数控车削加工基础
数控车床操作基础
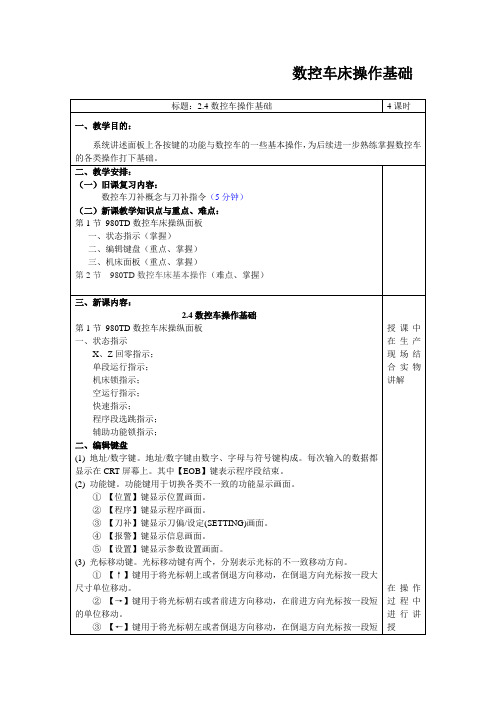
数控车床操作基础【X1】、【X10】、【X100】与【X1000】四个按钮都属于增量倍率修调按钮。
当系统工作在【步进】按钮按下时,用于调整每次步进的步进距离,即增量值。
每一步能够是最小输入增量单位的1倍、10倍、100倍与1000倍。
【冷却】按钮用于手动开/关切削液泵。
【手动换刀】按钮按下时,在手动方式下实现转塔转位换刀。
【+X】、【-X】、【+Z】与【-Z】四个按钮均属于轴向移动按钮,利用它们能够进行手动点动进给与手动步进进给,每次只能操纵一个坐标轴的运动。
按下其中之一,就能够实现刀架向坐标轴某一方向运动。
【快移】按钮与轴向移动按钮同时按下时,刀架按照NC参数设定的快速移动速度快速运动。
【主轴正转】、【主轴反转】与【主轴停】三个按钮可操纵主轴正转、反转与停转。
第二节:980TD数控车床基本操作(1 )开机、关机操作:a. 在确认急停开关按下的情况下,打开电源开关—打开机床开关—按下绿色开关(操纵系统上电)—向右旋转急停开关—机床启动。
b. 在任何情况下按下急停开关—按下红色开关(操纵系统下电)—关机床开关—关电源开关—完成。
(2)手动返回参考点操作:a. 先检查一下各轴是否在参考点的内侧,如不在,则应手动回到参考点的内侧,以避免回参考点时产生超程b. 按功能键区的“回零”功能按键c. 分别按+X 、+Z 轴移动方向按键,使各轴返回参考点,回参考点后,相应的指示灯将点亮。
(3)点动、步进操作a. 按功能键区的“手动”或者“增量”功能按键b.“增量”时按倍率选择键0.1 、0.01 、0.001 选择增量进给的倍率大小c.按机床操作面板上的“ +X ”或者“ +Z ”键,则刀具向X 或者Z 轴的正方向移动,按机床操作面板上的“-X ”或者“-Z ”键,则刀具向X 或者Z 轴的负方向移动;d.如欲使某坐标轴快速移动,只要在按住某轴的“+”或者“-”键的同时,按住“快移”键即可。
(4)手轮进给a. 按功能键区的“手轮” 功能按键;b. 按倍率选择键0.1 、0.01 、0.001 选择增量进给的倍率大小c.按中的“ X ”或者“ Z ”键,选择相应的轴。
数控车床编程基础
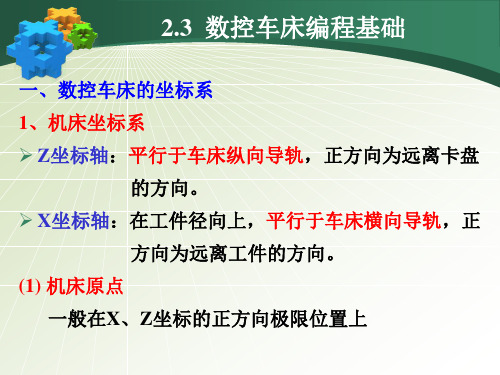
毛坯直径Φ45mm,长120mm,要求车出一段长为
80mm,直径为Φ40mm的轴
O0002;
N10T0101M03S800;
N20G00X40.0Z2.0;
N30G01Z-80.0F0.2; N40X46.0; N50G00X100.0Z50.0; N60T0100;
B
N30
N40 C
N50
A D
(1) 用G96方式的指令 ➢ G96是接通恒线速度控制的指令,用S指定的数值表
示切削速度,单位:m/min。 ➢ 车削过程中,若主轴转速不变,随着被加工工件直
径减小,切削速度会下降,最佳车削状态被破坏。 为保证在同一材料上加工时选取的最佳线切削速度 保持不变,可以用G96指令保持恒线速度切削。 ➢ 在恒线速度控制中,数控系统根据刀尖所在处的X 坐标值,作为工件的直径来计算主轴转速,在使用 G96指令前必须正确地设定工件坐标系。
④ 倒1/4圆角 编程格式:G01 Z(W)_ R(±r) ;圆弧倒角如图 或G01 X(U)_ R(±r);圆弧倒角如图
Z轴向X轴
X轴向Z轴
加工如图所示零件的倒棱程序
N20 G00 X10.0 Z2.0;
N50
N40
N30 G01 Z-11.0 R5.0 F0.2; D C
N40 X38.0 C-4.0; N50 Z-21.0;
② 自动返回参考点指令——G28和G30 ➢ 第一参考点返回指令
G28 X(U) ;X向回参考点 G28 Z(W) ;Z向回参考点 G28 X(U) Z(W) ;刀架回参考点 ➢ G30 P2 X(U) Z(W) ;第二参考点返回 G30 P3 X(U) Z(W) ;第三参考点返回 G30 P4 X(U) Z(W) ;第四参考点返回
车削加工基本内容

标题:车削加工那些事儿- 基础知识篇嘿,伙计们,今天咱们来侃侃这个车削加工的基本内容。
别看我这儿说得轻松,其实车削这活儿可讲究了,得有那么点手艺人才干得好。
不过别怕,咱们一点点来,不着急。
首先啊,咱得知道车削是啥。
简单来说,就是用个旋转的刀具去切一个转动的工件,就像你在家切菜似的,只不过咱们的工具和工件都是金属的,而且精度高得多。
咱们先说说车削加工的分类。
基本上,车削可以分为两大类:粗车和精车。
粗车嘛,就是为了快速去掉多余的材料,不太在乎表面光不光滑;精车呢,就是为了把工件加工到精确的尺寸和形状,表面得光滑得像婴儿的屁股一样。
再说说车削加工的设备。
最主要的设备就是车床,还有刀具、夹具这些。
车床有很多种,什么数控车床、普通车床等等,根据不同的需要来选。
刀具也得选对,不同的材料、不同的加工要求,用的刀都不一样。
夹具呢,就是用来固定工件的,保证它不会乱动。
接下来咱们看看车削加工的流程。
首先是准备工作,包括选材料、选刀具、装夹具这些。
然后是车削操作,这个时候要注意控制好切削速度、进给量这些参数。
最后是清理和检查,把工件表面的切屑清理干净,检查加工质量。
在车削过程中,还得注意几点:一是刀具得锋利,不然切不动;二是冷却液得够用,不然刀具和工件摩擦生热,会影响精度;三是测量要准确,不然加工出来的东西可能不合格。
当然啦,车削加工也不是万能的,有些材料太硬或者太粘,可能就不适合车削。
所以咱们得根据实际情况来选择合适的加工方法。
对了,还有一点很重要,就是安全。
车削加工的时候,一定要遵守安全规程,眼睛不能离工件太近,穿戴好防护装备,避免发生事故。
最后咱们聊聊车削加工的技巧。
这个就需要点经验了。
比如,你要是想提高加工效率,就得合理选择切削参数;要是想提高加工精度,就得仔细调整机床和夹具。
这些都是需要时间积累的。
好了,说了这么多,咱们这个车削加工基本内容就差不多了。
当然啦,这里面还有很多细节和技术要点,咱们以后可以慢慢聊。
数控车教案
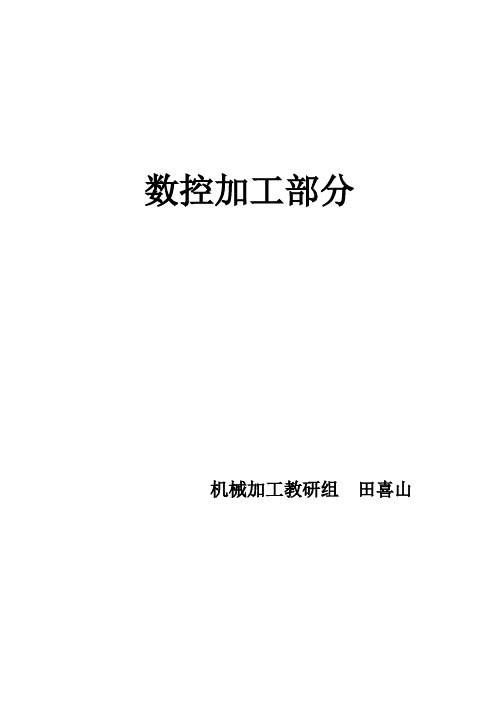
数控加工部分
机械加工教研组田喜山
课时计划
课时计划
课时计划
删除键。
删除光标所在的数据
插入键。
把输入域之中的数据插入到当前光标之后的消除输入域内的数据。
向上翻页。
偏值参数输入页面。
图形参数设置页面。
信息页面,如“报警”系统参数页面。
系统帮助页面。
课时计划
课时计划
课时计划
课时计划
.确定装夹方案
因前道粗加工工序已经将零件总长确定,本工序装夹关键是
课时计划
课时计划
图1-10 机夹可转位车刀
)涂层刀具涂层硬质合金刀片的耐用度至少可提高
倍,而涂层高速钢刀具的耐用度则
倍。
)非金属材料刀具用作刀具的非金属材料主要有陶瓷、金刚石及立方氮化硼等。
工件的装夹
课时计划
课时计划
课时计划
课时计划。
数控切削原理与刀具基础

在基面上 垂直于进给运 动方向测量的 切削层最大尺 寸,外圆车削: ap=(dw-dm)/2
vc、f、ap 构成了车削的切削用量三要素
车削速度计算示例
• 将一直径为50mm的轴切削至45mm, • 已知车床转速为600 r/min, • 问切削速度 vc=?
车削速度计算示例
• Vc = (πx
• =
通过主切削刃上的某一点,并 同时垂直于基面和切削平面的 平面
2.刀具角度参考系及其坐标平面
2.刀具角度参考系及其坐标平面
(1)正交平面Po中测量的刀具角度
1)前角γo前刀面与基面之间的夹角。 2) 后角αo后刀面与切削平面之间的夹角。 3)楔角βo 前刀面与后刀面之间的夹角,它是个派生 角。它与前角、后角有如下的关系:βo=90°-(γo +αo); βo也是判断标注是否正确的验证式之一。
数 控 切 削 原 理 与 刀 具 基 础
1.1 如何选择切削用量?
本节课主要研究:切削运动与切削要素,切削刀具及其刀具 几何参数,切削过程的基本规律,并运用规律控制切削过程、 改善切削性能、合理选用切削液。
切削过程中:切削力、切削变形、切削热与切削温度、刀具磨损等 现象及其规律,有利于控制和改善金属的切削过程。
W18Cr4V YT类
铸铁 HBS<200
精加工 切断(宽度<5mm)
YG类
训练题:P12
1.2 如何选用刀具几何角度
1.2.1车刀几何角度
各种刀具都是由切削部分(刀头)和被夹持部分(刀 体或刀柄)两部分组成,二者既可以是一体的,也可 以是由不同材料连接起来。
1.刀具切削部分的组成
刀杆:起夹持作用 刀头:(三面) 前刀面:刀具上切屑流过的表面 主后刀面:刀具上与过渡表面相 对的表面 副后刀面:刀具上与已加工表面 相对的表面 (两刃) 主切削刃:刀具上前刀面与主后 刀面的交线 副切削刃:刀具上前刀面与副后 刀面的交线 (一尖) 主切削刃与副切削刃的交点 ,通 常磨成圆角(修圆刀尖)或短平刃 (倒角刀尖) (修光刃):P14,图1-7。
CAXA数控车培训教程(2024)
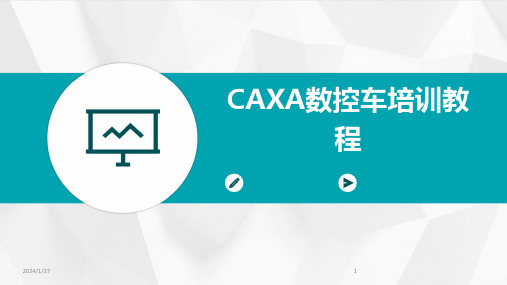
刀具路径优化
通过调整切削参数、刀具 轨迹等方式,优化刀具路 径,提高加工效率和表面 质量。
碰撞检测
检查刀具路径与夹具、机 床等是否存在碰撞,确保 加工安全。
16
仿真结果查看与分析
仿真结果查看
以图形化方式展示仿真加 工过程,包括切削力、切 削热、切屑形成等。
2024/1/27
仿真结果分析
数控系统故障
如数控系统硬件故障 、软件故障等,可通 过重启系统、更换硬 件或重新安装软件等 方式进行排除。
2024/1/27
26
维护保养及注意事项
定期清理机床内外的灰尘 和杂物,保持机床清洁。
定期检查各部件的磨损情 况,及时更换磨损严重的 部件。
2024/1/27
定期润滑各传动部件和导 轨,确保机床运转顺畅。
02
分析复杂零件的加工难点,提出高精度数控车削加工的解决方
案。
数控车削加工与其他制造技术的融合
03
研究数控车削加工与增材制造、减材制造等技术的融合应用,
拓展制造领域的发展空间。
30
相关资源推荐及学习建议
学习资源推荐
推荐一些优质的数控车削加工学习资源,如专业书籍、在线课程、 实践项目等。
学习方法建议
刀具补偿指令
讲解刀具长度补偿和刀具半径补偿 的原理及应用。
20
程序结构设计与优化
程序结构设计
讲解程序的结构设计原则,如模块化 、可读性、可维护性等。
高级编程技巧
探讨高级编程技巧,如宏程序、子程 序、固定循环等。
程序优化方法
介绍程序优化的常用方法,如减少空 行程、合理选择切削参数、优化刀具 路径等。
分享一些有效的学习方法,如理论学习与实践操作相结合、参加专 业竞赛和项目实践等,帮助学员提高学习效果和实际应用能力。
数控加工工艺基础ppt
模具类零件的数控加工工艺
• 模具类零件的数控加工工艺主要涉及铣削、磨削、钻孔和电火花加工等加工方 法。在铣削和磨削过程中,需要选择合适的刀具、切削参数和冷却方式,以确 保加工精度和表面质量。同时,还需要对工件进行装夹和定位,以减小加工误 差。
• 板类零件的数控加工工艺流程一般包括粗铣、半精铣、精铣等工序。在粗铣阶 段,主要去除余量,留有余量供后续加工;在半精铣阶段,对工件进行半精加 工,为精铣做准备;在精铣阶段,对工件进行精细加工,确保精度和表面质量 。
• 在钻孔和攻丝加工中,需要选择合适的钻头、丝锥和切削参数,以确保钻孔和 攻丝的质量和效率。同时,还需要注意工件的装夹和定位精度,以及切削液的 使用。
• 轴类零件的数控加工工艺还需要注意工件的装夹和定位精度,以及切削液的使 用。合理的装夹方式和切削液能够有效减小加工误差和提高表面质量。
板类零件的数控加工工艺
• 板类零件的数控加工工艺主要涉及铣削、钻孔和攻丝等加工方法。在铣削过程 中,需要选择合适的刀具、切削参数和冷却方式,以确保加工精度和表面质量 。同时,还需要对工件进行装夹和定位,以减小加工误差。
总结词
装夹方案的确定是数控加工工艺设计中的重要环节,合理的装夹方案能够有效提 高加工效率和质量。
详细描述
在确定装夹方案时,需要考虑零件的结构特点、装夹方式、夹具设计等因素。同 时,还需要根据现有设备和工艺条件进行选择和优化,确保装夹方案的可行性和 经济性。
刀具进给路线的确定
总结词
刀具进给路线的确定是数控加工工艺设计中的重要环节,合理的刀具进给路线能够有效提高加工效率和质量。
数控车削编程基础知识全解
程序段格式
程序字 主程序和子程序
程序的组成
一个完整的程序,一般由程序号、程序内容和程序结束三部分组成。 例如: 程序号 O0100 N1 N2 G0 G17 Z100.000 T1
N3 G0 Z2.000 S2000
程序内容 N4 N5 … N18 程序结束 N19 G0 M30 Z100.00 G1 G42 Z1-10.000 G46 F200 M70 M61
X、Y、Z U、V、W A、B、C I、J、K
意义
坐标轴地址指令 附加轴地址指令 附加回转轴地址指令 圆弧起点相对于圆弧中心的坐标指令
表3-2
G代码 A G00 B G00 C G00 组
FANUC 0-TD系统常用G指令表
功能 A G代码 B G70 C G72 精加工工循环 组 功能
快速定位 01
续 表
续表3-2
G代码
组 A G37 G40 G41 G42 G50 B G37 G40 G41 G42 G92 C G37 G40 G41 G42 G92 07
FANUC 0-TD系统常用G指令表
G代码
功能 A B G77 G78 G79 G96 97 C G20 G21 G24 G96 02 97 01 外径/内径车削循环 螺纹车削循环 端面车削循环 恒表面切削速度控制 恒表面切削速度控制取 消 组 功能
G70
G01
G02 G03 G04 G10 G11 G20 G21 G27 G28 G32 G34 G36
G01
G02 G03 G04 G10 G11 G20 G21 G27 G28 G33 G34 G36
G01
G02 G03 G04 G10 G11 G70 G71 G27 G28 G33 G34 G36
《数控车削技能训练(第2版)》电子教案 模块一 数控车削基础知识 项目二
任务一 数控车床坐标系及基本操作
• (1)Z 轴的确定 • Z 轴的方向一般根据产生切削力的主轴轴线方向来确定,刀具远离工
件的方向为Z 轴正方向. • (2)X 轴的确定 • 平行于导轨面,且垂直于Z 轴的坐标轴为X 轴.对于数控车床,在水平面
内取垂直工件回转轴线(Z 轴)的方向为X 轴,刀具远离工件的方向为正 向,如图2-1-2所示. • 3. 机床原点与机床参考点 • (1)机床原点
0000~9999,如O2255.程序名一般要求单列一段且不需要 段号. • 2. 程序内容 • 程序内容是由若干个程序段组成的,表示数控机床要完成的全部动作. 每个程序段由一个或多个指令构成,每个程序段一般占一行,用“;”作 为每个程序段的结束代码. • 程序段格式如下:
上一页 下一页 返回
任务三 数控车削程序的输入、编辑与 运行
• 在数控车床上加工零件,首先要编制程序.数控指令的集合称为程序.一 个完整的程序由程序名、程序内容和程序结束指令组成.
• 下面是一个完整的数控加工程序,该程序由程序号开始,以M30结束.
下一页 返回
任务三 数控车削程序的输入、编辑与 运行
• 1. 程序名 • FANUC系统程序名是O××××,其中××××是4位正整数,可以是
• 1.X 轴对刀 • 1)MDI方式下,按下PROG键,则屏幕显示“MDI”字样.输入主轴转速
“M03S500”,按下循环启动键. • 2)将所需要刀具调至工作位置.MDI方式下,按下PROG键,输入“T0
101”,按下循环启动键,1号刀转到当前加工位置.
上一页 下一页 返回
任务二 数控车床对刀操作
项目二 数控车床基本操作
• 任务一 数控车床坐标系及基本操作 • 任务二 数控车床对刀操作 • 任务三 数控车削程序的输入、编辑与运行
2024年度-CAXA数控车教程
图形编辑与修改
图形选择
使用鼠标或选择工具选择需要编 辑的图形元素。
图形移动
将选择的图形元素移动到新的位 置。
图形旋转
将选择的图形元素绕指定点旋转 一定角度。
图形修剪
将选择的图形元素进行修剪,删 除多余部分或保留需要部分。
图形镜像
将选择的图形元素沿指定轴线进 行镜像处理。
图形缩放
将选择的图形元素按比例缩放大 小。
发生,确保加工过程的安全性和稳定性。
22
06 数控车削加工实例分析
23
简单轴类零件加工实例
零件描述
简单轴类零件通常具有圆柱形 的外形,其加工表面主要是外
圆、端面和倒角。
加工工艺
首先进行粗车外圆和端面,然 后进行半精车和精车,最后进 行倒角处理。
刀具选择
根据零件材料和加工要求选择 合适的刀具,如外圆车刀、端 面车刀和倒角刀。
根据加工需求和切削条件选择合 适的冷却液类型和流量,以降低 切削温度和延长刀具寿命。
机床参数设置
根据机床性能和加工需求设置合 适的机床参数,如主轴转速、进 给速度等。
加工余量分配
根据工件形状和加工精度要求合 理分配各工序的加工余量,以保 证加工质量和效率。
18
数控车削加工仿真与验证
05
19
加工轨迹仿真
01
02
03
切削深度
根据工件余量和刀具刚性 设置合适的切削深度,以 保证加工效率和刀具寿命 。
进给量
根据工件材料、刀具类型 和机床性能设置合适的进 给量,以保证加工精度和 表面质量。
切削速度
根据工件材料、刀具材料 和切削条件设置合适的切 削速度,以保证加工效率 和刀具寿命。
- 1、下载文档前请自行甄别文档内容的完整性,平台不提供额外的编辑、内容补充、找答案等附加服务。
- 2、"仅部分预览"的文档,不可在线预览部分如存在完整性等问题,可反馈申请退款(可完整预览的文档不适用该条件!)。
- 3、如文档侵犯您的权益,请联系客服反馈,我们会尽快为您处理(人工客服工作时间:9:00-18:30)。
项目一数控车削加工基础1.1学习目标通过本课题学习,掌握数控车床的基本结构及其各轴移动方向对应的坐标轴;理解坐标系的确立原则,并结合加工前的对刀动作掌握机床上几种坐标系的联系与区别;掌握数控车床编程指令的基本格式;1.2 知识点本课题主要讲解以下知识点:1、机床结构及其对应坐标轴;2、坐标系的确立原则;3、机床坐标系、编程坐标系、加工坐标系的联系与区别;4、对刀的方法与原理;5、数控车床编程格式的确定。
1.3 学习容1.3.1机床结构及其坐标轴如图1.1示,操作机床面板,了解各坐标轴位置规定并弄清楚正、负方向等。
(可拓展讲解其他类型结构)附记机床操作安全规程。
图1.1数控车床1.3.2坐标系的确立原则1.刀具相对于静止工件而运动的原则这一原则使编程人员能在不知道是刀具移近工件还是工件移近刀具的情况下,就可依据零件图样,确定机床的加工过程。
附记机床操作安全规程。
2.标准坐标(机床坐标)系的规定在数控机床上,机床的动作是由数控装置来控制的,为了确定机床上的成形运动和辅助运动,必须先确定机床上运动的方向和运动的距离,这就需要一个坐标系才能实现,这个坐标系就称为机床坐标系。
标准的机床坐标系是一个右手笛卡尔直角坐标系,图1.2中规定了X轴为大拇指指向,Y轴为食指指向,Z轴为中指指向。
这个坐标系的各个坐标轴与机床的主要导轨相平行,它与安装在机床上的主要直线导轨找正的工件相关。
3.运动的方向数控机床的某一部件运动的正方向,是增大工件和刀具之间距离的方向。
图1.2 坐标系根据实际情况,结合具体机床,依次确定Z、X、Y轴1.3.3三点联系与区别1.机床原点机床原点是指在机床上设置的一个固定的点,即机床坐标系的原点。
它在机床装配、调试时就已确定下来了,是数控机床进行加工运动的基准参考点。
在数控车床上,一般取在卡盘端面与主轴中心线的交点处,如图1.3(a)中O1即为机床原点。
图1.3机床原点2.编程原点指根据加工零件图样选定的编制零件程序的原点,即编程坐标系的原点。
如上图(b)中所示的O2点。
编程原点应尽量选择在零件的设计基准或工艺基准上,并考虑到编程的方便性,编程坐标系中各轴的方向应该与所使用数控机床相应的坐标轴方向一致。
3.加工原点也称程序原点。
是指零件被装卡好后,相应的编程原点在机床原点坐标系中的位置。
1.3.4对刀设若有图1.4所示加工零件、程序,需要在加工前的完成对刀动作(移动刀具到起刀点位置)。
其加工程序如表1.1图1.4 加工零件表1.1程序表程序说明%1G92 X50 Z100 M03 S300 建立工件坐标系主轴正转G00 X45 Z-1G01 X0 F80G00 X50 Z100 M05.M30快速到达切削起点,进行端面切削快速返回起刀点,主轴停程序结束对刀方法多种多样,建议初学者先理解掌握一般对刀法。
为使结果更为精确,可反复进行“试切—测量—调整”几个阶段。
如图1.5,其对刀操作过程如下:1.回参考点进行回参考点操作,通过刀具返回机床零点消除刀具运行中插补累积误差。
图1.5 对刀2.试切削用手动方式操做机床,先切削工件外圆表面保持刀具在X方向位置不变退刀,记录此时X轴坐标值X t,并测量试切后的工件外圆直径为d;然后切削工件的右端面,保持刀具在Z方向位置不变退刀,记录此时Z轴坐标值Z t。
3.计算编程原点在机床坐标系中的坐标值设若工件长度为L,则编程原点为:X o=X t-d,Z o=Z t-L;若编程原点选在右端面,则此处L取0。
4.计算刀具机床坐标系中的起点位置若刀具起点位置设为A(60,100),则刀具起点坐标位置为X a=X o+60,Z a=Z o+100。
5. 建立工件坐标系移动刀具到起点位置,执行G92指令,则系统建立了新的工件坐标系。
若加工坐标系采用指令G54系列来选择,则只需计算出3步骤中的(X o,Z o)输入相应坐标系设置中即可;但依然显得旧而麻烦,现在常用的T方式对刀法(即将步骤2中测量直径d和工件长度L输入到指定的刀具偏置号中,然后在程序中调用相应偏置号,如T0101就意味着使用1号刀1号偏置来建立工件坐标系),十分简单明了。
1.3.5 程序结构与格式1.程序结构一个零件程序是一组被传送到数控装置中去的指令和数据,这个零件程序是由遵循一定结构、句法和格式规则的若干个程序段组成的,而每个程序段是由若干个指令组成的,其结构如下:O1012N10 G54 G90 G00 Z50N20 M03 S800N30 G00 X-50 Y0N40 Z3。
N110 M30一般由开始符(单列一段)程序名(单列一段)程序主体和程序结束指令(一般单列一段)组成。
程序的最后还有一个程序结束符。
程序开始符与程序结束符是同一个字符:在ISO代码中是%,在EIA代码中是ER。
程序结束指令可用M02(程序结束)或M30(程序结束返回)。
在使用中,执行M02指令结束程序时,自动运行结束后光标停在程序结束处;而执行M30指令来结束程序时,自动运行结束后光标和屏幕显示能自动返回到程序开始处,一按启动按钮就可以再一次运行程序。
虽然M02与M30允许与其他程序字合用一个程序段,但最好还是将其单列一段,或者只与顺序号共用一个程序段。
程序名位于程序主体之前、程序开始符之后,它一般独占一行。
程序名有两种形式:一种是以规定的英文字母(多用O)打头、后面紧随若干位数字组成,数字最多允许位数由数控系统决定,在使用说明书中可以查询到,常见的是两位和四位两种;另一种形式是,程序名由英文字母、数字或英文、数字混合组成,中间还可以加入“-”号。
程序名用哪种形式是由数控系统决定的。
2.程序段格式程序段是可作为一个单位来处理的连续的字组,它实际上是数控加工程序中的一句。
多数程序段是用来指令机床完成(执行)某一个动作的。
程序的主体是由若干个程序段组成的。
在书写和打印时,每个程序段一般占一行,在荧光屏显示程序时也是如此。
程序段格式是指程序段中的字、字符和数据的安排形式。
在数控机床的发展历史上,曾经用过固定顺序格式和分隔符程序段格式(也叫分隔符顺序格式)。
现在一般都使用字地址可变程序段格式,它称为字地址格式。
对这种格式,程序段由若干个字组成,字首是一个英文字母,它称为字的地址。
字的功能类别由地址决定。
在此格式程序中,上一段程序中已写明、本程序段里又不必变化的那些字仍然有效,可以不再重写。
具体地说,对于模态(连续有效)G指令(如G01),在前面程序段中已有时可不再重写。
在这种格式中,每个字长不固定。
例如在尺寸字中可只写有效数字、省略前置零或后置零。
各个程序段中的长度(即字符个数)和程序字的个数都是可变的,故属于可变程序段格式。
下面列出某程序中的两个程序段:N30 G01 X88.467 Z47.5 F50 S250 T03 M08N40 X75.4这两段的字数和字符个数相差甚大,但除X坐标有变化外其他情况不变。
当今的数控系统绝大多数对程序段中各类字的排列不要求有固定的顺序。
即在同一程序段中各个指令字的位置可以任意排列。
上例N30段也可写成:N30 M08 T03 S250 F50 Z47.5 X88.467 G01当然,还有很多排列形式,它们在数控系统中执行都是等效的。
在大多数场合,为了书写、输入、检查和校对的方便,程序字在程序段中习惯按一定的顺序排列,如N、G、X、Y、Z、F、S、T、M顺序。
其相关文字码含义如表1.2所示表1.2 文字码及其含义3.M、S、T指令1)辅助功能M代码辅助功能由地址字M和其后的一或两位数字组成,主要用于控制零件程序的走向,以及机床各种辅助功能的开关动作。
非模态M功能和模态M功能二种形式。
非模态M功能:当段有效代码;模态M功能:续效代码,号上电初始化;前置M功能:在程序段编制的轴运动之前执行;后置M功能:在程序段编制的轴运动之后执行。
表1.2 常用M代码及功能M00、M02、M30、M98、M99用于控制零件程序的走向,是CNC定的辅助功能,不由机床制造商设计决定,与PLC程序无关;其余M代码用于机床各种辅助功能的开关动作,其功能不由CNC定,而是由PLC程序指定,所以有可能因机床制造厂不同而有差异(表为标准PLC指定的功能),请使用者参考机床说明书。
2)主轴功能S代码主轴功能S控制主轴转速,其后的数值表示主轴速度,常见单位为转/每分钟(r/min)。
恒线速度功能时S指定切削线速度,其后的数值单位为米/每分钟(m/min)。
(G96恒线速度有效、G97取消恒线速度)S是模态指令,S功能只有在主轴速度可调节时有效。
S所编程的主轴转速可以借助机床控制面板上的主轴倍率开关进行修调。
3)刀具功能T代码T代码用于选刀,其后的4位数字分别表示选择的刀具号和刀具补偿号。
T 代码与刀具的关系是由机床制造厂规定的,请参考机床厂家的说明书。
当一个程序段同时包含T代码与刀具移动指令时,先执行T代码指令。
T指令同时调入刀补寄存器中的补偿值。
刀具补偿功能目前常用于简便对刀中,见本课题对刀知识点。
1.4思考与练习1.任意给定两个坐标轴的方向,练习根据右手笛卡儿原则判定第三个坐标轴方向2.如图1.6所示零件其编程原点可如何选择,其坐标轴位置又如何?3.M、S、T代码在程序中有何作用?图1.6 练习零件。