EIA-364-28E 电子连接器振动测试方法-中英
EIA 364-27、28 机械冲击讲义
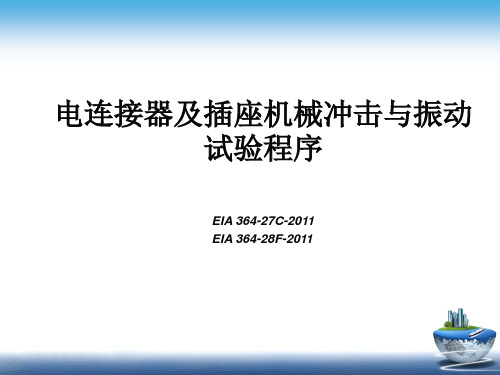
锯齿冲击脉冲终点峰值公差
速度的变化量:Vi= 0.5AD X10-3 (P 为加速度的峰值,D 为脉冲持续时间)的±10%以内。 最大峰值脉冲振幅±15%以内,峰值加速度±15%以内。
中文名称: 后峰锯齿冲击脉冲 英文名称: final peak sawtooth shock pulse 定义: 时间历程曲线为三角形的,即运动量 由零线性地增加到最大值然后在一瞬间降落 到零的理想冲击脉冲。
8、瞬断,及连接方法:
EIA-364-46:电子连接器的微秒间断试验程 序,连接器和插座。 1、监控设备电压电流 DC5V 100MA 电源调节响应时间应0.1微 秒或更好。 2、连接每个监控串联电路不超过50个连接 点,且初始电阻小于3 Ω.
❖EIA-364-87:电子连接器的纳秒事件检测, 连接器和插座。
1、测试的目的:
❖1、范围:描述一种电连接器机械冲击试验 的标准方法,以便评估电连接器及其组件 耐机械冲击的性能。
❖ 2、目的:进行本试验是为了确定连接器及 其组件当遭到诸如粗鲁搬运、运输或军用 时可能出现的冲击的适应性。
2、机械冲击的概念
定义:能激起系统瞬态扰动的力、位置、速 度和加速度的突然变化。
1.2 目的: 进行本试验是为了确定连接器及其组件在 寿命期间可能遭遇在主要频段或随机振动 频段范围内及其幅度上受振动的影响情况。
5、振动的概念
机械振动是物体在一定位置附近所作的周
期性往复的运动。
机械振动系统,就是指围绕其静平衡位置 作来回往复运动的机械系统,单摆就是一 种简单的机械振动系统。
振动测试的基本参数
测试方向: ±(X、Y、Z)
冲击波形: 半正弦 锯齿波
冲击次数: 每轴向的次数
机械 冲击
00-EIA-364系列标准

EIA-364系列标准EIA-CB18 固體的鉭式電容器儲存期限EIA-364-E 電子連接器/ 插座測試過程包括環境類別EIA-364-01B 加速度電子連接的測試過程EIA-364-02C 空氣滲漏電子連接的測試過程EIA-364-03B 高度浸入電子連接的測試過程EIA-364-05B 接觸插入,釋放,移動迫使電子連接的測試過程EIA-364-06C 接觸電阻電子連接的測試過程EIA-364-07C 與軸向的Concentricity電子連接的測試過程聯繫EIA-364-08B 捲曲抗拉的力量電子連接的測試過程EIA-364-09C 耐久性電子連接和接觸的測試過程EIA-364-10E 流動的浸入電子連接和插座的測試過程EIA-364-11B 電阻到溶劑電子連接和插座的測試過程EIA-364-13D Mating和Unmating 力量電子連接的測試過程EIA-364-14B 臭氧暴露電子連接的測試過程EIA-364-17B 有或沒有電負荷電子連接和插座的測試過程的溫度生命EIA-364-18B 接线盒和插座的外观与尺寸检查的测试流程EIA-364-20D 禁得住電壓電子連接,插座和同軸的接觸的測試過程EIA-364-21D 絕緣電阻電子連接,插座和同軸的接觸的測試過程EIA-364-22B 類比生命電子連接的測試過程EIA-364-23C 低的水準接觸電阻電子連接和插座的測試過程EIA-364-24B 維修使電子連接的測試過程變老EIA-364-25C 探查損壞電子連接的測試過程EIA-364-26B 鹽水霧電子連接器,接觸和插座的測試過程EIA-364-27B 機械震動(指定的脈搏)電子連接的測試過程EIA-364-28D 振動電子連接和插座的測試過程EIA-364-29C 接觸保留電子連接的測試過程EIA-364-31B 濕度電子連接和插座的測試過程EIA-364-32D 熱震(溫度週期變化)電子連接和插座的測試過程EIA-364-35B 插入保留電子連接的測試過程EIA-364-36B DETERMINATION OF GAS-TIGHT CHARACTERISTICS TEST PROCEDURE FOR ELECTRICAL CONNECTORS, AND OR CONTACT SYSTEMSEIA-364-37B 接觸約會和分離力量電子連接的測試過程EIA-364-38B 電報拔電子連接的測試過程EIA-364-39B 電子連接器,接觸和插座的液壓靜力測試過程EIA-364-40B 壓壞電子連接的測試過程EIA-364-41C 電報在電子連接的測試過程屈曲EIA-364-42B 影響電子連接的測試過程EIA-364-45A 防火牆火焰電子連接的測試過程EIA-364-46BEIA-364-48AEIA-364-50AEIA-364-53B 氮的Adic 蒸汽測試,金完成電子連接和插座的測試過程EIA-364-54A 有磁性的滲透性電子連接器,接觸和插座的測試過程EIA-364-56D 為了焊接熱電子連接和插座的測試過程的電阻EIA-364-66A EMI 保護效力電子連接的測試過程EIA-364-70BEIA-364-71B 焊接燈芯(波焊接技術)測試過程適合電子連接器和插座EIA-364-75EIA-364-81A 燃燒特性電子連接器住房,連接器會議和插座的測試過程EIA-364-82A 塑膠電子連接和插座住房的測試過程的Corrosivity EIA-364-83 殼牌公司轟炸和轟炸在艙壁測試過程抵抗適合電動汽車連接器EIA-364-89AEIA-364-90 串音比率電子連接,插座,電纜組件的測試過程或者相互連接系統EIA-364 91A 灰塵電子連接和插座的測試過程EIA-364-95 充分的鋪席子和鋪席子穩定電子連接的測試過程EIA-364-99 規格位置和保留電子連接的測試過程EIA-364-100 標明永久為電子連接和插座的測試過程EIA-364-101 Attentuation電子連接器,插座,電報會議或者相互聯繫系統的測試過程EIA 364-102 上升時間墮落電子連接器,插座,電報會議或者相互聯繫系統的測試過程EIA-364-103 傳播延遲電子連接器,插座,電報會議或者相互聯繫系統的測試過程EIA-364 104A 可燃性電子連接的測試過程EIA-364-105A 高度低溫電子連接的測試過程EIA-364-106 駐波比率(SWR)電子連接的測試過程EIA-364-107 眼睛圖案和在電子連接器,插座,電報會議或者相互聯繫系統的測試過程感到緊張EIA-364-108 阻抗,反射系數,返回損失,並且VSWR在時間和頻率領土電子連接器,電報會議或者相互聯繫系統的測試過程測量EIA-364 1000.01 評價電子連接器的性能的環境考試方法學和插座在生意辦公室應用方面使用EIA-364-109 環電感測量電子連接(1 nH 10 nH)的測試過程EIA-364-110。
EIA-364(连接器产品常用测试规范之目录)

EIA-364(连接器产品常用测试规范之目录)Item Standard NO.Rev.Description1EIA-CB18Solid Tantalum Capacitor Shelf-Life固体的钽式电容器储存期限2EIA-364E ELECTRICAL CONNECTOR/SOCKET TEST PROCEDURES INCLUDING ENVIRONMENTAL CLASSIFICATIONS 电子连接器/插座(包括环境类)的测试程序3EIA-364-01B Acceleration Test Procedure for Electrical Connectors电子连接器的加速测试程序4EIA-364-02C Air Leakage Test Procedure for Electrical Connectors空气渗漏电子连接器的测试程序5EIA-364-03B Altitude Immersion Test Procedure for Electrical Connectors高度浸入电子连接器的测试程序6EIA-364-05B Contact Insertion, Release and Removal Force Test Procedure for Electrical Connectors电子连接器的端子插入、释放及取出测试程序7EIA-364-06C Contact Resistance Test Procedure for Electrical Connectors电子连接器的接触电阻测试程序8EIA-364-07B Contact Axial Concentricity Test Procedure for Electrical Connectors电子连接器的端子同心度测试程序9EIA-364-08B Crimp Tensile Strength Test Procedure for Electrical Connectors电子连接器的卷曲抗拉强度测试程序10EIA-364-09C Durability Test Procedure for ElectricalConnectors and Contacts端子连接器与端子的耐久性测试程序11EIA-364-10D Fluid Immersion Test Procedure for Electrical Connectors电子连接器的液体浸没测试程序12EIA-364-11B Resistance to Solvents Test Procedure for Electrical Connectors and Sockets电子连接器和插座的电阻测试程序13EIA-364-13D Mating and Unmating Forces T est Procedure for Electrical Connectors电子连接器的插入力和拔出力测试程序14EIA-364-14B Ozone Exposure Test Procedure for Electrical Connectors电子连接器的臭氧暴露测试程序15EIA-364-17B Temperature Life with or without Electrical Load Test Procedure for Electrical Connectors andSockets. 电子连接器和插座的温度寿命测试或没有电负载测试程序16EIA-364-18B Visual and Dimensional Inspection Test Procedure for Electrical Connectors and Sockets电子连接器和插座的外观与尺寸检验程序17EIA-364-20C Withstanding Voltage Test Procedure for Electrical Connectors, Sockets and Coaxial Contacts电子连接品、插座和同轴端子的耐电压测试程序18EIA-364-21C Insulation Resistance Test Procedure for Electrical Connectors, Sockets, and Coaxial Contacts电子连接品、插座和同轴端子的绝缘电阻测试程序19EIA-364-22B Simulated Life Test Procedure for Electrical Connectors电子连接器的模拟寿命测试程序20EIA-364-23C Low Level Contact Resistance T est Procedure for Electrical Connectors and Sockets电子连接器与插座的接触电阻测试程序21EIA-364-24B Maintenance Aging Test Procedure for Electrical Connectors电子连接器的维持能力测试程序22EIA-364-25C Probe Damage Test Procedure for Electrical Connectors电子连接器的探伤测试程序23EIA-364-26B Salt Spray Test Procedure for Electrical Connectors, Contacts and Sockets电子连接器、端子和插座的盐雾测试程序24EIA-364-27B Mechanical Shock (Specified Pulse) Test Procedure for Electrical Connectors电子连接器的机械震动(指定的脉搏)测试程序25EIA-364-28E Vibration Test Procedure for Electrical Connectors and Sockets电子连接器与插座的振动测试程序26EIA-364-29C Contact Retention Test Procedure for Electrical Connectors电子连接器的端子保持力测试程序27EIA-364-30A Capacitance Test Procedure for Electrical Connectors and Sockets电子连接器与插座的电容测试程序28EIA-364-31B Humidity Test Procedure for Electrical Connectors and Sockets电子连接器与插座的湿度测试程序29EIA-364-32D Thermal Shock (Temperature Cycling) Test Procedure for Electrical Connectors and Sockets电子连接器与插座的热冲击(温度周期变化)测试程序30EIA-364-35B Insert Retention Test Procedure for Electrical Connectors电子连接器的保持力测试程序31EIA-364-36B Determination of Gas-tight Characteristics test procedure for Electrical connectors and or contact systems. 电子连接器和(或)端子系统的气密特性测试程序32EIA-364-37B Contact Engagement and Separation Force Test Procedure for Electrical Connectors电子连接器端子结合力和分离力测试程序33EIA-364-38B Cable Pull-Out Test Procedure for Electrical Connectors电子连接器的电材拉拔力测试程序34EIA-364-39B Hydrostatic Test Procedure for Electrical Connectors, Contacts and Sockets电子连接器、接触和插座的液压静力测试程序35EIA-364-40B Crush Test Procedure for Electrical Connectors电子连接器v压坏测试程序36EIA-364-41C Cable Flexing Test Procedure for Electrical Connectors电报在电子连接的测试程序屈曲37EIA-364-42B Impact Test Procedure for Electrical Connectors电子连接器的机械冲压测试程序38EIA-364-45A Firewall Flame Test Procedure for Electrical Connectors电子连接器的阻燃火焰测试程序39EIA-364-46B MICROSECOND DISCONTINUITY TEST PROCEDURE FOR ELECTRICAL CONNECTORS,CONTACTS AND SOCKETS电子连接器、端子和插座的瞬断(微秒不间断)测试程序40EIA-364-48A Metallic Coating Thickness Measurement of Contacts Test Procedure for Electrical Connectors电子连接器端子喷涂层厚底测试程序41EIA-364-50A Dust (Fine Sand)Test Procedure for Electrical Connectors电子连接器的粉尘(细沙)测试程序42EIA-364-53B Nitric Acid Vapor Test, Gold Finish Test Procedure for Electrical Connectors and Sockets电子连接器与插座的硝酸蒸汽测试、黄金制品测试程序43EIA-364-54A Magnetic Permeability Test Procedure for Electrical Connectors, Contacts, and Sockets电子连接器、端子和插座的导电率测试程序44EIA-364-56C Resistance to Soldering Heat Test Procedure for Electrical Connectors and Sockets电子连接器和插座的焊接热电阻测试程序45EIA-364-59A LOW TEMPERATURE TEST PROCEDURE FOR ELECTRICAL CONNECTORS AND SOCKETS电子连接器和插座的低温测试程序46EIA-364-66A EMI Shielding Effectiveness Test Procedure for Electrical Connectors电子连接器的电磁干扰屏蔽效应测试程序47EIA-364-70B TEMPERATURE RISE VERSUS CURRENT TEST PROCEDURE FOR ELECTRICAL CONNECTORS AND SOCKETS 电子连接器与插座的温升与电流测试程序48EIA-364-71B Solder Wicking (Wave Solder Technique) Test Procedure for Electrical Connectors and Sockets电子连接器与插座的溢锡(波峰焊接技术)测试程序49EIA-364-75LIGHTNING STRIKE TEST PROCEDURE FOR ELECTRICAL CONNECTORS电子连接器的雷击测试程序50EIA-364-81A Combustion Characteristics Test Procedure for Electrical Connector Housings, Connector Assemblies and Sockets. 电子连接器塑料、组装成品与插座的燃烧特性测试程序51EIA-364-82A Corrosivity of Plastics Test Procedure for Electrical Connector and Socket Housings电子连接器与插座塑胶的塑胶腐蚀性测试程序52EIA-364-83Shell-to-Shell and Shell-to-Bulkhead Resistance Test Procedure for Electrical Connectors电子连接器的接地壳与接地壳及接地壳与主板之电阻测试程序53EIA-364-89A Space Application Test Procedure for Electrical Connectors and Sockets电子连接器与插座的空间应用测试程序54EIA-364-90Crosstalk Ratio Test Procedures for Electrical Connectors, Sockets, Cable Assemblies orInterconnect Systems电子连接器、插座、线束或互联系统的串扰率测试程序55EIA-364-91A Dust Test Procedure for Electrical Connector and Sockets电子连接器与插座的粉尘测试程序56EIA-364-95Full Mating and Mating Stability Test Procedures for Electrical Connectors电子连接器的完整互配与互配稳定测试程序57EIA-364-99Gage Location and Retention Test Procedure for Electrical Connectors电子连接器的计量位置与保留测试程序58EIA-364-100Marking Permanence Test Procedure for Electrical Connectors and Sockets电子连接器与插座的永久性标识测试程序59EIA-364-101Attenuation Test Procedure for Electrical Connectors, Sockets, Cable Assemblies or Interconnection Systems 电子连接器、插座、线束或互联系统的衰减测试程序60EIA-364-102Rise Time Degradation Test Procedure for Electrical Connectors, Sockets,Cable Assemblies orInterconnection Systems。
EIA-364-D中文

重新認可時,可僅針對受改變影響之特定部份 測試。
要成功取得認可或再認可,每一測試件必須符 合測試組中所有的測試要求,任何的不符合 (Defects)皆不允許。特採允收僅能由驗證單位 來決定。
相似性應認可所有尺寸大到測試件水準的產品。 當與認可的端子在接合(Termination area)區域設計不同,
但在接觸區域具相同的尺寸外觀、基材、電鍍種類與 厚度時,只需針對接合技術相對應的適當測試來認證 (e.g. crimp, solder, IDC, etc.)。
Qualification(Cont.)
Unless otherwise specified, all measurements shall be made within the following ambient conditions:一般測試環 境要求
Temperature: 15 °to 35 °C, 溫度 Atmospheric pressure: 650 millimeters of mercury to 800
EIA-364-D
Greg Lin Aug. 11, 2004
EIA-364-D
EIA – Electronic Industries Association 美國電子工業 協會
對電子工業產品訂定各種標準, 作為製造商及採購者 對產品交換性及引進提供一有效的橋樑
EIA-364系列是針對電子連接器及插座(Connectors/ Sockets) 的測試程序, 其下包括許多TP (Test Procedure)
EIA-364-28F_(2011-01-14)_Vibration

EIASTANDARDTP-28FVIBRATION TEST PROCEDURE FOR ELECTRICAL CONNECTORS AND SOCKETSEIA-364-28FJANUARY 2011EIA StandardsElectronic Components AssociationANSI/EIA-364-28F-2011Approved: January 14, 2011E I A -364-28FNOTICEThis standard is based upon the major technical content of International Electrotechnical Commission standard 60512-2-1 2005-Febuary (was IEC 512-2, test 2a), contact resistance - millivolt level method. It conforms in all essential respects this IEC standard.EIA Engineering Standards and Publications are designed to serve the public interest through eliminating misunderstandings between manufacturers and purchasers, facilitating interchangeability and improvement of products, and assisting the purchaser in selecting and obtaining with minimum delay the proper product for his particular need. Existence of such Standards and Publications shall not in any respect preclude any member or nonmember of ECA from manufacturing or selling products not conforming to such Standards and Publications, nor shall the existence of such Standards and Publications preclude their voluntary use by those other than ECA members, whether the standard is to be used either domestically or internationally.Standards and Publications are adopted by ECA in accordance with the American National Standards Institute (ANSI) patent policy. By such action, ECA does not assume any liability to any patent owner, nor does it assume any obligation whatever to parties adopting the Standard or Publication.This major portion of this Standard is based upon the technical content of International Electrotechnical Commission standard IEC 60512-6-4, (was IEC 512-4, test 6d) Dynamic Stress, Vibration (Sinusoidal), 2002 and also IEC 60512-6-5, Dynamic Stress, Random Vibration, 1997. It differs from IEC Publication 60068-2-6 (was IEC 68-2-6, test Fc), Vibration (Sinusoidal), 2007; by specifying a single test with closely controlled conditions and methods for random vibration. These differences have been called to the attention of the U.S. Committee of Experts for IEC (or ISO) Technical Committee TC48 and resolution of these differences will be sought in future meetings of SC48. Test condition VII is based on International Electrotechnical Commission standard IEC 60068-2-34, (was IEC 68-2-34, Test Fd), Random Vibration Wide Band, 1993.This Standard does not purport to address all safety problems associated with its use or all applicable regulatory requirements. It is the responsibility of the user of this Standard to establish appropriate safety and health practices and to determine the applicability of regulatory limitations before its use.(From Standards Proposal No. SP-5212 formulated under the cognizance of the CE-2.0 National Connector Standards Committee).Published by©ELECTRONIC COMPONENTS ASSOCIATION 2011Engineering Department2500 Wilson Boulevard, Suite 310Arlington, VA 22201PRICE: Please call: IHSUSA and Canada (1-800-854-7179)All rights reservedPrinted in U.S.A.PLEASE!DON'T VIOLATETHELAW!This document is copyrighted by the ECA and may not be reproduced without permission.Organizations may obtain permission to reproduce a limited number of copies through entering into a license agreement. For information, contact:IHS15 Inverness Way EastEnglewood, CO 80112-5704 or callUSA and Canada (1-800-854-7179), International (303-397-7956)CONTENTSClause Page 1 Introduction (1)1.1 Scope (1)1.2 Object (1)1.3 Applicable documents (1)1.4 Definitions (1)2 Test resources (2)2.1 Equipment (2)3 Test specimen (3)4 Test procedure (4)4.1 Test conditions I, II, III and IV (4)4.2 Test conditions V, VI and VII (10)5 Details to be specified (16)6 Test documentation (17)Table1 Vibration conditions (4)2 Values for test condition V (13)3 Values for test condition VI (14)4 Values for test condition VII (15)Figure1 Mounting axis definitions (2)2 Vibration test curves - high frequency (displacement in mm) (6)3 Vibration test curves - high frequency (displacement in inches) (7)4 Test condition V, random vibration test curve envelope (13)5 Test condition VI, random vibration test curve envelope (14)6 Test condition VII, random vibration test curve envelope (15)(This page left blank)TEST PROCEDURE No. 28FVIBRATION TEST PROCEDUREFORELECTRICAL CONNECTORS AND SOCKETS(From EIA Standards Proposal No. 5212, formulated under the cognizance EIA CE-2.0 Committee on National Connector Standards, and previously published in EIA-364-28E.)1 Introduction1.1 ScopeThe standard test procedure details a method to assess the ability of electrical connector components to withstand specified severities of vibration.1.2 ObjectThe object of this test is to determine the effects of vibration within the predominant or random vibration frequency ranges and magnitudes that may be encountered during the life of the connector.1.3 Applicable documentsThe following documents form a part of this standard to the extent indicated herein. In the event of conflict between the requirements of this standard and the referenced documents, this standard takes precedence.1.3.1 EIA standardsEIA-364-46: Microsecond Discontinuity Test Procedure for Electrical Connectors, Contacts and SocketsEIA-364-87: Nanosecond Event Detection for Electrical Connectors, Contacts and Sockets1.4 Definitions1.4.1 AxisThe following mounting axis definitions shall be employed during the performance of this test. Figure 1 indicates a pictorial view of the axis definitions. The referencing document shall indicate the fixturing required or the axis definitions if different than as stated in figure 1. Axis definitions for symmetrical, square and “free” connectors shall be defined in the Detail Specification.1.4.1.1 X-axisAlong the longitudinal length of the test sample1.4.1.2 Y-axisThe axis perpendicular to the longitudinal length of the sample (transverse direction).1.4.1.3 Z-axisThe axis perpendicular to the fixture seating plane attached to the test table.Figure 1 - Mounting axis definitions1.4.2 The term gnThis term is the SI unit for the standard acceleration due to the earth’s gravity, which itself varies with altitude and geographic latitude. NOTE — In this standard the value of g n is 9.81 m/s 2.2. Test resources2.1 Equipment2.1.1 The monitoring transducer shall be calibrated against a standard transducer having an accuracy of ±2%. The vibration system consisting of the vibration machine, together with its auxiliary test equipment, shall be capable of generating either a sinusoidal or random excitation.2.1.2 Test equipment for random vibration shall produce random excitation that possesses a gaussian (normal) amplitude distribution, except that the acceleration magnitudes of the peak values may be limited to a minimum of three times the rms [three-sigma (3σ) limits].3 Test specimen3.1 A vibration test sample shall be a fully wired connector consisting of one of the following, as applicable;3.1.1 A connector plug and its mating connector receptacle.3.1.2 A printed circuit connector receptacle and its mating connector board(s).3.1.3 An integral, functional connector assembly.3.2 Each test sample shall be prepared with wire and other materials or processes, simulating application assembly of the sample. If normal connector mating is dependent upon forces external to the connector, then such forces and mounting arrangement shall be as closely duplicated as possible (example: printed circuit connectors). If mating is achieved with normal locking means, then only normal locking means shall be used.3.3 Method of mounting3.3.1 Test conditions I, II, III and IV (sinusoidal evaluation conditions)The specimen shall be attached to a fixture capable of transmitting the vibration conditions specified. The test fixture shall be designed so that resonant vibration inherent in the fixture within the frequency range specified for the test shall be minor. The magnitude of the applied vibration shall be monitored on the test fixture near the specimen mounting points. The test specimen shall be mounted rigidly to the test fixture as specified and shall simulate as closely as possible the normal mounting of the specimen. A minimum of 200 mm (approx 8 in) of wire or cable shall be unsupported on both ends of the connector. For specimens with attached brackets, one of the vibration-test directions shall be parallel to the mounting surface of the bracket. Vibration input shall be monitored on the mounting fixture in the proximity of the support points of the specimen.3.3.2 Test conditions V, VI and VII (random excitation conditions)The specimen shall be mounted as specified. The orientation of the specimen or direction of application of the applied vibration motion shall be specified in one or more directions. If the order of application of the different directions is critical, it also shall be specified. Any special test fixtures or jigs required to run the test shall be specified in sufficient detail to assure reproducibility of the input motion applied to the specimen. These details shall include the dimensions, the materials, temper, etc., as applicable.4 Test procedureTests and measurements before, during and after vibration shall be as specified in the referencing document.4.1 Test conditions I, II, III and IV4.1.1 Electrical load and discontinuity4.1.1.1 Unless otherwise specified in the referencing document, an electrical load of 100 milliamperes maximum with a detector capable of detecting a discontinuity of 1.0 microsecond or longer. Said monitoring shall be performed in accordance with EIA-.364-46.4.1.1.2 Unless otherwise specified in the referencing document, low nanosecond event detection shall be performed in accordance with EIA-364-87. A 100 milliamperes test current shall be applied to the areas being monitored. A detector capable of measuring an event resulting in a 10 ohm change lasting longer than 10 nanoseconds, unless otherwise specified in the referencing document.4.1.1.2.1 Low nanosecond event detection shall not be used as a substitute for the standard 1.0 microsecond requirement. This monitoring test was developed to detect different failure mechanisms than that described in 4.1.1.1. It is designed to detect large resistance fluctuations or voltage variations that may result in improper triggering of high speed digital circuits.4.1.2 Vibration conditionsVibration conditions shall be in accordance with table 1, as applicable.Table 1 - Vibration conditionsTest conditions Frequency range, Hz Peak levelg n m/s2I Low - 10 to 55II High - 10 to 500 10 98.1III High - 10 to 2,000 15 147.1IV High - 10 to 2,000 20 196.14.1.3 ResonanceA critical resonant frequency is that frequency at which any point on the specimen is observed to have a maximum amplitude more than twice that of the support points. When specified, resonant frequencies shall be determined either by monitoring parameters such as contact opening, or by use of resonance-detecting instrumentation.4.1.4 Test condition IThe specimens shall be subjected to a simple harmonic motion having an amplitude 1.52 mm (0.06 in) double amplitude (maximum total excursion), the frequency being varied uniformly between the approximate limits of 10 Hz and 55 Hz. The entire frequency range, from 10 Hz to 55 Hz and return to 10 Hz, shall be traversed in approximately 1 minute. Unless otherwise specified, this motion shall be applied for 2 hours in each of three mutually perpendicular directions (total of 6 hours). If applicable, this test shall be made under electrical load conditions.4.1.5 Test condition II [98.1 m/s2 (10 g n) peak]The specimens, while deenergized or operating under the load conditions specified, shall be subjected to the vibration amplitude, frequency range, and duration specified 4.1.5.1, 4.1.5.2 and 4.1.5.3, respectively; see figures 2 and 3.4.1.5.1 AmplitudeThe specimens shall be subjected to a simple harmonic motion having an amplitude of either 1.52 mm (0.06 in) double amplitude (maximum total excursion) or 98.1 m/s2(10 g n) peak, whichever is less. The tolerance on vibration amplitude shall be ±10%.4.1.5.2 FrequencyThe vibration frequency shall be varied logarithmically between the approximate limits of 10 Hz and 500 Hz (see 4.1.8) except that the procedure (see 4.1.4) of this standard may be applied during the 10 Hz to 55 Hz band of the vibration frequency range.4.1.5.3 Sweep time and durationThe entire frequency range of 10 Hz to 500 Hz and return to 10 Hz shall be traversed in 15 minutes. This cycle shall be performed 12 times in each of three mutually perpendicular directions (total of 36 times), so that the motion shall be applied for a total period of approximately 9 hours. Interruptions are permitted provided the requirements for rate of change and test duration are met. Completion of cycling within any separate band is permissible before going to the next band. When the procedure (see 4.1.4) is used for the 10 Hz to 55 Hz band, the duration of this portion shall be same as the duration for this band using logarithmic cycling (approximately 1-1/3 hours in each of three mutually perpendicular directions).4.1.6 Test condition III 147.1 m/s2 (15 g n) peak]The specimens, while deenergized or operating under the load conditions specified, shall be subjected to the vibration amplitude, frequency range, and duration specified in 4.1.6.1, 4.1.6.2 and 4.1.6.3, respectively; see figures 2 and 3.NOTE: g = 0.00201f 2 DA (f = frequency in hertz, DA = double amplitude in mm)Figure 2 - Vibration test curves - high frequency (displacement in mm)NOTE: g = 0.0512f 2 DA (f = frequency in hertz, DA = double amplitude in inches) Figure 3 - Vibration test curves - high frequency (displacement in inches)4.1.6.1 AmplitudeThe specimens shall be subjected to a simple harmonic motion having an amplitude of either 1.52 mm (0.06 in) double amplitude (maximum total excursion) or 147.1 m/s2(15 g n) peak, whichever is less. The tolerance on vibration amplitude shall be ±10%.4.1.6.2 Frequency rangeThe vibration frequency shall be varied logarithmically between the approximate limits of 10 Hz to 2,000 Hz (see 4.1.8) except that the procedure (see 4.1.4) of this standard may be applied during the 10 Hz to 55 Hz band of the vibration frequency range.4.1.6.3 Sweep time and durationThe entire frequency range of 10 Hz to 2,000 Hz and return to 10 Hz shall be traversed in 20 minutes. This cycle shall be performed 12 times in each of three mutually perpendicular directions (total of 36 times), so that the motion shall be applied for a total period of approximately 12 hours. Interruptions are permitted provided the requirements for rate of change and test duration are met. Completion of cycling within any separate band is permissible before going to the next band. When the procedure (see 4.1.4) of this standard is used for the 10 Hz to 55 Hz band, the duration of this portion shall be the same as the duration for this band using logarithmic cycling (approximately 1-1/3 hours in each of three mutually perpendicular directions).4.1.7 Test condition IV [196.1 m/s2 (20 g n) peak]The specimens, while deenergized or operating under the load conditions specified, shall be subjected to the vibration amplitude, frequency range, and duration specified in 4.1.7.1, 4.1.7.2 and 4.1.7.3, respectively; see figures 2 and 3.4.1.7.1 AmplitudeThe specimens shall be subjected to a simple harmonic motion having an amplitude of either 1.52 mm (0.06 in) double amplitude (maximum total excursion) or 196.1 m/s2(20 g n) peak, whichever is less. The tolerance on vibration amplitude shall be ±10%.4.1.7.2 Frequency rangeThe vibration frequency shall be varied logarithmically between the approximate limits of 10 Hz to 2,000 Hz (see 4.1.8).4.1.7.3 Sweep time and durationThe entire frequency range of 10 Hz to 2,000 Hz and return to 10 Hz shall be traversed in 20 minutes. This cycle shall be performed 12 times in each of three mutually perpendicular directions (total of 36 times), so that the motion shall be applied for a total period of approximately 12 hours. Interruptions are permitted provided the requirements for rate of change and test duration are met.Completion of cycling within any separate band is permissible before going to the next band. When the procedure (see 4.1.4.) of this standard is used for the 10 Hz to 55 Hz band, the duration of this portion shall be the same as the duration for this band using logarithmic cycling (approximately 1-1/3 hours in each of three mutually perpendicular directions).4.1.8 Alternative procedure for use of linear in place of logarithmic change of frequency Linear rate of change of frequency is permissible under the following conditions:4.1.8.1 The frequency range above 55 Hz shall be subdivided into no fewer than three bands. The ratio of the maximum frequency to the minimum frequency in each band shall be not less than two (2).4.1.8.2 The rate of change of frequency in Hz per minute shall be constant within any one band.4.1.8.3 The ratios of the rate of change of frequency of each band to the maximum frequency of that band shall be approximately equal.4.1.8.3.1 Example of alternative procedureAs an example of the computation of rates of change, assume that the frequency spectrum has been divided into three bands, 55 Hz to 125 Hz, 125 Hz to 500 Hz and 500 Hz to 2,000 Hz, in accordance with 4.1.8.1. For each band, let the constant, κ, represent the frequency change (in Hz/minute), divided by the maximum frequency (in Hz). Then the rates of change for the three bands will be 125κ, 500κ and 2,000κ, respectively. The times (in minutes) to traverse the three frequency bands are1255512550012550020005002000−−−κκκ,,,andSince the minimum total sweep time is 30 minutes,701253755001500200030κκκ++=,,whence κ = 0.0687/minute.The required maximum constant rates of frequency change for the three bands are therefore 8.55 Hz per minute, 34.2 Hz per minute and 137 Hz per minute, respectively. The minimum times of traverse of the bands are 8.2 min, 10.9 min and 10.9 min, respectively.4.2 Test conditions V, VI and VII4.2.1 Control and analysis of random vibration4.2.1.1 Spectral density curvesThe output of the vibration machine shall be presented graphically as power-spectral density versus frequency; see 4.2.1.1.1. The spectral-density values shall be within +40% and -30% (±1.5 dB) of the specified values between a lower-specified frequency and 1,000 Hz, and within +100% and -50% (±3 dB) of the specified values between 1,000 and an upper-specified frequency (2,000 Hz). A filter bandwidth will be a maximum of 1/3-octave or a frequency of 25 Hz, whichever is greater.4.2.1.1.1 Power-spectral densityPower-spectral density is the mean-square value of an oscillation passed by a narrow-band filter per unit-filter bandwidth. For this application it is expressed as g 2 / f, where g 2 / f is the mean-square value of acceleration expressed in gravitational units per number of cycles of filter bandwidth. The spectral density curves are usually plotted either on a logarithmic scale, or in units of decibels (dB). The number of decibels is defined by the equation:The rms value of acceleration within a frequency band between f 1 and f 2 is:g = f df rms 2f f 12g ∫//12where g r 2 / f is a given reference value of power-spectral density, usually the maximum specified value.4.2.1.2 Distribution curvesA probability density-distribution curve may be obtained and compared with a gaussian-distribution curve. The experimentally-obtained curve shall not differ from the gaussian curve by more than ± 10% of the maximum value.4.2.1.3 MonitoringMonitoring involves measurements of the vibration excitation and of the test item performance. When required in the referencing document, the specimen may be monitored during the test. The details of the monitoring circuit, including the method and points of connection to the specimen, shall be specified.dB = 10 g /f g /f = 20 g /fg /f2r r log log 24.2.1.4 Vibration inputThe vibration magnitude shall be monitored on a vibration machine, on mounting fixtures, at locations that are as near as practicable to the test item mounting points. When the vibration input is measured at more than one point, the minimum input vibration shall normally be made to correspond to the specified test curve; see figures 4 and 5. For massive test items and fixtures, and for large force exciters or multiple vibration exciters, the input control value may be an average of the average magnitudes of three or more inputs. Accelerations in the transverse direction, measured at the test item attachment points, shall be limited to 100% of the applied vibration. The number and location of the test points shall be specified.4.2.2 ProcedureThe specimen, or substitute equivalent mass, shall be mounted in accordance with 3.3.2 and the monitoring equipment attached, if applicable, in accordance with 4.2.1.3. The vibration machine shall then be operated and equalized or compensated to deliver the required frequencies and intensities conforming to the curves specified in test condition V, figure 4, or test condition VI, figure 5, or test condition VII, figure 6 (see 2.1). The specimen shall then be subjected to the vibration specified by the test condition letter (see tables 2, 3 and 4) for the duration as specified:3 minutes; 15 minutes; 1-1/2 hours; or 8 hours;in each of three mutually perpendicular directions, and in the order specified (see 3.3.2), as applicable.The measurements made before, during, and after the test shall be specified and if the specimen is to be monitored during the test, the details shall be in accordance with 4.2.1.3.4.2.3 Electrical load and discontinuities4.2.3.1 Unless otherwise specified in the referencing document, an electrical load of 100 milliamperes maximum with a detector capable of detecting a discontinuity of 1.0 microsecond or longer. Said monitoring shall be performed in accordance with EIA-.364-46.4.2.3.2 Unless otherwise specified in the referencing document, low nanosecond event detection shall be performed in accordance with EIA-364-87. A 100 milliamperes test current shall be applied to the areas being monitored. A detector capable of measuring an event resulting in a 10 ohm change lasting longer than 10 nanoseconds, unless otherwise specified in the referencing document.4.2.3.2.1 Low nanosecond event detection shall not be used as a substitute for the standard 1.0 microsecond requirement. This monitoring test was developed to detect different failure mechanisms than that described in 4.2.3.1. It is designed to detect large resistance fluctuations or voltage variations that may result in improper triggering of high speed digital circuits.Figure 4 - Test condition V, random vibration test-curve envelope (see table 2).Table 2 - Values for test condition V 1)Test condition letter Power spectral density, g 2/Hz Overall rms gA 0.02 5.35B 0.04 7.56C 0.06 9.26D 0.1 11.95E 0.2 16.91F 0.3 20.71G 0.4 23.91H 0.6 29.28I Superseded by Test condition letterJ J 1.0 37.80K 1.5 46.301) For duration of test; see 4.2.2.Figure 5 - Test condition VI, random vibration test-curve envelope (see table 3).Table 3 - Values for test-condition VI 1)Test condition letter Power spectral density, g 2/Hz Overall rms gA 0.02 6.21B 0.04 8.78C 0.06 10.76D 0.1 13.89E 0.2 19.64F 0.3 24.06G 0.4 27.78H 0.6 34.02I Superseded by Test condition letterJ J 1.0 43.92K 1.5 53.791) For duration of test; see 4.2.2.Figure 6 - Test condition VII, random vibration test-curve envelope (see table 4)Table 4 - Values for test condition VII 1)Test condition letter Power spectraldensity, g 2/Hz Overall rms gA 0.002 0.98B 0.005 1.55C 0.01 2.19D 0.02 3.10E 0.05 4.90F 0.1 6.93G 0.29.801) For duration of test; see 4.2.2.5 Details to be specifiedThe following details shall be specified in the referencing document:5.1 Type of sample; see 3.15.2 Number of samples to be tested5.3 Method of mounting; see 3.35.4 Test condition number; see tables 1, 2, 3 or 45.5 Electrical load conditions, all contacts, if other than 100 milliamperes maximum; see 4.1.1 or 4.2.35.6 Discontinuity requirement if other than 1 microsecond5.7 Measurement of discontinuities during vibration; see 4.1.1 or 4.2.35.8 Method of determining resonance, if applicable; see 4.1.35.9 Direction of motion and order, if critical; see 3.35.10 Tests or measurements before, during and after vibration; see clause 45.11 Duration of vibration; see 4.1.4 or 4.2.25.12 Monitoring instrumentation, if applicable; see 4.2.1.35.13 Number and location of test points, if applicable; see 4.2.1.35.14 Mounting axes definitions if other than indicated in figure 1; see 1.46 Test documentationDocumentation shall contain the details specified in clause 5, with any exceptions, and the following:6.1 Title of test6.2 Sample description include fixture, if applicable6.3 Test equipment used, and date of last and next calibration6.4 Photographs, plots, values and observations necessary for proof of conformance6.5 Name of operator and start/finish date(s) of testRevision HistoryRevision letter ProjectnumberAdditions, changes and deletionsE SP-5125 Changed test condition letter I to J. Superseded testcondition letter I by J in table 2 and 3.F SP-5212 Add paragraph 1.3.Revise paragraph 4.1.1 and 4.2.3.EIA Document Improvement ProposalIf in the review or use of this document, a potential change is made evident for safety, health or technical reasons, please fill in the appropriate information below and mail or FAX to:Electronic Components AssociationEngineering Department2500 Wilson Blvd, Suite 310.Arlington, VA 22201FAX: (703-875-8908)Document No.: Document Title:Submitter’s Name: Telephone No.:FAX No.:e-mail:Address:Urgency of Change:Immediate: At next revision:Problem Area:a. Clause Number and /or Drawing:b. Recommended Changes:c. Reason/Rationale for Recommendation:Additional Remarks:Signature: Date:2FOR ECA USE ONLYResponsible Committee:Chairman:Date comments forwarded to Committee Chairman:Electronic Components Association2500 Wilson Boulevard, Suite 310 * Arlington, VA 22201 * tel 703-907-8021 * fax 703-875-8908。
EIA-364-D中文

Qualification Procedure-Sequence
• 此建議測試順序是最低限度要求,適 用所有的等級。 • 依照不同應用,特定測試項目可自 測試順序、補充測試、及/或接合測 試項中增加或刪除。
Qualification Procedure-Sample Size
測試件應含對應端。每一特性量測的數據數量應為 測試件25%的端子量,但不應低於25筆數據。若低於 25筆數據,則所有端子必頇量測; 若還不足25筆,就 必頇提供額外的測試件。
EIA-364-D目的/範圍
針對電子連接器及插座建議基本的 (recommended minimum) 測試次序(Sequence) 及方法(Procedures) 依照預定的應用環境分級, 以便對每一分級能 作合適的評估 定義各環境分級的儀器操作狀況, 包含溫度與 溼度的最大範圍, 以及海洋氣候與嚴苛環境之 可能性
Contact resistance at rated current shall be used in those applications where the current levels are in excess of 100 milliamperes and the voltage levels are in excess of 3.0 volts. 選定電流的電阻測試(CRRC)用於 I>100mA & V>3V.
Qualification Procedure-Sequence
Visual examination shall be performed on the test specimens initially and after each environmental and stress test. Unless otherwise specified, unmating of the test specimens shall not be permitted until completion of the test sequence. The referencing document shall specify if the test specimens are to be unmated after vibration, physical shock and salt spray for visual examination. If not specified, the test samples shall remain mated.測試前後的外觀檢驗之必要性與解除互配狀態之許可. Unless otherwise specified, IR and/or DWV shall be tested between the closest spaced contacts (adjacent and/or between rows). Six contact pairs or 25% of the positions whichever is greater shall be tested per specimen. In the event that hardware and/or metal shells are used, the test shall also be performed between the metal accessories and the contacts closest to them in accordance with EIA-364-20 and/or EIA-364-21. IR與DWV之 測試點數量要求6對或25%的端子, 及端子與鐵殼/其他鐵件之測試 必要.
EIA-364-28E 电子连接器振动测试方法-中英

T E N T53standspecifiedseveritiesofvibration.件承受特定强度振动的能力。
quencyrangesandmagnitudesthatmaybeencounteredduringthelifeoftheconnector.振动幅度的环境,以此验证对产品性能的影响情况.icatesapictorialviewoftheaxisdefinitions.Thereferencingdocumentshal lindicatethefixturingrequiredortheaxisdefinitionsifdiffe 的轴向与图1不同,则在相关参考文件中需对试验装置要求及轴向进行定义。
对于具有对称性,方形及不规则的连接eandgeographiclatitude.hevibrationsystemconsistingofthevibrationmachine,togetherwithitsauxiliarytestequipment,shallbecapableofgeneratingeitheras 试设备,整个系统应能产生正弦或随机振动。
amplitudedistribution,exceptthattheaccelerationmagnitudesofthepeakvaluesmaybelimitedtoaminimumofthreetimestherms[thre 可限emblyofthesample.Ifnormalconnectormatingisdependentuponforcesexternaltotheconnector,thensuchforcesandmountingarrang 接器的连接方式需要依靠外力,那么这些外力与连接方式应尽可能模拟实际的状况(例如:印刷电路连接器)。
若是hetestfixtureshallbedesignedsothatresonantvibrationinherentinthefixturewithinthefrequencyrangespecifiedforthetestshallbemi elyaspossiblethenormalmountingofthespecimen.Aminimumof200mm(approx8in)ofwireorcableshallbeunsupportedonbothend donthemountingfixtureintheproximityofthesupportpointsofthespecimen.有共振频率在试验所规定的频率范围内达到最小。
EIA-364连接器专项测试标准简介

Firewall Flame Test Procedure for Electrical Connectors
EIA-364-46B
MICROSECOND DISCONTINUITY TEST PROCEDURE FOR ELECTRICAL CONNECTORS,CONTACTS AND SOCKETS
Thermal Shock (Temperature Cycling) Test Procedure for Electrical Connectors and Sockets
EIA-364-35B
Insert Retention Test Procedure for Electrical Connectors
EIA-364-90
Crosstalk Ratio Test Procedures for Electrical Connectors, Sockets, Cable Assemblies or Interconnect Systems
EIA-364-91A
Dust Test Procedure for Electrical Connector and Sockets
EIA-364-56C
Resistance to Soldering Heat Test Procedure for Electrical Connectors and Sockets
EIA-364-59A
LOW TEMPERATURE TEST PROCEDURE FOR ELECTRICAL CONNECTORS AND SOCKETS
EIA-364-95
Full Mating and Mating Stability Test Procedures for Electrical Connectors
- 1、下载文档前请自行甄别文档内容的完整性,平台不提供额外的编辑、内容补充、找答案等附加服务。
- 2、"仅部分预览"的文档,不可在线预览部分如存在完整性等问题,可反馈申请退款(可完整预览的文档不适用该条件!)。
- 3、如文档侵犯您的权益,请联系客服反馈,我们会尽快为您处理(人工客服工作时间:9:00-18:30)。
1.3.
2.The term g n术语g n
This term is the SI unit for the standard acceleration due to the earth’s gravity, which itself varies with
4.1.3Resonance 共振
A critical resonant frequency is that frequency at which any point on the specimen is observed to have
Amplitude 振幅
The specimens shall be subjected to a simple harmonic motion having an amplitude of either
1.52 mm (0.06 in) double amplitude (maximum total excursion) or 147.1 m/s2 (15 g n) peak, whichever is less. The tolerance on vibration amplitude shall be ±10%.
样品承受振幅为1.52mm(P-P)或峰值为15g的简谐振动,在两者之间选择振幅较小的一个.振幅的容许误差为±10%.。
Frequency range 频率
The vibration frequency shall be varied logarithmically between the approximate limits of 10 Hz to
three frequency bands are
The required maximum constant rates of frequency change for the three bands are therefore 8.55 Hz per minute, 34.2 Hz per minute and 137 Hz per minute, respectively. The minimum times of traverse of the bands are 8.2 min, 10.9 min and 10.9 min, respectively.
按照4.1.8.1的规定,假设将整个频段分为
频段,令频率的变化率与该段频段的最高频率之比值为
of decibels (dB). The number of decibels is defined by the equation:
The rms value of acceleration within a frequency band between f
Figure 4 - Test condition V, random vibration test-curve envelope (see table 2).
Table 2 - Values for test condition V 1)
Figure 5 - Test condition VI, random vibration test-curve envelope (see table 3).
Table 3 - Values for test-condition VI 1)
Figure 6 - Test condition VII, random vibration test-curve envelope (see table 4)。