FMEA失效模式与效应分析(第三版)
失效模式与效应分析
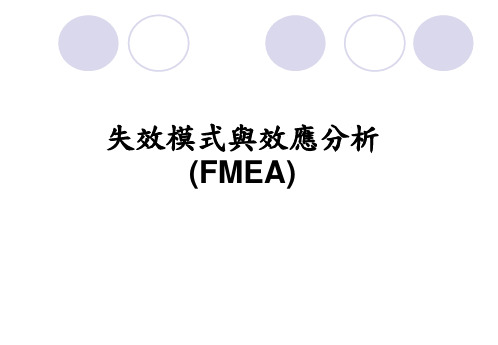
低
6
出貨前
----------------------------------------------------------------------------------------------------------------
非常低
7
客戶尚未收到貨
----------------------------------------------------------------------------------------------------------------
幾乎無法檢出
10
不良發生後知道
21
表格內容介紹及說明-風險優先指數
22
風險優先指數(Risk Priority Number)
定義: 相等於發生率(O)、嚴重度(S)、難檢度(D)三 項數據之乘積,可做為關鍵要因及產品特性之 優先評估依據。
說明: RPN為較高數據之項目代表較高風險,需優先 加以處理,反之則異。 RPN數據較低時亦有特殊狀況需優先處理之。
FMEA 的基本概念
將失效依照其應用的目的或特性加以分類:
1.依失效發生原因分類 2.依失效發生時間情況分類
• 先天性弱點的失效 • 誤用失效
• 突發性失效 • 漸次性失效
3.依失效範圍程度分類 4.依失效根源分類
• 局部性失效 • 全面性失效
• 老化、組件、環境、人員
4
表格內容介紹及說明-失效模式
* 錯誤 * 遺漏 * 沒有或僅有部份動作 * 產生危險 * 有障礙
2
FMEA型式
設計FMEA(DFMEA) 1. 零件 2. 次系統 3. 系統
將系統之失敗效應減 至最低 將系統之品質與可靠 度提昇之最高
风险评估技术-失效模式和效应分析(FMEA)及失效模式、效应和危害度分析(FMECA)

失效模式和效应分析(FMEA及失效模式、效应和危害度分析(FMECA)1 概述失效模式和效应分析(Failure Mode and Effect Analysis ,简称FMEA)是用来识别组件或系统未能达到其设计意图的方法。
FMEA 用于识别:•系统各部分所有潜在的失效模式(失效模式是被观察到的是失误或操作不当);•这些故障对系统的影响;• 故障原因;• 如何避免故障及 /或减弱故障对系统的影响。
失效模式、效应和危害度分析(Failure Mode and Effect and Criticality Analysis ,简称 FMECA)拓展了 FMEA 的使用范围。
根据其重要性和危害程度,FMECA 可对每种被识别的失效模式进行排序。
这种分析通常是定性或半定量的,但是使用实际故障率也可以定量化。
2 用途FMEA 有几种应用:用于部件和产品的设计(或产品) FM EA ;用于系统的系统FMEA ;用于制造和组装过程的过程 FMEA ;服务FMEA和软件FMEA。
FMEA/ FMECA 可以在系统的设计、制造或运行过程中使用。
然而,为了提高可靠性,改进在设计阶段更容易实施。
FMEA/ FMECA 也适用于过程和程序。
例如,它被用来识别潜在医疗保健系统中的错误和维修程序中的失败。
FMEA/FMECA 可用来:•协助挑选具有高可靠性的替代性设计方案;•确保所有的失效模式及其对运行成功的影响得到分析;•列出潜在的故障并识别其影响的严重性;•为测试及维修工作的规划提供依据;• 为定量的可靠性及可用性分析提供依据。
它大多用于实体系统中的组件故障,但是也可以用来识别人为失效模式及影响。
FMEA 及 FMECA 可以为其他分析技术,例如定性及定量的故障树分析提供输入数据。
3 输入数据FMEA 及 FMECA 需要有关系统组件足够详细的信息,以便对各组件出现故障的方式进行有意义的分析。
信息可能包括:• 正在分析的系统及系统组件的图形,或者过程步骤的流程图;• 了解过程中每一步或系统组成部分的功能;• 可能影响运行的过程及环境参数的详细信息;• 对特定故障结果的了解;• 有关故障的历史信息,包括现有的故障率数据。
失效模式与效应分析 (FMEA)

失效模式與效應分析 (FMEA)何謂「FMEA、FMECA」?FMECA 是兩種分析技術的總稱:1.FMEA﹝故障型式及其影響分析﹞2.CA﹝Criticality Analysis, 嚴重度分析﹞與失誤樹分析一樣,故障型式影響及嚴重度分析﹝failure modes, effects and criticality analysis, 簡稱 FMECA﹞,首先在美國國防科技中研究發展,且在國防部各機構中普遍應用﹝DOD, 1980﹞,後來漸應用於工業界。
在核能、化工、石化、海上鑽油等高風險工業中,自不例外。
工業界的設計工程師與可靠度﹝Reliability﹞工程師常運用 FMECA 以預測複雜的產品的可靠度,預估一件產品的零件在某特定的時間及情況下,如何失去其功能,故障的次數是多少,故障之後對其他零件或對整個系統會產生怎樣的影響等。
FMECA 的功用不止於可靠度一端,其分析所得的資料,尚可作下列用途:1.協助評估所設計的裝置,如複聯系統﹝Redundancy﹞、故障偵測,以及fail-safe 特性等。
2.對測試、採購﹝Procurement﹞、檢查、改善措施等提供先後順序的參考資料。
3.提供失誤隔絕﹝Fault isolation﹞及維護性﹝Maintainability﹞分析的參考資料。
4.提供系統安全分析﹝如失誤樹分析﹞所需的硬體資料。
FMECA 可在系統週期的任一階段中,依計劃內容之需要,以不同深淺程度實施,但在設計階段的初期,一旦所需的設備確定之後,即應實施。
FMECA 的對象是系統或子系統中的零組件,尤其對於複雜的系統中的設備零件,最能發揮其故障針砭的功效,此為其他系統安全分析技術不能望其項背之處。
但因其分析對象大多限於硬體,故對於人為因素和作業環境因素較少納入分析考慮範圍。
因此,如能將 FMECA 與失誤樹分析合併使用,必更能瞭解整個作業系統的危害,進而防範事故生。
摘於【環安 Q&A】。
失效模式与效应分析(FMEA)
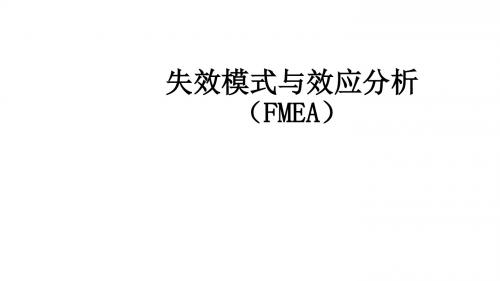
失效模式与效应分析 (FMEA)
起源
FMEA大约于1950年代由美国Grumman公 司提出,当时由于飞机系统复杂并且需要 预防失效情况发生,因此渐渐发展成安全 性与可靠度的设计模式,以期能够增加产 品质量,降低不良问题的发生。
FMEA具体项目
• 累积经验,早期发现失效原因及采取因应之道。 • 促进设计改良。 • 改善操作方法及建立维护计划的参考。 • 帮助操作人员之训练,让员工能在短期内找出 失效原因与解决之法。 • 公司人员异动时,能让员工快速上手。
FMEA表格建立
失效机率
字码体系
严重性分析
多要因评估法
单要因评估法
列表评估法
失效报告
范例
范例
范例
范例
范例
故障树分析符号
故障树分析范例
故障树简化
故障树关键性估计范例
结论
• 透过FMEA模式,可有效找出来自品失效原因,进而解决问题,是一 个可靠性的解析手法。 • 藉由实施FTA ,能让不希望发生的事情明确化,并能判别事件发 生时所带来的一些事象与对成品的影响。
FMEA失效模式与效应分析课件(PPT 82张)

过程流程图
• 初始过程流程图 从预料的材料和产品/过程方案中得出 的预期加工过程的描述 • 过程流程图 描述材料的整个加工流程,包括任何 的返工和修理操作
prepared by liuliangcheng, Not copy without permission.
什么是 FMEA ?
1 . 对失效的产品进行分析,找出零组件之失效模 式,鑑定出它的失效原因,研究该项失效模式对系 统会产生什么的影响。
2. 失效分析在找出零组件或系统的潜在弱点,提供 设计,制造,品保等单位采取可行之对策。
prepared by liuliangcheng, Not copy without permission.
prepared by liuliangcheng, Not copy without permission.
典型的FMEA s
系统
部件 子系统 主系统
注意:将系统的 失效模式降为最小
设计
部件 子系统 主系统 注意:将设计的 失效模式降为最小
过程
人 机 料 法 环 测
注意:将全过程的 失效模式降为最小 目标:最大化的 全过程质量、 可靠性、成本 和可维护性
prepared by liuliangcheng, Not copy without permission.
Agenda
• • • • • 掌握FMEA的概念和运用时机。 D- FMEA填写说明 P- FMEA填写说明 FMEA范例解说 Q&A
prepared by liuliangcheng, Not copy without permission.
prepared by liuliangcheng, Not copy without permission.
六西格玛工具之失效模式与效果分析(FMEA)精选全文完整版
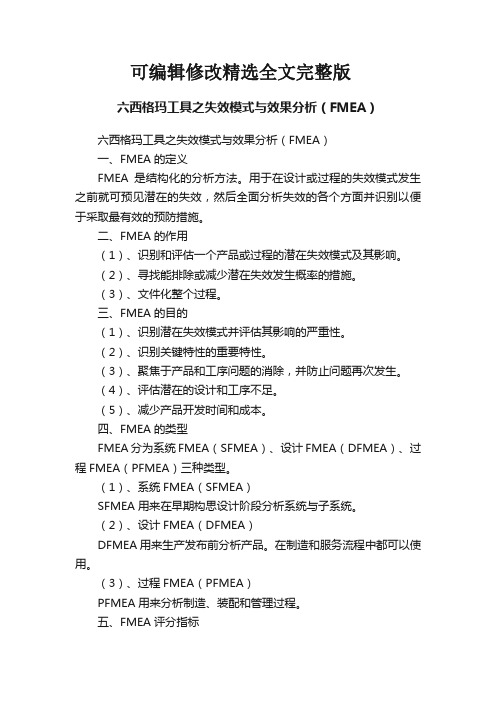
可编辑修改精选全文完整版六西格玛工具之失效模式与效果分析(FMEA)六西格玛工具之失效模式与效果分析(FMEA)一、FMEA的定义FMEA是结构化的分析方法。
用于在设计或过程的失效模式发生之前就可预见潜在的失效,然后全面分析失效的各个方面并识别以便于采取最有效的预防措施。
二、FMEA的作用(1)、识别和评估一个产品或过程的潜在失效模式及其影响。
(2)、寻找能排除或减少潜在失效发生概率的措施。
(3)、文件化整个过程。
三、FMEA的目的(1)、识别潜在失效模式并评估其影响的严重性。
(2)、识别关键特性的重要特性。
(3)、聚焦于产品和工序问题的消除,并防止问题再次发生。
(4)、评估潜在的设计和工序不足。
(5)、减少产品开发时间和成本。
四、FMEA的类型FMEA分为系统FMEA(SFMEA)、设计FMEA(DFMEA)、过程FMEA(PFMEA)三种类型。
(1)、系统FMEA(SFMEA)SFMEA用来在早期构思设计阶段分析系统与子系统。
(2)、设计FMEA(DFMEA)DFMEA用来生产发布前分析产品。
在制造和服务流程中都可以使用。
(3)、过程FMEA(PFMEA)PFMEA用来分析制造、装配和管理过程。
五、FMEA评分指标(1)、严重度(S):潜在失效模式对客户的严重度。
在此所指的客户包括系统及下道工序和最终用户。
严重度只适用于结果。
(2)、发生频率(O):造成某种失效模式的某个原因多长时间发生一次。
发生频率的重点并不在于它的的得分,而是它的意义。
(3)、可探测度(D):指当前或将要用来探测或鉴别失效模式的控制设备能探测出失效模式的概率。
风险有限指数(RPN):RPN=OxSxD/E式中:O——发生频率;S——严重度;D——可探测度;E——有效性。
优先级别范围优先级别范围A >200 C 26-99B 100-199 D 1-25。
失效模式与效应分析(FMEA)
失效模式与效应分析(FMEA)一、定义失效模式与效应分析(failure mode and effects analysis,FMEA)是一种前瞻性的管理模式,是在行动之前就认清问题并预防问题发生的分析。
FMEA由失效模式(failure oode,FM)及效应分析(effects analysis,EA)两部分组成。
其中,失效模式是指能被观察到的错误或缺陷(俗称安全隐患),应用于护理质量管理中就是指任何可能发生的护理不良事件;效应分析是指通过分析该失效模式对系统的安全和功能的影响程度,提出可以或可能采取的预防改造措施,以减少缺陷,提高质量。
二、目的、目标FMEA的目的是防患未然;设计屏障,让事情不要发生;降低损害,即使有风险存在,也是可容许的最低风险;是发现、评价流程中潜在的失效及其后果,找到能够避免或减少这些潜在失效的措施,并将上述过程文件化。
FMEA的主要目标是分析现有系统(流程)或将建立之系统(流程):哪里会出错?一旦出错会有多糟糕?哪里需要修正以避免事故发生?三、执行时机1、新设计的流程2、修改现行的流程3、旧的流程用于新的情境中四、实施步骤(一)步骤一:确认问题选择那些高风险或非常薄弱的程序进行研究。
高风险流程的特性有:高复杂性(步骤多)的作业、高差异性的输入来源、未标准化的作业、紧密相依的作业、作业时间间隔太紧或太松、高度依赖人员的判断或决定。
医疗行为中的高风险流程有:用药、病人处于危险的操作流程(放射治疗,CT扫描,磁振造影)、输血与输成分血、抑制作用的药物、对高危人群进行照顾或提供服务、与复苏相关等。
(二)步骤二:组建团队组建一个多学科的综合FMEA团队,团队中至少应该有一个领导者、一个所硏究流程方面的专家、一个FMEA咨询师(即FMEA专家,可以为团队领导者提供建议,保证FMEA的顺利实施)、一个对所研究流程不太熟悉的人(可以从不同的角度和方面提出有价值的建议)。
一般建议团队成员在6〜10人之间,以便于管理,所有成员必须接受过FMEA培训。
PFMEA第3版
满意。
被 丢 弃 , 或 车 辆 /系 统 要 在 修 理 部 门 花 上 少 于 半 小 时
加以修理。
低
车 辆 或 系 统 能 运 行 ,但 舒 适 性 /方 便 性 项 目 运 行 性 能 下 或 ,100% 的 产 品 需 要 重 新 加 工 ,或 车 辆 /系 统 要 下 生 5
降。
产线修理,但不用到修理部门。
2020/11/23
集體的努力
• 過程FMEA是一份動態文件,應在生產工裝準備之前 ,在過程可行性分析階段或之前開始,而且要考慮以 單個零件到總成的所有製造工序。在新車型或零件項 目的製造計劃階段,對新工藝或修訂過的工藝進行早 期評審和分析能夠促進預測、解決或監控潛在的過程 問題。
• 過程FMEA假定所設計的產品會滿足設計要求。因設 計缺陷所產生失效模式不包含在過程FMEA中。它們 的影響及避免措施由設計FMEA來解決。
11/23
4) 编制者
• 填入负责准备FMEA工作的工程师的姓 名、电话及所在公司名称
2020/11/23
5) 年型/車型
• 填入将使用和/或正被分析过程影响的预 期的年型及车型(如果已知的话)
2020/11/23
6) 关键日期
• 填入最初FMEA预定完成的日期, 不能超 過開始計劃生產的日期
FMEA 编号:
页次:
OF
准备者:
(修订)
过程 潜在失 潜在失 严 等 潜在原因 发 现行预防 现行侦测 难 风险 建议 负责人
重
生
检 优先
与
执行结果
功能 效模式 效后果 度 级 /机理 度 过程控制 过程控制 度 数 措施 日期 执行措施 S O D RPN
S
失效模式与效应分析(failure modes and effects analysis,FMEA)
失效模式与效应分析(failure modes and effects analysis, FMEA)又名:潜在失效模式与效应分析(potential failure modes and effects analysis),失效模式、影响与危害性分析(failure modes,effects,and criticality analysis,FMECA)概述失效模式与效应分析( FMEA)是一步步地识别在设计、生产或装配过程以及最终产品和服务中所有可能失效的一种方法。
“失效模式”意思是可能产生某些失效的方式或模式。
失效是任何的错误或者缺陷,尤其是那些影响顾客的、潜在的或实际的。
“效应分析”指的是研究这些失效的后果或效应。
这些失效按照他们结果的严重性、发生的频率以及被检测到的容易度优先排序。
FMEA的目的是从有最高的、优先级的开始来采取行动消除或者减少失效。
FMEA通常把当前有关失效的知识以及所采取的行动文档化,用于持续的改进。
FMEA用于设计中预防失效的发生,之后又用于正在进行的过程操作中的控制。
理想地说,FMFA开始于产品的概念设计阶段,贯穿于产品或服务的整个生命期中。
FMEA在19世纪40年代最早被应用于美国的军队中,然后在航空和自动化行业得到进一步的发展应用。
一些行业已经把FMEA的标准正规化,下面是一个综述。
在采取F'MEA过程之前,需通过其他的参考资料和培训,从而学习更多关于组织和行业的标准和具体的方法。
适用场合·当一个产品或服务正在被设计或者重复设计时,在QFD之后或者在设计完成之后;·当以全新的方式应用现有的过程、产品或服务时;·在形成新的或改进过程的控制方法以前;·当对现有的过程、产品或服务计划改进的时候;·当分析现有的过程、产品或者服务失效原因时;·贯穿于过程、产品或者服务的生命期中定期进行检查。
实施步骤这只是一个大概的过程,具体的细节则随着组织或行业的标准而有所变化。
3FMEA第三版-名词解释
2.7 KPC
——影响安全、国家法律法规、功能、配合的质量特性 影响安全、国家法律法规、功能、 影响安全
SPC (standard)
Product characteristic
PC KPC (key)
S/C F/F SCC (standard) CC KCC (key)
KCC: 2.8 KCC:
yes失效分析设计fmea41基本信息42fmea分析101843fmea改进192244跟踪验证表头18对象9411fmea文件编号及页码412系统子系统部件的名称及称号413设计责任414编制人姓名电话email职称或职位415车型年车辆类型416关键日期预定fmea的完成日期417fmea日期原始日期最新修订日期418核心小组成员419项目功能项目的名称和编号项目的功能尽可能用简洁的语言描述fmea421潜在失效模式可能发生但不一定发生的失效专业化规范化的语言描述每种失效模式尽可能单列出来422潜在失效后果失效模式对系统功能的影响根据顾客可能的发现和经历来评价需要集体的智慧423严重度s对失效后果的严重程度的评价只能通过修改设计来降低设计失效严重度评价准则qs9000424级别产品质量特性分为一般质量特性和关键质量特性对关键质量特性在分级栏中应用适当的字母或符号注明425潜在失效起因机理一个设计薄弱部分的迹象征兆列出所有可能想到的起因机理426频度o评价准则见p23描述失效起因机理出现的可能性频度值参考现行控制p设计更改是降低频度数的唯一途径427现行设计控制用于或正用于相同或相似设计中的那些方法有三种设计控制方法预防起因机理的出现p查出失效起因机理d查出失效模式d428探测度d查出失效模式起因机理的探测能力的度量表格见p27429风险顺序数rpn描述对象风险的大小rpnsod按rpn值的大小确定优先改进顺序s值高不管rpn值大小如何都必须关注431建议措施按rpn值的大小确定改进顺序以及s值高的项目任何建议措施的目的都是为减小rpn值即sod432责任及目标完成日期落实措施的执行组织和个人预计完成的日期433采取的措施措施的简单说明措施的生效日期434措施结果重新评价采取措施后的rpn值按照统一标准判断是否fmea结束设计确认和验证不能降低探测度跟踪设计主管工程师负责建议措施的实施与落实fmea是一份动态文件永远体现当前最新设计水平过程pfmea案例
- 1、下载文档前请自行甄别文档内容的完整性,平台不提供额外的编辑、内容补充、找答案等附加服务。
- 2、"仅部分预览"的文档,不可在线预览部分如存在完整性等问题,可反馈申请退款(可完整预览的文档不适用该条件!)。
- 3、如文档侵犯您的权益,请联系客服反馈,我们会尽快为您处理(人工客服工作时间:9:00-18:30)。
2.开发阶段
3制造阶段
4.客户抱怨阶段
FMEA之演变
1.FMECA之前身为FMEA,系在1950由格鲁曼 飞机提出,用在飞机主控系统的失效分析。 2.波音与马丁公司在1957年正式编订FMEA的作 业程序,列在其工程手册中。 3.60年代初期,美太空总署将FMECA成功的应用 于太控计划。美军同时也开始应用FMECA技术,并 于1974年出版MIC-STD-1629 FMECA作业程序。 4.1980修改为MIC-STD-1629A,延用至今。 5.1985由国际电工委员会(IEC)出版之 FMECA国际标准(IEC812),即参考MIC-STD-1629A 加以部份修改而成。
6
FMEA之特征
1.是一项以失效为讨论重点的支持性与辅助性的可靠度 技术。 2.用表格方式进行工程分析,使产品在设计与制程规划时 ,早期发现缺陷及影响程度以便及早提出解决之道。 3.是一种系统化之工程设计辅助工具。 4.QS 9000 FMEA因分析对象不同分成“设计FMEA” 及“制程FMECA”,而MIC-STD-1629A因分析项目缺少现行 管制方法,故适合设计时使用。 5.FMEA为归纳法之应用,根据另组件的失效数据,由下而 上推断系统的失效模式及其效应,是一种向前推演的方 法。
優先數
Paper Core * 無 法 *無法捲繞 *捲繞膠帶 固 定 於 捲 繞機 8
大 1320± 2mm
5
2
80
2mm * 加 偵 測 器,未固 定測警報 E/I *加裝偵測 器 Oper -ator *要求 Operator 確實記錄 操作條件 QC *更改尺寸 1320 2mm EI *加裝對邊 器 ±
这个系统作业相关环境的信息(如:设定温度、压力、湿度范围)。
如果项目包含一个以上有不同潜在失效模式功能时,则列出所有个别 功能。
17
设计FMEA填写说明
(10)潜在失效模式 潜在失效模式是零件、子系统、或系统于符合设计意图过程 中可能失效的种类。潜在失效模式也可能是较高阶子系统或系统之 失效原因,或较低阶零组件的失效效应。 列出特别项目和功能的每一潜在失效模式。假设失效是将发 生的,但不是必须发生的。 潜在失效模式仅可能发生于某些作业条件下(如:热、冷、 干、多灰尘的条件)和在某些使用条件下(如:行驶哩数在平均数 以上、粗糙不平的地形、仅在市区行驶)。 一般的失效模式包含下列各项,但不限于此:破碎的、变形、 松弛、泄漏、黏着、短路、生锈氧化、龟裂。
12
设计FMEA表(范例2)
系统 子系统 零组件: 22092720 设计责任: 车型/年份: 通用汽车‘96 生效日期:85.08 核心小组: 如附表
項目 功能 沖模作業 潛在失 效模式 潛在失 效效應
FMEA编号: 0001 页次: 1of 1 准备者: FMEA日期(制订)85.7.15(修订)
(3)设计责任者:填入OEM、部门和小组,也包括供货商名称。
(4)准备者:填入准备FMEA责任工程师的姓名、电话号码、公司。 A.系统FMEA范围: -底盘系统;-点火系统;-内部系统
B.子系统FMEA范围
-底盘系统之前悬吊系统 C.零件范围 -〝Strut〞为前悬吊系统之零件。
16
设计FMEA填写说明
FMEA讲授内容
一.FMEA基本概念 二.FMEA之演变
三.国际间采用FMEA之状况
四.设计FMEA表填写说明 五.制程FMEA表填写说明 六.FMEA结果之应用
1
FMEA的基本概念
1.对失效的产品进行分析,找出零组件之 失效模式,鉴定出它的失效原因,研究 该项失效模式对系统会产生什么影响。
2.失效分析在找出零组件或系统的潜在弱 点,提供设计、制造、品保等单位采取 可行之对策。
7
国际间采用FMEA之状况
1.ISO 9004 8.5节FMEA作为设计审查之要项
,另FTA亦是。
2.CE标志,以FMEA作为安全分析方法。
3.ISO 14000,以FMEA作为重大环境影响面分 析与改进方法。
4.QS 9000以FMEA作为设计与制程失效分析方法。
8
设计FMEA之目的
1.帮助设计需求与设计方案的评估。 2.帮助初始设计对制造和装配的需求。 3.在设计发展阶段,增加失效模式和系统效应分析的次数。 4.提供另一项分析信息,帮助设计验证之规划。 5.根据对顾客需求的影响性,列出失效模式的排序,并按序 改善。
難 檢 度
風 險 優先數 168
建議 措施
負責人 與 日 期
執行結果 採行措施 S O D RPN
冷媒 造 成 冷 氣 洩漏 不 冷 或 將高壓高溫 A/C 不 作 氣態冷煤, 動 變為高壓中 溫液態冷媒
一般可靠 度 8 項目實驗 同上 7
7
4
196
7
‧振動接點 破損
6
同上
5
210
依測試報告編 加嚴耐腐蝕 實驗課 號 : 1212 變更 測試 材質 依測試報告編 加嚴高溫測 號 : 3212 容許 試 彎曲 2-13mm 實驗結果可接 受 5%變異 加嚴振動測 試 以上需作實車 作動耐久
發現加磨損即予更換
壓鑄 2 小時定時檢查 課長 管制 2 件外觀及 模具 模具堪用 課長 8 2 3 48
擺放不當
Hale Waihona Puke 5加強人 員之 教育訓練
5
200
須經特殊專長訓練由資深 壓鑄 經 由 定 時 檢 查 員工擔任之 課長 管制
8
4
4 128
13
设计FMEA表(范例3)
系统 FMEA编号: 0001 子系统 页次: 1of 1 零组件: 主油压缸 设计责任: 准备者: 车型/年份: 生效日期:85.10.1 FMEA日期(制订)85.9.01(修订) 核心小组: 设计系统开发小组
項目 功能 潛在失 效模式 潛在失 效效應
嚴 重 度
等 級
潛在原因 設備失效 活塞卡住,
發 生 度
現行預 防設計 管 制
現行檢 測設計 管 制 自測
難 檢 度
風 險 優先數
建議 措施 加強活塞零
負責人 與 日 期
執行結果 採行措施 S O D RPN 同建議措施
提高堆高機 活 塞 無 無法煞車 油壓煞車動 法 正 常 力 動作 活 塞 無 持續煞車 法正常 還原 8 8
高低壓油杯 蓋不良 高低壓油杯 蓋不良,彈 簧片折損
8
6
384
件檢驗是否 在設計規格 內,全檢 全檢
品管
8 3 6 144
自測 8 4 256
作疲勞度評 估
品管 品管 工程
8 3 6 144 8 3 4 96 8 2 4 64
14
设计FMEA表(范例4)
系统 FMEA编号: 1350 子系统 页次: 1of 1 零组件: PAPER 设计责任: 准备者: 车型/年份: 1350电气胶带生效日期:85.10.25 FMEA日期(制订)85.10.10(修订) 核心小组: 如附表
2
失效的定义
在失效分析中,首先要明确产品的失效是什么 ,否则产品的数据分析和可靠度评估结果将不一样, 一般而言,失效是指: 1.在规定条件下(环境、操作、时间)不能完成既 定功能。 2.在规定条件下,产品参数值不能维持在规定的上 下限之间。 3.产品在工作范围内,导致零组件的破裂、断裂、 卡死等损坏现象。
現行檢 測設計 管 制 更換沖模機
沖模之 成 品 崩 裂 過多 致外觀嚴 重不良 毛邊殘 成 品 外 觀 留過多 不良 5
當(力量不 適)
修補沖 模模 6 沖模模具崩 裂 4 具
壓鑄 模 具 週 保 養 並 課長 登 錄 於 保 養 檢 模具 查表 課長 6 2 3 36
更換模具 成品 變形 裝配及加 工受影響 8 沖模模具加 損壞 4 4 128
*變形
*無法裁切 8
*張力太高 5
設備操作 3 120
*更改操作 條件並記 錄 *改用紙管 公尺寸公 差 1320± 2mm *加裝自動 邊器
8
1
3
24
*紙管尺寸 與生產機 器公差太 大 1320± 2mm 6
說明書 IQC
2
84
8
1
2
16
15
设计FMEA填写说明
(1)FMEA编号:填入FMEA文件编号,以便可以追踪使用。 (2)系统、子系统及零组件:指示合适的分析等级,并填入系统 、子系统或零件名称或零件名称和编号。
18
设计FMEA填写说明
(11)潜在失效效应 为被客户查觉在功能特性上失效模式的效应。也就是:失 效模式一旦发生时,对系统或设备以及操作时使用的人员所造成 的影响。一般在讨论失效效应时,先检讨失效发生时对于局部所 产生的影响,然后循产品的组合架构层次,逐层分析一直到最高 层级人员、装备所可能造成的影响。例如:由于某个间歇性的系 统作业造成某个零组件的破碎,可能造成于组合过程的震动。这 个间歇性系统作业降低了系统功效,最后引起客户不满意。 常见的失效效应包括:噪音、漏气、操作费力、电动窗不 作用、煞车不灵、跳动、乱档、冷却不够、车辆性能退化、产生 臭气、外观不良…等。
10
选择关键失效模式 矫正预防 填写矫正后风险优先数
N
所有RPN小 于规定值?
Y FTA分析 DFMEA报告
进行DFMEA分析 选择关键失效模式
设计FMEA表
(2) 系统 (2) 子系统 (2) 零组件: (2) 车型/年份: (5) 核心小组:
項目 功能 潛在失 潛在失 效模式 效效應
设计责任: 生效日期: (8)
難 檢 度 5 風 險 優先數 建議 措施 由氣壓式沖模機更換,油 90 壓式 定期保養模具 5 120 負責人 與 日 期 壓鑄 課程 採行措施 2 小時檢查一次 確保外觀良好 5 2 3 30 執行結果 S O D RP N