塑料模具毕业设计说明书范本(doc 42页)
塑料模具课程设计说明书范本
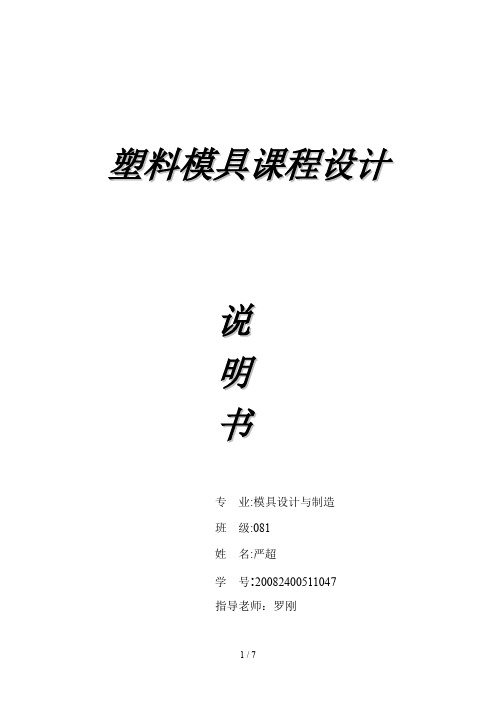
塑料模具课程设计说明书专业:模具设计与制造班级:081姓名:严超学号:20082400511047指导老师:罗刚一、塑件分析、塑料的选取及其工艺性分析该塑件应该是一个塑料板、称套,且承载不高,此符合低压聚乙烯(PE)的特点,并且聚乙烯还拥有硬、耐磨、耐蚀、耐热、及绝缘性好等优点,价格也比较便宜。
而且聚乙烯流动性好、对压力变化敏感,适用高压注射,料温均与,填充速度快、保压充分、易脱模。
聚乙烯的缺点就是成型收缩率范围及收缩值大,易产生缩孔,在流动方向与垂直方向上的收缩差异较大,方向性明显,易变形、翘曲等。
所以,在成型时应控制模温,冷却时应保证冷却均匀、稳定、速度慢且充分冷却。
结果:塑料用聚乙烯成型方式为注塑成型附:聚乙烯(PE)的主要技术指标密度ρ(g/cm3):0.19-0.96收缩率s:1.5-3.6成型温度t/°C:140-22二.确定注射机选用注射机型号为:ft-s200/400型卧式注射机ft-s200/400型卧式注射机有关技术参数如下:最大开合模行程/mm:260模具厚度/mm:165——406喷嘴圆弧半径/mm:18喷嘴孔直径/mm: 4拉杆空间/mm:290×368锁模力/KN:2540额定注射量/cm3:200/400最大注射压力/MPa:109最大注射面积/cm2:645三、型腔数目确定我们小组采用按注射机的额定锁模力来确定型腔数目n,有npA ≤Fp – pA1式中Fp——注射机的额定锁模力254000(N)A——单个塑件在分型面上的投影面积8167.14(mm2)A1——浇注系统在分型面上的投影面积200(mm2)P ——塑料熔体对型腔的成型压力(MPa),其大小一般是注射压力的80%。
代值计算得n = 14.27 故取值为14综合考虑塑件的尺寸及表面的精度要求以及塑件的结构,宜采用盘型浇口。
若采用一模多腔设计、加工难度大,成本高。
所以采用一模两腔。
结果:型腔数目为二四、分型面的选择及浇注系统设计分型面选择一般原则1.分型面应选在塑件外形最大轮廓处2.避免模具结构复杂3.分型面应便于塑件脱模4分型面应有利于侧面分型及抽芯5.分型面应保证塑件质量6.分型面的选择用力与防止溢流7.分型面的选择应有利与排气8.分型面的选择应使成型零件便于加工9.应尽量减少由于脱模斜度造成塑件大小端的差异参考着以上原则,我们的分型面选在了A面浇注系统设计原则1.了解塑料的工艺特性2.排气量好3.防止型芯和塑件变形4.减少熔体流程即塑料耗量5.修整方便,并保证塑件的外观质量6.要求热量及压力损失小参考着以上原则,我们采用如图所示浇注系统(2)浇口套选用浇口套如图所示材料T10A钢,热处理淬火后表面硬度为53HRC~57HRC五、成型零部件设计查有关资料得聚乙烯(PE)的收缩率为S = 1.5% ——3.5% ,故平均收缩率Sca = (1.5%+3.5%)/2 = 2.5% =0.025 根据塑件尺寸公差要求,模具的公差取δz = Δ/4 。
塑料模具设计说明书(样本).docx
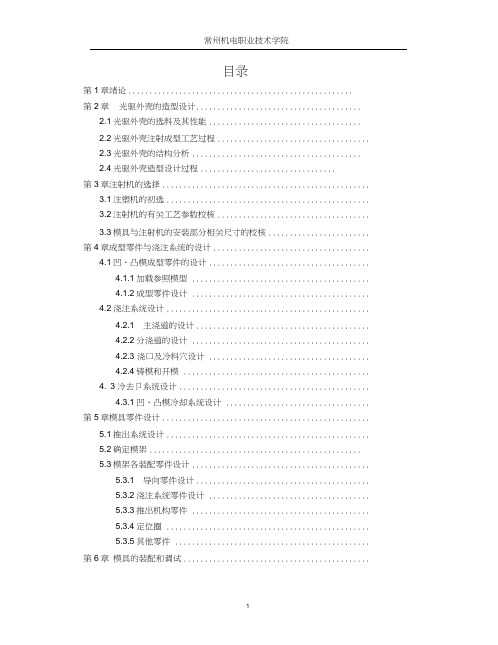
目录第1章绪论.....................................................第2章光驱外壳的造型设计.......................................2.1光驱外壳的选料及其性能....................................2.2光驱外壳注射成型工艺过程....................................2.3光驱外壳的结构分析........................................2.4光驱外壳造型设计过程................................第3章注射机的选择.................................................3.1注塑机的初选................................................3.2注射机的有关工艺参数校核....................................3.3模具与注射机的安装部分相关尺寸的校核........................ 第4章成型零件与浇注系统的设计.....................................4.1凹、凸模成型零件的设计......................................4.1.1加载参照模型 ..........................................4.1.2成型零件设计 ..........................................4.2浇注系统设计................................................4.2.1 主浇道的设计.........................................4.2.2分浇道的设计 ..........................................4.2.3 浇口及冷料穴设计 ......................................4.2.4铸模和开模 ............................................4. 3 冷去卩系统设计.............................................4.3.1凹、凸模冷却系统设计 .................................. 第5章模具零件设计.................................................5.1推出系统设计................................................5.2确定模架..................................................5.3模架各装配零件设计..........................................5.3.1 导向零件设计.........................................5.3.2浇注系统零件设计 ......................................5.3.3推出机构零件 ..........................................5.3.4定位圈 ................................................5.3.5其他零件 .............................................. 第6章模具的装配和调试............................................6.1模具的装配..................................................6.2模具的调试.................................................. 结束语.....参考文献...附录一图纸第1章绪论注射成型也称注塑,是塑料的一种重要成型方法。
塑料模具毕业设计说明书

河南机电高等专科学校课程设计说明书题目:端盖塑料模具设计系部材料工程系专业模具制造与设计专业班级模具081班学生姓名韩雪飞学号081304129指导教师于智宏2011年 3 月15 日目录绪论……………………………………………………………………………………1一、模塑工艺工艺规程的编制 (2)1.塑件工艺性分析 (2)1.1塑件的原材料分析 (2)1.2.1塑件的结构和尺寸精度及表面质量分析 (3)1.3计算塑件的体积和质量 (3)1.4塑件注塑工艺参数的确定 (4)1.5塑件成型设备的选取 (4)二、注塑模具结构设计 (5)2.1分型面选择 (5)2.2.1确定型腔数目和排列方式 (6)2.2.1.1按注射机的额定锁模力确定型腔数量 (6)2.2.1.2按注射机的注塑量确定型腔数量 (6)2.2.2型腔的排列方式 (7)2.3浇注系统的设计 (8)2.4.推出机构的设计 (9)2.5凹模的设计 (10)三、端盖注塑模具的有关计算 (11)四、模具加热和冷却系统的设计 (12)五、模具闭合高度确定 (13)六、注塑机有关参数的校核 (13)七、注塑模具的安装和调试 (13)八、结论 (16)九、参考文献 (17)绪论大学三年的学习即将结束,毕业设计是其中最后一个实践环节,是对以前所学的知识及所掌握的技能的综合运用和检验。
随着我国经济的迅速发展,采用模具的生产技术得到愈来愈广泛的应用。
随着工业的发展,工业产品的品种和数量不断增加。
换型不断加快。
使模具的需要补断增加。
而对模具的质量要求越来越高。
模具技术在国民经济中的作用越来越显得更为重要。
模具是制造业的重要工艺基础,在我国,模具制造属于专用设备制造业。
中国虽然很早就开始制造模具和使用模具,但长期未形成产业。
直到20世纪80年代后期,中国模具工业才驶入发展的快车道。
近年,不仅国有模具企业有了很大发展,三资企业、乡镇(个体)模具企业的发展也相当迅速。
虽然中国模具工业发展迅速,但与需求相比,显然供不应求,其主要缺口集中于精密、大型、复杂、长寿命模具领域。
塑料模具设计说明书(参考)
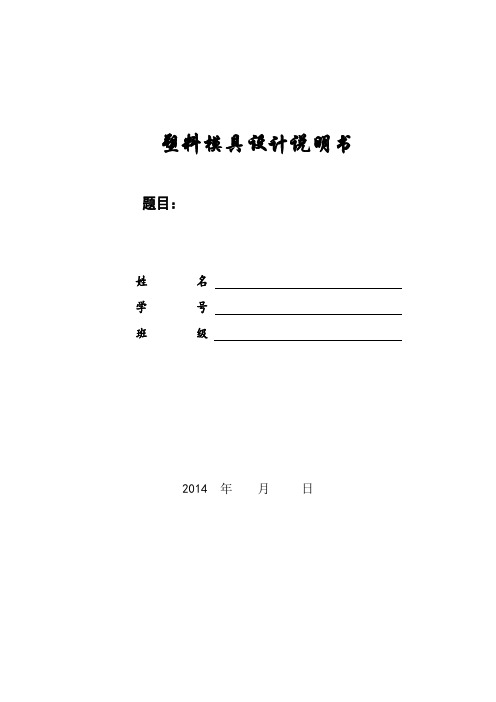
塑料模具设计说明书题目:姓名学号班级2014 年月日目录第一章塑件的工艺分析1.1 任务要求1.2 原料ABS的成型特性和工艺参数1.3 塑件的结构工艺性第二章注射设备的选择2.1 注射成型工艺条件2.2 选择注射机第三章型腔布局与分型面的选择3.1 塑件的布局3.2 分型面的选择第四章浇注系统的设计4.1主流道和定位圈的设计4.2 分流道设计4.3 浇口的设计4.4冷料穴的设计4.5 排气系统的分析第五章主要零部件的设计计算5.1 型芯、型腔结构的确定5.2 成型零件的成型尺寸第六章成型设备的校核6.1、注射成型机注射压力校核6.2、注射量的校核6.3、锁模力的校核相关零件图第一章塑件的工艺分析1.1 任务要求图1 盒盖1.2原料ABS的成型特性和工艺参数ABS是目前产量最大、应用最广的工程塑料。
ABS是不透明非结晶聚合物,无毒、无味,密度为 1.02~1.05 g/cm3。
ABS 具有突出的力学性能,坚固、坚韧、坚硬;具有一定的化学稳定性和良好的介电性能;具有较好尺寸稳定性,易于成型和机械加工,成型塑件表面有较好光泽,经过调色可配成任何颜色,表面可镀铬。
其缺点是耐热性不高,连续工作温度约为70℃,热变形温度约为93℃,但热变形温度比聚苯乙烯、聚氯乙烯、尼龙等都高;耐候性差,在紫外线作用下易变硬发脆。
可采用注射、挤出、压延、吹塑、真空成型、电镀、焊接及表面涂饰等多种成型加工方法。
ABS的成型特性:(1)ABS易吸水,成型加工前应进行干燥处理,表面光泽要求高的塑件应长时间预热干(2)流动性中等,溢边值0.04 mm左右。
(3)壁厚、熔料温度对收缩率影响极小,塑件尺寸精度高。
(4)ABS比热容低,塑化效率高,凝固也快,故成型周期短。
(5)ABS的表观黏度对剪切速率的依赖性很强,因此模具设计中大都采用点浇口形式。
(6)顶出力过大或机械加工时塑件表面会留下白色痕迹,脱模斜度宜取2°以上。
(7)易产生熔接痕,模具设计时应注意尽量减少浇注系统对料流的阻力。
塑料模具毕业设计说明书

河南机电高等专科学校课程设计说明书题目:端盖塑料模具设计系部材料工程系专业模具制造与设计专业班级模具081班学生姓名韩雪飞学号081304129指导教师于智宏2011年 3 月15 日目录绪论……………………………………………………………………………………1一、模塑工艺工艺规程的编制 (2)1.塑件工艺性分析 (2)1.1塑件的原材料分析 (2)1.2.1塑件的结构和尺寸精度及表面质量分析 (3)1.3计算塑件的体积和质量 (3)1.4塑件注塑工艺参数的确定 (4)1.5塑件成型设备的选取 (4)二、注塑模具结构设计 (5)2.1分型面选择 (5)2.2.1确定型腔数目和排列方式 (6)2.2.1.1按注射机的额定锁模力确定型腔数量 (6)2.2.1.2按注射机的注塑量确定型腔数量 (6)2.2.2型腔的排列方式 (7)2.3浇注系统的设计 (8)2.4.推出机构的设计 (9)2.5凹模的设计 (10)三、端盖注塑模具的有关计算 (11)四、模具加热和冷却系统的设计 (12)五、模具闭合高度确定 (13)六、注塑机有关参数的校核 (13)七、注塑模具的安装和调试 (13)八、结论 (16)九、参考文献 (17)绪论大学三年的学习即将结束,毕业设计是其中最后一个实践环节,是对以前所学的知识及所掌握的技能的综合运用和检验。
随着我国经济的迅速发展,采用模具的生产技术得到愈来愈广泛的应用。
随着工业的发展,工业产品的品种和数量不断增加。
换型不断加快。
使模具的需要补断增加。
而对模具的质量要求越来越高。
模具技术在国民经济中的作用越来越显得更为重要。
模具是制造业的重要工艺基础,在我国,模具制造属于专用设备制造业。
中国虽然很早就开始制造模具和使用模具,但长期未形成产业。
直到20世纪80年代后期,中国模具工业才驶入发展的快车道。
近年,不仅国有模具企业有了很大发展,三资企业、乡镇(个体)模具企业的发展也相当迅速。
虽然中国模具工业发展迅速,但与需求相比,显然供不应求,其主要缺口集中于精密、大型、复杂、长寿命模具领域。
注塑模具毕业设计【范本模板】
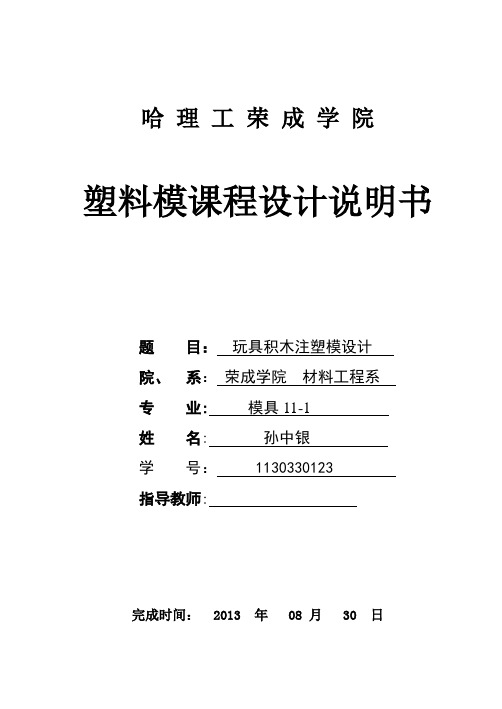
哈理工荣成学院塑料模课程设计说明书题目:玩具积木注塑模设计院、系:荣成学院材料工程系专业:模具11-1姓名: 孙中银学号: 1130330123指导教师:完成时间: 2013 年 08 月 30 日哈理工荣成学院塑料模课程设计任务书目录第1章塑件工艺分析 (3)1。
1 设计任务 (3)1.2 塑件工艺分析 (4)1。
2.1 材料工艺性分析 (4)1.2。
2 尺寸精度工艺性分析 (5)第2章模具结构设计 (6)2。
1模具总体方案确定 (6)2.1 成型设备的选择 (11)第3章模具材料及其热处理方案设计 (11)3.1 模具型芯型腔材料 (12)3.2 模具材料热处理方案 (12)第4章模具及注塑机的校核 (14)4。
1注塑机工艺参数的校核 (14)第5章模具总装图图5-1 (15)结论 (16)参考文献 (17)第1章塑件工艺分析1.1设计任务根据任务设计玩具积木三视图如下图1-11—1玩具积木三视图1-2玩具积木实物图已知技术参数:材料:ABS生产批量:大批量生产1.2塑件工艺分析1.2.1材料工艺性分析ABS是丙烯腈、丁二烯和苯乙烯三种单体聚合而成的非结晶型的高聚物.它是在聚丙乙烯基础上改性而发展起来的一种热塑性工程塑料。
由于聚苯乙烯的突出缺点是耐冲击性能较差,耐热性不够高,因而限制了它的应用范围。
而三种单体合成的ABS塑料是一种综合性能优良的在工程技术中广泛应用的新型塑料。
1.ABS塑料的使用性能:由于ABS是三种单体聚合而成的,因此它具有三种组成物的综合性能。
丙烯腈可使ABS具有较高的强度、硬度、耐热性及耐化学稳定性;丁二烯可使ABS具有弹性和较高的冲击强度;苯乙烯可使ABS具有优良的介电性能和成型加工性能。
由此可见,还可以通过改变组成物的比例,生产出不同品种的ABS塑料。
ABS塑料在一定的温度范围内具有较高的冲击强度和表面硬度及耐磨性;它的热变形温度为100℃左右,比聚苯乙烯、聚氯乙烯、聚酰胺都高;还具有一定的化学稳定性和良好的介电性能;此外它还有能与其他塑料和橡胶混溶等特性;其制品尺寸稳定性不好,表面光泽,可以抛光和电镀。
塑料模具设计说明书【范本模板】

湖南工学院课程设计设计课题注塑模具设计设计学院机械工程学院设计班级成型1001班设计者姓名原育民设计时间2013 年 12月目录1. 塑件的工艺分析 (4)1。
1塑件的成型工艺性分析 (4)1。
1.1 塑件材料ABS的使用性能 (5)1.1。
2 塑件材料ABS的加工特性 (5)1.2 塑件的成型工艺参数确定 (6)2 模具的基本结构及模架选择 (6)2。
1 模具的基本结构 (6)2.1.1 确定成型方法 (6)2。
1。
2 型腔布置 (7)2.1.3 确定分型面 (7)2.1。
4 选择浇注系统 (8)2。
1。
5 确定推出方式 (8)2。
1.6 侧向抽芯机构 (9)2.1。
7选择成型设备 (9)2.2 选择模架 (11)2.2.1 模架的结构 (11)2。
2。
2 模架安装尺寸校核 (11)3 模具结构、尺寸的设计计算 (12)3.1 模具结构设计计算 (12)3。
1.1 型腔结构 (12)3.1.2 型芯结构 (12)3。
1.3 斜导柱、滑块结构 (12)3.1。
4 模具的导向结构 (12)3。
2 模具成型尺寸设计计算 (13)3。
2.1 型腔径向尺寸 (13)3。
2。
2 型腔深度尺寸 (13)3.2。
3 型芯径向尺寸 (14)3.2.4 型芯高度尺寸 (14)3。
3 模具加热、冷却系统的计算 (15)3。
3。
1 模具加热 (15)3.3.2 模具冷却 (15)4. 模具主要零件图及加工工艺规程 (16)4。
1 模具定模板零件图及加工工艺规程 (16)4.2 模具侧滑块零件图及加工工艺规程....... 错误!未定义书签。
4.3 模具动模板(型芯固定板)零件图及加工工艺规程 (17)5 模具总装图及模具的装配、试模.......................... 错误!未定义书签。
5。
1 模具的安装试模。
.。
.。
.。
..。
...。
..。
.。
...。
.。
.。
.。
.。
.。
.。
..。
..。
.。
.。
185.2。
塑料底座模具毕业设计说明书

第1章绪论1.1塑料成型在工业生产中的重要性1.1.1塑料及塑料工业的发展塑料是以树脂为主要成分的高分子有机化合物,简称高聚物。
塑料其余成分包括增塑剂、稳定剂、增强剂、固化剂、填料及其它配合剂。
塑料制件在工业中应用日趋普遍,这是由于它的一系列特殊的优点决定的。
塑料密度小、质量轻。
塑料比强度高;绝缘性能好,介电损耗低,是电子工业不可缺少的原材料;塑料的化学稳定性高,对酸、碱和许多化学药品都有很好的耐腐蚀能力;塑料还有很好的减摩、耐磨及减震、隔音性能也较好。
因此,塑料跻身于金属、纤维材料和硅酸盐三大传统材料之列,在国民经济中,塑料制件已成为各行各业不可缺少的重要材料之一。
塑料工业的发展阶段大致分为一下及个阶段:1.初创阶段 30年代以前,科学家研制分醛、硝酸纤维和聚酰胺等热塑料,他们的工业化特征是采用间歇法、小批量生产。
2.发展阶段 30年代,低密度聚乙烯、聚氯乙烯等塑料的工业化生产,奠定了塑料工业的基础,为其进一步发展开辟了道路。
3.飞跃阶段 50年代中期到60年代末,塑料的产量和数量不断增加,成型技术更趋于完善。
4.稳定增长阶段 70年代以来,通过共聚、交联、共混、复合、增强、填充和发泡等方法来改进塑料性能,提高产品质量,扩大应用领域,生产技术更趋合理。
塑料工业向着自动化、连续化、产品系列化,以及不拓宽功能性和塑料的新领域发展。
我国塑料工业发展较晚。
50年代末,由于万吨级聚氯乙稀装置的投产和70年代中期引进石油化工装置的建成投产,使塑料工业有了两次的跃进,于此同时,塑料成型加工机械和工艺方法也得到了迅速的发展,各种加工工艺都已经齐全。
塑料由于其不断的被开发和应用,加之成型工艺的不断发展成熟于完善,极大地促进了成型模具的开发于制造。
随着工工业塑料制件和日用塑料制件的品种和需求的日益增加,而且产品的更新换代周期也越来越短,对塑料和产量和质量提出了越来越高的要求。
1.1.2塑料成型在工业生产中的重要作用模具是工业生产中重要的工艺装备,模具工业是国民经济各部门发展的重要基础之一。
- 1、下载文档前请自行甄别文档内容的完整性,平台不提供额外的编辑、内容补充、找答案等附加服务。
- 2、"仅部分预览"的文档,不可在线预览部分如存在完整性等问题,可反馈申请退款(可完整预览的文档不适用该条件!)。
- 3、如文档侵犯您的权益,请联系客服反馈,我们会尽快为您处理(人工客服工作时间:9:00-18:30)。
塑料模具毕业设计说明书范本(doc 42页)目录1 绪论1.1 我国模具技术的现状及今后发展趋势20世纪80年代开始,发达工业国家的模具工业已从机床工业中分离出来,并发展成为独立的工业部门,其产值已超过机床工业的产值。
改革开放以来,我国的模具工业发展也十分迅速。
近年来,每年都以15%的增长速度快速发展。
许多模具企业十分重视技术发展。
加大了用于技术进步的投入力度,将技术进步作为企业发展的重要动力。
此外,许多科研机构和大专院校也开展了模具技术的研究与开发。
模具行业的快速发展是使我国成为世界超级制造大国的重要原因。
今后,我国要发展成为世界制造强国,仍将依赖于模具工业的快速发展,成为模具制造强国。
中国塑料模工业从起步到现在,历经了半个多世纪,有了很大发展,模具水平有了较大提高。
在大型模具方面已能生产48"(约122cm)大屏幕彩电塑壳注射模具,精密塑料模方面,以能生产照相机塑料件模具,多形腔小模数齿轮模具及塑封模具。
经过多年的努力,在模具CAD/CAE/CAM技术,模具的电加工和数控加工技术,快速成型与快速制模技术,新型模具材料等方面取得了显著进步;在提高模具质量和缩短模具设计制造周期等方面作出了贡献。
尽管我国模具工业有了长足的进步,部分模具已达到国际先进水平,但无论是数量还是质量仍满足不了国内市场的需要,每年仍需进口10多亿美元的各类大型,精密,复杂模具。
与发达国家的模具工业相比,在模具技术上仍有不小的差距。
今后,我国模具行业应在以下几方面进行不断的技术创新,以缩小与国际先进水平的距离:(1)注重开发大型、精密、复杂模具;随着我国轿车、家电等工业的快速发展,成型零件的大型化和精密化要求越来越高,模具也将日趋大型化和精密化。
(2)加强模具标准件的应用;使用模具标准件不但能缩短模具制造周期,降低模具制造成本而且能提高模具的制造质量。
因此,模具标准件的应用必将日渐广泛。
(3)推广CAD/CAM/CAE技术;模具CAD/CAM/CAE技术是模具技术发展的一个重要里程碑。
实践证明,模具CAD/CAM/CAE技术是模具设计制造的发展方向,可显著地提高模具设计制造水平。
(4)重视快速模具制造技术,缩短模具制造周期;随着先进制造技术的不断出现,模具的制造水平也在不断地提高,基于快速成形的快速制模技术,高速铣削加工技术,以及自动研磨抛光技术将在模具制造中获得更为广泛的应用。
1.2 注射成型原理注射模又称注塑模,注射成型是根据金属压铸成型原理发展起来的,首先将颗粒或粉状的塑料原料加入到注射机的料筒中,经过加热熔融成粘流态,然后在柱塞或螺秆的推动下,以一定的流速通过料筒前端的喷嘴或模具的浇注系统注射入闭合的模具行腔中,经过一定时间后,塑料在模内硬化定型,接着打开模具,从模内脱出成型的塑件。
注射模主要用于热塑性塑料的成型。
注射成型原理:首先注射机的合模机构带动模具的活动部分从左向右移动,最终与模具的固定部分闭合,然后注射机的柱塞(螺杆)将由料斗中落入料筒里的粒料或粉料向前推进,与此同时,料筒中已经熔融成黏流态的塑料,在柱塞(螺杆)的高度和高压的推动下,通过料筒前端的喷嘴和模具浇注系统以较高的速度注入已经闭合的模具型腔中,充满型腔的通体在受压情况下,经冷却固化而保持型腔所赋予的形状。
最后,柱塞(螺杆)复位,料斗中的料又落入料筒,注射机的合模机构带动模具的动模部分向左运动而打开模具,模具的推出机构将塑件推出模具,至此完成一个成型周期,如此周而复始的进行注射成型。
2 塑件的工艺性分析塑件的工艺性分析包括:塑件的原材料分析、塑件的尺寸精度分析、塑件表面质量和塑件的工艺性分析。
2.1 塑件材料选择通常,选择塑件的材料依据是它所处在的工作环境及使用性能的要求,以及原材料厂家提供的材料性能数据。
对于常温工作状态下的结构件来说,要考虑的主要是材料的力学性能,如屈服应力、弹性模量、弯曲强度、表面硬度等;其次才是成型难易和经济性问题,以下是对几种常用塑料材料的性能对比,如表2-1所示:材料最终选定为ABS.2.2 ABS概述ABS( Acrylonitrile - Butadiene - Styrene)俗称超不碎胶,是一种高强度改性PS,由丙烯腈、丁二烯和苯乙烯三种组元以一定的比例共聚而成,化学结构式为:[ ( CH2 CH )x ( C2H3 C2H3 )y ( CH2 CH )z ]nCN图2-1三元结构的ABS兼具各组分的多种固有特性:丙烯腈能使制品有较高的强度和表面硬度,提高耐化学腐蚀性和耐热性;丁二烯使聚合物有一定的柔顺性,使制件在低温下具有一定的韧性和弹性、较高的冲击强度而不易脆折;苯乙烯使分子链保持刚性,使材质坚硬、带光泽,保留了良好的电性能和热流动性,易于加工成型和染色。
ABS本色为浅象牙色,不透明,无毒无味,属于无定形塑料。
粘度适中,它的熔体流动性和温度、压力都有关系,其中压力的影响要大一些。
属于减敏性塑料。
2.2.1 ABS塑料的主要优点综合性能比较好:机械强度高;抗冲击能力强,低温时也不会迅速下降;缺口敏感性较好;抗蠕变性好,温度升高时也不会迅速下降;有一定的表面硬度,抗抓伤;耐磨性好,摩擦系数低;电气性能好,受温度、湿度、频率变化影响小;耐低温达-40℃;耐酸、碱、盐、油、水;可以用涂漆、印刷、电镀等方法对制品进行表面装饰;较小的收缩率,较宽的成型工艺范围。
2.2.2 ABS塑料的主要缺点不耐有机溶剂,会被溶胀,也会被极性溶剂所溶解;耐候性较差,特别是耐紫外线性能不好;耐热性不够好。
普通ABS的热变形温度仅为95℃~98℃。
综上所述,ABS是一类较理想的工程塑料,为各行业所广为采用。
航空、造船、机械、电气、纺织、汽车、建筑等制造业都将ABS作为首选非金属材料。
其综合性能优异,具有较高的力学性能,流动性好,易于成型;成型收缩率小,理论计算收缩率为0.5%;溢料值为0.04 mm;比热容较低,在模具中凝固较快,模塑周期短,制件尺寸稳定,表面光亮。
2.3 塑件形状分析塑件的造型如图1-1图2-2(1)从图纸上分析,该塑件的外形对称,壁厚均匀,且符合最小壁厚要求。
(2)该塑件需用三个侧抽型和两个斜顶杆,以便于塑件的取出。
(3)该塑件的未注公差按MT5级公差要求。
结论:该塑件可采用注射成型加工,且加工性能较好,但成型以后需要设置侧抽芯机构才能将塑件顺利脱出.3.注塑工艺性的分析3.1 计算塑件的体积估算塑件体积和质量:cm,收缩率为,计算其平该产品材料为ABS,查书本得知其密度为1.13-1.14g/3均密度为1.135 g/3cm,平均收缩率为0.6﹪。
使用UGNX软件画出三维实体图,软件能自动计算出所画图形浇道凝料和塑件的体积。
另预置浇道凝料为330cm,因此估算塑件体积为3138cm。
170cm。
由于该塑件选择一模一腔的方式,因此估算出需要塑料的体积为33.2 注塑机的初步选择注塑机的主要参数有公称注射量,注射压力、注射速度、塑化能力、锁模力、合模装置的基本尺寸,开合模速度,空循环时间等。
这些参数是设计,制造,购买和使用注塑机的主要依据。
(1)公称注塑量:指在对空注射的情况下,注射螺杆或柱塞做一次最大注射行程时,注射装置所能达到的最大注射量,反映了注塑机的加工能力。
(2)注射压力:为了克服熔料流经喷嘴,浇道和型腔时的流动阻力,螺杆(或柱塞)对熔料必须施加足够的压力,我们将这种压力称为注射压力。
(3)注射速率:为了使熔料及时充满型腔,除了必须有足够的注射压力外,熔料还必须有一定的流动速率,描述这一参数的为注射速率或注射时间或注射速度。
塑件成型所需的注射总量应小于所选注塑机的注射容量.注射容量以容积(3cm )表示时,塑件体积(包括浇注系统)应小于注塑机的注塑容量,其关系是:(3-1)(3-2)式中V 件- 塑件与浇注系统的体积(3cm )V 注- 注射机注射容量(3cm )0.8- 最大注射容量利用系数根据塑件的原材料分析,查相关手册得知该塑件的原材料所需的注射压力为60-100Mpa ,由于塑件的尺寸较大,型芯较多,所以选择较大的注射压力=90Mpa P 成.模具所需的注射压力应小于或等于注射机的额定注射压力,其关系按下式:P P ≤注成 (3-3)90pa P M ≥注式中P 成- 塑件成型是所需的压力(Mpa )P 注- 所选注射机的额定注射压力(Mpa )模具所需的最大锁模力应小于或等于注射机的额定锁模力,其关系式如下:P F P ≤腔锁(3-4)9025560=2300400N=2300.4kN P ≥⨯式中P 腔- 模具型腔压力,取90MPaF - 塑件与浇注系统在分型面上的投影面积(3mm )P 锁- 注射机额定锁模力( N )再根据塑件形状及尺寸采用一模一腔的模具结构,由以上数据,相关资料初选螺杆式注塑机:XS-ZY-500 .它的注射容量为5003cm ,注塑压力为145Mpa ,锁模力为3500kN ,均满足以上条件.3.3 塑件塑料的注射工艺参数0.8V V ≤注件0.8V V ≥件注3170=212.5cm0.8≥表3-1ABS 注射成型工艺参数见下表,试模时,可根据实际情况作适当调整3.4 填写塑件工艺卡对塑件使用moldflow2010进行模流分析,参数如下: 1、 材料使用ABS 工程塑料 2、 使用XS-ZY-500注塑机分析后得到注塑填充的时间如图3-1所示:图3-1该塑件所需的填充时间为2.186s 塑件的冷却时间如图3-2:预热和干燥 温度t/℃: 80-95成型时间/s注射时间 0-5 时间τ/h: 4-5保压时间 15-30料筒温度t/℃ 后段 150-170 冷却时间 15-30 中段 165-180总周期40-70 前段180-200 螺杆转速n /(1minr -⋅)30-60 喷嘴温度t/℃ 170-180后处理方法 红外线灯 烘箱 模具温度t/℃ 50-80 温度t/℃ 70 注射压力p/Mpa60-100时间τ/h2-4多旋钮控制器面板工艺卡片零件名称多旋钮控制器面板材料牌号ABS 设备型号XS-ZY-500 装配图号材料定额每模件数1件图3-2塑件所需的冷却时间为121.8s填写成型工艺卡片4 模具设计注射模结构设计主要包括: 分型面的选择、模具型腔数目的确定及型腔的排列、浇注系统设计、型芯、型腔结构的确定、推件方式、侧抽芯机构的设计、模具结构零件设零件图号 09403070119-17单件质量 241.2g工装号材料干燥 设备 温度/℃80-85 时间/h2-3 料筒温度 后段/℃150-170 中段/℃165-180 前段/℃180-200 喷嘴/℃170-180 模具温度/℃ 50-80 时间 注射/s2.186 冷却与保压/s 121.8 压力注射压力/ Mpa49.97 后处理温度/℃ 烘箱 70 时间定额 辅助/min0.5 时间/h2-4单件/min2.4计等内容。