焊接坡口标准汇总
焊接坡口尺寸标准

焊接坡口尺寸标准焊接坡口尺寸标准是指在进行焊接工艺时,对于坡口的尺寸要求和规范。
坡口尺寸的标准化对于焊接工艺的质量和效率具有重要的影响,因此在实际应用中必须严格遵守相关标准,以确保焊接质量和安全。
首先,焊接坡口的尺寸应符合国家标准或行业规范的要求。
不同的焊接材料、焊接方法和焊接位置都有相应的坡口尺寸标准,必须根据具体情况进行选择和执行。
在选择坡口尺寸时,需要考虑焊接材料的厚度、焊缝的类型、焊接位置和所需的焊接强度等因素,以确保焊接质量和可靠性。
其次,焊接坡口的尺寸要求必须严格执行。
在进行坡口准备时,必须按照设计要求和规范进行尺寸标定和加工,不得随意改变或超出规定范围。
特别是在焊接厚板或高强度材料时,坡口尺寸的误差会直接影响焊接接头的质量和强度,因此必须严格控制坡口尺寸的偏差。
另外,焊接坡口尺寸的选择和加工要根据具体的焊接要求进行合理确定。
在进行焊接工艺设计时,必须充分考虑焊接材料的性能、焊接接头的受力情况、焊接方法的选择等因素,以确定最合适的坡口尺寸和形式。
在进行坡口加工时,必须使用适当的工艺设备和加工工具,确保坡口的尺寸和形状符合要求。
最后,焊接坡口尺寸标准的执行和监督是确保焊接质量的关键。
在实际施工和生产中,必须严格按照标准和规范执行坡口尺寸的要求,不得擅自变更或忽视。
同时,必须对焊接坡口的尺寸进行检测和监控,及时发现和纠正尺寸偏差,以确保焊接接头的质量和可靠性。
总之,焊接坡口尺寸标准对于焊接工艺具有重要的意义,必须严格执行和监督。
只有在实际应用中严格遵守相关标准和规范,合理选择和加工坡口尺寸,才能确保焊接质量和安全,提高焊接工艺的效率和可靠性。
管道焊接坡口打磨要求
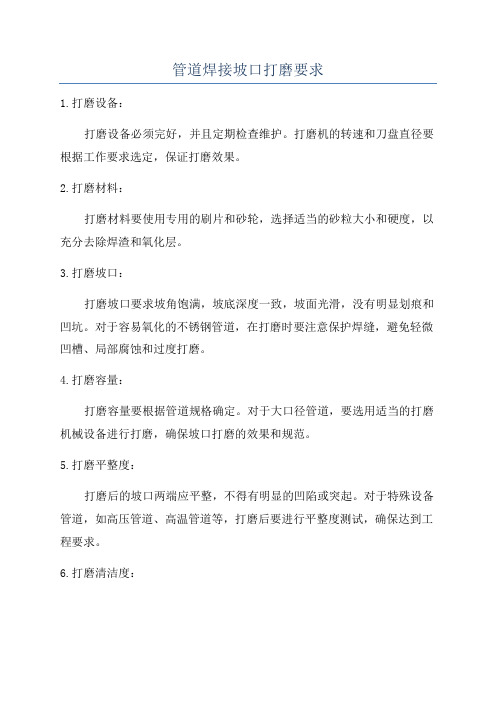
管道焊接坡口打磨要求1.打磨设备:打磨设备必须完好,并且定期检查维护。
打磨机的转速和刀盘直径要根据工作要求选定,保证打磨效果。
2.打磨材料:打磨材料要使用专用的刷片和砂轮,选择适当的砂粒大小和硬度,以充分去除焊渣和氧化层。
3.打磨坡口:打磨坡口要求坡角饱满,坡底深度一致,坡面光滑,没有明显划痕和凹坑。
对于容易氧化的不锈钢管道,在打磨时要注意保护焊缝,避免轻微凹槽、局部腐蚀和过度打磨。
4.打磨容量:打磨容量要根据管道规格确定。
对于大口径管道,要选用适当的打磨机械设备进行打磨,确保坡口打磨的效果和规范。
5.打磨平整度:打磨后的坡口两端应平整,不得有明显的凹陷或突起。
对于特殊设备管道,如高压管道、高温管道等,打磨后要进行平整度测试,确保达到工程要求。
6.打磨清洁度:打磨完毕后,要对焊缝进行清洁处理,确保没有杂质和焊渣。
可以用空气枪吹净焊缝,或者用棉纱蘸酒精进行清洁。
特别是对于不锈钢管道,要避免铁屑等杂质粘附在焊缝上,以免引起锈蚀。
7.打磨光洁度:打磨后的焊缝表面应平整光滑,没有明显的划痕和磨痕。
可以通过目测和手触检查光洁度,也可以使用光洁度仪进行精确的测试。
8.打磨结束标记:打磨结束后,要对每个焊缝进行标记,包括焊接坡口的编号、打磨人员的签字和日期等信息,以便质检人员进行复查。
在管道焊接坡口打磨过程中,要注意操作安全,戴好防护眼镜、面具和手套,避免操作中的意外伤害。
另外,操作人员要熟悉打磨设备和工艺要求,保证打磨质量符合相关标准和规范。
总之,管道焊接坡口打磨对于管道焊接质量的保证至关重要,要严格按照规范要求进行操作,确保焊接接头的质量和可靠性。
管道焊接坡口规范
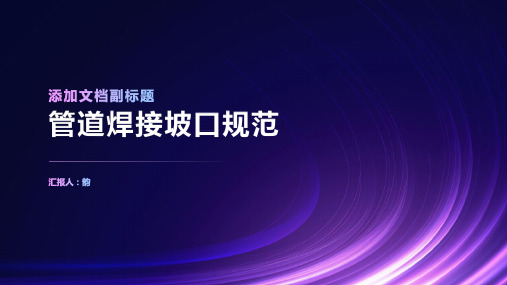
施工安全措施
焊接前应检查管道坡口是否符合规范要求,确保无裂纹、夹渣等缺陷。 焊接时应采取措施防止飞溅和弧光伤人,如使用防护面罩、手套等。 焊接时应保持工作场所整洁,避免易燃易爆物品,并配备灭火器等消防器材。 焊接完成后应进行质量检查,确保无焊接缺陷,并进行必要的防腐处理。
施工质量控制
焊接前检查坡口角度、间隙和钝边是否符合要求 控制焊接电流和电压,保持稳定的焊接参数 焊接过程中注意焊缝的层间温度,避免过热 焊后进行外观检查和无损检测,确保质量合格
火焰加工法:使 用火焰对管道坡 口进行加热,利 用热胀冷缩的原 理进行加工。
激光加工法:利 用激光的高能量 对管道坡口进行 加工,具有精度 高、速度快的特 点。
等离子加工法: 利用等离子弧的 高温对管道坡口 进行切割和加工。
V型坡口
定义:V型坡口是 一种常见的管道 焊接坡口形式, 其形状类似于英 文字母“V”,具 有较大的坡口角 度。
施工记录与报告
记录施工过程:包 括焊接设备、材料、 工艺参数等
报告问题与处理:如 发现焊接缺陷、设备 故障等,应及时报告 并记录处理过程
验收报告:焊接完成 后,应提交验收报告, 包括焊接质量、外观 检测等内容
存档管理:施工记 录与报告应妥善保 存,以便后期查阅 和追溯
感谢您的观看
适用范围:适用于各种类型的管道系统,尤其适用于需要同时传输液体和气体的管道系统
注意事项:在选择和使用复合型坡口时,需要考虑管道系统的压力、温度、介质等参数,以及 管道的安装和维护要求
手工加工坡口
定义:使用手工工 具对管道进行坡口 加工的方法
适用范围:适用于 小批量、小直径管 道的坡口制备
加工工具:砂轮机 、角磨机、坡口机 等
管道焊接坡口规范
钢板开坡口标准

钢板开坡口标准
一、钢板开坡口的概念和作用
钢板开坡口是指在钢板的边缘位置切除一定宽度的坡口,以便焊接工人在坡口内进行操作。
坡口在焊接时可以提高焊接接头的强度和质量,同时也便于后期的加工和维护。
二、钢板开坡口的标准要求
钢板开坡口的厚度标准一般是根据板厚来确定的。
根据国际标准,钢板开坡口的厚度不应超过板厚的三分之一,同时坡口的宽度应为板厚的二倍左右。
具体来说,一般板厚在10mm以下的钢板,开坡口的
厚度应该控制在3mm以内;10mm至50mm的钢板开坡口的厚度应该控制在5mm以内;50mm以上的厚板,坡口的厚度应该控制在板厚的三
分之一以内。
此外,钢板开坡口的出角半径和内角半径也应符合标准。
我们需要根据具体的板厚来控制坡口的出角半径和内角半径,一般角度应大于60度。
三、常见问题解答
1. 钢板开坡口时,切割机的刀具应该如何选择?
一般来说,板厚较小的钢板可以使用手动切割机进行切割,板厚较大的钢板则应选用重型切割机或火焰切割机进行切割。
2. 钢板开坡口时,如何保证坡口的精度?
保证坡口的精度需要从多个方面来控制,如选择合适的切割工具、
控制切割速度和切割深度、保持刀具的锋利度等。
3. 钢板开坡口的角度是否需要注意?
钢板开坡口的角度一般应大于60度,因为过小的角度可能会导致焊接时出现裂纹等问题。
四、总结
钢板开坡口是一项重要的加工工艺,需要严格遵守标准要求,并注意保证坡口的精度和角度。
在实际操作中,我们需要针对具体情况选择合适的工具和操作方法,以保证坡口的质量和焊接接头的强度。
《焊接坡口标准》课件

焊接坡口的定义:焊接时,为了便于焊接和保证焊接质量,在焊接件的连接处预先加工出的一定 形状的斜面
焊接坡口的分类:根据焊接方法、焊接材料、焊接位置等因素,可以分为多种类型
焊接坡口的标准制定原则:保证焊接质量、提高焊接效率、降低焊接成本
焊接坡口的标准制定过程:根据实际需求,制定相应的标准,包括坡口形状、尺寸、角度等参数, 并进行试验验证,确保标准的可行性和可靠性。
焊接过程:控制焊接参数,确保 焊接质量
添加标题
添加标题
添加标题
添加标题
坡口验收:检查坡口尺寸、角度 和表面粗糙度是否符合标准
焊接后处理:对焊接接头进行无 损检测,确保焊接质量
焊接坡口在 管道焊接中 的作用:提 高焊接质量, 减少焊接缺
陷
焊接坡口的 类型:V型、 U型、J型等
焊接坡口的 选择:根据 管道材质、 厚度、焊接 方法等因素 选择合适的
单面坡口:适 用于单面焊接, 如T形接头、角
接接头等
双面坡口:适 用于双面焊接, 如对接接头、
搭接接头等
复合坡口:适 用于复合焊接, 如T形接头、角
接接头等
特殊坡口:适 用于特殊焊接, 如U形接头、V
形接头等
根据焊接方法选择:如电弧焊、气焊、激光焊等 根据焊接材料选择:如钢、铝、铜等 根据焊接位置选择:如平焊、立焊、横焊等 根据焊接质量要求选择:如强度、韧性、耐腐蚀性等
汇报人:PPT
环保型焊接材料的研发:减 少环境污染,提高焊接安全 性
自动化焊接技术的应用:提 高焊接质量和效率
智能化焊接设备的发展:实 现焊接过程的自动化和智能
化
焊接工艺的优化:提高焊接 质量和效率,降低成本
自动化焊接技术的发展:提高焊接质量和效率 3D打印技术的应用:实现复杂结构的焊接 环保型焊接材料的研发:减少环境污染,提高焊接安全性 智能化焊接设备的研发:实现焊接过程的智能化控制和监测
管道坡口标准

管道坡口标准
管道坡口是指管道在安装过程中需要进行切割、倒角和坡口处理的部分,其质
量直接影响着管道的安装和使用效果。
为了确保管道的安全和稳定运行,制定了一系列的管道坡口标准,以规范管道坡口的加工和质量要求。
首先,管道坡口的标准主要包括以下几个方面,坡口形式、坡口角度、坡口长度、坡口加工工艺、坡口质量要求等。
在实际生产中,根据不同的管道材质、管径和工作环境的要求,会有相应的标准来指导坡口的加工和检验。
其次,管道坡口的形式通常包括V型坡口、U型坡口、X型坡口等,其中V型坡口是最常见的一种形式,适用于大多数管道的连接。
坡口角度一般为45度,这
是为了在焊接时能够更好地保证焊缝的质量和强度。
坡口长度则根据管道壁厚和焊接要求来确定,一般为坡口深度的1.5倍至2倍。
另外,管道坡口的加工工艺也是至关重要的。
在进行坡口加工时,需要选择合
适的工艺和设备,确保坡口的加工精度和表面质量。
常见的加工工艺包括机械加工、火焰切割、等离子切割等,其中火焰切割适用于壁厚较大的管道,而等离子切割则适用于壁厚较薄的管道。
最后,管道坡口的质量要求是保证管道连接牢固和密封性能的关键。
坡口的表
面应平整、无裂纹、夹渣和氧化皮等缺陷,焊缝应均匀、牢固,无气孔和夹渣现象。
在进行坡口检验时,需要进行外观检查、尺寸测量和焊缝质量检测等多项内容,确保管道坡口的质量符合标准要求。
总之,管道坡口标准的制定和执行,对于保证管道连接的质量和安全具有重要
意义。
只有严格按照标准要求进行坡口的加工和检验,才能确保管道在使用过程中不出现泄漏、断裂等安全隐患,为工业生产和生活供水等领域提供可靠的支持。
《焊接坡口标准》课件
04
焊接坡口标准的实施与监管
焊接坡口标准的实施流程
焊接坡口标准的制定
根据行业标准和实际需求,制 定焊接坡口标准。
标准培训与宣传
通过培训、宣传等方式,让相 关人员了解和掌握焊接坡口标 准。
标准实施与监督
在生产过程中,对焊接坡口质 量进行检查和监督,确保符合 标准要求。
反馈与改进
02
焊接坡口标准内容
坡口的基本参数
坡口角度
指坡口截面与水平面的 夹角,根据焊接工艺要 求确定,一般取30°-60°
。
钝边高度
指坡口截面垂直于坡口 表面的高度,一般为1-
3mm。
根部间隙
指钝边与焊缝根部的距 离,一般为1-3mm。
坡口宽度
指坡口截面的水平宽度 ,根据板厚和坡口角度
确定。
坡口的制作与加工要求
坡口的加工精度和表面处理能 够影响焊缝的外观和防腐性能 ,进而影响产品质量和使用寿 命。
坡口在焊接安全中的考虑
坡口的设计和加工需要考虑到焊 接过程中产生的气体、飞溅和弧
光等因素,确保作业安全。
在坡口加工过程中,应使用合适 的工具和工艺,避免因操作不当
导致的安全事故。
在焊接过程中,应采取适当的防 护措施,如戴口罩、手套和护目
检查坡口表面质量,应无油污 、锈迹、毛刺、凹凸等缺陷。
对于特殊要求的坡口,应按照 相关标准或规范进行无损检测
,确保坡口内部质量。
验收合格的坡口应做好标识, 并妥善保管,防止损坏或污染
。
03
焊接坡口标准的应用
坡口在焊接工艺中的应用
坡口是焊接工艺中的重要环节,它能够确保焊缝的填充和熔合,提高焊接质量和效 率。
焊接标准汇编
本篇是《焊接材料资料汇编》第五篇。
本篇主要收集了与焊接有关的技术条件、焊接检验、焊接工艺、焊接评定等方面的标准。
本标准集含8个支集,132个标准。
本篇主要考虑焊接技术、检验人员使用,销售人员应掌握其中主要检验方法的知识。
本篇基本包括了焊接材料产品标准中提及的引用标准(除化学试验)部分;产品标准中引用的化学试验标准,将在以后的篇章中予以汇编。
本篇包含的标准目录如下:一、焊接术语、工艺代号、焊缝符号、坡口形式:1、 GB 324-88 焊缝符号表示法2、 GB 985-88 气焊、手工电弧焊及气体保护焊焊缝坡口的基本形式与尺寸3、 GB 986-88 埋弧焊焊缝坡口的基本形式和尺寸4、 GB/T 3375-1994 焊接术语5、 GB/T 5185-2005 焊接及相关工艺方法代号6、 GB/T 19804-2005 焊接结构的一般尺寸公差和形位公差7、 GB/T 16672-1996 焊缝工作位置倾角和转角的定义8、 GB 5185-85 金属焊接及钎焊方法在图样上的表示代号(已被2005版代替)二、硬度试验国家标准集:GB/T230 金属洛氏硬度试验9、 GBT230.1-2004 金属洛氏硬度试验第1部分:试验方法10、 GBT230.2-2002 金属洛氏硬度试验第2部分:硬度计的检验与校准11、 GBT230.3-2002 金属洛氏硬度试验第3部分:标准硬度块的标定GB/T231-2002 金属布氏硬度试验12、 GBT231.1-2002 金属布氏硬度试验第1部分:试验方法13、 GBT231.2-2002 金属布氏硬度试验第2部分:硬度计的检验与校准14、 GBT231.3-2002 金属布氏硬度试验第3部分:标准硬度块的标定GB/T4340-1999 金属维氏硬度试验15、 GB/T 4340.1-1999 金属维氏硬度试验第1部分:硬度的试验16、 GB/T 4340. 2-1999 金属维氏硬度试验第2部分:硬度计的检验17、 GB/T 4340. 2-1999 金属维氏硬度试验第2部分:硬度计的检验GB/T18449-2001 金属努氏硬度试验18、 GB/T 18449.1-2001 金属努氏硬度试验第1部分:试验方法19、 GB/T 18449.2-2001 金属努氏硬度试验第2部分:硬度计的检验20、 GB/T 18449.3-2001 金属努氏硬度试验第3部分:标准硬度块的标定21、 GB/T 4341- 2001 金属肖氏硬度试验方法22、 GB/T 17394-1998 金属里氏硬度试验方法23、 YS/T 471-2004 铜及铜合金韦氏硬度试验方法三、力学性能和扩散氢含量试验24、 GB/T 228-2002 金属材料室温拉伸试验25、 GB/T 229-1994 金属夏比缺口冲击试验方法26、 GB/T 2649-1989 焊接接头机械性能试验取样方法27、 GB/T 2650-1989 焊接接头冲击试验方法28、 GB/T 2651-1989 焊接接头拉伸试验方法29、 GB/T 2652-1989 焊缝及熔敷金属拉伸试验方法30、 GB/T 2653-1989 焊接接头弯曲及压扁试验方法31、 GB/T 2654-1989 焊接接头及对焊金属硬度试验方法32、 GB/T 3965-1995 熔敷金属中扩散氢测定方法33、 GB/T 7314-2005 金属材料室温压缩试验方法34、 GB/T 13239-2006 金属材料低温拉伸试验方法35、 GB/T 11363-89 钎焊接头强度试验方法36、 GB/T 16957-1997 复合钢板焊接接头力学性能试验方法37、 GB/T 19748-2005 钢材夏比V型缺口摆锤冲击试验仪器化试验方法38、 GBT13450-1992 对接焊接头宽板拉伸试验方法(已废止)39、 GBT15747-1995 正面角焊缝接头拉伸试验方法(已废止)40、 GBT7032-1986 T型角焊接头弯曲试验方法(已废止)四、力学性能和扩散氢含量试验41、 GB 17925-1999 气瓶对接焊缝X 射线实时成像检测42、 GB/T 3323-2005 金属熔化焊焊接接头射线照相43、 GB/T 9445-2005 无损检测人员资格鉴定与认证44、 GB/T 11345-1989 钢焊缝手工超声波探伤方法和探伤结果分级45、 GB/T 12604.1-2005 无损检测术语超声检测46、 GB/T 12604.2-2005 无损检测术语射线照相检测47、 GB/T 12604.3-2005 无损检测术语渗透检测48、 GB /T 1260 4. 4-2005 无损检测术语声发射检测49、 GB/T 12604.5-1990 无损检测术语磁粉检测50、 GB/T 15749-1995 定量金相手工测定方法51、 GB/T 15822.1-2005 无损检测磁粉检测第1部分:总则52、 GB/T 15822.2-2005 无损检测磁粉检测无损检测磁粉检测第2部分:检测介质53、 GB/T 15822.3-2005 无损检测磁粉检测第3部分:设备54、 GB/T 18256-2000 焊接钢管(埋弧焊除外)用于确认水压密实性的超声波检测方法55、 GB/T 19500-2004 X射线光电子能谱分析方法通则56、 GB/T 19501-2004 电子背散衍射分析方法通则57、 GB/T 19799.1-2005 无损检测超声检测1号校准试块58、 GB/T 19799. 2-2005 无损检测超声检测2号校准试块59、 GB/T 19937-2005 无损检测渗透探伤装置通用技术要求60、 GB/T 19938-2005 无损检测焊缝射线照相和底片观察条件像质计推荐型式的使用61、 GB/T 19943-2005 无损检测金属材料X和伽玛射线照相检测基本规则62、 JB/T 4930.1-2005 承压设备无损检测第1部分:通用要求63、 JB/T4730.2-2005 承压设备无损检测第2部分射线检测64、 JB/T 4730.3-2005 承压设备无损检测第3部分超声检测65、 JB/T 4730.4-2005 承压设备无损检测第4部分磁粉检测66、 JB/T 4730.5-2005 承压设备无损检测第5部分渗透检测67、 JB/T 4730.6-2005 承压设备无损检测第6部分涡流检测68、 JB/T 8931-1999 堆焊层超声波探伤方法五、裂纹和时效敏感性试验69、 GB /T 4160-2004 钢的应变时效敏感性试验方法(夏比冲击法)70、 GB/T 15248-1994 金属材料轴向等幅低循环疲劳试验方法71、 GB/T 6398-2000 金属材料疲劳裂纹扩展速率试验方法72、 JB/T 4291-1999 焊接接头裂纹张开位移(COD) 试验方法73、 JB/T 6044-1992 焊接接头疲劳裂纹扩展速率侧槽试验方法74、 GB-T4675.5-1984 焊接性试验:焊接热影响区最高硬度试验方法(已废止)75、 GBT2655-1989 焊接接头应变时效敏感性试验方法(已废止)76、 GBT2656-1981 焊缝金属和焊接接头的疲劳试验法(已废止)77、 GBT9446-1988 焊接用插销冷裂纹试验方法(已废止)78、 GBT9447-1988 焊接接头疲劳裂纹扩展速率试验方法(已废止)79、 GBT13816-1992 焊接接头脉动拉伸疲劳试验方法(已废止)80、 GBT13817-1992 对接接头刚性拘束焊接裂纹试验方法(已废止)81、 GB-T4675.1-1984 焊接性试验:斜Y型坡口焊接裂纹试验方法((已废止)82、 GB-T4675.2-1984 焊接性试验:搭接接头(CTS)焊接裂纹试验方法(已废止)83、 GB-T4675.3-1984 焊接性试验:T型接头焊接裂纹试验方法(已废止)84、 GB-T4675.4-1984 焊接性试验:压板对接(FISCO)接头焊接裂纹试验方法(已废止)六、焊接接头质量缺陷分级、评定85、 GB/T 6417.1-2005 金属熔化焊接头缺欠分类及说明86、 GB/T 6417.2-2005 金属压力焊接头缺欠分类及说明87、 GB/T 19418-2003 钢的弧焊接头缺陷质量分级指南88、 JB/T 5104-1991 焊接接头脆性破坏的评定89、 JB/T 6061-1992 焊缝磁粉检验方法和缺陷磁痕的分级90、 JB/T 6062-1992 焊缝渗透检验方法和缺陷迹痕的分级91、 GBT12469-1990 焊接质量保证钢熔化焊接头的要求和缺陷分级(已废止)92、 GBT6417-1986 金属熔化焊焊缝缺陷分类及说明(已废止)七、钢材、不锈钢腐蚀试验、铁素体含量、硬化层深度测量等93、 GB/T 2976-2004 金属材料线材缠绕试验方法94、 GB/T 4334.1-2000 不锈钢10%草酸浸蚀试验方法95、 GB/T 4334.2-2000 不锈钢硫酸-硫酸铁腐蚀试验方法96、 GB/T 4334.3-2000 不锈钢65%硝酸腐蚀试验方法97、 GB/T 4334.4-2000 不锈钢硝酸-氢氟酸腐蚀试验方法98、 GB/T 4334.5-2000 不锈钢硫酸-硫酸铜腐蚀试验方法99、 GB/T 4334.6-2000 不锈钢5%硫酸腐蚀试验方法100、 GB/T 5617-2005 钢的感应淬火或火焰淬火后有效硬化层深度的测定101、 GB/T 9450-2005 钢检渗碳淬火硬化层深度的测定和校核102、 GB/T 9451-2005 钢件薄表面总硬化层深度有效硬化层深度的测定103、 GB/T 15970.1-1995 金属和合金的腐蚀应力腐蚀试验第1部分试验方法总则104、 GB/T 15970.2-2000 金属和合金的腐蚀应力腐蚀试验第2部分弯梁试样的制备和应用105、 GB/T 15970.3-1995 金属和合金的腐蚀应力腐蚀试验第3部分U型弯曲式样的制备和应用106、 GB/T 15970.4-2000 金属和合金的腐蚀应力腐蚀试验第4部分单轴加载拉伸试样的制备和应用107、 GB/T 15970.6-1998 金属和合金的腐蚀应力腐蚀试验第6部分预裂纹试样的制备和应用108、 GB/T 15970.7-2000 金属和合金的腐蚀应力腐蚀试验第7部分慢应变速率试验109、 GB/T 15970.8-2005 金属和合金的腐蚀应力腐蚀试验第8部分:焊接试样的制备和应用110、 GB/T 17898-1999 不锈钢在沸腾氯化镁溶液中应力腐蚀试验方法111、 GB/T 17899-1999 不锈钢点蚀电位测量方法112、 JB/T 7853-1995 铬镍奥氏体不锈钢焊缝金属中铁素体数的测量113、 GBT 1954-80 铬镍奥氏体不锈钢焊缝鉄素体含量测量方法(已被JB/T7853-1995替代)八、焊接工艺评定规程、焊材质量管理规程、焊接技术条件114、 GB/T 11038-2000 船用辅锅炉及受压容器受压元件焊接技术条件115、 GB/T 11364-89 钎料铺展性及填缝性试验方法GB/T 12467-1998 焊接质量要求金属材料的熔化焊116、 GB/T 12467.1-1998 焊接质量要求金属材料的熔化焊第1部分选择及使用指南117、 GB/T12467.2-1998 焊接质量要求金属材料的熔化焊第2部分完整质量要求118、 GB/T 12467.3-1998 焊接质量要求金属材料的熔化焊第3部分一般质量要求119、 GB/T12467.4-1998 焊接质量要求金属材料的熔化焊第4部分基本质量要求120、 GB/T 13147-1991 铜及铜合金复合钢板焊接技术条件121、 GB/T 13148-1991 不锈钢复合钢板焊接技术条件122、 GB/T 13149-1991 钛及钛合金复合钢板焊接技术条件123、 GB/T 18591-2001 焊接预热温度、道间温度及预热维持温度的测量指南124、 GB/T 19419-2003 焊接管理任务与职责125、 GB/T 19805-2005 焊接操作工技能评定126、 GB/T 19866-2005 焊接工艺规程及评定的一般原则127、 GB/T 19867.1-2005 电弧焊焊接工艺规程128、 GB/T 19868.1-2005 基于试验焊接材料的工艺评定129、 GB/T 19868.2-2005 基于焊接经验的工艺评定130、 GB/T 19868.3-2005 基于标准焊接规程的工艺评定131、 GB/T 19868.4-2005 基于预生产焊接试验的工艺评定132、 GB/T 19869.1-2005 钢、镍及镍合金的焊接工艺评定试验。
焊接坡口标准
焊接接头形式及坡口选用焊接结构设计与坡口设计焊接变形产生的原因焊接变形的控制与矫正一、焊接接头形式及坡口选用(a)I形坡口(b)V形坡口(c)X坡口(d)U形坡口(e)双U形坟口两焊件端面间构成300-1350夹角的接头称两焊件端面间构成3001350夹角的接头,称为角接接头。
根据坡口型式的不同,分为不开坡口、单边V形、V形及K形等4种型式坡口单边V形V形及K形等4种型式(a)不开坡口(b)单边V形坡口(c)V形坡口(d)K形坡口一焊件端面与另一焊件表面构成复角或近似直角的接头,称为T形接头。
其应用范围仅次于对接接头。
根据坡口形式不同,分为不开坡口、单边V形、K形和双U形等4种(a)I形坡口(b)单边V形坡口(c)K形坡口(d)双U形坡口以T形接头连接焊缝时,板厚小于3mm可不开放口。
3个焊件装配成“十”字形接头,叫十字接头。
实际上是两T形接头的组合。
装十字接头叫十字接头实上接头的组合两焊件部分重叠构成的接头,叫搭接接头。
根据结构形式和对强度要求不同,分为不开坡口、圆孔内塞焊和长孔内角焊等3种图(a)为不开坡口的搭接接头,用于厚度12mm以下的焊件,有时可采用双面焊接。
这类接头承载能力低,用于不重要结构,有时可采用双面焊接这类接头承载能力低用于不重要结构遇到重叠面积较大时,为保证焊接强度,可分别选用图(b)、(c)两种形式。
获得较好的焊缝(3)调整焊缝成型系数,获得较好的焊缝(4)调节基本金属与填充金属的比例。
(4)焊后应力和变形尽可能小。
(6)铲削或磨削:用手工或风动、电动工具铲削或使用砂轮机(或角向磨光机)磨削加工,效率较低,多用于焊效率较低多用于焊坡口加工质量对焊接过程有很大影响,应符合图纸或技坡口加工质量对焊接过程有很大影响应符合图纸或技二、焊接结构设计与坡口设计工作焊缝:与被连接的元件是串联的,它承失效,其应力称为工作应力。
联系焊缝则需考虑经济性而减小、减短焊缝;联系焊缝则需考虑经济性而减小减短焊缝不考虑联系应力;以对接Y坡口角度α:钝边高度p:需要熔透时一般为1~3mm;需要熔透时般为3根部间隙b坡口深度H或带垫板的对接适合于厚小于16 mm。
焊接坡口标准
四、焊接变形的控制与矫正
1. 设计措施 • (1)合理地选择焊缝
的尺寸和形状(如图)
• 在保证结构承载力的 情况下,尽可能采用较小 的焊缝尺寸, 减少热输 入对材料性能的影响, 并降低成本。
(2)合理选择焊缝长度和数量
只要允许,多采用型材、 冲压件;焊缝多且密集处,可 以采用铸—焊联合结构,就可 以减少焊缝数量。此外,适当 增加壁板厚度,以减少肋板数 量,或者采用压型结构代替肋 板结构,都对防止薄板结构的 变形有利。
矫正焊接变形的措施
3.火焰加热矫正法 • 火焰矫正的原理与机械矫正相反,它是通过局部加热并随之
快冷,使焊件伸长的部位缩短,达到矫正变形的目的。 • 火焰加热的方式有点状加热、线状加热和三角形加热。
• 此法一般使用的是气焊炬,不需专门设备。操作简单方便, 机动灵活,可以在大型复杂结构上进行矫正。
矫正焊接变形的措施
2、坡口的准备 2.1坡口的定义及作用
根据设计或工艺要求,在焊件的待 焊部位加工成一定几何形状和尺寸的沟 槽,叫坡口。 作用是: (1)使热源(电弧或火焰)能到达焊缝根部 ,保证根部焊透。 (2)便于操作和清理焊渣。 (3)调整焊缝成型系数,获得较好的焊缝 成型。 (4)调节基本金属与填充金属的比例。
矫正焊接变形的措施
1. 手工矫正法
2. 机械矫正法
• 用机械方法矫正变形的原理就 是将缩短的尺寸拉长,使之与 较长的部分相适应,从而恢复 到原来的尺寸,或达到技术条 件对几何尺寸的要求。
• 机械矫正法会使金属材料因冷
作硬化而变脆,并产生附加应
力,因此一般适用于变形不大
的小型结构件。
机械矫正法矫正梁的弯曲变形
2.3对称布置变形小;
2.4焊缝布置求分散;