不计换相时间的条件下的无刷直流电机驱动器的脉动
无刷直流电机工作原理
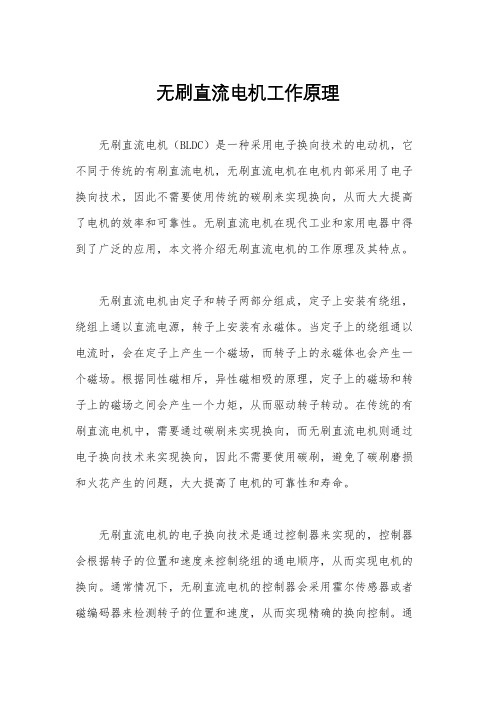
无刷直流电机工作原理无刷直流电机(BLDC)是一种采用电子换向技术的电动机,它不同于传统的有刷直流电机,无刷直流电机在电机内部采用了电子换向技术,因此不需要使用传统的碳刷来实现换向,从而大大提高了电机的效率和可靠性。
无刷直流电机在现代工业和家用电器中得到了广泛的应用,本文将介绍无刷直流电机的工作原理及其特点。
无刷直流电机由定子和转子两部分组成,定子上安装有绕组,绕组上通以直流电源,转子上安装有永磁体。
当定子上的绕组通以电流时,会在定子上产生一个磁场,而转子上的永磁体也会产生一个磁场。
根据同性磁相斥,异性磁相吸的原理,定子上的磁场和转子上的磁场之间会产生一个力矩,从而驱动转子转动。
在传统的有刷直流电机中,需要通过碳刷来实现换向,而无刷直流电机则通过电子换向技术来实现换向,因此不需要使用碳刷,避免了碳刷磨损和火花产生的问题,大大提高了电机的可靠性和寿命。
无刷直流电机的电子换向技术是通过控制器来实现的,控制器会根据转子的位置和速度来控制绕组的通电顺序,从而实现电机的换向。
通常情况下,无刷直流电机的控制器会采用霍尔传感器或者磁编码器来检测转子的位置和速度,从而实现精确的换向控制。
通过精确的换向控制,无刷直流电机可以实现高效率、低噪音和低电磁干扰的运行。
无刷直流电机相比传统的有刷直流电机具有许多优点。
首先,无刷直流电机不需要使用碳刷,因此避免了碳刷磨损和火花产生的问题,提高了电机的可靠性和寿命。
其次,无刷直流电机可以实现精确的换向控制,从而实现高效率、低噪音和低电磁干扰的运行。
此外,无刷直流电机还可以实现无级调速,具有良好的动态特性和响应速度。
因此,无刷直流电机在现代工业和家用电器中得到了广泛的应用。
总之,无刷直流电机采用电子换向技术,不需要使用传统的碳刷来实现换向,因此具有高效率、低噪音和低电磁干扰等优点。
通过精确的换向控制,无刷直流电机可以实现无级调速和良好的动态特性,因此在现代工业和家用电器中得到了广泛的应用。
无刷直流电机工作原理
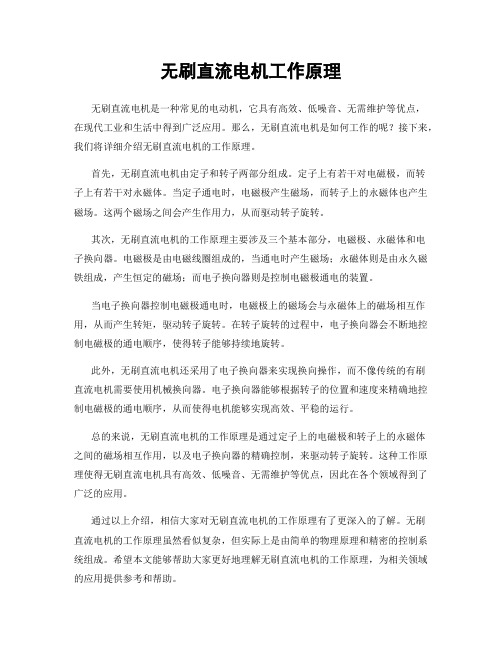
无刷直流电机工作原理无刷直流电机是一种常见的电动机,它具有高效、低噪音、无需维护等优点,在现代工业和生活中得到广泛应用。
那么,无刷直流电机是如何工作的呢?接下来,我们将详细介绍无刷直流电机的工作原理。
首先,无刷直流电机由定子和转子两部分组成。
定子上有若干对电磁极,而转子上有若干对永磁体。
当定子通电时,电磁极产生磁场,而转子上的永磁体也产生磁场。
这两个磁场之间会产生作用力,从而驱动转子旋转。
其次,无刷直流电机的工作原理主要涉及三个基本部分,电磁极、永磁体和电子换向器。
电磁极是由电磁线圈组成的,当通电时产生磁场;永磁体则是由永久磁铁组成,产生恒定的磁场;而电子换向器则是控制电磁极通电的装置。
当电子换向器控制电磁极通电时,电磁极上的磁场会与永磁体上的磁场相互作用,从而产生转矩,驱动转子旋转。
在转子旋转的过程中,电子换向器会不断地控制电磁极的通电顺序,使得转子能够持续地旋转。
此外,无刷直流电机还采用了电子换向器来实现换向操作,而不像传统的有刷直流电机需要使用机械换向器。
电子换向器能够根据转子的位置和速度来精确地控制电磁极的通电顺序,从而使得电机能够实现高效、平稳的运行。
总的来说,无刷直流电机的工作原理是通过定子上的电磁极和转子上的永磁体之间的磁场相互作用,以及电子换向器的精确控制,来驱动转子旋转。
这种工作原理使得无刷直流电机具有高效、低噪音、无需维护等优点,因此在各个领域得到了广泛的应用。
通过以上介绍,相信大家对无刷直流电机的工作原理有了更深入的了解。
无刷直流电机的工作原理虽然看似复杂,但实际上是由简单的物理原理和精密的控制系统组成。
希望本文能够帮助大家更好地理解无刷直流电机的工作原理,为相关领域的应用提供参考和帮助。
无刷直流电机换相转矩脉动分析及抑制

无刷直流电机换相转矩脉动分析及抑制近年来,随着技术的进步,无刷直流电机(BLDC)经常被应用到多种领域,这种电机具有良好的稳定性、可靠性、节能性和高效率等特点。
无刷直流电机采用驱动器来驱动其旋转,并通过换相来控制其转速。
但是,在实际的换相过程中,由于硬件结构和电路的特性,会引起换相转矩脉动这种不利的现象。
因此,为了提高无刷直流电机的精确性和可靠性,如何有效的抑制换相转矩脉动成了当前应用无刷直流电机的研究人员面临的一个重要问题。
为了解决换相转矩脉动问题,我们首先需要了解换相转矩脉动的本质及其影响因素。
首先,换相转矩脉动是由于驱动器控制电机时产生的脉动现象,其主要原因是电机的动态特性,例如电机的电流响应与输入电压时间延迟、滞后特性,以及电机阻抗等。
此外,控制器的设计也会影响换相转矩脉动的大小,例如电压控制(PWM)、电流控制等。
此外,电机的结构参数,如齿数、磁极和电枢直径等,也会影响换相转矩脉动的大小。
为了降低换相转矩脉动,需要从两个方面出发。
首先,。
控制算法设计。
控制算法是控制电机转矩脉动的核心,根据电机的特性,采用适当的控制算法,可以有效的抑制换相转矩脉动。
例如,在电机控制中采用模糊控制和自适应控制等算法,可以有效的抑制转矩脉动;此外,采用调整电压滤波器参数的方法也可以减小换相转矩脉动。
其次,需要采取设计优化的方法。
设计优化可以改变电机结构参数,提高电机控制系统的精确度,从而有效地减少换相转矩脉动。
例如,可以考虑增加电机齿数,增加舵机驱动器输出电流,减少电机阻抗等。
此外,可以从电机材料和结构参数方面考虑优化结构,以降低电机内部转矩脉动。
此外,为了更好的抑制换相转矩脉动,除了考虑控制算法和设计优化外,还可以考虑采用某种机械补偿方法。
比如,采用小型回路控制器,可以有效抑制换相转矩脉动,其原理是在无刷直流电机换相过程中,采用小型回路控制器对转矩信号进行补偿,从而减小换相转矩脉动的大小。
综上所述,换相转矩脉动是应用无刷直流电机的一个致命性问题,控制算法、设计优化和机械补偿等方法可以有效的抑制换相转矩脉动,从而提高无刷直流电机的精确性和可靠性。
无刷直流电动机的转矩脉动

定子斜槽 转子斜极 无槽 分数槽 增大气隙
其他因素
四、电枢反应的影响 五、机械加工的影响
二、电流换向引起的转矩脉动
定义:相电流换向过程引起 原因:转速
电流换向原理
换向转矩脉动与转速的关系
电流换向引起的转矩脉动
结论:换向转矩脉动决定于绕组反电势,
即转速。与稳态电流无关。
转速很低或堵转时,△T=50% 转速很高时, △T=-50% 转速满足U=E时,△T=0
三、齿槽引起的转矩脉动
转速满足U=E 时,△T=0பைடு நூலகம்
极电弧磁宽 因度素为引1起8的0°转:矩转脉矩极动最大弧,转宽矩脉度动为增零 加:转矩增加,转矩脉动减小
转速满足U=E 时,△T=0 转矩系数与气隙磁感应强度波形宽度的关系
二定、义电 :流相换电向流引换起向的过 转程极矩引脉起弧动 宽度为180°:转矩最大,转矩脉动为零
转速很高时, △T=-50% 定义:定子电流和转子磁场相互作用而产生 原因:气隙磁密的分布、电流波形、绕组形式 定义:定子电流和转子磁场相互作用而产生 极弧宽度增加:转矩增加,转矩脉动减小 转速很高时, △T=-50% 极弧宽度增加:转矩增加,转矩脉动减小 第四节无刷直流电动机的转矩脉动 换向转矩脉动与转速的关系 电磁因素引起的转矩脉动 气隙磁场与通电绕组的位置关系 二、电流换向引起的转矩脉动
电磁因素引起的转矩脉动 定义:相电流换向过程引起
定义:相电流换向过程引起 定义:定子电流和转子磁场相互作用而产生 定义:相电流换向过程引起 原因:气隙磁密的分布、电流波形、绕组形式 极弧宽度为180°:转矩最大,转矩脉动为零
电电流流换 换向向引引起起的的转转结矩矩脉脉论动动 :对两相导通星形三相六状态的方波电动机
无刷直流电机工作原理

无刷直流电机工作原理
无刷直流电机是一种将直流电能转换为机械能的电动机。
与传统的有刷直流电机相比,无刷直流电机采用了新的控制技术和结构设计,以提高效率、减少噪音和提高可靠性。
无刷直流电机的工作原理基于霍尔效应和电磁感应原理。
无刷直流电机通常由定子、转子和控制器组成。
定子是无刷直流电机的固定部分,通常由一系列电磁线圈组成,这些线圈被称为相。
每个相都有一个对应的霍尔传感器,用于检测转子的位置。
转子是无刷直流电机的旋转部分,通常由永磁体或电磁体组成。
转子上安装有若干个永磁体或电磁体的磁极,这些磁极和定子相的电磁线圈之间建立起磁场。
控制器是无刷直流电机的核心部分,用于控制电流流向电磁线圈。
控制器根据霍尔传感器检测到的转子位置信号,准确地控制电流的方向和大小。
通过改变电流的方向和大小,控制器能够实现转子的旋转。
当电流通过定子相的线圈时,根据电磁感应原理,线圈会产生磁场。
根据磁场的方向和大小,可以吸引或排斥转子上的磁极,从而使转子旋转。
通过不断地改变电流的方向和大小,控制器可以使转子以恒定的速度旋转。
此外,控制器还可以根据外部输入信号调整电机
的转速和扭矩。
总之,无刷直流电机通过控制电流的方向和大小,将直流电能转换为旋转运动。
它具有高效率、低噪音和高可靠性等优点,被广泛应用于工业和消费电子领域。
不计换相时间的条件下的无刷直流电机驱动器的脉动

不计换相时间的条件下的无刷直流电机驱动器的脉宽调制技术以减少换相转矩脉动Yong-Kai Lin Yen-Shin Lai学生会员,IEEE 高级会员,IEEE 国立台北科技大学电力电子中心台湾台北孝庄东路10608yslai@.tw摘要- 本文介绍了为无刷直流电机驱动器设计的三相脉冲宽度调制技术,以减少换相转矩。
以前的方法相比,所提出的技术并不需要任何的扭矩观察员和减刑时间计算,这可能对电机参数很敏感,并需要更多的计算时间。
换时间对所提出的技术是由一个简单的比较器电路组成的检测电路。
基于FPGA控制的无刷直流电机驱动器以降低电流纹波提出的PWM技术,可显着降低电流纹波。
指数条款- 直流无刷电机,转矩脉动减少,换相转矩脉动I 导言图1(A)显示反电动势和相电流的无刷直流电机的理想波形。
正如图1(A)中所示,目前是平坦的波形,这是在与反电动势相,从而使平滑的扭矩。
然而,由于逆变器的电流转换率和减刑的限制,电流波形是不平坦图所示。
1(B)。
这一事实提供了显着的转矩脉动,可高达平均转矩的50%如[1]中解决的。
提出了一些文件来处理这个问题。
已经提出了一种电流控制方法[2],以减少转矩脉动。
然而,通过减刑所造成的转矩脉动是没有充分考虑[2]。
[3],通过改变直流母线电压,这就需要额外的直流母线电压控制电路和电容器,从而增加了成本,减少换相转矩。
预测电流的方法,这就要求电机参数显示在[4],以减少换相转矩脉动。
正如图所示。
13[4],结果似乎不符合理想的。
在减刑,可减少换相转矩脉动[5-6]所示,通过改变税。
然而,两相PWM保留在[5-6]限制减少转矩脉动的贡献[7-8]讨论。
三相PWM技术,以减少[7-9]的换相转矩脉动。
无论是三相电流传感器或转矩观测[7]和[8]分别为改变PWM方法三阶段。
因此,这些无论是成本增加或计算及参数敏感性分析的结果。
在[9]中,三相PWM 交换控制交换的时间是通过计算确定。
无刷直流电动机的转矩脉动

理想的方波直流无刷电机中,假定气隙磁密为理想方波 或梯形波,其电枢绕组电动势平顶宽度接近120°,这时, 如果忽略电流上升和下降的过渡过程,认为可以控制电流使 其为方波或顶部宽度接近120°的梯形波,并且电流与电势 同相,此时电磁转矩是平滑而稳定的恒定转矩,不随电机转 子转角的变化而变化。而在实际系统中,无刷直流电动机的 电磁转矩并不是理想的恒定值,而是具有较大的脉动。引起 电磁转矩脉动的原因主要有以下几方面:
(4)反电动势非理想。 因为电机制造工艺或转子永磁体充磁不理想等因素, 可能造成电机反电动势不是理想梯形波,但是控制系统依 然按照反电动势为理想梯形波的情况供给方波电流,从而 引起电磁转矩脉动。此类电磁转矩脉动虽可以通过适当的 控制方法以及寻找最佳的定子电流波形来消除,但最佳电 流波形是建立在对反电动势进行精确测定的基础上,而各 电机反电动势波形又不尽相同,使其通用性受到限制。
图10-17 考虑换相过程的三相方波无刷直流电动机电流波形示意图
为分析换相过程,给出功率开关电路与电机耦合的模型
如图10-18所示,其中的V1~V6为开关器件采用的MOSFET 管。假设电机最初工作在图10-14中所示的0°~60°区间,
即A相正向、B相反向通电,功率开关管V1和V6导通。在 ωt=60°时开始换相,V6关断V2导通,即保持A正向通电不 变,从B相换相到C相。B相电流将沿B→VD3→V1→A→B的 续流路径衰减到0,C相电流将沿Us(+)→V1→A→B→V 2→Us(-)的激励路径逐渐建立。若忽略管压降,则有回路 电势平衡方程:
图10-20 齿槽转矩随转子位置变化的规律
齿槽转矩一般需要通过电机的设计来消除。设计时首 先要选择恰当的槽数和极数配合,例如一种典型设计是采 用两极下三槽的分数槽绕组。其他常用的方法有采用斜槽 或斜极结构,将定子槽或转子磁极斜一个定子齿距,显然, 斜槽或斜极也会影响电枢绕组的反电动势。也有采用定子 大齿表面开浅槽、无槽电枢或无铁心电枢结构等方案。
无刷直流电机换相转矩脉动分析及抑制
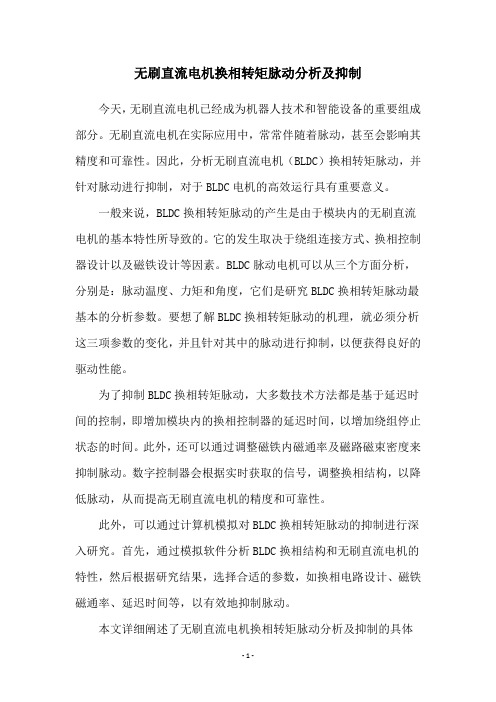
无刷直流电机换相转矩脉动分析及抑制今天,无刷直流电机已经成为机器人技术和智能设备的重要组成部分。
无刷直流电机在实际应用中,常常伴随着脉动,甚至会影响其精度和可靠性。
因此,分析无刷直流电机(BLDC)换相转矩脉动,并针对脉动进行抑制,对于BLDC电机的高效运行具有重要意义。
一般来说,BLDC换相转矩脉动的产生是由于模块内的无刷直流电机的基本特性所导致的。
它的发生取决于绕组连接方式、换相控制器设计以及磁铁设计等因素。
BLDC脉动电机可以从三个方面分析,分别是:脉动温度、力矩和角度,它们是研究BLDC换相转矩脉动最基本的分析参数。
要想了解BLDC换相转矩脉动的机理,就必须分析这三项参数的变化,并且针对其中的脉动进行抑制,以便获得良好的驱动性能。
为了抑制BLDC换相转矩脉动,大多数技术方法都是基于延迟时间的控制,即增加模块内的换相控制器的延迟时间,以增加绕组停止状态的时间。
此外,还可以通过调整磁铁内磁通率及磁路磁束密度来抑制脉动。
数字控制器会根据实时获取的信号,调整换相结构,以降低脉动,从而提高无刷直流电机的精度和可靠性。
此外,可以通过计算机模拟对BLDC换相转矩脉动的抑制进行深入研究。
首先,通过模拟软件分析BLDC换相结构和无刷直流电机的特性,然后根据研究结果,选择合适的参数,如换相电路设计、磁铁磁通率、延迟时间等,以有效地抑制脉动。
本文详细阐述了无刷直流电机换相转矩脉动分析及抑制的具体技术方法。
首先,结合基本特性分析了脉动温度、力矩和角度变化,然后,根据分析结果选择有效的抑制手段,如延迟控制、调整磁铁磁通率,最后,通过计算机模拟进行深入研究。
经过系统的研究,可以获得有效的结果,从而提高无刷直流电机的精度和可靠性。
- 1、下载文档前请自行甄别文档内容的完整性,平台不提供额外的编辑、内容补充、找答案等附加服务。
- 2、"仅部分预览"的文档,不可在线预览部分如存在完整性等问题,可反馈申请退款(可完整预览的文档不适用该条件!)。
- 3、如文档侵犯您的权益,请联系客服反馈,我们会尽快为您处理(人工客服工作时间:9:00-18:30)。
不计换相时间的条件下的无刷直流电机驱动器的脉动Document number:BGCG-0857-BTDO-0089-2022不计换相时间的条件下的无刷直流电机驱动器的脉宽调制技术以减少换相转矩脉动Yong-Kai Lin Yen-Shin Lai学生会员,IEEE 高级会员,IEEE国立台北科技大学电力电子中心台湾台北孝庄东路 10608摘要 - 本文介绍了为无刷直流电机驱动器设计的三相脉冲宽度调制技术,以减少换相转矩。
以前的方法相比,所提出的技术并不需要任何的扭矩观察员和减刑时间计算,这可能对电机参数很敏感,并需要更多的计算时间。
换时间对所提出的技术是由一个简单的比较器电路组成的检测电路。
基于FPGA控制的无刷直流电机驱动器以降低电流纹波提出的PWM技术,可显着降低电流纹波。
指数条款 - 直流无刷电机,转矩脉动减少,换相转矩脉动I 导言图1(A)显示反电动势和相电流的无刷直流电机的理想波形。
正如图1(A)中所示,目前是平坦的波形,这是在与反电动势相,从而使平滑的扭矩。
然而,由于逆变器的电流转换率和减刑的限制,电流波形是不平坦图所示。
1(B)。
这一事实提供了显着的转矩脉动,可高达平均转矩的50%如[1]中解决的。
提出了一些文件来处理这个问题。
已经提出了一种电流控制方法[2],以减少转矩脉动。
然而,通过减刑所造成的转矩脉动是没有充分考虑[2]。
[3],通过改变直流母线电压,这就需要额外的直流母线电压控制电路和电容器,从而增加了成本,减少换相转矩。
预测电流的方法,这就要求电机参数显示在[4],以减少换相转矩脉动。
正如图所示。
13[4],结果似乎不符合理想的。
在减刑,可减少换相转矩脉动[5-6]所示,通过改变税。
然而,两相PWM保留在[5-6]限制减少转矩脉动的贡献[7-8]讨论。
三相PWM技术,以减少[7-9]的换相转矩脉动。
无论是三相电流传感器或转矩观测[7]和[8]分别为改变PWM方法三阶段。
因此,这些无论是成本增加或计算及参数敏感性分析的结果。
在[9]中,三相PWM 交换控制交换的时间是通过计算确定。
然而,电机绕组的电感需要换时间计算。
请在[9]看(27)几个PWM技术[10-12]已经提出了消除逆转直流母线电流或循环的无刷直流电机驱动器的电流。
这些研究成果尚未讨论减少换向无刷直流电机驱动器的电流纹波。
在本文中,为减少转矩脉动的PWM技术建议。
此外,决定减刑期的检测电路。
最后,实验结果的形式基于FPGA的无刷直流电机驱动器显示,减刑电流纹波提出的PWM技术,可显着降低。
(A)理想反电势和相电流(B)实际相电流,CH2图1。
无刷直流电机的理想与实际波形II 提出的交换扭矩降低的PWM技术一种新的用来减少三相无刷直流电机驱动换相转矩的脉冲宽度调制技术被提出。
以前的方法相比,所提出的技术并不需要任何的扭矩观察员和减刑时间计算,这可能是敏感的电机参数,并需要更多的计算时间。
换时间对所提出的技术是由一个简单的比较器电路组成的检测电路。
A.基本概念图2显示了无刷直流电机驱动器的框图。
图3显示了减少换相转矩脉动的基本思路。
正如图3中所示使用相“a”作为非换相,相“b”为即将离任的阶段而相“c”为进入阶段,基本思路是作为一个例子,保留同样大小的电流转换率而符号相反的传入和传出的阶段。
这个基本的想法,可以通过控制在交换时的多少来实现图4显示了建议的交换控制专长。
在非减刑期间(CP=“L”),所需的导通时间,“TN”,适用于PWM控制,在此期间,保留两相PWM控制。
“TN”可以从一个控制回路,如速度控制环和转矩控制回路等,相比之下,派生,反过来加倍,“TC1”和“TC2”,用于在交换期间(控制面板的“H”)和三相PWM控制应用,如图所示。
4。
“TC1”和“TC2”将在下一节派生图2 无刷直流电机驱动器图3所提及技术的基本思想图4 提出的减少换相转矩的三相PWM控制B.在交换期间的 tc1 and tc2 的推导正如图所示。
3,三相绕组的无刷直流电机可分为非交换阶段,进入阶段和在交换时期传出阶段。
非换相电流维持在交换时期。
传入相电流随控制摆率而增加相比之下,目前传出阶段降低在交换时期。
以“tc1”and “tc2”派生的一般形式,本文使用阶段的“X”,“Y”和“Z”代表非换相,相传出和传入阶段,分别为。
此外,表I显示“X”,“Y”和“Z”的三相无刷直流电机绕组在不同部门之间的关系。
表 I三相绕组“x”, “y” and “z”之间的关系在部门2的交换期,无刷直流电机的电路如图5(A)所示,而信号是“开”。
根据表一,无刷直流电机等效模型可以得出如图 6(一)如果绕组电阻被忽略。
图5 在部门2交换期间的无刷直流电机的电路图6 图5的等效电路正如图6(A), (1)-(3) 中的可以由基尔霍夫电压定律导出由 (1)-(3), 中央抽头电压可以导出(4)代入(1) - (3),每相的电流转换率可写为:信号变为“关闭”时,无刷直流电机的电路如图 5(B)。
并且图5(B)的等效电路正如图 6(B)所示。
正如图6(B)所示,(8) - (10)由基尔霍夫电压定律可以得出:由(8)—(10)得,中央抽屉电压可被推导为把(11)代入(8) - (10),每相电流转换率可以写为:平均每相的电流转换率可以写成:“dc1“是部门2在交换期间的占空比,它可以被定义为(18),在(18)中,“Ts”代表开关周期为了保持相同幅度的电流转换率而符号相反的传入和传出的阶段可以得到以下结果:此外,合上时间,“tc1”,在交换时期可以被推导为假设,(20)可以被写成:当同样,合上时间“tc2“,部门3在交换时间可以被写成假设,(22)可以被写成C 建议的交换时间的检测电路图7显示了交换期检测电路的框图。
传出相“断开”控制用于这种检测。
图7(B)和图 7(C)显示零电流和零电流条件。
在图 7(B)中,如果传出相电流不为零,比较器输出“DYP”为“高”。
反之当传出相电流为零,“DYP”为“低”如图(C)所示。
因此,当交换期结束,“DYP”的状态变低,从而表明交换期。
交换期间,由“CP”在图4中表示,结束时,比例会随着所需的开通时间而改变,“tn”如图4所示和两相PWM控制恢复。
第三。
实验结果图8显示了基于FGPA的实验系统。
正如图8所示,直流母线电流反馈电流控制。
直流母线电压和逆变器的开关频率为24 V 和20千赫。
图9显示提出的方法是使用FPGA实现框图。
正如图9所示,无刷直流电机转速的计算方法,通过检测霍尔信号。
根据图4信号的“chopdn”用于产生PWM信号时,“CP”=“L”的。
如“CP”变为“H”,信号“chopdc”用于产生PWM 信号无刷直流电机的规格载于附录。
图10和图 12显示终端电压的测量结果,相电流和检测减刑期间,建议减少转矩脉动技术与方法。
纹波电流比较图。
比较图10(A)中和图 10(B)的纹波电流,其中图10(A)没有用所提的技术而图10(B)有用。
很显然所提出的技术,大大降低纹波电流和电流波形几乎是正方形。
其他当前命令如图11和图12分别为定额和定额时,可以得出类似的结果。
这些实验结果完全支持建议的技术的有效性。
图7 部门2,4和6传出相交换时的检测电路图8 基于FGPA的实验系统图9 FPGA中的框图图10 实验结果CP 图11 实验结果CP图12 实验结果CPIV. 结论本文介绍了无刷直流电动机驱动的三相脉宽调制技术,以减少换相转矩。
该技术不需要任何扭矩观察员和换时间的计算,这可能是敏感的电机参数和需要更多的计算时间。
所提出的技术交换时间由检测电路检测。
实验结果表明,基于FPGA控制依靠PWM技术的无刷直流电机驱动器的换向电流纹波可显着降低。
附录3φ BLDCM, L = mH, R = , P rated =70 W,I rated = 3 A.参考[1]R. Carlson, M. Lajoie-Mazenc,and J. C. D. S. Fagundes,“Analysis of torque ripple dueto phase commutation inbrushless DC machines,” IEEETrans. on Industry Applications, Vol. 28, No. 3, pp. 632-638,1992.[2]C. T. Pan and E. Fang, “Aphase-locked-loop-assistedinternal model adjustable-speedcontroller for BLDC motors,”IEEE Trans. on IndustrialElectronics, Vol. 55, No. 9, pp.3415-3425, 2008.[3]K. Y. Nam, W. T. Lee, C. M. Leeand J. P. Hong, “Reducingtorque ripple of brushless DCmotor by varying inputv oltage,” IEEE Trans.onMagnetics, Vol. 42, No. 4, pp.1307-1310, 2006.[4]J. Cao, B. Cao, P. Xu, S. Zhou,G. Guo and X. Wu, “Torqueripple control of position-sensorless brushless DC motorbased on neural networkidentification,” in Proc. ofIEEE ICIEA, pp. 752-757, 2008.[5]X. Xiao, Y. Li, M. Zhang and M.Li, “A novel control strategyfor brushless DC motor drivewith low torque ripples,” inProc. of IEEE IECON, , 2005. [6]D. K. Kim, K. W. Lee and B. I.Kwon, “Commutation torqueripple reduction in a positionsensorless brushless DC motordrive,” IEEE Trans. on PowerElectronics, Vol. 21, No. 6, pp.1762-1768, 2006.[7]H. Lu, L. Zhang and W. Qu, “Anew torque control method fortorque ripple minimization ofBLDC motors with un-ideal backEMF,” IEEE Trans. on PowerElectronics, Vol. 23, No. 2, pp.950-958, 2008.[8]Y. Liu, Z. Q. Zhu and D. Howe,“Commutation-torque-rippleminimization in direct-torque-controlled PM brushless DCdrives,” IEEE Trans. onIndustry Applications, Vol. 43,No. 4, pp. 1012-1021,2007.[9]S. S. Bharatkar, R. Yanamshetti,D. Chatterjee and A. K. Ganguli,“Reduction of commutationtorque ripple in a brushless DCmotor drive,” in Proc. of IEEEPECon, pp. 289-294, 2008.[10]Y. S. Lai and Y. K. Lin,“Quicken the pulse,” IEEEIndustry Applications Magazine,Vol. 14, No. 5, pp. 34-44, 2008.[11]Y. S. Lai, F. S. Shyu and Y. K.Lin, “Novel PWM techniquewithout causing reversal DC-link current for brushless DC motordrives with bootstrap driver,”in Proc. of IEEE IAS, Vol. 3,pp. 2182-2188, 2005.[12]Y. S. Lai and Y. K. Lin,“Assessment of pulse-widthmodulationtechniques for brushless DCmotor drives,” in Proc. of IEEE IAS, Vol. 4, pp. 1629-1636,2006.。