降低员工异常出清比数QC圈活动案例PPT课件
合集下载
QC活动降低--

验证场所
NC和精车设备
判定
验证情况
气缸粗加 精加工
NC
内圆磨 床
8件
2件
8件夹具夹紧部位设有避空位
2件夹具夹紧部位设有避空位
非要因
改进小组专用章
验证结果 验证人 末端原因 验证方法
夹具设计本身无法粘附铁削,工件夹紧状况OK
林占男 朱东华 吴志全
验证时间
2006年7月9号
⑧ 设备主轴精度差(NC/精车)
油孔存有铁质异物
…… 内径精加工后有粗加工痕迹 平面精加工后有粗加工痕迹 ……
铁质异物脱落导致压缩机不运转
…… 压缩机运转过程中异常音,部品寿命缩短 组装密封性不好 ……
泵 体
压缩机
家用空调
从源头 开始关注我 们的客户品 质!
4
课题:降低气缸内径目残不良!
活动计划
为了更好的开展本次QC活动,我们制定了详细的活动计划,并严格按照计划执行
33.66 31.23 40.88 无
30.99 34.87 41.34 无
验证结果 验证人
因C点圆度较差,当夹具磨损夹到C点时,引起内径目残很少的可能!
陈周英 林占男 朱东华
验证时间
2006年7月10日
13
要因论证( 7、8 )
末端原因 验证方法
场所
⑦ 夹爪上有铁屑
现场确认验证
设备名 数量 确认状况
200 150 100 50 0
内径目残
品质月报】
单位%
0.65
0.75 0.55
目 标:0.05%
0.42
100% 80% 82 53 39 20
打痕
0.49
60% 40% 18
QC七大手法培训课件PPT课件

用于描述一个过程或系统的 运作流程。
数据收集与整理
确保数据的准确性和 完整性,避免遗漏和 错误。
使用合适的方法和工 具进行数据收集和整 理,提高效率和质量。
对数据进行分类和整 理,以便于分析和处 理。
分析问题原因
利用因果图、流程图等工具,深入分 析问题的原因。
考虑各种可能的原因,不遗漏任何潜 在的因素。
强调预防措施和持续改进,有助于企业不断优化生产流程和管理体系。
QC七大手法的优点与局限性
• 提供了可视化的图表和统计分析工具,有助于快速识别问 题和改进点。
QC七大手法的优点与局限性
01
局限性
02
03
04
过度依赖数据和统计分析,可 能导致忽略实际经验和直觉判
断。
某些方法可能不适合特定行业 或企业规模,需要灵活应用和
用于收集、整理和记录数 据,以便于观察和统计。
排列图
用于找出影响质量的主要 因素。
直方图
用于表示数据的分布情况, 以便发现数据的异常值。
选择合适的手法
01
02
03
04
散布图
用于分析两个变量之间的关 系。
因果图
用于分析问题的原因,找出 潜在的影响因素。
控制图
用于监控过程的稳定性,及 时发现异常。
流程图
详细描述
通过将两个变量之间的关系绘制在图 上,可以了解它们之间的相互影响。 这种方法有助于团队成员更好地理解 两个变量之间的关系,并找出它们之 间的规律和特点。
箱线图法
总结词
用于表示一组数据的最大值、最小值、中位数和平均数等统计指标,以便了解数据的集中趋势和离散 程度。
详细描述
通过将数据分成若干组,并计算每组的最大值、最小值、中位数和平均数等统计指标,可以绘制出箱 线图。这种方法有助于团队成员更好地了解数据的分布情况和离散程度。
数据收集与整理
确保数据的准确性和 完整性,避免遗漏和 错误。
使用合适的方法和工 具进行数据收集和整 理,提高效率和质量。
对数据进行分类和整 理,以便于分析和处 理。
分析问题原因
利用因果图、流程图等工具,深入分 析问题的原因。
考虑各种可能的原因,不遗漏任何潜 在的因素。
强调预防措施和持续改进,有助于企业不断优化生产流程和管理体系。
QC七大手法的优点与局限性
• 提供了可视化的图表和统计分析工具,有助于快速识别问 题和改进点。
QC七大手法的优点与局限性
01
局限性
02
03
04
过度依赖数据和统计分析,可 能导致忽略实际经验和直觉判
断。
某些方法可能不适合特定行业 或企业规模,需要灵活应用和
用于收集、整理和记录数 据,以便于观察和统计。
排列图
用于找出影响质量的主要 因素。
直方图
用于表示数据的分布情况, 以便发现数据的异常值。
选择合适的手法
01
02
03
04
散布图
用于分析两个变量之间的关 系。
因果图
用于分析问题的原因,找出 潜在的影响因素。
控制图
用于监控过程的稳定性,及 时发现异常。
流程图
详细描述
通过将两个变量之间的关系绘制在图 上,可以了解它们之间的相互影响。 这种方法有助于团队成员更好地理解 两个变量之间的关系,并找出它们之 间的规律和特点。
箱线图法
总结词
用于表示一组数据的最大值、最小值、中位数和平均数等统计指标,以便了解数据的集中趋势和离散 程度。
详细描述
通过将数据分成若干组,并计算每组的最大值、最小值、中位数和平均数等统计指标,可以绘制出箱 线图。这种方法有助于团队成员更好地了解数据的分布情况和离散程度。
QC七大手法详细讲解ppt课件
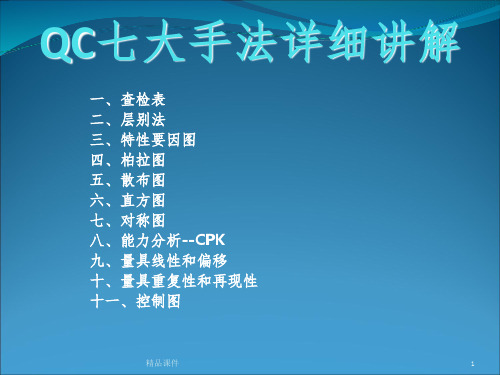
QC七大手法详细讲解
一、查检表 二、层别法 三、特性要因图 四、柏拉图 五、散布图 六、直方图 七、对称图 八、能力分析--CPK 九、量具线性和偏移 十、量具重复性和再现性 十一、控制图
精品课件
1
查检表
定义 :
为了便于收集数据,使用简单记录表填记并予统计整 理,以作进一步分析或作为核对、检查之用而设计的一 种表格或图表.
精品课件
21
实例数据:
Байду номын сангаас
10.05 9.98 10.05
10 9.99
10 10.01 9.96 10.01 9.96
10.05 9.98 10.05
10 9.99
10 10.01 9.96 10.01 9.96
10.05 9.98 10.05
10 9.99
10 10.01 9.96 10.01 9.96
则可采用与此特性有关系存在的另一个或两个测试成 本较低或测试容易之特性,以降低检验成本。 5、以利在以后的品质管制中,若同一制品之二特性间 有密切关系时,则可舍去其中一个管制图,以降低预 防成本。 6、两组数据间若呈直线变化,可依散布图求出直线方 程式,以为订定标准之用。
精品课件
16
散布图的判读:
A NO.1
B NO.2
A NO.1
B NO.2
日期 不良项目 尺寸 外观 材料 其它 尺寸 外观 材料 其它 尺寸 外观 材料 其它 尺寸 外观 材料 其它
精品课件
3
2.点检用查检表:
主要功用是为要确认作业实施、机械设备的实施 情形,或为预防发生不良或事故,确保安全时使用.这 种点检表可以防止遗漏或疏忽造成缺失的产生. 把非作不可、非检查不可的工作或项目,按点检顺 序列出,逐一点检并记录之.
一、查检表 二、层别法 三、特性要因图 四、柏拉图 五、散布图 六、直方图 七、对称图 八、能力分析--CPK 九、量具线性和偏移 十、量具重复性和再现性 十一、控制图
精品课件
1
查检表
定义 :
为了便于收集数据,使用简单记录表填记并予统计整 理,以作进一步分析或作为核对、检查之用而设计的一 种表格或图表.
精品课件
21
实例数据:
Байду номын сангаас
10.05 9.98 10.05
10 9.99
10 10.01 9.96 10.01 9.96
10.05 9.98 10.05
10 9.99
10 10.01 9.96 10.01 9.96
10.05 9.98 10.05
10 9.99
10 10.01 9.96 10.01 9.96
则可采用与此特性有关系存在的另一个或两个测试成 本较低或测试容易之特性,以降低检验成本。 5、以利在以后的品质管制中,若同一制品之二特性间 有密切关系时,则可舍去其中一个管制图,以降低预 防成本。 6、两组数据间若呈直线变化,可依散布图求出直线方 程式,以为订定标准之用。
精品课件
16
散布图的判读:
A NO.1
B NO.2
A NO.1
B NO.2
日期 不良项目 尺寸 外观 材料 其它 尺寸 外观 材料 其它 尺寸 外观 材料 其它 尺寸 外观 材料 其它
精品课件
3
2.点检用查检表:
主要功用是为要确认作业实施、机械设备的实施 情形,或为预防发生不良或事故,确保安全时使用.这 种点检表可以防止遗漏或疏忽造成缺失的产生. 把非作不可、非检查不可的工作或项目,按点检顺 序列出,逐一点检并记录之.
QC活动降低--课件

不良分布
平面端与内径是处 要 因 平面端与内径处
小结:当NC内径-端面跳动>0.05mm时, 内径目残不良比NC内径-端面跳动≤ 0.改05进m小m组, 专用章
产生的内径目残不良率要高61%
粗加工平面磨床加工完U\V面之后气缸工件的内径与端面直角度不能保证在合格的精度
陈
缺点
因NC第二工程以V面为基准
①开槽后 ②到V面磨削
①清洗后 ②到U面磨削
加工,磨床以U面先为基准 磨削产生内径与端面的直角 度有误差,导致内径目残不稳
定
(内径与端面直角度: 0.06)
合格定义:100%熟悉岗位改标进准小组专用章
规格书熟悉程度和执行性差
陈周英 朱东华 林占男
验证时间 2006年7月10日
10
要因论证(3)
末端原 因
验证方 法
③ V面铆钉孔/排气口有毛刺凸出
判
小批生产内径--端面直角度对比 验证场所
GMCC部品车间
定
验证情况
加工工艺 开槽后①
平面磨床 工序②
检查
作业描述
OP1
OP2
OP1
OP2
精车
精车 判定
规格
0.02mm 以下
0.02mm 0.02mm 0.02mm 0.01mm 0.01mm
以下
以下 以下
以下
以下
X向精度
0.01
0.01
0.01
0.01
0.01
0.01
OK
Z向精度 0.012
0.06
0.015 0.03
0.008 0.009 OK
经过确认主轴纵向和横向跳动在规格内,确认精度合格
13非要因改进小组专用章末端原因夹爪上有铁屑判定验证方法现场确认验证验证场所nc和精车设备验证情况验证结果夹具设计本身无法粘附铁削工件夹紧状况ok验证人林占男朱东华吴志全验证时间2006年7月9号场所设备名数量确认状况气缸粗加nc8件8件夹具夹紧部位设有避空位精加工内圆磨床2件2件夹具夹紧部位设有避空位8要因论证778非要因改进小组专用章末端原因设备主轴精度差nc精车判定验证方法用打表法对设备主轴跳动量检测验证场所gmcc部品车间验证情况验证结果经过确认主轴纵向和横向跳动在规格内确认精度合格验证人叶建辉孙洪标朱东华吴志全验证时间2006年7月8号工序op1op2op1op2精车精车判定确认人规格002mm以下002mm以下002mm以下002mm以下001mm以下001mm以下孙洪标朱东华叶建辉刘志伟x向精度001001001001001001okz向精度0012006001500300080009ok14非要因改进小组专用章要因确定磨床加工时工艺不合理磨床加工时工艺不合理经过小组严格论证后得出以下三个主要原因
QC改善案例精品PPT课件

计划 实际
D
对策实施
计划 实际
C
效果验证
计划 实际
A
巩固措施
计划 实际
总结打算
计划 实际
课题背景
主机现场 客户不满
ZL20DBA为我公司为徐工特机提供的油缸: 1、3月10日主机厂反馈此型号油缸有内泄装切现象,共4件; 2、7月30日主机厂反馈此型号油缸有内泄装切现象,共2件。
造成返工 返修
换缸
车间要求 进行改善
倒角及油口毛刺依靠目测和手测
确认标准: 确认质量意识
确认方法: 调查验证
确认人: 王海元
确认时间: 2012.8.23
确认情况:通过调查总装工序5名操作者的2011年度 的绩效考核发现,他们的考核排名比较靠前,只有一 人排名偏后。
姓名 年度考 月度考核 绩效考评 得分 考评等级
毕春虎 32.9 46.8 79.7 159.4 优秀
实完好件数 发出数
80
80
40
40
80
80
42
42
60
60
40
40
40
40
40
40
40
40
接收数 80 40 80 42 60 40 40 40 40
通过前期数据统计分析,6~8月份因装切更换OK圈数量为20个,在这 期间共生产四个批次180件产品,得出此ZL20DBA的装切不良率为11.1%。
课题确定
12-07-11 ZL20DBA 涂装油缸 Φ100×Φ55×785
12-08-16 ZL20DBA 涂装油缸 Φ100×Φ55×785
12-09-05 ZL20DBA 涂装油缸 Φ100×Φ55×785
qc七大手法培训资料ppt完整版

提高员工对QC七大手法的理解和应用能力 01
促进企业产品质量提升,降低生产成本 02
适应市场竞争,提升企业核心竞争力 03
qc七大手法简介
01 检查表
通过表格形式进行数据收集和整理,便于分析和 解决问题。
02 层别法
将数据按照不同层次进行分类,找出数据间的差 异和规律。
03 柏拉图
根据数据大小排序,以直观的图形展示主要问题。
03
04
05
直观展示两组数据之间 的相关关系;
可用于判断数据之间的 相关程度;
为进一步的数据分析和 问题解决提供线索。
散布图绘制步骤与技巧
步骤 1. 收集两组相关数据;
2. 选择合适的坐标轴比例;
散布图绘制步骤与技巧
01 3. 在坐标轴上标出数据点;
02 4. 观察点的分布情况和趋势。
散布图绘制步骤与技巧
练习
提供几个实际案例,让学员尝试使用因果图进行分析,并讨论分析结果和改进措施的有 效性。通过练习加深学员对因果图原理和应用的理解。
06
qc七大手法之五:散布图
散布图原理及意义
01
02
原理:通过收集两组数 意义 据(自变量和因变量), 在坐标轴上以点的形式 表示出来,通过观察点 的分布情况和趋势,分 析两组数据之间的关系。
VS
直方图意义
能够清晰地展示数据的分布规律,帮助分 析人员快速识别数据中的异常值、偏态分 布等问题,为后续的数据分析和质量控制 提供有力支持。
直方图绘制步骤与技巧
绘制步骤 收集数据并进行整理;
确定数据分组数和数据组距;
直方图绘制步骤与技巧
计算每个数据组的频数和频率; 绘制直方图,用矩形条的高度表示每个数据组的频率。
促进企业产品质量提升,降低生产成本 02
适应市场竞争,提升企业核心竞争力 03
qc七大手法简介
01 检查表
通过表格形式进行数据收集和整理,便于分析和 解决问题。
02 层别法
将数据按照不同层次进行分类,找出数据间的差 异和规律。
03 柏拉图
根据数据大小排序,以直观的图形展示主要问题。
03
04
05
直观展示两组数据之间 的相关关系;
可用于判断数据之间的 相关程度;
为进一步的数据分析和 问题解决提供线索。
散布图绘制步骤与技巧
步骤 1. 收集两组相关数据;
2. 选择合适的坐标轴比例;
散布图绘制步骤与技巧
01 3. 在坐标轴上标出数据点;
02 4. 观察点的分布情况和趋势。
散布图绘制步骤与技巧
练习
提供几个实际案例,让学员尝试使用因果图进行分析,并讨论分析结果和改进措施的有 效性。通过练习加深学员对因果图原理和应用的理解。
06
qc七大手法之五:散布图
散布图原理及意义
01
02
原理:通过收集两组数 意义 据(自变量和因变量), 在坐标轴上以点的形式 表示出来,通过观察点 的分布情况和趋势,分 析两组数据之间的关系。
VS
直方图意义
能够清晰地展示数据的分布规律,帮助分 析人员快速识别数据中的异常值、偏态分 布等问题,为后续的数据分析和质量控制 提供有力支持。
直方图绘制步骤与技巧
绘制步骤 收集数据并进行整理;
确定数据分组数和数据组距;
直方图绘制步骤与技巧
计算每个数据组的频数和频率; 绘制直方图,用矩形条的高度表示每个数据组的频率。
QC小组活动及QC七大手法PPT课件

应用注意事项:
1项目分类一定要按照同一维度.
2分类方法不同,得到的排列图不同.
3为了抓住关键的少数,在柏拉图上通常把累计比率分为三 类:0%~80%间的因素为A类因素,也即主要因素;在 80%~90%间的因素为B类因素,也即次要因素;在 90%~100%间的因素为C类因素,也即一般因素.
4如果其他项所占百分比很大,则分类不够理想.
应用实例:
装车质量点检单
NO 日期 车号 发往地 搬运情况打√
装车情况打√
码放情况打√
防护情况打√
□合格 / □不合格 □合格 / □不合格 □合格 / □不合格 □合格 / □不合格
1
处置:
损坏数量:
处置:
处置:
□合格 / □不合格 □合格 / □不合格 □合格 / □不合格 □合格 / □不合格
4根据不同目的,设计用于记录资料的调查表格式,其内 容应包括:调查者、调查的时间、地点和方式等栏目.
5对收集和记录的部分资料进行预先检查,目的是审查表 格设计的合理性.
6如有必要,应评审和修改该调查表格式.调查表的样式 多种多样,可根据需要调查的项目灵活设计.
应用注意事项:
必须按照一定的规则对调查项目进行分类,分类的规则即 考察事务的维度,如人的年龄、学历、收入状况等;不合格的 类别、位置、模式等,不可混淆. 合理选择维度,有利于层别
概念与用途:
因果图是一种用于分析质量特性结果与可能影响质量 特性的因素原因的一种工具.它可用于以下几个方面: 1分 析因果关系;
2表达因果关系; 3通过识别症状、分析原因、寻找措施,促进问题解 决. 许多可能的原因可归纳成原因类别与子原因,画成形 似鱼刺的图,所以该工具又称鱼刺图,
QCC案例分享 ppt课件

2020/11/29
17
➢ 延展项目
No.
文件编号
目标
实际完 达成 成状况 率
责任人
预计完 成日期
执行 范围
附件
持续更新看板文件,水平展开 1 至其他封装产品(MSD,SIM, 2件
BGA等)
2件 100% 仲燕
12-31
外检 QC
2020/11/29
18
➢ 活动感言
通过这次的活动,我们学习到了很多之前未曾接触 到的知识。理解了持续改善的概念,学习如何由基层 员工组成小组,通过适当的训练及引导,通过定期的 会议去发现、分析及解决问题,用品管的分析手法解 决工作中的困难。
客户反馈
5
AK内部异常
23
AK误放率
17.86%
8月 4 14
22.22%
2020/11/29
8
数据来源:CQE客诉清单及MES系统
➢ 数据收集及分析
团队组织 原因分析
主题选定 改善措施
数据收集及 分析
改善效果验证
目标设定 标准化
累计不良率
异常反馈件数
封装外检关卡误放率
客户反馈 总内部异常 总误放率
成率145%
11/10 LGA-00AK-014打标 字符偏移,Pin1 Mark点圆 圈切割后缺失
2020/11/29
依目前统计数据误放率符合前期目标设定
16
➢ 标准化
团队组织 原因分析
主题选定 改善措施
数据收集及分析 改善效果验证
目标设定
标准化
培训教材标准化:入品管内部培训资料库
文件编号:Q5-01(封装)-0004 文件编号:Q5-01(封装)-0005 完成人:仲燕 完成时间:10-30
- 1、下载文档前请自行甄别文档内容的完整性,平台不提供额外的编辑、内容补充、找答案等附加服务。
- 2、"仅部分预览"的文档,不可在线预览部分如存在完整性等问题,可反馈申请退款(可完整预览的文档不适用该条件!)。
- 3、如文档侵犯您的权益,请联系客服反馈,我们会尽快为您处理(人工客服工作时间:9:00-18:30)。
y3
刷卡錯誤筆數 流程衡量項目 離散資料 人資修正的異常筆數 資料收集期間 直方圖
y4
系統異常次數--刷 卡紀錄未能導入出 流程衡量項目 離散資料 勤
出勤系統中無當天的刷 卡紀錄
資料收集期間
直方圖
y5
部門未及時申請異 常筆數
流程衡量項目
離散資料
交給人資異常修正的筆數資料收集期間 直方圖
否
否
否
否
否
否
否
員工未按照規 定上下班準時刷卡
卡鍾刷卡不正常 卡鍾電源不通
原因分析 確
一次因
認 二次因
對策
效 掌 困成
優
益 握 難本 合 先
性 性 性性 計 順
高5低 高5低 高1低高1低
序
延遲下班延後刷卡 導致異常 連班加班不刷正常下班卡
忘記刷卡
全天在外辦公未刷卡
部門要求加班 留下來做5S 訂單多,不下班連續上班
降低員工異常出勤筆數
1/
專案立案
2/
專案立案
一、來自內外部顧客的聲音
3/
專案立案
二、 VOC To CTQ
通過魚骨圖將VOC轉化為可衡量的服務特性指標
4/
專案立案
三、 QFD 品質表: PIKPI
5/
專案立案
四、 CTQ Tree 分析表
6/
專案立案
五、 1-3月份資料分析表:
備註:通過以上資料分析,運用二八原則設定範圍職級為DL,產品廠選擇為NB廠
1
2
3
4
5
卡鐘設置收 取資料異常
次數
网絡連結 異常次數
刷卡錯誤 筆數
系統異常 次數--刷 卡紀錄未 能導入出
勤
部門未及 時申請異 常筆數
序號
優先度
10
15
61
5
9
100
1 卡鐘維護次數 2 檢核IP設置準確 3 卡鍾時間准確 4 卡鍾電源連通 5 卡鍾可正常刷卡 6 卡鍾系統運行正常 7 网絡檢核次數 8 网絡連通 9 培訓內容完整性 10 部門宣導執行 11 廠卡可正常感應 12 按照規定上下班準時刷卡 13 部門申請準確 14 部門檢核及時 15 出勤刷卡控制時間合理 16 系統運行正常
否
否
否
16/
17
2019/12/2
不良定義表
代 碼
名稱 / 用語
說明
1 卡鐘設置收取資料異常次數 卡鐘資料自動收取
2 网絡連通異常次數
卡鐘與電腦程式連通
3 刷卡錯誤次數
忘刷卡/未在規定時間內刷卡
4 系統異常--刷卡紀錄未能導入 卡鐘刷卡資料未能導入出勤系統 出勤
5 部門申請不及時
部門在員工助理出勤系統中申請
未能刷上卡或超過規定時間
卡鐘及人員安排布局不合理,太擁 擠排隊刷不上
v
卡鐘重新布置,人員予以分流
下班時間與加班時間不充足,超出 控制時間
v
修訂出勤加班控制時間提前15
4
4 4 3 15 3
5
4 5 5 19 1
v 1. 聯繫資訊進行維修
4
3 3 4 14 3
卡鐘數據收集滿 卡鐘未及時維護
网絡不通,無法自動收集 電源插座掉
13/
當地開模
專案流程圖 Y當Neo地s 開模
14/
KP OV 1.卡鐘設置 收取資料 異常次數
Process
Mapping
KP OV 1.网絡連結 異常次數
KP OV 1.刷卡錯誤筆數
KP OV 1.系統異常次數--刷卡 紀錄未能導入出勤 2.部門未及時申請異常
卡鐘設置
网絡測試 連通
員工上下班 刷卡
抽樣方式 圓形圖
使用的查檢表 …
Y
降低NB廠DL人員 異常出勤比數
產出衡量項目
離散資料
人資修正的異常刷卡、 異常加班、請假的比數
資料收集期間
直方圖
y1
卡鐘設置收取資料 異常次數
流程衡量項目
離散資料
人資修正的異常筆數 資料收集期間 直方圖
y2
网絡連結異常次數 流程衡量項目 離散資料 人資修正的異常筆數 資料收集期間 直方圖
部門在員工 助理出勤系
KPI
統中申請
降 低 NB廠 DL 人員異常出勤 比 數 到 6725
X1.卡 鐘 維 護 次 數 X2.檢 核 IP 設 置 準 確 X3.卡 鐘 時 間 準 確 x4卡鐘電源連通 X4.卡 鍾 可 正 常 刷 卡 N5.卡 鍾 系 統 運 行 正 常 X6.專 人 負 責
X1.网 絡 檢 核 次 數 X2.网 絡 連 通
檢驗判定標準
Bakeup庫中無資料或收資料系統顯示未接收 電腦測試IP不通為異常 系統出現異常需填寫表單人資進行修正
員工有刷`卡,出勤系統顯示刷卡異常
超過40H未申請的為異常
18/
改善目標確認表
Y
降低NB廠DL人員出勤 異常比數
專案改善目標確認表
目前水準 13450
目標水準 6725
19/
因果矩陣圖
因公在外工作無法刷卡
v 發聯絡單要求制造部,下班後先正常刷下 v 班卡
4
v
發聯絡單要求制造部,下班後先正常刷下 班卡,再刷加班卡加班
5
針對忘刷卡每月5次以上人員每月匯總提 醒並要求部門改善
3
v
發聯絡單規定:因公外出需在系統中請公 假,主管開具公假證明
5
3 3 5 15 3 3 2 5 15 3 4 3 4 14 4 5 4 4 18 2
15/
衡量作業計劃表
如何使用/展示 樣本是否符合 是否需衡量 是否需
項目
衡量的項目 衡量的類型 資料類型 資料的操作型定義 資料收集計劃 所收集的資料 常態分配 Cpk或ppm GRR
所要衡量 說明 的因素
產出衡量項目 離散資料 投入衡量項目 連續資料 流程衡量項目
資料收集期間 直方圖
抽樣數
柏拉圖
X1.培 訓 內 容 完 整 性 X2.部 門 宣 導 執 行 X3.廠 卡 可 正 常 感 應 X4 按照規定上下班 準時刷卡
X1.部 門 申 請 準 確 X2.部 門 檢 核 及 時 X3 出 勤 刷 卡 控 制 時 間合理 N3.系 統 運 行 正 常
X: Critical 可控制 N: Noise 不可控制 C:Controllable 常數 S:SOP
1
1
1
1
1
5
1
1
1
1
1
1
1
1
1
5
5
3
3
1
4
3
5
5
1
5
1
1
1
1
3
5
1
4
1
5
5
1
4
1
1
1
2
1
2
1
1
2
1
3
1
1
2
1
1
1
1
5
1
5
1
1
1
1
3
1
1
1
3
5
1
1
2
1
1
4
5
1
5
1
總和
100
140
100
332
424
140
195
215
170
179
161
380
118
146
161
210
20/
21/
系統圖(問題與對策)
問題
v 2. 手動先收取數據
7/
專案案
六、品質失敗成本分析:
根據目前異常出勤比數狀況, 分析內部失敗成本如下
8/
專案SIPOC
9/
QFDCCP
10/
CCP 一覽表
11/
專案目標
12/
專案預期效果
1.財務面: 每年可節省1581.48美元 2.流程面:異常比數降低50% 3.客戶面:滿意度從2.9,提升到3.5,提高0.6