塑胶不良分析
塑胶件常见缺陷不良分析及对策讲解
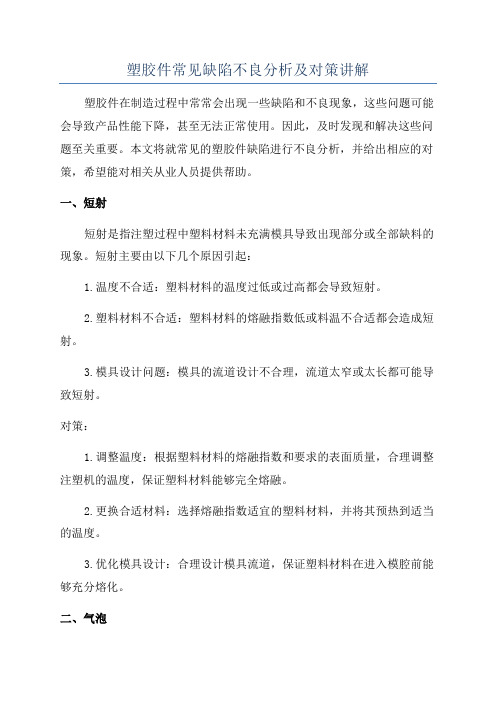
塑胶件常见缺陷不良分析及对策讲解塑胶件在制造过程中常常会出现一些缺陷和不良现象,这些问题可能会导致产品性能下降,甚至无法正常使用。
因此,及时发现和解决这些问题至关重要。
本文将就常见的塑胶件缺陷进行不良分析,并给出相应的对策,希望能对相关从业人员提供帮助。
一、短射短射是指注塑过程中塑料材料未充满模具导致出现部分或全部缺料的现象。
短射主要由以下几个原因引起:1.温度不合适:塑料材料的温度过低或过高都会导致短射。
2.塑料材料不合适:塑料材料的熔融指数低或料温不合适都会造成短射。
3.模具设计问题:模具的流道设计不合理,流道太窄或太长都可能导致短射。
对策:1.调整温度:根据塑料材料的熔融指数和要求的表面质量,合理调整注塑机的温度,保证塑料材料能够完全熔融。
2.更换合适材料:选择熔融指数适宜的塑料材料,并将其预热到适当的温度。
3.优化模具设计:合理设计模具流道,保证塑料材料在进入模腔前能够充分熔化。
二、气泡气泡是指塑胶件表面或内部出现的小气孔或气泡。
气泡可能导致产品外观不良或性能下降。
气泡的产生主要有以下几个原因:1.塑料材料中含有挥发性成分:一些塑料材料中含有挥发性成分,如果注塑温度过高,这些挥发性成分就会挥发出来形成气泡。
2.模具表面不洁净:如果模具表面不干净或有油污等杂质,气泡就会在塑料注入过程中被吸附在塑料中形成。
3.注塑机压力过高:注塑机压力过高会导致空气被压进模具中,形成气泡。
对策:1.调整注塑温度:根据塑料材料的特性,合理调整注塑温度。
温度过高易导致气泡产生,温度过低则容易短射。
2.模具清洁:保持模具表面干净,定期对模具进行清洗,去除杂质和油污。
3.控制注塑机压力:根据塑料材料的特性和模具的要求,合理控制注塑机的压力,避免空气进入模具。
三、热处理不当塑胶件经过热处理后,如果处理不当,可能导致产品性能下降或出现变形等问题。
常见的热处理问题有:1.温度不合适:热处理时,温度不合适会导致产品硬度不均匀或过硬。
塑胶成型不良分析
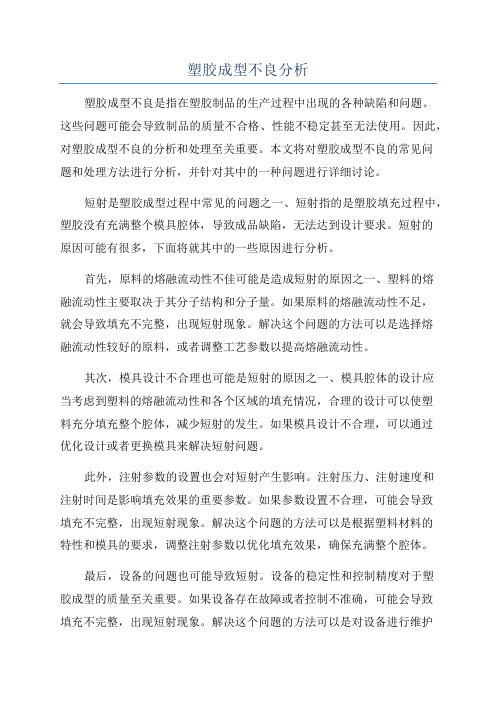
塑胶成型不良分析塑胶成型不良是指在塑胶制品的生产过程中出现的各种缺陷和问题。
这些问题可能会导致制品的质量不合格、性能不稳定甚至无法使用。
因此,对塑胶成型不良的分析和处理至关重要。
本文将对塑胶成型不良的常见问题和处理方法进行分析,并针对其中的一种问题进行详细讨论。
短射是塑胶成型过程中常见的问题之一、短射指的是塑胶填充过程中,塑胶没有充满整个模具腔体,导致成品缺陷,无法达到设计要求。
短射的原因可能有很多,下面将就其中的一些原因进行分析。
首先,原料的熔融流动性不佳可能是造成短射的原因之一、塑料的熔融流动性主要取决于其分子结构和分子量。
如果原料的熔融流动性不足,就会导致填充不完整,出现短射现象。
解决这个问题的方法可以是选择熔融流动性较好的原料,或者调整工艺参数以提高熔融流动性。
其次,模具设计不合理也可能是短射的原因之一、模具腔体的设计应当考虑到塑料的熔融流动性和各个区域的填充情况,合理的设计可以使塑料充分填充整个腔体,减少短射的发生。
如果模具设计不合理,可以通过优化设计或者更换模具来解决短射问题。
此外,注射参数的设置也会对短射产生影响。
注射压力、注射速度和注射时间是影响填充效果的重要参数。
如果参数设置不合理,可能会导致填充不完整,出现短射现象。
解决这个问题的方法可以是根据塑料材料的特性和模具的要求,调整注射参数以优化填充效果,确保充满整个腔体。
最后,设备的问题也可能导致短射。
设备的稳定性和控制精度对于塑胶成型的质量至关重要。
如果设备存在故障或者控制不准确,可能会导致填充不完整,出现短射现象。
解决这个问题的方法可以是对设备进行维护和保养,确保设备正常运行。
此外,定期检查和校准设备的控制系统,确保精度和稳定性。
综上所述,塑胶成型不良是塑胶制品生产过程中常见的问题。
对于短射这一问题,其原因可能包括原料、模具设计、注射参数和设备等方面。
为了解决短射问题,可以选择合适的原料,优化模具设计,调整注射参数以及维护设备等措施。
塑胶成型常见不良原因分析及对策
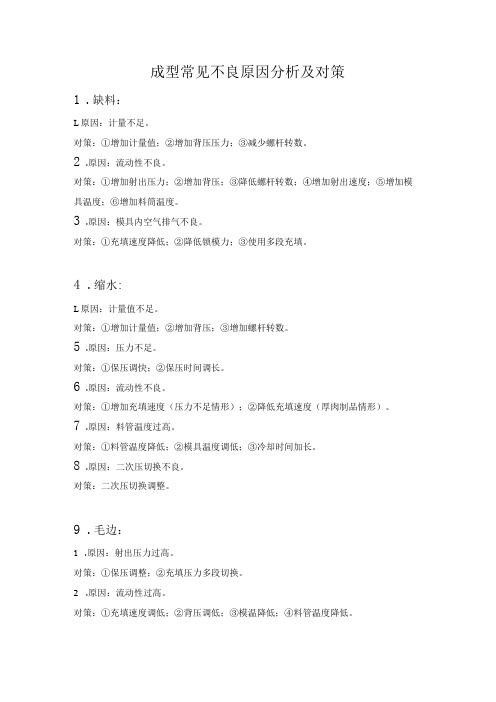
成型常见不良原因分析及对策1.缺料:L原因:计量不足。
对策:①增加计量值;②增加背压压力;③减少螺杆转数。
2.原因:流动性不良。
对策:①增加射出压力;②增加背压;③降低螺杆转数;④增加射出速度;⑤增加模具温度;⑥增加料筒温度。
3.原因:模具内空气排气不良。
对策:①充填速度降低;②降低锁模力;③使用多段充填。
4.缩水:L原因:计量值不足。
对策:①增加计量值;②增加背压;③增加螺杆转数。
5.原因:压力不足。
对策:①保压调快;②保压时间调长。
6.原因:流动性不良。
对策:①增加充填速度(压力不足情形);②降低充填速度(厚肉制品情形)。
7.原因:料管温度过高。
对策:①料管温度降低;②模具温度调低;③冷却时间加长。
8.原因:二次压切换不良。
对策:二次压切换调整。
9.毛边:1.原因:射出压力过高。
对策:①保压调整;②充填压力多段切换。
2.原因:流动性过高。
对策:①充填速度调低;②背压调低;③模温降低;④料管温度降低。
3.原因:二次压切换不良。
对策:①提前切换二次压;②减少计量值。
4.原因:模内空气排出不良。
对策:①充填速度降低;②多段射出;③型缔力调低。
5.原因:锁模力不足,模具密合不够。
对策:锁模力增大。
4.气泡:1.原因:计量时空气进入。
对策:①背压调高;②螺杆转数调低;③进料段温度降低;④降低加热筒后段温度。
2.原因:加热筒内部异常发热。
对策:①增加背压;②减少螺杆转数。
3.原因:松退量过多。
对策:①松退量减少;②松退速度减小。
4.原因:体积收缩。
对策:①增加背压;②延长保压时间;③增高模具温度;④降低料管温度;⑤降低充填速度(厚肉制品情形);⑥增加充填速度(压力不足情形)。
5.原因:模具内空气排出不良。
对策:①降低充填速度;②多段射出;③降低锁模力。
6.气纹:1.原因:速度过快或压力过大。
对策:降压或减速。
2.原因:料温过低。
对策:提高前段温度。
对策:提升模具温度。
4.原因:浇口或太小或太大。
对策:模具改善。
塑胶注塑不良的分析以及处理措施

尺寸标准
对比设计图纸,检查塑胶制品的关键 尺寸是否在允许的公差范围内。
性能标准
根据塑胶制品的具体用途,评估其物 理性能和化学性能是否满足使用要求 。
安全标准
确保塑胶制品在使用过程中不会对人 体造成伤害,符合相关国家和地区的 法律法规。
检测与评估工具
放大镜
用于观察塑胶制品的细 微缺陷。
卡尺
用于测量塑胶制品的尺 寸。
注射压力、温度、时间等参数设置不合理, 影响塑料的流动和成型。
塑料材料问题
塑料材料性能不佳,如收缩率大、流动性差 等,导致成型不良。
模具保养不当
模具保养不善,如清洁不彻底、润滑不足等 ,影响塑料的流动和成型。
02
塑胶注塑不良的检测与评估
检测方法
目视检测
通过观察塑胶制品的外观,检 查是否存在缺料、缩水、气泡
02
塑胶注塑不良的原因多种多样,如模 具设计不合理、塑料材料选择不当、 注塑工艺参数设置不正确等。针对不 同类型的不良现象,需要采取不同的 处理措施。本文对各种不良现象进行 了分类和总结,并详细介绍了相应的 处理方法,有助于提高生产效率和产 品质量。
03
本文还对塑胶注塑技术的发展趋势进 行了展望。随着科技的不断发展,新 型塑料材料和加工技术不断涌现,注 塑技术将朝着高效、环保、智能化的 方向发展。未来,注塑技术将更加注 重节能减排、提高生产效率、降低成 本等方面,为工业生产带来更多的便 利和效益。
案例三:某产品内部气孔问题
总结词
内部气孔是指产品内部存在大小不一的气孔,影响产品的机械性能和外观。
详细描述
气孔通常分布在产品内部,形状不规则。可能的原因包括塑料原料中含有水分或挥发性物质、模具排气不良、塑 料熔体流动不均匀等。
塑胶常见不良及解决方法

塑胶常见不良及解决方法塑胶是一种常见的材料,广泛应用于各种行业和领域。
然而,由于塑胶的特性以及制造过程中的一些问题,常常会出现一些不良现象。
本文将重点介绍一些常见的塑胶不良及其解决方法。
1.氣泡:塑膠制品中常見的一種不良現象是氣泡,這會在成品表面或内部形成小气囊。
气泡的形成是由于塑胶熔融时含有的空气或挥发物没有充分释放出来。
解决方法包括降低加工温度、增加熔体压力、增加注射速度和使用抗气泡添加剂等。
2.热胀冷缩:塑胶制品在温度变化下会发生热胀冷缩,导致尺寸变化。
这可能会导致配件无法正常连接或安装。
为了解决这个问题,可以采用材料改性或加工工艺改进,如增加冷却时间、降低注射温度等。
3.白化:白化是指塑胶制品表面或内部出现白色斑点或条纹。
这种现象通常是由于塑胶在注射过程中发生气泡聚集或制品未达到均匀熔融所致。
解决方法包括优化注射工艺、增加熔体压力、使用抗白化添加剂等。
4.热裂纹:热裂纹是指在塑胶产品成型过程中出现的裂纹现象。
这通常是由于塑胶在成型过程中存在过大的应力集中,导致塑胶产生裂纹。
解决方法包括改变模具设计、增加冷却时间、预混塑胶料等。
5.变色:变色是指塑胶制品在使用或储存过程中出现颜色变化。
这可能是由于塑胶材料受到光、热、氧化等外界因素的影响所致。
解决方法包括选择适当的防褪色添加剂、合理储存塑胶制品等。
6.毛刺:毛刺是指塑胶制品表面出现不平整、刺状的小颗粒。
这通常是由于模具表面不平整或注射工艺不当所导致的。
解决方法包括优化模具设计、控制注射压力、调整注射速度等。
7.缩水:缩水是指塑胶制品在冷却过程中发生体积收缩。
这可能导致尺寸偏离设计要求。
解决方法包括优化塑胶成型工艺、增加冷却时间和选择合适的材料等。
8.潜伏期延长:有些塑胶在使用一段时间后会发生不良现象,如变形、断裂等。
这可能是由于塑胶受到环境因素、应力或热老化的影响导致的。
解决方法包括选择合适的材料、控制加工温度、降低应力等。
总结起来,塑胶制品的不良现象可能是由于材料、工艺或环境等多种因素造成的。
塑胶产品外观常见不良分析

塑胶产品外观常见不良分析塑胶产品在日常生活中被广泛使用,它们可以用于制作各种产品,如家庭用品、工业部件、玩具等。
由于制作工艺以及原材料的原因,塑胶产品的外观常常会出现一些不良,这不仅会影响产品的美观度,还有可能影响产品的性能和使用寿命。
对于塑胶产品的外观不良分析非常重要。
下面我们将对常见的塑胶产品外观不良进行分析。
一、表面缺陷1. 水波纹水波纹是指塑胶产品表面出现的波纹状不平整,通常是由于注塑时模具温度不均匀或注射压力不稳定造成的。
如果注射速度过快或者模具表面磨损,也会导致水波纹的出现。
水波纹不仅影响塑胶产品外观美观度,还可能降低其强度和耐磨性。
2. 毛刺毛刺是指塑胶产品表面出现的细小而锋利的突起,在注塑工艺中,毛刺通常是由于模具设计不当或者模具磨损严重造成的。
毛刺会影响产品的手感和安全性,同时也会影响产品的使用寿命。
3. 烧结烧结是指塑胶产品表面出现的凹凸不平的现象,通常是由于模具温度设置不当或者注塑过程中料温不均匀导致的。
烧结会影响产品的美观度和尺寸精度,严重时还会导致产品的性能下降。
二、色差1. 色泽不均匀在注塑过程中,如果原料的分散性不好或者混料不均匀,就会导致塑胶产品的表面色泽不均匀。
这不仅会影响产品的外观质量,还会影响产品的一致性和品质稳定性。
三、气泡气泡是指塑胶产品表面或内部出现的空洞状现象,通常是由于注塑过程中原料受潮或者含有挥发性成分,或者注射压力不足造成的。
气泡会影响产品的外观质量和性能稳定性,甚至会导致产品的强度和密封性下降。
四、变形针对上述常见的塑胶产品外观不良,我们可以采取一些措施来进行预防和解决。
对于表面缺陷,我们可以通过优化模具设计,提高模具制造精度和加工质量,以及优化注塑工艺参数来减少水波纹、毛刺和烧结的出现。
对于色差问题,我们可以选择优质的原料并保证混料均匀,严格控制注塑工艺参数,尽量避免色泽不均匀和色斑的出现。
对于气泡和变形问题,我们可以在原料筛选和混合过程中严格控制原料含水量和挥发性成分,保证原料质量。
塑胶产品外观常见不良分析

塑胶产品外观常见不良分析塑胶产品是我们日常生活中常见的产品,如电器外壳、日用品、玩具等等。
而塑胶制品的外观质量不仅影响到产品的销售和使用效果,更关系到企业的信誉和声誉。
下面就来介绍一些常见的塑胶产品外观不良情况及分析。
1. 热痕热痕是塑胶制品在制造或运输过程中,由于受到高温或摩擦等因素造成的表面缺陷。
热痕通常表现为一条或多条近似线性的凹陷或凸起痕迹,在阳光下或特定角度观察时容易看到。
热痕的产生原因有很多,如模具温度过高、注塑速度过快、模具结构有缺陷等。
解决热痕问题主要是要从生产工艺和模具设计两个方面入手。
2. 透光差透光差是指塑胶制品在不同角度下的透光效果不同,呈现出明暗交错的状况,影响了产品的美观度,也可能影响到产品的实用性。
透光差的原因很多,如材料的质量、模具的设计、注塑工艺等。
解决透光差问题需要在材料选择、模具设计、生产工艺等方面采取相应措施。
3. 毛边毛边是塑胶制品在冷却收缩过程中,由于材料未充满模具或冷却不均匀而形成的。
毛边会严重影响产品的美观度和实用性。
解决毛边问题主要可以从以下几个方面入手:一是提高注塑压力,保证塑胶充满模具;二是优化模具结构,排除设计缺陷;三是调整冷却系统,使温度分布均匀。
4. 气泡气泡是指塑胶制品中出现的空气囊肿,严重影响了产品的质量和美观度。
气泡的原因有很多,如材料中含有水分或杂质、注塑过程中气体存在等。
解决气泡问题需要注意材料的存储和使用、调整注塑工艺等。
5. 瘤型瘤型是指塑胶制品表面凸起的突起,会影响到产品的美观度和质量。
瘤型的原因可能是由于模具设计、注塑工艺等因素导致材料无法均匀填充模具,从而出现凸起的瘤型。
解决瘤型问题可以从优化模具结构、调整注塑工艺等方面入手。
塑胶产品外观常见不良分析

塑胶产品外观常见不良分析塑胶产品是现代工业生产中不可或缺的一部分,它们广泛应用于各个领域,包括家电、汽车、日用品等。
塑胶产品的外观质量直接关系到产品的市场竞争力,因此对于塑胶产品外观常见不良的分析尤为重要。
塑胶产品外观常见不良主要包括以下几种:气泡、缺陷、变色、浸料、开裂等。
下面,我们将对这些常见的不良现象进行分析。
首先是气泡。
气泡是塑胶制品生产过程中常见的外观不良现象。
气泡的形成通常是由于塑胶原料中含有挥发性有机物质,其在高温下挥发产生气体,导致气泡的形成。
生产过程中操作不当、模具设计不合理以及塑胶制品内部结构设计不当等也会导致气泡的产生。
解决气泡问题的关键是要从源头控制挥发性有机物质的含量,并严格控制生产工艺及操作流程,确保塑胶产品的成型质量。
其次是缺陷。
塑胶制品在生产过程中,由于模具设计、生产工艺、原材料等方面的原因,常常会出现表面上的缺陷,比如表面不光滑、有裂纹、有划痕等。
这些缺陷不仅影响产品的美观度,还可能导致产品在使用过程中出现性能问题。
要有效避免和解决塑胶制品的表面缺陷问题,需要从生产工艺、原材料选择和模具设计等方面入手,提高产品的成型质量。
再次是变色。
塑胶制品长期受到外部环境的影响,可能会出现变色的情况。
变色的原因主要包括原料的质量问题、生产工艺和环境条件等因素。
变色不仅影响产品的视觉效果,还可能会影响产品的物理性能。
要避免塑胶制品的变色问题,首先要选择质量稳定的原材料,并严格控制生产工艺参数,同时要尽量避免产品长时间暴露在阳光下或受到化学品的侵蚀。
浸料也是塑胶制品常见的不良现象之一。
浸料是指塑胶制品在使用或存放过程中,表面的浸渍物质产生的现象。
浸料的原因可能与原料的选择、添加剂的使用、生产工艺等相关。
浸料影响了产品的外观和手感,使得产品在市场上失去竞争力。
解决浸料问题的关键是选择质量稳定的原料,并严格控制生产工艺,确保产品表面的光洁度和耐用性。
塑胶产品外观常见不良的分析对于提高产品的市场竞争力具有重要意义。
- 1、下载文档前请自行甄别文档内容的完整性,平台不提供额外的编辑、内容补充、找答案等附加服务。
- 2、"仅部分预览"的文档,不可在线预览部分如存在完整性等问题,可反馈申请退款(可完整预览的文档不适用该条件!)。
- 3、如文档侵犯您的权益,请联系客服反馈,我们会尽快为您处理(人工客服工作时间:9:00-18:30)。
4.縮小熔結線的條件
提高注射速度合模具溫度,提高熔料溫度合注射壓力,模具上開排氣槽。 5.改變熔結線的位置 5.改變熔結線的位置 根據制品形狀,有的制品中不可能完全消除熔結線,有時熔結線又偏偏 在制品正表面或需要高強度的位置,這種情況下須設法改變熔結線的位置。 熔結線位置隋澆口位置的改變而改變。 熔結線部位受到高壓易發生飛邊,在發生飛邊的部位開個足夠大的溢料 槽,讓熔結線發生在溢料贅物上,成型後再切除溢料贅物,確保制品的強度。
三. 充
1.充填不足的主要原因 充填不足的主要原因
填
不 足
(1)成型工藝條件不當(注射壓力不足); (2)注塑機的塑化能力不足; (3)塑料的流動性太差; (4)多型腔模具的.各澆口不平衡,型腔排氣不暢。
2.多型腔模具中,有一個型腔充填不足 多型腔模具中, 多型腔模具中
未采取澆口平衡措施,簡便的方法是將充填不足的那個型腔擴大澆口截面積。
4.把模具換到其他注射機上(相同機種),盡管是同樣的成型條件,尺寸發生 把模具換到其他注射機上(相同機種),盡管是同樣的成型條件, 把模具換到其他注射機上 ),盡管是同樣的成型條件 誤差
即使把儀表上的工藝數據調節到完全相同,不同注射機反映的成型條件會有微小差別, 換注射機須重新調整工藝條件。 不同機種,成型條件的差別更大,應重新尋找合適的工藝條件。
3.夜間和白天生產的制品尺寸不同 夜間和白天生產的制品尺寸不同
成型條件(溫度、壓力、時間)未嚴格按工藝規定。操作應標准化。消除成型條 件波動因素,特別要強調夜間的成型周期必須輿白天相同,操作工不得擅自變動成 型周期.。 夜間輿白天的氣候條件不同也會影響制品尺寸。通過修正工藝條件,消除氣溫影 響,使實際成型條件保持恆定。
五. 脫
1.脫模損傷的主要原因 脫模損傷的主要原因
a.出模斜度不夠; b.模腔毛糙。
模
損
傷
2.出模斜度不夠,制品出模時受損傷 2.出模斜度不夠, 出模斜度不夠
模具的側壁沒有出模斜度或出模斜度太小,塑件冷卻後緊緊包住型芯,在訂出力 的作用下,發生塑件碎裂、頂桿頂穿等弊病。
3.便於制品脫傷的成型條件 3.便於制品脫傷的成型條件
5.直澆口周圍脫模碎裂 5.直澆口周圍脫模碎裂
澆口周圍所受的壓力很高,在澆口周圍是高應力區和高定向區,脫模時會產 生裂紋。在澆口周圍設一園環狀的框能起增強作用,不過這圓環狀的框一定不能薄 而小,直澆口的直徑以細一點為好,或用多點澆口,適當降低注射壓力。
六. 熔 結 線
1.熔結線產生的主要原因 1.熔結線產生的主要原因 制品平面上的孔、窗口等周圍都有熔結線。熔料流動中遇到成型孔和窗 口的型芯時,被分割成兩股,由於熔料同型芯接觸,溫度迅速降低,被分割 的兩股的料流再度匯合時,前沿不能熔合,便形成一條拼縫線,就是熔結線。 熔結線是因熔料熔合不良引起,此處的強度明顯減弱。 2.熔結線變粗的原因 2.熔結線變粗的原因 (1)型腔內的空氣未能迅速排出,熔結線變粗。這種情況時發生在排氣槽 被堵塞,開充分的排氣槽或疏通被堵塞的排齊槽後熔結線便恢復不明顯; (2)使用過量脫模劑,熔結線也會變粗。脫模劑被熔料推著前進脫模劑夾 雜在兩股料流的前鋒之間,阻擋前鋒熔合,機械強度減弱; (3)模腔表面若沾有水分和油等雜質,情況基本上同脫模劑,模腔應經常 保持清潔; (4)流道小,注射壓力損耗大,距澆口遠的部位無足夠的力使熔料熔合, 熔結線也就變粗了。 3.熔結線的鑒別 3.熔結線的鑒別 鑒別熔結線還是裂紋,常用塗洋(品)紅顏料的方法。
一. 尺 寸 超 差
1.尺寸超差的主要原因 尺大; (2)成型工藝條件波動; (3)模腔尺寸超差; (4)制品壁厚相差懸殊; (5)測量時和使用時的溫度誤差。
2.成型條件沒有變化,發生尺寸超差 成型條件沒有變化, 成型條件沒有變化
塑膠有收縮率誤差,首先檢查是否用原來相同的材料,材料入庫前應該批號取樣 檢驗收縮率,牌號相同的原料並不等於收縮率也完全相同;其次,確認尺寸測量方 法是否可靠,各種儀表是否准確顯示成型工藝條件。 核對工藝片卡,檢查以往成型條件的詳細記錄和生產記錄,尺寸的測量方法應預 先明確規定。塑料制品應進行狀態調節後再測量尺寸,即待制品尺寸穩定後,在一 定的溫度環境中測量(如:48h,23± 2℃ ).
3.成型收縮率大的材料容易縮水 成型收縮率大的材料容易縮水
結晶性大的塑料成型收縮率都很大,如聚乙烯、聚丙烯、聚甲醛等, 這些塑料的壁厚稍有誤差或壁較厚(4mm以上),就會出現縮水。
4.澆口遠的部位發生縮水 澆口遠的部位發生縮水
熔料在充填過程中,離澆口越遠壓力降低越大,或遇到難以流動的地 方,壓力傳遞有困難,不能對正在收縮中的熔料實現保壓補料,造成制 品縮水。
5.生產當時尺寸合格的制品,交貨時尺寸超差 生產當時尺寸合格的制品, 生產當時尺寸合格的制品
主要原因是尺寸測量的方法未統一。後,隨著溫度和濕度變化,尺寸跟著變化,經過 一段時間之後,結晶趨向穩定,變化結束,尺寸也趨向穩定。 測量尺寸的季節不同,溫度變化,對制品尺寸的影響很大。 塑料有:事效變化“的性質。成型中注射壓力過大或脫模力不均恆等原因,在制品中 殘留較大的內應力。塑料成型另外,未按規定堆放和儲存也會引起塑件變形導致尺寸超差。
5.減少縮水的條件 減少縮水的條件
工藝方面,向減少收縮方向調整成型工藝條件。 降低料筒和模具溫度,提高注射壓力和注射速度,增加保壓時 間和冷卻時間,增加注射料量。 材料方面,選用熔體指數低或含有增強填料的材料。 模具方面,縮短主流道,擴大澆口,合理分布冷卻水孔。形腔 表面施以皮紋、布紋、脈沖等裝飾花紋,掩蓋縮水。 設備方面,准確控制溫度、壓力、時間等工藝參數。 制品方面。減少壁厚,使壁厚均勻,制品形狀簡單、對稱。 離抗沖聚苯乙烯成型中,降低模溫,塑件表面無光澤縮水也變 得不明顯。
5.粘度低的塑料容易發生飛邊 5.粘度低的塑料容易發生飛邊
粘度低的塑料容易發生飛邊。防止飛邊的方法是努力提高模具精度,靠盛行條 件彌補模具的不足是很困難的。
6.減少飛邊的成型條件 6.減少飛邊的成型條件
控制飛邊發生,首先應提高模具精度,用硬度高的鋼作模具型材不易出現飛邊。 經淬火研磨的精密模具對付飛邊更可靠。 從成型工藝方面,主要朝減少流動性方向設定工藝條件。 降低注射壓力,降低熔料溫度和模具溫度,降低注射速度,減少加料量。 為減少飛邊而改變工藝條件的直接後果是對制品的其他特性帶來不良影響。
塑膠不良分析指導書
講師: 講師:
前
言
我司生產之產品,塑膠件為重要零件,其直接影 響產品之外觀及功能,故而提高塑膠件品質意義重 大。塑膠件質量的好壞是由材料成品設計、模具、 成型技術、二次加工技術等多種技術決定的。提高 塑件質量的前提是熟悉各工序之間的關係及技術, 技術人員能力的提升,為提升公司人員對塑膠件品 質問題的認識及解決分析能力,經過參考相關資料, 結合工作中之經驗,總結了塑件不良問題成因及改 善對策,以利大家共同學習提高! 謝謝!
降低注射壓力,縮短注射時間和保壓時間,降低模具溫度和料筒溫度,減少加料 量,用慢速頂出。遇到制品出模不暢情況,主要從模具方面找原因,靠成型條件彌 補是困難的。
4.使用脫模劑 4.使用脫模劑
脫模注射壓力,縮短注射時間和保壓時間,降低模具溫度和料筒溫度,減少加料 量,用慢速頂出。遇到制品出模不暢情況,主要從模具方面找原因,靠成型條件彌 補是困難的。
4.薄壁制品充填不足 薄壁制品充填不足
成型薄壁制品要流動型好的料,在牌號的選用尚上需認真研究;其次,成型 薄壁制品需要提高注射壓力,在提高注射壓力的同時,鑠模力也須相應增加。成 型薄壁制品的兩個條件是高流動性的料和高壓高速注射機。
5.連續生產中,逐漸充填不足 連續生產中, 連續生產中 先檢查料斗內是否斷料,如料斗內尚有料,則進一步檢查塑料粒子在 料斗內是否發生架橋狀況。加料口溫度過高,使塑料粒子軟化結團也會阻 礙下料,造成螺桿空料。電加熱器斷線,料筒和模具溫度溫度下降也是逐 漸填充不足的原因。 6.改善填充不足狀況的措施是向提高流動性方向調整工藝條件 改善填充不足狀況的措施是向提高流動性方向調整工藝條件 提高熔料的溫度和模具的溫度,提高注射壓力和注射速度,選用流動 性好的料。 7.根據實驗結果,成型條件輿填充長度之間的關係 根據實驗結果, 根據實驗結果 (1)注射、保壓時間超過規定時,充填長度不再增加,太短則充填不 足; (2)注射速度慢,填充不足,但超過一定速度,充填增加不多; (3)熔料在料筒內的停留時間同充填長度無關係; (4)模具溫度同充填長度成比例增加,但比例非常小; (5)螺桿後退距離越大,充填長度越長; (6)注射壓力同充填長度呈直線關係;
6.多型腔模具成型的各制品尺寸不一 多型腔模具成型的各制品尺寸不一
如果各型腔的尺寸完全相同,那麼主要原因是澆口不平衡。對於尺寸要求較高的制品 來說,型腔數目不宜取得過多,以1-2個為宜,最多不超過4個月。
7.縮水引起尺寸超差 縮水引起尺寸超差
塑件上壁很厚的部分會因收縮引起尺寸變小,如改進設計,使厚壁均勻,問題便會迎刃 而解。
8.成型收縮率過大的材料尺寸精度難以控制 8.成型收縮率過大的材料尺寸精度難以控制 除了特殊場合,成型收縮率波動估計在25%左右,成型收縮率的材 料,當然難以控制尺寸精度。 9.穩定尺寸精度的成型條件 提高注射壓力,增加注射和保壓時間,延長冷卻時間,提高注射 速度。 以上條件中影響最大的是模具溫度和注射壓力。一般規律為:模 具溫度上升,尺寸變小,模具溫度變化應控制在1 ℃ 左右,型腔壓 力增加,尺寸相應變大(成型收縮減小),應當使用型腔壓力檢測 裝置。
3.制品中某一部分充填不足 制品中某一部分充填不足
在充填不足的部分增設澆口,或采用多點澆口進料。熔料在流道內流動過程 中能量損失,動能減少,流動性降低,熔料不足以沖破壓縮空氣的阻截,被迫停 止前進,造成局部缺料,針對這鐘情況,在充填不足部位的分型面上開排氣槽 (深0.02~0.04mm),充分排齊,減少流動阻力,便可解決問題。
四. 飛 邊