挤压模具毕业设计论文
冲压模具毕业设计论文 (14)

目录摘要 (2)1 模具的介绍 (3)1.1冲压技术的进步 (3)1.2 模具的发展与现状 (3)2 冲压工艺方案的制定 (5)2.1 工艺分析 (5)2.2 排样图设计 (6)3 模具总体结构设计 (8)3.1 条料定位装置 (8)3.2 出料装置 (10)3.3 模具结构特点 (10)3.4 模具工作过程 (10)4 模具零件的设计与计算 (12)4.1 凸、凹模刃口尺寸的计算 (12)4.1.1 凸、凹模间隙的选择 (12)4.1.2 凸、凹模刃口尺寸计算 (12)4.2 凸、凹模的设计 (17)4.2.1 凸模的结构和固定形式 (17)4.2.2 凸模长度的确定 (18)4.2.3 凸模的强度计算 (18)4.2.4 凹模结构形式设计 (20)4.2.5 凹模结构尺寸的确定 (20)4.3 模板的设计 (22)4.4 卸料弹簧的选用 (22)4.5 其它零件的设计 (23)5 冲压设备的选用 (25)5.1 冲压力的计算 (25)5.2 选择压力机 (26)6 压力中心的计算 (27)6.1 计算步骤 (27)6.2 计算压力中心 (27)7 总结 (28)参考文献 (29)致谢 (30)摘要冲压成形作为现代工业中一种十分重要的加工方法,用以生产各种板料零件,具有很多独特的优势,其成形件具有自重轻、刚度大、强度高、互换性好、成本低、生产过程便于实现机械自动化及生产效率高等优点,是一种其它加工方法所不能相比和不可替代的先进制造技术,在制造业中具有很强的竞争力,被广泛应用于汽车、能源、机械、信息、航空航天、国防工业和日常生活的生产之中。
在吸收了力学、数学、金属材料学、机械科学以及控制、计算机技术等方面的知识后,已经形成了冲压学科的成形基本理论。
以冲压产品为龙头,以模具为中心,结合现代先进技术的应用,在产品的巨大市场需求刺激和推动下,冲压成形技术在国民经济发展、实现现代化和提高人民生活水平方面发挥着越来越重要的作用。
冲压模具毕业设计论文[2]
![冲压模具毕业设计论文[2]](https://img.taocdn.com/s3/m/9200aa4902d8ce2f0066f5335a8102d276a26185.png)
冲压模具毕业设计论文[2]1. 引言冲压模具是冲压工艺中不可或缺的关键组成部分。
它的优劣直接影响着冲压产品的质量和生产效率。
因此,在冲压模具的设计和制造上要注重各个方面的优化,以实现高效、高质量的冲压生产。
本文将探讨冲压模具在毕业设计中的应用,通过分析冲压模具的设计要点和制造过程,提出一种在制造过程中提高模具质量和降低成本的方法。
2. 冲压模具设计要点冲压模具的设计是一个综合性的工作,需要考虑多个方面的因素。
下面列举了冲压模具设计的要点:2.1 材料选择冲压模具需要具备高强度和耐磨损的特性。
因此,在材料选择上应当考虑使用高硬度材料,如合金工具钢。
同时,还要考虑材料的加工性能和耐热性能。
2.2 结构设计冲压模具的结构设计应当考虑到产品形状和尺寸的特点,并且要与冲压设备的工作方式相匹配。
在结构设计中,需要合理安排模具的凸模、凹模和导向系统,确保冲压过程中的定位和导向准确。
2.3 寿命设计冲压模具的寿命设计是一个重要的考虑因素。
寿命设计时要考虑冲压过程中的应力、变形和磨损等因素,以确保模具在长期使用中具有稳定的性能。
2.4 润滑设计冲压模具在工作过程中需要进行润滑,以降低摩擦和磨损。
因此,在模具设计中需要考虑润滑系统的设计,合理设置润滑通道和喷油装置。
3. 冲压模具制造过程冲压模具的制造过程可以分为以下几个步骤:3.1 制造工艺规划制造工艺规划是整个制造过程的基础。
在制造工艺规划中,需要确定模具的加工顺序、方法和工艺参数等,确保模具的加工精度和质量要求。
3.2 加工制造冲压模具的加工制造包括以下几个方面:材料切割、零件加工、工艺装配和热处理等。
其中,热处理是提高模具硬度和耐磨性的重要步骤。
3.3 调试与试模制造完成后,需要对模具进行调试和试模。
通过调试和试模可以发现和解决模具的问题,确保模具在使用时能够正常运行。
4. 优化冲压模具制造过程的方法为了提高冲压模具制造的效率和质量,可以采用以下方法进行优化:4.1 CAD/CAM技术应用CAD/CAM技术可以提高冲压模具的设计和制造效率。
AZ61镁合金挤压模具毕业设计
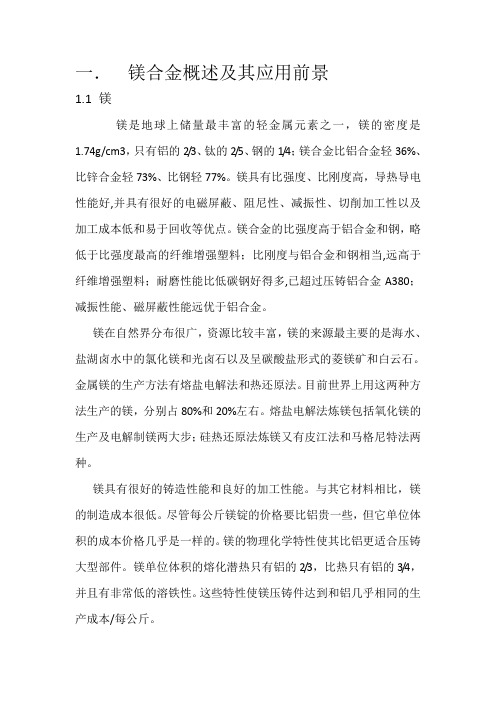
一.镁合金概述及其应用前景1.1 镁镁是地球上储量最丰富的轻金属元素之一,镁的密度是1.74g/cm3,只有铝的2/3、钛的2/5、钢的1/4;镁合金比铝合金轻36%、比锌合金轻73%、比钢轻77%。
镁具有比强度、比刚度高,导热导电性能好,并具有很好的电磁屏蔽、阻尼性、减振性、切削加工性以及加工成本低和易于回收等优点。
镁合金的比强度高于铝合金和钢,略低于比强度最高的纤维增强塑料;比刚度与铝合金和钢相当,远高于纤维增强塑料;耐磨性能比低碳钢好得多,已超过压铸铝合金A380;减振性能、磁屏蔽性能远优于铝合金。
镁在自然界分布很广,资源比较丰富,镁的来源最主要的是海水、盐湖卤水中的氯化镁和光卤石以及呈碳酸盐形式的菱镁矿和白云石。
金属镁的生产方法有熔盐电解法和热还原法。
目前世界上用这两种方法生产的镁,分别占80%和20%左右。
熔盐电解法炼镁包括氧化镁的生产及电解制镁两大步;硅热还原法炼镁又有皮江法和马格尼特法两种。
镁具有很好的铸造性能和良好的加工性能。
与其它材料相比,镁的制造成本很低。
尽管每公斤镁锭的价格要比铝贵一些,但它单位体积的成本价格几乎是一样的。
镁的物理化学特性使其比铝更适合压铸大型部件。
镁单位体积的熔化潜热只有铝的2/3,比热只有铝的3/4,并且有非常低的溶铁性。
这些特性使镁压铸件达到和铝几乎相同的生产成本/每公斤。
1.2 镁合金性能(1)、在实用金属中是最轻的金属镁的比重大约是铝的2/3,是铁的1/4。
它是实用金属中的最轻的金属。
应用范围:镁合金广泛用于携带式的器械和汽车行业中,达到轻量化的目的。
(2)、高强度、高刚性镁合金的比重虽然比塑料重,但是,单位重量的强度和弹性率比塑料高,所以,在同样的强度零部件的情况下,镁合金的零部件能做得比塑料的薄而且轻。
另外,由于镁合金的比强度也比铝合金和铁高,因此,在不减少零部件的强度下,可减轻铝或铁的零部件的重量。
应用范围:手机电话,笔记本电脑上的液晶屏幕的尺寸年年增大,在它们的枝撑框架和背面的壳体上使用了镁合金。
冲压模具毕业设计论文[1]
![冲压模具毕业设计论文[1]](https://img.taocdn.com/s3/m/f70dea08376baf1ffc4fadf4.png)
第一章绪论1.1 中国冲压模具现状根据考古发现,早在2000多年前,我国已有冲压模具被用于制造铜器,证明了中国古代冲压成型和冲压模具方面的成就在世界领先。
1953年,长春第一汽车制造厂在中国首次建立了冲模车间,该厂于1958年开始制造汽车覆盖件模具。
我国于20世纪60年代开始生产精冲模具。
在走过了漫长的发展道路之后,目前我国已形成了300多亿元(未包括港、澳、台的统计数字,下同。
)各类冲压模具的生产能力。
近年来,我国冲压模具水平已有很大提高。
大型冲压模具已能生产单套重量达50多吨的模具。
为中档轿车配套的覆盖件模具国内也能生产了。
精度达到1~2μm,寿命2亿次左右的多工位级进模国内已有多家企业能够生产。
表面粗糙度达到Ra≦1.5μm的精冲模,大尺寸(Φ≧300mm)精冲模及中厚板精冲模国内也已达到相当高的水平。
1.1.1 模具CAD/CAM技术状况我国模具CAD/CAM技术的发展已有20多年历史。
由原华中工学院和武汉733厂于1984年共同完成的精冲模CAD/CAM系统是我国第一个自行开发的模具CAD/CAM 系统。
由华中工学院和北京模具厂等于1986年共同完成的冷冲模CAD/CAM系统是我国自行开发的第一个冲裁模CAD/CAM系统。
上海交通大学开发的冷冲模CAD/CAM系统也于同年完成。
20世纪90年代以来,国内汽车行业的模具设计制造中开始采用CAD/CAM技术。
国家科委863计划将东风汽车公司作为CIMS应用示范工厂,由华中理工大学作为技术依托单位,开发的汽车车身与覆盖件模具CAD/CAPP/CAM集成系统于1996年初通过鉴定。
在此期间,一汽和成飞汽车模具中心引进了工作站和CAD/CAM 软件系统,并在模具设计制造中实际应用,取得了显著效益。
1997年一汽引进了板料成型过程计算机模拟CAE软件并开始用于生产。
模具CAD/CAM技术能显著缩短模具设计与制造周期,降低生产成本,提高产品质量,已成为人们的共识。
挤压模具毕业设计论文

目录一、冷挤压零件分析 31、材料选择 32、形状设计 33、尺寸分析 4二、冷挤压工艺分析 41、坯料尺寸确定 42、毛坯软化处理 43、冷挤压毛坯表面处理与润滑 54、变形程度计算 65、确定挤压次数 66、工序设计 8三、冷挤压设备选择121、挤压力的确定 122、压力机吨位计算123、挤压设备类型选择 134、液压式压力机型号选择 13四、冷挤压模具结构设计13五、凸模设计141、凸模的长度尺寸计算 152、凸模加工工艺路线 15六、凹模设计161、组合凹模结构设计 172、棘轮套挤压齿形模芯的设计 173、齿形模芯加工20七、冷挤压件质量分析20八、凸模机加工工艺23九、非标准件三维结构图24 致谢30 参考文献31棘轮套冷挤压成形工艺及模具设计重庆工商大学机械设计制造及其自动化专业2006级模具班郭建军指导老师唐全波黄少东中文摘要:冷挤压是精密塑性体积成形技术中的一个重要组成部分。
冷挤压是指在冷态下将金属毛坯放入模具模腔内,在强大的压力和一定的速度作用下,迫使金属从模腔中挤出,从而获得所需形状、尺寸以及具有一定力学性能的挤压件。
显然,冷挤压加工是靠模具来控制金属流动,靠金属体积的大量转移来成形零件的。
本设计介绍了棘轮套零件结构分析、挤压工艺过程、挤压设备选择、模具结构的设计、凸凹模设计、挤压件质量分析、棘轮套齿形模芯的结构、凸模加工工艺及模具各部件三维造型进行了叙述,并计算了毛坯体积、毛坯尺寸、变形程度、挤压比和挤压力。
与常规的棘轮套加工工艺相比,冷挤压成形的棘轮套具有齿形强度高、齿形尺寸精度较高、表面粗糙度值低、材料利用率高、生产效率高、设备投资少等优势。
关键词:冷挤压棘轮套正挤压凸缘Gear Cold Extrusion of the process and die design(Chongqing Technology and Business University ,mechanical design automation and manufacturing professionals ,06 mold Guo JianJun)Abstract:V olume precision plastic cold extrusion forming technology is an important component. Cold extrusion is the next in the cold metal blank into the mold cavity, the strong pressure and under a certain speed, forced metal extrusion from the mold cavity to obtain the required shape, size, and has some mechanical performance of extrusion Obviously, the cold extrusion process is to control the metal flow by mold, by transfer to a large number of metal forming volume parts.Ratchet sets introduced structure of parts, extrusion process, extrusion equipment selection, die structure design, punch and die design, extrusion quality analysis, ratchet sets of the structure of tooth punch, punch and die processing of parts, Three-dimensional modeling of the narrative, and calculate the rough size, blank size, deformation, extrusion ratio and extrusion pressure. And conventional processing technology compared to ratchet set, ratchet set of cold extrusion with gear, high strength, high precision gear size, low surface roughness, high utilization ratio, high efficiency, less investment in equipment and other advantages.key words: Cold extrusion Ratchet sets Extrusion Flange图1—棘轮套零件图图1所示为棘齿套零件图。
模具设计与制造毕业论文范例

模具设计与制造毕业论文范例绪论{一} 【模具在加工工业中的地位】模具是利用其特定形状去成型具有一定的形状和尺寸制品的工具。
在各种材料加工工业中广泛的使用着各种模具。
例如金属铸造成型使用的砂型或压铸模具、金属压力加工使用的锻压模具、冷压模具等各种模具。
对模具的全面要求是:能生产出在尺寸精度、外观、物理性能等各方面都满足使用要求的公有制制品。
以模具使用的角度,要求高效率、自动化操作简便;从模具制造的角度,要求结构合理、制造容易、成本低廉。
模具影响着制品的质量。
首先,模具型腔的形状、尺寸、表面光洁度、分型面、进浇口和排气槽位置以及脱模方式等对制件的尺寸精度和形状精度以及制件的物理性能、机械性能、电性能、内应力大小、各向同性性、外观质量、表面光洁度、气泡、凹痕、烧焦、银纹等都有十分重要的影响。
其次,在加工过程中,模具结构对操作难以程度影响很大。
在大批量生产塑料制品时,应尽量减少开模、合模的过程和取制件过程中的手工劳动,为此,常采用自动开合模自动顶出机构,在全自动生产时还要保证制品能自动从模具中脱落。
另外模具对制品的成本也有影响。
当批量不大时,模具的费用在制件上的成本所占的比例将会很大,这时应尽可能的采用结构合理而简单的模具,以降低成本。
现代生产中,合理的加工工艺、高效的设备、先进的模具是必不可少是三项重要因素,尤其是模具对实现材料加工工艺要求、塑料制件的使用要求和造型设计起着重要的作用。
高效的全自动设备也只有装上能自动化生产的模具才有可能发挥其作用,产品的生产和更新都是以模具的制造和更新为前提的。
由于制件品种和产量需求很大,对模具也提出了越来越高的要求。
因此促进模具的不断向前发展,首选[二] 【模具的发展趋势】近年来,模具增长十分迅速,高效率、自动化、大型、微型、精密、高寿命的模具在整个模具产量中所占的比重越来越大。
从模具设计和制造角度来看,模具的发展趋势可分为以下几个方面:(1)加深理论研究在模具设计中,对工艺原理的研究越来越深入,模具设计已经有经验设计阶段逐渐向理论技术设计各方面发展,使得产品的产量和质量都得到很大的提高。
铝型材(散热型)挤压工艺与模具设计毕业设计

摘要铝合金因质轻、美观、良好的导热性和易加工成复杂的形状,而被广泛地用于生产散热器材。
铝合金散热器型材主要有三种类型:扁宽形,梳子形或鱼刺形;圆形或椭圆形以及树枝形。
与其他铝型材比,散热器有其自身的特点:散热片之间距离短,相邻两散热片之间形成一个槽形,其深宽比很大;壁厚差大,散热片的齿部很薄,而其根部的底板厚度大。
散热器复杂的截面形状给模具设计、制造和生产带来很大的难度。
本文以两种常用散热器为实例,在总结大量散热器模具设计制造经验的基础上,论述了散热片挤压模具设计的步骤和关键点。
散热器型材挤压模具设计既要保证模具有足够的强度又要平衡金属在模具中的流速。
根据散热器的产品图,将梳子型散热器挤压模具设计成平摸,与导流模配合使用。
把太阳花散热器挤压模具设计成分假流模,以保证在挤压时的金属流动比平模更均匀,这也是太阳花散热器模具设计的关键点。
文中选用4Cr5MoSiV1模具钢作为模具材料,讨论了散热器挤压模具的热处理工艺和散热器的挤压工艺特点。
关键词:散热器挤压模具设计挤压工艺铝型材Extrusion Process and Die Design for Radiator Aluminum Extruded SectionsABSTRACTAluminum alloy, for its light weight, beautiful, good thermal conductivity and easy processing into complex shapes,is widely used to produce cooling equipment. Aluminum radiator profiles are mainly three typesg: flat wide shape, or a fishbone-shaped comb-shaped; round or oval-shaped;and branching shape. Compared with the other aluminum extruded sections radiator has its own characteristics: the distance between the heat sink is short, between two adjacent heat sink to form a trough, and its large aspect ratio; differential wall thickness, heat sink teeth thin, and its roots in the bottom thick. The mold design, manufacturing and production are very difficulty for the complexity of the shape of radiator extruded sections.In this paper, the extruded die design of two common heat sink radiators are discussed in detail on the basis of a lot of experiences in mold design and manufacture for the radiator. Extruded die design has two key parts,the first is sufficient strength to ensure that mold; the second is to balance the flow of metal in the mold. Based on the Product plans of radiators, the radiator comb flat extrusion die are designed to touch, used in conjunction with the diversion mode. The extrusion die is designed radiator sunflowers streaming mode, split mode when the metal flow in the extrusion die is more complex than flat, so how to balance the flow rate of the metal mold is key points for the design of radiator sunflowers. 4Cr5MoSiV1 die steel is usedand also the radiator heat treatment process and extruded process are discussed.Keywords:Radiator Extrude mold design Extrusion processAluminum extruded sections目录摘要 (I)Extrusion Process and Die Design for Radiator Aluminum Extruded Sections (II)ABSTRACT (II)第一章绪论 (1)1.1引言 (1)1.2挤压模具在铝型材挤压生产中的重要性 (1)1.3铝型材挤压模具技术发展概况 (3)1.4论文的主要研究内容 (5)第二章型材挤压模具设计技术 (6)2.1型材模具的设计原则及步骤 (6)2.1.1挤压模具设计时应考虑的因素 (6)2.1.2模具设计的原则与步骤 (6)2.1.3模具设计的技术条件及基本要求 (9)2.2挤压模典型结构要素的设计 (9)2.2.1模角 (9)2.2.2定径带长度和直径 (10)2.2.3出口直径或出口喇叭锥 (10)2.2.4入口圆角 (11)2.3确定采用平面和分流模的原则 (11)2.4平面分流组合模的特点与结构 (12)2.4.1工作原理与特点 (12)2.4.2分流组合模的结构 (13)2.5模具外形尺寸的确定原则 (14)第三章典型散热器挤压模具设计 (16)3.1太阳花散热器的模具设计 (16)3.1.1太阳花散热器产品结构分析 (16)3.1.2太阳花散热器挤压模具整体结构设计方案 (17)3.1.3太阳花散热器分流组合模结构设计 (18)3.2梳子型散热器模具设计 (30)3.2.1梳子型散热器产品结构分析 (30)3.2.2梳子型散热器挤压模具整体结构设计方案 (32)3.2.3梳子型散热器结构设计 (32)第四章模具的选材与热处理及维护与保养 (45)4.1模具材料的选择 (45)4.1.1模具材料的使用条件 (45)4.1.2模具材料的性能要求 (45)4.1.3挤压工模具选材的特点 (46)4.1.4模具材料的选择 (48)4.2模具材料的热处理 (50)4.2.1退火工艺 (50)4.2.2淬火工艺 (50)4.2.3回火工艺 (51)4.2.4 4Cr5MoSiV1钢的热处理工艺 (52)4.3模具的维护与保养 (53)4.3.1模具的修正 (53)4.3.2模具的合理使用 (54)第五章型材挤压工艺 (55)5.1铝及铝合金材料挤压生产工艺流程 (55)5.2挤压工艺的制定 (56)5.2.1挤压方法的选择 (56)5.2.2坯料形状尺寸的确定 (56)5.2.3挤压温度范围 (57)5.2.4流动速度和挤压速度 (58)5.2.5挤压工具的结构 (58)第六章结论 (59)参考文献 (60)致谢 (62)第一章绪论1.1引言挤压工模具设计与制造是铝合金挤压材,特别是铝合金型材生产的关键技术,不仅影响产品的质量、生产效率和交货周期,而且也是决定产品成本的重要因素之一。
挤压模具毕业设计

挤压模具毕业设计挤压模具毕业设计在当今的制造业中,模具设计是一个非常重要的环节。
而挤压模具设计更是其中的一个关键领域。
挤压模具的设计质量直接影响到产品的质量和效率。
在毕业设计中,我选择了挤压模具设计作为研究的主题,旨在深入探讨挤压模具的设计原理和优化方法,以提高产品的生产效率和质量。
一、挤压模具的基本原理挤压模具是一种用于将金属材料挤压成特定形状的工具。
其基本原理是通过施加压力将金属材料从模具的出料口挤出,并在模具的形状限制下形成所需的产品。
挤压模具的设计需要考虑多个因素,如材料的流动性、模具的结构和形状等。
二、挤压模具的设计要求1. 合理的模具结构:挤压模具的结构应该合理,能够满足产品的形状要求,并且易于加工和维修。
同时,模具的结构应该尽可能简单,以降低制造成本。
2. 充分考虑材料特性:不同的金属材料具有不同的流动性和变形特性。
在挤压模具的设计中,需要充分考虑材料的特性,以确保挤压过程中的变形和缺陷尽可能小。
3. 合理的模具温度控制:挤压过程中,模具的温度对产品的质量和效率有着重要影响。
合理的模具温度控制可以提高产品的表面质量和尺寸精度。
4. 优化模具流道设计:模具流道的设计对产品的质量和生产效率有着重要影响。
通过优化模具流道的设计,可以提高金属材料的流动性,减少挤压过程中的阻力和能量损失。
三、挤压模具的优化方法1. 模具材料的选择:不同的模具材料具有不同的热导率和耐磨性。
在挤压模具的设计中,可以选择合适的模具材料,以提高模具的耐用性和导热性能。
2. 模具结构的优化:通过优化模具的结构,可以提高产品的质量和生产效率。
例如,可以通过增加模具的冷却通道来提高模具的温度控制效果,减少产品的变形和缺陷。
3. 模具流道的优化:通过优化模具流道的设计,可以提高金属材料的流动性,减少挤压过程中的阻力和能量损失。
例如,可以采用曲线型流道设计来减少金属材料的流动阻力。
4. 模具表面的处理:通过对模具表面进行特殊处理,可以提高产品的表面质量和尺寸精度。
- 1、下载文档前请自行甄别文档内容的完整性,平台不提供额外的编辑、内容补充、找答案等附加服务。
- 2、"仅部分预览"的文档,不可在线预览部分如存在完整性等问题,可反馈申请退款(可完整预览的文档不适用该条件!)。
- 3、如文档侵犯您的权益,请联系客服反馈,我们会尽快为您处理(人工客服工作时间:9:00-18:30)。
挤压工艺及模具设计题目:棘轮套冷挤压模具设计课程设计学院(系):___机械与电子学院___________专业:___模具设计与制造___________班级:_______0540902______________姓名:____喻庆勇______________任课教师:_____丁常汶______________设计时间:__二 0 一一年十月________目录一、冷挤压零件分析 31、材料选择 32、形状设计 33、尺寸分析 4二、冷挤压工艺分析 41、坯料尺寸确定 42、毛坯软化处理 43、冷挤压毛坯表面处理与润滑 54、变形程度计算 65、确定挤压次数 66、工序设计 8三、冷挤压设备选择121、挤压力的确定 122、压力机吨位计算123、挤压设备类型选择 134、液压式压力机型号选择 13四、冷挤压模具结构设计13五、凸模设计141、凸模的长度尺寸计算 152、凸模加工工艺路线 15六、凹模设计161、组合凹模结构设计 172、棘轮套挤压齿形模芯的设计 173、齿形模芯加工20七、冷挤压件质量分析20八、凸模机加工工艺23九、非标准件三维结构图24 致谢29 参考文献30一、挤压零件分析图1—棘轮套零件图图1所示为棘齿套零件图。
它是一种两端带孔,中间带凸缘的轴类齿轮零件,其各截面变化较大、直径为φ39mm的外表面为异形齿且精度要求较高,外齿齿顶圆角太小(R0.5),成形工艺性较差。
内孔型腔表面要求光滑平整,无毛刺,划痕,裂纹和折叠等缺陷存在,表面粗糙度Ra3.2以下。
对于这种具有外齿形、两端带孔﹑中间带凸缘轴类零件,要获得具有外齿形的精密锻件,采用单工序成形是不可能的,必须采用多工序成形工艺。
根据零件的结构特点和材料的工艺特性,采用冷挤压成形工艺比较适宜。
1,材料选择该棘轮套选用20CrMo钢,该钢材参照国家标准:GB/T 3077-1988。
其化学成分(质量分数,﹪)为:0.17~0.24C,0.17~0.37Si,0.40~0.70Mn,≤0.035S,≤0.035P,0.80~1.10Cr,≤0.030Ni,≤0.030Cu,0.15~0.25Mo,属于低碳合金结构钢。
该材料的强度较低、塑性很好,是典型的冷成形材料。
2,形状设计(a)对称性棘轮套为轴对称,对称性最好,(b)断面积的差根据冷挤压棘轮套工序,第一道正挤压工序断面积差=1909.562mm,第二道工序断面积差:2513.312mmmm,第三道工序断面积差:1010.262(c)断面过渡第一道正挤压工序,由于直径φ46圆柱与直径φ63.6的中间凸缘相差较大,截面变化较剧烈,是变形和应力分布最不均匀的区域,材料在该处易产生裂纹。
故应设计成锥形过渡。
①挤压比G (引用《挤压实用技术》p113) G=10F F式中 F 0—冷挤压变形前毛坯的横截面积(2mm) F1—冷挤压变形后制件的横截面积(2mm )经计算得G=2.57。
查《挤压模具简明设计手册》P25表2.13 冷挤压件尺寸的极限值,选取a=45°。
②过渡圆角半径 (引用《挤压模具简明设计手册》P26表 2.13 冷挤压件尺寸的极限值)查表取R=1.0mm;r=3.0mm(d )断面形状根据零件图分析知,棘轮套无锥形、细小深孔、通孔,故适合于冷挤压断面形状。
3,尺寸分析(a )最小压余厚度t由于棘轮套采用正挤压工艺,故t ≥d/2满足其要求。
(b )最小壁厚s壁厚越小,挤压力越大,变形程度越大,变形抗力越大,金属流动越困难。
查《挤压模具简明设计手册》P38表1-31 冷挤压工艺尺寸的极限数值,得低碳钢S ≥d/5。
根据零件图分析知,S=7mm 、d=23mm 故S ≥d/5满足其要求。
(c )最大挤压深度L为防止过长的凸模,工作时容易弯曲,稳定性差。
查《挤压模具简明设计手册》P38表1-31 冷挤压工艺尺寸的极限数值知,L ≤(2.5~3.0)d 满足其要求。
根据零件图分析知,L=26mm 、d=23mm 故L ≤(2.5~3.0)d 满足其要求。
(d )最大挤出长度L为防止挤出部分过长,润滑和退料将发生困难。
查《挤压模具简明设计手册》P38表1-31 冷挤压工艺尺寸的极限数值知,L ≤10d根据零件图分析知,L=23mm 、d=46mm 故L ≤10d 满足其要求。
二、挤压工艺分析1,坯料尺寸的确定根据挤压件毛坯的三维造型图,可以得到挤压件毛坯体积为96941.71853mm 。
市场出售标准圆钢直径有φ45,φ48,φ50,φ60,φ65mm 等,根据毛坯图最大直径为φ63.6mm,故选用直径为φ65mm 的圆钢。
下料方式采用带锯下料,因为剪切下料H/d ≥0.8(H —下料的高度;d —下料的直径)而板料冲裁下料利用率很低,带锯锯切的断面比较平整,一般不需要整形就可直接进行挤压,且材料利用率较高。
经计算得毛坯下料高度H=30.53mm2,毛坯软化处理市场提供20CrMo 材料,硬度≤197HBS 相对较高,晶粒粗大不均匀,塑性较差,变形抗力较大,若不经软化退火处理而直接进行冷挤压成形,则金属流动困难,棘轮套凸缘部位可能充填不饱满而法兰的边缘部位可能会出现局部开裂,模具也很容易损坏。
为了降低材料的变形抗力,提高塑性,应对坯料进行适当的退火处理,其退火规范如右图所示。
经过退火后的组织为细小均匀的晶粒组织,其硬度为HB130~140。
3,冷挤压毛坯表面处理与润滑毛坯表面处理与润滑主要包括以下内容:(a )去除表面缺陷。
棘轮套毛坯,去除表面缺陷在冶金厂内进行,各挤压工序制件,由于润滑不当或模具的缺陷等原因往往会引起新的表面缺陷,必须在后续工序前去除表面缺陷。
(b )清洁、去脂、为了清洁毛坯表面,以便经磷酸盐处理后使整个金属表面都能为磷酸盐处理层所覆盖,必须将毛坯上所有的油、沙、锈斑和垢壳彻底去掉,使全部金属表面都能够直接与磷酸盐处理液相接触。
该棘轮套采用化学去油的配方与工艺如下:氢氧化钠OH N a 60~100g/L碳酸钠(大苏打)32CO N a 60~80g/L磷酸钠43PO N a 25~80g/L水玻璃32SiO N a 10~15g/L处理温度 ≥85°C处理时间 15~25min在化学去油后,应当在热水中对毛坯进行冲洗。
一般在温度≥80°C 的热水中经过4~6次吊动即可。
去油效果检查十分简单,只要用水直接淋在零件上,如果已彻底去油,则水能浸润所有的表面。
(c )去除表面氧化层结合棘轮套冷挤压工艺,由于先热处理再机械加工后下料,在机械加工中将表层热处理氧化层去除,故采用机械处理去表面氧化层。
(d )磷化处理钢毛坯经磷酸盐处理后,在表面上形成磷酸盐处理层,可以避免挤压件产生鱼鳞状裂纹,可以避免模具的擦伤与碎裂。
在冷挤压变形中,其可作为润滑支承层。
经过磷酸盐处理及润滑处理后的钢毛坯具有十分理想的润滑性能,因而可以降低挤压力,防止零件表面裂纹,防止材料粘在模具上,提高模具寿命。
对于棘齿轮套磷化处理工艺如表1。
(e )润滑处理润滑处理能降低挤压的摩擦力是零件表面质量好,避免裂纹,提高模具寿命。
表1—表面与润滑处理工艺4,变形程度计算该零件采用断面缩减率表示其变形程度。
断面缩减率F εF ε=010F F F -%100⨯式中 F 0—冷挤压变形前毛坯的横断面积(2mm) F1—冷挤压变形后制件的横断面积(2mm ) (a)计算总变形程度已知机加工后坯料直径ΦD0=63.6mm,零件最大变形程度地方为零件φd1=37mm ,φd2=23mm 环形端面,故零件总变形程度为F0=∏20D /4 εF =010F F F -%100⨯=78.29% 5,确定挤压次数假设采用一道工序,经计算得ε1F =78.29%ε1F =εF <ε许F =80%, 其ε许F 由表3.3(P38《挤压模具简明设计手册》)差得。
考虑挤压件尺寸因素,挤压件形状复杂程度,采用一次挤压难以保证精度和形状,故选用多道工序进行挤压。
假设采用三道挤压工序工序3变形程度:已知D0=63.6mm,d1=46mm,d2=23mm 。
F0=∏20D /4F1= ∏(21d -2d )/4 F ε=010F F F -%100⨯=60.77% 工序4变形程度:已知D0=63.6mm,d1=37mm,d2=23mm 。
F0=∏20D /4 εF =010F F F -%100⨯=78.29%总的变形程度af=78.29%,由于20CrMo 钢含C 量为0.008%~0.20%属于低强度钢,查表3.3(P38《挤压模具简明设计手册》)得af 许为78%~88%.故各工序af<af 许。
宗上考虑,采用三次正挤压。
三次正挤压方式如(图2-图4)图2—第一次正挤压图3—第二次正挤压图4—第三次正挤压6,工序设计冷挤压生产零件,从毛坯变为成品要以系列工序。
挤压工艺的设计的实质,在于确定一系列必要的工序,使毛坯逐步接近挤压件形状。
棘齿套的形状复杂,其个部位变形程度较大,变形工序较复杂,根据冷挤压工艺的特点,采用冷挤压成形工艺可以成形出此零件φ37mm、φ49.5mm的环形凸台,两端φ23mm的不通孔和齿形。
为了保证冷挤压工艺的顺利进行,在制定冷挤压件图时必须考虑棘轮套各部分的尺寸结构及技术要求和冷挤压工艺性问题:(a)对于棘轮套零件的φ37mm凸缘部分,由于尺寸公差要求不高,可以直接冷挤压成形。
(b)对于大头直径为φ39mm凸缘、零件齿形,由于尺寸精度要求也不高,只要预成形凸缘大小,深度适当,完全可以冷挤压成形。
(c)对于φ49.5mm凸缘与零件最大外径φ63.6mm相差较大,变形程度大,截面变化较剧烈,是变形和应力分布最不均匀的区域,材料在该处易产生裂纹需采用过渡断面。
(d)对于φ49.5mm端面圆角R1.5部分,考虑节约成本,模具寿命,不必要用冷挤压成形工艺直接加工出来,待成形加工后再进行切削加工。
(e)为了保证各工序间,上工序成形间便于放置于下工序凹模,应该考虑各工序间的合理间隙。
综合考虑以上因素,对于图1所示挤压零件,成形工艺制定为机械加工棒材、下料、正挤压φd=49.5mm端、正挤压φd=37mm端、正挤压齿形(如图5-图10)、图5—机械加工毛坯图6—下料图7—第一次正挤压图8—第二次正挤压图9—齿形挤压图10—机械加工R1.5圆角三、挤压设备选择1,挤压力的确定挤压力的影响因素很多,有挤压材料、变形程度、模具形状、润滑毛坯尺寸、变形方式和挤压速度等,故采用经验公式计算挤压力较准确。
P=Znbσ式中p—单位及压力,MPa;bσ—被挤压材料的强度极限,MPa;Z—模具形状的修正系数;n—变形程度系数;已知bσ=580MPa(表4-1 挤压材料的强度极限《挤压工艺及模具》p60),z=1.0(图4-33模具形状修正系数《挤压工艺及模具》p60),n=4.5(图4-34变形程度系数《挤压工艺及模具》p60)。