车身连接强度检验介绍
汽车车身强度标准

汽车车身强度标准全文共四篇示例,供读者参考第一篇示例:汽车车身强度是指汽车车身在发生碰撞或受到外部冲击时所能承受的力量。
车身强度标准是制定汽车安全标准的重要组成部分之一,它直接关系到乘客在车祸中的安全性。
汽车车身强度标准的制定和执行对提高汽车安全性和减少交通事故的发生具有重要意义。
在现代社会,汽车已成为人们生活中不可或缺的交通工具,然而交通事故频发,给人们的生命财产造成了巨大的损失。
汽车的安全性成为了汽车制造商以及政府部门一直十分重视的问题。
而汽车车身强度恰恰就是汽车安全性的一个重要方面。
汽车车身强度标准通常包括车身材料、车身结构设计、车身抗撞性能等内容。
车身材料是决定车身强度的基础。
目前,汽车车身的主要材料有钢铁、铝合金、碳纤维等。
钢铁是目前汽车车身主要的材料,因其良好的强度和韧性而被广泛应用。
而汽车车身的结构设计也是影响车身强度的关键因素之一。
合理的结构设计能够使汽车车身在碰撞或受到冲击时更加稳定和坚固,从而减少乘客受伤的概率。
车身的抗撞性能也是评价汽车车身强度的重要指标之一。
抗撞性能包括车身的抗压、抗拉、抗弯等性能。
汽车车身要能够在碰撞事故中承受住外部的压力,从而保护乘客的安全。
汽车车身强度标准的制定要从整体上考虑汽车的安全性和可靠性。
制定汽车车身强度标准需要进行广泛的研究和测试,并结合实际情况进行合理的设计。
汽车车身强度标准的执行也是至关重要的。
只有确保汽车制造商严格按照标准制造汽车,才能真正保障乘客在车祸中的安全。
在全球范围内,各国对汽车车身强度标准的规定不尽相同。
欧美等发达国家对汽车的安全性要求较高,制定了相对严格的汽车车身强度标准。
而一些新兴国家对汽车的安全性要求较低,汽车车身强度标准相对较为宽松。
一些国际组织也出台了相关的汽车安全标准,如欧洲UN/ECE R94碰撞标准、美国FMVSS 208碰撞标准等。
汽车车身强度标准的不断提高是汽车安全性发展的必然趋势。
随着科技的进步和人们生活水平的提高,人们对汽车安全性的要求也越来越高。
车载测试中的车身结构强度与刚度测试技术

车载测试中的车身结构强度与刚度测试技术随着汽车工业的快速发展和技术的不断进步,车辆的安全性能及各种性能指标的测试已成为汽车制造商和消费者重视的焦点。
而车身结构强度与刚度是衡量汽车安全性能的重要指标之一。
本文将介绍车载测试中的车身结构强度与刚度测试技术,并探讨其在汽车设计与制造中的应用。
一、背景介绍车身结构强度与刚度是指汽车车身在受到外部载荷作用时的抗变形与抗破坏能力。
它们直接关系到车辆的安全性能和乘客的生命安全。
因此,对车身结构的强度与刚度进行准确的测试和评估是非常重要的。
二、测试方法1. 静态弯曲测试静态弯曲测试是一种常用的测试方法,通过在汽车车身上施加静载来评估车身的强度与刚度。
这种测试方法可以模拟车辆行驶过程中受到的不同载荷,如悬架系统的压力、载荷和冲击力。
通过测量汽车车身的形变和应力分布,可以评估车身的强度和刚度。
2. 动态碰撞测试动态碰撞测试是一种用来评估车身结构强度和刚度的重要测试方法。
在这种测试中,使用碰撞试验装置模拟不同方向和速度的碰撞情况,以评估车身在碰撞时的变形和损坏情况。
这种测试方法可以帮助设计师改进车辆的结构,提高碰撞时的安全性能。
3. 模态测试模态测试用于评估车身结构的固有振动特性,包括固有频率、固有振型和振动模态等信息。
通过模态测试可以了解车身结构的刚度及其在不同频率下的振动特性,以及确定设计中可能存在的问题。
这对于优化车身结构以提高刚度和减少振动有很重要的意义。
三、技术应用车身结构强度与刚度测试技术在汽车设计与制造中有着广泛的应用。
首先,它可以帮助汽车制造商评估和改进车辆结构,确保车辆在日常使用和不同情况下具备足够的强度和刚度。
其次,这些测试结果还可以为汽车工程师提供重要的数据,用于优化车身结构,提高车辆的性能和安全性。
此外,现代汽车制造业中还出现了车载测试设备的发展,这些设备可以模拟不同的驾驶条件和道路状况,以评估车辆在不同环境下的结构强度和刚度。
这为汽车设计和制造提供了更加准确和全面的数据支持。
白车身强度分析报告

白车身强度分析报告1. 引言白车身是指汽车的主体骨架部分,它承受着车辆的重量和各种外部力的作用。
白车身的强度是保证车辆在运行过程中能够承受各种力和压力而不发生变形或破裂的重要指标。
本文将对白车身的强度进行分析,以提供有关白车身设计和改进的参考。
2. 强度分析方法为了分析白车身的强度,我们可以采用有限元分析(FEA)方法。
有限元分析是一种工程设计和分析的常用方法,通过将结构细分为有限数量的元素,利用数值计算方法对每个元素进行分析,从而得出整个结构的行为。
以下是强度分析的步骤:2.1 几何建模首先,需要建立一个准确的白车身的几何模型。
可以利用计算机辅助设计(CAD)软件或三维扫描技术获得车身的三维模型。
2.2 材料属性定义每种材料都有其特定的力学性质,如弹性模量、屈服强度和断裂韧性等。
在分析中,需要将这些材料属性定义在模型中。
2.3 边界条件设定在分析中,需要考虑车身受到的各种外部力和约束条件。
这些外部力可以是来自引擎、悬挂系统或碰撞等。
同时,还需要考虑车身的支撑条件和连接点的约束。
2.4 网格划分为了对车身进行数值计算,需要将其细分为有限数量的元素。
这些元素可以是三角形、四边形或六边形等。
网格划分的密度和精度对分析结果的准确性有很大影响。
2.5 载荷施加在分析中,需要根据实际情况施加各种载荷,如静载荷、动载荷和碰撞载荷等。
这些载荷将作用于车身结构上,并导致应力和变形的产生。
2.6 求解和结果分析经过以上步骤的准备,可以使用有限元软件对车身进行数值计算。
通过求解有限元方程,可以得到车身在不同载荷下的应力和变形分布。
然后,可以对分析结果进行评估和比较,以了解车身的强度和刚度。
3. 强度改进措施根据强度分析结果,可以提出一些改进措施来增强白车身的强度和刚度。
以下是一些常见的改进措施:3.1 材料优化选择具有更高强度和刚度的材料,如高强度钢或铝合金,可以显著提高白车身的整体强度。
3.2 结构优化通过对车身结构进行优化设计,可以减少材料的使用量,同时提高整体的强度。
汽车车身强度分析技术打造坚固安全的驾乘空间

汽车车身强度分析技术打造坚固安全的驾乘空间在汽车设计与制造过程中,确保驾乘空间的坚固安全是至关重要的一环。
汽车车身强度分析技术作为现代汽车制造领域的重要工具,可以帮助工程师们将车辆的结构设计得更加牢固,提供更安全的驾乘环境。
本文将探讨汽车车身强度分析技术的应用,并重点介绍几种常见的分析方法。
1. 强度分析概述汽车车身的强度分析是通过计算和模拟车辆受力情况,评估车身结构的强度和刚度。
这项技术可以为汽车制造商提供关键的工程数据,以确保车辆在不同的受力情况下能够承受压力并保持结构完整性。
强度分析通常包括静态刚度分析、动态强度分析以及车辆碰撞测试等。
2. 静态刚度分析静态刚度分析是评估车辆结构在不同工况下的刚度特性。
通过使用有限元分析方法,可以计算出车辆受到各种载荷(如转矩、相对位移和弯曲力)时产生的刚度响应。
这些数据可以用于优化车辆结构设计,确保车身在正常使用时具有足够的刚度,以提供稳定的驾乘体验和安全性能。
3. 动态强度分析动态强度分析是评估车辆在行驶过程中受到不同路况和振动影响时的强度表现。
通过结合实验数据和计算模拟,可以分析车辆在路况不均匀、制动、悬挂系统振动等情况下的应力分布和变形情况。
这些数据有助于工程师们优化车辆结构,并确保在行驶过程中车身的强度和安全性得到充分保障。
4. 车辆碰撞分析车辆碰撞分析是汽车设计中最重要的一环,也是车辆安全性能的关键评估指标之一。
通过模拟车辆在不同碰撞情况下的响应,可以评估车辆结构所能承受的冲击力和吸能能力,并且预测车辆在各种碰撞条件下的变形和破坏情况。
这些分析结果可以指导车辆设计和制造过程,确保驾乘空间的安全性。
5. 刚性体结构分析刚性体结构分析是一种广泛应用于汽车设计领域的分析方法。
它通过建立汽车车身模型,并应用有限元分析,计算车身结构的应力和应变等物理量。
通过这种分析方法,工程师们可以评估车身结构的刚度、强度和稳定性,并及时发现存在的问题。
这使得设计师们能够针对性地进行结构优化,确保驾乘空间的坚固安全。
汽车车身结构强度

汽车车身结构强度引言汽车车身结构强度是衡量汽车安全性能的重要指标之一。
一个具有高强度车身的汽车在碰撞、侧翻和颠簸等情况下能更好地保护乘客的安全。
本文将介绍汽车车身结构强度的定义、相关测试方法和常见的强度设计措施。
定义汽车车身结构强度是指车身在外部力量作用下抵抗变形和破坏的能力。
它是通过承受和传递荷载来保护乘客免受伤害的关键。
强度设计旨在确保在意外事故中车身能够保持结构完整性和乘客舱的相对稳定性,从而最大程度地减轻事故对乘客的影响。
测试方法汽车车身结构强度测试是评估车身在碰撞、侧翻和颠簸等情况下的安全性能的关键测试之一。
以下是一些常见的强度测试方法:1.正面碰撞测试:通过模拟两辆车正面相撞的情况,评估车身前部的强度和能量吸收能力。
2.侧面碰撞测试:模拟侧面撞击,评估车身对侧向冲击的抵抗能力。
3.颠簸测试:通过模拟车辆在不平路面上行驶的情况,评估车身结构对颠簸冲击的响应。
4.倒车撞击测试:评估车身在倒车时的强度和保护乘客的能力。
这些测试方法通常使用专业的测试设备和标准来进行。
测试结果将帮助制造商改进汽车车身设计,确保其满足安全性能要求。
强度设计措施为了提高汽车车身的结构强度,制造商采取了一系列的设计措施,如下所示:1.使用高强度钢:高强度钢材具有较高的屈服强度和抗拉强度,能够在受力时保持较小的变形。
在车身关键部位使用高强度钢材,可以提高整体车身的强度和刚性。
2.智能化加强梁系统:加强梁系统位于车身底部,能够在碰撞时吸收和分散能量。
智能化加强梁系统可以根据碰撞的严重程度自动调整刚度,提供更好的保护效果。
3.增加车身连接点:在车身结构设计中增加连接点,可以提高各个部件的相互支撑性和整体强度。
这有助于减轻碰撞时的应力集中和车身的变形。
4.预紧安全带系统:预紧安全带系统能够在碰撞前迅速紧绷,确保乘客在碰撞时能紧密地与座椅保持接触,减少意外伤害。
结论汽车车身结构强度是确保车辆安全性能的重要因素。
通过进行正面碰撞、侧面碰撞、颠簸等测试,制造商可以评估车身的强度和能量吸收能力。
汽车车身强度与刚度分析与优化
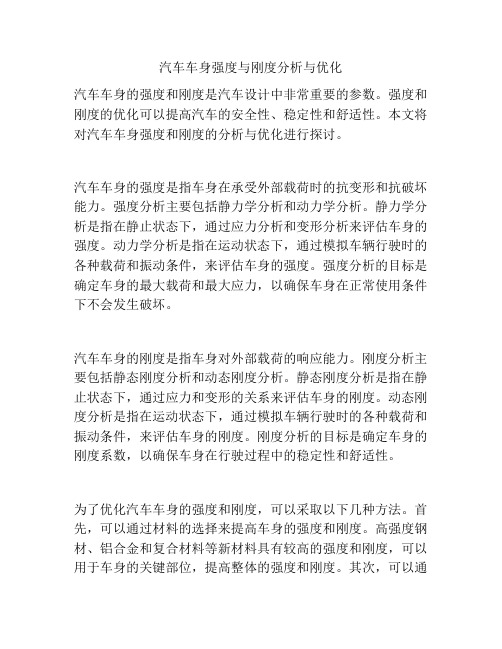
汽车车身强度与刚度分析与优化汽车车身的强度和刚度是汽车设计中非常重要的参数。
强度和刚度的优化可以提高汽车的安全性、稳定性和舒适性。
本文将对汽车车身强度和刚度的分析与优化进行探讨。
汽车车身的强度是指车身在承受外部载荷时的抗变形和抗破坏能力。
强度分析主要包括静力学分析和动力学分析。
静力学分析是指在静止状态下,通过应力分析和变形分析来评估车身的强度。
动力学分析是指在运动状态下,通过模拟车辆行驶时的各种载荷和振动条件,来评估车身的强度。
强度分析的目标是确定车身的最大载荷和最大应力,以确保车身在正常使用条件下不会发生破坏。
汽车车身的刚度是指车身对外部载荷的响应能力。
刚度分析主要包括静态刚度分析和动态刚度分析。
静态刚度分析是指在静止状态下,通过应力和变形的关系来评估车身的刚度。
动态刚度分析是指在运动状态下,通过模拟车辆行驶时的各种载荷和振动条件,来评估车身的刚度。
刚度分析的目标是确定车身的刚度系数,以确保车身在行驶过程中的稳定性和舒适性。
为了优化汽车车身的强度和刚度,可以采取以下几种方法。
首先,可以通过材料的选择来提高车身的强度和刚度。
高强度钢材、铝合金和复合材料等新材料具有较高的强度和刚度,可以用于车身的关键部位,提高整体的强度和刚度。
其次,可以通过优化车身结构来提高强度和刚度。
例如,增加加强筋和支撑结构,提高车身的整体刚度。
此外,还可以通过优化焊接和连接工艺,减少焊接接头的应力集中,提高车身的强度和刚度。
最后,可以通过模拟和仿真分析来优化车身的强度和刚度。
利用计算机辅助设计软件,可以对车身进行各种载荷和振动条件的仿真分析,以评估车身的强度和刚度,并进行优化设计。
总之,汽车车身的强度和刚度是汽车设计中非常重要的参数。
通过强度和刚度的分析与优化,可以提高汽车的安全性、稳定性和舒适性。
材料的选择、结构的优化和仿真分析等方法可以用于优化车身的强度和刚度。
随着科技的不断进步,汽车车身的强度和刚度将不断提高,为用户提供更加安全和舒适的驾驶体验。
FMVSS-571.221学童客车的车身联结强度

美国联邦机动车安全标准第571.221条学童客车的车身联结强度摘要:联邦机动车辆安全标准的第571.221条给出了学童客车的车身联结强度试验要求及试验过程。
1 范围本标准规定了校车车身面板联结强度要求。
2 目的本标准的目的是为了在校车车身碰撞过程中从结构崩溃上减少人员的伤亡。
3 适用性本标准适用于校车。
4 定义车身元件是指汽车车身上的一部分,它是由一单片均匀材料组成或者是一单片复合材料组成,如胶合板。
车身面板是指一个应用于外表面或内表面的车身元件,用来密封巴士中的乘员空间。
车身面板联结副是指在一个车身面板和另外的车身元件之间接触或接近的区域。
包括不限于地板,和由复合材料如塑料或胶合板制成的车身面板。
巴士车身是指巴士中包围乘员空间的那部分,包括地板和前围(从乘客区中分离的发动机舱车身面板),但是不包括保险杠和底盘框架和前方的最前点的任何结构挡风玻璃的安装。
维护检修面板是指一个车身面板,它必须可以被移动或拆卸以便获得一个或多个可维修组件。
乘客区是指位于校车内部的空间,在最前面的乘客座位前面762毫米的垂直横向平面参考点和在汽车中心线的后部内壁包含有一个垂直横向平面切线之间。
维修组件是指汽车上的任一零件,无论是具有机械或电子特性,都在客车底盘及车身制造商的使用说明书或厂家售后服务手册上有明确确定需要在一年或一年以内进行日常维护。
管路、电线及线束只有在附件上才是维修组件。
5 要求5.1 除了5.2,每个车身面板接头应符合5.1.1和5.1.2。
5.1.1 车身面板互相联结是在结合处将不会有任何超过203毫米未联结的段。
5.1.2 按照第6条的测试步骤测试时,每一个车身面板接头应保持每个车身面板到组件上,联结时受到相当于车身最弱处联结强度的60%的力,由此来确定6.2。
5.2 不包括的内容5.2.1以上5.1.1和5.1.2不适用于以下:(1)任何位于前方乘客区的室内维修面板或者两点之间测得的相对直径超过305毫米的维修面板。
白车身焊接强度检验控制管理办法

南京汽车集团有限公司车身生产部管理标准白车身焊接强度检验控制管理办法版本C NAC 31 / G 0402-20091 范围1.1 本准则规定了车身生产部白车身焊接质量评定的方法、要求与频次,确保各车型白车身焊接质量评定结果的可比性。
1.2 本评定方法适用于车身生产部白车身自制件及采购件所有焊接质量的评定。
2 定义2.1 焊接强度:是指对焊缝(熔核)及其周围母材热影响区组织的抗拉性能和屈服性能的可靠性评价。
2.2 破坏检验:指将工具插入焊接部件直到零部件彻底分离,通过检查焊缝尺寸大小,以确定焊缝的可靠性。
2.3 直观检查:是指通过目视观察的方法,检查焊缝的数量、位臵和外观成型等质量。
2.4 非破坏性检查(无损凿检):指将凿子敲入(或敲击)焊接工件,当整个工件变形达到焊点拉长而焊缝无断裂或损坏的一种试验方法。
3 职责3.1 技术平台负责制订《车身生产部白车身焊接强度检验控制管理方法》。
3.2 生产工段依据焊接质量评定方法通过首检、过程自检、抽检等方法,负责对生产所涉及到的所有焊接质量实施过程控制。
3.3 质量保证部负责直观及无损焊接质量检查的巡检、白车身总成分总成破坏性焊接质量检验、焊接金相检验、并依据此办法对焊接质量做出最终的质量评定。
4 管理内容4.1 点焊质量评定4.1.1 点焊缺陷数量的评定由于车身焊点设计都有安全系数,凡符合下表情形的,焊接质量可判定为合格,不必要求追溯(缺陷焊点不得连续发生,不得出现在焊接件首尾焊点)。
4.1. 2 点焊质量评定4.1. 3 焊点间距及焊点与边距的要求焊点间距与边缘距离的技术要求(单位:mm):e为焊点间点距,v为焊点边缘距离板材厚度比t v=0.8×t1+0.2×t2,t1:薄板厚度,t2:厚板厚度。
A类焊点:+3mm;B类焊点:+6mm;C类焊点:+9mm,负的误差受到最小焊点间距离的限制。
注:A类焊点:那些如果发生误差和疏忽可能导致人生安全的焊点;B类焊点:在故障发生的情况下往往会造成产品无法照常使用或导致一些财产损失;C类焊点:如果在连续中发生故障,它将对产品的正常使用等几乎没有影响。
- 1、下载文档前请自行甄别文档内容的完整性,平台不提供额外的编辑、内容补充、找答案等附加服务。
- 2、"仅部分预览"的文档,不可在线预览部分如存在完整性等问题,可反馈申请退款(可完整预览的文档不适用该条件!)。
- 3、如文档侵犯您的权益,请联系客服反馈,我们会尽快为您处理(人工客服工作时间:9:00-18:30)。
表面杂质
咬边
不合格
操作问题
h<0.1t
—部门: 奥迪质保部 轿车一厂质保科 P-Q-AU-2—时间:2012-09-20—第22页/共52页
MIG/MAG
破坏性检验
Q A
u lity ssurance
SN(最小焊缝厚度)>tmin, f(熔深)>0.2mm
无熔深
气孔 P<0.1焊缝截面
—部门: 奥迪质保部 轿车一厂质保科 P-Q-AU-2—时间:2012-09-20—第23页/共52页
Q A
u lity ssurance
11:30-13:30 午休 13:30-15:30 破检操作实践
•缺陷实物展示 •目视检查练习(分组对比) •破坏性检验实际操作 •缺陷判定练习(分组对比) •提问交流
—部门: 奥迪质保部 轿车一厂质保科 P-Q-AU-2—时间:2012-09-20—第2页/共52页
Q A
经验交流
u lity ssurance
F4:点焊焊接一般进行锤击检查,母材撕裂到什么程度才算 合格? A:点焊的连接标准:焊核直径大于或者等于最小点径。 F5:焊接螺母扭矩检查合格,却没有明显的粘连是否合格? A:焊接螺母的评价
F6:点焊对压痕深度是否有要求,要求是多少?特别是三层 板? A:点焊的连接标准;
操作问题
位置
三层板错焊成两层板 V>1.25dmin 门框区域热成型钢板 VE>2.5mm
—部门: 奥迪质保部 轿车一厂质保科 P-Q-AU-2—时间:2012-09-20—第11页/共52页
点焊
目视检查
Q A
u lity ssurance
毛刺 飞溅
焊接电流过大
变形
电极未对中
—部门: 奥迪质保部 轿车一厂质保科 P-Q-AU-2—时间:2012-09-20—第12页/共52页
焊接螺柱、螺母
目视检查
Q A
u lity ssurance
螺纹通过性
焊接电流过大
—部门: 奥迪质保部 轿车一厂质保科 P-Q-AU-2—时间:2012-09-20—第29页/共52页
焊接螺柱、螺母
角度
目视检查
Q A
u lity ssurance
焊枪未对中
焊瘤
焊接电流过大
必须进行返修处理!
—部门: 奥迪质保部 轿车一厂质保科 P-Q-AU-2—时间:2012-09-20—第30页/共52页
点焊
破坏性检验
Q A
u lity ssurance
•合格≧dpmin •dpmin >有条件合格≧85% dpmin •不合格<85% dpmin
例:dpmin =5mm; b.i.o:4.25mm~5mm;
Soll:4.6mm ist:4.0mm b.i.o
n.i.o:<4.25mm
n.i.o
—部门: 奥迪质保部 轿车一厂质保科 P-Q-AU-2—时间:2012-09-20—第15页/共52页
—部门: 奥迪质保部 轿车一厂质保科 P-Q-AU-2—时间:2012-09-20—第17页/共52页
MIG/MAG
目视检查
数量
Q A
u lity ssurance
长度
—部门: 奥迪质保部 轿车一厂质保科 P-Q-AU-2—时间:2012-09-20—第18页/共52页
MIG/MAG
位置
目视检查
Q A 议题
连接强度检验概述 点焊的强度检验及标准 MAG/MIG的强度检验及标准 焊接螺柱、螺母检验及标准
u lity ssurance
经验交流
—部门: 奥迪质保部 轿车一厂质保科 P-Q-AU-2—时间:2012-09-20—第41页/共52页
Q A
经验交流
u lity ssurance
F1:焊接强度检验频次怎么确定,1件/班次是否合理? A:焊接强度检验频次由车间、规划和质保3方一起制定,在不同的过程 稳定性状态下,频次是不相同的;
—部门: 奥迪质保部 轿车一厂质保科 P-Q-AU-2—时间:2012-09-20—第34页/共52页
Q A
u lity ssurance
焊接螺柱、螺母(凸焊) 破坏性检查(金相)
>0.2mm
—部门: 奥迪质保部 轿车一厂质保科 P-Q-AU-2—时间:2012-09-20—第35页/共52页
焊接螺柱(引弧) 破坏性检查
点焊
目视检查
Q A
u lity ssurance
压痕深
10%t , 20%t
焊接电流过大 /匹配间隙大
表面裂纹,过烧
—部门: 奥迪质保部 轿车一厂质保科 P-Q-AU-2—时间:2012-09-20—第13页/共52页
点焊Biblioteka 破坏性检验Q Au lity ssurance
—部门: 奥迪质保部 轿车一厂质保科 P-Q-AU-2—时间:2012-09-20—第14页/共52页
Q A 议题
连接强度检验概述
u lity ssurance
点焊的强度检验及标准
MAG/MIG的强度检验及标准 焊接螺柱、螺母检验及标准 经验交流
—部门: 奥迪质保部 轿车一厂质保科 P-Q-AU-2—时间:2012-09-20—第10页/共52页
点焊
目视检查
Q A
u lity ssurance
数量
焊接螺柱、螺母
数量
目视检查
Q A
u lity ssurance
—部门: 奥迪质保部 轿车一厂质保科 P-Q-AU-2—时间:2012-09-20—第27页/共52页
焊接螺柱、螺母
位置
目视检查
Q A
u lity ssurance
—部门: 奥迪质保部 轿车一厂质保科 P-Q-AU-2—时间:2012-09-20—第28页/共52页
Q A 焊接螺柱、螺母(凸焊) 破坏性检查
u lity ssurance
顶出力检查
—部门: 奥迪质保部 轿车一厂质保科 P-Q-AU-2—时间:2012-09-20—第31页/共52页
Q A 焊接螺柱、螺母(凸焊) 破坏性检查
u lity ssurance
顶出力检查
—部门: 奥迪质保部 轿车一厂质保科 P-Q-AU-2—时间:2012-09-20—第32页/共52页
Q A
u lity ssurance
车身连接强度检验
—部门: 奥迪质保部 轿车一厂质保科 P-Q-AU-2—时间:2012-09-20—第1页/共52页
日程安排: 8:45-11:30 理论培训+提问讨论
•连接强度检验概述 •点焊的强度检验 •MAG/MIG强度检验 •休息 •焊接螺母及螺柱强度检验 •提问交流 (车身焊接胶的检验)
焊接螺柱、螺母(凸焊) 破坏性检查(扁铲)
Q A
u lity ssurance
—部门: 奥迪质保部 轿车一厂质保科 P-Q-AU-2—时间:2012-09-20—第33页/共52页
Q A
u lity ssurance
焊接螺柱、螺母(凸焊) 破坏性检查(扁铲)
Soll 4.0mm ist 4.0mm
破坏性检验
扁铲试验
Q A
金相试验
u lity ssurance
力学性能试验
扁铲枪
高频打磨机
—部门: 奥迪质保部 轿车一厂质保科 P-Q-AU-2—时间:2012-09-20—第8页/共52页
非破坏性检验
扁铲试验
Q A
力矩检验
u lity ssurance
—部门: 奥迪质保部 轿车一厂质保科 P-Q-AU-2—时间:2012-09-20—第9页/共52页
MIG/MAG
目视检查
Q A
u lity ssurance
母材过烧 不合格
焊穿
不合格
焊接电流过大 焊接时间过长
—部门: 奥迪质保部 轿车一厂质保科 P-Q-AU-2—时间:2012-09-20—第21页/共52页
MIG/MAG
目视检查
Q A
u lity ssurance
D<0.3有效焊缝厚度
气孔 不合格
—部门: 奥迪质保部 轿车一厂质保科 P-Q-AU-2—时间:2012-09-20—第43页/共52页
Q A
经验交流
u lity ssurance
F7:破坏性检验是否可以不用零件去做,而采用相同 材料、相同板厚的试片代替? A:试片的使用一般是在项目初期,焊钳调试参数时 用。在批量生产过程中,对零件的破坏性检验是必 不可少的。 例:四门、两盖结构无法进行非破检,可以采用两 种方式进行监控: 1、试片; 2、超声波无损检测; 但是必须定期进行破坏性检验 验证。
MIG/MAG
破坏性检验
Q A
u lity ssurance
合格
开焊
零件匹配间隙大
—部门: 奥迪质保部 轿车一厂质保科 P-Q-AU-2—时间:2012-09-20—第24页/共52页
MIG/MAG
Q A
u lity ssurance
没有非破坏性检验; 要求操作者 按照目视检查标准100% 自检; 终检工位100%检查,一旦目视检查 不合格,必须进行返修处理
Q A
u lity ssurance
—部门: 奥迪质保部 轿车一厂质保科 P-Q-AU-2—时间:2012-09-20—第19页/共52页
MIG/MAG
目视检查
Q A
u lity ssurance
裂纹
裂纹
不合格
填充物堆积太高
不合格
焊接电流过大 焊接时间过长 表面杂质
—部门: 奥迪质保部 轿车一厂质保科 P-Q-AU-2—时间:2012-09-20—第20页/共52页