螺杆压缩比和螺槽深度
挤出机螺杆参数及影响
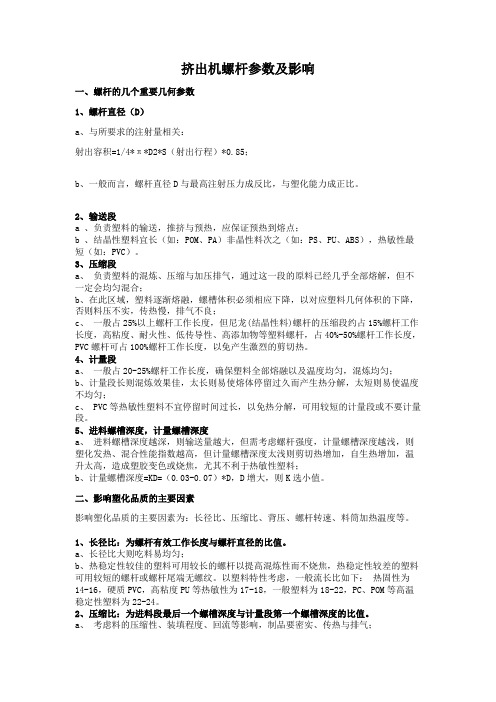
挤出机螺杆参数及影响一、螺杆的几个重要几何参数1、螺杆直径(D)a、与所要求的注射量相关:射出容积=1/4*π*D2*S(射出行程)*0.85;b、一般而言,螺杆直径D与最高注射压力成反比,与塑化能力成正比。
2、输送段a 、负责塑料的输送,推挤与预热,应保证预热到熔点;b 、结晶性塑料宜长(如:POM、PA)非晶性料次之(如:PS、PU、ABS),热敏性最短(如:PVC)。
3、压缩段a、负责塑料的混炼、压缩与加压排气,通过这一段的原料已经几乎全部熔解,但不一定会均匀混合;b、在此区域,塑料逐渐熔融,螺槽体积必须相应下降,以对应塑料几何体积的下降,否则料压不实,传热慢,排气不良;c、一般占25%以上螺杆工作长度,但尼龙(结晶性料)螺杆的压缩段约占15%螺杆工作长度,高粘度、耐火性、低传导性、高添加物等塑料螺杆,占40%-50%螺杆工作长度,PVC螺杆可占100%螺杆工作长度,以免产生激烈的剪切热。
4、计量段a、一般占20-25%螺杆工作长度,确保塑料全部熔融以及温度均匀,混炼均匀;b、计量段长则混炼效果佳,太长则易使熔体停留过久而产生热分解,太短则易使温度不均匀;c、 PVC等热敏性塑料不宜停留时间过长,以免热分解,可用较短的计量段或不要计量段。
5、进料螺槽深度,计量螺槽深度a、进料螺槽深度越深,则输送量越大,但需考虑螺杆强度,计量螺槽深度越浅,则塑化发热、混合性能指数越高,但计量螺槽深度太浅则剪切热增加,自生热增加,温升太高,造成塑胶变色或烧焦,尤其不利于热敏性塑料;b、计量螺槽深度=KD=(0.03-0.07)*D,D增大,则K选小值。
二、影响塑化品质的主要因素影响塑化品质的主要因素为:长径比、压缩比、背压、螺杆转速、料筒加热温度等。
1、长径比:为螺杆有效工作长度与螺杆直径的比值。
a、长径比大则吃料易均匀;b、热稳定性较佳的塑料可用较长的螺杆以提高混炼性而不烧焦,热稳定性较差的塑料可用较短的螺杆或螺杆尾端无螺纹。
螺杆的基本参数

螺杆的基本参数————————————————————————————————作者:————————————————————————————————日期:一般螺杆分为三段即加料段,压缩段,均化段。
加料段——底经较小,主要作用是输送原料给后段,因此主要是输送能力问题,参数(L1,h1),h1=(0.12-0.14)D。
压缩段——底经变化,主要作用是压实、熔融物料,建立压力。
参数压缩比ε=h1/h3及L2。
准确应以渐变度A=(h1-h3)/L2。
均化段(计量段)——将压缩段已熔物料定量定温地挤到螺杆最前端、参数(L3,h3),h3=(0.05-0.07)D。
对整条螺杆而言,参数L/D-长径比L/D利弊:L/D与转速n,是螺杆塑化能力及效果的重要因素,L/D 大则物料在机筒里停留时间长,有利于塑化,同时压力流、漏流减少,提高了塑化能力,同时对温度分布要求较高的物料有利,但大之后,对制造装配使用上又有负面影响,一般L/D为(18~20),但目前有加大的趋势。
其它螺距S,螺旋升角φ=πDtgφ,一般D=S,则φ=17°40′。
φ对塑化能力有影响,一般来说φ大一些则输送速度快一些,因此,物料形状不同,其φ也有变化。
粉料可取φ=25°左右,圆柱料φ=17°左右,方块料φ=15°左右,但φ的不同,对加工而言,也比较困难,所以一般φ取17°40′。
棱宽e,对粘度小的物料而言,e尽量取大一些,太小易漏流,但太大会增加动力消耗,易过热,e=(0.08~0.12)D。
规格:公制螺纹外径是以毫米为单位,如6,8,10,12,18,20毫米等等螺距也是以毫米为单位,如0.5,0.75,1,1.5,2,3,等等英制螺纹外径是以英寸为单位,(每英寸等于25.4毫米)如3/16,5/8,1/4,1/2,等等所以用公制卡尺量外径读数常带不规则的小数。
英制螺距是用每英寸含多少个牙表示。
挤塑机螺杆的的基本参数

挤塑机螺杆的的基本参数1、螺杆直径Ds 螺杆直径即螺纹的外径,挤塑机的生产能力(挤塑量)近似与螺杆直径的平方成正比,在其它条件相同时,螺杆直径少许增大,将引起挤出量的显著增加,其影响甚至比螺杆转数的提高对挤出量的影响还大。
故常用螺杆直径来表征挤塑机规格大小的技术参数。
2、螺杆长径比L/Ds 螺杆工作部分长度L与螺杆直径Ds之比称为长径比,在其它条件一定时(如螺杆直径),增大长径比就意味着增加螺杆的长度。
L/Ds值大,温度分布合理有利于塑料的混合和塑化,此时塑料在机筒中受热的时间也较长,塑料的塑化将充分、更均匀。
从而提高机塑质量。
如果在塑化质量要求不变的前提下,长径比增大后,螺杆的转速可提高,从而增加了塑料的挤出量。
但是,选择过大的长径比,螺杆消耗的功率将相应增大,而且螺杆和机筒的加工和装配鸡难度增加;螺杆弯曲的可能性也会增加,将会引起螺杆与机筒内壁的刮磨,降低使用寿命。
另外,对于热敏性塑料,过大的长径比因停留时间长而热分解,影响塑料的塑化和挤出质量。
因此,在充分利用长径比加大后的优点,选取时要根据加工塑料的物理性能和对产品的挤塑质量要求而定。
3、压缩比ε亦称为螺杆的几何压缩比,是螺杆加料段第一个螺槽容积与均化段最后一个螺槽容积之比。
它是由塑料的物理压缩比――即制品的密度与进料的表现密度之比来决定的。
使挤塑机压缩比较大,目的是为了使颗粒状塑料能充分塑化、压实。
加工塑料的种类不同时,压缩比的选择也应不同。
按压缩比来分,螺杆的型式可分为三种:等距不等深、等深不等距、不等深不等距。
其中等距不等深是最常用的一种,这种螺杆加工容易,塑料与机筒的接触面积大,传热效果好。
信息来源:东莞华鸿塑料机械厂。
螺杆设计质量的标准1
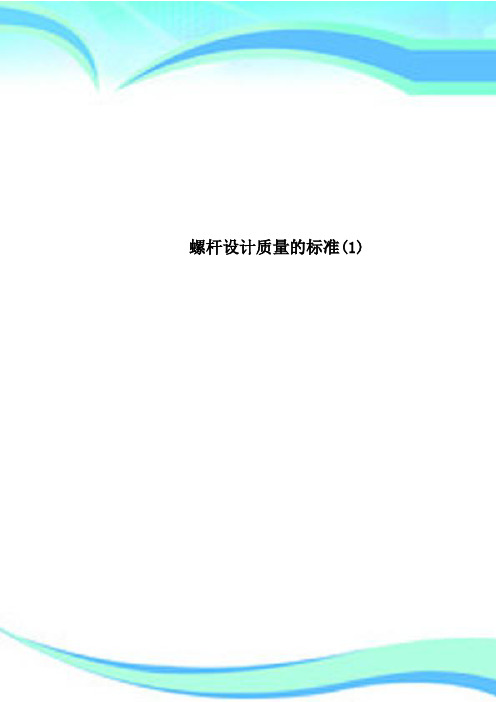
螺杆设计质量的标准(1)————————————————————————————————作者: ————————————————————————————————日期:1.1螺杆设计质量的标准螺杆和料筒组成了挤出机的挤压系统。
为说明挤压系统的重要性,人们通常称之为挤出机的心脏。
塑料(橡胶)正式在这一部分由玻璃态转变为黏流态,然后通过口模、辅机而被做成各种制品的。
由挤出过程分析可以看出,至少应当从以下几个方面评价螺杆:(一)产量所谓产量是指在保证塑化质量的前提下,通过给定机头的产量或挤出量。
如前所述,产量一般用公斤/小时或公斤/转来表示。
一根好的螺杆,应当具有较高的塑化能力。
(生产能力)应当指出,低温挤出是目前的一个发展趋势,它能改善挤出制品的质量(如降低内应力等),防止热敏性物料过热分解,降低能量消耗,减少主辅机冷却系统的负担,提高生产率。
ﻫ(二)塑化质量一根螺杆首先必须能生产出合乎质量要求的制品。
所谓合乎质量要求是指所生产的制品应当合乎以下几个方面的要求:ﻫ 1.具有合乎要求的各种性能。
具有合乎规定的物理、化学、力学、电学性能;2、具有合乎要求的表观质量。
如能达到用户对气泡、晶点、染色分散均匀性的要求等。
3、具有合乎要求的螺杆的塑化质量:(1)螺杆所挤出的熔体温度是否均匀,轴向波动、径向温差多大。
(2)是否有得以成型的最低的熔体温度。
(3)挤出的熔体是否有压力波动。
染色和其它填加剂的分散是否均匀等。
(三)单耗单耗,是指每挤出一公斤塑料(橡胶)所消耗的能量,一般用N来表示。
其中N为功率(千瓦),Q为产量(公斤/小时)。
这个数值越大,表示塑化同样重量的塑料(橡胶)所需要的能量越多,即意味着所耗费的加热功率越多,电机所做的机械功通过剪切和摩擦热的形式进入物料越多。
反之亦然。
一根好的螺杆,在保证塑化质量的前提下,单耗应尽可能低。
(四)适应性所谓螺杆的适应性是指螺杆对加工不同塑料、匹配不同机头和不同制品的适应能力。
挤出机螺杆的几个重要几何参数

挤出机螺杆的几个重要几何参数作者:-1、螺杆直径(D)a、与所要求的注射量相关:射出容积=1/4*π*D2*S(射出行程)*0.85;b、一般而言,螺杆直径D与最高注射压力成反比,与塑化能力成正比。
2、输送段a 、负责塑料的输送,推挤与预热,应保证预热到熔点;b 、结晶性塑料宜长(如:POM、PA)非晶性料次之(如:PS、PU、ABS),热敏性最短(如:PVC)。
3、压缩段a、负责塑料的混炼、压缩与加压排气,通过这一段的原料已经几乎全部熔解,但不一定会均匀混合;b、在此区域,塑料逐渐熔融,螺槽体积必须相应下降,以对应塑料几何体积的下降,否则料压不实,传热慢,排气不良;c、一般占25%以上螺杆工作长度,但尼龙(结晶性料)螺杆的压缩段约占15%螺杆工作长度,高粘度、耐火性、低传导性、高添加物等塑料螺杆,占40%50%螺杆工作长度,PVC螺杆可占100%螺杆工作长度,以免产生激烈的剪切热。
4、计量段a、一般占2025%螺杆工作长度,确保塑料全部熔融以及温度均匀,混炼均匀;b、计量段长则混炼效果佳,太长则易使熔体停留过久而产生热分解,太短则易使温度不均匀;c、 PVC等热敏性塑料不宜停留时间过长,以免热分解,可用较短的计量段或不要计量段。
5、进料螺槽深度,计量螺槽深度a、进料螺槽深度越深,则输送量越大,但需考虑螺杆强度,计量螺槽深度越浅,则塑化发热、混合性能指数越高,但计量螺槽深度太浅则剪切热增加,自生热增加,温升太高,造成塑胶变色或烧焦,尤其不利于热敏性塑料;b、计量螺槽深度=KD=(,D增大,则K选小值。
二、影响塑化品质的主要因素影响塑化品质的主要因素为:长径比、压缩比、背压、螺杆转速、料筒加热温度等。
1、长径比:为螺杆有效工作长度与螺杆直径的比值。
a、长径比大则吃料易均匀;b、热稳定性较佳的塑料可用较长的螺杆以提高混炼性而不烧焦,热稳定性较差的塑料可用较短的螺杆或螺杆尾端无螺纹。
以塑料特性考虑,一般流长比如下:热固性为1416,硬质PVC,高粘度PU等热敏性为1 718,一般塑料为1822,PC、POM等高温稳定性塑料为2224。
螺杆的功能及选型
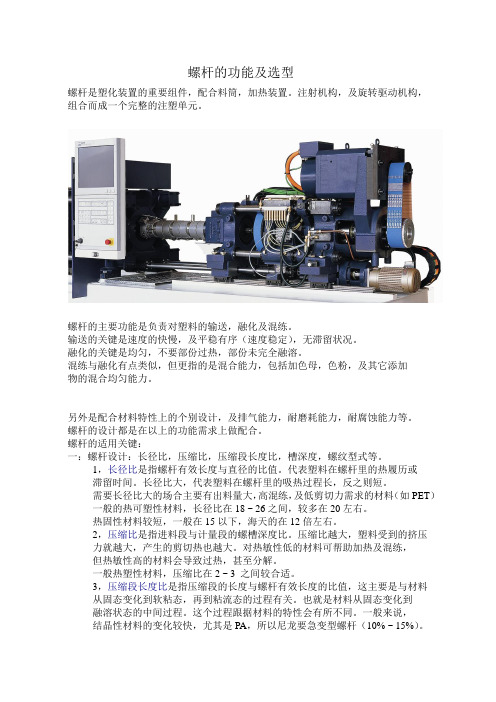
螺杆的功能及选型螺杆是塑化装置的重要组件,配合料筒,加热装置。
注射机构,及旋转驱动机构,组合而成一个完整的注塑单元。
螺杆的主要功能是负责对塑料的输送,融化及混练。
输送的关键是速度的快慢,及平稳有序(速度稳定),无滞留状况。
融化的关键是均匀,不要部份过热,部份未完全融溶。
混练与融化有点类似,但更指的是混合能力,包括加色母,色粉,及其它添加物的混合均匀能力。
另外是配合材料特性上的个别设计,及排气能力,耐磨耗能力,耐腐蚀能力等。
螺杆的设计都是在以上的功能需求上做配合。
螺杆的适用关键:一:螺杆设计:长径比,压缩比,压缩段长度比,槽深度,螺纹型式等。
1,长径比是指螺杆有效长度与直径的比值。
代表塑料在螺杆里的热履历或滞留时间。
长径比大,代表塑料在螺杆里的吸热过程长,反之则短。
需要长径比大的场合主要有出料量大,高混练,及低剪切力需求的材料(如PET)一般的热可塑性材料,长径比在18 ~ 26之间,较多在20左右。
热固性材料较短,一般在15以下,海天的在12倍左右。
2,压缩比是指进料段与计量段的螺槽深度比。
压缩比越大,塑料受到的挤压力就越大,产生的剪切热也越大。
对热敏性低的材料可帮助加热及混练,但热敏性高的材料会导致过热,甚至分解。
一般热塑性材料,压缩比在2 ~ 3 之间较合适。
3,压缩段长度比是指压缩段的长度与螺杆有效长度的比值,这主要是与材料从固态变化到软粘态,再到粘流态的过程有关。
也就是材料从固态变化到融溶状态的中间过程。
这个过程跟据材料的特性会有所不同。
一般来说,结晶性材料的变化较快,尤其是PA,所以尼龙要急变型螺杆(10% ~ 15%)。
而非结晶性材料的变化较慢,例如PMMA,所以PMMA的压缩段要较长(可达50%)。
而一般的通用型螺杆约20% ~ 30%。
压缩段太短会使材料来不及转化,而形成堵塞,产生高压,导致过热烧焦。
太长会形成空洞,混入气体,导致射胶不稳,有气纹等。
4,槽深是指螺顶到螺底的高度。
螺杆压缩比和螺槽深度

• 螺杆其它参数的选取与确定 a.螺纹宽度 e太小会使漏流量增加,消弱螺 棱强度,降低产量;e太大,增加动力消耗, 有局部过热的危险,故要适当选取。 由经验公式 (0.08~0.12)D b.螺距S
e.螺杆的转速范围:根据电动机和传动系统 的工作特性知螺杆的转速范围是n=(0~150) r/min
• • • • •
一般固体输送的分析都用到这五条假设: 压力仅为顺螺槽距离的函数; 摩擦系数与压力无关; 重力不计; 离心力不计; 固体塞中的密度变化不计。
在开槽机筒中形成的挤出压力趋势图
二、熔融理论
• 固体物料充满螺槽 →→→→ 形成熔膜→→
• →→→→→→→→→→ 螺纹刮下熔体进入 熔池
• 螺杆压缩比和螺槽深度 确定几何压缩比 i 等距不等深(通用型)螺杆压缩比的计算 式如下:
对于大多取经验数据来确定,通用公式 H3=(0.025~0.06)Ds。 再根据确定的螺杆压缩比计算加料段螺杆槽 深度。
• 螺杆各段的确定 高聚物在螺杆中的挤出过程,实际上经历 固体输送,熔融和均化的过程。所以一般 螺杆都设计成三段:加料段,压缩段及均 化段。 螺纹断面形状及螺杆头部型式 由实验用挤出机的使用特性及要求,确定 螺杆头部型式为: 梯行螺纹的断面的倾斜角α=10°~15°, 圆弧半径取(0.07~0.13),常用于小直螺 杆上。
4
C.螺杆的强度计算 a.由轴向力产生的压应力 c
c =
D 2 (1.15 ~ 1.25) Pmax 4 2 2 (d s d 0 ) 4
C= ds c. 由螺杆自重G产生的弯曲应力:
d0
b =
M b L2 (D ds )2 3 Wb ds (1 C 4 )
பைடு நூலகம்
螺杆挤出机基本结构

1、规格尺寸
螺杆直径D :Db —螺杆外径
Ds —螺杆根径
D —螺杆平均直径
螺杆长度L :L —螺杆有效工作部分长度 L= L1 + L2 + L3
L1—加料段长度 L2—压缩段长 L3—均化段长度
螺杆长径比 L/D
塑料在普通单螺杆挤出机中的挤出过程
2、螺槽尺寸
宽度:B —螺槽轴向宽度
W —螺槽法向宽度
深度:H1(h1)—加料段深度
H2(h2)—压缩段深度
H3(h3)—均化段深度
压缩比ε:加料段第一个螺槽容积与均化段最 后一个螺槽容积之比 渐变度A : 描述螺槽深度变化的几何参数,
3、螺纹尺寸
螺纹头数 i
螺旋升角ϕ ( ϕ b , ϕ s , ϕ )
螺旋线展开长度 Z ( Zb , Zs ,Z )
螺纹导程 t , 螺距 S
螺棱宽度
e —螺棱轴向宽度
e ’—螺棱法向宽度,e ’= e cos ϕ
螺纹展开图(i=2)
4、螺杆的安装尺寸
螺杆与机筒内壁的间隙 δ。
- 1、下载文档前请自行甄别文档内容的完整性,平台不提供额外的编辑、内容补充、找答案等附加服务。
- 2、"仅部分预览"的文档,不可在线预览部分如存在完整性等问题,可反馈申请退款(可完整预览的文档不适用该条件!)。
- 3、如文档侵犯您的权益,请联系客服反馈,我们会尽快为您处理(人工客服工作时间:9:00-18:30)。
.
12
• 螺杆其它参数的选取与确定
a.螺纹宽度 e太小会使漏流量增加,消弱螺 棱强度,降低产量;e太大,增加动力消耗, 有局部过热的危险,故要适当选取。
由经验公式 (0.08~0.12)D
b.螺距S
e.螺杆的转速范围:根据电动机和传动系统
的工作特性知螺杆的转速范围是n=(0~150)
r/min
.
13
螺纹断面形状及螺杆头部型式
由实验用挤出机的使用特性及要求,确定 螺杆头部型式为:
梯行螺纹的断面的倾斜角α=10°~15°, 圆弧半径取(0.07~0.13),常用于小直螺 杆上。
.
11
• 螺杆的螺纹头数 在螺杆直径,螺槽深度和螺纹升程相等的条件下, 多头螺纹与单头螺纹相比,多头螺纹对物料的正 推力大,攫取物料的能力较强,并可降低熔料的 倒流现象。但是,整个螺杆都是多头螺纹时,物 料分别从螺杆料斗区几条螺槽通道进入到达螺杆 头部。在料斗区,往往由于几条螺槽的进料不均 匀和各条螺槽的熔融均化和对溶料输送能力不一 致,容易引起生产能力波动,压力波动。其结果 是制品质量下降。但是有时为了提高某一段的工 作能力,单独在某一段上设置多头螺纹。如单头 螺纹的螺杆,为了提高加料段攫取物料的能力, 加料段设置双头螺纹,提高固体输送能力。采用 单头螺纹的螺杆。
(0.125~0.25)P1
则:
PZ=(1.125~1.25)D 2 p 4
.
16
C.螺杆的强度计算
a.由轴向力产生的压应力 c
c =
D2
(1.15 ~ 1.25)Pmax 4
4
(d s 2
d02 )
.
17
C=
d0 ds
c. 由螺杆自重G产生的弯曲应力:
b =
Mb L2(Dds)2
Wb ds3(1C4)
- 螺杆材料比重
.
18
d.螺杆的合成应力,对塑性材料合成应力用 等强度理论计算
= 242 p
c b [ p ]= s n
.
19
3.7.4机筒的强度计算
机筒内部受熔料的压力作用,物料在机筒内 产生压力沿机筒轴向的分布是相当复的, 各处压力不等,因机头压力最大,故一般 取机头压力为计算压力值。并且由于机筒 外径与内径之比大于1.1, 所以用厚壁圆筒理 论来进行强度计算。
机筒间隙正常,机头最大压力可由下式计
算:
pmax
6 L3Dn h32 tan
其中:
螺杆直径D
h 3 挤出段长度挤段的螺
槽深度 螺旋角 =17.7º 物料粘度
.
15
B、螺杆轴向力的确定
螺杆轴向力: Pz P1P2
物料作用在螺杆端面上的总压力P1 = D2 p 4 动载荷产生的附加压力的轴向分量 P2 =
.
7
螺杆长径比 L/D
故螺杆工作部分长度L螺杆长径比的增加有以 下的好处:
• 螺杆加压充分可以提高塑料制品的物理机 械性能。
• 可以提高塑化的质量,使制品的外观质量 更好。
• 螺杆特性曲线斜率小,挤出量稳定,切挤 出量能提高20%—40%。
• 有利于类似于PVC粉料挤管的成型。
.
8
但螺杆长径比过大,会使螺杆加工及 装配困难,功率消耗也会有所增加, 加大悬臂端自重的弯曲,以至螺杆头 部与筒壁间隙的不均匀,甚至造成磨 刮筒壁,降低螺杆与机筒的寿命。
.
9
• 螺杆压缩比和螺槽深度 确定几何压缩比 i 等距不等深(通用型)螺杆压缩比的计算 式如下:
对于大多取经验数据来确定,通用公式 H3=(0.025~0.06)Ds。
再根据确定的螺杆压缩比计算加料段螺杆槽 深度。
.
10
• 螺杆各段的确定
高聚物在螺杆中的挤出过程,实际上经历 固体输送,熔融和均化的过程。所以一般 螺杆都设计成三段:加料段,压缩段及均 化段析图
螺杆综合受力为:螺杆轴向力、螺杆扭矩 及螺杆自重产生的压、扭弯的组合。一般 加料段及排气段螺杆根径较小,其承受载 荷力最低,所以螺杆的加料段以加料段的 根径截面计算、校核裁面。
.
14
A.机头压力的确定
机头压力可用理论计算方法和实测方法得到。
当关闭机头,可认为挤出量Q=0,若螺杆与
螺杆与机筒的间隙δ的选择既要根据加工条件决定, 也要考虑被加工物料的性能。一般粘度大的塑料, δ可取大值;粘度小的塑料,δ应取小值。螺杆与 机筒的间隙可参考下表选取。
.
25
螺杆与机筒的对中性,在设计上要求螺杆中心线 与机筒中心线重合。但由于制造、装配过程中所 产生的螺杆径向跳动、螺杆定位面与螺杆中心线 不同心、螺杆推力面与螺杆中心线不垂直、机筒 内孔偏差、法兰平面对机筒中心不垂直、内孔径 向跳动等加工误差及安装误差都会影响对中性。 要保证螺杆与机筒的对中性,一般可以采取以下 措施:提高零件的加工与装配精度,减少零件数 目;选取有效的定位基准和合理的连接方式。例 如螺杆个段之间的连接采用止口连接,便于安装, 也提高定位基准。
xd 1 2(rt)2(tz)2(zr)2
[σ]=σs/n
.
24
3.7.5螺杆与机筒的配合要求
螺杆与机筒的配合间隙。螺杆与机筒的配合间隙δ的 大小涉及到挤出机的生产能力、功率消耗、使用 寿命、机器加工成本等问题。δ取值过大,加工、 装配容易,但生产能力则会下降,塑料在机筒内 的停留时间难以控制,甚至造成熟分解。δ取值过 小,加工装配困难,功率消耗增大,且容易使螺 杆与机筒磨损,降低机器的使用寿命。
3.7 单螺杆机出机设计
单螺杆挤出机示意图
.
1
.
2
.
3
.
4
3.7.1螺杆与机筒的材料选择
螺杆常用材料的性能要求为:机械强度 好,耐腐蚀和抗磨性能好,加工性能 好,取材容易。一般选用38CrMoAl氮 化钢。
38CrMoAl氮化钢的性能如下表:
.
5
.
6
3.7.2螺杆的主要参数的选取与确定
螺杆直径:
.
20
.
21
.
22
• 由轴向力引起的轴向拉应力在机筒全长上 不变,即:
•
z
=
Pz A
prb2 (Rb2 rb2)
=
pr b 2 R b 2 rb 2
.
23
• 因机筒多为塑性材料,所以当计算出三个 主应力的最大值后,可用第四强度理论进 行设计计算及校核。 按第四强度理论最大变形能理论计算,机筒壁厚的强度条 件为:
我国挤出机标准所规定的螺杆直径系列有: 30、45、65、90、120、150、200。螺杆 直径的大小一般根据所加工制品的断面尺 寸、加工塑料的种类和所加工的生产率来 确定。制品截面积的大小和螺杆直径的大 小有一个适当的关系。通常:大截面的制 品所选的螺杆直径要大一些,这对于制品 的质量、设备的利用率和操作比较有利。