课程设计---设计一座年产制钢生铁(L08)280万吨的高炉
年产280万吨1810热轧带钢车间设计毕业设计说明书
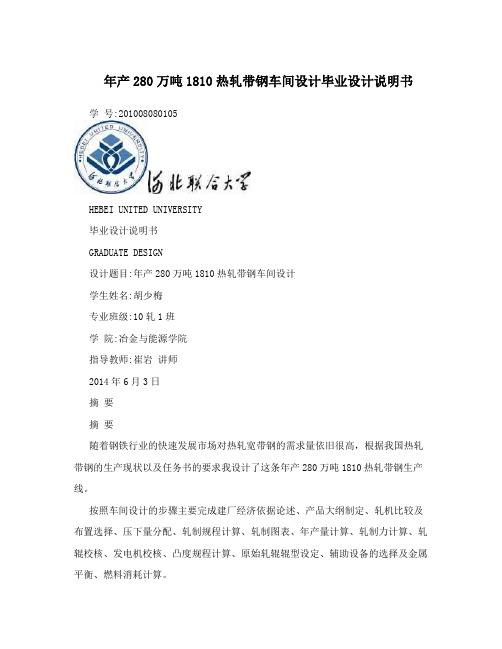
年产280万吨1810热轧带钢车间设计毕业设计说明书学号:201008080105HEBEI UNITED UNIVERSITY毕业设计说明书GRADUATE DESIGN设计题目:年产280万吨1810热轧带钢车间设计学生姓名:胡少梅专业班级:10轧1班学院:冶金与能源学院指导教师:崔岩讲师2014年6月3日摘要摘要随着钢铁行业的快速发展市场对热轧宽带钢的需求量依旧很高,根据我国热轧带钢的生产现状以及任务书的要求我设计了这条年产280万吨1810热轧带钢生产线。
按照车间设计的步骤主要完成建厂经济依据论述、产品大纲制定、轧机比较及布置选择、压下量分配、轧制规程计算、轧制图表、年产量计算、轧制力计算、轧辊校核、发电机校核、凸度规程计算、原始轧辊辊型设定、辅助设备的选择及金属平衡、燃料消耗计算。
设计中参阅了国内外有关的先进工艺轧机的设备、技术及一些辅助设备的论述特别参考了本钢1700、唐钢1700、鞍钢1780等热轧带钢生产参数和现场数据,使本设计车间达到工艺合理、设备先进,为今后车间的后续发展创造条件。
本设计车间能生产的带钢品种多、规格齐全。
产品规格为1.5~18mm,典型产品为5mm。
设计附有车间平面图。
关键词:1810热轧带钢;车间设计;CVC轧机;HC轧机I目录AbstractWith the development of iron industry, the market requirement forhot rolled broad steel is still in a high level. According to the modern state of iron industry of our country and the task requirements, I designed this hot-rolling workshop for an annual output of 2.8 million tons.Steps in accordance with the workshop design, I mainly complete building of economy, the product outline of the development, comparison and mill layout options, press distribution, the calculation of order rolling, rolling chart, annual terms, the calculation of rolling force and roll strength, the electrical heat check, crown of order, the original roll-type settings, the choice of auxiliary equipment and the calculation of fuel consumption.Refer to the design of domestic and foreign advanced technology of the rolling mill, rolling mill equipment, technology and some discussionof auxiliary equipment, especially reference to the Anshan Iron and Steel hot-rolled sheet production line parameters, making the design process to achieve a reasonable workshop, advanced equipment, and making rooms for the future development.The steel plant can produce more complete specifications. Theproduct specifications range 1.5 to18mm.Keywords: 1810 hot-rolling; workshop design; CVC rolling mill; HC rolling millII目录目录摘要...................................................................... . (I)Abstract ........................................................... .. (II)第1章绪论...................................................................... ....................................... - 1 -1.1 热轧带钢的发展 ..................................................................... ............................. - 1 -1.2 热轧带钢生产工艺 ..................................................................... ......................... - 2 -1.2.1 热轧带钢的应用性 ..................................................................... ................... - 2 -1.2.2 热轧带钢的发展趋势及特点 ..................................................................... ..... - 4 - 1.3本课题的来源 ..................................................................... ................................. - 8 -1.4本文主要内容 ..................................................................... ................................. - 9 -1.5 本章小结 ..................................................................... ....................................... - 9 -第2章建厂依据及产品大纲...................................................................... ......... - 10 -2.1建厂依据 ..................................................................... .......................................- 10 -2.1.1可行性研究 ..................................................................... ............................ - 10 -2.1.2 地理与资源 ..................................................................... ........................... - 10 - 2.2 产品大纲 ..................................................................... ...................................... - 11 -2.2.1 产品大纲的编制原则 ..................................................................... ............. - 11 -2.2.2产品大纲...................................................................... ............................... - 11 -2.2.3 产品规格 ..................................................................... ............................... - 11 -- 2.5本章小结 ..................................................................... .......................................- 12第3章生产工艺流程制定...................................................................... ............. - 13 -3.1 制定生产工艺流程的主要依据 ..................................................................... .......- 13 -3.2 生产工艺简介 ..................................................................... ...............................- 14 -3.3 本章小结 ..................................................................... ......................................- 15 -第4章坯料的选择...................................................................... ......................... - 16 -4.1 坯料的种类 ..................................................................... ...................................- 16 -4.2 坯料的尺寸 ..................................................................... ...................................- 16 -4.3 坯料的材质 ..................................................................... ...................................- 16 -4.4 坯料表面的缺陷清理 ..................................................................... .....................- 17 -4.5 本章小结 ..................................................................... ......................................- 17 -第5章主要设备的选择与布置...................................................................... ..... - 18 -5.1 轧机的选择 ..................................................................... ...................................- 18 -5.1.1 粗轧机的选择 ..................................................................... ........................ - 18 -5.1.2精轧机的选择...................................................................... ........................ - 23 - 5.2保温装置 ..................................................................... .......................................- 34 -5.2.1保温装置的概述 ..................................................................... ..................... - 34 -5.2.2 保温装置的选择 ..................................................................... .................... - 35 - 5.3本章小结 ..................................................................... .......................................- 35 -第6章典型产品的压下规程设计....................................................................... - 36 -6.1 压下规程设计 ..................................................................... ...............................- 36 -6.1.1 轧制道次选择 ..................................................................... ........................ - 37 -6.1.2 粗轧机组压下量分配 ..................................................................... ............. - 37 -III目录6.1.3 精轧机组的压下量分配 ..................................................................... .......... - 38 - 6.1.4 校核咬入能力 ..................................................................... ........................ - 39 - 6.2 确定速度制度 ..................................................................... ...............................- 39 -6.2.1 粗轧速度制度 ..................................................................... ........................ - 39 - 6.2.2 粗轧延续时间 ..................................................................... ........................ - 39 - 6.2.3 精轧速度制度确定 ..................................................................... ................. - 40 - 6.2.4 精轧轧制延续时间 ..................................................................... ................. - 40 - 6.3 轧制温度的确定 ..................................................................... ............................- 41 -6.3 本章小结 ..................................................................... ......................................- 43 -第7章力能参数的计算...................................................................... ................. - 44 -7.1 轧制力的计算 ..................................................................... ...............................- 44 -7.1.1 粗轧段轧制力计算 ..................................................................... ................. - 44 - 7.1.2 精轧段轧制力计算 ...................................................................................... - 45 - 7.1.3 各机架的空载辊缝设定: .................................................................... ....... - 46 - 7.2 轧制力矩的计算 ..................................................................... ............................- 47 -7.3 附加摩擦力矩的计算 ..................................................................... .....................- 49 -7.4 空转力矩的计算 ..................................................................... ............................- 50 -7.5 动力矩的计算 ..................................................................... ...............................- 51 -7.6 轧辊辊型设计 ..................................................................... ...............................- 52 -7.6.1 各架出口凸度的确定 ..................................................................... ............. - 53 - 7.6.2 热膨涨热凸度 ..................................................................... ........................ - 53 - 7.6.3 轧辊挠度曲线 ..................................................................... ........................ - 54 - 7.6.4 凸度分配 ..................................................................... ............................... - 55 - 7.7 本章小结 ..................................................................... ......................................- 55 -第8章轧辊强度的校核与电机的选择............................................................... - 56 -8.1 综述 ..................................................................... .............................................- 56 -8.2 轧辊强度校核 ..................................................................... ...............................- 56 -8.2.1 支承辊强度校核 ..................................................................... .................... - 56 - 8.2.2 工作辊的校核 ..................................................................... ........................ - 58 - 8.2.3工作辊与支撑辊间的接触应力 ..................................................................... - 60 - 8.3 电机的选择 ..................................................................... ...................................- 63 -8.3.1轧制过程中静负荷图的制定...................................................................... ... - 63 - 8.3.2主电机的校核...................................................................... ........................ - 65 - 8.4本章小结 ..................................................................... .......................................- 66 -第9章轧机产量的计算...................................................................... ................. - 67 -9.1轧机小时产量 ..................................................................... ................................- 67 -9.2轧机平均小时产量 ..................................................................... .........................- 68 -9.3轧钢车间年产量计算 ..................................................................... .....................- 68 -9.4本章小结 ..................................................................... .......................................- 69 -第10章辅助设备的选择...................................................................... ............... - 70 -10.1热炉选择 ..................................................................... .....................................- 70 -10.1.1加热能力的确定 ..................................................................... ................... - 71 - 10.1.2炉子数量的确定 ..................................................................... ................... - 71 -IV目录10.1.3炉子尺寸的确定 ..................................................................... ................... - 71 - 10.2除鳞装置的选择...................................................................... ..........................- 72 -10.2.1除鳞的必要性 ..................................................................... ....................... - 72 - 10.2.2各种除鳞方式的比较 ..................................................................... ............ - 73 - 10.2.3本次设计除鳞装置的选择 ..................................................................... ..... - 73 - 10.3剪切设备的选择...................................................................... ..........................- 74 -- 75 - 10.4带钢冷却装置 ..................................................................... ..............................10.5卷取设备的选择...................................................................... ..........................- 77 -10.6辊道的选择...................................................................... .................................- 78 -10.7活套支撑器...................................................................... .................................- 79 -10.7.1概述 ..................................................................... ..................................... - 80 - 10.7.2活套支撑器的相关参数的计算 ................................................................... - 81 - 10.8控制设备 ..................................................................... .....................................- 82 -10.8.1厚度控制 ..................................................................... .............................. - 82 - 10.8.2板形控制 ..................................................................... .............................. - 84 - 10.8.3宽度控制 ..................................................................... .............................. - 85 - 10.9本章小结 ..................................................................... .....................................- 86 -第11章轧钢车间平面布置及经济技术指标..................................................... - 87 -11.1轧钢车间平面布置 ..................................................................... .......................- 87 -11.2车间技术经济指标 ..................................................................... .......................- 87 -11.2.1各类材料消耗指标 ..................................................................... ................ - 87 - 11.2.2综合技术经济指标 ..................................................................... ................ - 89 - 11.3本章小结 ..................................................................... .....................................- 91 -结论...................................................................... ............................................... - 92 -参考文献...................................................................... ........................................... - 93 -谢辞...................................................................... ............................................... - 95 -V第1章绪论第1章绪论1.1 热轧带钢的发展改革开放之前中国热轧带钢轧机只有鞍钢建国初期由前苏联援建的鞍钢1700半连轧机和20世纪70年代武钢从日本引进的3/4连续式1700热连轧机,技术水平与国际上有很大的差距。
年产值刚生铁450吨的高炉车间中高炉内型设计

课程设计说明书题目名称:年产值钢生铁450吨的高炉车间中高炉内型设计系部:机械系工程系专业班级:学生:学号:指导教师:完成日期:新疆工程学院课程设计评定意见设计题目系部_________________ 专业班级学生_________________ 学生学号评定意见:评定成绩:指导教师〔签名〕:年月日新疆工程学院____________系(部)课程设计任务书学年学期年月日教研室主任〔签名〕系〔部〕主任〔签名〕目录前言 (1)配料计算方法 (3)配料计算原始条件 (3)吨铁简易配料计算 (5)物料平衡计算方法 (10)物料平衡计算的原始条件 (10)吨铁物料平衡计算 (10)高炉内型设计方法 (15)炉缸 (15)炉腹 (16)炉身 (17)炉腰 (17)炉喉 (17)死铁层厚度 (18)高炉内型计算 (18)高炉内型图 (20)参考资料 (21)一、前言近年来,随着我国经济的快速发展,在基础设施建设,,比上年度增长15.19%,占世界总产量的49.74%,08年全国生铁产量4.7067亿t,炼铁生产能力超过6亿t,09年全国生铁产量达5.4375亿t,但有6000万t/年的生产能力居于淘汰之列〔主要是300m³以下容积小高炉〕。
在产量不断增长的同时,我国的高炉炼铁技术也取得了较大的进步,入炉焦比和炼铁工序能耗不断下降,喷煤比、热风温度和利用系数也不断提高,高炉操作技术也日趋成熟,各项技术经济指标得到进一步改善。
我国现有高炉1300多座,大于1000m3以上容积的高炉有150多座。
近年来,高炉大型化的步伐加快,宝钢建成三座4 000m³级的高炉,另外已建成和在建的7 座4000m³级高炉以及首钢曹妃甸2座5500 m³高炉。
大型高炉均采用了先进的技术装备,一大批成熟高新技术和装备的应用大大降低了生产成本和劳动强度,自动化程度也进一步提升,生产环境有了很大改善,企业生产效率和经济效益得到明显提高。
《高炉本体设计》课件

高炉本体设计流程
1
高炉结构分析
2
通过结构分析,评估高炉本体的承载能
力和稳定性,并确定设计参数。
3
结构优化和方案选择
4
进一步优化高炉本体设计,选择最合适 的方案以实现高炉的高效运行。
设计流程概述
设计高炉本体的流程包括需求分析、结 构分析、设计和方案选择等多个阶段。
高炉本体结构设计
根据结构分析的结果,设计高炉本体的 具体细节和构造方式。
关键技术及应用
壳体结构材料选择
钢铁高炉壳体由特殊耐火材料构 成,能够抵御高温和化学腐蚀。
高炉内部构件设计
高炉内部构件的设计需要考虑耐 磨、耐高温和保护钢铁质量等因 素。
高炉维护与检修
高炉维护和检修是确保高炉长期 稳定运行的关键,需要定期进行。
总结
1 设计的重要性
高炉本体设计对于钢铁生产具有重要意义, 直接关系到工艺效率和产品质量。
பைடு நூலகம்
2 总结与展望
本课件详细介绍了高炉本体设计的内容和流 程,并展望了未来的发展方向。
参考文献
1. 钢铁行业标准化委员会. 高炉本体设计技术规范[M]. 北京:中国标准出版社, 2018。
2. Smith, John. Blast Furnace Design: Principles and Practice[M]. London: Steel Publishing, 2019.
高炉本体设计案例分享
1 国内案例
中国在高炉本体设计领域取得了丰硕成果,例如某钢铁集团的高炉本体设计。
2 国外案例
国外也有很多优秀的高炉本体设计案例,比如日本的某钢铁公司的高炉。
年产200万吨炼钢生铁的高炉炼铁车间

毕业设计(论文)任务书冶金与能源工程学院冶金工程专业 2008 级学生:宝富毕业设计(论文)题目:根据昆钢原、燃料条件,设计一座年产炼钢生铁200万吨的高炉炼铁车间毕业设计(论文)容:1.主要技术经济指标选择与论证;2.炼铁全计算(配料计算;物料平衡与热平衡计算);3.炉座规划、炉型计算;4.炉体结构设计与主要附属设备选型;5.绘制车间平面布置图、车间纵剖面图各一;6.编制设计说明书一份。
专题(子课题)题目:专题(子课题)容:毕业设计(论文)指导教师(签字):主管教学院(部)长(签字):年月日年产200万吨炼钢生铁的高炉炼铁车间设计说明书编制人: 宝富学号: 0专业: 冶金工程年级: 2008级学院: 冶金与能源工程学院指导教师: 丁跃华指导教师职称: 教授指导教师单位: 冶金与能源工程学院提交日期:2012年6月1日Design Specificationon a Blast Furnace Iron-making Plantwith Annual Capacity of 2.0 Million Tons of Hot MetalDesigner:School Number:Specialty:Grade:Faculty: YangBaoFu 0Metallurgical Engineering2008Metallurgical Engineering and energy, KUSTSupervisor:Title:Set-up: Ding YuehuaProfessorEngineering,KUST Faculty of Metallurgical and energySubmission Date: Jun. 1, 2012目录摘要VIABSTRACTVII前言IX第一章高炉炼铁设计11.1高炉炼铁设计概述11.1.1 高炉炼铁的发展现状11.1.2 高炉炼铁生产工艺流程31.1.3 高炉与其附属设备41.2高炉炼铁设计的基本原则51.2.1 高炉炼铁设计应遵循的基本原则51.2.2 钢铁厂的组成61.3设计任务61.4高炉生产主要技术经济指标71.5设计所采用的先进技术101.6高炉炼铁厂的厂址选择12第二章高炉炼铁综合计算132.1原始资料142.2配料计算162.2.1 铁矿石用量的计算162.2.2渣量与炉渣成分的计算192.3物料平衡计算222.3.1 鼓风量的计算22G的计算262.3.2鼓风质量b2.3.3 煤气量的计算272.3.4煤气中水蒸气量的计算322.3.5考虑炉料的机械损失后的实际入炉量322.3.6编制物料平衡表332.4高炉热平衡计算342.4.1热量收入的计算342.4.2热量支出的计算37第三章高炉炼铁车间设计453.1高炉座数与容积确定453.1.1 生铁产量的确定453.1.2 高炉炼铁车间总容积的确定453.1.3 高炉座数的确定463.2高炉炼铁车间平面布置463.2.1 高炉炼铁车间平面布置应遵循的原则463.2.2 高炉炼铁车间平面布置形式473.3高炉车间劳动定员47第四章高炉本体设计494.1高炉炉型494.1.1 五段式高炉炉型494.1.2 炉型设计与计算554.2高炉炉衬594.2.1 炉衬破损机理594.2.2 高炉用耐火材料的选择634.2.3 高炉炉衬的设计与砌筑65 4.3高炉冷却设备714.3.1 冷却设备的作用714.3.2 冷却介质714.3.3 高炉冷却结构形式724.3.4 高炉给排水系统774.3.5 高炉冷却系统784.4高炉送风管路794.4.1热风围管804.4.2 送风支管804.4.3 直吹管814.4.4 风口装置824.5高炉钢结构844.5.1 高炉本体钢结构854.5.2 炉壳864.5.3 炉体框架874.6高炉基础874.6.1 高炉基础的负荷874.6.2 对高炉基础的要求88第五章附属设备系统895.1供料系统895.1.1 贮矿槽、贮焦槽与槽下运输称量895.1.2 皮带运输925.2装料设备935.2.1 并罐式无钟炉顶装料设备935.2.2 探料装置965.3送风系统975.3.1 高炉鼓风机975.3.2 热风炉1005.3.3 提高风温的途径1035.4煤粉喷吹系统1045.4.1 煤粉制备工艺1055.4.2 喷吹工艺1075.5煤气处理系统1085.5.1 重力除尘器1095.5.2 溢流文氏管1115.5.3 脱水器1115.6渣铁处理系统1125.6.1 风口平台与出铁场设计1125.6.2 炉前主要设备1145.6.3 铁水处理设备1165.6.4 炉渣处理设备116第六章能源回收利用和环境保护118 6.1高炉炉顶余压发电1186.2热风炉烟道废气余热回收119 6.3环境保护120第七章成本核算1217.1营业收入1217.2成本费用估算122结论124总结与体会125辞126参考文献126附录一(英文原文)127附录二(翻译)146摘要本论文是根据昆钢原、燃料条件,设计一座年产200万吨炼钢生铁的高炉炼铁车间。
高炉本体尺寸设计
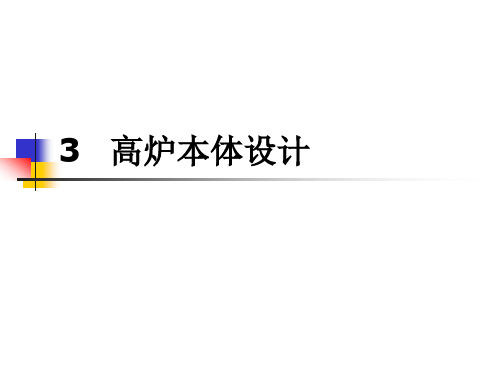
1. 比较法:
由给定的产量确定炉容,根据建厂的冶炼 条件,寻找条件相似,炉容相近,各项生产技 术指标较好的合理炉型作为设计的基础。经过 几次修订参数和计算,确定较为合理的炉型。 目前,设计高炉多采用这种方法。
风口中心线与铁口中心线间距离称 为风口高度(hf)。
风口高度可参照下式计算:
hf
hZ k
式中:
k ——渣口高度与风口高度之比,一般
取0.5~ 0.6,渣量大取低值。
(4)风口数目(n): 主要取决于炉容大小,与炉缸直径
成正比,还与冶炼强度有关。 风口数目可以按下式计算:
中小型高炉:
n 2(d 1)
2. 计算法:
计算法即经验数据的统计法。 计算时可选定某一关系式,算出某一主
要尺寸,再根据炉型中各部位尺寸间的关系 式作炉型计算,最后校核炉容,修定后确定 设计炉型。
经验公式 :
大型高炉:
Hu 6.44Vu0.2
d 0.32Vu 0.45
适应于我国50~70年代1000~2000m3高 炉的基本情况,炉型为瘦长型。
炉腹高度由下式计算 :
h2
D 2
d
tg
炉腹角一般为79º~83º,过大不利于煤气
分布并破坏稳定的渣皮保护层,过小则增
大对炉料下降的阻力,不利于高炉顺行。
4. 炉身: 炉身呈正截圆锥形。
作用:
(1)适应炉料受热后体积的膨胀,有利于 减小炉料下降的摩擦阻力,避免形成料拱。
(2)适应煤气流冷却后体积的收缩,保证 一定的煤气流速。
D
d1 2
tg
《高炉炼铁生产》课程单元教学设计
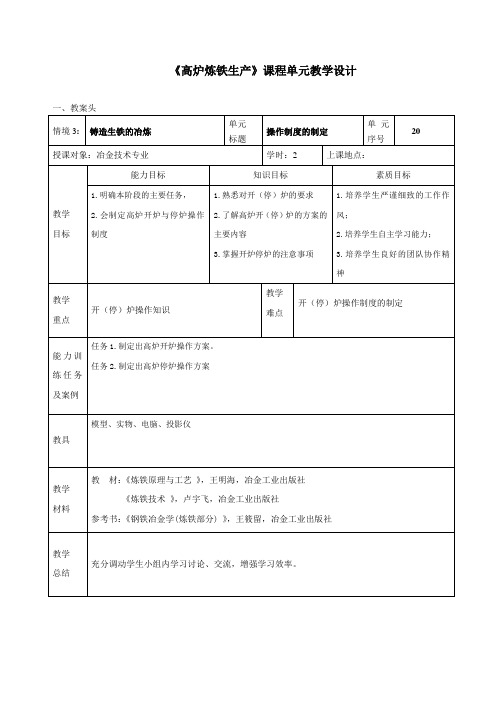
2.培养学生自主学习能力;
3.培养学生良好的团队协作精神
教学
重点
开(停)炉操作知识
教学难点
开(停)炉操作制度的制定
能力训练任务及案例
任务1.制定出高炉开炉操作方案。
任务2.制定出高炉停炉操作方案
教具
模型、实物、电脑、投影仪
教学
材料
教材:《炼铁原理与工艺》,王明海,冶金工业出版社
3.掌握开炉停炉的注意事项
讲授设问
多媒体课件
听讲、讨论
5分钟
引入
(任务项目)
任务导入:提出问题:
1.如何制定开炉设备验收与试运转方案
2.如何制定开炉烘炉方案
3.如何制定开炉装料方案
4.如何制定开炉送风方案
5.如何制定开炉炉前操作方案
6.高炉停炉需要做哪些工作?
图片展示
指导
分析任务
看图
小组讨论
熟悉任务
《炼铁技术》,卢宇飞,冶金工业出版社
参考书:《钢铁冶金学(炼铁部分)》,王筱留,冶金工业出版社
教学
总结
充分调动学生小组内学习讨论、交流,增强学习效率。
二、教案格式
步骤
教学内容
教学方法
和手段
学生活动
时间分配
告知
(内容、目的)
教学内容:操作制度的制定
教学目标:
1.熟悉对开(停)炉的要求
2.了解高炉开(停)炉的方案的主要内容
5分钟
操练
(掌握初步或基本能力)
1.布置任务,明确信息
2.知识准备
(1)高炉开炉操作方案的内容
(2)高炉停炉方案的主要内容
讲授讨论
多媒体课件
高炉炉型设计

4、炉腹高度h2 ;炉腰直径D;炉腹角α
• 选取炉腹角α : 一般取值79o~83o h2 =
1 2 ( D d ) tg
选取 D/d 炉型 D/d 小型高炉 1.25~1.5 中型高炉 1.15~1.25 大型高炉 1.09~1.15
5、选取炉身角β; 炉身高度 h4 ; 炉喉直径 d1
世界高炉之王——沙钢5860立方米炼铁高炉
日本第二大钢铁集团——日本JFE钢铁福山厂 。
(左起)第2高炉、第3高炉、第4高炉、第5高炉,4号高炉 2006年5月扩容到5000立方米,5号高炉扩容到5500立方米
全世界共有9座5500m³ 以上特大型炼铁高炉
• 1、沙钢的5860m³ 高炉;
• 2、日本新日铁大分厂1号、2号高炉(容积均为5775m³ ) • 3、俄罗斯北方钢铁切列波维茨厂5号高炉(容积5580m³ ) 4、日本新日铁君津厂4号高炉(容积5555m³ ) • 5、德国蒂森钢铁斯韦尔根厂2号高炉(容积5513m³ ), • 6、日本JFE福山厂5号高炉(容积5500m³ ) • 7、韩国浦项光阳钢厂4号高炉(容积5500m³ )
h z 1 . 27
0 . 45
bP ' Nc d 铁
2
hf
hz k
― 渣口高度与风口高度之比
k = 0.5~0.6 ; k
炉缸高度: h =h + a ; 1 f
a―风口结构尺寸,一般取值0.35~0.5m
hz― 渣口与铁口中心线的距离称为渣口高度 P ― 生铁日产量,t b ― 生铁产量波动系数,一般取值1.2 N ― 昼夜出铁次数,8~12次/d (大高炉取大值)
• 通过对高炉炉型的大量研究和探索,人们 逐步认识了高炉炉型与原燃料和鼓风制度 的适应关系,即炉型与炉料运动和煤气流 运动规律的适应性。炉型是随着原燃料条 件的改善,操作技术水平的提高,科学技 术的进步而不断发展变化的,逐步形成了 现代的五段式高炉炉型。
3 高炉本体
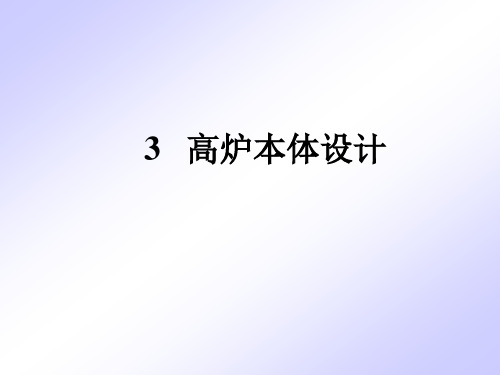
计算得到的炉缸直径再用Vu/A进 行校核,不同炉容的Vu/A取值为:
大型高炉:22~28 中型高炉:15~22 小型高炉:11~15
(2)渣口高度: 渣口中心线与铁口中心线间距离。
渣口过高,下渣量增加,对铁口的维护 不利;渣口过低,易出现渣中带铁事故, 从而损坏渣口;大、中型高炉渣口高度 多为1.5~1.7m。也可以参照下式计算:
2. 炉缸
高炉炉型下部的圆筒部分为炉缸, 炉缸的上、中、下部位分别设有风口、 渣口与铁口。
(1)炉缸直径
炉缸截面燃烧强度:指每小时每平方 米炉缸截面积所燃烧的焦炭的数量, 一般为1.0~1.25t/m2·h。
d 0.23 I •Vu i燃
式中: I——冶炼強度, t/m3·d
i 燃——燃烧強度,t/m2·h
校核炉容:
炉缸体积:
V1
4
d 2 h1
4
9.82
3.5
264 .01m 3
炉腹体积:
V2
12
h2 (D2
Dd
d
2
)
3.5 (112 119.8 9.82 ) 297.65m3
12
炉腰体积:
V3
4
D 2 h2
4
112
2.2
209.08m3
炉身体积:
V4
12
h4
(
D
2
Dd1
d12 )
3 高炉本体设计
3.1 高炉炉型
概念:高炉内部工作空间剖面的形 状称为高炉炉型或高炉内型。
3.1.1 炉型的发展过程
1.无型阶段
2.大腰阶段——炉腰尺寸过大的炉型。 炉缸和炉喉直径小,有效高度低,
- 1、下载文档前请自行甄别文档内容的完整性,平台不提供额外的编辑、内容补充、找答案等附加服务。
- 2、"仅部分预览"的文档,不可在线预览部分如存在完整性等问题,可反馈申请退款(可完整预览的文档不适用该条件!)。
- 3、如文档侵犯您的权益,请联系客服反馈,我们会尽快为您处理(人工客服工作时间:9:00-18:30)。
课程设计题目:设计一座年产制钢生铁(L08)280万吨的高炉目录原始数据: ........................................................................................................................... - 2 -一配料计算 ....................................................................................................................... - 3 -1.矿石和熔剂消耗量的计算(以生产1t生铁为单位)................................................... - 3 -2.渣量和炉渣成分的计算 .................................................................................................... - 4 -3.生铁成分校正: ................................................................................................................ - 5 -二物料平衡计算: ............................................................................................................. - 5 -1.风量的计算 ........................................................................................................................ - 6 -2.煤气量的计算: ................................................................................................................ - 6 -3.编制物料平衡表 ................................................................................................................ - 8 -三.热平衡的计算 .................................................................................................................. - 9 -1.热收入: ........................................................................................................................... - 9 -2.热支出的计算 ................................................................................................................. - 10 -3.热平衡表 .......................................................................................................................... - 13 -四.设计一座年产制钢生铁220万吨的高炉 ................................................................. - 14 -五. 高炉砌砖计算(高铝砖) ................................................................................................ - 16 -原始数据成分TF e Fe2O3 FeO S MnO P SiO2 Al2O3 CaO MgO CO2 H2O 1/2S 3/2S P2O5 烧损∑品种烧结矿56 69.5 9.7 0.06 0.35 0.11 5.4 2.02 9.5 3.0 0.2 0.03 0.25 99.75 球团矿62.5 70 17.7 0.06 0.038 8.7 0.7 1.6 1.05 0.03 0.08 99.86 澳矿65.6 92.7 0.4 0.04 0.12 0.16 2.4 1.6 0.02 0.26 0.06 0.37 97.93 石灰石 1.15 1.6 1.38 1.47 53.5 0.5 42.1 42.1 100.55 炉尘48.1 55.2 12.5 0.12 1.4 0.125 15 1.4 4.65 0.95 1.72 6.60 0.06 0.29 8.32 106.31 焦炭灰分 4.2 5.5 51.9 38.6 3.1 1.0 100.1 煤灰分 2.2 2.86 58.4 33.6 3.72 1.22 99.8据上表校核原料成分:TF e Fe2O3 FeO S MnO P SiO2 Al2O3 CaO MgO CO2 H2O 1/2S 3/2S P2O5 烧损∑成分品种烧结矿56.14 69.67 9.72 0.06 0.35 0.11 5.41 2.03 9.52 3.01 0.20 0.03 0.25 100 球团矿62.59 70.1 17.72 0.06 0.38 8.71 0.78 1.6 1.05 0.03 0.08 100 澳矿66.99 94.66 0.41 0.04 0.12 0.16 2.45 1.63 0.02 0.27 0.06 0.38 100 石灰石 1.14 1.59 1.37 1.46 53.21 0.5 41.87 41.87 100 炉尘45.25 51.92 11.76 0.12 1.32 0.125 14.11 1.32 4.37 0.89 1.62 6.21 0.06 0.27 7.83 100 焦炭灰分 4.2 5.5 51.84 38.56 3.1 1.0 100 煤灰分 2.20 2.87 58.52 33.67 3.73 1.22 100焦碳和煤粉及其挥发分的成分如下表品种\成分Fcd Ad Vd St.d H20焦炭85.6 12.8 1.4 0.55 4.0煤粉74.5 16.6 9.5 0.5品种\成分CO2 CO CH4 H2 N2 O2焦炭挥发分22.8 20.5 3.85 19.6 29.4煤粉挥发分43.2 26.5 22.3生铁预定成分如下表生铁预定成分Fe Si Mn S P C ∑(L08)/%94.516 0.48 0.03 0.026 0.098 4.85 100.00其他条件焦比Kg/t 煤比Kg/t 炉渣碱度直接还原度炉尘Kg/t 鼓风湿度% 风温440 125 1.1 0.54 20.00 1.00 1100 一配料计算1.矿石和熔剂消耗量的计算(以生产1t生铁为单位)矿石配比取烧结矿/球团矿/澳矿=76/10/14,计算混合矿成分。
品种TFe FeO SiO2Al2O31/2SCaO MgO Fe2O3P2O5MnO烧结矿56.14 9.72 5.41 2.03 0.03 9.52 3.01 69.67 0.25 0.35 球团矿62.59 17.72 8.71 0.78 0.03 1.6 1.05 70.1 0.08澳矿66.99 0.41 2.45 1.63 0.06(3/2S)0.02 0.27 94.66 0.38 0.12 混合矿58.30 9.22 5.33 1.85 0.03 7.40 2.48 73.21 0.25 0.28设需要混合矿为X kg/t ,石灰石为Y kg/t由 TFe 的平衡可列出: (1)由二元碱度R 可列出:28608.41411.0205852.0166.01255184.0128.04450137.00533.00437.0200373.0166.0125031.0128.04455321.0074.01.1⨯-⨯-⨯⨯+⨯⨯++⨯-⨯⨯+⨯⨯++=y x y x (2)联立(1)(2)解得X=1636.52 Kg/t Y = 8.89Kg/t所以:烧结矿的用量为:1636.52×76% = 1243.76 kg/t球团矿的用量为:1636.52×10% = 163.65 kg/t澳矿的用量为: 1636.52×14% = 229.11 kg/t2.渣量和炉渣成分的计算CaOm= 127.50 kg/t 由(2)式分子可得 2sio m= 115.91 kg/t 由(2)式分母可得FeOm= 945.16×(0.003/0.997)×(72/56)= 3.65 kg/t MnOm=(1636.52×0.0028-20×0.0132)×0.5=2.16 kg/tMgOm=1636.52×0.0248 + 8.89×0.005 + 440×0.128×0.01 + 125×0.166×0.0122-20×0.0089 = 41.27kg/t23Al Om =1636.52×0.0185 + 8.89×0.0146 + 440×0.128×0.3856+125×0.166×0.3367-20×0.0132 = 59.09 kg/t4525.020997.0003.016.94516.9450223.0166.0125042.0128.04450114.05830.0⨯+⨯+=⨯⨯+⨯⨯++Y X进入高炉的总S量:m s=1636.52×0.0006+440×0.0055+125×0.005=4.05 kg/t进入生铁的m s =1000×0.026%=0.26 kg/t进入煤气的m s =4.05×5%=0.20kg/t进入炉尘的m s =20×0.0012=0.02kg/t则进入炉渣的m s =4.05-0.26-0.20-0.02=3.57 kg/t炉渣化学成分和渣量成分SiO2 Al2O3 CaO MgO FeO MnO S/2 ∑重量/kg 115.91 59.09 127.50 41.27 3.65 2.16 1.79 351.37 百分率/%32.99 16.82 36.29 11.75 1.03 0.61 0.51 100 3.生铁成分校正:W[S]=0.026 %W[Si]=0.48 %W[Fe]=94.516 %W[Mn]=2.16×(55/71)×100/1000=0.17 %W[P]=1636.52×0.0025×(62/142)×100/1000=0.179 %W[C]=100-94.516-0.026-0.48-0.17-0.179=4.63% 二物料平衡计算:= 0.54 ,鼓风湿度f= 1.0%直接还原度rd1. 风量的计算C 总=440×0.856+125×0.745=469.77kg/t= 469.77×0.7%=3.29 kg/tC CH4C生铁=1000×4.63%=46.30 kg/tC直接=1.7×12/55+4.8×24/48+1.79×60/62+945.16×0.54×12/56=113.87 kg/tC尘=20×0.0783=1.57kg/tC燃=469.77-3.29-46.30-113.87-1.57=304.74 kg/t密度=0.21(1-0.01)+0.5×0.01=0.2129O2C燃烧需要的氧气 V=304.74×22.4/24=284.42 m3O2:VO2 =125×0.095×0.223×22.4/32=1.85 m3煤挥发分提供的O2=(284.42-1.85)/0.2129=1327.24 m3则需鼓风量为:V风M=1.28×1327.24=1698.87 kg/t风2.煤气量的计算:1).CH4碳生成CH4=3.29×22.4/12=6.14 m3焦炭挥发分中的CH4=440×0.014×0.0385×22.4/16=0.33 m3总的CH4=6.14+0.33=6.47 m32).H2鼓风带入的H=1327.24×0.015=19.91 m32=125×0.095×0.432×22.4/2=57.46 m3煤分带入的H2=440×0.014×0.196×22.4/2=13.52 m3焦炭带入的H2还原消耗的H 2=(19.91+57.46+13.52) ×40%=36.36 m 3生成CH 4消耗的H 2=6.14×2=12.28 m 3所以:炉顶煤气中的H 2=19.91+57.46+13.52-36.36-12.28=42.25 m 33).CO 2还原Fe 2O 3生成的CO 2=(1636.52×0.7321+8.89×0.015) ×22.4/160=167.75 m 3还原FeO 生成的CO 2=564.22)16.9454.225636.3654.01(16.945⨯⨯⨯--⨯=137.54 m 3石灰石分解产生的CO 2=444.224187.089.8⨯⨯=1.89 m 3焦炭带入的CO2=444.22228.0014.0440⨯⨯⨯=0.72 m 3所以:进入炉顶煤气的CO2=167.75+137.54+1.89+0.72=307.90 m 34).COC 燃烧生成的CO =124.22304.74⨯=568.85 m 3 直接还原产生的CO =124.22113.87⨯=212.56 m 3 焦炭挥发分中的CO =284.22205.0014.0440⨯⨯⨯=1.01 m 3 间接还原消耗的CO =137.54167.75+=305.29 m 3所以:进入炉顶煤气中的CO =568.85+212.56+1.01-305.29=477.13 m 35).N 2鼓风中的N 2=79.0)015.01(1327.24⨯-⨯=1032.79m 3 焦炭中的N 2=45.1284.22294.0014.0440=⨯⨯⨯ m 3 煤分中的N 2=52.2284.22265.0095.0125=⨯⨯⨯ m 3 所以炉顶煤气中的N 2=1032.79+1.45+2.52=1036.76 m 3煤气成分如下CO 2COCH 4 H 2 N 2 ∑ 体积/m3 307.90 477.13 6.47 42.25 1036.76 1870.51 百分比/%16.4625.510.352.2655.431003.编制物料平衡表煤气密度ρ煤气=3396.14.22285543.020226.0160035.0282551.0441646.0=⨯+⨯+⨯+⨯+⨯kg/m 3 煤气重量m 煤气=74.25053396.151.1870=⨯ kg氢气还原生成的H 2O =22.294.221836.36=⨯kg物料平衡表收入 kg支出 kg烧结矿 1243.76 生铁 1000 球团矿 163.65 炉渣 351.37 澳矿 229.11 煤气 2505.74 焦炭 440.00 炉尘 20.00 煤粉 125.00 水分 29.22 石灰石 8.89 鼓风 1698.87 ∑3909.28∑3906.33绝对误差:3909.28-3906.33=2.95 kg相对误差:%3.0%075.028.390995.2<= 满足要求三.热平衡的计算风温:1100℃ 冷矿:25℃ 铁水:1450℃炉渣: 1500℃ 炉顶煤气:200℃1.热收入:1).碳氧化放热:由C 氧化成1 m 3CO 2放热:17869.50 KJ由C 氧化成1 m 3 CO 放热:5241.72 KJ则C 氧化放热Q 1=kJ 04.798148672.5241)01.113.477(50.17869)54.13775.167(=⨯-+⨯+2).热风带入的热:1100℃空气热容 1.4233KJ/(m 3·℃)水蒸气热容 1.7393 KJ/(m 3·℃)2%的空气用于输送煤粉 入炉热风V 风=70.130098.024.1327=⨯m 3 热风带入热量Q 2=()kJ79.204319611007393.1015.070.13004233.1)015.01(70.1300=⨯⨯⨯+⨯-⨯ 3). H 2氧化放热1m 3 H 2氧化成H 2O 蒸气放热 10788.58KJH 2氧化放热Q 3=42.25×10788.58=455817.51KJ4). 成渣热1KgCaO和MgO的成渣热为 1128.60KJ成渣热Q4=8.89×(0.5321+0.005)×1128.60=5388.86KJ 5). 矿石带入热量25℃炉料热容为 0.6897 KJ/(Kg·℃)矿石带入热量Q5=1636.52×0.6897×25=28217.70KJ总热收入Q收=10514106.90KJ2. 热支出的计算1).氧化物分解吸热:(1).铁氧化物分解吸热:(存在状态Fe2O3、Fe3O4、2FeO·SiO2)烧结矿中FeO的20%以2FeO·SiO2状态存在80%以Fe3O4状态存在球团矿中FeO 100%以Fe3O4存在焦炭灰分、煤粉灰分中FeO100%以2FeO·SiO2存在以2FeO·SiO2存在的FeO=87.270287.0166.0125055.0128.04402.00972.076.1243=⨯⨯+⨯⨯+⨯⨯kg 以磁铁矿状态存在的FeO=kg65.1260041.011.2291772.065.1638.00972.076.1243=⨯+⨯+⨯⨯以磁铁矿状态存在的Fe2O3=kg44.2817216065.126=⨯Fe3O4=kg09.40844.28165.126=+游离的赤铁矿Fe2O 3=kg80.91644.2810159.089.87321.052.1636=-⨯+⨯分解1Kg以2FeO·SiO2状态存在的FeO需要耗热4068.52KJ分解1Kg 磁铁矿耗热4791.78KJ分解1Kg 赤铁矿耗热5144.28KJ则铁氧化物分解吸热Q 1=kJ 06.678514328.514480.91678.479109.40852.406887.27=⨯+⨯+⨯(2).非铁氧化物分解吸热:(Mn 、Si 、P )分解生成1Kg Mn 耗热:7350.53KJ分解生成1Kg Si 耗热 :31028.14KJ分解生成1Kg P 耗热 :35697.20KJQ =kJ 96.22532820.3569779.114.310288.453.73507.1=⨯+⨯+⨯则 Q 1=06.6785143 + 96.225328=7010472.02 kJ2). 脱硫吸热:CaO 脱硫耗热: 5392.20KJ/KgMgO 脱硫耗热: 8025.60KJ/KgMnO 脱硫耗热: 6249.10KJ/KgFeO 脱硫耗热 :5496.90KJ/Kg取平均为: 6290.90KJ/Kg脱硫吸热Q 2=(3.58+0.20)×6290.90=23779.60 kJ3). 碳酸盐分解由CaCO 3分解成1KgCaO 吸热:4037.88KJ由MgCO 3分解成1KgMgO 吸热:2482.92KJ碳酸盐分解吸热Q 3=kJ 03.1921192.2482005.089.888.40375321.089.8=⨯⨯+⨯⨯4). H 2O 分解吸热分解1m 3水蒸气吸热10788.58KJH 2O 分解吸热Q 4 =kJ 52.21478558.10788015.024.1327=⨯⨯ 5). 煤粉分解吸热分解1Kg 煤粉分解吸热:836KJ煤粉分解吸热Q 5=kJ 104500836125=⨯ 6). 游离水蒸发吸热1Kg 水从0℃ 100℃吸热:418KJ100℃水 100℃水蒸气吸热:2257.2KJ游离水蒸发吸热Q 6=kJ 70.47083)21.2257418(04.0440=+⨯⨯ 7). 铁水带走的热量1Kg 1450℃铁水带走的热量:1237.28KJ铁水带走的热量Q 7=kJ 123728028.12371000=⨯ 8). 炉渣带走的热量1Kg 1500℃炉渣带走的热量:1851.74KJ炉渣带走的热量Q 8=KJ 88.65064574.185137.351=⨯9). 煤气带走热量200℃有关煤气成分的热容(Kg/(m 3·℃))成分 N 2 CO CO 2 H 2 H 2O CH 4热容 1.3104 1.3104 1.7844 1.2996 1.5086 1.8166干煤气热容C 煤气=)℃·Kg/(m 39.13104.15543.08166.10035.02996.10226.07844.11646.03104.12551.03=⨯+⨯+⨯+⨯+⨯干煤气带走的热量Q 煤气=KJ 78.520001020039.151.1870)=-(⨯⨯煤气中水分带走的热量Q 水=KJ 71.142745086.1020036.365086.1100200184.2204.0440=)-()-(⨯⨯+⨯⨯⨯⨯ 炉尘热容C 尘:0.836 KJ/(Kg ·℃)炉尘带走的热量Q 尘=20×0.836×200=3344KJ则煤气带走的热量Q 9=37620.49KJ 510). 热损失热损失Q 损= Q 收- 101ii Q=∑=668728.66KJ3.热平衡表热收入 热支出 项目 热量KJ 比例% 项目 热量KJ 比例% 碳氧化放热 7981486.04 75.91 氧化物分解7010472.02 71.21 热风 2043196.79 19.43 脱S 23779.60 0.24 氢氧化 455817.51 4.34 碳酸盐分解 19211.03 0.195 成渣热 5388.86 0.051 水分分解 214785.522.18矿石物理热28217.700.27 煤粉分解1045001.06 游离水蒸发 47083.70 0.48 铁水带走 1237280 12.57炉渣带走650645.886.61煤气带走 537620.49 5.46 ∑10514106.90100∑9845378.24100热损失668728.660.23四.设计一座年产制钢生铁280万吨的高炉.确定工作日d 347%95365=⨯日产量 t p 2.8069347102804=⨯=1.定容积 利用系数 )(0.23d m t v ⋅=η2. 每座高炉日产量P=2p=4034.6 每座高炉容积 3'20180.26.4034m pV vu ===η 3.炉缸尺寸 炉缸直径选择冶炼强度 )(95.03d m t I ⋅= 燃烧强度 )(05.13h m t i ⋅=燃 则 m i IV d u 83.905.1201895.023.0=⨯==燃 取 m d 8.9= 校核75.268.9420182=⨯=πAV u 合理炉缸高度渣口高度 m d Nc bp h z 64.18.91.755.0106.40342.127.127.122=⨯⨯⨯⨯⨯==铁ρ 取 m h z 7.1= 风口高度 m k h h z f 03.356.07.1===取 m h f 0.3=风口数目 6.23)28.9(2)2(2=+=+=d n 取24个 风口结构尺寸选取 m 5.0=α炉缸高度 m h h f 5.35.00.31=+=+=α ○3死铁层厚度 选取m h 5.10= 4.炉腰直径,炉腰角,炉腰高度 选取 10.1=d D则 m D 07.118.913.1=⨯= 取 m D 0.11= 选取80=α则 4.38028.91122=-=-=tg tg d D h α 取 m h 4.32= 校核α '268083.58.9114.3222 ==-⨯=-=ααd D h tg 5.炉喉直径,炉喉高度选取 68.01=D d 则 48.71168.01=⨯=d 取 m d 5.71= 选取 m h 0.25=6.炉身角,炉身高度,炉腰高度 选取 84=β 则 65.168425.711214=-=-=tg tg d D h β 取 m h 174=校核β9218417.86.83.132.192214'''==-⨯=-=ββd D h tg选取 56.2/=D H u则 m H u 16.281156.2=⨯= 取 m H u 2.28=求得 m h h h h H h u 3.20.2174.35.32.2854213=----=----= 7.校核炉容 炉缸体积 3212101.2645.38.944m h d V =⨯⨯==ππ炉腹体积32222222.289)8.98.91111(4.312)(12m d Dd D h V =+⨯+⨯⨯=++=ππ炉腰体积 323230.2003.21144m h D V =⨯⨯==ππ炉身体积 32221124404.1156)5.7115.711(1712)(12m d Dd D h V =+⨯+⨯⨯=++=ππ炉喉体积 32521536.880.25.744m h d V =⨯⨯==ππ高炉容积35432161.199936.8804.115620020.28901.264m V V V V V V u =++++=++++= 误差 %1%91.0201861.19992018''<=-=-=∆u u u V V V V炉型设计合理符合要求五. 高炉砌砖计算(高铝砖)高炉炉身用冷却模块砌筑,高炉炉底采用综合炉底,炉缸采用碳砖砌筑。