基于ADAMS的轻卡动力总成悬置系统怠速隔振性能优化设计-王宇航
基于ADAMS的动力总成悬置系统的隔振仿真研究

A于ADAMS的发动机总成悬置系统的改进设计

O p tim iza tio n o f Eng ine Mo un ts S ys tem B a se d o n ADAM S
表 5 优化后悬置系统各向刚度值 Ta b. 5 Ea ch R ig id ity o fM o un t S ys tem a fte r O p tim iza tio n
方向
x
y
前悬置
117
40
后悬置
30
26
N /mm z 528 58
·92·
拖拉机与农用运输车 第 4期 2007年 8月
质量 / kg
J xx
J yy
J zz
J xy
J xz
J yz
327. 2
9. 58 34. 18 31. 65 0. 466 1 - 4. 663 - 0. 503 3
表 3 原车发动机总成悬置点的各向刚度
Ta b. 3 Ea ch R ig id ity o fM o un t Po in ts o f O rig ina l Eng ine Pow e r Tra in
3. 2 目标函数
由表 4分析可知 ,悬置系统需要改进的就是要实现在其主要激
振力作用方向上解耦程度的提高及模态频率的合理安排 ,为此基于
能量法解耦 ,建立优化目标函数 ,定义系统沿 z轴移动和绕 x轴转动
的动能百分比为 100%。
3. 3 约束条件
基于能量法解耦 ,需要考虑如下约束 :对选取的设计变量 (后悬
《2024年汽车动力总成悬置系统振动分析及优化设计》范文

《汽车动力总成悬置系统振动分析及优化设计》篇一一、引言随着汽车工业的快速发展,汽车动力总成悬置系统的性能逐渐成为影响汽车舒适性和稳定性的关键因素。
本文旨在分析汽车动力总成悬置系统的振动问题,并提出相应的优化设计方案,以提高汽车的驾驶体验和性能。
二、汽车动力总成悬置系统概述汽车动力总成悬置系统是连接发动机、变速器和底盘的重要部分,其主要作用是减少振动和噪声的传递,提高汽车的乘坐舒适性和行驶稳定性。
该系统通常由发动机悬置、变速器悬置和副车架等组成。
三、汽车动力总成悬置系统振动分析1. 振动产生原因汽车动力总成悬置系统的振动主要来源于发动机的运转和道路的不平度。
发动机运转时产生的振动会通过悬置系统传递到车身和底盘,而道路不平度则会导致整个动力总成系统的振动。
2. 振动影响分析动力总成悬置系统的振动会对汽车的乘坐舒适性、行驶稳定性和发动机性能产生不良影响。
长期振动还可能导致悬置系统零部件的疲劳损坏,增加维修成本。
四、汽车动力总成悬置系统优化设计1. 材料选择优化优化材料选择是提高动力总成悬置系统性能的有效途径。
采用高强度、轻量化的材料,如铝合金、复合材料等,可以降低系统质量,提高系统的刚度和减振性能。
2. 结构优化设计结构优化设计是解决动力总成悬置系统振动问题的关键。
通过改进悬置系统的结构布局、增加减振元件和优化阻尼特性等措施,可以有效地减少振动和噪声的传递。
例如,采用多级减振结构,使系统在不同频率下的减振效果更加明显。
3. 智能控制技术应用智能控制技术如主动或半主动悬置系统,可以通过传感器实时监测系统的振动状态,并自动调整控制参数,以实现更好的减振效果。
这种技术可以提高系统的自适应能力和性能稳定性。
五、实例分析以某款汽车的动力总成悬置系统为例,通过对其振动问题进行详细分析,发现主要问题在于发动机运转时产生的振动过大。
针对这一问题,我们采用了上述的优化设计方案,包括采用高强度铝合金材料、优化结构布局和增加减振元件等措施。
基于ADAMS的悬架系统动力学仿真分析与优化设计

基于ADAMS的悬架系统动力学仿真分析与优化设计摘要:本文基于ADAMS软件,对悬架系统进行了动力学仿真分析与优化设计。
通过建立悬架系统的模型,应用动力学仿真技术,研究了悬架系统在不同工况下的动力学性能,并进行了相应的优化设计。
仿真结果表明,通过优化设计,悬架系统的动力学性能得到了明显的提升,进而提高了整车的操纵稳定性和行驶舒适性。
1. 引言随着汽车工业的发展,悬架系统的性能对于整车的操纵稳定性和行驶舒适性起着至关重要的作用。
因此,对悬架系统进行动力学仿真分析和优化设计具有重要的理论意义和工程应用价值。
2. 悬架系统模型建立首先,根据悬架系统的实际结构和工作原理,建立了悬架系统的运动学和动力学模型。
模型包括弹簧、减振器、转向杆等各个部件,并考虑了车轮与地面之间的接触力和摩擦力。
通过ADAMS软件的建模工具和功能,对悬架系统进行了准确地建模。
3. 悬架系统动力学仿真基于悬架系统的模型,进行了不同工况下的动力学仿真分析。
通过设定不同的工况参数,如路面不平度、悬架系统参数等,研究了悬架系统在不同路况下的动力学性能。
仿真结果显示了悬架系统的悬架行程、车体加速度、横向加速度、滚动转矩等关键参数的变化规律。
4. 悬架系统优化设计根据悬架系统动力学仿真的结果,对悬架系统进行了优化设计。
通过改变悬架系统的参数和结构,优化了悬架系统的动力学性能。
具体而言,通过增加弹簧刚度、调整减振器阻尼等方式改善了悬架系统的行程和刚度特性。
通过优化悬架系统的参数,达到了提高整车操纵稳定性和行驶舒适性的目的。
5. 结果与分析通过悬架系统动力学仿真和优化设计,得到了悬架系统在不同工况下的性能变化趋势。
仿真结果表明,通过合理的优化设计,悬架系统的行程和刚度均得到了明显的改善。
同时,整车的操纵稳定性和行驶舒适性也得到了显著提升。
6. 结论本文基于ADAMS软件,对悬架系统进行了动力学仿真分析与优化设计。
通过建立悬架系统的模型,进行了不同工况下的仿真分析,并进行了相应的优化设计。
基于ADAMS的某客车动力总成悬置隔振性能分析

基于ADAMS的某客车动力总成悬置隔振性能分析悬置隔振系统是客车动力总成中重要的部分,其主要功能是减少发动机和驱动系统产生的振动传递到车身上,提高行车舒适度和乘坐品质。
本文将通过ADAMS软件对客车动力总成悬置隔振性能进行分析。
首先,建立悬置隔振系统的ADAMS模型。
模型包括发动机、传动系统、悬置部件和车身等组成部分。
通过ADAMS中的建模工具,可以将实际客车的悬置隔振系统进行准确的建模和仿真。
在建模完成后,我们需要设定模型的初始参数,包括发动机的转速、传动系统的传动比、悬置部件的刚度和阻尼等。
这些参数的设定将直接影响到悬置隔振系统的性能。
接下来,进行动力总成悬置隔振性能的仿真分析。
首先,我们可以对模型进行静态分析,确定悬置部件的初始位移和应力分布。
然后,通过ADAMS的动力学仿真工具进行动态分析,模拟车辆在不同路况下的行驶情况。
通过仿真分析,我们可以得到悬置隔振系统的关键性能指标,包括悬置部件的位移、速度和加速度等。
这些指标可以直接反映出悬置隔振系统的动力学性能和舒适性。
在分析过程中,还可以通过ADAMS的优化工具进行参数优化。
根据实际需求,我们可以通过调整悬置部件的刚度、阻尼和质量等参数,来优化悬置隔振系统的性能。
通过反复的优化过程,可以得到最佳的悬置隔振系统参数组合,以提高客车动力总成的舒适性和乘坐品质。
最后,根据仿真分析的结果,我们可以对悬置隔振系统进行改进和优化。
例如,增加悬置部件的刚度和阻尼,可以提高系统的抗震性能;调整悬置部件的质量分布,可以平衡车身的重心,提高行驶稳定性。
综上所述,基于ADAMS的客车动力总成悬置隔振性能分析,可以通过建立准确的ADAMS模型,进行静态和动态的仿真分析,优化参数组合,改进和优化悬置隔振系统的性能,以提高客车的行车舒适度和乘坐品质。
基于ADAMS的汽车悬架系统建模与优化

基于ADAMS的汽车悬架系统建模与优化摘要:汽车悬架系统是车辆中起到缓冲和支撑作用的重要组成部分,对车辆的行驶稳定性和乘坐舒适度起着重要的影响。
为了提高汽车悬架系统的性能,本文基于ADAMS软件对汽车悬架系统进行建模和优化。
首先,介绍了汽车悬架系统的组成和原理,然后利用ADAMS软件对其进行动力学建模,并进行了参数化设计。
然后,通过ADAMS的优化模块建立了优化模型,并设定了优化目标和约束条件。
最后,利用ADAMS进行参数优化,评估了优化后的悬架系统的性能和稳定性。
1.引言汽车悬架系统是车辆中起到缓冲和支撑作用的重要组成部分,对车辆的行驶稳定性和乘坐舒适度起着重要的影响。
随着汽车工业的发展和人们对行驶安全和乘坐舒适度要求的增加,对汽车悬架系统的性能和稳定性提出了更高的要求。
因此,对汽车悬架系统进行建模和优化具有重要的理论和实际意义。
2.汽车悬架系统建模汽车悬架系统主要由弹簧、减震器和悬挂结构组成。
弹簧用于支撑车身和车轮之间的重量,减震器则用于减少由于路面不平而产生的振动。
悬挂结构起到连接车轮和车身的作用,并提供运动约束。
为了对汽车悬架系统进行建模,本文选用ADAMS软件进行动力学仿真。
首先,建立汽车悬架系统的三维模型,并设置合适的运动约束和连接关系。
然后,对系统进行刚体化处理,即将弹簧和减震器视为刚体,并通过刚体连接建立弹簧和减震器与车身和车轮的连接关系。
最后,通过添加合适的约束条件和初始条件,完成悬架系统的建模。
3.参数化设计为了对汽车悬架系统进行优化,需要对其相关参数进行设计和优化。
本文利用ADAMS的参数化设计功能对悬架系统的参数进行建模,并设置了相应的参数范围和步长。
通过参数化设计,可以根据实际需求快速调整和优化悬架系统的参数。
4.悬架系统优化在悬架系统优化中,本文设定了性能指标和约束条件,以最小化车身加速度和最大化车轮垂直位移为优化目标,同时考虑到车身重心的稳定性和悬架系统的刚度。
通过ADAMS的优化模块,对悬架系统的参数进行优化,并得到了最优解。
基于ADAMS的驾驶室悬置优化设计

基于ADAMS的驾驶室悬置优化设计
随着汽车技术的不断进步,驾驶舒适性成为越来越重要的设计指标之一。
驾驶室悬置系统是影响驾驶舒适性的重要因素之一。
本文通过ADAMS软件对驾驶室悬置系统进行了优化设计,旨在提高驾驶舒适性和行驶稳定性。
首先,建立了驾驶室、悬架系统和轮毂的三维虚拟模型,并在ADAMS软件中进行约束和边界条件设置。
然后,采用模态分析方法计算了模态频率和振型,并根据模态频率的大小和分布情况对悬置系统进行了初步分析。
接着,通过人体振动舒适性的相关标准,对驾驶室的振动舒适性进行了评估。
结果表明,驾驶室在某些工况下存在明显的振动不适感。
为了解决这一问题,采用了形状优化方法对驾驶室支架进行优化设计。
通过对支架几何形状的改进,提高了其刚度和强度,从而有效减少了驾驶室的振动幅值。
同时,为了验证优化效果,在ADAMS软件中进行了模拟分析。
与未优化前相比,优化后的驾驶室振动幅值大幅降低,满足了人体振动舒适性的要求,同时行驶稳定性也有所提高。
基于ADAMS的电动汽车动力总成悬置系统优化
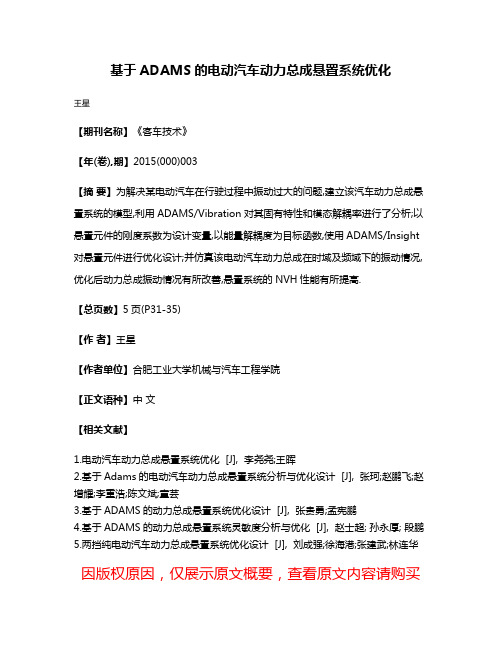
王星【Leabharlann 刊名称】《客车技术》【年(卷),期】2015(000)003
【摘 要】为解决某电动汽车在行驶过程中振动过大的问题,建立该汽车动力总成悬置系统的模型,利用ADAMS/Vibration对其固有特性和模态解耦率进行了分析;以悬置元件的刚度系数为设计变量,以能量解耦度为目标函数,使用ADAMS/Insight对悬置元件进行优化设计;并仿真该电动汽车动力总成在时域及频域下的振动情况,优化后动力总成振动情况有所改善,悬置系统的NVH性能有所提高.
4.基于ADAMS的动力总成悬置系统灵敏度分析与优化 [J], 赵士超; 孙永厚; 段鹏
5.两挡纯电动汽车动力总成悬置系统优化设计 [J], 刘成强;徐海港;张建武;林连华
因版权原因,仅展示原文概要,查看原文内容请购买
【总页数】5页(P31-35)
【作 者】王星
【作者单位】合肥工业大学机械与汽车工程学院
【正文语种】中 文
【相关文献】
1.电动汽车动力总成悬置系统优化 [J], 李尧尧;王晖
2.基于Adams的电动汽车动力总成悬置系统分析与优化设计 [J], 张珂;赵鹏飞;赵增耀;李重浩;陈文斌;童芸
3.基于ADAMS的动力总成悬置系统优化设计 [J], 张贵勇;孟宪鹏
- 1、下载文档前请自行甄别文档内容的完整性,平台不提供额外的编辑、内容补充、找答案等附加服务。
- 2、"仅部分预览"的文档,不可在线预览部分如存在完整性等问题,可反馈申请退款(可完整预览的文档不适用该条件!)。
- 3、如文档侵犯您的权益,请联系客服反馈,我们会尽快为您处理(人工客服工作时间:9:00-18:30)。
基于ADAMS的轻卡动力总成悬置系统
怠速隔振性能优化设计
王宇航余显忠刘洲
江铃汽车股份有限公司江西南昌330001
【摘要】针对某轻型卡车的橡胶悬置系统, 用机械系统动力学仿真分析软件ADAMS,建立了动力总成悬置系统六自由度的动力学模型. 通过对动力总成橡胶悬置系统在怠速工况下的自振频率、系统的能量分布的计算,得到系统解耦的能量指标, 并以该能量指标为设计目标, 以各悬置橡胶悬置的三向刚度值为约束条件进行优化设计.结果表明:优化后的动力总成悬置系统能量分布的解耦程度明显优于优化前系统,
优化后悬置系统的隔振性能有所提高.
【关键词】:ADAMS 动力总成悬置系统怠速隔振优化
1 前言
动力总成悬置系统的怠速工况隔振设计是一项复杂的系统优化问题。
在汽车设计开发中,合理地设计悬置系统,可以降低动力总成激励产生的振动传递到车架和车身,提高乘坐舒适性和降低振动噪声,提高汽车产品品质和竞争力。
理想的悬置系统应可以将动力总成自身产生的振动与车架结构相隔离。
它必须在汽车突然加速、制动、转向等非稳态干扰时,有效限制发动机的过分弹跳和过大的位移。
从隔振理论可知,理想的动力总成悬置系统应在低频范围有较大的刚度和阻尼,而在高频范围有较低的动刚度。
目前国内外主要通过两种途径来改善动力总成悬置系统的性能。
其一是使动力总成悬置自身的动态性能接近最佳状态,另一种是应用振动理论对传统橡胶垫的刚度、位置及倾角等参数应用计算机进行优化设计。
针对工程试验中反映的某轻卡怠速隔振效果不佳的问题,基于解耦的能量法,我们应用大型商业软件——机械系统动态分析软件ADAMS对悬置进行优化设计。
2 动力总成悬置系统的建模
2.1 悬置系统动力学方程的建立
动力总成悬置系统的固有频率一般在5~30 Hz之间,其固有频率远低于动力总成的弹性模态,可以系统低频隔振分析为主要目标的设计过程中,将动力总成视为刚体,悬置元件简化为三向正交的弹性阻尼元件。
动力总成悬置系统构成了质量、刚度的振动系统, 在无外力作用情况下, 可得发动机悬置系统六自由度自由振动的运动方程式为:
M q,,+ C q,+ K q=0,(1)
式中:M为系统的质量矩阵; q,,为系统的广义加速度向量;C为系统的阻尼矩阵;q,为系统的广义速度向量; K为系统的刚度矩阵; q为系统广义位移向量。
由于悬置块的阻尼不大,其主要作用是降低共振峰值,在小振幅振动作用下,可以在分析系统自由振动时略去阻尼, 系统的振动微分方程为:
M q+ K q = 0 ,(2)
设微分方程式的同步运动解为: q = A sin (ω t +φ ),(3)
其中:A 为振幅; ω为固有频率; φ为相位.,
将(3)代入(2),方程存在非零解的条件是│K-ω2M│=0,(4)
(4)即为求解发动机悬置系统固有频率的一般方程式,其解值ω即为各项固有频率值。
2.2 模型描述
已知该轻卡动力总成位置、质量惯量参数及改进前后橡胶悬置的刚度参数见下表:
表1 动力总成质量惯量参数
表2 动力总成悬置坐标(发动机质心坐标系)
设定动力总成系统坐标系:定坐标系为Go- XYZ,原点Go取在动力总成的质心处,X轴平行于曲轴轴线,指向发动机前方;Z轴平行于活塞缸轴线向上;Y轴按右手定则确定。
动坐标系G- xyz原点G固结在动力总成质心处,静平衡时,动、定坐标系重合。
广义坐标为动力总成质心沿X,Y,Z三向的平移x,y,z及绕x,y,z轴的转角θx,θy,θ z。
对橡胶垫认为在正常工况下弹性是线性的,所有的悬置支架均视为刚体,与车架相连接的部分固接于地而上,于是得到如下的ADAMS模型(见图1)。
图1 四点悬置模型
3 解耦分析及优化设计
3.1 目标函数的确定
悬置系统设计目标是实现整个系统6个方向的振动全部或者部分解耦。
通常动力总成悬置系统的6个刚体模态之间存在比较严重的耦合作用,即耦合振动中的某一模态受到激励的同时,其它模态振动也受到激发。
这使系统的激振频带加宽,给隔振和频率配置带来困难。
根据系统总的能量矩阵及每个广义坐标所分配到的能量可以得到每阶固有频率下每一方向的能量解耦率,因此通过解耦率方程表达式可以看出,悬置系统的位置、方向角度及刚度都对解耦率有影响。
本案例即以每个方向的能量分布为目标函数。
3.2 设计变量及约束条件
由于整车布置的限制,动力总成悬置相对车架的位置和角度不能改动,那么最具可行性的就是对悬置弹性元件的刚度就是优化。
这也显示出悬置设计在车辆性能开发早期就应该充分的考虑。
3.3优化结果分析
对模型中各元件赋值后,利用ADAMS的振动分析求解器vibration,很方便地求出系统的六阶频率及各阶频率中的能量分布。
由于该轻卡是四缸四冲程柴油发动机,在怠速时的稳定转速750 r/min,故可算出发动机怠速的激振频率为25 Hz。
根据隔振理论,悬置系统的最高频率不得超过激振频率的0.707倍,即17.6 Hz。
又由于底盘系统及路面激振频率的影响,悬置系统的最小频率应高于3 Hz。
由此可见,悬置系统各阶频率分布合理。
又由于来自发动机的激励主要有垂直方向和绕曲轴轴线旋转方向两种,因此应尽量使这两个方向的振动耦合程度减少,由表4可见,Ox方向的能量分布百分比仅为51.86%, z方向的能量分布百分比也仅为52.96%,两方向解耦程度都不高,因此悬置系统在解耦度上还不合理,需要进行改进。
通过悬置刚度优化,系统在保持频率合理分布的同时,解耦度有了明显提高(见表6)。
表3 动力总成悬置初始线刚度
表4 优化前系统自振频率和能量分布
表5 动力总成悬置优化后线刚度
表6 优化后系统自振频率及能量分布
四结论
动力总成是汽车的重要激励源,通过某轻卡怠速共振的工程问题,通过对动力总成悬置系统进行动力学建模,结合悬置系统振动解耦理论和固有频率匹配理论研究了其能量解耦特性,利用ADAMS软件,在能量解耦理论基础上对动力总成悬置主刚度进行了优化设计。
结果表明,优化后的刚度值提高了动力总成悬置系统的主振动解耦率,有效地降低了该卡车动力总成的振动,改善了整车的NVH 特性。
参考文献:
1、ADAMS. help. MSC.software,2011。
2、赵建才等. 车辆动力总成悬置系统的能量法解耦仿真分析. 上海交通大学学报,2008
3、龙岩等. 动力总成悬置系统优化方法的对比研究. 汽车工程,2011。