模具抛光的常见方法

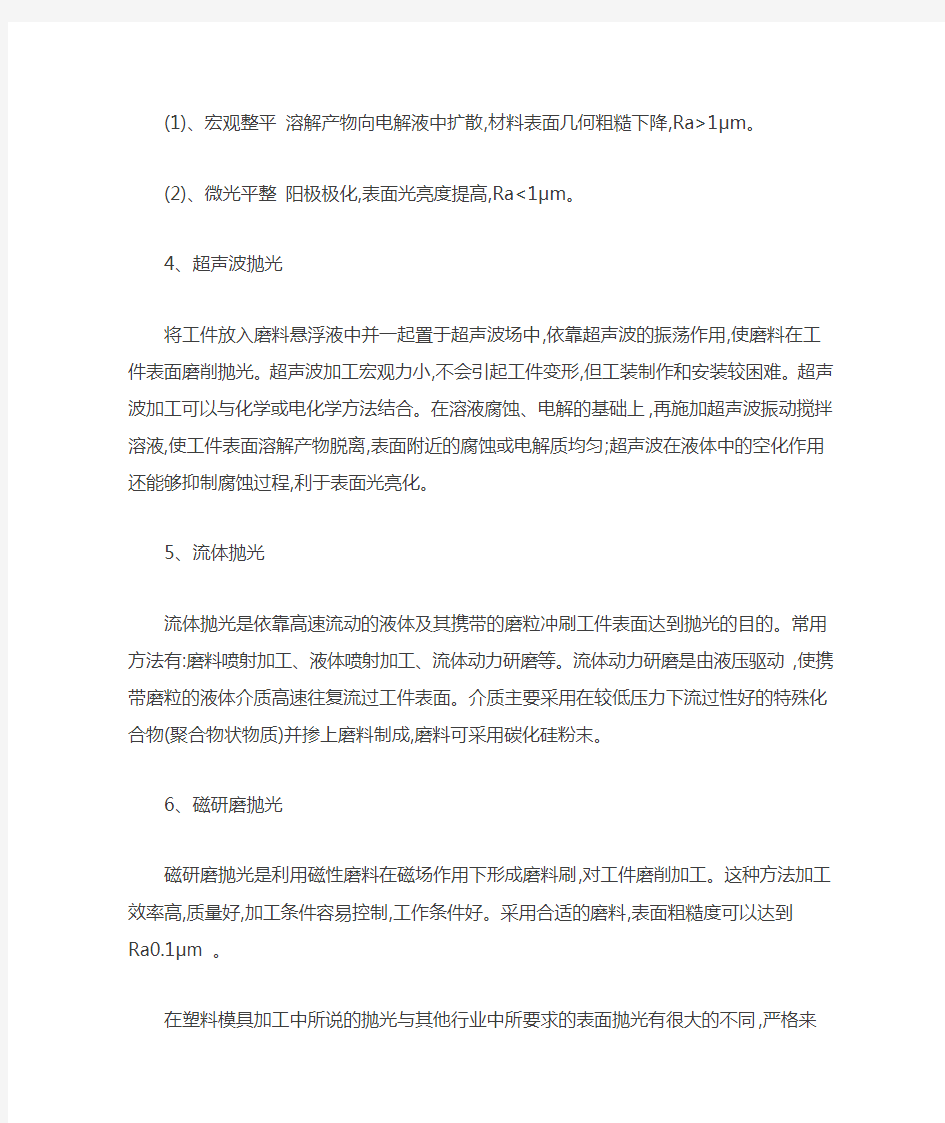
模具抛光的常见方法
模具抛光主要是用来降低工件的表面粗糙程度,对金属工件进行选择抛光工艺方法时,根据不同需求可以选不同的方法,作为在模具抛光行业的巨人毅顺锦鸿,就来为大家分享抛光常见的几种方法。
1、机械抛光
机械抛光是靠切削、材料表面塑性变形去掉被抛光后的凸部而得到平滑面的抛光方法,一般使用油石条、羊毛轮、砂纸等,以手工操作为主,特殊零件如回转体表面,可使用转台等辅助工具,表面质量要求高的可采用超精研抛的方法。超精研抛是采用特制的磨具,在含有磨料的研抛液中,紧压在工件被加工表面上,作高速旋转运动。利用该技术可以达到 Ra0.008μm 的表面粗糙度,是各种抛光方法中最高的。光学镜片模具常采用这种方法。
2、化学抛光
化学抛光是让材料在化学介质中表面微观凸出的部分较凹部分优先溶解,从而得到平滑面。这种方法的主要优点是不需复杂设备,可以抛光形状复杂的工件,可以同时抛光很多工件,效率高。化学抛光的核心问题是抛光液的配制。化学抛光得到的表面粗糙度一般为数 10μm。
3、电解抛光
电解抛光基本原理与化学抛光相同,即靠选择性的溶解材料表面微小凸出部分,使表面光滑。与化学抛光相比,可以消除阴极反应的影响,效果较好。电化学抛光过程分为两步:
(1)、宏观整平溶解产物向电解液中扩散,材料表面几何粗糙下降,Ra>1μm。
(2)、微光平整阳极极化,表面光亮度提高,Ra<1μm。
4、超声波抛光
将工件放入磨料悬浮液中并一起置于超声波场中,依靠超声波的振荡作用,使磨料在工件表面磨削抛光。超声波加工宏观力小,不会引起工件变形,但工装制作和安装较困难。超声波加工可以与化学或电化学方法结合。在溶液腐蚀、电解的基础上,再施加超声波振动搅拌溶液,使工件表面溶解产物脱离,表面附近的腐蚀或电解质均匀;超声波在液体中的空化作用还能够抑制腐蚀过程,利于表面光亮化。
5、流体抛光
流体抛光是依靠高速流动的液体及其携带的磨粒冲刷工件表面达到抛光的目的。常用方法有:磨料喷射加工、液体喷射加工、流体动力研磨等。流体动力研磨是由液压驱动,使携带磨粒的液体介质高速往复流过工件表面。介质主要采用在较低压力下流过性好的特殊化合物(聚合物状物质)并掺上磨料制成,磨料可采用碳化硅粉末。
6、磁研磨抛光
磁研磨抛光是利用磁性磨料在磁场作用下形成磨料刷,对工件磨削加工。这种方法加工效率高,质量好,加工条件容易控制,工作条件好。采用合适的磨料,表面粗糙度可以达到Ra0.1μm 。
在塑料模具加工中所说的抛光与其他行业中所要求的表面抛光有很大的不同,严格来说,模具的抛光应该称为镜面加工。它不仅对抛光本身有很高的要求并且对表面平整度、光滑度以及几何精确度也有很高的标准。表面抛光一般只要求获得光亮的表面即可。镜面加工的标准分为四级:AO=Ra0.008μm,A1=Ra0.016μm , A3=Ra0.032μ m ,A4=Ra0.063μm,由于电解抛光、流体抛光等方法很难精确控制零件的几何精确度,而化学抛光、超声波抛光、磁研磨抛光等方法的表面质量又达不到要求,所以精密模具的镜面加工还是以机械抛光为主。
毅顺锦鸿在模具抛光方面可谓是领头人,别人不能做的,毅顺能做,别人能做的,毅顺会做的更好!
省模抛光步骤
随着塑料制品日溢广泛的应用,如日化用品和饮料包装容器等,外观的需要往往要求塑料模具型腔的表面达到镜面抛光的程度。而生产光学镜片、镭射唱片等模具对表面粗糙度要求极高,因而对抛光性的要求也极高。抛光不仅增加工件的美观,而且能够改善材料表面的耐腐蚀性、耐磨性,还可以使模具拥有其它优点,如使塑料制品易于脱模,减少生产注塑周期等。因而抛光在塑料模具制作过程中很重要的一道工序。 1 抛光方法 目前常用的抛光方法有以下几种: 1.1 机械抛光 机械抛光是靠切削、材料表面塑性变形去掉被抛光后的凸部而得到平滑面的抛光方法,一般使用油石条、羊毛轮、砂纸等,以手工操作为主,特殊零件如回转体表面,可使用转台等辅助工具,表面质量要求高的可采用超精研抛的方法。超精研抛是采用特制的磨具,在含有磨料的研抛液中,紧压在工件被加工表面上,作高速旋转运动。利用该技术可以达到Ra0.008μm的表面粗糙度,是各种抛光方法中最高的。光学镜片模具常采用种方法。 1.2 化学抛光 化学抛光是让材料在化学介质中表面微观凸出的部分较凹部分优先溶解,从而得到平滑面。这种方法的主要优点是不需复杂设备,可以抛光形状复杂的工件,可以同时抛光很多工件,效率高。化学抛光的核心问题是抛光液的配制。化学抛光得到的表面粗糙度一般为数10μm。 1.3 电解抛光 电解抛光基本原理与化学抛光相同,即靠选择性的溶解材料表面微小凸出部分,使表面光滑。与化学抛光相比,可以消除阴极反应的影响,效果较好。电化学抛光过程分为两步: (1)宏观整平溶解产物向电解液中扩散,材料表面几何粗糙下降,Ra>1μm。 (2)微光平整阳极极化,表面光亮度提高,Ra<1μm。 1.4 超声波抛光
模具抛光的工艺流程及技巧
模具抛光的工艺流程及技巧 模具抛光的工艺流程及技巧 抛光在模具制作过程中是很重要的一道工序,也是收官之作,随着塑料制品的日溢广泛应用,对塑料制品的外观品质要求也越来越高,所以塑料模具型腔的表面抛光质量也要相应提高,特别是镜面和高光高亮表面的模具对模具表面粗糙度要求更高,因而对抛光的要求也更高。抛光不仅增加工件的美观,而且能够改善材料表面的耐腐蚀性、耐磨性,还可以方便于后续的注塑加工,如使塑料制品易于脱模,减少生产注塑周期等。目前常用的抛光方法有以下几种: ㈠机械抛光 机械抛光是靠切削、材料表面塑性变形去掉被抛光后的凸部而得到平滑面的抛光方法,一般使用油石条、羊毛轮、砂纸等,以手工操作为主,特殊零件如回转体表面,可使用转台等辅助工具,表面质量要求高的可采用超精研抛的方法。超精研抛是采用特制的磨具,在含有磨料的研抛液中,紧压在工件被加工表面上,作高速旋转运动。利用该技术可以达到Ra0.008μm的表面粗糙度,是各种抛光方法中最高的。光学镜片模具常采用这种方法。 ⑴机械抛光基本程序 要想获得高质量的抛光效果,最重要的是要具备有高质量的油石、砂纸和钻石研磨膏等抛光工具和辅助品。而抛光程序的选择取决于前期加工后的表面状况,如机械加工、电火花加工,磨加工等等。机械抛光的一般过程如下: ①粗抛经铣、电火花、磨等工艺后的表面可以选择转速在35 000—40 000 rpm的旋转表面抛光机或超声波研磨机进行抛光。常用的方法有利用直径Φ3mm、WA # 400的轮子去除白色电火花层。然后是手工油石研磨,条状油石加煤油作为润滑剂或冷却剂。一般的使用顺序为#180 ~ #240 ~ #320 ~ #400 ~ #600 ~ #800 ~ #1000。许多模具制造商为了节约时间而选择从#400开始。 ②半精抛半精抛主要使用砂纸和煤油。砂纸的号数依次为:#400 ~ #600 ~ #800 ~ #1000 ~ #1200 ~ #1500。实际上#1500砂纸只用适于淬硬的模具钢(52HRC以上),而不适用于预硬钢,因为这样可能会导致预硬钢件表面烧伤。 ③精抛精抛主要使用钻石研磨膏。若用抛光布轮混合钻石研磨粉或研磨膏进行研磨的话,则通常的研磨顺序是9μm(#1800)~ 6μ m(#3000)~3μm(#8000)。9μm的钻石研磨膏和抛光布轮可用来去除#1200和#1500号砂纸留下的发状磨痕。接着用粘毡和钻石研磨膏进行抛光,顺序为1μm(#14000)~ 1/2μm(#60000)~1/4μm(#100000)。 精度要求在1μm以上(包括1μm)的抛光工艺在模具加工车间中一个清洁的抛光室内即可进行。若进行更加精密的抛光则必需一个绝对洁净的空间。灰尘、烟雾,头皮屑和口水沫都有可能报废数个小时工作后得到的高精密抛光表面。 ⑵机械抛光中的技巧 Ⅰ用砂纸抛光应注意以下几点: ①用砂纸抛光需要利用软的木棒或竹棒。在抛光圆面或球面时,使用软木棒可更好的配合圆面和球面的弧度。而较硬的木条像樱桃木,则更适用于平整表面的抛光。修整木条的末端使其能与钢件表面形状保持吻合,这样可以避免木条(或竹条)的锐角接触钢件表面而造成较深的划痕。 ②当换用不同型号的砂纸时,抛光方向应变换45°~ 90°,这样前一种型号砂纸抛光后留下的条纹阴影即可分辨出来。在换不同型号砂纸之前,必须用100%纯棉花沾取酒精之类的清洁液对抛光表面进行仔细的擦拭,因为一颗很小的沙砾留在表面都会毁坏接下去的整个抛光工作。从砂纸抛光换成钻石研磨膏抛光时,这个清洁过程同样重要。在抛光继续进行之前,所有颗粒和煤油都必须被完全清洁干净。 ③为了避免擦伤和烧伤工件表面,在用#1200和#1500砂纸进行抛光时必须特别小心。因而有必要加载一个轻载荷以及采用两步抛光法对表面进行抛光。用每一种型号的砂纸进行抛光时都应沿两个不同方向进行两次抛光,两个方向之间每次转动45°~ 90°。 Ⅱ钻石研磨抛光应注意以下几点: ①这种抛光必须尽量在较轻的压力下进行特别是抛光预硬钢件和用细研磨膏抛光时。在用#8000研磨膏抛光时,常用载荷为100~200g/cm2,但要保持此载荷的精准度很难做到。为了更容易做到这一点,可以在木条上做一个薄且窄的手柄,比如加一铜片;或者在竹条上切去一部分而使其更加柔软。这样可以帮助控制抛光压力,以确保模具表面压力不会过高。 ②当使用钻石研磨抛光时,不仅是工作表面要求洁净,工作者的双手也必须仔细清洁。 ③每次抛光时间不应过长,时间越短,效果越好。如果抛光过程进行得过长将会造成“橘皮”和“点蚀”。 ④为获得高质量的抛光效果,容易发热的抛光方法和工具都应避免。比如:抛光轮抛光,抛光轮产生的热量会很容易造成“橘皮”。 ⑤当抛光过程停止时,保证工件表面洁净和仔细去除所有研磨剂和润滑剂非常重要,随后应在表面喷淋一层模具防锈涂层。 由于机械抛光主要还是靠人工完成,所以抛光技术目前还是影响抛光质量的主要原因。除此之外,还与模具材料、抛光前的表面状况、
不锈钢产品抛光方法
不锈钢产品抛光方法: 目前常用的不锈钢抛光方法有以下几种: 1 机械抛光机械抛光是靠切削、材料表面塑性变形去掉被抛光后的凸部而得到平滑面的抛光方法,一般使用油石条、羊毛轮、砂纸等,以手工操作为主,特殊零件如回转体表面,可使用转台等辅助工具,表面质量要求高的可采用超精研抛的方法。超精研抛是采用特制的磨具,在含有磨料的研抛液中,紧压在工件被加工表面上,作高速旋转运动。利用该技术可以达到Ra0.008μm的表面粗糙度,是各种抛光方法中最高的。光学镜片模具常采用这种方法。 很显然本公司出售的麻轮用于此类型的抛光,主要用于不锈钢的中抛。 2 化学抛光化学抛光是让材料在化学介质中表面微观凸出的部分较凹部分优先溶解,从而得到平滑面。这种方法的主要优点是不需复杂设备,可以抛光形状复杂的工件,可以同时抛光很多工件,效率高。化学抛光的核心问题是抛光液的配制。化学抛光得到的表面粗糙度一般为数10μm。 3 电解抛光电解抛光基本原理与化学抛光相同,即靠选择性的溶解材料表面微小凸出部分,使表面光滑。与化学抛光相比,可以消除阴极反应的影响,效果较好。电化学抛光过程分为两步:(1)宏观整平溶解产物向电解液中扩散,材料表面几何粗糙下降,Ra>1μm。(2)微光平整阳极极化,表面光亮度提高,Ra<1μm。 4 超声波抛光将工件放入磨料悬浮液中并一起置于超声波场中,依靠超声波的振荡作用,使磨料在工件表面磨削抛光。超声波加工宏观力小,不会引起工件变形,但工装制作和安装较困难。超声波加工可以与化学或电化学方法结合。在溶液腐蚀、电解的基础上,再施加超声波振动搅拌溶液,使工件表面溶解产物脱离,表面附近的腐蚀或电解质均匀;超声波在液体中的空化作用还能够抑制腐蚀过程,利于表面光亮化。 5 流体抛光流体抛光是依靠高速流动的液体及其携带的磨粒冲刷工件表面达到抛光的目的。常用方法有:磨料喷射加工、液体喷射加工、流体动力研磨等。流体动力研磨是由液压驱动,使携带磨粒的液体介质高速往复流过工件表面。介质主要采用在较低压力下流过性好的特殊化合物(聚合物状物质)并掺上磨料制成,磨料可采用碳化硅粉末。 6 磁研磨抛光磁研磨抛光是利用磁性磨料在磁场作用下形成磨料刷,对工件磨削加工。这种方法加工效率高,质量好,加工条件容易控制,工作条件好。采用合适的磨料,表面粗糙度可以达到Ra0.1μm。
抛光工艺流程及技巧
模具抛光的工艺流程及技巧 抛光在模具制作过程中是很重要的一道工序,随着塑料制品的日溢广泛应用,对塑料制品的外观品质要求也越来越高,所以塑料模具型腔的表面抛光质量也要相应提高,特别是镜面和高光高亮表面的模具对模具表面粗糙度要求更高,因而对抛光的要求也更高。抛光不仅增加工件的美观,而且能够改善材料表面的耐腐蚀性、耐磨性,还可以方便于后续的注塑加工,如使塑料制品易于脱模,减少生产注塑周期等。目前常用的抛光方法有以下几种: ㈠机械抛光 机械抛光是靠切削、材料表面塑性变形去掉被抛光后的凸部而得到平滑面的抛光方法,一般使用油石条、羊毛轮、砂纸等,以手工操作为主,特殊零件如回转体表面,可使用转台等辅助工具,表面质量要求高的可采用超精研抛的方法。超精研抛是采用特制的磨具,在含有磨料的研抛液中,紧压在工件
被加工表面上,作高速旋转运动。利用该技术可以达到Ra0.008μm的表面粗糙度,是各种抛光方法中最高的。光学镜片模具常采用这种方法。 ⑴机械抛光基本程序 要想获得高质量的抛光效果,最重要的是要具备有高质量的油石、砂纸和钻石研磨膏等抛光工具和辅助品。而抛光程序的选择取决于前期加工后的表面状况,如机械加工、电火花加工,磨加工等等。机械抛光的一般过程如下: ①粗抛经铣、电火花、磨等工艺后的表面可以选择转速在35 000—40 000 rpm的旋转表面抛光机或超声波研磨机进行抛光。常用的方法有利用直径Φ3mm、WA # 400的轮子去除白色电火花层。然后是手工油石研磨,条状油石加煤油作为润滑剂或冷却剂。一般的使用顺序为#180 ~ #240 ~ #320 ~ #400 ~ #600 ~ #800 ~ #1000。油石抛光方法,这个作业是最重要的高难度作业,根据加工品的不同规格,分别约70度的角位均衡的进行交叉研磨。最理想
常用的抛光加工方法比较
常用的抛光加工方法比较 一、常用的抛光法 古典拋光法是一种传统的玻璃冷加工方法,抛光机是采用摩擦轮传动,主轴转速较低,用平面摆动三角架施压,压力靠负荷重量调节。在工作时,负荷的压力始终是铅直向下的,加工平面时上下盘之间的垂直压力是稳定的。而在加工球面时摆动位置不同压力在球心方向的分量也不同,这样就造成上下盘的抛光压力随时变化,增加了球面表面形状不稳定性。拋光膜用松香柏油或毛毡等材料制作,由于抛光膜比较柔软,加工后的表面粗糙度小、表面缺陷小,可以加工较高精度等级的零件。在古典拋光过程中,抛光膜的表面的形状容易变化,需要随时进行修整,这就要求作业人员有较高操作技能,必须经过长期的培训才能掌握,而且生产效率低。在少量和小批量加工中,它有很大的优点,对于抛光机的精度要求低,抛光模的代用率较高,设备、工装夹具的投入费用小。 目前中等精度以下大批量生产的光学零件普遍都采用高速拋光的方法进行加工,高速拋光是以高主轴转速、大压力来提高拋光的效率。高速拋光机所使用的设备以准球心的方法设计的(另外还有一些是假准球心式拋光机,又有用平摆式拋光机用气压增加压力的方法充当高速拋光机),所谓准球心,是在拋光过程中负荷的压力始终指向被加工球面的球心位置。这种设计最大的优点就是,压力从始至终都是在拋光膜和工件接触面的正面施加的,正向压力的大小是不变的,这种方法加工的球面面形比较稳定。准球心抛光法对设备精度要求较高,抛光模必须是专用的,很少有代用的情况,设备、工装夹具的投入较大,只适合批量生产。由于抛光膜材料比较硬、耐磨性好,拋光膜修整的频率小,对作业员的技术要求较低,通过简单培训的新工人就可以上岗。 在各种文献中还常常提到范成法高速拋光机,这种拋光机的设计就象铣磨机一样,工件装在主轴上,拋光膜好象磨轮一样在辅轴上高速旋转对工件进行拋光,两条轴都不做摆动。这种拋光机的设计构思是非常好的,但是它对制造的精度要求非常高,由于受到成本的制约,目前还不能广泛的使用这种拋光机。首先说辅轴与主轴的对准精度,只要有微小的误差,加工出来的表面就不是球面了,象散差就出现了。工件表面的中心点不是高就是低,就象瓜的脐一样。如果以辅轴作为定位基准,拋光膜磨损以后基准点就产生变化,所以以辅轴为定位基准不合适。再说主轴一侧,每个工件的厚度是有区别的,以主轴为定位基准也不合适。每一个工件都有边厚差存在,每一次装后表面的位置、方向都有所变化,这个误差用拋光是无法消除的,拋光后的表面可能是一半亮一半不亮。工件装夹后要一次从铣磨或从精磨开始一直加工拋光,这样才能保证工件表面的有效加工。但是在同一个工位上同时进行不同工序的
塑料模具的抛光处理工序(doc 8)
塑料模具的抛光处理工序(doc 8)
塑料模具的抛光处理 随着塑料制品日溢广泛的应用,如日化用品和饮料包装容器等,外观的需要往往要求塑料模具型腔的表面达到镜面抛光的程度。而生产光学镜片、镭射唱片等模具对表面粗糙度要求极高,因而对抛光性的要求也极高。抛光不仅增加工件的美观,而且能够改善材料表面的耐腐蚀性、耐磨性,还可以使模具拥有其它优点,如使塑料制品易于脱模,减少生产注塑周期等。因而抛光在塑料模具制作过程中是很重要的一道工序。 目前常用的抛光方法有以下几种: 1.1 机械抛光 机械抛光是*切削、材料表面塑性变形去掉被抛光后的凸部而得到平滑面的抛光方法,一般使用油石条、羊毛轮、砂纸等,以手工操作为主,特殊零件如回转体表面,可使用转台等辅助工具,表面质量要求高的可采用超精研抛的方法。超精研抛是采用特制的磨具,在含有磨料的研抛液中,紧压在工件被加工表面上,作高速旋转运动。利用该技术可以达到Ra0.008μm的表面粗糙度,是各种抛光方法中最高的。光学镜片模具常采用这种方法。
拌溶液,使工件表面溶解产物脱离,表面附近的腐蚀或电解质均匀;超声波在液体中的空化作用还能够抑制腐蚀过程,利于表面光亮化 1.5 流体抛光 流体抛光是依*高速流动的液体及其携带的磨粒冲刷工件表面达到抛光的目的。常用方法有:磨料喷射加工、液体喷射加工、流体动力研磨等。流体动力研磨是由液压驱动,使携带磨粒的液体介质高速往复流过工件表面。介质主要采用在较低压力下流过性好的特殊化合物(聚合物状物质)并掺上磨料制成,磨料可采用碳化硅粉末。 1.6 磁研磨抛光 磁研磨抛光是利用磁性磨料在磁场作用下形成磨料刷,对工件磨削加工。这种方法加工效率高,质量好,加工条件容易控制,工作条件好。采用合适的磨料,表面粗糙度可以达到Ra0.1μm。 在塑料模具加工中所说的抛光与其他行业中所要求的表面抛光有很大的不同,严格来说,模具的抛光应该称为镜面加工。它不仅对抛光本身有很高的要求并且对表面平整度、光滑度以及几何精确度也有很高的标准。表面抛光一般只要求获得光亮的表面即可。镜面加工的标准分为四级:AO=Ra0.008μm,A1=Ra0.016μm,A3=
塑胶模具抛光常用方法
塑胶模具抛光及其常用方法 模具抛光就是利用适当的抛光器具(如砂纸、抛光膏、油石、抛光机或其他机械抛光器具)对已加工了的模具型腔表面进行微量的再次加工,使该表面达到要求的尺寸、表面粗糙度要求。一般是最后一道工序(再有的话就是研磨)。 模具抛光有两个目的;一个是增加模具的光洁度,使模具出的产品的表面光洁、漂亮、美观,另一个是可以模具很容易脱模,使塑料不被粘在模具上而脱不下来。模具抛光一般是使用油石,砂纸,抛光膏等,对模具的型腔表面进行打磨,使模具的工作表面能够光亮如镜的过程,称之为模具打磨。 那么,我们在对模具进行抛光的时候,要怎么去作业才能使抛光效果最好呢? 模具抛光不要一开始就使用最细的油石,砂纸,研磨抛光膏,那样是不能把粗的纹路抛掉的。那样打磨出来的活的表面看起来很光亮,但是侧面一照,粗的纹路就显现出来了。因此,要先从粗的油石,砂纸或者研磨抛光膏打磨,然后再换比较细的油石,砂纸或研磨抛光膏进行打磨,最后再用最细的研磨抛光膏进行抛光。这样看起来好像比较麻烦,工序多。实际上并不慢,一道接一道的工序,将前面粗的加工纹路打磨掉,再进行下面的工序,不会返工,一次走下来就可以使模具的光洁度达到要求。 下面来介绍几种抛光方法: 1、磁研磨抛光 是利用磁性磨料在磁场作用下形成磨料刷,对工件磨削加工。这种方法加工效率高,质量好,加工条件容易控制,工作条件好。采用合适的磨料,表面粗糙度可以达到Ra0.1μm。
2、机械抛光基本方法 在塑料模具加工中所说的抛光与其他行业中所要求的表面抛光有很大的不同,严格来说,模具的抛光应该称为镜面加工。它不仅对抛光本身有很高的要求并且对表面平整度、光滑度以及几何精确度也有很高的标准。表面抛光一般只要求获得光亮的表面即可。镜面加工的标准分为四级:AO=Ra0.008μm,A1=Ra0.016μm,A3=Ra0.032μm, A4=Ra0.063μm,由于电解抛光、流体抛光等方法很难精确控制零件的几何精确度,而化学抛光、超声波抛光、磁研磨抛光等方法的表面质量又达不到要求,所以精密模具的镜面加工还是以机械抛光为主。 2.1机械抛光基本程序 要想获得高质量的抛光效果,最重要的是要具备有高质量的油石、砂纸和钻石研磨膏等抛光工具和辅助品。而抛光程序的选择取决于前期加工后的表面状况,如机械加工、电火花加工,磨加工等等。机械抛光的一般过程如下: (1)粗抛 经铣、电火花、磨等工艺后的表面可以选择转速在35 000—40 000 rpm的旋转表面抛光机或超声波研磨机进行抛光。常用的方法有利用直径Φ3mm、WA # 400的轮子去除白色电火花层。然后是手工油石研磨,条状油石加煤油作为润滑剂或冷却剂。一般的使用顺序为#180 ~ #240 ~ #320 ~ #400 ~ #600 ~ #800 ~ #1000。许多模具制造商为了节约时间而选择从#400开始。 (2)半精抛 半精抛主要使用砂纸和煤油。砂纸的号数依次为:#400 ~ #600 ~ #800 ~ #1000 ~ #1200 ~ #1500。实际上#1500砂纸只用适于淬硬的模具钢(52HRC以上),而不适用于预硬钢,因为这样可能会导致预硬钢件表面烧伤。 (3)精抛 精抛主要使用钻石研磨膏。若用抛光布轮混合钻石研磨粉或
玉石常见的3种抛光方法
玉石常见的3种抛光方法 摘要:抛光粉的配法:钻石抛光粉一般是用食用油或水调配成膏状即抛光。其他抛光膏一般绿色的为氧化铬,橙红色的为氧化铈,震动抛光机一般适合大批量的抛光,而且一般是菱角不是很多的产品拿去抛光。一般抛光时间比较长。一般要一天一宿甚至更长时间,圆盘抛光机通常用抗压力较强的硬质材料如金属、塑料、木头等制作抛光盘。常将以金属制作的抛光盘称为硬盘,木头、塑料甚至沥青制作的抛光盘称中硬盘。玉石加工因多以弧面或曲面多见,所以更常用软质抛光工具。 奇石“是一种具有观赏价值的天然石质艺术品。”奇石的美,美在天然神奇,虽然打磨奇石破坏了奇石的自然属性,有违“求原貌”的赏石观。但不可否认,必要的打磨抛光提高了观赏性,增加了艺术性。这里讨论的是经过简单的处理使石头更具观赏性,与刻意的造假,人为的加工不是一个意思。 1、粗加工:一般使用吊磨机,算是艺术的创作。粗坯加工分局部加工和整体加工。工具精度不高,加工技术也很有限。局部加工是对原石残缺面或水洗度不够的“死面”进行粗坏打磨。一般是把残破的尖锐部分磨圆,或把“死面”的一层粗糙表皮磨掉。整体加工是一些经敲击取下的山石石块或毫无水水冲度的块状原石,则全部将石表磨掉,再磨制
成需要的形状。 2、精磨:用1000#-1200#进口磨片研磨,将粗坯上的原磨痕完全清除掉,有经验的工匠们大都采用“注水磨”的方法,可以很好的掌握磨的分寸。 3、抛光:用软磨具加抛光膏进行机械抛光,抛光后可达镜而效果。 奇石的打磨抛光是“去璞,是为美女洗去脸上的泥污,打磨出的纹理和色彩并没有改变,所不同的就是没有了污垢,少了粗糙,隐含的天然纹理更加灿烂夺目”。 抛光有很多种方法,有带砂轮的钻头,这是粗打磨,再细点砂布,砂布又分型号,粗细,基本上用人手不能感觉到沙粒的,工匠可以将砂布剪下来,粘贴在钻头上,进行打磨,当然在打磨时候是要加水的,这样更滑些.古法对玉石的加工和抛光是先用皮,后用丝绸。现在都用现代化的工具了。先把玉雕刻成你要的形状,然后再撂进震动抛光机里用钻石粉进行千次打磨。常见的3种抛光方法: 1、使用吊磨机抛光。 2、使用圆盘抛光机抛光。 3、震动抛光机一般适合大批量的抛光。
塑料模具抛光方式有些塑料模具常见的六大抛光方法
塑料模具抛光方式有些塑料模具常见的六大抛光方法 抛光在塑料模具制作过程中是很重要的一道工序,那么,塑料模具中,常见的抛光方式有哪些大家知道吗?下面,为大家分享塑料模具常见的抛光方法,希望对大家有所帮助! 化学抛光 化学抛光是让材料在化学介质中表面微观凸出的部分较凹部分优先溶解,从而得到平滑面。这种方法的主要优点是不需复杂设备,可以抛光形状复杂的工件,可以同时抛光很多工件,效率高。 化学抛光的核心问题是抛光液的配制。化学抛光得到的表面粗糙度一般为数10μm。 电解抛光 电解抛光基本与化学抛光相同,即靠选择性地溶解材料表面微小凸出部分,使表面光滑。与化学抛光相比,可以消除阴极反应的影响,效果较好。电化学抛光过程分为两步: (1)宏观平整。溶解产物向电解液中扩散,材料表面几何粗糙度下降,Ra>1μm; (2)微光平整。阳极极化,表面光亮度提高,Ra<1μm。 流体抛光 流体抛光,是依靠高速流动的液体及其携带的磨粒冲刷工件表面达到抛光的目的。常用方法有:磨料喷射加工、液体喷射加工、流体动力研磨等。
流体动力研磨是由液压驱动,使携带磨粒的液体介质高速往复流过工件表面。介质主要采用在较低压力下流过性好的特殊化合物(聚合物状物质)并掺上磨料制成,磨料可采用碳化硅粉末。 机械抛光 机械抛光是靠切削、材料表面塑性变形去掉被抛光后的凸部而得到平滑面的抛光方法,一般使用油石条、羊毛轮、砂纸等,以手工操作为主,特殊零件如回转体表面,可使用转台等辅助工具,表面质量要求高的可采用超精研抛的方法。 超精研抛是采用特制的磨具,在含有磨料的研抛液中,紧压在工件被加工表面上,作高速旋转运动。利用该技术可以达到Ra0.008μm的表面粗糙度,是各种抛光方法中最高的。光学镜片模具常采用这种方法。 磁研磨抛光 磁研磨抛光,是利用磁性磨料在磁场作用下形成磨料刷,对工件磨削加工。这种方法加工效率高,质量好,加工条件容易控制,工作条件好。采用合适的磨料,表面粗糙度可以达到Ra0.1μm。 超声波抛光 将工件放入磨料悬浮液中,并一起置于超声波场中,依靠超声波的振动作用,使磨料在工件表面磨削抛光。超声波加工宏观力小,不会引起工件变形,但工装制作和安装较困难。 超声波加工可以与化学或电化学方法结合。在溶液腐蚀、电解的基础上,再施加超声波振动搅拌溶液,使工件表面溶解产物脱离,
抛光方法
抛光方法 目前常用的抛光方法有以下几种: 1.1机械抛光 机械抛光是靠切削、材料表面塑性变形去掉被抛光后的凸部而得到平滑面的抛光方法,一般使用油石条、羊毛轮、砂纸等,以手工操作为主,特殊零件如回转体表面,可使用转台等辅助工具,表面质量要求高的可采用超精研抛的方法。超精研抛是采用特制的磨具,在含有磨料的研抛液中,紧压在工件被加工表面上,作高速旋转运动。利用该技术可以达到Ra0.008μm的表面粗糙度,是各种抛光方法中最高的。光学镜片模具常采用这种方法。1.2化学抛光 化学抛光是让材料在化学介质中表面微观凸出的部分较凹部分优先溶解,从而得到平滑面。这种方法的主要优点是不需复杂设备,可以抛光形状复杂的工件,可以同时抛光很多工件,效率高。化学抛光的核心问题是抛光液的配制。化学抛光得到的表面粗糙度一般为数10μm。 1.3电解抛光 电解抛光基本原理与化学抛光相同,即靠选择性的溶解材料表面微小凸出部分,使表面光滑。与化学抛光相比,可以消除阴极反应的影响,效果较好。电化学抛光过程分为两步:(1)宏观整平溶解产物向电解液中扩散,材料表面几何粗糙下降,Ra>1μm。 (2)微光平整阳极极化,表面光亮度提高,Ra<1μm。 1.4超声波抛光 将工件放入磨料悬浮液中并一起置于超声波场中,依靠超声波的振荡作用,使磨料在工件表面磨削抛光。超声波加工宏观力小,不会引起工件变形,但工装制作和安装较困难。超声波加工可以与化学或电化学方法结合。在溶液腐蚀、电解的基础上,再施加超声波振动搅拌溶液,使工件表面溶解产物脱离,表面附近的腐蚀或电解质均匀;超声波在液体中的空化作用还能够抑制腐蚀过程,利于表面光亮化。 1.5流体抛光 流体抛光是依靠高速流动的液体及其携带的磨粒冲刷工件表面达到抛光的目的。常用方法有:磨料喷射加工、液体喷射加工、流体动力研磨等。流体动力研磨是由液压驱动,使携带磨粒的液体介质高速往复流过工件表面。介质主要采用在较低压力下流过性好的特殊化合物(聚合物状物质)并掺上磨料制成,磨料可采用碳化硅粉末。 1.6磁研磨抛光 磁研磨抛光是利用磁性磨料在磁场作用下形成磨料刷,对工件磨削加工。这种方法加工效率高,质量好,加工条件容易控制,工作条件好。采用合适的磨料,表面粗糙度可以达到Ra0.1μm。 在塑料模具加工中所说的抛光与其他行业中所要求的表面抛光有很大的不同,严格来说,模具的抛光应该称为镜面加工。它不仅对抛光本身有很高的要求并且对表面平整度、光滑度以及几何精确度也有很高的标准。表面抛光一般只要求获得光亮的表面即可。镜面加工的标准分为四级:AO=Ra0.008μm,A1=Ra0.016μm,A3=Ra0.032μm,A4=Ra0.063μm,由于电解抛光、流体抛光等方法很难精确控制零件的几何精确度,而化学抛光、超声波抛光、磁研磨抛光等方法的表面质量又达不到要求,所以精密模具的镜面加工还是以机械抛光为主。
模具抛光方法
模具抛光方法 磁研磨抛光是利用磁性磨料在磁场作用下形成磨料刷,对工件磨削加工。这种方法加工效率高,质量好,加工条件容易控制,工作条件好。采用合适的磨料,表面粗糙度可以达到Ra0.1μm。 2 机械抛光基本方法 在塑料模具加工中所说的抛光与其他行业中所要求的表面抛光有很大的不同,严格来说,模具的抛光应该称为镜面加工。它不仅对抛光本身有很高的要求并且对表面平整度、光滑度以及几何精确度也有很高的标准。表面抛光一般只要求获得光亮的表面即可。镜面加工的标准分为四级:AO=Ra0.008μm,A1=Ra0.016μm, A3=Ra0.032μm,A4=Ra0.063μm,由于电解抛光、流体抛光等方法很难精确控制零件的几何精确度,而化学抛光、超声波抛光、磁研磨抛光等方法的表面质量又达不到要求,所以精密模具的镜面加工还是以机械抛光为主。 2.1 机械抛光基本程序 要想获得高质量的抛光效果,最重要的是要具备有高质量的油石、砂纸和钻石研磨膏等抛光工具和辅助品。而抛光程序的选择取决于前期加工后的表面状况,如机械加工、电火花加工,磨加工等等。机械抛光的一般过程如下: (1)粗抛经铣、电火花、磨等工艺后的表面可以选择转速在35 000—40 000 rpm的旋转表面抛光机或超声波研磨机进行抛光。常用的方法有利用直径Φ3mm、WA # 400的轮子去除白色电火花层。然后是手工油石研磨,条状油石加煤油作为润滑剂或冷却剂。一般的使用顺序为#180 ~ #240 ~ #320 ~ #400 ~ #600 ~ #800 ~ #1000。许多模具制造商为了节约时间而选择从#400开始。 (2)半精抛半精抛主要使用砂纸和煤油。砂纸的号数依次为:#400 ~ #600 ~ #800 ~ #1000
目前常用的超光滑表面加工方法
目前常用的超光滑表面加工方法,是由传统的研磨抛光加工技术改进而来的,如浴法抛光、浮法抛光等,此类方法材料去除率低,也能够达到亚纳米量级的表面粗糙度,但很难避免机械接触式抛光对工件表面带来的亚表面损伤和加工变质层。各种基于新原理的抛光方法逐渐被提出,如离子束抛光、等离子体辅助化学抛光、液体喷射抛光、磁流变抛光、化学机械抛光和弹性发射加工等。其中日本大阪大学学者发明的弹性发射加工方法利用工件材料与磨料之间发生固相反应实现原子级材料去除,被认为是获得最高表面质量的加工方法,可以达到RMS 0.1nm 的表面粗糙度,但其加工效率很低,并且设备复杂,维护成本高。纳米颗粒射流抛光是借鉴了弹性发射加工的去除原理的一种超光滑表面加工方法,结合数控技术可以实现光学零件纳米级粗糙度、无表面损伤的精确抛光,但仍然存在抛光效率不高的问题。 光学元件的加工一般都需要三大基本步骤:铣磨、精磨和抛光,其中铣磨和抛光是最主要的两道工序。抛光的目的是在去除表面破坏层的同时精修面形。现行的抛光理论认为抛光是三种作用的结果:磨料与工件之间的机械磨削、抛光液的化学作用和工件表面的热流动。这些理论对于超光滑表面加工已经不完全适用,基于新原理的超光滑表面加工方法不断涌现。 液体喷射抛光技术:液体喷射抛光技术(Fluid Jet Polishing, FJP)是近几年提出的用于加工脆性材料光学元件的新方法。液体喷射抛光技术系统如图1-4 a)所示,其思想源于磨料射流加工技术,高压泵加速混有磨料粒子的抛光液,利用磨料粒子对工件表面材料的冲击和剪切作用实现材料去除。该方法通过控制液体喷射的压力、方向及驻留时间实现对工件面形的定量修正。
模具的省模方法
注塑课模具教育训练课文 塑料模具的省模 各位今天我们就讲一讲塑料模具的省模。我们塑料模具制作完成,或修理塑料模具后,一项很重要的后续工作就是省模(省模:我们也叫做抛光)。为什么我们说很重要呢?因为某些一套模具、省模的好坏关系到模具的成败,省模不好会导致模具在生产过程中,模具产品脱模不顺利,顶穿,拉花,拉伤,粘前模等等一些问题,特别是透明塑料模具,成品镜面模具等等,抛光不成功就是这套模具不成功。 首先我们了解一下抛光的步骤:1下锉刀油石。2推砂纸,3镜面抛光。也可以用超声波,电动,电子,气动等等的、一些抛光工具下锉刀、油石,不需要过砂纸就可以镜面抛光。 接下来我们就来具体了解一下省模的方法: 1:下锉刀,我们先在下锉刀前,看看我们要省模的工件是用什么机械加工的,机械加工的表面精度怎样?一般的经验是:EDM加工后精度低我们就先下锉刀,再用油石轻轻的推顺,就可以用砂纸。EDM加工精度高的我们就可以直接下砂纸就可以了。CNC,铣床、车床加工件精度低的就用油石推顺,精度高的也可以直接用砂纸就可以了。接下来我们就了解一些省模过程中所用到的锉刀;省模我们一般用到的是合金锉刀,合金锉刀有粗、中、细之分(一般的合金锉刀都没有标号),我们很好分别,用肉眼就可以分辨出来。它们有各种型状:扁平的,我们一般用
来省模平面,又薄又细的锉刀一般用在省模骨位,或一些大锉刀下不了的地方;三角型的,一般用在省模有角的地方;圆型的,一般用在省模圆型,椭圆型等等地方;刀型的,一般用在省模方型的底部各种角落; 还有像弯型,钩型,半圆半扁型,圆圈型等等,都是要在省模的过程中根据各种需要,而用到的合金锉刀,这里就不一一表述了,只要我们在省模的过程中会灵活运用各种锉刀,才能使省模工作变得快而轻松。省模下锉刀的一个原则就是:先粗后细。一般而言,因为开始省模用细锉刀,粗糙的地方省不下去,省模的速度就会变得很慢,浪费工时。 2:推砂纸:砂纸的标号一般分:120〞240〞400""600" 800〞1000"1200"1500" 2000 "2500".它的标号越大砂纸就越细。我们可以将砂纸用剪刀剪成一条或小方块型的,用木头或竹片压住来推动砂纸,省模骨位的时候用薄木片或薄竹片压来压住砂纸。推砂纸的一个最重要的原则就是:推一个同样型号的砂纸,一定要推到加工件看不见条纹、砂眼,才可以推下一种标号更高的砂纸,否则下一种砂纸就很难推下去。 了解这个原则,我们就可以对任何模具都又快又好的抛光加工。在一般的大模具例如:电视模具,冰箱模具等等,后模的骨位又多又深,这个时候对我们省模带来很大的麻烦,像这样的模具,我们应该在模具设计的时候就应该想到模具抛光的问题,例如是不是在条件允许的前提下,我们可以在有骨位的地方用镶接方法,这样就在省模的加工的时候,我们就变的很容易了。 3镜面抛光。镜面抛光要根据:模具的所注塑产品塑料差别,塑料产品的要求等等来抛光。特别是透明塑料成品,它们一般是前后模都要抛光
抛光机的选择和常用的磨料磨具抛光方法
抛光机的选择和常用的磨料磨具抛光方法 抛光机关于许多的出产公司是十分的重要的,有十分多的工序具有了抛光机之后就会变得愈加的简略,所以抛光机的挑选天然就成为了一项十分重要的作业,挑选一款好的抛光机不管是关于公司仍是小我都是至关重要的。所以在挑选抛光机的时分仍是应该十分的稳重,在知道所有的产物的常识的基础上,能够找到最棒的抛光机然后进步出产的功率关于公司的开展也是十分的重要的,挑选抛光机其实仍是有必定的窍门的,首要就是看一下出产厂家的资质是不是够好,由于大厂家的产物在质量上才会有充沛的保证。 抛光机的操作能否简略也是一项十分重要的查核的方针,若是抛光机的操作太过于杂乱的话就会招致公司的职工不能在最短的时间内把握到新的机器的使用方法,也是十分耗费本钱的一项作业,所以有的时分简略的操作,也是十分吸引人的一个优势,所以易操作的抛光机仍是十分的受欢迎的,抛光机能够替代大家做十分多的作业,让双手的作业能够变得愈加的轻松。 挑选抛光机,大厂家固然是十分的重要,操作简略也是十分的有吸引力,可是最重要的仍是出来的作用必定要好,不然所有的一切都是没有任何的含义的,所以不管是怎么的进行挑选,归根到底就是就能够必定要切切实实的在出产线上有好的体现,能够给公司带来看得见的经济效益,这样就能够到达一个抛光机的真实的意图。怎么挑选抛光机关于许多人来说都是十分的重要的,所以把握一些实践的挑选抛光机的窍门,就能够更大几率的成功挑选到最实惠并且功能也是最棒的抛光机了。在磨料磨具的抛光中,有很多种方法是可以采用的,东莞维益机械厂,专门至力于抛光机和抛光技术方法的研究工作,公司10多年来,一直以客户的需要为出发点,以提高抛光技术和方法为要本,不断开拓创新,东莞维益机械厂我们总结一些抛光方法: 一、化学抛光:化学抛光是让材料在化学介质中表面微观凸出的部分较凹部分优先溶解,从而得到平滑面。这种方法的主要优点是不需复杂设备,可以抛光形状复杂的工件,可以同时抛光很多工件,效率高。化学抛光的核心问题是抛光液的配制。 二、机械抛光:机械抛光是靠抛光机设备来切削材料表面塑性变形去掉被抛光后的凸部而得到平滑面的抛光方法,一般使用油石条、羊毛轮、砂纸,砂带,尼龙轮等,以手工操作抛光机为主,特殊零件如回转体表面,可使用转台等辅助工具,表面质量要求高的可采用超精研抛的方法。超精研抛是采用磨料特制的磨具,在含有磨料的研抛液中,紧压在工件被加工表面上,作高速旋转运动。是各种抛光方法中最高的。光学镜片模具常采用这种方法。 三、流体抛光:流体抛光是依靠高速流动的液体及其携带的磨粒冲刷工件表面达到抛光的目的。常用方法有:磨料的金刚砂喷射加工、液体喷射加工、流体动力研磨等。流体动力研磨是由液压驱动,使携带磨粒的液体介质高速往复流过工件表面。介质主要采用在较低压力下流过性好的特殊化合物并掺上磨料制成,磨料可采用磨料磨具的碳化硅粉末。 四、电解抛光:电解抛光基本原理与化学抛光相同,即靠选择性的溶解材料表面微小凸出部分,使表面光滑。与化学抛光相比,可以消除阴极反应的影响,效果较好。电化学抛光过程分宏观整平,微观整平。 五、超声波抛光:将工件放入磨料悬浮液中并一起置于超声波场中,依靠超声波的振荡作用,使磨料在工件表面磨削抛光。超声波加工宏观力小,不会引起工件变形,但工装制作和安装较困难。超声波加工可以与化学或电化学方法结合。在溶液腐蚀、电解的基础上,再施加超声波振动搅拌溶液,使工件表面溶解产物脱离,表面附近的腐蚀或电解质均匀;超声波在液体中的空化作用还能够抑制腐蚀过程,利于表面光亮化。
塑料模具抛光过程【详解】
塑料模具抛光过程 内容来源网络,由“深圳机械展(11万㎡,1100多家展商,超10万观众)”收集整理!更多cnc加工中心、车铣磨钻床、线切割、数控刀具工具、工业机器人、非标自动化、数字化无人工厂、精密测量、数控系统、3D打印、激光切割、钣金冲压折弯、精密零件加工等展示,就在深圳机械展 塑料模具抛光基本程序 要想获得高质量的抛光效果,最重要的是要具备有高质量的油石、砂纸和钻石研磨膏等抛光工具和辅助品。塑料模具抛光的一般过程如下: 1、精抛 精抛主要使用钻石研磨膏。若用抛光布轮混合钻石研磨粉或研磨膏进行研磨的话,则通常的研磨顺序是9μm(#1800)~6μm(#3000)~3μm(#8000)。9μm的钻石研磨膏和抛光布轮可用来去除#1200和#1500号砂纸留下的发状磨痕。接着用粘毡和钻石研磨膏进行抛光,顺序为1μm(#14000)~1/2μm(#60000)~1/4μm(#100000)。精度要求在1μm以上(包括1μm)的抛光工艺在模具加工车间中一个清洁的抛光室内即可进行。若进行更加精密的抛光则必需一个绝对洁净的空间。灰尘、烟雾,头皮屑和口水沫都有可能报废数个小时工作后得到的高精密抛光表面。
2、粗抛 经铣、电火花、磨等工艺后的表面可以选择转速在35 000—40 000 rpm的旋转表面抛光机或超声波研磨机进行抛光。常用的方法有利用直径Φ3mm、WA#400的轮子去除白色电火花层。然后是手工油石研磨,条状油石加煤油作为润滑剂或冷却剂。一般的使用顺序为#180~#240~#320~#400~#600~#800~#1000。许多模具制造商为了节约时间而选择从#400开始。 3、半精抛 半精抛主要使用砂纸和煤油。砂纸的号数依次为: #400~#600~#800~#1000~#1200~#1500。实际上#1500砂纸只用适于淬硬的模具钢(52HRC以上),而不适用于预硬钢,因为这样可能会导致预硬钢件表面烧伤。 ⒋精抛 用研磨膏进行精抛,8000,10000就达到镜面了。 内容来源网络,由“深圳机械展(11万㎡,1100多家展商,超10万观众)”收集整理!更多cnc加工中心、车铣磨钻床、线切割、数控刀具工具、工业机器人、非标自动化、数
目前常用的抛光方法
目前常用的抛光方法 目前常用的抛光方法有以下几种: 1.1 机械抛光 机械抛光是靠切削、材料表面塑性变形去掉被抛光后的凸部而得到平滑面的抛光方法,一般使用油石条、羊毛轮、砂纸等,以手工操作为主,特殊零件如回转体表面,可使用转台等辅助工具,表面质量要求高的可采用超精研抛的方法。超精研抛是采用特制的磨具,在含有磨料的研抛液中,紧压在工件被加工表面上,作高速旋转运动。利用该技术可以达到Ra0.008 μ m 的表面粗糙度,是各种抛光方法中最高的。光学镜片模具常采用这种方法。 1.2 化学抛光 化学抛光是让材料在化学介质中表面微观凸出的部分较凹部分优先溶解,从而得到平滑面。这种方法的主要优点是不需复杂设备,可以抛光形状复杂的工件,可以同时抛光很多工件,效率高。化学抛光的核心问题是抛光液的配制。化学抛光得到的表面粗糙度一般为数10 μ m 。 1.3 电解抛光 电解抛光基本原理与化学抛光相同,即靠选择性的溶解材料表面微小凸出部分,使表面光滑。与化学抛光相比,可以消除阴极反应的影响,效果较好。电化学抛光过程分为两步: (1 )宏观整平溶解产物向电解液中扩散,材料表面几何粗糙下降,Ra > 1 μ m 。 (2 )微光平整阳极极化,表面光亮度提高,Ra < 1 μ m 。 1.4 超声波抛光 将工件放入磨料悬浮液中并一起置于超声波场中,依靠超声波的振荡作用,使磨料在工件表面磨削抛光。超声波加工宏观力小,不会引起工件变形,但工装制作和安装较困难。超声波加工可以与化学或电化学方法结合。在溶液腐蚀、电解的基础上,再施加超声波振动搅拌溶液,使工件表面溶解产物脱离,表面附近的腐蚀或电解质均匀;超声波在液体中的空化作用还能够抑制腐蚀过程,利于表面光亮化。 1.5 流体抛光 流体抛光是依靠高速流动的液体及其携带的磨粒冲刷工件表面达到抛光的目的。常用方法有:磨料喷射加工、液体喷射加工、流体动力研磨等。流体动力研磨是由液压驱动,使携带磨粒的液体介质高速往复流过工件表面。介质主要采用在较低压力下流过性好的特殊化合物(聚合物状物质)并掺上磨料制成,磨料可采用碳化硅粉末。 1.6 磁研磨抛光 磁研磨抛光是利用磁性磨料在磁场作用下形成磨料刷,对工件磨削加工。这种方法加工效率高,
塑料模具的抛光处理工序
塑料模具的抛光处理 随着塑料制品日溢广泛的应用,如日化用品和饮料包装容器等,外观的需要往往要求塑料模具型腔的表面达到镜面抛光的程度。而生产光学镜片、镭射唱片等模具对表面粗糙度要求极高,因而对抛光性的要求也极高。抛光不仅增加工件的美观,而且能够改善材料表面的耐腐蚀性、耐磨性,还能够使模具拥有其它优点,如使塑料制品易于脱模,减少生产注塑周期等。因而抛光在塑料模具制作过程中是专门重要的一道工序。 目前常用的抛光方法有以下几种: 1.1 机械抛光 机械抛光是*切削、材料表面塑性变形去掉被抛光后的凸部而得到平滑面的抛光方法,一般使用油石条、羊毛轮、砂纸等,以手工操作为主,专门零件如回转体表面,可使用转台等辅助工具,表面
质量 要求高的可采纳超精研抛的方法。超精研抛是采纳特制的磨具,在含有磨料的研抛液中,紧压在工件被加工表面上,作高速旋转运动。利用该技术能够达到Ra0.008μm的表面粗糙度,是各种抛光方法中最高的。光学镜片模具常采纳这种方法。 1.2 化学抛光 化学抛光是让材料在化学介质中表面微观凸出的部分较凹部分优先溶解,从而得到平滑面。这种方法的要紧优点是不需复杂设备,能够抛光形状复杂的工件,能够同时抛光专门多工件,效率高。化学抛光的核心问题是抛光液的配制。化学抛光得到的表面粗糙度一般为数10μm。 1.3 电解抛光 电解抛光差不多原理与化学抛光相同,即*选择性的溶解材料表面微小凸出部分,使表面光滑。与化学抛光相比,能够消除阴极反应的阻碍,效果较好。电化学抛光过程分为两步:
(1)宏观整平溶解产物向电解液中扩散,材料表面几何粗糙下降,Ra>1μm。 (2)微光平坦阳极极化,表面光亮度提高,Ra<1μm。 1.4 超声波抛光 将工件放入磨料悬浮液中并一起置于超声波场中,依*超声波的振荡作用,使磨料在工件表面磨削抛光。超声波加工宏观力小,可不能引起工件变形,但工装制作和安装较困难。超声波加工能够与化学或电化学方法结合。在溶液腐蚀、电解的基础上,再施加超声波振动搅拌溶液,使工件表面溶解产物脱离,表面附近的腐蚀或电解质均匀;超声波在液体中的空化作用还能够抑制腐蚀过程,利于表面光亮化 1.5 流体抛光 流体抛光是依*高速流淌的液体及其携带的磨粒冲刷工件表面达到抛光的目的。常用方法有:磨料喷射加工、液体喷射加工、流体动力研磨等。流体动力研磨是由液压驱动,使携带磨粒的液体介质