微絮凝—大梯度磁滤工艺去除金属离子
分散-絮凝对某微细粒磁铁矿弱磁精选效果的影响
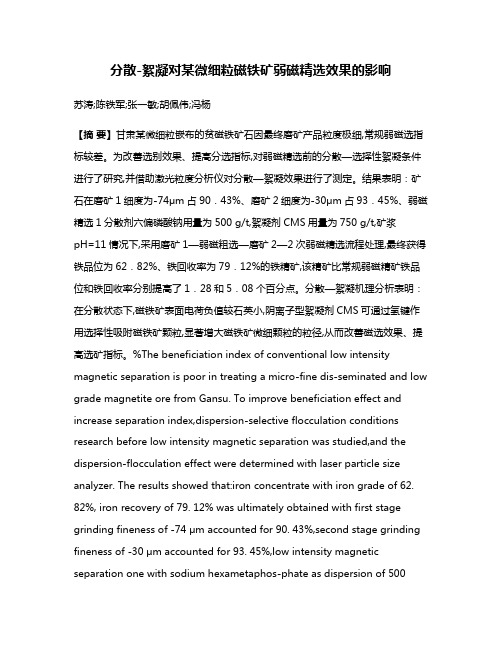
分散-絮凝对某微细粒磁铁矿弱磁精选效果的影响苏涛;陈铁军;张一敏;胡佩伟;冯杨【摘要】甘肃某微细粒嵌布的贫磁铁矿石因最终磨矿产品粒度极细,常规弱磁选指标较差。
为改善选别效果、提高分选指标,对弱磁精选前的分散—选择性絮凝条件进行了研究,并借助激光粒度分析仪对分散—絮凝效果进行了测定。
结果表明:矿石在磨矿1细度为-74μm占90.43%、磨矿2细度为-30μm占93.45%、弱磁精选1分散剂六偏磷酸钠用量为500 g/t,絮凝剂CMS用量为750 g/t,矿浆pH=11情况下,采用磨矿1—弱磁粗选—磨矿2—2次弱磁精选流程处理,最终获得铁品位为62.82%、铁回收率为79.12%的铁精矿,该精矿比常规弱磁精矿铁品位和铁回收率分别提高了1.28和5.08个百分点。
分散—絮凝机理分析表明:在分散状态下,磁铁矿表面电荷负值较石英小,阴离子型絮凝剂CMS可通过氢键作用选择性吸附磁铁矿颗粒,显著增大磁铁矿微细颗粒的粒径,从而改善磁选效果、提高选矿指标。
%The beneficiation index of conventional low intensity magnetic separation is poor in treating a micro-fine dis-seminated and low grade magnetite ore from Gansu. To improve beneficiation effect and increase separation index,dispersion-selective flocculation conditions research before low intensity magnetic separation was studied,and the dispersion-flocculation effect were determined with laser particle size analyzer. The results showed that:iron concentrate with iron grade of 62. 82%, iron recovery of 79. 12% was ultimately obtained with first stage grinding fineness of -74 μm accounted for 90. 43%,second stage grinding fineness of -30 μm accounted for 93. 45%,low intensity magnetic separation one with sodium hexametaphos-phate as dispersion of 500g/t,carboxymethyl starch(CMS) as flocculation of 750 g/t,pulp pH of 11,via grinding 1-low inten-sity magnetic rough separation-grinding 2-two times low intensity magnetic cleaning separation process,the grade and recovery of iron concentrate increased by 1. 28 and 5. 08 percentage points compared with the conventional low intensity magnetic con-centrate. Dispersion-flocculation mechanism analysis showed that:little absolute value of surface charge compared with quartz makes Polymer CMS adsorbed on the surface of magnetite by hydrogen bond in dispersion condition,which lead to increased particle size of fine magnetiteore,improve the magnetic separation effect and the beneficiation indexes.【期刊名称】《金属矿山》【年(卷),期】2016(000)009【总页数】5页(P83-87)【关键词】微细粒嵌布的磁铁矿;分散;选择性絮凝;弱磁选【作者】苏涛;陈铁军;张一敏;胡佩伟;冯杨【作者单位】武汉科技大学资源与环境工程学院,湖北武汉430081;武汉科技大学资源与环境工程学院,湖北武汉430081; 冶金矿产资源高效利用与造块湖北省重点试验室,湖北武汉430081;武汉科技大学资源与环境工程学院,湖北武汉430081; 冶金矿产资源高效利用与造块湖北省重点试验室,湖北武汉430081;武汉科技大学资源与环境工程学院,湖北武汉430081; 冶金矿产资源高效利用与造块湖北省重点试验室,湖北武汉430081;武汉科技大学资源与环境工程学院,湖北武汉430081【正文语种】中文【中图分类】TD923+.2;TD924.1+2微细粒嵌布的磁铁矿石属典型的难选铁矿石,在高品位、易选铁矿石资源匮乏的我国,开展此类矿石的选矿试验研究很有必要[1-5]。
微絮凝工艺
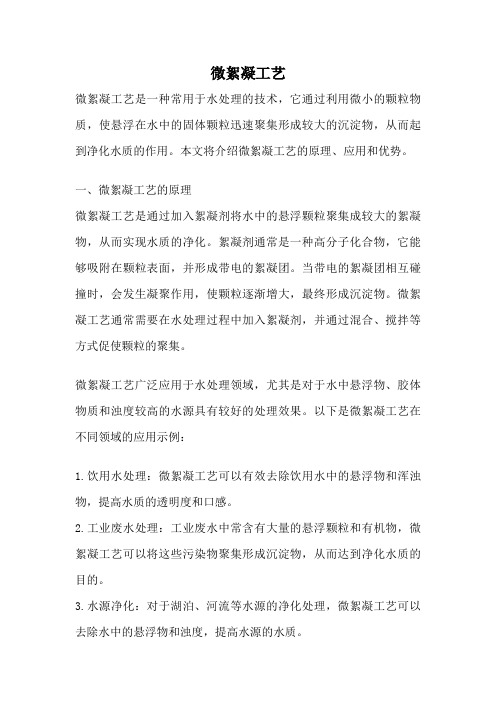
微絮凝工艺微絮凝工艺是一种常用于水处理的技术,它通过利用微小的颗粒物质,使悬浮在水中的固体颗粒迅速聚集形成较大的沉淀物,从而起到净化水质的作用。
本文将介绍微絮凝工艺的原理、应用和优势。
一、微絮凝工艺的原理微絮凝工艺是通过加入絮凝剂将水中的悬浮颗粒聚集成较大的絮凝物,从而实现水质的净化。
絮凝剂通常是一种高分子化合物,它能够吸附在颗粒表面,并形成带电的絮凝团。
当带电的絮凝团相互碰撞时,会发生凝聚作用,使颗粒逐渐增大,最终形成沉淀物。
微絮凝工艺通常需要在水处理过程中加入絮凝剂,并通过混合、搅拌等方式促使颗粒的聚集。
微絮凝工艺广泛应用于水处理领域,尤其是对于水中悬浮物、胶体物质和浊度较高的水源具有较好的处理效果。
以下是微絮凝工艺在不同领域的应用示例:1.饮用水处理:微絮凝工艺可以有效去除饮用水中的悬浮物和浑浊物,提高水质的透明度和口感。
2.工业废水处理:工业废水中常含有大量的悬浮颗粒和有机物,微絮凝工艺可以将这些污染物聚集形成沉淀物,从而达到净化水质的目的。
3.水源净化:对于湖泊、河流等水源的净化处理,微絮凝工艺可以去除水中的悬浮物和浊度,提高水源的水质。
三、微絮凝工艺的优势微絮凝工艺相比传统的絮凝工艺具有以下优势:1.处理效果好:微絮凝工艺可以有效去除水中的悬浮颗粒和浊度,提高水质的透明度和纯净度。
2.运行成本低:微絮凝工艺不需要大量的化学药剂和设备投入,运行成本较低。
3.操作简便:微絮凝工艺的操作相对简单,只需要加入适量的絮凝剂并进行混合搅拌即可。
4.适用范围广:微絮凝工艺适用于各种规模和类型的水处理系统,能够应对不同水质和处理要求。
微絮凝工艺是一种有效的水处理技术,通过利用微小的颗粒物质将水中的固体颗粒聚集形成较大的沉淀物,实现水质的净化。
微絮凝工艺在饮用水处理、工业废水处理和水源净化等领域具有广泛的应用,并具有处理效果好、运行成本低、操作简便和适用范围广等优势。
随着水质要求的提高和环境保护意识的增强,微絮凝工艺在水处理行业的应用前景将更加广阔。
超磁分离技术设计要点

一,工程说明超磁分离技术设计要点一、超磁分离技术的特点超磁分离水体净化技术是一项新颖的水处理技术,其成套设备与普通的沉淀和过滤相比,具有无反冲洗,分离悬浮物效率高,工艺流程短,占地少,投资省,运行费用低等特点;针对城市污水、工业废水、矿井水、油田采出水、河道水、景观水等不同种类的废水,长期的净化试验和工程实例表明该技术具有以下显著特点:1、处理时间短、速度快、处理量大,磁盘瞬间产生大于重力 640 倍的磁力,处理效率高,流程短,总的处理时间大约3 min,可多台并联运行,满足大流量处理要求;2、占地少,出水稳定,占地面积约为传统絮凝沉淀的1 /8,混凝时间1min,絮凝时间2min,过水平均流速320m/h;占地面积:600m3/d,2.4×4.0;3000 m3/d,9.6×6.0;10000 m3/d,磁盘机外形尺寸6.0×3.0×1.9,磁分离磁鼓外形尺寸,3.3×2.0×1.453、排泥浓度高,磁盘直接强磁吸附污泥,连续打捞提升出水面,通过卸渣系统得到高浓度污泥;4、运行费用低,采用微磁絮凝技术,投加药量少,且磁种循环利用率高,运行费用低;5、日常维护方便,设备无需反洗,自动化程度高,运行稳定可靠;二、超磁分离技术的原理直接磁选技术在分离污水如钢厂废水中的铁磁性杂质方面效果明显,但对于造纸、化工、制药、食品、石油等工业废水,由于废水中的有毒有害物质大多为酸碱离子、有机物、油等,主要是非磁性或弱磁性物质,因此采用直接磁分离方法很难将这些有害物质有效分离,必须通过预先加入磁种的方法,使本身无磁性的有害物质带上磁性,然后在高梯度磁场中实现磁分离;磁种—絮凝分选法主要包括磁种絮凝、磁分离和磁种回收三大主要步骤;具体方法是在一定的化学条件下,向污水中添加专用磁种和絮凝剂,或铁磁性絮凝剂如表面处理过的三价铁盐,水中有害物质通过氢键、范德瓦尔斯力或静电力与经表面官能团修饰的磁种絮接,从而使非磁性物质具有磁性或使弱磁性物质的磁性增强,与污染物结合的磁絮凝剂可以被高梯度磁滤网或磁盘捕获,从而实现污染物的去除;磁分离设备分离出的废渣磁种和悬浮物的混合体经输送装置进入高速搅拌剪切环节,实现磁种和悬浮物的分离,再经由磁鼓回收装置,就可将其中的磁种分选出来,磁种回收率可达99.4 %以上;回收的磁种可循环利用,既节约了生产成本,又减少了环境负荷;图:超磁分离水体净化技术工艺流程三、设计要点1、混凝反应设计1停留时间:磁分离设备的分离方式不同于沉淀池,无需形成大颗粒的密实絮体,属于微絮凝技术,其混凝反应停留时间约 3min,同时投加混凝剂和助凝剂,前段投加混凝剂,通常为聚合氯化铝PAC或硫酸铝,反应时间 1min,后段投加助凝剂,通常为聚丙烯酰胺PAM,反应时间 2min; 在SS=200mg/L~450mg/L,磁种200目44μm投加量为200 mg/L~300mg/L,PAC:40 mg/L,PAM:1 mg/L. 2药剂投加设计:混凝剂和助凝剂采用隔膜或柱塞计量泵以溶液的形式定比自动投加,不同水体药剂投加量需要根据混凝试验确定,在缺乏混凝试验资料时,混凝剂的投加量一般采用 10mg/L~15mg/L,助凝剂投加量为 1mg/L~2mg/L;混凝剂配置浓度一般为 5%~10%,助凝剂配制浓度一般为 0.5‰~1‰;混凝剂需要定期配置,溶药池容积保证每天溶药次数不多于两次,储药箱容积至少保证每天 24 小时连续运行所需的药剂量;助凝剂溶解需要较长的时间,特别是在冬季气温较低的情况下,但不易吸潮,目前大型水处理或污泥处理均采用自动溶解投加一体机,极大的减轻了劳动强度;3混凝工艺设计在分析超磁分离设备工艺的基础上,选择机械混合,用电动机驱动搅拌器,使水和药剂混合;机械搅拌机一般采用立式安装,搅拌机轴中心适当偏离混合池的中心,可减少共同旋流;机械混合搅拌器有:桨板式、螺旋式和透平式;桨板式搅拌器结构简单,加工制造容易,适用于容积较小的混合池,其他两种适用于容积较大的混合池;桨板式搅拌器的直径 D0=1/3~2/3DD为混合池直径,搅拌器宽度 B=0.1~0.25D,搅拌器离池底0.5~0.75D;当 H︰D≤1.2~1.3 时H为池深,搅拌器设计成 1 层,当 H︰D≥1.3 时,搅拌器可以设成两层或多层;2、强磁分离机系统:磁盘表面场强大于4000Gs,流道中心磁场场强大于800Gs;过水流速一般取 0.08m/s~0.1m/s,在设计范围内过水流速越低,处理效果越好,但是过水流速过低,单位面积磁盘上将吸附过多的絮团,导致磁盘磁场强度衰减,影响处理效果;目前采用的磁盘直径一般为 1200mm 和1500mm,水体与磁盘的最大有效接触时间为 12s~18.75s,磁场强度随离开磁盘表面的距离增大而减小,超过 30mm,磁场强度将大幅降低,所以一般磁盘间距控制在 10mm~30mm;磁盘转速 0.1r/min ~1.0r/min,磁盘转速过低单位面积磁盘接触絮团的量将增加,造成吸附不充分;磁盘转速过高将会导致吸附絮体中的水份来不及脱出,造成污泥含水率升高;根据处理水体污染物浓度和出水水质要求不同,设备参数会有所变化;超磁分离设备多为非标准设备,设计单位提处理水质水量和要求,设备厂家根据相应要求进行加工,目前市场上超磁分离设备的磁盘强度、磁盘直径和间距一般都是固定的,设备加工中根据水质水量不同改变磁盘的数量来增加或减少吸附面积来适应处理水量和水质的变化;3、磁种回收投加系统:磁种回收投加系统中的回收用磁分离磁鼓的表面场强大于 6000Gs,吨水处理磁种耗损率小于 3g /m3;磁回收及投加设备的作用是实现磁粉的回收并将其二次投加到混凝反应工艺单元,同时将产生的污泥排出系统;从超磁分离设备分离出的絮团是磁粉和污泥的混合物,首先需要对磁粉进行消磁,使絮团之间得以分散,然后自流排入磁分散装置,内部设置高速搅拌机和退磁装置,通过高速搅拌,将单个絮团打散,使磁粉和污泥分离,在装置的溢流口设置磁回收磁鼓,磁粉和污泥的混合物在溢流到磁鼓表面时,磁粉被磁鼓吸附回收,污泥无法被磁鼓吸附,通过在磁鼓底部设置的污泥管排出系统;被回收的磁粉通过刮板将其从磁鼓上刮离,再次退磁后返回磁粉投加装置,然后通过计量泵再次加入到混凝反应单元;由于磁粉重力比水大得多,且不溶于水,在水体中极易沉淀,向混凝反应单元投加的是磁粉和水的混合悬浊液,要通过不断搅拌保证磁粉始终处于悬浮状态,磁粉浓度相对均匀,才能保证相对准确的磁粉投加量,磁粉投加量需要根据试验确定,在缺乏试验数据的情况下,一般景观水体磁粉的投加量是悬浮物的 1.5 倍;随着磁粉悬浊液的投加,磁粉投加装置的液位将逐步降低,需要根据液位的变化自动补充自来水,保持磁粉浓度基本不变;磁铁粉的回收再应用问题;国外采用三种方法;一是用大离心力的旋流分离器可回收7 5 ~9 8 % 的磁铁粉,二是利用超声装置,用强剪力使磁铁粉与絮凝体分离,但运转费用高,三是用泵使反洗水高速送入另一套高磁分离装置,磁铁粉即被捕捉与反洗水分离,使磁铁粉能循环使用;该系统包括絮凝、磁分离、反洗、浓缩、磁种回收等,可全部自动化;4、磁种微絮凝系统:Fe3O4含量大于 95%,粒径小于 44 μm 的占 80% 以上,剩磁小于 8Gs,易于分散药剂投加量: PAC 投加15mg /L,PAM 投加0. 5mg /L;麦秸秆磁种材料制备麦秸秆磁种是通过在无磁性的麦秸杆中植入 Fe3O4磁性颗粒来实现的过程如下,将物质的量比2:1 的 FeCl3·6H2O和 FeSO4·7H2O 溶于纯水,将机械粉碎得到的麦秸杆粉末分散在该溶液中在氮气保护和磁力搅拌下将 25%的氨水缓慢滴入上述混合溶液中,然后70 度反应 4h 所得反应产物洗涤后磁性分离、烘干;创新点:增加悬浮物测定仪,根据悬浮物多少控制磁盘转速;采用推流、折流板、管道混合器方式,提高混合率,防止磁种和絮凝体沉淀;采用齿轮抓手,用于磁鼓分离含磁种污泥;磁种和絮凝剂的开发;四、机械加工要点1、混凝剂投加系统加工要点投加系统分为:螺杆式固体絮凝剂投加装置,搅拌溶解池,计量泵投加及管路系统;2、磁盘机械加工要点圆盘磁分离器的工作原理是在非磁性的圆板上嵌进永久磁铁,将数块同样的圆板以一定间隔装在同一轴上;当废水进入装置时,废水中的磁性颗粒被圆盘板边上的磁铁所吸附而被捕;随着圆盘的旋转,被捕集的磁性颗粒从水中进入空间,再由刮板刮下来;磁盘是磁分离装置的核心,也是该装置的设计关键所在;根据磁分离装置基本设计要求:合理的表面磁场、高的磁场梯度、高的作用深度、宽的工作间隙、尽可能长的磁化流程、适当的工作温度、适合的转速、方便刮泥、节能、安全、操作简单等;提出磁盘的主要设计步骤:1磁性材料的选用;2磁系的设计;3磁块的性能的选择;4磁盘间隙大小和磁场分布;磁盘的磁系设计要考虑多种因素,既有磁体经济利用的要求,又有磁体产生足够的场强和合理的磁场特性等要求;磁系设计时应着重解决主要矛盾,首先考虑磁系,保证它有足够的场强和合理的磁场特性,在此基础上再很好地考虑磁体的经济利用问题,并使磁体的工作点尽量靠近最大磁能积点;磁盘直径取1.6米,磁铁外侧为圆弧形状,覆板厚度4毫米,中间用8毫米厚加强肋,覆板用铆钉连接,钕铁硼为易腐蚀材料,必须保证磁块密封在磁盘中,所有接口处均采用用橡胶圈密封,磁块放置好后灌胶固定和密封;装配流程示意图与实体图如下所示;5 个磁盘的总重为 5×500=2500Kg,轴的材料选用 45优质中碳钢,采用调质表面处理;由于 5 个磁盘均匀分布在轴的中间部分 500mm 内,轴径为d=80mm,轴承受径向载荷为转速范围 0~6 r/min;其他部件设计1动密封:在工作过程中,承载磁盘部分的轴段需要沉浸在水中,其他部件是不需要浸没在水中,因此轴的两端需要采用动密封,根据设计手册查得,对于低速、常温、常压的液体密封使用普通的接触式毛毡密封就可以满足使用要求;而磁盘转速小于 3m/s,因此选用接触式粗毛毡密封;2水泵助卸及卸料刮片:为了快速去除磁盘表面吸附的絮体,使用聚四氟乙烯材料制成了“V”字形的刮片,用螺钉紧固在钢架结构上其大小刚好可以装配在磁盘间隙中起到刮的作用;由于刮下的絮体缺乏流动性,短时间内会填满“V”形槽,因此设计了助卸水泵,四个分管以一定压力的水流冲走槽内的絮体;刮片是损耗件,使用一段时间后需要对其更换以保证卸料稳定;3电器部分:主要由配电柜、变频器和操作按钮,动力由额定功率为4Kw 的小型三相异步电机提供;根据被处理污水的水质和絮凝的状况需要使用变频器控制磁盘的转动速度,从而达到最佳的分离效果;3、污泥输送装置加工要点被磁盘分离出来的渣经螺旋输送装置输送到磁种回收系统中, 磁性絮团通过高速分散机高剪切机后再流经磁分离磁鼓机,磁种被筛选出来,剩余污泥从磁鼓的底部排污阀流出,排出的污泥被收集送至污泥处理系统中筛选出来的磁种被再次配制成一定浓度的溶液,配制磁种所需的补充水由补水电磁阀根据磁种液位的高低,自动控制补充; 磁种溶液通过磁种计量泵泵组以一定的量投加到混凝系统中,磁种在此完成循环回收及再利用;。
广州大学教务处

广州大学教务处广大教字[2009] 20号关于进行2008年度本科生科学研究立项项目结题验收工作的通知校属各有关单位:根据《关于确定2008年本科生科学研究立项项目的通知》(广大[2008]209号文)的精神,学校决定对2008年本科生科研立项项目进行结题验收,现将有关事项通知如下:一、验收范围:2008年确定的58项本科生科学研究立项项目(见附件一)。
二、验收方式:由学院(部门)组织结题验收工作。
三、验收时间:验收工作于2009年5月20日之前完成。
四、验收须交材料:(一)广州大学本科生科学研究立项结题报告书(见附件二)。
(二)研究成果:一般为研究论文、调查报告、设计图纸及设计说明书、开发的软件或程序(提供源代码)、仪器装置等。
五、验收要求:(一)项目负责人根据立项申报时填报的《广州大学本科生科学研究立项申报书》,认真填写《广州大学本科生科学研究立项结题报告书》,同时提供项目研究成果。
(二)各学院(部门)组织专家对立项项目的结题材料进行审查和结题验收(以校级校内基地为单位进行立项的项目由所属学院或部门负责),并填写各项目结题报告书的“专家评价”栏和“学院(部门)验收意见”栏。
(三)重点资助项目的结题验收工作须进行现场答辩,填写《广州大学本科生科学研究立项重点资助项目答辩时间、地点一览表》(见附件三),答辩前三天报到教务处实践科。
(四)各学院(部门)要认真组织,安排专人负责,做好2008年本科生科学研究立项项目的验收工作,给出验收意见,并按照结题验收情况,做好《广州大学2008年本科生科学研究立项项目结题验收情况汇总表》(见附件四)。
六、其它工作:(一)学院验收通过后,须提交如下材料:1、《结题报告书》的电子文档和书面文稿各一份。
2、研究成果如果是研究论文、调查报告、设计图纸及设计说明书等,提交电子文档和书面文稿各一份;如果是开发的软件或程序,提供源代码;如果是仪器装置,则提供仪器装置的有关图片。
反硝化深床滤池简介与原理
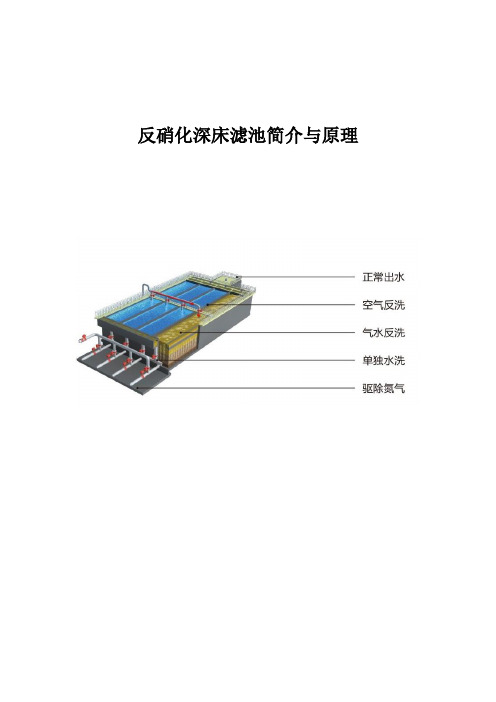
反硝化深床滤池简介与原理✧反硝化滤池简介反硝化深床滤池是集生物脱氮及过滤功能合二为一的处理单元,是业界认可度较高的脱氮及过滤并举的先进处理工艺。
1969年世界上第一个反硝化滤池诞生。
近40年来反硝化滤池在全世界有数百个系统在正常运行。
滤料采用2~3mm石英砂介质,滤床深度通常为1.83m,滤池可保证出水SS低于5mg/L以下。
绝大多数滤池表层很容易堵塞或板结,很快失去水头,而独特的均质石英砂允许固体杂质透过滤床的表层,深入滤池的滤料中,达到整个滤池纵深截留固体物的优异效果。
✧工艺流程图4-1 反硝化深床滤池工艺流程图✧反冲洗流程无论在深床滤池模式还是在反硝化深床滤池运行模式,滤池均需反冲洗,将截留和生成的固体排出。
反冲洗流程通常需要三个阶段:①气洗;②气水联合反洗;③水洗或漂洗。
✧滤池组成反硝化深床滤池结构简单,安装方便,滤池内无活动部件,滤料无流失,终身无需维护。
主要组件如下:A.滤料硬硅质砂,圆形尺寸范围2-3mmB.砾层圆形硬硅质砂尺寸范围3-40mmC.滤砖提供超强的反冲洗气水分配性能D.进气管当需要进气管配置时,不锈钢的进气管能够提供均匀的反冲洗气分配E.堰板使滤池与反冲洗水槽分开,为进水和反冲洗出水的均匀分配提供条件F.控制系统专为控制滤池的各种设备而开发的控制系统。
G.阀门自动和手动的阀门控制水和空气的进出H.碳源存储和供给系统通常设计为乙酸钠或乙酸,根据进入滤池的硝酸氮量来控制碳源投加量I.反冲洗泵为滤池提供反冲洗水,用于反冲洗滤料和驱氮。
J.鼓风机为滤池提供反冲洗空气来源,用于反冲洗滤料。
✧功能组件反硝化深床滤池结构简单实用,集多种污染物去除功能于一个处理单元,包括对悬浮物、TN和TP均有相当好的去除效果。
现有的运行经验表明,在无需化学加药除磷的情况下,可以满足出水水质BOD<5mg/L,SS<5mg/L,TN<3mg/L,TP<1mg/L。
在进行化学除磷的情况下,出水TP<0.3mg/L。
磁分离技术在高浓度废水去除微小颗粒中的应用
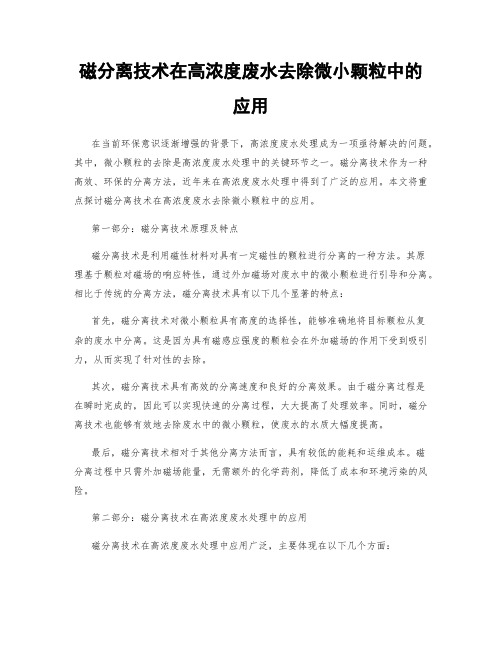
磁分离技术在高浓度废水去除微小颗粒中的应用在当前环保意识逐渐增强的背景下,高浓度废水处理成为一项亟待解决的问题。
其中,微小颗粒的去除是高浓度废水处理中的关键环节之一。
磁分离技术作为一种高效、环保的分离方法,近年来在高浓度废水处理中得到了广泛的应用。
本文将重点探讨磁分离技术在高浓度废水去除微小颗粒中的应用。
第一部分:磁分离技术原理及特点磁分离技术是利用磁性材料对具有一定磁性的颗粒进行分离的一种方法。
其原理基于颗粒对磁场的响应特性,通过外加磁场对废水中的微小颗粒进行引导和分离。
相比于传统的分离方法,磁分离技术具有以下几个显著的特点:首先,磁分离技术对微小颗粒具有高度的选择性,能够准确地将目标颗粒从复杂的废水中分离。
这是因为具有磁感应强度的颗粒会在外加磁场的作用下受到吸引力,从而实现了针对性的去除。
其次,磁分离技术具有高效的分离速度和良好的分离效果。
由于磁分离过程是在瞬时完成的,因此可以实现快速的分离过程,大大提高了处理效率。
同时,磁分离技术也能够有效地去除废水中的微小颗粒,使废水的水质大幅度提高。
最后,磁分离技术相对于其他分离方法而言,具有较低的能耗和运维成本。
磁分离过程中只需外加磁场能量,无需额外的化学药剂,降低了成本和环境污染的风险。
第二部分:磁分离技术在高浓度废水处理中的应用磁分离技术在高浓度废水处理中应用广泛,主要体现在以下几个方面:首先,磁分离技术能够有效去除高浓度废水中的铁矿石颗粒。
矿石颗粒是众多工业废水的主要组成部分,通过磁分离技术可以快速将矿石颗粒从废水中分离出来,减少水体污染。
其次,磁分离技术在高浓度废水中的微生物去除方面也具有广泛的应用。
在一些生产过程中,废水中可能存在大量微生物,通过磁分离技术可以对微生物进行快速引导和去除,降低水中微生物的浓度,减少环境污染的风险。
同时,磁分离技术还可以应用于高浓度废水中的重金属颗粒去除。
重金属被广泛应用于工业生产中,而含有重金属的废水对环境造成较大危害。
磁絮凝除磷
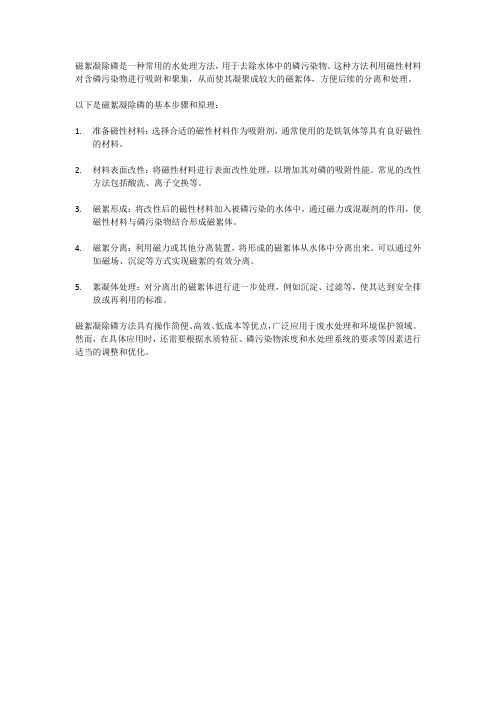
磁絮凝除磷是一种常用的水处理方法,用于去除水体中的磷污染物。
这种方法利用磁性材料对含磷污染物进行吸附和聚集,从而使其凝聚成较大的磁絮体,方便后续的分离和处理。
以下是磁絮凝除磷的基本步骤和原理:
1.准备磁性材料:选择合适的磁性材料作为吸附剂,通常使用的是铁氧体等具有良好磁性
的材料。
2.材料表面改性:将磁性材料进行表面改性处理,以增加其对磷的吸附性能。
常见的改性
方法包括酸洗、离子交换等。
3.磁絮形成:将改性后的磁性材料加入被磷污染的水体中,通过磁力或混凝剂的作用,使
磁性材料与磷污染物结合形成磁絮体。
4.磁絮分离:利用磁力或其他分离装置,将形成的磁絮体从水体中分离出来。
可以通过外
加磁场、沉淀等方式实现磁絮的有效分离。
5.絮凝体处理:对分离出的磁絮体进行进一步处理,例如沉淀、过滤等,使其达到安全排
放或再利用的标准。
磁絮凝除磷方法具有操作简便、高效、低成本等优点,广泛应用于废水处理和环境保护领域。
然而,在具体应用时,还需要根据水质特征、磷污染物浓度和水处理系统的要求等因素进行适当的调整和优化。
磁絮凝技术的原理

磁絮凝技术的原理什么是磁絮凝技术?磁絮凝技术是一种新型的水处理技术,它利用磁场作用于水中微小的磁性颗粒,使其有序排列,从而形成磁性絮凝团聚体,使悬浮物颗粒和微生物凝集在一起,最后通过过滤器进行分别,达到净化水质的目的。
这种技术具有高效、省电、环保等优点,被广泛应用于生活饮用水、工业用水、废水处理等领域中。
磁絮凝技术的原理磁絮凝技术的原理基于磁性粒子同性相斥和异性相吸的特性,将磁性颗粒及其四周的悬浮物通过磁力作用聚合成大的絮凝体,而这种聚合作用可以通过更改磁场的方向和强度来掌控。
实在来说,磁絮凝技术的原理紧要包括以下三个方面:1. 磁性颗粒的制备磁性颗粒是磁絮凝技术的核心部分,它们既可以通过合成化学方法制备,也可以通过天然矿物提取得到。
在生产实际中,常用的磁性颗粒有Fe3O4、Fe2O3、γ—Fe2O3、MnFe2O4、CoFe2O4等多种。
这些颗粒的平均粒径一般在10~100 nm之间,具有较高的饱和磁化强度和磁导率,且表面具有丰富的活性基团。
2. 磁场的作用原理在磁絮凝技术中,磁场的作用是至关紧要的,它能够更改水中悬浮物的分布规律和运动方式。
当磁场作用于水中的微小磁性颗粒时,由于颗粒的磁性会受到磁场的影响,磁性颗粒将在磁场的作用下发生定向聚合,最后形成大的絮凝体。
此外,磁场的强度和方向、水中磁性颗粒的含量等因素也会影响磁絮凝的效果。
3. 过滤器的作用原理磁絮凝技术的最后一步是通过过滤器将凝集后的絮凝体和悬浮物分别开来,实现水的净化。
过滤器的作用原理是通过纤维滤料、陶瓷滤芯等滤材将水中的悬浮物筛除,达到净化目的。
此外,在过滤前还可加入膜分别装置、反渗透装置等设备进一步提升水质。
磁絮凝技术的应用磁絮凝技术具有高效节能、操作简单、净化效果稳定等优点,渐渐被应用于生活饮用水、工业废水处理等领域。
在生活饮用水方面,磁絮凝技术可以有效的去除水中异色、臭味、浑浊度等杂质;在工业废水处理方面,磁絮凝技术可用于直接或间接处理有机污染物和重金属离子等难降解物质,节省处理费用及资源成本。
- 1、下载文档前请自行甄别文档内容的完整性,平台不提供额外的编辑、内容补充、找答案等附加服务。
- 2、"仅部分预览"的文档,不可在线预览部分如存在完整性等问题,可反馈申请退款(可完整预览的文档不适用该条件!)。
- 3、如文档侵犯您的权益,请联系客服反馈,我们会尽快为您处理(人工客服工作时间:9:00-18:30)。
大梯 度磁 滤 技 术 ( G ) 近 年来 发 展 起 来 的 H MF 是
g a i n a e i ir t n p o e s r de t m gn t fta i r c s c l o
Ca n f n Z n f n Zha g Cha s e g, ngHo g i oYo g e g, ha gKe a g, n o h n Ro n we
r m o a a e r e v lr ts a e 90.% . . % a d 69.% , e pe tv l 4 67 9 n 3 r s c i ey.Bu h e v lr t s o n a d Zn insa e n tditn— tt e r mo a ae fM n o r o si
效 果 当硫 酸铝 投加 量 为 1 I/ F 3 加 量 为 1 / 磁 场 强 度 为 02 7T、 速 5 h、 凝 时 间 为 8mi 搅 拌 2igL、 eO 投 T 5mgL、 .6 滤 0m/ 絮 n、
速度 为 1 0r i 5 m n时 , 工 艺 对 铁 、 、 3种 金 属 离 子 的去 除效 果 较 好 , 均 去 除率 分 别 为 9 .% 、79 6 . , / 该 铜 铅 平 04 6 .%、 93 但 % 对 锰 和锌 离 子 的 去 除 效 果 不 明 显 , 均 去 除 率 仅 为 69 、 23 。 平 . 1. % % [ 键 词 ]微 絮 凝 ; 梯 度 磁 滤 ; 场 强 度 ; 属 离 子 关 大 磁 金
( n t d ct na dG a g ogPo ic e a oa rf r a r u lyS c ryadP o ci Mii r o u ai n u n d n rvn e y b r oy o t ai e ui t t ni s y fE o K L t W eQ t tn r e o n
g ih. ea e a er mo a ae r n y 6 9 a d 1 .% . u s t v r g e v l t sa eo l .% n 3 h r 2
Key wor s:mi r fo c l to h g r d e tma n tcflr t n; g e i e d i t n iy; t l o s d c o c u a i n; i h g a i n g e i ta i ma n tcf l n e st me a n l i o i i
P a f v r l , a g h u U iest Gu n z o 1 0 6, hn ) e T Rie t Gu n z o nv ri De a y, a g h u5 0 0 C ia
Ab t c :Mi r n c u a in h g r d e tma n t l a in p o e sh sb e s d frte t g me a n fF , sr t a c 0 o c l t0 — i h g a i n g e i f t t r c s a e n u e o ai tli so e ci r o r n o
ra t n t n,n gttrsi igrt 0rmi t er mo a ae fF , u, b in r etr tea ea e e ci i 8 mi a da i o t rn ae 1 / n, e v l tso e C P o saeb t ,h v rg o me a r 5 h r e
第 3 卷 第 5期 1 21 0 1年 5月
工业 水 处理
I du tilW a e e t e t n sra trTr am n
Vo _ . l 31 NO 5 Ma 2 1 y. 01
微 絮 凝一 大 梯 度磁 滤 工 艺 去 除金 属 离 子
曹 勇锋 , 可 方 , 张 张朝 升 , 荣宏 伟
( 州 大 学教 育部 广 东省 珠 江三 角 洲水 质安 全 与保 护 实验 室 , 东广 州 5 00 ) 广 广 10 6
[ 要 ]采 用 微 絮 凝 一 大 梯 度 磁 滤 工艺 对 水 中铁 、 、 、 、 5种 金 属 离 子进 行 处 理 , 考 察 了该 工 艺 的处 理 摘 铜 锰 锌 铅 并
[ 中图 分 类 号 ]T 9 . [ 献 标 识 码 ] A [ 章 编 号 ]1 0 — 2 X( 0 1 0 — 0 9 0 U9 12 文 文 0 5 8 9 2 1 )5 0 3 — 4
Re o a f m v l t lo s b ir f c ua i n h g o me a in y m c o l c lt — i h o o
Cu, Mn, n a d Pb i t r a t r ame fe t r nv si ae Th e ulss o t twh n a u n m u f t Z n n wa e , nd iste t ntef c sa e i e tg t d. e r s t h w ha e l mi u s la e d s g i 1 mgL, e 04 o a e mg L, g tc ie d i e i 26 T, l a in a e 0 oae s 2 / F 3 d s g 1 5 / ma nei f l ntnst 0. 7 y i r o f t t r t 5 m/ fo c l to h, c u a in l