多失效模式机械系统可靠性稳健设计方法研究
第3次课-机械可靠性设计原理与可靠度计算
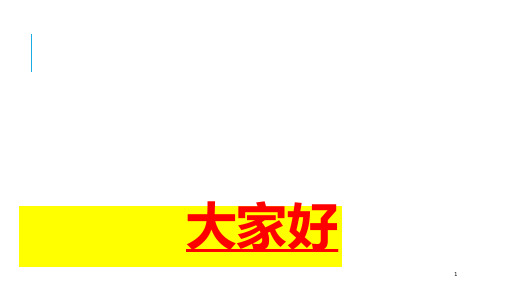
强度衰减曲线
g(r)
f (s) n
Y轴
f (s)
t0
ts
t/h
应力—强度随时间变化曲线
8
应力强度模型的启示:
(1)模型的描述:强度应力离散性
在机械设计中强度与应力具有相同的量纲,概率密度 曲线表示在同一坐标系中。通常要求零件的强度高于其 工作应力,但由于强度值与应力值的离散性,使应力强 度两概率密度曲线在一定的条件可能相交,相交的区域 为产品产生或可能出现故障的区域,即干涉区。
16
二、应力分布确定的步骤
确定零件的失效模式及其判据
应力单元件分析(复合应力引起失效)根据有限元分 析或实验应力分析,将最有可能失效的点取作应力单 元体。
计算应力分量
确定每一应力分量的最大值
计算主应力:当以最大主应力或最大剪切应力为失效 判据时需计算主应力
将上述应力分量综合为复合应力,复合应力值最大处 即为零件失效概率最大的部位
41
二、随机变量函数的变差系数(变异系数)
在机械设计中,许多计算公式常包含多 个随机变量,变量间为乘除关系、非线 性关系、复杂的多元函数。求 , 比较繁琐,利用变差系数有时可使之简 化
42
(2)一些复杂函数的变差系数
1.变量为乘除关系的函数的变差系数
43
44
45
46
47
48
49
3.4已知应力与强度的分布时的可靠度计算
10
5.可靠度的计算
工作应力的最大值小于强度的极小值,当 工作应力与强度发生干涉时,虽 远小 于 ,但不能保证工作应力在任何情况下 都不大于极限应力(强度)
11
12
13
14
15
3.2应力分布的确定
机械工程可靠性工艺规划

机械工程可靠性工艺规划713100【摘要】:随着我国机械制造工业进程的快速发展,对机械工程产品的质量要求也更加具体化,可靠性要求指标更加明确。
从产品的初期可靠性工艺设计规划方案的制定、制造流程及标准执行、可靠性试验和产品使用,它贯穿于产品的整个寿命周期之内。
通过对机械产品各组成零部件进行可靠性试验,结合出现的失效模式及对产品功能的影响进行分析,并把每个潜在失效模式按它的严酷程度予以分类,确定失效源,提出采用的预防改进措施并予以实施,完善可靠性工艺规划,从而降低产品在设计过程的潜在失效风险,使机械产品可靠性逐步得到增长,提高机械产品固有可靠性,最终完成机械工程工艺规划设定的可靠性指标。
关键词:机械工程;可靠性;工艺规划前言机械产品可靠性工艺设计规划及测试方案的制定,是保证产品实现可靠性设计目标的关键要素。
机械产品可靠性设计功能是以使用为目,对产品可靠性工艺设计时,结合产品的使用要求,在满足产品的使用及功能的基础上,保证机械产品可靠性工艺设计规划需求。
为了安全、可靠、高效的生产出所需的机械产品,从设计产品可靠性工艺规划入手,强化测试工艺管理,明确影响机械产品使用质量的理论根源,为提升机械工程产品质量和生产效率创造条件。
在制定可靠性测试方案中,完善可靠性工艺规划,直接影响到机械产品生产工艺预设的固有可靠性指标。
加强可靠性工艺控制,保持工艺规程的稳定性,设置各个工序检验点,有效控制并实施产品工艺设计规划目标,确保产品的可靠性及使用的安全。
1.国内外机械工程可靠性研究现状分析林有志;刘凌霜;宋爱斌;刘明等[1]概述并分析了机械可靠性的设计和研究及其发展,探讨了机械产品设计现状,对可靠性评估方法逐一做了介绍;侯郁[2]综述了国内外可靠性工程的发展概况,李永华;何卫东;[3]对提高机械产品的零部件的稳健性,提出了优化设计方法,通过产品零部件证明其优化设计的有效性和设计的合理性及有效性。
高金梅[4阐述了我国目前机械工程技术的应用,探究了其发展现状及所产生的影响,提出了适合我国目前在机械工程技术的发展模式,从而实现提高机械工程技术设计运用质量水平目的;蒋平[5]对开展机械产品可靠性的保障进行了研究,探讨了机械产品设计工艺可靠性,提出了机械制造过程中的有效控制设计,为完成产品可靠性设定的最终目标提供技术支持。
设计失效模式和影响分析_DFMEA

5
November 01, 2013
_Sector
Confidential
FMEA : 失效模式及其后果分析
风险管理: 识别并减轻失效风险
目标
识别新产品、新工艺或者新的服务流程中可能出现的失效 模式,从而设法改进设计,使产品在实际应用中更稳健。
6
November 01, 2013
输出: 风险, 提高过程能力/过程控制的措施 举例: 过程步骤: 连接风道和电机外壳 过程需求: 确保气密性 失效模块: 气密性差 起因: 空气导管直径过大/变形
设计FMEA 产生风险
过程步骤
过程FMEA 过程能力:
提高过程能力 (控制预防)
14
November 01, 2013 _Sector
改善风管的注射成型工艺
5. 生产
3
3
November 01, 2013
_Sector
Confidential
FMEA步骤与FMEA方法
准备
头脑风暴
分析 时间
跟踪
准备 :
策划FMEA 搜集必要输入信息 准备参数图和功能/结构框图等等
头脑风暴 : 分析 :
列出FMEA中可能存在的失效模式和后果 识别原因 确定风险级别
降低风险措施 定期更新风险级别
过程 FMEA
过程步骤: 连接风道和电机外壳 需求 (目的): 气密连接 失效模式:气密连接性能不好 原因:空气导管直径太大或已变形 (过程)
• • •
设计FMEA不依靠过程控制来克服设计缺陷,但应考虑制造过程(如过程能力)技术的局限性 过程FMEA 不依靠产品设计变更来克服过程缺陷,但应考虑与装配相关的产品设计特性 因此,设计FMEA不关注诸如“操作者风管安装不当”或“风管直径超差”的原因,但如有与设计相关的因素导致 连接不当,就需加以考虑
机械零件的可靠性设计.ppt

n 则在强度和应力的可靠度分别为Rδ和Rs时的安全系数 R,
称为可靠度意义下的安全系数,用下式表示:
nR
min (R )
smax (Rs )
例,当 smax s 3 s min 3 时
R P( min) 1 0.0013 0.9987 Rs P(s sm )a2x7
例1 在结构件的设计中,已知强度与应力均服从正态分布,
f ( )
f (s)
1 2
y
0 exp[
(y
y
2
2 y
)2
]dy
y S
y=-S
0
-10
0
10
20
y =-S
y0 y0
30
40
S
50
y=
2
2 S
不可靠度为: F P ( y 0)
1
2 y
0
exp[
(
y
y
2
2 y
)2
]dy
11
可靠度为 R P( y 0)
1
2 y
0
exp[
则他们之间具有下列关系:
2 ln
s=ln
2 s
s2
1
ln
s=ln
s-12
2 ln
s
2 ln
=ln
2
2
1
ln
=ln
-12
2 ln
15
当应力和强度均为对数状态分布时,有:
y ln ln S ln( )
服从正态分布
s
知道了 ln 和ln S 的均值标准差为的lns、ln 和 lns、 ln
当强度均值大于应力的均值时,方差越大,可靠度越小。
第四章 机械可靠性设计原理与可靠度计算讲解
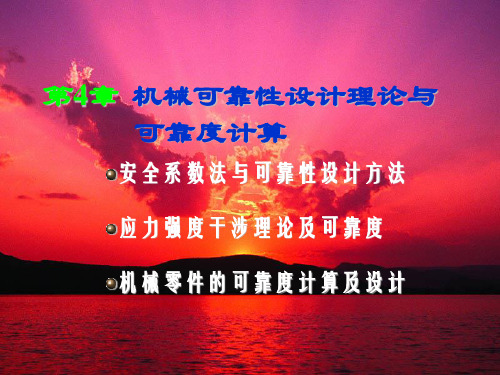
机械可靠性设计实质:
(1) 就在于揭示载荷(应力)及零部件的分布规律 (2) 合理地建立应力与强度之间的力学模型,严格 控制失效概率,以满足可靠性设计要求。
4.2.1 应力强度干涉理论
应力S及强度δ本身是某些变量的函数,即
s f s1 , s2, , sn
表4-1 蒙特卡洛 模拟法可 靠度计算 的流程
4.3 机械零件的可靠度计算
4.3.1 应力强度都为正态分布时的可靠度计算
应力S和强度δ均呈正态分布时,其概率密度函数:
2 1 1 S S f (S ) exp (∞ < S < ∞) 2 S S 2
机械可靠性设计与安全系数法:
1) 相同点
都是关于作用在研究对象上的破坏作用与抵抗这种破坏 作用的能力之间的关系。 破坏作用:统称为“应力”。 抵抗破坏作用的能力:统称为“强度
“应力”表示为
S f s1, s2, , sn
其中,
表示影响失效的各种因素。 s1 , s2, , sn
如力的大 小、作用位置、应力的大小和位置、环境因
第4章 机械可靠性设计理论与 可靠度计算
安全系数法与可靠性设计方法 应力强度干涉理论及可靠度 机械零件的可靠度计算及设计
4.1安全系数法与可靠性设计方法
4.1.1 安全系数设计法
在机械结构的传统设计中,主要从满足产品使用要求 和保证机械性能要求出发进行产品设计。在满足这两方面 要求的同时,必须利用工程设计经验,使产品尽可能可靠, 这种设计不能回答所设计产品的可靠程度或发生故障概率 是多少。 安全系数法的基本思想:机械结构在承受外在负荷后,计 算得到的应力小于该结构材料的许用应力,即
机械设计上冗余设计的例子

机械设计上冗余设计的例子冗余设计在机械工程中是一种重要的设计策略,它通过增加额外的组件、系统或功能,来确保在原始设计失效或发生故障时,整个机械系统仍能维持其基本性能和安全操作。
这种方法不仅提高了设备的可靠性和耐久性,而且在一定程度上降低了由于单点故障导致系统完全失效的风险。
本文将探讨冗余设计在机械设计中的几个实际应用案例,并分析其如何提升整体系统的稳健性。
一、冗余设计的基本概念在机械设计领域,冗余设计通常指的是在系统中引入额外的、超出基本功能需求的元素。
这些元素可以是硬件组件,如备用发动机、双重电源系统等;也可以是软件功能,比如故障检测和自动切换程序。
冗余设计的核心思想是预防因单一故障点导致的整体系统崩溃,从而增强系统的鲁棒性和容错能力。
二、冗余设计的类型在机械设计中,冗余设计可以根据其实现方式和目的分为不同类型,主要包括硬件冗余和软件冗余。
1. 硬件冗余硬件冗余通常涉及在关键部位安装备份组件。
例如,在飞机设计中,双发动机配置就是一种典型的硬件冗余设计。
如果其中一个发动机失效,另一个发动机能够接管飞行任务,确保飞机安全着陆。
类似地,在重型机械如挖掘机或矿用卡车的设计中,关键液压系统可能会采用双泵或双回路设计,以防止单个泵的故障导致整个机器停工。
2. 软件冗余软件冗余则更多体现在控制系统的编程逻辑上。
现代机械设备往往配备有复杂的电子控制系统,这些系统通过软件算法监控设备的运行状态,并在检测到异常时采取纠正措施。
例如,汽车中的防抱死刹车系统(ABS)就包含了软件冗余设计,它能够在检测到车轮即将锁死时迅速调整刹车压力,防止车辆失控。
三、机械设计中的冗余设计案例以下是一些展示了冗余设计在机械工程中实际应用的案例。
案例一:航天器的冗余设计航天器是冗余设计应用最为广泛的领域之一。
由于航天任务的高风险性和难以进行维修的特性,航天器必须在设计之初就考虑到各种可能的故障情况。
例如,国际空间站(ISS)就采用了多重冗余设计,包括备用电源系统、生命维持系统以及通讯系统等。
机械结构的可靠性评估与优化设计

机械结构的可靠性评估与优化设计引言:机械结构的可靠性是指在一定运行条件下,结构能够保持其设计的功能和性能,不发生失效或损坏的能力。
对于任何工程项目而言,确保机械结构的可靠性至关重要。
本文将探讨机械结构的可靠性评估与优化设计,从多个角度深入分析。
一、可靠性评估方法1.1 统计学方法统计学方法是最常用的可靠性评估方法之一。
它基于概率论,通过收集和分析实际数据,计算出机械结构在给定条件下的失效概率。
常见的统计学方法有可靠度预测、可靠度增长模型等。
1.2 有限元分析方法有限元分析方法利用数值计算技术,通过离散化对结构进行建模,模拟各种工况和负载条件下的应力和变形情况,从而评估结构的可靠性。
这种方法可以更准确地分析结构在复杂工况下的受力状况,但也需要大量的计算资源和较高的技术水平。
1.3 可靠度设计方法可靠度设计方法是在结构设计过程中考虑可靠性要求,采取一系列的优化设计措施,以满足可靠性指标。
这种方法将可靠性作为设计的重要指标,通过设计参数的优化来提高结构的可靠性。
二、可靠性评估的影响因素2.1 材料特性材料的力学性能和寿命是影响可靠性的重要因素。
选用合适的材料,并进行合理的热处理和表面处理,可以提高结构的强度和耐久性,从而提高可靠性。
2.2 结构几何形状结构的几何形状对其强度和刚度等力学性能有很大影响。
合理的结构形状设计可以减少应力集中和应力过大的区域,提高结构的可靠性。
2.3 加工工艺和装配质量加工工艺和装配质量是影响结构可靠性的关键因素。
合理的加工流程和精密的装配过程可以提高结构的质量,减少缺陷和失效的可能性。
2.4 负载条件和环境因素负载条件和环境因素是决定结构可靠性的重要因素。
合理的负载设计和结构防护措施可以减小结构的失效风险,延长结构的使用寿命。
三、优化设计方法3.1 结构拓扑优化结构拓扑优化是一种通过改变结构的形状和尺寸,以最小化体积或质量为目标,满足约束条件的设计方法。
这种方法可以减少应力集中和应力过大的区域,提高结构的可靠性。
稳健设计方法

机研142孙利文2100一、稳健设计方法在产品设计开发中的作川。
稳健设计又称作鲁棒设计。
是关于产品质量和成本的一种工程设计方法。
在产品或工艺系统设计中,正确的应用稳健设计的基本理论和方法可以使产品在制造或使用中,或是在规定寿命内当结构或材料发生老化、变质、工作环境发生微小的变化时,都能保证产品质量的稳足。
通过稳健设计,可以使产品的性能对各种噪声因素的不可预测的变化,拥有很强的抗干扰能力。
产品性能将更加稳定、质量更加可靠。
任何一种产品〃影响其质量的因素有很多〃主要可分为两类:一类是在设计中人们可以控制的因素如设计变量、变量的容差等;另一类是所谓的噪声因素指由生产条件、使用环境及时间等的变化而影响产品质量的因素如载荷、儿何尺寸、工程材料特性的变异以及制造、安装误差等,其基本特点是具有不确定性和随机性,是不可控制的因素。
实际存在的不确定因素的变化有可能导致产品的性能指标有较大的波动,使其功能劣化我至失效,还有一些材料或元器件会随着时间的推移而发生失效等。
对于这些因素有两种处理方法: 一是尽可能消除这些因素这对可控因素是可以做到的,而对噪声因素往往很难实现。
即使能够消除也需要花费很大的代价;二是尽量降低这些因素的影响。
这是相对容易和低代价的方法,也就是使产品性能对这些因素的变化不敏感,为了使所设计的产品在不确定因素的影响下,其性能指标不仅能达到设计要求,而且对各种不确定因素的变化不敏感,就需要用稳健设计方法來实现。
稳健设计就是使产品的性能对在制造期间的变异或使用环境的变异不敏感,并使产品在其寿命周期内不管其参数、结构发生漂移或老化在一定范围内都能持续满意地工作。
二、试验设计在稳健设计中的作用。
试验设计就是运用正交试验法或优化方法确定零部件参数的最佳组合,在系统内、外因素作用下,所产生的质量波动最小,即质量最稳定(健壮)。
试验设计的目的是根据系统设计中所确定的所有参数,通过多因素的优选方法来考察三种干扰(内干扰,外干扰,产品间波动)对系统质量特性的影响,寻求最佳的参数组合,以求得抗干扰性最佳的设计方案,使系统质量特性波动小,稳健性好,并且价格低廉。