镁法脱硫废水处理技术初探
探究脱硫废水常规处理及零排放分析

探究脱硫废水常规处理及零排放分析作为社会力量发展的主力军,火力发电,在构建和谐社会和发展循环经济的背景下,如何减少火电技术对环境的污染,对不可再生能源的影响,在过剩电力容量的情况,只有火电技术可以不断改良和发展,以满足和谐社会的要求。
在发电过程中,水与我们身体的血液一样重要。
废水的产生是不可防止的。
为了实现来自火力发电的废水的零排放要求,以下是废水零排放的技术,并分析相应的优点和缺点。
1脱硫废水的来源及特点1.1脱硫废水的来源脱硫废水主要来源于湿法脱硫工艺。
湿法脱硫是锅炉排出的烟气脱硫的主要方法。
脱硫方法可以到达降低烟气中二氧化硫含量的目的,但需要认识到。
是的,为了保持脱硫装置中的物料平衡,系统中存在的废水必须适当排放,产生的废水称为脱硫废水。
脱硫废水中有许多有害物质。
其中,氯化物和痕量金属是重要的组成部分。
如果未经处理就排出,很容易影响环境。
因此,有必要注意这个问题。
脱硫废水处理方法的应用已成为必然。
1.2脱硫废水的特点脱硫废水的特点主要表达在以下方面:第一,脱硫废水中,含有重金属以及氯化物等元素,PH值集中在4-6.5之间。
第二,脱硫废水中,包括石膏6kg.h-1。
第三,脱硫废水中,含可溶性盐分的H20为45006kg.h-1o除此之外,脱硫废水还包括MgC03等物质。
2脱硫废水常规处理原理及工艺流程由于脱硫装置浆液中的水富含重金属元素,C1-和细颗粒在连续循环过程中,脱硫设备的腐蚀加速,影响脱硫效率,另一方面影响质量石膏因此,脱硫装置应将一定量的废水排入脱硫废水处理系统,经中和,沉淀,絮凝,沉淀,脱水处理后,到达标准后排入工业废水调节池。
原废水处理工艺系统由中和、沉降、絮凝、沉淀和脱水系统组成。
2.1中和反应首先,将来自脱硫系统的吸收塔的废浆收集在废水缓冲罐中并泵送到废水处理系统的反应罐和罐中。
在中和槽中参加定量的石灰乳,将废水的PH值提高到9~9.7,以降低废水的腐蚀性,同时减少大部分重金属的含量。
镁法脱硫废水处理技术初探

氧化镁湿法烟气脱硫废水处理技术探讨1镁法脱硫技术的发展氧化镁法在湿法烟气脱硫技术中是仅次于钙法的又一主要脱硫技术。
据介绍,氧化镁再生法的脱硫工艺最早由美国开米科公司(Chemico—Basic)在20世纪60年代开发成功,70年代后费城电力公司(PECO)与United&Constructor合作研究氧化镁再生法脱硫工艺,经过几千小时的试运行之后,在三台机组(其中两台分别为150MW和320MW)进行了全规模的FGD系统和两个氧化镁再生系统建设,上述系统于1982年建成并投入运行,1992年以后停运硫酸制造厂,直接将反应产物硫酸镁销售。
1980年美国DUCON公司在PHILADELPHAELECTRICEDDYSTONESTATION成功建成实施氧化镁湿法脱硫系统,运行至今,效果良好。
随后韩国和台湾地区也发展了自己的湿式镁法脱硫技术,目前在台湾95%的电站采用氧化镁法脱硫。
近几年国内的氧化镁湿法脱硫发展较快,2001年,清华大学环境系承担了国家“863”计划中《大中型锅炉镁法脱硫工艺工业化》的课题,对镁法脱硫的工艺参数、吸收塔优化设计和副产品回收利用等进行了深入的研究,并在4t/h、12t/h锅炉上进行了中试,在35t/h锅炉上进行了工程应用。
湿式镁法脱硫工艺又可分为氧化镁/亚硫酸镁法、氧化镁/硫酸镁抛弃法、氧化镁/硫酸镁回收法等。
本文主要介绍应用规模较大、前景广阔的氧化镁/亚硫酸镁工艺中的废水处理工艺。
2脱硫废水处理技术概况湿法烟气脱硫工艺中存在废水处理问题,虽然有很多电厂的脱硫系统都配有废水处理系统,但国内目前对脱硫废水的处理工艺研究较少,其中关注最多的是石灰石/石膏法产生的脱硫废水,对于镁法脱硫产生的废水的研究就更少了。
镁法脱硫废水处理现在多是引用和借鉴石灰石/石膏法脱硫废水处理经验。
为了维持脱硫装置浆液循环系统物质的平衡,防止烟气中可溶物质超过规定值和保证副产物品质,必须从循环系统中排放一定量的废水。
镁法脱硫技术方案

镁法脱硫技术方案镁法脱硫(MgO法脱硫)是一种高效的燃煤电厂脱硫技术,它通过利用镁原料与SO2反应生成MgSO3/MgSO4及相应的MgO等反应产物,将燃煤电厂的SO2排放量降低到国家标准以下。
下面将给出镁法脱硫技术方案。
一、工艺流程镁法脱硫的工艺流程主要包括石灰石粉碎、煤粉预处理、喷吹预处理剂、燃烧脱硝、湿法脱硫等。
具体流程如下:1.石灰石粉碎:将所使用的石灰石经过粉碎处理,得到细小的石灰石粉末。
2.煤粉预处理:对烟煤进行预处理,如振动筛等,去除其中粉尘、杂质等。
3.喷吹预处理剂:在燃烧炉的上部喷吹预处理剂,作用是在燃烧过程中将SO2转化为SO3,利于后续脱硫。
4.燃烧脱硝:燃烧过程中产生的NOx会通过脱硝设备进行处理,降低NOx的排放浓度。
5.湿法脱硫:利用镁石粉、石灰石、水等混合成脱硫液,在脱硫装置内与烟气反应,将SO2转化为MgSO3/MgSO4等产物,达到脱硫的效果。
二、反应原理在燃煤电厂中,SO2是主要的污染物之一。
利用镁法脱硫技术,通过以下的反应原理将SO2转化为硫酸镁等无害物质。
首先,在喷吹预处理剂的作用下,SO2被氧化为SO3,如下所示:SO2 + 1/2O2 → SO3然后,SO3与镁原料反应,生成MgSO4,如下所示:MgO + SO3 → MgSO4最后,MgSO4与石灰反应,生成硫酸镁和CaSO4,如下所示:MgSO4 + CaO → MgO + CaSO4反应结束后,CaSO4可被制成石膏板等建筑材料,实现资源循环利用。
三、技术优势镁法脱硫技术相较于其他脱硫技术,有如下优势:1. 高效:镁法脱硫吸收塔内通过喷淋镁石浆料获得10~15s的接触时间,比其他脱硫技术的接触时间更长,故脱硫效率高。
2.适用性强:镁法脱硫技术适用于高温、高湿、高硫、高脱硝等复杂工况下,且可以灵活调节反应参数,适应不同的燃煤电厂要求。
3.反应产物无污染:镁法脱硫技术所产生的硫酸镁等有用产物可以回收利用,不会造成排放物的二次污染。
镁法脱硫技术方案

镁法脱硫技术方案一、技术原理镁法脱硫技术指的是利用镁矿石制取镁粉,在饱和溶解的氧化钙乳液中加入镁粉,反应后生成氧化镁和二氧化硫,反应方程式如下:Mg + CaO + SO2 → MgO + CaSO3大量的氧化镁溶于氧化钙水浆中,由于氧化钙的石灰石的晶体结构很松散且易被水分解,再分解时放出大量的热同时产生氢氧化钙。
因此,在这种体系中,氢氧化钙气泡将氧化镁迅速搬移到并联反应区与SO2反应,将SO2转换为硫酸钙,从而达到脱硫的目的。
二、技术流程1. 镁粉的制备首先需要进行镁粉的制备,一般可以采用炉渣还原法、气相反应法等多种方法。
2. 制备饱和氧化钙乳液将石灰石粉末加水稀释,制备成水浆,然后再加热至80℃左右,用氧气吹制成悬液,最后控制pH值,制备成饱和氧化钙乳液。
3. 反应区的设计反应区一般设在石灰石浆液进口处,应具有足够的长度以达到充分反应的效果。
4. 镁粉投加将制备好的镁粉均匀地投入到氧化钙乳液中,以保证反应能够充分进行。
5. SO2的吸收在反应区内,SO2与氧化钙溶液和镁粉反应,生成氧化镁和硫酸钙,并逐渐沉淀析出。
6. 硫酸钙的回收硫酸钙沉淀下来后,可以通过旋滤机、压滤机等设备进行回收和处理,使其作为一种宝贵的工业原料应用。
7. 氧化钙的再生经过反应产生的氢氧化钙水浆可以通过水的蒸发,从而继续再生成氧化钙水浆,以备后续的脱硫过程。
三、优缺点分析优点:1. 镁法脱硫可以在较低的温度下进行,降低了能量消耗和反应的难度。
2. 镁法脱硫保持了硫酸钙的价值,使它可以作为工业原料进行回收和再利用。
3. 操作简单,操作环境相对较安全。
缺点:1. 镁法脱硫单次反应的速度较慢,需要较长的处理时间才能达到脱硫效果。
2. 进行镁法脱硫需要使用大量的镁粉,在生产成本上具有一定的影响。
四、应用领域镁法脱硫技术主要应用于钢铁、非金属矿山、电力等行业的脱硫处理过程中,能够较为有效地去除工业废气中的二氧化硫,达到环保要求,减少对环境的影响,可以推广到许多相关产业的实际生产中。
镁法脱硫废液和副产物处理系统
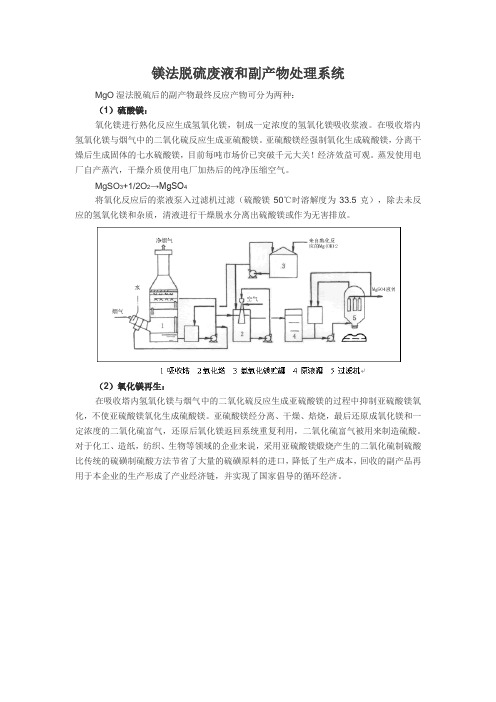
镁法脱硫废液和副产物处理系统
MgO湿法脱硫后的副产物最终反应产物可分为两种:
(1)硫酸镁:
氧化镁进行熟化反应生成氢氧化镁,制成一定浓度的氢氧化镁吸收浆液。
在吸收塔内氢氧化镁与烟气中的二氧化硫反应生成亚硫酸镁。
亚硫酸镁经强制氧化生成硫酸镁,分离干燥后生成固体的七水硫酸镁,目前每吨市场价已突破千元大关!经济效益可观。
蒸发使用电厂自产蒸汽,干燥介质使用电厂加热后的纯净压缩空气。
MgSO3+1/2O2→MgSO4
将氧化反应后的浆液泵入过滤机过滤(硫酸镁50℃时溶解度为33.5克),除去未反应的氢氧化镁和杂质,清液进行干燥脱水分离出硫酸镁或作为无害排放。
(2)氧化镁再生:
在吸收塔内氢氧化镁与烟气中的二氧化硫反应生成亚硫酸镁的过程中抑制亚硫酸镁氧化,不使亚硫酸镁氧化生成硫酸镁。
亚硫酸镁经分离、干燥、焙烧,最后还原成氧化镁和一定浓度的二氧化硫富气,还原后氧化镁返回系统重复利用,二氧化硫富气被用来制造硫酸。
对于化工、造纸,纺织、生物等领域的企业来说,采用亚硫酸镁煅烧产生的二氧化硫制硫酸比传统的硫磺制硫酸方法节省了大量的硫磺原料的进口,降低了生产成本,回收的副产品再用于本企业的生产形成了产业经济链,并实现了国家倡导的循环经济。
镁渣湿法脱硫性能的实验研究

渣呈炽热椭球状,温度可达1100 ℃,自然 冷 却 后 变
成灰色粉末,经 230μm 工 业 分 析 筛 筛 分 后 用 于 实 验.镁渣样品的元素组成如表1所示.
Keywords: magnesiumslag;wetfluedesulfurizationefficiency
我 国 镁 产 量 居 世 界 首 位 ,镁 渣 是 在 镁 冶 炼 过 程 中 产 生 的 工 业 废 渣 . 据 统 计 ,我 国 每 年 有 大 量 镁 渣 产 生[1]2,且 主 要 以 集 中 堆 砌 方 式 处 置 ,造 成 严 重 的 环境污染.有学者提出将镁渣应用于建筑材料制 造 [2]、环 境 污 染 治 理 等 [3] 方 面 . 镁 渣 中 的 碱 性 物 质 可 用 作 干 法 脱 硫 剂 . [4] 姬 克 丹 等 已 [5] 初 步 研 究 将 镁 渣 直 接 用 作 干 法 脱 硫 剂 ,但 其 脱 硫 效 率 较 低 . 目 前 镁 渣 在 湿 法 脱 硫 中 的 应 用 还 未 见 报 导 ,而 我 国 的 火 电 厂 脱 硫 装 置 超 过 90% 使 用 的 是 湿 法 脱 硫 . [6] 因 此 ,研 究 镁 渣 用 作 湿 法 脱 硫 剂 意 义 更 为 重 大 ,而 要提高脱硫效率关键要掌握影响脱硫效率的因素. 张 东 平 等 研 [7] 究 发 现 ,通 入 氧 气 比 不 通 氧 气 的 脱 硫 效 率 约 高 5% ;ZHAO 等 指 [8] 出 ,反 应 温 度 会 通 过 改 变 脱 硫 剂 的 溶 解 性 能 来 影 响 脱 硫 效 率 ;ORTIZ 等 研 [9] 究 表 明 ,钙 硫 比 对 脱 硫 效 率 也 有 重 要 影 响 .
Abstract: Inordertoachievewasterecycling,magnesiumslagwasusedasadesulfurizertoremoveSO2inwet fluegasdesulfurization.Thedesulfurizationproductsand mechanism werestudied.Theinfluencesofoxygendose,
镁法脱硫技术
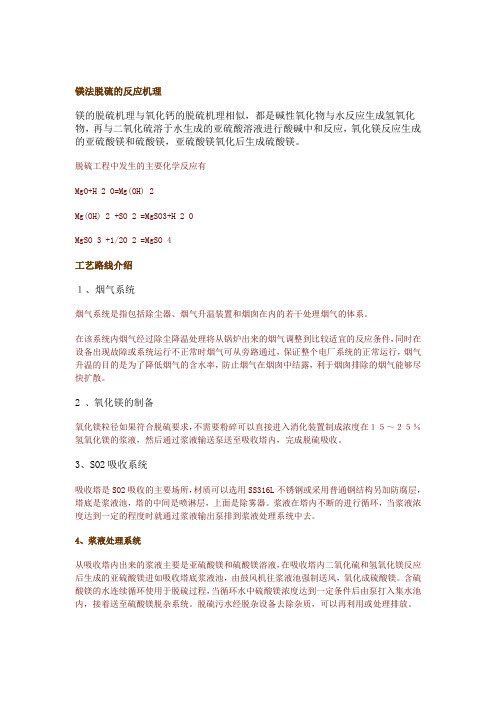
镁法脱硫的反应机理镁的脱硫机理与氧化钙的脱硫机理相似,都是碱性氧化物与水反应生成氢氧化物,再与二氧化硫溶于水生成的亚硫酸溶液进行酸碱中和反应,氧化镁反应生成的亚硫酸镁和硫酸镁,亚硫酸镁氧化后生成硫酸镁。
脱硫工程中发生的主要化学反应有MgO+H 2 O=Mg(OH) 2Mg(OH) 2 +SO 2 =MgSO3+H 2 OMgSO 3 +1/2O 2 =MgSO 4工艺路线介绍1、烟气系统烟气系统是指包括除尘器、烟气升温装置和烟囱在内的若干处理烟气的体系。
在该系统内烟气经过除尘降温处理将从锅炉出来的烟气调整到比较适宜的反应条件,同时在设备出现故障或系统运行不正常时烟气可从旁路通过,保证整个电厂系统的正常运行,烟气升温的目的是为了降低烟气的含水率,防止烟气在烟囱中结露,利于烟囱排除的烟气能够尽快扩散。
2 、氧化镁的制备氧化镁粒径如果符合脱硫要求,不需要粉碎可以直接进入消化装置制成浓度在15~25%氢氧化镁的浆液,然后通过浆液输送泵送至吸收塔内,完成脱硫吸收。
3、SO2吸收系统吸收塔是SO2吸收的主要场所,材质可以选用SS316L不锈钢或采用普通钢结构另加防腐层,塔底是浆液池,塔的中间是喷淋层,上面是除雾器。
浆液在塔内不断的进行循环,当浆液浓度达到一定的程度时就通过浆液输出泵排到浆液处理系统中去。
4、浆液处理系统从吸收塔内出来的浆液主要是亚硫酸镁和硫酸镁溶液,在吸收塔内二氧化硫和氢氧化镁反应后生成的亚硫酸镁进如吸收塔底浆液池,由鼓风机往浆液池强制送风,氧化成硫酸镁。
含硫酸镁的水连续循环使用于脱硫过程,当循环水中硫酸镁浓度达到一定条件后由泵打入集水池内,接着送至硫酸镁脱杂系统。
脱硫污水经脱杂设备去除杂质,可以再利用或处理排放。
很多情况下,尤其是中小型锅炉的脱硫,由于规模小,副产品发生量也小,大多采用处理排放,是将反应后的浆液经过固液分离后回收大部分水。
三氧化镁脱硫工艺的技术特点氧化镁脱技术是一种成熟度的脱硫工艺,氧化脱硫工艺在世界各地都有非常多的应用业绩。
氧化镁湿法脱硫废水处理工艺流程探讨

氧化镁湿法脱硫废水处理工艺流程探讨首先,酸性废水中的二氧化硫氧化。
这一步骤是通过将酸性废水喷洒
或者雾化至一个碱性环境中,将二氧化硫氧化为硫酸镁。
这里的碱性环境
可以通过加入氢氧化钙或者氢氧化钠等碱性物质来实现。
在此过程中,通
过控制喷洒浓度和温度等参数,可以使废水中的二氧化硫得到充分氧化。
其次,硫酸镁的沉淀。
在氧化反应结束后,废水中的硫酸镁会形成固
体沉淀。
这一步骤的关键是控制碱性物质的投加量,使其超过硫酸镁的溶
解度,以促进硫酸镁的沉淀。
硫酸镁的沉淀是一种放热反应,因此需要适
当降低反应温度,防止温度过高造成放热过程不可控。
最后,废水后续处理。
经过上述两个步骤处理后的脱硫废水,仍然含
有一定量的固体颗粒物质和硫酸残余。
为了达到排放标准,需要对废水进
行进一步处理。
常见的处理方法包括沉淀处理、过滤处理和吸附处理等。
沉淀处理是通过加入适当的沉淀剂,使废水中的固体颗粒物质沉淀并分离
出来;过滤处理是通过将废水通过滤料进行过滤,去除固体颗粒物质;吸
附处理是通过添加适当的吸附剂,吸附废水中的硫酸镁和其他残余物质。
综上所述,氧化镁湿法脱硫废水处理工艺流程包括二氧化硫氧化、硫
酸镁沉淀和废水后续处理三个步骤。
通过合理控制各个步骤中的操作参数,可以有效处理脱硫废水,达到排放标准。
值得注意的是,在实践应用中,
还需要根据具体情况来选择化学药剂和处理设备,并结合其他工艺优化措施,以实现更高效的废水处理。
- 1、下载文档前请自行甄别文档内容的完整性,平台不提供额外的编辑、内容补充、找答案等附加服务。
- 2、"仅部分预览"的文档,不可在线预览部分如存在完整性等问题,可反馈申请退款(可完整预览的文档不适用该条件!)。
- 3、如文档侵犯您的权益,请联系客服反馈,我们会尽快为您处理(人工客服工作时间:9:00-18:30)。
氧化镁湿法烟气脱硫废水处理技术探讨
1镁法脱硫技术的发展
氧化镁法在湿法烟气脱硫技术中是仅次于钙法的又一主要脱硫技术。
据介绍,氧化镁再生法的脱硫工艺最早由美国开米科公司(Chemico—Basic)在20世纪60年代开发成功,70年代后费城电力公司(PECO)与United&Constructor合作研究氧化镁再生法脱硫工艺,经过几千小时的试运行之后,在三台机组(其中两台分别为150MW和320MW)进行了全规模的FGD系统和两个氧化镁再生系统建设,上述系统于1982年建成并投入运行,1992年以后停运硫酸制造厂,直接将反应产物硫酸镁销售。
1980年美国DUCON公司在PHILADELPHAELECTRICEDDYSTONESTATION成功建成实施氧化镁湿法脱硫系统,运行至今,效果良好。
随后韩国和台湾地区也发展了自己的湿式镁法脱硫技术,目前在台湾95%的电站采用氧化镁法脱硫。
近几年国内的氧化镁湿法脱硫发展较快,2001年,清华大学环境系承担了国家“863”计划中《大中型锅炉镁法脱硫工艺工业化》的课题,对镁法脱硫的工艺参数、吸收塔优化设计和副产品回收利用等进行了深入的研究,并在4t/h、12t/h锅炉上进行了中试,在35t/h锅炉上进行了工程应用。
湿式镁法脱硫工艺又可分为氧化镁/亚硫酸镁法、氧化镁/硫酸镁抛弃法、氧化镁/硫酸镁回收法等。
本文主要介绍应用规模较大、前景广阔的氧化镁/亚硫酸镁工艺中的废水处理工艺。
2脱硫废水处理技术概况
湿法烟气脱硫工艺中存在废水处理问题,虽然有很多电厂的脱硫系统
都配有废水处理系统,但国内目前对脱硫废水的处理工艺研究较少,其中关注最多的是石灰石/石膏法产生的脱硫废水,对于镁法脱硫产生的废水的研究就更少了。
镁法脱硫废水处理现在多是引用和借鉴石灰石/石膏法脱硫废水处理经验。
为了维持脱硫装置浆液循环系统物质的平衡,防止烟气中可溶物质超过规定值和保证副产物品质,必须从循环系统中排放一定量的废水。
因此,没有预处理塔的镁法脱硫和石灰石/石膏法脱硫过程产生的废水均来源于吸收塔的排放水。
3镁法脱硫废水水量和水质
3.1脱硫废水水量
脱硫废水的水量与烟气中的HCl和HF、吸收塔内浆液中的Cl-和SO42-浓度、脱硫用水的水质等有关。
当进入吸收塔内的烟气量一定时,废水排放量由以下条件确定:
(1)脱硫废水的水量取决于烟气中的HCl(HF)浓度,而烟气中的HCl(HF)主要来自于机组燃烧的煤。
煤中Cl(F)的含量越高,烟气中的HCl(HF)浓度就越高,废水排放量也就越大。
(2)脱硫废水的水量关键取决于吸收塔内Cl-的控制浓度。
浆液中的Cl-浓度太高,亚硫酸镁品质下降且脱硫效率降低,对设备的抗腐蚀要求提高;对浆液中的Cl-浓度要求过低,脱硫废水的水量增大,废水处理的成本提高。
根据经验,脱硫废水中的Cl-浓度控制在10~20g/L为宜。
(3)脱硫废水的水量还取决于吸收塔内SO42-的控制浓度。
浆液中SO42-浓度太高,会造成浆液粘性增加,影响亚硫酸镁的结晶,脱硫效率降低;浆液中SO42-的控制浓度过低,SO32-氧化成SO42-的正反应加速,
亚硫酸镁的产量降低。
(4)脱硫废水的水量还与脱硫工艺用水的Cl-浓度有关。
脱硫工艺用水的Cl-浓度越高,脱硫废水量越大。
但由于常规脱硫工艺用水Cl-浓度一般不超过0.1g/L,远远小于脱硫废水中的Cl-浓度,故脱硫工艺用水的Cl-浓度对脱硫废水量的影响较小。
同时可以查看中国污水处理工程网更多技术文档。
3.2脱硫废水水质
脱硫废水的特点如下:
(1)镁法脱硫系统废水pH值较钙法(钙法一般为4~6)高,一般在6~7;
(2)悬浮物(亚硫酸镁颗粒、SiO2、Al和Fe的氢氧化物)含量很高,浓度可达几万mg/L;
(3)氟化物、COD和重金属超标,其中包括我国严格限制排放的第Ⅰ类污染物,如Hg、As、Pb等;
(4)盐分极高,含有大量的SO42-、Cl-和SO32-等离子,其中SO42-质量分数可达12%,Cl-的质量分数在1%~2%。
脱硫废水的具体水质与燃煤的种类、电除尘器的极数、脱硫氧化风量、吸收塔内Cl-的控制浓度、脱硫工艺用水的水质情况等因素有关。
4镁法脱硫废水处理系统
脱硫废水处理典型工艺见下图。
从脱硫塔排出的浆液含固量约15%,主要的固体成分是亚硫酸镁,经
系统,其含固量约3%。
脱硫废水处理系统包括:中和、反应、絮凝、澄清。
(1)中和
烟气脱硫产生的酸性废水首先进入中和箱,通过控制石灰乳的投加量,维持废水在中和箱中的pH值,一般为8.5~9.0,由于在不同的pH值下,金属氢氧化物的溶度积相差较大,故反应时应严格控制其pH值。
在这一范围内可使一些重金属,如铁、铜、铅、镍和铬生成氢氧化物沉淀。
同时废水中大量的SO42-与Ca2+结合产生石膏沉淀。
(2)反应
中和箱中的废水自流进入反应箱,废水中大量Mg等金属离子以非常细小的氢氧化物和络合物形式从废水中析出。
对于汞、铜等重金属,一般采用加入有机硫如TMT15,以产生HgS、CuS等沉淀,这两种沉淀物质溶解度都很小,溶度积数量级在10-50~10-40之间。
(3)絮凝
由于形成的氢氧化物及金属硫化物颗粒细小,在废水中不易沉降下来,因此通过投加复合铁使废水中细小颗粒在缓慢搅拌的条件下形成絮凝体。
在进入澄清器前向废水中投加助凝剂(PAM)来降低颗粒的表面张力,强化颗粒的长大过程,进一步促进氢氧化物和硫化物的沉淀,使细小的絮凝物慢慢变成更大、更容易沉积的絮状物,确保在澄清器中能完成固液分离。
(4)澄清
由絮凝箱来的废水在澄清器中进行固液分离,澄清器常采用易安装维护的竖流式澄清器,运行稳定可靠。
澄清器在重力作用下形成浓缩污泥,
浓缩污泥通过污泥螺杆泵将污泥排出,大部分污泥经污泥泵排到板框压滤机进行脱水,小部分污泥作为接触污泥返回废水反应池,提供沉淀所需的晶核。
清水由周边出水三角堰流入出水箱。
由于废水中pH较高(8.5~9.0),配备pH调节系统,当pH值高于9时,pH调节系统控制HC1计量泵投加,以确保出水箱中水质达标排放(pH 为6~9)。
5结论与建议
(1)目前国内对镁法脱硫废水处理的研究力度不够,现仅有武汉大学做过关于混凝剂的试验研究,且还没有进行系统的处理试验研究;
(2)镁法脱硫废水的水质和钙法脱硫废水的水质差异很大,但整体工艺还是沿用钙法脱硫废水工艺,不能适应水质的变化,污泥浓缩效果差,出水达标困难;
(3)镁法脱硫废水中的COD较高,尚待解决COD的去除问题;
(4)随着镁法脱硫技术的推广,其废水处理技术必须深入研究,以适应其发展。