大型曲轴车铣机床伺服进给系统设计研究
数控机床进给系统的研究与设计

数控机床进给系统的研究与设计一、引言数控机床作为现代制造业的重要设备,具有高精度、高效率、高灵活性和自动化程度高等优点,在工业生产中扮演着重要角色。
而数控机床的进给系统则是实现工件在加工过程中沿坐标轴进行精确定位和控制的核心部件。
因此,研究和设计数控机床进给系统具有重要的理论意义和实际应用价值。
二、数控机床进给系统的结构及工作原理1. 进给系统的结构数控机床进给系统一般由驱动器、传感器、电机、滚珠丝杠等组成。
其中驱动器用于接收并解码来自数控系统的指令,将指令转换为电信号发送给电机,控制电机的运动;传感器用于检测机床加工的实际位置,并反馈给数控系统进行闭环控制。
2. 进给系统的工作原理进给系统的工作原理可分为四个阶段:指令译码、位置测量、电机控制和运动传动。
首先,驱动器将数控系统发出的指令进行译码,确定机床运动的方向和距离。
然后,传感器对机床的位置进行测量,将实际位置信息反馈给数控系统,实现闭环控制。
接下来,电机根据驱动信号进行控制,驱动滚珠丝杠的旋转,实现机床进给运动。
最后,运动传动将电机的旋转运动转换为机床工件的线性运动,完成加工任务。
三、数控机床进给系统的关键技术研究1. 驱动器技术研究驱动器是数控机床进给系统的核心部件,直接影响机床的运动控制精度和稳定性。
目前,常用的驱动器技术包括脉宽调制(PWM)技术、脉冲方向(PD)技术和模数调制(AM)技术。
通过研究驱动器的优化设计和控制策略,提高驱动器的工作性能,能够实现更精确的机床加工控制。
2. 传感器技术研究传感器在数控机床进给系统中的作用是实时测量机床位置和速度,为数控系统提供准确的反馈信息。
目前,常用的传感器技术包括光电编码器、磁性编码器和激光干涉式测长仪等。
通过研究传感器的精度、灵敏度和抗干扰性等性能指标,提高传感器的测量精度和稳定性,能够提高数控机床的加工精度和效率。
3. 电机技术研究电机是数控机床进给系统的驱动装置,直接影响机床的运动速度和力矩输出。
数控铣床Z轴进给系统设计(毕业设计论文)
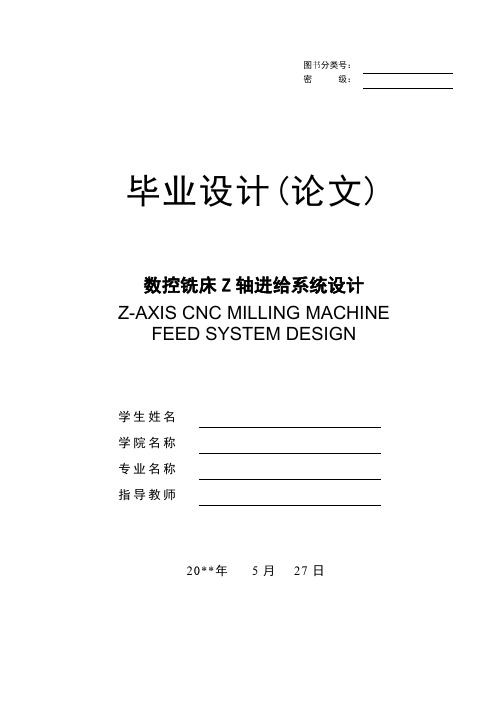
图书分类号:密级:毕业设计(论文)数控铣床Z轴进给系统设计Z-AXIS CNC MILLING MACHINE FEED SYSTEM DESIGN学生姓名学院名称专业名称指导教师20**年5月27日摘要本论文主要研究数控铣床的Z轴进给系统。
数控铣床是数控机床中的典型机床,它对国家的机械行业的发展具有重要的贡献,其加工精度也决定了一个国家的机械行业的发展水平。
其Z轴进给系统主要内容包括进给部件的计算与选用。
进给部件首选滚珠丝杠螺母副,它拥有摩擦损失小、传动效率高、运动平稳、摩擦力小、灵敏度高、低速时无爬行,并且轴向刚度高、反向定位精度高精度稳定性好、磨损小、寿命长、维护简单、传动具有可逆性等特点,对于数控铣床的精确传动提供了保障,使其加工精度精度越来越高。
关键词数控铣床;Z轴进给系统;滚珠丝杠螺母副;AbstractIn this thesis, the Z-axis CNC milling machine feed systems. CNC milling machine is a typical CNC machine tools in the machine bed, its country's machinery industry has an important contribution to the development of its precision also determine a country home level of development of machinery industry. The Z-axis feed system mainly includes the calculation of the feed components with the election use. Feed components preferred ball screw pair, it has friction loss, high transmission efficiency, movement in stability, small friction, high sensitivity, low speed without crawling, and axial stiffness, high precision positioning reverse accuracy, good stability, wear and tear, long life, easy maintenance, transmission characteristics are reversible, the number of controlled milling machine to provide a guarantee for the precise transmission, making it more and more high precision accuracy.Keywords CNC milling machine Z-axis feed system Ball screw pair目录摘要 (I)Abstract (II)1 绪论 (1)1.1 数控铣床 (1)1.1.1 数控铣床的简介 (1)1.1.2数控的加工过程 (1)1.1.3数控铣床的组成 (1)1.1.4 数控铣床的分类 (2)1.1.5 数控铣床的用途和工艺特点 (2)1.2我国的数控产业 (3)1.2.1我国数控产业的现状 (3)1.2.2数控产业发展面临的问题 (3)1.2.3数控产业的发展趋势 (4)1.3数控机床的优点 (4)1.4数控铣床Z轴进给系统的大致整体设计 (6)2 Z轴传动系统的设计 (7)2.1Z轴传动系统的参数设定 (7)2.2数控机床对主传动的要求 (7)2.3数控铣床变速机构形式 (7)2.4主轴的设计 (8)2.4.1主轴材料的选择 (8)2.4.2主轴结构的确定 (8)2.4.3轴的校核计算 (9)2.5齿轮传动的设计计算 (12)2.5.1模数的估算: (13)2.5.2齿轮分度圆直径的计算 (13)2.5.3齿轮宽度B的确定 (14)2.5.4齿轮其他参数的计算 (14)2.5.5齿轮的校核(接触疲劳强度): (14)3 Z轴进给系统总体方案的设计 (15)3.1设计参数 (15)3.2工作原理 (15)3.3总体方案设计 (15)3.3.1 数控系统的选择 (15)3.3.2传动机构的选择 (16)3.3.3联轴器选择 (16)4 主要零部件的计算与选用 (18)4.1Z轴工作载荷分析 (18)4.2 Z轴工作载荷计算 (18)4.3滚珠丝杠螺母副的计算与选用 (18)4.3.1丝杠导程的确定 (18)4.3.2动载荷C计算 (19)4.3.3效率计算 (20)4.3.4滚珠丝杠的精度选择 (20)4.3.5滚珠丝杠的制动 (20)4.4滚珠丝杠螺母副支承的选择 (21)4.5滚珠丝杠螺母副的间隙消除与预紧 (22)4.6轴承的计算与选用 (22)4.6.1轴承初选 (22)4.6.2轴承的计算 (23)4.6.3确定轴承的规格型号 (24)4.7传动系统的刚度计算 (24)4.7.1丝杠拉压刚度KT (24)4.7.2滚珠丝杠螺母副的轴向接触刚度KN (25)4.7.3支承轴承的轴向刚度KH (25)4.7.4丝杠传动的综合拉压刚度K (25)4.8伺服电动机的选择计算 (25)4.8.1确定步进电动机的类型 (25)4.8.2确定脉冲当量 (26)4.8.3最大静态转矩的选择 (26)4.9负载转动惯量的计算 (26)4.9.1工作台折算到丝杠上的转动惯量J (27)J (27)4.9.2丝杠折算到电动机的转动惯量pJ (27)4.9.3传动系统折算到电机轴上的总转动惯量r4.10负载力矩的计算 (27)T (27)4.10.1计算折算到电动机主轴上切削负载力矩CT (27)4.10.2计算折算到电动机上的摩擦负载力矩T (28)4.10.3计算附加负载力矩f4.10.4加速力矩T (28)a4.10.5计算空载时的快进力矩T (28)Kj4.10.6计算切削时的工进力矩T (28)gj4.10.7计算空载启动力矩T (28)q4.10.8确定步进电动机的最大静转矩T (29)s4.11导轨的选择 (29)4.11.1导轨的介绍 (29)4.11.2导轨的参数选取 (30)4.11.3导轨的间隙调整 (31)4.11.4导轨材料与热处理 (32)5主要零件的校核 (33)5.1 滚珠丝杠螺母副的校核 (33)5.1.1 滚珠丝杠螺母副临界转速的校核 (33)5.1.2滚珠丝杠螺母副寿命的校核 (33)结论 (34)致谢 (35)参考文献 (36)谢谢朋友对我文章的赏识,充值后就可以下载此设计说明书(不包含CAD图纸)。
大型数控车床进给伺服系统建模与分析

性和加工1卷第 6期
动 与
冲
击
J OURNAL OF VI BRAT ON I AND HOC S K
大 型数 控 车床 进给 伺 服 系统 建模 与分 析
刘 丽兰 ,刘宏 昭 ,吴子英 ,王建平
( 西安理工大学 机械与精密仪器工程学 院 , 西安 7 04 ) 10 8
摘 要 :针对某大型数控车床的横向进给伺服系统, 建立考虑摩擦和传动刚度的综合力学模型与数学模型。通过
关 键 词 :进 给伺 服 系统 ; 擦 ; 摩 刚度 ; 行 爬
中图 分 类 号 :T 17 T 69 H 1; G5 文献 标 识 码 :A
M o e i n n l ss o e d s r o s se o a g d lng a d a a y i fa f e e v y t m f r a l r e CNC a hi o l m c ne t o
s se s y tm .
Ke y wor : f e e v y tm ;f cin; sif e s;sik—l ds e d s r o s se i r to tfn s tc si p
进给伺服系统作 为数控机床 的核心组成部分 , 是
一
速进 给下导 致 系 统 爬 行 的 原 因 , 进行 现 场 实 验 予 以 并
L U L — n, I Ho g z a I i a L U n —h o, l
X5032铣床进给系统数控毕业设计.

摘要本次毕业设计主要研究了X5032铣床进给系统数控改造,首先是在图书馆和网上查阅了大量的资料,对X5032铣床有了一个大概的了解,记录了相关的数据,也对要改造的部分改造后的尺寸数据有了一个大致的评估。
再是在改造设计的过程中,通过大量的资料,初定了部分参数,然后根据这些参数计算选用滚珠丝杠副和步进电机,而减速机构只进行了简单的设计。
最后在画图时,借助了CAD等软件工具,并且手绘了一张齿轮零件图。
X5032铣床进给系统改造前与改造后差别不是很大,主要改造的部分就是替换滚珠丝杠和步进电机。
滚珠丝杠部分根据动载荷选取,然后再进行校核,包括刚度和压杆稳定性校核;步进电机是根据初步计算的转矩选取,然后在进行转矩校核,解决频率问题。
至于减速齿轮,考虑到步进电机传动的转矩较小,故可以不进行减速齿轮和轴的校核。
通过进行进给系统的数控改造,使我较深入的了解了铣床进给系统的结构,以及数控方面的相关知识,也确实感受到了对普通机床进行数控改造带来的巨大经济效益。
AbstractThe graduation design mainly studies numerical control reform about feeding system of milling machine X5032.At first,I look up a large amount of material from the library and the Internet and it let me jeneral understanding to milling machine X5032. I write down some data of the machine and also take a rough evaluation of the size and data about the part which will be reformed to.At second,I Preliminarily determine some parameters in the reconstruction design process,then choose the ball screw assembly and stepping motor according to these parameters. And the reduction gear institutions made only simple design.At last,I not noly drawing some figure by the software tools such as CAD,but also hand draw a A1 drawings about reduction gear.There is not a very big difference between transformation of the former and after the transformation of the X5032 milling machine feeding system,and the main part of the reform is to replace the ball screw and stepping motor. The selection of ball screw according to the dynamic load, and then check out, including stiffness and push rod stability checking. Stepping motor is according to the torque of preliminary calculation selection, then check the torque and solving the problem about frequency. As for the reduction gear, considering drive torque of stepping motor is small, so checking for the reduction gear and axis is unnecessary.T hrough CNC transform of feeding system, make me a deep understanding of the structure about milling machine feeding system, also the knowledge about numerical control aspects.I indeed feel that numerical control transform to general-purpose machine tool take us great economic benefits.绪论 (5)1.课题目的与意义 (5)2.研究范围与主要解决问题 (7)1.X5032铣床基本介绍 (8)1.1 定义: (8)1.2 应用范围: (8)1.3 X5032立式铣床主要结构特点: (8)1.4 X5032立式铣床主要技术参数: (9)1.5 应用行业: (9)2.铣削力的计算 (10)2.1 改造后的相关参数 (10)F: (10)2.2计算铣削力c3.滚珠丝杠副设计 (11)3.1 概述 (11)3.1.1 简介 (11)3.1.2 滚珠丝杠副的特点及应用 (11)3.1.3 滚珠丝杠副的结构形式 (12)3.1.4 滚珠丝杠副的精度和性能 (13)3.1.5 滚珠丝杠副计算、选用的基本原则 (14)3.2 X向滚珠丝杠副的设计 (14)F的计算: (14)3.2.1 进给牵引力m3.2.2 最大动负载C的计算 (15)3.2.3 选取滚珠丝杠副 (16)3.2.4 滚珠丝杠副压杆稳定性校核 (16)3.2.5 滚珠丝杠副的临界转速校核 (17)3.2.6 滚珠丝杠副的刚度校核 (18)3.3 Y向滚珠丝杠副的设计 (19)3.3.1进给牵引力*mF的计算: (19)3.3.2 最大动负载*C的计算 (20)3.3.3 选取滚珠丝杠副 (21)3.3.4 滚珠丝杠副压杆稳定性校核 (21)3.3.5 滚珠丝杠副的临界转速校核 (22)3.3.6 滚珠丝杠副的刚度校核 (23)4. 齿轮减速器设计 (25)4.1 概述 (25)4.1.1 齿轮传动优缺点 (25)4.1.2 齿轮传动的分类 (25)4.1.3 齿轮失效形式的介绍 (26)4.1.4 齿轮设计准则 (28)4.1.5 齿轮的材料及其选择原则 (29)4.2 齿轮减速器传动比计算 (31)4.2.1 传动比设计的注意事项 (31)4.2.2 X向齿轮减速器传动比计算 (33)4.2.3 Y向齿轮减速器传动比计算 (36)5 步进电机的计算与选择 (38)5.1 概述 (38)5.1.1 步进电机的特点与种类介绍 (38)5.1.2 步进电机的工作原理 (39)5.1.3应用步进电机时应注意的事项: (41)5.2 X向步进电机的计算与选择 (42)5.2.1 初选步进电机 (42)5.2.2 校核步进电机转矩 (43)5.3 Y向步进电机的计算与选择 (48)5.3.1 初选步进电机 (48)5.3.2 校核步进电机转矩 (50)结论 (56)谢辞 (57)绪论1.课题目的与意义制造业是国民经济和国防建设的基础性产业,先进制造技术是振兴传统制造业的技术支撑和发展趋势,而数控技术是先进制造技术的基础技术和共性技术。
数控铣床伺服进给系统的设计计算与验证
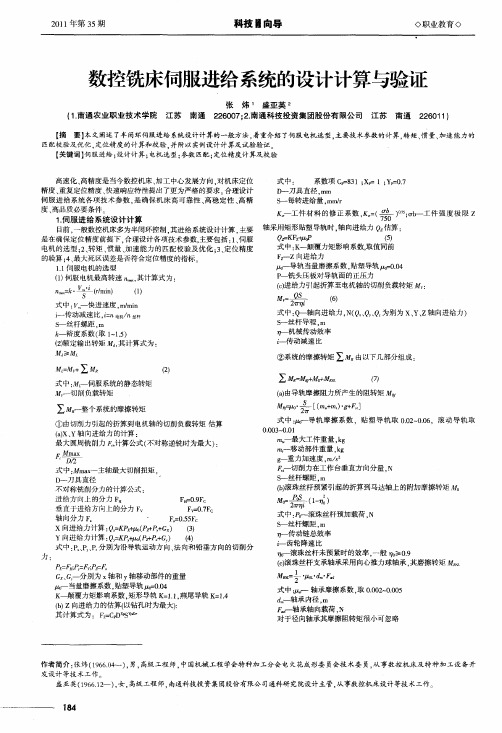
—
M= ・ [时m ‘ c  ̄告 ( g ] p - , )+ o
式 中 : ~导轨 摩擦 系数 ,贴 塑导 轨取 O0 . ,滚动导 轨取 £ . 00 2 6
0.0 ~ 01 0 3 0.
ax
—
D/ 2
式 中: a一主轴最大切 削扭矩 , Mm x D 一刀具直径 不对 称铣 削分力 的计算公式 : 进 给方向上的分力 F H F . 09 F 垂 直于进 给方向上 的分力 F F= . v07 轴 向分力 F ‘ = .5 O5 R x向进给力计算 : : ( + () G) 3 Y向进给力计算 : 产 尸 蛳( 只 G) Q ’ + + ( 4 ) 式中 : … 分别 为沿导轨运动方 向、 P 法向和铅垂方 向的切削分
一
∑M M+ M M L
( 由导轨摩擦阻力所产生的阻转矩 a )
∑肘一 个 统的 擦 矩 整 系 摩 转
① 由切削力 引起 的折算到 电机轴的切削负载转矩 估算 (X、 向进给力的计算 : a Y轴 ) 最大圆周铣 削力 , 计算公式 ( 不对称逆铣时为最大) :
FMm
—
式 中: 一轴 向进给力 , Q y 为别为 x、 z轴 向进给力 ) Q N( …Q Y、 s 一丝杆导程 . i n 竹 一机械传动效率 传动减速 比
—
Mt M f ≥
②系 摩 转 统的 擦 矩∑M 由 下 部 组 R以 几 分 成
式 中: _伺 服系统 的静态转矩 朋f_ 切削负载转矩
高速化、 高精度是 当今数控机床 、 加工中心发展方向 . 对机床定位 精 度、 重复定位精度 、 快速响应特性提出了更 为严格 的要求 。 合理设计 伺 服进 给系统各项技 术参数 , 是确保机 床高可靠 性 、 高稳 定性 、 高精 度、 高品质 必要条件
高速精密数控机床进给伺服系统的控制研究的开题报告

高速精密数控机床进给伺服系统的控制研究的开题报告一、选题背景随着现代工业的发展,高速精密数控机床在工业生产中的应用越来越广泛。
而高速精密数控机床的进给伺服系统作为控制机床各个运动轴的重要组成部分,对机床的稳定性、精度、速度等方面都有着极高的要求。
因此,对高速精密数控机床进给伺服系统的控制研究具有重要意义。
二、研究目标本研究旨在探索高速精密数控机床进给伺服系统的控制方法,解决机床在高速、高精度加工中可能面临的控制难题。
具体目标如下:1. 研究进给伺服系统的控制原理及其应用;2. 探索高速精密数控机床进给伺服系统的控制方法;3. 设计可靠的控制策略,提高机床的加工效率和精度;4. 进行仿真分析,验证控制策略的有效性。
三、研究内容1. 进行高速精密数控机床进给伺服系统的控制原理分析,研究伺服系统的结构、工作原理和主要技术参数等;2. 探索高速精密数控机床进给伺服系统的控制方法,包括传统PID控制、模糊控制、神经网络控制等;3. 设计高速精密数控机床进给伺服系统的可靠控制策略,基于模糊控制和神经网络等方法;4. 利用MATLAB/Simulink等工具进行仿真实验,验证控制策略的有效性;5. 撰写实验报告,总结研究成果。
四、研究意义通过研究高速精密数控机床进给伺服系统的控制方法,不仅可以提高机床的加工效率和精度,还可以减少人工操作的误差,降低企业生产成本。
本研究的成果对于推广智能制造、提高企业竞争力具有重要意义。
五、研究方法本研究将采用文献调查、理论分析、仿真实验等方法,结合实际工作和研究需求,不断深化和完善研究内容和研究方向。
六、研究进度安排1. 第一阶段(1-3周):文献调研,明确研究方向;2. 第二阶段(4-6周):进给伺服系统的控制原理分析;3. 第三阶段(7-9周):高速精密数控机床进给伺服系统的控制方法探索;4. 第四阶段(10-12周):控制策略设计及仿真实验;5. 第五阶段(13-14周):实验数据分析和论文撰写。
大型数控车床进给伺服系统建模与分析(1)
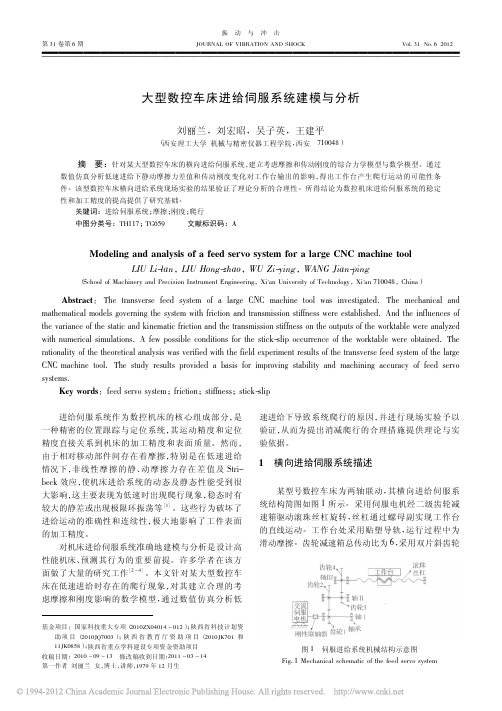
式中: A 为丝杠轴截面面积; E 为杨氏模量; L 为丝杠轴 支撑间的跨距。 由式( 11 ) 可见, 当 a 变化时, 丝杠轴的轴向刚度也 随之变化, 且当 a = L / 2 时 K b 最小。 该进给伺服系统的综合等效传动刚度 K e 可由等 效扭转刚度 K θ 和等效轴向刚度 K l 获得: 1 1 1 = r2 + Ke Kθ Kl ( 12 )
同时, 电机负载转矩 T L 用以驱动工作台轴向运动, 有: T L = rF d = 1 F 2 πη d ( 8)
式中: F d 为工作台直线运动驱动力; r 为转动与移动之 间的转换比; l 为丝杠的导程; η 为传递效率, 取 η = 1。 在电机转矩的驱动下, 丝杠的转动转化为螺母 ( 工 作台) 的轴向移动, 但由于轴向弹性变形二者存在位移 差, 因此工作台的驱动力 F d 为: Fd = Kl ( xs - xt ) ( 9)
式中: J1 为轴 Ⅰ 的转动惯量; J2 为轴 Ⅱ 的转动惯量; J3 为轴Ⅲ的转动惯量; C1 为轴 Ⅰ 的粘性阻尼系数; C2 为 轴Ⅱ的粘性阻尼系数; C3 为轴Ⅲ 的粘性阻尼系数; i1 为 齿轮 1 和齿轮 2 的传动比; i2 为齿轮 3 和齿轮 4 的传动 比。 电机轴与丝杠之间 由 于 扭 转 变 形 产 生 的 角 度 偏 差为: Δθ = θ m - θ s 式中, θ s 为丝杠转角。 电机负载转矩为: T L = k θ ·Δθ K θ 为等效扭转刚度, 式中, 由下式计算。 ( 5) ( 4)
。 本文针对某大型数控车
对其建立合理的考 床在低速进给时存在的爬行现象, 虑摩擦和刚度影响的数学模型, 通过数值仿真分析低
基金项目: 国家科技重大专项 ( 2010ZX04014 - 012 ) ; 陕西省科技计划资 助项 目 ( 2010JQ7003 ) ; 陕 西 省 教 育 厅 资 助 项 目 ( 2010JK701 和 11JK0858 ) ; 陕西省重点学科建设专项资金资助项目 收稿日期: 2010 - 09 - 13 修改稿收到日期: 2011 - 03 - 14 1979 年 12 月生 第一作者 刘丽兰 女, 博士, 讲师,
大型曲轴车铣机床伺服进给系统设计研究

传 动机构 的数 学模 型 , 并运 用传 统 P D 算法对 所 设计 的进 给 系统进 行控 制 计算 , 用 MAT A I 利 L B对
系统 的动态性 能进行仿 真 , 并确 定 了伺服机构 的参 数 , 以此 又 给 出 了避 免 直线 双 驱动 过定 位 的条 并 件, 为大型 曲轴加 工机床进 给 系统的设计 提供 了理论 依据 。 关键 词 : 大型 曲轴 车铣机床 伺 服进给 系统 中 图分 类号 : P 7 T 23 文献标 识码 : A
t e s r o s co s d tr n d h e v e t ri ee mi e .Fi l h t h v i o d to ft e ln a o bl d r e f o ai n i ’ n t a ,t e a od c n iin o h i e rd u e- iv -o lc t s o o
万 吨轮 以上 的超大功 率低速 曲轴) 是一 个 国家  ̄1 H2 综合 制造能 力 的体 现 , 全世 界 只有极 少数 国家 能生产 。 超 大型 曲拐 的加 工 更是 超 大功 率 低速 } 轴 加 工 的 瓶 } } i
颈, 高效 、 高精超 大型 曲拐加工 机床 和 车铣 加工 见 图 1 所 示 。此类 机床 只德 国有 , 机 床 又依 据 车铣 这 一现 该 代加工 方法 设计 而成 。
我 国近几 年引进 了超大 型 曲轴 的精 加 工机 床 ( 图
2 。 目前 我 国 曲 拐还 是 采 用 传 统 普 通 的单 柱 立 车 进 ) 行车 削加工 , 加工 效率 和精度都很 低 , 制超大 型 曲 其 研
拐 加工 的车铣机 床就 显得 十分必要 。 由于单 曲拐的重 量 在 十几 吨 以上 , 加 工过 程 中 且 又 是偏心 安装 , 因而在加 工 中会 产生 很大 的离心力 ; 离
- 1、下载文档前请自行甄别文档内容的完整性,平台不提供额外的编辑、内容补充、找答案等附加服务。
- 2、"仅部分预览"的文档,不可在线预览部分如存在完整性等问题,可反馈申请退款(可完整预览的文档不适用该条件!)。
- 3、如文档侵犯您的权益,请联系客服反馈,我们会尽快为您处理(人工客服工作时间:9:00-18:30)。
大型曲轴车铣机床伺服进给系统设计研究
[摘要]本文运用传统PID算法对所设计的进给系统进行控制计算,利用MATLAB对系统的动态性能进行仿真,并确定了伺服机构的参数,并以此又给出了避免直线双驱动过定位的条件,为大型曲轴加工机床进给系统的设计提供了理论依据。
[关键词]大型曲轴;车铣机床;伺服进给系统
1 双蜗杆无间隙驱动回转工作台结构设计
在加工中,回转工作台要承受较大的切削力、工件偏心造成方向在时刻变化的惯性力、工件的自重和底座滑台的驱动力。
工作台受力平衡方程为:
由公式(1)可知,工作台受力平衡方程式是一个时间函数,这就导致了该机床伺服系统具有特殊性。
由于工件形貌呈椭圆状而且又是偏心装夹,工件在加工过程中会产生周期性变化的离心力。
离心力大小和方向不断变化,导致单蜗杆传动机构产生传动间隙,传动间隙使加工产生一定的空行程,导致较大的切削颤振的发生,对曲拐的加工精度造成较大影响并严重地降低了刀具的寿命,更为严重的是可能会导致切削无法进行。
为了避免上述现象发生,这里采用双蜗杆无间隙驱动机构。
设计的这种大型回转工作台还设置有:蜗杆的轴向力液压伺服平衡机构,双蜗杆的同步驱动机构,启动和刹车时的惯性飞轮机构等。
2 交流伺服双驱动进给系统设计
伺服进给系统包括有:伺服电动机、机械传动装置和执行件、检测和反馈单元、控制单元等,各种元件在这里都是2套。
由于采用双驱动进给,设计中还要重点考虑2个轴的同步转动问题(转动过程中的过定位)及在安装中调整与定位基准等问题。
虽然是采用交流伺服双驱动进给系统,但在设计中还是以研究交流伺服单驱动进给系统为基础,再加入设定的条件,以满足交流伺服双驱动进给系统的驱动要求,解决双驱动的过定位问题。
2.1 交流伺服进给系统数学模型
(1)交流伺服电动机数学模型的建立
伺服进给系统中,驱动电动机采用三相永磁交流同步电动机。
为了使电动机具有较高的控制性能,采用矢量变换进行线性化解耦合的控制方法。
由此,可在dqo坐标系中建立三相永磁同步电动机的电压ud、uq的平衡方程为
3 伺服传动系统特性仿真
3.1 传动系统的时域特性仿真
在仿真时选取电动机为三菱HA-LP系列,MR-J3系列驱动器,具体参数:n max =1200r/min,T max =536N•m,Jm=0.187 0kg•m,减速传动比i=4,工作台自重10t,工件重量20t,转子直径65mm,长度780mm。
运用经典控制理论,取不同的相对阻尼比进行仿真,以此确定适合于本系统的阻尼比。
为了在实际控制中能获取较短的过渡时间,使系统始终处于欠阻尼状态下工作,取ζ在0.4~0.8之间。
本文选择0.6、0.7和0.8三个阻尼比,并用MATLAB进行仿真。
不论系统阻尼的大小其响应时间都是在0.03s之内,超调量不大于20%,说明此时的伺服传动系统无振荡产生。
但随着阻尼比的减小,系统的快速响应性能有所提高,而系统的相对稳定性降低,超调量增大。
为了使系统具有较好的稳定性和快速响应性能,这里选择阻尼比在0.6~0.8范围内。
3.2 传动系统的频域特性仿真
由公式(2)ζω=B/J和ω 2=K/J可知,阻尼比与系统的传动刚度和黏性阻尼系数、等效转动惯量有关。
因此,进给系统应尽可能增大刚度,减小转动惯量,保证系统在稳定基础上具有较好的快速性。
将转动惯量、刚度和阻尼值代入,可得到系统的频域响应。
当对数相频特性 为- H时,对数幅频特性小于0.4dB,所以闭环系统是稳定的。
同时通过MATLAB计算得到系统的幅值裕度和相位裕度都为无穷大,所以该传动系统也是相对稳定的。
4 直线双驱动中的过定位分析
在直线双驱动技术带来了优越性的同时也带来了一个问题,那就是过定位的出现。
假设整个伺服系统稳定,那么仅需要保证两根丝杠在传递过程中的扭转角差值在一个合理的范围内就可以实现双驱动。
在进给系统的结构设计中将支撑导轨的间隙保持在±0.02mm范围内可以解决过定位问题。
这里所选的光电编码器为262.144P/r,即:电动机每转一转发出的脉冲数为262.144,因此电动机每转一度发出的脉冲数约为728.2,因此当a=0.00132 0时,两电动机所发出的脉冲数
相差个数N为:
N=0.00132°×728.2=0.961≈1
即:当两台交流伺服电动机发出的脉冲数相差一个脉冲时,就能避免伺服直线双驱动中过定位的发生。
5 结论
曲拐的高速、高精车铣加工机床的设计不同于传统的机床设计;在主运动系统中,要重点考虑在车铣过程中的减振问题,在大型的盘铣刀上采用8个冲击减振器来消振;在本机床伺服进给系统中的回转工作台的驱动采用了双蜗杆无间隙传动;为了消除时时变化离心力的影响,直线伺服进给采用了双驱动机构;通过对该进给系统的仿真,证明了其数学模型具有良好的可靠性;利用MATLAB对系统
进行动态仿真,得到了系统响应性能曲线,证明系统具有良好的响应性能;通过修改传动系统和PID控制器的参数所得出的仿真结果,验证了本系统有较好的响应特性和稳定特性;通过对直线双驱动的过定位的分析,给出了两台伺服电动机发出脉冲的相差值。