日本服装生产工艺流程的两个特点
针织工艺流程

针织工艺流程-标准化文件发布号:(9456-EUATWK-MWUB-WUNN-INNUL-DDQTY-KII针织服装的工艺流程:纺纱→编织→验布→裁剪→缝制→整烫→检验(一)纺纱纺纱的目的是使进厂的棉纱卷绕成一定结构与规格的卷装筒子,以适合针织生产之用。
在纺纱过程中要消除纱线上存在的一些疵点,同时使纱线具有一定的均匀的张力,对纱线进行必要的辅助处理,如上蜡、上油等,以改善纱线的编织性能,提高生产效率和改善产品质量。
(二)编织编织是通过织机使纱线组织成线卷互相串套而成为织物的过程。
这也是针织服装和梭织服装的根本区别。
编织方法可分为纬编和经编两大类,作为针织用衣的面料大都是纬编织物。
纬编是将一根或数根纱线由纬向喂入针织机的工作针上,使纱线顺序地弯曲成圈,且加以串套而形成纬编针织物。
用来编织这种针织物的机器称为纬编针织机。
纬编对加工纱线的种类和线密度有较大的适应性,所生产的针织物的品种也甚为广泛。
纬编针织物的品种繁多,既能织成各种组织的内外衣用坯布,又可编织成单件的成形和部分成形产品,同时纬编的工艺过程和机器结构比较简单,易于操作,机器的生产效率比较高,因此,纬编在针织工业中比重较大。
纬编针织机的类型很多,一般都以针床数量,针床形式和用针类别等来区分。
经编是由一组或几组平行排列的纱线分别排列在织针上,同时沿纵向编织而成。
用来编织这种针织物的机器称为经编针织机。
一般经编织物的脱散性和延伸性比纬编织物小,其结构和外形的稳定性较好,它的用途也较广,除可生产衣用面料外,还可生产蚊帐、窗帘、花边装饰织物、医用织物等等,经编机同样也可以以针床、织针针型来进行区分。
(三)验布由于坯布的质量直接关系到成品的质量和产量,因此裁剪前,必须根据裁剪用布配料单,核对匹数、尺寸、密度、批号、线密度是否符合要求,在验布时对坯布按标准逐一进行检验,对影响成品质量的各类疵点,例如色花、漏针、破洞、油污等须做好标记及质量记录。
(四)裁剪针织服装裁剪的主要工艺过程:断料→借疵→划样→裁剪→捆扎。
服装生产的制作实用工艺设计流程介绍
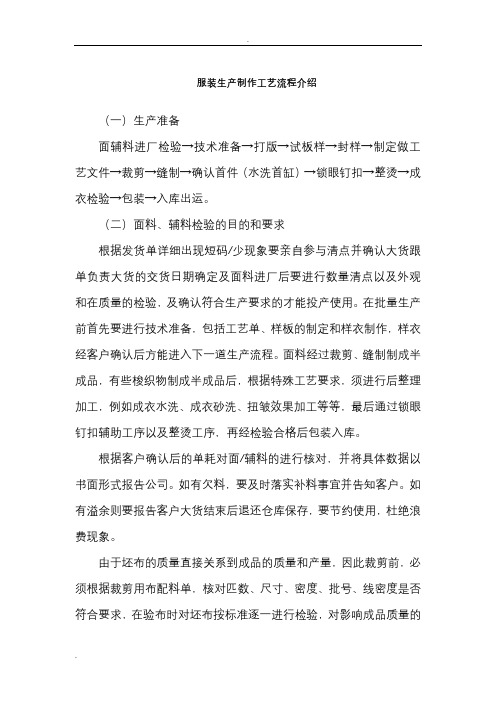
服装生产制作工艺流程介绍(一)生产准备面辅料进厂检验→技术准备→打版→试板样→封样→制定做工艺文件→裁剪→缝制→确认首件(水洗首缸)→锁眼钉扣→整烫→成衣检验→包装→入库出运。
(二)面料、辅料检验的目的和要求根据发货单详细出现短码/少现象要亲自参与清点并确认大货跟单负责大货的交货日期确定及面料进厂后要进行数量清点以及外观和在质量的检验,及确认符合生产要求的才能投产使用。
在批量生产前首先要进行技术准备,包括工艺单、样板的制定和样衣制作,样衣经客户确认后方能进入下一道生产流程。
面料经过裁剪、缝制制成半成品,有些梭织物制成半成品后,根据特殊工艺要求,须进行后整理加工,例如成衣水洗、成衣砂洗、扭皱效果加工等等,最后通过锁眼钉扣辅助工序以及整烫工序,再经检验合格后包装入库。
根据客户确认后的单耗对面/辅料的进行核对,并将具体数据以书面形式报告公司。
如有欠料,要及时落实补料事宜并告知客户。
如有溢余则要报告客户大货结束后退还仓库保存,要节约使用,杜绝浪费现象。
由于坯布的质量直接关系到成品的质量和产量,因此裁剪前,必须根据裁剪用布配料单,核对匹数、尺寸、密度、批号、线密度是否符合要求,在验布时对坯布按标准逐一进行检验,对影响成品质量的各类疵点,例如色花、漏针、破洞、油污等须做好标记及质量记录把好面料质量关是控制成品质量重要的一环。
通过对进厂面料的检验和测定可有效地提高服装的正品率。
面料检验包括外观质量和在质量两大方面。
外观上主要检验面料是否存在破损、污迹、织造疵点、色差等等问题。
经砂洗的面料还应注意是否存在砂道、死褶印、披裂等砂洗疵点。
影响外观的疵点在检验中均需用标记注出,在剪裁时避开使用。
面料的在质量主要包括缩水率、色牢度和克重(姆米、盎司)三项容。
在进行检验取样时,应剪取不同生产厂家生产的、不同品种、不同颜色具有代表性的样品进行测试,以确保数据的准确度。
同时对进厂的辅料也要进行检验,例如松紧带缩水率,粘合衬粘合牢度,拉链顺滑程度等等,对不能符合要求的辅料不予投产使用。
生产特点

服装工业生产特点服装工业技术管理工作即在现代工业企业中,对发生的一切技术活动,按照行业本身的特点和规律,并参照政府发布的各项技术政策,有计划、有组织、有目的地进行指挥和协调及检查和督促等活动。
为此,了解服装工业生产特点对加强服装工业的技术管理事关重要。
服装工业生产特点主要有如下几个方面:1.生产之间的协作性服装生产的形式因科技进步和先进专用设备配备的使用起了很大变化,批量性的成衣生产代替了一家一户的个体生产方式,从而使生产技术进步及产品质量的提高都是个体手工业生产无法比拟的。
同时,生产技术的进步也给生产管理带来了新课题,那就是生产过程广泛的协作性,即如何加强部门之间、工序之间的衔接与协调建立起良好的协作关系。
订做工作服实践证明,现代化的服装生产流水作业,没有管理就不能维护正常的生产秩序。
现代服装生产己形成了一项系统工程,每道工序有其独立性,各工序之间又有严密的相关性,使工序之间形成有机的结合。
由众多的技术工人合作一件产品,如果没有合理的工艺流程及严格的流程管理,没有严谨有效的生产技术的组织者和指挥者,没有部门之间、工序之间的相互协调、检查和督促,要使生产有序进行是不可能的.广泛的协作不仅是企业内部,而且还会延伸到原料、辅料和供应以及有关生产协作单位。
由此可见,广泛的生产协作性是服装生产管理的内容之一。
工作服制作2.生产技术的专业性在同一个服装市场上,你可以看到五颜六色、千姿百态的服装,但是作为一个企业由于受生产专用设备及生产技术的局限性,很难做到样样服装都生产,即使是很大的服装集团公司,也不可能在一个车间生产所有品种的服装。
服装的品种很多.按面料的结构可以分为梭织服装、针织服装及皮革服装.按照用途可以分为礼仪服装、休闲服装、时装、男衬衫、睡衣睡袍、防寒服、雨衣、工作服等。
这些服装的生产要采用流水作业,并配备各类专用设备。
由于分工比较细,形成生产工人的技术单一和生产技术的专业性,不仅各大类品种之间“隔行如隔山”,就是在一个企业中,生产流水线上80%的工人只会操作2一3道工序,技术全面的工人很少。
服装具体工艺流程及展示

具体工艺展示拱针:为加强西服领.门襟.口袋等关键部位的造型,更具有耐穿度与美观。
里布:铂纶西服里布采用日本宾霸内里,做了防静电处理,使穿着更加方便舒适。
加强布:在腋下肢体动作最大的地方设计加强布,预防破裂的可能性。
内袋:本布捆大口袋耐力设计,除了大的口袋,增加了笔袋和卡片袋,让西服穿着者有更多的收纳空间。
止滑带:裤腰特别加上一整圈止滑带,让衬衫不易外露,更加得体。
挂面:出芽加拱针的工艺,巩固与装饰并重,让西服下摆更加服帖。
预留缝:铂纶每一套西服都在版型中贴心设计了预留缝,以便日后修改。
耐磨布:为了增加西裤的穿着寿命,特别在最常摩擦的部位增加了裆部和裤口耐磨布工艺流程一.常用缝制线迹(针码密度)需求1.明线:每3厘米为14~17针。
2.手工针:每3厘米不少于7针,肩缝.袖笼处每3厘米不少于9针。
3.三线包缝(码边):每3厘米不少于9针。
4.手拱止口:每3厘米不少于5针。
5.三角针:每3厘米不少于5针。
6.锁眼:机锁.细线每1厘米为12~14针。
手锁.粗线每1厘米不少于9针。
7.钉扣:细线每孔8根线。
粗线每孔4根线。
且缠脚高不能小于止口的厚度。
缝制时的工艺技术需求1.缝制线迹(针码密度)需求:(1)明线:每3厘米为14~17针。
(2)手工针:每3厘米不少于7针,肩缝.袖笼处每3厘米不少于9针。
(3)三线包缝(码边):每3厘米不少于9针。
(4)手拱止口:每3厘米不少于5针。
(5)三角针:每3厘米不少于5针。
(6)锁眼:机锁.细线每1厘米为12~14针。
手锁.粗线每1厘米不少于9针。
(7)钉扣:细线每孔8根线。
粗线每孔4根线。
且缠脚高不能小于止口的厚度。
2.缝制时的技术需求:(1)缝制时,各部位缝合线路顺直,无跳线.脱线,且缝制整齐牢固.平服美观。
(2)缝制时的面.底线应松紧适宜,并且起针和落针时应回针固缝,以免缝线脱落。
(3)缝合后的部位,不能有针板.送布牙所造成的痕迹。
(4)缝制滚条.压条时要保障宽窄一致.平服。
服装生产制作工艺流程介绍

服装生产制作工艺流程介绍1.布料采购:制作服装的第一步是采购布料。
制造商根据服装样式的设计和要求选择合适的面料,以满足成品的属性和功能需求。
布料的选择通常涉及纺织品的品质、颜色、纹理、重量和面料的用途等因素。
2.裁剪:下一步是将布料进行裁剪。
根据服装的尺寸和样式,在面料上标记出所需的形状和尺寸,并使用裁剪工具沿着标记线进行裁剪。
这个步骤非常关键,因为它直接影响到后面的缝纫和组装过程。
3.缝纫:裁剪后,布料的各个部件将被缝合在一起。
缝纫工人根据裁剪好的布料部件之间的拼接方式,使用缝纫机进行针线缝合。
在这个过程中,确保缝合处的强度和平整度非常重要,以保证成品的质量和外观。
4.烫压:缝纫完成后,服装需要经过烫压处理,以去除布料在裁剪和缝合过程中产生的皱纹。
烫压不仅可以使衣物看起来更平整,还可以提升成品的质感和外观。
烫压还可以帮助一些特殊面料保持其特定的形状和纹理。
5.细部加工:在服装的制作过程中,还需要进行一些细部加工,例如添加拉链、纽扣、口袋、袖口等。
这些细部加工在提升服装的功能性和美观性方面起着重要作用。
6.质量检验:完成细部加工后,服装需要进行质量检验。
质量检验旨在确保成品符合预期的标准和质量要求。
质量检验可以包括外观检查、尺寸测量、强度测试等。
8.成品存储和配送:最后,成品被储存起来,等待配送。
成品可以存储在仓库中,等待分配给零售商、分销商或直接发送给最终消费者。
在存储和配送的过程中,需要确保成品的安全和保护,以及及时准确地满足订单和客户需求。
以上是一般服装生产制作工艺流程的介绍。
实际上,每个服装制造商可能会有自己的工艺流程,以满足其独特的生产需求和标准。
生产工艺流程、设备、技术介绍、特色
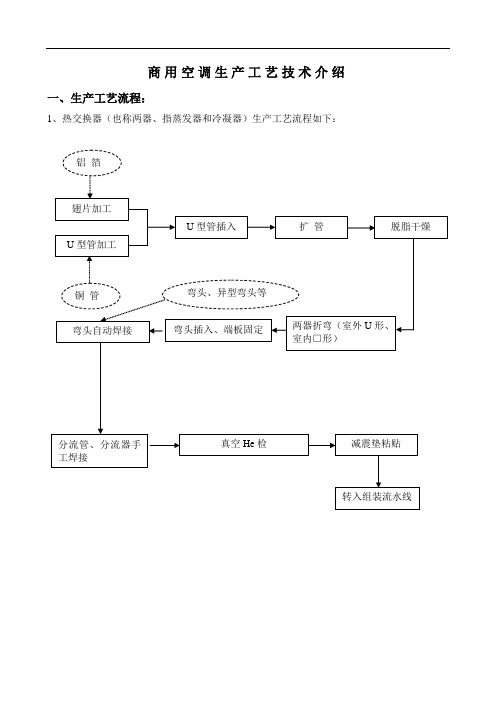
商用空调生产工艺技术介绍一、生产工艺流程:1、热交换器(也称两器、指蒸发器和冷凝器)生产工艺流程如下:2、空调产品组装生产工艺如下:(1).室外机组装生产工艺:二、生产工艺特色:青岛日立商用空调生产车间采用从日立引进的成熟先进的生产工艺技术,主要生产设备及检测设备均为日本进口。
(一)、热交换器(也称两器)生产设备及工艺:1、冲片机和冲片模具:本设备和模具为全部为日本进口,设备模具厂家日高精机株式会社是日本专业生产冲片模具的厂家,其生产的冲片模具技术水平(技术优势)在世界同行业中处于领先水平。
本工序采用亲水铝箔,经精密模具高速冲片,形成波纹形双面桥形翅片,此种材料的片型技术先进,有利于提高换热器的换热效率和整机性能,同时可提高空调的使用寿命。
2、长U弯管机:本设备主要是日本进口设备,其技术水平在世界处于领先地位。
本工序采用薄壁内螺纹铜管加工U型管,此种内螺纹铜管能改善制冷剂在管路系统中的流动状态,从而提高其换热效率,它比一般光滑管可提高换热效率20%~30%左右。
3、胀管机:本设备主要是日本进口设备,其技术水平在世界处于领先地位。
本设备采用高光洁度球型胀头对工件进行胀管,保证了铜管与翅片孔之间的合理过盈量,同时避免了胀管过程中胀头对铜管内螺纹部分的破坏,保证了胀管后产品的质量。
4、脱脂干燥炉:由于产品循环系统中的残留油分会对空调的性能存在一定的影响,所以需对热交换器进行脱脂干燥,本工序就是对胀管完成的热交换器半成品进行高温脱脂干燥(脱脂温度为150~160℃),以去除工件翅片表面和铜管内部的挥发油,工件经过脱脂干燥后,可使其铜管内部的残油量在3mg/m2以下。
5、热风干燥炉:由于空调循环系统内部冷媒中如果混入过多的水分,会严重影响到空调的整机性能,本工序的作用就是去除油分离器、气液分离器、热交换器组件、配管等系统零部件内部的水分,零部件经本工序去水干燥后,可保证工件内部残留水分量60ppm在以下。
服装厂西服生产工艺流程

服装厂西服生产工艺流程一、流程:--打印麦头排版〔归类〕--拉布——开剪-—编号——压衬-—精裁 ——订标签——验片 --分包,扎包 (大约3天)开包--分工(做领、袖、前片、后片…)—-中检-—拼叶子片-—烫-—开袋—-复衬——门襟——拼缝——检验-—上领袖(大约7天)后检配套:打套结——锁眼-—订纽扣——拆线头——立体整烫——补烫--总检 (大约4—5天)整个生产周期大约15天整个生产工序:共445道工序二、生产工艺介绍:服装版型以欧洲版型为基础,宽肩、收腰、修长、圆润,总体有“H"型感觉,具有轻、挺、柔、薄的特点。
专业量体师进行量体时,首先对人体的着装进行目测,确定哪一种版型。
然后,对不同的体型,如凸肚、塌肩等体态采用不同的手势,掌握好收放尺码的技术处理。
再次采用样衣套穿,对尺寸进行技术处理的方法,量定尺寸后,尺码输入电脑进行分类整理,打印出所有人员的花名册及尺码表,生产工人能时时时核对,以免发生误差。
同时,根据中国人的体型特点,设计出了符合国人穿着的版型,版型的尺码之间结构合理、设计严谨,对各部位之间的距离进行灵活的调节,保证整体线条的流畅。
然后,利用法国力克电脑设计系统专门设计各种款式.专职人员将客户量体资料输入电脑,并在电脑排版系统上自动排版,排好版后,通过网络传输到法国力克自动裁床上直接进行裁剪。
在裁剪前先对面料进行预缩处理,保证裁剪的精确,裁剪下来的毛皮经粘合衬高温粘合后,再对毛片进行第二次精心裁剪,保证尺寸的稳定.然后各部位打上尺码,保证各部分毛片能准确无误的缝合在一起。
整件衣服的上袖、上领、上胸衬、开袋、上里布等工艺皆由专门的德国杜克普专用设备完成,并由整烫机整烫后进入下道工序.整烫时,整套衣服按胸、肩、领、脖、腰、裤腿、臀的顺序,由专门男、女人体模具整烫机进行大烫,最后要按人身体的曲线进行补烫。
整个过程一丝不苟,使各部位之间的线条过渡自然、圆润.我司还引进了法国力克自动拉布机和瑞典铱腾公司的自动吊挂系统,提高了服装生产的自动化程度,使服装的生产工艺更加完美。
喷气涡流纺纱产品设计与开发
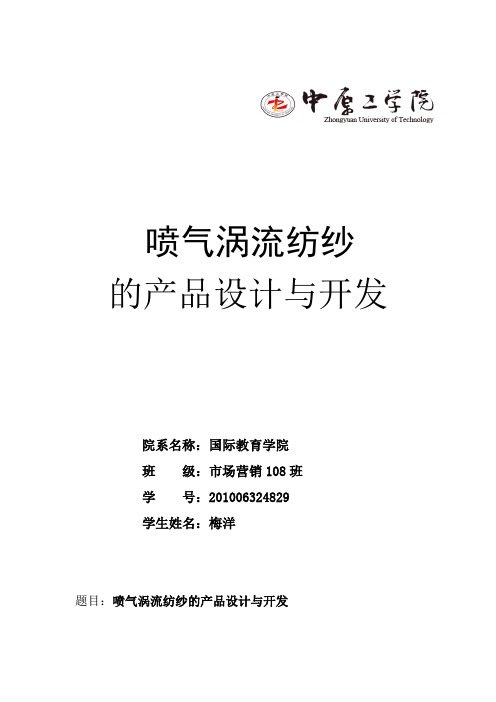
喷气涡流纺纱的产品设计与开发院系名称:国际教育学院班级:市场营销108班学号:201006324829学生姓名:梅洋题目:喷气涡流纺纱的产品设计与开发喷气涡流纺纱产品设计与开发引言喷气涡流纺(MVS)是日本村田公司在喷气纺纱机(MJS)的基础上成功研制的一种更新的纺纱机。
一、纺纱原理喷气涡流纺(MVS)既不同于环锭纺,也不同于转杯纺,它是由棉条喂入并经过四罗拉(或者五罗拉)牵伸机构牵伸后达到需要的纱线支数的平行纤维束,在负压的作用下被吸入喷嘴中。
纤维束的前端在导引针的周围,受正在形成纱的尾端的拉引而导入引纱管中;而纤维束的后端受到高速涡流轴向分力的作用,部分纤维在引纱管入口处呈伞状倒状,倒状的纤维便露在喷孔喷出的回旋气流中。
随气流的回转捻到纱尾上,形成实捻状的短纤维纱输出,纤维束沿着锭子包缠的角度和回转角度都是可以控制的。
二、纺纱的特性及特点喷气涡流纺(MVS) 无高速回转机件(如环锭纺中的锭子,钢丝圈等)采用旋转涡流加捻成纱,比机械式加捻效率高,高速回转的涡流只作用在纤维上,与前罗拉引出的纤维的功能一起形成对纤维的加捻作用,高速涡流除了完成加捻任务外,并不影响纱线支数的高低,因此可实现高速纺纱,最高纺速实际可达380m/min,每锭的产量相当于环锭纺单锭产量的22倍左右。
由于纤维受到具有声速的喷气涡流及卷取罗拉作用而形成真捻,因此这种特殊的加捻作用是其它纺纱机械不能取代的,纱线高的回旋速度下的成纱结构比环锭纱线的结构更为紧密和稳定。
三、生产工艺特点和技术措施1.1 试验用原料及品种原棉:原棉等级:2级;主体长度:29.4mm;短绒率:12.2%;细度(马克隆值):4.02;成熟度:1.53。
品种:JK18tex1.2 工艺流程清梳联合机→并条机→条卷机→精梳机→并条机→并条机→喷气涡流纺纱机→成件。
1.3 设备及测试仪器设备:清梳联合机:德国特吕斯特纺织机械有限公司DK903并条机:陕西宝成纺织机械有限公司FA311条卷机:瑞士立达纺织机械有限公司E3/2精梳机:瑞士立达纺织机械有限公司E6/2喷气涡流纺纱机:日本村田纺织机械有限公司MVS810 72锭/台仪器:条干仪:瑞士乌斯特公司Uster- 4型电子捻度仪:山东莱州电子仪器有限公司Y331(LN)强力仪:山东莱州电子仪器有限公司YG061F毛羽仪:日本Toray DT2012.1 纺纱工艺要点涡流纺纱的机理是纤维条经牵伸后形成纤维束,纤维束在喷管中稳定的涡流控制下加捻及末端扩张,再经空心锭子的捻搓作用后旋转,完成外部包缠纤维和纱芯纤维的加捻作用,成纱具有独特的内外结构特征。
- 1、下载文档前请自行甄别文档内容的完整性,平台不提供额外的编辑、内容补充、找答案等附加服务。
- 2、"仅部分预览"的文档,不可在线预览部分如存在完整性等问题,可反馈申请退款(可完整预览的文档不适用该条件!)。
- 3、如文档侵犯您的权益,请联系客服反馈,我们会尽快为您处理(人工客服工作时间:9:00-18:30)。
日本服装生产工艺流程的两个特点
日本人向来以严谨仔细著称,接下来,我们来了解一下日本女装的生产工艺,日本
高级女装生产的特点是少批量多品种。
因此,生产流水线的安排与我国女装企业相比存在较大的差异。
高级女装生产一般采用半自动吊挂生产系统,一个衣架按一定的规则挂上同一件衣服的各个裁片,而且每个衣架都标注序号,这样虽然在吊挂时稍显费时,但对于整个生产管理则是利大于弊。
其一可减少占地,取置方便,快速流通;其二可避免色差;其三前后工序互相监督和帮助,不仅能提高产量,而且也保证了产品的质量。
具体的生产工艺流程一下两大特点:
一、辅料的检验、测试和整理
面料(包括部分辅料)在裁剪前,均经热缩、定型加工,其热缩工艺可确保成衣尺寸稳定,定型工艺能将面料丝绺归正,固定织物的经纬纱组织。
因此,不同类型、不同厚薄的面料均可在同类缝纫设备上加工,简单方便,从而可减少调试机器所带来的损耗。
另外,经热缩与定型加工的面料,即可直接裁剪,无须长时间松布冷却,减少布匹堆压起皱,从而节省了裁剪时间(一般可达到24匹/8小时)。
二、工序分析
1、工序平衡
工序平衡是工序分析的重点内容,也是最难掌握之处。
管理人员需要根据产品、设备及员工的具体情况,进行认真仔细的分析研究,促使流水线通畅快速。
主要须做好以下工作:
科学合理地计算出流水线小组每道工序的平均加工时间,如标准夹克衫为3分钟。
同时要做到每道工序有3个吊挂衣架(即3件半成品),保持均等。
根据工人的技术情况调整工序安排,这里主要考虑工人的技术特长和综合素质。
如有些工人适合做前道工序就不能安排在后道工序;而有些工人技术不全面,则应避免安排在技术难度较大的工序。
员工有时会因生病、请假缺勤等情况,这时也要作适当的调整,否则流水线将出现停顿阻塞现象。
及时调整“亚健康”的流水作业。
这里所指的“亚健康”是指整个流水线表面看上去比较顺畅,其实不然,经常会出现产量下降的现象,其主要原因往往是每道工序的速度变慢。
这时只需调整其中一道关键工序的速度就能改变这种状况,加快整条流水线的速度。
2、工序分析的作用及重要性
工序是构成作业系列的最小单元。
工序分析是指对基本材料加工使之成为成品这一过程的所有作业进行分解,明确每个加工步骤的作业性质、先后顺序、使
用的设备、以及所消耗的时间等内容,以便有效地利用劳动力和设备,确保产品以最快的速度、最低的成本加工出来。
明确女装产品加工工序的内容、顺序、所用时间及需要的工具和设备,使生产有条不紊,便于生产指导和管理。
工序分析表或工艺流程图可作为工序编制、生产计划与安排等工作的基础材料,有利于生产线平衡。
发现生产流水线设计的不足,进一步改善工序组织,不断提高生产效率。
服装企业生产流程
不同的服装企业有不同的组织结构、生产形态和目标管理,但其生产过程及工序是基本一致的。
服装生产大体上由以下8道主要的生产环节组成;
1.服装设计一般来说,大、中型服装厂都有自已的
计师来设计服装系列款式。
企业的服装设计大致分两娄;第一类是成衣设计,根椐大多数人的号型比例,制定一套有规律的尺码,进行大规模生产。
设计时,不仅要选择面料、辅料,还要了解服装厂的设备和工人的技术;第二娄是时装设计,根椐市场流行趋势和时装潮流设计时装。
2.纸样设计当服装设计的样衣为客户确认后,下一步就是
按照客户的要求绘制不同尺码的纸样。
将标准纸样进行放大或缩小的绘图,称为“纸样放码”,又称“推档”。
目前,大型的服装公司多采用电脑来完成纸样的放码工作。
在不同尺码纸样的基础上,还要制作生产用纸样,并画出排料图。
3.生产准备生产前的准务备工作很多,如对生产所需的面料、辅料、缝纫线等材料进行必要的检验与测试;材料的预缩和整理;样衣的缝制加工等。
4.裁剪工艺一般来说,裁剪是服装生产的第一道工序,其内容是把面料、里料及其他材料按排料、划样要求剪切成衣片,还包括排料、铺料、算料坯布疵点的借裁、套裁、验片、编号、捆扎等工作。
5.缝制工艺缝制是服装加工过程中技术性较强,也较重要的加工工序。
按不同的款式要求,通过合理的缝合,把各衣片组合成服装的一个工艺处理过程。
所以,如何合理地组织缝制工序,选择缝迹、缝型、工具和机器设备等都十分重要。
6.熨烫工艺服装制成后,经过熨烫处理,会达到理想的外观,使其造型美观。
熨烫一般可分为生产中的熨烫(中烫)和成衣熨烫(大烫)两娄。
7.成衣品质控制是使产品质量在整个加工过程中得到保证的一项十分必要的措施,是根据产品在加工过程中产生的质量问题,制定必要的质量检验标准。
8.后处理包括包装、储运等内容,是整个生产过程中的最后一道工序。
操作工按包装工艺要求将每一件整烫好的服装整理、折叠好,放在胶袋里,然后按装箱单上的数量分配装箱。
有时成衣也会被吊装发运,即将服装吊装在贷架上,送到交贷地点。
为了使工厂按时交贷,赶上销售季节,在分析服装产品的结构、加工工艺等特点后,对纸样设计、成品规格、裁剪工艺、缝纫加工、整烫、包装等各生产环节制定出标准技术文件,才能生产出保质、保量、成本低并满足消费者、客户需求的服装。
确定服装流水线的人数
我们没有流水线人数计算的准确的方法,但流水线的组织也是有原则的,首先我们抛开流水线人数的多少,单单从工作站产能平衡的角度反过来认识流水线,从理论上讲,只有每一个工作站的产能相平衡才能发挥流水线的真正作用.每个工作站的产能要与整个流水线的产能平衡才能真正发挥流水线的作用,从理论上讲,我们取得服装每一个工序标准工时的最小公倍数(近似)来确定流水线的人数是最合理的流水作业人数,但服装的品种数量是时常变换的,职工的熟练程度也自然不均,所以这样的理论是不符合实践的.
服装设备很多是通用设备,我们可以把相临的工序进行合并,分成一系列单元,然后还可以求得单元作业时间的最小公倍数(近似)以次来确定我们的流水线人数,但这同样会面临品种数量变换\职工熟练程度不一的问题.但这已经接近了我们流水线人数的理论测算方法,这里要考虑一个问题,就是我们的分
解与合并的单元,它们的标准作业时间必须一致或成整数倍数(近似).我们的工作单元不可能过大与过小,这个“度”的把握也是没有准确理论作为依据的。
通常我们按下列原则合并工序组织生产单元:
1、流程kao近原则,同一单元的工序尽可能的kao近,以免形成连续生产,避免产生不必要的搬运;
2、难度相近原则,流水线职工水品参差不齐,对于操作水平好的缝纫工,如果让她做简单的产品,是一种人力资源的浪费,同样对于水平差的职工,如果让她做复杂的工序,必然影响后续生产,降低整个流水线的产能;
3、设备相同原则,合并的工序应该是适合同一种设备来生产的工序;
4、颜色相同原则,对于拼色产品还要注意颜色的相同,这样可以避免因为颜色变换引起的换线。
另外一个因素就是,即使同一工人操作同一机台,其产出也是不稳定的,机械故障,操作者状态,上下工序产量与质量的制约等等都可以随时打破流水线的平衡,这也是服装生产不同于机械制造的主要因素.
正是由于服装流水线的这些因素,我们无法从理论上标准计算服装流水线的人数,这就必然存在一个问题,那就是动态平衡流水线的问题,这个动态平衡包括了品种变换的动态平衡与同一品种生产过程中动态平衡的问题流水线的产能计算方法是:
1、工作时间/单元工序时间;
2、[工作时间/产品整体工序时间]*流水线人数
在流水线平衡的状态下,1、2的计算结果是一致的,但通常我们1的计算结果,总是要小于2的计算结果,生产越是不平衡,这个数字的差距就会越大,流水节拍就越是不合,单元也就越是不同步。
我们可以用2的方法来计算流水线产能的最高目标,用1的方法来计算我们现有的产能水平,从而改善我们的流水线。
这种改善自然就是班组长与相关管理者的作用了,从这种意义上讲,流水线人数的合理数值更大程度的取决于流水线管理者的能力与精力。
试想一条40人的流水线,如果产生了不平衡,任凭管理者的能力有多高,也只能是顾此失彼,要想做到动态平衡是很难的。
如果一条流水线仅仅7、8个人,那一般的管理者完全有经理管理这条线,这个时候我们可以让管理者半脱产,当然这主要是由简单工序构成的流水线。
这个人数的把握一定要在实践中摸索才能确定,这不是凭经验而是实践检验,我们的任何理论都是来自实践并受检验于实践。
在长期的实践过程中我提
出15+5(15台车20名员工)的"万能型"流水线组合。
这也是国内外很多企业实际生产中较为合理的设置。
当然对于长期稳定生产单一品种的企业,这个人数可以适当增加的,但减少往往会形成生产混乱,因为这不利于工序的合并(单元划分)。