取样长度在表面粗糙度测量中的应用
取样长度
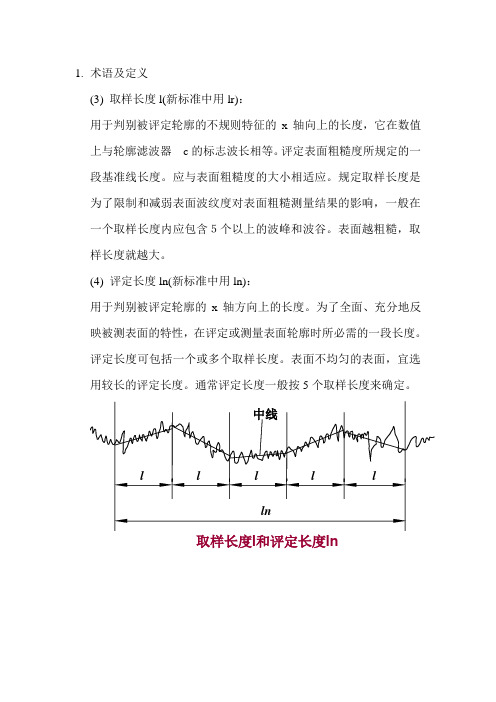
1.术语及定义
(3) 取样长度l(新标准中用lr):
用于判别被评定轮廓的不规则特征的x轴向上的长度,它在数值上与轮廓滤波器 c的标志波长相等。
评定表面粗糙度所规定的一段基准线长度。
应与表面粗糙度的大小相适应。
规定取样长度是为了限制和减弱表面波纹度对表面粗糙测量结果的影响,一般在一个取样长度内应包含5个以上的波峰和波谷。
表面越粗糙,取样长度就越大。
(4) 评定长度ln(新标准中用ln):
用于判别被评定轮廓的x轴方向上的长度。
为了全面、充分地反映被测表面的特性,在评定或测量表面轮廓时所必需的一段长度。
评定长度可包括一个或多个取样长度。
表面不均匀的表面,宜选用较长的评定长度。
通常评定长度一般按5个取样长度来确定。
中线
l l l l
l
ln
取样长度l和评定长度ln
≥0.008~0.02>0.02~0.1>0.1~2.0>2.0~10.0>10.0~80.0
Ra/μm Rz/μm lr/mm ln/mm ≥0.025~0.10>0.10~0.50>0.50~10.0>10.0~50.0>50.0~320.0
0.080.250.802.508.0
0.41.254.012.540.0
常用取样长度及评定长度
亚表面缺陷按照抛光加工过程和缺陷形貌可分为2 类: (1) 抛光点,即在抛光过程中形成的非常细小的分散凹点; (2) 抛光划痕,通常是由较大的抛光粉颗粒在工件表面滚动而形成的“香蕉形”凹坑,宽度为1~3μm ,长度不等。
表面粗糙度的测量方法1

y
i 1
5
pi
y vi
i 1
5
5
在取样长度内,也可从平行于轮廓中线m的任意一根线算起, 计算被测轮廓的五个最高点(峰)到五个最低点(谷)之间 的平均距离
Rz
(h2 h4 ...h10 ) (h1 h3 ...h9 ) = 5
3.轮廓最大高度
在取样长度内,轮廓峰顶线和轮廓谷底线之间的距离 (图4-3)。
实际工作中,对加工表面粗糙度的评 定可归纳为如下四种方式。
1.与表面粗糙度标准样板比较的方法
表面粗糙度样板:按各种加工方法做成的不同几何形状的 一套标准表面样块,用来与被测的表面 相比较。
表面粗糙度样板
测量方法:
目测法:Ra值2.5-80m的表面;
用5~10倍放大镜比较:Ra值0.32-2.5m的表面;
(2)算术平均中线: 在取样长度范围内,划分实际轮廓为上、下两部分, 且使上下两部分面积相等的线。
轮廓的算术平均中线
二、评定参数及数值:
对评定参数的基本要求:
(1)正确、充分反映表面微观几何形状特征;
(2)具有定量的结果; (3)测量方便。
国标从水平和高度两方向各规定了三个评定参数:三个基本 参数(水平),三个附加的评定参数(高度)
图4-5 光切原理
2.测量仪器原理及定度
(1)原理 光切显微镜的光路原理如图4-6所示。用测微目镜量出a、 a’的距离N,即可求出峰谷间的高度。
图4-6 光切显微镜光路
由于物镜分辨率及景深的限制,光切法测量范围一般为:
Rz= (80~0.8)m(旧国标3~9)。
粗糙度测量中取样长度、评定长度的合理选用

2 取样长度 与评 定长度在 实际J -过 jr n
程 中 的体 现
任 何表 面 的粗 糙度 都 是 由一 系列 不同 高
来稿时间:0 7年 5月 20
用 小于 5个取 样长度 的评定 长度值 ;对 于均
维普资讯
( 《 东方电 ̄ )0 " 20 年第 4 / 期
机床 一 刀具 一工 件 系统 、加 工方 匀 性较 差的表 面 ,则 可选 用大 于 5个取 样长 多种 因素 ( 度 的评 定长度 值 。对 于微 观 不平 度 间距 较大 法 、切 削 用量 、冷却 润 滑液 )共 同作 用 的结
结果的 准确 度 。 因此 寻 求一 个取样 长度 、 评 定 长度 在仪 器测 量 中的正 确 实施途 径尤 为必要 。 本 文着 重叙 述 了取 样 长度 、 评定 长度在粗 糙度 测量 中的重要 性及 如何选 取 、
应用。
关键 词
取 样 长度
评定 长度
表 面粗糙 度
表 1 R 、 zR aR 、 y的取 样长度 』 定 评 长度 』选 用值
特性 。一般情 况下 ,可 根据 表 面加 工 方法 和
> O.O ~ l O 5 O.
> l. ~ 5 O O0 0.
O. 8
2. 5
4. O
l . 25
粗糙度 参 数值 大 小选用 。 GB F 0 l一 19 F 13 95 规 定 了取样 长度推 荐值 ,见 表 1 。在 测 量 R R 和 R 时推荐 按表 1 z 选用 对应 的取 样值 , 此
> l ~ 8 O0 0O
8. O
400 .
Rz Ry1 , (m) a
≥ 0.2 ~ 0.O 05 1
表面粗糙度及其标注
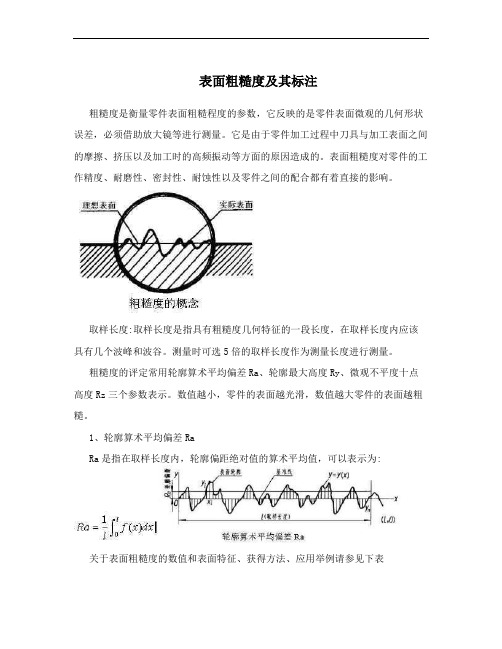
表面粗糙度及其标注粗糙度是衡量零件表面粗糙程度的参数,它反映的是零件表面微观的几何形状误差,必须借助放大镜等进行测量。
它是由于零件加工过程中刀具与加工表面之间的摩擦、挤压以及加工时的高频振动等方面的原因造成的。
表面粗糙度对零件的工作精度、耐磨性、密封性、耐蚀性以及零件之间的配合都有着直接的影响。
取样长度:取样长度是指具有粗糙度几何特征的一段长度,在取样长度内应该具有几个波峰和波谷。
测量时可选5倍的取样长度作为测量长度进行测量。
粗糙度的评定常用轮廓算术平均偏差Ra、轮廓最大高度Ry、微观不平度十点高度Rz三个参数表示。
数值越小,零件的表面越光滑,数值越大零件的表面越粗糙。
1、轮廓算术平均偏差RaRa是指在取样长度内,轮廓偏距绝对值的算术平均值,可以表示为:关于表面粗糙度的数值和表面特征、获得方法、应用举例请参见下表从上图中也可以看出,粗糙度参数的数值.基本上成倍数的关系。
标注时应当选用这些数值,不能选用其他的数值。
2、轮廓最大高度Ry3、轮廓不平度十点高度Rz1、代号及意义粗糙度代号可以分为:符号,粗糙度项目及数值。
常用标注参数是Ra, 标注Ra时Ra可以省略,标注Rz和Ry时,在粗糙度数值前加对应的符号Rz和Ry。
2、标注原则1)、在同一图样上每一表面只注一次粗糙度代号,且应注在可见轮廓线、尺寸界线、引出线或它们的延长线上,并尽可能靠近有关尺寸线。
2)、当零件的大部分表面具有相同的粗糙度要求时,对其中使用最多的一种,代(符)号,可统一注在图纸的右上角。
并加注“其余”二字。
3)、在不同方向的表面上标注时,代号中的数字及符号的方向必须下图的规定标注。
4)、代号中的数字方向应与尺寸数字的方向一致。
5)、符号的尖端必须从材料外指向表面。
标注举例:6)、齿轮、蜗轮齿面对于齿轮、蜗轮齿面的粗糙度,应标注在表示分度圆的点画线上。
如果图形中的位置有限,粗糙度也可以引出标注或注在尺寸线的延长线上。
7)、两个表面的粗糙度要求相同,也可以一个符号使用两个指引线。
表面粗糙度的测量方法
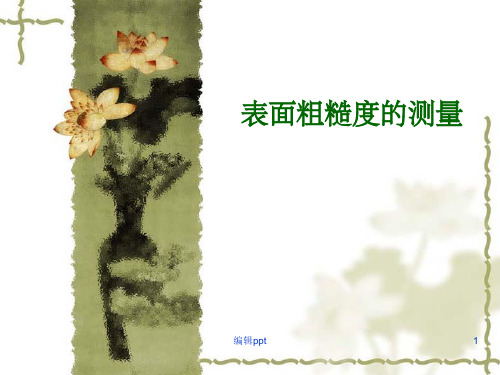
编辑ppt
1
第一节表面粗糙度的评定参数
主要内容:
1、主要术语及定义
取样长度L
评定长度L
n
轮廓中线m
2、6个评定参数
3个基本、3个附加
3、一般规定
重点: 3个基本评定参数
编辑ppt
2
一.主要术语及定义
1.实际轮廓:平面与实际表面相交所得的轮廓线。
按照相截方向的不同,它又可分为横向实际轮廓和纵向实 际轮廓。在评定或测量表面粗糙度时,除非特别指明,通 常均指横向实际轮廓,即与加工纹理方向垂直的截面上的 轮廓。
编辑ppt
17
取得表面测量信号以后,亦可用人工进行计算处理给出结果。
编辑ppt
18
❖ 15.2 表面粗糙度测量的基本原则
❖
(1)测量方向
❖
按现行标准所定义的各种粗糙度评定参数,是基于轮廓法确定数值,
是在被测表面的法向截面上的实际轮廓上进行测量的结果。由于垂直于
被测表面的法向截面存在各种不同的测量方向.试验表明,大多数的切
削加工表面,在横向轮廓上测得的粗糙度数值比较大,只是有的该铣加
工和个别端铣加工表面,在纵向轮廓上会有较大的数值。 如果在被测表
面上难以确定加工纹理方向,以及某些加工纹理紊乱或不存在固定方向
的表面,应分别在多个方向上测量,以获取最大参故值为结果.或取其
峰谷高度的最大值,计算一个区域的测量结果。
❖
编辑ppt
❖ 15.1 测量方法综述
❖ 对加工表面质量的评定,除了用视觉和触觉进行定性地比较检验的方 法以外,并逐步实现了用数值确定表面粗糙度参数值的定量测量。从本 世纪30年代陆续提出了测量粗糙度的方法原理和仪器以来,已发展了一 系列利用光学、机械、电气原理的表面粗糙度专用测量仪器,其基本结 构模式如图9—7所示。
表面粗糙度定义

表面粗糙度的国家标准主要术语及定义(1)表面粗糙度取样长度l取样长度是用于判断和测量表面粗糙度时所规定的一段基准线长度,它在轮廓总的走向上取样。
(2)表面粗糙度评定长度Ln由于加工表面有着不同程度的不均匀性,为了充分合理地反映某一表面的粗糙度特性,规定在评定时所必须的一段表面长度,它包括一个或数个取样长度,称为评定长度Ln。
(3)表面粗糙度轮廓中线m轮廓中线m是评定表面粗糙度数值的基准线。
评定参数及数值国家规定表面粗糙度的参数由高度参数、间距参数和综合参数组成。
表面粗糙度高度参数共有三个:(1)轮廓算术平均偏差Ra在取样长度l内,轮廓偏距绝对值的算术平均值。
(2)微观不平度十点高度Rz在取样长度内最大的轮廓峰高的平均值与五个最大的轮廓谷深的平均值之和。
(3)轮廓最大高度Ry在取样长度内,轮廓峰顶线和轮廓谷底线之间的距离。
表面粗糙度间距参数共有两个:(4)轮廓单峰平均间距S两相邻轮廓单峰的最高点在中线上的投影长度Si,称为轮廓单峰间距,在取样长度内,轮廓单峰间距的平均值,就是轮廓单峰平均间距。
(5)轮廓微观不平度的平均间距Sm含有一个轮廓峰和相邻轮廓谷的一段中线长度Sm i,称轮廓微观不平间距。
表面粗糙度综合参数(6)轮廓支承长度率t p轮廓支承长度率就是轮廓支承长度n p与取样长度l之比。
工件表面粗糙度是数字越小表面越光滑吗?数字的单位是um,看下面的参数可以知道数值越小工件表面越光滑表面粗糙度参数共有3个分别是Ra Rz RyRa 在取样长度内,轮廓偏距绝对值的算术平均值Rz 在取样长度内最大的轮廓峰高的平均值与五个最大的轮廓谷深的平均值之和Ry 在取样长度内,轮廓峰顶线和轮廓谷底线之间的距离顺便说一下表面粗糙度的表示方法:如果粗糙度表示符号是一个对号,里面加小短横,意思是通过加工的方法获得的表面粗糙度如果粗糙度表示符号是一个对号,里面加小圆圈,意思是非加工表面的粗糙度如果粗糙度表示符号是一个对号,里面什么也没有,意思是表面粗糙度无论用什么办法获得都可以如果图面没标注粗糙度选用Ra 还是Rz 还是Ry 的情况下应选用Ra.旧标准是级数越高越光洁,新标准是标注数字越小越光洁.(RMS)微粗糙度表面粗糙度是影响表面的物理和化学性能的重要因素。
取样长度、评定长度在粗糙度测量中的应用
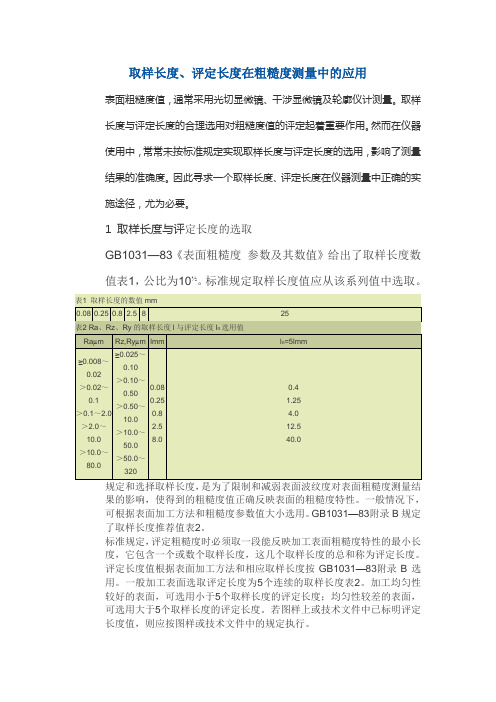
度和加工纹理》始于1940年。1947年,1955年,1962年三次修订成 ASA
B46.1.1962,1971年重新肯定了1962年标准。表中给出的美国标准为 ASA
B46.1.1962,1978年又修订成现行的 ANSI B46.1.1978《表面结构表面粗糙度、
波纹度和加工纹理》。
4.
英国的第一个国家标准是1950年发布的
有表面加工过程中所用加工方法的特征。
车、铣、刨削加工表面往往带有均匀的间距和清晰的刀具痕迹方向,其纹
理具有明显的规律性,它所形成的是一个典型的周期轮廓有时也叠加有不
同程度的随机成分有明显的周期,这一周期反映了进给量是均匀相等的,
加工表面均匀性好。
磨削加工表面虽有一般的方向性,但是间距通常是不规则的,纹理没有明
截止波长是轮廓谱中数值上等于取样长度的一个正弦波的波长,习惯上也
叫做切除长度,通常叫截止值。所以仪器的截止值就相当于测量时的取样
长度。
截止值与取样长度的区别是,截止值是一种手段,利用它可使获得的轮廓
波形限制在取样长度内进行评定的效果。而取样长度是用于判别具有表面
粗糙度特征的一段基准线长度,它可使表面粗糙度参数
根据截止值旋钮的位置来决定,两者必须一一对应。
各种轮廓仪计行程长度不尽相同,TALYSURF—4型轮廓仪 J、K、L 档对
应 截 止 值 为 0.25 、 0.8 、 2.5mm 的 行 程 长 度 是
0.25×8≈1.9mm,0.5×8≈3.8mm,2.5×3≈7.6mm。测量时行程长度旋钮调到
与截止值旋钮一致的相当位置。如 TALYSURF—4型测量行程长度旋钮 K
样长度。轮廓仪计的评定长度由仪器测量行程长度来表征。轮廓仪计的测
粗糙度知识摘要

粗糙度知识摘要一、英国泰勒TR120粗糙度仪工作原理测针垂直于表面横移,测针便随着表面微观几何形状的变化作垂直运动,压电传感器把测针位移的信号转换成电信号,通过滤波,计算出表面粗糙度参数值。
测针的尺寸和形状是影响获取表面轮廓信息是否真实的首要因素。
二、粗糙度评定参数及数值1、取样长度L取样长度是用于判断和测量表面粗糙度时所规定的一段基准线长度,它在轮廓总的走向上取样。
一般情况下当Ra>0.1~2.0µm时,取样长度为0.8µm。
2、评定长度Ln由于加工表面有着不同程度的不均匀性,为了充分合理地反映某一表面的粗糙度特性,规定在评定时所必须的一段表面长度,它包括一个或数个取样长度,称为评定长度Ln。
(一般取的5个取样长度,且其测量长度不能低于评定长度,这样才能提供足够的数据量进行分析。
)3、轮廓中线(也有叫曲线平均线)M轮廓中线M是评定表面粗糙度数值的基准线。
4、国家规定表面粗糙度的参数由高度参数、间距参数和综合参数组成。
4.1、表面粗糙度常用高度参数:4.1.1 Ra--轮廓算术平均偏差:在取样长度L内,轮廓偏离平均线的绝对值的算术平均值。
R a的图形解释Ra的局限性:不同特性的表面可能产生相同的Ra值。
4.1.2 Rz--粗糙度最大峰-谷高度:平均峰谷高度,是指每一个取样长度内粗糙度轮廓的最大轮廓峰顶高度与最大谷底深度之和,通常取5个取样长度范围内的平均值;R z的图形解释局限性当考虑摩擦和磨损特性时,由于表面的相互作用集中在此,因此峰是重要的。
峰的存在使得零件尺寸的测量受到磨损而不可靠,因为磨损去除了应包括在原始测量中的峰。
谷对于润滑油的保持是重要的。
然而破裂传播和侵蚀从谷开始。
不能保证测量会包括极端的表面。
因此,如果一个表面被重新测量偶数次以上,那么表面的一点不同部分可能引起结果的变化。
4.1.3 Rp--原始最大的轮廓峰高:在取样长度内,在平均线以上的轮廓的最大高度,通常取5个取样长度范围内的平均值。
- 1、下载文档前请自行甄别文档内容的完整性,平台不提供额外的编辑、内容补充、找答案等附加服务。
- 2、"仅部分预览"的文档,不可在线预览部分如存在完整性等问题,可反馈申请退款(可完整预览的文档不适用该条件!)。
- 3、如文档侵犯您的权益,请联系客服反馈,我们会尽快为您处理(人工客服工作时间:9:00-18:30)。
取样长度、评定长度在粗糙度测量中的应用
来源:温州三和量具仪器有限公司
表面粗糙度值,通常采用光切显微镜、干涉显微镜及轮廓仪计测量。
取样长度与评定长度的合理选用对粗糙度值的评定起着重要作用。
然而在仪器使用中,常常未按标准规定实现取样长度与评定长度的选用,影响了测量结果的准确度。
因此寻求一个取样长度、评定长度在仪器测量中正确的实施途径,尤为必要。
1 取样长度与评定长度的选取
GB1031—83《表面粗糙度参数及其数值》给出了取样长度数值表1,公比为10½。
标准规定取样长度值应从该系列值中选取。
规定和选择取样长度,是为了限制和减弱表面波纹度对表面粗糙度测量结果的影响,使得到的粗糙度值正确反映表面的粗糙度特性。
一般情况下,可根据表面加工方法和粗糙度参数值大小选用。
GB1031—83附录B规定了取样长度推荐值表2。
标准规定,评定粗糙度时必须取一段能反映加工表面粗糙度特性的最小长度,它包含一个或数个取样长度,这几个取样长度的总和称为评定长度。
评定长度值根据表面加工方法和相应取样长度按GB1031—83附录B选用。
一般加工表面选取评定长度为5个连续的取样长度表2。
加工均匀性较好的表面,可选用小于5个取样长度的评定长度;均匀性较差的表面,可选用大于5个取样长度的评定长度。
若图样上或技术文件中已标明评定长度值,则应按图样或技术文件中的规定执行。
所谓“加工表面均匀性”是指加工后表面各部位粗糙度数值一致的程度。
如果在一个加工表面上按取样长度连续测量几段所得粗糙度值一样,说明加工表面均匀;反之粗糙度值不一样,有时甚至相差很大,则表明加工表面不均匀。
任何表面的粗糙度都是由一系列不同高度和间距的峰谷组合而成,这些峰谷反映了加工表面微观几何形特性。
从外观上或感觉上这种特性通常总带有表面加工过程中所用加工方法的特征。
车、铣、刨削加工表面往往带有均匀的间距和清晰的刀具痕迹方向,其纹理具有明显的规律性,它所形成的是一个典型的周期轮廓有时也叠加有不同程度的随机成分有明显的周期,这一周期反映了进给量是均匀相等的,加工表面均匀性好。
磨削加工表面虽有一般的方向性,但是间距通常是不规则的,纹理没有明显的规律。
研磨加工表面是通过磨料的往复作用所产生的表面,往往没有什么方向性。
磨削、研磨分别用砂轮和磨料进行切削抛光,使表面光滑平整。
但由于砂轮的磨粒大小、磨料颗粒尺寸形状不规则,切削力不等,使加工表面形成随机轮廓,虽有周期成分,但随机成分是主要的,表面均匀性差。
因此,加工表面的粗糙度是加工过程中多种因素机床—刀具—工件系统、加工方法、切削用量、冷却润滑液共同作用的结果。
这些因素的作用过程相当复杂,而且是不断变化的。
所以用不同加工方法或在同样加工方法、同样切削条件下切削出来的同一批零件,不同表面不同部位其粗糙度值也不完全相同。
根据每一种加工方法具有的独特表面特征,表3列出了各种典型方法选用的取样长度和评定长度经验值。
2 取样长度与评定长度在测量仪器中的实施
轮廓仪计利用滤波器抑制波纹度的影响来实现取样长度的选择。
通常滤波器特性在截止波长处急剧变化,轮廓谱通过滤波后使间距小于截止波长的粗糙度都无变化地通过,而间距大于截止波长的粗糙度却被完全抑制。
截止波长是轮廓谱中数值上等于取样长度的一个正弦波的波长,习惯上也叫做切除长度,通
常叫截止值。
所以仪器的截止值就相当于测量时的取样长度。
截止值与取样长度的区别是,截止值是一种手段,利用它可使获得的轮廓波形限制在取样长度内进行评定的效果。
而取样长度是用于判别具有表面粗糙度特征的一段基准线长度,它可使表面粗糙度参数
值从波度和波距大于其值的不平度中区分开来。
由记录器记录表面轮廓曲线时,不必考虑截止值。
而用平均值量表测量时,必须考虑截止值。
截止值旋钮置于电器箱上,通常有三档截止节距值对TALY-SURF—4轮廓仪三档为J、K、L,它们分别对应着0.25、0.8、2.5mm取样长度值。
截止值的选取,应首先了解被测件的加工方法,并对表面粗糙度值作初步判断,根据表4确定。
评定长度是评定轮廓表面粗糙度所必须的一段长度,它包括一个或数个取样长度。
轮廓仪计的评定长度由仪器测量行程长度来表征。
轮廓仪计的测量行程长度,是用作测量表面粗糙度的一段修整轮廓长度,即在测量时由于滤波器作用产生的与传感器同步的触针移动轨迹。
测量行程长度包括一个或数个取样长度。
测量行程长度与评定长度不同之处是,评定表面粗糙度参数值所依据的“长度”有差异,前者是实际测量中采用轮廓仪计所得到的一段修整轮廓长度,而后者是理论上定义的评定表面粗糙度所必须的一段长度。
由此可以说,行程长度是评定长度在实际测量中,使轮廓仪计实现表面粗糙度参数测量的具体体现。
测量行程长度与评定长度相同处是,都包括一个或数个取样长度。
一般行程长度取5个截止值相当于5个取样长度,这与一般选用评定长度为5倍取样长度相一致。
行程长度旋钮置于驱动箱上,标记J、K、L三档。
行程长度旋钮的位置根据截止值旋钮的位置来决定,两者必须一一对应。
各种轮廓仪计行程长度不尽相同,TALYSURF—4型轮廓仪J、K、L档对应截止值为0.25、0.8、2.5mm的行程长度是0.25×8≈1.9mm,0.5×8≈3.8mm,2.5×3≈7.6mm。
测量时行程长度旋钮调到与截止值旋钮一致的相当位置。
如TALYSURF—4型测量行程长度旋钮K档,仪器测读的粗糙度值是一个测量行程长度3.8mm的平均值。
必须指出,目前使用的触针式轮廓仪可以直接测读粗糙度Ra值,一般不能按粗糙度Rz、Ry 定义直接测得结果,但可通过记录轮廓图形进行计算。
此时应注意尽量使记录图形的走向处于水平线上,截止值在轮廓总的走向上量取。
只要记录图形的垂直放大倍率可靠,截取截止值的水平放大倍率准确,可以获得可信赖的Rz、Ry值。
应注意水平放大倍率的变化。
该变化是靠变动驱动箱上速度选择旋钮改变传感器运动速度获得的,因此正确选择速度旋钮的档位很重要。
表5给出了速度选择旋钮的参考值。
速度旋钮选用的总原则是使轮廓图形中峰与峰之间距离不要太密集而要拉开一些。
当选用截止值为0.8mm,水平放大倍率为20X,则应在轮廓图总的走向上量取0.8×20=16mm。
多参数轮廓仪可直接显示粗糙度RZ,RY值,但仪器显示的粗糙度RY值与标准定义的粗糙度RY有区别。
一般是在行程长度内给出的结果或是微观不平度高度相邻峰谷的最大值。
光切显微镜、干涉显微镜通常用来测量粗糙度RZ,RY参数值。
测量时应按规定确定取样长度、评定长度。
对粗糙度RZ而言,在仪器示场中取样长度内,测出5个最高点5个最低点数值计算粗糙度RZ值,在评定长度内测出数个连续取样长度上的粗糙度RZ值,取其平均值作为测量结果。
如果仪器视场直径不足一个取样长度或一个评定长度,以及测量圆弧曲面时不大可能按定义取点计算表6,在这种情况下,必须在一次测量中移动工作台,使被测部位顺次移入视场。
建议采用下述方法计算:把选定的取样长度l分成5个相等的分量l′1、l′2、……l′5,在每个取样长度分量上各测一个最大峰谷高附图得h1、h2、……h5,计算得到RZ=(h1+h2+h3+h4+h5)/5
需指出,各取样长度分量之间必须是连续的。
为保证l′1=l′2=……=l′5,应均匀移动工作台,使工作台移动量相等,同时从目镜视场中注意观察被测表面轮廓移动情况,以免重复测量同一长度轮廓曲线。
对粗糙度RY而言,如果仪器视场直径小于一个规定取样长度时,可取视场直径为取样长度,在观测范围内取最大峰谷值,然后在相邻视场中再测出一个轮廓最大高度,取两读数中大者作为一个取样长度的测量值。
严格地说,按上述方法求得的粗糙度RZ、RY值是近似值。
文章链接:中国化工仪器网/Tech_news/Detail/18556.html。