工件的定位和机床夹具2
合集下载
机械加工工艺规程设计—机床夹具与工件定位

(3)夹紧元件:是执行夹紧的最终元件,直接与工 件接触的元件。如各种螺钉、压板等。
一般情况把夹紧元件和中间传动机构统称为夹 紧机构。有的时候以上三者也会混在一起,很难区 别。
对夹紧装置的基本要求
1) 夹紧时应保证工件的定位,而不能破坏工件的定位。 2) 夹紧力的大小应适宜,既要保证工件在整个加工过程 中位置稳定不变,还不能产生振动、变形和表面损伤。 3) 应根据生产类型设计相应的夹紧机构。 4) 为防止夹紧后自动脱开,夹紧机构须具备良好的自锁 性能。
只考虑切削力(或切削矩)对夹紧的影响,并假设工艺系 统是刚性的,切削过程是稳定不变的,然后找出加工过程中对 夹紧最不利的状态,按静力平衡原理求出夹紧力,最后乘上安 全系数(粗加工取2.5-3,精加工取1.5-2)。
在实际夹具设计中,对于夹紧力的大小并非所有情况都要 用计算确定。如手动夹紧用经验法或类比法。
有些重、大、复杂的工件,往往先在待加 工处划线,然后装上机床,按所划的线进行找 正定位。
适用场合:生产批量较小,毛坯精度较低, 以及大型工件等不宜使用夹具的粗加工中。图4-6 工件划线找正装夹工件的装夹方法
2.机床专用夹具装夹法 所谓机床专用夹具,是 指为某零件的某道工序而专门设计制造的夹具。
2)经验类比法。前面说过,精确计算夹紧力的大小是件很 不容易的事,因此在实际夹具设计中,有时不用计算的方法 来确定夹紧力的大小。如手动夹紧机构,常根据经验或用类 比的方法确定所需夹紧力的数值。但对于需要比较准确地确 定夹紧力大小的,如气动、液压传动装置或容易变形的工件 等,仍有必要对夹紧状态进行受力分析,估算夹紧力的大小。
图4-20 辅助支承应用 1—加工面 2—辅助支承
图4-21 推式辅助支承 1—支承滑柱 2—推杆 3—半圆键 4—手柄 5—钢球
一般情况把夹紧元件和中间传动机构统称为夹 紧机构。有的时候以上三者也会混在一起,很难区 别。
对夹紧装置的基本要求
1) 夹紧时应保证工件的定位,而不能破坏工件的定位。 2) 夹紧力的大小应适宜,既要保证工件在整个加工过程 中位置稳定不变,还不能产生振动、变形和表面损伤。 3) 应根据生产类型设计相应的夹紧机构。 4) 为防止夹紧后自动脱开,夹紧机构须具备良好的自锁 性能。
只考虑切削力(或切削矩)对夹紧的影响,并假设工艺系 统是刚性的,切削过程是稳定不变的,然后找出加工过程中对 夹紧最不利的状态,按静力平衡原理求出夹紧力,最后乘上安 全系数(粗加工取2.5-3,精加工取1.5-2)。
在实际夹具设计中,对于夹紧力的大小并非所有情况都要 用计算确定。如手动夹紧用经验法或类比法。
有些重、大、复杂的工件,往往先在待加 工处划线,然后装上机床,按所划的线进行找 正定位。
适用场合:生产批量较小,毛坯精度较低, 以及大型工件等不宜使用夹具的粗加工中。图4-6 工件划线找正装夹工件的装夹方法
2.机床专用夹具装夹法 所谓机床专用夹具,是 指为某零件的某道工序而专门设计制造的夹具。
2)经验类比法。前面说过,精确计算夹紧力的大小是件很 不容易的事,因此在实际夹具设计中,有时不用计算的方法 来确定夹紧力的大小。如手动夹紧机构,常根据经验或用类 比的方法确定所需夹紧力的数值。但对于需要比较准确地确 定夹紧力大小的,如气动、液压传动装置或容易变形的工件 等,仍有必要对夹紧状态进行受力分析,估算夹紧力的大小。
图4-20 辅助支承应用 1—加工面 2—辅助支承
图4-21 推式辅助支承 1—支承滑柱 2—推杆 3—半圆键 4—手柄 5—钢球
第4章定位原理和机床夹具设计2
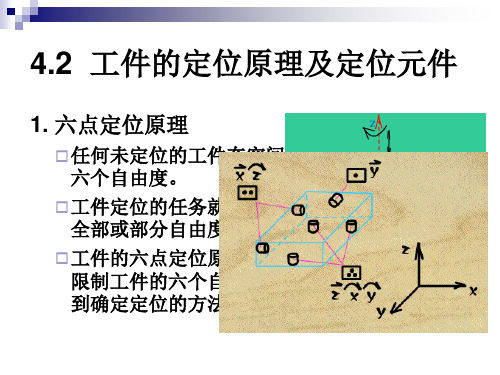
间隙配合心轴
H7 g 6( f 7)
Z
△Z≠ 0 △Y≠ 0
Y
圆柱心轴
X
y
4.2 工件的定位原理及定位元件
3.工件以外圆柱面定位
V形块 定位套 半圆套 支承定位
3.工件以外圆柱面定位
V形块
固定V形块 活动V形块 长V形块 短V形块
3.工件以外圆柱表面定位
3.工件以外圆柱表面定位
定位套
工件以外圆定位的定位套
yz
销2
x y
销1
y 0
x
支承平面
z x y
(3) 过定位
案例4 一面两销定位方案
B 削边销
(3) 过定位
z
案例4 一面两销定位方案
z x y
销1 削边销
y 0
x
支承平面
z x y
(3) 过定位
案例5
滚齿加工的定位方案
x y x y
待加工 的齿轮
z x y
(3) 过定位
案例5
滚齿加工的定位方案
(1)正确的定位 工件定位面与夹具定位元件的定位工 作面相接触或配合来限制工件的自由度, 二者一旦脱离接触或配合,则定位元件就 丧失了工件自由度的作用。
2.应用六点定位原理应注意的问题
(2)一个定位支撑点仅限制一个自由度:原 则上不超过六个。 (3)分析定位支撑点的定位作用时,不考虑 力的影响
2.应用六点定位原理应注意的问题
常用的定位元件
1.工件以平面定位
主要支承
固定支承 可调支承 自位支承
支承钉 支承板
辅助支承
1.工件以平面定位
固定支承
支承钉和支承板
钻套
支承板
支承板
H7 g 6( f 7)
Z
△Z≠ 0 △Y≠ 0
Y
圆柱心轴
X
y
4.2 工件的定位原理及定位元件
3.工件以外圆柱面定位
V形块 定位套 半圆套 支承定位
3.工件以外圆柱面定位
V形块
固定V形块 活动V形块 长V形块 短V形块
3.工件以外圆柱表面定位
3.工件以外圆柱表面定位
定位套
工件以外圆定位的定位套
yz
销2
x y
销1
y 0
x
支承平面
z x y
(3) 过定位
案例4 一面两销定位方案
B 削边销
(3) 过定位
z
案例4 一面两销定位方案
z x y
销1 削边销
y 0
x
支承平面
z x y
(3) 过定位
案例5
滚齿加工的定位方案
x y x y
待加工 的齿轮
z x y
(3) 过定位
案例5
滚齿加工的定位方案
(1)正确的定位 工件定位面与夹具定位元件的定位工 作面相接触或配合来限制工件的自由度, 二者一旦脱离接触或配合,则定位元件就 丧失了工件自由度的作用。
2.应用六点定位原理应注意的问题
(2)一个定位支撑点仅限制一个自由度:原 则上不超过六个。 (3)分析定位支撑点的定位作用时,不考虑 力的影响
2.应用六点定位原理应注意的问题
常用的定位元件
1.工件以平面定位
主要支承
固定支承 可调支承 自位支承
支承钉 支承板
辅助支承
1.工件以平面定位
固定支承
支承钉和支承板
钻套
支承板
支承板
工件在数控机床上的定位与装夹
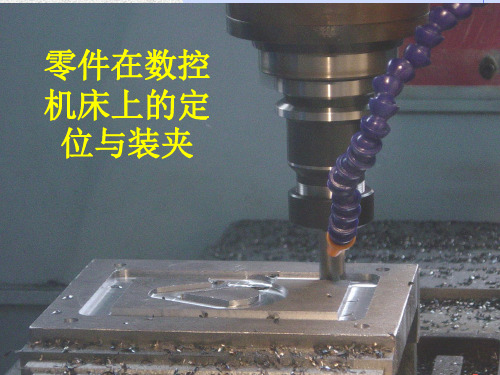
精基准的选择
Ø 在实际生产中,经常使用的统1基准形式有: 1 轴类零件常使用两顶尖孔作统1基准; 2 箱体类零件常使用1面两孔 1个较大的平面和两个距离较
远的销孔 作统1基准; 3 盘套类零件常使用止口面 1端面和1短圆孔 作统1基准; 4 套类零件用1长孔和1止推面作统1基准
Ø 采用统1基准原则好处: 1 有利于保证各加工表面之间的位置精度; 2 可以简化夹具设计,减少工件搬动和翻转次数
a)
b)
c)
图5-2 粗基准选择比较
粗基准的选择
工序1
工序1
工序2
工序2
图5-3 床身粗基准选择比较
重要表面原则
为保证重要表面的加工余量均匀,应选择重要加 工面为粗基准
精基准的选择原则
应保证加工精度和工件安装方便可靠
基准重合原则 基准统1原则 自为基准原则
选用设计基准作为定位基准,避免因基 准不重合带来的误差
课堂讨论
数控车床的装夹找正
Ø 打表找正 通过调整卡爪,使得工件坐标系 的Z轴与数控车床的主轴回转中心轴线重合
Ø 单件的偏心工件 Ø 使用3爪自动定心卡盘装夹较长的工件 Ø 3爪自动定心卡盘的精度不高
7、数控铣床的装夹
通用夹具的选用
平口钳分固定侧与活动侧,固定侧与底面 作为定位面,活动侧用于夹紧
选择平整、光洁、面积大、无飞边毛刺和浇 冒口的表面以便定位准确、夹紧可靠
作为粗基准的表面粗糙且不规则,多次使用 无法保证各加工表面的位置精度
粗基准的选择
◆保证相互位置要求原则——如果首先要求保证工件上加 工面与不加工面的相互位置要求,则应以不加工面作为粗基 准 ◆余量均匀分配原则——如果首先要求保证工件某重要表 面加工余量均匀时,应选择该表面的毛坯面作为粗基准
15-2 工件在夹具上的定位

是几个定位表面的组合。
常见的定位表面组合有: 平面与平面的组合 平面与圆孔的组合 平面与外圆表面的组合 平面与其他表面的组合 锥面与锥面的组合 等等。
共60页
36
在多个表面同时参与定位的情况下,各表
面在定位中所起的定位作用有主次之分。
一般称定位点数最多的定位表面为第一
定位基准面或主要定位面或支承面;
它还适用于阶梯轴及曲轴的定位,并且装卸工 件很方便。
一般来说,长V形块(或两个短V形块的组合) 限制工件的4个自由度,而短V形块一般只限制2个
自由度。V形块又有固定和活动之分。
共60页
27
图中所示为活 动V形块结构图, 它可兼作定位件和 夹紧件。
活动V形块只 限制垂直于活动方 向的一个自由度。
活动V形块的 结构尺寸已标准化。
时,相应的定位元件有下面几种。 1. 套筒、半圆孔
图中所示为装在夹具体上的套 筒结构。其中图(a)为长定位套, 它相当于长销定位,限制工件的 四个自由度;图(b)为短定位套,相 当于短销定位,限制两个自由度。 为了保证轴向定位精度,常与端 面联合定位,这样共限制五个自 由度。
共60页
24
图中为外圆柱面用半圆孔 定位的结构。
对于定位点数次多的定位表面称为第二
定位基准面或导向面;
对于定位点数为1的定位表面称为第三定
位基准面或止动面。
共60页
37
孔与 端面 组合, 如图:
图(a):工件以其孔及与孔中心线垂直的端面组合定
位。这种定位出现了过定位问题。
为了解决该定位方式的过定位问题,应首先确定工件 的哪一个定位基准是起主要定位作用的,即第一定位 基准;哪一个是起次要定位作用的,即第二定位基准, 然后采取适当措施。
常见的定位表面组合有: 平面与平面的组合 平面与圆孔的组合 平面与外圆表面的组合 平面与其他表面的组合 锥面与锥面的组合 等等。
共60页
36
在多个表面同时参与定位的情况下,各表
面在定位中所起的定位作用有主次之分。
一般称定位点数最多的定位表面为第一
定位基准面或主要定位面或支承面;
它还适用于阶梯轴及曲轴的定位,并且装卸工 件很方便。
一般来说,长V形块(或两个短V形块的组合) 限制工件的4个自由度,而短V形块一般只限制2个
自由度。V形块又有固定和活动之分。
共60页
27
图中所示为活 动V形块结构图, 它可兼作定位件和 夹紧件。
活动V形块只 限制垂直于活动方 向的一个自由度。
活动V形块的 结构尺寸已标准化。
时,相应的定位元件有下面几种。 1. 套筒、半圆孔
图中所示为装在夹具体上的套 筒结构。其中图(a)为长定位套, 它相当于长销定位,限制工件的 四个自由度;图(b)为短定位套,相 当于短销定位,限制两个自由度。 为了保证轴向定位精度,常与端 面联合定位,这样共限制五个自 由度。
共60页
24
图中为外圆柱面用半圆孔 定位的结构。
对于定位点数次多的定位表面称为第二
定位基准面或导向面;
对于定位点数为1的定位表面称为第三定
位基准面或止动面。
共60页
37
孔与 端面 组合, 如图:
图(a):工件以其孔及与孔中心线垂直的端面组合定
位。这种定位出现了过定位问题。
为了解决该定位方式的过定位问题,应首先确定工件 的哪一个定位基准是起主要定位作用的,即第一定位 基准;哪一个是起次要定位作用的,即第二定位基准, 然后采取适当措施。
工件在夹具中的定位与夹紧

1)选择不加工面为粗基准 2)合理分配加工余量的原则 3)便于工件装夹原则 4)同方向上粗基准不得重复使用
(3)精基准的选择
主要应保证加工精度和装夹方便
选择精基准一般应遵循以下原则:
1)基准重合原则
设计(工序)与定位
2)基准统一原则
各工序的基准相同
3)互为基准原则
两表面位置精度高
4)自为基准原则
加工余量小而均匀
考虑定位方案时,先分析必须消除哪些自由度, 再以相应定位点去限制。
(3)欠定位与过定位
工件应限制的自由度未被限制的定位,为欠定位, 在实际生产中是绝对不允许的。
工件一个自由度被两个或以上支承点重复限制的 定位称为过定位或重复定位。一般来说也是不合 理的。
过定位造成的后果: (1)使工件或夹具元件变形,引起加工误差; (2)使部分工件不能安装,产生定位干涉(如一面两销)
六点定位原理。
实际中一个定位元件可体现一个或多个支承点, 视具体工作方式及其与工件接触范围大小而定
定位与夹紧的区别: 定位是使工件占有一个正 确的位置,夹紧是使工件保持这个正确位置。
(2)完全定位与不完全定位 工件的六个自由度被完全限制的定位称完全定位, 允许少于六点的定位称为不完全定位。 都是合理的定位方式。
(2)夹紧力作用点的确定 1)夹紧力应作用在刚度较好部位
2)夹紧力作用点应正对支承元件或位于支承元件
形成的支承面内
3)夹紧力作用点应尽可能靠近加工表面
(3)夹紧力大小的估算
夹紧力的大小根据切削力、工件重力的 大小、方向和相互位置关系具体计算,并 乘以安全系数K ,一般精加工K =1.5~2, 粗加工K = 2.5~3。
向上的变动量。由工件定位面和夹具定位元件的制造误差 以及两者之间的间隙所引起。
(3)精基准的选择
主要应保证加工精度和装夹方便
选择精基准一般应遵循以下原则:
1)基准重合原则
设计(工序)与定位
2)基准统一原则
各工序的基准相同
3)互为基准原则
两表面位置精度高
4)自为基准原则
加工余量小而均匀
考虑定位方案时,先分析必须消除哪些自由度, 再以相应定位点去限制。
(3)欠定位与过定位
工件应限制的自由度未被限制的定位,为欠定位, 在实际生产中是绝对不允许的。
工件一个自由度被两个或以上支承点重复限制的 定位称为过定位或重复定位。一般来说也是不合 理的。
过定位造成的后果: (1)使工件或夹具元件变形,引起加工误差; (2)使部分工件不能安装,产生定位干涉(如一面两销)
六点定位原理。
实际中一个定位元件可体现一个或多个支承点, 视具体工作方式及其与工件接触范围大小而定
定位与夹紧的区别: 定位是使工件占有一个正 确的位置,夹紧是使工件保持这个正确位置。
(2)完全定位与不完全定位 工件的六个自由度被完全限制的定位称完全定位, 允许少于六点的定位称为不完全定位。 都是合理的定位方式。
(2)夹紧力作用点的确定 1)夹紧力应作用在刚度较好部位
2)夹紧力作用点应正对支承元件或位于支承元件
形成的支承面内
3)夹紧力作用点应尽可能靠近加工表面
(3)夹紧力大小的估算
夹紧力的大小根据切削力、工件重力的 大小、方向和相互位置关系具体计算,并 乘以安全系数K ,一般精加工K =1.5~2, 粗加工K = 2.5~3。
向上的变动量。由工件定位面和夹具定位元件的制造误差 以及两者之间的间隙所引起。
第一章 工件的定位

32
3、过定位与欠定位
1).分析:工件的定位支 承点少于应限制的自由度 数时,会造成什么后果? 结果:应限制了自由度来 被限制,导致加工时达不 到要求的加工精度。 ① 欠定位:加工中,工件定位点数少于应限制的自由度
数。会产生不良后果。 ② 过定位:工件的某个自由度被限制两次以上。
2).过定位是否允许?一般来说过定位将使工件定位不确定, 夹紧后会使工件或定位元件产生变形。
②过定位不一定就是完全定位? ③多于六个定位点的定位一定是过定位?
38
4、应用六点定位原则应注意的问题 1)方法问题:
①根据工序加工技术要求和工件形状的特点,确 定应限制 那些自由度,而用相应的定位点数目去消除。 ②分析时也可反过来分析哪几个自由度可不必限 制,剩下 的就是要限制的了。
(2)过定位有时是允许的,而欠定位决不允许,欠定位的 后果只导致加工时达不到加工精度。 过定位优点:使定位可能更为可靠,如冰箱有四个支 承点。 缺点:易使工件的定位精度受影响,使工件或夹具夹 39 紧后产生变形。
②优点:夹具结构简单,可避免因夹具本身的制造误差而产生
的定位误差,因此,定位精度高。 如:加工误差 < 0.01~0.005mm,采用夹具加工难以达到。 适用场合:单件小批生产中(如工具修理车间)。
(2)划线找正安装
对重、大、复杂工件的加工,往往是在待加工处划 线,然后
6 装上机床,工件在机床或夹具上位置按所 划的线进行找正定位。
10
11
三、机床夹具的分类 1、分类方法:
1)按夹具的应用范围:通用夹具、专用夹具、可调夹具、组合 夹具、随行夹具; 2)按加工类型:车床夹具、钻床夹具、镗床夹具、磨床夹具、 数控机床夹具等; 3)按夹紧力来源:手动夹具、气动夹具、液压夹具、电磁夹具、 真空夹具。 机床夹具通常按夹具的应用范围进行。
第2章 工件的定位和机床夹具
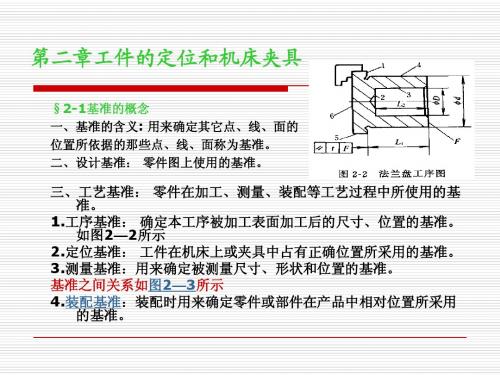
定位心轴
轮加工。
主要用于套筒类和空心盘类工件的车、铣、磨及齿
圆柱心轴 图a为间隙配合圆柱心轴,其定位精度不高,但装卸工件较方便; 图b为过盈配合圆柱心轴,常用于对定心精度要求高的场合; 图c为花键心轴,用于以花键孔为定位基准的场合。当工件孔的长径 比L/D>1时,工作部分可略带锥度。 短圆柱心轴限制工件两个自由度,长圆柱心轴限制工件的四个自由度
支承板:用于精基准,工件重,较大平面支承,相当2个支承点
固定式V形块
图a用于较短的精基准定位; 图b用于较长的粗基准(或门路轴)定位; 图c用于两段精基准面相距较远的场合; 图d中的V形块是在铸铁底座上镶淬火钢垫而成, 用于定位基准直径与长度较大的场合。
活动V形块应用实例
活动式V形块限制工件在Y方向上的移动自由度。 它除定位外,还兼有夹紧作用。
垂直度
长柱销限制 X、X、Z、 Z四个自由 度
Φ8
Z O Y
0.08 14±0.1
A
3.2
中心线 位置
X
A
基准重合原 则选基准孔 基准重合原 则选基准面
小端面限 制Y自由度 靠销限制 Y自由度
需进行定位 误差计算
图2-48 需保证的工序尺寸
夹具设计举例
(2) 确定导向装置。 采用快换钻套,用固定钻模板支撑钻套。
(1) 应标注的尺寸及配合
① 工件与定位元件的联系尺寸; ② 夹具与刀具的联系尺寸; ③ 夹具与机床的联系尺寸; ④ 夹具内部的配合尺寸; ⑤ 夹具的外廓尺寸。
(2) 应标注的技术条件
① 定位元件之间或定位元件与夹具体底面间的位置要求; ② 定位元件与连接元件间的位置要求; ③ 对刀元件与连接元件间的位置要求; ④ 定位元件与导引元件的位置要求。
第8章(1-2)机床夹具的基本概念和工件的定位与定位误差

2、由于加工精度要求,不必限制所有自由度
(三)欠定位:工件在夹具中定位时,若定位 支承点数目少于工序加工所要求的数目,工 件定位不足,称为欠定位。
(四)重复定位:工件在夹具中定位时,若几 个定位支承点重复限制一个或几个自由度, 称为重复定位(超定位)。
*当以形、位精度较低的毛坯面定位时,不允 许重复定位。 *为提高定位稳定性和刚度,以加工过的表面 定位时,可以出现重复定位。
=
d 1 (1 ) 2 sin 2
2)尺寸H2的定位误差 设计基准 为C,定位基准为A,其最大的位 置变动量为 C1C2 即定位误差:
H C1C2 AC2 AC1
2
( AO2 O2C2 ) ( AO1 O1C1 )
3)尺寸H3的定位误差 设计基准 = 为O,定位基准为A,其最大的 位置变动量为 O1O2 即定位误差:
计算得到,根据一批工件的定位由一种可能的极端 位置变为另一种极端位置时δ位置和δ不重的方向的异 同,以确定公式中的加减号。
(二)几种典型表面定位时的定位误差 1、平面定位时的定位误差 *毛坯表面定位: 由于实际表面相 对于其理想位置 有较大的变动范 围,存在基准位 置误差。
δ定位(H)= δ位置(M)
分析:机床保证 了小孔与销的轴线 之间的尺寸,但因 销孔之间存在间隙, 销、孔、外圆均存 在尺寸误差,均会 引起尺寸H的变化。 Hmax:当销最小、 孔最大、外圆最大, 销孔右边接触 Hmin:当销最小、 孔最大、外圆最小, 销孔左边接触
例:孔—销配合例子
基准位置误差δ位置(O):定位基准O相对于其 理想位置O’的最大变动量
(2)对定误差δ对定:与夹具相对于刀具及
切削成形运动有关的加工误差。 包括: 对刀误差δ对刀:夹具相对于刀具位置有关的
- 1、下载文档前请自行甄别文档内容的完整性,平台不提供额外的编辑、内容补充、找答案等附加服务。
- 2、"仅部分预览"的文档,不可在线预览部分如存在完整性等问题,可反馈申请退款(可完整预览的文档不适用该条件!)。
- 3、如文档侵犯您的权益,请联系客服反馈,我们会尽快为您处理(人工客服工作时间:9:00-18:30)。
2 2 2 2
D b d D X ; EH ; Ox E ; 2 2 2 2 1 AE Og Ox (THg THx) 2 2 D 2 b THg THx 2 D X 2 b 2 代入后得 ( ) ( ) ( ) ( ) 2 2 2 2 T THx 2 2 XD X 2 ( Hg ) 2 展开后简化得 b 2(THg THx) 略去二阶微量, 得 b XD THg THx b(THg THx ) D
图2-21
2
在非工作位置时,不与工件接触。工件定 位夹紧后,推出支承顶在工作表面上。
图2-22
弹簧力使支承滑柱的工作面与工件接触
内孔定位用的定位元件
锥形心轴
1. 心轴
过盈配合圆柱心轴
间隙配合圆柱心轴
2. 定位销
图2-23
a) 锥形心轴,锥 度为1/10001/5000;依靠心轴 的锥体定心和胀紧; 限制5个自由度
例1 两定位孔为2 12 0 0.027 mm , 孔中心距为 0.06 mm , 设计两销尺寸。 80
最小配合间隙X推导
双点划线是工件上的孔 粗实线是夹具上的销
在定位销和定位孔的中心距都处在最大误差情况下, 孔与销中心的偏移量: 1 (THg THx ) 2 2 由三角形 Ox AH和Ox EH可得: Og Ox Ox A AH Ox E EH 式中 Ox A
A型:精基准平面 B型:粗基准平面 C型:摩擦大,易 积屑,侧面定位
支承钉相对于大 平面为一个点, 限制一个自由度 如图2-15
图2-15
限制 X方向移动
限制 X方向转动
两支承钉成一直线限制一 个移动和一个转动自由度
三支承钉成一平面限制一 个移动和两个转动自由度
图2-16
A型:结构简单,埋头钉难清理切屑, 适用于侧面和顶面定位; B型:斜凹槽,适用于底面定位。
第二章 工件的定位和机床夹具
§2-4 工件在夹具中定位的基本规律
自由度
自由度:一个自由刚 体在某个方向上活动 的可能性。 一个自由刚体有六个 自由度。
(1)沿X轴移动,用 X表示;
(2)沿Y轴移动,用 表示; (3)沿Z轴移动,用 Y 表示; (4)绕X轴转动,用 表示; Z (5)绕Y轴转动,用 表示; (6)绕Z轴转动,用 X表示。
工件上两定 位孔中心距 公差
一面两孔定位时参数确定步骤
3. 菱形销直径d2的基本尺寸及公差。查 表得菱形销b与B,代入下式:
d 2 max D2 min b(TLg TLx ) D2min
菱形销直径 最大允许值
与菱形销相配合的 孔的最小极限尺寸
一面两孔定位时参数确定(实例)
解 1 确定圆柱销直径为: ) 12g6= 0..006 mm 120 017
2) 确定圆柱销与菱形销之 间中心距: 1 1 取 Ld= LD= 0.12mm 0.04mm 3 3 所以圆柱销与菱形销之 间的 中心距及公差为: 0.02)mm (80 3) 确定菱形销直径: 查表得b 4mm, B 10mm,菱形销最大直径为 b( Ld LD ) 4(0.04 0.12) d 2 max D2 min [12 ]mm D2 min 12 11.947mm 菱形销与定位孔的配合 h6, 其下偏差为 .011mm, 取 0 所以菱形销直径为: d 2 11.947h6 11.9470 0.011 120..053 0 064
定位概念
完全定位:六个自由度都需要限制的定位方法,称为 完全定位。 不完全定位:没有完全限制六个自由度而仍然保证有关 工序尺寸的定位方法称为不完全定位。 过定位:当两种定位元件均能限制工件的同一个方向自 由度时称为过定位。 欠定位:若定位支承点少于所应消除的自由度数时,则 工件定位不足,称为欠定位。
X移动自由度过定位
ˆ x A的第一类自由度:, y, z ˆ ˆ B的第一类自由度: z , x, y 工件第一类自由度为: ˆ ˆ ˆ x, z , x, y, z
菱形销与孔最 小配合间隙X
ˆ ˆ 1限制的自由度: z , x, y ˆ 2限制的自由度: y, z 3限制的自由度: x, z z 为过定位自由度
一面两孔定位时参数确定步骤
1. 圆柱销直径d1的基本尺寸及公差。基本尺 寸应等于与之配合的工件定位孔的最小极限 尺寸,公差取g6或f7 2. 圆柱销与菱形销之间的中心距及公差。两 销中心距平均尺寸等于两定位孔中心距平均 尺寸,公差一般为:
夹具上两定 位销中心距 公差
1 1 TL x= ~ TLg 3 5
结构和尺寸均已标准化。 夹角α一般有60度、90度和 120度三种,以90度最常用。在V形块工作图上必须标 注T尺寸。T必须通过计算获得。
N和H可参照《机床夹具零件及 部件标准》制定: N: 当=90 0 时,N 1.41d 2a 当= 0 时,N 2d 3.46 a 120 式中a (0.14 ~ 0.16 ) d H: 用于大直径定位时,H 0.5d 用于小直径定位时,H 1.2d
b) 过盈配合圆柱心 轴,经压力机压入心 轴;定心精度高,用 于多刀车床盘套类零 件;限制4个自由度
c) 间隙配合心轴, 心轴轴肩轴向定位; 靠右端螺母夹紧; 限制5个自由度
图2-24
L L L L
a) 固定式 b) 可换式:定位销与衬套配合,用螺母拉紧 长销:L/D>=1,限制四个自由度(单指与孔配合的 圆 柱定位面) 短销:L/D<1,限制两个自由度 平头锥销:接触线为圆,限制三个方向的移动自由度
外圆定位的定位元件
V形块、半圆定位块、定位套、自动定心机构等。
在工件定位时主要起 对中作用:使工件外 圆轴线与V 形块两斜 面的对称平面重合。 特点:对中性好,装 夹方便 长V形块: 限制四个自由度 (两个移动自由度,两 个转动自由度) 短V形块: 限制两个自由度 (两个移动自由度)
V形块标准定位高度计算
1、习题4.12 (P135页); 2、习题4.19 (P137页) ;
平面定位用的支承件
1. 支承钉
2. 支承板 基础支承 限制工件自 由度,起独 立定位作用
标 准 件
3. 可调支承
4. 自位支承
5. 辅助支承
不限制工件 推式辅助支承 自由度,加 弹性辅助支承 强刚性和稳 定性
图2-14
X
图2-12
第一类自由度:Z移动,X转动
第一类自由度:X移动, Y移动,X转动,Y转动
常见加工形式所需限制的自由度
球体加工平面
柱体加工平面
长方体加 工平面
总结
圆柱轴向通孔:4个; 圆柱轴向通槽:4个; 平面上通孔:5个;
圆柱轴向盲孔:5个; 圆柱轴向不通槽:5个; 平面上盲孔:6个;
图2-17
定位基准平面较大时,用几块支承板组合成一个平面 I-Z方向移动,X和Y方向转动 II-X方向移动和Z方向转动
两个固定支承钉
用于粗基准平面,可调性适应粗基准位置变化
图2-19
特点:多点支承之间的浮动联 接,实现一个支承点的作用, 所以只限制一个自由度
图2-20
辅助支承不能作为定位元件, 只用于增加刚性和稳定性,不 允许破坏工件定位,可以承受 切削力。
H
图2-27
定位时兼夹紧作用,能补偿毛坯尺寸变化对定位的影响
组合表面的定位元件
组合表面定位:以两个以上的几何要素作为定 位基准的,如一孔一端面、一面两孔(两销)、 一个外圆一个端面等。
一面两孔定位
箱体,杠杆,盖板和支架等
2 Z
菱形销
X
Y
两孔及两销中心距都存在较大误 差时,会使工件无法正确装夹 支承板:Z移动,X转动,Y转动 短销1:X移动,Y移动 短销2:X移动,Z转动
限制高度方面自由度
第一类自由度判断:
– 1. 找出工序尺寸的工序基准 – 2. 确定工序基准需要限制的自由度
三、定位元件及其所限制的自由度
工件在机床上或夹具上定位时,其第一类自由 度是通过工件的定位基准与机床或夹具定位元 件接触或配合而被限制的。 定位基准(或定位基面):平面、内圆、外圆、 内锥面、外锥面等; 定位元件:支承钉、支承板、定位销(心轴)、 定位套、V型块等 定位元件的性能要求: – 1.精度:一般定位元件的尺寸及位置公差 只有工件相应部位公差的1/5~1/2。 –2.耐磨性:避免因磨损影响精度。 –3、刚性:避免或减少受力变形影响精度。
T H OB O1B OB d 2 sin 所以 T d 2 sin ; O1B N N 2 tg
d-V形块的标准心轴直径(工
件定位基面外圆直径) H-V形块高度 T-V形块标准定位高度-V形的 检验心轴至V形块底面距离(加工 和检验尺寸)
2
2
2 tg 2 2 当=90 0 时,T=H+0.707 d - 0.5 N 当=120 0 时,T=H+0.578 d - 0.289 N
常用的定位形式
1. 工件以平面为定位基准 2. 工件以内孔为定位基准
3. 工件以外圆为定位基准
4. 工件以组合表面为定位基准
习题(下面两本书选一本即可)
《汽车拖拉机制造工艺学》第2版,王宝玺主编, 机械工业出版社,2000年:
1、习题一(1)(P66页); 2、习题二(6) (P66页) ;
《汽车制造工艺学》曾东建主编,机械工业出版 社,2005年:
所以最小配合间隙为 X
菱形销
D b d D X ; EH ; Ox E ; 2 2 2 2 1 AE Og Ox (THg THx) 2 2 D 2 b THg THx 2 D X 2 b 2 代入后得 ( ) ( ) ( ) ( ) 2 2 2 2 T THx 2 2 XD X 2 ( Hg ) 2 展开后简化得 b 2(THg THx) 略去二阶微量, 得 b XD THg THx b(THg THx ) D
图2-21
2
在非工作位置时,不与工件接触。工件定 位夹紧后,推出支承顶在工作表面上。
图2-22
弹簧力使支承滑柱的工作面与工件接触
内孔定位用的定位元件
锥形心轴
1. 心轴
过盈配合圆柱心轴
间隙配合圆柱心轴
2. 定位销
图2-23
a) 锥形心轴,锥 度为1/10001/5000;依靠心轴 的锥体定心和胀紧; 限制5个自由度
例1 两定位孔为2 12 0 0.027 mm , 孔中心距为 0.06 mm , 设计两销尺寸。 80
最小配合间隙X推导
双点划线是工件上的孔 粗实线是夹具上的销
在定位销和定位孔的中心距都处在最大误差情况下, 孔与销中心的偏移量: 1 (THg THx ) 2 2 由三角形 Ox AH和Ox EH可得: Og Ox Ox A AH Ox E EH 式中 Ox A
A型:精基准平面 B型:粗基准平面 C型:摩擦大,易 积屑,侧面定位
支承钉相对于大 平面为一个点, 限制一个自由度 如图2-15
图2-15
限制 X方向移动
限制 X方向转动
两支承钉成一直线限制一 个移动和一个转动自由度
三支承钉成一平面限制一 个移动和两个转动自由度
图2-16
A型:结构简单,埋头钉难清理切屑, 适用于侧面和顶面定位; B型:斜凹槽,适用于底面定位。
第二章 工件的定位和机床夹具
§2-4 工件在夹具中定位的基本规律
自由度
自由度:一个自由刚 体在某个方向上活动 的可能性。 一个自由刚体有六个 自由度。
(1)沿X轴移动,用 X表示;
(2)沿Y轴移动,用 表示; (3)沿Z轴移动,用 Y 表示; (4)绕X轴转动,用 表示; Z (5)绕Y轴转动,用 表示; (6)绕Z轴转动,用 X表示。
工件上两定 位孔中心距 公差
一面两孔定位时参数确定步骤
3. 菱形销直径d2的基本尺寸及公差。查 表得菱形销b与B,代入下式:
d 2 max D2 min b(TLg TLx ) D2min
菱形销直径 最大允许值
与菱形销相配合的 孔的最小极限尺寸
一面两孔定位时参数确定(实例)
解 1 确定圆柱销直径为: ) 12g6= 0..006 mm 120 017
2) 确定圆柱销与菱形销之 间中心距: 1 1 取 Ld= LD= 0.12mm 0.04mm 3 3 所以圆柱销与菱形销之 间的 中心距及公差为: 0.02)mm (80 3) 确定菱形销直径: 查表得b 4mm, B 10mm,菱形销最大直径为 b( Ld LD ) 4(0.04 0.12) d 2 max D2 min [12 ]mm D2 min 12 11.947mm 菱形销与定位孔的配合 h6, 其下偏差为 .011mm, 取 0 所以菱形销直径为: d 2 11.947h6 11.9470 0.011 120..053 0 064
定位概念
完全定位:六个自由度都需要限制的定位方法,称为 完全定位。 不完全定位:没有完全限制六个自由度而仍然保证有关 工序尺寸的定位方法称为不完全定位。 过定位:当两种定位元件均能限制工件的同一个方向自 由度时称为过定位。 欠定位:若定位支承点少于所应消除的自由度数时,则 工件定位不足,称为欠定位。
X移动自由度过定位
ˆ x A的第一类自由度:, y, z ˆ ˆ B的第一类自由度: z , x, y 工件第一类自由度为: ˆ ˆ ˆ x, z , x, y, z
菱形销与孔最 小配合间隙X
ˆ ˆ 1限制的自由度: z , x, y ˆ 2限制的自由度: y, z 3限制的自由度: x, z z 为过定位自由度
一面两孔定位时参数确定步骤
1. 圆柱销直径d1的基本尺寸及公差。基本尺 寸应等于与之配合的工件定位孔的最小极限 尺寸,公差取g6或f7 2. 圆柱销与菱形销之间的中心距及公差。两 销中心距平均尺寸等于两定位孔中心距平均 尺寸,公差一般为:
夹具上两定 位销中心距 公差
1 1 TL x= ~ TLg 3 5
结构和尺寸均已标准化。 夹角α一般有60度、90度和 120度三种,以90度最常用。在V形块工作图上必须标 注T尺寸。T必须通过计算获得。
N和H可参照《机床夹具零件及 部件标准》制定: N: 当=90 0 时,N 1.41d 2a 当= 0 时,N 2d 3.46 a 120 式中a (0.14 ~ 0.16 ) d H: 用于大直径定位时,H 0.5d 用于小直径定位时,H 1.2d
b) 过盈配合圆柱心 轴,经压力机压入心 轴;定心精度高,用 于多刀车床盘套类零 件;限制4个自由度
c) 间隙配合心轴, 心轴轴肩轴向定位; 靠右端螺母夹紧; 限制5个自由度
图2-24
L L L L
a) 固定式 b) 可换式:定位销与衬套配合,用螺母拉紧 长销:L/D>=1,限制四个自由度(单指与孔配合的 圆 柱定位面) 短销:L/D<1,限制两个自由度 平头锥销:接触线为圆,限制三个方向的移动自由度
外圆定位的定位元件
V形块、半圆定位块、定位套、自动定心机构等。
在工件定位时主要起 对中作用:使工件外 圆轴线与V 形块两斜 面的对称平面重合。 特点:对中性好,装 夹方便 长V形块: 限制四个自由度 (两个移动自由度,两 个转动自由度) 短V形块: 限制两个自由度 (两个移动自由度)
V形块标准定位高度计算
1、习题4.12 (P135页); 2、习题4.19 (P137页) ;
平面定位用的支承件
1. 支承钉
2. 支承板 基础支承 限制工件自 由度,起独 立定位作用
标 准 件
3. 可调支承
4. 自位支承
5. 辅助支承
不限制工件 推式辅助支承 自由度,加 弹性辅助支承 强刚性和稳 定性
图2-14
X
图2-12
第一类自由度:Z移动,X转动
第一类自由度:X移动, Y移动,X转动,Y转动
常见加工形式所需限制的自由度
球体加工平面
柱体加工平面
长方体加 工平面
总结
圆柱轴向通孔:4个; 圆柱轴向通槽:4个; 平面上通孔:5个;
圆柱轴向盲孔:5个; 圆柱轴向不通槽:5个; 平面上盲孔:6个;
图2-17
定位基准平面较大时,用几块支承板组合成一个平面 I-Z方向移动,X和Y方向转动 II-X方向移动和Z方向转动
两个固定支承钉
用于粗基准平面,可调性适应粗基准位置变化
图2-19
特点:多点支承之间的浮动联 接,实现一个支承点的作用, 所以只限制一个自由度
图2-20
辅助支承不能作为定位元件, 只用于增加刚性和稳定性,不 允许破坏工件定位,可以承受 切削力。
H
图2-27
定位时兼夹紧作用,能补偿毛坯尺寸变化对定位的影响
组合表面的定位元件
组合表面定位:以两个以上的几何要素作为定 位基准的,如一孔一端面、一面两孔(两销)、 一个外圆一个端面等。
一面两孔定位
箱体,杠杆,盖板和支架等
2 Z
菱形销
X
Y
两孔及两销中心距都存在较大误 差时,会使工件无法正确装夹 支承板:Z移动,X转动,Y转动 短销1:X移动,Y移动 短销2:X移动,Z转动
限制高度方面自由度
第一类自由度判断:
– 1. 找出工序尺寸的工序基准 – 2. 确定工序基准需要限制的自由度
三、定位元件及其所限制的自由度
工件在机床上或夹具上定位时,其第一类自由 度是通过工件的定位基准与机床或夹具定位元 件接触或配合而被限制的。 定位基准(或定位基面):平面、内圆、外圆、 内锥面、外锥面等; 定位元件:支承钉、支承板、定位销(心轴)、 定位套、V型块等 定位元件的性能要求: – 1.精度:一般定位元件的尺寸及位置公差 只有工件相应部位公差的1/5~1/2。 –2.耐磨性:避免因磨损影响精度。 –3、刚性:避免或减少受力变形影响精度。
T H OB O1B OB d 2 sin 所以 T d 2 sin ; O1B N N 2 tg
d-V形块的标准心轴直径(工
件定位基面外圆直径) H-V形块高度 T-V形块标准定位高度-V形的 检验心轴至V形块底面距离(加工 和检验尺寸)
2
2
2 tg 2 2 当=90 0 时,T=H+0.707 d - 0.5 N 当=120 0 时,T=H+0.578 d - 0.289 N
常用的定位形式
1. 工件以平面为定位基准 2. 工件以内孔为定位基准
3. 工件以外圆为定位基准
4. 工件以组合表面为定位基准
习题(下面两本书选一本即可)
《汽车拖拉机制造工艺学》第2版,王宝玺主编, 机械工业出版社,2000年:
1、习题一(1)(P66页); 2、习题二(6) (P66页) ;
《汽车制造工艺学》曾东建主编,机械工业出版 社,2005年:
所以最小配合间隙为 X
菱形销