第三单元 套类工件的车削
套类零件的车削加工

8
机械零件切削加工实训
机电信息工程系
2020/5/14
1
项目五 套类零件的车削加工
一:实训目标
●学会内孔刀的选用和装夹 ●学会钻孔、车内孔及内孔倒角
2012.6.8
2
项目五 套类零件的车削加工
二:实训任务及要求
其余 倒角C1.5 未注尺寸公差IT14 去毛刺,倒钝锐边
A
2012.6.8
3
套类零件图
项目五 套类零件的车削加工 二:实训任务及要求
●完成阀腔零件的工艺分析及工艺文件的编写 ●完成阀腔零件的加工操作
2012.6.8
4
2012.6.8
项目五 套类零件的车削加工
三:实训注意事项
●严格遵守实训室各项规章制度,安全文明生产。 ●在实训教师指导下进行操作。
2012.6.8
6
项目五 套类零件的车削加工
第三单元套类工件的车削

第三单元套类工件的车削在机械零件中,一般把轴套、衬套等零件称为套类零件。
由于齿轮、带轮等工件的车削工艺与套类工件相似,在此将其作为套类工件分析。
为了与轴类工件相配合,套类工件上一般加工有精度要求较高的孔,尺寸精度为IT7~IT8,表面粗糙度要求达到R a0.8~1.6μm。
此外,有些套类工件还有形位公差的要求,如图3—1所示。
套类工件的车削工艺主要是指圆柱孔的加工工艺,圆柱孔的加工比车外圆要困难得多,有以下几个特点:(1)孔加工是在工件内部进行的,观察切削情况较困难。
尤其是孔小而深时,根本无法观察。
(2)刀柄受孔径和孔深的限制,不能做得太粗,又不能太短,因此刚度不足。
特别是加工孔径小、长度长的孔时,此问题更为突出。
(3)排屑和冷却困难。
(4)圆柱孔的测量比较困难。
图3—1 轴承套因此,在学习本章时更应该引起重视。
项目一钻孔一、学习目标1. 掌握麻花钻的几何形状、选用和安装方法。
2. 掌握麻花钻的刃磨技术。
3. 掌握麻花钻的钻孔方法。
二、学习任务1. 项目任务本项目的任务是学习麻花钻的刃磨技术和钻孔方法。
2. 任务流程图麻花钻的几何形状→麻花钻的刃磨→钻孔的方法→麻花钻的刃磨实训→钻孔实训三、环境设备学习所需设备、刀具、夹具、量具和材料清单见下表。
用钻头在实体材料上加工孔的方法称为钻孔。
钻孔属于粗加工,其尺寸精度一般可达IT11~IT12,表面粗糙度R a12.5~25μm。
根据形状和用途的不同,钻头可分为中心钻、麻花钻、锪钻和深孔钻等,本节只介绍麻花钻。
1. 麻花钻的几何形状(1)麻花钻的组成麻花钻由柄部、颈部和工作部分组成,如图3—2所示。
1)柄部麻花钻的柄部在钻削时起夹持定心和传递转矩的作用。
麻花钻的柄部有直柄和莫氏锥柄两种。
直柄麻花钻的直径一般为0.3~16mm。
莫氏锥柄麻花钻的直径见表3—1。
2)颈部直径较大的麻花钻在颈部标有麻花钻的直径、材料牌号与商标。
直径较小的直柄麻花钻没有明显的颈部。
数控车床单元三 套类零件的加工

四、任务准备
1.设备选择
选用广州数控GSK980T系统数控车床;计 算机及仿真软件;采用三爪自定心卡盘装夹
2.零件毛坯
选用 Ф42mm×65mm 圆钢,毛坯材质为 45钢。
3.刀具类型
选用90°外圆车刀、主偏角为93°内孔 车刀及刀宽为4mm的切断刀。
4.量具选用
(1)钢直尺:0~300mm。 (2)游标卡尺:0.02mm/0~150mm。 (3)外径千分尺:0.01mm/25~50mm、 内卡钳。 (4)塞规:Ф28mm。 (5)表面粗糙度样板。
G71粗加工循环
表3-4 台阶孔套加工程序(用复合循环指令G71编写)续表2
G00 X120. Z120.; M00; M03 T0303 S600; G00 X44. Z2.; Z-44.; G01X19.F0.1; G00 X120. Z120.; M30;
2号刀快速退刀 程序暂停,测量尺寸 换3号刀及3号刀补,机床 转速600r/min 3号刀快速靠近工件 3号刀快速到达切断位置 切断工件 3号刀快速退刀 程序结束光标回程序头
G90 X40. Z-23. F0.15;
G00 X100. Z100.; M30;
尺寸不对
1.对刀不正确 2.产生积屑瘤 3.程序中计算错误
1.刀具磨损 2.刀柄刚性差,产生“让刀”现象 1.车刀磨损 2.车刀刃磨不良,表面粗糙度大 3.车刀几何角度不合理,装刀低于 中心 4.切削用量选择不当 5.刀柄细长,产生振动
内孔有锥度
内孔表面 粗糙度差
任务2 薄壁套的编程与加工
图3-9 薄壁套
三、相关知识
1.孔加工刀具
孔加工刀具按其用途可分为两大类:一类是 钻头,它主要用于在实心材料上钻孔(有时 也用于扩孔)。根据钻头构造及用途不同, 又可分为麻花钻、扁钻、中心钻及深孔钻等; 另一类是对已有孔进行再加工的刀具,如镗 刀、扩孔钻及铰刀等。镗刀分通孔和盲孔两 种。
车工工艺第三章项目三 车削套类工件

项目3车削套类工件
§3.1套类工件简介
一、套类工件的特点
1.作用
支承、导向、连接以及和轴组成精密的配合
2.组成
内、外回转表面以及端面、阶台、沟槽等
3.车削套类工件的圆柱孔比车外圆困难,因为:
⑴加工孔再内部进行,观察比较困难。
⑵刀杆受孔径限制,刚性差。
⑶排屑和冷却比较困难。
⑷测量比较困难。
⑸装夹时容易变形(特别是薄壁的套类工件)。
1.铰刀
⑴几何形状
柄部、颈部和工作部分组成
柄部的作用:夹持和传递扭矩分直柄、锥柄和方榫形
⑵铰刀的种类
按用途可分机用铰刀和手用铰刀
按材料可分高速钢和硬质合金两种
⑶装夹
为保证同轴度,常采用浮动套筒
2.铰孔余量
高速钢铰刀为0.08㎜-0.12㎜;硬质合金为0.15㎜-0.20㎜
3.注意事项
①铰刀的选择和保管
采用哪些装夹方式。
Ⅳ.布置作业
P89 1,2,3
Ⅴ.板书设计
项目3车削套类工件
§3.1套类工件简介
一、套类工件的特点
1.作用
2.组成
3.车削套类工件的圆柱孔比车外圆困难,因为:
二、套类工件的技术要求
⑴尺寸精度
⑵形状精度
⑶位置精度
扬州市职业教育中心备课笔记纸(续页)
第 页
⑷表面粗糙度
§3.2套类工件的装夹
原则工件材料软,横刃↓
扬州市职业教育中心备课笔记纸(续页)
第 页
⑵前刀面外缘处:工件材料较硬→γ0↓→钻头强度↑(扩孔)
横刃处:工件材料较软→γ0↑→钻头强度↑
⑶双重刃磨双重顶角,改善外缘转角处的散热条件,钻头强
度↑,孔的表面粗糙度↓
套类工件车削质量研究

偏外 、 偏高、 偏低) 。钻头两主切削刃不对称。工件 端面不平 , 钻孔前 没有钻 中心孔 , 一开始进 给量过 大, 钻头产生摆动。钻头细长, 刚性不足或钻头本身 弯 曲 。钻夹 头偏 心或 锥 柄 、 套精 度 不高 。工件 材 钻
料 有缩孔 、 眼 和硬 度 不 均 匀 等 现象 。工 件装 夹 不 砂 紧 , 削时产 生位 移 。钻 头上粘 附刀 瘤 。 钻
按上述所列原因, 采取相应措施 : 修磨横刃 , 减 小横 刃 长度 。钻 中心 孔 , 不 同长 度 和 直径 的钻 头 用 多次钻削。勤清除切屑 , 勤加冷却液 。尾架 中心线 必须与工件中心线一致 , 钻套卡爪不能有喇叭 口。
刀, 勤加冷却液 , 保持切削刃 , 保持切削刃锋利。控 制钻孔深度的方法有 : 利用尾架套筒上 的刻度控制 钻孔 深度 ; 在钻 头上 装夹 定距套 或 定距 指针 ; 在钻 头
后角 , 两主切削刃刃磨要对称。分两次钻削 , 第一个 钻头的直径约为第二个钻头的 05~ . ,ቤተ መጻሕፍቲ ባይዱ. 07 两个钻头
的顶 角要 基本 相 同 。
1 钻 孔 容 易 产 生钻 头 摆 动 , 径 偏 大 , 孔
孔壁有深坑 , 长度钻深
1 1 产 生原 因 .
尾架 中心 与 车床 主 轴 中心 不 重 合 ( 架 偏 里 、 尾
利, 棱带( 即刃带 ) 磨损。工件材料硬度不均匀。刀 瘤严 重 , 力大 , 给量 过大 。 抗 进
3 2 排 除方法 .
按 上述 所列 原 因 , 取 相 应 措施 。也 可 以在 工 采 件 上试 钻 1 2 m长 , ~r a 停止 检 查 孔径 。孔 壁 深 坑 主 要 因排 屑 受 阻 和 刀 瘤 引起 , 因此 , 孔 时 必 须 勤退 钻
套类零件数控车削工艺分析
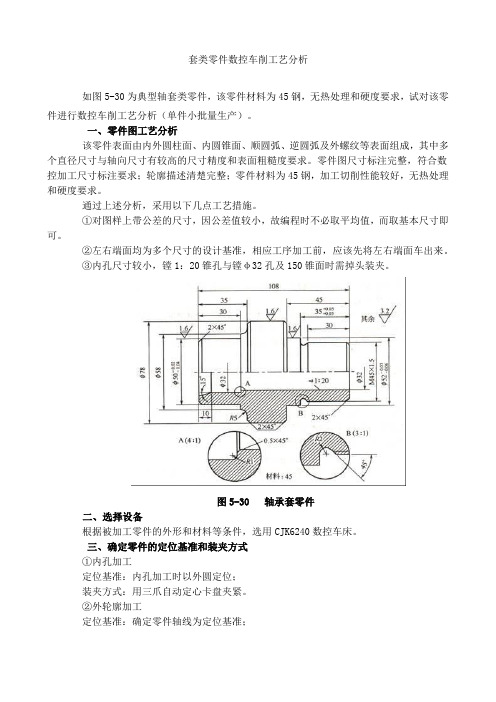
套类零件数控车削工艺分析如图5-30为典型轴套类零件,该零件材料为45钢,无热处理和硬度要求,试对该零件进行数控车削工艺分析(单件小批量生产)。
一、零件图工艺分析该零件表面由内外圆柱面、内圆锥面、顺圆弧、逆圆弧及外螺纹等表面组成,其中多个直径尺寸与轴向尺寸有较高的尺寸精度和表面粗糙度要求。
零件图尺寸标注完整,符合数控加工尺寸标注要求;轮廓描述清楚完整;零件材料为45钢,加工切削性能较好,无热处理和硬度要求。
通过上述分析,采用以下几点工艺措施。
①对图样上带公差的尺寸,因公差值较小,故编程时不必取平均值,而取基本尺寸即可。
②左右端面均为多个尺寸的设计基准,相应工序加工前,应该先将左右端面车出来。
③内孔尺寸较小,镗1:20锥孔与镗φ32孔及150锥面时需掉头装夹。
图5-30 轴承套零件二、选择设备根据被加工零件的外形和材料等条件,选用CJK6240数控车床。
三、确定零件的定位基准和装夹方式①内孔加工定位基准:内孔加工时以外圆定位;装夹方式:用三爪自动定心卡盘夹紧。
②外轮廓加工定位基准:确定零件轴线为定位基准;装夹方式:加工外轮廓时,为保证一次安装加工出全部外轮廓,需要设一圆锥心轴装置(见图5-31双点划线部分),用三爪卡盘夹持心轴左端,心轴右端留有中心孔并用尾座顶尖顶紧以提高工艺系统的刚性。
四、确定加工顺序及进给路线加工顺序的确定按由内到外、由粗到精、由近到远的原则确定,在一次装夹中尽可能加工出较多的工件表面。
结合本零件的结构特征,可先加工内孔各表面,然后加工外轮廓表面。
由于该零件为单件小批量生产,走刀路线设计不必考虑最短进给路线或最短空行程路线,外轮廓表面车削走刀路线可沿零件轮廓顺序进行(见图5-32)。
五、刀具选择将所选定的刀具参数填入表5-11轴承套数控加工刀具卡片中,以便于编程和操作管理。
注意:车削外轮廓时,为防止副后刀面与工件表面发生干涉,应选择较大的副偏角,必要时可作图检验。
本例中选κ =55 。
车工工艺与技能训练项目三 盘套类零件的车削 教案(1)
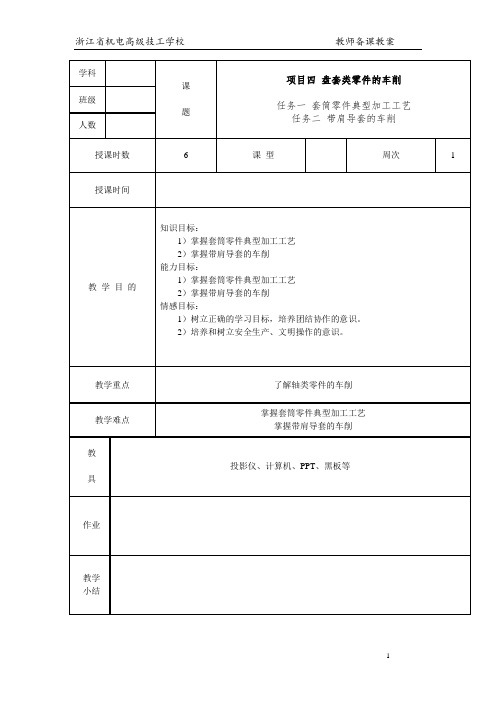
如图3-23所示的套类零件。
该零件中需要进加工的面有:75mm的台阶面、85mm的外圆面、两个端面以及内孔面。
其中两个端面有要求粗糙度不大于Ra1.6mm。
2.确定装夹方案零件的毛坯为Ø90×27的棒料,采用三爪自定心卡盘进行装夹。
伸出卡盘长度在14mm左右,校正后夹紧。
3.选择刀具及切削用量在本任务中有钻孔和扩孔的工序,除了选择90°的外圆车刀和45°倒角刀外,还需A3中心钻,Ø30钻头、Ø50钻头以及4mm宽切断刀。
在钻孔和扩孔的时候要特别注意主轴转速的选择,钻孔和扩孔时的切削量较大,所以应该选择较小的主轴转速。
4.确定加工方案按照先粗后精、先近后远的加工原则确定加工顺序。
工步一:粗车削端面。
工步二:钻中心孔,钻、扩孔。
工步三:精车端面。
工步四:粗车Ø85外圆面。
工步五:粗车Ø75台阶面。
工步六:精车Ø75台阶面至图样要求。
工步七:精车Ø85台阶面至图样要求。
工步八:倒角,切断。
工步九:调头装夹,车削端面至满足图样要求。
二、加工步骤1.右端面的粗加工(1)用三爪自定心卡盘夹住毛坯,工件伸出卡爪长度14mm,用钢直尺测量,装夹时需找正工件的轴线,使其与主轴轴线相重合。
(2)调整主轴转速手柄,将主轴转速调至800r/min。
(3)操纵手柄,用90°车刀粗车端面,车平即可。
2.粗车外圆和台阶面(1)调整主轴转速为560r/min,90°车刀粗车Ø85外圆至Ø86,长度11.5。
(2)粗车Ø75外圆至Ø76,长度5。
3.钻扩孔(1)调整主轴转速为1250r/min,用A3中心钻钻中心孔。
(2)调整主轴转速为355r/min,用Ø30钻头钻通Ø30底孔。
(3)调整主轴转速为280r/min,用Ø50钻头扩Ø50通孔。
浅谈套类工件车削工艺分析的教学方法

在 进 行 套 类 工 件 车 削 工 艺 分 析 教 学 的 过 程 中 , 根据 上 面 的 轴 套 图 ,教 师 让 学 生 找 出 内孔 的 尺 寸 。学 生 很 快 找 出 内孔 的 尺 寸 为 2 2 H7 ,通 过 公 差表 得 知 具 体 的 公 差 尺 寸 要 求
是2 2 . O ~2 2 . 0 2 1 。
车 削工 艺
教 学
在 机 械 加工 中 ,套 类 工件 是其 中的一 类 重要 零 件 ,套类 对 形 位 公 差 要 求 较 高 ,学 生 在 实 践 的 过 程 中往 往 觉 得 很 难 工件 加 工 对 尺 寸精 度 有 非 常严 格 的 要求 , 同时对 形 位 公 差 也 有 很 高 的要 求 。 因此 , 在套 类 工 件 加 工过 程 中 , 需要 采 用合 达 到 要 求 。 因 此 , 教 师 在 理 论 教 学 的 过 程 中 , 应 该 让 学 生
析 讲解 。通 过 精 车 孔 方 法 实 现 公 差 值 的 时 候 ,操 作 者 能 够 孔 车 外 圆 ,保 证 工 件 的 形位 公差 。 在 套类 工件车 削工艺 分析教 学中 ,教师应 结合 实例 , 采 用 互 动 的 教 学 方 法 , 让 学 生 能 够 更 加 积 极 主 动 地 参 与 到 到 解 决 的 方 法 。通 过 这 样 的 教 学 方 法 , 教 师 将 理 论 知 识 逐
能够 达 到 的 精 度 也 不 同 。利 用 小 锥 度 心 轴 支 撑 内 孔 时 ,彤
位公差在0 . 0 l mm 以 内 ; 而 使 用 台 阶 心 轴 时 , 形 位 公 差 只 能
根 据 这 些 条 件 , 教 师 首 先 发 问 : “该 公 差 尺 寸 的 要 求 ,
- 1、下载文档前请自行甄别文档内容的完整性,平台不提供额外的编辑、内容补充、找答案等附加服务。
- 2、"仅部分预览"的文档,不可在线预览部分如存在完整性等问题,可反馈申请退款(可完整预览的文档不适用该条件!)。
- 3、如文档侵犯您的权益,请联系客服反馈,我们会尽快为您处理(人工客服工作时间:9:00-18:30)。
第三单元套类工件的车削在机械零件中,一般把轴套、衬套等零件称为套类零件。
由于齿轮、带轮等工件的车削工艺与套类工件相似,在此将其作为套类工件分析。
为了与轴类工件相配合,套类工件上一般加工有精度要求较高的孔,尺寸精度为IT7~IT8,表面粗糙度要求达到R a0.8~1.6μm。
此外,有些套类工件还有形位公差的要求,如图3—1所示。
套类工件的车削工艺主要是指圆柱孔的加工工艺,圆柱孔的加工比车外圆要困难得多,有以下几个特点:(1)孔加工是在工件内部进行的,观察切削情况较困难。
尤其是孔小而深时,根本无法观察。
(2)刀柄受孔径和孔深的限制,不能做得太粗,又不能太短,因此刚度不足。
特别是加工孔径小、长度长的孔时,此问题更为突出。
(3)排屑和冷却困难。
(4)圆柱孔的测量比较困难。
图3—1 轴承套因此,在学习本章时更应该引起重视。
项目一钻孔一、学习目标1. 掌握麻花钻的几何形状、选用和安装方法。
2. 掌握麻花钻的刃磨技术。
3. 掌握麻花钻的钻孔方法。
二、学习任务1. 项目任务本项目的任务是学习麻花钻的刃磨技术和钻孔方法。
2. 任务流程图麻花钻的几何形状→麻花钻的刃磨→钻孔的方法→麻花钻的刃磨实训→钻孔实训三、环境设备用钻头在实体材料上加工孔的方法称为钻孔。
钻孔属于粗加工,其尺寸精度一般可达IT11~IT12,表面粗糙度R a12.5~25μm。
根据形状和用途的不同,钻头可分为中心钻、麻花钻、锪钻和深孔钻等,本节只介绍麻花钻。
1. 麻花钻的几何形状(1)麻花钻的组成麻花钻由柄部、颈部和工作部分组成,如图3—2所示。
1)柄部麻花钻的柄部在钻削时起夹持定心和传递转矩的作用。
麻花钻的柄部有直柄和莫氏锥柄两种。
直柄麻花钻的直径一般为0.3~16mm。
莫氏锥柄麻花钻的直径见表3—1。
2)颈部直径较大的麻花钻在颈部标有麻花钻的直径、材料牌号与商标。
直径较小的直柄麻花钻没有明显的颈部。
3)工作部分工作部分是麻花钻的主要切削部分,由切削部分和导向部分组成。
切削部分主要起切削作用;导向部分在钻削过程中能起到保持钻削方向、修光孔壁的作用,同时也是切削的后备部分。
a)b)c)图3—2 麻花钻的组成a)直柄麻花钻b)锥柄麻花钻c)镶硬质合金麻花钻麻花钻的几何形状如图3—3所示,它的切削部分可看成是正反两把车刀。
所以其几何角度的概念和车刀基本相同,但也有其特殊性。
1)螺旋槽麻花钻的工作部分有两条螺旋槽,其作用是构成主切削刃、排出切屑和通入切削液。
螺旋槽上螺旋角的有关内容见表3—2。
2)前面指切削部分的螺旋槽面,切屑由此面排出。
3)主后面指麻花钻钻顶的螺旋圆锥面,即与工件过渡表面相对的表面。
4)主切削刃指前面与主后面的交线,担负着主要的切削工作。
钻头有两个主切削刃。
5)顶角2K r 在通过麻花钻轴线并与两条主切削刃平行的平面上,两条主切削刃投影间的夹角称为顶角,用符号2 K r 表示。
一般麻花钻的顶角2 K r 为100°~140°,标准麻花钻的的顶角2 K r 为118°。
在刃磨麻花钻时可根据表3—3来判断顶角的大小。
6)前角γ0 主切削刃上任一点的前角是过该点的基面与前刀面之间的夹角,如图3—4所示。
用符号γ0表示。
其有关内容见表3—2。
7)后角a 0 主切削刃上任一点的后角是该点正交平面与主后刀面之间的夹角,用符号a 0表示。
后角的有关内容见表3—2。
为了测量方便,后角在圆柱面内测量,如图3—5所示。
图3—3 麻花钻的几何形状a )几何角度b )外形图a )b )图3—4 麻花钻前角和后角的变化 图3—5 在圆柱面内测量后角a )靠近外缘处b )靠近钻心处表3—2 麻花钻切削刃上不同位置处的螺旋角、前角和后角的变化着钻心处的钻削任务。
横刃太短,会影响麻花钻的钻尖强度,横刃太长会使轴向力增大,对钻削不利。
9)横刃斜角ψ在垂直于钻头轴线的端面投影中,横刃与主切削刃之间的夹角称为横刃斜角,用符号ψ表示。
横刃斜角的大小与后角有关,后角增大时,横刃斜角减小,横刃也就变长。
后角小时,情况相反,横刃斜角一般为55°。
10)棱边也称刃带,它既是副切削刃,也是麻花钻的导向部分。
在切削中能保持确定的钻削方向、修光孔壁及作为切削部分的后备部分。
表3—3 麻花钻顶角的大小对切削刃和加工的影响(1)麻花钻的刃磨要求麻花钻的刃磨质量直接关系到钻孔的尺寸精度、表面粗糙度和钻削效率。
如同车刀的刃磨一样,它也是车工必须掌握的基本功。
麻花钻一般只刃磨两个主后面并同时磨出顶角、后角以及横刃斜角。
麻花钻的刃磨要求如下:1)保证顶角(2K r)和后角a 0大小适当。
2)两条主切削刃必须对称,即两主切削刃与轴线的夹角相等,且长度相等。
3)横刃斜角ψ为55°。
(2)麻花钻的刃磨情况对钻孔质量的影响(见表3—4)表3—4 麻花钻的刃磨情况对加工质量的影响3. 钻孔的方法(1)麻花钻的选用1)对于精度要求不高的内孔,可用麻花钻直接钻出;对于精度要求较高的内孔,钻孔后还要再经过车削或扩孔、铰孔才能完成,在选用麻花钻时应留出下道工序的加工余量。
2)选用麻花钻长度时,一般应使麻花钻螺旋槽部分略长于工件孔深;麻花钻过长则刚性较差,不利于钻削,过短又会使排屑困难,也不宜钻穿孔。
(2)麻花钻的安装1)钻夹头装夹直柄麻花钻用钻夹头直接装夹,再将钻夹头的锥柄插入尾座套筒的锥孔中,如图3—6 a所示。
a)b)图3—6 麻花钻的安装a)直柄麻花钻的安装b)锥柄麻花钻的安装2)用过渡套安装锥柄麻花钻可直接安装或用莫氏(MORSE)过渡锥套(变径套)插入尾座锥孔中,如图3—6b所示。
3)专用工具装夹有的时候,因加工需要,锥柄麻花钻也使用专用工具进行装夹,如图3—7所示。
a)b)图3—7 用专用夹具装夹钻头(3)钻孔时切削用量与切削液的选择1)切削用量的选用切削用量包括三个要素:①背吃刀量pa钻孔时的背吃刀量为麻花钻的半径,即:2pda (3—1)式中 p a —背吃刀量(mm );d —麻花钻的直径(mm )。
②切削速度c v 可按下式计算: 1000c dnv π= (3—2 )式中 c v —切削速度(m/min );d —麻花钻直径(mm );n —车床转速(r/min )。
用高速钢麻花钻钻钢料时,切削速度一般取v c =15~30m/min ;钻铸铁时,切削取v c =10~25m/min ;钻铝合金时,取v c =75~90m/min 。
③进给量 ƒ 在车床上钻孔时的进给量是用手转动尾座手轮来实现的。
用小直径麻花钻钻孔时,进给量太大会使麻花钻折断。
用直径为12~15mm 的麻花钻钻钢料时,选ƒ=0.15~0.35mm/r ;钻铸件时,进给量略大一些,一般选ƒ=0.15~0.4mm/r 。
2)切削液的选用 钻孔时切削液的选用见表3—5。
表3—5 钻孔时切削液的选用(4)钻孔步骤1)钻孔前先将工件平面车平,中心处不允许留有凸台,以利于钻头正确定心。
2)找正尾座,使钻头中心对准工件的旋转中心,否则可能会使孔径钻大、钻偏甚至折断钻头。
3)用细长麻花钻钻孔时,为防止钻头晃动,可在刀架上夹一挡铁,以支持钻头头部来帮助钻头定心,如图3—8所示。
具体操作是:先用钻头钻入工件端面少许,然后缓慢摇动中滑板,移动挡铁逐渐接近钻头前端,以使钻头的中心稳定在工件回转中心的位置上,但挡铁不能将钻头支顶过工件回转中心,否则容易折断钻头,当钻头已正确定心后,则可退出挡铁。
另一种办法是先将直径小于5mm 麻花钻钻孔,钻孔前先在工件端面上钻出中心孔,这样既便于定心且钻出的孔同轴度好。
4)在实体材料上钻孔,小径孔可一次钻出,若孔径超过30mm ,不宜一次钻出。
最好先用小直径钻头钻出底孔,再用大钻头钻出所需尺寸孔径,一般情况下,第一支钻头直径为第二次钻孔直径的0.5~0.7倍。
5)钻不通孔与钻通孔的方法基本相同,不同的是钻不通孔时需要控制孔的深度。
具体操作是:开动车床,摇动尾座手轮,当钻尖开始切入工件端面时,用钢直尺量出尾座套筒的伸出长度,那么钻不通孔的深度就应该控制为所测伸出长度加上孔深,如图3—9所示。
(5)钻孔时的注意事项1)保证钻头轴线与工件旋转轴线相重合,否则钻削时会使钻头折断。
2)钻孔时,工件端面不能留有凸头。
图3—8 用挡铁支顶钻头图3—9 钻不通孔3)当钻头起钻时或是快钻穿孔时,手动进给要缓慢,以防钻头折断。
4)在钻削过程中,要经常退出钻头清除切屑,以免切屑堵塞在孔内造成钻头被“咬死”或折断。
5)在钻削钢料时必须浇注切削液,但在钻削铸件时可不用切削液。
4. 麻花钻的刃磨实训(1)麻花钻的刃磨方法麻花钻的刃磨方法如下:1)砂轮修整刃磨前应检查砂轮表面是否平整,如果不平整或有跳动,则应先对砂轮进行修正。
2)手握姿势用右手握住钻头前端作支点,左手紧握钻头柄部。
3)刃磨位置将钻头放置于砂轮中心平面以上,摆正钻头与砂轮的相对位置(使钻头轴心线与砂轮外圆母线在水平内的夹角等于顶角的1/2。
即为59°),同时钻尾向下倾斜,如图3—10所示。
a) b)图3—10 麻花钻刃磨时与砂轮的相对位置4)刃磨方法刃磨时,将切削刃逐渐靠向砂轮,见火花后,给钻头加一个向前的较小压力,并以钻头前端支点为圆心,缓慢使钻头作上下摆动并略带转动,见图3—11所示。
同时磨出主切削刃和后面。
但要注意摆动与转动的幅度和范围不能过大,以免磨出负后角或将另一条主切削刃磨坏。
重复上述刃磨动作4~5次,即可刃磨好。
双手握钻头的位置转动过180°刃磨另一个主切削刃,方法与上相同。
a)b)图3—11 麻花钻的刃磨方法(2)麻花钻角度的检测麻花钻角度的检测量方法有以下几种:1)目测法把刃磨好的麻花钻垂直竖在与眼等高的位置上,转动钻头,交替观察两条主切削刃的长短、高低以及后角等,如图3—12所示。
如果不一致,则必须进行修磨,直到一致为止。
2)角度尺检查将游标万能角度尺的一边贴在麻花钻的棱边上,另一边靠近钻头的刃口上,测量刃长和角度,如图3—13所示。
3)在钻削过程中检测若麻花钻刃磨正确,切屑会从两侧螺旋槽内均匀排出,如果两主切削刃不对称,切屑则从主切削刃高的那边螺旋槽向外排出;据此可卸下钻头,将较高的一边主切削刃磨低一些,以避免钻孔尺寸变大。
麻花钻在刃磨时应该注意以下几点:①刃磨时用力要均匀,不能过大,应经常目测磨削情况,随时修正。
②刃磨时,钻头切削刃的位置应略高于砂轮中心平面,以免磨出负后角,致使钻头无法使用。
③刃磨时不要用刃背磨向刀口,以免造成刃口退火。
④刃磨时应注意磨削温度不应过高,要经常用水冷却,以防钻头退火降低硬度,使切削性能降低。
a)b)图3—12 目测法检测图3—13 用角度尺检测a)刃磨正确b)刃磨错误(3)麻花钻的修磨由于麻花钻在结构上存在很多缺点,因而麻花钻在使用时,应根据工件材料、加工要求,采用相应的修磨方法进行修磨。