炼铁厂能源工艺评价
炼铁工艺中的能源消耗与节能技术探索

炼铁工艺中的能源消耗与节能技术探索炼铁工艺是钢铁生产过程中至关重要的一环,同时也是一个高能耗行业。
随着能源资源的紧张和环境污染的加剧,如何减少炼铁工艺中的能源消耗并开展节能技术探索成为了当前的重要课题。
本文将围绕炼铁工艺的能源消耗分析和节能技术探索展开讨论。
一、炼铁工艺中的能源消耗分析在炼铁工艺中,能源消耗主要来自于两方面:一是燃料的消耗,二是电力的消耗。
燃料的消耗包括焦炭、煤炭、天然气等,而电力的消耗则主要用于激活炉料、通风、冷却以及一些辅助设备等方面。
1. 燃料消耗燃料在炼铁生产过程中主要用于冶炼过程中产生高温,以及提供还原、脱氧、燃烧等化学反应所需的热能。
传统的炼铁工艺,在高炉炼铁过程中主要使用焦炭作为还原剂,而焦炭的大量消耗不仅导致能源的浪费,还对环境造成了严重的污染。
因此,如何减少燃料的消耗,提高能源利用效率成为了迫切需求。
2. 电力消耗电力在炼铁工艺中主要用于提供动力和操作设备的供电,如驱动风机、循环水泵、输送带、起重机等。
随着炼铁工艺技术的发展,电力在工艺中的比重越来越大。
同时,炼铁工艺中一些辅助设备的能耗也逐渐增加。
因此,如何减少电力的消耗,实现节能减排成为了必然选择。
二、节能技术探索为了减少炼铁工艺中的能源消耗,许多节能技术不断被引入和应用。
下面将重点介绍一些有效的节能技术。
1. 高炉炼铁节能技术高炉炼铁是传统的炼铁工艺,其能源消耗较高。
为了提高高炉炼铁的能源利用效率,可以采取一系列节能技术措施,如提高燃烧温度、增加炉渣比例、改善燃料燃烧等。
此外,高炉炼铁还可以与其他冶金工艺相结合,进行能量互补,实现能源的综合利用。
2. 氧气炼铁技术氧气炼铁技术是近年来快速发展的一种新型炼铁工艺。
相比传统高炉炼铁,氧气炼铁工艺在能源消耗上具有明显的优势。
氧气炼铁可以减少焦炭的消耗量,增加反应温度,提高还原效果,从而在一定程度上实现了降低能源消耗、提高炼钢效率的目标。
3. 余热利用技术炼铁工艺中产生的大量余热往往未能得到合理利用,导致能源的浪费。
国家节能中心能效评价技术依据

国家节能中心能效评价技术依据钢铁行业(征求意见稿)一、能效评价技术依据的适用范围本技术依据适用于国家节能中心相关工作涉及的钢铁生产企业,主要适应于传统的高炉-转炉生产流程。
对于电炉生产流程及非高炉生产流程评价依据另行制订。
二、能效评价指标钢铁企业生产的工艺流程比较复杂,从流程长短可以分为“长流程”和“短流程”企业。
电炉与转炉流程的吨钢综合能耗指标相差数倍,很难有一个或者某几个指标单独评价一个企业整体能效利用水平。
钢铁企业的能源评价指标较多,有全厂性能源指标如吨钢综合能耗,有焦化、烧结、球团、炼铁、炼钢、轧钢等工序能耗指标,以及焦比、煤比等主要设备能效指标等。
由于钢铁行业中钢铁联合企业吨钢综合能耗受生产工艺流程、物料条件、装备水平、工序完整程度、加工深度、环保因素、能源加工转换、管理水平等多方面因素影响,造成吨钢综合能耗可比性不强。
在行业单位产品能耗限额标准中,钢铁行业未制订吨钢综合能耗的产品限额值,仅有烧结、炼铁、炼钢等几个工序能耗数值。
工序能耗指标用于评价企业某一生产工序的能效利用水平,工序能耗指标虽然也受物料条件、装备大小等因素影响,但用于评价一个工序的水平相对比较准确。
但由于工序之间能耗也互相影响,某一个工序节能不代表一个系统节能,如烧结、球团、焦化工序是为炼铁服务的,烧结、球团、焦化工序能耗不能仅追求本工序能耗达到最低,也要考虑产品质量为高炉服务,应以整个铁前工序能耗能够达到最低为最终目的。
转炉炼钢系统将铁水预处理、转炉冶炼、精炼和连铸放在一个系统考虑,近年来主要考虑的是炼钢冶炼系统能耗;电炉冶炼由于目前多采用不同比例的铁水比,电炉冶炼能耗值波动范围太大,暂不作研究。
钢铁联合企业加工深度不一,但是加工深度到一次材的吨钢综合能耗指标波动在一个合适范围,可以研究到加工深度只到一次材的钢铁企业吨钢综合能耗合理水平。
为此,从系统节能角度出发,充分考虑现有工作基础和能耗数据的可获得性,重点研究3个主要能耗指标:(1)铁前系统(含烧结、球团、焦化和炼铁)能耗折吨铁产品能耗;(2)转炉炼钢系统(含铁水预处理、转炉冶炼、精炼和连铸)折吨坯能耗;(3)高炉-转炉生产流程到一次材的吨钢综合能耗。
钢铁行业先进生产工艺评定结果
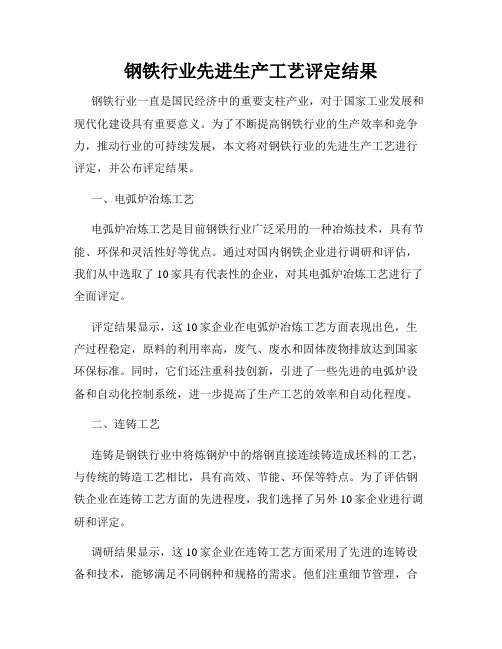
钢铁行业先进生产工艺评定结果钢铁行业一直是国民经济中的重要支柱产业,对于国家工业发展和现代化建设具有重要意义。
为了不断提高钢铁行业的生产效率和竞争力,推动行业的可持续发展,本文将对钢铁行业的先进生产工艺进行评定,并公布评定结果。
一、电弧炉冶炼工艺电弧炉冶炼工艺是目前钢铁行业广泛采用的一种冶炼技术,具有节能、环保和灵活性好等优点。
通过对国内钢铁企业进行调研和评估,我们从中选取了10家具有代表性的企业,对其电弧炉冶炼工艺进行了全面评定。
评定结果显示,这10家企业在电弧炉冶炼工艺方面表现出色,生产过程稳定,原料的利用率高,废气、废水和固体废物排放达到国家环保标准。
同时,它们还注重科技创新,引进了一些先进的电弧炉设备和自动化控制系统,进一步提高了生产工艺的效率和自动化程度。
二、连铸工艺连铸是钢铁行业中将炼钢炉中的熔钢直接连续铸造成坯料的工艺,与传统的铸造工艺相比,具有高效、节能、环保等特点。
为了评估钢铁企业在连铸工艺方面的先进程度,我们选择了另外10家企业进行调研和评定。
调研结果显示,这10家企业在连铸工艺方面采用了先进的连铸设备和技术,能够满足不同钢种和规格的需求。
他们注重细节管理,合理控制凝固过程中的温度和速度,从而保证铸坯质量的良好。
此外,他们还采用了先进的冷却水循环系统和废热回收装置,减少了对水资源的消耗,提高了能源利用效率。
三、转炉冶炼工艺转炉冶炼是钢铁行业中最常用的炼钢方法之一,通过对炼钢过程中的废气和废渣进行综合利用,可以实现资源的高效利用和减少环境污染。
我们挑选了10家转炉企业进行评定,以了解他们在转炉冶炼工艺方面的先进性。
评定结果表明,这些转炉企业在炼钢过程中采取了一系列的技术措施,如合理控制氧气吹吹量、优化炉渣组成、提高炉渣脱磷效果等,从而达到了降低温室气体排放和减少废渣产生的目标。
同时,他们还关注提高转炉炼钢的自动化程度,引进了自动控制系统和智能化设备,提高了生产效率和质量稳定性。
炼铁生产中的能耗优化与节能减排措施

炼铁生产中的能耗优化与节能减排措施能源是现代社会发展的基石,然而在能源有限的情况下,如何优化炼铁生产中的能耗,实现节能减排已经成为了一个迫切的问题。
本文将探讨炼铁生产中的能耗优化与节能减排措施,并提出具体的解决方案。
一、炼铁生产中的能耗现状炼铁生产是消耗能源的重要行业之一,其能耗情况直接关系到国家能源安全和环境保护。
然而,目前我国炼铁企业的能耗水平普遍较高,存在一系列问题。
首先,传统的高炉炼铁工艺存在能源利用率低的问题。
其次,炼铁生产中的废气、废水和废渣等排放物对环境造成了严重的污染。
因此,亟需采取有效的节能减排措施,优化能源利用,降低能耗水平。
二、能耗优化措施1. 提高高炉燃烧效率高炉是炼铁生产的核心设备,提高高炉燃烧效率是降低能耗的关键一步。
可以通过优化燃烧参数、改善高炉炉况、提高燃烧设备的热效率等方式来提高高炉的燃烧效率。
2. 采用先进的炼铁技术传统的高炉炼铁工艺存在能源损失较大的问题,可以考虑采用先进的炼铁技术来降低能耗。
比如,采用高炉煤气发电技术、煤气制氢技术等可以实现能源的全面利用。
3. 引进节能设备与技术在炼铁生产过程中,引进先进的节能设备与技术是降低能耗的重要手段。
比如,可以引进高效节能的燃烧设备、烟气余热回收技术、废气处理设备等来提高能源利用效率。
三、节能减排措施1. 废气治理高炉炼铁过程中产生大量的废气,其中含有大量的烟尘和有害气体。
应建立完善的废气治理系统,采用高效的除尘设备和废气脱硫、脱硝技术,减少废气的排放,降低对环境的影响。
2. 废水处理炼铁生产中的废水含有较高的悬浮固体和重金属等有害物质,对水环境造成较大污染。
应采用生物法、化学法等多种处理技术对废水进行处理,确保排放水质符合相关标准。
3. 废渣综合利用炼铁过程中产生的废渣具有一定的资源价值,应加强废渣的综合利用。
比如,可以将废渣进行回收再利用,用于生产水泥、建材等,减少对自然资源的占用。
四、结语炼铁生产中的能耗优化与节能减排是实现可持续发展的关键之一。
铁合金冶炼工艺中的能耗与能源优化

铁合金冶炼工艺中的能耗与能源优化铁合金作为一种重要的基础材料,在钢铁、有色金属等行业中具有广泛的应用。
铁合金的冶炼工艺对能源的消耗和环境影响日益受到关注。
本文将探讨铁合金冶炼工艺中的能耗问题,并对能源优化提出建议。
铁合金冶炼工艺的能耗分析铁合金的冶炼工艺主要包括炼铁、炼钢和合金化三个阶段。
每个阶段的能耗都有所不同,但总体来说,铁合金冶炼工艺的能耗较高。
炼铁阶段的能耗炼铁阶段是铁合金冶炼工艺中的第一个阶段,主要是将铁矿石还原成铁。
在这个过程中,能耗主要来自于还原剂的制备和炉料的加热。
目前,常用的还原剂有焦炭和煤气。
焦炭的制备过程能耗较高,而且煤气中含有大量的一氧化碳,对环境造成污染。
因此,降低炼铁阶段的能耗是提高铁合金冶炼工艺能源效率的关键。
炼钢阶段的能耗炼钢阶段是将炼铁后的铁水进行精炼,以达到所需的合金成分和性能。
在这个过程中,能耗主要来自于炉料的加热和熔化,以及合金元素的添加。
炉料的加热和熔化需要大量的能源,而且合金元素的添加通常需要高温下的合金化反应,进一步增加了能耗。
因此,炼钢阶段的能耗也是铁合金冶炼工艺中的一个重要问题。
合金化阶段的能耗合金化阶段是将炼钢后的钢水加入各种合金元素,以制备出所需的铁合金。
在这个过程中,能耗主要来自于合金元素的加入和熔化,以及合金化反应的进行。
合金元素的加入通常需要高温下的熔化,而且合金化反应需要一定的能量来驱动。
因此,合金化阶段的能耗也是铁合金冶炼工艺中的一个重要问题。
能源优化的建议针对铁合金冶炼工艺中的能耗问题,本文提出以下能源优化的建议:1.提高能源利用效率:通过改进工艺流程和技术设备,提高能源的利用效率,减少能源的浪费。
例如,可以采用高效燃烧器和炉衬材料,减少能源的损失。
2.优化原料选择:选择合适的原料和还原剂,可以降低能耗和环境污染。
例如,可以采用直接还原铁技术,减少炼铁阶段的能耗。
3.采用先进的技术和设备:通过采用先进的技术和设备,可以提高生产效率和能源利用效率。
炼铁工艺的能源利用效率与环境效益评估
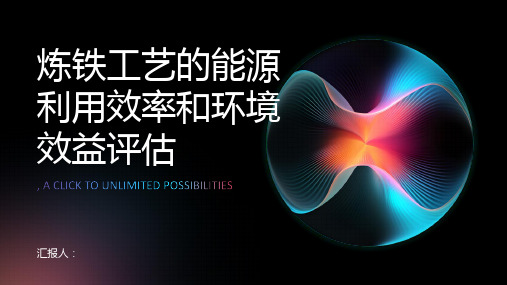
环境效益评估:污染物排放、生态影响、碳排放等指标
案例分析:国内外典型炼铁工艺的能效与环境效益对比分析
国内典型炼铁工艺:高炉炼铁、转炉炼铁、电炉炼铁等
国外典型炼铁工艺:高炉炼铁、转炉炼铁、电炉炼铁等
能效评估:能耗、排放、回收率等指标
不同炼铁工艺的能效与环境效益比较分析
高炉炼铁工艺:能耗高,环境污染严重
炼铁工艺的主要能源消耗:煤炭、焦炭、天然气等
炼铁工艺的能源消耗效率:随着技术的进步,能源消耗效率不断提高
炼铁工艺的能源消耗对环境的影响:煤炭燃烧产生的二氧化碳、二氧化硫等污染物对环境造成严重影响
炼铁工艺的能源消耗比例:煤炭占主导地位,焦炭次之,天然气较少
炼铁工艺的能源利用效率评估方法
提高炼铁工艺能源利用效率的途径
05
加强国际合作,引进国外先进技术和管理经验
06
加强环保宣传教育,提高公众的环保意识
技术建议
加强废气、废水、废渣处理,减少环境污染
提高设备自动化程度,减少人工操作误差
加强能源管理,提高能源利用效率
采用高效节能技术,如余热回收、热泵等
优化工艺流程,减少能源消耗
采用清洁能源,如太阳能、风能等
管理建议
添加标题
推动技术创新,提高炼铁工艺技术水平
添加标题
促进能源结构调整,推动清洁能源发展
提高炼铁工艺能效与环境效益的建议
PART 06
政策建议
01
加强政策引导,鼓励企业采用节能环保技术
04
02
03
加大对炼铁企业的监管力度,确保企业遵守环保法规
提供财政补贴和税收优惠,鼓励企业投资节能环保项目
加强技术研发,推动炼铁工艺的升级换代
电炉炼铁工艺:能耗低,环境污染较小
炼铁过程中的资源利用效率与能源消耗分析

采用先进的生产技术和设备,提高生产效率
加强设备维护和保养,提高设备利用率
提高操作人员的技能和素质,减少操作失误
优化生产流程,减少能源消耗
开发和应用新能源
太阳能:利用太阳能进行炼铁,减少对传统能源的依赖
风能:利用风能进行炼铁,减少对传统能源的依赖
生物质能:利用生物质能进行炼铁,减少对传统能源的依赖
Байду номын сангаас
氢能:利用氢能进行炼铁,减少对传统能源的依赖
03
04
促进技术创新:鼓励企业加大研发投入,推动炼铁技术进步,提高生产效率和环保水平。
加强国际合作:加强与国际组织和其他国家的合作,共同应对全球气候变化和资源短缺问题。
05
06
炼铁行业可持续发展的技术创新和人才培养
炼铁行业可持续发展的实践和案例
提高资源利用效率:通过技术创新和设备改造,提高铁矿石、煤炭等资源的利用率,降低能源消耗。
焦炭利用率的衡量标准:焦炭消耗量与铁产量的比例关系
焦炭的利用率对炼铁过程的影响:提高炼铁效率,降低能源消耗
熔剂的利用率
熔剂的种类:石灰石、白云石等
添加标题
熔剂的作用:降低炉渣熔点,提高炉渣流动性
添加标题
熔剂的用量:根据炉渣成分和温度进行调整
添加标题
熔剂的利用率:通过优化熔剂配比和添加时机,提高熔剂利用率,降低能源消耗
炼铁行业可持续发展的战略和政策
提高资源利用效率:通过技术创新和设备改造,提高铁矿石、煤炭等资源的利用率,降低能源消耗。
发展循环经济:推广废钢回收利用,减少铁矿石开采量,降低环境污染。
01
02
推广清洁能源:鼓励使用天然气、生物质能等清洁能源,减少煤炭消耗,降低二氧化碳排放。
金属冶炼中的能源分析与优化

电能消耗
02
各种设备的运行需要大量电力。
化学能消耗
03
金属提取和分离过程中的化学反应需要消耗相应的化学物质。
能源效率分析
热效率
冶炼过程中热能的利用率,通常以百 分比表示。
化学效率
化学反应过程中原料转化为产品的效 率。
电效率
电能转化为机械能的效率,也以百分 比表示。
能源成本分析
直接能源成本
直接用于金属冶炼的燃料、电力和化学品的费 用。
方案实施
按照优化方案,逐步实施各项措施,包括采购高效设备、改进生产工艺、加强能源管理等,确保优化方案的落地 。
优化效果评估与改进
效果评估
通过对比优化前后的能源消耗数据,评估优化方案的实施效果,包括节能减排的成果、经济效益的提 升等。
改进措施
根据效果评估结果,针对存在的问题和不足,制定改进措施,持续优化能源利用效率和生产工艺。
数据挖掘与分析
利用大数据和人工智能技术,挖掘和分析能源数据,为能源管理 和优化提供决策支持。
能源调度与优化
通过智能化能源管理系统,实现能源的调度和优化,提高能源的 稳定性和可靠性。
绿色低碳的金属冶炼未来发展方向
低碳排放
通过节能减排和可再生能源的应用,降低金属冶炼过程中的碳排 放,实现低碳发展。
资源循环利用
优化过程中的挑战与解决方案
挑战1
高能耗、高污染的传统冶炼工艺 难以改变。解决方案:加强科技 创新,研发更加节能环保的冶炼 技术和设备,逐步替代传统工艺
。
挑战2
企业资金和技术实力有限,难以 承担高额的节能改造费用。解决 方案:政府提供政策支持和资金 补贴,鼓励企业进行节能技术改
造。
挑战3
- 1、下载文档前请自行甄别文档内容的完整性,平台不提供额外的编辑、内容补充、找答案等附加服务。
- 2、"仅部分预览"的文档,不可在线预览部分如存在完整性等问题,可反馈申请退款(可完整预览的文档不适用该条件!)。
- 3、如文档侵犯您的权益,请联系客服反馈,我们会尽快为您处理(人工客服工作时间:9:00-18:30)。
炼铁厂工艺技术评价炼铁厂2012年6月15日(一)炼铁厂生产简介:炼铁厂现有3座1080立方米高炉,分别与2005年11月,2007年8月及12月份投产,有配套的烧结和竖炉工艺。
炼铁厂产能为280万吨/年。
主要产品为炼钢生铁和部分铸造生铁。
(二)高炉主要装备情况装备5#高炉6#高炉7#高炉炉顶气密箱加旋转布料器气密箱加旋转布料器气密箱加旋转布料器除尘重力加布袋除尘器重力加布袋除尘器重力加布袋除尘器热风炉4座顶燃式3座顶燃式3座顶燃式开口机KD-ⅡA型同侧式全液压开口机KD-ⅡA型同侧式全液压开口机KD-ⅡA型同侧式全液压开口机液压炮DT100型矮式泥炮DT100型矮式泥炮DT100型矮式泥炮天车16/5t桥式起重机16/5t桥式起重机16/5t桥式起重机(三)高炉主体参数指标5#高炉6#高炉7#高炉炉容m31080 1080 1080 炉缸直径mm 6150 6150 6150炉腰直径mm 7150 7150 7150炉喉直径mm 4600 4600 4600炉腹角°80.838 80.838°80.838°炉身角°83.388°83.388°83.388°有效高度mm 20398 20700 20700 高径比 2.9 2.9 2.9三、有限公司炼铁厂工艺简介图1:炼铁厂5-7#高炉工艺流程图矿槽称量振动筛返矿焦槽振动筛称量返焦料车净煤气调压阀组布袋除尘器重力除尘器重力灰布袋灰均压煤气渣沟 冲渣池 抓吊 储渣场装车外运干渣厂炼钢铸铁机 铁水罐撇渣器循环水泵制粉喷吹罐鼓风机 热风炉铁块转炼钢高炉本体烧结配料 烧结配料冷却水烧结配料煤气管网正在上水渣微粉微粉项目图2 :喷煤生产工艺流程图(5#高炉):4图3 :喷煤生产工艺流程图(6#、7#高炉):5图4:铸铁工艺流程图67图5:炼铁厂除尘工艺流程图铁水流槽回收车 链带打水 水泵房铁块车电绞 车 铸铁机电绞车铁水罐车铁块铁块库铁模8布袋除尘器布袋灰重力灰 净煤气灰斗叶轮给料机调压阀组高炉 重力除尘器 切断阀净煤气管网均压煤气 淀灰加湿机皮带运输机 斗式提升机螺旋输送机中间仓叶轮给料机球阀烧结配料灰车 除尘灰炉前出铁场电除尘原料电除尘四、2011年4月至2012年6月实际能源消耗指标能源介质单位单耗折算系数能耗(kg标煤/t铁)占总能耗的比例(%)焦碳kg/t 348 0.9714 338.04 81.55无烟煤Kg/t 119.3 0.7143 85.22 20.56烟煤kg/t 62.4 0.7143 44.57 10.75电kwh/t 96.42 0.1229 11.85 2.86水t/t 0.71 0.255 0.18 0.04 高炉煤气回收m3/t -705.24 0.1286 -90.69 -21.88 压缩空气m3/t 2.82 0.04 0.11 0.03 氮气m3/t 89.74 0.1 8.97 2.17氧气m3/t 46.42 0.35 16.25 3.92总能耗414.50 100.001、确定主要能源使用从2011年5月到2012年6月实际能源消耗指标中可以看出,焦炭、煤消耗量分别占总能耗的81.55%、31.31%,其中高炉煤气是炼铁过程中回收的。
因此,将焦炭消耗、煤消耗作为本次工艺技术评价中的主要能源使用进行分析。
2、影响主要能源使用的项目炼铁过程中对焦炭消耗、煤消耗有影响的主要因素为入炉矿品位、富氧量、风温、炉料结构、焦炭质量、煤粉质量、炉温控制等。
9五、指标对比2012年炼铁厂与兄弟单位指标如下表:单位综合入炉品位富氧风温炉料结构焦比煤比烧结球团生矿% % ℃%%%kg/t kg/t普阳52.96 2.62 1185 81 13 6 351 181 文丰55.91 1.47 1171 80 18 1 359 170 唐山德龙55.26 2.25 1194 77 6 17 392 165 邢台德龙54.68 2.2 1160 68 19 13 368 183注: 1、以上数据来源于各厂家的财务报表;数据为2012年1~5月份累计指标。
2、焦比为含焦丁指标。
3、富氧率按计算标准,统一折算。
10六、能耗对比分析与兄弟单位指标对比分析通过与以上兄弟单位较好水平(普阳)相比,炼铁厂入炉焦比高17kg/t,煤比高2kg/t,入炉铁矿品位高1.72%,平均热风温度低25℃,富氧率低0.42%。
A 入炉焦比1、炼铁厂6#高炉炉缸侧壁温度升高,采用钛球护炉,高炉焦比升高7kg/t左右;2、5#高炉热风炉设备陈旧,耐火球在大修期间未全部更换,导致送风风温低约25℃,导致焦比升高3kg/t左右;3、为降低铁前成本我厂采用高煤比操作,煤比达到183kg/t,并且配加55%的烟煤,烟煤热值低,影响焦比约8kg/t;4、炉料结构为68%高碱度烧结矿+19%球团+13%块矿,熟料率比较低,焦比升高10kg/t;5、我厂全部重力灰和布袋灰在烧结矿中配用,造成入炉料减负荷升高,比2011年吨铁上升约1kg,影响焦比约5kg/t;6、品种钢冶炼,我厂生铁含【Si】升高约0.1%,影响焦比约4kg/t;7、为降低铁前成本,我厂配用25%质量较差的低价二级焦炭,导致焦比升高5kg/t。
以上原因导致我厂入炉焦比较高。
B 风温1、5#高炉热风炉设备陈旧,耐火球在大修期间未全部更换,导致送风风温低约20℃;2、6#、7#高炉热风炉由于热风出口质量问题,拱顶温度人为控制;3、我厂热风炉全烧高炉煤气,高炉煤气发热值较低;4、富氧率比普阳低0.42个百分点。
以上原因导致我厂风温较低。
C 炉料结构1、由于烧结与炼铁产能不匹配,不得不配加13%生矿。
2、烧结原料中配用的低品位料主要为印粗,造成高炉炉渣中三氧化二铝含量较高。
3、烧结矿配用重力灰、布袋灰及本地碱粉,增加了入炉料减负荷。
4、整体来看,综合入炉品位偏低,不足55%。
以上原因导致我厂炉料结构不合理。
七、建议及采取措施A 入炉焦比比普阳高17kg/t。
采取措施:1、将>10mm的焦丁回收入炉,目前回收焦丁筛底为14mm,可降低焦比2kg/t;2、对多种护炉钛球进行试验,最终使用对焦比影响较小又不影响护炉效果的品种;3、热风炉采取转炉煤气,可提高风温30℃,可降低焦比3kg/t,此项难度较大;4、烧结产能与炼铁相匹配后,熟料率将提高13%,焦比降低10kg/t;5、采用高热值煤粉喷吹;6、提高入炉品位至55%以上,可降低焦比2.4kg/t;7、煤气利用率较低,平均为41.5%左右,与同行业(45%~50%)还存在一定的差距,主要是上下部调节上还未达到最佳状态。
如以上采取措施均到位,可降低焦比17.4kg/t。
B 风温与文丰相比低25℃。
采取措施:1、根据煤气总量平衡,如有可能热风炉烧炉采用转炉煤气,可提高一区风温20℃。
2、条件允许情况下,适当提高高炉富氧率。
3、优化烧炉制度,提高热工参数,全厂风温提高5℃。
4、热风炉高温区压浆,防止吹开,全厂风温提高5℃。
如以上采取措施均到位,全厂风温可提高30℃。
C 炉料结构(炉料结构为68%高碱度烧结矿+19%球团+13%块矿,)不合理,熟料率及综合入炉品位低。
采取措施:1、下调烧结矿中布袋灰的配加量,一降低入炉碱负荷。
2、提高烧结、球团矿产量,提高熟料率。
3、增大高品位矿粉比例,提高烧结矿品位。
通过以上采取措施改善我厂厂炉料结构和提高综合入炉品位。
八、工艺评价总体来说,炼铁水平主要受限于原燃料条件,不存在技术问题,我厂技术水平应在全国同类型企业的中等水平。
针对炼铁工艺流程,解决目前所有矛盾的最好办法是改善原料料条件,另外还必须做到精心操作,加强生产和设备的管理水平,提高作业率,避免事故;完善生产对设备的操作点检,及时发现设备异常,减设备故障;对相关设备制定周期性管理;严格执行设备操作标准,减少因操作原因造成的设备损坏,点检进行技术业务培训,做到事前预防而不是事后抢修。
九、能源回收利用方面:冲渣水余热利用方面,进在炼铁渣粒化过程中,产生大量温度为90℃左右的冲渣热水。
不但其中的热能未充分利用,而且如果利用高温热水重新进行冲渣,更容易汽化产生大量蒸汽,带走更多粉尘。
不但需要大量的补充水,而且蒸汽对周围的设备产生腐蚀作用。
如果经过高炉冲渣口冲渣后,冲渣热水回流到热水池,经过预处理后进入扩容器,减压蒸发后,得到低压饱和蒸汽和热水。
经扩容并降温的热水经管道由水泵抽出扩容器并输送至冷水池。
经扩容后的饱和蒸汽、进入汽水分离器,除去所含水分,得到湿度为0.5%的饱和蒸汽。
蒸汽进入汽轮机,带动汽轮机转动做功,并带动发电机发电。
蒸汽经过汽轮机做功后排出,进入冷凝器,经过冷却水冷凝后,变成凝结水输出冷凝器,由凝结水泵输送至冷水池,从而得到温度在50℃以下的冷水,并且产生额外的电能,一旦可以实施成功则可以有效的进行能源再利用,降低生产成本。
炼铁厂2012-7-20。