Deep Hydrodesulfurization over Ni-Mo Catalysts Supported on the Mixed Molecular Sieves
参考文献
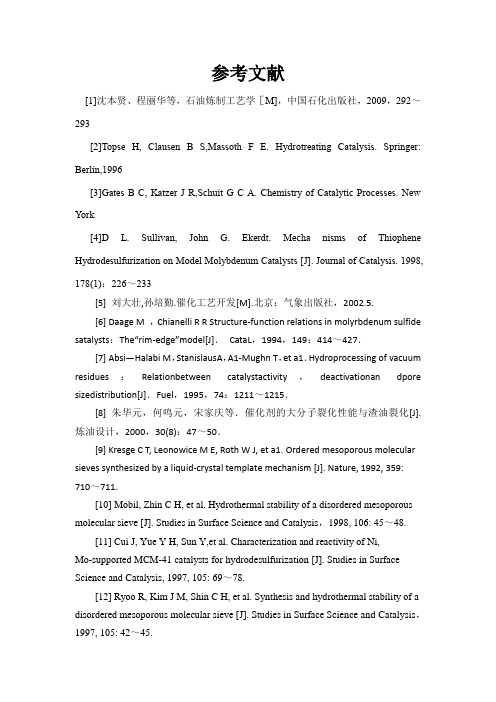
参考文献[1]沈本贤、程丽华等,石油炼制工艺学[M],中国石化出版社,2009,292~293[2]Topse H, Clausen B S,Massoth F E. Hydrotreating Catalysis. Springer: Berlin,1996[3]Gates B C, Katzer J R,Schuit G C A. Chemistry of Catalytic Processes. New York[4]D L. Sullivan, John G. Ekerdt. Mecha nisms of Thiophene Hydrodesulfurization on Model Molybdenum Catalysts [J]. Journal of Catalysis. 1998, 178(1):226~233[5] 刘大壮,孙培勤.催化工艺开发[M].北京:气象出版社,2002.5.[6]Daage M ,Chianelli R R Structure-function relations in molyrbdenum sulfide satalysts:The“rim-edg e”model[J].CataL,1994,149:414~427.[7] Absi—Halabi M,StanislausA,A1-Mughn T,et a1.Hydroprocessing of vacuum residues:Relationbetween catalystactivity,deactivationan dpore sizedistribution[J].Fuel,1995,74:1211~1215.[8] 朱华元,何鸣元,宋家庆等.催化剂的大分子裂化性能与渣油裂化[J].炼油设计,2000,30(8):47~50.[9] Kresge C T, Leonowice M E, Roth W J, et a1. Orderedmesoporous molecular sieves synthesized by a liquid-crystaltemplate mechanism[J]. Nature, 1992, 359: 710~711.[10] Mobil, Zhin C H, et al. Hydrothermal stability of a disordered mesoporous molecular sieve [J]. Studies in Surface Science and Catalysis,1998, 106: 45~48.[11] Cui J, Yue Y H, Sun Y,et al. Characterization and reactivity of Ni,Mo-supported MCM-41 catalysts for hydrodesulfurization [J]. Studies in Surface Science and Catalysis, 1997, 105: 69~78.[12] Ryoo R, Kim J M, Shin C H, et al. Synthesis and hydrothermal stability of a disordered mesoporous molecular sieve [J]. Studies in Surface Science and Catalysis,1997, 105: 42~45.[13] Angelici R J.Theoretical study of ethanethiol adsorption on HZSM-5 zeolite[J].Polyhedron,1997,16(18):3073~3088.[14] 安高军,柳云骐,柴永明等.柴油加氢精制催化剂制备技术[J].化学进展, 2007,19(2/3):243~249.[15] Oyama S. T, Clark P, Teixeira da Silva V. L. S, Lede E. J, and Requejo F G..XAFS characteriza tion of highly active alumina-supported molybdenumphosphide[J].J. Phys.Chem. B, 2001,105 (1):4961~4966.[16]BejSK,MaltySK,TuragaU.Searchforaneficient4,6-DMDBThydrodesulfuriz-ationcatalyst:a review of recent studies[J].Energy Fuels,2004,l8:1227~1237.[17]Ramirez J,Cedeno L,Busca G.The role oftitania support in Mobased hydrodesulfurization catalysts[J].Cata1.1999,l84:59~67.[18] Malty S K,Ancheyta J,Soberanis L,et a1.Alum ina-titania binary mixed oxide used as support of catalysts for bydrotreating of Maya heavy crude[J].App1.CataL A,2003,244:141~153.[19] Breys M,AfanasievP,GeantetC,eta1.Deep desulfurization:Reactions,catalysts and technological challenges[J].CataL Today,2003,86:5~l6.[20] DharGM,SrinivasBN,RanaM S,et a1.Mixed oxide supported hydrodesulfurization catalysts:A review[J].Cata1.Today,2003,86:45~60.[21] 刘志红.提高柴油加氢精制催化剂活性的方法[J].化工进展2008,27(2):173~179.[22] M P Boreque, A L Apez-Agudo. Catalytic activities of Co(Ni)/TiO2-Al2O3 catalysts in gasoil and thiophene HDS and pyridine HDN:effect of the TiO2-Al2O3 composition[J]. Applied Catalysis,1999,180:53~54.[23] S Yoshinaka, K Segawa. Hydrodusulfurization of dibenzothiophenes over molybdenum catalyst supported on TiO2-Al2O3[J]. Catalysis Today, 1998,45:293~294[24] DharGM,SrinivasBN,RanaM S,et a1.Mixed oxide supported hydrodesul furization catalysts:A review[J].Cata1.Today,2003,86:45~60.[25] Damyanova S,Petrov L,Centeno M A,et a1.Characterization of molybdenum hydrod esulfurization catalysts suppo rted on ZrO2-Al2O3 and ZrO2-SiO2 carriers[J].AppL CataLA,2002,224:271~284.[26] 周亚松等.以TiO2-SiO2为载体的催化剂加氢脱硫性能研究[J].复旦学报(自然科学版),2003,42(3):387~391.[27]Dzwigaj S,Louis C,Breysse M,et a1.New Generation of Titanium DioxideSupport for Hydrodesulfurization[J].Applied Catalysis B ,2003,41:18l~191.[28] Escalona Emir, PereiraAlmaoPedro, CastilloJimmy, etal. Nanometric bimetallic sulfides prepared via thermal decomposition of Ni and Feheteropolymolybdate emulsions[J]. Catalysis Letters, 2006, 112(3-4): 227~230.[29] 王萍, 周志军, 田晓飞, 孙桂大. 负载型氮化钴钼催化剂的制备及催化性能[J]. 石油化工高等学校学报, 2003, 16(2):13~15.[30] HADA K, Tanabe J, Omi S, et al. Characterization of cobalt molybdenum nitrides for thiophene HDS by XRD、TEM and XPS [J]. Journal of Catalysis, 2002, 207(24): 10~22.[31] 李建伟, 李英霞, 陈标华, 等. Co-Mo/A1203催化剂上裂解汽油中单烯烃加氢宏观动力学[J]. 燃料化学学报, 2006, 34(2): 170~174.[32] Wang Yuhong, Li Wei, Zhang Minghui, Guan Naijia, etal. Characterization and catalytic properties of supported nickel molybdenum nitrides for hydrodenitrogenation[J]. Applied Catalysis A, 2001, 215(1-2): 39~45.[33] 柳云骐, 刘晨光, 阙国和. 二苯并噻吩在CoMoN x催化剂上的加氢脱硫[J]. 催化学报, 2000, 21(4): 337~340.[34] 李庆杰, 赵志芳, 李凤艳, 等. 负载型磷化钼加氢精制催化剂的制备研究[J]. 燃料化学学报, 2006, 34 (1): 126~128.[35] 左东华, 谢玉萍, 聂红, 等. 4,6-二甲基二苯并噻吩加氢脱硫的反应机理研究[J]. 催化学报, 2002, 23(3): 271~275.[36] 刘武灿, 何兴娇, 卢春山. 金属氮化物/碳化物催化加氢性能研究进展[J]. 工业催化, 2005, 13(3): 1~5.[37] 李凤艳, 孙桂大, 赵天波, 等. 含磷加氢处理催化剂[J]. 石油化工高等学校学报, 2002, 15(2): l~5.[38] Escalona Emir, PereiraAlmaoPedro, CastilloJimmy, etal. Nanometric bimetallic sulfides prepared via thermal decomposition of Ni and Fe heteropolymolybdate emulsions[J]. Catalysis Letters, 2006, 112(3-4): 227~230.[39] Hubaut Robert. Characterization and hydrodesufurization activities of mixed Fe-Mo sulfides supported on alumina and carbon [J]. Fuel, 2007, 86(5-6): 743~749.[40] Levy R B, Boudart M. Platinum-like Behavior of Tungsten Carbide in Surface Catalysis [M]. Science, 1973, 181: 547~549.[41] Aegerter P A, Quigley W W C, Simpson G J, et al. Thiophene Hydrodesulfurization Over Alumina-Supported Molybdenum Carbide and NitrideCatalysts: Adsorption Sites, Catalytic Activities, and Nature of the Active Surface [J]. Journal ofCatalysis,1996, 164(1): 109~121.[42] Sajkowski D J, Oyama S T. Catalytic Hydrotreatment of Illinois No. 6Coal-Derived Naphtha: The Removal of Individual Nitrogen and Sulfur Compound. Applied Catalysis A, 1996, 134: 339~349.[43] 张耀军, 李新生. 催化新材料γ-Mo2N的合成和表征[J].分子催化, 1996,10(2):103~108.[44] 丁正新, 盛世善.碳化钼催化剂的XPS研究[J].化学物理学报,1997,10(3):235~240.[45] 王新平, 张文郁.Mo2N的表面性质加氢脱氮活性[J].物理化学学报,1996,12(6):513~517[46] 周振华, 张辉军.Mo2N催化剂的加氢脱硫活性[J].石油化工,1996,25(10):689~692[47] 杨树武, 纪纯新.催化剂上及H2和NO吸附性能的TDP-MS研究[J].物理化学学报[J],1996,12(12):1084~1089.[48] 王远强, 陈思浩. Ni P/Ti02的制备、表征及其加氢脱硫反应性能[J].上海化工, 2006, 31(11): 10~12.[49] 鄢景森, 王安杰, 李翔, 等. 负载型磷化钼的原位还原制备及其加氢脱硫反应活性[J]. 石油学报(石油加工), 2006, 22(1): 15~21.[50] 李翠清, 王洪学, 李成岳, 等. 噻吩在不同负载磷化钨催化剂上的加氢脱硫[J]. 分子催化, 2O04, 18(1): 15~l8.[51] Yasuhiro Iwama,Nobuyuki Ichikuni, Kyoko Bando. Effect of Co addition for carburizing process of Ti-oxide/SiO2 into TiC/SiO2[J]. Applied Catalysis, A: General, 2007, 323: 104~109.[52] Vit Zdenek. Iridium sulfide and Ir promoted Mo based catalysts[J]. Applied Catalysis A: General, 2007, 322: 142~151.[53] Leyva Carolina, Jorge Ancheyta, Mohan SRana, et al. A comparative study on the effect of promoter content of hydrodesulfurization catalysts at different evaluation scales[J]. Fuel, 2007, 86(9): 1232~1239.。
节流脱重烃工艺在膜脱碳系统中的应用
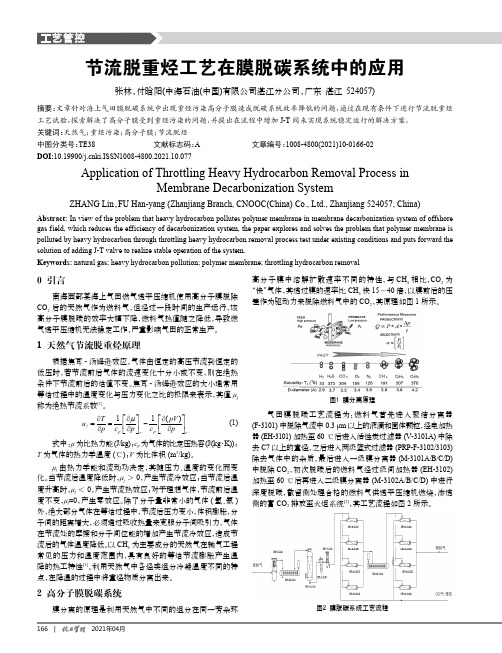
高分子膜中溶解扩散速率不同的特性,与CH 4相比,CO 2为“快”气体,其透过膜的速率比CH 4快15~40倍,以膜前后的压差作为驱动力来脱除燃料气中的CO 2,其原理如图1所示。
图1 膜分离原理气田膜脱碳工艺流程为:燃料气首先进入聚结分离器(F-3101)中脱除气流中0.3 μm 以上的液滴和固体颗粒,经电加热器(EH-3101)加热至60 ℃后进入活性炭过滤器(V-3101A)中除去C7以上的重烃,之后进入两级篮式过滤器(PRP-F-3102/3103)除去气体中的杂质,最后进入一级膜分离器(M-3101A/B/C/D)中脱除CO 2,初次脱碳后的燃料气经过级间加热器(EH-3102)加热至60 ℃后再进入二级膜分离器(M-3102A/B/C/D)中进行深度脱碳,截留侧处理合格的燃料气供透平压缩机燃烧,渗透侧的富CO 2排放至火炬系统[2],其工艺流程如图2所示。
图2 膜脱碳系统工艺流程0 引言南海西部某海上气田燃气透平压缩机使用高分子膜脱除CO 2后的天然气作为燃料气,但经过一段时间的生产运行,该高分子膜脱碳的效率大幅下降,燃料气热值随之降低,导致燃气透平压缩机无法稳定工作,严重影响气田的正常生产。
1 天然气节流脱重烃原理根据焦耳-汤姆逊效应,气体由恒定的高压节流到恒定的低压时,若节流前后气体的流速变化十分小或不变,则在绝热条件下节流前后的焓值不变。
焦耳-汤姆逊效应的大小通常用等焓过程中的温度变化与压力变化之比的极限来表示,其值μj 称为绝热节流系数[1]。
11()j p p r rT pV u p c p c p µ ∂∂∂==− ∂∂∂ (1)式中:μ为比热力能(J/kg);c p 为气体的比定压热容(J/(kg ·K));T 为气体的热力学温度(℃);V 为比体积(m 3/kg)。
μj 由热力学能和流动功决定,其随压力、温度的变化而变化。
当节流后温度降低时,μj >0,产生节流冷效应;当节流后温度升高时,μj <0,产生节流热效应;对于理想气体,节流前后温度不变,μj =0,产生零效应。
氢等离子体法制备MoP加氢脱氮催化剂
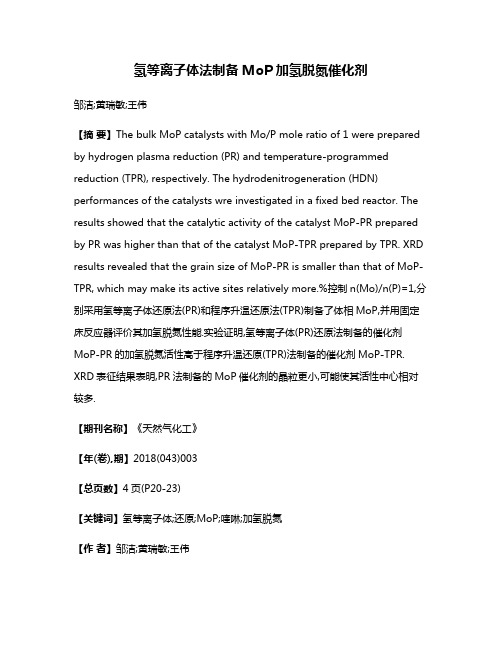
氢等离子体法制备MoP加氢脱氮催化剂邹洁;黄瑞敏;王伟【摘要】The bulk MoP catalysts with Mo/P mole ratio of 1 were prepared by hydrogen plasma reduction (PR) and temperature-programmed reduction (TPR), respectively. The hydrodenitrogeneration (HDN) performances of the catalysts wre investigated in a fixed bed reactor. The results showed that the catalytic activity of the catalyst MoP-PR prepared by PR was higher than that of the catalyst MoP-TPR prepared by TPR. XRD results revealed that the grain size of MoP-PR is smaller than that of MoP-TPR, which may make its active sites relatively more.%控制n(Mo)/n(P)=1,分别采用氢等离子体还原法(PR)和程序升温还原法(TPR)制备了体相MoP,并用固定床反应器评价其加氢脱氮性能.实验证明,氢等离子体(PR)还原法制备的催化剂MoP-PR的加氢脱氮活性高于程序升温还原(TPR)法制备的催化剂MoP-TPR. XRD表征结果表明,PR法制备的MoP催化剂的晶粒更小,可能使其活性中心相对较多.【期刊名称】《天然气化工》【年(卷),期】2018(043)003【总页数】4页(P20-23)【关键词】氢等离子体;还原;MoP;喹啉;加氢脱氮【作者】邹洁;黄瑞敏;王伟【作者单位】银川能源学院,宁夏银川 750105;银川能源学院,宁夏银川 750105;银川能源学院,宁夏银川 750105【正文语种】中文【中图分类】O643.3;TE62;TQ426随着汽车拥有量的快速增加,汽车尾气排放带来的环境污染越来越严重。
超临界水氧化技术处理含油污泥

abstract
The oxidation of oily sludge in supercritical water is performed in a batch reactor at reaction temperatures between 663 and 723 K, the reaction times between 1 and 10 min and pressure between 23 and 27 MPa. Effect of reaction parameters such as reaction time, temperature, pressure, O2 excess and initial COD on oxidation of oily sludge is investigated. The results indicate that chemical oxygen demand (COD) removal rate of 92% can be reached in 10 min. COD removal rate increases as the reaction time, temperature and initial COD increase. Pressure and O2 excess have no remarkable affect on reaction. By taking into account the dependence of reaction rate on COD concentration, a global power-law rate expression was regressed from experimental data. The resulting pre-exponential factor was 8.99 × 1014 (mol L−1)−0.405 s−1; the activation energy was 213.13 ± 1.33 kJ/mol; and the reaction order for oily sludge (based on COD) is 1.405. It was concluded that supercritical water oxidation (SCWO) is a rapidly emerging oily sludge processing technology.
芳香杂环含硫化合物C-S键断裂方式
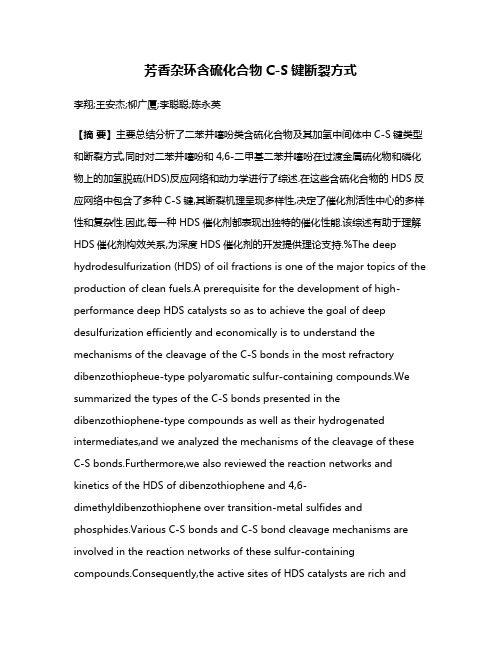
芳香杂环含硫化合物C-S键断裂方式李翔;王安杰;柳广厦;李聪聪;陈永英【摘要】主要总结分析了二苯并噻吩类含硫化合物及其加氢中间体中C-S键类型和断裂方式,同时对二苯并噻吩和4,6-二甲基二苯并噻吩在过渡金属硫化物和磷化物上的加氢脱硫(HDS)反应网络和动力学进行了综述.在这些含硫化合物的HDS反应网络中包含了多种C-S键,其断裂机理呈现多样性,决定了催化剂活性中心的多样性和复杂性.因此,每一种HDS催化剂都表现出独特的催化性能.该综述有助于理解HDS催化剂构效关系,为深度HDS催化剂的开发提供理论支持.%The deep hydrodesulfurization (HDS) of oil fractions is one of the major topics of the production of clean fuels.A prerequisite for the development of high-performance deep HDS catalysts so as to achieve the goal of deep desulfurization efficiently and economically is to understand the mechanisms of the cleavage of the C-S bonds in the most refractory dibenzothiopheue-type polyaromatic sulfur-containing compounds.We summarized the types of the C-S bonds presented in the dibenzothiophene-type compounds as well as their hydrogenated intermediates,and we analyzed the mechanisms of the cleavage of these C-S bonds.Furthermore,we also reviewed the reaction networks and kinetics of the HDS of dibenzothiophene and 4,6-dimethyldibenzothiophene over transition-metal sulfides and phosphides.Various C-S bonds and C-S bond cleavage mechanisms are involved in the reaction networks of these sulfur-containing compounds.Consequently,the active sites of HDS catalysts are rich andcomplex.Therefore,each HDS catalyst exhibits unique catalytic performance.This paper is helpful for the understanding of structure-performance relationships of HDS catalysts,and it also provides theoretical support for the development of deep HDS catalysts.【期刊名称】《石油学报(石油加工)》【年(卷),期】2017(033)006【总页数】14页(P1039-1052)【关键词】加氢脱硫;芳香杂环含硫化合物;C-S键;断裂;机理【作者】李翔;王安杰;柳广厦;李聪聪;陈永英【作者单位】大连理工大学精细化工国家重点实验室,辽宁大连116024;辽宁省高校石油化工技术与装备重点实验室,辽宁大连116024;大连理工大学精细化工国家重点实验室,辽宁大连116024;辽宁省高校石油化工技术与装备重点实验室,辽宁大连116024;大连西太平洋石油化工有限公司,辽宁大连116600;辽宁省高校石油化工技术与装备重点实验室,辽宁大连116024;大连理工大学精细化工国家重点实验室,辽宁大连116024【正文语种】中文【中图分类】TE624.9清洁油品的生产是解决我国日益严峻的环境污染问题的迫切需求,而深度脱硫则是清洁油品生产面临的一个重要课题。
乙酸蒸汽催化重整制氢的研究进展
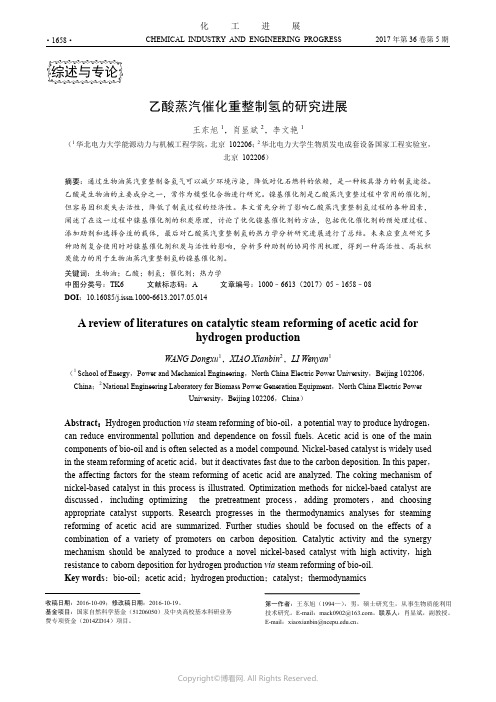
CHEMICAL INDUSTRY AND ENGINEERING PROGRESS 2017年第36卷第5期·1658·化 工 进展乙酸蒸汽催化重整制氢的研究进展王东旭1,肖显斌2,李文艳1(1华北电力大学能源动力与机械工程学院,北京 102206;2华北电力大学生物质发电成套设备国家工程实验室,北京 102206)摘要:通过生物油蒸汽重整制备氢气可以减少环境污染,降低对化石燃料的依赖,是一种极具潜力的制氢途径。
乙酸是生物油的主要成分之一,常作为模型化合物进行研究。
镍基催化剂是乙酸蒸汽重整过程中常用的催化剂,但容易因积炭失去活性,降低了制氢过程的经济性。
本文首先分析了影响乙酸蒸汽重整制氢过程的各种因素,阐述了在这一过程中镍基催化剂的积炭原理,讨论了优化镍基催化剂的方法,包括优化催化剂的预处理过程、添加助剂和选择合适的载体,最后对乙酸蒸汽重整制氢的热力学分析研究进展进行了总结。
未来应重点研究多种助剂复合使用时对镍基催化剂积炭与活性的影响,分析多种助剂的协同作用机理,得到一种高活性、高抗积炭能力的用于生物油蒸汽重整制氢的镍基催化剂。
关键词:生物油;乙酸;制氢;催化剂;热力学中图分类号:TK6 文献标志码:A 文章编号:1000–6613(2017)05–1658–08 DOI :10.16085/j.issn.1000-6613.2017.05.014A review of literatures on catalytic steam reforming of acetic acid forhydrogen productionWANG Dongxu 1,XIAO Xianbin 2,LI Wenyan 1(1 School of Energy ,Power and Mechanical Engineering ,North China Electric Power University ,Beijing 102206,China ;2 National Engineering Laboratory for Biomass Power Generation Equipment ,North China Electric PowerUniversity ,Beijing 102206,China )Abstract :Hydrogen production via steam reforming of bio-oil ,a potential way to produce hydrogen , can reduce environmental pollution and dependence on fossil fuels. Acetic acid is one of the main components of bio-oil and is often selected as a model compound. Nickel-based catalyst is widely used in the steam reforming of acetic acid ,but it deactivates fast due to the carbon deposition. In this paper ,the affecting factors for the steam reforming of acetic acid are analyzed. The coking mechanism of nickel-based catalyst in this process is illustrated. Optimization methods for nickel-baed catalyst are discussed ,including optimizing the pretreatment process ,adding promoters ,and choosing appropriate catalyst supports. Research progresses in the thermodynamics analyses for steaming reforming of acetic acid are summarized. Further studies should be focused on the effects of a combination of a variety of promoters on carbon deposition. Catalytic activity and the synergy mechanism should be analyzed to produce a novel nickel-based catalyst with high activity ,high resistance to caborn deposition for hydrogen production via steam reforming of bio-oil. Key words :bio-oil ;acetic acid ;hydrogen production ;catalyst ;thermodynamics第一作者:王东旭(1994—),男,硕士研究生,从事生物质能利用技术研究。
柴油深度加氢脱硫反应的主要影响因素研究
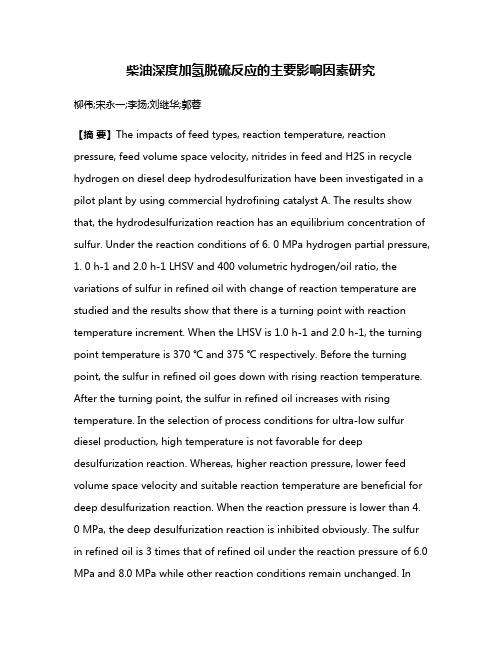
柴油深度加氢脱硫反应的主要影响因素研究柳伟;宋永一;李扬;刘继华;郭蓉【摘要】The impacts of feed types, reaction temperature, reaction pressure, feed volume space velocity, nitrides in feed and H2S in recycle hydrogen on diesel deep hydrodesulfurization have been investigated in a pilot plant by using commercial hydrofining catalyst A. The results show that, the hydrodesulfurization reaction has an equilibrium concentration of sulfur. Under the reaction conditions of 6. 0 MPa hydrogen partial pressure, 1. 0 h-1 and 2.0 h-1 LHSV and 400 volumetric hydrogen/oil ratio, the variations of sulfur in refined oil with change of reaction temperature are studied and the results show that there is a turning point with reaction temperature increment. When the LHSV is 1.0 h-1 and 2.0 h-1, the turning p oint temperature is 370 ℃ and 375 ℃ respectively. Before the turning point, the sulfur in refined oil goes down with rising reaction temperature. After the turning point, the sulfur in refined oil increases with rising temperature. In the selection of process conditions for ultra-low sulfur diesel production, high temperature is not favorable for deep desulfurization reaction. Whereas, higher reaction pressure, lower feed volume space velocity and suitable reaction temperature are beneficial for deep desulfurization reaction. When the reaction pressure is lower than 4.0 MPa, the deep desulfurization reaction is inhibited obviously. The sulfur in refined oil is 3 times that of refined oil under the reaction pressure of 6.0 MPa and 8.0 MPa while other reaction conditions remain unchanged. Inaddition, nitrides in feed and H2S in recycle hydrogen are detrimental to hydrodesulfurization reaction and has strong inhibition on hydrodesulfurization.%采用中国石油化工股份有限公司抚顺石油化工研究院已工业化应用的加氢精制催化剂A,在中型试验装置上考察了原料油种类、反应温度、反应压力、体积空速等对深度脱硫反应过程的影响,加氢脱硫反应存在平衡硫浓度,在氢分压6.0 MPa、体积空速1.0,2.0 h-1、氢油体积比400的反应条件下,考察了不同反应温度下常三线+催化裂化混合柴油的加氢脱硫情况,发现在体积空速为1.0,2.0h-1时,生成油硫含量-反应温度变化曲线分别在370℃和375℃下出现拐点,拐点之前生成油硫含量随着反应温度的提高而降低,进一步提高反应温度,产品硫含量有所提高.在生产超低硫柴油工艺条件选择上,过高的温度不利于超深度脱硫反应的进行,而较高的反应压力和较低的体积空速以及适宜的反应温度有利于反应进行.研究表明,其他反应条件不变,当反应压力低于4.0 MPa时,深度脱硫反应效果明显下降,生成油硫含量是反应压力为6.0,8.0 MPa时的3倍以上.此外,循环氢中的硫化氢以及原料中的氮化物对脱硫反应有显著的抑制作用,是深度脱硫反应的毒物.【期刊名称】《炼油技术与工程》【年(卷),期】2012(042)011【总页数】4页(P10-13)【关键词】柴油;加氢;深度脱硫;硫化氢;氮化物【作者】柳伟;宋永一;李扬;刘继华;郭蓉【作者单位】中国石油化工股份有限公司抚顺石油化工研究院,辽宁省抚顺市113001;中国石油化工股份有限公司抚顺石油化工研究院,辽宁省抚顺市113001;中国石油化工股份有限公司抚顺石油化工研究院,辽宁省抚顺市113001;中国石油化工股份有限公司抚顺石油化工研究院,辽宁省抚顺市113001;中国石油化工股份有限公司抚顺石油化工研究院,辽宁省抚顺市113001【正文语种】中文随着环保法规的日趋严格,柴油低硫化成为世界各国和地区柴油新规格的发展趋势。
219525878_超声辅助低共熔溶剂提取红松树皮原花青素及动力学研究
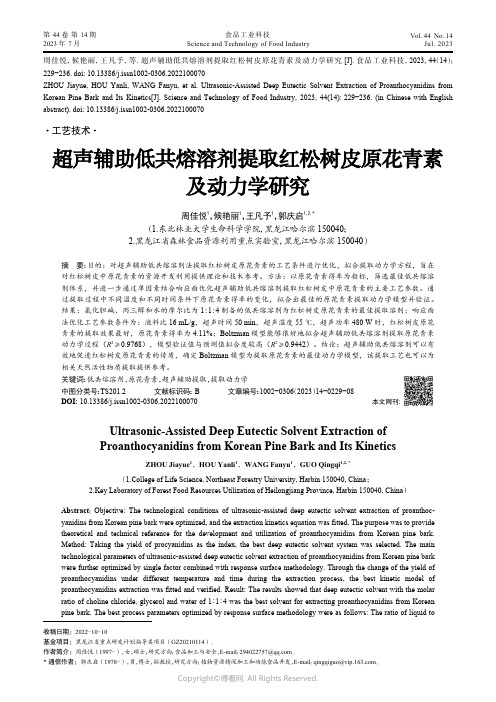
周佳悦,候艳丽,王凡予,等. 超声辅助低共熔溶剂提取红松树皮原花青素及动力学研究[J]. 食品工业科技,2023,44(14):229−236. doi: 10.13386/j.issn1002-0306.2022100070ZHOU Jiayue, HOU Yanli, WANG Fanyu, et al. Ultrasonic-Assisted Deep Eutectic Solvent Extraction of Proanthocyanidins from Korean Pine Bark and Its Kinetics[J]. Science and Technology of Food Industry, 2023, 44(14): 229−236. (in Chinese with English abstract). doi: 10.13386/j.issn1002-0306.2022100070· 工艺技术 ·超声辅助低共熔溶剂提取红松树皮原花青素及动力学研究周佳悦1,候艳丽1,王凡予1,郭庆启1,2,*(1.东北林业大学生命科学学院,黑龙江哈尔滨 150040;2.黑龙江省森林食品资源利用重点实验室,黑龙江哈尔滨 150040)摘 要:目的:对超声辅助低共熔溶剂法提取红松树皮原花青素的工艺条件进行优化,拟合提取动力学方程,旨在对红松树皮中原花青素的资源开发利用提供理论和技术参考。
方法:以原花青素得率为指标,筛选最佳低共熔溶剂体系,并进一步通过单因素结合响应面优化超声辅助低共熔溶剂提取红松树皮中原花青素的主要工艺参数。
通过提取过程中不同温度和不同时间条件下原花青素得率的变化,拟合出最佳的原花青素提取动力学模型并验证。
结果:氯化胆碱、丙三醇和水的摩尔比为1:1:4制备的低共熔溶剂为红松树皮原花青素的最佳提取溶剂;响应面法优化工艺参数条件为:液料比16 mL/g ,超声时间50 min ,超声温度55 ℃,超声功率480 W 时,红松树皮原花青素的提取效果最好,原花青素得率为4.11%;Boltzman 模型能够很好地拟合超声辅助低共熔溶剂提取原花青素动力学过程(R 2≥0.9768),模型验证值与预测值拟合度较高(R 2≥0.9442)。
- 1、下载文档前请自行甄别文档内容的完整性,平台不提供额外的编辑、内容补充、找答案等附加服务。
- 2、"仅部分预览"的文档,不可在线预览部分如存在完整性等问题,可反馈申请退款(可完整预览的文档不适用该条件!)。
- 3、如文档侵犯您的权益,请联系客服反馈,我们会尽快为您处理(人工客服工作时间:9:00-18:30)。
DEEP HYDRODESULFURIZATION OVERNi-Mo CATALYSTS SUPPORTED ON THEMIXED MOLECULAR SIEVESJing Ren 1, Anjie Wang 1*, Xiang Li 1, Mohong Lu 1, LifengRuan 1, Jia Yan 1, Yongying Chen 1,Yongkang, Hu 21.State Key Laboratory of Fine Chemicals,Dalian University of Technology, Dalian 116012 China;2.Fushun Research Institute of Petroleum and Petrochemicals,Fushun, 113001 China * Corresponding author. Fax: +86-411-88993919. E-mail address: anjwang@ Introduction The increasing concerns of global air environment have stimulated the demand for cleaner and cleaner engine fuels. Hydrodesulfurization is a key process used in producing clean engine fuels. In the process, Mo and W sulfide catalysts supported on γ-Al 2O 3 and promoted by Co and Ni have been applied to the industrial hydrotreatment of petroleum and liquefied coal. 1 However, new environmental regulations require that the sulfur content in diesel fuel be significantly reduced to less than 0.05 %, which is not currently achievable with the γ-Al 2O 3-based catalysts. The conventional catalysts are active in converting thiophene and benzothiophenes, but not active enough to desulfurize efficiently the most refractory sulfur-containing polyaromatic compounds, e.g., dibenzothiophene (DBT) and its alky-substituted derivatives. Whitehurst et al. concluded, based on the composition of typical gas oil and the first-order kinetics for Hydrodesulfurization (HDS) of different sulfur-containing compounds, that the reaction time will have to be increased up to 4 times when using conventional catalysts to reduce the sulfur content from 2500 to 500 ppm. 2Thus deep HDS becomes of great research interest, aiming at removing DBT and its derivatives. Mesoporous MCM-41 has been the focus of much research interest since its discovery because it offers a uniform pore of 1.5 to 10.0 nm and a very high surface area. 3The unique properties of MCM-41 provide a potential for catalytic application to the bulky molecule involved reactions. The extremely high surface area favors a high dispersion of active species and is often conducible to high catalytic activity. The MCM-41-supported catalysts have been developed for a variety of reactions, 4including HDS .5-8Recently, Wang et al. studied the HDS of DBT oversiliceous MCM-41-supported Co-Mo and Ni-Mo.9,10 It isshown that siliceous MCM-41-supported catalysts weresuperior in HDS activity to the conventionalalumina-supported counterparts. It is assumed that the highperformance is due to the higher dispersion of the activespecies on the surface of MCM-41.Despite the extensive use of zeolite in catalysis, there hasbeen relatively little research work on their application inhydrotreating processes until recently. Mann et al. 11 studiedthe HDS and hydrodenitrogenation (HDN) of heavy gas oil over Ni-Mo sulfide catalysts supported on zeolite-alumina-silica, and found that over the catalysts 99 % sulfur-containing compounds and 86 % nitrogen-containingcompounds can be removed at 425 °C . Harvey and Pratt 12studied the HDN reaction of quinoline over catalysts of metal ion-exchanged Y zeolite mixed with a standard Ni-Mo/γ-Al 2O 3 and found that ruthenium-exchanged Y zeolite promotes the HDN activity of the standard Ni-Mo/γ-Al 2O 3 catalyst. More recently, Yumoto 13 reported a new type of γ-Al 2O 3-zeolite-based catalyst for deep HDS, and found that asmall amount of zeolite accelerates the hydrogenation rate of the DBT ring. Li et al. 14 studied HDS of DBT over Ni-Mosulfides catalysts supported on γ-Al 2O 3-USY , and found that the Ni-Mo catalysts supported on γ-Al 2O 3-USY zeolite havehigher HDS activity. In the present study, the HDS of DBT over Ni-Mo catalysts supported over the mixed molecular sieves has been investigated. The mixed molecular sieves consist of proton-exchanged MCM-41 and HY .2. Experimental 2.1 Materials. The materials used were sodium silicate hydrate (commercial GR grade), cetytrimethylammonium bromide (CTAB) (A.R.grade), 4 M H 2SO 4, 0.5 M HNO3. Both ammonium heptamolybdate tetrahydrate [(NH 4)6Mo 7O 24.4H 2O] and nickel nitrate hexahydrate [Ni(NO 3)2.6H 2O] were of commercial GR grade (Dalian Chemical reagents Co.). DBT was synthesized according to the method in the literature.9 Decalin was a product of Shanghai Chemical Reagents Co. HY zeolite was provided by FuShun Research Institute of Petroleum and Petrochemicals. 2.2 Catalysts. Siliceous MCM-41 and theproton-exchanged MCM-41 were prepared according to the procedure reported in the paper.15 Ni-Mo/HY-H-MCM-41 catalysts were prepared in the following way: the support wasmade by milling H-MCM-41 with HY . The aqueous solution of (NH 4)6Mo 7O 24.4H 2O and Ni(NO 3)2.6H 2O was dropped onsupport in vacuum condition. The mixture was stirred for 2 h at room temperature, then the water was evaporated and the solid product was dried at 120 °C overnight, and calcined at 450 °C for 5 h. A 20 wt % MoO 3 loading level was chosen for preparing this series of catalysts. The content of nickel was determined by varying the atomic ratio of Ni/Mo in the range of 0-1.0. The prepared catalysts was denoted asNi-Mo(α)/Y(β)-M, where α represents Ni/Mo atomic ratioand β represents the weight percent of HY in support.The temperature programmed reduction (TPR) patterns ofthe catalysts were measured on a Chembet-3000 analyzer.Before the measurement, the sample had been treated inhelium at 200 °C for 2 h. A gas mixture of H 2 and N 2 (10 vol % H 2 in nitrogen) was used as the reacting agent. The patterns of the catalysts were measured from room temperature to ca. 1000 °C at 10 °C /min. Nitrogen adsorption measurementswere performed using a Quantachrome adsorption analyzer, which reports adsorption isotherm, BET specific surface area, and pore volume automatically. The samples were outgassed for 4 h at 300 °C before the adsorption. 2.3 System and Procedure for HDS. HDS of DBT was carried out in a fixed-bed stainless steel tubular reactor. The HDS activities of the prepared catalysts were evaluated using a model fuel: 0.8 wt % DBT in decalin.The catalysts were presulfided before HDS reaction. The products were analyzed by an Agilent-6890+ gas chromatograph equipped with an FID detector using an HP-5 column.3. Result and discussion 3.1 Characterization of Supported Catalysts. The physical properties of the support and the supported Ni-Mo catalysts are summarized in Table 1. It is shown that both BET specific surface area and pore volume of catalysts were reduced after being deposited by the metal species. The decreases in specific surface area and pore volume might result partly from the density increase of the catalysts and partly from the pore blocking by the metal species.The TPR profiles of Ni-Mo(0.75)/Y(β)-M catalysts are illustrated in Fig 1. The main H 2 consumption peak temperatures are summarized in Table 2. Two TPR peaks are observed, one around 500 °C and the other around 800 °C . As HY is added, the low temperature (LT) peak of the Ni-Mo site shifted to lower temperature, but the high temperature (HT) peak changed a little. Moreover, when the HY exceeds 25 %, the LT peak shifted to higher temperature. Ni-Mo(0.75)/Y(0.25)-M showed the lowest consumption peak temperature, indicating that this catalyst has the highest reducibility. The shift of LT peak by introduction of HY might be attributed to accelerating the hydrogen spillover from Ni to Mo sites on the surface of the support.Table 1. Physical Properties of the Support and the Ni-Mo (α)/Y(β)-M CatalystsCatalyst BET surface area(m 2/g)Pore volume (cm 3/g) Ni-Mo (0.75)/Y (0)-M Ni-Mo (0.75)/Y (0.1)-M Ni-Mo (0.75)/Y (0.25)-M Ni-Mo (0.75)/Y (0.75)-M Ni-Mo (0.75)/Y (1.0)-M Ni-Mo (0)/Y (0.25)-M Ni-Mo (0.25)/Y (0.25)-M Ni-Mo (0.5)/Y (0.25)-M Ni-Mo (1.0)/Y (0.25)-M 366.6 361.3 462.8 353.7 411.7 380 414.3 434 433.8 0.52 0.47 0.44 0.28 0.21 0.54 0.47 0.42 0.41The TPR profiles of Ni-Mo(α)/Y(0.25)-M andNi/Y(0.25)-M catalysts are illustrated in Fig 2. The main H 2consumption peak temperatures are also summarized in Table2. Two peak temperatures were 420 °C and 519 °C forNi/Y(0.25)-M, and there were 578 °C and 935 °C forMo/Y(0.25)-M, indicating that the reducibility of Ni species is superior to that of Mo species.Table 2. The Main H 2 Consumption Temperatures in the TPRProfiles of Ni-Mo(0.75)/Y(β)-M Catalysts .Catalyst The LT peak temperature (°C )Ni-Mo (0.75)/Y (0)-M 501 Ni-Mo (0.75)/Y (0.1)-M 489 Ni-Mo (0.75)/Y (0.25)-M 461 Ni-Mo (0.75)/Y (0.75)-M 555 Ni-Mo (0.75)/Y (1.0)-M 576 Ni-Mo (0)/Y (0.25)-M 578 Ni-Mo (0.25)/Y (0.25)-M 492 Ni-Mo (0.5)/Y (0.25)-M 478 Ni-Mo (1.0)/Y (0.25)-M44220040060080010001200e d c b aT e m p e ratu re,¡æFigure 1. TPR profiles of Ni-Mo(0.75)/Y(β)-M catalysts.(a) Ni-Mo (0.75)/Y(0)-M, (b) Ni-Mo (0.75)/Y(0.1)-M, (c) Ni-Mo (0.75)/Y(0.25)-M, (d) Ni-Mo (0.75)/Y(0.75)-M, (e). Ni-Mo (0.75)/Y(1.0)-M,20040060080010001200T e m p e ra tu re ,¡æf e d c b aFigure 2. TPR profiles of Ni-Mo (α)/Y (0.25)-M catalysts(a) Ni-Mo (0)/ Y (0.25)-M, (b) Ni-Mo (0.25)/ Y (0.25)-M(c)Ni-Mo (0.5)/ Y (0.25)-M, (d) Ni-Mo (0.75)/ Y (0.25)-M,(e) Ni-Mo (1.0)/ Y (0.25)-M ,(f) Ni/ Y (0.25)-MTwo TPR peaks are also observed for Ni-Mo(α)/Y (0.25)-M catalysts, at about 500 °C and 800 °C. As the Ni/Mo atomic ratio increases, the LT peak temperature of the Mo site shifts to lower temperature, suggesting a strong interaction between Ni and Mo species. It is shown that Ni-Mo(0.75)/Y (0.25)-M shows the lowest consumption temperature, indicating that it has the highest reducibility. The shift of the LT reduction peaks by the introduction of Ni species may have resulted from the interaction among the metal species, andfrom the hydrogen spillover from Ni sites to Mo sites on the surface of the support.3.2 HDS of DBT3.2.1 HDS of DBT Over Ni-Mo(0.75)/Y(β)-M. In general, there two possible reaction pathways for removal of sulfur from DBT. The first pathway is direct extraction of the sulfur atom from the molecule yielding biphenyl (BP), the second pathway is prehydrogenation of one aromatic ring followed by extraction of the atom yielding cyclohexylbenzene (CHB).1 In the present study, the detectable compounds in the liquid samples are BP, CHB, and traces of benzene and cyclohexane. For the catalytic reaction, the conversion of DBT represents the activity of HDS for the catalysts.Fig.3 shows the conversion of DBT during HDS catalyzed by Ni-Mo(0.75)/Y(β)-M as a function of temperature. All the Ni-Mo(0.75)/Y(β)-M catalysts showed substantially high activity for converting DBT into hydrocarbons. Maximum activity was observed for the Ni-Mo(0.75)/Y(β)-M catalysts at β is 0.25.3.2.2 HDS of DBT Over Ni-Mo(α)/Y(0.25)-M. Fig.4 shows the conversion of DBT during HDS catalyzed by Ni-Mo(α)/Y(0.25)-M as a function of temperature. All the Ni-Mo(α)/Y(0.25)-M catalysts showed extremely high activity for converting DBT into hydrocarbons. Moreover, Ni-Mo(0)/Y(0.25)-M also showed relatively high HDS activity at high temperature. It is shown that Ni-Mo(0.75)/Y(0.25)-M catalyst exhibited the highest activity for DBT HDS. The optimal Ni-Mo atomic ratio for the mixed molecular sieves supported catalysts is different from that for conventional γ-Al2O3-supported catalysts, which generally falls in the range of 0.2-0.5.126028030032034036020406080100DBTConversion,%Temperature,¡æFigure 3. Variation of DBT conversion with temperatureduring HDS over Ni-Mo(0.75)/Y(β)-M(■)Ni-Mo(0.75)/Y(0)-M (●)Ni-Mo(0.75)/Y(0.1)-M(▲)Ni-Mo(0.75)/Y(0.25)-M(▼)Ni-M(0.75)/Y(0.75)-M (□) Ni-Mo (0.75)/Y (1.0)-M26028030032034036020406080100DBTConversion,%Temperature,¡æFigure 4. Variation of DBT conversion with temperature during HDS over Ni-Mo(α)/Y(0.25)-M(■)Ni-Mo(0)/Y(0.25)-M (●) Ni-Mo(0.25)/Y(0.25)-M (□)Ni-Mo(0.5)/Y(0.25)-M, (▼) Ni-Mo(0.75)/Y(0.25)-M (○) Ni-Mo(1.0)/Y(0.25)-M4.Discussion4.1 HDS Activity of DBT. It is generally accepted that small nickel suifide species are located at the MoS2 edges in the active phase. EXAFS measurements revealed that the Ni suifide species located at the MoS2 edges differ locally in size and ordering. It is believed that only the Ni-Mo-S structure is active in HDS. 9It is well accepted that high dispersion of Ni-Mo species on the support surface is essential for preparation of high-performance HDS catalysts and that the surface properties, such as acidity, affect the dispersion and local environment of the metal species. It was reported that siliceous MCM-41-supported Ni-Mo sulfides catalysts exhibited very high activity for DBT HDS.10 It is assumed that the high surface area and the mild acidity of the support may lead to a high dispersion of the metal species on the surface.The conversion of DBT for Ni-Mo(α)/Y(β)-M catalysts indicated that the optimal Ni/Mo atomic ratio is 0.75, higher than the conventional γ-Al2O3-supported catalysts. It is believed that a high dispersion of MoS2 and the promoters onthe surface of the support is essential to form a monolayer or tiny Ni-Mo-S crystallite structure so as to achieve a very high HDS activity. 24.2 Correlation of HDS Activity With ReducibilityAccording to the literature,15,16 a correlation exists between the reducibility of oxidic catalyst and the HDS activity of its sulfides. In order to correlate HDS activity and reducibility, both have to be quantified. HDS activity is easily represented by the conversion of DBT. Reducibility can be characterized in several ways, i.e., the temperature of reduction onset method or the average temperature method. Any of the above mentioned methods lead to the same conclusions.16 Thus, in this study, the reducibility is characterized by main H 2 consumption peak temperature. The DBT conversion at 280 °C is plotted against the main H 2 consumption peak temperature for the Ni-Mo(α)/Y(β)-M catalysts In Fig.5. Line M represents the Ni-Mo(0.75)/Y(β)-M series catalysts, and line N represents Ni-Mo(α)/Y(0.25)-M series catalysts. It is indicated that DBT conversion is well correlated with the main H 2 consumption peak temperature for the Ni-Mo(α)/Y(β)-M catalysts except Ni-Mo(1.0)/Y(0.25)-M catalysts. The exception may be due to the overloading of Ni on the surface, leading to the appearance of new species, which might be difficult to be reduced. It is indicated that HDS activity increased with the decrease of the main H 2 consumption peak temperature. This suggests that reduction of the transition metal compounds is a crucial step in the transformation of the oxidic precursor catalyst into the sulfided catalyst. The high DBT conversion for Ni-Mo (0.75)/Y(0.25)-M catalysts corresponds very well with its good reducibility. TPR thus appears to be a promising technique, which can be applied for a preliminary screening of the oxidic HDS catalysts.44046048050052054056058020406080100D B T C o n v e r s i o n ,%Main H 2consumption Temperature,¡æFigure 5. The DBT conversion at 280 ℃versus H 2 consumption temperature in the TPR profiles of the Ni-Mo(α)/Y(β)-M(M) Ni-Mo(0.75)/Y(β)-M,(N) Ni-Mo(α)/Y(0.25)-M, (a)Ni-Mo(0.75)/Y(1.0)-M,(b)Ni-Mo(0.75)/Y(0.75)-M,(c) Ni-Mo (0.75)/Y(0)-Mo(d) Ni-Mo (0.75)/Y(0.1)-M,(e) Ni-Mo (0.75)/Y(0.25)-M (f) Ni-Mo(0)/Y(0.25)-M, (g) Ni-Mo(0.25)/Y(0.25)-M, (h) Ni-Mo(0.5)/Y(0.25)-M, (i) Ni-Mo(1.0)/Y(0.25)-M,5. ConclusionIn summary, the mixed molecular sieve is a promising support for preparing deep HDS catalysts. The optimal weight percent of HY in the mixture was 25 %. A maximum HDSactivity was observed at Ni/Mo atomic ratio of 0.75. It is assumed that tiny Ni-Mo sulfide clusters might be created on the extremely high surface area, yielding considerably high activity for HDS of DBT. TPR data revealed that the H 2 consumption peak at low temperature shifted to lower temperature when the weight percent of HY in the support and the Ni/Mo atomic ratio increased. It is assumed that the shifting of the reduction peak might be attributed to the interaction between metal species and the support and to the synergetic effect of the binary metal species. A correlation exists between the reducibility of oxidic Ni-Mo(α)/Y(β)-M catalysts and the HDS activity of their sulfides. High reducibility corresponds to high HDS activity. TPR could be used as a time-saving preliminary screening technique the HDS catalysts.Acknowledgments. This research was partly supported by the Natural Science Foundation of China (Grant No. 20003002 and 20333030), by CNPC Innovation Foundation and by Education Ministry of China(20030141026). The authors are grateful to Mr Zequn Yin, Mr Guanwei Cao, Mr Yang Teng for their kind helps in the research work.References(1) Topsoe, H.; Clausen, B. S.; Massoth. “Hydrotreating Catalysis:Science and Technology” .Spinger-Verlag, Berlin. 1996,310 (2) Whitehurst, D. D.; Isoda. T. ; Mochida. I. Adv.Catal .1998,42,345.(3) Beck J. S.; Vartuli, J. C.; Roth, W. J. Leonowicz, M. E.; Kresge,C. T.; Schmitt, K.D.; Chu, C. T. W.; Olsen, D. H.; Sheppard,E. W.; McCullen, S. B., Higgins, J. B.; Schlenker, J. L. J.Am.Chem.Soc .1992, 114, 10834.(4) Ying, J. Y .; Mehnert, C.P.; Wong, M. S. Angew. Chem. Int. Ed.1999,36,56.(5) Coma, A.; Martinez, A.; Martinez-Soria V .; Monton, J.B. J.Catal .1995,153,25.(6) Song, C. S.; Reddy, K. M. Appl. Catalysis . 1999,176,1(7) Reddy, K. M; Wei, B. L; Song, C. S. Catal.Today. 1998,43,261. (8) Tyraga, U. T.; Ma, X. L.; Song, C. S. Catal.Today. 2003,86,265. (9) Wang, A. J.; Wang. Y , Kabe; T., Chen, Y . Y .; Ishihara; Qian, W.J.Catal . 2001,199,19.(10) Wang, A. J.; Wang. Y; Kabe, T.; Chen,Y . Y .; Ishihara.; Qian, W.;Yao, P. J. J.Catal . 2002,210,319.(11) Mann, R.S.; Sambi, I. S.; Khulbe K. C. Ind. Eng. Chem. Res .1988,27,1788.(12) Harvey, T.G .; Pratt, K.C. Appl.Catal . 1989,87,335.(13) Yumoto, M.; Usui, K.; Watanabe, K.; Idei, K.; Yamazaki, H.Catal.Today. 1998,35,45.(14) Li, D.; Nishijima, A.; Morris, D. E.; Guthrie, G . D. J. Catal .1999,188,111.(15) Li, X.; Wang, A. J.; Wang, Y .; Chen, Y . Y . ; Liu, Y . H.; Hu, Y . K.Catalysis Letters . 2002,84,1.(16) Thomas, R.; Van Oers, E. M.; De Beer, V .H.J., Medema, J.;Moulijn, J.A. J. Catal . 1982,76,241.。