齿 轮 的精度等级一般取成相同,也允许取成不相同。 齿轮的各项公差和极限偏差分成三个组(参见)。 根据使用的要求不同,允许各公差组选用不同的精度等级,但在同一公差组,各项公差与极限偏差应保持相同的精度等级。参见齿轮传动精度等级选择 (2) 齿轮检验与公差(参见) 根据齿轮副的使用要求和生产规模,在各公差组中选定检验组来检定和验收齿轮精度。 (3) 齿轮副的检验与公差(参见) 齿轮副的要求包括齿轮副的切向综合误差ΔF ic′,齿轮副的一齿切向综合误差Δf ic′,齿轮副的接触班点位置和大小以及侧隙要求,如上述四方面要求均能满足,则此齿轮副即认为合格。 (4) 齿轮侧隙 齿轮副的侧隙要求,应根据工作条件用最大极限侧隙j nmax(或j tmax)与最小极限侧隙j nmin(或j tmin)来规定。 中心距极限偏差(±f a)按“中心距极限偏差”表的规定。 齿厚极限偏差的上偏差E ss及下偏差E si从齿厚极限偏差表来选用。例如上偏差选用F(=-4f Pt),下偏差选用L(=-16f Pt),则齿厚极限偏差用代号FL表示。参看图“齿轮、齿轮副误差及侧隙的定义和代号”。 若所选用的齿厚极限偏差超出齿厚极限偏差表所列14种代号时,允许自行规定。 (5) 齿轮各项公差的数值表 齿距累积公差F P及K个齿距累公差F PK齿向公差Fβ公法线长度变动公差F w 轴线平行度公差中心距极限偏差(±f a)齿厚极限偏差接触斑点 齿圈径向跳动公差F r径向综合公差F i″齿形公差F f齿距极限偏差(±f Pt) 基节极限偏差(±f Pb)一齿径向综合公差f i″齿坯尺寸和形状公差 齿坯基准面径向和端面跳动齿轮的表面粗糙度R a圆柱直齿轮分度圆上弦齿厚及弦齿高 (6) 图样标注
齿轮基础知识问答
齿轮基础知识问答 1.什么是齿廓啮合基本定律,什么是定传动比的齿廓啮合基本定律?齿廓啮合基本定律的作用是什么? 答:一对齿轮啮合传动,齿廓在任意一点接触,传动比等于两轮连心线被接触点的公法线所分两线段的反比,这一规律称为齿廓啮合基本定律。若所有齿廓接触点的公法线交连心线于固定点,则为定传动比齿廓啮合基本定律。 作用;用传动比是否恒定对齿廓曲线提出要求。 2.什么是节点、节线、节圆?节点在齿轮上的轨迹是圆形的称为什么齿轮? 答:齿廓接触点的公法线与连心线的交点称为节点,一对齿廓啮合过程中节点在齿轮上的轨迹称为节线,节线是圆形的称为节圆。具有节圆的齿轮为圆形齿轮,否则为非圆形齿轮。 3.什么是共轭齿廊? 答:满足齿廓啮合基本定律的一对齿廓称为共轭齿廓。 4.渐开线是如何形成的?有什么性质? 答:发生线在基圆上纯滚动,发生线上任一点的轨迹称为渐开线。 性质:(1)发生线滚过的直线长度等于基圆上被滚过的弧长。 (2)渐开线上任一点的法线必切于基圆。 (3)渐开线上愈接近基圆的点曲率半径愈小,反之则大,渐开线愈平直。 (4)同一基圆上的两条渐开线的法线方向的距离相等。 (5)渐开线的形状取决于基圆的大小,在展角相同时基圆愈小,渐开线曲率愈大,基圆愈大,曲率愈小,基圆无穷大,渐开线变成直线。 (6)基圆内无渐开线。 5.请写出渐开线极坐标方程。 答:rk = rb / cos αk θk= inv αk = tgαk一αk 6.渐开线齿廓满足齿廓啮合基本定律的原因是什么? 答;(1)由渐开线性质中,渐开线任一点的法线必切于基圆 (2)两圆的同侧内公切线只有一条,并且两轮齿廓渐开线接触点公法线必切于两基圆,因此节点只有一个,即 i12 =ω1 / ω2 =O2P / O1P =r2′/ r1′= rb2 / rb1 = 常数 7.什么是啮合线? 答:两轮齿廓接触点的轨迹。 8.渐开线齿廓啮合有哪些特点,为什么? 答:(1)传动比恒定,因为i12 =ω1 /ω2=r2′/r1′ ,因为两基圆的同侧内公切线只有一条,并且是两齿廓接触点的公法线和啮合线,因此与连心线交点只有一个。故传动比恒定。 (2)中心距具有可分性,转动比不变,因为i12 =ω1 /ω2=rb2 / rb1 ,所以一对齿轮加工完后传动比就已经确定,与中心距无关。
齿轮箱设计基础知识
目录 1 机械制图基础知识 (1) 1.1 尺寸注法的常用简化表示法 (1) 1.2 中心孔表示法 (2) 1.2.1 75°、90°中心孔 (3) 1.2.2 60°中心孔 (4) 1.3 退刀槽 (5) 1.4 焊缝 (6) 1.5 装配通用技术条件 (7) 1.5.1 连接装配方式 (7) 1.5.2 滚动轴承的装配 (8) 1.5.3 齿轮与齿轮箱装配 (9) 2 螺纹及螺纹连接 (10) 2.1 螺纹的标记方法 (10) 2.2 螺塞与连接螺孔尺寸 (10) 2.3 孔沿圆周的配置 (11) 2.4 螺栓和螺钉通孔尺寸 (11) 2.5 六角螺栓和六角螺母用沉孔尺寸 (11) 2.6 普通螺纹的余留长度 (11) 2.7 扳手空间 (12) 3 键连接 (13) 3.1 平键键槽的尺寸与公差 (13) 3.2 普通平键的尺寸与公差 (14) 4 轴承的选型 (15) 4.1 轴承的分类 (15) 4.2 轴承与轴的配合 (16) 4.3 轴承与外壳的配合 (17) 4.4 配合表面的粗糙度和形位公差 (17) 4.5 选择润滑油或润滑脂的一般原则 (18)
4.6 轴承配置 (19) 5 渐开线圆柱齿轮 (22) 5.1 渐开线圆柱齿轮模数 (22) 5.2 传动参数选择 (23) 5.3 变位齿轮传动 (24) 5.4 最少齿数 (25) 5.5 标准齿轮传动的几何计算 (25) 5.6 高变位齿轮传动的几何计算 (26) 5.7 角变位齿轮传动的几何计算 (27) 5.8 端面重合度εα的确定 (29) 6 减速器设计 (31) 6.1 焊接箱体钢板厚度及焊接尺寸 (31) 6.2 箱体结构设计 (31) 6.3 减速器附件 (35) 6.3.1 油尺和油尺套 (35) 6.3.2 透气塞 (36) 6.3.3 通气罩 (36) 6.3.4 螺塞 (36) 6.3.5 视孔盖 (37) 6.4 齿轮传动的润滑 (37) 6.5 减速器技术要求 (38) 7 齿轮传动设计计算 (39) 7.1 轮齿受力计算 (39) 7.2 齿轮主要尺寸的初步确定 (39) 7.2.1 齿面接触强度 (39) 7.2.2 初步确定模数、齿数 (40) 7.3 齿轮疲劳强度校核计算 (41) 7.3.1 齿面接触强度校核 (41) 7.3.2 轮齿弯曲强度校核 (45) 7.4 计算例题 (46)
齿轮的基本知识
齿轮的基本知识 1、齿轮的种类和特点 齿轮传动是机械传动中应用最广泛的一种传动形式。通常,根据具体用途和工作条件来选用齿轮的类型和传动形式。按照两轮轴线在机器中的相对位置,齿轮传动可用于传递平行轴、相交轴和交错轴之间的运动和动力。其结构和特点见下表。 名称齿轮形状主要特点 直齿圆柱齿轮传动1.两轮轴线平行; 2.轮齿的齿长方向与齿轮 轴线相互平行; 3.外齿轮副,两轮转动方向 相反; 4.内齿轮副,两轮转动方向 相同; 5.此传动形式应用最广 斜齿圆柱齿轮传动1.轮齿的齿长方向与齿轮 轴线倾斜一个角度;2.与前者相比,同时啮合的 齿数增多,传动平稳,传 递的扭矩比较大; 3.有轴向力; 人字齿轮传动1.具斜齿轮传动的优点,但 无轴向力; 2.适用于传递功率大,需正 反向运转的机构中;3.制造麻烦
齿轮齿条传动1.齿条是圆柱齿轮的一种 特例; 2.可用来把旋转运动变为 直线运动,也可以反过来 非圆齿轮传动1.目前常见的有椭圆形和 扇形两种; 2.当主动轮等速转动时从 动轮可以实现有规律的 不等速转动; 3.多用于自动化机构 名称齿轮形状主要特点 直齿锥齿轮传动1.两轮轴线相交于锥顶点, 轴交角有三种:大于,等 于和小于90°。 2.轮齿齿线的延长线通过 锥顶点 斜齿锥齿轮传动1.轮齿齿线的延长线不通 过锥顶点,而是与某一圆 相切; 2. 两轮螺旋角相等,螺旋方向相反 弧齿锥齿轮传动1.轮齿齿线呈圆弧形; 2.两轮螺旋角相等,螺旋方 向相反; 3.与直齿锥齿轮传动相比, 同时参与啮合的齿数增 多,传动平稳,传递扭矩 较大
名称齿轮形状主要特点 交错轴斜齿轮传动1.两轮轴线不在同一平面 上,成空间交错; 2.两轮螺旋角可以相等,也 可以不相等; 3.两轮螺旋方向可以相同, 也可不相同,就单个齿轮 而言,与斜齿圆柱齿轮相 同,其中一齿也可以是直 齿圆柱齿轮 蜗杆传动1.轴线垂直交错; 2.可实现较大的传动比,传 动平稳,噪声小,有自锁 性; 3.传动效率较低,蜗杆线速 度受一定限制 准双曲面齿轮传动1.轴线垂直交错; 2.两轮螺旋角不等,螺旋方 向相反; 3.与弧齿锥齿轮传动相比, 传动更平稳可靠,噪声小
齿轮基础知识全(建议收藏)
渐开线标准直齿齿形:轮齿的轮廓线就是渐开线。 一:基本概念介绍 渐开线: 将一端系有铅笔的线缠在圆筒的外周上,然后在线绷紧的状态下将线渐渐放开。此时,铅笔所画出的曲线即为渐开曲线。圆筒的外周被称为基圆。 一个示例:8齿渐开线齿轮示例。 将圆筒8等分后,系上8根铅笔,画出8条渐开曲线。然后,将线向相反方向缠绕,按同样方法画出8条曲线,这就是以渐开曲线作为齿形,齿数为8的齿轮。 当直线沿一圆周作相切纯滚动时,直线上任一点在与该圆固联的平面上的轨迹k0k,称为该圆的渐开线。
渐开线的性质 (1)直线NK = 曲线N K0 (2) 渐开线上任意一点的法线必切于基圆,切于基圆的直线必为渐开线上某点的法线。与基圆的切点N为渐开线在k点的曲率中心,而线段NK是渐开线在点k处的曲率半径。 (3)渐开线齿廓各点具有不同的压力角,点K离基圆中心O愈远,压力角愈大。 (4)渐开线的形状取决于基圆的大小,基圆越大,渐开线越平直,当基圆半径趋于无穷大时,渐开线成为斜直线。(故齿条的齿轮廓线为斜线) (5)基圆内无渐开线。
渐开线的方程式 rk为渐开线再任意点K的向径。
模数: 模数是决定齿大小的因素。齿轮模数被定义为模数制轮齿的一个基本参数,是人为抽象出来用以度量轮齿规模的数。目的是标准化齿轮刀具,减少成本。直齿、斜齿和圆锥齿齿轮的模数皆可参考标准模数系列表。 分度圆上的齿距p对Π的比值称为模数,用m表示,单位为mm,即m=p/Π,已标准化。模数是齿轮的主要参数之一,齿轮的主要几何尺寸都与模数成正比,m越大,则齿距p越大,轮齿就越大,轮齿的抗弯能力就越强,所以模数m又是轮齿抗弯能力的标志。 不同模数的轮齿大小对比。
全面各种齿轮的基本知识及其画法
齿轮是应用非常广泛的传动件,用以传递动力和运动,并具有改变转速和转向的作用。依据两齿合齿轮轴线在空间的相对位置不同,常见的齿轮传动可分为下列三种形式(图9-43): (1) 圆柱齿轮传动——有于两平行之间的传动。 (2) 圆锥齿轮传动——用于两相之间的传动。 (3) 蜗杆蜗轮传动——用于两交叉之间的传动。 齿轮传动的另一种形式为齿轮齿条传动(图9-44),可用于转动和移动之间的运动转换。 常见的齿轮轮齿是直齿和斜齿。齿轮又有标准齿和非标准齿之分,具有标准齿的齿轮称为标准齿轮。本节介绍具有渐开线齿形的标准齿轮的有关知识与规定画法。
一、直齿圆柱齿轮(直齿轮) (一) 直齿圆柱齿轮各部分名称及有关参数(图9-45) 1、齿顶圆(直径d1) 通过圆柱齿轮齿顶的曲面称为齿顶圆柱面。齿顶圆柱面与端平面的交线称为 齿顶圆。 2、齿根圆(直径d2) 通过圆柱齿轮齿根的曲面称为齿根圆柱面。齿根圆柱面与端平面的交线称为 齿根圆。 3.分度圆(直径d) 齿轮设计和加工时计算尺寸的基准圆称为分度圆。它位于齿顶圆和齿根圆之间,是一个约定的假想圆。 4.节圆(直径d) 两齿轮合时,位于连心线OO上的两齿廓点P,称为节点。分别以O O为圆心,OP为半径所作的两个相切的园称为节圆。正确安装的标准齿轮的d=d。
5.齿高h 轮齿在齿顶圆与齿根圆之间的径向距离称为齿高。齿高h分为齿顶高h,齿 根高h两段(h=h+h): 齿根高h齿根圆与分度圆之间的径向距离; 吃根高h齿根圆与分度圆之间的径向距离; 6.齿数z 即轮齿的个数,它是齿轮计算的主要参数之一。 8.模数m 由于分度圆周长πd=pz 所以 d=p/πz 令 p/π=m 则 d=mz 式中m称为齿轮的模数,它等于齿距与圆周率π的比值。模数以毫米为单位,为了便于设计和制造,模数的数值已标准化,如图9-12所示。 模数是设计、制造齿轮的重要参数。由于模数m与齿距p成正比。而p决 定了轮齿的大小,所以m的大小反映了轮齿的大小。模数大,轮齿大,在其他条件相同的情况下,轮齿的承载能力也就大,反之承载能力就小。另外, 能配对折合的两个齿轮,其没,模数必须相等。加工齿轮也须选用与齿轮模 数相同的刀具,因而模数又是选择刀具的依据。 9.压力角、齿形角a 如图9-45所示,轮齿在分度圆上齿合点p的受力方向(即渐开线齿廓曲线 的法线方向)与该点的瞬时速度方向(分度圆的切线方向)所夹的锐角a称为压力角。我国规定的标准压力角a=20度。 加工齿轮用的基本齿条的法向压力角称为吃形角。故齿形角也为20度,也 用a表示。
齿轮基本知识
齿轮基本知识 1.什么是齿廓啮合基本定律,什么是定传动比的齿廓啮合基本定律?齿廓啮合基本 定律的作用是什么? 答:一对齿轮啮合传动,齿廓在任意一点接触,传动比等于两轮连心线被接触点的公法线所分两线段的反比,这一规律称为齿廓啮合基本定律。若所有齿廓接触点的公法线交连心线于固定点,则为定传动比齿廓啮合基本定律。 作用;用传动比是否恒定对齿廓曲线提出要求。 2.什么是节点、节线、节圆?节点在齿轮上的轨迹是圆形的称为什么齿轮? 答:齿廓接触点的公法线与连心线的交点称为节点,一对齿廓啮合过程中节点在齿轮上的轨迹称为节线,节线是圆形的称为节圆。具有节圆的齿轮为圆形齿轮,否则为非圆形齿轮。 3.什么是共轭齿廊? 答:满足齿廓啮合基本定律的一对齿廓称为共轭齿廓。 4.渐开线是如何形成的?有什么性质? 答:发生线在基圆上纯滚动,发生线上任一点的轨迹称为渐开线。 性质:(1)发生线滚过的直线长度等于基圆上被滚过的弧长。 (2)渐开线上任一点的法线必切于基圆。 (3)渐开线上愈接近基圆的点曲率半径愈小,反之则大,渐开线愈平直。 (4)同一基圆上的两条渐开线的法线方向的距离相等。 (5)渐开线的形状取决于基圆的大小,在展角相同时基圆愈小,渐开线曲率愈大,基圆愈大,曲率愈小,基圆无穷大,渐开线变成直线。 (6)基圆内无渐开线。 5.请写出渐开线极坐标方程。 答:rk = rb / cos αkθk= inv αk = tgαk一αk 6.渐开线齿廓满足齿廓啮合基本定律的原因是什么? 答;(1)由渐开线性质中,渐开线任一点的法线必切于基圆 (2)两圆的同侧内公切线只有一条,并且两轮齿廓渐开线接触点公法线必切于两基圆,因此节点只有一个,即 i12 =ω1 / ω2 =O2P / O1P =r2′/ r1′= rb2 / rb1 = 常数 7.什么是啮合线? 答:两轮齿廓接触点的轨迹。 8.渐开线齿廓啮合有哪些特点,为什么? 答:(1)传动比恒定,因为i12 =ω1 /ω2=r2′/r1′ ,因为两基圆的同侧内公切线只有一条,并且是两齿廓接触点的公法线和啮合线,因此与连心线交点只有一个。故传动比恒定。 (2)中心距具有可分性,转动比不变,因为i12 =ω1 /ω2=rb2 / rb1 ,所以一对齿轮加工完后传动比就已经确定,与中心距无关。
齿轮油基础知识
齿轮油基础知识(中级经验可阅读) 车辆齿轮油(中级版) 1. 概述 车辆齿轮油是润滑油重要产品,主要用于各种汽车手动变速器和驱动桥中。自1925年Gleason Works 开发了第一个双曲线齿轮驱动桥以来,在短短几年间,几乎全部的美国制造商都推广使用。接着,在欧洲也逐步得到应用。为了满足双曲线齿轮驱动桥的润滑要求。开发了极压车辆齿轮油,这种早期的齿轮油为S-Pb型或S-P-Cl型。二次世界大战以后,为了制得具有高速冲击性能和高扭矩性能的多效齿轮油,引入了S-P-Cl型复合剂。以后由于卡车载重和功率的提高,加上轴偏置增大,复合剂在原来的S-P-Cl基础上又引入了二烷基二硫代磷酸锌,大大提高了极压性能。进入60年代,由于汽车工业不断追求高速度,大马力,需要热氧化安定性更高的润滑油,研制出第一代S-P型双曲线齿轮油,并逐渐在全世界得到普及。 硫磷型车辆齿轮油经过40年的使用,经久不衰,其主要是围绕着含磷添加剂和添加剂复配技术的发展。第二代、第三代硫磷型齿轮油具有好的热稳定性和水解稳定性,解决了含磷剂消耗快的问题,并可作为车辆、工业齿轮通用油。 1.1国外车辆齿轮油情况 代表着发达国家的欧洲,每年需要车辆齿轮油30万吨,其中75%为GL-5车辆齿轮油,其余为GL-4齿轮油。见表1: 由于欧洲市场上对齿轮油的质量要求不断提高,添加剂用量增加,换油期延长,使销售量增长很小。出现了全寿命油,要求汽车齿轮油的基础油越来越多地使用合成润滑油,同时有轻质化趋势,好处是改进了燃料经济性,也容易换档。欧洲汽车生产商要求车辆齿轮油延长换油周期,甚至要求与车辆同寿命,目前汽车寿命约为75万公里,将来要延长到100万公里,因此齿轮油与橡胶密封材料配伍性受到特别重视,要求在长期运转中齿轮油对密封材料既不能使其硬化、收缩,又不能使其膨胀、降低强度。 目前欧洲轿车多为前桥驱动,前桥中装有同步器。欧洲同步器设计与美国不同,美国的同步器由一组摩片组成,而欧洲的同步器由一组黄铜环组成,为使其同步器能正常工作,在要求使用GL-4、GL-5齿轮油时,还要补充进行密封件试验和同步器试验。由此可见,欧洲车辆齿轮油规格高于相应的美国规格。 1.2 我国车辆齿轮油的发展概况 从20世纪50-70年代,我国车辆齿轮油尚未形成完整的体系,只分为齿轮油和双曲线齿轮油这两种残渣型的黑色齿轮油和一种馏分型的合成双曲线齿轮油。1960年公布我国第一个双曲线齿轮油的规格,基础油主要是残渣油,常用添加剂是硫化蓖麻油,也有用硫化松脂油。1962年公布第一个用于汽车、拖拉机变速箱及后桥的齿轮油规格,其油品由残渣油或加入部分馏分油构成,使用性能差,寿命短,耗能大,还需用低粘度润滑油或低凝点柴油稀释,才能冷启动。1967年开始生产渣油型S-P-Cl-Zn型双曲线齿轮油,主要添加剂是二烷基二硫代磷酸锌(T202)和氯化石蜡(T301)。油品的主要特性如极压抗磨性有较大提高,但热氧化安定性、防锈性、颜色等均较差。1971开始试制和生产精制型双曲线齿轮油,按添加剂类型
齿轮及润滑基础知识
齿轮及润滑知识 齿轮 - 基本定义 齿轮是能互相啮合的有齿的机械零件。 直齿圆柱齿轮各部分的名称和基本参数 齿轮模数标准系列
标准直齿圆柱齿轮轮齿各部分的尺寸计算 齿轮可按齿形、齿轮外形、齿线形状、轮齿所在的表面和制造方法等分类。 1)齿轮的齿形包括齿廓曲线、压力角、齿高和变位。 渐开线齿轮比较容易制造,因此现代使用的齿轮中渐开线齿轮占绝对多数,而摆线齿轮和圆弧齿轮应用较少。在压力角方面,以前有些国家采用过14.5°和15°,但是多数国家已统一规定为20°小压力角齿轮的承载能力较小;而大压力角齿轮,虽然承载能力较高,但在传递转矩相同的情况下轴承的负荷增大,因此大压力角齿轮仅用于特殊情况。齿高已标准化,一般均采用标准齿高。变位齿轮优点较多,已遍及各类机械设备中。 2)齿轮按其外形分为圆柱齿轮、锥齿轮、非圆齿轮、齿条、蜗杆-蜗轮。 3)按齿线形状齿轮分为直齿轮、斜齿轮、人字齿轮、曲线齿轮。4)按轮齿所在的表面齿轮分为外齿轮、内齿轮。外齿轮齿顶圆比齿根圆大;而内齿轮齿顶圆比齿根圆小。 5)按制造方法齿轮分为铸造齿轮、切制齿轮、轧制齿轮、烧结齿轮等。 材料和热处理对齿轮的承载能力和尺寸、重量有很大的影响。20世纪50年代前多用碳钢,60年代改用合金钢,而70年代多用表面硬化钢。齿面按硬度可区分为软齿面和硬齿面两种。 1)软齿面:齿面硬度HB≤350,在调质或正火热处理之后进行精切齿。
这种齿轮承载能力较低,但制造比较容易,跑合性好,用于传动尺寸和重量无严格限制以及小量生产的一般机械中。因为配对的齿轮中小轮负担较重,为使大小齿轮工作寿命大致相等,小轮齿面硬度比大轮的高HB20~50。 2)硬齿面:齿面硬度HB>350。这种齿轮承载能力高,在齿轮精切之后进行淬火、表面淬火或渗碳淬火,一般齿面硬度HRC45~65。但在热处理中,齿轮不可避免地产生变形,因此在热处理之后须进行磨削、研磨或精切,以消除因变形产生的误差,提高齿轮的精度。如果硬齿面齿轮精度不够,其承载能力往往不如软齿面的。经渗氮处理的齿面硬度HV≥600,抗胶合能力较高。由于渗氮时温度较低,齿轮的变形很小,可不再进行机械加工,但渗氮层较薄,适于制造小尺寸的齿轮,但不能承受冲击载荷或磨料磨损。 齿轮是现代机械中应用最广泛的重要基础零件之一。齿轮类型很多,有直齿轮、斜齿轮、人字齿等,齿面硬度有软齿面和硬齿面,齿轮转速有高有低,传动装置有开式装置和闭式装置,载荷有轻重之分,因此影响因素很多,所以实际应用中会出现各种不同的失效形式。齿轮的失效主要发生在轮齿部分,其常见失效形式有:轮齿折断、齿面点蚀、齿面磨损、齿面胶合和齿面塑性变形五种。 1 轮齿折断 轮齿折断有多种形式,在正常情况下,有以下两种: 1)过载折断。对于由铸铁或高硬度合金钢等脆性材料制成的齿轮,由于严重过载或受到冲击载荷作用,会使齿根危险截面上的应力超过极限值而发生突然断齿。过载折断的断口一般都在齿根部位。断口比较平直,并且具有很粗糙的特征。 2)疲劳折断。①疲劳断齿由于轮齿根部在载荷作用下所产生的弯曲应力为脉动循环交变应力,以及在齿根圆角、加工刀痕、材料缺陷等应力集中源的复合作用下,会产生疲劳裂纹。裂纹逐步蔓延扩展,最终导致轮齿发生疲劳断齿。3)局部断齿。当齿面加工精度较低、或齿轮检修安装质量较差时,沿齿面接触线会产生一端接触、另一端不接触的偏载现象。偏载使局部接触的轮齿齿根处应力明显增大,超过极限值而发生局部断齿。局部断齿总是发生在轮齿的端部。齿面较小的直齿轮常发生全齿折断,齿面较大的直齿轮,因制造装配误差易产生载荷偏置一端,导致局部折断;斜
齿轮基本知识定稿版
齿轮基本知识精编 W O R D版 IBM system office room 【A0816H-A0912AAAHH-GX8Q8-GNTHHJ8】
齿轮基本知识 1.什么是齿廓啮合基本定律,什么是定传动比的齿廓啮合基本定律?齿廓啮合基本 定律的作用是什么? 答:一对齿轮啮合传动,齿廓在任意一点接触,传动比等于两轮连心线被接触点的公法线所分两线段的反比,这一规律称为齿廓啮合基本定律。若所有齿廓接触点的公法线交连心线于固定点,则为定传动比齿廓啮合基本定律。 作用;用传动比是否恒定对齿廓曲线提出要求。 2.什么是节点、节线、节圆节点在齿轮上的轨迹是圆形的称为什么齿轮 答:齿廓接触点的公法线与连心线的交点称为节点,一对齿廓啮合过程中节点在齿轮上的轨迹称为节线,节线是圆形的称为节圆。具有节圆的齿轮为圆形齿轮,否则为非圆形齿轮。 3.什么是共轭齿廊? 答:满足齿廓啮合基本定律的一对齿廓称为共轭齿廓。 4.渐开线是如何形成的有什么性质
答:发生线在基圆上纯滚动,发生线上任一点的轨迹称为渐开线。 性质:(1)发生线滚过的直线长度等于基圆上被滚过的弧长。 (2)渐开线上任一点的法线必切于基圆。 (3)渐开线上愈接近基圆的点曲率半径愈小,反之则大,渐开线愈平直。 (4)同一基圆上的两条渐开线的法线方向的距离相等。 (5)渐开线的形状取决于基圆的大小,在展角相同时基圆愈小,渐开线曲率愈大,基圆愈大,曲率愈小,基圆无穷大,渐开线变成直线。 (6)基圆内无渐开线。 5.请写出渐开线极坐标方程。 答:rk = rb / cos αk θk= inv αk = tgαk一αk 6.渐开线齿廓满足齿廓啮合基本定律的原因是什么? 答;(1)由渐开线性质中,渐开线任一点的法线必切于基圆 (2)两圆的同侧内公切线只有一条,并且两轮齿廓渐开线接触点公法线必切于两基圆,因此节点只有一个,即 i12 =ω1 / ω2 = O2P / O1P =r2′/ r1′= rb2 / rb1 = 常数
齿轮知识大全
齿状有许多种类,依照齿轮轴性区分,有平行轴(parallel axis),直交轴(intersecting axis),错交轴 (non-parallel and non-intersecting axis) 1.决定齿轮要传递多少的功率P 2.两配合的齿轮转速为何?N1, N2 3.算出速度比(velocity ratio)VR = N1 /N2 4.查表得模数大小(m),并使用最小且可能的齿数N 代入式子去试验 5.用速度比和pinion 齿数来决定gear 的齿数N= VR×N1 6.由上可求得节圆直径D1 = m×N 1;D2 = m×N2及中心轴距 C = (D1+D2)÷2 7.由上条件可计算出法向受力及切线速度Vt 8.考虑齿面宽F 及齿形系数u 9.依据所需的负荷、硬度、弹性系数等机械性质,选择适当的材料
齿轮加工时的特殊用语: 1.齿形修整(tip relief) 齿形修整有齿冠部份之修整及齿根部份之修整两种,大部分是轴类的齿冠修整较普遍使用,且一各国标准及齿轮级数不同,修整量也有不同. 优点是可缓和干扰,降低噪音,增长齿轮寿命.但若修整量过大,将会发生咬合不良. 2.鼓形加工及削端加工 鼓形加工及削端加工都是齿筋方向的修整方法.鼓形加工为使齿面之接触集中在齿幅之中央部位,而将齿筋修整成带有鼓形之状态,若鼓形加工过甚,对齿轮强度有不良影响. 削端加工为将齿筋之两端轻微倒角,如此可得近似鼓形加工之效果. 3.扫外径及倒角(topping and semi-topping) 以刀具加工齿轮时,顺便将齿轮外径削除称作topping, 此种作法可降低外径偏差,削除齿尖所产生之毛边,增加美观. 加工时将齿顶部份倒角切除,而没切削到外径,称做semi-topping , JIS 及DIN 规范各有不同. 单件齿轮无法传达任何动力,至少要2个以上齿轮咬合一起才能传达动力. 1.一段减速机构 速度传达比:Z1/Z2=N2/N1 Z1:主动齿轮之齿数Z2:被动齿轮之齿数N1:主动齿轮之转数N2:被动齿轮之转数 速度传达比>1 增速齿轮机构 速度传达比<1 减速齿轮机构 速度传达比=1 等速齿轮机构 此外,一段齿轮机构尚有齿条与正齿轮之组合(Rack and Pinion) 2.2段齿轮机构 2段齿轮机够为一段齿轮机构使用两组之情形,
齿轮传动装置装配基础知识(沐风教育)
齿轮传动装置装配基础知识 常用的齿轮传动装置有圆柱齿轮、圆锥齿轮和蜗杆蜗轮等三种。 齿轮传动装置正确装配的基本要求是:正确装配和固定→精确保持相对位置→具有啮合间隙→保证工作表面良好接触。装配正确的齿轮运转时:速度均匀、无振动和噪音。 装配步骤是: ①对零件进行清洗、去除毛刺,并按图纸要求检查零件的尺寸、几何形状、位置精度及表面粗糙度等。 ②对装配式齿轮(蜗轮),先进行齿轮(蜗轮)的自身装配,并固定之。 ③将齿轮(蜗轮)装于轴上,并装配好滚动轴承。 ④齿轮—轴(蜗杆、蜗轮—轴)安装就位。 ⑤安装后的齿轮接触质量(啮合间隙、接触面积)检查。 (一)圆柱齿轮传动装置的装配 1.齿轮与轴的配合 齿轮与轴的配合面在压入前应涂润滑油。配合面为锥形面时,应用涂色法检查接触状况,对接触不良的应进行刮削,使之达到要求。装配好后的齿轮—轴应检查齿轮齿圈的径向跳动和端面跳动。 2.两啮合齿轮的中心距和轴线平行度的检查 (1)中心距的检查 在齿轮轴未装入齿轮箱中以前,可以用特制的游标卡尺来测量两轴承座孔的中心距。或利用检验心轴和内径千分尺或游标卡尺来进行测量。 (2)轴线平行度的检查 1m 长度上轴线平行度的偏差量为δfx 和δfy (即为轴线平行度),可分别用下面的两式来表示: )/(1000),/(1000m mm b f f m mm b f f y y x x ?=?=δδ 检查前,先将齿轮轴或检验心轴放置在齿轮箱的轴承座孔内,然后用内径千
分尺来测量x方向上轴线的平行度(即两根轴线在1m长度上的中心距的差值),再用水平仪来测量y方向上的轴线的平行度(即两根轴线水平度的差值)。 3.啮合间隙的检查 齿轮啮合间隙的功用是储存润滑油、补偿齿轮尺寸的加工误差和中心距的装配误差,以及补偿齿轮和齿轮箱在工作时的热变形和弹性变形。一般正常啮合的圆柱齿轮的顶隙(C=0.25m n ,) 齿轮啮合间隙的检查方法有以下三种: (1)塞尺法用塞尺可以直接测量出齿轮的顶隙和侧隙。 (2)千分表法用千分表可以间接测量出正齿轮的侧隙。 若被测的是斜齿轮,则法面上的实际侧隙j n=cosαn cosβ。式中αn为斜齿轮的法向压力角(20°),β为斜齿轮的螺旋角(8°~ 20°)。 当被测齿轮副的中心距为可调时,则中心距的变化量Δf a与实际侧隙的变化量Δj n之间的关系为:Δj n=2Δf a·sinα(正齿轮)或Δj n=2Δf a·sinαn(斜齿轮)。 (3)压铅法压铅法是测量顶隙和侧隙最常用的方法。测量时,先将铅丝放置在齿轮上,然后使齿轮啮合滚压,压扁后的铅丝厚度,就相当于顶隙和侧隙的数值,其值可以用游标卡尺或千分尺测量,铅丝最厚部分的厚度为顶隙c,相邻两较薄部分的厚度之和为侧隙j n=j n′+j n″。 对于大型的宽齿轮,必须放置两条以上的铅丝,才能正确的测量出啮合间隙。此时不仅可以根据它来检查间隙,而且还能检查出齿轮轴线的平行度。 4.齿轮啮合接触面的检查与调整 其检查方法一般采用涂色法,即将红铅油均匀的涂在主动齿轮的轮齿面上,用其来驱动从动齿轮数圈后,则色迹印显出来,根据色迹可以判定齿轮啮合接触面是否正确。装配正确的齿轮啮合接触面必须均匀的分布在节线上下,接触面积应符合要求。装配后齿轮啮合接触面常有几种情况。 为了纠正不正确的啮合接触,可采用改变齿轮中心线的位置、研刮轴瓦或加工齿形等方法来修正。当齿轮啮合位置正确,而接触面积太小时,可在齿面上加研磨剂,并使两齿轮转动进行研磨,使其达到足够的接触面积。