基于PLC的压力过程控制系统设计
基于PLC的压力控制回路设计【毕业作品】
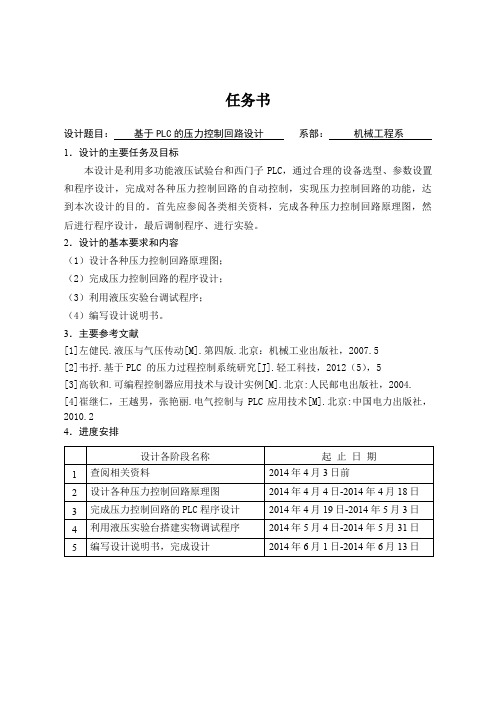
任务书设计题目:基于PLC的压力控制回路设计系部:机械工程系1.设计的主要任务及目标本设计是利用多功能液压试验台和西门子PLC,通过合理的设备选型、参数设置和程序设计,完成对各种压力控制回路的自动控制,实现压力控制回路的功能,达到本次设计的目的。
首先应参阅各类相关资料,完成各种压力控制回路原理图,然后进行程序设计,最后调制程序、进行实验。
2.设计的基本要求和内容(1)设计各种压力控制回路原理图;(2)完成压力控制回路的程序设计;(3)利用液压实验台调试程序;(4)编写设计说明书。
3.主要参考文献[1]左健民.液压与气压传动[M].第四版.北京:机械工业出版社,2007.5[2]韦抒.基于PLC 的压力过程控制系统研究[J].轻工科技,2012(5),5[3]高钦和.可编程控制器应用技术与设计实例[M].北京:人民邮电出版社,2004.[4]崔继仁,王越男,张艳丽.电气控制与PLC应用技术[M].北京:中国电力出版社,2010.24.进度安排基于PLC的压力控制回路设计摘要:PLC控制的液压系统克服了继电器控制系统手工接线、可靠性差、控制不方便、响应速度慢等不足,将PLC应用到液压系统,能较好地满足控制系统的要求,并且测试精确,运行高速、可靠,提高了生产效率,延长了设备使用寿命。
本设计是通过查阅相关资料,设计出调压回路、卸荷回路和保压回路三种压力控制回路,然后用西门子PLC编程实现控制,利用多功能液压试验台和西门子S7-200系列PLC 进行实验验证,达到本次设计的目的。
关键词:PLC,压力控制回路,实验台The design of the pressure control loop based on PLCAbstract:PLC controlled hydraulic system overcomes manual relay control system wiring, poor reliability and lack of control is inconvenient, slow response, and applying PLC to hydraulic systems, can better meet the requirements of control system, and the test accurately, running fast, reliable, improved production efficiency, extend equipment life. This design is by reviewing the relevant literature, design a voltage regulator circuits, unloading pressure control circuits and circuits of keeping pressure in three loops, and then controlled by Siemens PLC programming, by means of multifunctional hydraulic test machine and PLC Siemens series of experiments, achieve the purpose of this design.Keywords: PLC, pressure control circuits, test-bed目录1.绪论 (1)1.1PLC控制在国内外的发展近况 (1)1.2液压技术的发展现状及趋势 (2)1.3课题的研究意义 (4)2.压力控制回路的设计 (6)2.1压力控制阀 (6)2.1.1溢流阀 (6)2.1.2减压阀 (8)2.1.3顺序阀 (9)2.1.4压力继电器 (10)2.2调压回路 (11)2.2.1定义、功用及分类 (11)2.2.2调压回路的设计 (11)2.3卸荷回路 (12)2.3.1定义、功用及分类 (12)2.3.2卸荷回路的设计 (12)2.4保压回路 (13)2.4.1定义、功用及分类 (13)2.4.2保压回路的设计 (13)3.PLC控制程序 (14)3.1编程装置、软件、指令介绍 (14)3.1.1 S7-200PLC介绍 (14)3.1.2编程软件介绍 (14)3.1.3设计相关指令介绍 (15)3.2调压回路的PLC控制 (19)3.2.1 I/O地址分配表 (19)3.2.2 PLC控制程序 (19)3.3卸荷回路的PLC控制 (20)3.3.1 I/O地址分配表 (20)3.3.2 PLC控制程序 (20)3.4保压回路的PLC控制 (21)3.4.1 I/O地址分配表 (21)3.4.2 PLC控制程序 (22)4.实验 (23)4.1实验所需相关设备介绍 (23)4.1.1实验台介绍 (23)4.1.2实验装置组成 (23)4.1.3实验台各模块介绍 (24)4.2实验实物连接图 (31)4.2.1调压回路 (31)4.2.2卸荷回路 (32)4.2.3保压回路 (33)4.3实验结果 (34)4.3.1调压回路 (34)4.3.2卸荷回路 (34)4.3.3保压回路 (34)结论 (35)参考文献 (36)致谢 (37)1.绪论1.1PLC控制在国内外的发展近况世界上公认的第一台PLC是1969年美国数字设备公司(DEC)研制的。
基于PLC的压力过程

MCGS软件编程 软件编程
“基于PLC的压力过程控制系统”界面分成三个部分,分别是“压力过程控制系统” (图3.1)、“实时曲线”(图3.2)和“PID”(图3.3)。
图3.1 压力过程控制系统 图3.2 实时曲线
图3.3 PID控制
硬件部分实现
PLC特点 特点
1 可靠性高,抗干扰能力强 2 配套齐全,功能完善,适用性强 3 易学易用,深受工程技术人员欢迎 4 系统的设计、建造工作量小,维护方便,容易改造 5.体积小,重量轻,能耗低 FX2N特殊功能模块的应用 FX2N特殊功能模块的应用 为了扩大PLC的应用范围,FX2N系列PLC开发出各种特殊功能I/O模块,以满足各种 工业控制的不同需求。特殊功能I/O模块的类型有:模拟量输入、输出处理模块、高 速处理模块、定位控制模块、PID模块、数字控制模块、联网通信模块、多参数输入 模块、温度传感器输入模块、语言输出模块等等。
基于PLC的压力过程控制系统方案 的压力过程控制系统方案 基于
控制方式的选择
在控制系统中,串级控制系统对改善控制过程的品质极为有效,它改善了 单回路系统时间常数大、容易受到干扰等缺点,因此在生产过程中得到了 广泛的应用。鉴于其能够提高系统的放大系数、抗干扰能力以及有一定的 自适应能力等优点。“基于PLC的压力过程控制系统”采用串级控制系统。 1.串级系统的组成
控制器1 控制器 2 V P1 P2
压力变送器1
压力变送器2
软件部分的实现
组态软件的应用
利用MCGS组态软件设计。在设备组态窗口中选择适当的串口通讯设备.添加 三菱FX2N,正确设置其属性。 正确设置组态软件中数据变量设备通道的连接, 即可实现PLC与组态软件的通讯。将PLC中的串口驱动程序与组态软件的需求响 应相结合,使电脑对PLC发出 的信号有响应。在MCGS组态软件的用户窗口中, 制作一个动画界面。在界面上设置各个控件的属性,使设置的控件按照真实的情 况动作,检验和测试电梯PLC 控制系统对电梯的运行状态的控制效果。MCGS用 主控窗口、设备窗口和用户窗口来构成一个应用系统的人机交互图形界面.组态 配置各种不同类型和功能的对象 或结构。可以对实时数据进行可视化处理。
压力设备中安全PLC系统的设计及应用

添加主 副调节器 , 对其属 靠运 行。 为 降低 电网干扰 , 主 电机 采用星~ 三角启动 , 同时接入 备组态 窗 口选 择适 当串口通讯设备, 然后设置 组态软件中数据变量设备通 道的连 P L C 的电源 应增 加滤波 功能 。 大功率感 性负载 的通 断会 引起火 性进行正确设置 ,
入 接 口或 输 出接 口。 做好 外围元件 比如变频 器按钮 、 接触器 等 失效 , 系统也不会失效 , 其二是失效总是在可预测范围内, 一旦 的选 型 , 以有效提升 安全P L C 控 制系统 的可靠性 。 另外, 做 好电 实现 , 系统将会 自动进入安全模 式, 系统抗干扰能力强 , 可靠性 气 柜 的布线 , 电气元 件的走线和 布局应 遵循 相互干扰最 小、 强 高 , 适用于工业现 场, 对于提高压 力设备运行 的安全性、 稳定性 弱电线分别走线 的原则, 弱电输 出线、 信号输入线应分开, 若无 和可靠 性具有重要 作用 。 相信随着科 学技术 的不断进 步, 安全 法 分 开, 则应采 用屏蔽线使 信号输入 线可 靠接地 ,电气 柜 内存 P L C 系统 的软硬件性 能稳定性将会越 来越 好, 压力 设备 的运 行 在很多不同功 能的线, 应用颜色将这些先区分 开来。 将会更加安全。
实 花, 干 扰P L C 正常运 行, 基于此 , 采 用消火花 电路。 直流 电路可 接 , 软件的需求 响应 结合起来 , 使计算 机能够快 速响应P L C 系统所 在负载 并联续流二 极管, 交流 电路可在负载并联 阻容或 压敏电
备压 力检测信 号、 关 键部件 和元器件 的检 测信号作为P L C 的输 不亮 , 说明拓 展模块 自身存在 问题, 当两者都亮 , 可能通信参 数 入信号, 这样 以来 , 压力设备的滑 块位置、 压力大小等 都会 在触 的设 置有 问 题; 若通讯连 接不可靠 , 其原 因可能是通信距 离过 摸 屏上清 晰显 示出来 , 根 据触摸屏记录确认 压力设备 是否处于 远 、 现场干扰过 大、 采样周期太短, 为此 , 尝试 缩短通讯距离, 正常运 行状态 , 判断压力设备是 否存在故 障,以及时 找出故 障 使用屏蔽线, 改变采样周期 。
基于PLC的压力过程控制系统

轻工科技
LIGH INDUSTRY SCIENCE AND TECHNOLOGY
计算机与信息技术
基于 P L C 的压力过程控制系统研究
韦抒
(广西电力职业技术学院, 广西 南宁 530007 ) 【摘
然后用 PLC 进行智能控制设计 。在众多生产领 要】 基于 PLC 的压力过程控制系统要求首先辨识压力的数学模型, 域中, 经常需要对压力罐等容器中的液位进行监控, 以往常采用传统的继电器接触控制, 使用硬连接电器多, 可靠性差, 自动化程度 不高。本文采用可编程控制器 (PLC ) 对压力进行监控, 其电路结构简单, 投资少, 监控系统不仅自动化程度高, 还具有在线修改功 能, 灵活性强, 可直接运用于锅炉压力控制中, 也可用于恒压供水系统中, 具有一定的理论意义和现实意义。 PLC; MCGS; PID 【关键词】 压力过程控制; 【中图分类号】TP391 【文献标识码】 A (2012) 05 - 72 - 02 【文章编号】 2095- 3518
1 基于 P L C 的压力过程控制系统方案
基于 PLC 的压力过程控制系统的被控对象是由两个压力 容器对象组成, 可以根据需要构成不同阶 (1 或 2 阶) 的被控对 象。 压缩空气经过两路进入压力容器中, 经过两个流量调节阀, 在单回路控制过程中, 可以把一路作为主回路, 另一路作为干 扰回路。被控对象调节采用线性的理想特征, 构成的控制系统 为线性控制系统。 1.1 设计方案 “基于 PLC 的压力过程控制系统”利用工业控制计算机 (IPC ) 作为上位机, 利用 MCGS 软件作为程序开发平台, 下位 机采用可编程序控制器 (三菱 FX2N- 16M PLC ) , 组成一个压 力过程控制监控系统, 如图 1 所示。
基于PLC的流量与压力控制系统的研究运用

基于PLC的流量与压力控制系统的研究运用摘要随着科技的不断发展,PLC控制系统已经成为工业控制领域中最为常见和重要的控制方式之一。
本文主要介绍了基于PLC的流量与压力控制系统的研究运用。
首先对PLC技术进行了简要介绍,随后对流量与压力控制系统的原理与结构进行了详细分析,最后通过实验验证了基于PLC的流量与压力控制系统的可行性和实用性。
关键词:PLC;流量控制;压力控制;控制系统一、引言PLC是可编程逻辑控制器的缩写,它是一种专门用于工业控制领域的电子设备。
在工业生产中,PLC可以完成逻辑控制和运行控制等任务,通过其高度的灵活性和可编程性,能够满足不同工业场景的需求。
流量与压力是工业生产中重要的物理参数,对于保证生产过程的稳定性和质量具有至关重要的作用。
基于PLC的流量与压力控制系统的研究和运用具有很大的现实意义。
二、PLC技术的特点PLC是一种硬件可编程控制器,它的工作原理是通过控制不同的逻辑元件,如继电器、计数器、定时器等,来实现对工业生产过程的控制。
PLC具有以下几个特点:1. 可编程性强:PLC可以通过编程灵活地修改和调整控制逻辑,适应不同的生产需求;2. 稳定可靠:PLC的硬件结构稳定,能够在恶劣的工作环境下正常运行;3. 易于维护:PLC的模块化设计和可编程特性,使得故障检测和维护更加方便。
基于以上特点,PLC在工业控制领域得到了广泛的应用,成为了工业自动化的重要组成部分。
三、流量与压力控制系统的原理与结构流量与压力是工业生产中常见的控制对象,控制系统的主要目标是实现对流体的流量和压力进行精确的控制。
流量与压力控制系统的结构包括传感器、执行元件、控制器和执行装置等组成。
1. 传感器:传感器用于对流体的流量和压力进行检测和监控,将采集到的信息反馈给控制器;2. 控制器:控制器接收传感器反馈的信息,并根据预设的控制逻辑计算出控制命令,向执行装置发出控制信号;3. 执行装置:执行装置根据控制命令对流量阀门和压力阀门进行控制,调整流体的流量和压力。
基于PLC的加热炉压力控制系统

基于PLC的加热炉压力控制系统设计摘要加热炉是冶金工业生产中主要的过程设备,其自动控制策略是过程控制领域内的一个重要的研究方向。
为了使自动控制系统能够确保钢坯的加热质量、保证加热炉安全、高效的运行,必须设计一个切实可行的炉膛压力、煤气总管压力以及空气总管压力的控制方案。
本文在查阅相关文献资料的基础上,以冶金企业的加热炉控制系统为研究对象,应用过程控制理论及PLC技术,根据加热炉正常运行的特点,设计了基于PLC的加热炉压力控制系统。
论文首先介绍了加热炉生产工艺及现状、根据工艺要求,着重介绍了加热炉的压力控制系统的设计。
然后,对控制系统中所使用的下位机PLC和编程软件STEP7的功能和特点做了详细描述,并对I/O资源进行了分配,在控制系统软件平台上编制了具体的控制程序。
最后,利用组态软件设计了上位机人机交互界面,对加热炉压力控制系统进行监控。
经过理论分析,本系统采用的控制策略可满足生产要求,并能保证加热炉合理经济燃烧以及安全稳定运行。
关键词:加热炉;PLC;压力控制;组态PLC based furnace pressure control system designAbstractThe furnace is a metallurgical industrial production process equipment, automatic control strategy is an important research direction in the field of process control. To make the automatic control system to ensure that the billet heating quality, to ensure the furnace safe, efficient operation, we must devise a feasible chamber pressure, gas mains pressure and air mains pressure control program.Access to relevant documents on the basis of the metallurgical enterprises of the furnace control system for the study, application of process control theory and PLC technology design characteristics of the normal operation of the furnace, the furnace pressure control system based on PLC. The paper first introduces the furnace production process and the status quo, and focuses on the design of the furnace pressure control system according to process requirements. Then, the control system by the use of lower machine PLC programming software STEP7 function and characteristics described in detail as well as I / O resources, carry out the allocation of the specific design of the control system software platform, which carried out the programming work. Finally, the furnace pressure control on the design of control systems using the PC configuration screen monitor. Through theoretical analysis, this system uses a control strategy to meet production requirements, and to ensure the furnace reasonable economic combustion as well as safe and stable operation.Keywords: furnace; PLC; pressure control; configuration目录摘要 (I)Abstract (II)第一章绪论 (1)1.1 加热炉概述 (1)1.2 加热炉自动控制现状及发展趋势 (1)第二章加热炉控制系统总体方案设计 (4)2.1 加热炉生产工艺流程 (4)2.2 加热炉控制系统总体方案 (4)2.2.1 炉温控制系统 (4)2.2.2 煤气和空气流量控制系统 (5)2.2.3 炉膛压力控制系统 (5)2.2.4 煤气总管、空气总管压力控制系统 (6)第三章加热炉压力控制系统的设计 (7)3.1 加热炉压力对生产的影响 (7)3.2 加热炉控制系统构成 (7)3.3 加热炉压力控制系统设计 (8)3.3.1 助燃空气压力控制系统 (8)3.3.2 煤气压力控制 (8)3.3.3 炉膛压力控制 (8)3.3.4 压力检测元件的选择 (8)3.3.5 执行器的选择 (9)3.3.6 控制器的选择 (11)3.4 PLC选型 (13)3.4.1 S7-200简介 (14)3.4.2 S7-200的模块选择 (14)3.4.3 模拟量扩展模块EM235简介 (14)3.4.4 PLC的I/O口分配 (15)第四章加热炉压力控制系统的软件设计 (16)4.1 软件介绍 (16)4.2 主程序设计 (18)4.3 子程序设计 (19)4.3.1 A/D采样滤波子程序设计 (19)4.3.2 PID算法子程序 (20)4.4 炉膛压力控制系统设计 (21)4.5 煤气压力控制系统设计 (22)4.6 空气压力控制系统设计 (23)4.7 监控画面设计 (24)第五章总结 (28)参考文献 (29)附录A 源程序 (30)附录B 组态图 (41)附录C 加热炉仪表图 (42)致谢 (45)第一章绪论1.1 加热炉概述加热炉是一种加热物料或工件的设备。
基于PLC的流量与压力控制系统的研究运用

基于PLC的流量与压力控制系统的研究运用随着工业技术的不断发展,PLC(可编程逻辑控制器)在自动化控制领域中发挥着越来越重要的作用。
在各种自动化控制系统中,PLC流量与压力控制系统是一种应用广泛、效果显著的智能自动化控制系统。
PLC流量与压力控制系统是一个具有自主控制、数据测量、数字处理、调节控制、信息传输、可编程控制等功能的智能控制系统。
该系统主要应用于工业自动化、生产线控制等领域,不仅提高了生产效率与质量,还降低了生产成本,使企业能够更加高效、精准地运行。
PLC流量与压力控制系统的运用,首先需要进行系统设计。
系统设计需要根据实际控制需要,确定控制对象、流程方式、测量方式、控制算法等方案。
然后依据设计方案进行PLC程序设计,确定输入输出点、程序控制、参数设置等。
程序设计好后,需要进行PLC现场安装,将PLC连接各类传感器、执行器、工业计算机等设备。
最后进行系统调试与检测,确保系统稳定运行。
基于PLC的流量与压力控制系统的应用具有很多优点。
首先,该系统具有较高的控制精度和可靠性,能够实现连续、准确、可控的流量与压力控制。
其次,PLC控制系统采用数字化控制方式,可以实现实时监控、自动控制、自适应控制等功能,大大降低了人工干预和控制误差。
最后,PLC控制系统具有灵活性、可扩展性和可编程性,能够根据实际需求进行灵活调整与扩展,满足不同控制要求。
在PLC流量与压力控制系统的实际应用中,需要注重以下几个方面。
首先,要保证系统运行稳定、可靠,防止系统崩溃或数据丢失等情况的发生。
其次,要注重数据安全保护,采取相应的措施防止数据泄露或被攻击。
最后,需要进行定期维护和更新,保证系统始终处于最佳工作状态。
基于PLC的压力控制系统设计概要

序号参数数值作用
1Pr.180上限频率
2Pr.220下限频率
3Pr.360基准频率
4Pr.730模拟频率输入电压信号
5Pr.792外部运行频率设定方式
6Pr.1844Au信号
2结束语
上述控制在实际使用过程中运行良好,能对两种溶液进行充分融合反应。本控制将PLC易于编程的特点与变频器频率调节灵活的特点很好的结合起来了。当然不同的PLC的编程和硬件配置方法会不同,尽管是相同的变频器配用不同,只要在编程环境下的硬件配置中添加该模块即可,比如选用三菱的其他模拟量转换成数字量的模块,编程就不能使用RD3A和WR3A指令。总之,充分利用PLC模拟量输出功能可以控制变频器从而控制设备的速度,满足生产的需要。
本例接线是接入模拟量输入通道1,当调整通道1的偏移和增益时,另一个通道(通道2的偏移和增益也会自动调整好。
运行并监控模拟量输入输出处理程序如图4
。
图4模拟量输入输出处理程序
1 2 3注意事项
a .电压信号的输入接线,不要将V I N1和I I N1短接;
b .如果存在干扰,可以在V I N 1和C OM 1之间接一个耐压25V,容量0.1 F ~0.47 F的电容器;
1 2 2模拟量模块输入的增益及偏置调节
增益决定了校正线的角度或者斜率,在FX 0N -3A模块中用250来标识,偏移是校正线的位置,由数字值0标识。FX 0N -3A模块在出厂时已经按照0V ~10
!
28!机床电器2010 6
PLC ∀变频器∀计算机!!!基于PLC的压力控制系统设计
V进行了调整。在FX 0N -3A模块的面板上分别有A /D OFFSE T、A /D GAI N、D /A OFFSET、D /A GA I N四个旋钮,用于进行偏移和增益的调整。
- 1、下载文档前请自行甄别文档内容的完整性,平台不提供额外的编辑、内容补充、找答案等附加服务。
- 2、"仅部分预览"的文档,不可在线预览部分如存在完整性等问题,可反馈申请退款(可完整预览的文档不适用该条件!)。
- 3、如文档侵犯您的权益,请联系客服反馈,我们会尽快为您处理(人工客服工作时间:9:00-18:30)。
论文基于PLC的压力过程控制系统设计班级:BM电气091学号:0951402144姓名:孟海东目录第一章绪论.................................................................................................................................... - 2 -1.1 PLC控制在国内外的发展近况....................................................................................... - 2 -1.2 基于PLC的压力过程控制系统的发展前景.................................................................. - 3 -1.3 MCGS6.2软件................................................................................................................... - 3 -1.4 设计目的和要求.............................................................................................................. - 3 - 第二章基于PLC的压力过程控制系统方案............................................................................... - 5 -2.1 设计方案.......................................................................................................................... - 5 -2.1.1 设计方案.............................................................................................................. - 5 -2.1.2 控制阀的选择...................................................................................................... - 6 -2.1.3 控制方式的选择.................................................................................................. - 7 -2.2 控制算法.......................................................................................................................... - 8 -2.2.1 控制算法的选择.................................................................................................. - 8 -2.2.2 PID控制的原理和特点....................................................................................... - 9 -2.2.3 PID控制器的参数整定..................................................................................... - 10 - 第三章软件部分的实现.............................................................................................................. - 12 -3.1 MCGS组态软件............................................................................................................... - 12 -3.1.1 组态软件的介绍................................................................................................ - 12 -3.1.2 国内组态软件的比较与选择............................................................................ - 12 -3.2 组态软件的应用............................................................................................................ - 14 -3.2.1 MCGS软件编程................................................................................................... - 14 -3.3.2 MCGS软件连接设置........................................................................................... - 16 -3.3 FX2N编程软件的应用................................................................................................... - 22 -3.3.1 PLC编程指令..................................................................................................... - 22 -3.3.2 控制程序的编写................................................................................................ - 23 - 第四章硬件部分实现.................................................................................................................. - 27 -4.1 PLC特点......................................................................................................................... - 27 -4.2 FX2N特殊功能模块的应用........................................................................................... - 28 -4.2.1 FX2N-4AD模拟量转换模块............................................................................... - 28 -4.2.2 FX2N-4DA 模拟特殊模块.................................................................................. - 33 -4.2.3 PLC与计算机连接通讯..................................................................................... - 36 - 第五章调试.................................................................................................................................. - 37 -5.1 调试步骤........................................................................................................................ - 37 -5.2 调试结果与常见故障分析............................................................................................. - 37 -5.2.1 调试.................................................................................................................... - 37 -5.2.2 常见故障分析.................................................................................................... - 37 - 第六章结论.................................................................................................................................. - 39 - 参考文献.......................................................................................................................................... - 40 - 谢辞.................................................................................................................................................. - 41 -第一章绪论自二十世纪六十年代美国推出可编程逻辑控制器(Programmable Logic Controller,PLC)取代传统继电器控制装置以来,PLC得到了快速发展,在世界各地得到了广泛应用。