基于UG的发动机整体叶轮数控编程研究
基于UG NX6.0的整体叶轮数控加工仿真研究
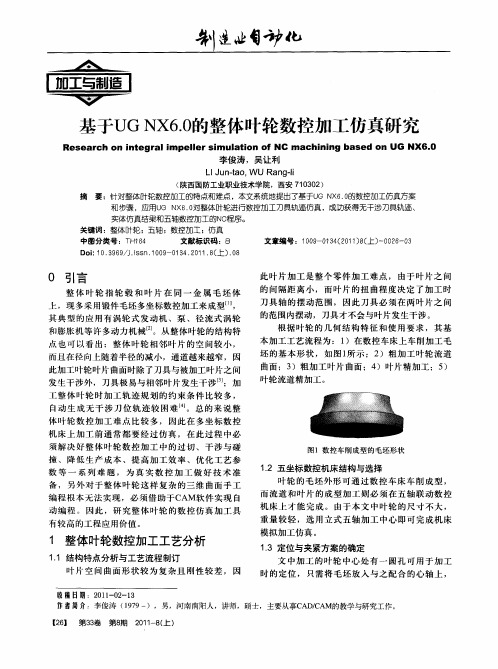
点也 可 以 看 出 :整 体 叶 轮 相 邻 叶 片 的 空 间较 小 ,
而且在 径 向上 随着 半径 的减 小 ,通 道 越来越 窄 ,因 此加 工叶 轮叶 片 曲面时 除 了刀具 与被 加工 叶片 之 间 发生 干涉 外 ,刀具 极 易与相 邻 叶 片发 生干 涉 ;加 】 工 整 体 叶 轮 时 加 工 轨 迹 规 划 的约 束 条 件 比较 多 , 自动 生 成 无 干 涉 刀 位 轨 迹 较 困 难 】 总 的 来 说 整 。
此 叶 片加 工 是 整 个 零 件 加 工 难 点 , 由于 叶 片 之 间 的 间 隔距 离 小 , 而 叶 片 的扭 曲程 度 决 定 了加 工 时 刀具 轴 的摆 动 范 围 , 因 此 刀具 必 须在 两 叶 片之 间
的范 围 内摆 动 ,刀具 才不会 与 叶片 发生干 涉 。 根 据 叶 轮 的 几 何 结 构 特 征 和 使 用 要 求 ,其 基
编 程 根 本 无 法 实 现 ,必 须借 助 于CAM软件 实现 自
动 编 程 。因 此 ,研 究 整 体 叶 轮 的数 控 仿 真 加 工 具
1 五坐标数控机床结构与选择 . 2 叶轮的毛坯外形可通过数控车床车 削成型 , 而 流 道 和 叶 片 的 成 型 加 工 则必 须 在 五 轴联 动 数 控 机 床 上 才 能 完 成 。 由于 本 文 中 叶 轮 的 尺 寸 不 大 , 重量较轻 ,选用立式五轴加工中, l 可完成机床 I ̄ bP 模拟 加工 仿 真 。 1 定位与夹紧方案的确定 . 3 文 中加 工 的 叶 轮 中心 处 有 一 圆孔 可 用 于 加 工
实体仿真结果和五轴数控加工的N 程序。 O
关键词 :整体 叶轮 ;五轴 ;数控加工 ;仿真 中囝分类号 :T 1 4 H 8 文献标 识码 :B 文章编 号 :1 0 - 14 2 1 ) ( - 0 6 3 9 0 ( 0 18 上) 0 2-0 0 3
基于UG NX的整体叶轮五轴数控加工

1 前言叶轮是压缩机、透平机和泵等的核心部件,其加工质量的优劣对压缩机的性能有着决定性的影响。
20世纪80年代中期,在先进透平机械的结构设计中,出现了“三元整体叶轮”结构。
三元叶轮是根据透平式流体机械内部流体的三元真实流动状况而设计的,能大幅度地降低能耗。
整体式三元叶轮是指轮毂和叶片在同一毛坯上,具有结构紧凑、曲面误差小、强度高等优点。
由于叶轮采取了整体式结构,而叶片的形状又是机械加工中较难加工的复杂形状曲面构成的,因此加工时轨迹规划的约束条件比较多,相邻叶片空间较小,加工时极易发生碰撞干涉,自动生成无干涉刀位轨迹较困难。
目前国外一般应用整体叶轮的五坐标加工专用软件,主要有美国叶轮制造公司NREC推出的专用软件包:MAX-5,MAX-AB;瑞士Starrag生产的数控机床所带的整体叶轮加工模块,还有Hypermill等专用叶轮加工软件。
此外,一些通用的软件如:UG、CATIA、PRO/E、 MasterCAM等也能用于整体叶轮的加工。
本文选用UG NX4.0对整体叶轮进行加工轨迹规划。
2 加工工艺及装备分析2.1 加工工艺流程规划叶轮的一般构成形式是若干组叶片均匀分布在轮毂上,相邻两个叶片间构成流道,叶片与轮毂的连接处有一个过渡圆角,使叶片与轮毂之间光滑连接。
叶片曲面为直纹面或自由曲面。
整体叶轮的几何形状比较复杂,一般流道较狭窄且叶片扭曲程度大,容易发生干涉碰撞。
因此主要难点在于流道和叶片的加工,刀具空间、刀尖点位和刀轴方位要精确控制,才能加工到其几何形状的每个角落,并使刀具合理摆动,避免发生干涉碰撞。
叶轮加工首先由最初的毛坯——棒料、铸造件或者锻压件采用车床进行外轮廓的车削加工,得到叶轮回转体的基本形状。
通过对叶轮结构和加工工艺的分析,叶轮加工主要由粗加工叶片间流道(叶轮开粗)、流道曲面的半精加工、叶片精加工、流道精加工和倒圆部分的清根加工等工序组成。
2.2 刀具选择刀具刚性和几何形状是叶轮加工刀具选择的主要因素,在流道尺寸允许的情况下尽可能采用大直径的刀具。
基于ug的发动机整体叶轮三维造型研究

换 ]命令 ,选择要复制的叶片 ,在 [ 角度 ] 文本框中输入参数值
360 / n ( n 为叶片个数) ,连续复制 n - 1 次 ,这样就完成了 n 个叶
片在轮毂上的均匀分布 ,如图 15 。
2. 5 建立整体叶轮
到 3. 4 叶片 、轮毂已经建立完毕 ,但它们都是独立的实体 ,
因此 ,把它们组合成一个实体 ,最终完成叶轮的三维实体造型
part 文件 ,从菜单栏中选择[应用 ]| [建模 ]命令 ,进入建模状态 。 但是 ,通常情况下 ,叶片的基元线主要分为两类 ,一类是平
面曲线 (一般出现在涡轮中) ,一类是空间曲线 (一般出现在压气 机叶轮中) 。而 UG 中对这两类曲线生成叶片实体的处理方法 是不一样 。下面将分这两种情况来讨论 。 2. 1. 1 叶片基元线为平面曲线时的创建
叶片原始文件提供的是 :一系列数据点坐标 ,数据点坐标格 式为 “: XC 空格 YC 空格 ZC 空格”。
收稿日期 :2005 - 03 - 17 3 基金项目 :国家 985/ 国家教育部教育振兴行动计划项目 (BHA985 - 1 - 4)
作者简介 :李群 (1981 - ) ,女 ,河北衡水人 ,北京航空航天大学硕士研究生 ,主要从事整体叶轮的数控加工技术研究 , ( E - mail) lq0616 @163. com ;陈 五一 (1951 - ) ,男 ,北京航空航天大学博士生导师 ,主要研究方向为先进制造技术 。
理论计算是根据流体力学原理计算出来的叶片的叶型数 据 ,本文的原始造型数据就是通过理论计算得出的 。如图 2 所 示为整体叶轮叶片的理论造型数据截面 。 1. 2 创建 UG支持的数据文件
叶轮造型的叶片是根据截面数据进行拟合的 ,所以必须把 原始数据文件进行处理使之符合 UG 所能识别的格式 ,为后续 建模提供合法的数据源文件 。
基于UG的闭式叶轮数控编程方法研究的开题报告

基于UG的闭式叶轮数控编程方法研究的开题报告【开题报告】一、选题背景叶轮是一种广泛应用于水泵、风机、涡轮机等各种机械设备中的重要零部件之一。
在叶轮制造过程中,数控加工已经逐渐取代传统的手工加工,该方法可以提高加工效率、保证加工精度,降低人工成本和材料浪费。
而闭式叶轮作为叶轮的一种,有着更高要求的加工精度和表面质量。
因此,如何设计出高效、高精度的闭式叶轮数控编程方法,成为了制造业研究的重点之一。
二、研究目的和意义本研究旨在探究基于UG的闭式叶轮数控编程方法,通过研究其特点,提出针对不同加工要求的编程方法,从而实现闭式叶轮的高效、高精度加工。
叶轮作为机械中的重要部件,其性能直接影响着机械设备的工作效率和稳定性。
而数控加工已成为现代工业制造的重要手段,其应用可以大幅提高生产效率和产品质量,降低材料和人工成本。
因此,本研究对于叶轮加工制造企业提高生产效率、降低成本、提高产品质量的实际需求非常明显。
三、研究内容与方法本研究将以UG软件为平台,探究基于UG的闭式叶轮数控编程方法,具体研究内容如下:1、闭式叶轮的几何建模方法研究:包括了闭式叶轮的参数化建模、基于点云数据的叶轮建模,通过建立闭式叶轮的数学模型,为后续数控编程计算提供依据。
2、闭式叶轮数控编程方法研究:包括闭式叶轮的加工路径规划、刀具轨迹生成和加工工艺选择等。
通过编写程序实现叶轮的自动化加工。
3、闭式叶轮加工模拟与试验研究:通过UG加工模拟,验证数控编程方法的正确性和可行性,并通过实验验证闭式叶轮的加工性能。
四、预期结果与进度安排本研究预期实现基于UG的闭式叶轮数控编程方法研究,主要研究结果包括:1、提出了闭式叶轮数控编程方法,该方法可以根据不同加工要求,选择不同的加工工艺和刀具轮廓,实现闭式叶轮的高效、高精度加工。
2、通过加工模拟和试验验证数控编程方法的正确性和可行性。
本研究的进度安排如下:1、5月-6月:文献综述和专业知识学习2、7月-8月:闭式叶轮几何建模方法研究3、9月-10月:闭式叶轮数控编程方法研究4、11月-12月:闭式叶轮加工模拟与试验研究五、预期贡献预计本研究的主要贡献有:1、提供了闭式叶轮数控编程方法研究的新思路,为叶轮的高效、高精度加工提供技术支持。
基于UG10.0整体叶轮数控成形仿真研究
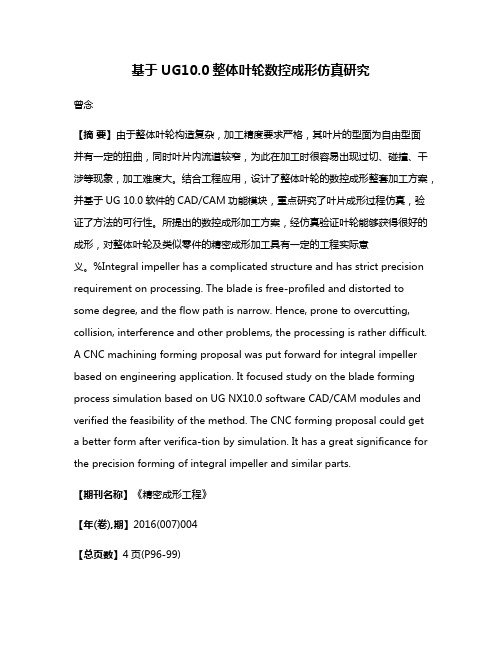
基于UG10.0整体叶轮数控成形仿真研究曾念【摘要】由于整体叶轮构造复杂,加工精度要求严格,其叶片的型面为自由型面并有一定的扭曲,同时叶片内流道较窄,为此在加工时很容易出现过切、碰撞、干涉等现象,加工难度大。
结合工程应用,设计了整体叶轮的数控成形整套加工方案,并基于UG 10.0软件的CAD/CAM功能模块,重点研究了叶片成形过程仿真,验证了方法的可行性。
所提出的数控成形加工方案,经仿真验证叶轮能够获得很好的成形,对整体叶轮及类似零件的精密成形加工具有一定的工程实际意义。
%Integral impeller has a complicated structure and has strict precision requirement on processing. The blade is free-profiled and distorted to some degree, and the flow path is narrow. Hence, prone to overcutting, collision, interference and other problems, the processing is rather difficult.A CNC machining forming proposal was put forward for integral impeller based on engineering application. It focused study on the blade forming process simulation based on UG NX10.0 software CAD/CAM modules and verified the feasibility of the method. The CNC forming proposal could get a better form after verifica-tion by simulation. It has a great significance for the precision forming of integral impeller and similar parts.【期刊名称】《精密成形工程》【年(卷),期】2016(007)004【总页数】4页(P96-99)【关键词】涡轮叶片;自由型面;数控仿真;CAD/CAM;UGNX【作者】曾念【作者单位】自贡市职业培训学院,四川自贡 643000【正文语种】中文【中图分类】TH164叶轮类零件在矿山、军工、船舶、航空等许多行业领域中应用广泛,如风机和飞机发动机叶轮、水泵叶轮等,也是这些机械设备的核心部件,其制造技术水平和制造质量将直接决定该设备的整体性能和稳定性。
毕业设计_基于UG叶轮的造型加工及数控编程

1 绪论1.1课题的确定整体式叶轮作为动力机械的关键部件,广泛应用于航天航空等领域,其加工技术一直是制造业中的一个重要课题。
从整体式叶轮的几何结构和工艺过程可以看出:加工整体式叶轮时加工轨迹规划的约束条件比较多,相邻的叶片之间空间较小,加工时极易产生碰撞干涉,自动生成无干涉加工轨迹比较困难。
因此在加工叶轮的过程中不仅要保证叶片表面的加工轨迹能够满足几何准确性的要求,而且由于叶片的厚度有所限制,所以还要在实际加工中注意轨迹规划以保持加工的质量。
目前,我国大多数生产叶轮的厂家多采用国外大型CAD/CAM软件,如UG NX、CATIA、MasterCAM等随着航空航天技术的发展,为了满足发动机高速、高推重的要求,在新型中小发动机的设计中大量采用整体结构叶轮。
选择数控加工仿真技术,适合加工种类多、需求少、难加工的整体叶轮,减少整体叶轮加工的成本。
本课题主要研究的是航空发动机上整体叶轮的数控加工工艺、造型、数控加工仿真及数控编程。
而且且本文选用目前流行且功能强大的UG NX4.0对复杂曲面整体叶轮进行加工轨迹规划。
下图是叶轮零件图1-1,1-2,1-3.前视图1-1俯视图1-2叶片之间的角度以上各图在后面会详细的分析。
1.2国内(外)发展概况及现状的介绍通常在整体叶轮的设计图上给出的是叶片中性面上顶部和根部的两组数据点,包括顶部和根部的一系列离散数据点和对应点的叶片厚度值。
本课题采用B 样条方法对叶轮曲面进行造型。
整体结构叶轮(图1-1)的应用可使航空发动机推重比、工作效率、寿命及可靠性大大提高,因此在各类新型发动机及大推力火箭发动机中应用愈来愈多,其加工质量的优劣对发动机的性能有着决定性的影响,而其叶片的形状又是机械中最难加工的曲面构成的。
因此,整体叶轮的加工一直是机械加工中长期困扰工程技术人员的难题。
为了加工出合格的叶轮,人们想出了很多的办法。
由最初的铸造成型后修光,到后来的石蜡精密铸造,还有电火花加工等方法。
基于UG NX6.0的整体叶轮数控加工仿真校验与后置处理

基于UG NX6.0的整体叶轮数控加工仿真校验与后置处理4.4.1 整体叶轮数控加工路径规划叶轮整体数控铣削加工是指轮廓与叶片在同一毛坯上铣削加工成形。
其加工过程大致包括以下几个主要工序:1.粗加工叶轮流道曲面;2.粗加工叶片曲面;3.叶片精加工;加工。
下面对其路径规划方法分别讨论。
1)创建整体叶轮数控加工父级组。
打开已经建构的整体叶轮三维CAD文件,进入UG加工界面,选择“mill_muti-axis(多轴铣削)”CAM加工配置模板,先后创建程序组、几何组、刀具组和方法组,为下面的加工仿真做准备,具体如下:a.创建程序组。
程序组是用于组织各加工操作和排列各操作在程序中的次序。
由于在单个叶片的多轴加工程序编制后,要使用旋转复制功能生成其余叶片的加工程序,因此这里先采用UG 缺省的程序组,待全部叶片加工程序完成后再统一修改、管理。
b.创建几何组。
在“导航器”中选择“几何视图”功能,进入几何视图工作界面,设置叶轮的圆柱圆心点为加工坐标系位置(双击MCS_MILL 在CSYS 状态下单击点对话框将捕捉类型设置为“圆弧中心/椭圆中心/球心”并将加工坐标系移至到圆心点),如图4.11所示;在铣削几何体中选择已经车削完成的回转体作为毛坯几何体,如图4.12所示c.创建刀具组根据前面已经确定的刀具类型和相关刀具参数,利用“创建刀具”功能,分别创建粗、精加工刀具,并且从内定库中检索刀具夹持器,创建刀具夹持器,本文中选取了库代号为“HLD001_00041”的刀具夹持器。
由于上一节中对刀具选择已作了比较详细的论述,这里不再重复,且此步的操作比较简单。
e.创建方法组由于叶片及流道曲面加工采用了表面积驱动方法,不便设置统一的加工余量、几何体的内外公差、切削步距和进行速度等参数,先选用内定的“METHOD ”加工方法,可根据需要再设置上述加工参数。
2)粗加工叶轮流道曲面通过可变轮廓铣程序控制驱动方法和刀具轴,根据叶轮流道曲面的加工要求创建多轴联动粗加工程序。
基于UG编程的叶轮5轴数控仿真加工教学案例研究

基于UG编程的叶轮5轴数控仿真加工教学案例研究冷家融(长春工业大学人文信息学院,吉林长春130122)【摘要】应用UG软件编程,在发动机叶轮的数控仿真加工过程中,辅以动画演示功能,使学生更好地了解编程的步骤、命令的选用以及相关参数的设置。
通过虚拟工作环境,调整参数设置,生动地演示其加工效果与差异,教授学生掌握5轴数控加工的编程要领,以此提高课堂教学效果与教学质量。
关键词:UG;叶轮;5轴仿真加工;机械专业教学中图分类号:TG659 文献标识码:BDOI:10.13596/ki.44-1542/th.2024.01.022Teaching Case Study on Impeller Five Axis Numerical ControlSimulation Processing Based on UG ProgrammingLeng Jiarong(College of Humanities & Information Changchun University of Technology,Changchun,Jilin 130122,CHN)【Abstract】Using UG software programming, in the numerical control simulation machining process ofengine impellers, animation demonstration functions are supplemented to help students betterunderstand the programming steps, command selection, and related parameter settings. By using avirtual working environment, adjusting parameter settings, and vividly demonstrating the processingeffects and differences, students can better grasp the programming essentials of five axis CNCmachining, thereby improving classroom teaching effectiveness and quality.Key words:UG; impeller; five axis simulation machining; mechanical teaching1 引言UG(Unigraphics NX)是Siemens PLM Software公司出品的一个产品工程解决方案,它为用户的产品设计及加工过程提供了数字化造型和验证手段。
- 1、下载文档前请自行甄别文档内容的完整性,平台不提供额外的编辑、内容补充、找答案等附加服务。
- 2、"仅部分预览"的文档,不可在线预览部分如存在完整性等问题,可反馈申请退款(可完整预览的文档不适用该条件!)。
- 3、如文档侵犯您的权益,请联系客服反馈,我们会尽快为您处理(人工客服工作时间:9:00-18:30)。
整体叶轮作为发动机的关键部件,对发动机的性能影响很大,它的加工成为提高发动机性能的一个关键环节。
但是由于整体叶轮结构的复杂性,其数控加工技术一直是制造行业的难点。
以典型的CAD/CAM软件——UG,编制出深窄槽道、大扭角、变根圆角的微型涡轮发动机压气机的转子的五坐标加工程序,并在MIKRON HSM400U五坐标数控机床上进行实验验证,证明该整体叶轮数控加工方案及程序的可行性。
该加工件已经用于微型发动机中进行试车实验。
1前言整体叶轮作为透平(Turbine)机械的关键部件,广泛地用于航空、航天等领域,其质量直接影响其空气动力性能和机械效率。
因此它的加工技术一直是透平制造行业中的一个重要课题。
目前国外一般应用整体叶轮的五坐标加工专用软件[1],主要有美国NREC公司的MAX-5,MAX-AB叶轮加工专用软件,瑞士Starrag 数控机床所带的整体叶轮加工模块,还有Hypermill等专用的叶轮加工软件。
此外,一些通用的软件如:UG、CATIA、PRO/E等也可用于整体叶轮加工。
目前,国内只有少数几家企业(如:西北工业大学等院校和航空航天系统一些发动机专业厂、专业所)可以加工整体叶轮,而且工艺水平距国际先进水平尚有很大差距。
总体上我国叶轮加工领域的研究与应用同发达国家相比还有很大差距,很多企业的软、硬件都依靠进口,自主版权的软件在生产中未见推广应用,在窄槽道、小轮毂比等高性能叶轮制造技术方面尚未过关,因此研究高性能叶轮的加工技术势在必行。
2整体叶轮的CAD/CAM系统结构图整体铣削叶轮加工是指毛坯采用锻压件,然后车削成为叶轮回转体的基本形状,在五轴数控加工中心上使轮毂与叶片在一个毛坯上一次加工完成,它可以满足压气机叶轮产品强度要求,曲面误差小,动平衡时去质量较少,因此是较理想的加工方法。
五轴数控加工技术的成熟使这种原来需要手工制造的零件,可以通过整体加工制造出来。
采用数控加工方法加工整体叶轮的CAD/CAM系统结构图[2]如图1所示。
3微型压气机转子的结构特点及加工难点国内大多数整体叶轮都是根据国外叶轮缩比仿制的,而本文研究的叶轮是北航能源与动力工程学院自主开发的微型航空发动机上的压气机转子。
压气机转子出口直径为81mm,有8片一级叶片,8片二级叶片,出口叶片高度3mm,叶轮进口直径44.3mm,进口叶片高度17.15mm,叶片厚度最薄处0.4mm,相邻叶片间最小间距为3.1mm,如图2。
为了使气动性设计达到了国际先进水平,压气机转子采用了大扭角,根部变圆角等结构,给加工提出了很高的要求。
转子加工难度如下:1、国际上同等直径81mm的整体叶轮通常有12片叶片或14片叶片,而此转子有16片叶片,而且它的二级叶片也较长,这些都使加工槽道进一步变窄,加工难度进一步增加。
2、在刀具直径为2.5mm情况下,刚性差,容易断,控制切削深度也是关键。
3、此叶轮曲面为自由曲面、流道窄、叶片扭曲严重,并且有后仰的趋势,加工时极易产生干涉,加工难度高。
有时为了避免干涉,有的曲面要分段加工,因此保证加工表面的一致性也有一定困难。
4、前缘圆角曲率半径变化很大,加工过程中机床角度变化较大,并且实现环绕叶片加工较难;5、由于叶轮强度的需要,轮毂与叶片之间还采用变圆角。
由于槽道窄,叶片高,变圆角的加工也是个难点。
总之,此叶轮的窄槽道、大扭角、变圆角给加工带来了很大困难,国内还未见有加工出此种高难度的整体叶轮。
4压气机转子的加工工艺方案叶轮整体加工采用轮毂与叶片在一个毛坯上进行成形加工,而不采用叶片加工成形后焊接在轮毂上的工艺方法。
其加工工艺方案如下[3-4]:1、为了提高整体叶轮的强度,毛坯一般采用锻压件,然后进行基准面的车削加工,加工出叶轮回转体的基本形状。
压气机转子的毛坯如图3所示。
2、叶轮气流通道的开槽加工开槽加工槽的位置宜选在气流通道的中间位置,采用平底锥柄棒铣刀平行于气流通道走刀,并保证槽底与轮毂表面留有一定的加工余量,如图4所示。
其中平底锥柄棒铣刀为硬质合金刀具,其规格为:平底部分直径为:3mm,半锥角为2°,刀具柄部直径为:6mm,带锥部分长度为:20mm。
此步选用的主轴转速为:10000r/min,进给速度为:800mm/min。
在数控机床的控制面板上一般备有主轴转速、进给速度修调(倍率)开关,可在加工过程中根据实际加工情况对主轴转速、进给速度进行调整。
3、叶轮气流通道的扩槽加工及叶片的粗加工扩槽加工采用球形锥柄棒铣刀,从开槽位置开始,从中心向外缘往两边叶片扩槽,扩槽加工要保证叶型留有一定的精加工余量。
通常情况下,扩槽加工与精铣轮毂表面在一次加工完成。
由于此叶轮槽道窄、叶片高、扭曲严重,且UG数控加工编程需要根据驱动面来决定切削区域,因此扩槽加工需要分两部分来加工。
第一部分:选择驱动面为轮毂面,进行扩槽。
此时不能加工到轮毂表面,还需进一步扩槽加工;第二部分:进一步扩槽及叶片粗加工。
选择驱动面为叶片表面的偏置面,在叶片粗加工的同时,进一步扩槽。
其中球形锥柄棒铣刀为硬质合金刀具,其规格为:球头部分直径为:3mm,半锥角为2°,刀具柄部直径为:6mm,带锥部分长度为:20mm。
此步选用的主轴转速为:20000r/min,进给速度为:3000mm/min。
4、叶片、轮毂的精加工在均匀余量下进行的精加工,保证了良好的表面加工质量,采用球头铣刀精加工,因为相邻叶片间最小间距为3.1mm,且叶片最深处为17.15mm,考虑到干涉,转子精加工刀具采用瑞士Fraisa公司的直径2.5的球头棒铣刀,刀具避空位为20mm。
加工时的主轴转速为:260000r/min,进给速度为:5000mm/min。
5、变圆角精加工大、小叶片的左侧为变圆角,圆角半径从叶片前缘到尾缘为1.25mm到2.2mm 到1.25mm线性变化。
其中最大圆角发生在靠近尾缘22%处。
叶片右侧为常数圆角1.25mm。
变圆角可以通过一次走刀加工完成,这时刀具球头部分的半径至大为变圆角的最小半径。
选择的刀具、主轴转速、进给速度,同叶片、轮毂的精加工。
以上程序都要经过分度、旋转,加工完全部的轮毂或叶片再执行下一个程序,保证应力均匀释放,减少加工变形误差。
5压气机转子的数控程序编制5.1用UG加工压气机转子的流程图用UG进行转子数控编程时,通常以如图5所示的流程图为引导,用以创建各操作的刀位轨迹,并贯穿加工的整个过程[2]。
5.2数控程序编制5.2.1建立父节点组1、在刀具节点下,加入加工用到的所有刀具,并设置其刀具参数;2、在几何节点下,选择毛坯、设置加工坐标系、选择避让几何为转子实体;3、在方法节点下,设置粗、半精、精加工时的主轴转速、进给率及刀位轨迹的显示颜色。
5.2.2叶轮气流通道的开槽加工抽取流道曲面,U、V参数线如图6(a)所示。
因为叶轮通道的加工需要沿气流方向,所以重新排列流道的U、V参数线,使U参数或V参数线沿气流方向。
因为此流道曲面的特殊性,重新调整U、V参数后,流道面分成了三片曲面。
重新排列后的V参数线如图6(b)所示,是沿气流方向的。
1、流道前端曲面(如图6(b)中的1面)的加工采用可变轴曲面轮廓铣(Variable Contour),加工深度越深,干涉越严重,采用一种刀轴控制方式不一定合适,因此分成两种刀轴控制方式进行。
一种为:Normal to Drive(用于上半层加工),一种为:Toward Point(用于下半层加工)。
加工上半层,程序的参数设置如下:1)驱动方法(Drive Method)采用Surface Area;2)驱动几何选用流道前端曲面,即图6(b)中的1面;3)建立避让几何,以零件整体作为避让几何,如果干涉则自动退刀,一般粗加工时选用自动退刀来避免干涉。
4)粗加工,行距选择Tolerance=0.1mm;5)刀轴控制方式为:Normal to Drive;6)切削区域中Surface%的Start step、End step都设置为:50,表示在加工面中间位置切削一刀;7)设置Non-Cutting,即非切削运动,选用沿刀轴进退刀;8)Cutting下,设置Stock余量:7mm;设置Multiple passes(多层加工),每层切深为0.5mm。
加工下半层,程序的参数设置如下:1)刀轴控制方式为:Toward Point;2)Cutting下,设置Stock余量:0.2mm;设置Multiple passes(多层加工),每层切深为0.5mm。
3)其它参数设置,同加工上半层的程序。
因为可变轴曲面轮廓铣关键是选择刀轴控制方式,因此后续的加工只说明刀轴控制方式。
2、流道左端曲面(如图6(b)中的2面)的加工采用的是可变轴曲面轮廓铣,加工本曲面,刀轴控制方式一种是Normal to Drive(用于上半部分加工),一种是Relative to Drive(用于下半部分加工)。
(3)流道右端曲面(如图6(b)中的3面)的加工此曲面曲率变化很平缓,曲面上各点法向与叶片曲面夹角都接近0o,因此加工此曲面所选择的刀轴控制方式为Normal to Drive。
生成加工刀轨如图7所示。
5.2.3叶轮气流通道的扩槽加工扩槽加工刀轨类似开槽加工,只是切削区域中Surface%的Start step设置为:0、End step:100,表示切削整个流道面,生成刀轨如图8所示。
5.2.4进一步扩槽和叶片的粗加工扩槽加工后已经加工掉流道大部分余量,为了保证精加工之前有均匀的加工余量,提高最终的表面加工质量,此步是继续扩槽和叶片粗加工。
加工驱动面选择叶片的偏置面,如图9所示,流道、叶片粗加工后的仿真结果如图10所示。
5.2.5转子一级、二级叶片的精加工(吸力面、压力面、前圆角)从吸力面过渡到压力面曲率变化剧烈,因此,采取吸力面、压力面、前圆角分开加工。
一级、二级叶片型面类似,加工参数是类似的,下面是叶片精加工的通用参数设置。
1)驱动几何选择要加工曲面;2)刀轴控制方式为:Relative to Drive,关键是选择参数Tilt、Lead;3)设置Non-Cutting,选用沿切削方向进刀、沿刀轴方向退刀;4)精加工Stock设置为:0mm;生成的加工刀轨,如图11。
5.2.6叶片根部变圆角精加工因为变圆角的曲率变化剧烈,因此用Relative(Normal) To Drive控制刀轴方向容易与其它叶片干涉,因此大、小叶片的刀轴控制方式都为:Toward Line,有时只用一条控制刀轴线,还不能控制加工一张完整的曲面,可能要选用几条控制线。
大叶片左侧变圆角加工刀轨如图12、小叶片左侧变圆角加工刀轨,如图13。
6结论在MIKRON HSM400U机床上实际加工出该压气机转子。
叶片粗加工结果如图14所示,大叶片背面的加工过程,如图15所示,转子的实物图如图16所示。