毕业设计论文 外文文献翻译 机械设计 中英文对照
机械设计制造及自动化中英文对照外文翻译文献
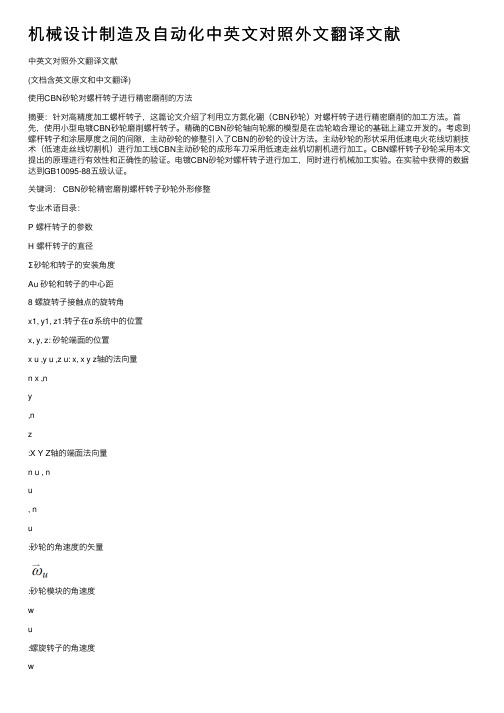
机械设计制造及⾃动化中英⽂对照外⽂翻译⽂献中英⽂对照外⽂翻译⽂献(⽂档含英⽂原⽂和中⽂翻译)使⽤CBN砂轮对螺杆转⼦进⾏精密磨削的⽅法摘要:针对⾼精度加⼯螺杆转⼦,这篇论⽂介绍了利⽤⽴⽅氮化硼(CBN砂轮)对螺杆转⼦进⾏精密磨削的加⼯⽅法。
⾸先,使⽤⼩型电镀CBN砂轮磨削螺杆转⼦。
精确的CBN砂轮轴向轮廓的模型是在齿轮啮合理论的基础上建⽴开发的。
考虑到螺杆转⼦和涂层厚度之间的间隙,主动砂轮的修整引⼊了CBN的砂轮的设计⽅法。
主动砂轮的形状采⽤低速电⽕花线切割技术(低速⾛丝线切割机)进⾏加⼯线CBN主动砂轮的成形车⼑采⽤低速⾛丝机切割机进⾏加⼯。
CBN螺杆转⼦砂轮采⽤本⽂提出的原理进⾏有效性和正确性的验证。
电镀CBN砂轮对螺杆转⼦进⾏加⼯,同时进⾏机械加⼯实验。
在实验中获得的数据达到GB10095-88五级认证。
关键词: CBN砂轮精密磨削螺杆转⼦砂轮外形修整专业术语⽬录:P 螺杆转⼦的参数H 螺杆转⼦的直径Σ砂轮和转⼦的安装⾓度Au 砂轮和转⼦的中⼼距8 螺旋转⼦接触点的旋转⾓x1, y1, z1:转⼦在σ系统中的位置x, y, z: 砂轮端⾯的位置x u ,y u ,z u: x, x y z轴的法向量n x ,ny,nz:X Y Z轴的端⾯法向量n u , nu, nu:砂轮的⾓速度的⽮量:砂轮模块的⾓速度wu:螺旋转⼦的⾓速度w1螺旋转⼦模块的⾓速度转⼦接触点的⾓速度转⼦表⾯接触点的初始速度砂轮表⾯接触点的⾓速度砂轮表⾯接触点的初始速度l砂轮的理论半径砂轮轴的理想位置砂轮表⾯的修改半径砂轮轴的修改位置砂轮表⾯的法向量1.引⾔螺旋转⼦是螺杆压缩机、螺钉、碎纸机以及螺杆泵的关键部分。
转⼦的加⼯精度决定了机械性能。
⼀般来说,铣⼑⽤于加⼯螺旋转⼦。
许多研究者,如肖等⼈[ 1 ]和姚等⼈[ 2 ],对⽤铣⼑加⼯螺旋转⼦做了⼤量的⼯作。
该⽅法可以提⾼加⼯效率。
然⽽,加⼯精度低和表⾯粗糙度不⾼是其主要缺点。
机械设计外文文献翻译、中英文翻译

外文原文Mechanical DesignAbstract:A machine is a combination of mechanisms and other components which transforms, transmits. Examples are engines, turbines, vehicles, hoists, printing presses, washing machines, and movie cameras. Many of the principles and methods of design that apply to machines also apply to manufactured articles that are not true machines. The term "mechanical design" is used in a broader sense than "machine design" to include their design. the motion and structural aspects and the provisions for retention and enclosure are considerations in mechanical design. Applications occur in the field of mechanical engineering, and in other engineering fields as well, all of which require mechanical devices, such as switches, cams, valves, vessels, and mixers.Keywords: Mechanical Design mechanisms Design ProcessThe Design ProcessDesigning starts with a need real.Existing apparatus may need improvements in durability, efficiency, weight, speed, or cost. New apparatus may be needed to perform a function previouslydone by men, such as computation, assembly, or servicing. With the objective wholly or partlyIn the design preliminary stage, should allow to design the personnel fully to display the creativity, not each kind of restraint. Even if has had many impractical ideas, also can in the design early time, namely in front of the plan blueprint is corrected. Only then, only then does not send to stops up the innovation the mentality. Usually, must propose several sets of design proposals, then perform the comparison. Has the possibility very much in the plan which finally designated, has used certain not in plan some ideas which accepts.When the general shape and a few dimensions of the several components becomeapparent, analysis can begin in earnest. The analysis will have as its objective satisfactory or superior performance, plus safety and durability with minimum weight, and a competitive cost. Optimum proportions and dimensions will be sought for each critically loaded section, together with a balance between the strengths of the several components. Materials and their treatment will be chosen. These important objectives can be attained only by analysis based upon the principles of mechanics, such as those of static for reaction forces and for the optimum utilization of friction; of dynamics for inertia, acceleration, and energy; of elasticity and strength of materials for stress and deflection; of physical behavior of materials; and of fluid mechanics for lubrication and hydrodynamic drives. The analyses may be made by the same engineer who conceived the arrangement of mechanisms, or, in a large company, they may be made by a separate analysis division or research group. Design is a reiterative and cooperative process, whether done formally or informally, and the analyst can contribute to phases other than his own. Product design requires much research and development. Many Concepts of an idea must be studied, tried, and then either used or discarded. Although the content of each engineering problem is unique, the designers follow the similar process to solve the problems. Product liability suits designers and forced in material selection, using the best program. In the process of material, the most common problems for five (a) don't understand or not use about the latest application materials to the best information, (b) failed to foresee and consider the reasonable use material may (such as possible, designers should further forecast and consider due to improper use products. In recent years, many products liability in litigation, the use of products and hurt the plaintiff accused manufacturer, and won the decision), (c) of the materials used all or some of the data, data, especially when the uncertainty long-term performance data is so, (d) quality control method is not suitable and unproven, (e) by some completely incompetent persons choose materials.Through to the above five questions analysis, may obtain these questions is does not have the sufficient reason existence the conclusion. May for avoid these questions to these questions research analyses the appearance indicating the direction. Although uses the best choice of material method not to be able to avoid having the product responsibility lawsuit, designs the personnel and the industry carries on the choice of material according to the suitable procedure, may greatly reduce the lawsuit the quantity.May see from the above discussion, the choice material people should to the material nature, the characteristic and the processing method have comprehensive and the basic understanding.Finally, a design based upon function, and a prototype may be built. If its tests are satisfactory, the initial design will undergo certain modifications that enable it to be manufactured in quantity at a lower cost. During subsequent years of manufacture and service, the design is likely to undergo changes as new ideas are conceived or as further analyses based upon tests and experience indicate alterations. Sales appeal.Some Rules for DesignIn this section it is suggested that, applied with a creative attitude, analyses can lead to important improvements and to the conception and perfection of alternate, perhaps more functional, economical,and durable products.To stimulate creative thought, the following rules are suggested for the designer and analyst. The first six rules are particularly applicable for the analyst.1. A creative use of need of physical properties and control process.2. Recognize functional loads and their significance.3. Anticipate unintentional loads.4. Devise more favorable loading conditions.5. Provide for favorable stress distribution and stiffness with minimum weight.6. Use basic equations to proportion and optimize dimensions.7. Choose materials for a combination of properties.8. Select carefully, stock and integral components.9. Modify a functional design to fit the manufacturing process and reduce cost.10. Provide for accurate location and noninterference of parts in assembly.Machinery design covers the following contents.1. Provides an introduction to the design process , problem formulation ,safety factors.2. Reviews the material properties and static and dynamic loading analysis ,Including beam , vibration and impact loading.3. Reviews the fundamentals of stress and defection analysis.4. Introduces fatigue-failure theory with the emphasis on stress-life approaches to high-cycle fatigue design, which is commonly used in the design of rotation machinery.5. Discusses thoroughly the phenomena of wear mechanisms, surface contact stresses ,and surface fatigue.6. Investigates shaft design using the fatigue-analysis techniques.7. Discusses fluid-film and rolling-element bearing theory and application8. Gives a thorough introduction to the kinematics, design and stress analysis of spurgears , and a simple introduction to helical ,bevel ,and worm gearing.9. Discusses spring design including compression ,extension and torsion springs.10. Deals with screws and fasteners including power screw and preload fasteners.11. Introduces the design and specification of disk and drum clutches and brakes. Machine DesignThe complete design of a machine is a complex process. The machine design is a creative work. Project engineer not only must have the creativity in the work, but also must in aspect and so on mechanical drawing, kinematics, engineerig material, materials mechanics and machine manufacture technology has the deep elementary knowledge. One of the first steps in the design of any product is to select the material from which each part is to be made. Numerous materials are available to today's designers. The function of the product, its appearance, the cost of the material, and the cost of fabrication are important in making a selection. A careful evaluation of the properties of a. material must be made prior to any calculations.Careful calculations are necessary to ensure the validity of a design. In case of any part failures, it is desirable to know what was done in originally designing the defective components. The checking of calculations (and drawing dimensions) is of utmost importance. The misplacement of one decimal point can ruin an otherwise acceptable project. All aspects of design work should be checked and rechecked.The computer is a tool helpful to mechanical designers to lighten tedious calculations, and provide extended analysis of available data. Interactive systems, based on computer capabilities, have made possible the concepts of computer aided design (CAD) and computer-aided manufacturing (CAM).How does the psychologist frequently discuss causes the machine which the people adapts them to operate. Designs personnel''s basic responsibility is diligently causes the machine to adapt the people. This certainly is not an easy work, because certainly does not have to all people to say in fact all is the most superior operating area and the operating process.Another important question, project engineer must be able to carry on the exchange and the consultation with other concerned personnel. In the initial stage, designs the personnel to have to carry on the exchange and the consultation on the preliminary design with the administrative personnel, and is approved. This generally is through the oral discussion, the schematic diagram and the writing material carries on.If front sues, the machine design goal is the production can meet the human need the product. The invention, the discovery and technical knowledge itself certainly notnecessarily can bring the advantage to the humanity, only has when they are applied can produce on the product the benefit. Thus, should realize to carries on before the design in a specific product, must first determine whether the people do need this kind of product Must regard as the machine design is the machine design personnel carries on using creative ability the product design, the system analysis and a formulation product manufacture technology good opportunity. Grasps the project elementary knowledge to have to memorize some data and the formula is more important than. The merely service data and the formula is insufficient to the completely decision which makes in a good design needs. On the other hand, should be earnest precisely carries on all operations. For example, even if places wrong a decimal point position, also can cause the correct design to turn wrongly.A good design personnel should dare to propose the new idea, moreover is willing to undertake the certain risk, when the new method is not suitable, use original method. Therefore, designs the personnel to have to have to have the patience, because spends the time and the endeavor certainly cannot guarantee brings successfully. A brand-new design, the request screen abandons obsoletely many, knows very well the method for the people. Because many person of conservativeness, does this certainly is not an easy matter. A mechanical designer should unceasingly explore the improvement existing product the method, should earnestly choose originally, the process confirmation principle of design in this process, with has not unified it after the confirmation new idea.外文资料翻译译文机械设计摘要:机器是由机械装置和其它组件组成的。
机械设计类英文文献及翻译

The Sunflower Seed Huller and Oil PressBy Jeff Cox-- from Organic Gardening, April 1979, Rodale PressIN 2,500 SQUARE FEET, a family of four can grow each year enough sunflower seed to produce three gallons of homemade vegetable oil suitable for salads or cooking and 20 pounds of nutritious, dehulled seed -- with enough broken seeds left over to feed a winter's worth of birds.The problem, heretofore, with sunflower seeds was the difficulty of dehulling them at home, and the lack of a device for expressing oil from the seeds. About six months ago, we decided to change all that. The job was to find out who makes a sunflower seed dehuller or to devise one if none were manufactured. And to either locate a home-scale oilseed press or devise one. No mean task.Our researches took us from North Dakota -- hub of commercial sunflower activity in the nation -- to a search of the files in the U.S. Patent Office, with stops in between. We turned up a lot of big machinery, discovered how difficult it is to buy really pure, unrefined vegetable oils, but found no small-scale equipment to dehull sunflowers or press out their oil. The key to success, however, was on our desk the whole time. In spring 1977, August Kormier had submitted a free-lance article describing how he used a Corona grain mill to dehull his sunflower seeds, and his vacuum cleaner exhaust hose to blow the hulls off the kernels. A second separation floated off the remaining hulls, leaving a clean product. We'd tried it, but because some kernels were cracked and the process involved drying, we hadn't been satisfied. Now we felt the best approach was to begin again with what we learned from Mr. Kormier and refine it.Staff Editor Diana Branch and Home Workplace Editor Jim Eldon worked with a number of hand- and electric-powered grain mills. While the Corona did a passable job, they got the best results with the C.S. Bell #60 hand mill and the Marathon Uni Mill, which is motor-driven. "I couldn't believe my eyes the first time I tried the Marathon," Diana says. "I opened the stones to 1/8th inch, and out came a bin full of whole kernels and hulls split right at the seams. What a thrill that was!"She found that by starting at the widest setting,and gradually narrowing the opening, almost every seed was dehulled. The stones crack the hulls open, then rub them to encourage the seed away from the fibrous lining. The Bell hand mill worked almost as well. "As long as the stones open at least as wide as the widest unhulled seed, any mill will work," she says.Because the seed slips through the mill on its flat side, grading is an important step to take before dehulling. We made three sizing boxes. Thefirst is 1/4-inch hardware cloth [wire screen]. The second is two layers of1/4-inch cloth, moved slightly apart to narrow the opening in one direction, and the third is two layers of screen adjusted to make a still-smaller opening. Since the smallest unhulled seeds are about the size of the largest hulled kernels, the grading step prevents these undersized seeds from passing through unhulled. Processed together at a closer setting, the smallest seeds hulled out.Jim Eldon's workshop is littered with strange-looking pieces of apparatus. They represent initial attempts to build a workable winnowing box, using Kormier's vacuum exhaust idea for a source of air. Jim, Fred Matlack and Diana finally made a box with a Plexiglas front, through which they could observe what was happening.They cut a hole in the back of the box with a sliding cover to regulate the air pressure, and fiddled with various arrangements of baffles. The result was a stream of hulls exiting through one hole while the kernels fell to the bottom of the box. Now they were ready to try a five-pound sample of unhulled sunflower seeds to see how much they could recover.The five pounds were graded and dehulled, then winnowed. We got about one hull for every ten kernels in the final, winnowed product. These are easily picked out. They usually contain kernels still held behind the fibrous strings of the hull. Their weight prevents them from blowing out with the empty hulls. We found that bug-eaten seeds do blow away with the chaff, which was a bonus for cleanliness of the final product. Toss the hulls to the birds, who will find broken seeds among them.Starting with 80 ounces of unhulled seed, we ended up with 41-1/4 ounces of edible whole seeds, 1.8 ounces of damaged seeds suitable for animal feed, and 36.6 ounces of hulls. It took us about an hour. Notbad.Sunflower seeds store perfectly in the hulls, but they deteriorate more rapidly when shelled out. The grain mill dehuller and winnowing box give the gardener a way to have the freshest possible seeds for eating at all times of the year. With the construction of one more piece of equipment -- the oil press -- he can have absolutely fresh, unrefined, polyunsaturated sunflower oil for salads, mayonnaise and cooking.Most light, refined vegetable oils have been extracted using hexane, a form of naphtha. The oil is then heated to boil off the hexane. Lye is dumped into it. It's washed with steam, then heated to remove odors and taste before being laced with preservatives and stabilizers. It may feel oily in the mouth, but you might as well taste air. No so with fresh-made sunflower oil -- it's deliciously yet subtly nutty in flavor, adding unsurpassed flavor to salads.There's good reason to believe that sunflower oil may become the #1 vegetable oil in the U.S. in a few years. It's already #1 in health-conscious Europe. Corn oil has already caught on here for health reasons, and sunflower oil is so much better. Sunflower oil's 70 percent polyunsaturate is just under safflower, with corn oil bringing up the rear with 55 percent. And sunflowers yield 40 percent oil, soybeans only 20 percent.Our oil press isrelatively simple, but it must be welded together. Check the construction directions for details. The press consists of a welded tubular frame which accepts a three-ton hydraulic jack. You may already have one. If not, it can be purchased at most auto and hardware stores for about $16. A metal canister with holes drilled in its sides and one end welded shut holds the mashed sunflower seeds. A piston is inserted in the canister and then inverted and slipped over a pedestal on the frame. The jack is set in place, and the pressure gradually increased over half an hour. The oil drips from the sides of the canister into a tray -- the bottom of a plastic jug slipped over the pedestal works fine -- which empties the oil into a cup. You can filter the oil with a coffee filter to remove pieces of seed and other fine particles that would burn if the oil were used for cooking. If it's for salads or mayonnaise, there's no need to filter it.We first tried using "confectionary" sunflower seeds for oil. These are the regular eating kernels we're used to seeing. They give less than half as much oil as the oilseed types of sunflower. Although you can use confectionary types such as MAMMOTH RUS- SIAN for oil, don't expect to get more than an ounce and a half from a pound of seed. Oilseed produces three or more ounces of oil from a pound of seed and is well worth planting along with confectionary-type seeds. Oilseed has another big advantage -- to prepare it, you can put the whole, unhulled seed into a blender and whiz it until it forms a fine meal, while confectionary seeds must be dehulled first. The entire sequence of grading, dehulling and winnowing is avoided with oilseed.Oil types produce about a tenth of a pound of seed per head in commercial production. Gardeners, with their better soil and care, invariably do better than that. Our conservative estimate is that 1,280 plants will be enough for three gallons of oil. Spaced one foot apart in rows two feet apart, 1,280 oilseed plants will take a space 40-by-56 feet, or 80-by-28 if you want a more rectangular patch to face south.We worked in pound batches, since the canister just holds one pound of mash. After blending, we heated it to 170 degrees F. (77 deg C) by placing it in a 300-degree F. (149 deg C) oven and stirring it every five minutes for 20 minutes. Heating gets the oil flowing and doubles the yield of oil. In case you're wondering,"cold-pressed" oils sold commercially are also heated, and some are subjected to the entire chemical process. The term has no firm meaning within the industry, according to the literature we've surveyed.Heating does not change the structure of fats. It will not turn polyunsaturated fats into saturated fats. In fact, Dr. Donald R. Germann in his book, "TheAnti-Cancer Diet", says that "... an unsaturated fat must be heated to high temperatures -- above 425 degrees F. or 200 degrees C. -- at least 8 or 10 times before any shift toward saturation occurs..." Dean C. Fletcher, Ph.D., of the American Medical Association Department of Foods and Nutrition in Chicago, says, "It's true that either high temperature or repeated heatingdoes change the nature of some of the unsaturated oil molecules. (But) the flavor of the oil changes as these chemical changes occur, spoiling its taste. This effect is probably more profound than any of the physiological changes the altered oil might produce within the body."From 500 gm. of heated mash, we pressed 89 gm. of oil, 89 percent of the entire amount available and twice as much as we could press from unheated oil! The decision is up to you whether or not to heat the mash, but that extra 50 percent seems like an awful lot, especially when the whole technique is so labor intensive. The oil should be stored in the refrigerator, and it's probably best to use it within a month, since it has no preservatives. Mayonnaise made with such fresh oils should be kept refrigerated and used within two weeks. The leftover cake, still containing 50 percent of its oil, is a nutritious addition to your dishes, and makes excellent feed for animals or winter birds. Store the pressed cake in the freezer.We're talking then about a sunflower patch with two kinds of plants -- confectionary such as MAMMOTH RUSSIAN and oilseed such as PEREDOVIK. The oilseed plants should be grown 12 inches apart in rows two feet apart. Four average confectionary heads yield about a pound of unhulled seed. You'll need about 35 pounds of unhulled seed, or 140plants-worth, to yield 20 pounds of hulled kernels, about what a family of four will use in a year. That many plants can be grown in an area 26-by-10 feet. That's 260 square feet. Put that together with the 2,240 square feet for the oilseed sunflowers, and you need a patch about 2,500 square feet -- 25 100-foot rows -- to keep yourself supplied year-round with super nutrition and unsurpassable taste.Winnowing Machine For Sunflower SeedsThe winnowing machine operates on the age-old principle of blowing the chaff away from the heavy grain with a controlled current of air.The unit uses a household or shop-type vacuum cleaner for its air supply. A vacuum cleaner was used as a power source because it can supply a large volume of air over an extended period of time, and most homes and farms have a vacuum cleaner.A cloth bag has been attached to the chaff chute to catch the chaff as it is separated from the seed. The bag allows the hulls to be collected and greatly reduces the amount of waste material normally blown into the air by conventional systems.The unit has been constructed in such a way that the cloth bag and cleaner box can be placed inside the seed box, making a compact package for storage.Tools Required1. Table Saw2. Drill Press3. Band Saw4. Saber SawProcedure (cleaner box)1 . Cut out the two sides of the cleaner box from 1/4-inch plywood.2. Cut out the six interior pieces of the cleaner box from 3/4 x 3-1/2-inch select pine.3. Assemble the cleaner box elements with glue and nails.4. Cut four 1/4-inch square strips of pine four inches long.5. Glue the strips around the end of the chaff chute.6. Sand all surfaces and edges.7. Finish with clear lacquer finish.Procedure (seed box)1. Cut two pieces of pine /34" x 5 /12 x 15 inches for the sides.2. Cut two pieces of pine 3/4 x 5-1/2 x inches for the top and bottom.3. Plow a /14 x 1/4 groove for the front and back panels in all four pieces.4. Rip the top board to 5 inches so that the front panel can slide into the grooves in the side boards.5. Rabbet both ends of each 15-inch side piece to accept the top and bottom boards.6. Drill a hole in the left side board 2-1/2 inches from the top. The size of the hole is determined by the vacuum cleaner hose fitting.7. Cut a 3-1/4 x 4 inch hole in the top 1/2 inch from the right end. This hole will accept the cleaner box.8. Cut two pieces of pine for the baffle.9. Drill two 1-inch holes in the bottom of the baffle box.10. Cut a piece of 1/4 x 8-1/2 x 14 inch plywood for the back panel.11. Cut a 3-inch hole, centered 1-7/8 inches from the top and left sides of the plywood back.12. Assemble the sides, baffles, top, bottom, and back panel with glue and nails.13. Cut an 8-7/16 x 15-3/4-inch piece of Plexiglas for the front.14. Cut a one-inch radius on the top corners of the front.and sand the edges.15. Drill a one-inch thumb hole centered 7/8 inch from the top edge.16. Cut a 3-1/2-inch disk of 1/4-inch plywood for the vent cover.17. Drill a 3/16-inch hole 3/8 inch from the edge of the disk.18. Mount the disk over the vent with a #10 x 1-inch screw.19. Sand all surfaces and edges of the, box.20. Finish with clear lacquer finish.MaterialsCleaner Box2 -- 7-3/4 x 7-1/2 x 3/4" plywood (sides)6 -- 3/4 x 3-1/2 x 24" for all members (baffles)4 -- 1/4 x 1/4 x 4" pine (chute cleats)22 -- 1" x 18 ga. headed nailsWhite vinyl glueClear lacquer finishSeed Box2 -- 3/4' x 5-1/2 x 15" select pine (sides)2 -- 3/4 x 5-1/2 x 8-1/2" select pine (top and bottom)1 -- 3/4 x 3-1/2 x 4-1/2" select pine (baffle)1 -- 3/4 x 4-1/2 x 4-1/2" select pine (baffle)1 -- 1/4 x 8-1/2 x 14" plywood (back)1 -- 1/4 x 3-1/2" dia. plywood (control valve)1 -- 1/4' x 8-7/16 x 15-1/4" Plexiglas (front)1 - #10 x 1" flat head screw18 - 4d finish nailsWhite vinyl glueClear lacquer finish1 -- 17 x 31" cloth laundry bagSunflower Seed Oil PressThe press was designed so that homesteaders can produce sunflower oil from their own seeds. The oil can be pressed as is or heated to 170 degrees F., which doubles oil yield.Both methods require the seed to be ground to fine powder. If you are pressing the oil seed variety, a meat grinder or electric blender will do an excellent job of grinding the seed. The confectionary type of seed will require the seed to be hulled and winnowed before it is ground. A food mill with the stones set at the coarse setting can be used to accomplish this step. The ground kernels are placed in the cylinder with the piston closing the bottom portion of the cylinder.The cylinder is mounted in the press frame and a three-ton hydraulic jack is used to supply the pressure.Because of the great pressures created by the hydraulic jack, it is important that the frame be properly constructed and firmly mounted to the work surface before the pressing operation begins. The following instructions can be given to a welder.Tools Required1. Power Hacksaw2. Metal Band Saw3. Metal Lathe4. Drill Press5. Belt or Disk Grinder6. Arc Welder7. Hand ClampsProcedure (Frame)1. Cut two pieces of 1-3/4" O.D. x 1-3/8" I.D. x 24-1/2 inch long tubing for the uprights.2. Cut one piece of 1-3/4" O.D. x 1-3/8" I.D. x 6-1/2 inch long tubing for the center tube.3. Cut one 3/4" x 2-3/4 x 5-1/2 inch steel bar for the top cross member.4. Cut two pieces of 1-3/4 x 1-3/4 x 8 inch angle iron for the base members.5. Drill two 9/32-inch holes in each base member 1/2 inch from the outer edges.6. Weld the base members, tubes and cross member together as per the drawing.7. Grind all edges to remove any burrs.8. Paint the frame.9. If a mounting board is desired, cut a piece of pine 1-1/4 x 6-1/2 x 12 inches long.10. Center the frame on the board and mark the location of the four mounting holes.11. Drill four 7/8-inch holes 1/4-inch deep to accept the T-nuts.12. Drill four 5/16-inch holes through the mounting board using the same centers created by the 7/8-inch holes.13. Round the edges of the base and sand all surfaces.14. Install four 1/4-20 T-nuts.15. Finish the base with clear lacquer finish.16. Assemble the base to the frame using four 1/4-20 x 1-1/4-inch round head bolts.Procedure (Cylinder)1. Cut a piece of 3-1/2" O.D. x 3-1/4" I.D. tubing 5-3/8 inches long.2. Face both ends on the lathe.3. Cut out a 3-1/2-inch round disk from 1/4-inch plate steel.4. Weld the disk to one end of the tube.5. Drill a series of 3/32-inch holes around the side of the tube on 1/2-inch centers.6. Remove all burrs on the inside and outside of the tube.Procedure (Piston)1. Cut out a 3-3/8-inch disk of 1/4-inch plate steel.2. Cut a 1-3/8" O.D. x 1-1/8" I.D. piece of tubing 1-1/8 inches long.3. Face both ends of the tube.4. Weld the tube in the center of the 3-3/8-inch disk. All welds should be made on the inside of the tube.5. Mount the piston in the lathe and turn the disk to fit the inside diameter of the cylinder. This will be about 3-15/64 inches in diameter.6. Remove any sharp edges.Procedure (Collector Ring)1. Cut the bottom out of a one-gallon plastic bottle. The cut line should be approximately 1-1/2 inches from the bottom of the bottle.2. Make a 1/8 x 1 inch slot at one edge of the bottom outside ring. This will allow the oil to pour into a receiving cup.3. Cut a 1-3/4-inch hole in the center of the bottom, so that the unit will fit over the center tube in the frame.MaterialsFrame2 -- 1-3/4 O.D. x 1-3/8 I.D. x 24-1/2" long H.R.S. (frame tubes)1 -- 1-3/4 O.D. x 1-3/8 I.D. x 6-1/2 inch long H.R.S. (center tube)1 -- 3/4 x 2-3/4 x 5-1/2" flat bar H.R.S. (top cross member)2 -- 1-3/4 x 1-3/4 x 8" angle iron H.R.S. (base members)1 -- 1-1/4 x 6-1/2 x 12" #2 white pine (wood base)4 -- 1/4-20 x 1-1/4 R.H. mounting bolts4 -- 1/4-20 T-nutsBlack enamel for frame (finishing material)Clear lacquer finish for wood base3 -- 1/8" dia. welding rodsCylinder1 -- 1/4 x 3-1/2" dia. C.R.S. disk (top)1 -- 3-1/2 O.D. x 3-1/4 I.D. C.R.S. tube (cylinder)1 -- 1/8 dia. welding rodPiston1 -- 1/4 x 3-3/8 D.A. C.R.S. disk (piston top)1 -- 1-1/4 O.D. x 1 I.D. x 1" long H.R.S. (piston tube)1 -- 1/8 dia. welding rodCollector Ring1 -- Bottom from a one-gallon plastic bottle (oil collector ring)葵花籽脱壳机和油压机由Jeff考克斯-从有机园艺,1979年4月,罗代尔新闻2,500平方尺,一个四口之家每年可以长到足以产生三种葵花籽国产蔬菜沙拉或烹调油和20磅的营养丰富,适合脱皮加仑种子 - 与遗留养活一个冬天的产值,破碎的种子鸟类。
机械专业毕业设计英文文献翻译
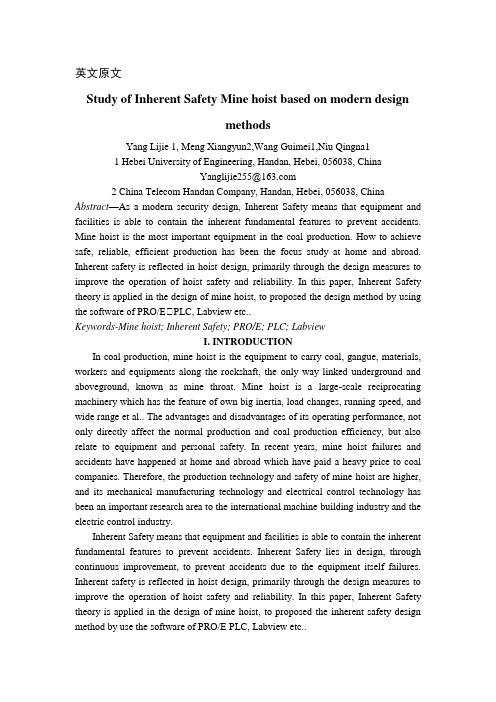
英文原文Study of Inherent Safety Mine hoist based on modern designmethodsYang Lijie 1, Meng Xiangyun2,Wang Guimei1,Niu Qingna11 Hebei University of Engineering, Handan, Hebei, 056038, ChinaYanglijie255@2 China Telecom Handan Company, Handan, Hebei, 056038, China Abstract—As a modern security design, Inherent Safety means that equipment and facilities is able to contain the inherent fundamental features to prevent accidents. Mine hoist is the most important equipment in the coal production. How to achieve safe, reliable, efficient production has been the focus study at home and abroad. Inherent safety is reflected in hoist design, primarily through the design measures to improve the operation of hoist safety and reliability. In this paper, Inherent Safety theory is applied in the design of mine hoist, to proposed the design method by using the software of PRO/E PLC, Labview etc..Keywords-Mine hoist; Inherent Safety; PRO/E; PLC; LabviewI. INTRODUCTIONIn coal production, mine hoist is the equipment to carry coal, gangue, materials, workers and equipments along the rockshaft, the only way linked underground and aboveground, known as mine throat. Mine hoist is a large-scale reciprocating machinery which has the feature of own big inertia, load changes, running speed, and wide range et al.. The advantages and disadvantages of its operating performance, not only directly affect the normal production and coal production efficiency, but also relate to equipment and personal safety. In recent years, mine hoist failures and accidents have happened at home and abroad which have paid a heavy price to coal companies. Therefore, the production technology and safety of mine hoist are higher, and its mechanical manufacturing technology and electrical control technology has been an important research area to the international machine building industry and the electric control industry.Inherent Safety means that equipment and facilities is able to contain the inherent fundamental features to prevent accidents. Inherent Safety lies in design, through continuous improvement, to prevent accidents due to the equipment itself failures. Inherent safety is reflected in hoist design, primarily through the design measures to improve the operation of hoist safety and reliability. In this paper, Inherent Safety theory is applied in the design of mine hoist, to proposed the inherent safety design method by use the software of PRO/E PLC, Labview etc..II. INHERENT SAFETY THEORYThe term of inherent safety originates the development of world space technology in the 1950s. The concept is widely accepted closely linked with scientific technological progress and human understanding of safety culture. The concept of inherent safety produced after the World War II which became major safety concept in many industrialized countries since the mid 20th century.Inherent safety design as the basic method of hazard control, by selecting safe materials, process routes, mechanical equipment, devices, to eliminate or control hazards source rather than relying on "additional" security measures or management measures to control them. As inherent safety design, firstly analyze and identify hazards that may occur in system, and then choose the best methods to eliminate, control hazards, which reflected in project design.Ⅲ. THE DESIGN OF INHERENT SAFETY MINE HOISTMine hoist mainly includs the working device, control system, transmission system and drag, protection systems and other components. To the inherent safety mine hoist design, mainly the mechanical system, control system and monitor system is the major part to considered.A.In-depth investigations to find malfunctionThe concept of inherent safety is required safety all the time in the product design process. That is, the equipment has little malfunction as much as possible during the operation and has long normal operation cycle length. How can design inherent safety equipment, the most important thing is understanding enough to the equipment, especially in work. After in-depth research, fully understanding the situation, try the best to reduce or eliminate the fault in the design. After in-depth understanding of research, design product.B. Mechanical SystemThe traditional method of product has long design cycle, high costs. However, the virtual prototype technology has the advantage in saving the design cost, shortening the design circle, by using the method of modeling, simulation first and then builds the physical prototype. Therefore, the virtual design is the developing trends of mechanical design. In mechanical system design, the application of virtual prototype is used to design mine hoist, not only speeded up the design process, also simulated a variety of conditions to the virtual prototype to discover design faults, to improve the design, to improve mine hoist performance.Mine hoist mechanical system is composed of spindle, roller, reducer, motor, brakes and other components. In its design, virtual design software PRO / E is applied to establish hoist prototype, application of simulation software ADAMS is used to simulate and optimize the design. Specific process shown in Figure 1:Figure 1. Mechanical system designC. Control system designMine hoist control system includes start, run, brake, etc., the requirements in control system are:In normal hoist operation, participation in hoist speed control, brake the hoist when reaching the destination, known as the service braking;In case of emergency, can quickly slow down as required, brake hoist, to prevent the expansion of the accident, that is the safety braking; Participate in the hoist speed control when decelerati; To double-roller hoist, should brake the moving roller and fix roller respectively when regulating rope length, replacement level and changing rope, so that, moving roller would not move when spindle rotates with the fixed roller.Most of mine hoists in China (more than 70%) use the traditional electric control system (tkd-a as the representative). Tkd control system is composed of relay logic circuits, large air contactors, tachometer generator etc., which is a touch control system. After years of development, tkd-a series of electric control system has formed its own characteristics, but its shortcomings are obvious. Its electrical circuit is too complicated, multi-line, causing hoist parking and accidents occurred due to electrical fault. With the computer and digital technology, to form a digital hoist control systemof PLC has become possible. PLC control system has high control precision, parameter stability, simple hardware structure, self-diagnostic capability and communication networking function.Mine hoist control system based on PLC technology structure shown in Figure 2, mainly including the following components: the main plc control circuits, hoist route detection and display circuits, speed detection, and signal circuits. The PLC of the main control circuits uses Mitsubishi FX2N series in Japan which more domestic applications.Figure 2 PLC electric control systemD. Monitoring system designTo ensure safe operation of the hoist, except for selecting the reasonable operation design parameters, the use of advanced control system, should also monitor the technological parameters on regular, conscientiously do performance test work to master the hoist performance, discover the defects in time, eliminate hidden danger,avoid unnecessary losses. In addition, the hoist operation state can be improved to work in the best conditions based on test data. Therefore, the hoist could work safely, reliably, have high efficiency, and extend its work life.Virtual instrument technology is computer-based instrumentation and measurement technology, is loaded some software and hardware on the computer with similar appearance and performance of the actual independent instrument. The user operating the computer, like manipulating a especially conventional electronic devices designed theirs. The essence of virtual instrument technology is that hardware softwarized technology, take full advantage of the latest computer technology to implement and expand the functions of traditional instruments.LabVIEW (laboratory virtual instrument engineering workbench) is a graphical programming and development environment, also known as "G" language. It is widely used by industry, academia and research laboratories, accepted as the standard data acquisition and instrument control software. LabVIEW not only provides and complies with all the functions of hardware and data acquisition cards communications of GPIB, VXI, RS-232 and RS-485 protocol, and built-in library functions support for TCP / IP, ActiveX and other software standards. The software for scientists and engineers is a programming language, it provides a simple, intuitive graphical programming mode, saves a lot of development time, has complete function, best embodied style of virtual instrument.In response to these circumstances, developed a mine hoist Integrate Performance Monitoring System based on virtual instrument LabVIEW-based. Show in Figure 3. With signal conditioning and data acquisition card to receive signals from sensors, then sent the received signal to the virtual instrument software platform, enables the following features:(1)show speed, acceleration, braking time, displacement, oil pressure, delay time and other relevant parameters in digital, and display speed, acceleration, traction, displacement and hydraulic curves.(2)Dynamically monitor the hydraulic oil pressure and oil pump running station, based on these parameters to avoid important braking system failure.(3)Test brake air travel time, relay delay time and other time parameters.(4)inquiry to the measured curve and hoist parameters; print a test report.Figure 3. Diagram of test systemThe monitoring system has characteristics such as compact, light weight, high precision, testing convenient and flexible, feature-rich software etc.. the system can not only display automatically test results, but also finish multiple functions, for example , data transmission, analysis, processing, storage and report printing. The system is high precision, can easily monitor the hoist operation state, to ensure the reliability of hoist operation.Ⅳ. CONCLUSIONSIn this paper, used virtual design software to design the hoist mechanical system, PLC to design control system, applied virtual instrument software-LABVIEW to design monitor system. Therefore, the mine hoist designed has good mechanical properties and safe operation, monitoring easy.REFERENCES[1] Weng qishu. The inherent safety and checks of cabin[J]. navigationTechnology 2006 (3):50-52. (in Chinese)[2] Li jangbo. Study of Test System of Composite Characteristic of Devices Based onVirtual instrument[D]. A Dissertation Submitted to Hebei University ofEngineering For the Academic Degree of Master of Engineering, 2007. (inChinese)[3] Wang chengqin, Li wei , Meng baoxing et al... Random vibration testing system ofhoisting gear based on virtual instrument. Coal mine machinery, 2008(4) :118-120.(in Chinese)[4] Chen baozhi Wu min. concept and practices of inherent safety[J]. Journal ofSafety Science and Technology,2008(6):79-83. (in Chinese)[5] Xu chenyi, Wu yongdong, Huanghe et al.. A PLC-based mine hoist control systemdesign [J]. LC&FA, 2008(10):52-56 (in Chinese)中文译文基于现代设计方法的矿井提升机内在安全性的研究Yang Lijie 1, Meng Xiangyun2,Wang Guimei1,Niu Qingna11河北工程大学,河北邯郸,056038,中国Yanglijie255@2中国电信邯郸分公司,河北邯郸,056038,中国摘要:作为一个现代的安全设计,内在的安全性意味着设备和设施能够包含防止事故发生的固有基本特征。
现代包装机械设备毕业课程设计外文文献翻译、中英文翻译
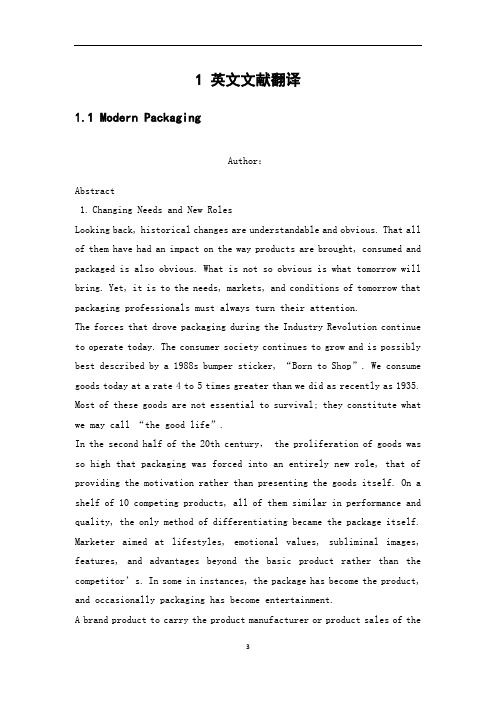
1 英文文献翻译1.1 Modern PackagingAuthor:Abstract1. Changing Needs and New RolesLooking back, historical changes are understandable and obvious. That all of them have had an impact on the way products are brought, consumed and packaged is also obvious. What is not so obvious is what tomorrow will bring. Yet, it is to the needs, markets, and conditions of tomorrow that packaging professionals must always turn their attention.The forces that drove packaging during the Industry Revolution continue to operate today. The consumer society continues to grow and is possibly best described by a 1988s bumper sticker, “Born to Shop”. We consume goods today at a rate 4 to 5 times greater than we did as recently as 1935. Most of these goods are not essential to survival; they constitute what we may call “the good life”.In the second half of the 20th century, the proliferation of goods was so high that packaging was forced into an entirely new role, that of providing the motivation rather than presenting the goods itself. On a shelf of 10 competing products, all of them similar in performance and quality, the only method of differentiating became the package itself. Marketer aimed at lifestyles, emotional values, subliminal images, features, and advantages beyond the basic product rather than the competitor’s. In some in instances, the package has become the product, and occasionally packaging has become entertainment.A brand product to carry the product manufacturer or product sales of theretailer’s label, usually by the buyer as a quality assessment guidance. In some cases, competing brands of product quality is almost no difference, a difference is the sale of its packaging. An interesting visually attractive packaging can give a key marketing advantage and convince impulse spending. However, the packaging should accurately reflect the quality of products/brand value in order to avoid the disappointment of consumers, encourage repeat purchases and build brand loyalty. Ideally, the product should exceed customer expectations.2. Packaging and the Modern Industrial SocietyThe importance of packaging to a modern industrial society is most evident when we examine the food-packaging sector. Food is organic in nature, having an animal or plant source. One characteristic of such organic matter is that, by and large, it has a limited natural biological life.A cut of meat, left to itself, might be unfit for human consumption by the next day. Some animal protein products, such as seafood, can deteriorate within hours.The natural shelf life of plant-based food depends on the species and plant involved. Pulpy fruit portions tend to have a short life span, while seed parts, which in nature have to survive at least separated from the living plant are usually short-lived.In addition to having a limited natural shelf life, most food is geographically and season-ally specific. Thus, potatoes and apples are grown in a few North American geographical regions and harvest during a short maturation period. In a world without packaging,we would need to live at the point of harvest to enjoy these products, and our enjoyment of them would be restricted to the natural biological life span of each. It is by proper storage, packaging and transport techniques that we are able to deliver fresh potatoes and apples, or the products derived from them, throughout the year and throughout the country. Potato-whole,canned, powdered, flaked, chipped, frozen, and instant is available, anytime, anywhere. This ability gives a society great freedom and mobility. Unlike less-developed societies, we are no longer restricted in our choice of where to live, since we are no longer tied to the food-producing ability of an area. Food production becomes more specialized and efficient with the growth of packaging. Crops and animal husbandry are moved to where their production is most economical, without regard to the proximity of a market. Most important, we are free of the natural cycles of feast and famine that are typical of societies dependent on natural regional food-producing cycles.Central processing allows value recovery from what would normally be waste by products of the processed food industry from the basis of other sub-industries. Chicken feathers are high in protein and, properly mill and treated, can be fed back to the next generation of chickens. Vegetable waste is fed to cattle or pigs. Bagasse, the waste cane from sugar pressing, is a source of fiber for papermaking. Fish scales are refined to make additives for paints and nail polish.The economical manufacture of durable goods also depends on good packaging.A product's cost is directly related to production volume. The business drive to reduce costs in the supply chain must be carefully balanced against the fundamental technical requirements for food safety and product integrity, as well as the need to ensure an. efficient logistics service. In addition, there is a requirement to meet the aims of marketing to protect and project brand image through value-added pack design. The latter may involve design inputs that communicate distinctive, aesthetically pleasing, ergonomic, functional and/or environmentally aware attributes. But for a national or international bicycle producer to succeed, it must be a way of getting the product to a market, which may be half a world away. Again, sound packaging, in this case distributionpackaging, is a key part of the system.Some industries could not exist without an international market. For example, Canada is a manufacturer of irradiation equipment, but the Canadian market (which would account for perhaps one unit every several years) could not possibly support such a manufacturing capability. However, by selling to the world, a manufacturing facility becomes viable. In addition to needing packaging for the irradiation machinery and instrumentation, the sale of irradiation equipment requires the sale packaging and transport of radioactive isotopes, a separate challenge in itself. In response to changing consumer lifestyles, the large retail groups and the food service industry development. Their success has been involved in a competition fierce hybrid logistics, trade, marketing and customer service expertise, all of which is dependent on the quality of packaging. They have in part led to the expansion of the dramatic range of products offered, technology innovation, including those in the packaging. Supply retail, food processing and packaging industry will continue to expand its international operations. Sourcing products around the world more and more to assist in reducing trade barriers. The impact of the decline has been increased competition and price pressure. Increased competition led to the rationalization of industrial structure, often in the form of mergers and acquisitions. Packaging, it means that new materials and shapes, increased automation, packaging, size range extension of lower unit cost. Another manufacturer and mergers and acquisitions, the Group's brand of retail packaging and packaging design re-evaluation of the growing development of market segmentation and global food supply chain to promote the use of advanced logistics and packaging systems packaging logistics system is an integral part of, and played an important role in prevention in the food supply or reduce waste generation.3. World Packaging.This discussion has referred to primitive packaging and the evolution of packaging functions. However, humankind's global progress is such that virtually every stage in the development of society and packaging is present somewhere in the world today. Thus, a packager in a highly developed country will agonize over choice of package type, hire expensive marketing groups to develop images to entice the targeted buyer and spend lavishly on graphics. In less-developed countries, consumers are happy to have food, regardless of the package. At the extreme, consumers will bring their own packages or will consume food on the spot, just as they did 2000 years ago.Packagers from the more developed countries sometimes have difficulty working with less-developed nations, for the simple reason that they fail to understand that their respective packaging priorities are completely different. Similarly, developing nations trying to sell goods to North American markets cannot understand our preoccupation with package and graphics.The significant difference is that packaging plays a different role in a market where rice will sell solely because it is available. In the North American market, the consumer may be confronted by five different companies offering rice in 30 or so variations. If all the rice is good and none is inferior, how does a seller create a preference for his particular rice? How does he differentiate? The package plays a large role in this process.The package-intensive developed countries are sometimes criticized for over packaging, and certainly over-packaging does exist. However, North Americans also enjoy the world's cheapest food, requiring only about 11 to 14% of our disposable income. European food costs are about 20% of disposable income, and in the less-developed countries food can take 95%of family income.4. The status and development trend of domestic and international packaging machineryWorldwide, the history of the development of the packaging machinery industry is relatively short, science and technology developed in Europe and America in general started in the 20th century until the 1950s the pace greatly accelerated.From the early 20th century, before the end of World War II World War II,medicine,food, cigarettes,matches,household chemicals and other industrial sectors, the mechanization of the packaging operations; the 1950s, the packaging machine widely used common electric switches and tube for the main components of the control system to achieve the primary automation; 1960s, Electrical and optical liquid-gas technology is significantly increased in the packaging machine, machines to further expand on this basis a dedicated automated packaging line; the 1970s, the micro- electronic technology into the automation of packaging machines and packaging lines, computer control packing production process; from the 1980s to the early 1990s, in some field of packaging, computer, robot application for service, testing and management, in preparation for the over-flexible automatic packaging lines and "no" automatic packaging workshop.Actively promoted and strong co-ordination of all aspects of society, and gradually establish a packaging material, packaging, printing, packaging machinery and other production sectors, and corresponding to the research, design, education, academic, management and organization, and thus the formation of independent and complete. The packaging of light industrial system, and occupies an important place in the national economy as a whole.Based on recent years data that members of the World Packaging Alliance output value of the packaging industry accounts for about 2% of the total output value of the national economy; in which the proportion of packaging machinery, though not large, but the rapid development of an annual average of almost growing at a rate of about 10%. Put into use at the packaging machine is now more than thousand species of packaging joint machines and automated equipment has been stand-alone equate. According to the new technological revolution in the world development trend is expected to packaging materials and packaging process and packaging machinery will be closely related to obtain the breakthrough of a new step, and bring more sectors into the packaging industry.China Packaging Technology Association was established in 1980. Soon, the China National Packaging Corporation have been born. Since then, one after another in the country organized a national and international packaging machinery exhibition, seminars, also published I had the first ever "China Packaging Yearbook and other packaging technology books. All this indicates that China is creating a new packaging historical perio d.1.2中文翻译现代包装1、不断变化的需求和新的角色,回顾以往,包装所带来明显的历史性变化是可以理解的, 一个产品包装方式的给他们的销量带来的影响也是显而易见的。
机械专业毕业设计外文翻译1

本科毕业设计(本科毕业论文)外文文献及译文文献、资料题目:High-rise Tower Crane designed文献、资料来源:期刊(著作、网络等)文献、资料发表(出版)日期:2000.3.25院(部):机电工程学院专业:机电工程及自动化High-rise Tower Crane designed under Turbulent Winds At present, construction of tower cranes is an important transport operations lifting equipment, tower crane accident the people's livelihood, major hazards, and is currently a large number of tower crane drivers although there are job permits, due to the lack of means to monitor and review the actual work of a serious violation . Strengthen the inspection and assessment is very important. Tower crane tipping the cause of the accident can be divided into two aspects: on the one hand, as a result of the management of tower cranes in place, illegal operation, illegal overloading inclined cable-stayed suspended widespread phenomenon; Second, because of the tower crane safety can not be found in time For example,Took place in the tower crane foundation tilt, micro-cracks appear critical weld, bolts loosening the case of failure to make timely inspection, maintenance, resulting in the continued use of tower cranes in the process of further deterioration of the potential defect, eventually leading to the tower crane tipping. The current limit of tower crane and the black box and can not be found to connect slewing tower and high-strength bolts loosening tightened after the phenomenon is not timely, not tower verticality of the axis line of the lateral-line real-time measurement, do not have to fight the anti-rotation vehicles, lifting bodies plummeted Meng Fang, hook hoists inclined cable is a timely reminder and record of the function, the wind can not be contained in the state of suspended operation to prevent tipping on the necessary tips on site there is a general phenomenon of the overloaded overturning of the whole security risks can not be accurately given a reminder and so on, all of which the lease on the tower crane, use, management problems,Through the use of tower crane anti-tipping monitor to be resolved. Tower crane anti-tipping Monitor is a new high-tech security monitoring equipment, and its principle for the use of machine vision technology and image processing technology to achieve the measurement of the tilt tower, tower crane on the work of state or non-working state of a variety of reasons angle of the tower caused by the critical state to achieve the alarm, prompt drivers to stop illegal operation, a computer chip at the same time on the work of the state of tower crane be recorded. Tower crane at least 1 day overload condition occurs, a maximum number of days to reach 23 overloading, the driver to operate the process of playing the anti-car, stop hanging urgency, such as cable-stayed suspended oblique phenomenon often, after verification and education, to avoid the possible occurrence of fatal accidents. Wind conditions in the anti-tipping is particularly important, tower cranes sometimes connected with the pin hole and pin do not meet design requirements, to connect high-strength bolts are not loose in time after the tightening of the phenomenon, through timely maintenance in time after the tightening of the phenomenon, through timely maintenance and remedial measures to ensure that the safe and reliable construction progress. Reduced lateral line tower vertical axis measuring the number of degrees,Observation tower angle driver to go to work and organize the data once a month to ensure that the lateral body axis vertical line to meet the requirements, do not have to every time and professionals must be completed by Theodolite tower vertical axismeasuring the lateral line, simplified the management link. Data logging function to ensure that responsibility for the accident that the scientific nature to improve the management of data records for the tower crane tower crane life prediction and diagnosis of steel structures intact state data provides a basis for scientific management and proactive prevention of possible accidents, the most important thing is, if the joint use of the black box can be easily and realistically meet the current provisions of the country's related industries. Tower crane safety management at the scene of great importance occurred in the construction process should be to repair damaged steel, usually have to do a good job in the steel tower crane maintenance work and found that damage to steel structures, we must rule out potential causes of accidents, to ensure safety in production carried out smoothly. Tower crane in the building construction has become essential to the construction of mechanical equipment, tower crane at the construction site in the management of safety in production is extremely important. A long time, people in the maintenance of tower crane, only to drive attention to the conservation and electrical equipment at the expense of inspection and repair of steel structures, to bring all kinds of construction accidents.Conclusion: The tower crane anti-tipping trial monitor to eliminate potential causes of accidents to provide accurate and timely information, the tower crane to ensure the smooth development of the leasing business, the decision is correct, and should further strengthen and standardize the use of the environment (including new staff training and development of data processing system, etc.).The first construction cranes were probably invented by the Ancient Greeks and were powered by men or beasts of burden, such as donkeys. These cranes were used for the construction of tall buildings. Larger cranes were later developed, employing the use of human treadwheels, permitting the lifting of heavier weights. In the High Middle Ages, harbour cranes were introduced to load and unload ships and assist with their construction – some were built into stone towers for extra strength and stability. The earliest cranes were constructed from wood, but cast iron and steel took over with the coming of the Industrial Revolution.For many centuries, power was supplied by the physical exertion of men or animals, although hoists in watermills and windmills could be driven by the harnessed natural power. The first 'mechanical' power was provided by steam engines, the earliest steam crane being introduced in the 18th or 19th century, with many remaining in use well into the late 20th century. Modern cranes usually use internal combustion engines or electric motors and hydraulic systems to provide a much greater lifting capability than was previously possible, although manual cranes are still utilised where the provision of power would be uneconomic.Cranes exist in an enormous variety of forms – each tailored to a specific use. Sizes range from the smallest jib cranes, used inside workshops, to the tallest tower cranes,used for constructing high buildings, and the largest floating cranes, used to build oil rigs and salvage sunken ships.This article also covers lifting machines that do not strictly fit the above definition of a crane, but are generally known as cranes, such as stacker cranes and loader cranes.The crane for lifting heavy loads was invented by the Ancient Greeks in the late 6th century BC. The archaeological record shows that no later than c.515 BC distinctive cuttings for both lifting tongs and lewis irons begin to appear on stone blocks of Greek temples. Since these holes point at the use of a lifting device, and since they are to be found either above the center of gravity of the block, or in pairs equidistant from a point over the center of gravity, they are regarded by archaeologists as the positive evidence required for the existence of the crane.The introduction of the winch and pulley hoist soon lead to a widespread replacement of ramps as the main means of vertical motion. For the next two hundred years, Greek building sites witnessed a sharp drop in the weights handled, as the new lifting technique made the use of several smaller stones more practical than of fewer larger ones. In contrast to the archaic period with its tendency to ever-increasing block sizes, Greek temples of the classical age like the Parthenon invariably featured stone blocks weighing less than 15-20 tons. Also, the practice of erecting large monolithic columns was practically abandoned in favour of using several column drums.Although the exact circumstances of the shift from the ramp to the crane technology remain unclear, it has been argued that the volatile social and political conditions of Greece were more suitable to the employment of small, professional construction teams than of large bodies of unskilled labour, making the crane more preferable to the Greek polis than the more labour-intensive ramp which had been the norm in the autocratic societies of Egypt or Assyria.The first unequivocal literary evidence for the existence of the compound pulley system appears in the Mechanical Problems (Mech. 18, 853a32-853b13) attributed to Aristotle (384-322 BC), but perhaps composed at a slightly later date. Around the same time, block sizes at Greek temples began to match their archaic predecessors again, indicating that the more sophisticated compound pulley must have found its way to Greek construction sites by then.During the High Middle Ages, the treadwheel crane was reintroduced on a large scale after the technology had fallen into disuse in western Europe with the demise of the Western Roman Empire. The earliest reference to a treadwheel (magna rota) reappears in archival literature in France about 1225, followed by an illuminated depiction in a manuscript of probably also French origin dating to 1240. In navigation, the earliest uses of harbor cranes are documented for Utrecht in 1244, Antwerp in 1263, Brugge in 1288 and Hamburg in 1291, while in England the treadwheel is not recorded before 1331.Generally, vertical transport could be done more safely and inexpensively by cranes than by customary methods. Typical areas of application were harbors, mines, and, in particular, building sites where the treadwheel crane played a pivotal role in the construction of the lofty Gothic cathedrals. Nevertheless, both archival and pictorial sources of the time suggest that newly introduced machines like treadwheels or wheelbarrows did not completely replace more labor-intensive methods like ladders, hods and handbarrows. Rather, old and new machinery continued to coexist on medieval construction sites and harbors.Apart from treadwheels, medieval depictions also show cranes to be powered manually by windlasses with radiating spokes, cranks and by the 15th century also by windlasses shaped like a ship's wheel. To smooth out irregularities of impulse and get over 'dead-spots' in the lifting process flywheels are known to be in use as early as 1123.The exact process by which the treadwheel crane was reintroduced is not recorded, although its return to construction sites has undoubtedly to be viewed in close connection with the simultaneous rise of Gothic architecture. The reappearance of the treadwheel crane may have resulted from a technological development of the windlass from which the treadwheel structurally and mechanically evolved. Alternatively, the medieval treadwheel may represent a deliberate reinvention of its Roman counterpart drawn from Vitruvius' De architectura which was available in many monastic libraries. Its reintroduction may have been inspired, as well, by the observation of the labor-saving qualities of the waterwheel with which early treadwheels shared many structural similarities.In contrast to modern cranes, medieval cranes and hoists - much like their counterparts in Greece and Rome - were primarily capable of a vertical lift, and not used to move loads for a considerable distance horizontally as well. Accordingly, lifting work was organized at the workplace in a different way than today. In building construction, for example, it is assumed that the crane lifted the stone blocks either from the bottom directly into place, or from a place opposite the centre of the wall from where it could deliver the blocks for two teams working at each end of the wall. Additionally, the crane master who usually gave orders at the treadwheel workers from outside the crane was able to manipulate the movement laterally by a small rope attached to the load. Slewing cranes which allowed a rotation of the load and were thus particularly suited for dockside work appeared as early as 1340. While ashlar blocks were directly lifted by sling, lewis or devil's clamp (German Teufelskralle), other objects were placed before in containers like pallets, baskets, wooden boxes or barrels.It is noteworthy that medieval cranes rarely featured ratchets or brakes to forestall the load from running backward.[25] This curious absence is explained by the high friction force exercised by medieval treadwheels which normally prevented the wheel from accelerating beyond control.目前,塔式起重机是建筑工程进行起重运输作业的重要设备,塔机事故关系国计民生、危害重大,而目前众多的塔机司机虽然有上岗证,由于缺少监督和复核手段,实际工作中违规严重。
毕业设计(论文)外文资料翻译【范本模板】

南京理工大学紫金学院毕业设计(论文)外文资料翻译系:机械系专业:车辆工程专业姓名:宋磊春学号:070102234外文出处:EDU_E_CAT_VBA_FF_V5R9(用外文写)附件:1。
外文资料翻译译文;2.外文原文.附件1:外文资料翻译译文CATIA V5 的自动化CATIA V5的自动化和脚本:在NT 和Unix上:脚本允许你用宏指令以非常简单的方式计划CATIA。
CATIA 使用在MS –VBScript中(V5.x中在NT和UNIX3。
0 )的共用部分来使得在两个平台上运行相同的宏。
在NT 平台上:自动化允许CATIA像Word/Excel或者Visual Basic程序那样与其他外用分享目标。
ATIA 能使用Word/Excel对象就像Word/Excel能使用CATIA 对象。
在Unix 平台上:CATIA将来的版本将允许从Java分享它的对象。
这将提供在Unix 和NT 之间的一个完美兼容。
CATIA V5 自动化:介绍(仅限NT)自动化允许在几个进程之间的联系:CATIA V5 在NT 上:接口COM:Visual Basic 脚本(对宏来说),Visual Basic 为应用(适合前:Word/Excel ),Visual Basic。
COM(零部件目标模型)是“微软“标准于几个应用程序之间的共享对象。
Automation 是一种“微软“技术,它使用一种解释环境中的COM对象。
ActiveX 组成部分是“微软“标准于几个应用程序之间的共享对象,即使在解释环境里。
OLE(对象的链接与嵌入)意思是资料可以在一个其他应用OLE的资料里连结并且可以被编辑的方法(在适当的位置编辑).在VBScript,VBA和Visual Basic之间的差别:Visual Basic(VB)是全部的版本。
它能产生独立的计划,它也能建立ActiveX 和服务器。
它可以被编辑。
VB中提供了一个补充文件名为“在线丛书“(VB的5。
机械毕业设计英文外文翻译97带式运输机

附录二:外文技术资料及中文翻译1、英文技术资料Belt ConveyorFIELD OF THE INVENTIONThe present invention relates to a belt conveyor having a circulating conveying belt, having carrying rollers, which are arranged between the top strand and the bottom strand of the conveying belt, and having a drive device and a force-transmission device for moving the conveying belt.BACKGROUND OF THE INVENTIONIt is known from practice for force to be transmitted from the drive device to the conveying belt of a belt conveyor via friction fitting. The friction between a driven carrying roller and the conveying belt, for example, may even be sufficient for this purpose. The rest of the carrying rollers are mounted in a movable manner and rotate along.DE 42 44 170 C2 discloses a belt conveyor having an endless conveying belt, the latter being driven by means of a force-transmission device which is present in the form of a friction wheel. A drive shaft extends beneath the bottom strand of the conveying belt. On the inner radius of the belt curve, a motor is connected as a drive device to the drive shaft and, in the region of the outer radius, a friction wheel is seated on the drive shaft and is in contact with the outer surface of the conveying belt. In this case, the friction wheel interacts with a carrying roller functioning as counterpressure roller. The drive shaft is mounted such that it can be moved at an angle both in the region of the outer radius and in the region of the inner radius of the belt curve. The movable-angle mounting of the drive shaft allows adaptation of the extent to which the friction wheel is pressed against the conveying belt in proportion to the actual load. In this way, the wear is reduced if, in part-load operation, the conveying belt is only subjected to the contact-pressure force which is necessary for this purpose.Although the belt conveyor known from DE 42 44 170 C2 reduces the wear of the conveying belt, it cannot rule it out altogether. The task of conveying foodstuffs or other goods which are to be kept clean involves, in addition to the mechanical damage to the conveying belt, the aspect of hygiene and of keeping goods clean. The abraded surface particles of the conveying belt could have a considerable adverse effect on the quality of the goods which are to be conveyed. Moreover, the known belt conveyor requires an extremely high level of structural outlay as far as the movable mounting of the separate drive shaft is concerned. SUMMARY OF THE INVENTIONTaking as departure point the belt conveyor known from DE 42 44 170 C2, the object of the invention is to specify a belt conveyor of the type in question which largely rules out any adverse effect to the surface of the conveying belt of the belt conveyor by the force-transmission device. According to a particularly preferred configuration, the belt conveyor is intended to require just a low level of structural outlay.The above object is achieved by the features of Patent claim 1. According to the latter, a belt conveyor of the type in question is configured such that a pair of elements which interact with one another with a form fit is provided for force-transmission purposes, and that one element is assigned to the force-transmission device and the other element is assigned to the conveying belt.According to the invention, it has been found that the surface of the conveying belt is not adversely affected as a result of the action of the force-transmission device if a separate pair of elements is providedin order to realize force transmission. It has also been found that the use of a pair of movement-converting elements which are known per se and interact with one another with a form fit largely eliminates the disadvantages which are known in the case of friction-fitting movement conversion, in particular wear and abrasion.According to a preferred exemplary embodiment of the belt conveyor according to the invention, the pair of elements could be present as toothed ring and toothed belt, the tooth flanks of the toothed ring and of the toothed belt interacting with one another. It would be possible for the toothed ring to be assigned to the force-transmission device and for the toothed belt to be assigned to the conveying belt.As far as a particularly low level of structural outlay is concerned, a preferred configuration of the abovementioned exemplary embodiment provides that the toothed ring is assigned to a carrying roller, and the latter thus simultaneously assumes the role of the force-transmission device. Via a journal projecting from the carrying roller, the drive takes place by means of a motor. The toothed ring could be plugged onto the carrying roller and fixed releasably—for example via a shaft/hub connection or a feather key—to the same. In the case of a plugged-on toothed ring, it is advantageous that it is possible to use carrying rollers which are already present. It is particularly advantageous for each carrying roller to be assigned at least one toothed ring. Over the entire running path of the conveying belt, it would then be the case that the toothed belt and the toothed rings interengage and move the conveying belt in a dimensionally stable manner. Corresponding to the toothed ring or rings which is/are arranged between the top and bottom strands and belongs/belong to the preferred configuration mentioned above, the toothed belt is arranged on the underside of the conveying belt, and extends in the running direction of the same. Arranging the toothed belt on the underside of the conveying belt once again ensures that the top side of the conveying belt, which is charged if appropriate with goods which are to be kept clean, is not subject to any force transmission, mechanical damage or production of abrasion particles or other contaminants.An expedient development of the preferred configuration of the belt conveyor according to the invention makes provision for the toothed ring to be arranged at the end of the carrying roller. As a result, on the one hand, straightforward maintenance of the force-transmission device is made possible and, on the other hand, this arrangement is also more cost-effective than a, for example, central arrangement. Direct force transmission over a short distance is achieved by a journal for the connection of the drive device projecting from that end of the carrying roller which is provided with the toothed ring.It is particularly advantageous if the toothed belt extends in the region of the side border of the conveying belt. As a result, on the one hand, straightforward production of the conveying belt with the toothed belt is made possible by the direct relationship to the border region and, on the other hand, a role is also played here by the accessibility to the pair of elements for maintenance purposes and, of course, by the coordination between the toothed belt and the arrangement of the toothed ring.In addition to toothed belts and toothed rings with normal toothing, it would also be possible to realize multisplining. This further reduces undesired sliding and thus wear, heating and noise development. In order to absorb high tensile forces, it would be possible for Kevlar filaments to be incorporated in the toothed belt, which usually consists of plastic. It would be possible for the conveying belt to be produced with the toothed belt by welding, vulcanizing or adhesive bonding.According to a particularly preferred configuration, it would be possible for the toothed belt to be a constituent part of a toothed- belt component which is of essentially U-shaped design in the transverse direction of the toothed belt. The U-shape makes it possible for the toothed- belt component simply to be plugged onto the border of the conveying belt until the border region has come into contact with the base part between the U-legs. The inner surface of the toothed- belt component may have been provided with adhesive beforehand. As a result of its shaping and of being produced in this way, the toothed- beltcomponent engages around the side-border region of the conveying belt.While the toothed belt of the conveying belt is subjected to compressive force by the toothed ring, and this largely rules out detachment of the toothed- belt component on the underside of the conveying belt, a counterpressure device could be provided in order to secure that region of the toothed- belt component which extends on the top side of the conveying belt. In design terms, the counterpressure device could be present in the form of an arm which acts on the U-leg of the toothed- belt component on the top side and thus constantly presses the same onto the top side of the conveying belt.As far as reliable guidance is concerned, it would be possible for the toothed belt or the toothed- belt component containing the toothed belt to form a bead. A bead ridge is thus produced over the length of the conveying belt. In the case of a U-shaped toothed- belt component, the bead ridge extends in each case at the free ends of the U-legs, at a distance from the border of the conveying belt, the distance depending essentially on the width of the toothed belt. As an alternative to a bead ridge, it would be possible for the toothed- belt component or for the straightforward toothed belt also to have at least one beveled free end. The guidance measure taken on the toothed belt or on the specific toothed- belt component is provided in order that a guide roller or a pair of guide rollers acts on the beveled surface or on the bead or bead ridge. The guidance measure explained above could be taken equally well in the case of belt curves and straight belt lines and of belt S-shapes bridging different heights.In the case of belt curves, the force acting on the conveying belt is directed toward the inner radius of the belt curve, with the result that the guide rollers, in an advantageous manner which is known per se, could have inclined running surfaces. Correspondingly angled retaining arms as a constituent part of retaining structures for the guide rollers could be arranged in each case in the region of a carrying roller. The guide rollers could be arranged in pairs on the top strand and on the bottom strand of the conveying belt.It should be emphasized at this point that, with the abovementioned configuration of the belt conveyor according to the invention having the bead or beveled free ends, two functions are combined in the pair of form-fitting elements. Not only the force transmission, but also the guidance of the conveying belt, takes place. The dimensional stability of the conveying belt is advantageously increased by the pair of form-fitting elements with the specific configuration of the toothed belt or of the toothed- belt component for action of the guide rollers thereon.In the case of the already cited design of the belt conveyor in the form of a belt curve, the carrying rollers are of conical design and the toothed ring is arranged at the larger-diameter end of the respective carrying roller, that is to say on the outer radius of the belt curve. The drive device is present as a motor and is assigned to the first carrying roller of the belt curve. The form-fitting interengagement of the toothed wheel and toothed belt takes place in the region of each carrying roller, the form fit, in relation to the first, motor-driven carrying roller, serving for force-transmission purposes and, in relation to the rest of the rollers, serving for guiding the conveying belt.The previously explained principle of force transmission via a pair of elements which interact with one another with a form fit could also be used in the case of a straight belt line or in the case of a height-changing belt S-shape. Here, the carrying rollers are of a cylindrical design and the force transmission takes place—as with the belt curve—at a first carrying roller, while the following carrying rollers, likewise equipped with the pair of form-fitting elements, serve for guiding the conveying belt. In contrast to the belt curve, however, it would be possible, in the case of the straight belt line or in the case of the belt S-shape, for the pair of elements to be arranged at the two free ends of the respective carrying roller and on the two border regions of the conveying belt. It would thus be possible specifically for the two border regions of the conveying belt to have a toothed belt or a toothed- belt component which interacts with the toothed rings at the two free ends of each carrying roller. Furthermore, it would also be possible, with these types of construction of the belt conveyor according to the invention, to provideguide rollers.A further advantage of the preferred embodiment of the belt conveyor according to the invention, the toothed ring and toothed belt interacting, consists in the improved capacity for controlling the belt speed in accordance with the current loading. It would be possible to provide a control device which senses a change in the speed by corresponding measuring sensors and adjusts the power of the drive device in line with the safety regulations.In comparison with the force transmission realized by friction fitting, the belt conveyor according to the invention not only has the advantage of better capacity for control, but also has the advantage that the conveying belt has a high level of dimensional stability as a result of the guidance by means of the pair of form-fitting elements and by means of the pairs of guide rollers and can be subjected to higher torques. Overall, it is possible to achieve an increased level of drive power during start-up. In the case of the belt conveyor according to the invention being designed in the form of a belt curve with an inner radius of 400 mm, the carrying rollers rotate at 230 rpm at a maximum speed of 1.5 m/sec.2、中文翻译带式运输机一、领域的发明本发明涉及一种具有循环带式输送机输送带,有托辊,这是链之间的顶部和底部的传送带链排列,有一个传动装置和一个移动传送带力传动装置。