Control and Prevention of Casting Defects - part 2
钟南山英语作文模板大全

关于钟南山的英语作文模板1Zhong Nanshan is a remarkable figure who has made extraordinary contributions to the field of medicine and public health. During the challenging period of the COVID-19 pandemic, he fearlessly ventured to the frontline, disregarding his personal safety. His presence was like a guiding star in the darkness, giving people hope and courage.He didn't hesitate for a moment. Instead, he plunged into the heart of the battle, offering professional guidance and strategic advice. His wisdom and experience were like a powerful shield, protecting countless lives.For many years before the pandemic, he had been committed to medical research, devoting himself tirelessly to the cause of public health. His efforts were like a steady stream of water, nurturing the growth of medical science.His spirit of dedication and responsibility is an inspiration to us all. He shows us that with determination and a sense of mission, one can overcome any difficulties and make significant contributions to society.We hold deep respect and admiration for Zhong Nanshan. His story is a shining example that will continue to inspire generations to come, encouraging us to strive for the betterment of the world with unwavering courage and selfless dedication.Zhong Nanshan is a remarkable figure who has left an indelible mark on the field of medicine. When an unknown virus emerged, casting a shadow of fear and uncertainty over the world, Zhong Nanshan fearlessly stepped forward. His determination and courage were like a bright beacon in the darkness, instilling hope and confidence in the hearts of the people.He devoted himself tirelessly to the battle against the virus, conducting in-depth research and formulating effective strategies. His expertise and wisdom guided us through the most challenging times. His words were not just words but a source of strength and reassurance.In the realm of medical science, Zhong Nanshan has continuously made groundbreaking innovations. He has spent years conducting rigorous studies and experiments, always striving for advancements that would benefit humanity's health. His achievements are not just individual triumphs but milestones in the progress of medical science worldwide.His dedication and sense of responsibility are truly exemplary. He has sacrificed personal comforts and faced countless difficulties with unwavering resolve. His story is one of bravery, perseverance, and selflessness. We are indebted to his contributions and should draw inspiration from his spirit to strive for the betterment of society and the well-being of humanity.Zhong Nanshan is a remarkable figure who has touched the hearts of countless people. His dedication and commitment to the medical field are truly inspiring.I was deeply moved by the scene where he patiently guided young doctors, passing on the medical spirit with kindness and wisdom. He would spend hours explaining complex medical theories and sharing his rich clinical experience, encouraging them to strive for excellence and never give up. His eyes sparkled with enthusiasm and care, making every young doctor feel supported and motivated.Moreover, Zhong Nanshan has always remained steadfast at his post, selflessly devoting himself to the well-being of the public. Even in the most challenging times, such as the epidemic, he never stepped back. He worked tirelessly, day and night, conducting research, formulating strategies, and providing valuable advice. His silent dedication is like a bright light guiding us through the darkness.The story of Zhong Nanshan has filled my heart with admiration. His unwavering spirit and sense of responsibility have set a remarkable example for all of us. I believe that his influence will continue to inspire generations of medical workers to pursue their dreams and contribute to the betterment of society.Zhong Nanshan is a remarkable figure who has played a crucial role in major public health events. During the SARS outbreak, the situation was extremely critical. However, Zhong Nanshan stepped forward bravely and took on the heavy responsibility. He conducted in-depth research and analysis, formulating effective prevention and control strategies. His decisions and actions were based on scientific knowledge and rich experience, which helped to control the spread of the disease and saved countless lives.In the face of the novel coronavirus epidemic, Zhong Nanshan once again emerged as a pillar of strength. Despite his advanced age, he did not hesitate to rush to the frontline. With his professional judgment and decisive decisions, he provided valuable guidance for the prevention and control of the epidemic. His words and actions gave people confidence and hope in the most difficult times.Zhong Nanshan's sense of social responsibility is truly commendable. He has always put the interests of the people and the public health first, disregarding personal gains and losses. His dedication and perseverance have set a shining example for us all. We should learn from him, strive to contribute to society, and take on our own responsibilities in times of difficulty and challenge.Zhong Nanshan is a remarkable figure whose name resonates throughout China and beyond. His contributions to the field of medicine and his unwavering dedication have had a profound and far-reaching impact on society and the medical profession.Zhong Nanshan's academic achievements have been nothing short of extraordinary. His in-depth research and groundbreaking discoveries have not only advanced medical knowledge but have also paved the way for new directions in medical research. His studies on respiratory diseases, for instance, have led to significant improvements in diagnosis and treatment methods, saving countless lives.His role as a role model is equally inspiring. For the younger generation of medical practitioners, he is a beacon of hope and determination. His perseverance and commitment in the face of difficult medical challenges have encouraged many young doctors to pursue excellence and to remain dedicated to the well-being of patients.During times of public health crises, Zhong Nanshan has always been at the forefront. His calm and authoritative presence has instilled confidence in the public, and his expert advice has guided the nation through difficult times.In conclusion, Zhong Nanshan's influence is multi-faceted and profound. His achievements in medicine and his exemplary conductcontinue to shape the medical field and inspire future generations to strive for the betterment of humanity's health.。
食品中铁、锰元素检测方法探讨

食品科技食品中铁、锰元素检测方法探讨史秋梅(临沂市河东区疾病预防控制中心,山东临沂 276034)摘 要:铁元素和锰元素是人体必需的微量元素,在多种生理机能中发挥着关键作用。
然而,过度摄入可能会对人体产生不利的影响,因此食品中铁元素和锰元素的分析检测显得尤为重要。
本文介绍了食品中铁元素和锰元素分析的必要性,并针对食品中铁、锰元素的检测分析方法,如原子吸收光谱法、高效液相色谱法、电感耦合等离子体原子发射光谱法、电感耦合等离子体质谱法以及X射线荧光光谱法等进行了概述,以期保障食品中铁、锰元素含量的安全性和合规性,从而更好地服务于食品分析领域。
关键词:铁元素;锰元素;分析方法;应用;食品安全Exploration of Detection Methods for Iron and ManganeseElements in FoodSHI Qiumei(Hedong District Center for Disease Control and Prevention, Linyi 276034, China) Abstract: Iron and manganese are essential trace elements for the human body and play crucial roles in various physiological functions. However, excessive intake may have adverse effects on the human body, so the analysis and detection of iron and manganese elements in food is particularly important. This article introduces the necessity of analyzing iron and manganese elements in food, and provides an overview of detection and analysis methods for iron and manganese elements in food, such as atomic absorption spectroscopy, high-performance liquid chromatography, ionization coupled plasma atomic emission spectroscopy, ionization coupled plasma mass spectrometry, and X-ray fluorescence spectroscopy, in order to ensure the safety and compliance of iron and manganese content in food, so as to better serve the field of food analysis.Keywords: iron; manganese; analytical methods; applications; food safety铁和锰是食品中的两种微量元素,对维持身体健康具有重要意义[1]。
ASTM B108108M-2015 铝和铝合金永久型模铸件的化学成分和力学性能
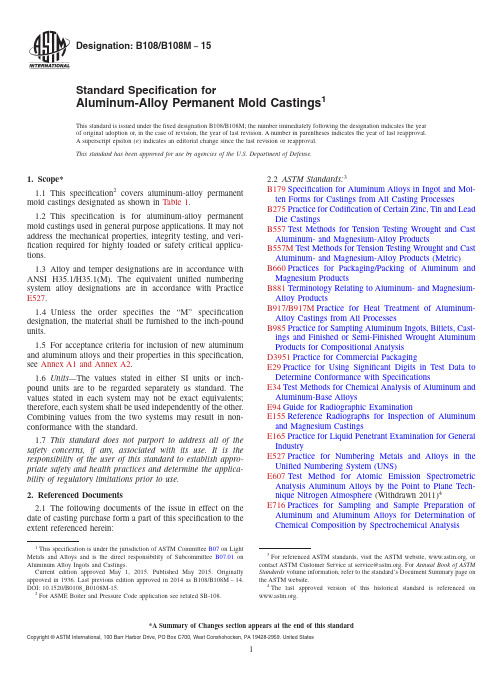
Designation:B108/B108M−15Standard Specification forAluminum-Alloy Permanent Mold Castings1This standard is issued under thefixed designation B108/B108M;the number immediately following the designation indicates the year of original adoption or,in the case of revision,the year of last revision.A number in parentheses indicates the year of last reapproval.A superscript epsilon(´)indicates an editorial change since the last revision or reapproval.This standard has been approved for use by agencies of the U.S.Department of Defense.1.Scope*1.1This specification2covers aluminum-alloy permanent mold castings designated as shown in Table1.1.2This specification is for aluminum-alloy permanent mold castings used in general purpose applications.It may not address the mechanical properties,integrity testing,and veri-fication required for highly loaded or safety critical applica-tions.1.3Alloy and temper designations are in accordance with ANSI H35.1/H35.1(M).The equivalent unified numbering system alloy designations are in accordance with Practice E527.1.4Unless the order specifies the“M”specification designation,the material shall be furnished to the inch-pound units.1.5For acceptance criteria for inclusion of new aluminum and aluminum alloys and their properties in this specification, see Annex A1and Annex A2.1.6Units—The values stated in either SI units or inch-pound units are to be regarded separately as standard.The values stated in each system may not be exact equivalents; therefore,each system shall be used independently of the other. Combining values from the two systems may result in non-conformance with the standard.1.7This standard does not purport to address all of the safety concerns,if any,associated with its use.It is the responsibility of the user of this standard to establish appro-priate safety and health practices and determine the applica-bility of regulatory limitations prior to use.2.Referenced Documents2.1The following documents of the issue in effect on the date of casting purchase form a part of this specification to the extent referenced herein:2.2ASTM Standards:3B179Specification for Aluminum Alloys in Ingot and Mol-ten Forms for Castings from All Casting ProcessesB275Practice for Codification of Certain Zinc,Tin and Lead Die CastingsB557Test Methods for Tension Testing Wrought and Cast Aluminum-and Magnesium-Alloy ProductsB557M Test Methods for Tension Testing Wrought and Cast Aluminum-and Magnesium-Alloy Products(Metric)B660Practices for Packaging/Packing of Aluminum and Magnesium ProductsB881Terminology Relating to Aluminum-and Magnesium-Alloy ProductsB917/B917M Practice for Heat Treatment of Aluminum-Alloy Castings from All ProcessesB985Practice for Sampling Aluminum Ingots,Billets,Cast-ings and Finished or Semi-Finished Wrought Aluminum Products for Compositional AnalysisD3951Practice for Commercial PackagingE29Practice for Using Significant Digits in Test Data to Determine Conformance with SpecificationsE34Test Methods for Chemical Analysis of Aluminum and Aluminum-Base AlloysE94Guide for Radiographic ExaminationE155Reference Radiographs for Inspection of Aluminum and Magnesium CastingsE165Practice for Liquid Penetrant Examination for General IndustryE527Practice for Numbering Metals and Alloys in the Unified Numbering System(UNS)E607Test Method for Atomic Emission Spectrometric Analysis Aluminum Alloys by the Point to Plane Tech-nique Nitrogen Atmosphere(Withdrawn2011)4E716Practices for Sampling and Sample Preparation of Aluminum and Aluminum Alloys for Determination of Chemical Composition by Spectrochemical Analysis1This specification is under the jurisdiction of ASTM Committee B07on LightMetals and Alloys and is the direct responsibility of Subcommittee B07.01on Aluminum Alloy Ingots and Castings.Current edition approved May1,2015.Published May2015.Originally approved st previous edition approved in2014as B108/B108M–14. DOI:10.1520/B0108_B0108M-15.2For ASME Boiler and Pressure Code application see related SB-108.3For referenced ASTM standards,visit the ASTM website,,or contact ASTM Customer Service at service@.For Annual Book of ASTM Standards volume information,refer to the standard’s Document Summary page on the ASTM website.4The last approved version of this historical standard is referenced on .*A Summary of Changes section appears at the end of this standard Copyright©ASTM International,100Barr Harbor Drive,PO Box C700,West Conshohocken,PA19428-2959.United StatesE1251Test Method for Analysis of Aluminum and Alumi-num Alloys by Spark Atomic Emission Spectrometry E2422Digital Reference Images for Inspection of Alumi-num CastingsIEEE/ASTM SI 10Standard for Use of the International System of Units (SI):The Modern Metric System 2.3ANSI Standard:5H35.1/H35.1(M)Alloy and Temper Designation Systems for Aluminum2.4Military Standards:6MIL-STD-129Marking for Shipment and StorageMIL-STD-276Impregnation of Porous Nonferrous Metal CastingsNA VSEA S9074-AR-GIB-010/278Requirements for Fabri-cation Welding and Inspection,and Casting Inspection and Repair for Machinery,Piping,and Pressure Vessels5Available from Aluminum Association,Inc.,1525Wilson Blvd.,Suite 600,Arlington,V A 22209,.6Available from Standardization Documents Order Desk,DODSSP,Bldg.4,Section D,700Robbins Ave.,Philadelphia,PA 19111-5098,.TABLE 1Chemical Composition Limits A ,B ,CAlloyComposition,%ANSI D UNS Aluminum Silicon Iron Copper Manga-neseMagne-sium Chromium Nickel Zinc Titanium Tin Other Elements E Each Total F 204.0A02040remainder 0.200.35 4.2–5.00.100.15–0.35...0.050.100.15–0.300.050.050.15242.0A02420remainder 0.7 1.0 3.5–4.50.35 1.2–1.80.25 1.7–2.30.350.25...0.050.15296.0remainder 2.0–3.0 1.2 4.0–5.00.350.05...0.350.500.25......0.35308.0remainder 5.0–6.0 1.0 4.0–5.00.500.10...... 1.00.25......0.50319.0A03190remainder 5.5–6.5 1.0 3.0–4.00.500.10...0.35 1.00.25......0.50332.0G A03320remainder 8.5–10.5 1.2 2.0–4.00.500.50–1.5...0.50 1.00.25......0.50333.0A03330remainder 8.0–10.0 1.0 3.0–4.00.500.05–0.50...0.50 1.00.25......0.50336.0G A03360remainder 11.0–13.0 1.20.50–1.50.350.7–1.3... 2.0–3.00.350.25...0.05...354.0A03540remainder 8.6–9.40.20 1.6–2.00.100.40–0.6......0.100.20...0.050.15355.0A03550remainder 4.5–5.50.6H 1.0–1.50.50H 0.40–0.60.25...0.350.25...0.050.15C355.0A33550remainder 4.5–5.50.20 1.0–1.50.100.40–0.6......0.100.20...0.050.15356.0A03560remainder 6.5–7.50.6H 0.250.35H 0.20–0.45......0.350.25...0.050.15A356.0A13560remainder 6.5–7.50.200.200.100.25–0.45......0.100.20...0.050.15357.0remainder 6.5–7.50.150.050.030.45–0.6......0.050.20...0.050.15A357.0A13570remainder 6.5–7.50.200.200.100.40–0.7......0.100.04–0.20...0.05I 0.15E357.0remainder 6.5–7.50.100.100.55–0.6.........0.10–0.20...0.05J 0.15F357.0remainder 6.5–7.50.100.200.100.40–0.7......0.100.04–0.20...0.05J 0.15359.0A03590remainder 8.5–9.50.200.200.100.50–0.7......0.100.20...0.050.15443.0A04430remainder 4.5–6.00.80.60.500.050.25...0.500.25......0.35B443.0A24430remainder 4.5–6.00.80.150.350.05......0.350.25...0.050.15A444.0A14440remainder 6.5–7.50.200.100.100.05......0.100.20...0.050.15513.0G A05130remainder 0.300.400.100.30 3.5–4.5...... 1.4–2.20.20...0.050.15535.0A05350remainder 0.150.150.050.10–0.25 6.2–7.5.........0.10–0.25...0.05K 0.15705.0A07050remainder 0.200.80.200.40–0.6 1.4–1.80.20–0.40... 2.7–3.30.25...0.050.15707.0A07070remainder 0.200.80.200.40–0.6 1.8–2.40.20–0.40... 4.0–4.50.25...0.050.15711.0G A07110remainder 0.300.7–1.40.35–0.650.050.25–0.45...... 6.0–7.00.20...0.050.15713.0A07130remainder 0.25 1.10.40–1.00.60.20–0.500.350.157.0–8.00.25...0.100.25850.0A08500remainder 0.70.70.7–1.30.100.10...0.7–1.3...0.20 5.5–7.0...0.30851.0G A08510remainder 2.0–3.00.70.7–1.30.100.10...0.3–0.7...0.20 5.5–7.0...0.30852.0GA08520remainder0.400.71.7–2.30.100.6–0.9...0.9–1.5...0.205.5–7.0...0.30A When single units are shown,these indicate the maximum amounts permitted.BAnalysis shall be made for the elements for which limits are shown in this table.CThe following applies to all specified limits in this table:For purposes of determining conformance to these limits,an observed value or a calculated value obtained from analysis shall be rounded to the nearest unit in the last right-hand place of figures used in expressing the specified limit in accordance with the rounding method of Practice E29.DASTM alloy designations are recorded in Practice B275.EOthers includes listed elements for which no specific limit is shown as well as unlisted metallic elements.The producer may analyze samples for trace elements not specified in the specification.However,such analysis is not required and may not cover all metallic Others elements.Should any analysis by the producer or the purchaser establish that an Others element exceeds the limit of Each or that the aggregate of several Others elements exceeds the limit of Total ,the material shall be considered nonconforming.FOther Elements —Total shall be the sum of unspecified metallic elements 0.010%or more,rounded to the second decimal before determining the sum.G336.0formerly A332.0,332.0formerly F332.0,513.0formerly A514.0,711.0formerly C712.0,851.0formerly A850.0,852.0formerly B850.0.HIf the iron content exceeds 0.45%,manganese content shall not be less than one half ofthe iron.IBeryllium 0.04–0.07.JBeryllium 0.002max KBeryllium 0.003–0.007,boron 0.005max.2.5AMS Specification:AMS 2771Heat Treatment of Aluminum Alloy Castings 72.6Federal Standard:6Fed Std.No.123Marking for Shipment (Civil Agencies)2.7Other Standards:8CEN EN 14242Aluminum and Aluminum Alloys,Chemical Analysis,Inductively Coupled Plasma Optical Emission Spectral Analysis3.Terminology3.1Definitions—Refer to Terminology B881for definitions of product terms used in this specification.4.Ordering Information4.1Orders for material under this specification shall include the following information (see 1.4and 1.5):4.1.1This specification designation (which includes the number,the year,and the revision letter,if applicable),N OTE 1—For inch-pound application,specify Specification B108and for metric application specify Specification B108M.Do not mix units.4.1.2Alloy (see Section 7and Table 1),4.1.3Temper (see Section 10and Table 2[Table 3]),TABLE 2Tensile Requirements A (Inch-Pound Units)N OTE 1—For purposes of determining conformance with this specification,each value for tensile strength and yield strength shall be rounded to the nearest 0.1ksi,and each value for elongation shall be rounded to the nearest 0.5%,both in accordance with the rounding method of Practice E29.AlloyTemperBTensile Strength,min,ksiYield Strength C (0.2%offset),min,ksiElongation in 2in.or 4×Diameter,min,%Typical Brinell Hardness D 500-kgf load,10-mm ballANSI E UNS 204.0A02040T4separately cast specimens 48.029.08.0...242.0A02420T57134.0...F 105T6140.0...F110296.0A02960T433.015.0 4.575T635.0... 2.090T733.016.0 3.0...308.0A03080F 24.0......70319.0A03190F 27.014.0 2.595332.0G A03320T531.0...F 105333.0A03330F 28.0...F 90T530.0...F 100T635.0...F 105T731.0...F 90336.0GA03360T55131.0...F 105T6540.0...F125354.0A03540T61separately cast specimens 48.037.0 3.0casting,designated area H47.036.0 3.0castings,no location designated H 43.033.0 2.0T62separately cast specimens 52.042.0 2.0castings,designated area H50.042.0 2.0castings,no location designated H 43.033.0 2.0355.0A03550T5127.0...F 75T6242.0...F 105T736.0...F 90T7134.027.0F80C355.0A33550T61separately cast specimens 40.030.0 3.085–90castings,designated area H40.030.0 3.0castings,no location designated H 37.030.0 1.085356.0A03560F 21.010.0 3.0T633.022.0 3.085T7125.0... 3.070A356.0A13560T61separately cast specimens 38.026.0 5.080–90castings,designated area H33.026.0 5.0castings,no location designated H 28.026.0 3.0357.0T645.0... 3.0...A357.0A13570T61separately cast specimens 45.036.0 3.0100castings,designated area H46.036.0 3.0...castings,no location designated H 41.031.0 3.0...E357.0IT61separately cast specimens 45.036.0 3.0100castings,designated area H46.036.0 3.0castings,no location designated H 41.031.03.0F357.0J T645.0 3.0359.0A03590T61separately cast specimens45.034.0 4.0907Availablefrom Society of Automotive Engineers (SAE),400Commonwealth Dr.,Warrendale,PA 15096-0001,.8Available from European Committee for Standardization (CEN),36Rue de Stassart,B-1050,Brussels,Belgium,http://www.cenorm.be.TemperBStrength,min,ksi(0.2%offset),min,ksi2in.or 4×Diameter,min,%Hardness 500-kgf load,10-mm ballANSI EUNScastings,designated area H45.034.0 4.0castings,no location designated H 40.030.0 3.0T62separately cast specimens 47.038.0 3.0100castings,designated area H47.038.0 3.0castings,no location designated H 40.030.0 3.0443.0A04430F 21.07.0 2.045B443.0A24430F 21.0 6.0 2.545A444.0A14440T4separately cast specimens 20.0...20...castings,designated area H 20.0...20...513.0G A05130F 22.012.0 2.560535.0A05350F35.018.08.0...705.0A07050T1or T537.017.010.0707.0A07070T142.025.0 4.0T745.035.0 3.0711.0G A07110T128.018.07.070713.0A07130T1or T532.022.0 4.0850.0A08500T518.0...8.0851.0G A08510T517.0... 3.0T618.0...8.0852.0GA08520T527.0...3.0A If agreed upon by manufacturer and the purchaser,other mechanical properties may be obtained by other heat treatments such as annealing,aging,or stress relieving.BRefer to ANSI H 35.1/H35.1(M)for description of tempers.CYield strength to be evaluated only when specified in contract or purchase order.DHardness values given for information only,not required for acceptance.EASTM alloy designations are recorded in Practice B275.FNot required.G332.0formerly F332.0,336.0formerly A332.0,513.0formerly A514.0,711.0formerly C712.0,851.0formerly A850.0,852.0formerly B850.0.HThese properties apply only to castings having section thicknesses not greater than 2in.except that section thicknesses of 3⁄4in.,max,shall apply to Alloy A444.0.IProperties copied from A357.0–T61.JProperties copied from 357.0–T6.TABLE 3Tensile Requirements (SI Units)–[Metric]ABN OTE 1—For purposes of determining conformance with this specification,each value for tensile strength and yield strength shall be rounded to the nearest 1MPa and each value for elongation shall be rounded to the nearest 0.5%,both in accordance with the rounding method of Practice E29.AlloyTemper CTensile Strength,min,MPa DYield Strength E (0.2%offset),min,MPa DElongationin5D,min,%Typical Brinell Hardness F 500-kgf load,10-mm ballANSIGUNS 204.0A02040T4separately cast specimens 3302007.0...242.0A02420T571235...H 105T61275...H110296.0A02960T4230105 4.575T6240... 2.090T7230110 3.0...308.0A03080F 165......70319.0A03190F 18595 2.595332.0I A03320T5215...H 105333.0A03330F 195...H 90T5205...H 100T6240...H 105T7215...H 90336.0IA03360T551215...H 105T65275...H125354.0A03540T61separately cast specimens 330255 3.0casting,designated area J325250 3.0castings,no location designated J 295230 2.0T62separately cast specimens 360290 2.0castings,designated area J345290 2.0castings,no location designated J 295230 2.0355.0A03550T51185...H 75T62290...H 105T7250...H 90T71235185H80C355.0A33550T61separately cast specimens 275205 3.085–90castings,designated area J2752053.0Temper C Strength,min,MPa D(0.2%offset),min,MPa Din5D,min,%Hardness F500-kgf load,10-mm ballANSI G UNScastings,no location designated J255205 1.085 356.0A03560F14570 3.0T6230150 3.085T71170... 3.070 A356.0A13560T61separately cast specimens260180 4.080–90castings,designated area J230180 4.0castings,no location designated J195180 3.0 357.0T6310... 3.0...A357.0A13570T61separately cast specimens310250 3.0100castings,designated area J315250 3.0...castings,no location designated J285215 3.0...E357.0K T61separately cast specimens310250 3.0100castings,designated area J315250 3.0castings,no location designated J285215 3.0 F357.0L T6310 3.0359.0A03590T61separately cast specimens310235 4.090castings,designated area J310235 4.0castings,no location designated J275205 3.0T62separately cast specimens325260 3.0100castings,designated area J325260 3.0castings,no location designated J275205 3.0 443.0A04430F14550 2.045B443.0A24430F14540 2.545A444.0A14440T4separately cast specimens140...18.0...castings,designated area J140...18.0...513.0I A05130F15080 2.560535.0A05350F2401257.0...705.0A07050T1or T52551159.0707.0A07070T1290170 4.0T7310240 3.0 711.0I A07110T1195125 6.070713.0A07130T1or T5220150 4.0850.0A08500T5125...7.0851.0I A08510T5115... 3.0T6125...7.0 852.0I A08520T5185... 3.0A If agreed upon by manufacturer and the purchaser,other mechanical properties may be obtained by other heat treatments such as annealing,aging,or stress relieving.B Guidelines for metric conversion from the“Tempers for Aluminum and Aluminum Alloys,Metric Edition”(Tan Sheets)Appendix A,were used to convert the tensile and yield values to SI units.6C Refer to ANSI H35.1/H35.1(M)for description of tempers.D For explanation of the SI Unit“MPa”see Appendix X2.E Yield strength to be evaluated only when specified in contract or purchase order.F Hardness values given for information only,not required for acceptance.G ASTM alloy designations are recorded in Practice B275.H Not required.I332.0formerly F332.0,336.0formerly A332.0,513.0formerly A514.0,711.0formerly C712.0,851.0formerly A850.0,852.0formerly B850.0.J These properties apply only to castings having section thicknesses not greater than2in.except that section thicknesses of19-mm max,shall apply to Alloy A444.0. K Properties copied from A357.0–T61.L Properties copied from357.0–T6.4.1.4Applicable drawing or part number,and4.1.5The quantity in either pieces or pounds[kilograms].4.2Additionally,orders for material to this specification shall include the following information when required by the purchaser.4.2.1Whether foundry control is required(see Section9), 4.2.2Whether yield strength tests are required(see10.1and Table2,Footnote C,[Table4,Footnote D]),4.2.3Whether castings or test bars,or both,are to be artificially aged for Alloys705.0-T5,707.0-T5,and713.0-T5 (see10.3),4.2.4Whether test specimens cut from castings are required in addition to or instead of separately cast specimens(see Sections10,12.2,13.2,and15),4.2.5Whether heat treatment is to be performed in accor-dance with AMS2771(see Section16),4.2.6Whether repairs are permissible(see Section17), 4.2.7Whether inspection is required at the producer’s works(see Section18),4.2.8Whether certification is required(see Section22), 4.2.9Whether surface requirements will be checked visu-ally or by observational standards where such standards are established(see19.1),4.2.10Whether liquid penetrant inspection is required (see 19.2),4.2.11Whether radiographic inspection is required and,if so,the radiographic grade of casting required (19.3,Table 4),and4.2.12Whether Practices B660applies and,if so,the levels of preservation,packaging,and packing required (see 23.4).5.Responsibility for Quality Assurance5.1Unless otherwise specified in the contract or purchase order,the producer shall be responsible for the performance of all inspections and test requirements specified herein.Unless otherwise agreed upon,the producer may use his own or any other suitable facilities for the performance of the inspection and test requirements specified herein.The purchaser shall have the right to perform any of the inspections and tests set forth in the specification where such inspections are deemed necessary to confirm that the material conforms to prescribed requirements.6.Manufacture6.1The responsibility of furnishing castings that can be laid out and machined to the finished dimensions within the permissible variations specified,as shown on the blueprints or drawings,shall rest with the producer,except where mold equipment is furnished by the purchaser.7.Chemical Composition7.1The product shall conform to the chemical composition limits prescribed in Table 1.Conformance shall be determined by the producer by taking samples at the time castings are poured in accordance with Practice E716and analyzed in accordance with Test Methods E34,E607,or E1251,or CEN EN 14242.If the producer has determined the composi-tion of the material during casting,they shall not be required to sample and analyze the finished product.7.1.1A sample for determination of chemical composition shall be taken to represent one of the following:7.1.2Not more than 4000lb [2000kg]of clean castings or a single casting poured from one furnace.The maximum elapsed time between determinations shall be established for each alloy,but in any case the maximum elapsed time shall not exceed 8h.7.1.3The maximum elapsed time between determinations shall be established for each alloy,but in any case the maximum elapsed time shall not exceed 8h.7.2If it becomes necessary to analyze castings for confor-mance to chemical composition limits,the method used to sample castings for the determination of chemical composition shall be accordance with Practice B985.Analysis shall be performed in accordance with Practice E716,Test Methods E34,E607,or E1251,or CEN EN 14242(ICP method).8.Material Requirements—Castings Produced for Governmental and Military Agencies 8.1Unless otherwise specified,only aluminum alloy con-forming to the requirements of Specification B179or producers foundry scrap,identified as being made from alloy conforming to Specification B179,shall be used in the remelting furnace from which molten metal is taken for pouring directly into castings.Additions of small amounts of modifying and grain refining elements or alloys are permitted.8.2Pure materials,recycled materials,and master alloys may be used to make alloys conforming to this specification,provided chemical analysis can be taken and adjusted to conform to Table 1prior to pouring any castings.9.Foundry Control—Castings Produced for Governmental or Military Agencies,or Both9.1When specified,castings shall be produced under foundry control approved by the purchaser.Foundry control shall consist of examination of castings by radiographic or other approved methods for determining internal discontinui-ties until the gating,pouring,and other foundry practices have been established to produce castings meeting the quality standards furnished by the purchaser or agreed upon betweenTABLE 4Discontinuity—Level Requirements for Aluminum Castings in Accordance with Film Reference Radiographs E155or DigitalReference Radiographs E2422Grade A AGrade BGrade CGrade DDiscontinuitySection Thickness,in.(mm)1⁄4to 3⁄4(6.4to 19.0)1⁄4(6.4)3⁄4(19.0)1⁄4(6.4)3⁄4(19.0)1⁄4(6.4)3⁄4(19.0)Gas holesnone 112255Gas porosity (round)none 113377Gas porosity (elongated)none 113455Shrinkage cavitynone 1B2B3BShrinkage porosity or spongenone 112243Foreign material (less dense material)none 112244Foreign material (more dense material)none 112143Segregation none none none none Cracks none none none none Cold shutsnonenonenonenoneSurface irregularity Core shaftnot to exceed drawing tolerance not to exceed drawing toleranceA Caution should be exercised in requesting grade A because of the difficulty in obtaining this level.BNo radiographs e 1⁄4-in.[6-mm]for allthicknesses.the purchaser and the producer.When foundry practices have been so established,the production method shall not be significantly changed without demonstrating to the satisfaction of the purchaser that the change does not adversely affect the quality of the castings.Minor changes in pouring temperature of650°F[628°C]from the established nominal temperature are permissible.10.Tensile Requirements10.1The separately cast tension test specimens representing the castings shall meet the mechanical properties prescribed in Table2[Table3].10.2When specified,the tensile strength and elongation of test specimens cut from castings shall be in accordance with Table2[Table3]for Alloys354.0,C355.0,A356.0,A357.0, E357.0,359.0,and A444.0.For other alloys a minimum of 75%of the tensile and yield strength values and not less than 25%of the elongation values specified in Table2[Table3]are required.The measurement of elongation is not required for test specimens cut from castings if25%of the specified minimum elongation value published in Table2[Table3]is0.5 %or less.If grade D quality castings as described in Table4 are specified,no tensile tests shall be specified nor tensile requirements be met on specimens cut from castings.10.3Although Alloys705.0,707.0,and713.0are most frequently used in the naturally aged condition,by agreement of the producer and the purchaser,the castings may be artificially aged.The producer and the purchaser may also agree to base the acceptance of castings on artificially aged test bars.The conditions of artificial aging shown in Practice B917/B917M or AMS2771shall be employed unless other conditions are accepted by mutual consent.11.Workmanship,Finish,and Appearance11.1Thefinished castings shall be uniform in composition and free of blowholes,cracks,shrinks,and other discontinui-ties in accordance with standards designated and agreed upon as acceptable by the purchaser.12.Test Specimens12.1Separately cast test specimens shall be cast in iron molds.A recommended gating method is shown in Fig.1[Fig. 2]and Fig.3[Fig.4].An alternative gating design is shown in Appendix X4.The test section of the tension test specimen shall be cast to size in accordance with the dimensions shown in Fig.1[Fig.2]and Fig.3[Fig.4],and not machined prior to test.Grip ends may be machined to adapt them in such a manner as to ensure axial loading.12.2When properties of castings are to be determined, tension test specimens shall be cut from the locations desig-nated on the drawings,unless otherwise negotiated.If no locations are designated,one or more specimens shall be taken to include locations having significant variation in casting thickness,except that specimens shall not be taken from areas directly under risers.The tension test specimens shall be the standard0.500-in.[12.5mm]diameter specimens shown in Fig.9of Test Methods B557[B557M]or a round specimen of smaller size proportional to the standard specimens.In no case shall the dimensions of the smallest specimen be less than the following:in.mm Diameter of reduced section.0.250[6.00]Length of reduced section11⁄4[32]Radius offillet3⁄16[5]Diameter of end section3⁄8[10]Overall length:With shouldered ends23⁄8[60]With threaded ends3[75]With plain cylindical ends4[100] 12.3When necessary,a rectangular specimen may be used proportional to that shown for the0.500in.[12.5mm]wide specimen in Fig.6of Test Methods B557[B557M],but in no case shall its dimensions be less than the following:in.mm Width of reduced section,1⁄4[6]Length of reduced section,11⁄4[32]Radius offillet,1⁄4[6]Overall length,4[100] The specified elongation values shall not apply to tests of rectangular specimens.12.4If the castings are to be heat treated and separately cast specimens are to be used,the specimens representing such castings shall be heat treated with the castings they represent. If castings are to be heat treated and tests are to be obtained on the castings,the test specimens shall be taken from the castings after heat treatment.13.Number of Tests13.1Unless otherwise agreed upon by the purchaser and producer,two tension test specimens shall be separately cast and tested to represent the following:13.1.1Not more than4000lb[2000kg]of clean castings (gates and risers removed)or a single casting poured from one furnace.13.1.2The castings poured continuously from one furnace in not more than eight consecutive hours.13.2When tensile properties of castings are to be determined,one per melt-heat combination shall be tested unless otherwise shown on the drawing or specified in the purchase order.13.3If any test specimen shows defective machining or flaws,it may be discarded,in which case the purchaser and the producer shall agree upon the selection of a replacement specimen.14.Test Methods14.1The tensile properties shall be determined in accor-dance with Test Methods B557[B557M].15.Retests15.1If the results of the tension test do not conform to the requirements prescribed in Table2[Table4],test bars repre-sentative of the castings may be retested in accordance with the replacement tests and retest provisions of Test Methods B557 [B557M]and the results of retests shall conform to the requirements as to mechanical properties specified in Table2 [Table4].。
PROPERTIES AND CONTROL MOLD FLUXES FOR INGOT CASTING AND CONTIOUS CASTING

PROPERTIES AND CONTROLOF FLUXES FOR INGOT CASTINGAND CONTINUOUS CASTINGR. Carli, A. Del Moro, C. RighiPresent chemical-physical characteristics of ingot and continuous casting powders can be critically evaluatedpointing out history of invention of these materials.In an original tone, pioneering nature of first developments of casting powders will be described, illustrating empirical know-how of casting powders technology, based on trial-and-error method.It will be originally emphasized that technology of continuous casting powders derives directly from studiesand developments followed for ingot casting setting-up.Latest developments will be analysed in terms of the value innovation business model. KEYWORDS: casting powders, breakthrough invention, ingot casting, continuous casting, value innovation1.0 INTRODUCTION: HISTORICAL PERSPECTIVEDuring 20th century major historical and economic events haveshaped production of steel across the world, see Fig. 1 [1].Early post-WWII-period attends first important challenge ingrowing steel-making field which was mass production. Pro-duction of steel scored a 7-fold increase since 1940 during aperiod of time generally named “The 30 glorious years”. Ofcourse, this achievement mainly stems from relevant break-throughs in technologies of steel making and casting, such assecondary metallurgy and continuous casting. However, at-taining better quality, which was vital characteristic for moreand more demanding market, has been possible owing to whatcan be easily considered a real breakthrough invention.Since 1910 steel was cast in ingot shape with some technicalhitches in terms of operations and final quality of semis, seeFig. 2.Significant improvements were made only across 1960’s withlaunch of a new class of products named casting powders, i.e.,powders to be used in steel casting likely to carry out someunprecedented duties as protect steel from oxidation, providethermal insulation to liquid steel surface, absorb non-metallic inclusions, give some kind of lubrication.2.0 PRINCES OF SERENDIP“As their Highnesses travelled, they were always making dis-coveries, by accident and sagacity, of things which they wereR. Carli, A. Del Moro, C. RighiProsimet SpA, via Rodi 10, 24040 Filago BG,.not in quest of”. This was written by Horace Walpole in his let-ter to Horace Mann on January 28th , 1754 giving an example of such attitude of discovering things by chance and sincere observation of reality.Although it’s difficult to say that invention of casting powders was due to serendipity or empathy based on understanding of operations and fundamentals of steel ingot casting, it was surely triggered in 1957 by the encounter between Edgar Bo-lens, steel plant manager of Cockerill Seraing Steelworks, that time close to retirement, and young engineer Hans J. Eitel, working for Carl Spaeter Duisburg representative for Veitscher Magnesit, a well-known refractory company.Bolens apprised Eitel about results of some experimentshe sFig. 1World steel production across the 20th century from Ref.[1].Produzione mondiale di acciaio nel XX secolo da Ref. [1].performed casting steel ingot with powders made by very poor components. This wide-open-minded young metallur-gist, who served the German army as frei williger with Luft-waffe engineer corps in Travemünde, enthusiastically embrac-es that new idea, developing in 40 years many new products to modern commercial casting powders, [2-3].With a sponsorship from Oerlichs GmbH & Co. KG, a com-pany whose business was production of consumables for steel-making, and commercial network of Carl Spaeter, Eitel started diffusing use of this new product, facing typical resistance to all new ideas of such dynamic but biased technical environ-ment, [2].He finally founded his own company Metallurgica GmbH & Co. KG in 1965. Three years later, Eitel hired from Bochumer Verein steel plant a young chemist, Heinz W. Schmidt, who’ll came out to be one of most valuable of his co-workers.Hans Eitel obtained a doctorate from Aachen University in his late 70ies, discussing a thesis on developing and manufactur-ing casting powders. This is still a significant document, not yet translated from German, reporting bright achievements of an entire life spent in following innovative vision of steel cast-ing technologies [2].3.0 POWDERS FOR INGOT CASTINGEarly products were only mechanical mixture of few compo-nents, based on poor raw materials such as fly ashes, soda ash and milled coke. In spite of their simple compositions these materials featured a complete set of important properties, whose control was made through a proper balance of each component. While spreading on surface of liquid steel was as-sured by intrinsic characteristic of fly ash, addition of specific amount of soda ash allowed tuning of melting temperature, see Fig. 3. Moreover dosing of milled metallurgical coke pre-vented excessive consumption of powder during casting, con-trolling its melting rate.Although these considerations appear almost trivial or evident even to dummy of casting powder field, it has to be consid -ered those are actual observations, meaning with that, results of long and intense period of experimentations.Dawning of casting powder technology was characterized by kind of magic, growing on that field of rough practice politely called trial-and-error method. Still basic know-how of casting powder technology is empirical one.A significant flourishing of scientific knowledge has been re -cently recognized in this field, being analogically associated to scientific domain of formulation chemistry [4].4.0 EXPLORING TECHNOLOGICAL PROPERTIES OF INGOT CASTING POWDERSIn the previous paragraph, past pioneering nature of devel-opment of casting powders has been evidenced. Initial ran-dom walking in a pseudo-bi-dimensional phases space - fly ash content and soda ash content were two parameters to be changed as depicted in Fig. 3 - allowed exploring technological properties of new products in connection with their physical and chemical characteristics. It was then possible to observe that different mineralogical and chemical compositions exten-sively affect spreading, insulation capability of powder layer, melting properties as melting temperature and melting rate, finally resulting in a better quality of cast ingot, see Fig. 4.Relevant improvements of final steel ingot quality, as inner cleanness, better ingot surface and a profitable increase ofprocess yield by reduction of pipe, were economic factors wid-s Fig. 2“Ingot Molds”, ca. 1910, rare Meissen porcelainplaque, Georg Haberecht (Germany), The Eckhart G. Grohmann Collection at Milwaukee School of Engineering.“Ingot Molds”, ca. 1910, raro dipinto su porcellana di Meissen, Georg Haberecht (Germania), The Eckhart G. GrohmannCollection alla Milwaukee School of Engineering.s Fig. 3Pseudo-bi-dimensional phases space. Fly ashcontent and soda ash content were two parameters to be changed, modifying products characteristics.Spazio delle fasi pseudo-bi-dimensionale. Il contenuto di ceneri e il contenuto di soda sono i due parametri che devono essere cambiati per modificare le caratteristiche dei prodotti.ening use of ingot casting powders.It was also possible to understand that different ingot size and different steel grades may surprisingly require different products, i.e., products having different physical and chemical characteristics. Although main cause was relevant inconsisten-cy of original raw materials in terms of melting rate or carbon content, it was clear from very beginning that some products tuning due to process peculiarities was required.Spreading and insulatingConcerning spreading, it has been already pointed out that this property of ingot casting powder derives from intrinsic char-acteristic of fly ash. In modern casting powders manufacturing technology, this characteristic is controlled by custom designed spreading test and eventually corrected with special additives. Good spreading of casting powder results in effective cover-ing of liquid steel free surface, preventing re-oxidation due to steel contact with atmosphere. Moreover, homogeneous dis-tribution of powder across liquid steel free surface combined with suitable thermal properties provides effective insulation to steel at ingot head even at the end of casting, contributing to pipe reduction. Thermal properties are generally correlated to apparent bulk density of products, in this case again correlated with intrinsic characteristics of fly ash. Similarly to spreading apparent bulk density, i.e., insulating properties is tested and eventually corrected with special additives in modern casting powder manufacturing technology.MeltingControlling melting properties has been the first real job. In -deed, changing proportion between components, eventually adding some milled coke without knowing exactly related chemistry has required time intensive testing, brain storming and sometime luck.Simple lab tests were set up to control these characteristics and to check deviations according to different chemistry. Actually, it was like to start playing around one of most important factor affecting melting of a flux which is lowest eutectic temperature which system can exhibit [6], see Fig. 5.In spite of the fact that elucidation of mechanism of castingpowders melting process is for some aspects still a research topic, changing of content of soda ash remains a rigorous ther-modynamic approach.Probably some failure analyses came out to be first insight on casting powder melting rate, evidencing that fly ashes with lower carbon content tended to melt faster. Trying to overcome this occurrence different milled coke was added with effect of obtaining kind of control of these characteristics.Present knowledge of so-called coating effect of free carbon particles is based in a similar empirical approach supported by some mechanistic understanding [7].5.0 CONTINUOUS CASTING: A NEW APPLICATION The advent of new technology of continuous casting opened up a new application field for these new products. Actually, spreading of use of casting powders wasn’t easy and immedi -ate; success came only because of combination of a number of key factors.Since early patents on continuous casting machine and their applications [8], major step forward of this technology was the commissioning of the world’s first slab continuous casting plant in 1961 by Dillinger Hutte GTS, in Dillingen Germany. It’s important to note that event was synchronic with initial spreading of use of ingot casting powder, see paragraph.2.To prevent sticking of solidifying steel shell into the mold, lu-bricant drawn into mold/strand gap by mold oscillation has to be applied. Traditionally vegetable oils composed mainly by linoleic or oleic acid were used. Later mineral and synthetic oils were applied.In spite of some drawbacks such as unstable distribution as well as Hydrogen and Carbon pick-up defects in steel, high breakouts and depression frequency, use of oil as lubricating agent was only choice [9]. Indeed, oil was used for many years in former Soviet Union countries even after introduction ofmodern powders for continuous casting.s Fig. 4Schematic representation of mold powderperformance stages, adapted from Ref.[5].Rappresentazione a blocchi delle fasi di funzionamento diuna polvere di colata, adattata da Ref. [5].s Fig. 5Equilibrium phase diagram of the Na 2O-SiO 2binary system. Red arrow highlights lowest eutectic composition, from Ref.[6].Diagramma di fase all’equilibrio del sistema binario Na 2O-SiO 2. La freccia rossa indica la composizione dell’eutettico più basso, da Ref. [6].Aiming to find better lubricating agent, first trial was made in Dillingen with a sample of standard ingot casting pow-der by steel plant technicians. Soon they realized that more sistematic and technical approach was required because of complexity of this problem. Therefore, supplier of this prod-uct was directly involved in this challanging development. Again, it’s interesting to stress that encounter between those engineers and Eitel staff sparked research in this uncharted ocean.From very first test was clear that infiltration of liquid slag resulting from powder melting was absolutely uneven and insufficient to assure good lubrication at least comparable to standard oil lubricant.Starting from some ground knowledge of metallurgical slag chemistry, particularly related to slag fluidity, they tried to manipulate casting powder slag fluidity mixing original sample with different amounts of a metallurgical slag con-taining CaO and CaF2. Thus, significant improvement of slaginfiltration was observed, see Fig. 6.Once more, it’s worth noting empirical nature of approach followed to explore unfamiliar field of casting powders for continuous casting machines.Remarkably, without exact consciuosness of mechanism af-fecting observedphenomena, these pioneers made signifi -cant stepforward to modern technology of continuous cast-ing powder then properly named mold flux. From a chemical point of view mixing parent ingot casting powder with CaO-CaF 2-based metallurgical slag resulted in a shift from mullite to pseudo-wollastonite region in a ternary phase dyagram SiO 2-CaO-Al 2O 3. System was becoming more and more com-plex since chemical elements were playing a role, still not completly understood, in defining physical-chemical prop -erties of molten slag. In particular, presence of Na, Ca and expecially F, was affecting number of tetrahedral coordinate cations, T, and non bridging oxygen, NBO, changing popu-lation of melt structural unit from Q0 to Q3, resulting in a rel-atively significant decrease of slag viscosity, see Fig. 7 [10].6.0 FROM INGOT TO CONTINUOUS CASTING MACHINESIn Fig. 8 similar scheme presented in paragraph.4 is reported. As one can infer, red coloured step represents technological properties being explored during challenging replacement of oil by casting powder, namely slag infiltration, while grey coloured steps represent attributes already investigated in development of casting powder for ingots. This considera-tion suggests that technology of continuous casting powders derives directly from early development of powders for in-got casting.All characteristics discussed for ingot casting powders were actually borrowed by new products used in continuous cast-ing machines and entire know-how was applied to develop innovative features of these new products. Of course bias cannot be excluded: modern casting powders actually have very peculiar characteristics mainly because of some histori-cal reasons.s Fig. 6Pseudo-bi-dimensional phases space.Ingot casting powder content and CaO-CaF 2-based metallurgical slag content were two parameters to be changed, modifying products characteristics.Spazio delle fasi pseudo-bi-dimensionale. Il contenuto di polvere per lingotti e il contenuto di slag metallurgico a base di CaO-CaF 2 sono i due parametri che devono essere cambiati per modificare le caratteristiche dei prodotti.s Fig. 7Typical structural unit of silicate glasses andmelts.Tipica unità strutturale di vetri e fusi silicatici.s Fig. 8Schematic representation of mold powderperformance stages, see Fig. 4.Rappresentazione a blocchi delle fasi di funzionamento di una polvere di colata, vedi Fig. 4.All well-defined qualities built-up during ground-breaking studies on ingot casting powders play almost same role in new continuous casting products. However, powder melt-ing and resultant liquid pool formation play far more im-portant roles in continuous casting equipment, being these processes strongly related to availability of liquid slag for infiltration-lubrication.Some tuning was required for further improvement. Then, random walking in pseudo-bi-dimensional phases space analogous to that one discussed in paragraph.4 - ingot cast-ing powder content and CaO-CaF 2-based metallurgical slag content were two parameter to be changed as depicted in Fig. 6 - disclosed technological properties of new products.Slag infiltrationInfiltration of slag formed by melting of casting powder is most important technological characteristic of these products and most important factor controlling lubrication of strand forming in a continuous casting mold. As stated above, in-filtration is enhanced by relative movement of mold and strand, particularly when mold is moving downward faster than strand.As far as chemical features of casting powder are concerned, based on present knowledge it’s clear that liquid slag viscos -ity and solidification temperature are major impact factors on infiltration-lubrication phenomena.These factors are presently monitored by means of high tem-perature rotational viscosimetry, DSC (differential scanning calorimetry): important resources are continuously invested to improve effectiveness of these analytical techniques [7].Other propertiesAmong other steps in scheme depicted in Fig. 8, formation of solid-liquid film and heat transfer control are very recent topic of advanced casting powders expertise. Thus, lubrica-tion only has been referred as most important breakthrough known from use of new continuous casting powders.Since mold fluxes fundamental recognized functions are to assure lubrication required by tribological system of mold-solidifying strand shell and to provide crystalline phase solid film contributing to control heat extraction between strand and mold wall, researchers have been and are still making huge efforts in these areas of investigations.7.0 VALUE INNOVATIONThanks to vertical growth of steel market along two decades, from 1960 until first big energy crisis, market of casting pow -ders followed same trend up, showing an impressive expan-sion.Reminding image given in paragraph.5 describing spread-ing application of these new products as a kind of ocean to be explored, it’s possible to affirm that casting powders market has clearly been for many years a ‘blue ocean’, re -ferring to business model discussed by W.Chan Kim and R.Mauborgne [11]. The statement is true mainly by virtue of ground-breaking nature of this innovation and fast market growth.However, products were relatively weak with respect to re-verse engineering and difficult to patent. Therefore, strategic focus for competing in such unlikely ‘red-shifting’ market was pursuing quantum leap in value, i.e., following so-called value innovation logic. In terms of product and service of-fering, value innovation consists in searching for the total solution customers seek beyond market traditional answers [11].Major following achievements of casting powders technol-ogy can be explained as steps of specific value innovation process.Synthetic powderOriginal fly-ash-based casting powders suffered some qual -ity instabilities due to batch to batch variations of chemical analyses of fly ashes. Those were difficult to manage due to primitive analytical instrumentations. Solution was found using different raw materials with reasonably constant chemistry as milled quartz sand, Portland cement, calcium oxide, bauxite … etc., replicating known properties of parent product. Then, a new product family, denominated synthetic casting powders, was commercialised giving advantage of much more stable quality and performance.Now, let’s try to schematise value innovation logic behind launch of synthetic casting powders.A value curve is drawn plotting performance elements vec-tor of a product in a high-low scale allowing instant com-parison with alternative products. These elements should describe aspects of product performance covering buyer experience cycle [12], likely to be very essential in case of a B2B goods. In the present work, some elements concerning casting powders have been considered crucial. Results are depicted in Fig. 9.It’s clear from value curve above proposed that synthetic casting powders were significant value innovated products for two elements where attention of end user was focused: better stability and improved quality of cast semis.Granulated powderSimilarly, it’s possible to analyse another improvement step in technology of casting powder which was the control of morphological properties of products.This relatively recent achievement resulted from application of well-known flash-drying process named spray-dryingwhich consists in drying drops of sprayed water-based slurry by as Fig. 9Value curve of casting powders.Curva di valore delle polveri di colata.ABSTRACTPROPRIETÀ E CONTROLLO DI POLVERI DI COLATA PER LINGOTTI E PER COLATA CONTINUAParole chiave: acciaio, acciaieria, colata continua, storia metallurgia.Le caratteristiche chimico-fisiche delle moderne polveri per lingotti e per colata continua possono essere valutate criticamente analizzando la storia dell’inven-zione di questi prodotti.Attraverso un approccio originale verrà descritta la natura pionieristica dei primi sviluppi delle polveri di colata illustrando il know-how empirico della tecnologia delle polveri basato sul metodo del trial-and-error.Si spiegherà come la tecnologia delle polveri di colata continua derivi diretta-mente dagli studi e gli sviluppi seguiti per la messa a punto delle polveri per il colaggio dei lingotti.Gli sviluppi più recenti saranno analizzati attraverso il business model della value innovation.counter flow of hot air in a special designed drying tower. Typi -cal spheroidal material obtained through this process is shown in Fig. 10.This new product family was differently named from supplier to supplier as granulated, spheroidal, atomised casting powder.The value curve of granulated casting powders is shown for comparison in Fig. 11.It’s evident that granulated casting powders were materials achieving significant value innovation of all product elements, from products shelf life to final quality of cast semis. In particu -lar, control of pollution of working environment due to sharp decrease of fine residue and possibility to feed automatically continuous casting mold with dedicated special machines repre-sented foremost characteristics to create a new ‘blue ocean’.8.0 CONCLUSIONSHistory of invention of casting powders for ingot and continuous casting machines has been considered in order to give some ele-ments for understanding present characteristics of these materi-als. Past pioneering nature of development of casting powders has been evidenced, showing that basic know-how of casting powder technology is empirical, i.e., based on trial-and-error method.It has been shown that early achievements of technology of cast-ing powders concern fundamental aspects of chemistry and phys-ics of these materials. Then, it has been made clear that technology of continuous casting powder derives directly from development of powder for ingot casting.More recent developments have been analysed in terms of the value innovation business model.BIBLIOGRAPHY[1] J-P .Birat, Innovation Paradigms for the Steel Industry of the 21st Century, M.M.Wolf - Memorial Symposium, Zurich, 2002.[2] H.J.Eitel, Entwicklung und Produktion von Gießpuwergranulat mittels Sprütrocknungverfahren sowie dessen Bedeutung für die Stahlindustrie, PhD Thesis, 1990, Fakultët für Bergbau, Hüttenwesen und Geowissenschaften der Rheinisch-West-fälischen Techniscen Hochschule Aachen.[3] H.W.Schmidt, private communication.[4] R.Carli, C.Righi, Composite Materials Formulation Chemistry, Ind.Chem.Master Course, Faculty of Science, University of Mi-lan, 2004.[5] ls, Review of ECSC-funded Research on mold pow-ders, EUR 13177, ECSC, Luxemburg, 1991[6] J-W.Kim, Y-D.Lee and H-G.Lee, ISIJ, 41(2)(2001)116-123.[7] C.A.Pinheiro, I.V .Samarasekera and J.K.Brimacombe, Keeping Current Series, I&SM, November 1994.[8] S.Junghans, Process and Device for the Casting of Metal Strands, German Patent 750301, 20/10/1933.[9] Y.Sahai, T.Emi, M.M.Wolf, A Short course on Advanced Tundish & Mold Technologies, Zurich, 1998.[10] D.Giordano and D.B.Dingwell, Bull.Volcan., 65(2003)8-14.[11] W-C. Kim and R.Mauborgne, Creating New Market Space, Harvard Business Review on Innovation, 2001.[12] W-C. Kim and R.Mauborgne, Value Innovation – The strategic Logic on High Growth, Harvard Business Review on Break-trough Thinking, 1999.s Fig. 10SEM pictures of a granulated casting powder.Immagine SEM di una polvere di colata granulata.s Fig. 11Value curve of casting powders.Curva di valore delle polveri di colata.。
美国商务部管制清单索引

ALPHABETICAL INDEXTO THE COMMERCE CONTROL LISTThis index is not an exhaustive list of controlled items.Description ECCN Citation Ablative liners, thrust or combustion chambers .................................................................. 9A106.a Abrin ................................................................................................................................. 1C351.d.1 Absettarov (Central European tick-borne encephalitis virus) ..................................... 1C360.a.1.a.1 Absolute reflectance measurement equipment .................................................................... 6B004.a Absorbers of electromagnetic waves ...................................................................................... 1C001 Absorbers, hair type ...............................................................................................1C001.a Note 1.a Absorbers, non-planar & planar ....................................................................... 1C001.a Note 1.b&c Absorption columns ............................................................................................................. 2B350.e Accelerators (electro-magnetic radiation) ............................................................................ 3A101.b Accelerators or coprocessors, graphics .............................................................................. 4A003.d Accelerometer axis align stations .............................................................................. 7B003, 7B101 Accelerometer test station .......................................................................................... 7B003, 7B101 Accelerometers & components therefor ................................................................ 7A101 Accelerometers & accelerometer components ........................................................................ 7A001 Acoustic beacons ........................................................................................................... 6A001.a.1.b Acoustic beam forming software ...................................................................................... 6D003.a.1 Acoustic hydrophone arrays, towed ............................................................................. 6A001.a.2.b Acoustic location & object detection systems ............................................................... 6A001.a.1.b Acoustic, marine, terrestrial equipment .................................................................................. 6A991 Acoustic mounts, noise reduction equipment for vessels .............................................. 8A002.o.3.a Acoustic-optic signal processing devices ......................................................................... 3A001.c.3 Acoustic positioning systems ......................................................................................... 6A001.a.1.d Acoustic projectors ........................................................................................................ 6A001.a.1.c Acoustic seabed survey equipment ................................................................................ 6A001.a.1.a Acoustic systems, diver deterrent ....................................................................................... 8A002.r Acoustic systems, marine ..................................................................................................... 6A001.a Acoustic transducers ...................................................................................................... 6A001.a.2.c Acoustic underwater communications systems ............................................................... 5A001.b.1 Acoustic vibration test equipment .......................................................................................... 9B006 Acoustic wave devices ......................................................................................................... 3A001.c Acoustic-wave device manufacturing equipment and systems .................................. 3B991.b Note Active compensating system rotor clearance control software ............................................ 9D004.d Active flight control system software .................................................................................. 7D003.e Active flight control system technology .............................................................................. 7E004.b Active magnetic bearing systems......................................................................................... 2A001.c Active acoustic systems .................................................................................................... 6A001.a.1 Export Administration Regulations Bureau of Industry and Security January 9, 2012Actively cooled mirrors .................................................................................................... 6A005.e.1 Adaptive control software .................................................................................................... 2D992.a Adaptive control software ................................................................................................. 2D002.b.2 ADCs (analog-to-digital converters).................................................................................... 3A101.a ADCs (analog-to-digital converters)................................................................................. 3A001.a.5 ADCs (analog-to-digital converters).................................................................................... 4A003.e Aero gas turbine engine/assemblies/component test software............................................. 9D004.b Aero gas turbine engines ......................................................................................................... 9A001 Aerodynamic isotope separation plant/element housings ................................................. 0B001.a.3 Aerodynamic separation process systems & components ................................................... 0B001.d Aerosol challenge testing chambers ..................................................................................... 2B352.g Aerosol generating units specially designed for fitting to the systems specified in 2B352.h.1 or h.2 ...................................................................................... 2B352.h.3 Aflatoxins .......................................................................................................................... 1C351.d.2 African horse sickness virus ........................................................................................... 1C352.a.17 African swine fever virus (animal pathogens) .................................................................. 1C352.a.1 Agitators (chemical manufacturing) .................................................................................... 2B350.b AHRS (Attitude Heading Reference Systems), source code .................................................. 7D002 Air traffic control software ............................................................................................... 6D003.h.1 Air independent power systems (for underwater use) ..........................................................8A002.j Air compressors and filtration systems designed for filling air cylinders ............................8A992.l Air Traffic Control software application programs ................................................................ 6D993 Airtight vaults ......................................................................................................................... 0A981 Airborne altimeters ................................................................................................................. 7A006 Airborne altimeters ................................................................................................................. 7A106 Airborne communication equipment ...................................................................................... 7A994 Airborne radar equipment ....................................................................................................... 6A998 Aircraft .................................................................................................................................... 7A994 Aircraft, civil ........................................................................................................................ 9A991.b Aircraft, demilitarized .......................................................................................................... 9A991.a Aircraft, n.e.s........................................................................................................................... 9A991 Aircraft, trainer ....................................................................................................................... 9A018 Aircraft breathing equipment and parts ............................................................................... 9A991.e Aircraft (military) pressurized breathing equipment ........................................................... 9A018.d Aircraft inertial navigation systems & equipment ............................................................... 7A103.a Aircraft inertial navigation systems & equipment .................................................................. 7A003 Aircraft parts and components ............................................................................................. 9A991.d Akabane virus ................................................................................................................ 1C360.b.1.a Alexandrite ........................................................................................................................... 6C005.b Alexandrite lasers........................................................................................................... 6A005.c.2.b Align & expose step & repeat equipment (wafer processing) ..........................................3B001.f.1 Alignment equipment for equipment controlled by 7A .......................................................... 7B001 Export Administration Regulations Bureau of Industry and Security January 9, 2012Description ECCN Citation Alkylphenylene ethers or thio-ethers, as lubricating fluids .............................................. 1C006.b.1 Alloy strips, magnetic .......................................................................................................... 1C003.c Alloyed materials production systems and components ......................................................... 1B002 Alloyed metal materials in powder or particulate form ....................................................... 1C002.b Alloyed metal materials in the form of uncomminuted flakes, ribbons, or thin rods .......... 1C002.c Alloys, aluminum ................................................................................................................. 1C202.a Alloys, aluminum ........................................................................................................... 1C002.a.2.d Alloys, magnesium ........................................................................................................ 1C002.a.2.e Alloys, metal powder or particulate form ............................................................................ 1C002.b Alloys, nickel ............................................................................................................... 1C002.a.2.a Alloys, niobium.............................................................................................................. 1C002.a.2.b Alloys, titanium.................................................................................................................... 1C202.b Alpha-emitting radionuclides, compounds, mixtures, products or devices ............................ 1C236 Altimeters, airborne ................................................................................................................ 7A006 Altimeters, radar or laser types ............................................................................................. 7A106 Alumina fibers ......................................................................................................... 1C010.c Note 1 Aluminides ........................................................................................................................ 1C002.a.1 Aluminides, nickel ......................................................................................................... 1C002.a.1.a Aluminides, titanium...................................................................................................... 1C002.a.1.b Aluminum alloys ............................................................................................................ 1C002.a.2.d Aluminum alloy/powder or particulate form ............................................................... 1C002.b.1.d Aluminum alloys as tubes/solid forms/forgings ................................................................. 1C202.a Aluminum electroplating equipment .................................................................................... 2B999.i Aluminum gallium nitride (AlGaN) “substrates”, i ngots, boules, or otherpreforms of those materials ................................................................................................. 3C005 Aluminum nitride (AlN) “substrates”, ingots, boules, or other preforms ofthose materials ..................................................................................................................... 3C005 Aluminum organo-metallic compounds ................................................................................. 3C003 Aluminum oxide powder, fine ................................................................................................ 0C201 Aluminum powder, spherical .......................................................................................... 1C111.a.1 Aluminum powder (spherical) production equipment ............................................................ 1B102 Amalgam electrolysis cells, lithium isotope separation .................................................. 1B233.b.3 Amalgam pumps, lithium and/or mercury ........................................................................ 1B233.b.2 Ammonia, aqueous ................................................................................................................. 1C980 Ammonia crackers ......................................................................................................... 0B004.b.2.d Ammonia distillation towers .......................................................................................... 0B004.b.4.b Ammonia synthesis converters & units .................................................................................. 1B227 Ammonia-hydrogen exchange plant ................................................................................. 0B004.a.2 Ammonia-hydrogen exchange equipment and components ........................................... 0B004.b.2 Ammonium bifluoride ............................................................. see ammonium hydrogen fluoride Ammonium hydrogen fluoride ......................................................................................... 1C350.d.1 Ammonium nitrate, including certain fertilizers containing ammonium nitrate .................... 1C997 Export Administration Regulations Bureau of Industry and Security January 9, 2012Description ECCN Citation Ammunition hand-loading equipment .................................................................................... 0B986 Amorphous alloy strips ........................................................................................................... 1C003 Amplifiers, microwave solid state .................................................................................... 3A001.b.4 Amplifiers, pulse .................................................................................................................. 3A999.d Analog instrumentation tape recorders ............................................................................. 3A002.a.1 Analog computers ................................................................................................................... 4A101 Analog-to-digital converters ................................................................................................ 3A101.a Analog-to-digital converters, integrated circuits .............................................................. 3A001.a.5 Analog-to-digital conversion equipment ............................................................................. 4A003.e Analyzers, network .............................................................................................................. 3A002.e Analyzers, spectrum .......................................................................................................... 3A002.c.1 Andes virus ....................................................................................................................... 1C351.a.1 Angular displacement measuring instruments ..................................................................... 2B206.c Angular measuring instruments ........................................................................................ 2B006.b.2 Angular measuring instruments .............................................................................................. 2B206 Angular-linear inspection equipment (hemishells) ................................................................. 2B206 Angular-linear inspection equipment (hemishells) .............................................................. 2B006.c Angular rate sensors ................................................................................................................ 7A002 Animal pathogens .................................................................................................................. 1C352 Annealing or recrystallizing equipment ...................................................................... 3B991.b.1.c.1 Antennae, for microwave power source ............................................................................ 0B001.i.3 Antennae, phased array ...................................................................................................... 5A001.d Antennae, phased array (for radar) ...................................................................................... 6A008.e Anti-vibration mounts (noise reduction), civil vessels .................................................. 8A002.o.3.a Antimony hydrides.................................................................................................................. 3C004 Aramid fibers & filamentary materials ................................................................................ 1C210.a Aramid fibers & filamentary materials ................................................................................ 1C010.a Arc remelt & casting furnaces ............................................................................................. 2B227.a Argon ion lasers ................................................................................................................... 6A205.a Argon ion lasers ................................................................................................................... 6A005.a Armor body ............................................................................................................................. 1A005 Armor plate drilling machines ............................................................................................. 2B018.a Armor plate planing machines ............................................................................................. 2B018.b Armor plate quenching presses ............................................................................................ 2B018.c Arms machinery, equipment, gear, parts, and accessories ..................................................... 2B018 Arms (small) chambering machines .................................................................................... 2B018.o Arms (small) deep hole drilling machines and drills therefor ............................................. 2B018.p Arms (small) rifling machines ............................................................................................. 2B018.q Arms (small) spill boring machines ......................................................................................2B018.r Aromatic polyimides ......................................................................................................... 1C008.a.3 Aromatic polyamide-imides .............................................................................................. 1C008.a.2 Aromatic polyetherimides ................................................................................................. 1C008.a.4 Export Administration Regulations Bureau of Industry and Security January 9, 2012Description ECCN Citation Array processor microcircuits .................................................................................. 3A001.a.3 Note Array processors/assemblies ................................................................................................. 4A004 Array processors/assemblies ................................................................................................... 4A003 Arrays of aerosol generating units or spray booms, specially designed forfitting to aircraft, “lighter than air vehicles,”or “UAVs”............................................ 2B352.h.2 Arsenic trichloride ............................................................................................................ 1C350.b.1 Arsenic hydrides ..................................................................................................................... 3C004 Asphalt paving mixtures ......................................................................................................... 1C980 Aspheric optical elements .................................................................................................... 6A004.e Assemblies to enhance performance by aggregation of computing elements ..................... 4A994.c Asynchronous transfer mode (ATM) equipment ......................................................... 5A991.c.10.d Asynchronous transfer mode (ATM), technology for the developmentof equipment employing ................................................................................................ 5E001.c.1 Atomic vapor laser isotope separation plant ..................................................................... 0B001.a.6 Atomic vapor laser isotope separation process equipment .................................................. 0B001.g Atomic frequency standards ................................................................................................ 3A002.g Atomic transition solid state lasers ...............................................................................6A005.a or b Attitude Heading Reference Systems (AHRS), source code software ................................... 7D002 Attitude control equipment for missiles .................................................................................. 7A116 Aujeszky’ disease virus (Porcine herpes virus) ................................................................ 1C352.a.6 Austenitic stainless steel plate, valves, piping, tanks and vessels ....................................... 2B999.n Autoclave temperature, pressure or atmosphere regulation technology ................................. 1E103 Autoclaves, ovens and systems ............................................................................................ 0B002.a Automated control systems, submersible vehicles .............................................................. 8A002.b Automatic drug injection systems ........................................................................................... 0A981 Automotive, diesel, and marine engine lubricating oil ........................................................... 1C980 Avian influenza virus ........................................................................................................ 1C352.a.2 Aviation engine lubricating oil ............................................................................................... 1C980 Avionic equipment, parts, and components ............................................................................ 7A994 Avionics EMP/EMI protection technology ............................................................................ 7E102 Bacillus anthracis .............................................................................................................. 1C351.c.1 Bacteria ................................................................................................................................ 1C351.c Bacteria ................................................................................................................................ 1C354.a Bacteria ................................................................................................................................ 1C352.b Baffles .................................................................................................................................. 0A001.h Baffles (rotor tube), gas centrifuge ................................................................................... 0B001.c.7 Balancing machines ............................................................................................................. 2B119.a Balancing machines ............................................................................................................. 7A104.a Balancing instrumentation ................................................................................................... 7A104.b Balancing machines, centrifugal multiplane ........................................................................... 2B229 Balancing mahcines, centrifugal multiplane ....................................................................... 2B999.m Ball bearings, precision hardened steel and tungsten carbide .............................................. 1C999.a Export Administration Regulations Bureau of Industry and Security January 9, 2012Description ECCN Citation Ball bearings, Radial ............................................................................................................... 2A101 Ball & solid roller bearings .................................................................................................. 2A001.a Band-pass filters, tunable .................................................................................................. 3A001.b.5 Barium metal vapor lasers ................................................................................................... 6A005.b Bartonella quintana ........................................................................................................... 1C351.b.1 Batch mixers .......................................................................................................................... 1B117 Bathymetric survey systems .......................................................................................... 6A001.a.1.b Batons, shock .......................................................................................................................... 0A985 Batons, spiked ......................................................................................................................... 0A983 Bay cable systems .......................................................................................................... 6A001.a.2.e Bay cable systems software ............................................................................................ 6D003.a.3 Bayonets ............................................................................................................................... 0A918.b Beam lead bonders, stored program controlled equipment ........................................... 3B991.b.3.b Beam steering mirrors ....................................................................................................... 6A004.a.4 Beamforming techniques ............................................................................................... 6A001.a.2.c Bearings, ball & solid roller ................................................................................................. 2A001.a Bearings, gas centrifuge .................................................................................................... 0B001.c.4 Bearings, gas centrifuge .................................................................................................... 0B001.c.5 Bearings, high precision/temperature/special ......................................................................... 2A001 Bearings, magnetic (active) ................................................................................................. 2A001.c Bearings, magnetic (suspension) ...................................................................................... 0B001.c.4 Bearings, precision hardened steel and tungsten carbide ..................................................... 1C999.a Bellow valves .................................................................................................................... 0B001.b.1 Bellow valves .................................................................................................................. 0B001.d.6 Bellows forming dies ........................................................................................................... 2B999.b Bellows manufacturing equipment ...................................................................................... 2B999.b Bellows or rings, gas centrifuge........................................................................................ 0B001.c.6 Bellows seal valves ............................................................................................................... 2A226 Bellows seal valves .............................................................................................................. 2B350.g Bellows sealed valves, n.e.s. ................................................................................................. 2A999 Bellows-forming mandrels................................................................................................... 2B228.c Bellows-forming dies ........................................................................................................... 2B228.c Benzilic acid...................................................................................................................... 1C350.b.2 Beryllium metal, alloys, compounds, or manufactures......................................................... 1C230 Beryllium metal particulate......................................................................................... 1C111.a.2.a.4 Beryllium/beryllium substrate blanks .................................................................................. 6C004.d Biological containment facilities, ACDP level 3 or 4 .......................................................... 2B352.a Biological isolators ............................................................................................................2B352.f.2 Biological manufacturing equipment & facilities ................................................................... 2B352 Biological safety cabinets ..................................................................................................2B352.f.2 Bismaleimides ................................................................................................................... 1C008.a.1 Bismuth ................................................................................................................................... 1C229 Export Administration Regulations Bureau of Industry and Security January 9, 2012。
汽车零部件制造行业职业病危害及其防控措施分析
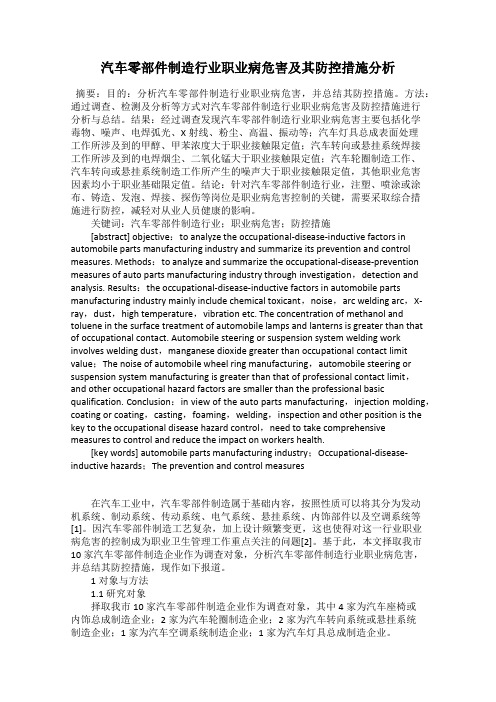
汽车零部件制造行业职业病危害及其防控措施分析摘要:目的:分析汽车零部件制造行业职业病危害,并总结其防控措施。
方法:通过调查、检测及分析等方式对汽车零部件制造行业职业病危害及防控措施进行分析与总结。
结果:经过调查发现汽车零部件制造行业职业病危害主要包括化学毒物、噪声、电焊弧光、X射线、粉尘、高温、振动等;汽车灯具总成表面处理工作所涉及到的甲醇、甲苯浓度大于职业接触限定值;汽车转向或悬挂系统焊接工作所涉及到的电焊烟尘、二氧化锰大于职业接触限定值;汽车轮圈制造工作、汽车转向或悬挂系统制造工作所产生的噪声大于职业接触限定值,其他职业危害因素均小于职业基础限定值。
结论:针对汽车零部件制造行业,注塑、喷涂或涂布、铸造、发泡、焊接、探伤等岗位是职业病危害控制的关键,需要采取综合措施进行防控,减轻对从业人员健康的影响。
关键词:汽车零部件制造行业;职业病危害;防控措施[abstract] objective:to analyze the occupational-disease-inductive factors in automobile parts manufacturing industry and summarize its prevention and control measures. Methods:to analyze and summarize the occupational-disease-prevention measures of auto parts manufacturing industry through investigation,detection and analysis. Results:the occupational-disease-inductive factors in automobile parts manufacturing industry mainly include chemical toxicant,noise,arc welding arc,X-ray,dust,high temperature,vibration etc. The concentration of methanol and toluene in the surface treatment of automobile lamps and lanterns is greater than that of occupational contact. Automobile steering or suspension system welding work involves welding dust,manganese dioxide greater than occupational contact limit value;The noise of automobile wheel ring manufacturing,automobile steering or suspension system manufacturing is greater than that of professional contact limit,and other occupational hazard factors are smaller than the professional basic qualification. Conclusion:in view of the auto parts manufacturing,injection molding,coating or coating,casting,foaming,welding,inspection and other position is the key to the occupational disease hazard control,need to take comprehensive measures to control and reduce the impact on workers health.[key words] automobile parts manufacturing industry;Occupational-disease-inductive hazards;The prevention and control measures在汽车工业中,汽车零部件制造属于基础内容,按照性质可以将其分为发动机系统、制动系统、传动系统、电气系统、悬挂系统、内饰部件以及空调系统等[1]。
铸造专业英语词汇.
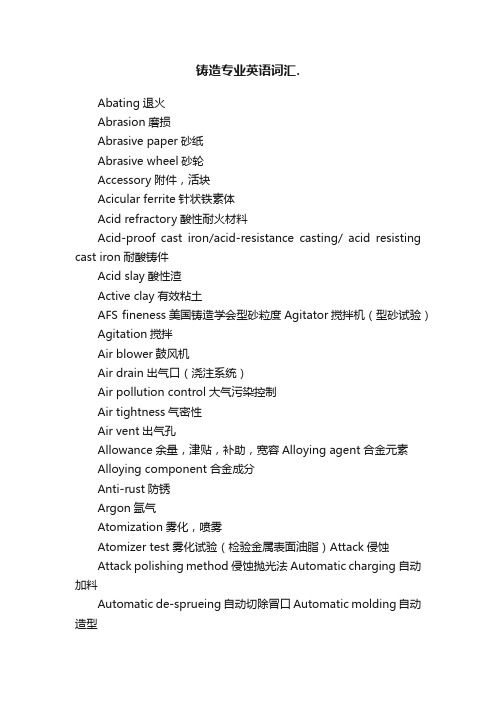
铸造专业英语词汇.Abating退火Abrasion磨损Abrasive paper砂纸Abrasive wheel砂轮Accessory附件,活块Acicular ferrite针状铁素体Acid refractory酸性耐火材料Acid-proof cast iron/acid-resistance casting/ acid resisting cast iron耐酸铸件Acid slay酸性渣Active clay有效粘土AFS fineness美国铸造学会型砂粒度Agitator搅拌机(型砂试验)Agitation搅拌Air blower鼓风机Air drain出气口(浇注系统)Air pollution control大气污染控制Air tightness气密性Air vent出气孔Allowance余量,津贴,补助,宽容Alloying agent合金元素Alloying component合金成分Anti-rust防锈Argon氩气Atomization雾化,喷雾Atomizer test雾化试验(检验金属表面油脂)Attack侵蚀Attack polishing method侵蚀抛光法Automatic charging自动加料Automatic de-sprueing自动切除冒口Automatic molding自动造型Automatic pouring device自动浇注装置Automatic sand plant 自动化砂处理装置Baked core干砂芯Balance天平/余额Ball feeder球状冒口Ball hardness布氏硬度Ball hardness testing machine布氏硬度机Ball mill球磨机Band/belt conveyer皮带输送机Band/belt elevator皮带斗式提升机Bar bend test试棒抗弯试验Base底,基础Base line基线Base plate底板Base sand原砂Basic碱性的,基本的Batch mill/batch sand mixer混砂机Beader pearlite珠光体Bed charge/coke底焦Belt grinder带式磨光机Bending strength抗弯强度Bentonite膨润土Binder粘结剂Bituminous coal dust/black dust煤粉Black short冷脆Black skin黑皮,铸皮Blank毛胚,下料Blast鼓风,送风Blast capacity风量Blast fan离心式鼓风机Blast hole风口Blast intensity鼓风强度Blast pressure gage风压表Blast regulator风量调节器Blast volume风量Bleed缺肉,台箱跑火Blender混砂机,搅拌机Blind feeder/head暗冒口Blind roaster马弗炉Blind scab起痂Blister皮下气泡Blow down停炉Boiling point沸点Bond粘结剂,合同Bond clay造型粘土Bond strength粘结强度Bottom door炉底们Bottom drop打炉Breaking-in带肉Brinell hardness布氏硬度Brittleness脆性Brittle fracture脆性断口,脆性断裂B type graphite B型石墨Buffing抛光Buffing machine抛光机Bunker料斗CE carbon equivalent碳当量Carbide碳化物carbon dioxide二氧化碳carbon monoxide一氧化碳carbon pick-up增碳carburetter增碳剂,汽化器case hardening表面硬化case gate内浇口casting alloy铸造合金casting defect/casting flaw铸造缺陷casting design铸造设计casting equipmentcasting ladle浇包casting lap铸造冷隔casting leakage铸造渗漏casting plan铸造方案casting property铸造性能casting rate浇注速度casting skin铸皮,黑皮casting strain铸造(内应力)变形casting stress铸造应力casting surface表皮casting technique铸造工艺/技术cast integral test bar单铸试棒caulk腻缝,抿灰Celsius thermometer摄氏温度计Cementite渗碳体,碳化铁Center gate中心浇口Center line中心线Chain hoist手动葫芦Charging加料Charger加料机Charging material炉料/批料Chilled cast iron冷铁Chill element促白口元素Chilling action激冷作用Chilling tendency白口倾向Chrysanthemum graphite菊花状石墨Cinder inclusion夹渣Cinder notch出渣口Clay washer洗砂机Clockwise rotation顺时针方向Clowhole/contraction cavity锁孔Cold box process冷芯盒制芯法Cold lap/cold shut冷隔Collapsibility/lubricate溃散性Consistency稠度,浓度,一致性Continuous desulfurization连续脱硫Contamination污染Conveyor belt输送带,传送带Cooling agent冷却剂Cooling curve冷却曲线Cooling effect冷却作用Cooling rate冷却速度Core砂芯Core box Coremaking制芯Coresetter下芯机Cover覆盖剂Cross gate横浇道Crush掉砂Cupola冲天炉Cupola drop打炉Cupola lining炉衬Cupola spout出铁槽Cut-off machine切割机Damper减震器Damping capacity/effect减震能力/效果Datum face/line基准面/线Deadhead冒口废料Deburring打毛刺Defect index废品率Deformation变形Density密度Degreaser脱脂剂Degree of graphitization石墨化程度Dimensional stability尺寸稳定性Descale除锈,除氧化皮Decaling除锈,除氧化皮Design drawing设计图Deslag扒渣Destructive testing/inspection破坏性试验/检验Desulfuration/desulphurization脱硫Desulfurizer脱硫剂Detection检查,摊伤Die cavity型腔,模腔Differential hardening/heating/quenching 局部硬化/加热/淬火Diffuse扩散Dilatant膨胀Dilute稀释,冲淡Dimensional error/tolerance尺寸误差/公差Direction l solidification顺序凝固,定向凝固Dirt/dirt inclusion夹渣Disintegration溃散,崩解,分解Disk feeder圆盘给料机Dislocation位错Displacement位移/置换Dissipation heat散热Distorted patter模变形Distortion变形,扭曲Divorced pearlite粒状珠光体Down runner/gate/downright直浇口Ductile iron球墨铸铁Duff煤粉Durability耐用性,耐久性Dust catcher集尘器elastic deformation弹性变形Elementary analysis元素分析Elevator提升机Elongation延伸率,延长Endurance耐用性,持久度Endurance limit疲劳极限Energy loss能量损失Environment contamination环境污染Environmental control 污染控制Equilibrium平衡Eutectic共晶体,恭晶的Examination performance/result考试成绩Fading衰退Failure stress破坏应力Feather毛刺,羽毛Feeding effect补缩效果Feeding gate内浇口Feed/feeder head(=riser)/feeding head冒口Ferric铁Ferric carbide渗碳体,碳化铁Ferrite铁素体Ferromanganese锰铁Ferromolybdenum钼铁Ferrosilicon硅铁Fettle铲除炉壁渣子File锉刀Filter paper/screen滤纸/网Fin毛刺Final machining精加工Fine silt粉尘Finished allowance加工余量Finished surface加工面Fire brick耐火砖Fire cracking热裂Fire resistance耐火性Fire waste烧损Fixture夹具Flake form片状Flake graphite片状石墨Flaking off(=spalling)剥落Flash point闪点Flaw detection探伤Floatation漂浮Flowability/fluidity流动性Flow-chart流程图Fluid contraction液态收缩Flushing流渣Fold冷隔Foreign substance杂质Forging锻造Forklift叉车Free carbide游离碳化物Free cementite游离渗碳体Free ferrite游离铁素体Freeting/fritting烧结Frictional coefficient摩擦系数Front slagging炉前出渣Galvanizing电镀Gas blow/hole气孔Gas blowhole气孔Gaseous diffusion气体扩散Gassy melt含气金属液Gas tightness气密性Gate area浇口面积Gating=gating system浇口,浇口系统Gating design浇口设计Gating proportion/ratio浇口比Gauge=gage表,计,规Globular cementite/pearlite粒状渗碳体/珠光体Grain-boundary segregation晶界偏析Grain fineness distribution粒度分布Graphite floatation石墨漂浮Graphitization 石墨化Green compression strength湿压强度Gray/grey cast iron灰铁Grinding打磨,磨制Grinding wheel砂轮Heat loss热损失Heat stress热应力Heat-treating/heat treatment热处理Heating effect热效应Heavy casting大型铸件/厚壁铸件Heavy-walled厚壁的Holding furnace保温炉Hot tear/pool热裂Hydraulic jack液压千斤顶Hydrogen氢Hyxagonal screen六角筛Impact hardness/toughness冲击硬度/韧性Impermeability气密性,不渗透性Impression压痕,型腔,凹腔Impurity杂质Included slag夹渣Indigeous graphite析出石墨Induction感应Inoculant孕育剂Inoculation fade孕育衰退Inside diameter内经Instantaneous ladle inoculation/stream inoculation瞬时浇包孕育Insulation绝缘,隔离Internal porosity内缩松Internal shrinkage内部缩孔Internal stress内应力Inverse chill反白口Inverted chill反白口Iron carbide渗碳体,碳化铁Iron-coke ratio铁焦比Jack千斤顶Jet test喷射试验(侧电镀层厚度)Job rate生产定额Knock-off head易割冒口Knockout落砂,出芯Knop钮,电钮Labile不稳定的Labor-intensive area强劳动(力)区Ladle浇包Lamellar pearlite/laminate pearlite片状珠光体Late inoculation/post inoculation二次孕育Laying out设计Leaker浇漏,漏铁水lift truck叉车Light casting小铸件,薄壁铸件Liquidus液相线Locating point/surface基准点/面Loss on ignition烧损Lower limit下限Luster光泽Machinability切削性能Machine allowance加工余量Machining机械加工Macrograph宏观Magnetic flaw detection磁力探伤Magnetic field磁场Magnetic-particle inspection磁粉探伤Magnetic powder inspection磁粉探伤Magnification放大倍数,放大倍率Manganese 锰Margin tolerance极限公差Mass production大量生产Matrix hardness机体硬度Mean diameter/stress平均直径/应力Mean value中间值Mechanical allowance加工余量Mechanical property机械性能Meltableness可溶性Melting溶解Melting capacity/condition/efficiency熔化率/状况/效率Melting point熔点Metal graphic microscope金相显微镜Metallic charge to coke ratio铁焦比Metallic pattern金属模Metallograph金相图片Metallographic examination金相检验Metallographic laboratory金相试验室Metallographic microscope金相显微镜Metallographic specimen金相磨片Metallurgy冶金学Metal material金属材料Microanalysis微量分析,显微分析Microlug球化率怀素测定试帮Micron微米Mismatch错模Misrun缺肉,浇不到Modulus of elongation延伸率Molding line造型线Natural gas天然气Nodularization球化Nodularizer球化剂Notch brittleness缺口脆性Off-dimension尺寸不合格(常指铸件)Off-gage尺寸不合格(常指型芯)Offset错位,偏置Operation life使用期限,寿命Outer inspection/visual inspection外观检验Outlet出口,排出口Oxidation氧化Oxide ferric氧化铁,三氧化二铁Partial hardening/local hardening局部淬火Parting face分型面,分模面Pattern plate模板Patter spray脱模液Pattern taper/patter draft拔模斜度Pearlite珠光体Permeability test透气性试验Phosphide磷共晶,磷化物Physical property物理性能Pig iron生铁Pin hole针孔Pitted skin麻面(铸造缺陷)Plastic binder树脂粘结剂Plastic deformation塑性变形Plate feeder圆盘给料机Plating电镀Polishing抛光Porous casting不致密铸件,多孔铸件Post inoculation二次孕育Premature freezing过早凝固Premium casting保质量逐件,优质逐件Preset program预定计划,预定程序表Pressure atmosphere大气压Pressure feeder加压冒口Production capacity生产能力Protective gloves劳保手套Prototype casting试生产铸件Push-off推出,顶出Quench aging淬火时效Radiator散热器,散热片,暖气片Radioactive element放射性元素Rare earth稀土Rare gas惰性气体Rat多肉Reamer铰刀Reclamation再生,回用Red brittleness=hot brittleness热脆性Reducibility还原能力Reduction in area断面收缩Refractoriness耐火性Refractory property耐久性能Regulator调节器Reinforcement加固Rejected casting不合格铸件Resin树脂Returns回炉料Reverse chill反白口Revolving table feeder圆盘给料机Rimhole皮下气泡Riser冒口Rockwell hardness洛氏硬度Rosette graphite菊花状石墨Roughing粗加工’Roughness粗糙度Rounding倒角Roust inhibitor防锈剂Runner gate横浇道Runner system浇注系统Running and feeding system浇冒口系统Rust prevention防锈Rustless steelSafety and industrial gloves劳动保护手套Safety factor安全系数Safety goggle护目镜Safety precaution安全措施Sample inspectionSampling取样Sand blister砂眼Sand blow气孔Sand buckle起皮、夹砂Sand burning粘砂Sand-conditioning system砂处理系统Sand control型砂控制Sand core砂芯Sand cut冲砂Sand defects型砂造成的(铸造)缺陷Sand drop掉砂Sand explosion砂眼Sand fineness砂子平均粒度Sand flowability型砂流动性Sand mill/sand mixer/sand mixing machine /sand muller混砂机Sand mold砂型Sand shakeout落砂Sand wash冲砂Scab铸痂Scar凹痕Semi-finished product半成品Sensitivity敏感性Separate cast test bar=cast integrate test bar单铸试棒Shakeout落砂/落砂机Shaking conveyer震动输送机Shift班次Short-run浇不满Short run casting浇不足铸件,缺肉铸件(未浇满)Shrink hole收缩、锁孔Shrinkage porosity缩松Shrinkage strain收缩变形Shrinkhead冒口Sintering烧结Size tolerance尺寸公差Slagging-off除渣/扒渣Solidification contraction/shrinkage凝固收缩Solid-liquid interface固液相交界面Solidus/solidus curve/solidus line固相线Solution concentration溶液浓度Sonic inspection听声检验Specific weight比重Spectroanalysis光谱分析Spherical graphite球状石墨Spheroidal iron=ductile iron球墨铸铁Spheroidization球化Spindle主轴Spotting point基准点Steam tight test/air tight test气密性试验Sticker/rat多肉Straightening校正Strength test强度试验Stress应力Stress relief应力消除Subskin blowhole/subsurface blow hole/ sub-surface blister 皮下气孔Superficial cementation表面渗碳Super heating过热Supersaturation过饱和Surface finish表面光洁度Surface folding冷隔Surface roughness表面粗糙度Swell胀砂Tap hole出渣口Telltale定位标记Tenacity/tensile strength抗拉强度/韧性Tensile testing machineTension-active element反球化元素、干扰元素Test bar试棒Test block试块Test piece试样Test specimen试样/试棒/试块Thermal balance热平衡Thermal conductivity导热系数,导热性Thermaldeformation/dilatometer/expansion/fatigue热变形/膨胀仪//膨胀/疲劳Tightness紧密度,致密度Tolerance公差Tooling point基准点Tuyere gate风眼Ultimate极限Upper limit上限Vacuum treatment真空处理Ventilating system/device/equipment通风系统/装置/设备Venting quality透气性Vibratory feeder震动给料机Vibratory shakeout machine=vibratory shakeout震动落砂机Visual examination/inspection外观检验Wash冲砂Washer洗砂机Wearability/wear resistance耐磨性Wrinkle皱皮Yield strength屈服强度Zero defect casting无缺陷铸件Zinc锌最新铸造标准应用手册(机械工业出版社)(铸造专业词汇)Foundry terminologyfoundry founding casting铸造foundry technology铸造工艺casting铸件sand casting process型砂铸造special casting process特种铸造fluidity流动性mold-filling capacity充型能力gas absorption吸气undercooling,supercooling过冷degree of undercooling过冷度nucleation成核homogeneous nucleation 自发成核heterogeneous nucleation非自发成核solidification range凝固温度范围directional solidification定向凝固solidification contraction凝固收缩liquid contraction液态收缩solid contraction 固态收缩solidification time凝固时间free contraction自由收缩hindered contraction受阻收缩shrinkage铸件线收缩率contraction stress收缩应力thermal stress热应力transformation stress相变应力casting stress铸造应力residual stress残留应力metallic raw material金属原物料pig iron生铁ferro-alloy铁合金foundry returns回炉料master alloy中间合金foundry coke铸造焦炭metallurgical coke冶金焦炭fixed carbon固定碳flux熔剂degassing flux除气熔剂covering flux覆盖熔剂refining flux精炼熔剂refractoriness耐火度firebrick耐火砖fireclay耐火黏土silica brick硅砖grain magnesite镁砂molding material造型材料sand砂washed-out sand水洗砂silica sand硅砂natural sand天然砂artificial sand人工砂naturally clay-bonded sand天然粘土砂olivine sand橄榄石砂chromite sand硌铁矿砂zircon sand锆砂carbon sand炭粒砂sharp sand精硅砂red sand红砂chamotte sand熟料砂binder粘结剂clay粘土inorganic binder无机粘结剂organic binder有机粘结剂kaolin高岭土bentonite膨润土sodium bentonite钠基膨润土calcium bentonite钙基膨润土activated bentonite活化膨润土drying oil干性油no bake binder自硬粘结剂(冷硬粘结剂)thermosetting resinbinder热固树脂粘结剂oil based binder油类粘结剂water glass binder,sodium silicate binder水玻璃粘结剂lignin liquor纸浆残液synthetic fat binder合脂粘结剂水玻璃模数sodium silicate modulus附加物additives发热剂exothermic mixture分型剂(脱模剂)parting agent;stripping agent 固化剂(硬化剂)hardener悬浮剂suspending agent涂料coating 型砂制备(砂处理)sand preparation混砂sand mixing;sand mulling型砂(造型混合料)molding sand芯砂(造芯混合料)core sand合成砂synthetic sand自硬砂self-hardening sand水玻璃砂sodium silicate-bonded sand覆模砂precoated sand烂砂泥(麻泥)loam调匀砂temper sand面砂facing sand背砂(填充砂)backing sand单一砂unit sand含泥量clay content含水量(水分,湿度)moisture content 旧砂floor sand枯砂(焦砂)burnt sand废砂waste sand热砂hot sand松砂aeration,sand-cutting筛分(筛析)screen analysis旧砂处理sand reconditioning旧砂再生sand reclamation沉降分选elutriation,decantation型砂试验sand testing透气性permeability流动性flowability型砂强度sand strength湿强度green strength干强度dry strength耐用性(复用性)durability砂型(芯)硬度mold hardness热变形hot deformation残留强度retained strength热强度hot strength韧性toughness发气率(发气速度)gas evolution rate发气性(发气量)gas evolution吸湿性moisture absorption落砂性knock-out capability溃散性collapsibility胶质价colloid index破碎指数shatter index热气流烘砂装置hot pneumatic tube drier 混砂机sand muller,sand mixer松砂机aerator,sand cutter冷却提升机cooling elevator,coolevator 筛砂机riddle磁力滚筒magnetic separator旧砂再生设备sand reclamation气力输送装置pneumatic tube conveyor铸铁cast iron铸铁石墨形态morphology of graphite in cast iron灰铸铁(灰口铸铁)gray cast iron白口铸铁white cast iron麻口铸铁mottled cast iron共晶度degree of saturation碳当量carbon equivalent片状石墨flake graphite初生石墨primary graphite孕育铸铁inoculated cast iron球墨铸铁spheroidal graphite cast iron,nodular graphite iron,ductile iron球状石墨spheroidal graphite,nodular graphite 可锻铸铁(马铁)malleable cast iron黑心可锻铸铁black heart malleable cast iron珠光体可锻铸铁pearlitic malleable cast iron铁素体可锻铸铁ferritic malleable cast iron白心可锻铸铁white heart malleable cast iron团絮石墨tempered graphite冷硬铸铁(激冷铸铁)chilled iron耐磨铸铁wear resisting cast iron耐热铸铁heat resisting cast iron耐酸铸铁acid resisting cast iron高硅铸铁high silicon cast iron蠕墨铸铁vermicular cast iron,compacted graphite cast iron 蠕虫状石墨vermicular graphite合金铸铁alloy cast iron铸钢cast steel碳素铸钢carbon cast steel低合金铸钢low alloy cast steel高锰钢high manganese steel铁素体钢ferritic steel青铜bronze铅青铜lead bronze铝青铜aluminum bronze黄铜brass铝铜合金aluminum-copper alloy铝镁合金aluminum-magnesium alloy铝硅合金aluminum-silicon alloy镁合金magnesium alloy轴承合金(减摩合金)bearing metal,antifrictional metal巴氏合金Babbitt metal 钛合金titanium alloy熔化(熔炼)melting重熔remelting炉料charge熔化率melting rate炉料计算charge calculation双联熔炼duplexing元素烧损(元素烧损率)melting losses of various chemical elements熔炼损耗(烧损)total melting loss还原气氛reducing atmosphere氧化气氛oxidizing atmosphere惰性气体inert gas碱度index of basicity碱性渣basic slag酸性渣acid slag精炼refining遗传性heredity风口比tuyere ratio有效高度effective height送风强度blast intensity预热送风hot blast底焦coke bed层焦coke split隔焦buffer coke charge炉衬furnace lining碱性炉衬acid lining棚料bridging熔池bath吸碳carbon pick-up焦铁比iron coke ratio出渣deslagging打炉cupoladrop氧化熔炼法oxidizing melting 不氧化熔炼法dead melting 真空熔炼vacuum refining熔渣slag沉渣sludge浮渣dross,cinder氧化期oxidizing stage还原期blocking stage还原渣reducing slag氧化渣oxidizing slag白渣white slag脱氧deoxidation扒渣slagging-off脱碳decarburization脱硫desulphurization脱磷dephosphorization增碳recarburizing脱氧剂deoxidizer挥发损耗volatilizing losses静置stewing,holding吹氮nitrogen flushing冲天炉cupola水冷冲天炉water-cooled cupola热风冲天炉hot blast cupola湿法除尘器wet cap炉缸cupola well前炉forehearth冲天炉加料机cupola charging machine爬式加料机ship hoist电磁配料称electro-magnetic weighing balancer 电磁盘electromagnetic chuck电弧炉direct arc furnace感应电炉electric induction furnace电渣炉electroslag furnace电磁搅拌electromagnetic agitation浇包ladle摇包shaking ladle底浇包bottom pouring ladle保温炉holding furnace坩呙炉crucible furnace孕育inoculation多孔塞法porous plug process变质modification墨化剂graphitizer过热superheating石墨球化处理nodularizing treatment of graphite碳当量仪eutectometer三角试块wdge test-piece真空除气vacuumdegassing浇注pouring 保护气氛浇注pouring under controlled atmosphere浇注速度pouring rate浇注温度pouring temperature浇注时间pouring time浇注位置pouring position型内孕育inmold inoculation压铁weight点冒口teeming捣冒口pumping补炉patching炉龄campaign铸造工艺设计mold design铸造工艺装备设计foundry tools design铸造工艺图foundry molding drawing铸件图drawing of rough casting起模斜度pattern draft收缩余量shrinkage allowance工艺补正量molding allowance加工余量machining allowance吃砂量mo9ld thickness补贴pad分型负数joint allowance铸件尺寸公差dimensional allowance of casting 铸件重量公差weight allowance of casting铸件加工基准面reference face for machining of casting铸件表面粗糙度surface roughness of casting浇注系统(浇口)gating system,running system 封闭式浇注系统chocked running system,pressurized gating system 半封闭式浇注系统enlarged runner system开放式浇注系统unchecked running system,non-pressurized gating system浇口盆(外浇口)pouring basin浇口杯pouring cup浇口塞blanking-off plug直浇道sprue直浇道窝sprue base横浇道runner筛网芯(滤网芯)strainer core内浇道ingate离心集渣浇注系统whirl gate,dirt trap system 顶注式浇注系统top gating system底注式浇注系统bottom gating system阶梯式浇注系统step gating system雨淋浇口shower gate缝隙浇口slot gate压边浇口lip runner,kiss runner牛角式浇口horn gate热结hot spot冒口riser,feeder head冒口效率riser efficiency明冒口open riser暗冒口bland riser侧冒口(边冒口)side riser压力冒口pressure riser大气压力冒口atmospheric riser发气压力冒口(气弹冒口)gas-delivered pressure riser 透气砂芯pencil core冒口径riser neck冒口根riser pad保温冒口套heat insulating feeder sleeve发热冒口套exorhermic feeder sleeve补缩距离feeding distance,feeding zone易割冒口knock-off head易割片(易割芯片)washburn core铸造工艺装备foundry tools and equipment模样(铸模、模)pattern母模master金属模metal pattern骨架模skeleton pattern石膏模plaster pattern塑料模plaslicn pattern整体模one-piece pattern分开模parted pattern,split pattern活块loose piece模板pattern plate模底板pattern mounting plate单面模板single face pattern plate双面模板match plate放样(伸图)hot dimensional drawing缩尺(模样工缩尺)shrinkage rule,pattern-maker’srule芯盒core box脱落式芯盒troughed core box下芯量具core setting scale 下芯夹具core jig烘芯板core dryingplate砂箱flask,molding box箱带(箱挡)flask bar,cross bar脱箱snap flask套箱mold jacket套销hollow pin,stubpin造型molding型腔mold cavity7.1.3铸型mold砂型sand mold上箱cope,top part下箱drag,bottom part手工造型hand molding机器造型machine molding自动化造型automatic molding分型面mold joint有箱造型flask molding两箱造型two-part molding三箱造型three-part molding不平分型面stepped joint无箱造型flaskless molding脱箱造型removable flask molding地坑造型pit molding刮板造型sweep molding抛砂造型impeller ramming组芯造型core assembly molding假箱造型oddside molding微振压造型vibratory squeezing molding 高压造型high pressure molding湿砂型green sand mold干砂型dry sand mold砂型烘干mold drying干砂型(干型)dry sand mold表面烘干型skin dried mold烂砂泥型loam mold砂床bed过渡角transition angle吊砂cod砂钩lifter负亚造型vacuum molding液态砂造型fluid sand molding漏砂pattern stripping 填砂molding-filling 紧实ramming 震实jolt ramming压实squeezing ramming 紧实度degree of ramming 二氧化碳法造型2CO process自硬砂造型self-hardening sand molding 塞砂tucking 刮砂strike-off造型生产线molding line 刷水swabbing 扎出气孔venting排气道venting channel 修型patching冷铁densener ,chill 外冷铁surface densener 内冷铁internal densener 验型(验箱)trial closing合型(合箱、组型)mold assembling ,closing造芯(制芯)core making 芯(芯子)core芯骨core rod ,core scab 油砂芯oil sand core预制砂embeded core ,ram up core 芯头core print 芯座core print芯头斜度core print taper 芯头间隙core print clearance 壳芯shell core 烘芯core baking 通气蜡线vent wax冷芯盒法cold box process 热芯盒法hot box process 芯撑chaplethand tools of molding 压勺heart and spoon 提钩cleaner双头铜勺doubleended radius sleeker 镘刀trowel 造型机molding machine压实造型机squeezing molding machine震击台bumper振动台vibrating table微振压实造型机vibratory squeezer 震实造型机jolt molding machine高压造型机high pressure molding machine射压造型机shooting and squeezing molding machine多触头造型机equalizing piston squeezer 抛砂机sand slinger 起模机drawing machine 射芯机core shooter 击芯机core extruder铸型输送机mold conveyor 落砂shake-out 除芯decoring喷砂清理sand blasting 抛丸清理shot blasting 水力清砂hydraulic blast 水砂清砂hydraulic blast 清理cleaning 清砂cleaning火焰表面清理scarfing 清铲chipping化学清砂chemical cleaning 精整dressing and finishing 落砂机knock-out machine 抛丸清理机shot blast machine 清理滚筒tumbling barrel抛丸落砂清理设备shot blast reclaiming equipment悬挂式磨轮swing frame grinder 矫正coining焊补repair welding 参补impregnation 金属型铸造permanent mold casting 金属型metal mold 金属芯metal core覆砂金属型sand-lined metal mold 排气赛venting plug 排气槽air vent 龟裂heat checking金属型铸造机gravity die casting machine 压力铸造die-casting 压铸型die-casting die动型moving die定型fixed die合型力clamping force压室pressure chamber鹅颈管gooseneck分流器spreader顶杆ejector pin溢流槽overflow well压射冲头injection piston压射比压injection pressure压射速度injection speed保压时间dwell time真空压铸vacuum die casting冲氧压铸pore-free die casting双冲头压铸acurad die casting压铸机die casting machine冷室压铸机cold chamber die casting machine 热室压铸机hot chamber die casting machine 镶铸法insert process离心铸造true centrifugal casting半离心铸造semi-centrifugal casting离心浇注centrifugal pressure casting双金属离心铸造bimetal centrifugal casting 离心铸造机centrifugal casting machine失模铸造lost pattern casting熔模铸造fusible pattern molding压制熔模fusible pattern injection压型pattern die熔模fusible pattern盐模salt pattern蜡模wax-pattern模组pattern assembly熔模涂料slurry面层涂料investment precoat撒砂stuccoing脱蜡dewaxing培烧sintering壳型制造shell molding结壳时间investing time结壳温度investing temperature硬化温度curing temperature硬化时间curing time陶瓷型制造ceramic slurry灌浆paste pouring喷烧torch firing低压铸造low-pressure diecasting 充型压力mold filling pressure保压压力dwell pressure升液管stalk真空吸铸suction casting差压铸造counter-pressure casting实型铸造full mold process泡沫塑料模Styrofoam pattern磁型铸造magnetic shot molding process凝壳铸造slush casting石膏型造型plaster molding连续铸造continuouscasting铸件检验inspection of casting铸件质量分析quality analysis of casting铸件外观质量visual quality of casting铸件内在质量internal quality of casting铸件使用性能service ability of casting单铸试块separated test bar of casting附铸试块test lug缺陷铸件defective casting废品reject无损检验(无损探伤)nondestructive inspection 破坏性试验destructivetesting飞翅(飞边)joint flash毛刺veining抬型(抬箱)cope raise,raised mold胀砂swell冲砂erosion,cut,wash掉砂drop,crush外渗物(外渗豆)sweat气孔blowhole针孔pinhole缩孔shrinkage缩松dispersed shrinkage疏松(显微缩松)porosity,microshrinkage冷裂cold cracking热裂hot tearing热处理裂纹heat treatment crack白点(发裂)flake冷隔cold shut,cold lap浇注断流interrupted pour鼠尾rat-tail沟槽buckle夹砂结疤(夹砂)scab机械粘砂(渗透粘砂)metal penetration 化学粘砂(烧结粘砂)burn-on表面粗糙rough surface皱皮elephant skin缩陷depression浇不到misrun未浇满poured short跑火run-out,bleeding型漏(漏箱)run-out,bleeding损伤(机械损伤)damage拉长exaggeration of dimension超重over-weight变形distortion,warping错型(错箱)shift错芯core shift偏芯(漂芯)core raised,corelift夹杂物inclusion冷豆cold shot内渗物(内渗豆)internal sweat渣气孔scum,slag-blow hole砂眼sand inclusion亮皮pearlite layer菜花头cauli-flowering石墨漂浮carbon flotation石墨集结kish graphite spot组织粗大open grain structure偏析segregation硬点hard spot反白口inverse chill球化不良under-nodularizing球化衰退degradated spheroidisation 脱碳decarburization。
球墨铸铁常见金相缺陷概述
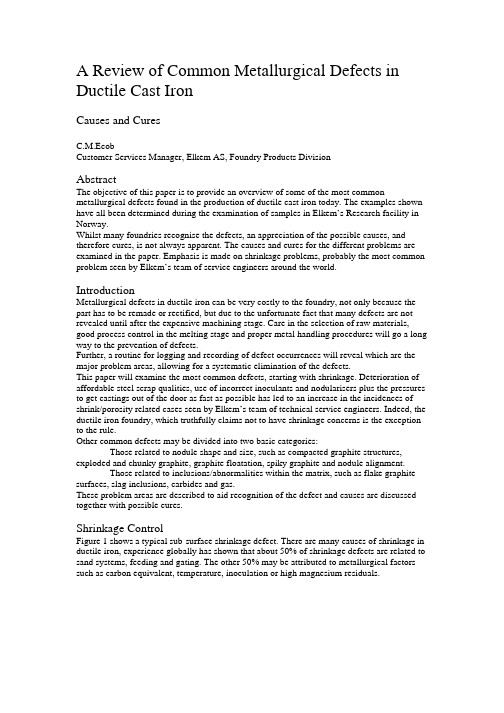
A Review of Common Metallurgical Defects in Ductile Cast IronCauses and CuresC.M.EcobCustomer Services Manager, Elkem AS, Foundry Products DivisionAbstractThe objective of this paper is to provide an overview of some of the most common metallurgical defects found in the production of ductile cast iron today. The examples shown have all been determined during the examination of samples in Elkem’s Research facility in Norway.Whilst many foundries recognise the defects, an appreciation of the possible causes, and therefore cures, is not always apparent. The causes and cures for the different problems are examined in the paper. Emphasis is made on shrinkage problems, probably the most common problem seen by Elkem’s team of service engineers around the world.IntroductionMetallurgical defects in ductile iron can be very costly to the foundry, not only because the part has to be remade or rectified, but due to the unfortunate fact that many defects are not revealed until after the expensive machining stage. Care in the selection of raw materials, good process control in the melting stage and proper metal handling procedures will go a long way to the prevention of defects.Further, a routine for logging and recording of defect occurrences will reveal which are the major problem areas, allowing for a systematic elimination of the defects.This paper will examine the most common defects, starting with shrinkage. Deterioration of affordable steel scrap qualities, use of incorrect inoculants and nodularisers plus the pressures to get castings out of the door as fast as possible has led to an increase in the incidences of shrink/porosity related cases seen by Elkem’s team of technical service engineers. Indeed, the ductile iron foundry, which truthfully claims not to have shrinkage concerns is the exception to the rule.Other common defects may be divided into two basic categories:-Those related to nodule shape and size, such as compacted graphite structures, exploded and chunky graphite, graphite floatation, spiky graphite and nodule alignment.-Those related to inclusions/abnormalities within the matrix, such as flake graphite surfaces, slag inclusions, carbides and gas.These problem areas are described to aid recognition of the defect and causes are discussed together with possible cures.Shrinkage ControlFigure 1 shows a typical sub-surface shrinkage defect. There are many causes of shrinkage in ductile iron, experience globally has shown that about 50% of shrinkage defects are related to sand systems, feeding and gating. The other 50% may be attributed to metallurgical factors such as carbon equivalent, temperature, inoculation or high magnesium residuals.Figure 1: Typical sub-surface shrinkage defect with dendrite arms partly covered with graphite sticking out.When a shrink or porosity is detected in a casting, there are several immediate and simple steps that can be taken to identify the cause of the problem. Firstly, the geometry of the casting should be examined to determine whether the location of the defect is close to a sharp radius or a potential hot spot. At the same time, the sand in the region of the shrink should be examined to look for any soft spots. Sand integrity accounts for a high proportion of shrinkage defects and a worn seal on the moulding machine, for example, resulting in a lower sand compaction can often be the cause of an unexplained sudden outbreak of shrinkage.The second avenue of investigation should be the gating / runner designs and the feeding of the casting. Whilst many foundries have computer aided design systems, patterns are often altered slightly over the years at shop floor level and can be significantly different from the original design. Also, changes to the feeder specification can lead to different burn characteristics and metal solidification patterns. This can affect the amounts of feed metal available to different parts of the casting.Metallurgically, there are many factors that can affect the shrinkage tendency. Figure 2 showsthe relationship between magnesium and shrinkage.Figure 2: Effect of magnesium content on shrinkageMagnesium, apart from being one of the most powerful carbide stabilisers, has a marked effect on the shrinkage tendency of ductile irons. Foundries operating at the higher end of the magnesium range, 0.05% or above, will find that the iron is more prone to shrink than foundries operating at lower, but very acceptable, levels, say 0.035-0.04%.Both under-inoculation and over-inoculation can cause shrinkage. In the case of under-inoculation, not enough dissolved carbon is precipitated as graphite. Graphite nodules have a far lower density than the matrix and to precipitate the low density, high volume graphite has an overall expansion effect, which helps to counter the natural tendency of the iron to shrink. With over-inoculation, too many nucleation points are active early in the solidification, resulting in an early expansion and sometimes large mould wall movements. Later in the solidification, when feeders become inactive and contraction takes place, there is no graphite coming out from solution to counteract the contraction and the result is shrinkage between the eutectic cells.In many foundries, the microstructure shows even sized nodules (accounting for the fact that the section cuts through nodules in 2-dimensions). Many foundrymen still consider this to be a good structure, even though the iron is prone to shrinkage. Nodularisers and specialist inoculants are available these days, which help to counter shrinkage by giving a skewed nodule distribution. These structures are shown in figure 3.Figure 3: The same base iron treated with two different nodularisers resulting in a) Skewed nodule distribution b) Unskewed nodule distributionA skewed nodule distribution indicates that some nodules are being created late in the solidification process and the drawing of graphite from solution at this stage is a very effective way to counter shrink. Most inoculants act almost instantaneously and this gives the even nodule size effect. Once the potency of the inoculant has gone, then there is no driver to create nodules late in the solidification and shrinkage can be the result. More recently, nodularisers have been developed by Elkem that have the same effect of producing the skewed and shrink reducing nodule distribution curve.A low carbon equivalent, or metal that has been held for some time at temperature, due to a mechanical breakdown, for example, is also prone to shrinkage. In these cases, the inherent nuclei within the melt will be low and some preconditioning may be necessary to achieve a good level of nucleation.Compacted Graphite within the structure.Figure 4 shows a good example of compacted graphite in the structure. There are several causes of this, the most common being that the nodularisation process has partly failed. Incorrect weighing of the nodulariser or the use of the wrong nodulariser are possible reasons for the failure, although a long holding time in the ladle or excessive temperatures can be contributory factors.Figure 4: Sample with compacted graphite present in the matrix due to partly failed nodularisation process.Another cause of CG particles in the matrix is an incorrect sulphur level in the base iron. Many foundries melt both grey and ductile charges and segregation of returns is essential. During the nodularisation process, the first reactions that take place are a desulphurisation and deoxidation, these elements combining preferentially with the magnesium. The base sulphur level must be accounted for in the calculation of MgFeSi charge weight.A note of caution here with regard to the addition of the MgFeSi to the ladle or treatment vessel. To add the MgFeSi early to a hot ladle and then hold the ladle for several minutes until the moulding line calls for metal is bad practise as the alloy will be burning or oxidising in the bottom of the ladle during this time. Higher and more consistent recoveries can easily be achieved by adding the alloy just before tap from the furnace.Low Nodule CountAs the compacted graphite mentioned above may commonly be attributed to the nodulariser, then low nodule counts tend to be a function of the inoculant. Figure 5 shows a low count compared to the foundry’s normal practise. Avoiding long holding times in the furnace and prolonged pouring time post-inoculation will help to achieve consistent nodule counts, as will improving the responsiveness of the iron via preconditioning. The use of a specialist powerful inoculant will give the most consistent results.Figure 5: Two casting with the same metal treatment resulting in a) low nodule count due to long pouring time and b) normal nodule count with normal practise.Exploded graphiteFigure 6 shows exploded graphite within the structure. Characteristically, exploded graphite looks exactly as the name might suggest that the graphite has been blown apart.Most MgFeSi alloys contain some rare earth metals, cerium, lanthanum, neodymium, praesodimium etc and these are beneficial in that they neutralise the effects of some detrimental tramp elements such as lead, bismuth, antimony, titanium etc..Rare earth elements are also nodularisers and aid the effects of the magnesium. In excess, however, rare earths can cause exploded graphite. This is more especially when high purity charges are used which are low in tramp elements. Exploded graphite is normally found in thicker section castings with slow cooling rates or at very high carbon equivalent levels.Figure 6: Sample with exploded graphite present due to excess concentration of rare earth metals.Care should be taken when using induction melting as rare earths can be cumulative in the iron. They tend to have very high melting points and do not volatilise, although some will be oxidised and come out in the slag. This is important to note if a low/zero RE containing nodulariser is substitutes to eliminate the problem as it may take time to dilute the residual RE out of the system.Should exploded graphite occur, then examination of the rare earth sources should be made –normally the MgFeSi. Melting a virgin charge with steel scrap, pig iron and no returns will quickly show if the returns and/or the MgFeSi are the problem. Latin America and countries in the Far East tend to use high levels of rare earth in the nodulariser.Reductions in the carbon equivalent may help to reduce exploded graphite.Chunky graphiteThis is shown in Figure 7. The causes of chunky graphite are exactly the same as for exploded graphite with the addition that the defect is also found in thinner casting sections and is not as sensitive to the carbon equivalent as exploded graphite.Figure 7: Sample with chunky graphite present due to excess concentration of rare earth metals. Graphite floatationThis is caused when large, low density graphite nodules are formed during the solidification of thick section or otherwise slow cooling castings. The nodules, being of a lower density than the matrix, tend to float towards the surface of the casting and thus can have a negative effect on the mechanical properties (and surface finish) in that region.A reduction in the carbon equivalent will help to control this, as will a reduction in the pouring temperature or increasing the cooling rate of the casting by the use of chills. The inoculation system should also be examined, as it is likely that the large graphite nodules have been formed very early during the solidification process and an inoculant, which will generate more, smaller nodules, could be an advantage. An example of graphite floatation is shown in Figure 8.Figure 8: Sample with graphite floatation present due to high carbon equivalent.Nodule AlignmentFigure 9 shows a classic case of nodule alignment, not too many examples as clear as this have been seen coming through our laboratory. This is caused by large dendrites growing during the solidification with the nodules being precipitated between the dendrite arms. Thus the nodules appear to be aligned. Whilst not normally a serious problem, this can have detrimental effects on such properties as tensile strength or impact resistance.The normal causes are low carbon equivalent where not enough graphite is precipitated during the cooling, under inoculation or too high a pouring temperature.Figure 9: Sample with nodule alignment caused by large dendrites growing during the solidification with the nodules being precipitated between the dendrite arms.Spiky GraphiteThe occurrence of spiky graphite in ductile iron is rare provided that the nodulariser used contains a small amount of rare earths. Normally, the rare earth metals neutralise such elements as lead, bismuth, titanium and antimony, as discussed in the section on exploded graphite, however the use of a rare earth-free nodulariser where traces of the deleterious elements are present results in spiky graphite. This is most commonly found in converter iron where the separate additions of RE have been left out by human error.The effect of spiky graphite is a dramatic reduction in the mechanical properties of the iron, the spikes provide points of weakness in the structure. Figure 10 shows a typical example of spiky graphite. The only cure for this type of defect is the addition of rare earths with the nodulariser.Figure 10 Sample with spiky graphite present in the matrix due to too elevated level of Pb. Flake Graphite on the Casting SurfaceThis is commonly seen in foundries, however many ignore the flake graphite on the surface as it forms part of the machining allowance. The defect is illustrated in Figure 11 and clearly shows the thin layer of flake graphite adjacent to the mould. This is found mainly in greensand systems and is caused by a build up of sulphur in the sand, which reacts with the magnesium in the iron to form magnesium sulphides and effectively de-nodularise the iron.A higher Mg or Re in the nodulariser can overcome this, subject to shrinkage restrictions discussed earlier, but the most common remedy is to use an inoculant containing cerium. This has the effect of re-nodularising the iron locally.Figure 11 Sample with flake graphite on the surface of the casting due to high sulphur content in the moulding sand.CarbidesIn the production of ductile iron, it must be remembered that magnesium is one of the most powerful carbide promoters. Coupled with this, the violence of the magnesium reaction during the nodularisation process tends to destroy nuclei. For these reasons, inoculation requirements are heavier than for grey irons and under-inoculation or the use of the wrong inoculant are amongst the most common causes of chill or carbides in ductile iron.Figure 12 shows typical carbides in a ductile iron structure. Poor inoculation is not the only cause of carbides, however, and all the potential reasons need to be explored to determine the reason behind carbide formation.Figure 12 Sample with carbide present in the matrix due to poor inoculationSteel scrap qualities have already been mentioned in this paper and increasing concentrations of carbide promoting elements, such as molybdenum, chromium, vanadium etc can lead to the promotion of carbides. These can be found particularly in the centre of castings or at grain boundaries, where the eutectic solidification front tends to concentrate the elements to the point where carbides form. Apart from steel scrap, use of molybdenum containing returns can be a source of undesirable carbide promoting materials.Low carbon equivalent and high pouring temperatures may also promote carbides, particularly in thin section castings.The cures for carbide problems usually revolve around the use of a more powerful proprietary inoculant, although nodularisers have been developed which have lower carbide promoting properties.SummaryThis paper has reviewed the most common metallurgical defects in ductile iron production. Extraneous effects, such as slag and gas have had to be omitted due to space constraints, but the elimination of these could form a paper on their own.As shrinkage is the most prevalent problem in most ductile foundries, then focus has been made on this.Systematic recording of defects, whether found in post casting inspection or even in post foundry operations is essential to identify the most common and the most costly problem areas. These can then be addressed in order of importance.。