脱硫废水处理工艺流程图
脱硫废水处理.
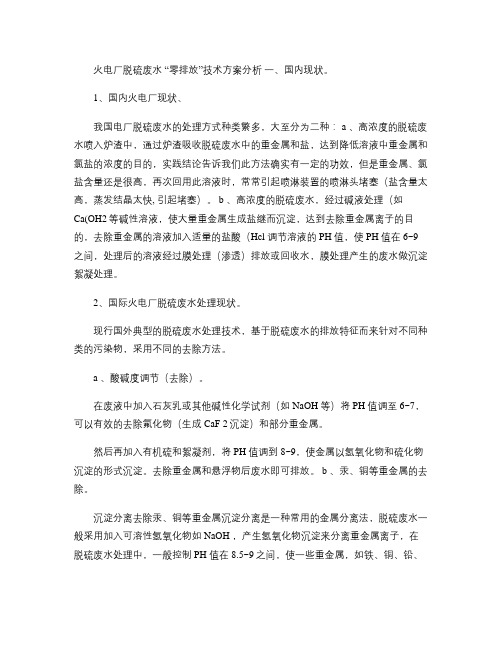
火电厂脱硫废水“零排放”技术方案分析一、国内现状。
1、国内火电厂现状、我国电厂脱硫废水的处理方式种类繁多,大至分为二种: a 、高浓度的脱硫废水喷入炉渣中,通过炉渣吸收脱硫废水中的重金属和盐,达到降低溶液中重金属和氯盐的浓度的目的,实践结论告诉我们此方法确实有一定的功效,但是重金属、氯盐含量还是很高,再次回用此溶液时,常常引起喷淋装置的喷淋头堵塞(盐含量太高,蒸发结晶太快, 引起堵塞)。
b 、高浓度的脱硫废水,经过碱液处理(如Ca(OH2等碱性溶液,使大量重金属生成盐继而沉淀,达到去除重金属离子的目的,去除重金属的溶液加入适量的盐酸(Hcl 调节溶液的PH 值,使PH 值在6~9之间,处理后的溶液经过膜处理(渗透)排放或回收水,膜处理产生的废水做沉淀絮凝处理。
2、国际火电厂脱硫废水处理现状。
现行国外典型的脱硫废水处理技术,基于脱硫废水的排放特征而来针对不同种类的污染物,采用不同的去除方法。
a 、酸碱度调节(去除)。
在废液中加入石灰乳或其他碱性化学试剂(如NaOH 等)将PH 值调至6~7,可以有效的去除氟化物(生成CaF 2沉淀)和部分重金属。
然后再加入有机硫和絮凝剂,将PH 值调到8~9,使金属以氢氧化物和硫化物沉淀的形式沉淀。
去除重金属和悬浮物后废水即可排放。
b 、汞、铜等重金属的去除。
沉淀分离去除汞、铜等重金属沉淀分离是一种常用的金属分离法,脱硫废水一般采用加入可溶性氢氧化物如NaOH ,产生氢氧化物沉淀来分离重金属离子,在脱硫废水处理中,一般控制PH 值在8.5~9之间,使一些重金属,如铁、铜、铅、镍和铬生成氢氧化物沉淀。
对于铜、汞等重金属,一般采用加入可溶性硫化物如硫化钠,使其产生Hg 2S 、CuS 等沉淀,这二种沉淀的物质溶解度都很小,溶度积数量级在10-40~10-50之间,对于汞使用硫化钠,只要添加小于1mg/L的S 2-,就对小于1ug/L浓度的汞产生作用,为了改善重金属析出过程制备一种能良好沉淀的泥浆,一般可使用三价铁盐如Fecl 3及一般为阴离子的絮凝剂,通过以上二级处理就可达标。
电厂脱硫废水的零排放技术

- 133 -生 态 与 环 境 工 程0 引言由于我国用电量急剧增加,燃烧煤炭释放的污染气体也有所增加。
为了减少这些污染气体的产生,脱硫技术快速发展。
常见的脱硫技术有以下4种:湿式洗涤器、喷雾干式洗涤器、吸附剂注射和可再生工艺[1]。
由于石灰石烟气脱硫系统的脱硫废水含盐浓度高,腐蚀设备,因此脱盐效率很低。
需要定期对脱硫浆进行稀释,用水清洗设备的同时排放脱硫废水[1]。
目前,电厂脱硫废水由于成分复杂,通常含有悬浮固体、盐(氯、硫酸盐)和镉、铅和汞等重金属,其通常呈酸性,会引起设备的腐蚀和结垢等问题[2]。
表1为安徽省某电厂脱硫废水中的主要离子浓度,其中含有不能充分利用的镁离子和氯离子。
随着脱硫废水循环,氯离子浓度增加,使废水呈酸性。
石灰石的溶解被抑制,导致腐蚀。
因此,不正确处理脱硫废水就会造成严重的环境问题[1]。
目前,低温浓缩-高温蒸发工艺、膜浓缩-蒸发结晶工艺以及离子置换电渗析-蒸发工艺是目前电厂废水零排放的主流工艺。
其中,与其他两种工艺相比,膜浓缩-蒸发结晶工艺效果更稳定、投资运行成本低以及具有一定经济效益[3]。
对此,该文以某电厂废水零排放技术的运行数据为依托,详细分析了膜浓缩-蒸发结晶技术在该项目中的应用情况,以期为电厂脱硫废水的零排放技术的发展提供参考。
表1 某电厂脱硫废水中主要离子浓度离子(mg/L)钙离子镁离子钠离子氯离子硫酸根镉离子化学需氧量SS 数值1971.125440.53107817204.34683.40.173.8754771 项目概述某电厂始建于2005年,主要用于供给电网用电和工业园区供热,共配备2台装机容量为60万kW 的发电机,年发电量约为50亿度。
由于建设久远,因此其产生的脱硫废水水质波动大、钙镁离子含量高。
由于国家对电力能源行业的改革,该电厂开始进行电厂脱硫废水的无害化和零排放处理。
对该某电厂采用膜浓缩-蒸发结晶工艺进行脱硫废水处理。
其主要原理是脱硫废水经过预处理,然后通过膜法浓缩。
常见的十七种脱硫工艺原理及工艺图
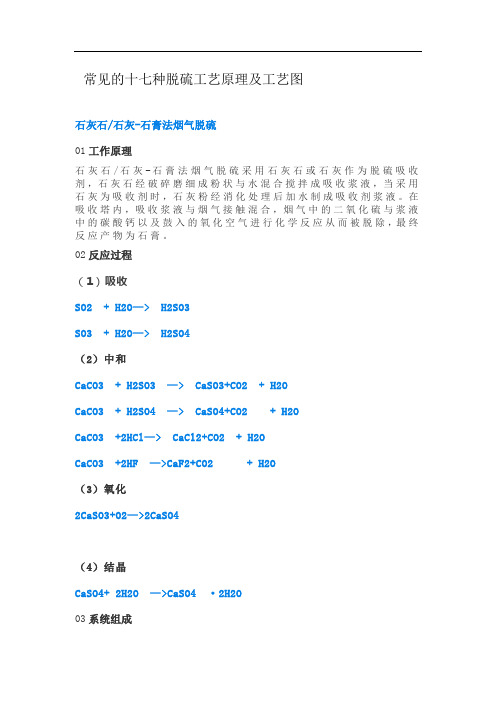
常见的十七种脱硫工艺原理及工艺图石灰石/石灰-石膏法烟气脱硫01工作原理石灰石/石灰-石膏法烟气脱硫采用石灰石或石灰作为脱硫吸收剂,石灰石经破碎磨细成粉状与水混合搅拌成吸收浆液,当采用石灰为吸收剂时,石灰粉经消化处理后加水制成吸收剂浆液。
在吸收塔内,吸收浆液与烟气接触混合,烟气中的二氧化硫与浆液中的碳酸钙以及鼓入的氧化空气进行化学反应从而被脱除,最终反应产物为石膏。
02反应过程(1)吸收SO2 + H2O—> H2SO3SO3 + H2O—> H2SO4(2)中和CaCO3 + H2SO3 —> CaSO3+CO2 + H2OCaCO3 + H2SO4 —> CaSO4+CO2 + H2OCaCO3 +2HCl—> CaCl2+CO2 + H2OCaCO3 +2HF —>CaF2+CO2 + H2O(3)氧化2CaSO3+O2—>2CaSO4(4)结晶CaSO4+ 2H2O —>CaSO4 ·2H2O03系统组成脱硫系统主要由烟气系统、吸收氧化系统、石灰石/石灰浆液制备系统、副产品处理系统、废水处理系统、公用系统(工艺水、压缩空气、事故浆液罐系统等)、电气控制系统等几部分组成。
04工艺流程锅炉/窑炉—>除尘器—>引风机—>吸收塔—>烟囱来自于锅炉或窑炉的烟气经过除尘后在引风机作用下进入吸收塔,吸收塔为逆流喷淋空塔结构,集吸收、氧化功能于一体,上部为吸收区,下部为氧化区,经过除尘后的烟气与吸收塔内的循环浆液逆向接触。
系统一般装3-5台浆液循环泵,每台循环泵对应一层雾化喷淋层。
当只有一台机组运行时或负荷较小时,可以停运1-2层喷淋层,此时系统仍保持较高的液气比,从而可达到所需的脱硫效果。
吸收区上部装二级除雾器,除雾器出口烟气中的游离水份不超过75mg/N m3。
吸收SO2后的浆液进入循环氧化区,在循环氧化区中,亚硫酸钙被鼓入的空气氧化成石膏晶体。
(完整版)氨法脱硫废水处理工艺流程.(详细方案)

加石灰浆进行废水碱化处理时,水中的酸(H2SO4 H2SO3)按如下反应得到中和:H2SO4+Ca(OH)2-->CaSO4+2H2O
H2SO3+Ca(OH)2-->CaSO3+2H2O OH-离子数量决定了基本范围内的废水PH值。
5)将氢氧化物泥浆输送至压滤机进行脱水。
在沉淀系统中,加入絮凝剂以便使沉淀颗粒长大更易沉降,悬浮物从澄清浓缩器中分离出来后,一部分泥浆通过污泥循环泵返回到中和箱,以利于更好地沉降,另一部分则通过污泥输送泵输送至压滤机进行脱水。处理后的清水送至厂区指定的排放点。
1.3脱硫废水处理流程
2、
2.1助凝剂加药系统
(6)石灰加药系统:5%~10%的石灰浆液加入到中和箱中,用作中和剂和沉淀剂。以达到设定的PH值。石灰加药系统流程如下:
2.2污泥压缩系统
污泥压缩系统 在废水加药混合澄清浓缩过程中产生的氢氧化物污泥、硫化物污泥经污泥输送泵送至压滤机进行压滤脱水。
其工艺流程为:
3、
3.1脱硫废水处理工艺
1)烟气脱硫设备产生的弱酸性废水(通常PH值为5.0~5.5左右)通过管道流入中和箱。同时,石灰浆按PH值和流量的比例及石灰浆浓度加入废水中。使废水的PH值提高到9.0~9.5左右,此PH值范围适于沉淀大多数重金属。监测废水PH计安装在沉降箱上,当pH计显示不准确时,需对PH电极用3~5%的稀盐酸清洗,然后重新校准后使用。
氨法脱硫废水处理工艺
脱硫废水处理包括以下三个分系统:废水处理系统,化学加药系统,污泥处理系统及排污系统。
1、
1.1脱硫废水处理过程
HPF脱硫工艺流程图
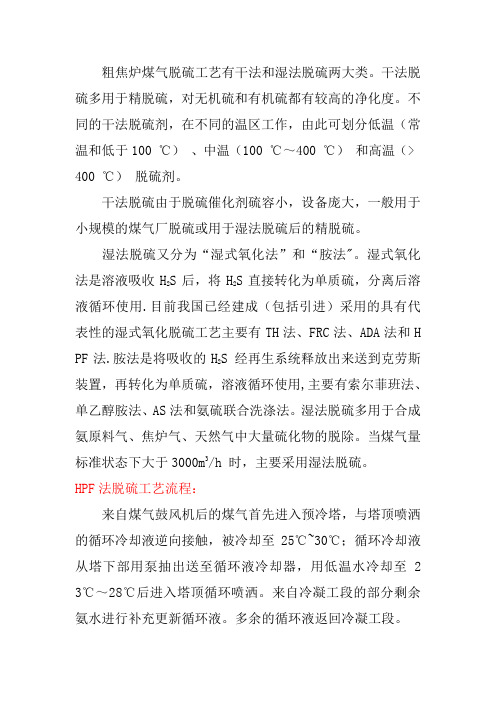
粗焦炉煤气脱硫工艺有干法和湿法脱硫两大类。
干法脱硫多用于精脱硫,对无机硫和有机硫都有较高的净化度。
不同的干法脱硫剂,在不同的温区工作,由此可划分低温(常温和低于100 ℃)、中温(100 ℃~400 ℃)和高温(> 400 ℃)脱硫剂。
干法脱硫由于脱硫催化剂硫容小,设备庞大,一般用于小规模的煤气厂脱硫或用于湿法脱硫后的精脱硫。
湿法脱硫又分为“湿式氧化法”和“胺法"。
湿式氧化法是溶液吸收H2S后,将H2S直接转化为单质硫,分离后溶液循环使用.目前我国已经建成(包括引进)采用的具有代表性的湿式氧化脱硫工艺主要有TH法、FRC法、ADA法和H PF法.胺法是将吸收的H2S 经再生系统释放出来送到克劳斯装置,再转化为单质硫,溶液循环使用,主要有索尔菲班法、单乙醇胺法、AS法和氨硫联合洗涤法。
湿法脱硫多用于合成氨原料气、焦炉气、天然气中大量硫化物的脱除。
当煤气量标准状态下大于3000m3/h 时,主要采用湿法脱硫。
HPF法脱硫工艺流程:来自煤气鼓风机后的煤气首先进入预冷塔,与塔顶喷洒的循环冷却液逆向接触,被冷却至25℃~30℃;循环冷却液从塔下部用泵抽出送至循环液冷却器,用低温水冷却至2 3℃~28℃后进入塔顶循环喷洒。
来自冷凝工段的部分剩余氨水进行补充更新循环液。
多余的循环液返回冷凝工段。
预冷塔后煤气并联进入脱硫塔A、脱硫塔B,与塔顶喷淋下来的脱硫液逆流接触,以吸收煤气中的硫化氢(同时吸收煤气中的氨,以补充脱硫液中的碱源)。
脱硫后煤气进入下道工序进行脱氨脱苯.脱硫基本反应如下:H2S+NH4OH→NH4HS+H2O 2NH4OH+H2S→(NH4)2S+2H2O NH4OH+HCN→NH4CN+H2O NH4OH+CO2→NH4HCO3NH4OH+NH4HCO3→(NH4)2CO3+ H2O吸收了H2S、HCN的脱硫液从脱硫塔A、B下部自流至反应槽,然后用脱硫液循环泵抽送进入再生塔再生.来自空压机站压缩空气与脱硫富液由再生塔下部并流进入再生塔A、B,对脱硫液进行氧化再生,再生后的溶液从塔顶经液位调节器自流回脱硫塔循环使用.再生塔内的基本反应如下:NH4HS+1/2O2→NH4OH+S (NH4)2S+1/2O2+ H2O→ 2NH4OH+S(NH4)2Sx+1/2O2+ H2O→2NH4OH+Sx除上述反应外,还进行以下副反应:2NH4HS+2O2→(NH4)2S2O3+ H2O 2(NH4)2S2O3+O2→2(NH4)2SO4+2S从再生塔A、B顶部浮选出的硫泡沫,自流入硫泡沫槽,在此经搅拌,沉降分离,排出清液返回反应槽,硫泡沫经泡沫泵加压后送压滤机进行脱水,形成硫膏成品。
现运行的各种脱硫工艺流程图汇总

现运行的各种脱硫工艺流程图汇总1. 烟气脱硫工艺流程图烟气脱硫是通过将烟气中的二氧化硫进行吸收除去的过程。
流程图中通常包括吸收塔、循环泵、再循环塔、氧化风机等设备,并通过往吸收塔中喷洒脱硫剂来实现脱硫的目的。
2. 石灰石脱硫工艺流程图石灰石脱硫是利用石灰石和水反应生成石灰浆,再通过与烟气接触,从而达到脱硫的效果。
流程图中通常包括石灰石仓、石灰石浆液制备系统、反应器、除尘器等设备。
3. 氨法脱硫工艺流程图氨法脱硫是利用氨水与烟气中的二氧化硫进行化学反应,生成硫酸铵,从而实现脱硫的目的。
流程图中通常包括氨液制备系统、氨喷射系统、除尘器、脱硫塔等设备。
4. 活性炭吸附脱硫工艺流程图活性炭吸附脱硫是通过将活性炭颗粒放置在烟气中,利用活性炭对烟气中的二氧化硫进行吸附,从而实现脱硫的目的。
流程图中通常包括活性炭吸附装置、再生系统、除尘器等设备。
以上为目前运行的几种常见脱硫工艺流程图的汇总,不同的工业生产场景可能会选择不同的脱硫工艺方案来满足排放标准和生产需求。
在工业生产中,二氧化硫是一种常见的排放物质,对环境和人体健康带来严重影响。
因此,脱硫工艺的实施是必不可少的。
脱硫工艺的选择通常取决于生产过程中产生的二氧化硫的量、浓度、烟气温度、湿度以及其他一些特殊的操作要求。
烟气脱硫工艺是应用较为广泛的一种脱硫方法。
其工艺流程图中通常包含吸收塔、循环泵、再循环塔、氧化风机等关键设备。
该工艺的关键在于将烟气中的二氧化硫进行吸收,以便将其除去。
通常会向吸收塔中喷洒脱硫剂,使得二氧化硫与脱硫剂发生化学反应,从而减少烟气中的污染物含量。
另一种常见的脱硫工艺是石灰石脱硫。
在该工艺中,石灰石和水发生反应生成石灰浆,然后通过与烟气接触,达到脱硫的效果。
流程图中主要包括石灰石仓、石灰石浆液制备系统、反应器、除尘器等关键设备。
石灰石脱硫工艺具有操作简单、成本较低、脱硫效率高的特点,因此在一些工业生产中得到了广泛应用。
氨法脱硫是另一种常用的脱硫工艺。
常见的十七种脱硫工艺原理及工艺图
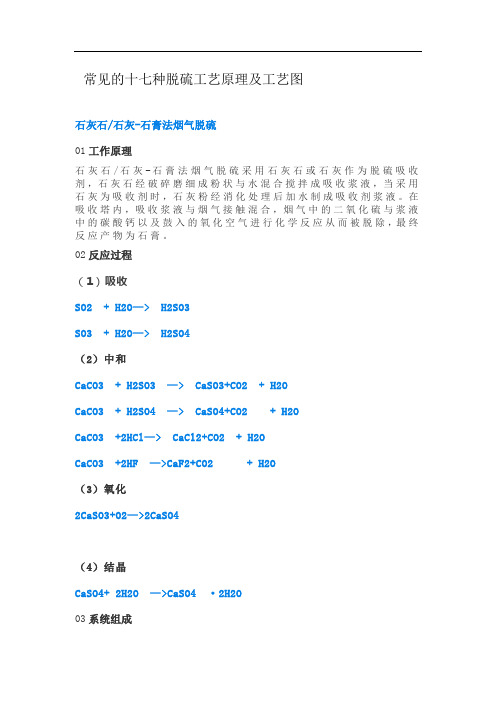
常见的十七种脱硫工艺原理及工艺图石灰石/石灰-石膏法烟气脱硫01工作原理石灰石/石灰-石膏法烟气脱硫采用石灰石或石灰作为脱硫吸收剂,石灰石经破碎磨细成粉状与水混合搅拌成吸收浆液,当采用石灰为吸收剂时,石灰粉经消化处理后加水制成吸收剂浆液。
在吸收塔内,吸收浆液与烟气接触混合,烟气中的二氧化硫与浆液中的碳酸钙以及鼓入的氧化空气进行化学反应从而被脱除,最终反应产物为石膏。
02反应过程(1)吸收SO2 + H2O—> H2SO3SO3 + H2O—> H2SO4(2)中和CaCO3 + H2SO3 —> CaSO3+CO2 + H2OCaCO3 + H2SO4 —> CaSO4+CO2 + H2OCaCO3 +2HCl—> CaCl2+CO2 + H2OCaCO3 +2HF —>CaF2+CO2 + H2O(3)氧化2CaSO3+O2—>2CaSO4(4)结晶CaSO4+ 2H2O —>CaSO4 ·2H2O03系统组成脱硫系统主要由烟气系统、吸收氧化系统、石灰石/石灰浆液制备系统、副产品处理系统、废水处理系统、公用系统(工艺水、压缩空气、事故浆液罐系统等)、电气控制系统等几部分组成。
04工艺流程锅炉/窑炉—>除尘器—>引风机—>吸收塔—>烟囱来自于锅炉或窑炉的烟气经过除尘后在引风机作用下进入吸收塔,吸收塔为逆流喷淋空塔结构,集吸收、氧化功能于一体,上部为吸收区,下部为氧化区,经过除尘后的烟气与吸收塔内的循环浆液逆向接触。
系统一般装3-5台浆液循环泵,每台循环泵对应一层雾化喷淋层。
当只有一台机组运行时或负荷较小时,可以停运1-2层喷淋层,此时系统仍保持较高的液气比,从而可达到所需的脱硫效果。
吸收区上部装二级除雾器,除雾器出口烟气中的游离水份不超过75mg/N m3。
吸收SO2后的浆液进入循环氧化区,在循环氧化区中,亚硫酸钙被鼓入的空气氧化成石膏晶体。
脱硫工段工艺流程图

脱硫工段工艺流程图
脱硫工段是热电厂燃煤发电过程中的重要环节,其主要目的是减少燃煤产生的二氧化硫排放,保护环境。
下面我将详细介绍脱硫工段的工艺流程图。
首先,燃煤进入燃烧室,与空气进行充分的燃烧反应,产生大量的烟尘和废气。
废气中含有二氧化硫,需要进行脱硫处理。
第一步是氧化反应。
废气经过预处理后,进入净化塔顶部分布的喷头区域,与一定比例的含氧气体进行接触。
氧化剂主要有空气和二氧化氯等,能够将二氧化硫氧化为二氧化硫酸。
第二步是吸收反应。
氧化后的废气经过喷头区域,进入喷雾层。
在喷雾层中,废气与喷雾液体进行接触,喷雾液体是一种含有吸收剂的溶液,一般为石灰石浆液。
在此过程中,二氧化硫与液滴中的吸收剂发生吸收反应,生成硫酸。
第三步是分离反应。
经过吸收的废气与喷头层中的液滴一起下沉,进入喷雾塔的下部,此处设有分离装置。
在分离过程中,废气和液滴发生反向冲刷,液滴中的硫酸被回收下来,而废气中的烟尘和其它颗粒物被截留,净化后的废气从塔顶排放。
第四步是脱水处理。
分离后的液滴中含有大量水分,需要进行脱水处理。
液滴进入脱水装置,通过旋流器等装置将水分与液滴分离,脱水后的液滴进入再生系统。
最后,通过再生系统,将脱水后的液滴进行再利用。
具体的再
生方式受到多种因素的影响,一般采用高温回归的方法,将液滴中的硫酸分解为二氧化硫和水,再经过氧化反应转化为硫酸,用于循环再利用。
以上就是脱硫工段的工艺流程图。
通过该流程,热电厂能够有效地减少燃煤产生的二氧化硫排放,保护环境,同时实现废气中的硫酸回收和再利用。