锡膏印刷机的机架对整机精度的影响研究
提高锡膏印刷生产效率的工艺改进
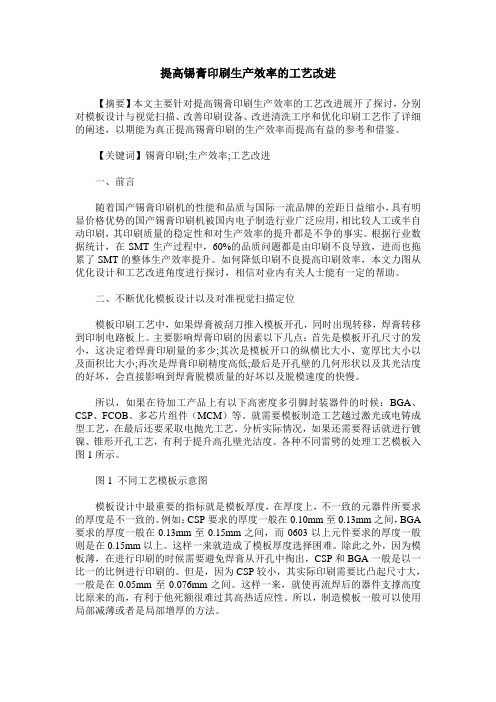
提高锡膏印刷生产效率的工艺改进【摘要】本文主要针对提高锡膏印刷生产效率的工艺改进展开了探讨,分别对模板设计与视觉扫描、改善印刷设备、改进清洗工序和优化印刷工艺作了详细的阐述,以期能为真正提高锡膏印刷的生产效率而提高有益的参考和借鉴。
【关键词】锡膏印刷;生产效率;工艺改进一、前言随着国产锡膏印刷机的性能和品质与国际一流品牌的差距日益缩小,具有明显价格优势的国产锡膏印刷机被国内电子制造行业广泛应用,相比较人工或半自动印刷,其印刷质量的稳定性和对生产效率的提升都是不争的事实。
根据行业数据统计,在SMT生产过程中,60%的品质问题都是由印刷不良导致,进而也拖累了SMT的整体生产效率提升。
如何降低印刷不良提高印刷效率,本文力图从优化设计和工艺改进角度进行探讨,相信对业内有关人士能有一定的帮助。
二、不断优化模板设计以及对准视觉扫描定位模板印刷工艺中,如果焊膏被刮刀推入模板开孔,同时出现转移,焊膏转移到印制电路板上。
主要影响焊膏印刷的因素以下几点:首先是模板开孔尺寸的发小,这决定着焊膏印刷量的多少;其次是模板开口的纵横比大小、宽厚比大小以及面积比大小;再次是焊膏印刷精度高低;最后是开孔壁的几何形状以及其光洁度的好坏,会直接影响到焊膏脱模质量的好坏以及脱模速度的快慢。
所以,如果在待加工产品上有以下高密度多引脚封装器件的时候:BGA、CSP、FCOB、多芯片组件(MCM)等。
就需要模板制造工艺越过激光或电铸成型工艺,在最后还要采取电抛光工艺。
分析实际情况,如果还需要得话就进行镀镍、锥形开孔工艺,有利于提升高孔壁光洁度。
各种不同雷劈的处理工艺模板入图1所示。
图1 不同工艺模板示意图模板设计中最重要的指标就是模板厚度,在厚度上,不一致的元器件所要求的厚度是不一致的。
例如:CSP要求的厚度一般在0.10mm至0.13mm之间,BGA 要求的厚度一般在0.13mm至0.15mm之间,而0603以上元件要求的厚度一般则是在0.15mm以上。
印刷机对品质的影响

6
3. 钢网擦拭速度即设备自动擦拭。
1). 擦拭过快:钢网擦不干净,出现短路、少锡等品质 异常。 2). 擦拭过慢:不会造成产品异常,只会影响产量。 4. 钢网厚度及开孔方式的影响。
7
二. 其他参数
1. Print Gap。 1). Print Gap是指印刷时PCB上表面和钢网下表面之 间的距离,一般设置为-0.5~0mm。 2). 距离偏大(大于0):刮不干净﹑印刷偏厚﹑拉尖和 连锡现象。 3). 距离偏小:通常在有刮不干净或者锡少现象时才 设置小于0,距离过小时会引起连锡的现象(相当于刮 刀压力偏大)。
1). MPM机可以选择其中任何两种或三种,其擦拭顺 序按照WET—DRY—VAC进行。DEK机可以设置任何 擦拭方式及擦拭的顺序。 2). 擦拭模式如果设置不恰当会出现短路、少锡、锡 膏偏厚等品质异常。
5
2. 钢网擦拭频率。 实际中我們根据产品上含的元件来选择设置擦拭的频 率。一般含有BGA、CSP的产品擦拭要频繁一些。 1). 擦拭频率偏高对产品的品质不会有不良影响﹐还能 减少不良现象的机率,但会延长印刷时间。 2). 擦拭频率偏低会因为擦拭不干净钢网而出现品质异 常,如:连锡﹑偏位﹑少锡等不良。
9
3. 脱膜速度。 1). 定义:用来表征刷好的PCB板由顶Pin或支撑治具 吸附着下降的速度快慢。 2). 脱膜速度过快:该情况与脱膜距离过小的后果是相 似的,一般会出现少锡、拉尖等现象。 3). 脱膜速度过慢:该情况与脱膜距离过大的后果是相 似的,通常易出现锡膏坍塌、短路等现象,另外还会 增加印刷工时。
8
2. 脱膜距离。 1). 脱膜定义是指PCB板印刷完成后,由顶Pin或支撑 治具吸附着板子轻微的高频振动并向下缓慢将板子与 钢网分离。 2). 脱膜距离就是在该动作内PCB板一直持续轻微的高 频振动,缓慢下降的距离。 3). 脱膜距离偏大:在脱膜的过程中,动作持续太久会 使印刷得整齐的锡膏向下坍塌成一片,若PCB上Pin脚 很密的话就容易出现短路,另外还会增加印刷工时。 4). 脱膜距离偏小:若脱膜距离过小,即板子和钢网还 没有充分分开,就被顶 Pin或支撑治具强行吸下,易造 成开孔粘锡,出现少锡或拉尖现象。
提升锡膏印刷厚度稳定性CPK
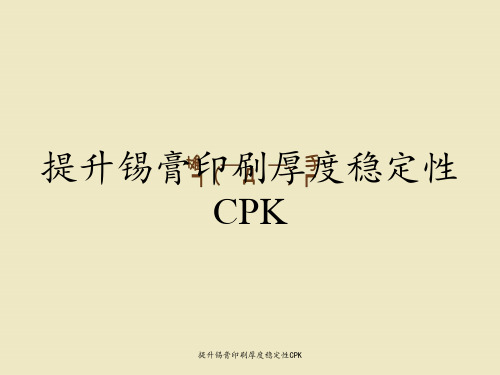
目标设定 ----确定改善的目标
要因分析 ----制定改善的方案
改善行动 ----实施改善方案
效果确认 ----确认改善的效果
标准化 ----改善过程总结
实际
1117
1118
计划小组活动
实际小组活动
1119
1120
1121
1122
五、现状调查 根据锡膏测厚仪自带SPC所收集数据计算出CPK值:
厚度值波动
印刷
参数 设置
有标准
九、对策实施
实施要因(四)顶针支撑设置不当
改善前
顶针的布置要拿实际的PCB板来做调设;
缺点:调设时间长;容易顶到元件;每次顶针的布置难确保一 样,导致过程不稳定。
九、对策实施
实施要因(四)顶针支撑设置不当
改善后
使用模板来布置顶针; 优点:调设时间短;不会顶到元件;确保每次顶针布置的一致性.
致
始位置高度达到平衡前后刮刀压力一致的目的。 张三发 11
2 测试程序制作不当
培训测试员如何正确的制作测试程序。
李春茂
2011-0520
3
印刷机参数设置不 通过反复调整、测试,实验出合适的参数,并制作 苏维 2011-05-
当
成作业指导书。
李春茂 16
4 顶针布置不均衡
制作顶针模板
吴海滨 2011-05陈庆军 18
九、对策实施
实施要因(二)测试程序制作不当
锡膏的特性

锡膏品质特性参数
锡膏品质特性参数
锡膏品质特锡膏为何要低温储
答:焊锡膏内部有活性物质,这些活性物质能够起到去除氧化物的作用。活性物质释放
活性剂的能力与温度是有关系的,温度越低,活性的释放就越微弱。所以为了保证锡膏 的品质,不至于在没有使用的时候内部就已经激烈反应,锡膏就应该低温下面保存。一 般的储存温度为1-10度。最好5-10度。温度太低对品质也是有影响的
锡膏品质特性参数
锡膏品质特性参数
锡膏印刷质量的主要因素
1.首先是钢网质量:钢网厚度与开口尺寸确定了锡膏的印刷量。锡膏量过多会 产生桥接,锡膏量过少会产生锡膏不足或虚焊,钢网开口形状及开孔壁是否光滑 也会影响脱模质量。 2.其次是锡膏质量:锡膏的粘度、印刷性(滚动性、转移性)、常温下的使用 寿命等都会影响质量。 3.印刷工艺参数:刮刀速度、压力、刮刀与网板的角度以及锡膏的粘度之间存 在的一定制约关系,因此只有正确控制这些参数,才能保证锡膏的印刷质量。 4.设备精度方面:在印刷高密度细间距产品时,印刷机的印刷精度和重复印刷 精度也会起一定影响。 5.环境温度、湿度、以及环境卫生:环境温度过高会降低锡膏的粘度,湿度过 大时锡膏会吸收空气中的水分,湿度过小时会加速锡膏中溶剂的挥发,环境中 灰尘混入锡膏中会使焊点产生针孔等缺陷。 6.基板支撑位置的分布:机板支撑绝对与印刷结果有关,利用两支刮刀来回刮 印如大部分锡膏被刮走,残余未被刮走的部分就是支撑不良,容易出现连锡。
• 为何锡膏使用前要回温
答:冷箱中取出锡膏时,其温度较室温低很多,若未经“回温”,而开启瓶盖,则容易
将空气中的水汽凝结,并沾附于锡浆上,在过回焊炉时(温度超过 200℃),水份因受 强热而迅速汽化,造成“爆锡”现象,产生锡珠,甚至损坏元器件。 回温方式:不开启瓶盖的前提下,放置于室温中自然解冻, 回温时间:4 小时以上
SMT用焊锡膏使用过程中常见问题之原因分析报告
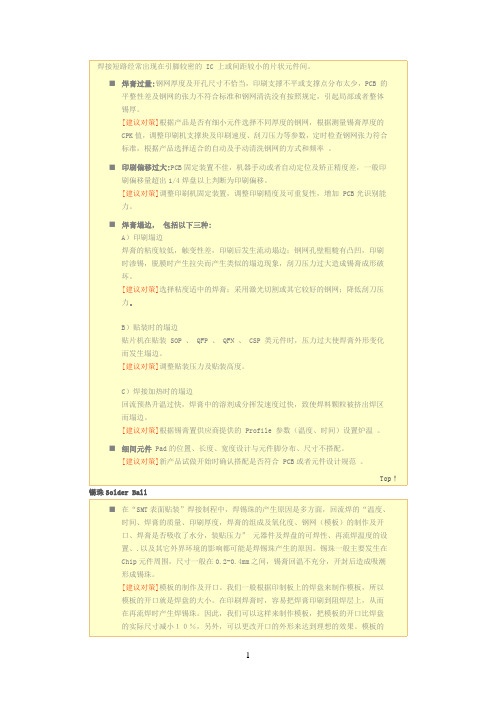
焊接短路经常出现在引脚较密的 IC 上或间距较小的片状元件间。
■焊膏过量:钢网厚度及开孔尺寸不恰当,印刷支撑不平或支撑点分布太少,PCB 的平整性差及钢网的张力不符合标准和钢网清洗没有按照规定,引起局部或者整体锡厚。
[建议对策]根据产品是否有细小元件选择不同厚度的钢网,根据测量锡膏厚度的CPK值,调整印刷机支撑块及印刷速度、刮刀压力等参数,定时检查钢网张力符合标准,根据产品选择适合的自动及手动清洗钢网的方式和频率。
■印刷偏移过大:PCB固定装置不佳,机器手动或者自动定位及矫正精度差,一般印刷偏移量超出1/4焊盘以上判断为印刷偏移。
[建议对策]调整印刷机固定装置,调整印刷精度及可重复性,增加 PCB光识别能力。
■焊膏塌边,包括以下三种:A)印刷塌边焊膏的粘度较低,触变性差,印刷后发生流动塌边;钢网孔壁粗糙有凸凹,印刷时渗锡,脱膜时产生拉尖而产生类似的塌边现象,刮刀压力过大造成锡膏成形破坏。
[建议对策]选择粘度适中的焊膏;采用激光切割或其它较好的钢网;降低刮刀压力。
B)贴装时的塌边贴片机在贴装 SOP 、 QFP 、 QFN 、 CSP 类元件时,压力过大使焊膏外形变化而发生塌边。
[建议对策]调整贴装压力及贴装高度。
C)焊接加热时的塌边回流预热升温过快,焊膏中的溶剂成分挥发速度过快,致使焊料颗粒被挤出焊区而塌边。
[建议对策]根据锡膏置供应商提供的 Profile 参数(温度、时间)设置炉温。
■细间元件 Pad的位置、长度、宽度设计与元件脚分布、尺寸不搭配。
[建议对策]新产品试做开始时确认搭配是否符合 PCB或者元件设计规范。
Top↑锡珠Solder Ball■在“SMT表面贴装”焊接制程中,焊锡珠的产生原因是多方面,回流焊的“温度、时间、焊膏的质量、印刷厚度,焊膏的组成及氧化度、钢网(模板)的制作及开口、焊膏是否吸收了水分,装贴压力” 元器件及焊盘的可焊性、再流焊温度的设置、.以及其它外界环境的影响都可能是焊锡珠产生的原因。
SMT锡膏印刷制造过程质量影响因素分析

【 关t t i  ̄ ] S M T锡 膏印刷 ; 输入影 响 ; 输 出质量评估
在 电动 汽车 使 用 的各种 电子零 部 件制 造 过程 中 . S M T ( S u f a c e M o u n t T e c h n o l o g y ) 技术被大量使用。 其生产过程优点在于降低生产成 本的 同时 . 制造出高品质 的电子产 品 但 由于极端复杂的 S M T 生产环 境 中, 生产 过程 充满着许多不确定 因素 , 影响着 电子 产品的质量 。在 S M T产品生产 流程 中 . 锡膏印刷 品质是影响最终的焊接质量 的最为显 著的工序。经 由文献整理发 现, 由于锡膏 印刷过程不 当说衍生 的焊接 不 良约 占总过程不 良品的 5 2 — 7 4 % 因此本文选择锡膏印刷质量作 为 分析 的对象 , 已期降低 目前 S M T 生产过程 中的不 良品比率 锡膏印刷工序操作一般可分解 为三个 阶段动作 。阶段一 : 锡膏经 由刮刀挤压而透过钢 网表面 ; 阶段 二 : 锡膏 附着于 印刷 电路板焊盘上 ; 阶段 三 : 钢 网脱离而锡膏停 留在焊盘上 在 阶段一刮刀 以某一角度、 速 度与压力使 锡膏通过钢 网表 面 。 于第二阶段 . 刮刀以高压将锡 膏挤 压 穿透钢模 开孑 L , 紧接着在第三 阶段 . 钢 网脱离并 使锡膏停 留在 印刷 电 路板焊 盘上 。 从 以上生产分解过程 看 . 锡膏印刷主要 通过设备操作完成 . 其 过 程较 复杂且个 生产步骤为非线性。 再加上锡 膏印刷生产过程影响因素 多, 如仅仅依赖设备本身精确度 , 很难确保生产过程零故障率。 锡膏印 刷过 程主要 的影 响因素有 : 1 ) 锡膏特性 : 黏度 、 颗粒 大小 、 金属含量 、 黏性 、 助焊剂含量 、 添 加 物等 : 2 ) 钢 网特 性: 钢 网制作方式 、 钢 网材质及厚度 、 钢 网开孔 面积及形
提高印刷设备框架结构精度

印刷机的整体结构是以两块墙板为支撑基础件,在两块墙板之间安装大量滚、轴、辊等零件,使连续行进的承印物从排列有序的轴、辊、滚筒间等功能机构穿过。
在承印物行进中,进行诸如张力控制、送纸、调偏、给水、给墨、印刷(套印)、裁切、输纸、纸张交接、打号码、烘干、冷却、上光及各种保证印刷过程自动完成的机构。
其中,一块墙板的外侧,安装有各种传动零件,以带动墙板内侧的滚、轴、辊作旋转、轴向或间歇地运动,从而达到各种印刷功能的实现。
另一块墙板的外侧则安装了各种操纵机构,以控制印刷的质量并保证印刷顺利进行。
因此,墙板在保证加工质量的前提下,它的装配质量的优劣,将直接影响整机质量和精度保持性。
作为印刷机的主要基础件,它还影响着完成印刷全过程各种功能零件的质量和寿命。
重视基础零部件的研究,是提高印刷机内在质量的重要手段。
本文准备从现有的装配定位工艺方法入手,通过定位产生误差的计算,分析主要基础零件产生定位误差的原因,从而提出几种供选择的新装配定位方法,以提高装配定位精度,进一步提高印刷的质量。
同时,也为印刷企业对印刷机大、中修提供的装配方法和手段。
一、传统工艺方法产生同轴度误差的计算传统的基础件同轴度精度的定位方法多采用芯轴定位方式。
这种方法从理论上讲可以做到设计基准、装配基准、定位基准三统一,基准重合可以提高装配精度。
但是,由于墙板定位孔存在形状、位置误差和尺寸误差,芯轴的定位部分也给定的公差值,因此两块墙板使用芯轴定位时,间隙的存在即使芯轴转动灵活也会产生同轴度误差。
显而易见,随着两块墙板距离的拉大,同轴度误差值和墙板间距成正比和配合间隙大小成正比。
大跨度的印刷机墙板由于间隙的存在,产生的同轴度误差不容忽视。
虽然,滚、轴、辊装配以后,可以从公共轴线来确定滚、轴、辊间的相对位置,似乎影响不大,但是,众多的传动、操纵和自动控制零件则会处于恶劣的工作条件,更重要的是精度保持性差。
为建立间隙,墙板间距和同轴度误差产生的关系式,先提出以下约束条件:1.墙板下平面是支承基准,也是加工时的导向基准,因此可以认为两块墙板上的所有同位孔相对支承基准高度尺寸一致,装配时,两块墙板的水平位置,由定位芯轴定位确定;2.可以从直观的角度想象出,产生最大同轴度误差的位置是:一个孔的两端与定位芯轴定位对角线接触,另一个孔内侧定位芯轴接触,从理论上讲,此时转动芯轴也应该灵活;或立式加工中工作台上合镗加工(也可以分镗加工),所以认为两块墙板孔轴线同向,但对墙板大平面的角度不同,这反映了拉轴(拉梁)零件的一致性精度;3.一般说来两块墙板对应孔径相同,为了使推导的关系式有普遍意义,特设两对应孔为不等径孔。
提升锡膏印刷厚度的稳定性(CPK)
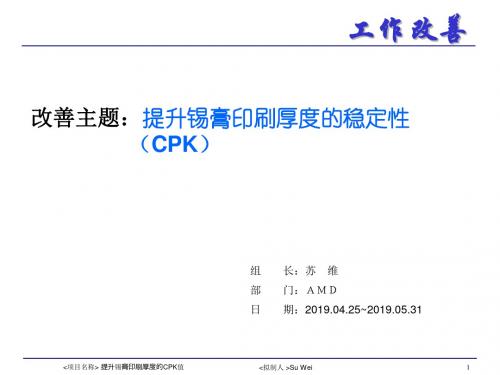
现有0.13厚度的钢网可以满足此控制范围要求。
3. 全自动印刷机都为新购设备,运行稳定。
<项目名称> 提升锡膏印刷厚度的CPK值
<拟制人 >Su Wei
9
七、原因分析及要因确认
机
测试不稳定 没有校正 测厚仪
软件问题 硬件故障
变形
人
刮刀 磨损
压力参数设置是一致的,但实际后刮刀印刷之后钢网表面 比前刮刀的要干净,说明前后刮刀实际的压力不一致。
刘朝阳 张三发
是主因
4
测试程序制作不当
测试程序基准点制作不正确和基准平面的选择不正确以及 测试点的选择都影响厚度测试稳定。
李春茂
是主因
5 印刷机参数设置不当印没刷有的工速艺度标,准分文离件速支度持,影印响刷过压程力的设稳置定不。规范,随意修改, 苏维
<项目名称> 提升锡膏印刷厚度的CPK值
<拟制人 >Su Wei
13
九、对策实施
实施要因(一)前后刮刀压力不一致
工作改善
前刮刀的实际压力要比后刮刀的小,更改机器参数,使前刮刀的初始高度 下降0.8mm,达到增加前刮刀压力的目的。
CPK= 0.8974
<项目名称> 提升锡膏印刷厚度的CPK值
<拟制人 >Su Wei
6
五、现状调查
工作改善
产品型号:MC8210K18-00PST3 使用钢网厚度:0.13mm
厚度值波动 0.104~0.175
CPK= 0.7030
<项目名称> 提升锡膏印刷厚度的CPK值
<拟制人 >Su Wei