品质——SPC
SPC品质指标

SPC各项品质指标一、SPC应用到的一些专有名词二、品质指标的来源1、产品计量值的规格2、统计学名词(1)组距(R):一组数据中的最大值减最小值。
R=MAX-MIN(2)平均数(Mean,但通常用Xbar或X表示):把一组数据全部相加,再除以该组数据的个数。
X=(X1+X2+……Xn)/n(3)中位数(Median,通常用M表示):把一组数据先按大小顺序排列起来,然后取最中间的一位。
如若该组数据为奇数,则取最中间一位,如若该组数据为偶数,则取中间两位的其中一位。
(4)方差(σ2,有时也用S来表示):有该组数据中每个数据减实际平均数平方的和再除以该数组数据的个数(N)σ 2 = ∑(Xi-Xbar)2n-1(5)标准差(S):可直接由方差开平方得来。
S=σ= [(X1-X )2 +(X2–X)2+…+ (X n-X )2] /(n-1)3管制界限(1)管制中心线(Center line)即实际数据的平均值(即Xbar)(2)管制上限(Upper Control Level, 缩写为UCL)由Xbar加上三倍的标准差(3)管制下限(Low Control Level, 缩写为LCL):由Xbar减去三倍的标准差CL=XbarUCL=Xbar+3σLCL= Xbar-3σ4.品质指标工程能力指數(C Pk),是將工程能力的實力與規格相比較,做為判斷工程是否能制出滿足規格的制品.(1).制程准确度Ca(Capability Of Accuracy)Ca =(實際平均值-規格中心值)/規格公差的一半╳100%(X-μ) ×100%T/2規格公差(T)=規格上限-規格下限=Su-Si(2). 製程精密度Cp(Capability Of Precision)Cp =規格公差/6倍標準差= T / 6單邊規格時:=規格上限-平均值/3倍標準差或= 平均值-規格下限/3倍標準差(3). 製程能力指數C Pk = (1-K)T / 6δ = (1- Ca) ×Cp(δ表示標準差). 单边规格时CPK=CP工程能力有無之評價基準(4).百万分之不良PPM:有的叫DPPM,它是一个概率的概念。
了解SPC对品质管理的作用

了解SPC对品质管理的作用SPC(Statistical Process Control)是一种统计过程控制方法,它在品质管理中起着重要作用。
通过收集并分析数据,SPC帮助企业监控和控制生产过程,从而提高产品的质量。
SPC通过监控数据的变异性,帮助企业了解生产过程的稳定性和可预测性。
它利用统计方法分析生产过程中的不确定性,提供了一种量化的评估方法。
SPC可以检测生产过程中的特殊因素,如机器故障、工艺变化或操作错误,这些因素可能导致产品质量的不稳定。
通过实时监控和反馈,SPC可以帮助企业及时发现问题,采取纠正措施,避免次品率的上升。
SPC帮助企业识别和分析可能导致质量问题的根本原因。
它通过收集大量的数据,构建数据模型,并运用统计分析方法,帮助企业确定哪些因素对产品质量起主导作用。
通过定量分析,SPC能够指导企业采取控制措施,优化生产过程。
例如,当SPC分析结果表明某个关键因素对产品质量影响较大时,企业可以针对这个因素进行优化,从而提高产品的品质。
SPC还可以辅助企业进行实时监测和提升生产过程的能力。
通过收集和分析大量的实时数据,SPC可以检测到任何小的异常和偏差,并及时发出警报。
这种实时的监测和控制系统可以帮助企业快速反应,并采取相应的纠正措施,从而减少不合格产品的产生。
通过分析历史数据,SPC可以提供预测性分析,帮助企业优化生产计划,减少资源的浪费。
SPC还在品质管理中起到了提高生产效率和降低成本的作用。
通过对生产过程的精确控制和优化改进,SPC可以减少生产的变异性,提高产品的一致性和稳定性。
这样一来,企业可以减少废品率,提高产出率,并降低返工和再制造的成本。
SPC还可以帮助企业及时发现生产过程中的浪费和瓶颈,并提供相应的改进措施,增加生产效率和产能。
综上所述,SPC对品质管理起着重要的作用。
它通过监控和控制生产过程的变异性,帮助企业提高产品的质量,降低不合格产品的产生。
SPC还可以辅助企业分析产生问题的根本原因,并优化生产过程。
SPC分析

SPC基础理论及实际应用第一部分第一部分::品质概念品质管制演进史一、操作者品质管制二、领班的品质管制三、检查员的品质管制四、统计品质管制(Statistical Quality Control, SQC)五、全面品质管制(Total Quality Control, TQC)六、全公司品质管理(Company-Wide Quality Control, CWQC)七、全集团品质管理(Group-Wide Quality Control, GWQC)第二部分:SPCSPC的起源与发展(二)(SPC)(Statistical Process Control ). SPC. SPCB. SPC(Q.C.)C.SPC. SPCSPC. SPCB. SPC UCLSPCD. SPC SPC. ------B.X- MR Chart ()NP Chart ()U Chart (). X-R Chart () 1. X-RR Chart.X()2. X-R2)K(K15---25)3)X R ΣRK(UCL)=R×D3x=R=X max-X minR=中心线5)X Chart ΣX i K (UCL)=X+A2RX=. X-MR Chart () 1.2. X-MR X-RX-R: (N=45)3. X-MR1XMR i= X i -X i-1 3)MR ChartM S MR i K-1(UCL)=D3MRMR=4)X ChartS X iK(UCL)=X+3X=MRMRd2d2. P Chart ()P Chart (N)UCL LCL2./(N)(N)UCL LCL3. P Chart1PD 1+D 2+D 3+D 4+--k N 1+N 2+N 3+N 4+--kP i==P=5)P Chart(UCL)=P+3P(1-P)P(1-P)N N. C Chart ()//1)(N)1-----D K3)C ChartD1+D2+---+D KK(UCL)=C+3 C=CC第三部分第三部分::制程能力指数Cp&Cpk 基础理论每件产品的尺寸与别的都不同范围范围次数由分布图可与规格比较分布又可以通过以下因素来加以区分*位置*分布宽度(从最小值至最大值之间的距离)*形状(是否对称是否对称、、偏斜等)范围范围范围分布之中心倾向---准确度分布的散布状态--精密度精密度与准确度精密度准确度规格上限规格下限规格上限规格下限规格上限规格下限规格上限规格下限×√√√√×××:所以我们最希望得到的分布是:所以我们最希望得到的分布是既准确又精密相关的参数相关的参数::XбLSLUSL S Mean 平均值Standard Deviation样本标准差Sigma 标准差--总体的标准差Upper Specification Limited规格上限Lower Specification Limited规格下限Cpu--Process Performance related to the USL能力指数上限Cpl--Process Performance related to the LSL能力指数下限CPK--Min(Cpl,Cpu)稳定过程的能力指数制程能力指数制程能力指数::Cp--Process Capability工序潜能指数S=(Xi-X)-1n =1i n 2相关参数之计算公式相关参数之计算公式::* 由于总体标准差永不可知,故而用样本标准差S 代替标准差бCp=USL-LSL6S*相关参数之计算公式相关参数之计算公式::Cpk=Min(Cpl,Cpk)Cpl=3S X-LSL Cpu=3SUSL-X正态分布(Normal Distribution)∞-1б+1б-2б-3б-4б-5б-6б+2б+3б+4б+5б+6б+∞68.26%95.44%99.73%99.9973%99.999943%99.9999998%-3S +3SX USLLSLX-LSLUSL-XUSL-LSLCpu=3SUSL-X 3S3S6SCpl=3S X-LSL Cpk=Min(Cpl,Cpk)Cp=USL-LSL 6S1Cpk≥1.671.67>Cpk≥1.331.33>Cpk≥1.001.00>Cpk≥0.670.67>Cpk LSL USL LSL USL LSL USL LSL USL LSL USL2 3 4 5Cpk分布与规格之关系制程能力判断太佳可考虑缩小规格简化或降低成本理想,保持必须保持,需注意有不良品要改善不足警告合格应采取紧急措施非常不足处置No.sssss本公司要求当Cpk<1.33时必须有改善行动之计划时必须有改善行动之计划。
品质SPC

1以顾客为关注焦点:组织依存于其顾客。
因此组织应理解顾客当前和未来的需求,满足顾客并争取超越顾客期望。
2领导作用:领导者确立本组织统一的宗旨和方向。
他们应该创造并保持使员工能充分参与实现组织目标的内部环境。
3全员参与:各级人员是组织之本,只有他们的充分参与,才能使他们的才干为组织获益。
4过程方法:将相关的活动和资源作为过程进行管理,可以更高效地得到期望的结果。
5管理的系统方法:识别、理解和管理作为体系的相互关联的过程,有助于组织实现其目标的效率和有效性。
6持续改进:组织总体业绩的持续改进应是组织的一个永恒的目标。
7基于事实的决策方法:有效决策是建立在数据和信息分析基础上。
8互利的供方关系:组织与其供方是相互依存的,互利的关系可增强双方创造价值的能力。
这八项质量管理原则形成了ISO9000族质量管理体系标准的基础。
一、质量管理八项原则产生的背景二、随着全球竞争的不断加剧,质量管理越来越成为所有组织管理工作的重点。
一个组织应具有怎样的组织文化,以保证向顾客提供高质量的产品呢?ISO/TC176/SC2/WG15结合ISO9000标准2000年版制订工作的需要,通过广泛的顾客调查制订成了质量管理八项原则。
三、质量管理八项原则最初以ISO/TC176/SC2/WG/N125号文件《质量管理原则及其应用指南》发布,在ISO/TC176召开的特拉维夫会议前以绝对多数的赞同票得到通过。
为了能对质量管理原则的定义取得高度的一致,又编制了仅包含质量管理八项原则的新文件ISO/TC176/SC2/WG15/N130《质量管理原则》。
在1997年9月27日至29日召开的哥本哈根会议上,36个投票国以32票赞同4票反对通过了该文件,并由ISO/TC176/SC2/N376号文件予以发布。
四、二、质量管理八项原则及其应用指南五、原则1—以顾客为中心六、组织依存于他们的顾客,因而组织应理解顾客当前和未来的需求,满足顾客需求并争取超过顾客的期望。
【品质管理资料】spc 知识精品版

SPC能解决之问题1.经济性:有效的抽样管制,不用全数检验,不良率,得以控制成本。
使制程稳定,能掌握品质、成本与交期。
2.预警性:制程的异常趋势可即时对策,预防整批不良,以减少浪费。
3.分辨特殊原因:作为局部问题对策或管理阶层系统改进之参考。
4.善用机器设备:估计机器能力,可妥善安排适当机器生产适当零件。
5.改善的评估:制程能力可作为改善前後比较之指标。
利用管制图管制制程之程序1.绘制「制造流程图」,并用特性要因图找出每一工作道次的制造因素(条件)及品质特性质。
2.制订操作标准。
3.实施标准的教育与训练。
4.进行制程能力解析,确定管制界限。
5.制订「品质管制方案」,包括抽样间隔、样本大小及管制界限。
6.制订管制图的研判、界限的确定与修订等程序。
7.绘制制程管制用管制图。
8.判定制程是否在管制状态(正常)。
9.如有异常现象则找出不正常原因并加以消除。
10.必要时修改操作标准(甚至於规格或公差)。
分析用管制图主要用以分析下列二点:(1)所分析的制(过)程是否处於统计稳定。
(2)该制程的制程能力指数(Process Capability Index)是否满足要求。
-控制图的作用:1.在质量诊断方面,可以用来度量过程的稳定性,即过程是否处于统计控制状态;2.在质量控制方面,可以用来确定什么时候需要对过程加以调整,而什么时候则需使过程保持相应的稳定状态;3.在质量改进方面,可以用来确认某过程是否得到了改进。
应用步骤如下:1.选择控制图拟控制的质量特性,如重量、不合格品数等;2.选用合适的控制图种类;3.确定样本容量和抽样间隔;4.收集并记录至少20~25个样本的数据,或使用以前所记录的数据;5.计算各个样本的统计量,如样本平均值、样本极差、样本标准差等;6.计算各统计量的控制界限;7.画控制图并标出各样本的统计量;8.研究在控制线以外的点子和在控制线内排列有缺陷的点子以及标明异常(特殊)原因的状态;9.决定下一步的行动。
SPC制程能力分析品质

SPC制程能力分析品质
SPC(统计过程控制)是一种广泛应用于品质管理领域的统计方法,
能够帮助企业监控和控制产品制造过程中的变异性。
通过收集和分析过程
中的数据,SPC可以评估制程的能力,确定该制程是否稳定且具有一致的
性能。
1.数据收集:首先,需要收集关于制程的数据。
这些数据可以包括来
自不同阶段的样本数据,例如原材料、加工过程中的中间产品和最终产品
的检测数据。
2.数据整理:将收集到的数据进行整理和准备,以便进行分析。
这包
括数据的清洗、筛选和对齐等操作。
3.基础统计分析:使用基本的统计方法来分析数据,例如计算平均值、标准差、极差等指标。
这些指标可以给出制程的平均性能和变异性。
4.制程稳定性分析:通过分析统计文件或绘制控制图来评估制程的稳
定性。
控制图可以显示制程数据的变化情况,并帮助判断制程是否受到特
殊原因的影响。
5. 制程能力分析:制程能力指标可以帮助评估制程的性能是否满足
产品要求。
常用的制程能力指标包括Cp、Cpk和Pp、Ppk等。
这些指标表
示制程的离散度与规范化能力。
- Cp和Cpk:用于评估制程的离散度和中心性,分别表示过程的总变
异度和自然过程偏离规格的变异度。
Cpk大于等于1时,表示制程能力满
足规格要求。
- Pp和Ppk:用于评估制程的离散度和中心性,与Cp和Cpk类似,由于Pp和Ppk考虑了过程所处的分布形状,并对过多偏离规格限制的量进行了惩罚。
spc质量管理
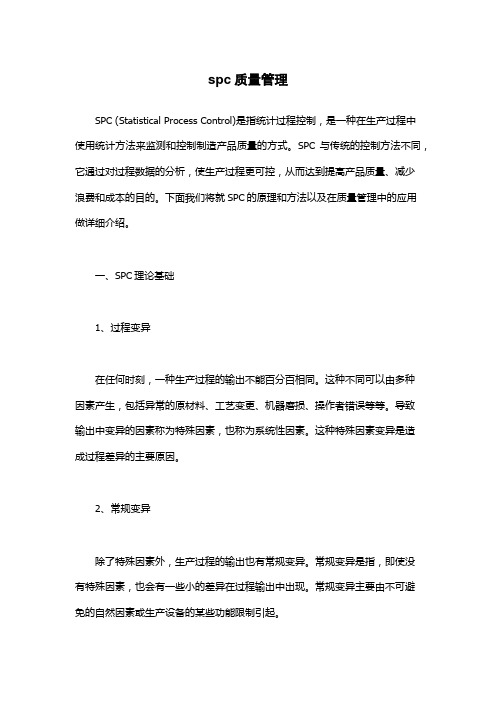
spc质量管理SPC (Statistical Process Control)是指统计过程控制,是一种在生产过程中使用统计方法来监测和控制制造产品质量的方式。
SPC与传统的控制方法不同,它通过对过程数据的分析,使生产过程更可控,从而达到提高产品质量、减少浪费和成本的目的。
下面我们将就SPC的原理和方法以及在质量管理中的应用做详细介绍。
一、SPC理论基础1、过程变异在任何时刻,一种生产过程的输出不能百分百相同。
这种不同可以由多种因素产生,包括异常的原材料、工艺变更、机器磨损、操作者错误等等。
导致输出中变异的因素称为特殊因素,也称为系统性因素。
这种特殊因素变异是造成过程差异的主要原因。
2、常规变异除了特殊因素外,生产过程的输出也有常规变异。
常规变异是指,即使没有特殊因素,也会有一些小的差异在过程输出中出现。
常规变异主要由不可避免的自然因素或生产设备的某些功能限制引起。
3、SPC方法SPC方法的核心是确定过程总体的变异范围,并确定过程中的差异是否在可接受的范围内。
在某些情况下,它可以通过实施统计控制来消除这种变异。
SPC方法可以有效地降低过程差异,提高产品质量,减少成本,增加可靠性,提高客户满意度。
二、SPC的应用范围SPC方法可以应用于所有类型的制造过程,包括离散、连续、传统目视检验和自动化检验。
以下是SPC可以处理生产过程的举例:•\t安装对象的物理特性:例如长度、宽度、高度、重量、颜色、性质等。
•\t材料特性:例如硬度、强度、韧性、导电性等。
•\t流体特性:例如温度、压力、流量、粘度等。
•\t机器特性:例如速度、功率、电流、温度、气压等。
•\t操作员特性:例如工作时间、工作速度、操作标准等。
三、SPC的主要原理SPC的主要原理是基于过程变异性的持续监测和控制,包括以下步骤:1、控制图建立控制图以时间为横轴,测量数据为纵轴。
每次收集数据时,都将点绘制到控制图上。
然后通过绘制中心线、上界和下界来确定控制限。
6品质管理方法
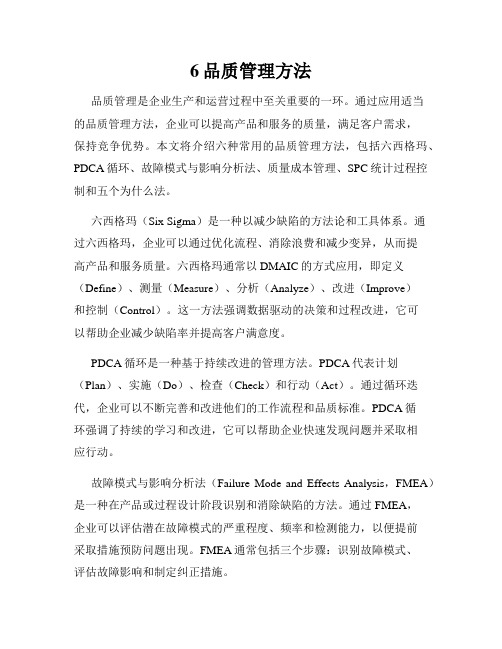
6品质管理方法品质管理是企业生产和运营过程中至关重要的一环。
通过应用适当的品质管理方法,企业可以提高产品和服务的质量,满足客户需求,保持竞争优势。
本文将介绍六种常用的品质管理方法,包括六西格玛、PDCA循环、故障模式与影响分析法、质量成本管理、SPC统计过程控制和五个为什么法。
六西格玛(Six Sigma)是一种以减少缺陷的方法论和工具体系。
通过六西格玛,企业可以通过优化流程、消除浪费和减少变异,从而提高产品和服务质量。
六西格玛通常以DMAIC的方式应用,即定义(Define)、测量(Measure)、分析(Analyze)、改进(Improve)和控制(Control)。
这一方法强调数据驱动的决策和过程改进,它可以帮助企业减少缺陷率并提高客户满意度。
PDCA循环是一种基于持续改进的管理方法。
PDCA代表计划(Plan)、实施(Do)、检查(Check)和行动(Act)。
通过循环迭代,企业可以不断完善和改进他们的工作流程和品质标准。
PDCA循环强调了持续的学习和改进,它可以帮助企业快速发现问题并采取相应行动。
故障模式与影响分析法(Failure Mode and Effects Analysis,FMEA)是一种在产品或过程设计阶段识别和消除缺陷的方法。
通过FMEA,企业可以评估潜在故障模式的严重程度、频率和检测能力,以便提前采取措施预防问题出现。
FMEA通常包括三个步骤:识别故障模式、评估故障影响和制定纠正措施。
质量成本管理是一种将质量成本纳入管理决策过程的方法。
质量成本包括预防成本、评估成本和故障成本。
通过对质量成本的测量和分析,企业可以发现低效的工作流程和低质量的产品,并采取相应措施降低质量成本,提高产品和服务质量。
SPC统计过程控制(Statistical Process Control)是一种通过统计技术监控和控制过程稳定性的方法。
SPC通过收集和分析过程的实时数据,判断过程是否处于可控状态,以及是否存在特殊原因变异。
- 1、下载文档前请自行甄别文档内容的完整性,平台不提供额外的编辑、内容补充、找答案等附加服务。
- 2、"仅部分预览"的文档,不可在线预览部分如存在完整性等问题,可反馈申请退款(可完整预览的文档不适用该条件!)。
- 3、如文档侵犯您的权益,请联系客服反馈,我们会尽快为您处理(人工客服工作时间:9:00-18:30)。
二项分布适用于无限总体。常用于计数检验中的计件 检验。
8
b)泊松分布
1 有关的概率知识
泊松分布总与计点过程相关联,并且计点是在一定时间内、 或一定区域内、或一特定单位内的前提下进行。 例如:检 查一个油漆零件,发现其缺陷数用c表示,c可以是0,1,2……
随机变量 X=c 出现的概率 0 p0 1 P1 2 P2 3 P3 „ „
= X– LSL –––––––– 3σ S
的最小值
28
2 统计过程控制原理
符 号 适 用 过 程 计 算 方 法 PPAP 要求 能力指数 CPk、CP 稳 定 ^ σ =R/d2 CPk≥ 1.33 ^ σ S= 性能指数 Ppk、Pp 不稳定
√
∑ (Xi –– X)2 –––––––––––– N –– 1 Ppk ≥ 1.67
统 计 过 程 控 制 SPC
1
1 有关的概率知识
1.1 随机现象 随机现象 :自然界和社会上发生的许多现 象,具有两种现象:确定现象和不确定现象。 有一类不确定现象,虽然就每次试验或观察 结果来说,它具有不确定性,在大量重复试 验或观察下,它的结果又呈现出某种规律, 称之为统计规律性。这种具有统计规律性的 现象称为随机现象。随机现象的某种结果称 为随机事件。
计数型(离散型)随机变量:(GB/T 3358.1––93 2.6) 只能取有限或可列个值(x1,x2……)的随机变量 x ,通 常又可分为计件和计点,如,抽取n个产品中的不合格品 数,每万米布的疵点数。
计量型(连续型)随机变量:(GB/T 3358.1––93 2.5) 如果随机变量的分布函数 F(x) 可表示为一非负函数 f(x) 的积分, F(x)=∫x-∞ f(x)dx ,如产品的寿命。
27
2 统计过程控制原理
性能指数PP 、Ppk –––– PP:性能指数,定义为不考虑过程有无偏移 时,容差宽度范围除以过程性能,一般表达为: USL– LSL PP=–––––––––– 6σ
★
S
பைடு நூலகம்
–––– Ppk:考虑过程有偏移的性能指数,定义为:
= USL– X ––––––––– 3σ S
或
15
2 统计过程控制原理
2.1 过程 过程是指共同工作以产生输出的供方、生产者、人、 设备、输入材料、方法和环境以及使用输出的顾客之 集合。 人 产品 机 服务 工作方式 / 料 顾客 资源的融合 法 环 输入 过程 / 系统 输出
图2––1
过程控制系统
16
2 统计过程控制原理
2.2 两种过程控制模型和控制策略
图2––8 均值与目标值(规范中心)的关系 ★ 过程能力指数(Cp,CPk) USL–μ – LSL CpkU = –––––– CpkL=μ––––––– Cpk为以上两值较小者 ^ ^
3σ
R/d2
3σ
R/d2
USL– LSL Cp= –––––––––– ^ 6σ
R/d2
26
2 统计过程控制原理
2
1 有关的概率知识
1.1.1 常用术语
频数、频率、概率 频数:(统计学术语 第一部分 一般条件术语 GB/T 3358.1-93 3.14)多次观测中一给定事件发生的次数,或 落入一特定组的观测值个数。 频率:(GB/T 3358.1-93 3.16)频数与试验或观测总数 之比。 概率:(GB/T 3358.1-93 2.1)度量一随机事件发生可 能性大小的实数,其值介于0与1之间。
14
1 有关的概率知识
b) 描述样本分布宽度 极差R=样本中最大值与最小值之差 Xmax-Xmin (GB/T 3358.1– –93 3.27) 估计标准差:(GB/T 3358.1––93 3.30)样本方差的平方根 σ= ^
√
n 1 ––– ∑ n-1 i=1
(Xi – X)2
–––– 计数型 ^ a) 0––1分布(二项分布) r 用不合格率描述:p=––– n 式中:r ––– 不合格个体数 n ––– 样本容量 b)不合格数分布:用每单元不合格数c描述。
3
1 有关的概率知识
1.2 两类随机变量
随机变量:用来表示随机现象结果的变量称为随机变 量。
由定义得知:随机变量 X 取的每一个值,就相应于某 一随机现象,且它具有下列特性:
随机变量的取值是随机的;
随机变量取每个值或在某一区间上取值的概率大小 是确定的。
5
1 有关的概率知识
常见的随机变量
–––– 过程控制系统应能提供正确的统计信息;
–––– 有用的特殊原因变差,应保留: a )该过程是成熟的,经过几个循环的持续改进; b) 允许存在的特殊原因,在已知一段时间内表现出产生稳 定的结果; c) 过程控制计划有效进行,可确保所有的过程输出,符合 规范并能防止出现别的特殊原因。
25
^
2 统计过程控制原理
图2––5
不稳定的过程分布
21
2 统计过程控制原理
两种过程状态 a)
仅存在变差的普通原因
分布是稳定的,呈典型分布
过程是统计受控的 过程是可预测的
图2––6
稳定的过程状态
22
2 统计过程控制原理
b)
存在变差的特殊原因
分布不稳定,偏离典型分布
过程是不受控的 过程是不可预测的 控制图可检出
图2––7
p0 +p1+ p2+ p3+„=1
若λ表示某特定单位内的平均点数(λ>0),又令X表示某特定单 位内出现的点数,则X取x值的概率为: P(X=x)= λxe-λ/x!,x=0,1,… e=2.71828182845…
泊松分布的均值 E(X) = λ, σ2= λ。
9
1 有关的概率知识
正态分布
正态分布图
c)工业经验,约占过程措施的85%。
–––– 局部措施 a)通常用来消除变差的特殊原因; b)通常由与现场有关的人员解决; c)工业经验,约占过程措施的15%。
24
2 统计过程控制原理
过程控制要点
–––– 属于系统的问题不要去责难现场人员,要由系统采 取措施(防止“控制不足–––需要控制时末采取措施”); –––– 属于局部的问题也不要轻易采取系统措施; –––– 考虑经济因素,作出合理的决定;
6
1 有关的概率知识
1.3 两种有关的随机变量的概率分布
计数型(离散型)随机变量分布
a) ― 0-1‖分布,又称[二项分布b(n、p)]
重复进行n次随机试验。如,一枚硬币连抛n次,检 查n个产品的质量,对一个目标连续射击n次等。 n次试验间相互独立。 每次试验只有两个可能结果。 每次试验中成功的概率均为p,失败的概率均为1-p。
29
2 统计过程控制原理
★“目标柱”模式:对于所在规范内的零件,不管它们位于规范内的 什么地方都是好的(可接受),反之都是坏的(不可接受)。 ★ 损失函数模式:顾客或社会的损失,取决于一抛物线且利用随着 某特定的特性值偏离规范目标值越远,呈二次方增加(线性相反) 的原理。 ★“ 目标柱”模式与损失函数模式的比较 表2––4 两种模式的比较
两种性质的变差原因 a) 如果仅存在变差的普通原因随着时间的推移,过程 的输出形成一个稳定的、可重复的分布并可预测。 普通原因:造成变差的一种原因,它影响被研究过 程输出的所有单值;在控制图分析中它表现为随机过 程变差的一部分。
图2––4
稳定的过程分布
20
2 统计过程控制原理
b) 如果存在变差的特殊原因,随着时间的推移,过程 的输出不稳定。 特殊原因:一种间断性的、不可预测的,不稳定的 变差根源。有时被称为可查明原因,存在它的信号( 在控制图中)是:存在超过控制限的点或存在在控制 限之内的链或其它非随机性的图形。
特点:单峰、对称、宽度。 μ –––– 均值 σ 2–––– 方差 σ –––– 标准差 ±3σ –––– 常用来表示变差大小
10
1 有关的概率知识
变量范围与正态分布概率值
变量范围 μ ±σ μ ±2σ μ ±3σ μ ±4σ μ ±5σ μ ±6σ
正态分布概率 0.682689 0.954499 0.997300 0.99993657 0.999999742 0.999999998
f) 样本(容)量:(GB/T 3358.1––93 所包含的个体(或抽样单元)的数量。 3.7)样本中
g)估计:(GB/T 3358.1––93 3.39)根据样本推断 总体分布的未知成份,例如参数。
13
1 有关的概率知识
★ 样本与统计量
统计量:不含有未知参数的样本函数称为统计量。 ––––计量型 a) 描述样本中心位置 n 1 均值 X=––– ∑ xi ~ n i=1 中位数 X:(GB/T 3358.1––93 3.25)当样本量为奇数时,样本的 中位数是一个次序统计量;当样本量为偶数时,是n/2个与第n/2 +1个次序统计量的算术平均数。 次序统计量:(GB/T 3358.1––93 3.24)将样本的各部分量由大到 小排列成X(1),X(2)…,X(n)称X(1),X(2)…,X(n)为次序统计量,X(i) 称为第i个次序统计量。 中位数与中程数不同,中程数:(GB/T 3358.1––93 3.26)样本中 最大值与最小值的算术平均数: (Xmax+Xmin)/ 2 。
控制策略:控制过程,预防缺陷。 图2––3 具有反馈的过程控制模型
18
2 统计过程控制原理
★ 两种模型的比较 两种控制模型的比较
控 制 点 方 法 经 济 性 产品质量
检测模型 最终产品 检 验 差 差
反馈模型 两种呼声 统计方法、信息 好 好