Fuzzy design of process tolerances to maximise process capability
Fuzzy Systems and Control
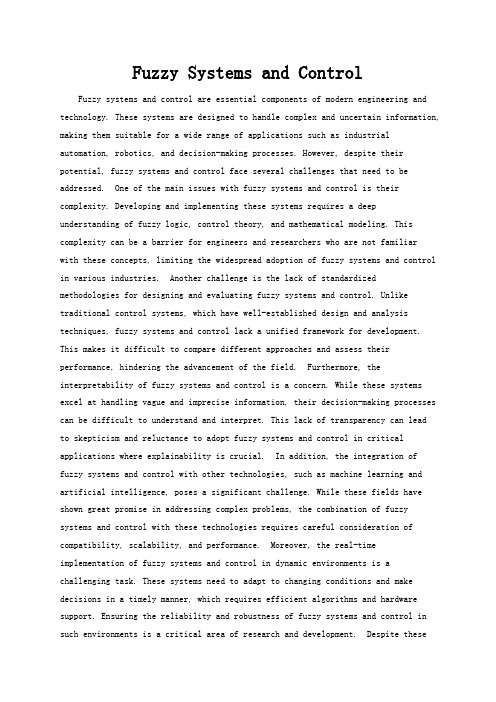
Fuzzy Systems and Control Fuzzy systems and control are essential components of modern engineering and technology. These systems are designed to handle complex and uncertain information, making them suitable for a wide range of applications such as industrial automation, robotics, and decision-making processes. However, despite their potential, fuzzy systems and control face several challenges that need to be addressed. One of the main issues with fuzzy systems and control is their complexity. Developing and implementing these systems requires a deep understanding of fuzzy logic, control theory, and mathematical modeling. This complexity can be a barrier for engineers and researchers who are not familiarwith these concepts, limiting the widespread adoption of fuzzy systems and control in various industries. Another challenge is the lack of standardized methodologies for designing and evaluating fuzzy systems and control. Unlike traditional control systems, which have well-established design and analysis techniques, fuzzy systems and control lack a unified framework for development. This makes it difficult to compare different approaches and assess their performance, hindering the advancement of the field. Furthermore, the interpretability of fuzzy systems and control is a concern. While these systems excel at handling vague and imprecise information, their decision-making processes can be difficult to understand and interpret. This lack of transparency can leadto skepticism and reluctance to adopt fuzzy systems and control in critical applications where explainability is crucial. In addition, the integration of fuzzy systems and control with other technologies, such as machine learning and artificial intelligence, poses a significant challenge. While these fields have shown great promise in addressing complex problems, the combination of fuzzy systems and control with these technologies requires careful consideration of compatibility, scalability, and performance. Moreover, the real-time implementation of fuzzy systems and control in dynamic environments is a challenging task. These systems need to adapt to changing conditions and make decisions in a timely manner, which requires efficient algorithms and hardware support. Ensuring the reliability and robustness of fuzzy systems and control in such environments is a critical area of research and development. Despite thesechallenges, there are ongoing efforts to overcome them and advance the field of fuzzy systems and control. Researchers are working on developing simplified design methodologies and tools to facilitate the implementation of fuzzy systems and control in practical applications. Moreover, there is a growing interest in explainable artificial intelligence, which aims to enhance the interpretability of fuzzy systems and control and address the concerns related to transparency. Furthermore, advancements in hardware technology, such as the emergence of high-performance computing and edge computing, are enabling the real-time implementation of fuzzy systems and control in dynamic environments. These developments are paving the way for the integration of fuzzy systems and control with other emerging technologies, opening up new possibilities for their application in diverse fields. In conclusion, while fuzzy systems and control face several challenges, there are promising developments and research efforts aimed at addressing these issues. By overcoming the complexity, standardizing methodologies, improving interpretability, integrating with other technologies, and enhancing real-time implementation, the potential of fuzzy systems and control can be fully realized, leading to significant advancements in engineering and technology.。
一个平行沟槽轴承与建模质量守恒空穴算法英文翻译
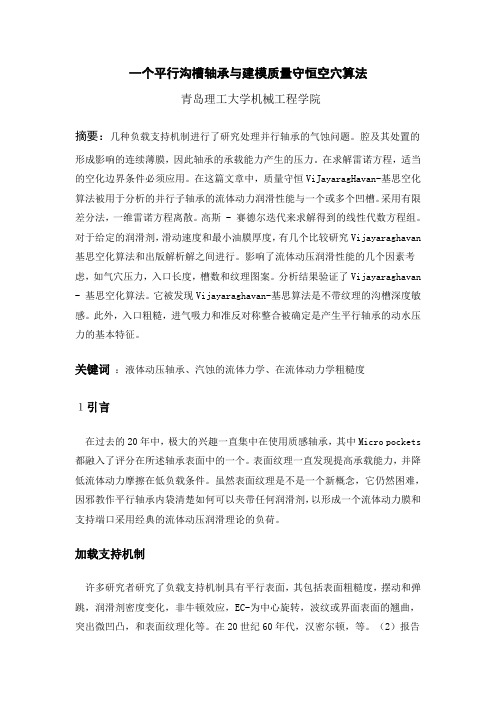
一个平行沟槽轴承与建模质量守恒空穴算法青岛理工大学机械工程学院摘要:几种负载支持机制进行了研究处理并行轴承的气蚀问题。
腔及其处置的形成影响的连续薄膜,因此轴承的承载能力产生的压力。
在求解雷诺方程,适当的空化边界条件必须应用。
在这篇文章中,质量守恒ViJayaragHavan-基思空化算法被用于分析的并行子轴承的流体动力润滑性能与一个或多个凹槽。
采用有限差分法,一维雷诺方程离散。
高斯 - 赛德尔迭代来求解得到的线性代数方程组。
对于给定的润滑剂,滑动速度和最小油膜厚度,有几个比较研究Vijayaraghavan 基思空化算法和出版解析解之间进行。
影响了流体动压润滑性能的几个因素考虑,如气穴压力,入口长度,槽数和纹理图案。
分析结果验证了Vijayaraghavan - 基思空化算法。
它被发现Vijayaraghavan-基思算法是不带纹理的沟槽深度敏感。
此外,入口粗糙,进气吸力和准反对称整合被确定是产生平行轴承的动水压力的基本特征。
关键词:液体动压轴承、汽蚀的流体力学、在流体动力学粗糙度1引言在过去的20年中,极大的兴趣一直集中在使用质感轴承,其中Micro pockets 都融入了评分在所述轴承表面中的一个。
表面纹理一直发现提高承载能力,并降低流体动力摩擦在低负载条件。
虽然表面纹理是不是一个新概念,它仍然困难,因邪教作平行轴承内袋清楚如何可以夹带任何润滑剂,以形成一个流体动力膜和支持端口采用经典的流体动压润滑理论的负荷。
加载支持机制许多研究者研究了负载支持机制具有平行表面,其包括表面粗糙度,摆动和弹跳,润滑剂密度变化,非牛顿效应,EC-为中心旋转,波纹或界面表面的翘曲,突出微凹凸,和表面纹理化等。
在20世纪60年代,汉密尔顿,等。
(2)报告最早工作在微织构,润滑表面。
作者描述的润滑理论基于表面微违规行为和相关薄膜腔。
反对称压力分布这通常会发生这些违规行为被修改由薄膜气蚀,这似乎使得薄膜高压力失去平衡低的膜的压力,从而产生一个净负荷支承通过压力的区域整合力。
毕业设计论文外文文献翻译机械设计制造及其自动化轴承的摩擦与润滑中英文对照

Friction , Lubrication of BearingIn many of the problem thus far , the student has been asked to disregard or neglect friction . A ctually , friction is present to some degree whenever two parts are in contact and move on each other. The term friction refers to the resistance of two or more parts to movement.Friction is harmful or valuable depending upon where it occurs. friction is necessary for fastening devices such as screws and rivets which depend upon friction to hold the fastener and the parts together. Belt drivers, brakes, and tires are additional applications where friction is necessary.The friction of moving parts in a machine is harmful because it reduces the mechanical advantage of the device. The heat produced by friction is lost energy because no work takes place. A lso , greater power is required to overcome the increased friction. Heat is destructive in that it causes expansion. Expansion may cause a bearing or sliding surface to fit tighter. If a great enough pressure builds up because made from low temperature materials may melt.There are three types of friction which must be overcome in moving parts: (1)starting, (2)sliding,and(3)rolling. Starting friction is the friction between two solids that tend to resist movement. When two parts are at a state of rest, the surface irregularities of both parts tend to interlock and form a wedging action. T o produce motion in these parts, the wedge-shaped peaks and valleys of the stationary surfaces must be made to slide out and over each other. The rougher the two surfaces, the greater is starting friction resulting from their movement .Since there is usually no fixed pattern between the peaks and valleys of two mating parts, the irregularities do not interlock once the parts are in motion but slide over each other. The friction of the two surfaces is known as sliding friction. A s shown in figure ,starting friction is always greater than sliding friction .Rolling friction occurs when roller devces are subjected to tremendous stress which cause the parts to change shape or deform. Under these conditions, the material in front of a roller tends to pile up and forces the object to roll slightly uphill. This changing of shape , known as deformation, causes a movement of molecules. As a result ,heat is produced from the added energy required to keep the parts turning and overcome friction.The friction caused by the wedging action of surface irregularities can be overcome partly by the precision machining of the surfaces. However, even these smooth surfaces may require the use of a substance between them to reduce the friction still more. This substance is usually a lubricant which provides a fine, thin oil film. The film keeps the surfaces apart and prevents the cohesive forces of the surfaces from coming in close contact and producing heat .Another way to reduce friction is to use different materials for the bearing surfaces and rotating parts. This explains why bronze bearings, soft alloy s, and copper and tin iolite bearings are used with both soft andhardened steel shaft. The iolite bearing is porous. Thus, when the bearing is dipped in oil, capillary action carries the oil through the spaces of the bearing. This type of bearing carries its own lubricant to the points where the pressures are the greatest.Moving parts are lubricated to reduce friction, wear, and heat. The most commonly used lubricants are oils, greases, and graphite compounds. Each lubricant serves a different purpose. The conditions under which two moving surfaces are to work determine the type of lubricant to be used and the system selected for distributing the lubricant.On slow moving parts with a minimum of pressure, an oil groove is usually sufficient to distribute the required quantity of lubricant to the surfaces moving on each other .A second common method of lubrication is the splash system in which parts moving in a reservoir of lubricant pick up sufficient oil which is then distributed to all moving parts during each cycle. This system is used in the crankcase of lawn-mower engines to lubricate the crankshaft, connecting rod ,and parts of the piston.A lubrication system commonly used in industrial plants is the pressure system. In this system, a pump on a machine carries the lubricant to all of the bearing surfaces at a constant rate and quantity.There are numerous other sy stems of lubrication and a considerable number of lubricants available for any given set of operating conditions. Modern industry pays greater attention to the use of the proper lubricants than at previous time because of the increased speeds, pressures, and operating demands placed on equipment and devices.Although one of the main purposes of lubrication is reduce friction, any substance-liquid , solid , or gaseous-capable of controlling friction and wear between sliding surfaces can be classed as a lubricant.V arieties of lubricationUnlubricated sliding. Metals that have been carefully treated to remove all foreign materials seize and weld to one another when slid together. In the absence of such a high degree of cleanliness, adsorbed gases, water vapor ,oxides, and contaminants reduce frictio9n and the tendency to seize but usually result in severe wear。
超高压食品工艺设计流程
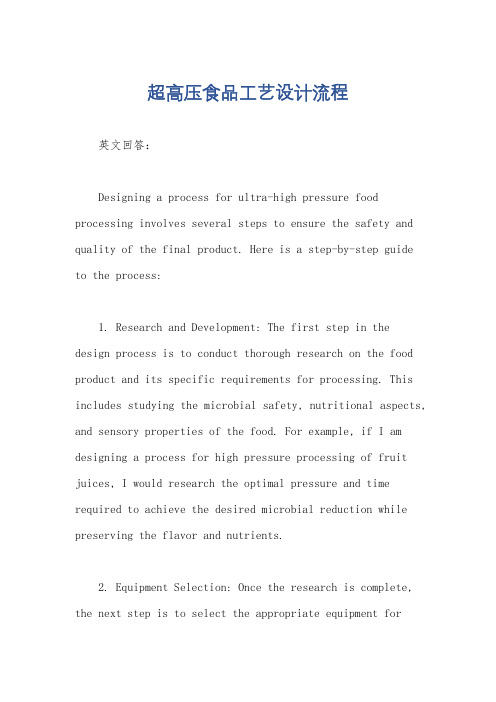
超高压食品工艺设计流程英文回答:Designing a process for ultra-high pressure food processing involves several steps to ensure the safety and quality of the final product. Here is a step-by-step guideto the process:1. Research and Development: The first step in the design process is to conduct thorough research on the food product and its specific requirements for processing. This includes studying the microbial safety, nutritional aspects, and sensory properties of the food. For example, if I am designing a process for high pressure processing of fruit juices, I would research the optimal pressure and time required to achieve the desired microbial reduction while preserving the flavor and nutrients.2. Equipment Selection: Once the research is complete, the next step is to select the appropriate equipment forhigh pressure processing. There are different types of equipment available, such as batch systems and continuous systems. I would consider factors like production capacity, cost, and maintenance requirements before choosing the equipment. For instance, if I am designing a process for high pressure processing of seafood, I might opt for a continuous system that can handle large volumes efficiently.3. Process Design: After selecting the equipment, the next step is to design the process parameters. Thisinvolves determining the pressure and temperature conditions, as well as the processing time required for the food product. It is essential to consider the specific characteristics of the food, such as its composition and structure, to ensure optimal processing. For example, if I am designing a process for high pressure processing of deli meats, I would consider the fat content, texture, and color changes that may occur under high pressure.4. Validation and Optimization: Once the process is designed, it needs to be validated to ensure its effectiveness in achieving the desired objectives. Thisinvolves conducting trials with different parameters and analyzing the results. For instance, I might conduct a series of experiments to determine the optimal pressure and time for high pressure processing of dairy products like yogurt. The results would then be analyzed to optimize the process parameters for maximum microbial reduction and product quality.5. Implementation and Monitoring: After validation and optimization, the designed process is ready for implementation. It is crucial to monitor the process continuously to ensure its consistency and effectiveness. Regular testing of the final product for microbial safety and quality is also necessary. For example, if I am designing a process for high pressure processing of ready-to-eat meals, I would regularly sample the products for microbial testing and sensory evaluation to ensure they meet the desired standards.中文回答:超高压食品工艺的设计流程包括以下几个步骤,以确保最终产品的安全和质量。
中英文翻译(Engineering Tolerance)

英文:Engineering ToleranceIntroductionA solid is defined by its surface boundaries. Designers typically specify a component’s nominal dimensions such that it fulfils its requirements. In reality, components cannot be made repeatedly to nominal dimensions, due to surface irregularities and the intrinsic surface roughness. Some variability in dimensions must be allowed to ensure manufacture is possible. However, the variability permitted must not be so great that the performance of the assembled parts is impaired. The allowed variability on the individual component dimensions is called the tolerance.The term tolerance applies not only to the acceptable range of component dimensions produced by manufacturing techniques, but also to the output of machines or processes. For example , the power produced by a given type of internal combustion engine varies from one engine to another. In practice, the variability is usually found to be modeled by a frequency distribution curve, for example the normal distribution (also called the Gaussian distribution).One of the tasks of the designer is to specify a dimension on a component and the allowable variability on this value that will give acceptable performance.Component TolerancesControl of dimensions is necessary in order to ensure assembly and interchangeability of components. Tolerances are specified on critical dimensions that affect clearances and interferences fits. One method of specifying tolerances is to state the nominal dimension followed by the permissible variation, so a dimension could be stated as 40.000mm ± 0.003mm.This means that the dimension should be machined so that it is between 39.997mm and 40.003mm.Where thevariation can vary either side of the nominal dimension, the tolerance is called a bilateral tolerance. For a unilateral tolerance, one tolerance is zero, e.g. 40+0.006 .0.000Most organizations have general tolerances that apply to dimensions when an explicit dimension is not specified on a drawing. For machined dimensions a general tolerance may be ±0.5mm. So a dimension specified as 15.0mm may range between 14.5mm and 15.5mm. Other general tolerances can be applied to features such as angles, drilled and punched holes, castings,forgings, weld beads and fillets.When specifying a tolerance for a component, reference can be made to previous drawings or general engineering practice. Tolerances are typically specified in bands as defined in British or ISO standards.Standard Fits for Holes and ShaftsA standard engineering ask is to determine tolerances for a cylindrical component, e.g. a shaft, fitting or rotating inside a corresponding cylindrical component or hole. The tightness of fit will depend on the application. For example, a gear located onto a shaft would require a “tight” interference fit, where the diameter of the shaft is actually slightly greater than the inside diameter of the gear hub in order to be able to transmit the desired torque. Alternatively, the diameter of a journal bearing must be greater than the diameter of the shaft to allow rotation. Given that it is not economically possible to manufacture components to exact dimensions, some variability in sizes of both the shaft and hole dimension must be specified. However, the range of variability should not be so large that the operation of the assembly is impaired. Rather than having an infinite variety of tolerance dimensions that could be specified, national and international standards have been produced defining bands of tolerances. To turn this information into actual dimensions corresponding tables exist,defining the tolerance levels for the size of dimension under consideration.Size:a number expressing in a particular unit the numerical value of a dimension.Actual size:the size of a part as obtained by measurement.Limits of size:the maximum and minimum sizes permitted for a feature.Maximum limit of size the greater of the two limits of size.Minimum limit of size:the smaller of the two limits of size.Basic size:the size by reference to which the limits of size are fixed.Deviation:the algebraic difference between a size and the corresponding basic size.Actual deviation:the algebraic difference between the actual size and the corresponding basic size.Upper deviation:the algebraic difference between the maximum limit of size and the corresponding basic size.Lower deviation:the algebraic difference between the minimum limit of size and the corresponding basic size.Tolerance:the difference between the maximum limit of size and the minimum limit of size.Shaft:the term used by convention to designate all external features of a part.Hole:the term used by convention to designate all internal features of a part.Heat Treatment of MetalThe generally accepted definition for heat treating metals and metal alloys is “heating and cooling a solid metal or alloy in a way so as to obtain specific conditions and I or properties.”Heating for the sole purpose of hot working(as in forging operations) is excluded from this definition.Likewise,the types of heat treatment that are sometimes used for products such as glass or plastics are also excluded from coverage by this definition.Transformation CurvesThe basis for heat treatment is the time-temperature-transformation curves or TTT curves where,in a single diagram all the three parameters are plotted.Becauseof the shape of the curves,they are also sometimes called C-curves or S-curves.To plot TTT curves,the particular steel is held at a given temperature and the structure is examined at predetermined intervals to record the amount of transformation taken place.It is known that the eutectoid steel (T80) under equilibrium conditions contains,all austenite above 723℃,whereas below,it is pearlite.To form pearlite,the carbon atoms should diffuse to form cementite.The diffusion being a rate process,would require sufficient time for complete transformation of austenite to pearlite .From different samples,it is possible to note the amount of the transformation taking place at any temperature.These points are then plotted on a graph with time and temperature as the axes.Classification of Heat Treating ProcessesIn some instances,heat treatment procedures are clear cut in terms of technique and application.whereas in other instances,descriptions or simple explanations are insufficient because the same technique frequently may be used to obtain different objectives .For example, stress relieving and tempering are often accomplished with the same equipment and by use of identical time and temperature cycles.The objectives,however,are different for the two processes .The following descriptions of the principal heat treating processes are generally arranged according to their interrelationships.Normalizing consists of heating a ferrous alloy to a suitable temperature (usually 50°F to 100 °F or 28 ℃to 56℃) above its specific upper transformation temperature. This is followed by cooling in still air to at least some temperature well below its transformation temperature range.For low-carbon steels.the resulting structure and properties are the same as those achieved by full annealing ;for most ferrous alloys, normalizing and annealing are not synonymous.Normalizing usually is used as a conditioning treatment, notably for refining the grain of steels that have been subjected to high temperatures for forging or other hot working operations.The normalizing process usually is succeededby another heat treating operation such as austenitizing for hardening, annealing,or tempering.Annealing is a generic term denoting a heat treatment that consists of heating to and holding at a suitable temperature followed by cooling at a suitable rate.It is used primarily to soften metallic materials,but also to simultaneously produce desired changes in other properties or in microstructure.The purpose of such changes may be,but is not confined to, improvement of machinability, facilitation of cold work ( known as in-process annealing),improvement of mechanical or electrical properties, or to increase dimensional stability.When applied solely to relieve stresses, it commonly is called stress-relief annealing, synonymous with stress relieving.When the term “anneali ng is applied to ferrous alloys without qualification, full annealing is implied.This is achieved by heating above the alloy’s transformation temperature,then applying a cooling cycle which provides maximum softness.This cycle may vary widely, depending on composition and characteristics of the specific alloy.Quenching is the rapid cooling of a steel or alloy from the austenitizing temperature by immersing the workpiece in a liquid or gaseous medium.Quenching media commonly used include water,5% brine,5% caustic in an aqueous solution,oil,polymer solutions,or gas(usually air or nitrogen).Selection of a quenching medium depends largely on the hardenability of the material and the mass of the material being treated(principally section thickness).The cooling capabilities ofthe above-listed quenching media vary greatly.In selecting a quenching medium, it is best to avoid a solution that has more cooling power than is needed to achieve the results,thus minimizing the possibility of cracking and warp of the parts being treated.Modifications of the term quenching include direct quenching,fog quenching,hot quenching,interrupted quenching selective quenching,spray quenching, and time quenching.Tempering .In heat treating of ferrous alloys ,tempering consists of reheating the austenitized and quench-hardened steel or iron to some preselected temperature that is below the lower transformation temperature (generally below 1300°F or 705℃) .Tempering offers a means of obtaining various combinations of mechanical properties.Tempering temperatures used for hardened steels are often no higher than 300°F (150℃).The term “tempering”should not be confused with either process annealing or stress relieving.Even though time and temperature cycles for the three processes may be the same,the conditions of the materials being processed and the objectives may be different.Stress Relieving.Like tempering, stress relieving is always done by heating to some temperature below the lower transformation temperature for steels and irons .For nonferrous metals,the temperature may vary from slightly above room temperature to several hundred degrees,depending on the alloy and the amount of stress relief that is desired.The primary purpose of stress relieving is to relieve stresses that have been imparted to the workpiece from such processes as forming, rolling,machining or welding.The usual procedure is to heat workpieces to the pre-established temperature long enough to reduce the residual stresses (this is a time-and temperature-dependent operation) to an acceptable level;this is followed by cooling at a relatively slow rate to avoid creation of new stresses.Introduction to CAD/CAMThroughout the history of our industrial society, many inventions have been patented and whole new technologies have evolved. Perhaps the single development that has impacted manufacturing more quickly and significantly than any previous technology is the digital computer. Computers are being used increasingly for both design and detailing of engineering components in the drawing office.Computer-aided design (CAD) is defined as the application of computers and graphics software to aid or enhance the product design from conceptualizationto documentation. CAD is most commonly associated with the use of an interactive computer graphics system, referred to as a CAD system. Computer-aided design systems are powerful tools and are used in the mechanical design and geometric modeling of products and components.There are several good reasons for using a CAD system to support the engineering design function:⑴To increase the productivity⑵To improve the quality of the design⑶To uniform design standards⑷To create a manufacturing data base⑸To eliminate inaccuracies caused by hand-copying of drawingsand inconsistency between drawingsComputer-aided manufacturing (CAM) is defined as the effective use of computer technology in manufacturing planning and control. CAM is most closely associated with functions in manufacturing engineering, such as process and production planning, machining, scheduling, management, quality control, and numerical control (NC) part programming. Computer-aided design and computer-aided manufacturing are often combined into CAD/CAM systems.This combination allows the transfer of information from the design stage into the stage of planning for the manufacturing of a product, without the need to reenter the data on part geometry manually. The database developed during CAD is stored; then it is processed further, by CAM, into the necessary data and instructions for operating an controlling production machinery, material-handling equipment, and automated testing and inspection for product quality.Rationale for CAD/CAMThe rationale for CAD/CAM is similar to that used to justify any technology-based improvement in manufacturing. It grows out of a need to continually improve productivity, quality and competitiveness. There are also other reasons why a company might make a conversion from manual processes toCAD/CAM:⑴Increased productivity⑵Better quality⑶Better communication⑷Common database with manufacturing⑸Reduced prototype construction costs⑹Faster response to customersCAD/CAM HardwareThe hardware part of a CAD/CAM system consists of the following components:(1) one or more design workstations,(2) digital computer, (3) plotters, printers and other output devices, and (4) storage devices. In addition, the CAD/CAM system would have a communication interface to permit transmission of data to and from other computer systems, thus enabling some of the benefits of computer integration.The workstation is the interface between computer and user in the CAD system. The design of the CAD workstation and its available features have an important influence on the convenience, productivity, and quality of the user’s output. The workstation must include a graphics display terminal and a set of user input devices. CAD/CAM applications require a digital computer with a high-speed control processing unit (CPU). It contains the main memory and logic/arithmetic section for the system. The most widely used secondary storage medium in CAD/CAM is the hard disk, floppy diskette, or a combination of both.Input devices are generally used to transfer information from a human or storage medium to a computer where “CAD functions” are carried out. There are two basic approaches to input an existing drawing:model the object on a drawing or digitize the drawing. The standard output device for CAD/CAM is a CRT display. There are two major types of CRT displays: random-scan-line-drawing displays and raster-scan displays. In addition to CRT, there are also plasma paneldisplays and liquid-crystal displays.CAD/CAM SoftwareSoftware allows the human user to turn a hardware configuration into a powerful design and manufacturing system. CAD/CAM software falls into two broad categories, 2-D and 3-D, based on the number of dimensions visible in the finished geometry. CAD packages that represent objects in two dimensions are called 2-D software. Early systems were limited to 2-D. This was a serious shortcoming because 2-Drepresentations of 3-Dobjects is inherently confusing. Equally problem has been the inability of manufacturing personnel to properly read and interpret complicated 2-D representations of objects. 3-D software permits the parts to be viewed with the three-dimensional planes-height, width, and depth-visible. The trend in CAD/CAM is toward 3-D representation of graphic images. Such representations approximate the actual shape and appearance of the object to be produced; therefore, they are easier to read and understand.Applications of CAD/CAMThe emergence of CAD/CAM has had a major impact on manufacturing, by standardizing product development and by reducing design effort, tryout, and prototype work; it has made possible significantly reduced costs and improved productivity.Numerical ControlNumerical control (NC) is a form of programmable automation in which the processing equipment is controlled by means of numbers,letters,and other symbols.The numbers,letters,and symbols are coded in an appropriate format to define a program of instructions for a particular workpart or job. Theinstructions are provided by either of the two binary coded decimal systems: the Electronic Industries Association (EIA) code, or the American Standard Code for Information Interchange (ASCII). ASCII-coded machine control units will not accept EIA coded instructions and vice versa. Increasingly, however, control units are being made to accept instructions in either code. Automation operation by NC is readily adaptable to the operation of all metalworking machines. Lathes, milling machines, drill presses, boring machines, grinding machines, turret punches, flame or wire-cutting and welding machines, and even pipe benders are available with numerical controls.Basic Components of NCA numerical control system consists of the following three basic components:(1) Program instructions(2) Machine control unit(3) Processing equipmentThe program instructions are the detailed step by step commands that direct the processing equipment In its most common form,the commands refer to positions of a machine tool spindle with respect to the worktable on which the part is fixed.More advanced instructions include selection of spindle speeds,cutting tools,and other functions.The machine control unit (MCU) consists of the electronics and control hardware that reads and interprets the program of instructions and convert it into mechanical actions of the machine tool or other processing equipment .The processing equipment is the component that performs metal process.In the most common example of numerical control ,it is used to perform machining operations. The processing equipment consists of the worktable and spindle as well as the motors and controls needed to drive them.Types of NCThere are two basic types of numerical control systems:point to point and contouring .Point to point control system, also called positioning, are simpler than contouring control system.Its primary purpose is to move a tool or workpiece from one programmed point to another. Usually the machine function,such as a drilling operation,is also activated at each point by command from the NC Program.Point to point systems are suitable for hole machining operations such as drilling, countersinking,counterboring,reaming,boring and tapping. Hole punching machines,spotwelding machines,and assembly machines also use point to point NC systems.Contouring system,also known as the continuous path system,positioning and cutting operations are both along controlled paths but at different velocities.Because the tool cuts as it travels along a prescribed path ,accurate control and synchronization of velocities and movements are important.The contouring system is used on lathes,milling machines,grinders,welding machinery,and machining centers.Movement along the path,or interpolation, occurs incrementally,by one of several basic methods .There are a number of interpolation schemes that have been developed to deal with the various problems that are encountered in generating a smooth continuous path with a contouring type NC system.They include linear interpolation, circular interpolation, helical interpolation, parabolic interpolation and cubic interpolation. In all interpolations,the path controlled is that of the center of rotation of the tool.Compensation for different tools,different diameter tools,or tools wear during machining,can be made in the NC program.Programming for NCA program for numerical control consists of a sequence of directions that causes an NC machine to carry out a certain operation ,machining being the most commonly used process .Programming for NC may be done by aninternal programming department,on the shop floor,or purchased from an outside source.Also,programming may be done manually or with computer assistance.The program contains instructions and commands.Geometric instructions pertain to relative movements between the tool and the workpiece. Processing instructions pertain to spindle speeds,feeds,tools,and so on.Travel instructions pertain to the type of interpolation and slow or rapid movements of the tool or worktable.Switching commands pertain to on/off position for coolant supplies,spindle rotation,direction of spindle rotation tool changes,workpiece feeding,clamping,and so on. The first NC programming language was developed by MIT developmental work on NC programming systems in the late 1950s and called APT(Automatically Programmed Tools).DNC and CNCThe development of numerical control was a significant achievement in batch and job shop manufacturing,from both a technological and a commercial viewpoint.There have been two enhancements and extensions of NC technology,including:(1) Direct numerical control(2) Computer numerical controlDirect numerical control can be defined as a manufacturing system in which a number of machines are controlled by a computer through direct connection and in real time.The tape reader is omitted in DNC,thus relieving the system of its least reliable component.Instead of using the tape reader,the part program is transmitted to the machine tool directly from the computer memory.In principle,one computer can be used to control more than 100 separate machines.(One commercial DNC system during the l970s boasted a control capability of up to 256 machine tools.) The DNC computer is designed to provide instructions to each machine tool on demand .When the machine needs control commands ,they are communicated to it immediately.Since the introduction of DNC ,there have been dramatic advances in computer technology.The physical size and cost of a digital computer has been significantly reduced at the same time that its computational capabilities have been substantially increased.In numerical control,the result of these advances has been that the large hard-wired MCUs of conventional NC have been replaced by control units based on the digital computer.Initially,minicomputers were utilized in the early 1970s .As further miniaturization occurred in computers ,minicomputers were replaced by today’s microcomputers.Computer numerical control is an NC system using dedicated microcomputer as the machine control unit .Because a digital computer is used in both CNC and DNC,it is appropriate to distinguish between the two types of system.There are three principal differences:(1) DNC computers distribute instructional data to,and collect data from, a large number of machines.CNC computers control only one machine,or a small number of machines.(2) DNC computers occupy a location that is typically remote from the machines under their control. CNC computer are located very near their machine tools.(3) DNC software is developed not only to control individual pieces of production equipment, but also to serve as part of a management information system in the manufacturing sector of the firm. CNC software is developed to augment the capabilities of a particular machine tool.中文翻译:工程公差引言固体由其表面边界确定界限。
机械设计名词术语中英文对照表
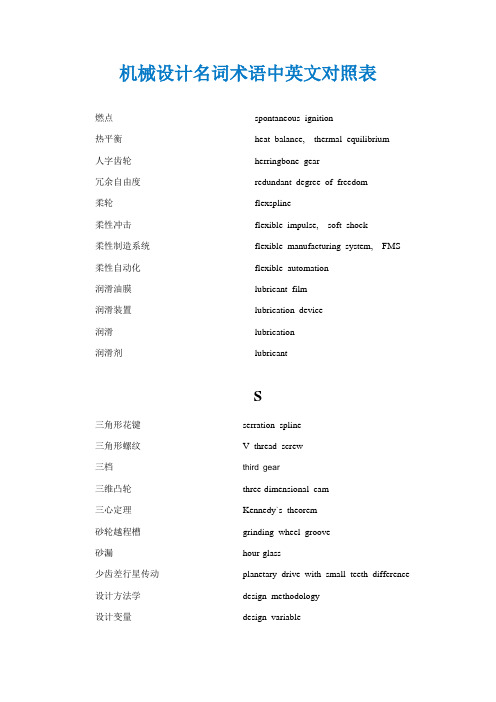
机械设计名词术语中英文对照表燃点spontaneous ignition热平衡heat balance, thermal equilibrium人字齿轮herringbone gear冗余自由度redundant degree of freedom柔轮flexspline柔性冲击flexible impulse, soft shock柔性制造系统flexible manufacturing system, FMS 柔性自动化flexible automation润滑油膜lubricant film润滑装置lubrication device润滑lubrication润滑剂lubricantS三角形花键serration spline三角形螺纹V thread screw三档third gear三维凸轮three-dimensional cam三心定理Kennedy`s theorem砂轮越程槽grinding wheel groove砂漏hour-glass少齿差行星传动planetary drive with small teeth difference 设计方法学design methodology设计变量design variable设计约束design constraints深沟球轴承deep groove ball bearing生产阻力productive resistance升程rise升距lift实际齿数actual number of teeth实际廓线cam profile实际啮合线段长度effective length of line of action十字滑块联轴器double slider coupling, Oldham‘s coupling 矢量vector输出功output work输出构件output link输出机构output mechanism输出力矩output torque输出轴output shaft输入构件input link数学模型mathematic model实际啮合线actual line of action双滑块机构double-slider mechanism, ellipsograph双曲柄机构double crank mechanism双曲面齿轮hyperboloid gear双头螺柱studs双万向联轴节constant-velocity (or double) universal joint 双摇杆机构double rocker mechanism双转块机构Oldham coupling双列轴承double row bearing双向推力轴承double-direction thrust bearing松边slack-side顺时针clockwise瞬心instantaneous center死点dead point四杆机构four-bar linkage速度velocity速度不均匀( 波动) 系数coefficient of speed fluctuation速度波动speed fluctuation速度曲线velocity diagram速度瞬心instantaneous center of velocityT塔轮step pulley踏板pedal台钳、虎钳vice太阳轮sun gear弹簧[刚度]系数spring constant弹性滑动elasticity sliding motion弹性联轴器elastic coupling, flexible coupling弹性套柱销联轴器rubber-cushioned sleeve bearing coupling 套筒sleeve梯形螺纹acme thread form特殊运动链special kinematic chain特性characteristics梯形螺纹;爱克米螺纹acme, acme thread替代机构equivalent mechanism调节modulation, regulation调心滚子轴承self-aligning roller bearing调心球轴承self-aligning ball bearing 调心轴承self-aligning bearing调速speed governing调速电动机adjustable speed motors 调速系统speed control system调压调速variable voltage control 调速器regulator, governor铁磁流体密封ferrofluid seal停车阶段stopping phase停歇dwell同步带synchronous belt同步带传动synchronous belt drive 凸的,凸面体convex凸轮cam凸轮倒置机构inverse cam mechanism 凸轮机构cam , cam mechanism 凸轮廓线cam profile凸轮廓线绘制layout of cam profile凸轮理论廓线pitch curve凸缘联轴器flange coupling图册、图谱atlas图解法graphical method推程rise推力球轴承thrust ball bearing推力轴承thrust bearing退刀槽tool withdrawal groove 退火anneal陀螺仪gyroscopeVV 带V beltW外力external force外圈outer ring外形尺寸boundary dimension万向联轴器Hooks coupling, universal coupling 外齿轮external gear弯曲应力beading stress弯矩bending moment腕部wrist往复移动reciprocating motion往复式密封reciprocating seal网上设计on-net design, OND微动螺旋机构differential screw mechanism位移displacement位移曲线displacement diagram位姿pose , position and orientation稳定运转阶段steady motion period稳健设计robust design蜗杆worm蜗杆传动机构worm gearing蜗杆头数number of threads蜗杆直径系数diametral quotient蜗杆蜗轮机构worm and worm gear蜗杆形凸轮步进机构worm cam interval mechanism蜗杆旋向hands of worm蜗轮worm gear涡圈形盘簧power spring无级变速装置stepless speed changes devices无穷大infiniteX系杆crank arm, planet carrier现场平衡field balancing向心轴承radial bearing向心力centrifugal force相对速度relative velocity相对运动relative motion相对间隙relative gap象限quadrant橡皮泥plasticine细牙螺纹fine threads销pin消耗consumption小齿轮pinion小径minor diameter橡胶弹簧balata spring修正梯形加速度运动规律modified trapezoidal acceleration motion修正正弦加速度运动规律modified sine acceleration motion斜齿圆柱齿轮helical gear斜键、钩头楔键taper key泄漏leakage谐波齿轮harmonic gear谐波传动harmonic driving谐波发生器harmonic generator斜齿轮的当量直齿轮equivalent spur gear of the helical gear 心轴spindle行程速度变化系数coefficient of travel speed variation行程速比系数advance-to return-time ratio行星齿轮装置planetary transmission行星轮planet gear行星轮变速装置planetary speed changing devices行星轮系planetary gear train形封闭凸轮机构positive-drive (or form-closed) cam mechanism虚拟现实virtual reality虚拟现实技术virtual reality technology, VRT虚拟现实设计virtual reality design, VRD虚约束redundant (or passive) constraint许用不平衡量allowable amount of unbalance许用压力角allowable pressure angle许用应力allowable stress, permissible stress悬臂结构cantilever structure悬臂梁cantilever beam循环功率流circulating power load旋转力矩running torque旋转式密封rotating seal旋转运动rotary motion选型type selectionY压力pressure压力中心center of pressure压缩机compressor压应力compressive stress压力角pressure angle牙嵌式联轴器jaw (teeth) positive-contact coupling 雅可比矩阵Jacobi matrix摇杆rocker液力传动hydrodynamic drive液力耦合器hydraulic couplers液体弹簧liquid spring液压无级变速hydraulic stepless speed changes液压机构hydraulic mechanism一般化运动链generalized kinematic chain移动从动件reciprocating follower移动副prismatic pair, sliding pair移动关节prismatic joint移动凸轮wedge cam盈亏功increment or decrement work应力幅stress amplitude应力集中stress concentration应力集中系数factor of stress concentration应力图stress diagram应力—应变图stress-strain diagram优化设计optimal design油杯oil bottle油壶oil can油沟密封oily ditch seal有害阻力useless resistance有益阻力useful resistance有效拉力effective tension有效圆周力effective circle force有害阻力detrimental resistance余弦加速度运动cosine acceleration (or simple harmonic) motion 预紧力preload原动机primer mover圆带round belt圆带传动round belt drive圆弧齿厚circular thickness圆弧圆柱蜗杆hollow flank worm圆角半径fillet radius圆盘摩擦离合器disc friction clutch圆盘制动器disc brake原动机prime mover原始机构original mechanism圆形齿轮circular gear圆柱滚子cylindrical roller圆柱滚子轴承cylindrical roller bearing圆柱副cylindric pair圆柱式凸轮步进运动机构barrel (cylindric) cam圆柱螺旋拉伸弹簧cylindroid helical-coil extension spring圆柱螺旋扭转弹簧cylindroid helical-coil torsion spring圆柱螺旋压缩弹簧cylindroid helical-coil compression spring 圆柱凸轮cylindrical cam圆柱蜗杆cylindrical worm圆柱坐标操作器cylindrical coordinate manipulator圆锥螺旋扭转弹簧conoid helical-coil compression spring圆锥滚子tapered roller圆锥滚子轴承tapered roller bearing圆锥齿轮机构bevel gears圆锥角cone angle原动件driving link约束constraint约束条件constraint condition约束反力constraining force跃度jerk跃度曲线jerk diagram运动倒置kinematic inversion运动方案设计kinematic precept design运动分析kinematic analysis运动副kinematic pair运动构件moving link运动简图kinematic sketch运动链kinematic chain运动失真undercutting运动设计kinematic design运动周期cycle of motion运动综合kinematic synthesis运转不均匀系数coefficient of velocity fluctuation 运动粘度kenematic viscosityZ载荷load载荷—变形曲线load—deformation curve载荷—变形图load—deformation diagram窄V 带narrow V belt毡圈密封felt ring seal展成法generating张紧力tension张紧轮tension pulley振动vibration振动力矩shaking couple振动频率frequency of vibration振幅amplitude of vibration正常齿高制system of normal addendum正公差positive allowrance正切机构tangent mechanism正向运动学direct (forward) kinematics正弦机构sine generator, scotch yoke织布机loom正应力、法向应力normal stress制动器brake直齿圆柱齿轮spur gear直齿锥齿轮straight bevel gear直角三角形right triangle直角坐标操作器Cartesian coordinate manipulator 直径系数diametral quotient直径系列diameter series直廓环面蜗杆hindley worm直线运动linear motion直轴straight shaft质量mass质心center of mass执行构件executive link, working link质径积mass-radius product智能化设计intelligent design, ID中间平面mid-plane中心距center distance中心距变动center distance change中心轮central gear中径mean diameter终止啮合点final contact, end of contact周节pitch周期性速度波动periodic speed fluctuation周转轮系epicyclic gear train肘形机构toggle mechanism轴shaft轴承盖bearing cup轴承合金bearing alloy轴承座bearing block轴承高度bearing height轴承宽度bearing width轴承内径bearing bore diameter轴承寿命bearing life轴承套圈bearing ring轴承外径bearing outside diameter轴颈journal轴瓦、轴承衬bearing bush轴端挡圈shaft end ring轴环shaft collar轴肩shaft shoulder轴角shaft angle轴向axial direction轴向齿廓axial tooth profile轴向当量动载荷dynamic equivalent axial load 轴向当量静载荷static equivalent axial load轴向基本额定动载荷basic dynamic axial load rating 轴向基本额定静载荷basic static axial load rating轴向接触轴承axial contact bearing轴向平面axial plane轴向游隙axial internal clearance轴向载荷axial load轴向载荷系数axial load factor轴向分力axial thrust load主动件driving link主动齿轮driving gear主动带轮driving pulley转动导杆机构whitworth mechanism转动副revolute (turning) pair转速swiveling speed, rotating speed转动关节revolute joint转轴revolving shaft转子rotor转子平衡balance of rotor装配条件assembly condition锥齿轮bevel gear锥顶common apex of cone锥距cone distance锥轮bevel pulley, bevel wheel锥齿轮的当量直齿轮equivalent spur gear of the bevel gear 锥面包络圆柱蜗杆milled helicoids worm准双曲面齿轮hypoid gear子程序subroutine子机构sub-mechanism自动化automation自锁self-locking自锁条件condition of self-locking自由度degree of freedom, mobility总重合度total contact ratio总反力resultant force总效率combined efficiency, overall efficiency 组成原理theory of constitution组合齿形composite tooth form组合安装stack mounting组合机构combined mechanism阻抗力resistance最大盈亏功maximum difference work between plus and minus work 纵向重合度overlap contact ratio纵坐标ordinate组合机构combined mechanism最少齿数minimum teeth number最小向径minimum radius作用点application point;action spot ;application point ;point of ac tion ;working point作用力applied force坐标系coordinate frameG杆组Assur group干涉interference刚度stiffiness; rigidity; severity; toughness刚度系数stiffness coefficient刚轮rigid circular spline钢丝软轴wire soft shaft刚体导引机构body guidance mechanism刚性冲击rigid impulse (shock)刚性转子rigid rotor刚性轴承rigid bearing刚性联轴器rigid coupling高度系列height series高速带high speed belt高副higher pair格拉晓夫定理Grashoff`s law根切undercutting公称直径nominal diameter高度系列height series高速档 a higher gear,top gear功work工况系数application factor工艺设计technological design工作循环图working cycle diagram工作机构operation mechanism工作载荷external loads工作空间working space工作应力working stress工作阻力effective resistance工作阻力矩effective resistance moment 公法线common normal line公共约束general constraint公制齿轮metric gears功率power功能分析设计function analyses design共轭齿廓conjugate profiles共轭凸轮conjugate cam构件link鼓风机blower固定构件fixed link, frame固体润滑剂solid lubricant关节型操作器jointed manipulator惯性力inertia force惯性力矩moment of inertia ,shaking moment 惯性力平衡balance of shaking force惯性力完全平衡full balance of shaking force惯性力部分平衡partial balance of shaking force惯性主矩resultant moment of inertia惯性主失resultant vector of inertia冠轮crown gear广义机构generation mechanism广义坐标generalized coordinate轨迹生成path generation轨迹发生器path generator滚刀hob滚道raceway滚动体rolling element滚动轴承rolling bearing滚动轴承代号rolling bearing identification code 滚针needle roller滚针轴承needle roller bearing滚子roller滚子轴承roller bearing滚子半径radius of roller滚子从动件roller follower滚子链roller chain滚子链联轴器double roller chain coupling滚珠丝杆ball screw滚柱式单向超越离合器roller clutch过度切割undercuttingH函数发生器function generator函数生成function generation含油轴承oil bearing耗油量oil consumption耗油量系数oil consumption factor赫兹公式H. Hertz equation合成弯矩resultant bending moment 合力resultant force合力矩resultant moment of force 黑箱black box横坐标abscissa互换性齿轮interchangeable gears花键spline滑键、导键feather key滑动轴承sliding bearing滑动率sliding ratio滑块slider环面蜗杆toroid helicoids worm环形弹簧annular spring缓冲装置shocks, shock-absorber 灰铸铁grey cast iron回程return回转体平衡balance of rotors混合轮系compound gear trainJ积分integrate机电一体化系统设计mechanical-electrical integration system design 机构mechanism机构分析analysis of mechanism机构平衡balance of mechanism机构学mechanism机构运动设计kinematic design of mechanism机构运动简图kinematic sketch of mechanism机构综合synthesis of mechanism机构组成constitution of mechanism机架frame, fixed link机架变换kinematic inversion机器machine机器人robot机器人操作器manipulator机器人学robotics机械machinery机械创新设计mechanical creation design, MCD机械系统设计mechanical system design, MSD机械动力分析dynamic analysis of machinery机械动力设计dynamic design of machinery机械动力学dynamics of machinery机械的现代设计modern machine design机械系统mechanical system机械利益mechanical advantage机械平衡balance of machinery机械手manipulator机械设计machine design, mechanical design 机械特性mechanical behavior机械调速mechanical speed governors机械效率mechanical efficiency机械原理theory of machines and mechanisms 机械运转不均匀系数coefficient of speed fluctuation机械无级变速mechanical stepless speed changes 基础机构fundamental mechanism基本额定寿命basic rating life基于实例设计case-based design,CBD基圆base circle基圆半径radius of base circle基圆齿距base pitch基圆压力角pressure angle of base circle基圆柱base cylinder基圆锥base cone急回机构quick-return mechanism急回特性quick-return characteristics急回系数advance-to return-time ratio急回运动quick-return motion技术过程technique process技术经济评价technical and economic evaluation 技术系统technique system棘爪pawl极限啮合点limit of action极位夹角crank angle between extreme (or limiting) positions 极限位置extreme (or limiting) position计算机辅助设计computer aided design, CAD计算机辅助制造computer aided manufacturing, CAM计算机集成制造系统computer integrated manufacturing system, CIMS计算力矩factored moment, calculation moment计算弯矩calculated bending moment加权系数weighting efficient加速度acceleration加速度分析acceleration analysis加速度曲线acceleration diagram尖点pointing, cusp尖底从动件knife-edge follower间隙backlash间歇运动机构intermittent motion mechanism减速比reduction ratio减速齿轮、减速装置reduction gear减速器speed reducer减摩性anti-friction quality渐开螺旋面involute helicoid渐开线involute渐开线齿廓involute profile渐开线齿轮involute gear渐开线发生线generating line of involute渐开线方程involute equation渐开线函数involute function渐开线蜗杆involute worm渐开线压力角pressure angle of involute渐开线花键involute spline简谐运动simple harmonic motion键key键槽keyway检修门Access door交变应力repeated stress交变载荷repeated fluctuating load交叉带传动cross-belt drive交错轴斜齿轮crossed helical gears胶合scoring角加速度angular acceleration角速度angular velocity角速比angular velocity ratio角接触球轴承angular contact ball bearing 角接触推力轴承angular contact thrust bearing 角接触向心轴承angular contact radial bearing 角接触轴承angular contact bearing铰链、枢纽hinge校正平面correcting plane接触应力contact stress接触式密封contact seal阶梯轴multi-diameter shaft结构structure结构设计structural design截面section节点pitch point节距circular pitch, pitch of teeth节线pitch line节圆pitch circle节圆齿厚thickness on pitch circle节圆直径pitch diameter节圆锥pitch cone节圆锥角pitch cone angle解析设计analytical design紧边tight-side紧固件fastener精加工余量allowance for finish精密度accuracy径节diametral pitch径向radial direction径向当量动载荷dynamic equivalent radial load 径向当量静载荷static equivalent radial load径向基本额定动载荷basic dynamic radial load rating 径向基本额定静载荷basic static radial load tating径向接触轴承radial contact bearing径向平面radial plane径向游隙radial internal clearance径向载荷radial load径向载荷系数radial load factor径向间隙clearance静力static force静密封static seal静平衡static balance静载荷static load局部自由度passive degree of freedom矩阵matrix矩形螺纹square threaded form锯齿形螺纹buttress thread form矩形牙嵌式离合器square-jaw positive-contact clutch 绝对尺寸系数absolute dimensional factor绝对运动absolute motion绝对速度absolute velocity均衡装置load balancing mechanismK抗压强度compression strength 开口传动open-belt drive开式链open kinematic chain 开链机构open chain mechanism 可靠度degree of reliability可靠性reliability可靠性设计reliability design, RD 空气弹簧air spring空间机构spatial mechanism空间连杆机构spatial linkage空间凸轮机构spatial cam空间运动副spatial kinematic pair 空间运动链spatial kinematic chain空转idle宽度系列width series框图block diagramL雷诺方程Reynolds‘s equation离心力centrifugal force离心应力centrifugal stress离合器clutch离心密封centrifugal seal理论廓线pitch curve理论啮合线theoretical line of action隶属度membership力force力多边形force polygon力封闭型凸轮机构force-drive (or force-closed) cam mechanism力平衡equilibrium力偶couple力偶矩moment of couple连杆connecting rod, coupler连杆机构linkage连杆曲线coupler-curve连心线line of centers链chain链传动装置chain gearing链轮sprocket, sprocket-wheel, sprocket gear, chain wheel 联组V 带tight-up V belt联轴器coupling, shaft coupling两维凸轮two-dimensional cam邻角adjacent angle临界转速critical speed六杆机构six-bar linkage龙门刨床double Haas planer轮坯blank轮系gear train螺杆screw螺距thread pitch螺母screw nut螺旋锥齿轮helical bevel gear螺钉screws螺栓bolts螺纹导程lead螺纹效率screw efficiency螺旋传动power screw螺旋密封spiral seal螺纹thread (of a screw)螺旋副helical pair螺旋机构screw mechanism螺旋角helix angle螺旋线helix ,helical line绿色设计green design, design for environmentM马耳他机构Geneva wheel, Geneva gear马耳他十字Maltese cross脉动无级变速pulsating stepless speed changes脉动循环应力fluctuating circulating stress脉动载荷fluctuating load美国齿轮制造业协会AGMA (American Gear Manufacturers Association)铆钉rivet迷宫密封labyrinth seal密封seal密封带seal belt密封胶seal gum密封元件potted component密封装置sealing arrangement面对面安装face-to-face arrangement面向产品生命周期设计 design for product`s life cycle, DPLC名义应力、公称应力nominal stress模块化设计modular design, MD模块式传动系统modular system模幅箱morphology box模糊集fuzzy set模糊评价fuzzy evaluation模数module摩擦friction摩擦角friction angle摩擦力friction force摩擦学设计tribology design, TD摩擦阻力frictional resistance摩擦力矩friction moment摩擦系数coefficient of friction摩擦圆friction circle磨料磨损abrasive wear磨蚀剂abrasive磨损abrasion, wear, scratching, abrade末端执行器end-effector目标函数objective functionN耐腐蚀性corrosion resistance耐磨性wear resistance挠性机构mechanism with flexible elements挠性转子flexible rotor内齿轮internal gear内齿圈ring gear内力internal force内圈inner ring能量energy能量指示图viscosity逆时针counterclockwise (or anticlockwise)粘附adhere啮出engaging-out啮合engagement, mesh, gearing, action啮合点contact points啮合轨迹path of action啮合弧arc of action啮合角working pressure angle, angle of action 啮合曲面surface of action啮合区域zone of action啮合线line of action啮合线长度length of line of action啮入engaging-in牛头刨床shaper凝固点freezing point, solidifying point 扭转应力torsion stress扭矩moment of torque扭簧helical torsion spring诺模图NomogramOO 形密封圈密封O ring sealP盘形凸轮disk cam盘形转子disk-like rotor抛物线运动parabolic motion疲劳极限fatigue limit疲劳强度fatigue strength偏置式offset偏( 心) 距offset distance偏心率eccentricity ratio偏心质量eccentric mass偏距圆offset circle偏心盘eccentric偏置滚子从动件offset roller follower偏置尖底从动件offset knife-edge follower偏置曲柄滑块机构offset slider-crank mechanism 拼接matching评价与决策evaluation and decision频率frequency平带flat belt平带传动flat belt driving平底从动件flat-face follower平底宽度face width平分线bisector平均应力average stress平均中径mean screw diameter平均速度average velocity平衡balance平衡机balancing machine平衡品质balancing quality平衡平面correcting plane平衡质量balancing mass平衡重counterweight平衡转速balancing speed平面副planar pair, flat pair平面机构planar mechanism平面运动副planar kinematic pair平面连杆机构planar linkage平面凸轮planar cam平面凸轮机构planar cam mechanism平面轴斜齿轮parallel helical gears普通平键parallel keyQ其他常用机构other mechanism in common use起动阶段starting period启动力矩starting torque气动机构pneumatic mechanism奇异位置singular position起始啮合点initial contact , beginning of contact气体轴承gas bearing千斤顶jack嵌入键sunk key强迫振动forced vibration切齿深度depth of cut切削精度cutting accuracy曲柄crank曲柄存在条件Grashoff`s law曲柄导杆机构crank shaper (guide-bar) mechanism曲柄滑块机构slider-crank (or crank-slider) mechanism 曲柄摇杆机构crank-rocker mechanism曲齿锥齿轮spiral bevel gear曲率curvature曲率半径radius of curvature曲面从动件curved-shoe follower曲线拼接curve matching曲线运动curvilinear motion曲轴crank shaft驱动力driving force驱动力矩driving moment (torque)全齿高whole depth权重集weight sets球ball球面滚子convex roller球轴承ball bearing球面副spheric pair球面渐开线spherical involute球面运动spherical motion球销副sphere-pin pair球坐标操作器polar coordinate manipulator。
Fuzzy constraint networks for process control

Figure 1: Constraint network for temperature conversion problem
100 and 273 are given for the objects F and K, respectively. Then, the system can infer that these values are not consistent, because the two constraints cannot be satis ed simultaneously. A generic fuzzy constraint associated with a set of objects is a fuzzy set, and it is interpreted as the joint possibility distribution for the objects involved in the constraint. Stated in more general terms, a fuzzy constraint network and its intent may be de ned as follows. De nition 1.1 (fuzzy constraint network): A fuzzy constraint network is a triple (U ; X; C) where U is a universe of discourse, X is a tuple of n nonrecurring objects X1 ; : : :; Xn, and C is a set of constraints C1 (T1 ), : : :, Cm (Tm ). In a constraint Cj (Tj ), Tj is a subtuple of X, of arity aj , and Cj (Tj ) is a (possibly fuzzy) subset of the Cartesian product U a . De nition 1.2 (intent): The intent of a fuzzy constraint network (U ; X; C), written U ;X;C , is an n-ary possibility distribution for the objects involved in the network. That is U ;X;C = C 1 (T1 ) \ : : : \ C m (Tm ) where, for each constraint Cj (Tj ) 2 C, C j (Tj ) is its cylindrical extension in the space X = (X1 ; : : :; Xn ). Here, the network intent is a fuzzy set of n-tuples, each tuple giving a valuation for the n objects in X. The membership of the tuple in the intent is the degree to which the valuation satis es all the constraints in C. A fuzzy network is consistent i the network intent is not the empty set. De nition 1.3 (domain): In a fuzzy constraint network (U ; X; C), the domain of any object Xi 2 X, which is denoted Di , is the set of support1 of the intersection of all the unary fuzzy constraints in C that reference Xi . A unary fuzzy constraint is one which refers to only one object in the network.
IEC61400-1-2005风电机组设计要求标准英汉对照

需要什么文档直接在我的文档里搜索比直接在网站大海捞针要容易的多也准确省时的多
INTERNATIONAL STANrbines – Part 1:
Design requirements
Publication numbering As from 1 January 1997 all IEC publications are issued with a designation in the 60000 series. For example, IEC 34-1 is now referred to as IEC 60034-1.
Further information on IEC publications The technical content of IEC publications is kept under constant review by the IEC, thus ensuring that the content reflects current technology. Information relating to this publication, including its validity, is available in the IEC Catalogue of publications (see below) in addition to new editions, amendments and corrigenda. Information on the subjects under consideration and work in progress undertaken by the technical committee which has prepared this publication, as well as the list of publications issued,is also available from the following: IEC Web Site (www.iec.ch) Catalogue of IEC publications The on-line catalogue on the IEC web site (www.iec.ch/searchpub) enables you to search by a variety of criteria including text searches,technical committees and date of publication. Online information is also available on recently issued publications, withdrawn and replaced publications, as well as corrigenda. IEC Just Published This summary of recently issued publications (www.iec.ch/online_news/justpub) is also available by email. Please contact the Customer Service Centre (see below) for further information. Customer Service Centre If you have any questions regarding this publication or need further assistance, please contact the Customer Service Centre: Email: custserv@iec.ch Tel: +41 22 919 02 11 Fax: +41 22 919 03 00 .
- 1、下载文档前请自行甄别文档内容的完整性,平台不提供额外的编辑、内容补充、找答案等附加服务。
- 2、"仅部分预览"的文档,不可在线预览部分如存在完整性等问题,可反馈申请退款(可完整预览的文档不适用该条件!)。
- 3、如文档侵犯您的权益,请联系客服反馈,我们会尽快为您处理(人工客服工作时间:9:00-18:30)。
Int J Adv Manuf Technol(1999)15:655–659©1999Springer-Verlag LondonLimitedFuzzy Design of Process Tolerances to Maximise Process CapabilityYeong-Hoang Lee1,Chiu-Chi Wei2and Ching-Liang Chang11Department of Industrial Engineering and Management,Ta-Hwa Institute of Technology,Hsin-Chu,Taiwan;and2Department of Industrial Engineering and Management,Chung-Hua University,Hsin-Chu,TaiwanA novel formulation for designing process tolerances to maxi-mise the process capability index is presented in this study. The proposed model simultaneously optimises the process capa-bility of each operation,and is consolidated into a single objective fuzzy programming.A step fuzzy membership function is employed to represent the lower and upper bounds of the process capability index,the problem is then solved byfinding the maximum value of the fuzzy number.This study is believed to be thefirst attempt to design process tolerance with the maximisation of process capability index.A comparison of the results shows that the fuzzy model is suitable for assigning tolerances to an existing process.Keywords:Fuzzy method;Process capability;Process toler-ance1.IntroductionTolerance is the allowable variation attached to a nominal dimension so that the product will still perform satisfactorily. Two types of tolerance are used in manufacturing,they are the product tolerance and the process tolerance.Product tolerance is designed by the R&D engineers in such a way that the product’s functional requirements are achieved as expected. Product tolerances together with dimensions are usually called the product specification.Process tolerances are allocated by the process planners,based on the manufacturing characteristics and requirements of each operation.The accumulated variation of all operations should be less than,or equal to,the product tolerance.This study limits the discussion to the process toler-ance,hence tolerance here refers to process tolerance. Conventionally,process tolerance is determined on the basis of an individual’s experience and expertise.As a result,the quality of the process varies significantly with different oper-ators.Therefore,a systematic approach should be developed Correspondence and offprint requests to:Dr C.-C.Wei,Department of Industrial Management,Chung-Hua University,30Tung Shiang,Hsin-chu,Taiwan.E-mail:ccweiȰ.tw to optimise objectively the process tolerance.Tolerance chart balancing[1]is the earliest method developed to help design the process tolerance;however,the need for extensive manufac-turing experience and tedious computation are two of the drawbacks.Several researchers later proposed different math-ematical formulations such as linear[2–5]and nonlinear pro-gramming[6–12]where most of the objective functions are manufacturing costs.Process tolerance can also be decided at the process selection stage,then an optimal process sequence and process tolerance can be concurrently achieved[7,9,10]. Ngoi[2]and Ngoi and Fang[3]used applied linear program-ming to minimise the total process tolerances,and a weighting additive function was used to measure the suitability of the process tolerance.Nagarwala et al.[6]developed a piecewise linear approximation approach to solve the tolerance-process selection problem by minimising the manufacturing cost.Zhang and Wang[7,9]established an analytical cost model for optimal process sequence selection through planning intermediate pro-cess tolerances.Yeo et al.[10]constructed a cost–tolerance function as a natural spline model,and introduced a method-ology to optimise the process sequence using an expert system. Cheng and Maghsoodloo[11]combined the cost–tolerance relationship with a quality loss function to optimise assembly tolerance.Wei and Lee[5]proposed a linear programming model which takes into account the standard deviation of the machine performing the operation,this permits the process capability of the machinery to be represented in a more precise way.Wei[12]developed a nonlinear formulation which can design process tolerance to minimise the loss of defective parts,this enables the process planners to predict the production loss at the planning stage.To move one step forward,this article proposes a fuzzy formulation which can design process tolerances to maximise the process capability index of each operation.2.Problem FormulationProcess tolerance was often designed to minimise the manufac-turing cost based on the fact that a large process tolerance656Y.-H.Lee et al.generates a lower manufacturing cost.Mathematically,this canbe expressed as:Minimise manufacturing cost Subject totolerance stackup constraints machining accuracy constraints(1)Many cost–tolerance functions have been proposed to describe the decreasing monotonic relationship,such as reciprocal and exponential [8].It is worth noting that low manufacturing cost results from wide process tolerances,whereas large process tolerances contribute to good process capability.Therefore,it is desirable to design process tolerance to maximise the process capability index,i.e.Maximize C p iSubject totolerance stackup constraints machining accuracy constraints i =1,2,%,n(2)where C p i is the process capability index of operation i .The tolerance stackup is the accumulation of the dimensional variations produced by individual operations.The addition of tolerances associated with each operation should be within the blueprint tolerance specification.The technique of the tolerance chain is often used to determine the tolerance stackup.The machining accuracy refers to the limitation or attainable toler-ances of individual operations,and is frequently expressed in terms of the upper and lower bounds.In other words,these tolerance bounds represent the economical precision that can be held by a specific machine,and the engineers should design products with these tolerances in mind.Equation (2)is composed of n objective functions to be concurrently maximised.It is necessary to consolidate this multi-objective problem into a single objective formulation.A fuzzy approach is introduced in this article to maximise the process capability index of each operation by obtaining a maximum value for the fuzzy number.A fuzzy membership function is first defined as in Eq.(3).Figure 1depicts the fuzzy membership function.i (z )=Ά1C p i ՆC U p i1−C U p i −C p i C Up i−C L p iC Lp iϽC p i ϽC U p i 0C p i ՅC Lpi(3)Fig.1.The fuzzy membership function.where C U p i and C Lp i are the upper and lower bounds of the process capability index of operation i ,and C p i is the process capability index of operation i to be maximised.Let 0ՅՅ(C p i −C L p i )/(C U p i −C Lp i ),then we have the follow-ing inequality,C p i −(C U p i −C L p i )ՆC Lp i(4)Figure 1reveals that finding a maximum value of would maximise the process capability index.Therefore,the prob-lem becomesMaximise Subject toC p i −(C U p i −C L p i )ՆC Lp ii =1,2,%,n tolerance stackup constraints machining accuracy constraints 0ՅՅ1(5)The multi-objective programming of Eq.(2)is now changedinto a single objective problem,which can be easily solved using any linear programming package.Assume that the bilat-eral limits of a dimensional specification are adopted and the process tolerances are normally distributed,then we haveC p i =U i −L i 6ˆi =2i 6ˆi =i 3ˆi =x i3(6)where U i and L i are the upper and lower limits of the dimensionat operation iˆi =standard deviation of operation i i =process tolerance to be designed x i =standardised process toleranceThe standard deviation of each operation can be obtained from either the daily statistical quality control chart or the small samples experiment [5].The graphical implication of the standardisation can be expressed using Fig.2,where r i rep-resents the scrap rate.Substituting Eq.(6)into Eq.(5),a new expression is formed,Maximize Subject tox i −3(C U p i −C L p i )Ն3C Lp ii =1,2,%,n tolerance stackup constraintsmachining accuracy constraints 0ՅՅ1(7)It is noted that the lower bound C Lp iis used to ensure a minimum acceptable quality level,while the upper bound C U piFig.2.The standardised process tolerances.Fuzzy Design of Process Tolerances657Fig.3.The workpiece.is to prevent the process tolerance of any operation from being over allocated.As a result,the tolerances of other operations are under allocated.3.Numerical ExampleTo verify the applicability of the model,an example worked out manually by Eary and Johnson [1]and solved mathemat-ically by Ngoi [2]is adopted.The example workpiece is machined using ten operations including turning,milling,car-burising,and grinding.Figure 3illustrates the workpiece lab-elled with dimensional specifications.The operation processes indicating the locating or reference surface and the processed surface are listed in Table 1.All capital letters represent the workpiece surfaces,and surfaces BC and GC are used to indicate the carburised surface of B and G,whereas B1and G1are the newly manufactured surfaces of B and G.To derive the tolerance stackup,the information given in Table 1can be used to draw the rooted tree representation shown in Fig.4.The arrows represent the manufacturing oper-ations,where the plain end is the referenced surface,and the arrowhead is the processed surface.The bold line implies the dimensional specifiing Fig.4,the tolerance stackup can be easily obtained based on the fact that the resultant tolerance should be less than,or equal to,the blueprint toler-ance specification.Assume that the machining accuracy of the operations is set at 0.005for the turret lathe and simplex mill,0.002for theTable 1.The operation processes.Operation number Reference surface Processed surface MachineWorking dimension 10A Surface G Turret lathe 1.97020a G Surface B Turret lathe 1.94020b G Surface C Turret lathe 1.78030a B Surface F Turret lathe 1.73030b F Surface E Turret lathe 0.10040B Surface D Simplex mill0.26050a G Surface GC Carburising and hardening equipment 0.02550b B Surface BC Carburising and hardening equipment 0.02560B Surface G1Rotary surface grinder 1.93070G1SurfaceB1Rotary surface grinder1.920Fig.4.The rooted tree representation.D i ,dimension of process i ;i ,process tolerance;DA,DB,DC,DE,DF,DG,blueprint dimension;TBi,blueprint tolerance.rotary surface grinder,and 0.01for the carburising process [2].The standard deviations of the machinery are obtained as ˆ1=0.002,ˆ2=ˆ3=0.001,ˆ4=ˆ5=0.0008,ˆ6=ˆ7=0.0003,ˆ8=ˆ9=0.003,ˆ10=0.0008[5].The upper and lower bounds of the process capability index are set at C U p i = 1.2and C Lp i =0.6,respectively.Then the complete model can be for-med as:Max (8)Subject to:x i −1.8Ն1.8i =1,2,%,100.003x 9+0.001x 2+0.0003x 6Յ0.01(TB 1)658Y.-H.Lee et al.Table2.Thefinal process tolerance and scrap rate.No.1020a20b30a30b4050a50b6070x i 2.5 2.174 2.174 3.16 3.48 2.174 3.0 2.816 2.174 2.5ˆi0.0020.0010.0010.00080.00080.00030.00030.0030.0030.0008i0.0050.00220.00220.003120.002530.000650.00090.008450.00650.002 r i0.01240.02930.02930.001600.02930.00270.00480.02930.0124parison with other methods.Operation Reference Processed Process tolerancesnumber surface surfaceEary and Ngoi Wei and Lee ProposedJohnson[1][2][5]model10A G0.0020.0050.0050.00520a G B0.0020.0020.002170.0022 20b G C0.0020.0020.002170.0022 30a B F0.0040.0040.003120.00312 30b F E0.0020.0030.002480.00253 40B D0.0010.0010.000650.00065 50a G GC0.0020.0010.000850.0009 50b B BC0.0070.0080.008490.00845 60B G10.0070.0070.006720.0065 70G1B10.0020.0020.0020.0020.0008x5+0.0003x6+0.0003x7Յ0.005(TB2)0.001x3+0.001x2+0.0003x6Յ0.005(TB3)0.0008x4+0.0003x6Յ0.005(TB4)0.0003x7Յ0.001(TB5)0.003x8+0.0003x6+0.0003x7Յ0.01(TB6)0.0008x10Յ0.002(TB7)0.002x1Յ0.005(lathe)0.001x2Յ0.005(lathe)0.001x3Յ0.005(lathe)0.0008x4Յ0.005(lathe)0.0008x5Յ0.005(mill)0.0003x6Յ0.002(grinder)0.0003x7Յ0.002(grinder)0.003x8Յ0.01(carburise)0.003x9Յ0.01(carburise)0.0008x10Յ0.005(lathe)0ՅՅ1The objective function is obtained as=0.207729with x1 =2.5,x2=2.174,x3=2.174,x4=3.155,x5=3.482,x6=2.174, x7=3.0,x8=2.816,x9=2.174,x10=2.5.Table2summarises thefinal process tolerances and the corresponding scrap rates. The comparison with other methods is given in Table3. Table2shows that all operations are expected to produce scrap rates of less than3.0%,and six out of ten operations are estimated to yield scrap rates of less than 1.3%.Being able to predict scrap rate is advantageous since tolerances can then be cost effectively designed.From comparing the process tolerances in Table3to Wei and Lee’s results,it can be seen that the proposed model tends to widen the process tolerances.On the other hand,three of Ngoi’s tolerances are increased, whereas anotherfive tolerances are slightly reduced.As to the tolerances obtained by Eary and Johnson,five operations are allocated with wider tolerances by the proposed formulation.4.ConclusionThe design of process tolerances affects not only the expense of manufacturing,but also the scrap and rework cost,and in the worst case,even the market share of the product.Previous approaches rely too much on the experience and expertise of the process planner,therefore,the tolerances allocated may not be economically manufacturable.A fuzzy model has been proposed to convert the multi-objective programming formu-lation into a single objective formulation,which optimises the process capability index in a very straightforward and easy manner.It is believed that the proposed model,if incorporated into the CAPP environment,can improve the quality of pro-cess planning.References1.D.F.Eary and G.E.Johnson,Process Engineering for Manufac-turing,Prentice-Hall,New Jersey,1962.2.B.K.A.Ngoi,“Applying linear programming to tolerance chartbalancing”,International Journal of Advanced Manufacturing Technology,7,pp.187–192,1992.3.B.K.A.Ngoi and S.L.Fang,“Computer aided tolerance chart-ing”,International Journal of Production Research,32(8),pp.1939–1954,1993.4.P.Ji,“A linear programming model for tolerance assignment ina tolerance chart”,International Journal of Production Research,31(3),pp.739–751,1993.Fuzzy Design of Process Tolerances6595.C.C.Wei and Y.C.Lee,“Determining the process tolerancesbased on the manufacturing process capability”,International Jour-nal of Advanced Manufacturing Technology,10(6),pp.187–192,1995.6.M.Y.Nagarwala,P.S.Pulat and S.Raman,“A slope-basedmethod for least cost tolerance allocation”,Concurrent Engineer-ing,3(4),pp.319–328,1995.7.C.Zhang and H.P.Wang,“Integrated tolerance optimization withsimulated annealing”,International Journal of Advanced Manufac-turing Technology,8,pp.187–192,1995.8.L.A.Malek and N.Asadathorn,“Process and design tolerancein relation to manufacturing cost:A review and extension”,The Engineering Economist,40(1),pp.73–100,1994.9.C.Zhang and H.P.Wang,“Optimal process sequence selectionand manufacturing tolerance allocation”,Journal of Design and Manufacturing,3,pp.135–146,1993.10.S.H.Yeo, B.K. A.Ngoi and H.Chen,“A cost–tolerancemodel for process sequence optimisation”,International Journal of Advanced Manufacturing Technology,12,pp.423–431,1996. 11.B.W.Cheng and S.Maghsoodloo,“Optimization of mechanicalassembly tolerances by incorporating Taguchi’s quality loss function”, Journal of Manufacturing Systems,14(4),pp.264–276,1995.12.C. C.Wei,“Designing process tolerances to minimize loss ofnonconforming parts”,IEEE Transactions on Components,Packag-ing,and Manufacturing Technology,Part C:Manufacturing,20(4), pp.1–5,1997.。