第一三章炉窑分类及玻璃制作
玻璃生产及制造含(池窑类型)
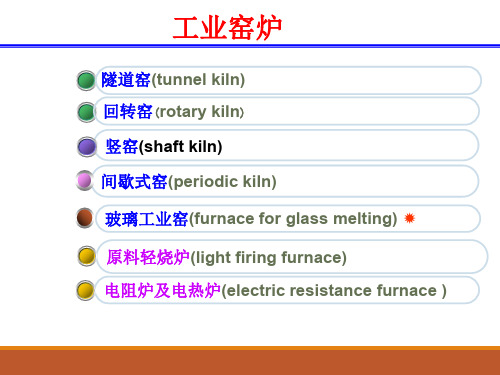
1.投料机
(a)螺旋式投料机 (b)垄式投料机 (c)振动式投料机
(d)辊筒式投料机 (e)弧毯式投料机 (f)倾斜式投料机
(a)螺旋式投料机 (c)振动式投料机
(b)垄式投料机 (d)辊筒式投料机
(e)弧毯式投料机
(f)倾斜毯式投料机
目前,国内、外大型的浮法玻璃池窑,已普遍采 用弧毯式投料机和倾斜毯式投料机。
玻璃液澄清阶段
玻璃液形成阶段后期,整个体系内包含大量气泡和灰泡(小气泡)。从玻 璃液中除去肉眼可见的气体杂质物,消除玻璃液的气孔组织阶段称为澄清 阶段。当温度升高时,玻璃液黏度迅速下降,使得大量气泡逸出。因此, 澄清阶段必须在更高温下进行。
玻璃液均化阶段 玻璃液形成后,各部分组分和温度并不均一。为消除这种不均匀,必须 进行均化处理。均化作用主要依靠扩散和对流完成,高温是必要条件, 高温降黏可以使得扩散加强。此外,搅拌也是一种均匀性的办法。均化 与澄清二者也没有特别明显的界限,可以看做一面澄清一面均化,而均 化往往在澄清之后。
2.投料池
在实际生产中,投料池型侵蚀的情况是十分严重的,尤其是在投料池的拐角 处(这也是玻璃池窑中最容易损坏的部位之一),这是由于在拐角处两面受热, 散热面小,冷却条件差,又经常受到配合料的强烈侵蚀和机械磨损的作用。 所以,投料池拐角处需要用高质量的耐火材料来砌筑。
3.前脸墙:是指正面投料时,投料口或投料池上部的挡墙。
玻璃液冷却阶段
澄清均化往往是高温下进行,此时玻璃液黏度太低不易成型,必须提高黏度以 有利于其成型,所以玻璃液需要冷却到成型温度。一般情况成形温度比澄清温 度低200~300℃。
以上五个阶段的作用和变化机理各有特点,但又彼此密切联系。在实际的 熔制过程中各个阶段之间并没有明显的界限,有些阶段是同时或者部分同时进 行的。
玻璃的熔制及熔窑.ppt
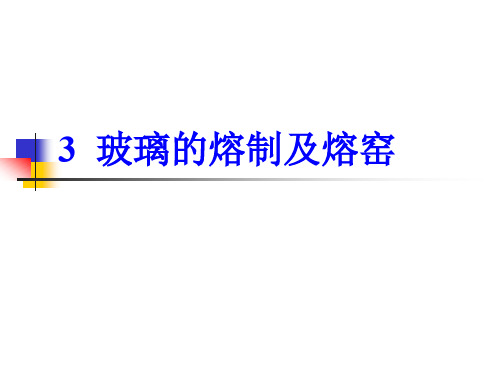
编篮式是连续通道式格子体结构的改进形式,由 于格子砖的两个端面都是受热面,所以其单位格 子体体积的受热面积最大,而且稳定性也好。
十字形格子砖是一种新型格子砖,是AZS电熔浇 注砖,耐高温侵蚀性能好,容积密度大、热容量 高、热导率大等特性。蓄热效能好,周期温度波 动小,是一种理想的格子体。
3 玻璃的熔制及熔窑
3.2.2 热源供给及余热回收部分
3.2.2.1 热源供给 主要指小炉和燃烧喷嘴。 小炉是玻璃熔窑的重要组成部分,是使燃料和
空气预热、混合、组织燃烧的配置。 (1)燃油与天然气小炉 (2) 燃煤气小炉
A.小炉结构:应保证火焰有一定长度、亮度、刚 度、角度,有足够的覆盖面积,不发飘,不分层, 还要满足窑内所需的温度和气氛的要求。
e.炉条碹
炉条是承受蓄热室格子体重力的砖材结构。实际上 也是拱碹结构,是由单一的碹砖砌成的一条一条拱 碹,条与条之间留空以通气体,俗称炉条碹。
炉条碹是承受格子体重力的拱碹,上面码砌格子砖, 因此拱碹上面必须找平。
找平的方法有几种: ①在拱碹的弧形上面用爬碴砖砌平 ②直接用上面平直而下面弧形的碹砖砌成。
玻璃池窑那些部位耐火材料受到的侵蚀 最严重?举例说明蓄热室格子体耐火材 料的配置方案?
A 连通式蓄热室 熔窑一侧小炉下面的空气蓄热室为连通的一个 室,煤气蓄热室也为连通的一个室。 气流分布不均,容易形 成局部过热使格子砖很快烧损,目前已不再使用。
B 分隔式蓄热室 熔窑一侧蓄热室以每个小炉分成若干个互不相通的独立室, 气体分配分别由各分支烟道上的闸板调节,并分别与煤气及 空气支烟道上的闸板调节,并分别与煤气及空气支烟道相通。 其结构特点是气体分配调节方便,热修条件较好,但分隔墙 占据较多空间,减少了格子体的有效体积。是最普遍采用的 方式之一.2.2 余热回收部分
玻璃窑炉生产工艺
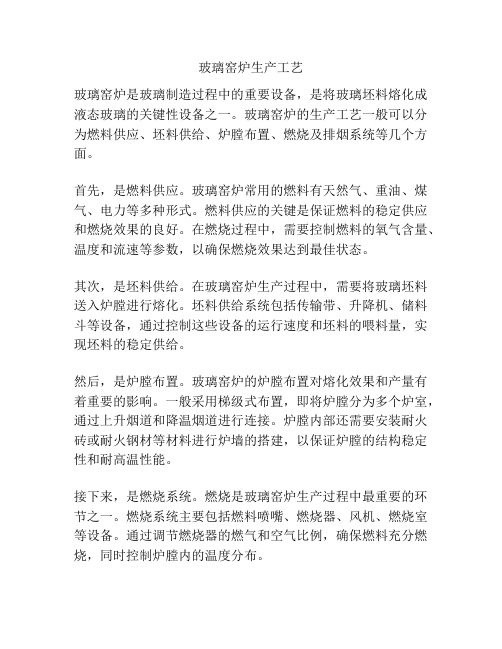
玻璃窑炉生产工艺玻璃窑炉是玻璃制造过程中的重要设备,是将玻璃坯料熔化成液态玻璃的关键性设备之一。
玻璃窑炉的生产工艺一般可以分为燃料供应、坯料供给、炉膛布置、燃烧及排烟系统等几个方面。
首先,是燃料供应。
玻璃窑炉常用的燃料有天然气、重油、煤气、电力等多种形式。
燃料供应的关键是保证燃料的稳定供应和燃烧效果的良好。
在燃烧过程中,需要控制燃料的氧气含量、温度和流速等参数,以确保燃烧效果达到最佳状态。
其次,是坯料供给。
在玻璃窑炉生产过程中,需要将玻璃坯料送入炉膛进行熔化。
坯料供给系统包括传输带、升降机、储料斗等设备,通过控制这些设备的运行速度和坯料的喂料量,实现坯料的稳定供给。
然后,是炉膛布置。
玻璃窑炉的炉膛布置对熔化效果和产量有着重要的影响。
一般采用梯级式布置,即将炉膛分为多个炉室,通过上升烟道和降温烟道进行连接。
炉膛内部还需要安装耐火砖或耐火钢材等材料进行炉墙的搭建,以保证炉膛的结构稳定性和耐高温性能。
接下来,是燃烧系统。
燃烧是玻璃窑炉生产过程中最重要的环节之一。
燃烧系统主要包括燃料喷嘴、燃烧器、风机、燃烧室等设备。
通过调节燃烧器的燃气和空气比例,确保燃料充分燃烧,同时控制炉膛内的温度分布。
最后,是排烟系统。
排烟系统主要负责排除炉膛内产生的废气和烟尘,保证炉膛内的正常工作环境。
排烟系统包括烟道、风机、过滤器等设备,通过控制风机的运行速度和过滤器的过滤效果,实现对炉膛内废气和烟尘的有效处理与排除。
总结起来,玻璃窑炉的生产工艺包括燃料供应、坯料供给、炉膛布置、燃烧及排烟系统等多个环节。
通过合理的控制和调节,可以实现玻璃窑炉的高效运行,保证玻璃生产的质量和产量。
玻璃窑的分类
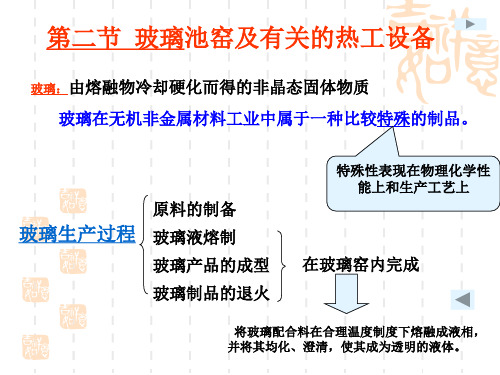
耳池:布置在平板玻璃两侧、与窑池相同、向外突出的长方形或正方形小池
耳池处玻璃液温度较低,其处玻璃液横向流动加强,对玻璃液流能够起到调 节和澄清作用
3.冷却部
作用:进一步均化玻璃液,将温度降低到一个合理的范围,
分配玻璃液到各个供料通道。
平板、压延、浮法 为矩形结构
结构形式
日用、医用、化工等成形与冷却 合为一体,即供料槽
国内浮法玻璃能耗为7500kJ/kg玻璃液,而国际知名公司平均水平为
玻璃液的分隔装置
卡脖作用:减少流向冷却部的热气流
和玻璃液的对流量,以及降低熔化部
作用:1)使澄清好的玻璃液迅速冷却
气体向冷却部的辐射传热量和溢流量。
2)挡住液面上的未熔化的砂粒和沧渣 其目的都是为了使玻璃液通过卡脖后
3)调节玻璃的流量
能用较小的冷却面积就使其冷却下来。
4)减少玻璃液从冷却区向熔化区回流
结构
上部空间:起冷却作用。 下部空间:起供料、分配作用。
4、分隔装置
将玻璃池窑的熔化部和冷却部之间分隔
包括玻璃液的分隔装置和气体空间的分隔装置
气体空间分隔装置:作用:减小熔化部高温火焰对冷却部的影响
1)矮碹分隔式 特点:矮碹处的下胸墙比较低,但还有一定空间(称为开度)。
这种分隔效果较差,如果要想提高分陋效果,还要配合卡脖。
料不均习
投料池:突出于窑池外和池窑相通的矩形小池,
组成
上平面与窑池上平面平行。
C 结构
上挡墙:又称前脸墙 处于投料池与池窑连接处 的上方 形状为L形。
投料池:用来集中配合料,摊平配合料并与使
作用
配合预热到一定的温度。
投
前脸墙:阻挡火焰不外溢,降低投料口的环境温度。
第一、三章炉窑分类及玻璃制作
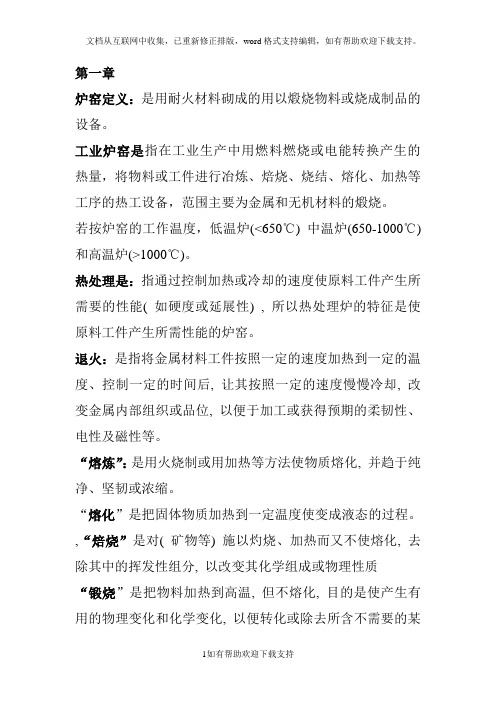
第一章炉窑定义:是用耐火材料砌成的用以煅烧物料或烧成制品的设备。
工业炉窑是指在工业生产中用燃料燃烧或电能转换产生的热量,将物料或工件进行冶炼、焙烧、烧结、熔化、加热等工序的热工设备,范围主要为金属和无机材料的煅烧。
若按炉窑的工作温度,低温炉(<650℃) 中温炉(650-1000℃)和高温炉(>1000℃)。
热处理是:指通过控制加热或冷却的速度使原料工件产生所需要的性能( 如硬度或延展性) , 所以热处理炉的特征是使原料工件产生所需性能的炉窑。
退火:是指将金属材料工件按照一定的速度加热到一定的温度、控制一定的时间后, 让其按照一定的速度慢慢冷却, 改变金属内部组织或品位, 以便于加工或获得预期的柔韧性、电性及磁性等。
“熔炼”:是用火烧制或用加热等方法使物质熔化, 并趋于纯净、坚韧或浓缩。
“熔化”是把固体物质加热到一定温度使变成液态的过程。
,“焙烧”是对( 矿物等) 施以灼烧、加热而又不使熔化, 去除其中的挥发性组分, 以改变其化学组成或物理性质“锻烧”是把物料加热到高温, 但不熔化, 目的是使产生有用的物理变化和化学变化, 以便转化或除去所含不需要的某种物质。
第三章玻璃熔制过程:硅酸盐形成阶段、玻璃液形成、玻璃液澄清、玻璃液均化、玻璃液冷却阶段。
横焰窑窑内的火焰流动方向是从窑的一侧流向另一侧,与玻璃流动的方向垂直,用蓄热室作为余热回收设备。
纵焰窑窑内的火焰流动方向与玻璃流动方向平行,用换热器作为余热回收设备。
玻璃池窑按生产过程的连续性分类可分为连续性窑和间歇式窑。
连续性窑:玻璃生产的各个阶段是在窑内的不同部位同一时间依次进行的,窑的温度制度是稳定的。
间歇式窑:玻璃生产的各个阶段是在窑内的同一部位不同时间依次进行的,窑的温度制度是变动的。
玻璃池窑由玻璃熔制、热能供给、排烟供气、余热回收四部分组成,沿长度方向可分熔化部(包括熔化带和澄清带)、冷却部和成型部,耳池是布置在熔窑两侧与窑池相通且凸出于窑池以外的矩形小池,一般成对设置在卡脖前后,其作用是加强玻璃液的横向对流,对玻璃液流起调节作用。
玻璃球窑之窑炉的结构和熔制

玻璃球窑之窑炉的结构和熔制一、球窑的种类1.E玻璃球窑生产E玻璃成分的窑炉被称为E玻璃球窑。
适合的窑型有:蓄热式马蹄焰窑;蓄热式横火焰窑;换热式单元窑。
其中单元窑能较好控制玻璃质量,但在我国玻璃球生产初期,国内缺少高热值燃油及煤气,燃烧器和金属换热器方面的技术落后,因此实际上单元窑从没有用于生产玻璃球。
横火焰窑生产的玻璃质量相对较好,但因蓄热式横火焰窑池宽度一般要求大于4mm,以保证燃烧完全和窑炉热效率高。
这样,横火焰窑的熔化面积较大,使制球机半圆型工作池的布置受到限制,因此这种窑型的使用也很少。
但可以认为,随着制球机的改进,以及能源供给的多样化,采用横火焰窑还是有一定应用前景的。
马蹄焰窑至今仍是国内制造E玻璃球的首选窑型。
2.C玻璃球窑生产C玻璃成分的窑炉被称为C玻璃球窑,C玻璃球窑也以采用马蹄形火焰窑为主。
过去4台制球机以下的C玻璃球窑曾采用过双碹窑。
应该说单元窑和横火焰窑同样也适用于C玻璃球窑,但由于如前所述的原因,实际生产中从未采用。
3.电熔球窑适合于小规模特种成分玻璃球或玻璃块的生产。
二、马蹄焰球窑结构设计1.结构尺寸(1)熔化面积。
窑炉的熔化率主要取决于熔化温度,因为中碱和无碱玻璃球窑的熔制温度比较高,如果进一步提高熔化温度来提高熔化率,会加速对耐火材料的侵蚀,降低球质和影响炉龄。
而采取鼓泡和电助熔技术可以相应提高中下层玻璃温度,促进玻璃的均化,并且提高熔化率。
(2)熔池长宽比。
长宽比越大,玻璃原料从熔化到澄清的行程也大,这有利于玻璃质量的控制和提高,而长宽比又受到小炉结构设计、火焰长度及拐弯要求的限制。
采用高热值燃料的球窑池长可达到10mm,所以可选择较大的长宽比。
而采用低热值燃料的球窑应选择较小的长宽比。
一般长宽比选用范围为1.4—2.0。
(3)池深。
池深不仅影响到玻璃液流和池底温度,而且影响玻璃液的物理化学均匀性以及窑炉的熔化率。
一般池底温度在1200—1360℃之间较为合适。
玻璃熔制及熔窑---熔窑1

L形吊墙结构
玻璃的池窑
(浮法玻璃熔窑各部分结构尺寸)
L形吊墙结构(a.45度 b.30度)
玻璃的池窑
(浮法玻璃熔窑各部分结构尺寸)
L形吊墙结构
玻璃的池窑
(浮法玻璃熔窑各部分结构尺寸)
L型吊墙结构:由多组耐热钢件制作吊挂单体组合拼装而成, 可任意组合,直墙部分采用高质量的硅砖,外墙采用陶瓷纤维 毡进行保温,鼻端部分采用烧结莫来石砖(或烧结AZS)。 特点:结构稳定牢固,安全可靠;可以设计为宽投料池,实 现薄层投料;鼻部的伸出部分复盖在配合料上,起预熔作用, 减轻窑内的粉尘飞扬;开度小,密封好,改善工作环境;鼻 区前端设有水包,可以将高料刮平,同时起冷却、密封作用。
玻璃的池窑
(浮法玻璃熔窑各部分结构尺寸)
碹碴:用优质硅砖或钢碹碴(保证吹冷却风),也可以采 用与火焰接触部分用硅砖,外面用钢材。 胸墙:重力由挂钩砖传递到托板,再到下巴掌铁,通过工 字钢立柱传到窑底次梁上。注意防止池壁砖侵蚀后胸墙下 倾和避免火焰长时烧胸墙。 胸墙与大碹之间有的采用上间隙砖密封,以保护大碹的碹 碴和碹碴角铁。 材质:硅砖---厚度450mm或500mm; 电熔刚玉砖 胸墙高度:燃发生炉煤气为800-900mm 燃油-----1500~2000mm
玻璃的池窑
(浮法玻璃熔窑各部分结构尺寸)
钢结构: 作用:将砖结构支撑,架设、固定,以保证窑体稳定安全。 钢结构包括:立柱、拉条、碹碴顶铁、上下巴掌铁和拉杆、 胸墙托板、池壁顶铁、立柱固定角钢、扁钢、次梁、主梁 等。 例如:窑两侧的立柱:支撑大碹和胸墙,顶住池壁受玻璃 液的横推力,自身又固定在窑底横向次梁或纵梁上,上面 用拉条拉住。 注意:熔化部的火焰空间还有各种操作孔,如测压孔、看 火孔测温孔等。
玻璃窑简介

Ⅳ
小炉
熔 化池
火焰 空间 花格 墙 工 作池
供料 道
油喷 嘴
流液 洞
蓄热式池窑立剖面图
玻璃窑炉
(4)换热式双碹池窑: F<20m2,也有>30m2,纵焰。烧煤、重油、
天然气等。 优点:与单碹池窑相比,窑顶散热小,炉温
较高,窑内温度分布均匀且稳定。 缺点:砌筑费时,内碹易被高温和粉料蚀损,
与蓄热式比热效率低,换热室易堵,易漏 气。
缓慢 煤炭 飞跃 高热值 持续 高热值
1920~1945年池窑 1945~1960年池窑 1960~至今池窑
窑龄
几个月
0.5年~1.0 年 1~2年 3~4年 7~8年
玻璃窑炉
1.1.2 池窑的几项主要技术指标 (1)熔化率k 窑池每平方米面积上每天熔制的玻璃液量。 t /(m2 ·24h)。 (2)燃料单位消耗量 熔化一吨玻璃液消耗的燃料重量(或体积)。
kg燃料/ t玻璃或m3 / t玻璃液。
玻璃窑炉
(3)有效热效率 (用于玻璃熔制的耗热量 / 单位耗热量)% (4)窑龄和周期熔化率 连续生产的时间。以年为单位。 周期熔化率=窑龄×熔化率(t/ m2 )
玻璃窑炉
1.1.3 玻璃窑炉现状
截止2008年我国玻璃行业约拥有玻璃窑 炉4000~5000座,生产各种玻璃 2800~3500万吨,耗用能源(主要燃料为 煤炭、重油、天然气及电等)折合标准 煤1700~2800万吨。
焰空间分隔
墙等.
形式
全分隔 完全分隔
玻璃窑炉
1.2.1 熔窑分类(3)
玻璃液分 流液洞 流液洞 隔形式 无流液洞
窑产量 大型>150t;中型: 50~100t;小型
窑的规模
- 1、下载文档前请自行甄别文档内容的完整性,平台不提供额外的编辑、内容补充、找答案等附加服务。
- 2、"仅部分预览"的文档,不可在线预览部分如存在完整性等问题,可反馈申请退款(可完整预览的文档不适用该条件!)。
- 3、如文档侵犯您的权益,请联系客服反馈,我们会尽快为您处理(人工客服工作时间:9:00-18:30)。
第一章
炉窑定义:是用耐火材料砌成的用以煅烧物料或烧成制品的设备。
工业炉窑是指在工业生产中用燃料燃烧或电能转换产生的热量,将物料或工件进行冶炼、焙烧、烧结、熔化、加热等工序的热工设备,范围主要为金属和无机材料的煅烧。
若按炉窑的工作温度,低温炉(<650℃) 中温炉(650-1000℃)和高温炉(>1000℃)。
热处理是:指通过控制加热或冷却的速度使原料工件产生所需要的性能( 如硬度或延展性) , 所以热处理炉的特征是使原料工件产生所需性能的炉窑。
退火:是指将金属材料工件按照一定的速度加热到一定的温度、控制一定的时间后, 让其按照一定的速度慢慢冷却, 改变金属内部组织或品位, 以便于加工或获得预期的柔韧性、电性及磁性等。
“熔炼”:是用火烧制或用加热等方法使物质熔化, 并趋于纯净、坚韧或浓缩。
“熔化”是把固体物质加热到一定温度使变成液态的过程。
,“焙烧”是对( 矿物等) 施以灼烧、加热而又不使熔化, 去除其中的挥发性组分, 以改变其化学组成或物理性质
“锻烧”是把物料加热到高温, 但不熔化, 目的是使产生有用的物理变化和化学变化, 以便转化或除去所含不需要的某种物质。
第三章
玻璃熔制过程:硅酸盐形成阶段、玻璃液形成、玻璃液澄清、玻璃液均化、玻璃液冷却阶段。
横焰窑窑内的火焰流动方向是从窑的一侧流向另一侧,与玻璃流动的方向垂直,用蓄热室作为余热回收设备。
纵焰窑窑内的火焰流动方向与玻璃流动方向平行,用换热器作为余热回收设备。
玻璃池窑按生产过程的连续性分类可分为连续性窑和间歇式窑。
连续性窑:玻璃生产的各个阶段是在窑内的不同部位同一时间依次进行的,窑的温度制度是稳定的。
间歇式窑:玻璃生产的各个阶段是在窑内的同一部位不同时间依次进行的,窑的温度制度是变动的。
玻璃池窑由玻璃熔制、热能供给、排烟供气、余热回收四部分组成,沿长度方向可分熔化部(包括熔化带和澄清带)、冷却部和成型部,
耳池是布置在熔窑两侧与窑池相通且凸出于窑池以外的矩形小池,一般成对设置在卡脖前后,其作用是加强玻璃液的横向对流,对玻璃液流起调节作用。
锡槽长度的确定锡槽主体包括槽底、锡槽的长度由拉引量、拉引速度、热平衡自动化水平的高低等因素决定。
一般来说,拉引量越大,速度越快,玻璃所带走的热量越多,当出口温度一定时,要加大锡槽长度;拉引量越小,速度越慢,玻璃所带走的热量越少,当出口温度一定时,锡槽长度可以缩短。
蓄热室工作原理:蓄热室是周期性工作。
烟气从熔窑的一侧小炉排出,流经蓄热室时,将热量传给蓄热室内的格子砖,格子砖的温度升高;换向后,空气或煤气流经已被加热过的格子砖进行加热;同时烟气从另一侧小炉排出,加热另一侧蓄热室的格子砖。
每隔一定的时间(即一个周期)换向一次,就这样周而复始地进行,所以蓄热室必须成对配置。
玻璃池窑的工作原理指玻璃液的流动和热交换。
(1)玻璃液的流动
玻璃液流动的原因之一是投料机的推力和玻璃成型的拉引力的作用,因而产生的玻璃液流称为成型流。
玻璃液流动的另一个主要原因是窑炉内温差的存在。
沿窑炉的横向,因池壁向外界环境散热,所以中间温度高,两边温度低;沿窑池的深度方向,因玻璃液是不良导体,上
层玻璃液贴近炽热的火焰,所以上层玻璃液温度高于底层玻璃液。
玻璃液内部温度差的存在引起了密度差,造成玻璃液的流动。
按流动方向可分为纵向流、横向流和回旋流。
①纵向流:热点向投料池和成型部的纵向流动。
从热点到投料口的温差形成了投料回流,从热点流向投料池的高温玻璃液在料堆下面不断地将热量传给料堆,料堆熔化后密度增大而下沉,汇入从热点回流来的玻璃液中,下沉到某一深度后,又随深层玻璃液流流向热点,这部分玻璃液流到热点后又分为两部分,一部分仍参与到投料回流中,另一部分与从成型部流回来的玻璃液汇合形成成型流。
从热点到成型部的温度差形成成型流。
在成型设备中,一部分玻璃液成型,而其中大部分由于温度下降而下沉,又流回热点处。
在回流的过程中被加热,温度升高,再与新熔成的玻璃液汇合。
②横向流沿池窑横向,中间接受火焰热量多,两侧接受火焰热量少。
又由于两侧玻璃液接触池壁,向外散热,使玻璃液产生温度差,形成了表层由中心向两侧流动,深层由两侧向中心流动的横向流。
③回旋流由于纵向流和横向流相互作用,结果形成了回旋流,玻璃液在流动过程中,在卡脖、耳池、流液洞等处都会产生回旋流。
泡界限控制在正常作业下,投料机将料堆向前推进的力和从热点相反方向来的回流建立了平衡。
料堆前进速度很慢,料堆的边缘只能移动到某一位置上,从窑池的液面可以看到一条整齐清晰的分界线,这就是泡界限,一侧液面有很多泡沫,一侧象镜子一样明亮。
要保持清晰稳定的泡界限,最主要是明确热点。
若泡界限与投料口太近,则料层面积小,接受上面热辐射量减小,熔化速度减慢,在投料量不变的情况下,熔化就不充分;若泡界限远移,就会使料堆占据面积加大,虽然料堆上层熔化速度加快,但料堆下层熔化并未跟上,含有未熔化完全的石英砂粒的泡沫区太远,热点模糊,容易跑料。
玻璃的退火可分为两个主要过程:一是内应力的减弱和消失,二是防止内应力的重新产生。
玻璃的应力玻璃内部因存在温度差而产生的应力称为热应力,热应力可分为暂时应力和永久应力。
(1)暂时应力成型后弹性状态的玻璃由于导热性差,在冷却过程中,其内外层之间会产生温度梯度,靠近表面的外层温度较内层温度低,外层有收缩趋势,但温度较高的内层却予以阻止。
所以在玻璃冷却时,玻璃的外层受张应力,内层受压应力;反之,在加热时,玻璃外层受压应力,内层受张应力。
如果玻璃中的温度梯度消失,玻璃的内外层温度一致,则上述应力随之消失,这种取决于温度梯度的应力称为暂时应力。
暂时应力只存在于弹性变形温度范围内,也就是在玻璃应变温度以下存在温度梯度时才产生,它的大小取决于玻璃内的温度梯度和玻璃的膨胀系数。
2、永久应力:如果玻璃在较高温度下(塑性状态)冷却,同样,由于它的传热较差,表面温度低,内层温度高,在内外层间产生温度梯度。
但在塑性状态下,玻璃内层质点可以作若干位移,内应力由于这种位移而抵消,因而内应力并不产生。
玻璃的退火原理:玻璃的退火,就是把具有永久应力的玻璃制品重新加热到玻璃内部质点可以移动的温度,利用质点的位移使应力分散(称为应力松弛)来消除或减弱永久应力。
应力松弛速度在很大程度上取决于玻璃温度,温度越高,松弛速度越快。
玻璃的退火过程与退火制度
玻璃的退火过程分为四个阶段。
(1)加热阶段玻璃制品成型后,在高于退火温度时直接送入退火窑进行退火,称为一次退火;制品冷却后,再加热到退火温度进行退火称为二次退火。
(2)保温阶段将玻璃保持在退火温度上限附近,以消除玻璃的永久应力,使玻璃的整体温度均匀。
(3)慢冷阶段退火区域属于慢冷却阶段,慢冷速度一般为2-10℃/min。
4)快冷阶段在退火温度以下,冷却速度一般为15-15℃/min。