离子氮化技术现状与发展趋势
冲压模具的表面处理技术

冲压模具的表面处理技术1. 引言冲压模具是在工业生产中广泛应用的一种工具。
它用于将金属板材等材料加工成所需形状的零件。
冲压模具的表面处理技术对于提高模具的耐磨性、延长使用寿命、增加工件的精度和减少摩擦阻力等方面起着至关重要的作用。
本文将介绍几种常用的冲压模具表面处理技术及其优缺点。
2. 高温气体渗氮高温气体渗氮是一种常用的冲压模具表面处理技术。
该技术通过在高温下将氮气渗入模具表面,使其形成氮化层。
这种氮化层具有高硬度、良好的耐磨性和抗腐蚀性能。
同时,氮化层能够降低摩擦系数,减少摩擦损失,提高模具的使用寿命。
然而,高温气体渗氮技术存在一些缺点。
首先,该技术的成本较高,需要投资大量的设备和材料。
其次,渗氮过程中需要严格控制温度和氮气流量,以保证氮化层的质量。
因此,该技术在应用中需要一定的专业知识和技术支持。
3. 离子氮化离子氮化是另一种常用的冲压模具表面处理技术。
该技术通过在真空环境中施加高电压,使模具表面形成氮化层。
离子氮化技术具有渗层速度快、渗氮层厚度均匀等优点。
此外,离子氮化过程中还可以控制温度和离子能量,以调节氮化层的硬度和结构。
然而,离子氮化技术也有一些局限性。
首先,该技术对模具材料的要求较高,只有一些特定的金属材料才能通过离子氮化得到理想的氮化层。
其次,由于离子氮化需要在真空环境下进行,因此设备的成本较高,操作难度较大。
4. 涂层涂层技术是一种简单且广泛应用的冲压模具表面处理技术。
该技术通过在模具表面涂覆一层特殊的涂层材料,以提高模具的表面硬度、耐磨性和抗腐蚀性能。
常见的涂层材料包括钛、钨、碳化物等。
涂层技术具有成本较低、适用性广等优点。
此外,涂层技术还可以根据不同的需求选择不同的材料和涂层厚度,以满足不同工艺要求。
然而,涂层技术也存在一些问题。
首先,涂层的附着力和耐磨性较低,容易剥落或磨损。
其次,涂层的加工工艺复杂,需要控制好涂层的厚度和均匀性。
5. 表面喷丸处理表面喷丸处理是一种常用的冲压模具表面处理技术。
2024年离子束技术市场前景分析

2024年离子束技术市场前景分析引言离子束技术是一种利用离子束对物质进行加工和改性的先进制造技术。
它在材料研究、微电子器件制造、生物医学和光学等领域具有广泛的应用前景。
本文将对离子束技术的市场前景进行分析,探讨其市场发展的趋势和潜力。
市场规模和增长趋势离子束技术市场的规模在过去几年里不断扩大,未来预计将持续增长。
离子束技术在材料加工、器件制造和研究领域的应用需求不断增长,推动了市场的发展。
根据市场研究机构的数据,离子束技术市场在过去五年里以每年10%的复合增长率增长,预计在未来五年内将保持相似增长趋势。
应用领域分析材料加工离子束技术在材料加工领域具有广泛的应用。
离子束可以对材料进行精确的刻蚀、表面改性和掺杂等加工,可以在微纳米尺度上进行高精度的加工。
这在半导体制造和光学元件制造等领域具有重要意义。
随着微电子器件的不断发展和精密度的提高,对离子束技术的需求将进一步增加。
生物医学离子束技术在生物医学领域也有广泛的应用。
离子束可以用于癌症治疗、组织修复和基因治疗等方面。
离子束可以在精确定位的情况下杀死癌细胞,对患者的身体造成较小的损害,并且可以减少放疗的副作用。
随着生物医学领域的发展和人们对健康需求的增加,离子束技术在生物医学领域的市场需求将继续增长。
研究领域离子束技术在研究领域的应用也非常广泛。
离子束可以用于表征材料的结构和性质,可以进行材料的表面分析、形貌观察和元素分析等。
离子束还可以用于制备纳米材料和研究材料的微观结构。
随着研究对材料性能和结构的需求不断增加,离子束技术在研究领域的市场需求也将增长。
市场竞争分析离子束技术市场的竞争激烈。
目前市场上存在多家离子束技术供应商,并且市场进入壁垒相对较低,新进入者也有机会进入市场。
市场上主要的竞争因素包括产品性能、价格、售后服务和技术支持等。
供应商需要不断提升产品技术,降低成本,并提供全面的技术支持和售后服务,才能在市场上获得竞争优势。
发展趋势和展望离子束技术在未来的发展趋势中有几个重要方面:1.精度和分辨率的提高:随着纳米器件的发展和微电子技术的进一步提升,对离子束技术的精度和分辨率要求将愈发严格。
氟化锂,氮化锂的锂离子传输势垒

氟化锂,氮化锂的锂离子传输势垒【摘要】本文旨在探讨氟化锂和氮化锂的锂离子传输势垒及其影响因素。
首先介绍了锂离子电池的重要性和研究背景,然后阐述了氟化锂和氮化锂在锂离子传输势垒方面的特点。
接着比较了两者的异同,并分析了影响锂离子传输势垒的主要因素。
最后探讨了氟化锂和氮化锂在能源领域的应用前景。
通过对比分析,得出了一些结论,并展望了未来研究的方向。
本文通过深入研究氟化锂和氮化锂的锂离子传输势垒,为锂电池技术的发展提供了有益的参考。
【关键词】氟化锂、氮化锂、锂离子传输、势垒、比较分析、应用领域、影响因素、研究背景、研究目的、研究展望1. 引言1.1 研究背景锂离子电池作为目前最主流的锂离子传输媒介,在电子设备、电动汽车等领域有着广泛的应用。
氟化锂和氮化锂作为锂离子电池中常见的电解质材料,其锂离子传输势垒的研究对于提高电池的性能具有重要意义。
目前对氟化锂和氮化锂的锂离子传输势垒的研究还相对较少,尤其是两者之间的比较研究更是罕见。
氟化锂和氮化锂作为锂离子传输的重要材料,其锂离子传输势垒的研究不仅可以帮助我们更深入地了解锂离子传输的机制,还可以为电池材料的设计和优化提供重要的参考。
本文旨在通过对氟化锂和氮化锂的锂离子传输势垒进行系统性的研究和比较分析,探讨影响锂离子传输势垒的因素,并探讨氟化锂和氮化锂在不同领域的应用前景,从而为相关研究提供参考和启示。
1.2 研究目的研究目的是深入探讨氟化锂和氮化锂中锂离子传输势垒的形成机制及特点。
通过分析两者的异同,揭示其对锂离子传输速率的影响,为设计新型锂离子导电材料提供理论依据。
通过研究锂离子传输势垒的影响因素,探讨如何改变或优化材料结构,以提高锂离子传输速率。
通过探究氟化锂和氮化锂的应用领域,了解其在电池、储能等领域的潜在应用价值。
最终旨在推动锂离子电池等领域的发展,提高电池性能,促进清洁能源的发展和应用。
2. 正文2.1 氟化锂的锂离子传输势垒氟化锂是一种常用的锂离子电池正极材料,其锂离子传输势垒是影响电池性能的重要因素之一。
离子氮化变形

离子氮化变形摘要:1.离子氮化变形简介2.离子氮化的基本原理3.离子氮化变形的影响因素4.离子氮化变形对材料性能的影响5.应对离子氮化变形的措施正文:离子氮化变形是一种材料表面处理技术,通过氮化处理,使材料表面形成一层氮化层,从而改善材料表面的硬度、耐磨性等性能。
然而,在离子氮化过程中,由于各种因素的影响,可能导致材料发生变形。
本文将详细介绍离子氮化变形的相关内容。
离子氮化是利用气体放电产生的氮离子,在高温、高压下与材料表面发生反应,形成氮化层的一种方法。
离子氮化变形的产生与氮化过程中的物理、化学反应密切相关。
氮化过程中的温度、压力、气体种类、材料成分等因素都会影响离子氮化变形。
离子氮化变形对材料性能的影响主要表现在以下几个方面:1.影响氮化层的均匀性:离子氮化变形可能导致氮化层厚度不均,从而降低氮化层的性能。
2.影响材料的硬度:氮化层硬度是离子氮化的主要目的之一,离子氮化变形会降低氮化层的硬度。
3.影响材料的耐磨性:离子氮化处理后,材料的耐磨性通常会得到提高。
然而,离子氮化变形可能导致耐磨性降低。
4.影响材料的其他性能:离子氮化变形还可能影响材料的其他性能,如疲劳强度、韧性等。
为了降低离子氮化变形对材料性能的影响,可以采取以下措施:1.合理设定氮化工艺参数:根据材料的特性和氮化目的,合理选择温度、压力、气体种类等工艺参数。
2.控制氮化过程中的气氛:确保氮化过程中的气氛稳定,避免因气氛波动导致的离子氮化变形。
3.选择合适的材料和处理方法:针对不同材料,选择合适的氮化处理方法,以降低离子氮化变形的风险。
4.加强过程监控:对氮化过程进行实时监控,及时发现并处理可能导致的离子氮化变形问题。
总之,离子氮化变形是离子氮化过程中常见的问题,对材料性能产生不利影响。
解耦等离子体氮化沉积

解耦等离子体氮化沉积
解耦等离子体氮化沉积是一种新兴的氮化技术,也称为解耦等离子体化学气相沉积技术。
它是基于等离子体化学反应沉积技术的一种发展,但是引入了解耦等离子体技术,从而使得沉积的氮化膜具有更好的质量和均匀性。
在解耦等离子体氮化沉积过程中,首先是将反应气体加热至高温,然后将其引入反应室内。
接下来通过解耦等离子体技术将气体分解成离子,这些离子与底物表面进行反应,从而形成氮化膜。
这种技术可以制备出高质量的氮化膜,同时还可以使沉积速率更快,从而提高生产效率。
解耦等离子体氮化沉积技术具有许多优点。
首先,它可以制备出非常均匀和光滑的氮化膜,并且膜的厚度可以精密控制。
其次,解耦等离子体技术可以在低温下实现氮化沉积,从而避免了材料在高温下的脆性问题。
此外,解耦等离子体氮化沉积技术还可以在非平面和非晶态表面进行氮化沉积,从而拓宽了应用领域。
总的来说,解耦等离子体氮化沉积技术是一种非常有前途的氮化技术,具有高质量、均匀性好、沉积速率快等优点。
随着该技术的不断发展和完善,相信它将会在更广泛的领域得到应用。
热处理科普氮化知识
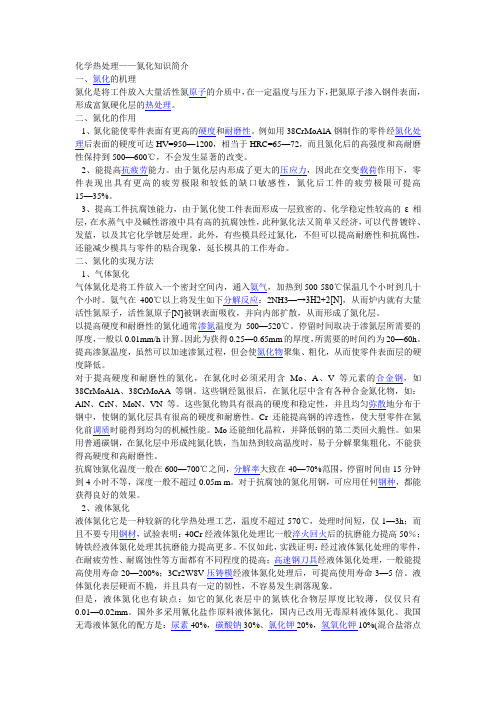
化学热处理——氮化知识简介一、氮化的机理氮化是将工件放入大量活性氮原子的介质中,在一定温度与压力下,把氮原子渗入钢件表面,形成富氮硬化层的热处理。
二、氮化的作用1、氮化能使零件表面有更高的硬度和耐磨性。
例如用38CrMoAlA钢制作的零件经氮化处理后表面的硬度可达HV=950—1200,相当于HRC=65—72,而且氮化后的高强度和高耐磨性保持到500—600℃,不会发生显著的改变。
2、能提高抗疲劳能力。
由于氮化层内形成了更大的压应力,因此在交变载荷作用下,零件表现出具有更高的疲劳极限和较低的缺口敏感性,氮化后工件的疲劳极限可提高15—35%。
3、提高工件抗腐蚀能力,由于氮化使工件表面形成一层致密的、化学稳定性较高的ε相层,在水蒸气中及碱性溶液中具有高的抗腐蚀性,此种氮化法又简单又经济,可以代替镀锌、发蓝,以及其它化学镀层处理。
此外,有些模具经过氮化,不但可以提高耐磨性和抗腐性,还能减少模具与零件的粘合现象,延长模具的工作寿命。
二、氮化的实现方法1、气体氮化气体氮化是将工件放入一个密封空间内,通入氨气,加热到500-580℃保温几个小时到几十个小时。
氨气在400℃以上将发生如下分解反应:2NH3—→3H2+2[N],从而炉内就有大量活性氮原子,活性氮原子[N]被钢表面吸收,并向内部扩散,从而形成了氮化层。
以提高硬度和耐磨性的氮化通常渗氮温度为500—520℃。
停留时间取决于渗氮层所需要的厚度,一般以0.01mm/h计算。
因此为获得0.25—0.65mm的厚度,所需要的时间约为20—60h。
提高渗氮温度,虽然可以加速渗氮过程,但会使氮化物聚集、粗化,从而使零件表面层的硬度降低。
对于提高硬度和耐磨性的氮化,在氮化时必须采用含Mo、A、V等元素的合金钢,如38CrMoAlA、38CrMoAA等钢。
这些钢经氮很后,在氮化层中含有各种合金氮化物,如:AlN、CrN、MoN、VN等。
这些氮化物具有很高的硬度和稳定性,并且均匀弥散地分布于钢中,使钢的氮化层具有很高的硬度和耐磨性。
不同氮化工艺对低碳钢离子镀铬的影响
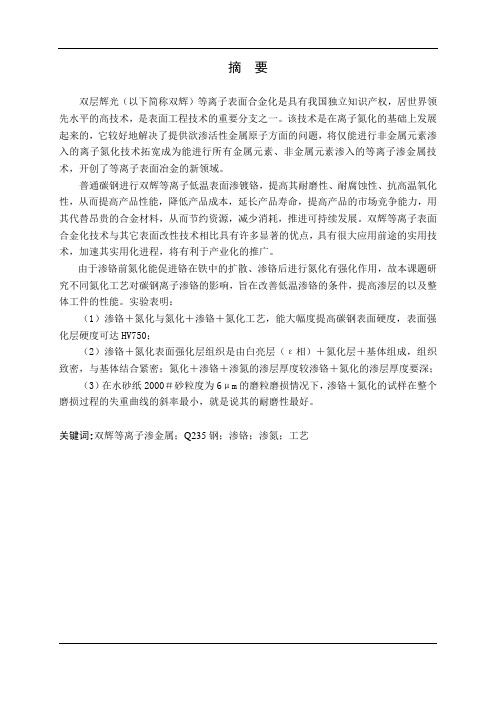
摘要双层辉光(以下简称双辉)等离子表面合金化是具有我国独立知识产权,居世界领先水平的高技术,是表面工程技术的重要分支之一。
该技术是在离子氮化的基础上发展起来的,它较好地解决了提供欲渗活性金属原子方面的问题,将仅能进行非金属元素渗入的离子氮化技术拓宽成为能进行所有金属元素、非金属元素渗入的等离子渗金属技术,开创了等离子表面冶金的新领域。
普通碳钢进行双辉等离子低温表面渗镀铬,提高其耐磨性、耐腐蚀性、抗高温氧化性,从而提高产品性能,降低产品成本,延长产品寿命,提高产品的市场竞争能力,用其代替昂贵的合金材料,从而节约资源,减少消耗,推进可持续发展。
双辉等离子表面合金化技术与其它表面改性技术相比具有许多显著的优点,具有很大应用前途的实用技术,加速其实用化进程,将有利于产业化的推广。
由于渗铬前氮化能促进铬在铁中的扩散、渗铬后进行氮化有强化作用,故本课题研究不同氮化工艺对碳钢离子渗铬的影响,旨在改善低温渗铬的条件,提高渗层的以及整体工件的性能。
实验表明:(1)渗铬+氮化与氮化+渗铬+氮化工艺,能大幅度提高碳钢表面硬度,表面强化层硬度可达HV750;(2)渗铬+氮化表面强化层组织是由白亮层(ε相)+氮化层+基体组成,组织致密,与基体结合紧密;氮化+渗铬+渗氮的渗层厚度较渗铬+氮化的渗层厚度要深;(3)在水砂纸2000#砂粒度为6μm的磨粒磨损情况下,渗铬+氮化的试样在整个磨损过程的失重曲线的斜率最小,就是说其的耐磨性最好。
关键词:双辉等离子渗金属;Q235钢;渗铬;渗氮;工艺AbstractDouble glow discharge plasma surface alloying process is plasma surface modification technology,which was invented by Chinese scholars have their own intellectual property rights.This technology was developed on the ion nitriding,it was better to provide wishes to solve the infiltration activity of metal atoms,will be only for non-metallic elements into the ion nitriding technology can be widened for all metal elements,non-metallic elements such as the infiltration of Metal Ion technology,creating a plasma surface metallurgy new areas.Of ordinary carbon steel double glow discharge Plasma Surface chromium plating to enhance the wear resistance, corrosion resistance, high temperature oxidation resistance and improve its product performance, reducing the cost of products to extend the lifespan of products, improving product competitiveness in the market. Replace it with expensive alloy materials to saving resources, reducing consumption and promoting sustainable development. Double glow discharge plasma surface alloying technology compared with the other surface modification technology ,it has many significant advantages ,it has the practical technologies’great of application, speed up the process of actually used, there will be conducive to the promotion of industrialization.Nitriding before the chromizing can promote the spread of the Chromium in the iron , nitriding can play a role in strengthening after chromizing, so the subject studys of the different c nitriding process’ effect in the ordinary carbon steel double glow discharge Plasma Surface chromium, the aimed to improving the conditions of the chromizing in the low temperature ,to improving the layer and the overall performance of the workpiece. Experiments show that:(1) The chromizing and nitriding’s and the second nitrid ing’s process, can greatly improve the carbon steel surface hardness ,and the hardness of the Strengthen surface layer is HV750;(2)The c hromizing and nitriding’s surface infiltration of the organization is composed of the white layer (ε phase) and the nitride layerand the Matrix. The organization is dense, and work closely with the matrix.The Layer thickness of the second nitriding is abysmal of the chromizing and nitriding’s(3) With the 2000 water of sandpaper (the Size is 6 μ m)of abrasive wear ,the weightlessness of the curve of the slope of the ch romizing and nitriding’s sample is smallest ,so its wearability is better .Key words: double glow discharge plasma surface alloying process; Q235steel; chromizing; nitriding; process目录引言 (1)1 资料综述 (2)1.1渗铬的国内外研究状况 (2)1.2渗铬的工业应用 (2)1.2.1抗腐蚀的应用 (2)1.2.2抗磨损的应用 (2)1.2.3抗高温氧化及高温腐蚀的应用 (3)1.3等离子渗金属技术 (3)1.3.1等离子体 (3)1.3.2离子氮化原理 (4)1.3.3辉光放电现象 (5)1.4双辉等离子渗金属技术 (7)1.4.1双辉等离子渗铬技术概况 (7)1.4.2 双辉等离子渗铬技术的物理过程 (8)1.4.3 双辉等离子渗铬特点 (8)1.5低温渗镀铬理论基础 (9)1.5.1. 铁材料渗铬的金属学理论基础 (9)1.5.2渗铬的表面改性理论基础 (11)1.6双辉等离子渗铬原理 (11)2 课题的提出 (13)2.1课题的提出 (13)2.2课题的研究内容 (13)2.3.课题的研究意义 (13)2.4技术路线 (13)2.5实施方案 (14)2.6课题的可行性分析 (14)3.试验工艺流程 (15)3.1材料的选择 (15)3.2工艺步骤 (15)3.2.1渗铬的工艺步骤 (15)3.2.2组织性能检测的工艺步骤 (15)4 实验结果与分析 (18)4.1渗层的显微硬度 (18)4.2渗层的显微组织 (19)4.3渗层相结构 (22)4.4摩擦磨损性能 (24)5 结论 (27)参考文献 (28)引言进入到20世纪,通过各种物理、化学机械或复合的方法,在材料表面制备涂层、薄膜或进行表面改性已发展为比较成熟、系统的工程技术并得到广泛应用,特别是近二三十年来,世界各国特别是先进工业国对表面技术提出更高、更特殊的要求:需要适应多种工作环境,尤其是十分恶劣的环境;具有较长的使用寿命,比以往的材料要更加耐磨损,耐腐蚀,耐高温氧化等等。
2024年离子束技术市场分析现状

2024年离子束技术市场分析现状离子束技术是一种重要的材料表面修饰和制造微纳器件的加工方法。
它利用离子束的高能量和高速度,在物料表面产生化学、物理反应,以改变材料的性质和形态。
离子束技术广泛应用于半导体制造、微电子器件制备、纳米材料合成等领域。
本文将对离子束技术市场的现状进行分析。
1. 行业背景和发展趋势离子束技术起源于20世纪50年代,经过几十年的发展,已经成为材料科学和微纳技术领域的重要工具。
随着科技的进步和相关领域的发展,离子束技术不断被应用于新的材料和器件制备领域。
目前,离子束技术的应用前景广阔,具有以下几个发展趋势:•半导体行业需求增加:随着集成电路的不断发展和需求的增加,半导体行业对高精度、高性能加工工艺的需求也在增加。
离子束技术可以实现高精度的纳米加工,满足半导体行业对器件制备的要求。
•新兴材料加工需求增长:随着新材料的不断涌现,如二维材料、纳米材料等,对相关加工技术的需求也在增长。
离子束技术能够对这些新材料进行精确加工,提供更多的制备手段。
•微纳米器件制备需求增强:微纳米器件在信息技术、生物医药、能源等领域具有广泛的应用前景。
离子束技术作为一种重要的微纳加工方法,能够实现高精度、高分辨率的器件制备,满足越来越复杂的需求。
2. 市场规模和市场竞争离子束技术市场规模逐年增长,根据市场研究机构的数据,预计未来几年离子束技术市场将保持稳定增长。
目前,该市场主要由少数几家领先厂商垄断,市场竞争激烈。
离子束技术市场的主要参与者包括设备制造商和材料供应商。
设备制造商根据市场需求研发和提供离子束设备,包括离子束刻蚀机和离子注入机等。
材料供应商则提供用于离子束加工的材料,如半导体材料、陶瓷材料等。
在市场竞争方面,领先厂商通过提供先进的技术、高性能的设备和可靠的售后服务来占据市场份额。
同时,他们还与研究机构和大学进行紧密合作,推动技术的进一步创新。
3. 市场应用和前景展望离子束技术在各个领域都有广泛的应用,主要包括以下几个方面:•半导体制造:离子束技术在半导体行业中用于半导体材料的刻蚀、离子注入、表面修饰等过程,以实现集成电路的制备。
- 1、下载文档前请自行甄别文档内容的完整性,平台不提供额外的编辑、内容补充、找答案等附加服务。
- 2、"仅部分预览"的文档,不可在线预览部分如存在完整性等问题,可反馈申请退款(可完整预览的文档不适用该条件!)。
- 3、如文档侵犯您的权益,请联系客服反馈,我们会尽快为您处理(人工客服工作时间:9:00-18:30)。
离子氮化技术现状与发展趋势陈立奇,朱文明(1江苏丰东热技术股份有限公司,江苏,大丰,224100;)摘要:通过分别介绍离子氮化的热处理设备、技术人员、产品结构、工艺流程以及该技术对环境的影响综述了国内外离子氮化热处理技术现状,最后针对国内外的研究现状提出离子氮化热处理技术方面的未来发展方向。
关键词:离子氮化;等离子热处理The Development Tendency and the State of Plasma NitrideChen Li-qi,Zhu Wen-ming(1Jiangsu fengdong thermal technology Co,Ltd,Jiangsu,Da feng,224100) Abstract:The state of Plasma Nitride technology of domestic heavy forgings was overviewed in this paper,such as f Plasma Nitride equipment,the technical personnel,the product structure, process and impact of Plasma Nitride on environment.And based on the domestic research status of Plasma Nitride,the research development tendency in the future is also put forward.Keywords:Plasma Nitride,Plasma heat treatment0前言离子氮化属于等离子热处理的范畴,也是渗氮化学热处理中的一种。
它是利用稀薄气体辉光放电形成活性氮离子,在直流电场中对工件进行热处理的一种表面改性技术。
相比于气体渗氮,离子氮化具有清洁无公害、渗速快、节能省气、畸变小、渗层组成可调、处理温度范围广(从380-850℃)等优点,已被广泛用于碳素结构钢、合金结构钢、工模具钢、不锈钢、球墨铸铁、灰口铸铁、钛合金、粉末冶金等材料的表面强化[1,8-12]。
1离子氮化设备离子氮化设备一般包括电气控制系统、真空炉体、渗剂气体配气系统、真空产生和维持系统、真空测量及控制系统、测温及控温系统等部分组成。
离子氮化设备应配备有电压、电流、温度、真空度及气体流量的测量指示仪表,对这些参数应能进行控制和记录。
现在发展趋势是使用斩波器及IGBT逆变型脉冲电源。
电气系统大多采用三相半控2组桥串联负边调压的可控硅整流电路,输出0-1000V连续可调的直流电源。
国内正逐步推广使用脉冲电源式离子氮化炉,其核心是直流斩波器。
脉冲电源是指提供的电压、电流是具有一定周期的近似方波的脉冲,工作频率固定,而脉冲宽度可调。
根据不同工件,可适当调整脉冲宽度,以达到清洗工件及保护工件表面的作用[1]。
2离子氮化技术人员国家政策“重冷轻热”,热处理车间现场环境较差,热处理人员待遇低,国民经济发展各环节不均衡,这些现实因素造成了国内热处理与世界发达国家的差距较大,形成所谓的“人才短板”效应。
目前,热处理技术及质量人员一般以大中专高校培养的专业技术人才为主。
完全按照现场的实际经验来完成工艺制定和技术指导的时代已经过去,现在大多数热加工企业对刚毕业的材料加工或热处理专业的大学生比较青睐,虽然他们的经验方面可能较欠缺,但他们的理论知识比较丰富,假以时日的培养与一线锻炼,理论与实践的有机结合,这些大学生也逐渐成长为企业的中高层技术骨干。
对于一直从生产一线训练有素的操作工,也是企业培养人才的一条重要途径,对于他们来讲,要从实践经验中提炼出可以用于指导实践的理论,也是一个较大的能力提升。
据不完全统计,现在材料专业的毕业生毕业后从事热处理方向工作的仅仅占0.67%,热处理行业的人才储备形势非常严峻。
而这0.67%的材料毕业生能够鼓足勇气来从事热处理方面的工作,也需要现在的企业管理人员的大力支持,而不是去持续打压,持续忽悠。
离子氮化技术人员应了解工件的上道工序(预备热处理)及下道工序(精加工),对产品的信息需要把握清楚,需要和原材料、锻造、锻后热处理、机加工等工序人员进行有效沟通,及时了解其下道工序的机加工方式及要求,为产品实现质量控制打下良好的基础。
3离子氮化产品结构离子氮化产品已广泛应用在机械制造、交通运输机械、动力机械、轻工机械和医疗器械等方面的中小负荷、精度高,渗氮后很少留磨量或不留磨量。
尤其是对那些耐疲劳、耐磨损的零件效果较为明显。
近年来,不锈钢、工模具钢与Ti及Ti合金的离子氮化及逐步成为离子氮化的应用范畴。
张国庆[4]等对0C r17N i12M o2奥氏体不锈钢试样在不同参数下进行等离子渗氮,结果表明,在炉内气压0.4kPa,渗氮温度350℃,渗氮12h,试样表面平均硬度能达到1000HV0.1以上,且具有较强的耐腐蚀性能。
吴凯[3]等对2Cr13不锈钢进行稀土催渗循环离子渗氮试验,并和常规离子渗氮进行对比研究。
结果表明:稀土催渗循环离子渗氮工艺加快渗氮速度,提高耐磨性;使渗氮层的表面硬度提高、显微硬度梯度变得平缓,渗氮效果随循环次数增加而愈好;还能优化2Cr13不锈钢渗氮层的相组成;添加到渗氮气氛中的纯稀土La存在于渗层中,既验证La的催渗效果,La起到一定的微合金化作用。
王瑞金[17]等针对常用的工模具材料,在不同的电流类型、气体气氛、渗氮温度、加氩工艺下进行离子渗氮处理,并对试件进行金相分析和硬度测量。
试验表明,带窄缝工模具,用IGBT逆变型脉冲电源的离子渗氮工艺较为合理;加氩工艺有利于减小表面ε层和增加渗氮层的硬度和厚度。
焦艳军[16]等研究等离子渗氮对钛表面的组织结构、性能及对变形链球菌黏附的影响。
结果表明,等离子渗氮表面处理仅使纯钛表面粗糙度略微增加,并均在0.2μm以下;等离子渗氮表面处理后材料表面的原始划痕消失;GDS检测分析结果表明,等离子渗氮表面处理后,表面主要由氮化钛化合物组成;经渗氮处理后,纯钛黏附细菌的量显著减少。
4离子氮化工艺设计一般认为,离子氮化处理的工序流程包括预备热处理——清洗——装炉——屏蔽——打弧升温——保温——冷却出炉。
4.1碳钢和铸铁碳钢和铸铁的离子氮化温度范围为540-570℃,氮化时间主要取决于硬化层DN或渗层深度,氮化气氛可以选择氨气加甲烷、丙烷、二氧化碳等,气体压强一般100-1000Pa,气体流量一般0.05-1.2L/min,合理调节气体比例可以调节化合物层的相组成及厚度。
4.2合金结构钢合金结构钢的离子氮化温度范围为510-540℃,氮化时间主要取决于硬化层DN或渗层深度,氮化气氛可以选择氨气或N2+H2,气体压强一般100-1000Pa,气体流量一般0.3-1.2L/min。
4.3工模具钢工模具钢的离子氮化温度范围为520-560℃,氮化时间主要取决于硬化层DN或渗层深度,氮化气氛可以选择氨气或N2+H2,气体压强一般100-3000Pa,气体流量一般0.3-1.2L/min。
4.4不锈钢不锈钢的离子氮化温度范围为560-620℃,氮化时间主要取决于硬化层DN或渗层深度,氮化气氛可以选择氨气或N2+H2,气体压强一般100-1000Pa,气体流量一般0.3-1.2L/min。
4.5纯Ti及Ti合金纯Ti和Ti合金的离子氮化温度范围为800-900℃,氮化时间主要取决于硬化层DN或渗层深度,氮化气氛可以选择N2或N2+Ar,气体压强一般100-1000Pa,气体流量一般0.3-1.2L/min。
5离子氮化处理对环境的影响离子氮化过程的氨气消耗量仅仅为气体氮化的百分之一。
由于离子氮化处理利用辉光放电对工件加热,其处理温度较低,比间接加热方式节能40%-70%。
6离子氮化技术的发展趋势6.1多元共渗技术为了提高碳钢和铸铁的硬度和耐磨性,降低脆性和减小变形,发展了以离子氮化为主的多元共渗技术,如S-N-C共渗层可以明显改善耐磨性和抗胶合能力;O-N-C共渗层可提高耐蚀性和摩擦磨损时的承载能力[8-12]。
6.2离子氮化辅助复合处理经过等离子渗氮后镀类金刚石涂层复合处理的H13钢表面硬度、膜/基结合强度、耐磨性能等均优于未氮化镀类金刚石涂层的样品;离子渗氮后渗铬的复合渗铬工艺能在低温短时间内能获得较为致密的纳米结构渗铬层,可以减小工件变形。
其他复合处理有离子渗氮-PCVD、离子渗氮-氧化复合处理、离子渗氮-激光复合处理,离子渗氮-淬火等[14-16]。
6.3ASPN技术活性屏离子渗氮(ASPN)是在真空室内安装一个与阴极高压相接的金属网状圆筒作为活性屏,工件置于活性屏内。
通过气体离子轰击活性屏,并使其加热活,再通过活性屏的热辐射将工件加热到渗氮温度。
在渗氮过程中,工件被活性屏包围着处于电悬浮状态,离子轰击活性屏而不轰击工件表面,从而解决了直流离子渗氮技术存在的边缘效应、空心阴极效应、打弧等问题。
利用活性屏离子渗氮技术可以处理不同形状的工件,能方便地测量工件的温度,能处理奥氏体不锈钢等较难氮化的材料[2,6]。
6.4空心阴极辅助离子渗氮技术研究空心阴极辅助离子渗氮技术可有效地对样品进行渗氮,避免弧光的产生而破坏表面光洁度,渗氮可以在压力很小的情况下进行,减小了氨气的使用量与尾气排放量,节省能源,减小污染[8,10]。
6.5快速离子渗氮技术常规离子渗氮DN≤0.6mm,而对于0.8-1.2mm的深层离子氮化,需要发展快速离子氮化技术。
真空高压渗氮可实现38CrMoAl保温时期渗速至0.03-0.04mm/h,40Cr保温时期渗速提高至0.06-0.08mm/h。
稀土催渗循环离子渗氮(约15h)比常规离子渗氮(约25h)渗层白亮层较小,总渗层更深。
冷塑性变形加上稳定化回火处理后渗氮速度提高1倍,耐磨性、疲劳强度及接触疲劳寿命均有提高[6-8]。
参考文献1中国机械工程协会热处理协会.热处理手册(第四版)第3卷热处理设备和工辅材料.北京,机械工业出版社,2008年1月2韩莉,赵程.40Cr钢富氮层快速离子渗氮技术的探索[J].材料热处理学报,2009,30(4):124-128.3吴凯,刘国权,王蕾.2Cr13不锈钢的稀土催渗循环离子渗氮工艺研究[J].材料热处理学报,2008,2:131-135.4张国庆,沈丽如,金亚凡.0Cr17Ni12Mo2奥氏体不锈钢低温等离子渗氮工艺研究[J].金属热处理,2008,33(8):138-141.5李红革.常用渗氮材料的调质硬度对渗氮层性能的影响[J].国外热处理,2005,8:26-28.6韩莉,赵程.富氮层快速离子渗氮工艺及机理研究[J].材料热处理学报,2009,10:187-191.7陈玮,王蕾,周磊.钢的快速渗氮技术研究现状[J].武汉科技大学学报,2006,29(3):225-229. 8龙发进,周祎,康广宇.离子渗氮新技术的研究现状[J].热加工工艺,2007,36(6):61-65. 9黄玉堂,周上祺,刘林飞.离子渗氮技术及其进展[J].热处理装备与技术,2008,29(1):48-51.10高仰之,刘英祺.离子渗氮技术的进展[J].机械工人,2003,7:9-11.11郑辉.离子渗氮技术的进展[J].机械工人,2007,9:47-49.12马贵成.离子氮化技术及应用[J].煤矿机械,2004,7:69-70.13李杨,徐久军,王亮.42CrMo钢表面纳米化对离子渗氮的影响[J].中国表面工程,2010,3:60-63.14伍翠兰,元敏,陈汪林.20钢氮化表面500℃盐浴镀铬微观组织结构分析[J].湖南大学学报(自然科学版).2010年第37卷第9期15侯惠君,代明江,林松盛.H13等离子渗氮-类金刚石膜复合处理的性能研究[J].材料研究及应用.2010年第4卷第1期16焦艳军,王珏,金恩龙.等离子渗氮表面处理对纯钛材料细菌黏附能力的影响.口腔颌面修复学杂志.2009年1月第10卷第1期17王瑞金,喻彩丽.离子渗氮工艺对工模具质量的影响.热加工技术.2003年第5期。