MILLINGPARTICLESIZEING
粉末冶金3 粉末的表征

第三部分粉末的表征目录1、粉末颗粒与粉末体的概念 (1)2、化学性能Chemistry-Features (3)3、粉末物理性能Physio- Features (3)4、粉末工艺性能 (7)课堂作业 (30)Part 2 粉末性能表征Powder Characterizations物理性能 Physical features化学性能 Chemical features工艺性能 Operational features1、粉末颗粒与粉末体的概念Concepts of particles and powders致密体bulk、粉末体powder、colloid 胶体------固体solid:根据不同分散程度dispersed degree粉末体 (1000微米,微米级,亚微米级sub-micrometer,纳米级nano grade (0.1微米以下))粉末颗粒表现出流体性质flow ability,粉末越细,流动性质越明显。
0.1微米以下的粉末工业中又称为超细super fine powder粉末0.01微米以下powders称为胶体colloid粉末颗粒与粉末体 particles and powders粉末颗粒: crystalline or poly-crystalline, amorphous, glass 晶粒或多晶聚合体, 粉末体:called powder simply简称粉末,是由大量的粉末颗粒组成的一种dispersed system 分散体系,其中的颗粒彼此可以分离devoice each other,或者说,粉末是由大量的颗粒及颗粒之间的空隙所构成的集合体。
Powder is combined by particles and pores among the particles粉末颗粒 Powder particles粉末聚集状态:单颗粒single particle,二次颗粒secondary parti.multi-particles单颗粒single particle 晶粒或多晶粒聚集\amorphous,粉末中能分开并独立independent presented unit 存在的最小实体称为单颗粒二次颗粒 secondary particles有多个单颗粒或一次颗粒构成;PowderFirstly primary particles一次颗粒往往不能单独存在而聚集在一起,agglomeration force 聚集力主要是物理作用力agglomeration,而非强化学健结合chemistry bonding; 一次颗粒粒度测定particle size testing, inert gas absorbent 惰性气体表面吸附方法BET二次颗粒粒度测定, other method; x-ray, optical microscope, TEM, SEM,light scattering图2-1描绘了由若干一次颗粒聚集成二次颗粒的情形。
Update_4 Particle Size Reduction MILLING TECHNOLOGY
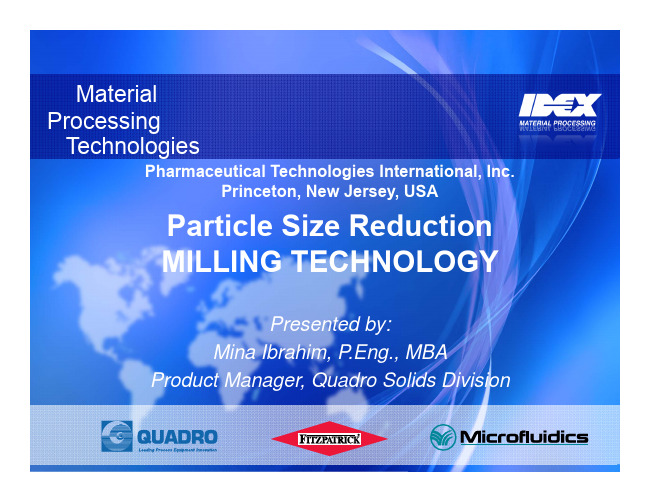
Technologies
Pharmaceutical Technologies International, Inc. Princeton, New Jersey, USA
Particle Size Reduction MILLING TECHNOLOGY
Presented by: Mina Ibrahim, P.Eng., MBA Product Manager, Quadro Solids Division
EVOLUTION OF MILLING TECHNOLOGY
Size ReductionStoOnve eGrrvinideewr
Roll Crusher
Lump Breaker Hammer Mill
Approx. 80 Years of recorded history
Oscillator Tornado Mill
• Specifically for Tablets:
– Increase bioavailability – Improve Flow – Reduce Segregation – Enhance Drying – Control Particle size – Repeatability – Batch to Batch
• How Powders must flow Powders must compress Particles must lock together PSD control → Weight control
Size Reduction Overview
Common Tableting Problems
Approx. 50 Years
DefinitionofTerms

Solids and Slurries - Definition of TermsAPPARENT VISCOSITYThe viscosity of a non-Newtonian slurry at a particular rate of shear, expressed in terms applicable to Newtonian fluids.CRITICAL CARRYING VELOCITYThe mean velocity of the specific slurry in a particular conduit, above which the solids phase remains in suspension, and below which solid-liquid separation occurs.EFFECTIVE PARTICLE DIAMETERThe single or average particle size used to represent the behavior of a mixture of various sizes of particles in a slurry. This designation is used to calculate system requirements and pump performance. FRICTION CHARACTERISTICA term used to describe the resistance to flow which is exhibited by solid-liquid mixtures at various rates of flow.HETEROGENEOUS MIXTUREA mixture of solids and a liquid in which the solids are net uniformly distributed.HOMOGENEOUS FLOW(FULLY SUSPENDEID SOLIDS)A type of slurry flow in which the solids are thoroughly mixed in the flowing stream and a negligible amount of the solids are ~iding along the conduit wall.HOMOGENEOUS MIXTUREA mixture of solids and a liquid in which the solids are uniformly distributed.NON-HOMOGENEOUS FLOW(PARTIALLY SUSPENDED SOUDS)A type of slurry flow in which the solids are stratified, with a portion of the solids sliding along the conduit wall. Sometimes called heterogeneous flow" or "flow with partially suspended solids."NON-SETTUNG SLURRYA slurry In which the solids will not settle to the bottom of the containing vessel or conduit, but will remain in suspension, without agitation, for long periods of time.PERCENT SOLIDS BY VOLUMEThe actual volume of the solid material in a given volume of slurry, divided by the given volume of slurry, multiplied by 100.PERCENT SOLIDS BY WEIGHTThe weight of dry solids in a given volume of slurry, divided by the total weight of that volume of slurry, multiplied by 100.SALTATONA condition which exists in a moving stream of slurry when solids settle in the bottom of the stream in random agglomerations which build up and wash away with irregular frequency.SETTLING SLURRYA slurry in which the solids will move to the bottom of the containing vessel or conduit at a discernible rate, but which will remain in suspension If the slurry Is agitated constantly.SETTLING VELOCITYThe rate at which the solids in a slurry will move to the bottom of a container of liquid that Is not in motion. (Not to be confused with tne velocity of a slurry that is less than the critical carrying velocity as defined above.)SQUARE ROOT LAWA rule used to calculate the approximate increase in critical carrying velocity for a given slurry when pipe size is increased. It states:NOTE: This rule should net be used when pipe size is decreased.VISCOSITY TYPES(For definitions of the various types of viscosities applicable to slurries. see Rheological Definitions.) YIELD VALUE (STRESS)The stress at which many non-Newtonian slurries will start to deform and below which there will be no relative motion between adjacent particles in the slurry.Solids and Slurries - Slurry Pump ApplicationsDetermining the when to use a slurry style centrifugal pump can be a challenging decision. Often the cost of a slurry pump is many times that of a standard water pump and this can make the decision to use a slurry pump very difficult. One problem in selecting a pump type is determining whether or not the fluid to be pumped is actually a slurry. We can define a slurry as any fluid which contains more solids than that of potable water. Now, this does not mean that a slurry pump must be used for every application with a trace amount of solids, but at least a slurry pump should be considered.Slurry pumping in its simplest form can be divided into three categories: the light, medium and heavy slurry. In general, light slurries are slurries that are not intended to carry solids. The presence of the solids occurs more by accident than design. On the other hand, heavy slurries are slurries that are designed to transport material from one location to another. Very often the carrying fluid in a heavy slurry is just a necessary evil in helping to transport the desired material. The medium slurry is one that falls somewhere in between. Generally, the Percent solids in a medium slurry will range from 5% to 20% by weight.After a determination has been made as to whether or not you are dealing with a heavy, medium, or light slurry, it is then time to match a pump to the application. Below is a general listing of the different characteristics of a light, medium, and heavy slurry.Light Slurry Characteristics:•Presence of solids is primarily by accident•Solids Size < 200 microns•Non-settling slurry•The slurry specific gravity < 1.05•Less than 5% solids by weightMedium Slurry Characteristics:•Solids size 200 microns to 1/4 inch (6.4mm)•Settling or non-settling slurry•The slurry specific gravity < 1.15•5% to 20% solids by weightHeavy Slurry Characteristics:•Slurry's main purpose is to transport material•Solids > 1/4 inch (6.4mm)•Settling or non-settling slurry•The slurry specific gravity > 1.15•Greater than 20% solids by weightThe previous listing is lust a quick guideline to help classify various pump applications. Other considerations that need to be addressed when selecting a pump model are: Abrasive hardness •Particle shape•Particle size•Particle velocity and direction•Particle density•Particle sharpnessThe designers of slurry pumps have taken all of the above factors into consideration and have designed pumps to give the end user maximum expected life. Unfortunately. there are some compromises that are made in order to provide an acceptable pump life. The following short table shows the design feature, benefit, and compromise of the slurry pump.Although selecting the proper slurry pump for a particular application can be quite complex, the selection task can be broken down into a simplified three-step process:1. Determine which group of possible pump selections best matches your specific application.2. Plot the system curve depicting the required pump head at various capacities.3. Match the correct pump performance curve with the system curve.Slurry pumps can be broken down into two main categories. The rubber-lined pump and the hard metal pump. However, because of the elastomer lining, the rubber-lined pumps have a somewhat limited application range. Below is a general guideline which helps distinguish when to apply the rubber-lined pumps.It should be noted, however, that a hard metal pump can also be used for services that are outlined for the rubber-lined pump. After a decision has been made whether to use a hard metal pump or a rubber-lined pump, It Is then time to select a particular pump model. A pump model should be selected by reviewing the application and determining which model pump will work best in the service.NOTES:The Model HS pump is a unique pump in that it is a recessed impeller or "vortex" pump. This style pump is well suited to handle light pulpy or fibrous slurries. The recessed impeller used in the HS family of pumps will pass large stringy fibers and should be considered when pump plugging is a concern.The Model AF is a specialized pump with an axial flow design. This design of pump is built specifically for high flow, low head applications. in general, slurry pumps have been designed to handle fluids withabrasive solids, and will give extended lives over standard water or process pumps. Although many features have been designed into the slurry pump, there are still two factors which directly relate to the pump's life that can be determined. The first choice to make is determining the metallurgy of the pump. In most cases, a hard metal slurry pump will be constructed of some hardened metal with a Brine ii hardness of at least 500. Goulds standard slurry pump material is a 28% chrome iron with a minimum hardness of 600 Brinell. This material is used for most abrasive services and can also be used in some corrosive fluids as well. if a more corrosive resistant material is required, then the pump may be constructed out of a duplex Stainless steel Such as CD4MCu. Please check with your nearest Goulds sales office If you are unsure what material will be best suited for a particular application.PUMP RUNNING SPEEDThe other factor that can be controlled by the sales or end user engineer is the pump running speed. The running speed of a slurry pump is one of the most important factors which determines the life of the pump. Through testing, It has been proven that a slurry pump's wear rate is proportional to the speed of the pump raised to the 2 1/2 power.EXAMPLE:If Pump (A) is running at 1000 RPM and Pump (B) is running at 800 RPM, then the life factor for Pump (B) as compared to Pump (A) is (1OOO/80O)2.5 or Pump (B) will last 1.75 times as long as Pump (A).With the above ratio in mind. it can be shown that by cutting a slurry pump speed in half, you get approximately 6 times the wear life. For this reason, most slurry pumps are V-belt driven with a full diameter impeller. This allows the pump to run at the slowest possible running speed and, therefore, providing the maximum pump life.WHY USE A V.BELT DRIVE? In most ANSI pump applications it is a reasonable practice to control condition point by trimming the impeller and direct connecting the motor. However, this is not always sound practice in slurry applications. the abrasive solids present, wear life is enhanced by applying the pump at the slowest speed possible.Another situation where V-belts are beneficial is in the application of axial flow pumps. Axial flow pumps cannot be trimmed to reduce the condition point because they depend on close clearances between the vane tips and the casing for their function. The generally low RPM range for axial flow application also makes it beneficial to use a speed reduction from the point of view of motor cost. The types of V-belt drives available for use in pump applications are termed fixed speed, or fixed pitch, and variable speed. The fixed pitch drive consists of two sheaves; each machined to a specific diameter, and a number of belts between them to transmit the torque. The speed ratio is roughly equal to the diameter ratio of the sheaves. The variable speed drive is similar to the fixed speed except that the motor sheave can be adjusted to a range of effective or pitch diameters to achieve a band of speed ratios. This pitch adjustment is made by changing the width of the Vgrooves on the sheave. Variable speed drives are useful in applications where an exact flow rate is required or when the true condition point is not well defined at the time that the pump is picked.V-belt drives can be applied up to about 2000 horsepower, but, pump applications are usually at or below 350 HP.Solids and Slurries-Useful Formulasa. The formula for specific gravity of a solids-liquids mixture or slurry, S m is:where,S m = specific gravity of mixture or slurryS i = specific gravity of liquid phaseS s = specific gravity of solids phaseC w = concentration of solids by weightC v = concentration of solids by volumeEXAMPLE: if the liquid has a specific gravity of 1.2 and the concentration of solids by weight is 35% with the solids having a specific gravity of 2.2, then:b. Basic relationships among concentration and specific gravities of solid liquid mixtures are shown below:Where pumps are to be applied to mixtures which are both corrosive and abrasive, the predominant factor causing wear should be identified and the materials of construction selected accordingly. This often results in a compromise and in many cases can only be decided as a result of test or operational experience.For any slurry pump application a complete description of the mixture components is required in order to select the correct type of pump and materials of construction.c. Slurry flow requirements can be determined from the expression:EXAMPLE: 2,400 tons of dry solids is processed in 24 hours in water with a specific gravity of 1.0 and the concentration of solids by weight is 30% with the solids having a specific gravity of 2.7 then:d. Abrasive wear: Wear on metal pumps increases rapidly when the particle hardness exceeds that of the metal surfaces being abraded. If an elastomer lined pump cannot be selected, always select metals with a higher relative hardness to that of the particle hardness. There is little to be gained by increasing the hardness of the metal unless it can be made to exceed that of the particles. The effective abrasion resistance of any metal will depend on its position on the mohs or knoop hardness scale. The relationships of various common ore minerals and metals is shown in Fig. A.Wear increases rapidly when the particle size increases. The life of the pump parts can be extended by choosing the correct materials of construction.Sharp angular particles cause about twice the wear of rounded particles.Austenetic maganese steel is used when pumping large dense solids where the impact is high.Hard irons are used to resist erosion and, to a lesser extent, impact wear.Castable ceramic materials have excellent resistance to cutting erosion but impeller tip velocities are usually restricted to 100 ft./sec.Elastomer lined pumps offer the best wear life for slurries with solids under 1/4" for the SRL/SRL-C and under 1/2" for the SRL-XT. Several Elastomers are available for different applications. Hypalon is acceptable in the range of 1-14 pH. There is a single stage head limitation of about 150' due to tip speed limitations of elastomer impellers.See the Classification of Pumps according to Solids Size chart (Fig. C) and Elastomer Quick Selection GuideFig. B Nomograph of the Relationship of Concentration to Specific Gravity in Aqueous SlurriesFig. D Standard Screen Sizes Comparison ChartFig. E Specific Gravities of Rocks, Minerals and OresFig. F Hardness Convertion Table for Carbon and Alloy SteelsFig. G Slurry Pump MaterialsFig. H Slurry Pump Application Guidelines。
旋转锥形分样器
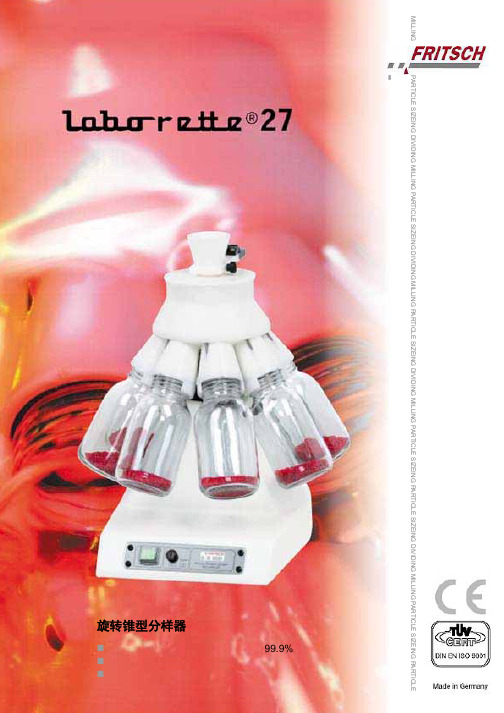
PARTICLE SIZEING DIVIDING MILLING PARTICLE SIZEING DIVIDING MILLING PARTICLE SIZEING DIVIDING MILLING PARTICLE SIZEING PARTICLE SIZEING DIVIDING MILLING PARTICLE SIZEING PARTICLEMILLING旋转锥型分样器具有代表性样品的分样准确率高达99.9% 可安全的应用于食品 可变的分样比率应用领域适用于干性固体或悬浮液具有代表性样品的分样。
旋转锥型分样器与极为精确的分析仪器形成了共生作用。
广泛的应用于研发及质量控制实验室,可为有效的分析提供少量却具有代表性的样品。
旋转锥型分样器 "laborette 27" 无需任何转换也可用于液体或悬浮液的分样。
特别是对于含有粗糙颗粒的悬浮液,旋转锥型分样器的分样可避免粗糙或较重颗粒沉降对分样造成的影响。
工作原理传统的诸如“锥形分样”,“四分法”及“旋转离心分样”的分样方法已远不能满足现代化分析技术的要求。
现在通过结合三项原则,即可在单一的仪器中实现准确的分样:样品通过轮廓类似于锥形四分法操作的漏斗进入旋转锥型分样器中。
样品经过旋转锥型的表面,受整个系统的离心力作用向外加速,均匀的输送至30个分离的通道中,分别收集在玻璃瓶中。
旋转作用和分样头的数目使旋转锥型分样器每分钟可以完成高达3000步的分样,因此,对于每一个通道的进料都将生成大量分离好的样品,这就是卓越的分样器最明显的区别标志。
由于这种设计,旋转锥型分样器 "laborette 27" 对样品分样的准确率为可达到99.9%。
设计特性基本的仪器配置共有6种分样头可供选择体积为250 ml 和500 ml 的分样瓶具有快速夹紧装置 每分钟可完成高达3000步的分样可拆卸的分样头可方便的清洗具有滑动离合器的免维护驱动马达,转速达100 rpm 可循环使用的坚固铸铝外壳优点标准配置中包括具有快速夹紧装置的体积为250 ml或500 ml 分样瓶可确保具有代表性样品的分样无需格外修饰,即可处理干性自由流动的样品或悬浮液可选择分样比率紧凑,占用空间小,轻巧,便于携带收集容器体积从15 ml到500 ml有多种尺寸可供选择可安全的应用于食品* 玻璃容器螺纹:GL 55可通过振动进样器 "laborette 24" 控制样品的进样速度通过TÜV 安全认证Fritsch 公司一年的保修期附件分样头— 分样头的分样比率有1:8,1:10和 1:30— 极化处理的铝制分样头适合腐蚀性的样品和悬浮液— POM (聚氧化亚甲烯)塑料的分样头适合非腐蚀性样品— PTFE (聚四氟乙烯)包裹铝的分样头适合可腐蚀POM 塑料或铝的固体和悬浮液样品进样使用振动进样器 "laborette 24" 进行匀速进样,又一次确保了分样的准确性。
ParticleIllusion参数的意义

ParticleIllusion参数的意义deman发布于:2012-3-9 15:03 |原作者: 飘落的心|查看: 21058|评论: 0|来自: 飞特网会员投稿教程|寻找原创分享者简介: 本教程向FEVTE的朋友们介绍ParticleIllusion参数的意义,很多朋友都会用到,快来把教程收藏了吧!给飞特影视后期处理爱好者们整理一下ParticleIllusion参数的意义,希望对大家有用,也算是对飞特的回报。
请兄弟姐妹们支持。
【本人也不是高手,有问题可以到飞特论坛AE区交流】在illusion中,选择Emitter喷射体来制造效果,而每个Emitter都有一个或者更多的particle分子组成particle参数用来调整分子特征emitter参数用来调整分子参数的设定1.weight重力对于particle而言(emitter-colorful-weight)当weight为正数,说明物体是重的。
所以发射的粒子方向向下当weight为负数,说明物体是轻的。
所以发射的粒子方向向上当weight为0,没有粒子对于emiter而言,无法从emitter/weight的值的大小正负中判断粒子的轻重,主要要根据particle/weight来决定注意,两个weight都不能为0,为0时没有任何效果2.Spin旋转emitter的spin旋转参数只有一个:emitter/spin,值域0--2000,只控制旋转速度,不可为0,否则无旋转效果。
调整这一参数将影响所有分子………………………………………………………………particle的旋转参数有三个,调整这三个参数只影响该分子,对其他分子不产生影响第一:particle/spin。
值域负值--0--正值,正值表示顺时针旋转,负值表示逆时针旋转,绝对值越大,转速越快。
为0时不旋转第二:particle/spin variation 旋转变化度让每个分子喷出的旋转速度都不同值域min到max,都是正数min不做任何随即处理越接近max,表示增加随即强度,即前后两次的旋转速度差异越大第三:particle/spin over life生命周期内旋转的变化x轴代表生命周期y轴代表旋转方向和旋转速度,值域-100到+100负数逆时针,正数顺时针…………………………………………………………用途:一般当第一个分子参数particle/spin不为0时,在整个周期内,分子的旋转方向将无法改变。
Maintaining particle size in the transformation of anatase to rutile titania nanostructures
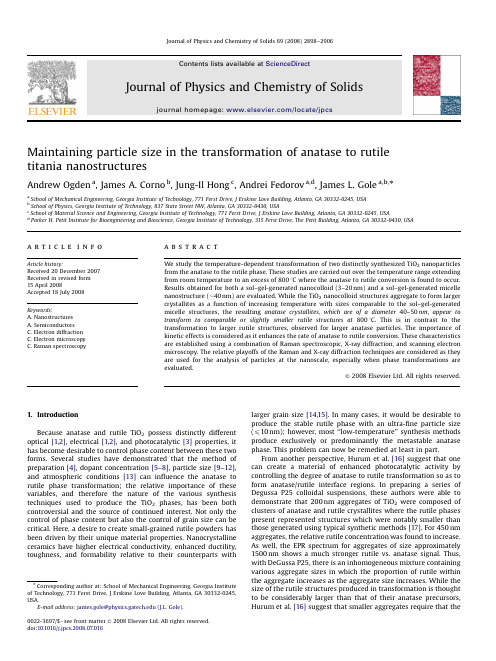
Maintaining particle size in the transformation of anatase to rutiletitania nanostructuresAndrew Ogden a,James A.Corno b,Jung-Il Hong c,Andrei Fedorov a,d,James L.Gole a,b,Ãa School of Mechanical Engineering,Georgia Institute of Technology,771Ferst Drive,J Erskine Love Building,Atlanta,GA30332-0245,USAb School of Physics,Georgia Institute of Technology,837State Street NW,Atlanta,GA30332-0430,USAc School of Material Science and Engineering,Georgia Institute of Technology,771Ferst Drive,J Erskine Love Building,Atlanta,GA30332-0245,USAd Parker H.Petit Institute for Bioengineering and Bioscience,Georgia Institute of Technology,315Ferst Drive,The Petit Building,Atlanta,GA30332-0430,USAa r t i c l e i n f oArticle history:Received20December2007Received in revised form15April2008Accepted18July2008Keywords:A.NanostructuresA.SemiconductorsC.Electron diffractionC.Electron microscopyC.Raman spectroscopya b s t r a c tWe study the temperature-dependent transformation of two distinctly synthesized TiO2nanoparticlesfrom the anatase to the rutile phase.These studies are carried out over the temperature range extendingfrom room temperature to an excess of8001C where the anatase to rutile conversion is found to occur.Results obtained for both a sol–gel-generated nanocolloid(3–20nm)and a sol–gel-generated micellenanostructure($40nm)are evaluated.While the TiO2nanocolloid structures aggregate to form largercrystallites as a function of increasing temperature with sizes comparable to the sol–gel-generatedmicelle structures,the resulting anatase crystallites,which are of a diameter40–50nm,appear totransform to comparable or slightly smaller rutile structures at8001C.This is in contrast to thetransformation to larger rutile structures,observed for larger anatase particles.The importance ofkinetic effects is considered as it enhances the rate of anatase to rutile conversion.These characteristicsare established using a combination of Raman spectroscopic,X-ray diffraction,and scanning electronmicroscopy.The relative playoffs of the Raman and X-ray diffraction techniques are considered as theyare used for the analysis of particles at the nanoscale,especially when phase transformations areevaluated.&2008Elsevier Ltd.All rights reserved.1.IntroductionBecause anatase and rutile TiO2possess distinctly differentoptical[1,2],electrical[1,2],and photocatalytic[3]properties,ithas become desirable to control phase content between these twoforms.Several studies have demonstrated that the method ofpreparation[4],dopant concentration[5–8],particle size[9–12],and atmospheric conditions[13]can influence the anatase torutile phase transformation;the relative importance of thesevariables,and therefore the nature of the various synthesistechniques used to produce the TiO2phases,has been bothcontroversial and the source of continued interest.Not only thecontrol of phase content but also the control of grain size can becritical.Here,a desire to create small-grained rutile powders hasbeen driven by their unique material properties.Nanocrystallineceramics have higher electrical conductivity,enhanced ductility,toughness,and formability relative to their counterparts withlarger grain size[14,15].In many cases,it would be desirable toproduce the stable rutile phase with an ultra-fine particle size(p10nm);however,most‘‘low-temperature’’synthesis methodsproduce exclusively or predominantly the metastable anatasephase.This problem can now be remedied at least in part.From another perspective,Hurum et al.[16]suggest that onecan create a material of enhanced photocatalytic activity bycontrolling the degree of anatase to rutile transformation so as toform anatase/rutile interface regions.In preparing a series ofDegussa P25colloidal suspensions,these authors were able todemonstrate that200nm aggregates of TiO2were composed ofclusters of anatase and rutile crystallites where the rutile phasespresent represented structures which were notably smaller thanthose generated using typical synthetic methods[17].For450nmaggregates,the relative rutile concentration was found to increase.As well,the EPR spectrum for aggregates of size approximately1500nm shows a much stronger rutile vs.anatase signal.Thus,with DeGussa P25,there is an inhomogeneous mixture containingvarious aggregate sizes in which the proportion of rutile withinthe aggregate increases as the aggregate size increases.While thesize of the rutile structures produced in transformation is thoughtto be considerably larger than that of their anatase precursors,Hurum et al.[16]suggest that smaller aggregates require that theContents lists available at ScienceDirectjournal homepage:/locate/jpcsJournal of Physics and Chemistry of Solids0022-3697/$-see front matter&2008Elsevier Ltd.All rights reserved.doi:10.1016/j.jpcs.2008.07.016ÃCorresponding author at:School of Mechanical Engineering,Georgia Instituteof Technology,771Ferst Drive,J Erskine Love Building,Atlanta,GA30332-0245,USA.E-mail address:james.gole@(J.L.Gole).Journal of Physics and Chemistry of Solids69(2008)2898–2906rutile crystallites from which they are composed are typically small,on the same order of magnitude as their anatase counter-parts.Although the anatase phase of TiO2can be readily produced at the10nm scale using sol–gel techniques[11,12],it is metastable with respect to the rutile phase.The anatase phase reverts spontaneously to the rutile phase at temperatures above9151C [18],as the process is kinetically unfavorable at low temperatures. Navrotsky and Kleppa[18]determined a negative enthalpy change for the anatase to rutile transformation,reporting that anatase is metastable with respect to rutile under all conditions of temperature and pressure.The JANAF tables[19]demonstrate that the free energy of formation of rutile is always less than anatase,making it the thermodynamically more stable structure.We have recently produced titania-based oxynitride structures [11,12,20]employing the direct nitridation of porous,sol–gel-generated,TiO2nanocolloids,using alkyl-ammonium compounds. Further,we have recently studied the room temperature anatase to rutile phase transformation[7]of these same porous nano-colloids induced by Co II ion seeding into$10nm nanostructures at concentrations exceeding2wt%.Here,we employ a combina-tion of Raman spectroscopy,X-ray diffraction(XRD),and scanning electron microscopy(SEM)to study two syntheses used to form (1)the$10nm porous structures that we have characterized previously and(2)$40nm anatase TiO2structures generated using the techniques of Stathatos et al.[21].Our purpose is to study the behavior of the synthesized structures over a tempera-ture range exceeding8001C,where we obtain evidence for the conversion of these porous anatase structures to rutile forms of similar size.These results are considered as they not only complement previous studies,but also indicate the surprising transformation to form rutile structures of size comparable to the precursor anatase phase.Within this framework,we discuss the nature of the Raman spectroscopic and XRD data and the manner in which they are to be correlated in the analysis of a temperature-dependent transformation at the nanoscale.Further,based on the time scales for transformation and on additional limited but complimentary data obtained for rapid annealing,we consider the potential importance of kinetic factors in the transformation of these highly active nanoparticles.2.ExperimentalThe anatase TiO2nanocolloid was prepared as250ml of doubly deionized water and80ml of acetic acid were combined in a1L flask,and the mixture was cooled to01C in an ice bath under vigorous stirring.A10ml aliquot of propanol mixed with37ml of titanium(IV)isopropoxide(Ti[OCH(CH3)2]4)was slowly added dropwise from a dropping funnelfixed to theflask,under a dry nitrogen atmosphere,as the solution was again vigorously stirred. Continued stirring of the initial mixture for24h produces a clear colloid solution with particle sizes ranging from3to20nm [11,12].This clear solution can be maintained under refrigeration for several months.Extended exposure of the colloid solution to air at room temperature or heating to501C produces an agglomeration of the nanoparticles and results in the formation of a semitransparent gel.Anatase TiO2also was prepared with a sol–gel method using reverse micelles.This approach to forming nanocrystalline TiO2films has been developed by Stathatos et al.[21].The reverse micelles were formed at room temperature by dissolving Triton X100(3.75ml)in cyclohexane(24ml)and adding water(0.2ml). Titanium isopropoxide was introduced into this solution under vigorous stirring,using a small syringe to yield a clear sol.This procedure produces$40nm TiO2particles,which precipitate in several hours.Therefore,they should be exposed to the necessary heating cycle after only short time periods.Except where noted,the sample heating of both the nanocol-loids and the Stathatos nanoparticles was done slowly at a rate of $201/min,followed by a30-min dwell at thefinal prescribed temperature.During the heating cycle,to ensure that the samples were not shock cooled when removed from the furnace,the samples were placed in a steel,closeable,sample holder at room temperature.The sample holder door was kept open as the samples were exposed in a manner to ensure that their temperature was equal to that of the furnace.Following this procedure,and before removal from the furnace,the sample holder door was closed to trap the sample air,and the sample holder was removed to room temperature to cool.The samples were allowed10min to cool at room temperature before being tested by the Raman system.The TiO2nanocolloid was heated to temperatures ranging from400to10501C,whereas the sol–gel-generated reverse micelle nanostructures were heated to temperatures ranging from400to8001C.The effect of a rapid heating on the nanocolloid was also assessed.Here the nanocolloid,at room temperature,was inserted directly into a 7001C furnace as described in the experimental section.Raman spectra were obtained using a Renishaw m-Raman system with a488nm excitation source.The focal length used in this system is1/4m.A longer focal length system is more sensitive (see Discussion).Further characterization of these systems was carried out using X-ray diffractometry.XRD patterns for the anatase TiO2 nanocolloid at room temperature were taken with the Mo K-alpha 1line(Fig.6).XRD patterns of the nanoparticles after annealing at various temperatures(Fig.7)were taken using the Cu K a1 (l¼1.54A˚)line with a Ge single crystal monochromator (Panalytical X’-pert Pro MPD diffractometer).The scanning electron micrographs were obtained using a thermalloy-assistedfield emission SEM,Leo1530,operated at10kV.3.Results3.1.Raman spectroscopyFigs.1and2demonstrate the Raman spectra obtained for the TiO2nanocolloid(3–20nm(average size10nm))extending from a room temperature,as-prepared,dried sample to a temperature of 10501C.It is apparent that no Raman signal can be obtained for the room temperature nanocolloids.In contrast,as we will consider,an XRD spectrum for the anatase form of TiO2is readily obtained.Fig.1demonstrates a weak Raman signal for the anatase form of TiO2as the sample is heated to4001C.As we will note, this is consistent with the relatively slow aggregation of the smaller nanocolloid particles.At temperatures in the range 400–7001C,the Raman spectrum appears to consist exclusively of the anatase phase.At8001C,the spectrum is seen to shift to that for the rutile phase,associated also with features that display a slight asymmetry.At temperatures over the range800–10501C, the spectrum is exclusively that of the rutile phase.After1h at 8001C,the spectra display full conversion.The FWHM(associated with the638cmÀ1symmetric stretching mode)of the anatase features plotted in Fig.3narrows over the temperature range 400–7001C.After conversion to the rutile form,there is a significant increase in FWHM band width(associated with the 606cmÀ1symmetric stretching mode of the rutile structure); however,the narrowing of the observed Raman peaks for the rutile structure over the range from800to10501C is notably muted relative to that for the anatase form(Fig.3).A.Ogden et al./Journal of Physics and Chemistry of Solids69(2008)2898–29062899Fig.4demonstrates the Raman spectra obtained for the sol–gel-generated reverse micelle structures,which SEM studies demonstrate are in the size range 40–50nm as they are formed at room temperature,in agreement with Stathatos et al.[21].For these notably larger structures,a Raman signal is obtained at room temperature.At temperatures in the range 400–6001C,the Raman spectrum appears to consist exclusively of the anatase phase,and the features again sharpen (Fig.3).At 8001C,the observed spectrum again shifts to that for the rutile phase,although the conversion does not appear to be as complete as that for the aggregated nanocolloids.A slight residual anatase signal is apparent.This observation might well signal the importance of kinetic effects associated with the observed transformations of the two distinctly synthesized sol–gel structures in this study.All of the Raman spectra presented in Figs.1,2and 4were taken for samples prepared with a 201/min temperature ramp to the indicated temperatures.However,if the room-temperature-prepared nanocolloid is subjected in the absence of slow heating to a temperature of 7001C,the result (Fig.5),in contrast to the spectrum in Fig.1,is a partial conversion to the rutile structure.In this rapid annealing process,the sample at room temperature was placed directly into the furnace (T ¼7001C).The sample was240000Nanocolloid Heating20000016000012000080000400000R a m a n C o u n t (-)150250350450Aggregation of Nanocolloid550650750850Room Temperature400 C500 C600 C700 C800 CWavenumber (Inverse cm)Fig.1.Raman spectra for TiO 2nanocolloid [12]as a function of temperature:No room temperature Raman spectrum is observed.After heating to 400,500,600,and 7001C,the spectrum corresponds to the anatase structure of TiO 2with bands at 400,515,and 635cm À1.After heating to 8001C,the spectrum corresponds to the rutile structure of TiO 2with vibrational bands at $235,440,and 605cm À1.Each spectrum is shifted an additional 20,000Raman counts relative to the previous spectrum.See text for discussion.20000016000012000080000400000R a m a n C o u n t (-)150250350450Raman Shift (Inverse cm)Aggregated Nanocolloid-Rutile Structure550650750850800 C850 C 950 C1050 CFig.2.Raman spectra for TiO 2nanocolloid as a function of temperature:The Raman spectra obtained after heating to 800,850,950,and 10501C correspond to the rutilestructure of TiO 2with vibrational bands at $235,440,and 605cm À1.Each spectrum is shifted an additional 20,000Raman counts relative to the previous spectrum.See text for discussion.A.Ogden et al./Journal of Physics and Chemistry of Solids 69(2008)2898–29062900removed after 5min and allowed to cool in the open air (in the absence of the sample holder’s temperature buffering)for 5min before being tested with the Raman system.In order to test for further transformation,the same sample was then reinserted into the furnace at the 7001C temperature for another 15min.The sample was again removed without a heat flux buffer and allowed to cool before investigation.Here,no significant change in the Raman spectra between the two tests was observed.This result,in concert also with a comparison to the data presented in Figs.1,2and 4,would seem to suggest the importance of kinetic effects in the anatase to rutile phase transformations observed in this study.3.2.X-ray diffractometryFig.6demonstrates clear XRD peaks for the room temperature-synthesized nanocolloids.As demonstrated previously [11],the spectrum is due exclusively to the anatase form of TiO 2.Thus,XRD has provided an assessment of the structure of the room temperature nanocolloids,whereas the present Raman system is unable to detect these nanoparticles.A fit to the XRD spectrum using the Debye–Scherer equation [11]indicates an average particle size of 10nm.With more refined collection optics,it is possible to obtain the Raman spectrum [7]for the anatase formPowder Comparison6050403020100F W H M (I n v e r s e c m )40050060070080090010001100Annealing Temperature (C)NanocolloidStathatosparison of Raman spectral feature FWHM peak widths for sol–gel-generated TiO 2nanocolloid [12]and sol–gel-generated TiO 2micelle nanostructures [21]as a function of annealing temperature.No Raman spectra are observed for the nanocolloid at room temperature.See text for discussion.080000160000240000320000150250350450550650750850R a m a n C o u n t (-)Raman Shift (Inverse cm)Heating of Stathatos Generated Structures400 C500 C600 C800 CRoom TemperatureFig.4.Raman spectra for sol–gel-generated TiO 2micelle nanostructures [21]as a function of temperature.The features at room temperature,400,500,and 6001C correspond to the anatase structure of TiO 2with bands at 400,515,and 635cm À1.At 8001C the spectrum is strongly dominated by features corresponding to the rutile structure of TiO 2,with bands at 235,440,and 605cm À1;however,a small component of anatase features can be observed.Each spectrum is shifted by 40,000Raman counts relative to the previous spectrum for clarity.See text for discussion.A.Ogden et al./Journal of Physics and Chemistry of Solids 69(2008)2898–29062901(see discussion following);however,the peaks are greatly broadened relative to those for Degussa P25($30nm).Fig.7demonstrates the XRD spectra obtained for both the nanocolloids and the sol–gel-generated micelle nanostructures at 400,700,and 8001C.The expanded portion of the XRD spectra from 201to 301taken for samples heated to 4001C clearly demonstrates a notably broader pattern for the nanocolloid than that from the sol–gel-generated micelle nanostructures.This is consistent with expectation from the Debye–Scherer relationship;however,the data at 7001C suggest a considerable broadening of the XRD features which is inconsistent with the pattern of structures observed in the Raman spectra of Figs.1and 4that,via their narrowing,suggest the growth of the basic nanostructures to larger particles.This suggests that the direct application of the Debye–Scherer equation [11]to the XRD data may be inappropri-ate as the broadening might reflect disorder.Concomitantly,the significant narrowing of the XRD pattern at 8001C suggests the formation of much larger crystalline struc-tures.This result can only be consistent with the Raman data of Figs.1,2and 4if the broadening in the Raman spectrum indicates20000016000012000080000400000R a m a n C o u n t (-)150250350450Wavenumber (Inverse cm)Nanocolloid--Rapid Heating Test550650750850200 C700 CFig.5.Raman spectrum for TiO 2nanocolloid rapidly heated to 7001C (vs.a slow 201/min temperature ramp).A partial conversion from the anatase to the rutile structure is observed with all bands as indicated in Figs.1and 4.No Raman features are observed when the process is carried out at 2001C.See text for discussion.15202530354045Two-Theta (deg)100200300400500600700I n t e n s i t y (C o u n t s )[Titania092807-repeat.xrdml] @298K01-071-1167> Anatase 2 - TiOFig.6.XRD spectrum for TiO 2nanocolloid at room temperature.The spectrum corresponds to the anatase structure and the diffraction patterns were obtained using the Mo K-alpha 1line.A.Ogden et al./Journal of Physics and Chemistry of Solids 69(2008)2898–29062902a substantial disorder introduced during the conversion from the anatase to the rutile structure as opposed to a decrease in the base nanoparticle size,consistent with the increased density of the rutile form of TiO 2.Further,the observed slight decrease in Raman broadening at temperatures from 800to 10501C (Fig.3)seems inconsistent with a significant increase in disorder.To consider this possible inconsistency,we have obtained SEM micrographs of the structures formed at 400and 8001C.3.3.Scanning electron microscopyFig.8depicts an SEM image for the sol–gel-generated (Stathatos et al.[22])micelle nanostructures at 4001C.The micrograph depicts an aggregate of several $40–50nm structures.This is not a surprising result in view of the previous studies of this material and the Raman data presented in Fig.4.Fig.9demonstrates that the nanocolloid nanostructure aggregates,which appear to be of notably smaller size than the micelle nanostructures,are much less easily observed [22].This result is also consistent with the much weaker nature of the Raman features observed in Fig.1vs.those in Fig.4.Fig.10corresponds to the SEM micrograph obtained for the nanocolloids at 8001C.The micrograph depicts aggregates of 40–50nm particles.These data,in concert with the Raman data in Figs.1,2and 4,are consistent with the combination of both increased disorder and comparable or smaller particle size resulting from the transformation from anatase to rutile TiO 2at180016001400120010008006004002000I n t e n s i t y202224262830NC 800NC 700NC 400ST 800ST 700ST 400Theta (deg)NC NC NC STST STXRD-TiO 2 PowdersFig.7.XRD spectra (expanded view of the 20–301region)for (1)sol–gel-generated TiO 2nanocolloid [11](NC)and (2)the sol–gel-generated TiO 2micelle nanostructures [21](ST)as a function of temperature after heating to 400,700,and 8001C.Expanded view of 20–301scattering region.The diffraction patterns were obtained using the Mo K-alpha 1line.See text fordiscussion.Fig.8.SEM micrographs of sol–gel-generated TiO 2micelle nanostructures after heating to 4001C.The spectrum corresponds to aggregates of 40–50nm structures.See text for discussion.A.Ogden et al./Journal of Physics and Chemistry of Solids 69(2008)2898–290629038001C.Further,for the nanocolloids in the range 400–7001C,an increase in particle size with increasing temperature is consistent with the structure observed in Fig.10.It appears that the broadening associated with the XRD spectra in Fig.7,if it is consistent with the Raman data,must be associated with an increased disorder in the crystal structure of the system and not with a decreasing particle size in the range to 7001C.Similarly,the apparent prediction of a much larger crystal structure at 8001C (considerable decrease in the width of the XRD pattern)is not consistent with the observed SEM micrographs or the Raman spectra at 8001C and above.The use of the Debye–Scherer equation to fit the XRD data in this region appears inappropriate.4.DiscussionThe generally accepted theory of anatase to rutile phase transformation is that two Ti–O bonds break in the anatase structure,allowing the rearrangement of TiO 2-based octahedralforms.The thermodynamically based critical particle theory [23]has been extended to titania by Kumar [9]to suggest that the phase transformation may have a grain size dependence.How-ever,no consistent correlation between grain size and the anatase–rutile phase transformation has been demonstrated.Gribb and Banfield [10]have proposed that a particle size-based kinetic effect controls the anatase to rutile phase transformation.With these provisos,it is not unreasonable to expect that,for certain forms of nanoparticles,it might be possible to readily overcome the kinetic barrier for anatase to rutile conversion,promoting an extremely high efficiency for the phase transforma-tion process.This may have important future implications for the sintering process [9–12,14,15].The stoichiometric conversion of anatase to rutile TiO 2can be carried out at temperatures in excess of 8001C but this process requires extended exposure times [24].This may not be surprising since the free energies of formation of anatase and rutile TiO 2are very similar [18].Although Navrotsky and Kleppa [18]have demonstrated that the anatase phase reverts spontaneously to the rutile phase at temperatures above 9151C,Fig.9.SEM micrograph of TiO 2nanocolloid after heating to 4001C.The spectrum corresponds to structures considerably smaller than 40nm.See text fordiscussion.Fig.10.SEM micrographs of TiO 2nanocolloid structures after heating to 8001C.The spectrum corresponds to aggregates of 40–50nm ‘‘spherical’’crystallites.See text for discussion.A.Ogden et al./Journal of Physics and Chemistry of Solids 69(2008)2898–29062904these authors have established that the process,at least for larger TiO2particles,is kinetically unfavorable.However,the present study clearly demonstrates that the anatase to rutile transforma-tion can be induced,at least for nanoparticles,at somewhat lower temperatures and on a much faster time scale.It seems apparent that the data we have obtained in this study suggest that,for sufficiently small nanoparticles,it is possible to induce the elevated temperature anatase to rutile transformation in TiO2to produce a similar,if not slightly smaller,rutile structure. This result appears consistent with the results of Hurum et al.[16],as theyfind that their smaller Degussa particles display evidence for rutile crystallites that are typically small and similar in size to their precursor anatase structures.These combined results then suggest a size threshold below which rutile particles of smaller dimension might be obtained through the combined kinetically and thermodynamically induced transformation of anatase TiO2.In other words,there appears to be a limiting anatase particle size from which smaller or comparable rutile particles can be formed.As one can expect a much higher surface reactivity to be associated with the nanostructures,the results would support the increased role of kinetics in inducing the anatase to rutile phase transformation.The results which are obtained for the fast annealing process would also support the increased importance of the kinetics of transformation at the nanoscale.In both comparison and contrast to the present studies,it is appropriate to consider the work of Kim et al.[25].These authors studied the homogeneous precipitation of TiO2ultra-fine (nanometer scale)particles from aqueous TiOCl2solutions at a Ti IV concentration of0.05M over the range from room tempera-ture to1001C.They found that,under1atm pressure,TiO2 precipitates to pure rutile phase200–400nm diameter spherical particles between0and651C,and that anatase phase formation onsets at temperatures4651C.The formation of a stable rutile phase was found to occur quite slowly between room temperature and651C,although the rutile phase can be formed more readily(from anatase)thermodynamically at temperatures exceeding7001C.The present study also points to the advantages and dis-advantages of Raman and XRD characterization in the nanometer regime.With the Raman system used in this study,it is apparent that we are unable to obtain a Raman scattering signal from the $10nm nanocolloids,whereas XRD is quite adequate to demon-strate the anatase crystal structure of the nanocolloid.In order to obtain the anatase spectrum we have used a m-Raman system which consisted of a Mitutoyo microscope and a SPEX Triplemate spectrometer equipped with a CCD and employed the514.5nm line of an Ar ion laser as the excitation source.The microscope had 10Â,50Â,and100Âobjectives for focusing the laser light and was coupled to the spectrometer through afiber optic bundle [7,8,11].For these experiments,the spot size was on the order of 100m m in order to reduce the power density.The light from the microscope wasfiltered by a514.5nm notchfilter.The results we have obtained in this study suggest,that in a system heated to the elevated temperatures at which we have operated to obtain the anatase to rutile phase transformation,the introduction of crystalline disordering with increasing tempera-ture can lead to a significant broadening of the features in the XRD spectrum.This renders mute the use of the Debye–Scherer equation to evaluate crystallite size.Similar problems would appear to be encountered when dopants are introduced to facilitate the anatase to rutile phase transformation.These results point to the difficulty of using XRD to characterize extremely small structures when a phase transformation and dopant seeding,in combination,are involved.However,in the application of Raman scattering,the two phases of TiO2have very distinct,widely spaced fundamental vibrational features[7,8]and thus are readily identified.5.ConclusionThe data we have obtained in this study suggest that if the transformation from anatase to rutile TiO2is carried out for nanoparticles of size o50nm it may be possible to produce rutile structures of comparable or somewhat smaller size.Kinetics would appear to play a more important role in the transformation of these nanoparticles.This result is consistent with the recent study of Hurum et al.[16].Further,the current results demon-strate the playoff between the use of XRD and micro-Raman characterization at the nanoscale.AcknowledgementWe acknowledge Dan‘‘The Man’’Jackson,whose incredible enthusiasm,as an NSF-REU student,for the development of novel catalyticfilmsfirst led us on this path.In addition,the generous aid of Dr.Samuel Graham in providing access to his lab and Raman spectrometer is greatly appreciated.We also are grateful to the referees of this manuscript for their very helpful comments. Partial support for this work was provided by a NIRT grant from the National Science Foundation(CTS-0608896).References[1](a)K.Sunada,Y.Kikuchi,K.Hashimoto,A.Fujishima,Environ.Sci.Technol.32(1998)726;(b)M.A.Fox,M.T.Dylay,Chem.Rev.93(1993)341;(c)lis,S.L.Hunte,J.Photochem.Photobiol.A108(1997)1.[2](a)A.L.Linsebiglser,G.Lu,J.T.Yates,Chem.Rev.95(1995)735;(b)T.L.Thompson,J.T.Yates,Chem.Rev.106(2006)4428;(c)H.Yamashite,M.Honda,M.Harada,Y.Ichihashi,M.Anpo,T.Hirao,N.Itoh,N.Iwamoto,J.Phys.Chem.B102(1998)10707;(d)Y.Wang,H.Cheng,Y.Hao,J.Ma,W.Li,S.Cai,Thin Solid Films349(1999)120.[3](a)T.Gerfin,M.Graetzel,L.Walder,Molecular and Supermolecular SurfaceModification of Nanocrystalline TiO2Films:Charge-Separating andCharge-Injecting Devices,Wiley,New York,1997,p.44;(b)M.R.Hoffman,S.T.Martin,W.Choi, D.W.Bahnemann,Chem.Rev.95(1995)69;(c)M.Graetzel,Nature414(2001)338;(d)lis,S.L.Hunte,J.Photochem.Photobiol.A108(1997)1;(e)S.Kumar,A.G.Fedorov,J.L.Gole,Appl.Catal.B:Environ.57(2)(2005)93.[4]S.Wilska,Acta Chem.Scand.8(1954)1796.[5]K.J.D.MacKenzie,The calcination of titania:the effect of additives on theanatase–rutile transformation,Trans.J.Br.Ceram.Soc.74(2)(1975)29.[6]J.F.Banfield,B.L.Bishoff,M.A.Anderson,Chem.Geol.110(1993)211.[7]J.L.Gole,S.M.Prokes,O.J.Glembocki,J.Phys.Chem.C112(6)(2008)1782–1788.[8]J.L.Gole,S.M.Prokes,X.Qui,C.Burda,O.J.Glembocki,A comparative study ofsimultaneous cobalt(II)ion seeding of TiO2and TiO2Àx N x at the nanoscale: evidence for formation of spinel structure and room temperature conversion of anatase to rutile TiO2,Surf.Sci.,submitted.[9]K.N.Kumar,Scr.Metall.Mater.32(1995)873.[10]A.A.Gribb,J.F.Banfield,Am.Mineral.82(1997)717.[11]X.Chen,Y.Lou, A.C.S.Samia, C.Burda,J.L.Gole,Adv.Funct.Mater.15(2005)41;S.M.Prokes,J.L.Gole,X.Chen,C.Burda,W.E.Carlos,Adv.Funct.Mater.15 (2005)161.[12]J.L.Gole,J.Stout,C.Burda,Y.Lou,X.Chen,J.Phys.Chem.B108(2004)1230.[13]J.A.Gamboa,D.M.Pasquevich,J.Am.Ceram.Soc.75(1992)2934.[14]S.Ashley,Mech.Eng.116(2)(1994)52.[15]M.Gell,Mater.Sci.Eng.A204(1995)246.[16]D.C.Hurum,A.G.Agrios,K.A.Gray,T.Rajh,M.C.Thurnauer,J.Phys.Chem.B107(2003)4545.[17]H.Yin,et al.,J.Mater.Chem.11(2001)1694.[18]A.Navrotsky,O.J.Kleppa,J.Am.Ceram.Soc.50(1974)626.[19]D.R.Stall,JANAF Thermochemical Tables,Joint Army–Navy–Air Force–ARPA-NASA Thermochemical Working Group,1996.[20]C.Burda,Y.Lou,X.Chen,A.C.S.Samia,J.Stout,J.L.Gole,Nano Lett.3(2003)1049.A.Ogden et al./Journal of Physics and Chemistry of Solids69(2008)2898–29062905。
小麦磨粉机的英文资料

3:Milling of wheat3.1.Introduction1Most cereal grains are used either for the production of animal feed or for the milling offlour for human consumption.If used as an animal feed,the grains have only to be crushed to obtain a granulated product.Any type of mill may be used for this purpose.In most cases it will be a hammer mill,which in one processing step fragments the grains and pulverizes them by a beating action of hammers.The grinding of wheat for human consumption,however,has to meet higher standards and is called milling.The main purpose of milling is to completely separate bran and germ from the mealy endosperm and to thor-oughly pulverize the mealy endosperm into middlings,semolina andflour (definitions of these substances are given in Section3.4).This is achieved through the shearing and scraping action of millstones(in windmills and watermills)or mill rollers(in a modernflour-milling factory).In this process it is essential to extend slightly thefloury particles to such a degree that their internal structure is made loose.In German this is called‘Auflösung’.The water absorption capacity at doughmaking will be higher in aflour with a loose structure and it will form a more elastic and stronger dough than in a flour with a compact ling offlour for human consumption is achieved in three steps:1.cutting open the grains,2.scraping bran from semolina and otherfloury substances,and3.reducing the size of the semolina and middlings to formflour.3.2.Conditioning or temperingIn European mills,grains of soft-kerneled wheats are usually brought to mois-ture contents of16%and hard-kerneled wheats to17.5%.Higher moisture levels are required for milling extremely hard wheats.Duration of tempering varies from about8hours(for soft wheats)to24hours(for hard wheats).A tough bran and a friable mealy endosperm are prerequisites for an ef-ficient separation of the two.As the bran becomes progressively tougher and less brittle with increasing moisture content,milling will produceflour that 1For more information see Hoseney(1986);Bass(1988).22is less contaminated by bran dust,thus being whiter and having a lower ash content.The mealy endosperm is rendered mellower and more friable with the addition of the correct amount of moisture.However,excessive moisture causesflaking,whereas insufficient moisture leads to undue pulverization. Since an ideal moisture distribution is achieved when the bran is slightly damper than the endosperm,a second light tempering(about0.5%moisture) is often applied shortly(less than1hour)before milling.To improve the physical state of the grains for milling,the actual milling process is preceded by conditioning or tempering of the wheat.This process involves the addition or removal of moisture(wetting or drying,respectively) for definite periods of time,in order to obtain the desired moisture content in the mass of grain,and the desired distribution of moisture throughout each kernel.lingling in a traditional millIn windmills and watermills,cereals are ground between a pair of horizontally placed millstones.The lower or bed stone isfixed to thefloor of the milling room.The upper stone rotates on a central axis.The two stones are approx-imately1.5m in diameter,but the thickness of the stones may vary from mill to mill.Wheat is poured from a bin in the upper storey of the mill into a hole (the eye)in the centre of the upper stone(Figure3.1).In this way the wheat is positioned centrally between the two millstones.The upper-side of the lower stone and the under-side of the upper stone arefluted(Figure3.2).The distance between the two stones is in the centre about1cm,in the periphery less.During thefirst few rotations the grains are cut and broken by the edges of theflutings,which work like scissors.Thereafter,the milling good goes in a spiral movement towards the periphery of the stones,where the next step of the process takes place:the inner part of the grains,i.e.the mealy endosperm,is separated from the outer part,i.e.the bran.The large and medium-large endosperm particles that are released during this process are called semolina.The diameter of these particles can vary from about300µm to750µm.Finally,the ground particles end up in the outer15cm of the millstones, where the distance between the stones is the smallest.Here,the semolina is rubbed into dust-like particles:flour.Floury particles ground on a millstone have a diameter of about200µm or less.If the stones are properly set,the tough bran will remain intact.Theflour that is ejected from between the millstones will be a mixture of bran,pure23Figure3.1.Driving gear of a stone-mill.Figure3.2.Carves on the milling surfaces of the two millstones(H.Titulaer,Mühlsteinbau, Geldern1-Veert D).24flour and semolina that has not been fully ground.Such a mixture is referred to as whole-wheatflour.This whole-wheatflour may be led through a round sieve(a bolter)in order to obtain pureflour.ling in a roller-millAround1850the idea arose,first in Switzerland and later in Hungary,to use porcelain or steel rollers instead of millstones.The diameter of these rollers is25or30cm and their length may vary between100and150cm.The rollers are positioned horizontally in pairs and rotate at different speeds in opposite directions.The distance between the rollers can be adjusted.Por-celain rolls are not used any more.Roller-mills have certain advantages over traditional stone-mills.The capacity of a roller-mill is much larger than that of a windmill or watermill.The range of products from a roller-mill is larger and better geared to the needs of industrial processing.Moreover,a roller-mill does not require the laborious and time-consuming sharpening of the furrow edges of the millstones.It is,therefore,not surprising that many modernflour-milling factories have been created since the1880s,in Europe as well as in North America.Life without these mills is hard to imagine nowadays.Roller-milling is a cleverly designed process.Although most of the work in a modern mill is done by special machines(e.g.rollers and plansifters)considerable milling experience and skill are still required to obtain good results.Roller-milling comprises several grinding steps,each being followed by a sifting operation.Broadly speaking,the grinding stages may be grouped into two successive sytems:the break system and the reduction system.The break system.Primarily,the break system aims to bring about a virtual separation between the bran and the mealy endosperm.It is carried out with the aid of corrugated orfluted iron rollers,called break rollers(Figure3.3). They operate in pairs,revolving in opposite directions and at different speeds (the speed differential is approximately1:2).The process includes successive milling steps,in which the corrugations of the rollers become progressively finer and the milling gap(distance between the rollers)smaller.Under each pair of rollers a set of horizontal sieves(plansifters)is placed so that the milled product is graded according to size.End products of the break system are mainly coarse offals(bran),germs,coarse endosperm particles(semolina, 300–750µm and middlings,125–300µm)and a certain amount offlour (diameter less than125µm).The reduction system.Primarily,the reduction system aims to reduce coarse endosperm particles(semolina and middlings)toflourfineness.It involves a series of reduction steps in which,as in the case of breaking,the rollers are set25Figure3.3.The milling of wheat with two break rollers. progressively closer at each successive processing step.The reduction rollers, also,operate in pairs.They have smooth,slightly roughened(mat)surfaces; and speed differentials are4:5(in Europe)or2:3(in USA and Canada).Each reduction is again followed by plansifters,through which the ground material is sifted according to particle size.The reduction process is repeated several times until ultimately most of the mealy endosperm has been converted to flour.End products of the reduction system are mainly:fine offals(shorts)and fine endosperm particles(flour).To illustrate the milling steps in some more detail,the simpleflow diagram of the experimental laboratory mill in Figure3.4will be discussed here.Conditioned wheat is fed to a pair of corrugated chilled-iron rollers known as thefirst break-rollers,one of which revolves at two-and-a-half times the speed of the other.The space between thefirst break-rollers is such that the grains are broken mainly into relatively coarse pieces with a minimum of crushing,so as to avoid powdering the bran(powdered bran cannot be sepa-rated fromflour).The material released from thefirst break-rollers passes to a sifter machine (plansifter),which separates the particles according to size by means of a stack of horizontal sieves of increasing degrees offineness.The sieve sizes are(from top to bottom)750,300and125µm,thus dividing the grinding stock into four fractions:coarse materials(larger than750µm),semolina (between300and750µm),middlings(between125and300µm)andflour (smaller than125µm).Thefinest material(flour)leaves the mill and passes directly to theflour bag.Intermediate-sized particles,those larger thanflour particles,are sent to thefirst reduction rollers(semolina)or(the smaller particles,middlings)to the third reduction rollers.26Figure3.4.Flow diagram of an experimental mill.The coarsest particles are fed to the second break-rollers,which havefiner flutings and are set closer than thefirst break-rollers.Again,the resulting grinding stock is divided into four sieve fractions:coarse material,semolina, middlings andflour.After passing through the third break-rollers,the coarse material(overtails of the top sieve)consists of branflakes from which almost all endosperm has been removed.The second and third break-rollers are meant to scrape all endosperm off the bran skin,releasing the mealy endosperm in large particles of semolina and middlings and leaving the bran in largeflatflakes so that it can be easily removed.Note that the production offlour is not the main object of the break system.The coarse endosperm particles released from the break-rollers are fairly pure,i.e.free from bran fragments.They are fed to reduction rollers,where smooth rollers crush these particles intoflour.One roller revolves at1.25 times the speed of the other.The smooth rollers desintegrate the endosperm, whereas most of the tougher bran and germ particles are merely somewhat flattened and can thus be sifted out.The reduction rollers(designated as first,second,third,and fourth reduction rollers)are set progressively closer together.Thus,the main object of the reduction system is the production offlour. In addition toflour,fine offals are obtained,called shorts.The simple mill27 diagram in Figure3.4shows only one offal.This byproduct consists of small bran fragments to which some endosperm is still attached.It also contains germ.In contrast to bran,germ can be easily separated from the endosperm, due to its putty-like consistency.It willflatten rather than pulverize under the force of the rollers.Laboratory roller-mills exist in many sizes and capacities.The smallest can mill100g of wheat intoflour within a few minutes.The largest have capacities of about100kg/h or more.All these mills,even the smallest, produceflour which is comparable toflour of commercial mills.They may be used in ordinary laboratory analyses such as those carried out by milling and breeding companies(including baking trials on a micro-scale).3.4.End-products of milling and their applicationSemolina is a milling product consisting of coarse particles of mealy endo-sperm with a diameter of300–750µm.Middlings are a product consisting of intermediate-sized endosperm particles with a diameter of125–300µm. Both are used as ingredients in porridge and for the production of pastas. Flour consists offine endosperm particles of less than125µm diameter.It is used for making white bread,confectionary products,and certain pasta products.Besidesfine endosperm particles orflour,meal contains a certain amount offlaky bran and,sometimes,germ.It is used for making light and dark types of brown bread.In so-called whole-mealflour and whole-meal bread,the endosperm,bran and germ are present in the same proportion as they are in wheat grains.ling qualityIn a commercial mill,the aim is to obtain a maximum yield offlour with a ‘healthy’white colour.As described in Section2,mealy endosperm generally has a very low ash content(about0.5%),whereas bran and germs are char-acterized by much higher ash levels(about7.2%and4.5%,respectively).In other words,the lower the ash content,the whiter theflour.A laboratory-scale mill may give a rough indication of the milling quality of wheat.A middle-sized mill with an hourly capacity of several kilogram is well equipped for giving reliable millingfirger mills with higher capacities will provide more detailed information;they are used exclusively in the laboratories offlour-milling factories.28The milling quality2of wheat is determined by successively measuring the following characteristics in a standard milling experiment:a)the amount of grain that can be milled per time unit,b)theflour yield of each milling passage,andc)the moisture and ash content of each milling passage.The values of(b)and(c)need to be converted to a standard moisture content (approximately14%).The successiveflour fractions are combined till an ex-traction rate of70%has been reached.If an extraction rate of70%cannot be reached,a small quantity of shorts is added.Finally,the ash content of this mixture is determined.The ash content offlour at a standard milling or extraction rate(in our case 70%)is a reliable indication of the milling quality of the wheat.The lower the ash content,the higher theflour yield in a commercial mill will be.The ash content offlour may vary between0.45%and0.60%. Theoretically,a reverse technique may be used whereby theflour yield at a standard ash content(e.g.0.45%)is taken as a measure for milling quality. The thus determined extraction rates vary from67%to75%.This method is generally used in commercial milling practice.3.6.Soft wheat versus hard wheatIn the milling of soft wheats,the mealy endosperm is fragmented indiscrim-inately.Therefore,theflour particles consist mainly of fragments of single cells or fragments of clusters of two or three neighbouring cells.The interior of the cells more or less bulges.When rubbed between thumb and forefinger, theflour has a soft,‘woolly’feel.Theflour of soft wheats contains many loose starch granules and protein particles due to the low degree of cohesion between starches and proteins.Theflour easily sticks together and sifts with difficulty,tending to close the apertures of sieves.In the milling of hard wheats,fracturing of the grain follows the middle lamellas of the mealy endosperm cells.As a consequence,flour particles consist of one or more intact cells,some with and some without adhering wall material.As the cohesion between starch and protein is much stronger in hard than in soft endosperm wheat,theflour contains hardly any loose starch granules and protein particles.Hard wheats yield a coarse,grittyflour which is free-flowing and easily sifted.When rubbed between thumb and forefinger, 2For more information see Russell Eggit&Hartley(1975).29 a more or less‘sandy’structure can be felt.Theflour yield of a hard wheat is generally a few percent higher than that of a soft wheat.3.7.Durum wheat millingSemolina from durum wheat is the preferred raw material for the manufacture of pastas(macaroni,spaghetti,noodles).In durum milling,the objective is to produce a maximum yield of highly purified semolina.Although the same sequence of operations is involved in the production of semolina as inflour, the milling systems differ in their design.Durum wheat milling involves thorough cleaning and proper condition-ing of the grains,light and careful grinding,and thorough purification.In a purifier,a shallow stream of impure semolina passes over a large sieve that is shaken rapidly backward and foreward.An upward air current through the sieve draws off very light material to dust collectors and tends to hold bran particles on the surface of the moving semolina so that they drift over the tail of the sieve.Cleaning,breaking,sifting and purifying systems are,therefore,much more elaborate and extensive than inflour mills.On the other hand,the reduc-tion system is much shorter in durum mills because the primary product is re-moved andfinished in granular condition;reduction rollers are only required for reduction of the tailings from the various parts of the break system. ReferencesBass EJ(1988)Wheatflour milling.In Pomeranz Y(ed),Wheat:chemistry and technology, V ol II,3rd edn.St Paul,MN:Am Assoc Cereal Chem:1–68.Hoseney RC(1986)Dry milling of cereals.In Hoseney RC(ed),Principles of cereal science and technology.St Paul,MN:Am Assoc Cereal Chem:133–152.Russell Eggit PW,Hartley AW(1975)Extraction rates–Milling processing implication.In Spicer A(ed),Bread:Social,nutritional and agricultural aspects of wheaten bread.London:Appl Sci Publ:219–233.。
[整理]particle详解.
![[整理]particle详解.](https://img.taocdn.com/s3/m/5b8f2724e45c3b3566ec8b4a.png)
Effects神奇的粒子特效系统,Particle Playground(粒子特效)和水波特效(Wave World)、散焦特效(Caustics)、泡沫特效(Foam)、爆炸特效(Shatter)同属于Simulation特效系统。
其中的Particle Playground(粒子特效)可以产生大量相似物体独立运动的模拟效果。
在今天我们来了解After Effects神奇的粒子特效系统,Particle Playground(粒子特效)和水波特效(Wave World)、散焦特效(Caustics)、泡沫特效(Foam)、爆炸特效(Shatter)同属于Simulation特效系统。
其中的Particle Playground (粒子特效)可以产生大量相似物体独立运动的模拟效果。
在自然界中存在很多个体独立而整体相似的物体运动,我们可以通过该粒子特效系统模拟这种符合自然规律的运动,比如雪花、雨点等都可以是我们模拟的对象。
象这种相互之间既有又有制约,整体相似个体不同的物质我们称之为粒子。
Particle Playground (粒子特效)特效可以从物理学和数学上对它们进行描述来模拟生产真实的粒子运动效果,比如纷飞的大雪,飘落的大雨等。
After Effects的粒子特效系统十分强大,我们在这里只对它进行一些入门级的介绍。
启动After Effects 6.5,新建一个项目文件,然后打开“Composition/New Composition”,新建一个Composition合成文件。
大小为720×576,其他选项默认即可。
然后打开“Layer/New/Solid”新建一个固态层,准备将来在这里显示粒子特效。
好了,现在可以增加粒子特效了。
选中Solid层,打开“Effect/Simulation/Particle Playground”菜单选项,就可以把粒子特效加入到图层中了。
默认情况下,你会在预览窗口中看到红色的粒子,按下小键盘上的0键预览,粒子就会以每秒100粒的速度朝窗口的顶部发射红色的粒子。
- 1、下载文档前请自行甄别文档内容的完整性,平台不提供额外的编辑、内容补充、找答案等附加服务。
- 2、"仅部分预览"的文档,不可在线预览部分如存在完整性等问题,可反馈申请退款(可完整预览的文档不适用该条件!)。
- 3、如文档侵犯您的权益,请联系客服反馈,我们会尽快为您处理(人工客服工作时间:9:00-18:30)。
PARTICLE SIZEING DIVIDING MILLING PARTICLE SIZEING DIVIDING MILLING PARTICLE SIZEING DIVIDING MILLING PARTICLE SIZEING PARTICLE SIZEING DIVIDING MILLING PARTICLE SIZEING PARTICLE
MILLING
微型研磨机
⏹ 极少的样品处理量 < 5 ml ⏹ 操作极其简单
⏹ 仪器精密紧凑,具有极高的性价比
⏹应用领域
适用于少量干性样品,或悬浮液中固体样品的研磨。
也可用于乳浊液的混合和均匀化处理。
样品处理量为5 ml。
是理想化的样品预处理设备,如化学分析,色谱,质谱或X—射线衍射分析等。
也可用于基因测量中的样品准备,均匀活化成份,法医分析提取物的预处理,颜料或者其它贵重样品的研磨。
⏹工作原理
研磨碗以较高的振幅垂直振荡,通过研磨球的冲击力以及研磨碗和研磨球之间的摩擦力来减小样品的尺寸。
⏹设计特性
⏹小容积的研磨碗(2种型号可供选择)⏹与研磨样品接触面积小
⏹快速锁紧的研磨碗
⏹旋钮锁紧装置
⏹垂直振荡振幅可达到9 mm
⏹研磨时间可重复,可调整
⏹压力频率可调节
⏹可规定振动频率(15 – 50 Hz)
⏹良好的机轴马达
⏹膜保护的操作键盘
⏹优点
⏹非常少的样品处理量< 5 ml
⏹操作十分简易
⏹研磨组件易于清洗
⏹快速可重复的研磨
⏹易于维修
⏹安全鉴定(CE标记)
⏹一年的保修期
⏹附件
⏹研磨碗和研磨球
为了避免由研磨组件磨损带来的不必要的污染,
共有4种不同材质的研磨碗和研磨球可供选择。
材质密度g/cm3耐磨程度研磨的样品
玛瑙
99.9% SiO22.65 好柔软到中等硬度样品的
“无铁”研磨
氧化锆94.8% ZrO25.7 非常好纤维性的,
易磨损的样品
不锈钢
碗:17-19% Cr+8-10% Ni 球:12.5-14.5 Cr+1% Ni 7.8 相当好中等硬度,
脆性的样品
普通钢
碗:11-12%Cr 球:1.0-1.65%Cr 7.9 好中等硬度,
脆性的样品
每个研磨碗推荐使用研磨球的数量
研磨碗/ 有效容量球直径
15 ml
0.5…5 ml
10 ml
0.2…1 ml
5 ml
0.1…1 ml
或15 mm 2 1
或10 mm 8 3
或 5
mm 60 30 20 在通常情况下,应使用相同材质的研磨碗和研磨球。
PARTICLE SIZEING DIVIDING MILLING PARTICLE SIZEING DIVIDING MILLING PARTICLE SIZEING DIVIDING MILLING PARTICLE SIZEING PARTICLE SIZEING DIVIDING MILLING PARTICLE SIZEING DIVIDING
MILLING
技术参数
最大进样尺寸 6 mm
最大处理量 可达到5 ml 最终精度 10 µm
电学参数 100-240V/1~,
50-60Hz ,100瓦
重量 净重15 kg ,毛重20 kg 尺寸 20 × 30 × 30 cm (宽×高×长)
包装描述 纸箱25 × 35 × 35 cm
订货参数
订货号 描述 标记询价
微型研磨机 “pulverisette 23”
不包括研磨碗和研磨球
23.1000.00 主机,100-240 V/1~, 50-60 Hz
研磨碗 体积为15 ml 23.1427.00 氧化锆 23.1410.00 不锈钢 23.1409.00 普通钢
研磨碗 体积为10 ml 23.1305.00 玛瑙 23.1327.00 氧化锆 23.1310.00 不锈钢 23.1309.00 普通钢
23.1600.00 研磨碗 体积为5 ml PTFE
研磨球 直径为15 mm 55.0150.05 玛瑙,抛光的 55.0150.27 氧化锆 55.0150.10 不锈钢 55.0150.09 普通钢
研磨球 直径为10 mm 55.0100.05 玛瑙,抛光的 55.0100.27 氧化锆 55.0100.10 不锈钢 55.0100.09 普通钢
研磨球 直径为5 mm 55.0050.05 玛瑙,抛光的 55.0050.27 氧化锆 55.0050.10 不锈钢 55.0050.09
普通钢。