Structure-sensitive CO2 electroreduction to hydrocarbons on-SI
非富勒烯有机受体-共扼聚合物太阳能电池的研究
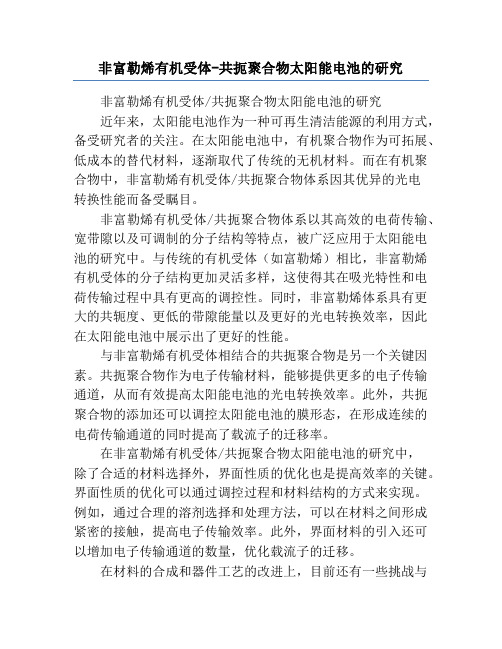
非富勒烯有机受体-共扼聚合物太阳能电池的研究非富勒烯有机受体/共扼聚合物太阳能电池的研究近年来,太阳能电池作为一种可再生清洁能源的利用方式,备受研究者的关注。
在太阳能电池中,有机聚合物作为可拓展、低成本的替代材料,逐渐取代了传统的无机材料。
而在有机聚合物中,非富勒烯有机受体/共扼聚合物体系因其优异的光电转换性能而备受瞩目。
非富勒烯有机受体/共扼聚合物体系以其高效的电荷传输、宽带隙以及可调制的分子结构等特点,被广泛应用于太阳能电池的研究中。
与传统的有机受体(如富勒烯)相比,非富勒烯有机受体的分子结构更加灵活多样,这使得其在吸光特性和电荷传输过程中具有更高的调控性。
同时,非富勒烯体系具有更大的共轭度、更低的带隙能量以及更好的光电转换效率,因此在太阳能电池中展示出了更好的性能。
与非富勒烯有机受体相结合的共扼聚合物是另一个关键因素。
共扼聚合物作为电子传输材料,能够提供更多的电子传输通道,从而有效提高太阳能电池的光电转换效率。
此外,共扼聚合物的添加还可以调控太阳能电池的膜形态,在形成连续的电荷传输通道的同时提高了载流子的迁移率。
在非富勒烯有机受体/共扼聚合物太阳能电池的研究中,除了合适的材料选择外,界面性质的优化也是提高效率的关键。
界面性质的优化可以通过调控过程和材料结构的方式来实现。
例如,通过合理的溶剂选择和处理方法,可以在材料之间形成紧密的接触,提高电子传输效率。
此外,界面材料的引入还可以增加电子传输通道的数量,优化载流子的迁移。
在材料的合成和器件工艺的改进上,目前还有一些挑战与瓶颈需要克服。
例如,非富勒烯有机受体的合成方法复杂,制备成本较高,还需要进一步降低材料成本。
此外,器件的稳定性和尺寸的可扩展性也需要进一步改进。
总结起来,非富勒烯有机受体/共扼聚合物太阳能电池的研究展示出了潜在的高效能源转换性能。
在材料的选择、界面性质的优化以及合成工艺的改进等方面,还存在着一些挑战和需求进一步解决。
通过持续的研究和不断的改进,相信非富勒烯有机受体/共扼聚合物太阳能电池将在未来成为一种重要的可再生能源转换技术综上所述,非富勒烯有机受体/共扼聚合物太阳能电池具有潜力成为一种高效的可再生能源转换技术。
co2选择性电化学还原的研究概况
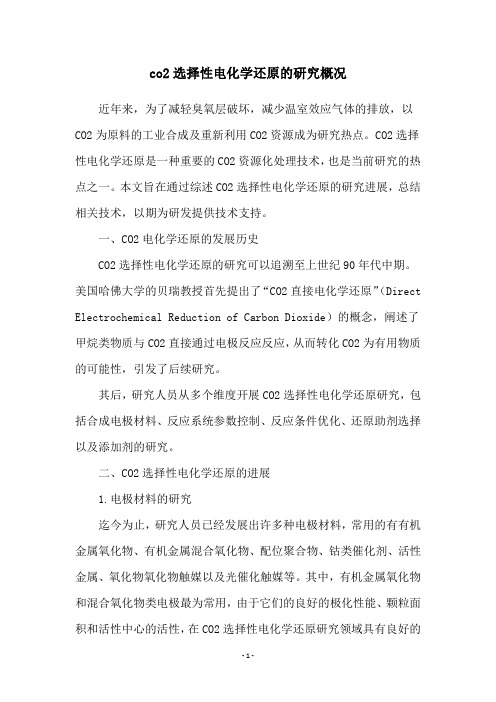
co2选择性电化学还原的研究概况近年来,为了减轻臭氧层破坏,减少温室效应气体的排放,以CO2为原料的工业合成及重新利用CO2资源成为研究热点。
CO2选择性电化学还原是一种重要的CO2资源化处理技术,也是当前研究的热点之一。
本文旨在通过综述CO2选择性电化学还原的研究进展,总结相关技术,以期为研发提供技术支持。
一、CO2电化学还原的发展历史CO2选择性电化学还原的研究可以追溯至上世纪90年代中期。
美国哈佛大学的贝瑞教授首先提出了“CO2直接电化学还原”(Direct Electrochemical Reduction of Carbon Dioxide)的概念,阐述了甲烷类物质与CO2直接通过电极反应反应,从而转化CO2为有用物质的可能性,引发了后续研究。
其后,研究人员从多个维度开展CO2选择性电化学还原研究,包括合成电极材料、反应系统参数控制、反应条件优化、还原助剂选择以及添加剂的研究。
二、CO2选择性电化学还原的进展1.电极材料的研究迄今为止,研究人员已经发展出许多种电极材料,常用的有有机金属氧化物、有机金属混合氧化物、配位聚合物、钴类催化剂、活性金属、氧化物氧化物触媒以及光催化触媒等。
其中,有机金属氧化物和混合氧化物类电极最为常用,由于它们的良好的极化性能、颗粒面积和活性中心的活性,在CO2选择性电化学还原研究领域具有良好的性能。
2.反应参数控制控制反应系统的参数是CO2选择性电化学还原效率的关键,包括电极电流密度、反应温度和反应压力等。
研究发现,当反应温度从室温升高至100℃或以上时,反应还原产物的收率会大大增加;当电极电流密度升高至2 mA/cm2时,CO2选择性电化学还原的效率也会大大提高;同时,降低反应压力也能够增加反应的收率。
3.反应条件优化研究表明,空气氧含量、水含量和添加剂等反应条件均会对CO2选择性电化学还原产物收率带来重要影响。
为了提高CO2选择性电化学还原的效率,需要考虑这些反应条件,并进行有效优化。
电催化二氧化碳还原催化剂、电解液、反应器和隔膜研究进展

物 理 化 学 学 报Acta Phys. -Chim. Sin. 2023, 39 (12), 2302037 (1 of 24)Received: February 23, 2023; Revised: March 28, 2023; Accepted: March 28, 2023; Published online: April 4, 2023. *Correspondingauthor.Email:**************.cn;Tel:+86-21-67792379;Fax:+86-21-67792159.The project was supported by the “Scientific and Technical Innovation Action Plan” Hong Kong, Macao and Taiwan Science & Technology Cooperation Project of Shanghai Science and Technology Committee, China (19JC1410500) and the National Natural Science Foundation of China (91645110). 上海市“科技创新行动计划”港澳台科技合作(19JC1410500)和国家自然科学基金(91645110)资助项目© Editorial office of Acta Physico-Chimica Sinica[Review]doi: 10.3866/PKU.WHXB202302037Research Advances in Electrocatalysts, Electrolytes, Reactors and Membranes for the Electrocatalytic Carbon Dioxide Reduction ReactionLuwei Peng 1,3, Yang Zhang 1, Ruinan He 1, Nengneng Xu 1, Jinli Qiao 1,2,*1 State Key Laboratory for Modification of Chemical Fibers and Polymer Materials, College of Environmental Science and Engineering,Donghua University, Shanghai 201620, China.2 Shanghai Institute of Pollution Control and Ecological Security, Shanghai 200092, China.3 Department of Applied Physics, Hong Kong Polytechnic University, Hong Kong 999077, China.Abstract: Human activities primarily rely on the consumption of the fossil energy, which has led to an energy crisis and environmental pollution. Since the industrial revolution, the atmospheric CO 2 concentration has been continuously increasing, and reached 414 × 10−6 in 2020, which has resulted in global warming and glacial ablation. Converting CO 2 into high-value-added fuels and chemicals can alleviate environmental problems, enable the storage of intermittent renewable energy (wind and solar power), and provide a new route for fuel synthesis. The electrochemical CO 2 reduction reaction (CO 2RR) has attracted extensive attention owing to its mild reaction conditions, controllability, environmental friendliness, and the ability to generate various products. There are four key steps in a typical CO 2RR: (1) charge transport (electrons are transported from the conductive substrate to the electrocatalyst); (2) surface conversion(CO 2 is adsorbed and activated on the surface of the catalyst); (3) charge transfer (electrons are transferred from the catalyst surface to the CO 2 intermediate); and (4) mass transfer (CO 2 diffuses from the electrolyte to the catalyst surface, and the products diffuse in the reverse pathway). The former two steps depend on the type of membrane and the development of highly conductive catalysts with abundant active sites, while the latter two steps rely on the properties of the electrolyte and the optimization of the electrolytic cell configuration. To meet the high-selectivity (> 90%), superior-activity (> 200 mA ∙cm −2), and excellent-stability (> 1000 h) requirements of the CO 2RR as per industrial standards, the design of efficient electrocatalysts has been a key research area in recent decades. However, other factors have rarely been investigated. In this review, we systematically summarize the development of electrocatalysts, effect of the electrolyte, progress in the development of the reactor, and type of membrane in the CO 2RR from industrial and commercial perspectives. First, we discuss how first-principles calculations can be used to determine the chemical rate for CO 2 reduction. Additionally, we discuss how in situ or operando techniques such as X-ray absorption measurements can reveal the theoretically proposed reaction pathway. The microenvironment (e.g., pH, anions, and cations) at the three-phase interface plays a vital role in achieving a high CO 2RR performance, which can be controlled by changing the electrolyte properties. Further, the suitable design and development of the reactor is very critical for commercial CO 2RR technology because CO 2RR reactors must efficiently utilize the CO 2 feedstock to minimize the cost of upstream CO 2 capture. Finally, different types of membranes based on different ion-transfer mechanisms can affect the CO 2RR performance. The development opportunities and challenges toward the practical application of the CO 2RR are also highlighted. Key Words: Electrochemical CO 2 reduction reaction; Electrocatalyst; Electrolyte; Membrane; Reactor;Industrialization电催化二氧化碳还原催化剂、电解液、反应器和隔膜研究进展彭芦苇1,3,张杨1,何瑞楠1,徐能能1,乔锦丽1,2,*1东华大学环境科学与工程学院,纤维材料改性国家重点实验室,上海 2016202上海市污染控制与生态安全研究院,上海 2000923香港理工大学应用物理系,香港999077摘要:人类社会的正常运转非常依赖化石能源,然而化石能源的消耗已导致能源危机和环境污染,同时空气中CO 2的含量从工业革命以来一直攀升。
二氧化碳电催化英文文献
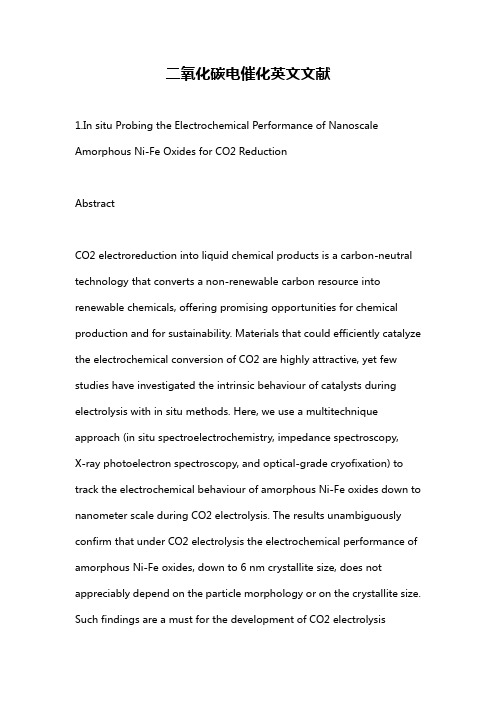
二氧化碳电催化英文文献1.In situ Probing the Electrochemical Performance of Nanoscale Amorphous Ni-Fe Oxides for CO2 ReductionAbstractCO2 electroreduction into liquid chemical products is a carbon-neutral technology that converts a non-renewable carbon resource into renewable chemicals, offering promising opportunities for chemical production and for sustainability. Materials that could efficiently catalyze the electrochemical conversion of CO2 are highly attractive, yet few studies have investigated the intrinsic behaviour of catalysts during electrolysis with in situ methods. Here, we use a multitechnique approach (in situ spectroelectrochemistry, impedance spectroscopy,X-ray photoelectron spectroscopy, and optical-grade cryofixation) to track the electrochemical behaviour of amorphous Ni-Fe oxides down to nanometer scale during CO2 electrolysis. The results unambiguously confirm that under CO2 electrolysis the electrochemical performance of amorphous Ni-Fe oxides, down to 6 nm crystallite size, does not appreciably depend on the particle morphology or on the crystallite size. Such findings are a must for the development of CO2 electrolysisreactors that require nanostructured materials with improved performance.2.Catalytic oxidation of formaldehyde to CO2 and H2O oxidation on Iridium oxide-based thin filmsAbstractThe catalytic oxidation of formaldehyde to CO2 and H2O on thin films of mainly Iridium oxide-based catalysts with composition IrOx/CeO2 and reinforcements of TiO2 and La2O3 is studied. Samples with Ir/Ce molar ratios equal to 1, 0.75, and 0.5 are studied. The films were synthesised by pulsed laser deposition on aluminosilicate substrates. The FBRM particle size distributions obtained by laser diffraction showed particles between 10 and 250 nm, in all the films. The BET surface area measured were 22, 26 and 36 m2 /g for Ir 1, Ir 0.75 and Ir 0.5, respectively. The XRD showed that the films were only composed by amorphous around Iridium, for the different molar ratios. The catalytic performance was evaluated in a fixed-bed flow reactor and carbon dioxide and water vapour selectivitiesobtained with Ir 0.75 as high as 100%. Temporal stability tests showed fast and monotonic deterioration in the activity of the Ir 1, while the Ir 0.75 showed the highest stability on 60 h of operation. These results are promising results for the development of thin film-catalysts for the fine chemicals industry.。
骨架非稠合的非富勒烯受体
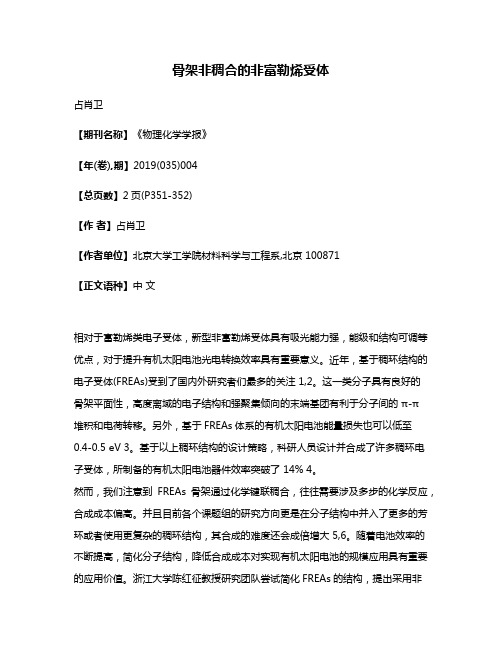
骨架非稠合的非富勒烯受体占肖卫【期刊名称】《物理化学学报》【年(卷),期】2019(035)004【总页数】2页(P351-352)【作者】占肖卫【作者单位】北京大学工学院材料科学与工程系,北京 100871【正文语种】中文相对于富勒烯类电子受体,新型非富勒烯受体具有吸光能力强,能级和结构可调等优点,对于提升有机太阳电池光电转换效率具有重要意义。
近年,基于稠环结构的电子受体(FREAs)受到了国内外研究者们最多的关注 1,2。
这一类分子具有良好的骨架平面性,高度离域的电子结构和强聚集倾向的末端基团有利于分子间的π-π堆积和电荷转移。
另外,基于FREAs体系的有机太阳电池能量损失也可以低至0.4-0.5 eV 3。
基于以上稠环结构的设计策略,科研人员设计并合成了许多稠环电子受体,所制备的有机太阳电池器件效率突破了 14% 4。
然而,我们注意到FREAs骨架通过化学键联稠合,往往需要涉及多步的化学反应,合成成本偏高。
并且目前各个课题组的研究方向更是在分子结构中并入了更多的芳环或者使用更复杂的稠环结构,其合成的难度还会成倍增大 5,6。
随着电池效率的不断提高,简化分子结构,降低合成成本对实现有机太阳电池的规模应用具有重要的应用价值。
浙江大学陈红征教授研究团队尝试简化FREAs的结构,提出采用非稠合环核作为构筑单元,利用分子内氢键构筑非富勒烯受体,成功制备了效率超过11%的有机太阳电池7,8,但其化学结构中仍包含了复杂的稠环结构。
如何使用巧妙的化学设计来避免复杂的稠环结构的使用,简化合成步骤,并且保留FREAs的优势,值得进一步研究。
最近,该团队进一步设计了一种结构简单的骨架非稠合的电子受体分子(ICTP),中心骨架仅有一个苯环和两个噻吩环;同时利用该团队之前掌握的碳氢活化技术 9,简单高效地合成了目标产物,并成功将其应用到了有机太阳电池中。
该工作已在物理化学学报上在线发表(doi: 10.3866/PKU.WHXB201805091) 10。
双功能羟基氧化铟催化剂中氧空位在生物质增值与co2转化电化学耦合中
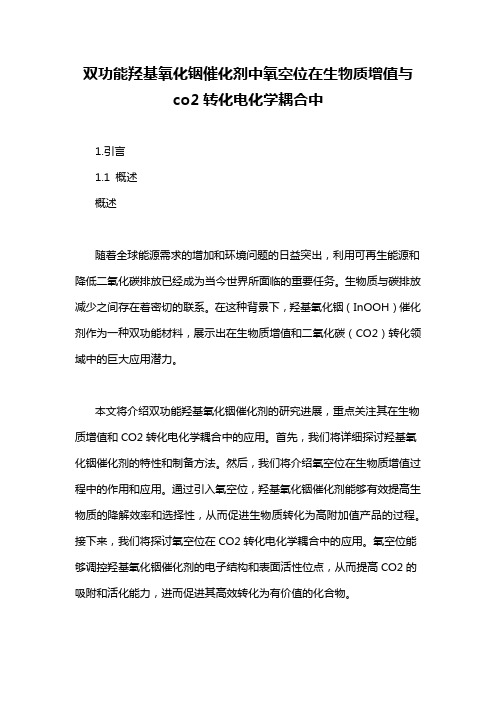
双功能羟基氧化铟催化剂中氧空位在生物质增值与co2转化电化学耦合中1.引言1.1 概述概述随着全球能源需求的增加和环境问题的日益突出,利用可再生能源和降低二氧化碳排放已经成为当今世界所面临的重要任务。
生物质与碳排放减少之间存在着密切的联系。
在这种背景下,羟基氧化铟(InOOH)催化剂作为一种双功能材料,展示出在生物质增值和二氧化碳(CO2)转化领域中的巨大应用潜力。
本文将介绍双功能羟基氧化铟催化剂的研究进展,重点关注其在生物质增值和CO2转化电化学耦合中的应用。
首先,我们将详细探讨羟基氧化铟催化剂的特性和制备方法。
然后,我们将介绍氧空位在生物质增值过程中的作用和应用。
通过引入氧空位,羟基氧化铟催化剂能够有效提高生物质的降解效率和选择性,从而促进生物质转化为高附加值产品的过程。
接下来,我们将探讨氧空位在CO2转化电化学耦合中的应用。
氧空位能够调控羟基氧化铟催化剂的电子结构和表面活性位点,从而提高CO2的吸附和活化能力,进而促进其高效转化为有价值的化合物。
通过本文的撰写和总结,我们旨在全面了解双功能羟基氧化铟催化剂的应用前景,为生物质增值和CO2转化电化学耦合领域的研究提供一定的指导和启示。
此外,我们还将展望氧空位在生物质增值与CO2转化电化学耦合中的未来发展方向,并提出一些建议和观点,以促进相关领域的进一步研究和应用推动可持续发展的进程。
文章结构部分主要介绍了整篇文章的组织结构,即各个章节的内容概述和连接关系。
文章结构的设计应当具有逻辑清晰、层次分明的特点,以确保读者能够快速把握文章的主旨和论点。
具体内容如下:1.2 文章结构本文主要分为引言、正文和结论三个部分,各个部分的内容安排如下:引言部分首先对本文的研究领域进行概述,介绍双功能羟基氧化铟催化剂在生物质增值和CO2转化电化学耦合中的重要性和应用前景。
接着阐述文章的结构,简要介绍各个章节的内容和主题。
引言部分的目的是引起读者的兴趣并明确本文的研究目的。
co2在ceo2的活化温度 -回复

co2在ceo2的活化温度-回复CO2在CEO2的活化温度引言:CO2是全球变暖的主要原因之一,其排放量的增加导致了地球气候的变化。
因此,寻找方法来减少CO2排放并将其转化为有价值的产物已成为科学界的研究热点。
CEO2是一种常见的催化剂,被广泛应用于化学工业中的多个领域。
因此,研究CO2在CEO2上的活化温度对于开发高效的CO2转化催化剂具有重要意义。
第一部分:CO2的结构和性质CO2是由一个碳原子和两个氧原子组成的分子,在常温常压下是一种无色无味的气体。
该分子是线性的,具有线性状分子的典型特征。
由于CO2分子中氧原子的电负性较高,这使得CO2具有一定的极性。
第二部分:CEO2的结构和性质CEO2(钙钛矿结构的二氧化钇)是一种重要的催化剂材料,其晶体结构是由钆原子和氧原子组成的。
CEO2具有较高的热稳定性和化学稳定性,并且在许多化学反应中表现出良好的催化性能。
此外,CEO2还具有良好的导电性和光学性能,使其在光催化和光电器件中具有广泛的应用前景。
第三部分:CO2在CEO2上的活化CO2在CEO2上的活化是将CO2转化为其他有用化合物的过程。
这种活化过程通常涉及复杂的化学反应,需要一定的催化剂和一定的温度条件。
研究表明,催化剂的选择和反应温度是影响CO2在CEO2上活化的关键因素之一。
第四部分:影响CO2活化温度的因素1. CEO2的晶体结构:CEO2的晶体结构中,钆原子和氧原子之间的键长和键角对CO2活化温度有重要影响。
晶体结构中键长较短、键角较小的CEO2通常具有较低的活化温度。
2. 催化剂表面的氧空位:氧空位是催化CO2活化反应的活性位点之一。
催化剂表面氧空位的数量和分布情况会影响CO2在CEO2上的活化能垒和活化温度。
3. 反应物浓度:CO2和其他反应物的浓度对CO2活化温度也有一定影响。
通常情况下,较高的反应物浓度能降低CO2活化温度。
第五部分:CO2活化温度的研究方法1. 理论计算方法:通过量子化学计算方法,可以计算得到CO2在CEO2上的活化能垒和活化温度。
电催化 co2还原中自由基对自旋态的有效磁场调节

电催化co2还原中自由基对自旋态的有效磁场调节
自旋态电催化CO2还原
随着全球温室气体排放的不断增加,CO2的浓度也在不断上升,加剧了全球变暖的问题。
因此,寻找一种高效、低成本的CO2还原方法变得尤为迫切。
自旋态电催化技术作为一种新兴的CO2还原方法,具有很大的潜力。
自旋态电催化是一种利用自旋态电子的催化方法,可以将CO2转化为有用的化学品,如甲醇、乙烯等。
自旋态电子是电子自旋的一种状态,它具有独特的电子结构和电子能级分布,可以在一定程度上影响催化反应的速率和产物选择性。
在自旋态电催化CO2还原中,通常使用金属催化剂来促进反应的进行。
金属催化剂可以提供活性位点,吸附并激活CO2分子,使其发生还原反应。
而自旋态电子的引入可以调控催化剂的反应活性和选择性,从而实现高效的CO2还原。
自旋态电催化CO2还原的关键是选择合适的催化剂和调控自旋态电子。
目前已有许多金属催化剂被用于CO2还原反应,如铜、银、铜银合金等。
这些金属催化剂具有丰富的自旋态电子结构,可以通过调控其自旋态电子的分布来实现高效的CO2还原。
此
外,还可以通过合成纳米材料、调控催化剂表面结构等方法来调控自旋态电子,进一步提高催化反应的效率和选择性。
除了催化剂的选择和自旋态电子的调控,反应条件也对自旋态电催化CO2还原的效果有重要影响。
温度、压力、电流密度等参数的调控可以影响反应速率和产物选择性。
此外,还可以通过调控溶液pH值、添加助催化剂等方法来进一步提高反应效果。
- 1、下载文档前请自行甄别文档内容的完整性,平台不提供额外的编辑、内容补充、找答案等附加服务。
- 2、"仅部分预览"的文档,不可在线预览部分如存在完整性等问题,可反馈申请退款(可完整预览的文档不适用该条件!)。
- 3、如文档侵犯您的权益,请联系客服反馈,我们会尽快为您处理(人工客服工作时间:9:00-18:30)。
Supporting Information for:Structure-sensitive CO2 electroreduction to hydrocarbons on ultrathin five-fold twinned copper nanowiresYifan Li1,3, Fan Cui1,3, Michael B. Ross1, Dohyung Kim2,5, Yuchun Sun1, Peidong Yang1,2,3,4,51 Department of Chemistry, University of California, Berkeley, CA 94720, USA2 Department of Materials Science and Engineering, University of California, Berkeley, CA 94720, USA3 Chemical Sciences Division, Lawrence Berkeley National Laboratory, Berkeley, CA 94720, USA4 Materials Sciences Division, Lawrence Berkeley National Laboratory, Berkeley, CA 94720, USA5 Kavli Energy Nanosciences Institute, Berkeley, CA 94720, USA* To whom correspondence should be addressed. Email: p_yang@MethodsSynthesis of Cu NWs. In a typical synthesis, 85mg of CuCl2•2H2O, 0.5g oftris(trimethylsilyl)silane were dissolved in 5 g of oleylamine in inert environment. The mixture was then slowly heated up to 110°C and kept at this temperature until the color of the solution turned light yellow. Then, the temperature of the reactants was slowly increased to 160°C. The reaction was left to continue for 12 hours. The copper nanowires were collected through centrifugation and further washed with toluene twice to remove ligands and unreacted reagents. The nanowires were finally dispersed in toluene and stored in a dry nitrogen box before use. Preparation and charaterization of copper-graphene oxide (GO) core-shell nanowires. Sub-ten nanometer graphene oxide nanosheets were synthesized using a previously reported approach.1 To make copper-GO core-shell nanowires, a dilute solution of graphene oxide nanosheets in methanol was prepared with a concentration of 0.05 mg/ml. 2.5 ml of 2 mg/ml copper nanowire toluene solution was added in 20 ml of GO solution in a dropwise fashion, upon vigorous stirring. Then, the mixture was ultrasonicated for 3 min. The core-shell nanowires were collected by centrifugation at 10000 rpm for 10min. Then, the sample was further washed twice with isopropyl alcohol (IPA) to remove excess graphene oxide. The final products were dispersed in IPA and stored in a dry N2 box. To change the thickness of the GO shell, we reduced the concentration of GO solution and follow the same procedure described above. The GO was then electrochemically reduced in situ to reduced graphene oxide (rGO). Energy dispersive spectroscopy (EDS) mapping was carried out with an FEI TitanX 60-300. Preparation and characterization of CuNW/CB/GC electrodes. The washed CuNWs were first loaded onto carbon black (Ketjen) at loading ratio of 20% w/w and sonicated in hexanes for 30 minutes, creating a CuNW/CB stock solution.This solution was then spread on 1cm2 glassy carbon plates (Goodfellow) by micropipette and dried under nitrogen such that a total mass of 20 micrograms CuNW/CB was loaded per electrode.Each individual electrode was only used for one electrolysis. After electrolysis, electrodes were immediately imaged using SEM (JEOL FE-SEM). The CuNW/CB catalyst was then recovered by sonication in solvents such as hexanes or 2-propanol and imaged under TEM (Hitachi H-7650). Between electrolyses, glassy carbon plates were wiped clear before being immersed in 0.5 M nitric acid overnight and rinsed copiously with nanopure water (EMD Milli-Q, 18.2 MΩ, <5 ppb TOC).Electrodes for Raman spectroscopy were prepared by dropcasting bare and wrapped Cu NWs onto a piece of titanium foil to prevent any carbon signal arising from the substrate, at a geometric surface area coverage equivalent to that on glassy carbon. For the post-electrolysis sample, electrolysis was conducted in CO2-saturated 0.1 M KHCO3 at -1.25 V vs. RHE. The foil was then rinsed lightly with nanopure water before characterization. Raman spectroscopy was performed using a Horiba confocal Raman microscope with a 20x objective at 633 nm. Raman spectra were normalized by laser power (typically ~10 mW) and collection time (30-120s) and then corrected to a linear baseline.Electrocatalytic testing for CO2 reduction activity. Electrocatalytic tests were conducted witha potentiostat (Bio-Logic) in a custom-built three-electrode cell. For both catholyte and anolyte,0.05 M potassium carbonate solution was prepared by dissolving potassium carbonate (99.997% puratronic, Alfa Aesar) in nanopure water. Before electrolysis, the electrolyte was purged through in a sealed cell with ultrahigh purity CO2 (99.999%, Praxair) for at least twenty minutes to make a CO2-saturated 0.1 M KHCO3 solution. A composite platinum wire and gauze (Alfa Aesar) was used as a counter electrode in an anodic compartment separated from the rest of the cell using a Nafion cation exchange membrane to prevent product re-oxidation. All experiments were conducted using a Ag/AgCl (1 M KCl) reference electrode (CHI Instruments). For polycrystalline copper foil experiments, a 0.6 cm2 rectangle of high-purity Cu foil (Alfa Aesar, 99.999%) was rinsed in 85% phosphoric acid for 30 seconds, then copiously rinsed with nanopure water before use as working electrode.In a typical experiment, 10 mL of electrolyte was magnetically stirred in the cathodic compartment, resulting in a headspace of 41 mL. The electrode was held at constant bias using chronoamperometry for either a set time or a set amount of charge, after which a 1mL gas sample was taken by syringe from the headspace. The gas was injected into a gas chromatograph (SRI) equipped with a molecular sieve 13X column, HayeSep D porous polymer column, thermal conductivity detector, and flame ionization detector. Ultra high purity Ar (99.999%, Praxair) was used as carrier gas. The concentration of product gases was determined using calibration curves from standard gases (Matheson TriGas). Liquid sample was taken at the end of electrolysis and mixed with D2O at a 9:1 ratio for product analysis. Quantitative NMR was conducted on a Bruker AV-500 instrument with dimethyl sulfoxide as internal standard. Further details regarding calculations for gas and liquid products can be found in the appropriate sections below.Figure S1: Comparison of Cu NW catalysts directly dropcast on a glassy carbon electrode before (a) and after (b) 1 C electrolysis at -1.25 V vs. RHE. In addition to a visible loss of catalyst material after electrolysis, the direct loading of Cu NWs results in significant bundling of wires.Figure S2: Comparison of Cu NW catalysts with carbon black loading on a glassy carbon electrode before (a) and after (b) 1 C electrolysis at -1.25 V vs. RHE. Dispersion with carbon black is observed to improve both catalyst adhesion and wire separation.iR compensation and current-time behaviorThe solution resistance was determined and compensated for using the in-built ZIR function of the potentiostat, compensating for 85% of the resistance. At all potentials tested, the potential was manually corrected for the remaining 15% using Ohm's law:ΔE=i∗0.15∗Rwhere R represents the calculated solution resistance, i the measured current, and ΔE the additional uncompensated potential shift felt by the working electrode.Figure S3: Typical i-t curves for 1 C electrolyses at various applied potentials. From top to bottom, the potentials shown here are -0.85, -0.95, -1.0, -1.05, -1.10, -1.15, -1.20, -1.25, and -1.35 (V vs. RHE). Electrolyses were stopped after 1 C of passed charge; thus, runs at more negative potentials (higher current) were conducted in a shorter amount of time. The curves are truncated at 200 s for visual clarity when comparing with the much shorter electrolyses at higher bias.GC quantification of gas productsBecause all experiments were conducted under a batch setup, the calculation of Faradaic efficiencies and partial current densities for gas products could be calculated simply using the charge passed and a measured headspace according to the following relation:F.E.=(ppm)(PV)(nF)Q(RT)where the ppm represents the measured concentration (by volume) of the analyte in the 1 mL sample, V represents the total headspace volume (typically 41 mL), P and T set by standard conditions (1 atm and 273.15 K), n the mole ratio of electrons to product formation from CO2 (e.g. 8 for CH4), Q the total charge in C passed, and F the Faraday constant. The partial current density could then be calculated by multiplying the F.E. for a given product by the total current density, or equivalently through the following relation:j=(ppm)(PV)(nF)t(RT)where t represents the total time of electrolysis.NMR quantification of liquid productsLiquid products were analyzed using quantitative nuclear magnetic resonance (qNMR) with a Bruker Avance 500 MHz instrument in a 9:1 mixture of sample to deuterium oxide with DMSO as an internal standard. Excitation sculpting2 was used to suppress the water signal, and each experiment consisted of 8 loops of 8 scans each with a delay time of 42 seconds to account for the long relaxation time of formate.Because of the long delay time for each scan, the area ratio between an analyte peak and the DMSO peak should correspond well to the ratio of protons from the analyte and from DMSO, which in turn derives the concentration ratio of the analyte to the known concentration of DMSO. In addition, a calibration curve for formate, methanol, ethanol, and acetate was constructed by using the area ratio of known concentrations of analyte to the DMSO internal standard. Quantification of liquid products, especially formate, did not differ by more than 5% F.E. between these two methods. Finally, Faradaic efficiencies could be calculated as follows:F.E.=[A](V)(nF)Qwhere [A] represents the concentration of analyte as determined by quantitative NMR and V the total volume of solution (typically 10 mL).NMR samples from the anodic compartment were also taken, but no products, including formate or acetate, were observed. It is likely that Nafion, as a cation exchange membrane, restricts formate and acetate diffusion across compartments as may be observed for an anion exchange membrane.Figure S4: Full product comparison of bare vs. rGO wrapped Cu NWs after 5 C passed at -1.25 V vs. RHE. All products are shown here for 5 C of electrolysis, compared between the bare Cu NW and the rGO-wrapped Cu NW. Slight shifts in selectivity for H2 and formate are observed, while the overall selectivity for EtOH and acetate is too small in both samples to observe a change. Other liquid products such as MeOH and acetaldehyde were detected but could not be quantified due to their low concentration. The 10% selectivity change in the hydrocarbons is the most salient selectivity shift between the two samples. Total F.E.s exceeded 95% at this potential, confirming the detection of all products from CO2RR.Figure S5: Large-area TEM micrographs of bare copper nanowires (a) before electrolysis and after (b) 3C, (c) 5C and (d) 60 C of electrolysis. Scale bar is 100 nm. Inset picture of (d) shows a larger-magnification TEM micrograph of a single copper nanowire after 60 C of electrolysis. The scale bar is 20 nm. During electrolysis, the bare Cu NWs are observed to dissolve, bundle, fracture, and form small Cu NPs.0 C (a) (b) (c) (d) 3 C5 C 60 CFigure S6: Large-area TEM micrographs of rGO-wrapped copper nanowires (a) before electrolysis and after (b) 3C, (c) 5C and (d) 60 C of electrolysis. Scale bar is 100 nm. Inset picture of (d) shows a larger-magnification TEM micrograph of a single rGO-wrapped copper nanowire after 60 C of electrolysis. The scale bar is 20 nm. The morphology of the copper nanowires are well maintained even after 60 C of electrolysis, for which the catalytic product distribution could not be reliably measured under a batch setup due to CO 2 depletion.0 C 5 C(b) (c) (d) (a) (b) 3 C5 C 60 CFigure S7: Current-time behavior of rGO-wrapped Cu NWs with varying degrees of wrapping, measured at -1.25 V vs. RHE for 5 C of electrolysis. The curves are truncated at 600 s for visual clarity. As with Fig. S3, electrolyses tended to be more stable at lower currents due to bubble formation, resulting in larger, difficult-to-control fluctuations of exposed surface area.Figure S8: Decreasing total steady-state current density with increased wrapping. The current density was observed to decrease with an increase of the rGO:Cu ratio used during wrapping. This observation is consistent with a blockage of active sites due to the GO, further confirming the active presence of GO on the exterior of the wire.Figure S9: Long-term stability of electrochemical selectivity for the rGO-CuNW catalyst. Stability measurements were conducted under a flow-cell configuration in which gas samples were taken roughly every 20 minutes. Over the course of 3 hours, the activity for methane steadily decreases, while hydrogen evolution increases. However, the shift toward ethylene selectivity consistent with structural degradation does not occur, consistent with the morphological preservation observed in Figure S6. Previous studies have identified consistent, rapid deactivation in catalysts that produce high levels of methane, which has been ascribed to poison species derived from key intermediates along the pathway to methane.3 The steady deactivation of the rGO-CuNW catalyst over extended electroreduction is expected to occur for a similar reason, unlike the structurally-induced selectivity shifts highlighted in the main text.References1. Sun, Y.; Wang, S.; Li, C.; Luo, P.; Tao, L.; Wei, Y.; Shi, G. Phys. Chem. Chem.Phys.2013, 15, 9907– 9913.2. Hwang , T-L.; Shaka, A.J. Journal of Magnetic Resonance A. 1995, 112, 275-279.3. Kas, R.; Kortlever, R.; Yılmaz, H.; Koper, M. T. M.; Mul, G. Chem. Electro. Chem. 2015, 2, 354–358.。