Cryogenic systems for superconducting devices
Hyper Tech(美国Hyper公司MgB2超导材料介绍)

FCL- 2 organizations for both resistive and inductive type plus Hyper Tech’s internal resistive FCL program
Plus – 2 DC cable projects and 1 –SMES project
Typical multifilament MgB2 conductor
MgB2 Nb
Cu
Monel
Lengths currently up to 6 km @ 0.8 mm, scaling up to over 60 km.
9
Wire Performance
Commercial 1st Generation MgB2 Wire
0 0 2 4 6 8 10 12 14
B (T)
Peak bore fields: 4.6 T at 4.2 K, 2.2 T at 20 K
11
Improving connectivity, continued
106 36 fil [CTFF-1] 1 fil [CTFF-2] 1 fil [CTFF-2] Interpolated 18 fil [CTFF-2] 105
Third , the superconductor needs to operate at a wire performance level that can significantly reduce the weight and cost of the generator.
Fourth- superconducting generator design needs to be easily manufactured, maintained and repaired in the field.
“人造太阳”中的“冰”——EAST低温系统
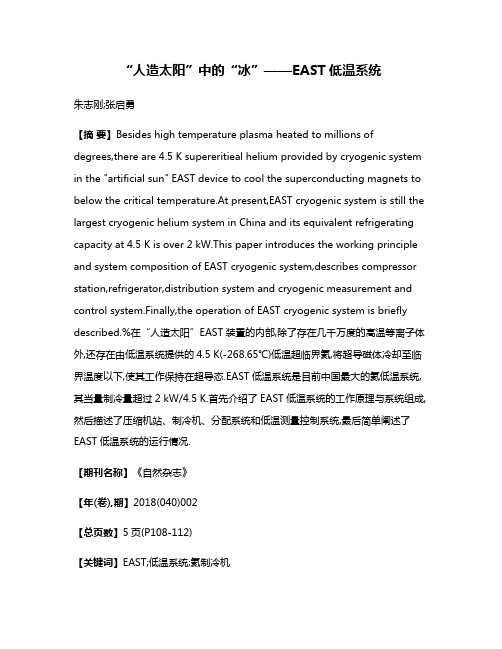
“人造太阳”中的“冰”——EAST低温系统朱志刚;张启勇【摘要】Besides high temperature plasma heated to millions of degrees,there are 4.5 K supereritieal helium provided by cryogenic system in the "artificial sun" EAST device to cool the superconducting magnets to below the critical temperature.At present,EAST cryogenic system is still the largest cryogenic helium system in China and its equivalent refrigerating capacity at 4.5 K is over 2 kW.This paper introduces the working principle and system composition of EAST cryogenic system,describes compressor station,refrigerator,distribution system and cryogenic measurement and control system.Finally,the operation of EAST cryogenic system is briefly described.%在“人造太阳”EAST装置的内部,除了存在几千万度的高温等离子体外,还存在由低温系统提供的4.5 K(-268.65℃)低温超临界氦,将超导磁体冷却至临界温度以下,使其工作保持在超导态.EAST低温系统是目前中国最大的氦低温系统,其当量制冷量超过2 kW/4.5 K.首先介绍了EAST低温系统的工作原理与系统组成,然后描述了压缩机站、制冷机、分配系统和低温测量控制系统,最后简单阐述了EAST低温系统的运行情况.【期刊名称】《自然杂志》【年(卷),期】2018(040)002【总页数】5页(P108-112)【关键词】EAST;低温系统;氦制冷机【作者】朱志刚;张启勇【作者单位】中国科学院等离子体物理研究所,合肥230031;中国科学院等离子体物理研究所,合肥230031【正文语种】中文由强磁场约束高温等离子体的磁约束核聚变,被认为是人类最终实现可控核聚变能利用最具前途的方法。
QUARC_Quancer公司产品,自动控制软件介绍

A SINGLE PC SOLUTION FOR RAPID CONTROL PROTOTYPING IN WINDOWS ®.QUARC generates real-time code directly from Simulink®-designed controllers and runs the generated code in real-time on the Windows® target - all on the same PC. The Data Acquisition Card seamlessly interfaces with Simulink® using Hardware-in-the-loop blocks provided in the QUARC T argets Library.SPLIT SECOND CONTROL DESIGN – A DECADE IN ThE MAkINGQUARC was built on the legacy of WinCon, the first real-time software to run Simulink®-generated code in Windows®. QUARC seamlessly integrates with Simulink® and redefines the traditional design-to-implementation interface toolset. Just click a button to enjoy more functionality and development flexibility, all geared towards improved real-time performance. Academics havesuccessfully deployed many advanced control and mechatronic systems, ranging from intelligent unmanned systems to force-feedback-enabled virtual reality.ADVANCEDINDUSTRIAL R&DACADEMIA INDUSTRYFOUR USES OF QUARCCONTROLS EDUCATION INNOVATIVERESEARCH GRADUATE-LEVEL EXPLORATION Enhance your engineering courses with industry- relevant hands-on learning Explore practical solutions for real-life challenges with a synergistic approachConduct ground-breaking research in emerging areas such as Unmanned Vehicle Systems and hapticsFast track time-to-market with an affordable rapid control prototyping solutionChoosing software for control system design andimplementation is critical for timely, successful research and development. Quanser knows this because we’ve pioneered control engineering for over 20 years. That’s why we created QUARC – a powerful rapid control prototyping tool that significantly accelerates control design and implementation. initially designed for industrial demands, QUARC is nonetheless ideal foradvanced research, masters-level, and evenundergraduate, teaching. QUARC is an integral part of all Quanser control lab workstations and is used all over the world by thousands of educational institutions and organizations, including the Canadian Space Agency and Defense Research and Development Canada. Discover what QUARC can help you achieve in less time and effort than you might be spending now.ACCELERATE CONTROLS EDUCATIONQUARC is an ideal tool to teach control concepts. It allows students to draw a controller, generate code and run it - all without Digital Signal Processing or without writing a single line of code. The capabilities of this powerful yet adaptable software are emphasized by the comprehensive curriculum that accompanies Quanser’s control lab equipment. The supplied Instructor and Student Workbooks feature lab exercises and projects based on Simulink®. They help focus students’ efforts on key control concepts rather than tedious code writing. The curriculum is developed by engineers for engineers to effectively demonstrate and teach the mechatronic design approach practised in industry. This includes modeling, controller design, simulation and implementation. An excellent low-cost rapid control prototyping system, QUARC is being usedby thousands of institutions worldwide. It is an effective and efficient teaching tool for undergraduate and graduate-level courses in classical and modern control theory.hOW QUARC FUSES MULTIPLEENGINEERING COURSESThe Integrated Learning Centre at Queen’s University fuses all engineering disciplines into one modern lab. Quanser’s workstations, featuring a wide range of modular Quanser experiments, are used here to teach introductory, intermediate and advanced controls. QUARC software is an integral part of all those workstations. An economical approach to outfitting a lab, it also keeps students motivated, providing access to even more hands-on learning.CONTROLS EDUCATIONis done, allowing the studentsto focus more on the controldesign theory and less on theworkings of MATLABSimulink, thus improvingthe learning experience.”Dr. Wen-Hua Chen,Loughborough University,United KingdomThis Flexible Link module furtherexpands your topics of study withthe SRV02 workstation.All on a Single PCQUARC provides a single PC solution for rapid control prototypingin Windows XP® or Vista®. It generates real-time code directly fromSimulink®-designed controllers – but for the same PC. This single PCSolution for rapid control prototyping significantly accelerates controldesign and implementation. This helps students focus on theimportant aspects of the control design process and completeproject-based assignments successfully.Simple. Intuitive.QUARC user interfaces are easy to understand without training.For example, QUARC’s “external mode” communications allow theSimulink® diagram to communicate with real-time code generatedfrom the model. Tune parameters of the running model by changingblock parameters in the Simulink® diagram. Want to view the statusof a signal in the model? Simply open a Simulink® Scope (or any otherSink in the diagram) while the model runs on the target. Furthermore,data can be streamed to the MATLAB® workspace or to a file on diskfor off-line analysis.Low MaintenanceQUARC streamlines the process of maintaining and servicing a laboratorywithout sacrificing system performance or an excessive amount of yourstaff’s time. The extremely flexible host-target structure allows QUARC usersto maximize limited resources (i.e. PC, laptop and hardware) with minimaleffort or cost. Host (control design environment) and target (platformwhich executes the real-time code) can be on separate computers yet stillcommunicate through a network connection. QUARC can sustain anypossible multi-configuration. Ask about License Server Architecture.The Integrated Learning Center, Queen’s University, Canada.BRING ThEORIES TO LIFEWhether you’re exploring emerging technologies or transforming knowledge into solutions for real-world challenges, count on Quanser to help you achieve your research goals. The power of QUARC software combined with Quanser’s innovative plants can helpresearchers test their theories in real-time, on real hardware. QUARC seamlessly integrates with Quanser’s research platforms toimplement virtually any control algorithm. Combine QUARC with Quanser’s multi-function Data Acquisition card and plants to create a self-contained control workstation ideal for advanced research. Use it to design, simulate, implement, and test a variety of time-varyingsystems: communications, controls, signal processing, video processing, and image processing.All this is achievable quickly , easily and affordably because the workstation is a fully integrated, open-architecture solution.The set-up pictured below shows a 3 DOF Gyroscope workstation as one example of a Quanser workstation for high level research. This typical configuration entails: • P lant • Amplifier• Data Acquisition Card • Virtual Plant Simulation• Rapid Control Prototyping Design Software • Pre-designed ControllersFor more information about the Quanser’s research platformsplease visit /MCC.14323 DOF GYROSCOPEFeaturing three Degrees Of Freedom (DOF), this dynamically diverse experimental platform is ideal for teaching rotational dynamic challenges.DATA ACQUISITION CARDMeasure and command real-time signals with high I/Osampling period. QUARC supports a wide range of Quanser and National Instruments data acquisition cards. For a complete list please visit /QUARC.AMPLIFIER AMPAQQuanser’s multi-channel linear current amplifier is ideal forprecision controls. The AMPAQ connects to the DAQ terminal board and is connected to the 3-DOF Gyroscope with its easy-connect cables.SOFTWARE TO ACCELERATE DESIGN3-DOF Gyroscope models are designed to run in real-time with QUARC ® software, which integrates seamlessly withMATLAB ®/Simulink ®.“Using Quanser’s software, we can easily design control systems for many plants. We can apply complex control strategies quickly and effectively - and it is very easy to verify theory on the real plant.”Kenichi yano,Associate Professor, Gifu University , JapanEFFORTLESS INTEGRATION FOR MEChATRONIC RESEARChQUARC is a powerful, flexible mechatronic integration tool, providing time-saving and simple solutions to those unique challenges encountered when you’re developing mechatronic systems. Whether you have custom-made research platforms or use manufactured equipment, QUARC is the only software that makes it easy to interface with all of them. QUARC offers a suite of third-party device blocks which help researchers seamlessly interface and control KUKA robots, PGR cameras and SensAble® PHANTOM devices, to name a few. These blocks not only allow a Simulink® model to communicate with external devices but also implement the mathematical framework for controlling them. All this is possible without the need to learn new tools or hand coding since the controller design and integration is performed in an environment most researchers are familiar with, such as Windows®, MATLAB®, Simulink®.“QUARC’s support of TCP/IP has been a tremendous help for our research. It allowed us to develop a distributed sensing system that isn’t dependent on expensive I/O hardware or DAQ boards. Further, this allows for safety-critical redundancy when we aredoing vehicle control tests.”Sean Brennan,Department of Mechanical and Nuclear Engineering,Pennsylvania State University , USAQUARC OFFERS OVER 10 BLOCKSETSThe table provides an overview. At a glance,you can see specific research applications, unique attributes and technical specifications.Now you can enjoy greater flexibility whenimplementing control schemes. QUARC expands the possibilities for complex control design by:multiple operating Systems Support.QUARC is designed so that code could be generated for multipleoperating systems and hardware platforms while maintaining a common, seamless and easy-to-use interface. Simulink® models can run in real-time on a variety of targets - a target being acombination of operating system and processor for which QUARC generates code from a Simulink® diagram. Targets includeWindows® and QNX®. The number of targets QUARC supports is continually increasing.Support for Communications.The QUARC Stream API offers a flexible and protocol-independent communications framework. Conduct standard communication between QUARC models and more: between a QUARC model and an external third-party application (e.g., graphical userinterface) or even between two external third-party applications. The Stream API is independent of the development environment and can be used in C/C++, .NET, MATLAB®, LabVIEW TM , etc. The Stream API enables the communication between multiple real-time model over the internet. This could be used for distributed control, teleoperation, device interfacing, etc. The stream API natively supports the following protocols: TCP/IP, UDP, serial, shared memory , named pipes, ARCNET, and more.For demos and tutorials on QUARC’s communication capabilities request a free trial of QUARC at /QUARC.increasing number of Blocksets.The number of interfaces QUARC supports is continuallyincreasing over time to ensure easy integration with recent and popular third-party devices. Here are a few more examples: • Nintendo Wiimote• Q bot- An Unmanned Ground Vehicle based on iRobot Create®• Schunk Grippers• SparkFun Electronics SerAccelGet an updated list of interfaces supported by QUARC at /QUARC/blocksetsDESCRIPTIONUsing the KUKA Robot Blockset you can control any KUKA robot equipped with RSI (Robot SensorInterface) through the interactive Simulink® environment without tedious hand coding and cumbersome hardware interfacing.This blockset is not included in the standard QUARC license and is sold separately.The Point Grey Research (PGR) Blockset is used to acquire images from some of the Point Grey Research cameras. QUARC also provides image processing blocksets that can be used to find objects of a given color within a source image or convert images from one format to another.This blockset is included in the standard QUARC license.The Wiimote (Wii Remote) block reads the state of the Wiimote and outputs the button, acceleration, and Infra Red (IR) camera information. Using this blockset you can easily interface the Wiimote into the controller. This blockset is included in the standard QUARC license.The Novint Falcon Blockset is used for implementing control algorithms for the Falcon haptic device. Using the Blockset significantly simplifies the task of designing controllers for the Falcon.This blockset is included in the standard Quarc license.TEChNICAL CAPABILITIES AND SPECIFICATIONS• E nables the deployment of real-time executables with GUI • S upport for setting and getting values (e.g., knobs, displays, scopes, and other inputs and outputs)Supported devices:• SensAble PHANTOM Omni • SensAble PHANTOM Desktop • SensAble PHANTOM Premium• SensAble PHANTOM Premium 6DOF Data provided as output,• GPS position (latitude, longitude, altitude)• Number of visible satellites (dilution of precision data)• Accuracy information (dilution of precision – DOP)Typical accuracy 1-3m (WAAS)SUGGESTED RESEARCh APPLICATIONS• GUI Design (e.g. Cockpit)• Force feedback virtual reality• Haptically-enabled medical simulations • Teleoperation• Precise robotic manipulation• Image-based control and localization • Autonomous navigation and control • Fault detection• Image-based control and localization• Autonomous navigation and control • Image recognition • Mapping• Obstacle detection and avoidance • Visual servoing and tracking • Vision feedback• Teleoperation• Robotic manipulation• Force feedback virtual reality• Haptically enabled medical simulations • Teleoperation• Localization• Autonomous navigation and control• M ission reconfiguration(e.g., for Unmanned Vehicle Systems)• Fault recovery • Safety watchdogDYNAMICRECONFIGURATIONkUkA ROBOT ALTIASENSABLEPhANTOM ® SERIESVISUALIzATIONPGR CAMERASWII REMOTENOVINT FALCONGPSNATURAL POINTOPTITRACkThe PHANTOM® Blockset lets you control the series of PHANTOM® haptic devices via Simulink®. For added flexibility researchers can combine the Phantom Blockset and Visualization Blockset to enjoy seamless haptics rendering of virtual environments.This blockset is not included in the standard QUARC license and is sold separately.The Visualization Blockset creates 3D visualizations of simulations or actual hardware in real-time. By combining meshes and textures, you can create objects to seamlessly integrate high-performance graphics with real-time controllers. Comprehensive documentation and examples along with additional content are provided to help new users get started and master this blockset quickly. QUARC Visualization blockset is used in the Virtual Plant Simulation of selected Quanser plants such as SRVO2 and Active Suspension. This blockset is included in the standard QUARC license.• Y coordinates of up to four IR points detected by the wiimote IR camera. Valid values range from 0 to 767 inclusive.• A compatible Bluetooth device must be installed on the PC• A bility to command either Cartesian or joint velocity set points • A bility to measure the Cartesian positions, joint angles and joint torques • A bility to set either Cartesian or the joint minimum and maximum velocity limits • K UKA built-in safety checks are still enabled for safe operation• S end forces and torques in Cartesian or joint space • Read encoder values, position, and joint angles• Send commands in two different work spaces to the Phantom device • T he block outputs the gimbal angles of the device plus the values associated with the buttons and the 7 DOF available on the device (thumb-pad or scissors)• R emotely connect to a visualization server with multiple clients • N o interference with the operation of your real-time controller• Plugins provided for Blender and Autodesk’s 3ds Max 2008, 2009 and 2010• S et different material properties such as diffuse color, opacity , specular color, shininess, and emissivity.• T exture map support for png, jpg, tiff, and bmp.• X 3D support• C onfigurable mouse and keyboard interface for manually navigating around the environment • P erformance far exceeds TMW’s Virtual Reality toolbox• U p to 16 cameras can be connected and configured for single or multiple capture volumes • C apture areass up to 400 square feet • S ingle point tracking for up to 80 markers, or 10 rigid-body objects • T ypical calibration time is under 5 minutes • P osition accuracy on the order of mm under typical conditions• U SB 2.0 connectivity to ground station PC• U p to 100 fps tracking• S upport for Draganflyer 2 HI-COL and the FireflyMV • F rame rate selection from 7.5 fps to 60 fps • R esolutions from 640 x 480 to 1024 x 768, • C olor or grayscale, and custom image (subimage) sizes supported for faster framerates• C ontinuity of states between the model being switched-out and the model being switched-in, as a necessary condition to the system stability • S witching within one sampling interval, as a necessary condition to the system stability • D ynamic reconfiguration can be triggered either automatically (e.g., from a supervisory model) or manually• D ynamic Reconfiguration can be triggered either locally or remotely (i.e., on a remote target)The OptiTrack Blockset allows motion capture and tracking by using 3 or more synchronized infrared (IR) cameras that capture images containing reflective markers within a workspace. The blockset can be used to track either individual markers or rigid bodies. This Blockset makes it easy to conduct vision-based control experiments in real-time, especially for objects that were previously difficult to track, such as indoor autonomous vehicles.This blockset is not included in the standard QUARC license and is sold separately.The GPS Blockset allows GPS receivers to be easily accessed, thereby adding GPS localization to an experimentalplatform. This Blockset integrates with Ublox GPS devices as well as NMEA compliant GPS devices. This blockset is not included in the standard Quarc license and is sold separately.The Altia Design Blockset enables the user to interact with the real-time code from Altia GUIs. Unlike theMATLAB® GUIs, MATLAB® and Simulink® are not required when using Altia GUIs. This blockset gives you the tools you need to generate complete production systems without writing a single line of code. This blockset is included in the standard QUARC license.The Dynamic Reconfiguration Blockset lets you dynamically switch models on the target machine within a sampling interval. A running model may be replaced with another model while ensuring continuity of states between both with no interruptions (i.e. no skipped sample). For a demo and tutorial on the Dynamic Reconfiguration blockset request a free trial of QUARC at /QUARC.This blockset is not included in the standard QUARC license and is sold separately.Data provided as output:• P osition: X, Y, and Z position in Cartesian coordinates• Button information: Whether a button is currently pressed or not • F orce: X, Y, and Z forces applied by the Falcon end-effectormodel 1model 2* Please note that prices for blocksets may vary. For more information or to request a quote please contact sales@.• Payload 5 kg • Number of axes 6• Repeatability <±0.02 mm • Weight 28 kg• Mounting positions floor or ceiling • Controller KR C2sr • Max speed 8.2 m/sData provided as output:• X, Y, and Z axis accelerations • Button states • X coordinates of up to four IR points detected by the wiimote IR camera. Valid values range from 0 to 1023 inclusive• S upport for setting values (i.e. Meters and other outputs)• F eatures the Quanser Plot library for AltiaBLOCkSET* • Virtual reality rendering• Game and medical simulation• Simulation of mechanical components • Data fusion • R eal-time status displays of physical hardware• Virtual cockpit for aerial vehicles REQUEST A FREE 30 DAY TRIAL OF QUARC TODAY. VISIT /QUARC• Robotic manipulation • Teleoperation“The Host Computer System for the Challenging Environment Assessment Laboratory (CEAL) at the Toronto Rehabilitation Institute (TRI) was developed using Quanser’s QU ARC real-time software. The power of QU ARC, with Quanser’s engineering support, enabled TRI to create a flexible developmentenvironment for researchers to implement sophisticated real-time experiments, using a large-scale 11-ton, 6-DOF motion platform and high-performance audio-visual rendering systems”Dr. Geoff Fernie , Vice President, Toronto Rehabilitation Institute, CanadaQUARC ACCELERATES MEChATRONIC DEVELOPMENT WITh RAPID CONTROL PROTOTYPINGQUARC is a powerful Rapid Control Prototyping (RCP) platform that meets industrial research and development demands. This robust software helps manage the increasing complexity of controlengineers’ tasks and accelerates their ability to test control strategies. Generating countless iterations of Simulink® control designsbecomes almost effortless - a block diagram design is automatically implemented on the system and computed in real time, eliminating the need for manual coding. This RCP platform is adaptable to virtually any mechatronic interfaces and scalable for complex multi-input and multi-output systems.Affordable Industrial-Grade PerformanceFor a fraction of the cost of comparable systems, Research and Development engineers can convert a PC into a powerful platform for control system development and deployment. When combined with a Quanser Power Amplifier and a Quanser Data Acquisition Card, QUARC software provides an ideal rapid prototyping and hardware-in-the-loop development environment. QUARC is also compatible with a wide range of commercially available data acquisition cards, including National Instruments boards.QUARC evolved from experience with its predecessor WinCon.The Canadian Space Agency played an intricate role in defining and confirming many of the features of QUARC. This was done in the context of their micro-satellite development program on an early stage prototype. It has since been adopted by industries requiring the latest in performance and development flexibility such as the Aerospace, Defence and Medical device industries.QUARC capabilities and features are designed to optimize the RCP process. Below are a few samples of such features.• F lexible and extensible communications blocks configurablefor real-time TCP/IP, UDP, serial, shared memory and other protocols • P erformance Diagnostics • R TW Code Optimization support • M odularity and incremental builds via model referencing • C ontrol of thread priorities and CPU affinity • A synchronous execution (e.g., ideal for efficient communication) • R un any number of models on one target – or simultaneously on multiple targets • S elf-booting models for embedded targets• E xternal Hardware-In-the-Loop card and communication interfacing provided in C/C++, MATLAB®, LabVIEW TM , and .NET languages • M ultiprocessor (SMP) support, e.g., on a quad-core Windows target QUARC models can take advantage of all four cores. • S imulink® 3D Animation (formerly known as Virtual Reality) Toolbox support• A bility to interface with MATLAB® GUIs, LabVIEW TM panels, and Altia“We have been using Quanser’s QU ARC software to do real-time robot control. QU ARC enables fast and easy prototyping of control algorithms with hardware in the loop and has been an invaluable tool for algorithm development, simulation, and verification.”Paul Bosscher, Harris Corporation, USAChallenging environment AssessmentLaboratory (CeAL) will be one of the most advanced rehabilitation research facilities in the world.INNO VATE, RESEARCHAND EXPLOIT KNOWLEDGE.QU ANSERCONSULTING SOFTWAREHARDWAREPlantDAQAmplifierQUARC®: A POWERFUL ENGINEFOR ENGINEERING DEPARTMENTSThree issues challenge university engineering departments everywhere: teaching, research and budget. One solution resolves them: QUARC software from Quanser!For T eaching: Created by engineers for engineers, QUARC is an excellent low-cost rapid control prototyping system. Working seamlessly with Simulink®, QUARC helps students put ideas andtheory into practice sooner. Plus curriculum is offered to help educators focus on what matters most. With more hands-on learning, undergraduate and graduate students alike are captivated and motivated to study further.For Research: Originally designed for industrial use, QUARC is idealfor advanced research. From the precise control of surgical robots to unmanned air vehicles and beyond, ideas can be tested in real-time- even ideas that are out of this world. Small wonder our client list includes NASA, the Canadian Space Agency and thousands of universities and colleges. (Look on your left.)For your department’s budget: QUARC seamlessly integrates over80 Quanser experiments - from introductory to very advanced. These are modular by design and maximize efficiencies, offering multiple uses for one workstation. Academics ourselves, Quanser appreciates your need for careful budgeting. So QUARC is competitively pricedand available with single- or multiple-user licenses.Learn more at /QUARCProducts and/or services pictured and referred to herein and their accompanying specifications may be subject to change without notice. Products and/or services mentioned herein are trademarks or registered trademarks of Quanser Inc. and/or its affiliates. Other product and company names mentioned herein are trademarks or registered trademarks of their respective owners.©2010 Quanser Inc. All rights reserved. Rev 2.0。
神奇的冷知识英语作文初一

神奇的冷知识英语作文初一Fascinating Cold FactsThe world around us is filled with countless wonders and intriguing phenomena that often go unnoticed in our daily lives. One such fascinating area is the realm of cold temperatures and their remarkable effects. From the icy landscapes of the Arctic to the chilling depths of the ocean, the power of cold can manifest in truly astonishing ways. Let us delve into some of the most captivating cold facts that may just leave you in awe.To begin with, did you know that the coldest temperature ever recorded on Earth was an astounding -129°F (-89°C) at Vostok Station in Antarctica? This mind-boggling figure is colder than the surface of Mars and highlights the extreme conditions that can exist on our planet. Imagine the sheer resilience of the hardy researchers and scientists who brave such inhospitable environments in the pursuit of knowledge.Another fascinating cold fact relates to the unique properties ofwater. At temperatures below 32°F (0°C), water transforms into a solid state, becoming ice. However, the true wonder lies in the fact that ice is less dense than liquid water. This anomaly is what allows ice to float on the surface of bodies of water, rather than sinking to the bottom. This remarkable characteristic is essential for the survival of aquatic ecosystems, as it prevents the entire water body from freezing solid and ensures the continued existence of life beneath the surface.Moving on, the power of cold can also be harnessed for practical purposes. One remarkable example is the use of cryogenics, the study and application of extremely low temperatures. Cryogenic technology has enabled remarkable advancements in fields such as medicine, transportation, and energy storage. For instance, certain medical procedures, such as the preservation of human organs for transplantation, rely on cryogenic techniques to maintain the integrity and viability of the tissues. Additionally, the use of cryogenic fuels, such as liquid hydrogen, has revolutionized the aerospace industry, allowing for more efficient and powerful rocket propulsion systems.Interestingly, the effects of cold can also be observed in the natural world beyond our planet. On the surface of Mars, for example, temperatures can plummet to a staggering -195°F (-125°C) during the winter months. This extreme cold has a profound impact on theMartian landscape, leading to the formation of unique geological features like dry ice glaciers and carbon dioxide ice caps. The study of these extraterrestrial cold environments provides valuable insights into the processes that shape the surfaces of other worlds and the potential for life in the universe.Furthermore, the impact of cold on the human body is another fascinating area of exploration. At extremely low temperatures, the human body can undergo remarkable adaptations to cope with the harsh conditions. One such adaptation is the phenomenon of cold-induced shivering, where the body generates heat by rapidly contracting and relaxing muscles. This involuntary response helps to maintain the core body temperature and prevent hypothermia. Additionally, certain individuals have been documented to possess genetic traits that allow them to better withstand the effects of cold, such as increased cold tolerance and the ability to conserve body heat more efficiently.The realm of cold also extends to the microscopic world, where the behavior of molecules and atoms is profoundly influenced by temperature. At extremely low temperatures, matter can exhibit unusual properties, such as superconductivity, where certain materials can conduct electricity without any resistance. This phenomenon has revolutionized technologies like magnetic resonance imaging (MRI) and particle accelerators, which rely on theunique properties of superconducting materials. Furthermore, the study of quantum mechanics, a fundamental branch of physics, has been greatly advanced by experiments conducted at cryogenic temperatures, where the behavior of subatomic particles can be observed and understood in unprecedented detail.In the realm of the natural world, the impact of cold is also evident in the stunning beauty of ice formations. From the delicate snowflakes that grace our winter landscapes to the awe-inspiring glaciers that carve through mountainous terrain, the intricate and diverse structures of ice are a testament to the power of cold. These icy wonders not only captivate our senses but also provide valuable insights into the complex processes that shape our planet's climate and ecosystems.Perhaps one of the most intriguing cold facts is the potential for life to thrive in the most extreme cold environments. In the depths of the ocean, where the pressure and darkness are immense, communities of microorganisms have adapted to survive and even thrive in near-freezing temperatures. These extremophiles, as they are called, challenge our understanding of the limits of life and inspire us to explore the vast and mysterious realms of the cryosphere, the frozen regions of our world.In conclusion, the realm of cold is a treasure trove of fascinating factsand phenomena that continue to captivate and inspire us. From the record-breaking temperatures of the Antarctic to the quantum-level behavior of matter, the power of cold has shaped our world in countless ways. As we delve deeper into the mysteries of the cryosphere, we uncover new insights that not only expand our scientific knowledge but also ignite our sense of wonder and curiosity about the natural world. The captivating cold facts presented here are just a glimpse into the extraordinary realm of low temperatures, and there is much more to explore and discover in this fascinating domain.。
magnetschwebebahn_engl

What is thedifference between the super-conducting magnet levitated sus-pension train and the TRANSRAPID,and can the former replace thetechnical principle of the latter some day?Up to now not, however:Should you be interested in purchasing such a magnet cushion train model, please get in touch with us. In case the demand is great enough, we would be pleased to produce such modelswithin an acceptable time. IFW Dresden will be happy to respond to your wishes.Can a model of the superconductor-based magnet cushion train be purchased?If you are interested, please contact:Prof. Dr Prof. Dr. Ludwig Schultz. Ludwig Schultz Director of Institute for Metallic Materials in the IFW Dresden Tel:0351 / 465 9 460Fax:0351 / 465 9 541Email:schultz@ifw-dresden.deProf. DrProf. Dr. Jörg F. Jörg F ink Director of Institute for Solid State Research in the IFW Dresden Tel:0351 / 465 9 425Fax:0351 / 465 9 313Email:j.fink@ifw-dresden.deDipl.-Ing. Wilfried PfeifferTechnology transfer in the IFW Dresden Tel:0351 / 465 9 424Fax:0351 / 465 9 600Email:w.pfeiffer@ifw-dresden.deF urther informations and a video please find under:http://www http://www.ifw-dresden.de.ifw-dresden.de Principle of the TRANSRAPID The Transrapid is kept hovering by powerful electromagnets which draw the train within a guiding system toward the rails;hovering heights of 10 ... 15 cm can be achieved in this way. A highly reliable, fully redundant electronic control system ensures that the vehicle hovers at an average distance of about 10 mm (3/8 in)from its guideway. In future, alsosuperconducting cables will be used for generating the necessary high magnetic forces in the coils (e.g. in Japan). A complex control system is needed to maintain the state of hovering. The train’s forward motion is caused by a linear drive for which an electromagnetic alternating field is generated by a string of coils in the rails which need to be powered - all this also calls for an appropriate control system.Whether a superconducting magnetic railroad can replace latter some day the TRANSRAPID - it can say it today no one.However, as is the case with so many predictions:Never say die ...The non-contact support andguidance system of the Transrapid maglev system functions according to the principle of electromagnetic levitation.Institut fürFestkörper- und Werkstofforschung DresdenPostfach 27 01 16D-01171 DresdenWith regard to melt-textured YBCOmaterials, work is being done to perceptiblyimprove the magnetic remanence fieldtrapped below the critical temperature, Tc.On the basis of the institute’s results andexperience, the work focuses on materialswhich have maximum remanence fields evenat temperatures of about 77 K and whichmeet the requirements of the most variedapplications in terms of size, form andcrystallographic orientation.Institut für Festkörper- und WerkstofforschungDresden (IFW) has made the most powerfulpermanent magnet from superconductingmaterial. The Dresden scientists succeeded inpushing up the record mark quite a bit. In theworldwide competition for higher field strengths,American researchers reached 10.1 Tesla asearly as 1996 which value had remainedunchallenged for a long time - i.e. until October1999 when IFW Dresden succeeded in stabilizingmagnetic fields of up to 14.4 Tesla insuperconducting magnets. Meanwhile, IFWmagnets achieve fields of 16 T. This correspondsto a force of approx. 5,000 Newton actingbetween two such permanent magnets having aface with an active area of 1 square centimeter.The new result was reached at a temperature of -250°C. The radial tensile forces acting in theseexperiments on the superconductor are so highthat they may rip up the material. To avoid it, themagnet is enclosed with a steel corset.The currentlystrongest perma-nent magnet in theworld -Bulk high-temperaturesuperconductorsmade by IFWDresden!What aresuperconductorsandsuperconductingmagnets?Superconductors are characterized by an abruptloss of electrical resistivity and by specificmagnetic properties below a criticaltemperature Tc. In comparison with the low-temperature superconductors as they wereknown until 1986, the high-temperaturesuperconductors (HTSC) discovered thereafterrequire much less cooling since the criticaltemperature of the HTSC is above thetemperature of liquid nitrogen (-196 °C).It is a specific feature of solid super-conducting materials that they can spinthe magnetic flux to a great extent. Thispinning effect is a result of the fact thatan applied field enters the superconduc-tor in form of magnetic flux bundleswhich will be pinned to point or lineardefects in the material under theinfluence of the superconducting currentloops which are generated duringcooling the material below ist super-conducting transformation temperatureThis property can be advantageously usedin magnetic bearings and for theproduction of strong permanent magnets.What do suchsuperconductingmaterials consistof, and how arethey made?The solid superconducting material (yttrium-barium-copper oxide, shortly: YBaCuO) ismade at IFW Dresden by means of a specificmelt crystallization method which permitssamples with diameters of up to 2 inches to beproduced in a reproducible quality. Intensivework is beeing done on the 3-inch technology.To produce solid HTSC material, first HTSCcompound powders, or suitable precursors, areground with additives, pressed , and subjectedto a modified melt crystallization process. Theuse of seed crystals allows theproduction of single-domain sampleswithout grain boundaries, whichwould interrupt the superconductingcurrent. The as grown materialcontains inclusionsof a second typeof crystals, less than 1 µm in size,which are essential for flux pinning.The final shaps of the bulk materialswith respect to specific applications is obtainedeither by appropriate preforming or byconventional ceramic working processes(grinding, polishing, sawing and milling).An important development objective is findingpossibilities and mechanisms whichsystematically influence these properties byway of doping or alternative compositions,crystal and grain structures, and of developingthe know-how for low-cost industrialmanufacturing processes.How aresuperconductorscooled down tothe requiredworkingtemperature?The above-described magnetic effect caused by…pinning“ the flux is maintained as long as itstemperature is kept (by cooling) below thetransition temperature level. Whereas coolingwith liquid nitrogen seems to be a quiteacceptable and reasonable solution forlaboratory and individual/selected commercialapplications, more sophisticated solutionsmust be found for a broad industrial use. Whatis required are maintenance-free, electricallyoperated cooling systems which are bothunsusceptible to faults and not too expensive,and have a long service life.Can the newpermanentmagnets alreadybe used inpractice?As is seen today, the most important field ofpermanent magnet application is that ofsuperconducting magnetic bearings inwhich, contrary to conventional magneticbearings, no active control is required sincethe magnetic flux of the permanent magnetis so trapped in the superconductor that itstabilizes itself. Superconducting magneticbearings may be linear or rotationallysymmetric, and can be used for manyapplications, e.g. for the contactless bearingof motors in pumps delivering cryogenicliquids or of flywheels used for storingenergy or of centrifuges running at very highspeeds (in excess of 100,000 rpm). It isconceivable to use such superconductinglinear systems in future in clean roomconveying applications.In another application, the high forcesoccurring may be used for driving low-losselectric rotating or linear motors. The figureshows a reluctance motor whose rotor isprovided with superconducting platesmounted on an iron core. The rotatingmagnetic field is generated in the statorcopper windings.What is left to bedone by scienceand research tomake the use ofsuperconductingmagnetspracticable?…Pinning effect“Disk of bulk HTSC materialPrinciple of superconductingmagnetic bearingYBCOIFW Dresden Flux densities of no more than1.2 to 1.5 Tesla can be reachedwith conventional permanentmagnets.。
Cryocooled Cooling System for Superconducting Magnet

Cryocooled Cooling System for Superconducting MagnetY.S. Choi, D.L. Kim, H.S. Yang, B.S. Lee and W.M. JungKorea Basic Science InstituteDaejeon, 305-333, KOREAABSTRACTA cryogenic cooling system using a two-stage cryocooler for a superconducting magnet has been designed, fabricated and tested. The superconducting magnet is composed of NbTi solenoid coils with an effective warm bore of 52¶mm and a maximum central field of 3¶T. The NbTi solenoid coils are wound around a copper form that is thermally connected to the second stage cold head of a cryocooler through a conductive link. The temperature distribution along the conductive link was measured during the cooldown process as well as at steady state. The contact resistance between the coldhead and conductive link was estimated from the cooling power of the cryocooler, the contact area, and the temperature gradient. The effect of the supplied current on the temperature distribution is also discussed.INTRODUCTIONCryocoolers have been applied to many academic and industrial applications, such as space exploration, cryo-surgery and liquefaction.1-4 Recently, many superconducting magnet systems have been required to use cryocoolers alone as the heat sink, instead of liquid helium or nitrogen, to achieve increased simplicity, compactness, and efficiency. The Korea Basic Science Institute (KBSI) has initiated the development of a conduction-cooled superconducting magnet system using a two-stage cryocooler for a material control application. The superconducting magnet for material con-trol has to be designed to have a strong magnetic field gradient in a control volume.In the conduction-cooled superconducting magnet system examined here, a 4¶K Gifford-McMahon (GM) or Pulse-tube cryocooler is employed to cool the magnet down to a certain operating tempera-ture. The cold head of the cryocooler has a positional restriction, in that it needs to be located in a low magnetic field area to avoid degradation of its cooling capacity. Therefore, a conductive link between the magnet and the cryocooler is crucial in developing the superconducting magnet system. This paper presents the design, fabrication, and test of a conduction-cooled superconducting magnet system with emphasis on the cryogenic cooling point of view. In addition, the conductive link between the magnet and cryocooler is discussed with respect to the contact resistance and the cool-ing power of the cryocooler.DESIGN OF CONDUCTION-COOLED MAGNET SYSTEMThe conduction-cooled superconducting magnet system considered here is schematically shown in Fig. 1. The NbTi solenoid coils are wound around the magnet form which is thermally connected6652nd cold stage 1st coldstageRadiationshieldSC coilMLISupportsVacuumvessel HTS lead Conduction plateVacuum portGM cryocoolerCu leadRoom temp.bore Powersupply to the second-stage cold head of the cryocooler through a conductive link . The room temperature bore with a 52¶mm diameter is located in the middle of the NbTi solenoid coils, which are sus-pended by four gravitational supports. The binary current lead, a series combination of a normal conductor in the high-temperature section and an HTS conductor in the low-temperature section, is employed for this application. The entire cold part is covered by a thermal shield and wrapped with multilayer insulation (MLI) to minimize the thermal radiation load.In the magnet system, the cryogenic cooling requirements are continuously generated primarily by three different physical mechanisms: thermal conduction through the mechanical supports, ther-mal radiation, and heat transferred from the current leads. The estimated cryogenic loads at the first and second stages are 52.8 and 1.1¶W, respectively; these match the cooling capacity of our two-stage GM cryocooler (Sumitomo, model RDK415D) with 20-30% margin.The operation of the cryocooler is limited by the magnetic field. The performance of our two-stage GM cryocooler is slightly degraded when the magnetic field is over 1 Tesla around the second-stage regenerator, and the magnetic field should be lower than 500 Gauss for the stepper motor in the warm end.5 In order to verify the performance of the cryocooler, an analysis of the magnetic field in the system was carried out and the results are plotted in Fig. 2. Several possible positions of the two-stage GM cryocooler for this application were considered. One of the simplest designs is to mount the cryocooler directly on top of the vacuum vessel so as to provide cooling to the first-stage thermal shield and the 4¶K superconducting magnet, as shown in Fig. 2. The magnetic field at the second-stage regenerator and at the stepper motor are low enough with this configuration to achieve the normal performance of the cryocooler in this system.MAGNET SYSTEM FABRICATION A ND T ESTINGThe NbTi superconducting coils were fabricated by the wet winding method using Stycast ®epoxy. The NbTi multifilamentary composite superconducting wire (I c = 870¶A at 3¶T and 4.2¶K ) of 0.9¶mm diameter was wound on the copper form which has a 1¶mm width slot along the axis to reduce eddy losses during magnet energizing. A stainless steel wire of 1¶mm diameter was em-ployed to support the electromagnetic force in the coils. The copper form was thermally connected to the second-stage cold head of the cryocooler by flexible, tinned copper braids that protect the cold head from thermal contraction during the cooldown process. Cryogenic thermal grease (or indium)was applied between the copper form and the cold head of the cryocooler as a thermal contactFigure 1. Schematic of conduction-cooled superconducting magnet system.666commercial cryocooler applicationSFigure 3. Left: Temperatures of first and second stages after turning on the cryocooler; Right: position of temperaturesensors in the magnet system.Figure 2. Magnetic field around superconducting coils in the conduction-cooled magnet system.medium, ensuring minimum thermal resistance. A copper thermal shield was suspended from the top plate of the cryostat with gravitational supports made of threaded G10 rod, and attached to the first-stage cold head.The temperatures in the magnet system were measured with platinum resistance thermometers (Lakeshore PT 111) for first stage, and Cernox TM for second stage, at a number of locations as indicated in Fig. 3. During the initial phase of the testing, the cryostat was pumped down to the range of 5×10-3 torr, and then was cooled down to liquid helium temperature using the conductive link connected to the cryocooler. Once the superconducting coils were cooled down, a current was supplied by the magnet power supply, and the magnetic field at the center of the coils was measured using a Gaussmeter (Lakeshore model 460). During the cooldown process, temperatures were re-corded every 2¶min with a data acquisition system operated through LabView TM software. Variables in this testing were the interfacial material and the magnitude of supplied current.667cryocooleD SyStem for SuperconDucting magnetTable 1. Temperature distribution along the conductive link in the magnet system.CooldownFigure 3 shows the temperature history of the first stage, second stage, and superconducting coils after turning on the cryocooler. During the initial cooldown process, the temperatures de-creased almost at a constant rate; it took approximately 15 hours for the first-stage cold head to reach 50¶K , and 14 hours for the second-stage cold head to reach 4.2¶K . After 18 hours running of the cryocooler, the temperature of the superconducting coils was stabilized, and the temperatures at the first and second-stage cold heads were 31.2 and 3.21¶K , respectively. At steady state, the tempera-ture gradient along the conductive link in the system was observed, and the temperature of the magnet form was 6.1¶K , resulting from the thermal contact resistances in the conductive link assembly . For practical contact between metals, the interface is irregular enough that only intermittent contact occurs. Therefore, even though enough force was applied to the contact, the effective contact area was much smaller than the apparent contact area. The effective contact area can be increased by the use of an interfacial film or bonding agent, resulting in increasing the thermal conductance.6 The cooldown process was repeated using different interfacial materials between the conductive link and the cold head of cryocooler.In Table 1, the temperature distributions along the conductive link are summarized at steady state. In test 1, no additional material was applied between the conductive link and the cold head; in other words, it was pure metal-to-metal contact. The cryogenic grease, Cryocon ®, and an indium sheet were applied as bonding agents in tests 2 through 5. The existence of a bonding agent at the interface increased the thermal conductance by increasing the effective contact area so that the tem-perature of the magnet form was below 4¶K .The effective contact conductance, h c,eff , can be estimated from the net heat transfer rate in steady state.Q ref = A ⋅ h c,eff (T 1 – T 2)(1)where A and T denote contact surface area and temperature, respectively. In our system, the effec-tive contact conductance between the cold head and the cooling plate in the case of tests 1, 2 and 5was 48.1, 296.1 and 887.3 W/m 2 K, respectively.Magnet EnergizationFigure 4 shows the temperatures at the second stage and the supplied current in the system with respect to elapsed time. The current was increased by 10∼30 A/min up to 80¶A, and the central magnetic field increased up to 1.4 Tesla. The temperatures at the second stage increased with supplied current, and the temperature at the superconducting coils was 4.89¶K when the current of 80¶A was supplied. In Fig. 5, the temperatures at the joints of the HTS current leads are plotted in the cooling capacity curve of the two-stage GM cryocooler. The temperature at the second-stage joint increased with the supplied current in the range of 0∼80¶A; this was mainly because of joule heating at the joint in our system.CONCLUSIONSA conduction-cooled superconducting magnet system using a two-stage GM cryocooler was successfully designed, fabricated and tested. The superconducting coils were cooled down to ap-proximately 4¶K and energized up to 80¶A. A temperature gradient between the superconducting 668commercial cryocooler applicationSFigure 4. Second-stage temperatures versus supplied current with respect to time. (Position oftemperature sensors is shown in Fig. 3)Figure 5. Temperatures achieved at the joints of the HTS current leadsplotted in the cooling capacity curve of the two-stage GM cry ocoolercoils and the cold head of the cryocooler was observed, and was reduced by increasing the interfa-cial thermal conductance using a bonding agent. An indium sheet between the cold head and cooling plate had a higher effective contact conductance than that of cryogenic grease in our application. The joint of the HTS current lead will be modified in the near future in order to maximize the cooling effect and minimize joule heating.ACKNOWLEDGMENTThis work is supported by KBSI grant T28051.REFERENCES1.Durand, D., “NGST Advanced Cryocooler Technology Development Program (ACTDP) CoolerSystem,” Cryocooler 14, ICC Press, Boulder, CO (2007), pp. 21-25.2.Lock, J.S., “Ball Aerospace Advances in 35¶K Cooling-The SB235E Cryocooler,” Adv. in CryogenicEngineering , Vol. 53, American Institute of Physics, Melville, NY (2008), pp. 903-908.3.Hoch, D., “Progress Towards a Micromachined Heat Exchanger for a Cryosurgical Probe,” Cryocooler14, ICC Press, Boulder, CO (2007), pp. 505-514.669cryocooleD SyStem for SuperconDucting magnet4.Cryogenic Engineering , Vol. 53, American Institute of Physics, Melville, NY (2008), pp. 1183-1189.5.Cryogenic Engineering , Vol. 53, American Institute of Physics, Melville, NY (2008), pp. 375-382.6.48.Van Sciver, S.W., “Thermal and Electrical Contact Conductance between Metals at Low Tempera-Choi, Y.S., “Development of Cooling System for Cryogenic Preamplifier in FT-ICR Ion Trap,” Adv. inNumazawa, T., Development of a Magnetic Refrigeration for Hydrogen Liquefaction,” Adv. in“ture,” Proceedings of the Space Cryogenics Workshop , Free University Berlin, Berlin (1984), pp. 37-670commercial cryocooler applicationS。
全超导磁体托卡马克装置 英语

全超导磁体托卡马克装置英语作文Title:Fully Superconducting Tokamak (FST)A Fully Superconducting Tokamak (FST) is a pioneering design in the realm of nuclear fusion research, aiming to harness the power of the stars for sustainable energy production. This essay will provide an overview of FST technology, its operational principles, and its significance in the quest for clean energy.The FST is based on the Tokamak configuration, a doughnut-shaped (toroidal) device that uses magnetic fields to confine plasma, the hot, ionized gas necessary for nuclear fusion reactions. Unlike traditional tokamaks that use copper coils for magnetic confinement, FSTs employ superconducting coils. These coils, operating at extremely low temperatures, can maintain strong magnetic fields with minimal electrical resistance, significantly enhancing the device's efficiency and operational time.The heart of an FST lies in its superconducting coils, which are cooled to cryogenic temperatures, typically near absolute zero, using liquid helium. At these temperatures, the coils become superconductors, meaning they can conductelectricity with zero resistance. This property allows for the creation of powerful, stable magnetic fields that can confine the plasma in the toroidal chamber for extended periods.The plasma, consisting of hydrogen isotopes such as deuterium and tritium, is heated to temperatures exceeding 100 million degrees Celsius, the conditions necessary for nuclear fusion to occur. The magnetic fields generated by the superconducting coils prevent the plasma from touching the chamber walls, which would cool the plasma and disrupt the fusion process.FST technology offers several advantages over conventional tokamaks. Firstly, the use of superconducting coils allows for a more compact design, reducing the overall size and cost of the device. Secondly, FSTs can operate continuously for extended periods, potentially leading to a steady-state fusion reactor that can provide a constant source of electricity. This is in contrast to traditional tokamaks, which can only operate in short bursts due to the limitations of their copper coils.The development of FSTs represents a significant step forward in the pursuit of clean, sustainable energy. Nuclear fusion, if successfully harnessed, could provide a virtuallylimitless supply of energy without the greenhouse gas emissions associated with fossil fuels or the radioactive waste produced by nuclear fission. FSTs, with their improved efficiency and operational stability, bring the dream of fusion power closer to reality.In conclusion, the Fully Superconducting Tokamak (FST) is a cutting-edge technology that promises to revolutionize the field of nuclear fusion. By employing superconducting coils to confine plasma, FSTs offer a more efficient and stable approach to fusion energy production. As research in this area continues, FSTs could pave the way for a future where clean, sustainable energy is a global reality.。
低温材料物性表
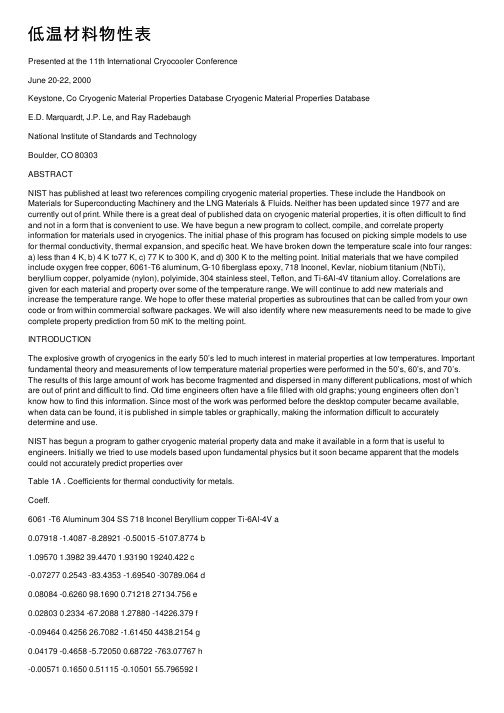
低温材料物性表Presented at the 11th International Cryocooler ConferenceJune 20-22, 2000Keystone, Co Cryogenic Material Properties Database Cryogenic Material Properties DatabaseE.D. Marquardt, J.P. Le, and Ray RadebaughNational Institute of Standards and TechnologyBoulder, CO 80303ABSTRACTNIST has published at least two references compiling cryogenic material properties. These include the Handbook on Materials for Superconducting Machinery and the LNG Materials & Fluids. Neither has been updated since 1977 and are currently out of print. While there is a great deal of published data on cryogenic material properties, it is often difficult to find and not in a form that is convenient to use. We have begun a new program to collect, compile, and correlate property information for materials used in cryogenics. The initial phase of this program has focused on picking simple models to use for thermal conductivity, thermal expansion, and specific heat. We have broken down the temperature scale into four ranges: a) less than 4 K, b) 4 K to77 K, c) 77 K to 300 K, and d) 300 K to the melting point. Initial materials that we have compiled include oxygen free copper, 6061-T6 aluminum, G-10 fiberglass epoxy, 718 Inconel, Kevlar, niobium titanium (NbTi), beryllium copper, polyamide (nylon), polyimide, 304 stainless steel, Teflon, and Ti-6Al-4V titanium alloy. Correlations are given for each material and property over some of the temperature range. We will continue to add new materials and increase the temperature range. We hope to offer these material properties as subroutines that can be called from your own code or from within commercial software packages. We will also identify where new measurements need to be made to give complete property prediction from 50 mK to the melting point.INTRODUCTIONThe explosive growth of cryogenics in the early 50’s led to much interest in material properties at low temperatures. Important fundamental theory and measurements of low temperature material properties were performed in the 50’s, 60’s, and 70’s. The results of this large amount of work has become fragmented and dispersed in many different publications, most of which are out of print and difficult to find. Old time engineers often have a file filled with old graphs; young engineers often don’t know how to find this information. Since most of the work was performed before the desktop computer became available, when data can be found, it is published in simple tables or graphically, making the information difficult to accurately determine and use.NIST has begun a program to gather cryogenic material property data and make it available in a form that is useful to engineers. Initially we tried to use models based upon fundamental physics but it soon became apparent that the models could not accurately predict properties overTable 1A . Coefficients for thermal conductivity for metals.Coeff.6061 -T6 Aluminum 304 SS 718 Inconel Beryllium copper Ti-6Al-4V a0.07918 -1.4087 -8.28921 -0.50015 -5107.8774 b1.09570 1.3982 39.4470 1.93190 19240.422 c-0.07277 0.2543 -83.4353 -1.69540 -30789.064 d0.08084 -0.6260 98.1690 0.71218 27134.756 e0.02803 0.2334 -67.2088 1.27880 -14226.379 f-0.09464 0.4256 26.7082 -1.61450 4438.2154 g0.04179 -0.4658 -5.72050 0.68722 -763.07767 h-0.00571 0.1650 0.51115 -0.10501 55.796592 I0 -0.0199 0 0 0 data range 4-300 K 4-300 K 4-300 K 4-300 K 20-300 Ka large temperature range and over different materials. Our current approach is to choose a few simple types of equations such as polynomial or logarithmic polynomials and determine the coefficients of different materials and properties. This will allow engineers to use the equations to predict material properties in a variety of ways including commercial software packages or their own code. Integrated and average values can easily be determined from the equations. These equations are not meant to provide any physical insight into the property or to provide ‘standard’ values but are for working engineers that require accurate values.MATERIALSInitial materials that we have compiled include oxygen free copper, 6061-T6 aluminum, G-10CR fiberglass epoxy, 718 Inconel, Kevlar 49, niobium titanium (NbTi), beryllium copper, polyamide (nylon), polyimide, 304 stainless steel, Teflon, and Ti-6Al-4V titanium alloy. These were chosen as some of the most common materials used in cryogenic systems in a variety of fields.MATERIAL PROPERTIESThermal ConductivityWidely divergent values of thermal conductivity for the same material are often reported in the literature. For comparatively pure materials (like copper), the differences are due mainly to slight material differences that have large effects on transport properties, such as thermal conductivity, at cryogenic temperatures. At 10 K, the thermal conductivity of commercial oxygen free copper for two samples can be different by more then a factor of 20 while the same samples at room temperature would be within 4%. It is also not uncommon for some experimental results to have uncertainties as high as 50%. Part of our program is to critically evaluate the literature to determine the best property values. Data references used to generate predictive equations will be reported.The general form of the equation for thermal conductivity, k , islog()log (log )(log )(log )(log )(log )(log )(log ),k a b T c T d T e T f T g T h T i T =++++++++2345678 (1)where a , b , c , d, e , f , g , h , and i are the fitted coefficients, and T is the temperature. These are common logarithms. While this may seem like an excessive number of terms to use, it was determined that in order to fit the data over the large temperature range, we required a large number of terms. It should also be noted that all the digits provided for the coefficients should be used, any truncation can lead to significant errors. Tables 1A and 1B show the coefficients for a variety of metals and non-metals. Equation 2 is the thermal conductivity for an average sample of oxygen free copper. It should be noted that thermal conductivity for oxygen free copper canTable 1B . Coefficients for thermal conductivity for non-metals.Coeff. Teflon Polyamide (nylon) Polyimide (Kapton) G10 CR (norm) G10 CR(warp)a2.7380 -2.6135 5.73101 -4.1236 -2.64827 b-30.677 2.3239 -39.5199 13.788 8.80228 c89.430 -4.7586 79.9313 -26.068 -24.8998 d-136.99 7.1602 -83.8572 26.272 41.1625 e124.69 -4.9155 50.9157 -14.663 -39.8754 f-69.556 1.6324 -17.9835 4.4954 23.1778 g23.320 -0.2507 3.42413 -0.6905 -7.95635 h-4.3135 0.0131 -0.27133 0.0397 1.48806 I0.33829 0 0 0 -0.11701 data range 4-300 K4-300 K 4-300 K 10-300 K 12-300 K Figure 1. Thermal conductivity of various materials.vary widely depending upon the residual resistivity ratio, RRR, and this equation should be used with caution. The thermal conductivities are displayed graphically in Figure 1.log .............k T T T T T T T T =?+?+?+?+22154088068029505004831000032071047461013871002043000012810515205152(2) Specific HeatThe specific heat is the amount of heat energy per unit mass required to cause a unit increase in the temperature of a material, the ratio of the change in energy to the change in temperature. Specific heats are strong functions of temperature, especially below 200 K. Models for specific heat began in the 1871 with Boltzmann and were further refined by Einstein and Debye in the early part of the 20th century. While there are many variations of these first models, they generally only provide accurate results for materials with perfect crystal lattice structures. TheTable 2. Coefficients for specific heat. Coeff. OFCHcopper 6061 -T6 Aluminum 304 SS G-10 Teflon a-1.91844 46.6467 22.0061 -2.4083 31.8825 b-0.15973 -314.292 -127.5528 7.6006 -166.519 c8.61013 866.662 303.6470 -8.2982 352.019 d-18.99640 -1298.30 -381.0098 7.3301 259.981 e21.96610 1162.27 274.0328 -4.2386 -104.614 f-12.73280 -637.795 -112.9212 1.4294 24.9927 g3.54322 210.351 24.7593 -0.24396 -3.20792 h-0.37970 -38.3094 -2.239153 0.015236 0.165032 I0 2.96344 0 0 0 data range 3-300 K 3-300 K 3-300 K 3-300 K 3-300 KFigure 2. Specific heat of various materials.specific heat of many of the engineering materials of interest here is not described well by these simple models. The general form of the equation is the same as Equation 1. Table 2 shows the coefficients for the specific heat. Figure 2 graphically shows the specific heats.Thermal ExpansionFrom an atomic perspective, thermal expansion is caused by an increase in the average distance between the atoms. This results from the asymmetric curvature of the potential energy versus interatomic distance. The anisotropy results from the differences in the coulomb attraction and the interatomic repulsive forces.Different metals and alloys with different heat treatments, grain sizes, or rolling directions introduce only small differences in thermal expansion. Thus, a generalization can be made that literature values for thermal expansion are probably good for a like material to within 5%. This is because the thermal expansion depends explicitly on the nature of the atomic bond, and only those changes that alter a large number of the bonds can affect its value. In general, largeTable 3A . Integrated Linear Thermal Expansion Coefficients for Metals.Coeff.6061 -T6 Aluminum 304 SS 718 Inconel Beryllium copper Ti-6Al-4V NbTi a-4.1272E+02 -2.9546E+02-2.366E+02-3.132E+02-1.711E+02 -1.862E+02b-3.0640E-01 -4.0518E-01-2.218E-01-4.647E-01-2.171E-01 -2.568E-01 c8.7960E-03 9.4014E-03 5.601E-03 1.083E-02 4.841E-03 8.334E-03 d-1.0055E-05 -2.1098E-05-7.164E-06-2.893E-05-7.202E-06 -2.951E-05 e0 1.8780E-080 3.351E-080 3.908E-08 data range 4-300 K 4-300 K 4-300 K 4-300 K 4-300 K 4-300 KTable 3B. Integrated Linear Thermal Expansion Coefficients for Non-metals.Coeff. Teflon Polyamide G10 CR (norm) G10 CR(warp)a-2.165E+03 -1.389E+03-7.180E+02-2.469E+02 b3.278E+00 -1.561E-01 3.741E-01 2.064E-01 c-8.218E-03 2.988E-02 8.183E-03 3.072E-03 d7.244E-05 -7.948E-05-3.948E-06-3.226E-06 e0 1.181E-07 0 0 data range 4-300 K 4-300 K 4-300 K 4-300 Kchanges in composition (10 to 20%) are necessary to produce significant changes in the thermal expansion (~5%), and different heat treatments or conditions do not produce significant changes unless phase changes are involved.8Most of the literature reports the integrated linear thermal expansion as a percent change in length from some original length generally measured at 293 K,()/.L L L T ?293293 (3) Where L T is the length at some temperature T and L 293 is the length at 293 K. While this is a practical way of measuring thermal expansion, the more fundamental property is the coefficient of linear thermal expansion,α,α()().T L dL T dT=1 (4) The coefficient of linear thermal expansion is much less reported in the literature. In principal, we can simply take the derivative of the integrated linear thermal expansion that results in the coefficient of linear thermal expansion. While we have had success with this method over limited temperature ranges, we have not yet determined an equation form for the integrated expansion value that results in a good approximation of coefficient of linear thermal expansion. For the time being, we will report the integrated linear thermal expansion as a change in length and provide the coefficient of linear thermal expansion when it is directly reported in the literature. The general form of the equation for integrated linear thermal expansion is L L L a bT cT dT eT T ?=++++??293293234510(). (5) Tables 3A and 3B provide the coefficients for the various materials while Figure 3 plots the integrated linear thermal expansions.FUTURE PLANSWe plan to continually add new materials, properties, and to expand the useful temperature range of the predictive equations for engineering use. We will report results in the literature but will also update our website on a continual basis. The initial phase of the program was a learningFigure 3. Integrated linear thermal expansion of various materials.experience on how to handle the information in the literature as well as for the development of a standard set of basic equation types used to fit experimental data. By using just a few types of equations, we hope to make the information easier to use. We shall now focus on developing large numbers of equations for a variety of materials and properties. Please check our web site at /doc/e6c9c70608a1284ac85043da.html /div838/cryogenics.html for updated information.REFERENCES1. Berman, R., Foster, E.L., and Rosenberg, H.M., "The Thermal Conductivity of SomeTechnical Materials at Low Temperature." Britain Journal of Applied Physics, 1955. 6: p.181-182.2. Child, G., Ericks, L.J., and Powell, R.L., Thermal Conductivity of Solids at RoomTemperatures and Below. 1973, National Bureau of Standards: Boulder, CO.3. Corruccini, R.J. and Gniewek, J.J., Thermal Expansion of Technical Solids at LowTemperatures. 1961, National Bureau of Standards: Boulder, CO.4. Cryogenic Division, Handbook on Materials for Superconducting Machinery. Mechanical,thermal, electrical and magnetic properties of structure materials. 1974, National Bureau of Standards: Boulder, CO.5. Cryogenic Division, LNG Materials and Fluids. 1977, National Bureau of Standards:Boulder, CO.6. Johnson, V.J., WADD Technical Report. Part II: Properties of Solids. A Compendium ofThe Properties of Materials at Low Temperature (phase I). 1960, National Bureau of Standard: Boulder, CO.7. Powells, R.W., Schawartz, D., and Johnston, H.L., The Thermal Conductivity of Metals andAlloys at Low Temperature. 1951, Ohio State University.8. Reed, R.P. and Clark, A.F., Materials at Low Temperature. 1983, Boulder, CO: AmericanSociety for Metals.9. Rule, D.L., Smith, D.R., and Sparks, L.L., Thermal Conductivity of a Polyimide FilmBetween 4.2 and 300K, With and Without Alumina Particles as Filler. 1990, National Institute of Standards and Technology: Boulder, CO.10. Simon, N.J., Drexter, E.S., and Reed, R.P., Properties of Copper Alloys at CryogenicTemperature. 1992, National Institute of Standards and Technology: Boulder, CO.11. Touloukian, Y.S., Recommended Values of The Thermophysical Properties of Eight Alloys,Major Constituents and Their Oxides. 1965, Purdue University.12. Veres, H.M., Thermal Properties Database for Materials at Cryogenic Temperatures. Vol. 1.13. Ziegler, W.T., Mullins, J.C., and Hwa, S.C.O., "Specific Heat and Thermal Conductivity ofFour Commercial Titanium Alloys from 20-300K," Advances in Cryogenic Engineering Vol. 8, pp. 268-277.。
- 1、下载文档前请自行甄别文档内容的完整性,平台不提供额外的编辑、内容补充、找答案等附加服务。
- 2、"仅部分预览"的文档,不可在线预览部分如存在完整性等问题,可反馈申请退款(可完整预览的文档不适用该条件!)。
- 3、如文档侵犯您的权益,请联系客服反馈,我们会尽快为您处理(人工客服工作时间:9:00-18:30)。
Cryogenic systems for superconducting devicesSteven W.Van Sciver *National High Magnetic Field Laboratory,Florida State University,1800E.Paul Dirac Drive,Tallahassee,FL 32310,USAAbstractThe principles entering into the selection of cryogenic systems for superconducting magnet applications are reviewed.Types of refrigeration systems,operating temperature ranges and e ciency are all issues that must be evaluated in selecting the most appropriate cryogenic system.Speci®c examples of magnet systems currently under development are discussed in the context of these principles.Ó2001Elsevier Science B.V.All rights reserved.Keywords:Cryogenics;Superconducting magnets;Cryocoolers1.IntroductionSafe and reliable cryogenic refrigeration is a requirement for the operation of all supercon-ducting devices from electronics to magnet sys-tems.In general,such devices require temperatures below 80K,a temperature that can be achieved using one of several boiling cryogens or closed-cycle refrigerators.Further,a wide range of cool-ing powers,from microwatts to kilowatts at low temperature,are required depending on applica-tion.Cooling systems for superconducting devices have undergone steady development since the ®rst liquefaction of helium and the discovery of su-perconductivity by H.Kamerlingh Onnes in the early 1900s.Today,a wide range of cryogenic technologies tailored to speci®c applications are available to superconducting system designers.All superconducting devices share the need for su cient refrigeration to overcome their low temperature heat loading.This loading typically comes in two forms:(1)heat leaks from the sur-roundings and (2)internal heat generation in the device.In addition,normally the refrigeration sys-tem needs to bring the superconducting device from ambient temperature to its low operating temperature in a reasonable length of time.The present paper is a survey of the cryogenic refrigeration options available for superconduct-ing magnet systems.Superconducting magnets span a wide range of sizes and shapes depending on application and thus their cooling systems also vary.The three main approaches to magnet cool-ing are:1.batch ®lling with a boiling cryogen such as liq-uid helium or liquid nitrogen where the heat is extracted by the evaporation of the liquid,2.closed cycle refrigeration that circulates cryo-gen through the magnet and removes heat at a lique®er/refrigerator located outside the mag-net vessel,Physica C 354(2001)129±135*Corresponding author.Tel.:+1-850-644-0998;fax:+1-850-644-0867.E-mail address:vnsciver@ (S.W.Van Sci-ver).0921-4534/01/$-see front matter Ó2001Elsevier Science B.V.All rights reserved.PII:S 0921-4534(01)00013-23.cryocooler cooling that extracts heat by direct contact between the magnet and a cold surface maintained by a specialized refrigeration cycle.Particular selection of a cryogenic system for a superconducting magnet depends on a number of factors.First among these is the required operat-ing temperature.With the early high®eld metallic superconductors,NbTi(T c 9K)and Nb3Sn (T c 18K),the only option is a helium system operating near the normal boiling point of LHe (NBP 4:2K).However,with the development of useful high temperature superconducting ceramic wires and tapes,it is now possible to operate mag-nets at considerably higher temperatures,possibly as high as the NBP of LN2(77K).These devel-opments have also led to innovative magnet sys-tems including magnets that are cooled only by direct contact with a cryocooler operating any-where from4to80K.Why is it advantageous to operate a supercon-ducting magnet at higher temperature?From the cryogenic viewpoint,the answers are obvious. Higher temperature implies higher thermodynamic e ciency of the refrigeration system.A quantita-tive measure of this e ciency is given by the co-e cient of performance(COP),which is a direct measure of the amount of ambient power needed to supply a given amount of low temperature re-frigeration.Speci®cally,the COP is de®ned as COP g T h=T cÀ1where the quantity in parentheses is the thermo-dynamically ideal Carnot factor and the g>1is a measure of the non-ideality of the system.For a moderate size helium system operating at10%of Carnot,the COP is about750W/W.The e ciency factor,g,also increases with refrigerator size[1]. High e ciency implies a smaller capital investment and operating cost for a given low temperature heat load.Another advantage to a higher operating tem-perature for a superconducting magnet comes from the increased thermal capacity of the system. Although the critical current in superconductors decreases with increasing temperature,the thermal capacity of the magnet strongly increases to the point where it is comparable with that of the liquid cryogen.Table1lists properties of several com-mon cryogens compared to that of copper.Note that the volumetric heat capacity of copper is comparable to that of liquid nitrogen at80K. Thus,although the magnet may not achieve as high an operating current or magnetic®eld if it operates at higher temperature,it may be more thermally stable due to the larger heat capacity of the winding.This potential advantage is most ev-ident in high temperature superconductors.2.Refrigeration/cooling technologiesAs discussed above,there are basically three methods in common use for cooling supercon-ducting magnets.The®rst and most common ap-proach is to batch®ll the magnet system vessel with cryogen,usually liquid helium.The magnet will thus be immersed in an isothermal bath and the heat deposited will go into evaporation of the liquid.Higher temperature cryogens have the de-sirable feature of larger heats of vaporization,see Table1.However,the operating temperature is restricted over a narrow range and therefore may not be suitable for many magnets.Many superconducting magnets are parts of systems and therefore should be integrated with a suitable closed-cycle refrigerator.Until recently, the most common approach to closed-cycle re-frigeration for magnets is to use a helium lique®er/ refrigerator to deliver liquid to the magnet and recover vapor.For the most part,such systems areTable1Thermal properties of selected cryogenic¯uids compared to that of copperFluid/material property LHe@4.2K LNe@30K LN2@77K Copper RRR 100Heat capacity/volume(kJ/m3K)570220016500.9@4.2K,240@30K,1750@77K Latent heat/volume(kJ/m3)2600104,000160,000N/AThermal conductivity(W/m K)0.0270.1130.14660@4.2K,2100@30K,540@77K 130S.W.Van Sciver/Physica C354(2001)129±135based on a recuperative Collins refrigeration cycle, shown in Fig.1.Recuperative cycles use a steady ¯ow of helium that passes through a combination of refrigerator components:compressor,heat ex-changers,expansion engines and/or Joule±Thom-son expansion valves to ultimately supply the cold helium.Such a system is rather complexin design and requires experience to operate and maintain. Recuperative lique®ers/refrigerators are moderate to large in size(10W to10s of kW at4.5K),have relatively high thermodynamic e ciencies(10±30%)and system costs in the range of a few $105±$107.They are capital intensive and require considerable technical support.In applications, the largest such systems are in operation at particle accelerator laboratories.For small scale applications,cryogenic technol-ogy has made considerable recent advances mostly in the area of closed cycle regenerative cryocoolers. The principal di erence between recuperative and regenerative cycles has to do with the¯uid¯ow.In recuperative cycles,the¯ow is steady and can be described by equilibrium thermodynamics laws.At any point in time,a given location in the¯ow stream has a thermodynamic state given by its local temperature and pressure.Therefore,the re-frigeration cycle can be optimized by evaluating the thermodynamic conservation equations for the components that make up the cycle.On the other hand,the¯ow in a regenerative cryocooler oscil-lates intermittently exchanging heat with the re-generator.In fact,many cryocoolers depend on non-equilibrium conditions to exist for operation. Thus,the thermodynamics of a regenerative cryo-cooler is much more di cult to model and opti-mize.There are many cryocooler cycles of interest to applications,but in current context of supercon-ducting magnet systems only two will be consid-ered,the Gi ord±McMahon(GM)cycle[2]and the ori®ce pulse tube(OPT)cryocooler[3].The GM cryocooler is the most common cryocooler in use today,while the OPT cryocooler is still under development.Schematic diagrams of these two cycles are shown in Fig.2.The principal compo-nents of a GM cryocooler are the compressor, displacer,rotary valve and regenerator.In this case,the rotary valve switches the¯uid¯ow back and forth through the regenerator and displacer. The OPT cryocooler replaces the displacer with a straight tube connected to a bu er volume through in this case two ori®ces.The ori®ces shift the phase between the¯uid velocity and pressure to optimize therefrigeration. Fig.1.Collins recuperative cryogeniccycle.In both cases,the regenerator stores the refrig-eration.It is designed much like a heat exchanger except that it uses materials that have large heat capacities at low temperatures.Conventional GM cryocoolers that are used for cryopump cooling and as shield coolers in bath cooled magnets use lead (Pb)or phosphor bronze as the regenerator material and have useful cooling power down to about 30K in single stage units and 15K in two stage units.This performance has been improving recently with the introduction of new materials.Interest in achieving liquid helium temperature with cryocoolers has inspired materials develop-ment for improved cryocooler performance.In particular,rare earth metals and compounds such as Nd,ErNi,HoCu 2,have magnetic ordering anomalies at low temperatures and associated large peaks in the speci®c heat.Fig.3displays the low temperature volumetric heat capacity of a se-lection of these materials [4].Thus,modern re-generators grade the materials into layers from the warm to cold end in order to achieve the highest volumetric heat capacity at the local operating temperature.The speci®c bene®t of this innovation has been the achievement of useful cooling powerto 20K in single stage and 4K in two stage commercial cryocoolers.3.Cryogenics for superconducting magnet systems Cryogenics is a necessary but often undesirable part of a superconducting system because it in-creases cost,reduces reliability and increases complexity.Clearly,the most desirable cryogenic system would have minimum impact on the oper-ation of the magnet.As discussed above,there are essentially three approaches to cooling of su-perconducting magnets:bath cooling in a liquid cryogen,closed-cycle cooling with a recuperative refrigerator/lique®er and direct cooling with a closed-cycle regenerative cryocooler.Each ap-proach has unique advantages that can meet a variety of magnet cooling requirements.To sum-marize the capability of each approach,we will consider the application to a particular magnet system.The best example of bath cooled magnet systems are those developed for the magnetic resonance imaging (MRI)industry.Thousands of MRI magnet systems are installed in health facil-ities worldwide with almost no visible evidence of cryogenics.This is accomplished through use of an optimized low-loss cryostat design including pos-sibly a cryocooler for refrigerating the thermal mercial MRI magnet systems are now to the point where they normally require only annual cryogenic service mostly for topping o the liquid cryogen.The magnet systems provide steady ®elds with a thermal isolation su cient to reduce liquid helium consumption to a minimum (usually less than 1W at 4.2K).Most often this level of helium consumption can only be achieved with the use of persistent current magnets with demount-able current leads.Similar magnet technology is in place for reciprocating magnetic separation (RMS)equipment,many of which are located in the Brazilian rainforest as shown in Fig.4.Clearly as with MRI magnet systems,this technology is best suited for unattended operation.For larger high current magnet systems that experience regular ®eld and current variations,it is necessary to provide active cooling byconnectingFig.3.Volumetric speci®c heat of common regenerative ma-terials [4].132S.W.Van Sciver /Physica C 354(2001)129±135the magnet vessel to a closed-cycle refrigerator.For large magnets using metallic superconductors,the refrigerator of choice is a Collins-type machine that delivers low temperature helium to the mag-net and recovers the cold return ¯ow to optimize the thermodynamic cycle.There are many exam-ples of this approach in high energy particle ac-celerators,nuclear fusion experiments and others.At the National High Magnetic Field Laboratory (NHMFL),we operate a large superconducting solenoid as part of our 45-T hybrid magnet,(Fig.5)[5].This magnet stores about 115MJ at full ®eld of 14T with an operating current of 10kA.The system is cooled with a pair of Collins-cycle re-frigerators with a total combined capacity of 400W at 4.5K (150l/h as lique®ers).An additional feature of this system is its 1.8K operating tem-perature in a bath of super¯uid helium.However,this system is not particularly user friendly.During operation the magnet and its cryogenic system are under constant automated monitoring with tech-nical support on call should a problem arise.The third option for superconducting magnet cooling has developed over the past 10years through the advent of two enabling technologies.First,there has been steady progress in regenera-tive cryocooler technology to the point where now one can obtain GM and OPT cryocoolers that can deliver greater than 1W of cooling at 4K.The other enabling technology is high temperature superconductor current leads.The combination of these two technologies has allowed for direct conduction cooling of NbTi and Nb 3Sn magnets.Such magnets do not require liquid cryogens for their operation and can be fully automated for cooldown,magnet energizing and safe operation.A number of such systems are in industrial appli-cation today for magnetic processing.For exam-ple,Cryomagnetics &Cryomech have developed a 9T,32mm warm bore NbTi conduction cooled by a 4K pulse tube cryocooler Fig.6.Such systems require relatively little technical support for oper-ation and can provide steady or slowly varying magnetic ®elds in moderate size volumes.The two principal disadvantages of conduction cooled low temperature superconducting magnets are that the magnet must be extremely well thermally insulated to stay under the allowable 4K heat removal ca-pacity of about 1W.This requirement often es-tablishes a limit to the size and operating current of conduction cooled LTS magnets as well as on the cool down time.Also,these magnets are in-herently unstable due to small heat capacity at 4K and thus must be operated with care to minimize AC loss and other disturbances that might quench the magnet.Many of the problems of scaling up conduction cooled magnet systems are alleviated when con-sidering HTS magnet systems operating at signif-icantly higher temperatures.At high temperatures the heat capacity of the magnet is much larger than its value at 4K.For example,at 30K the speci®c heat of magnet materials is about 250times that at 4K.This feature enhances the ther-mal stability of the magnet and allows larger AC loss,faster ramp and more reliable operation.InFig.5.45T hybrid magnet cryostat at theNHMFL.Fig.4.Two 500mm bore,5T reciprocating ore separator magnets in the Brazilian rain forest.S.W.Van Sciver /Physica C 354(2001)129±135133addition,since HTS magnets operate at 30K or above,the cryocooler technology is signi®cantly easier.Currently,commercial single stage GM cryocoolers with cooling powers in excess of 100W at 30K are rger cooling power and greater thermal capacity should allow for the de-velopment of larger conduction cooled magnet systems.Still one inherent disadvantage of direct cooling only is that the magnet has essentially no thermal store to permit continued operation should the cryocooler fail.Reliability can be built into the system by providing duplicate compo-nents (cold heads,compressors,etc.)but there are still limits to how well the system can be main-tained during a cooling system breakdown.In an e ort to provide magnets systems that still use cryocoolers for refrigeration but also can continue operation for some period of time,hybrid systems (which include liquid cryogen and cryo-coolers)have been developed.This approach was ®rst developed for MRI magnet systems,where the small liquid helium boil-o can be recondensed using a 4K two stage GM cryocooler to achieve essentially a zero-helium loss system.This concept has also been developed for conduction cooled LTS magnets where a small liquid helium reservoir is used to increase stability of the magnet [6].For HTS magnet systems that operate at higher temperatures,e.g.T 30K,it may similarly be desirable to provide a thermal reservoir to main-tain the system cold and operational even if the cryocooler is in service.This could be achieved by utilizing a small contained volume of liquid neon in direct contact with the superconducting magnet and cooled with a single stage cryocooler.Such a device would have signi®cant advantages over conventional direct cooling mostly in terms of re-liability of operation.4.SummaryThe goal of any superconducting magnet cryo-genics system should be to have minimum impact on the operation of the magnet.To achieve this goal,the cryogenic system must bring the magnet to its operating temperature,reliably maintain it at that temperature for as long as necessary.It also needs to deliver this condition at modest cost.At present most superconducting magnet cryogenic systems do not meet these requirements.For the most part,the systems are too capital intensive,require too much maintenance and technical sup-port.However,the recent combined development of high performance cryocoolers,HTS current leads and HTS magnets have allowed the appli-cation of considerably simpler cryogenic systems.Future magnet systems should bene®t from these technologies.AcknowledgementsThe National High Magnetic Field Laboratory is supported by the National Science Foundation and the State of Florida under grant DMR-9527035.The author also expresses appreciationtoFig.6.Conduction cooled 9T,32mm warm bore supercon-ducting NbTi magnet cooled by a 4K pulse tube cryocooler (Cryomagnetics,Inc.).134S.W.Van Sciver /Physica C 354(2001)129±135D.Richards of Carpco/Otokumpu and C.Wang of Cryomech,Inc.for technical information.References[1]R.A.Burns,M.A.Green,Adv.Cryog.Engng.43(1998)1661.[2]H.O.McMahon,W.E.Gi ord,Adv.Cryog.Engng.5(1960)354.[3]R.Radebaugh,J.Zimmerman,D.Smith,Adv.Cryog.Engng.31(1986)779.[4]ng,H.Hafner,C.Heiden,Adv.Cryog.Engng.43(1998)1573.[5]ler,et al.,IEEE Trans.Magn.30(1994)1563.[6]J.W.Burgoyne,P.Daniels,K.Timms,S.Vale,IEEE Trans.Appl.Supercond.10(2000)703.S.W.Van Sciver/Physica C354(2001)129±135135。