Effect of sintering temperature on aging resistance and mechanical properties of 3Y-TZP dental
以粉煤灰为原料制备高纯氧化铝(论文)

化
工
学Leabharlann 报JournaI of ChemicaI Industry and Engineering ( China)
VoI. 57 No. 9 September 2006
。、
。、
。。。。。、
研究简报
以粉煤灰为原料制备高纯氧化铝
。。。。。、
李来时1 ,翟玉春1 ,秦晋国2 ,吴 艳1 ,刘瑛瑛1
吹干,做 XRD 分析,并在 60C 重新溶解在 0. l mol ·L - l 的 H2 SO4 中,冷 却 至 室 温,滤 出 析 出 晶 体, 重复 3 次重结晶过程,得到纯的硫酸铝铵中间体.
实验中用化学滴定分析溶液中 Al 含量,用光度法测 定溶液中 Fe 和 Si 含量[9].
对中间体做热重失重( TG / DTA) 分析,确定
2. 5 重结晶对产品氧化铝纯度的影响 实验 证 明 硫 酸 铝 铵 3 次 重 结 晶 后, 制 得 的
Al2 03 纯度大于 99. 9% ,达到高纯氧化铝的要求. 重结晶方法提纯存在能耗大、提纯率不高等问
题,所以关于硫酸铝铵的提纯有待进一步研究. 相 关文献[13]也提出了一些工业提纯改进的方案. 也可 采用“ 酸化加氨法”[14]提纯硫酸铝铵. 2. 6 煅烧升温速率对产品氧化铝粒度的影响
从电厂直接出来的粉煤灰平均粒度在 40!m 左 右,大部分呈玻璃态[l0],其中 Al2 O3 为非活性体. 要提高 Al2 O3 的提取率就必须提高其活性. 国内外 大量研究采用氟化物作为助溶剂来提高 Al2 O3 的活 性[ll],但氟化物不但会对环境造成巨大危害,而且 操作也具一定的危险性. 本实验通过将粉煤灰磨细 至一定粒度,增大粉煤灰的比表面积,即增大与硫 酸铵反应的接触面积,达到提高其活性的目的.
烧结温度对BaTiO_3多孔陶瓷性能的影响_蒲永平
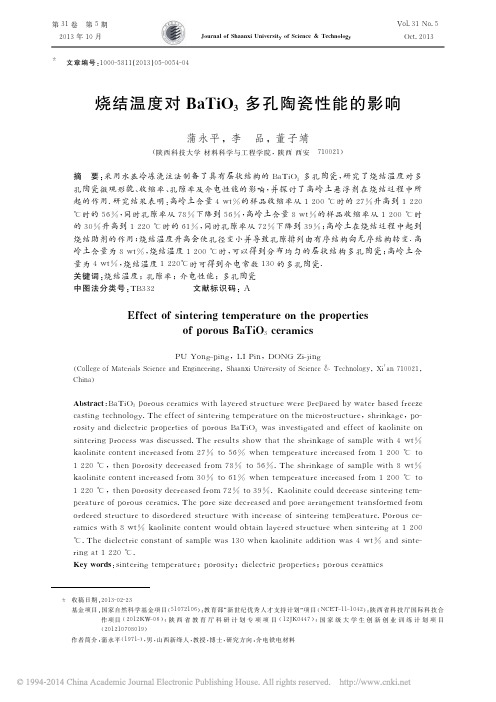
第31卷 第5期 陕西科技大学学报 Vol.31No.5
2013年10月 Journal of Shaanxi University of Science & Technology Oct.2013
* 文 章 编 号 :1000-5811(2013)05-0054-04
Abstract:BaTiO3 porous ceramics with layered structure were prepared by water based freeze casting technology.The effect of sintering temperature on the microstructure,shrinkage,po- rosity and dielectric properties of porous BaTiO3 was investigated and effect of kaolinite on sintering process was discussed.The results show that the shrinkage of sample with 4 wt% kaolinite content increased from 27% to 56% when temperature increased from 1 200 ℃ to 1 220 ℃,then porosity decreased from 78% to 56%.The shrinkage of sample with 8 wt% kaolinite content increased from 30% to 61% when temperature increased from 1 200 ℃ to 1 220 ℃,then porosity decreased from 72%to 39%.Kaolinite could decrease sintering tem- perature of porous ceramics.The pore size decreased and pore arrangement transformed from ordered structure to disordered structure with increase of sintering temperature.Porous ce- ramics with 8wt% kaolinite content would obtain layered structure when sintering at 1 200 ℃.The dielectric constant of sample was 130when kaolinite addition was 4wt% and sinte- ring at 1 220 ℃. Key words:sintering temperature;porosity;dielectric properties;porous ceramics
Effect of sintering temperature under high pressure in the uperconductivity for MgB2

a r X i v :c o n d -m a t /0102383v 1 [c o n d -m a t .s u p r -c o n ] 21 F eb 2001Effect of sintering temperature under high pressure in the superconductivity for MgB 2C.U.Jung,∗Min-Seok Park,W.N.Kang,Mun-Seog Kim,Kijoon H.P.Kim,S.Y.Lee,and Sung-Ik LeeNational Creative Research Initiative Center for Superconductivity and Department of Physics,Pohang University of Science and Technology,Pohang 790-784,Republic of Korea(February 1,2008)We report the effect of the sintering temperature on the superconductivity of MgB 2pellets prepared under a high pressure of 3GPa.The superconducting properties of the non-heated MgB 2in this high pressure were poor.However,as the sintering temperature increased,the superconducting properties were vastly enhanced,which was shown by the narrow transition width for the resistivity and the low-field magnetizations.This shows that heat treatment under high pressure is essential to improve superconducting properties.These changes were found to be closely related to changes in the surface morphology observed using scanning electron microscopy.PACS number:74.25.Fy,74.60.-w,74.70.Ad,74.72.-hThe recent discovery of superconductivity at about 40K in MgB 2has resulted in a surge of interest.1Conven-tional BCS superconductivity has been proposed for this compound,and a shift in the T c due to the boron iso-tope has been reported with an isotope critical exponent of αB ∼0.26.2,3The type of carrier has been predicted to be positive with boron planes acting like the CuO 2planes in cuprate high-temperature superconductors.4We demonstrated a hole-type carrier for MgB 2by us-ing Hall measurements.5Note that other transition metal borides,which are not superconducting,have been shown to have negative Hall coefficients.6,7Previously MgB 2was synthesized from a stoichiomet-ric mixture of Mg and B in a sealed Ta tube which was placed in a quartz ampoule at 950◦C.2,8,9However,these samples were found to be porous and mechanically weak.8,9Some have reported the synthesis of dense pel-lets sintered under high pressures of several GPa,10–12which makes it easy to study the transport properties.The physical properties for samples made at different pressures have been different from each other,10,11yet so far,the effect of the synthesis conditions on the super-conductivity has not been studied.Now the binary intermetallic compound MgB 2has be-come a strong candidate for superconductivity applica-tions because of its metallic nature and its simple struc-ture compared to oxide superconductors.Moreover,the compound is expected to be less anisotropic than layered high-temperature superconductors.However,the growth of a thin film has not yet been reported,the high melt-ing temperature of born being one of the major reasons.A proper target for synthesizing a thin film has not yet been fabricated.The most promising candidate is pulsed laser ablation technique,but large dense target is not yet available.13For large-scale device applications,as well as for small-scale electronic device applications,the relation between the synthesis conditions and the superconducting prop-erties should be well established.Previously,we reported the transport properties of hard and dense MgB 2sinteredat 950◦C under 3GPa.We found a clear difference in the resistivity as a function of the temperature and the mag-netic field between our sample prepared at high pressure and other bulk samples not prepared at high pressure.10The metallic nature of our sample could be inferred from its shiny surface.This sample was strong enough to pre-pare an optically clean and flat surface for a reflectivity measurement after polishing.In this paper we report the change in the resistiv-ity near T c ,the low-field magnetization,and the sur-face morphology of MgB 2with the sintering temperature at 3GPa.As the sintering temperature of the MgB 2pellet was increased from 500to 950◦C,the supercon-ducting transition width for a 10to 90%drop,∆T c ,de-creased systematically while the onset temperature,T co ,was nearly the same.Scanning electron microscope im-ages showed that these behaviors were accompanied by changes in the grain size and their connectivity.A 12-mm cubic multi-anvil-type press was used for the high-pressure sintering.14The starting material was a commercially available powder of MgB 2.15The pressed pellet was put into a Au capsule in a high-pressure cell and pressurized up to 3GPa.While the pressure was maintained,the heating was increased linearly;then,maintained at constant temperature for 2hours.The samples were then quenched to room temperature.The S(500),S(700),S(800),and S(950)in this paper were pellets sintered at 500,700,800,and 950◦C,respectively.The pellets,weighing about 130mg,were about 4.5mm in diameter and 3.3mm in height.For samples sintered at temperatures higher than 950◦C,the gold started to melt and to adhere strongly to the MgB 2.A dc SQUID magnetometer (Quantum Design,MPMS XL )and a field-emission scanning electron micro-scope (SEM)were used to investigate the low-field mag-netization and the surface morphology.For the resistiv-ity measurement,we cut the samples by using a diamond saw and then polished them into rectangular solid shapes with dimensions of about 1×1×4.5mm 3.The resistivity curve,R (T ),was measured by using a standard 4-probetechnique.N o r m a l i z e d R e s i s t i v i t yTemperature (K)FIG.1.Normalized resistivity of sintered MgB 2made un-der 3GPa.The resistivity values were normalized to 1.0at 40K,to observe the change in the superconducting tran-sition width with the sintering temperature.The solid cir-cles denoted by 20◦C are for the pellet which was pressur-ized without actual heating.The solid,dashed,dotted,and dash-dotted line are for the pellet sintered at 950,800,700,and 500◦C,respectively.Figure1shows the normalized resistivity of the sin-tered pellets near T c .The resistivity values were nor-malized to R(40K),just above T c ,for comparison.Thesolid circles represent the resistivity for the S(20)which was pressurized at 3GPa without subsequent heating for a conducting current path.The solid,dashed,dotted,and dash-dotted lines are for S(950),S(800),S(700),and S(500),respectively.As the sintering temperatures was increased from 500to 800◦C,the ∆T c decreased systematically,but the T co changed little.Also,the ∆T c of S(800)and S(950)were nearly the same,which indicates that the optimum sin-tering temperature region is wide under high pressure.8The absolute value of the resistivity at 40K of S(950)was nearly the same as that of S(800),but was about two times smaller than that of S(500).Figure 2shows the normalized magnetic susceptibil-ity,4πχ(T ),from the measured low-field magnetization of MgB 2.The solid circles are for the starting powder it-self.The solid,dashed,dotted,and dash-dotted lines are for S(950),S(800),S(700),and S(500),respectively.The lines for S(950)and S(800)nearly overlay each other.The pronounced hump around 30K shown for S(500)was due to a weak-link.This weak-link feature was also visible in the resistivity data in Fig.1.As the sintering tempera-ture was increased above about 700◦C,the weak-line fea-ture disappeared.These support that,in high pressure,originally-separated grains begin to develope a weak-link forms below 500◦C,and gradually a strong-link.This trend will be shown in the following paragraphs.The decrease in superconducting transition width is more ev-ident in the χZF C (T )measurement than in the resistiv-ity measurement.The field-cooling signal was found to mirror the χZF C (T );namely the pinning seems to be enhanced as the sintering temperature is increased.For samples sintered above 800◦C,the field-cooling signal was less than 0.5percent of the zero-field-cooling signal.FIG. 2.Normalized magnetic susceptibility from the low-field magnetization M (T )of sintered MgB 2made under 3GPa.The solid circles are for the as-purchased powder.With-out these data,the zero-field-cooling lines from the top cor-respond to the samples sintered at 500,700,800,and 950◦C,respectively.The curves for S(800)and S(950)nearly overlay each other.The pronounced hump around 30K shown for S(500)seems to be due to a weak-link.Figure 3shows SEM images of S(20),S(500),and S(950)with a magnification of 5,000.The scale bars are 1µm in length.The image in Fig.3(a)is for S(20).Here,we can clearly see separated grains and voids.The grain size is less than about 0.5µm.In Fig.3(b),some parts of the grains for S(500)adhered to each other while other parts of the grains remain isolated.In Fig.3(c),the S(950)pellet has grains that are very well con-nected with each other.We cannot even distinguish one grain from another over a wide area.Energy dispersive spectroscopy using SEM showed that gold used to wrap around the pellet smeared into the pellet by a depth of about 300µm for S(950).This feature was very helpful for attaching electric pads and could be another small advantage of this material for electrical applications.We observed well-interconnected changes in the trans-port and the magnetic properties,near T c ,which were accompanied by the microscopic changes in the observed surface morphology of MgB 2.The strong connection be-tween the grains with increasing sintering temperature seems to explain the change in the resistivity and the low-field magnetization.We are thankful for the SEM work to Mr.D.S.Kim at the Department of Material Science and Engineering.Discussion with Dong-Wook Kim on the film growth is also acknowledged.This work is supported by the Min-istry of Science and Technology of Korea through theCreative Research Initiative Program.FIG.3.SEM pictures of sintered MgB2made under3GPa.The scale bars are1µm in length.The sintering temperatureswere(a)20◦C,(b)500◦C,and(c)950◦C.The sample with-out actual heating,S(20),shows well-separated grains withspacious voids.As the sintering temperature is increased,theconnectivity of each grain increases and the porosity decreasesrapidly.。
SPS烧结Ti(C,N)基金属陶瓷的工艺研究--毕业设计论文

毕业设计(论文)题目SPS烧结Ti(C,N)基金属陶瓷的工艺研究学生姓名学号专业材料成型及控制工程班级指导教师评阅教师完成日期2012 年5 月23 日学位论文原创性声明本人郑重声明:所呈交的论文是本人在导师的指导下独立进行研究所取得的研究成果。
除了文中特别加以标注引用的内容外,本论文不包含任何其他个人或集体已经发表或撰写的成果作品。
本人完全意识到本声明的法律后果由本人承担。
作者签名:2012年5月17日学位论文版权使用授权书本学位论文作者完全了解学校有关保障、使用学位论文的规定,同意学校保留并向有关学位论文管理部门或机构送交论文的复印件和电子版,允许论文被查阅和借阅。
本人授权省级优秀学士学位论文评选机构将本学位论文的全部或部分内容编入有关数据库进行检索,可以采用影印、缩印或扫描等复制手段保存和汇编本学位论文。
本学位论文属于1、保密□,在_________年解密后适用本授权书。
2、不保密□`。
(请在以上相应方框内打“√”)作者签名:年月日导师签名:年月日目录摘要 (4)1 绪论 (6)1.1 Ti(C,N)基金属陶瓷 (6)1.1.1 Ti(C,N)基金属陶瓷介绍 (6)1.1.2 Ti(C,N)基金属陶瓷的结构与性能 (6)1.1.3 Ti(C,N)基金属陶瓷的显微组织 (7)1.1.4 Ti(C,N)基金属陶瓷的发展趋势与运用 (7)1.2 放电等离子烧结(SPS烧结) (8)1.2.1 放电等离子烧结介绍 (8)1.2.2 SPS(放电等离子烧结)的技术装置、原理及特点 (8)1.2.3 SPS技术在材料制备中的发展和运用 (10)1.2 研究的内容 (11)1.3 研究的技术路线 (12)1.4 研究的目的和意义 (12)2 研究SPS烧结Ti(C,N)金属陶瓷的实验方法 (15)2.1 Ti(C,N)金属陶瓷基体成分设计 (15)2.2 金属陶瓷基体材料的制备工艺 (15)2.3 性能测试 (16)3 Ti(C,N)基金属陶瓷显微组织的形成及特点 (17)3.1 普通真空烧结Ti(C,N)金属陶瓷的组织结构特点 (17)3.2 SPS烧结Ti(C,N)基金属陶瓷显微组织的形成及特点 (18)4 SPS烧结Ti(C,N)基金属陶瓷工艺研究 (22)4.1 SPS烧结工艺 (22)4.2 烧结温度对金属陶瓷组织和性能的影响 (23)4.3 升温速率对金属陶瓷组织和性能的影响 (25)4.4 保温时间对金属陶瓷组织和性能的影响 (27)4.5 SPS烧结工艺的确定 (29)5 全文小结 (30)致谢 (31)参考文献 (32)SPS烧结Ti(C,N)基金属陶瓷的工艺研究学生:指导老师:摘要:采用SPS烧结工艺制备了Ti(C,N)基金属陶瓷,研究了烧结温度、升温速率和保温时间对Ti(C,N)基金属陶瓷显微组织和力学性能的影响,并用SEM观察其断口形貌。
钨的扩散烧结温度

钨的扩散烧结温度钨是一种高熔点金属,具有良好的高温稳定性和机械性能,常用于高温部件、电子封接材料和切削工具等领域。
钨的扩散烧结是一种常用的制备方法,可以获得具有优异性能的钨制品。
本文将介绍钨的扩散烧结温度及相关参考内容。
钨的扩散烧结是指将粉末状的钨材料加热到高温,使颗粒之间发生扩散和液相烧结,形成致密的材料。
扩散烧结是一种重要的制备方法,能够获得高密度、高强度和高硬度的钨制品。
钨的熔点为3410℃,常温下为固态。
因此,要实现钨的扩散烧结,需要将钨材料加热到接近甚至高于其熔点的温度,以促进颗粒之间的扩散和液相烧结。
根据已有的文献和研究,钨的扩散烧结温度一般在2200℃至2500℃之间,具体的温度范围取决于钨材料的粒度、形状和添加剂等因素。
根据文献《Effect of sintering temperature on the properties of tungsten heavy alloy》中的研究,作者通过改变不同的烧结温度对重钨合金的性能进行了研究。
研究结果表明,在不同的烧结温度下,重钨合金的密度、硬度和屈服强度等性能均有所差异。
在烧结温度为2200℃时,重钨合金的相对密度达到了97%,而在2500℃时,相对密度进一步提高至99%。
研究还发现,随着烧结温度的升高,重钨合金的硬度和屈服强度也呈现出增加的趋势。
除了钨的扩散烧结温度对钨制品的性能影响外,研究还发现不同的添加剂和烧结方式对钨的扩散烧结过程和性能有重要的影响。
《Effects of sintering additives on densification of tungsten powder during multi-step sintering process》一文中,作者通过添加不同的烧结助剂对钨粉材料进行了扩散烧结研究。
研究发现,添加适量的助剂可以降低钨材料的烧结温度,提高烧结过程中的致密性和烧结效率。
总的来说,钨的扩散烧结温度一般在2200℃至2500℃之间,具体的温度范围取决于钨材料的粒度、形状和添加剂的种类与用量等因素。
烧结温度对陶瓷结合剂金刚石砂轮性能的影响

第37卷第7期 娃酸盐通报Vol.37 No.7 2018 年7 月________________BULLETIN OF THE CHINESE CERAMIC SOCIETY_____________________July,2018烧结温度对陶瓷结合剂金刚石砂轮性能的影响秦增锋\尹育航1>2,许鹏飞\刘凯2(1.西安建筑科技大学材料与矿资学院,西安710055;2.广东奔朗新材料股份有限公司,佛山528313)摘要:以金刚石和陶瓷结合剂为原料,以制备的陶瓷结合剂金刚石砂轮为研究对象,研究了烧结温度对其性能的影 响。
金刚石的热重(TG)和差示扫描量热(DSC)以及陶瓷结合剂的DSC、X射线衍射(XRD)和流动性的分析,确定 陶瓷结合剂金刚石砂轮试样的烧结温度上限。
通过对陶瓷结合剂金刚石砂轮试样的XRD、扫描电子显微镜 (SEM)、开口气孔率、弯曲强度和洛氏硬度的检测和分析,研究其最佳的烧结温度和微观结构。
结果表明,实验所 用的金刚石开始氧化温度为662.13 T:,完全氧化温度为888.00 T:。
陶瓷结合剂的玻璃转化温度是774.03 T:。
烧 结温度在740 t时,陶瓷结合剂未与金刚石发生化学反应。
温度升高时,结合剂的流动性增大,陶瓷结合剂金刚石 砂轮试样的开口气孔率也增大。
在烧结温度为700 T:时,试样的弯曲强度(84. 11 MPa)和洛氏硬度(87.66 HRB)达到最大值,金刚石之间的结合剂“桥”更致密,结合剂与金刚石之间润湿性更好,形成有合适气孔的整体。
关键词:烧结温度;陶瓷结合剂;陶瓷结合剂金刚石砂轮试样中图分类号:TG74 文献标识码:A文章编号:1001-1625(2018)07-2152-05 Effect of Sintering Temperatures on Properties of VitrifiedBond Diamond WheelsQIN Zeng-feng1, YIN Yu-hangia ,XU Peng-fei1 ,LIU Kai(1. College of Materials and Mineral Resource,Xi ’ an University of Architecture and Technology,Xi ’ an 710055,China;2. Monte-Bianco Diamond Applications Co.,Ltd.,Foshan 528313, China)Abstract : The effect of sintering temperature on the properties of vitrified bond diamond wheels consisting of diamond and vitrified bond and as research project was investigated. The analysis thermogravimetric (TG) and differential scanning calorimetry ( DSC) of diamond and DSC, X-ray diffraction ( XRD) and the fluidity of vitrified bond can determine the upper limit of sintering temperature of vitrified bond diamond wheels samples. The optimum sintering temperature and microstructure of vitrified bond diamond wheels samples can be investigated by tests and analysis of XRD, scanning electron microscopy ( SEM), open porosity, bending strength and Rockwell hardness. The beginning of the oxidized temperature of the experimental diamond is 662. 13 Tl and completely oxidized temperature is 888. 00 T l. Transitioned temperature of the glass of vitrified bond is 774. 03 T l. As the sintering temperature of the vitrified bond diamond wheels samples is 740 ,the vitrified bond does not react with the diamond. The fluidity of vitrified bond adds and the open porosity of vitrified bond diamond wheels samples increases with the increasing of sintering temperatures. Meanwhile, as the sintering temperature is 700 Tl , the bending strength (84. 11 MPa) and the Rockwell hardness (87.66 HRB) of the samples are the highest and the bridges of vitrified bond between the diamonds are denser and the wettability between vitrified bond and the diamond is better, forming a whole with suitable porosity.Key words :sintering temperature ;vitrified bond ;vitrified bond diamond wheels sample1引言金刚石砂轮广泛的应用于材料的磨削加工如冶金,陶瓷等行业。
烧结温度和钙含量对CaNdTiNbO7型陶瓷固化体晶相结构的影响

第38卷 第2期 2023年6月 西 南 科 技 大 学 学 报 JournalofSouthwestUniversityofScienceandTechnology Vol.38No.2 June2023DOI:10.20036/j.cnki.1671 8755.2023.02.002收稿日期:2022-10-08;修回日期:2022-12-07基金项目:国家自然科学基金(12105235,22176157,U2167221);四川省科技计划项目(2021JDTD0019);西南科技大学博士基金(20zx7146)作者简介:第一作者,许保亮(1986—),男,博士研究生,助教,研究方向为高放废物陶瓷固化;通信作者,段涛(1976—),男,博士,教授,研究方向为纳米功能材料、ICF靶物理与材料、核工程材料与化学,E mail:duant@ustc.edu.cn;通信作者,吉诗银(1993—),男,博士,副教授,研究方向为高放废物陶瓷固化及材料粒子束辐照效应,E mail:jishy@swust.edu.cn烧结温度和钙含量对CaNdTiNbO7型陶瓷固化体晶相结构的影响许保亮1,2,3,4 黄建秋2,3 吴俊翔2,3 吉诗银2,3,4 熊 鹰1 段 涛2,3,4(1.西南科技大学材料与化学学院 四川绵阳 621010;2.西南科技大学环境友好能源材料国家重点实验室 四川绵阳 621010;3.西南科技大学核废物与环境安全省部共建协同创新中心 四川绵阳 621010;4.西南科大四川天府新区创新研究院 成都 610299)摘要:萤石及其衍生结构陶瓷是高放废物固化的潜在基体材料,针对烧绿石型高放废物固化体CaNdTiNbO7存在缺陷萤石相和钙钛矿杂相问题,设计了一系列温度与Ca含量效应实验,通过传统高温固相法在1000~1600℃下合成CaNdTiNbO7固化体样品,并在1400℃合成Ca0.99NdTiNbO6.99和Ca0.9NdTiNbO6.9陶瓷,通过XRD和SEM-EDS研究烧结温度与钙含量对合成CaNdTiNbO7型纯相烧绿石固化体的影响。
温度对半导体影响的书

温度对半导体影响的书英文回答:The effect of temperature on semiconductors is acrucial aspect to consider in the field of electronics. As temperature changes, it can have both positive and negative impacts on the performance and reliability of semiconductor devices.One of the main effects of temperature on semiconductors is the change in electrical conductivity. Generally, as temperature increases, the conductivity of a semiconductor also increases. This is due to the increased thermal energy, which allows more charge carriers to move freely within the material. As a result, the resistance of the semiconductor decreases, and it becomes more conductive.However, this positive effect of temperature on conductivity can also have negative consequences. For instance, if the temperature rises too high, it can lead tothermal runaway, where the increased conductivity causes excessive heating and further increases the temperature. This can ultimately result in the device failing or even burning out.Another important effect of temperature on semiconductors is the impact on bandgap energy. The bandgap energy is the energy difference between the valence band and the conduction band in a semiconductor. At higher temperatures, the bandgap energy decreases, which meansthat the semiconductor becomes more conductive and allows more charge carriers to move across the bandgap. This can affect the performance of devices such as diodes and transistors, as it can lead to increased leakage currents and reduced efficiency.Furthermore, temperature can also affect the mobility of charge carriers in semiconductors. Mobility refers to the ease with which charge carriers can move through the material. At higher temperatures, the mobility of both electrons and holes in a semiconductor generally increases. This can lead to improved device performance, as the chargecarriers can move more freely and quickly. However, at extremely high temperatures, the mobility can besignificantly reduced due to scattering effects, which can negatively impact device performance.In addition to these electrical effects, temperaturecan also affect the mechanical properties of semiconductors. For example, as the temperature changes, the coefficient of thermal expansion of the semiconductor material can cause stress and strain in the device. This can lead to mechanical failure or even cracking of the semiconductor.中文回答:温度对半导体的影响是电子领域中需要考虑的一个关键因素。
- 1、下载文档前请自行甄别文档内容的完整性,平台不提供额外的编辑、内容补充、找答案等附加服务。
- 2、"仅部分预览"的文档,不可在线预览部分如存在完整性等问题,可反馈申请退款(可完整预览的文档不适用该条件!)。
- 3、如文档侵犯您的权益,请联系客服反馈,我们会尽快为您处理(人工客服工作时间:9:00-18:30)。
Effect of sintering temperature on aging resistance and mechanical properties of 3Y-TZP dental ceramicsZHANG Jingchao1,2, LIAO Yunmao1,2, LI Wei1,2,*, JIANG Li1,2, ZHAO Yongqi1,2, YUNXiaofei1,2(1. West China College of Stomatology, Sichuan University, Chengdu, 610041, China; 2. State Key Laboratory of Oral Diseases,Sichuan University, Chengdu, 610041, China)Abstract:In order to investigate the effect of sintering temperature on aging properties and mechanical properties of 3Y-TZP dental ceramics in a simulated oral environment, 3Y-TZP nanopowder compacts were prepared by pressureless sintering at 1350℃,1400℃,1450℃,1500℃, respectively, then treated by soaking in artificial saliva (65℃,pH=7) for two months. The treated specimens sintered at 1350℃showed no phase transformation but significantly improved strength and toughness(P<0.05), while those sintered at 1400℃-1500℃revealed a small amount of phase transformation and insignificant mechanical reinforcement (P>0.05). No micro-cracks were detected but increase in lattice volume was found in all specimens. Lowering sintering temperature favors aging resistance and mechanical reinforcement of 3Y-TZP in simulated oral environment.Key words:3Y-TZP; dental ceramic; sintering temperature; simulated oral environment; low temperature degradation1 IntroductionAll-ceramic dental restorations have become more and more important due to their favorable esthetics and outstanding biological compatibility when compared with metal and resin restorations. In particular, 3mol% yttria-stabilized tetragonal zirconia polycrystal (3Y-TZP) attracts the most attention due to exceptionally high strength and toughness, which provides the base for applications in multi-unit fixed partial dentures and dental implant abutments. The superior mechanical properties of 3Y-TZP are related to the stress-induced phase transformation of tetragonal zirconia into monoclinic symmetry (t-ZrO2→m-ZrO2) accompanied by an volume expansion of ~4% that opposes the crack propagation, which is called transformation toughening [1].Unfortunately, Y-TZPs are susceptible to various environment such as humid air, water vapor and other fluids over a temperature range of 65℃-500℃. This phenomena, is calledlow-temperature degradation (LTD), which is related to the metastability of the t-ZrO2 at low temperature and is responsible for the formation of micro-cracks and deterioration of mechanical properties [2,3]. There are many mechanisms that have been put forward to explain LTD of Y-TZP ceramics. It is worth mentioning the mechanism proposed by Lange et al. and confirmed later by Li et al. using X-ray photoelectron spectroscopy (XPS) analysis [4,5]. These authors proposed that there was a reaction between water molecules and Y2O3 at the surface of Y-TZP resulting in the formation of small crystallites of Y(OH)3 of nanometric size (20–50nm). Thus, a tetragonal surface grain is destabilized and transforms into the monoclinic structure when water vapor draws out a sufficient amount of yttrium. After this, growth of monoclinic sites can continue spontaneously without further yttrium diffusion. Oral cavity is a moist environment in which temperature varies frequently with the food-intake. Although the above mechanism is usually veryslow at oral temperatures, it may lead to a significant decrease in the strength of dental restorations over periods of several decades [6]. Thus, determining the influence of LTD to mechanical properties in simulated oral environment is prerequisite to predicting the sustainable success of Y-TZP-based restorations in dentistry.Though LTD of densely-sintered 3Y-TZP is well documented in the literature [7], the LTD of3Y-TZP with compromised density and its effect on mechanical properties are still not yet well known. In fact, most 3Y-TZP restorations in dental clinics are not densely sintered due to limitations in time, technique, equipment, etc during fabrication process. Moreover, prefabricated 3Y-TZP bulks manufactured by different companies show different degree of densification. In this study, 3Y-TZP sintered at 1350℃, 1400℃, 1450℃, 1500℃, respectively, were exposed to simulated oral environment (artificial saliva, 65℃,pH=7)in vitro for 2 months. The phase composition, microstructure and mechanical properties of the treated specimens were examined.2 Experiments2.1 Preparation of 3Y-TZP specimensThe fabrication of bulk ceramics was established with a commercially availablebiomedical-grade 3Y-TZP nanopowder (TZ-3YB-E, Tosoh, Japan) containing 3mol% yttria,0.25wt% alumina and 3wt% organic binder. The powder was dual phase including 23wt% monoclinic phase and 77wt% tetragonal phase. Green compacts were fabricated by mold-pressing under 80MPa following cold isostatic pressing under 200MPa. Four sets of bar compacts (n=40 in each set) were randomly grouped then sintered in air at 1350℃, 1400℃, 1450℃and 1500℃, respectively, for 1.5 h at a heating rate of 5℃/min, in order to obtain 3Y-TZP specimens with different microstructural features (grain size and relative density). All sintered specimens were ground with sand paper in a stepwise process. Finally, the standard specimens with final dimensions of 18mm×4mm×2mm were polished with a diamond paste of 1μm particles, then washed and annealed at 920℃for 1 h.2.2 Aging treatmentArtificial saliva was prepared according to the recipe in ISO/TR 10271 [8]. The pH of the solution was adjusted to 7 with 0.5 mol/L NaOH and 30% acetic acid.The specimens sintered at each temperature were randomly divided into 2 groups of 20 each and subjected to different process: (a) control group, the specimens were analyzed without any treatment; (b) experimental group, the specimens were subjected to aging treatment by soaking in artificial saliva at 65℃for 2months, then washed in deionized water, dried and analyzed.2.3 CharacterizationThe bulk density of the specimens in control group was measured by the Archimedes method in distilled water at 20℃at standard atmospheric pressure(ρwater=0.998g/cm3), and the relative density was determined correlating the bulk density with theoretical density (D T = 6.1 g/cm3). Average grain size of the specimens was measured by the planimetric method using scanning electron microscopy (SEM) (Model S-4500, Hitachi, Tokyo, Japan).The phase composition of all specimens was determined using X-ray diffraction (XRD) (Philips X’Pert System, Almelo, Overijssel, Netherlands) using Cu-Kα radiation in the range of15°–70°(2θ), with a step width of 0.02°and 3 s of exposure time per position. The volume fraction of the monoclinic phase on the surface of the specimens, X m, was calculated using the following equation [16]:where (111)mI ,_(111)m I and (111)t I were the integrated intensity from the monoclinic (111),monoclinic _(111) and the tetragonal (111) peaks, respectively. The predicted microcracks resulted from phase transformation in experimental group were detected by atomic forcemicroscope (AFM) (Model CH-3, Shimadzu Corporation, Kyoto, Japan).2.4 Mechanical testMechanical test was carried out using a universal testing machine (Fast Track 8874, Instron, UK) at room temperature. The bending strength of all specimens (10 for each subgroup) was measured by three-point bending with a span of 15 mm and a crosshead rate of 0.5 mm/min. Their fracture toughness (10 specimens for each subgroup) was measured by the single-edge-notched-beam method (SENB) with a notch thickness of 0.2 mm, a span of 15 mm, and crosshead rate of 0.05 mm/min. The data were evaluated by statistical analysis (SPSS 11.0) using One-way ANOVA and LSD test to compare the strength and toughness values among the groups. P<0.05 was considered as significant.3 Results and Discussion3.1 CharacterizationTable 1 summarizes the results of relative density and average grain size of 3Y-TZP specimens in control group. Below 1450℃, the density increased gradually with the sintering temperature rising and almost fully dense specimens with a relative density of 99.64% were obtained at1450℃. Afterwards, remarkable decrease in density was revealed in specimens sintered at 1500℃, indicating rapid grain growth and recrystallization at high temperature.Table 1 The relative density and average grain size of as-sintered 3Y-TZP against sintering temperature Sintering temperature (℃)1350 1400 1450 1500 Relative density (%)95.95 98.96 99.64 99.07 Average grain size (nm) 198.4 248.3 295.3 423.1 As shown in Fig.1, XRD analysis revealed monophase t-ZrO 2 in all as-sintered specimens regardless of sintering temperature. After treatment, both t-ZrO 2 and transformation-produced m-ZrO 2 were found in all specimens except those sintered at 1350℃, suggesting a critical grain size larger than the 198.4nm in simulated oral environment. Table 2 presented the quantitative results of the degree of phase transformation. With sintering temperature rising, the amount of monoclinic phase increased and the most intensive phase transformation was found in specimens sintered at 1500℃ due to the largest grain size. Besides, the cell volume of tetragonal grains in each subgroup decreased after treatment regardless of sintering temperature as shown in Table 3. According to the research by Lange et. al., whether t-ZrO 2 transforms to monoclinic structure or not, grain boundary segregation of yttrium ions (yttrium diffusion) is inevitable for Y-TZPs exposed to aqueous solution [4]. 3Y-TZP is substitutional solutes and the ionic radii of Y 3+(0.089nm )is larger than that of Zr 4+(0.079nm ), yttrium diffusion undoubtedly lead to the cell volume reduction of t-ZrO 2, which was confirmed in this study.__(111)+(111)=(111)+(111)+(111)m mm m m tI I X I I I (1)Fig.1 XRD spectrum of 3Y-TZP specimens sintered at the temperature range 1350℃-1500℃. (a) Control group;(b) Experimental group。